Проектирование литейного цеха


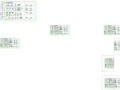
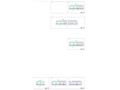
- Добавлен: 24.01.2023
- Размер: 2 MB
- Закачек: 3
Описание
Состав проекта
![]() |
![]() |
![]() ![]() ![]() |
![]() ![]() ![]() |
![]() ![]() ![]() |
![]() ![]() ![]() |
![]() ![]() ![]() |
![]() ![]() ![]() |
![]() |
![]() ![]() ![]() ![]() |
![]() ![]() ![]() ![]() |
Дополнительная информация
Диплом безопасность.doc
1 Техника безопасности
1.1 Требования безопасности к машинам для литья в металлические формы (кокили).
К машинам для литья в металлические формы (кокили) предъявлены следующие требования безопасности:
- конструкция кокилей и прессформ должна обеспечивает совершенно плотное соединение двух и более форм точную и надежную подвижных частей;
- операции по заливке металла в кокиль нанесение защитных покрытий на их рабочие поверхности на многопозиционных машинах следует механизировать. Позиции на которых производятся эти операции снабжены вытяжной вентиляцией;
- при ручной установке стержней необходимо предусматривать блокировку предотвращающую возможность смыкания подвижных частей при их простановке;
- кокили и прессформы оснащаются толкателями для выталкивания отливок исключающие необходимость применения заключающими необходимость введения руками ломика или крючка в опасную зону;
- машины для литья в кокиль оборудованы термостатами для нагрева кокилей перед первой заливкой и поддержание технологической температуры во всех его частях в процессе изготовления отливок;
- машины для литья в кокиль оборудованы вытяжными зонтами (на позициях заливки);
- установлена аппаратура автоматически обеспечивающая технологическую выдержку времени кристаллизации и охлаждения отливки в кокиле сборке и разборке подвижных частей.
1.2 Требования безопасности при подготовке заливки металла в кокиль . Требования безопасности приведены в таблице 5.1
Таблица 7.1 Требования безопасности при подготовке к заливке металла в кокиль
Минимальная ширина проходов между кокилями м
Температура нагрева кокиля перед началом работы °С
Нанесение слоя облицовочного покрытия на поверхность кокиля
Толщина слоя облицовочного покрытия мм
Рабочая температура формы при литье тонкостенных отливок °С
Перед заливкой металлические формы окрашиваются просушиваются и нагреваются. Нагрев форм жидким металлом не допускается.
Металлические ковши для заливки металла покрываются литейной краской и просушиваются.
1.3 Безопасность производственных процессов.
Транспортировка расплавленного металла к местам его заливки в формы производится по заранее установленным маршрутам погрузчиками.
В отдельных случаях допускается переноска жидкого металла в ковшах при ширине проходов не менее 2 м. вручную при массе переносимого груза не более 15 кг.
Заполнение заливочных ковшей и тиглей раздаточных печей металлом допускается не более чем на 088 их внутренней высоты.
Для разливки металла разрешается использовать только ковши с предварительно проверенными исправленными поворотными механизмами и стопорными устройствами тщательно просушенные и подогретые.
Шлак и остатки металла сливают из ковшей в сухие изложницы
1.4 Электробезопасность
Заливочный участок по степени поражения электрическим током согласно ПУЭ (раздел 1 – «Общие требования») относится к особо опасным что определяется наличием токоведущего пола возможностью прикосновения человека к имеющим соединения с землей металлоконструкциям с одной стороны и металлическим корпусом с другой.
Для питания электрооборудования принята электрическая сеть 3-х фазная 4-х проводная схема с глухо-заземленной нейтралью. Для устранения опасности поражения людей током в проекте предусмотрено:
- производить измерение сопротивления изоляции проводников;
- электроразводки выполнить в трубах и металлорукавах;
- оборудование занулить;
-использование сигнализации включения силовых частей оборудования знаков безопасности;
2 Производственная санитария
2.1 Метеорологические условия в производственных помещениях
Метеорологические условия определяются по ГОСТу 12.1.005-88.
Участок заливки в кокиль относится к участкам со значительным выделением тепла. Выделение его от металлических форм более 23 ДЖмС.
Категория работы заливщика – III . Это тяжелые физические работы переноска значительных тяжестей (свыше 10 кг) тепловое излучение энергозатраты свыше 290 ДЖ. Согласно ГОСТу 12.1.005-88 определяем допустимые нормы температуры относительной влажности скорости движения воздуха в рабочей зоне производственных помещений с избытком явного тепла в теплый и холодный период года. Эти данные сведены в таблицу 5.2
Таблица 7.2 Температура относительной влажности и скорость
движения воздуха в рабочей зоне участка литья в кокиль
Скорость движения воздуха мс
Допустимая (при т=24°С)
Оптимальная(небо-лее)
На участке кокильного литья источником теплового излучения является жидкий металл поэтому допустимая интенсивность теплового излучения при
% облучения тела–140 Втм2. Для защиты необходимы средства индивидуальной защиты лица и глаз.
2.2 Содержание вредных веществ в воздухе рабочей зоны.
В воздухе рабочей зоны содержится следующие вредные вещества:
- окись углерода ПДК= 20 мг м3 – 4 класс опасности;
- кремнеземосодержащая пыль (S
- аэрозоли алюминиевых сплавов ПДК=2 мг м3—4 класс опасности ;
- фенол ПДК = 01 мг м3—2 класс опасности ;
- формальдегид ПДК=005 мг м3—2 класс опасности.
2.3 Организация вентиляции
Задачей вентиляции является обеспечение чистоты воздуха и заданных метеорологических условий. Для исключения попадания в воздух рабочей зоны газа и пыли применяют местную вытяжную вентиляцию над кокильной машиной в виде поворотного зонта.
Общеобменная вентиляция на кокильном участке обеспечивает приток свежего воздуха вдоль колонн в рабочую зону с высоты 3 метра и создание комфортных температурных условий на рабочих местах.
Кратность воздухообмена – 8.
Для исключения загазованности воздуха внутри помещений от плавильных печей в их конструкции предусмотрено наличие вытяжной вентиляции для отвода пыли вредных газов паров избыточного тепла. В конструкции вентиляции предусмотрено наличие циклонов для осаждения взвешенных частиц и фильтров для улавливания вредных веществ.
2.4 Организация отопления производственных и служебных помещений.
По СНИП 2.04.05 – 91 для производственного здания применяем воздушное отопление совмещенное с вентиляцией.
В осенне-зимнее время для защиты рабочих мест от притока холодного воздуха при открытии ворот и дверей предусматриваются завесы и тамбуры.
Для отопления административных помещений применяется водяное отопление с радиаторами и ребристыми трубами.
2.5 Организация производственного освещения
В соответствии со СНИП 2-2305-95 освещение обеспечивает: санитарные нормы освещенности на рабочих местах; отсутствие резких теней и блеклости; постоянство освещенности во времени и правильность направления светового потока.
Освещенность на рабочих местах и в производственных помещениях контролируется не реже одного раза в год
На заливочном участке предусмотрено естественное искусственное общее и местное освещение.
Характеристика зрительной работы заливщика
а) зрительная работа – малой точности
б) наименьший объект различения – 3-5 мм
в) разряд зрительной работы по СНиП2 –2305-95 «Естественное и искусственное освещение» разряд - 4 подразряд - Г
д) освещенность Е=200лк.
2.6 Защита от шума и вибрации
а) Источниками шума на участке являются вентиляторы. Шум от вентиляторов аэродинамический и механический постоянный уровень звука которого за восьмичасовой рабочий день изменяется во времени не более чем на 5дБА при измерении на временные характеристики шумометром по ГОСТу 17. 187-81.
По ГОСТ 12.1.003-83 уровень шума допускается не более 80 дБА. Предусматриваются следующие мероприятия по снижению уровня шума:
- ограждение участков шума в отдельные помещения;
- применение вентиляторов с уменьшенными аэродинамическими показателями.
- эластичные вставки в воздуховоды .
б) Причиной вибрации на кокильном участке является работа кокильных машин.
Характеристика вибрации – общая технологическая по характеру возникновения – механические колебания вызванные работой кокильной машины.
В проекте для борьбы с вибрацией предусмотрено:
- установка оборудования на фундамент;
- дистанционное управление оборудованием;
- применение виброизоляции.
Согласно ГОСТ 12.1.012 – 90 «Вибрационная безопасность» допускается значение вибрации на рабочих местах 92 дБ.
3 Защита окружающей среды
По ГОСТу 17.21.01-89 выбросы в атмосферу относятся к газообразному агрегатному состоянию. По химическому составу относятся к металлам и их соединениям с массой выброса менее 1 кгчас и с размерами частиц менее 05х10 -6 м. Высота выброса 24 м.
Охраной окружающей среды является неотъемлемой частью требований по производственной санитарии. Для соблюдения правил по охране окружающей среды необходимо:
- для очистки воздуха от пыли используют пылеулавливающее оборудование:
а) ячейковые фильтры коэффициент очистки до 80%. Фильтр состоит из ячеек рамного типа заполненных фильтрующим материалом . (металлической сеткой).
б) в циклонах (центробежных пылеотделителях) частицы пыли отделяются от воздуха за счет сил инерции которые действуют на частицы при вращении потока очищенного газа коэффициент очистки 80 – 90 %.
- для осаждения копоти применять специальные шахты;
- вокруг цеха предусмотрены участки зеленых насаждений и газоны
4 Пожарная безопасность
Согласно НПБ 105-95 производство в литейном цехе (на заливочном участке) по степени пожарной безопасности «Г» - к производству связанному с обработкой не сгораемых материалов в горении в раскаленном и расплавленном состоянии.
- неисправность электрооборудования;
- нарушение технологического режима (отклонения от действующей технологии);
- неудовлетворительная подготовка оборудования к ремонту;
- самовозгорание материалов;
- несоблюдение графика планового обслуживания и ремонта оборудования;
- конструктивные недостатки оборудования.
В соответствии со СНИП 2.09.02-85 принята II степень огнестойкости.
Минимальные пределы огнестойкости по СНИП -2.09.02-85 строительных конструкций:
Стены лестничных клеток 2 часа
Лестничные площадки ступеньки2 часа
Наружные плиты из навесных панелей025 часа
Внутренние несущие стены (перегородки)05 часа
Мероприятия по пожарной безопасности:
Здание цеха окружено наружной системой противопожарного водоснабжения.
Около здания и внутри имеются щиты с инвентарем необходимым для тушения пожара укомплектованными огнетушителями ОХП-10 и ОП-6г ящиком с песком лопатой багром кошмой а также пожарные гидранты.
Участок оборудован электросигнализацией с установкой автоматических приборов- извещателей.
Все горючие материалы хранятся в отдельных закрытых помещениях.
Все проезды и проходы выполняются в соответствии с противопожарными нормами.
Для эвакуации персонала предусмотрены эвакуационные выходы в количестве 6 штук
5 Анализ опасных и вредных факторов на производстве и основные мероприятия по предупреждению травматизма.
Таблица 7.3 Анализ опасных и вредных факторов
Опасный фактор ГОСТ 12.0.003-74
Мероприятия по предупреждению травматизма
Перемещение подвижных частей оборудования и литейной оснастки.
Определение запретных зон и установка ограждений в пределах границ работы движущихся частей.
Высокая температура металла плавильных и раздаточных печах.
Установление над плавильными и раздаточными печами крышек с гидравлическим или механическим приводом .
Установка ограждения рабочих зон.
Повышенная запыленность и загазованность воздуха рабочей зоны.
Применение общеобменной и местной вентиляции.
Движение робота-манипулятора во время съема горячих отливок (в случае механизированной работы).
Установление датчиков и ограждений в пределах границ действия робота
При очистке и окраске кокиля:
а) попадание краски при распылении в глаза;
б) попадание газов краски в легкие.
в) очистка кокиля сухим льдом
а) использование специальных очков;
б) использование респираторов;
в) использование специальных масок с приточной вентиляцией
6 Расчет искусственного освещения участка литья в кокиль
С учетом высоты подвеса в качестве источника света на кокильном участке применены лампы ДРЛ-400. Согласно СНиП 2-2305-95 освещение должно быть не менее 200 ЛК.
А – длина кокильного участка;
В - ширина кокильного участка;
п - высота подвески
I - 126*1811* (126+18) = 14;
Расчет потребного количества ламп определяемого по методу коэффициента использования ведем по формуле:
Где N - количество светильников; Е – норма освещения (ЛК);
K3 - коэффициент запаса K3 = 18; Ф – световой поток 19000 мм; S – площадь участка S = 2160 м2;
h- коэффициент использования
N= 200*18*226819000*06=716 шт
Принимаем N= 72 ламп.
Гражданская оборона.
1 Задачи гражданской обороны
Гражданская оборона - составная часть общегосударственных оборонных мероприятий осуществляемых в мирное и военное время в целях защиты населения и народного хозяйства от оружия массового поражения применяемых противником. Для проведения эвакуационных и аварийно – спасательных работ в случаях угроз поражения зонах катастроф и стихийных бедствий проводятся мероприятия предусмотренные штабом ГО и ЧС предприятия.
Главная задача гражданской обороны промышленных объектов – повышение их устойчивости в условиях применения оружия массового поражения катастроф и других стихийных бедствий. Решение этой задачи обеспечивается в первую очередь организацией защиты рабочих и служащих а так же повышения устойчивости зданий сооружений оборудования технологических процессов производства против поражающих факторов.
2 Общезаводские мероприятия проводимые при угрозе нападения
Цеха переводятся на новую производственную специализацию. Срок исполнения – 15 часов. Ответственный исполнитель – директор завода. Прекращается капитальное строительство строительство в жилищно-бытовом секторе – консервируется. Ответственный исполнитель – начальник капитального строительства.
Заполняются водой резервуары и запасные емкости. Проверяется санитарно- гигиеническое состояние всех видов защитных сооружений.
Производятся работы по защите ценного и уникального оборудования.
Организуется строительство убежищ и укрытий.
3 Мероприятия проводимые в литейном цехе при угрозе нападения
При угрозе нападения цех переводится на другой режим работы. Работа организуется в две смены по 12 часов. Сокращается численность рабочих за счет вспомогательного персонала. Освободившиеся от работы люди подготавливают имеющиеся защитные устройства убежища и средства индивидуальной защиты.
Проводится проверка запасов воды и пищи в убежищах. Руководящий состав гражданской обороны занимает пункт управления. Управление цехом производится в убежище.
4 Общезаводские мероприятия проводимые при внезапном нападении
Завод прекращает работу оставляя в цехах энергетических службах у плавильных агрегатов нагревательных печей дежурных электриков.
Отключается электроснабжение на заводе и электроснабжение постоянных потребителей питающихся от заводской сети за исключением кузнечных и литейных цехов.
Работа компрессоров прекращается давление в воздушных баллонах снижается до 15 атмосфер.
Перекрывается газовая сеть. Подготавливаются и выключаются насосы повышенного давления.
Находящиеся в цехах баллоны с кислородом и углекислым газом наглухо перекрываются и выносятся за пределы цеха в специально подготовленные места-укрытия.
Прекращается выпуск транспорта с территории завода.
В ночное время включается дежурное освещение.
5 Мероприятия в цехе по сигналу «Воздушная тревога».
По сигналу «Воздушная тревога» в ремонтных мастерских на складах шихтовых и формовочных материалов немедленно прекращаются все работы.
Оборудование отключается от электрической сети и сети газового и воздушного снабжения.
Плавильные печи останавливаются и расплавленный металл сливается.
Останавливается работа термообрубного и смесеприготовительных участков. Краны рассредотачиваются по краям пролетов грузы опускаются легковоспламеняющиеся материалы изолируются. Срок исполнения – 10 минут
6 Обеспечение защиты рабочих и служащих цеха
Для защиты персонала на заводе расположены убежища с фильтровентиляционным оборудованием промышленного изготовления и СИЗ.
7 Мероприятия по защите ценного и технологического оборудования.
Наиболее ценным оборудованием в цехе являются плавильные и термические печи стержневые автоматы автоматические линии карусельно- кокильные машины.
С целью предупреждения повреждения этого оборудования предусматривается установка специальных зонтов и металлических балок. Зонт представляет собой сборную конструкцию из четырех стальных колонн опирающихся на фундамент машины и верхних балок двутаврового сечения.
Аннотация.doc
- плавильного отделения;
-четырех отделений литья в кокиль для получения отливок из алюминиевых сплавов;
-отделения литья под низким давлением для получения отливок из алюминиевых сплавов;
-участка изготовления песчаных стержней;
-участка термической обработки отливок;
-участка финишной обработки отливок;
- склада готовой продукции.
В цехе применяется два способа литья:
- литье под низким давлением;
В строительной части рассматриваются географические данные местоположения цеха технологические особенности производства и архитектурно-конструктивное решение данного задания также рассмотрен вопрос гражданской обороны.
Рассмотрены вопросы безопасности и экологичности.
Организационно-экономическая часть включает расчет себестоимости одной тонны отливок и прибыль цеха.
The casting shop was projected in this diploma. The casting shop produces castings with the help of gravity die casting and high pressure die hasting using non organic resins to produce sand cores. It has capacity of 12000 ton per year in ZMZ conditions.
The shop consists of :
- sand core production department
- heat treatment department
- finishing department
- warehouse for ready made production
- two methods of casting are applied in the shop:
- gravity die casting
- high pressure die casting
Building part describes the location of the shop technological particularities and architecture constructional ideas of the building. The civil defense problem is also considered here.
Economical and Safety questions are considered.
Organizational and Economical part includes one ton casting cost and shop profitability.
In diesem Diplomprojekt wurde die Giesserei fuer die Herstellung der Kokillen- und Niederdruckgussteile mit dem Einsatz der anorganischen Bindmittel bei der Produktion der Sandkerne mit der Kapazitaet von 10 000 Tonnen pro Jahr in Bedingungen von der “ZMZ” AG projektiert.
Diese Giesserei besteht aus:
-Lager fuer Fertigproduktion.
In der Giesserei werden 2 Giessverfahren eingesetzt:
In Bauabschnitt werden sowohl die geografischen Daten des Standortes der Giesserei technologische Besonderheiten der Produktion und Architektur- Konstruktionsloesung dieser Aufgabe als auch die Frage des Zivilschutzes betrachtet.
Die Fragen der Sicherheit und Umweltfreundlichkeit werden betrachtet.
Organisatorisch-wirtschaftlicher Abschnitt beinhaltet die Berechnung der Selbstkosten von einen Tonne der Gussteile und Gewinn der Giesserei.
экономика.DOC
1.Научная организация труда в литейном цехе
1.1 Управление литейным цехом
Цели и задачи управления
Основными целями деятельности цеха является выполнение производственных заданий выпуск продукции в установленной номенклатуре повышение культуры производства и технико-экономических показателей.
-ритмичный выпуск продукции в заданном объеме
-обеспечение выпуска продукции согласно требованиям НТД
-повышение культуры производства
-выполнение требований системы охраны труда техники безопасности эксплуатации и правил пожарной безопасности.
1.2 Функции управления
-принятие управленческого решения
-укомплектование штата
1.3 Схема управления
1.4 Научная организация труда.
Научная организация труда (НОТ) – это наиболее рациональное т.е. самое эффективное в технико-экономическом социальном и психофизическом отношениях соединение техники и людей в едином производственном процессе на основе достижений науки и передовой практики. НОТ решает экономические задачи – повышение производительности труда полное использование ресурсов.
Основные цели и направления современного развития НОТ концентрируется в следующем комплексе задач: совершенствование кооперирования и разделения труда его нормирования и оплаты; обоснование и распространение передовых приемов труда; рациональная организация и обслуживание рабочих мест; совершенствование санитарно-гигиенических и эстетических условий труда применение научных методов подбора расстановки и продвижения кадров повышения их квалификационного и общеобразовательного уровня; развитие творческой активности работников.
1.4.1 Рациональная организация рабочего места
Результаты работы объединения предприятия цеха участка уровень производительности труда во многом зависит от результатов труда на каждом рабочем месте.
Рабочее место – это участок производственной площади оснащенный оборудованием и другими средствами труда соответствующих характеру работ выполняемых на этом рабочем месте. Для обеспечения высокопроизводительной работы большое значение имеет правильная организация рабочего места. Формы организации рабочих мест зависят от типа производства и специфики выполняемого трудового процесса. Организовать рабочее место – это значит выбрать оснащение (оборудование инструмент и т.п.) и правильно его разместить на отведенной для рабочего места площади т.е. выполнить его планировку.
Оснащение рабочего места определяется его технологическим назначением уровнем специализации и степенью механизации выполняемых работ. Оснащение принято делить на следующие группы: основное технологическое оборудование – станок; технологическая оснастка – инструмент приспособления; вспомогательное оборудование – транспортеры подъемники; организационная оснастка – тумбочки стулья сигнализация тара подставки под ноги; защитные устройства – ограждения и другие устройства предусмотренные техникой безопасности.
Рациональная конструкция оборудования организационной оснастки позволяет выполнять заданную работу при движении предплечья и пальцев рук не допуская движения корпуса т.е. с помощью самых простых и наименее утомительных движений. Но удобство при работе зависит не только от рациональности конструкции оснащения но и от правильности планировки рабочего места. Планировка должна удовлетворять следующим требованиям: удобное положение рабочего во время работы свободный обзор рабочего места экономия производственных площадей строгое соблюдение правил техники безопасности и требований промышленной санитарии.
На рабочем месте должно быть предусмотрено индивидуальное освещение обеспечивающее нормальную освещенность рабочей зоны. Для размещения технологических карт которыми рабочий пользуется при выполнении операции обычно используют специальные полочки или стеклянные экранчики прикрепленные к тумбочке или станку.
При организации рабочих мест большое внимание уделяется конструкции инструментальных тумбочек и правильному расположению в них всех необходимых для работы предметов. Располагая предметы в определенном порядке рабочий добивается некоторого автоматизма: движения его становятся привычными сокращается время на выполнение таких приемов как «взять инструмент» «зажать деталь» и др. Все это способствует меньшей утомляемости и увеличивает выработку рабочего.
Поддержание чистоты и порядка на рабочем месте оказывает влияние не только на производительность но и на качество выпускаемой продукции. Необходимо тщательно убирать не только рабочее место но все помещение цеха каждому рабочему соблюдать личную гигиену оборудовать рабочие места хотя бы простейшими механизмами и приспособлениями для сбора отходов стружки правильно организовать вентиляцию.
Немаловажное значение в организации рабочего места имеет организация его обслуживания. Обслуживание рабочих мест организуется на основе сменно-суточного задания которое устанавливается мастером. Хорошая организация снабжения не отвлекает рабочего от основной работы рабочий не тратит время на получение инструментов деталей и др.
Рабочие места закрепляются за определенными рабочими на длительное время так как переход с одного места на другое требует некоторого времени на его освоение что приводит к временному снижению производительности. Закрепление за рабочим определенного места повышает его ответственность за станок и другое оборудование.
При выборе оптимального варианта рабочего места заливщика следует учитывать время охлаждения отливок в кокиле время охлаждения кокиля до следующей заливки расстояние транспортировки жидкого металла от плавильных печей до кокилей площадь занимаемую машиной и подсобными механизмами трудоемкость обслуживания машины.
2.Технико-экономическое обоснование выбора стержневых автоматов LB 50 взамен стержневых автоматов мод.4705
Приведем технико-экономическое обоснование выбранного оборудования на примере автомата для изготовления стержней. Для изготовления стержней можно использовать как стержневой автомат 4705 (изготовление стержней по нагреваемой оснастке) так и стержневой автомат LB 50 (изготовление стержней методом « Beach-Box».
Необходимо произвести расчет экономической эффективности применения каждого из этих автоматов. В качестве показателя эффективности применяется минимум приведенных затрат на изготовление одного стержня.
Приведенные технологические затраты выражаются следующей формулой:
ЭТ – затраты на электрическую энергию;
ЗП – заработная плата рабочих обслуживающих машину;
ЕН = 2 (норматив внутреннего накопления);
А – затраты на амортизацию оборудования;
Р – затраты на ремонт;
f – затраты на содержание производственной площади;
К – капиталовложение;
ЕСН – единый социальный налог.
Исходные данные для расчета приведены в таблице 1.
Наименование исходных данных
Величина по вариантам
Балансовая стоимость
Установленная мощность электродвигателя
Категория ремонтосложности:
- по механической части
- по электрической части
Количество обслуживающего персонала
Средний разряд рабочих
Средний тарифный коэффициент
Тарифный коэффициент:
2.1 Расчет приведенных затрат по автомате 4705
ЗП = 8700164 = 53 руб
2.1.2 Единый социальный налог
ЕСН = 0.26 × 31 = 138 руб
2.1.3 Затраты на электроэнергию
2.1.4 Расчет амортизационных отчислений
2.1.5 Затраты на содержание производственной площади
2.1.6 Расчет капиталовложений
К = КОБ + КЗД + КОС (1.4)
где КОБ – капиталовложения в оборудование;
КЗД – капиталовложение в здание;
КОС – капиталовложение в оборотные средства.
где RОС – коэффициент учитывающий затраты на создание оборотных средств.
Итого капиталовложения:
Кi =1390.5 +12.8 +166.9 = 15702 руб
2.1.6 Расчет приведенных затрат
Зi = СМЧ + Ен ×Кi (1.5)
СМЧ – итого себестоимость машино-часа работы оборудования;
СМЧ = ЗП + Э + А + Р + f (1.6)
Смч =53+1006+1543+119=22926
Зi = 22926+2×15702 = 33697 руб
Таким образом приведенные технологические затраты на изготовление 1 стержня будут составлять:
2.2 Расчет приведенных затрат для автомата LB 50
ЕСН = 0.26 × 53 = 138 руб
Кi = 34398 + 172 + 4127 = 38697 руб.
Смч= 53+88+381.81+159=4595
Зi = 4595+2×38697 = 81989 руб
Таким образом затраты на производство одного стержня на автомате 4705 составляют 962 рубст а на автомате LB 50 4099 рубст. Следовательно затраты на автомате LB 50 значительно ниже чем на автомате 4705 и поэтому экономически более выгодно применять стержневой автомат LB 50.
3 Определение стоимости основных фондов и расчет амортизационных отчислений
3.1 Здания. Стоимость здания подсчитывается отдельно по его промышленной и непромышленной (бытовой) частям исходя из площади и цены за 1м3.
Fi – площадь здания.
Площадь производственного помещения определяется по планировке цеха. Площадь бытовых помещений принимается из расчета 3.2м2 – на одного списанного рабочего; 3.5 м2 – на одного руководителя специалиста служащего. Стоимость здания приведена в таблице 4.2.
Наименование помещений
Стоимость здания руб
3.2 Сооружения. Стоимость сооружения принимается в размере 4% от стоимости здания.
Ссооружения = 0.04 × СЗД
Ссооружения = 0.04 × 211 902 000 = 8 476 080
Нормы амортизационных отчислений приведены в таблице 4.1
3.3 Машины и оборудование. Стоимость машин и оборудования принимается по инвентаризационным ведомостям предприятия. Затраты на транспортировку и монтаж не учитываются.
Перечень машин и оборудования проектируемого цеха их себестоимость и амортизационные отчисления представлены в таблице 4.3.
Наименование оборудования
Сумма амортизационных отчислений руб
I Плавильное отделение
Печь подогрева шихты
Уст-ка дегазации сплава
II Заливочное отделение
III Стержневое отделение
Установка мех. регенерации
Обрабатывающий центр
Всего учтенное оборудование
V Неучтенное оборудование
Амортизационные отчисления для оборудования рассчитаны по формуле: (4) где
На – норма амортизации %;
Цп – первоначальная цена машины руб.
Неучтенное оборудование принимается равным 10% от стоимости учтенного;
Производственный инвентарь принимаем равным 1% от стоимости оборудования.
Спр.инв = 0.01 × Собор
Спр.инв = 0.01 ×518 336 790 = 5 183 368 руб
Хозяйственный инвентарь принимаем из расчета 1% от стоимости производственного помещения
Схоз.инв = 0.01 × Спроизв.пом
Схоз.инв = 0.01 × 209 952 000 = 2 099 520 руб
Состав и структура основных фондов цеха приведены в таблице 4.4.
Группа основных фондов
Машины и оборудование
Производственный инвентарь
Хозяйственный инвентарь
4 Расчет материально-энергетических затрат
Из вспомогательных материалов определен расход и стоимость тех которые потребляются на плавильном участке проектируемого цеха. Данные о расчете материально-энергетических затрат приведены в таблице 4.5.
Наименование затрат материалы энергия
На 1 тонну годного литья
I Материалы основные для АК9ч ЛК
II Материалы основные
III Материалы основные для АКМ3ч ЛК
IV Материалы основные для АК9ч ЛНД
V Материалы вспомогательные
Итого за вспомогательные материалы
Неучтенные вспомогательные материалы
Всего за вспомогательные материалы
5 Расчет штатов цеха
Количество рабочих определяем расстановочным путем по нормам обслуживания. Расчет количества рабочих ведется по формуле:
где М – количество работающих на данном оборудовании;
s - количество оборудования;
5.1 Расчет количества основных рабочих
Плавильный участок(1 человек на 2 печи)= 05×8×3 = 12 чел
Шихтовый двор= 1×4×3 = 12 чел
Стержневой участок= 1×6×3 = 18 чел
Участок обрезки= 1×8×3 = 24 чел
Участок выбивки (1 человек на 2 уст-ки)= 05×6×3 = 9 чел
Крановое хозяйство= 05×12×3 = 13 чел
Транспорт= 1×10×2 = 20 чел
Участок финишной обработки= 1×12×3 = 36 чел
S RЯВ = +++++++++= 192 чел
RСПИС = RЯВ × КСПИС (6)
где RСПИС – списочное количество рабочих
КСПИС – коэффициент списочности КСПИС = 1.15
RСПИС = 192 × 1.15 = 2208 чел
5.2 Расчет численности ремонтных рабочих
Численность ремонтных рабочих определим по трудоемкости работ.
Исходные данные для расчета сведены в таблицу 4.6
Группа ремонто-сложности
Печь УИП-800-10-10х2
Установка дегазации сплава
Стержневой автомат LB50
Стержневой автомат LL5
Установка регенерации
Обрезной комплекс LCC120
Обрезной комплекс LCC350
Обрезной комплекс LCC420
Дробеметная установка
Расчет трудоемкости работ ведем по следующей формуле:
где - трудоемкость ремонтных работ в проектируемом цехе;
- трудоемкость ремонтных работ в базовом цехе;
- суммарная ремонтосложность в проектируемом и базовом цехах.
Численность рассчитаем по следующей формуле:
где R – численность ремонтных рабочих;
- действительный фонд времени рабочего;
- коэффициент выполнения норм.
Службу механика увеличиваем на 15% а службу энергетика на 20% т.к. в расчете трудоемкости ремонтов учитывалось только основное технологическое оборудование. Таким образом численность работников по механической части –13 человек а по электрической - 14 человек.
Штатное расписание руководителей специалистов рабочих служащих представлено в таблице 4.7
Категория работающих
Зам.начальника цеха по производству
Зам.начальника цеха по технической части
Ведущий инженер-технолог
Инженер- технолог I категории
Инженер- технолог II категории
Инженер- технолог III категории
наладчик оборудования
рабочий по уходу и ремонту оборудования
уборщик производственных помещений
уборщик бытовых помещений
6 Расчет фонда заработной платы
Годовой фонд зарплаты рабочих рассчитывается по формуле:
где - среднемесячная зарплата рабочего в проектируемом цехе.
где - среднемесячная зарплата рабочего в базовом цехе принимаем 8700 рублей а с вычетом премии получаем 6960 руб.
КПР – коэффициент роста производительности труда в проектируемом цехе по сравнению с базовым;
где и - мощности базового и проектируемого цехов тыс.тгод
6.1 Расчет ЗП основных рабочих:
- для заливщиков ЛК
-для заливщиков ЛНД
6.2 Расчет ЗП вспомогательных рабочих:
Среднемесячная зарплата вспомогательных рабочих в базовом цехе –6500руб. с вычетом премии получим 5200
6.3 Расчет ЗП руководителей специалистов и служащих рассчитывается с помощью контрактной ставки исходя из средневзвешенной ЗП основных и вспомогательных рабочих.
Средневзвешенную зарплату находим по формуле:
где ЗПОСН ЗПВСП – заработная плата основных и вспомогательных рабочих;
РОСН РВСП – количество основных и вспомогательных рабочих.
Заработная плата руководителей специалистов служащих рассчитывается по формуле:
ЗПРУК = ЗПСР.ВЗВ × ККОНТР
где К – контрактная ставка.
ЗПРУК = 10206 × 30 = 30619 руб
ЗПРУК = 10206× 2.5 = 25516 руб
Начальник смены участков служб
ЗПРУК = 10206 × 20 = 20412 руб
Начальник техбюро ст.мастер
ЗПРУК = 10206× 1.5 = 15309 руб
ЗПРУК = 10206 × 1.4 = 14289 руб
ЗПРУК = 10206 × 13 = 13268 руб
Инженер-технолог I-ой категории
ЗПРУК = 10206 × 12 = 12247 руб
Инженер-технолог II-ой категории
ЗПРУК = 10206 × 11 = 11227 руб
Инженер-технолог III-ой категории
ЗПРУК = 10206 × 10 = 10206 руб
Экономист нормировщик диспетчер
Таблица 4.8 Фонд заработной платы
Дополнительная зарплата руб
начальники смен служб участков
инж-технолог I-ой категории
инж-технолог II-ой категории
инж-технолог III-ой категор.
экономисты нормировщики диспетчеры
7 Расчет и составление сметы на содержание и эксплуатацию оборудования
7.1 Амортизация оборудования
АОБОР = 50380161 руб
7.2 Эксплуатация оборудования
7.2.1 Затраты на вспомогательные материалы принимаем в размере 1% от стоимости оборудования
ЗВСП.МАТ = 0.01 × 518336790 = 5183367 руб
7.2.2 Зарплата рабочих обслуживающих оборудование
ЗПОБС = (6960 + 0.329 × 6960) × 8 × 111 = 887714 руб
7.2.3 Единый социальный налог (в размере 26%)
ЕСН = 0.26 × 887714= 230805руб
7.2.4 Затраты на силовую электрическую энергию и сжатый воздух
Таким образом эксплуатация оборудования равна:
ЗОБ = ЗВСП + ЗПОБС + ЕСН + ЗЭ
ЗОБ = 51833689 + 887714 + 288507 + 7188000 = 13489888 руб
7.3 Ремонт оборудования
7.3.1 Зарплата ремонтным рабочим
ЗПРЕМ = (6960 + 0.329 × 6960) × 12 × 111 = 1231704 руб
7.3.2 Единый социальный налог
ЕСН = 0.26 × 1231704 = 320243 руб
7.3.3 Стоимость материалов и запасных частей для ремонта – 20% от амортизации оборудования
СЗАП = 0.2 × 50803161 = 100760322 руб
Таким образом ремонт оборудования:
РОБ = ЗПРЕМ + ЕСН + СЗАП
РОБ = 1231704 + 320243 + 10076032 = 11627979 руб
7.3.4 Внутризаводское перемещение грузов
ПГ = 44.6 × 10000 = 446000 руб
7.3.5 Прочие расходы по цеху
ПР = 34.2 × 10000 = 342000 руб
7.4 Перемещение грузов
ПГ = 44.6 × 10000 =446000 руб
7.5 Прочие расходы по цеху
ПР = 34.2 × 10000 =342000 руб
8 Расчет сметы общехозяйственных расходов
8.1 Содержание аппарата управления цехом
С8ПР = ЗПРУК + ЕСНРУК
СУПР = 8929456 + 2321658 = 11251114 руб
8.2 Содержание прочего цехового персонала
СПР = ЗПСЛУЖСПЕЦ + ЕСНСЛУЖСПЕЦ
СПР = 5517185 + 1434467 = 6951653 руб
8.3 Амортизация зданий сооружений инвентаря
А = АЗД + АСООР + АИНВ
А = 2119020 + 84761 + 51834 = 2255614 руб
8.4 Испытания опыты исследования
Принимаем по данным базового цеха равным 300 рублей на 1 работающего
И = 300 × 344 = 103200 руб
8.5 Охрана труда – принимаем по данным базового цеха равным 250 рублей на 1 работающего
ОТ = 250 × 344 = 86000 руб
8.6 Текущий ремонт зданий сооружений принимаем 2% от их стоимости
ТР = 0.02 × 220037080 = 4407561 руб
8.7 Износ малоценного быстроизнашивающегося инвентаря принимаем 2% от АОБ
ИЗ = 0.02 × 50380161 = 1007603 руб
8.8 Содержание зданий сооружений инвентаря принимаем равной 4% от их стоимости
С = 0.04 × 225561448 = 9022457 руб
ПР = 25 ×10000 = 250000 руб
Результаты заносим в таблицу
Таблица 4.9 Смета общепроизводственных расходов
А Расходы на содержание и эксплуатацию оборудования
Амортизация оборудования
Эксплуатация оборудования
Внутризаводское перемещение грузов
Б Общецеховые расходы
Содержание аппарата управления цехом
Содержание прочего персонала
Амортизация зданий сооружений инвентаря
Испытания опыты исследования
Текущий ремонт зданий сооружений
Износ малоценного быстроизнашивающегося инвентаря
Содержания зданий сооружений инвентаря
9 Калькуляция себестоимости продукции
В проектируемом цехе применяется 2способа литья и 3 вида сплава: ЛК (АК9ч АК9М3-К АК8М3ч) ЛНД (АК9ч). Для каждого способа составим нормативную калькуляцию себестоимости 1 тонны отливок в расчете на весь выпуск.
Расход по статьям затрат нормативной калькуляции принимаем пропорционально массе годных отливок на программу по данному способу литья.
Цеховые расходы и расходы на содержание и эксплуатацию оборудования распределяются пропорционально основной зарплате основных рабочих.
Таблица 4.10 – Нормативная калькуляция себестоимости 1 тонны отливок для литья в кокиль (АК9ч 24159 тг)
Вспомогательные материалы
Общепроиводственные расходы
Итого цеховая себестоимость
Общехозяйственные расходы
Итого производственная себестоимость
Полная себестоимость
Таблица 4.11 Нормативная калькуляция себестоимости 1 тонны отливок для литья в кокиль (АК9М3-К 4859 тг)
Таблица 4.12 Нормативная калькуляция себестоимости 1 тонны отливок для литья в кокиль (АК8М3ч 70738 тг)
Таблица 4.13 – Нормативная калькуляция себестоимости 1 тонны отливок для литья в кокиль (АК9ч ЛНД 99927 тг)
10 Финансовый менеджмент
10.1.1 Расчет оптовой цены предприятия 1 тонны годных отливок
где SП – полная себестоимость;
где Р – рентабельность (Р = 20%).
= 107081 × 02 = 21416 руб
= 104404 × 02 = 20880 руб
= 33691 × 02 = 6738 руб
= 100781 × 02 = 20156 руб
= 107081 + 21416= 128497 руб
= 104404+ 20880 = 125285 руб
= 33691+ 6738= 40429 руб
= 100781 + 20156 = 120238 руб
Где НДС – налог на добавленную стоимость 18%
Цотл АК9ч= 223577 + 23129 = 151627
Цотл АК9М3-К= 216351 + 22551 = 147837
Цотл АК8М3ч= 285220 + 7277 = 47706
Цотл АК9ч= 216018 + 21768 = 142707
где В – выручка от реализации выпущенной продукции
= 128497× 241593 – 73264142 = 293056570 руб
= 125285 × 4859 – 143668402 = 57467373611 руб
= 40429 × 70738 – 6749415= 26997662 руб
= 120238 × 99927 – 28520605 = 114082422 руб
10.1.2 Определение точки безубыточности производства
где a – постоянная затрата на весь выпуск;
а= А+ЗП всп +ЕСНвсп +ОПР+ОХР+ВНПР
где А –амортизация оборудования руб;
ЗП всп – зарплата вспомогательных рабочих руб;
ЕСН всп - единый социальный налог;
ОПР – общепроизводственные расходы;
ОХР – общехозяйственные расходы;
ВНПР –внепроизводственные расходы.
= 1217148183+3196684+83113781+2146858258+878678049+1485504789=14403904145
= 244797202+6429285+167161413+63388211472+1713140236+267588267=2940416845
= 35638069+935988+2433569+42283984+327658349+59347211=476721067
= 13759482+1322206+3437735+6469735+350855231+6144315=5439989771
b – переменная затрата на единицу продукции;
bN – переменные затраты.
b = М0 + МВСП + ЭТ + И + ЗПОСН + ЗПДОП + ЕСН+ 03 ОПР
где М0 – расходы на основные материалы рубт;
МВСП – расходы на вспомогательные материалы рубт;
ЭТ – энергия технологическая;
И – износ специального инструмента;
ЗПОСН – зарплата основных рабочих;
ЗПДОП – дополнительная зарплата рабочих;
ЕСН – единый социальный налог
ОРП – обще производственные расходы
= 12056465+4113+855+1539+3761+705+997+2830= 71358 руб
= 4558329+82723+855+153+3761+705+997+4078= 66773 руб
= 2183367+12043+855+1539+3761+705+997+1957=14878 руб
= 1206606+170123+855+1539+3761+705+997+2106=68222 руб
Sкр АК9ч ЛК = 101960787 + 71358 × 241593 = 274356921 руб
Sкр АК9М3-К = 220037425 + 66773 × 4859 = 544491789 руб
Sкр АК8М3ч = 18578089 + 14878 × 70738 = 29102951 руб
Sкр АК9ч ЛК= 38504711+ 68222 × 99927 = 106677784 руб
Из S = b + aN находим зависимость себестоимости 1 тонны отливок от коэффициента использования производственной мощности.
Таблица 4.14 – Зависимость себестоимости 1 тонны отливок от коэффициента использования производственной мощности
Коэффициент использования производственной мощности
Себестоимость 1 тонны отливок
График 4.1 – Зависимость себестоимости 1 тонны отливок от коэффициента использования производственной мощности
График 4.2 – Зависимость себестоимости продукции и выручки от объема производства
10.1.3 Расчет прибыли
Пв = 1018810267 – 890545787 = 118264480 руб
Расчет налогооблагаемой прибыли
где НИ – налог на имущество – 2%.
Ни= 0.02 × 197934373 = 39586875 руб
Пно = 118264480 – 39586875 = 114305793 руб
10.1.4 Расчет чистой прибыли
где Ппр – налог на прибыль 22% от ПНо
ПЧ = 114305793 – 0.22 × 114305793 = 89158518 руб
11 Расчет капитальных вложений
Определим капиталовложения в следующем составе:
К = Коф +Кос+ Кпи +Кпр где
Коф - капиталовложения в основные фонды руб;
Кос – капиталовложения в оборотные средства руб;
Кпи - затраты на проектно-изыскательские работы руб;
Кпр - прочие капиталовложения руб.
Капиталовложения по цеху определяются по формуле:
Кзд – капиталовложения в здание и сооружения руб;
Ко - капиталовложения в оборудование руб.
К оф = 211902000 + 518336790 = 730238790 руб
Оборотные средства рассчитываются по формуле:
Кос = ПЗ+НПЗ+ГП+И+ЗЧ где
ПЗ – оборотные средства в производственных запасах руб;
НЗП –оборотные средства незавершенного производства руб;
ГП – оборотные средства в готовой продукции на складе руб;
И – оборотные средства вложенные в специнструмент хозинвентарь малоценные и быстроизнашивающиеся предметы руб;
ЗЧ - оборотные средства вложенные в запчасти для текущего ремонта руб.
Производственные запасы рассчитываем по формуле:
В – среднегодовой расход материала руб;
Дн – норма запаса для материалов в сутках: для основных материалов Дн=5 для вспомогательных материалов Дн=15 .
ПЗ осн =1107274970× 5 360 = 1537881903 руб
ПЗ всп = 89692623.3 × 15 360 = 37371926 руб
ПЗ = 1537881903 + 37371926 = 1508099293 руб
Размер незавершенного производства определяем по формуле:
НЗП = Сп × Nг × Тц × Кнз 360 где
Сп - полная себестоимость 1 отливки руб;
Nг - годовой объем производства годных отливок шт; Nг = 1863750 шт
Тц - длительность производственного цикла изготовления отливок дн. Тц =1 день.
Кнз - коэффициент нарастания затрат.
Кнз = (Мн + Сп ) 2Cп
Мн - начальные материально-топливные затраты руб;
Мн =1371480758 : 1775000 = 77267
Сп - полная себестоимость 1 отливки руб.
Сп =8648989*10000 : 1775000 = 4873
Кнз = (77267+4873) 2 × 4873= 129
НЗП = 4873 × 1775000 × 1 ×129 360 = 3106082
Остаток готовой продукции на складе определяется
ГП = Сп × Nг ×Дхр 360
Д хр - срок хранения готовой продукции на складе Д хр = 1 день
ГП = 4873 × 10000 × 1 360 = 2402497
И – принимается в расчете 5-8 руб на 1000руб выпуска продукции по производственной себестоимости.
ЗЧ – принимается в расчете 15-19 руб на 1000руб выпуска продукции по производственной себестоимости.
Кпи принимаются в размере 20-25 руб от суммы основных фондов
Кпр принимаем в размере 8-10% от суммы основных фондов
Кос = 19116011 + 3106082 + 2402497 + 4184264+ 1335886 =42167042 руб.
К= Коф +Кос+ Кпи +Кпр
К= 730238790 + 42167042 + 14604776 ++ 53448567 = 840459176 руб
Куд =624058738 10000 = 4735 руб
Таблица 4.15 Технико-экономические показатели спроектированного цеха
Годовой объем производства
Количество наименований отливок
Литье по способам литья:
Среднесписочная численность работающих:
- прочий производственный персонал
Производительность труда:
- выпуск годных отливок на 1 работающего
- выпуск годных отливок на 1 рабочего
Себестоимость 1 тонны литья
Среднемесячная зарплата
Объем литья с 1 м2 площади
Удельные капитальные вложения
Уровень рентабельности производства
строительная.DOC
1 Исходные данные для проекта
Цех цветного литья мощностью 10000 тгод предназначен для нужд автомобилестроения.
Географическое место расположения площадки строительства:
Климатическая характеристика района строительства:
- климат умеренный континентальный с умеренно-холодной продолжительной зимой и теплым летом;
- средняя температура января минус 12 - 13°С июня плюс 18 - 19°С;
- годовое количество осадков колеблется от 450-500мм до 500-600мм;
Основание фундамента – мелкозернистый песок с расчетным сопротивлением R = 0.0002 кгсм2 на глубине 1.5-2 метра. Глубина промерзания грунта 1.7 метра. Уровень залегания грунтовых вод на глубине 3.5 метра от планировочной отметки.
Район строительства не сейсмичен.
Производственный режим цеха:
а) Классификация зданий:
- производственные –
- административно-бытовые – II.
б) Категория пожарной безопасности:
- производственного здания – “Г”;
- административно-бытовые - “Д”.
в) Производственные вредные факторы:
- расплавленный металл тепловое излучения;
Реконструированный цех отвечает требованиям СНиП.
На производственной площади расположены производственные здания складские транспортные и энергетические сооружения. Административно-бытовые помещения расположены в примыкающим здании.
- отопление от заводской ТЭЦ электроэнергия с центральной распределительной подстанции;
- сжатый воздух от компрессорной станции расположенной на территории цеха охлаждение компрессоров водяное что позволяет рециркулировать отводящее тепло от компрессоров на отопление;
- водопровод от заводской сети;
- транспорт общезаводской.
Данный район располагает квалифицированной рабочей силой крупными энергоресурсами дешевыми видами топлива. Через город Заволжье проходят железнодорожные водные и автомобильные транспортные пути.
2 Объемно-планировочное решение
Здание литейного цеха представляет собой прямоугольный одноэтажный корпус из унифицированных типовых секций. Шихтово-плавильное отделение расположено в двух поперечных пролетах размерам 90х18 метра высотой 10.8 метра в осях 1-4. Остальные пролеты выполнены в продольными. В них размещено заливочное обрубное стержневое и оборудование для финишной обработки а также складские площади. Из них три пролета размерами 108 х 24 м. Один пролет размером 108 х 18 м. Высота пролетов 10.8 м. Оси размещения 4-35
3 Архитектурно-строительное решение
Несущий каркас здания состоит из следующих железобетонных конструкций:
- колонны прямоугольного сечения 400х800
- ступенчатые монолитные фундаменты сборного типа
- железобетонные фермы
- подкрановые балки таврового сечения серии К-9-01-10
- стеновые панели длиной 12м шириной 16 м и толщиной 240 мм..
Покрытие выполнено из типовых железобетонных плит длиной 12 и 3 метра.
Водостоки внутренние.
Кровля – четырехслойный ковер на цементной стяжке.
Светоаэрационные фонари – металлические. Они обеспечивают естественное освещение помещений в дневное время и вентиляцию.
Полы в соответствии с проектными нормами в плавильном отделении а также на магистральных проездах предусмотрены из чугунных перфорированных плит уложенных на прослойку из мелкозернистого бетона. Тяжелое оборудование размещено на специальных фундаментах.
Ворота оборудованы автоматическим закрыванием – открыванием и воздушными завесами шириной и высотой 3.6м.
Внутрицеховые перегородки кирпичные и щитовые металлические облицованные ГВЛ.
В цехе установлено 12 кранов грузоподъемностью 5 тонн.
Таблица 6.1 Основные технико-экономические показатели
технология.DOC
1. Номенклатура и программа выпуска отливок
2. Программа выпуска отливок с учетом брака
3. Режим работы и фонды времени работы оборудования
Технологические процессы. Расчет оборудования. Описание цеха
1. Расчет программы плавильного участка по выпуску жидкого металла на год
2. Выбор плавильного агрегата
3. Склад шихтовых материалов
4. Характеристика сплавов
5.Описание приготовления сплавов
6.Рафинирование модифицирование и дегазация сплавов.
7. Расчет баланса и состав шихты для плавки сплавов
8. Расчет количества оборудования плавильного отделения
9. Заливочное отделение. Расчет оборудования
10. Участок смесеприготовления и изготовления стержней
11. Регенерация стержневых смесей
12.Участок выбивки стержней
13. Обрубное отделение
14. Участок термической обработки
15. Контроль отливок
16. Вспомогательные службы проектируемого цеха
Технологическая часть
1. Анализ технологичности конструкции детали
2. Выбор положения отливки в форме
3. Выбор поверхности и разъемы формы
4. Выбор литниковой системы и ее расчет
5. Выбор режима заливки и охлаждения отливки
6. Специфические виды брака
Экономическая часть
1. Научная организация труда в литейном цехе
2. Технико-экономическое обоснование выбора стержневых автоматов LB50 взамен стержневых автоматов мод.4705.
3. Определение стоимости основных фондов
4. Расчет материально-энергетических затрат
5.Расчет штатов цеха
6. Расчет фонда заработной платы
7. Расчет и составление сметы на содержание и эксплуатацию оборудования
8. Расчет сметы общепроизводственных расходов
9. Калькуляция себестоимости продукции
10.Финансовый менеджмент
1. Исходные данные для технического проекта
2. Объемно-планировочное решение
3. Архитектурно-строительное решение
Безопасность и экологичность
1. Техника безопасности
2. Производственная санитария.
3.Защита окружающей среды
4.Пожарная безопасность
5.Анализ опасных и вредных факторов на производстве
6.Расчет искусственного освещения участка литья в кокиль
Гражданская оборона
1. Задачи гражданской обороны
2.Общезаводские мероприятия проводимые при угрозе нападения
3.Мероприятия проводимые в литейном цехе при угрозе нападения
4.Общезаводские мероприятия проводимые при внезапном нападении
5.Мороприятия в цехе по сигналу «Воздушная тревога»
6.Обеспечение защиты рабочих и служащих цеха
7.Мореприятия по защите ценного и технологического оборудования
Список используемой литературы
Литейное производство является одной из основных заготовительных баз машиностроения. Широкое распространение литейного производства объясняется большими его преимуществами по сравнению с другими способами производства заготовок (ковка штамповка):
возможностью получения деталей с заданными физико-механическими свойствами;
универсальностью и экономичностью методов формообразования сложных металлических изделий
максимальным приближением отливок по конфигурации и размерам к готовой детали;
снижением цикла изготовления;
отходы в стружку при изготовлении специальными способами литья сведены до минимума;
изготовлением деталей из сплавов которые трудно поддаются механической обработке;
безвозвратные потери у отливок составляют 7 – 9 % у деталей из сварных соединений около 11 – 12 % у поковок 13 – 14.
Примерно около 70 % (по массе) заготовок получают литьем а в некоторых отраслях машиностроения например в станкостроении 90 – 95 %. Литьем можно получить заготовки практически любой сложности с минимальными припусками на механическую обработку. Это очень важное преимущество так как сокращение затрат на обработку резанием снижает себестоимость изделий и уменьшает расход металла. Кроме того производство литых заготовок значительно дешевле чем например производство поковок.
В последнее время большое развитие получили специальные методы литья. К ним относятся:
литье по выплавляемым моделям;
литье в оболочковые формы
литье под давлением;
литье под низким давлением;
центробежное литье и т.д.
Отливки получаемые специальными методами литья по конфигурации и размерной точности приближаются к готовым деталям и объем их обработки резанием невелик.
Выход годного литья увеличивается для кокильного литья до 40 – 60 %.
При литье специальными способами увеличивается производительность процесса снижается трудоемкость изготовления деталей возможно получение тонкостенных отливок широко используются средства механизации и автоматизации.
Литье в кокиль является одним из самых экономичных способов литья который нашел широкое применение во многих отраслях промышленности особенно в машиностроении.
Сущность процесса литья в кокиль заключается в заливке жидкого сплава в металлическую форму в которой благодаря высокой теплопроводности материала формы происходит быстрое затвердевание и охлаждение отливки. Металлическая форма применяется многократно и имеет высокую стойкость. С целью регулирования скорости затвердевания отливок рабочие поверхности кокилей облицовывают и окрашивают теплоизоляционными красками. Покрытие наносят также и для защиты формы от воздействия жидкого металла.
Область применения литья в кокиль в значительной степени определяется технологическими возможностями и экономической целесообразностью производства отливок этим способом.
Литье в кокиль дает следующие качественные и количественные преимущества:
повышение физико-механических и эксплуатационных свойств отливок;
увеличение выхода использованного для изготовления отливок металла т.е.отношения массы полученной отливки к залитому в форму расплаву;
повышение размерной точности и качества поверхностей отливок;
уменьшение допусков и припусков на механическую обработку;
частичное или полное исключение формовочных материалов из производства;
увеличение производительности труда и съема отливок с производственной площади;
улучшение санитарно-гигиенических условий труда.
Недостатки литья в кокиль – высокие трудоемкость изготовления и стоимость металлической формы повышенная склонность к возникновению внутренних напряжений в отливке вследствие затрудненной усадки и более узкого по сравнению с литьем в песчаную форму интервала оптимальных режимов литья обеспечивающих получение качественной отливки.[ЦЛ]
Литьем под низким давлением изготавливают отливки подвергаемые испытаниям на герметичность сложной конфигурации с тонкими и толстыми стенками крупногабаритные с несколькими массивными тепловыми узлами.
Основные преимущества литья под низким давлением: большой выход годного (80-98 %) повышенная плотность отливок высокий уровень автоматизации процесса.
Литье под низким давлением состоит в вытеснении газом жидкого металла из раздаточной печи в литейную форму. Помимо принудительного заполнения литейной формы в этом методе литья эффективно используют питание затвердевающей отливки жидким металлом из естественной прибыли – металлопровода.
В целом цехи специальные виды литья: ЛНД ЛПД литье в кокиль являются более производительными и экономичными по сравнению с традиционными видами литья (литье в песчаные формы) в этих цехах гораздо выше уровень автоматизации процессов и культура производства.
Проектное задание и его анализ.
Изготовление отливок производится специальными видами литья:
литье под низким давлением
Эти способы рациональны при массовом производстве отливок.
Номенклатура отливок включает в себя 19 отливок весом от 04 до 17 кг.
Проектируемый цех предполагается построить в городе Заволжье Нижегородской области.
Расчетная зимняя температура – 25 °С.
В районе имеется зона из зеленых насаждений. Удаление отходов осуществляется через систему очистки.
Транспорт общезаводской.
отопление от заводской ТЭЦ;
электроэнергия с центральной распределительной подстанции завода;
сжатый воздух от заводской компрессорной станции;
водопровод от заводской сети.
Канализация общезаводская.
1 Номенклатура и программа выпуска отливок.
Номенклатура и программа выпуска отливок проектируемого цеха приведена в таблице 1.1.
Номер и наименование отливки
Масса одной отливки кг
Количество на изделие шт
Корпус водяного насоса
Корпус масляного насоса
21.1003015 Головка цилиндров
2. Программа выпуска отливок с учетом брака.
Программа выпуска отливок с учетом брака для проектируемого цеха представлена в таблице 1.2.
Годовой выпуск отливок
Годовой брак отливок
Годовая программа с учетом брака
3 Режим работы и фонды времени работы оборудования.
В механизированных и автоматизированных цехах при массовом производстве отливок когда идет разделение операций по месту и совмещение их по времени самый рациональный режим работы – параллельный.
Рациональнее применить трехсменный режим работы наиболее характерный для цехов в машиностроительной промышленности. Техническое обслуживание и подготовка оборудования производятся в выходные дни работниками ремонтных служб.
Расчет фондов времени производится исходя из 40-часовой рабочей недели. Применяем пятидневную рабочую неделю с двумя выходными. Продолжительность рабочей смены 8 часов.
Плавильное 5377 чгод;
Заливочное 5377 чгод;
Термическое 5521 чгод;
Стержневое 5034 чгод.
Технологические процессы. Расчет оборудования. Описание цеха
1. Расчет программы плавильного участка по выпуску жидкого металла на год.
Программа плавильного отделения для проектируемого цеха представлена в таблице 2.1.
Наименование отливки
Годовое количество отливок с учетом брака
Масса литников и прибылей
Годовое количество жидкого металла на программу
На программу с учетом брака
4.1118066-20 Патрубок
4.1118055-30 Патрубок
-11-1003015-02 Головка цилиндров
-06-1003015-30 Головка цилиндров
2 Выбор плавильного агрегата.
В настоящее время в литейном производстве для плавки алюминия и алюминиевых сплавов применяют следующие печи:
пламенные отражательные печи;
индукционные канальные и тигельные печи;
электропечи сопротивления.
Для производства вторичных литейных алюминиевых сплавов применяют пламенные отражательные печи емкостью от 10 до 30 тонн и тигельные индукционные печи емкостью от 25 до 6 тонн. В пламенных отражательных печах имеет место повышенный угар металла низкая производительность и насыщение расплава газами. В результате этих недостатков широкого применения данные печи не находят.
Плавка в индукционных печах вследствие меньшей удельной площади сопровождается меньшей газонасыщенностью расплава меньшей его окисляемостью и более низкими безвозвратными потерями.
В последнее время широкое применение получили индукционные печи промышленной частоты с сердечником. Эти печи имеют низкий удельный расход электроэнергии порядка 305 большую производительность и высокий коэффициент полезного действия (КПД) (до 75%). Однако данные печи имеют ряд существенных недостатков таких как:
зарастание каналов печи окисью алюминия а также флюсами и шлаками;
низкая стойкость футеровки (2-3 месяца).
Свободными от данных недостатков и более удобными в эксплуатации являются тигельные индукционные печи. Индукционный нагрев металла получил в настоящее время широкое распространение. При индукционном нагреве теплота выделяется непосредственно в металле нагреваемом в тигле благодаря чему использование тепла оказывается более совершенным и обеспечивается значительно большая скорость нагрева.
Индукционные тигельные печи промышленной частоты просты по своей конструкции. Они представляют собой тигель помещенный в индуктор питаемый переменным током. После слива каждой плавки можно легко осмотреть и очистить а затем если это необходимо загрузить в него шихту другого по композиции сплава.
Тигельные индукционные печи применяются главным образом для плавки высококачественных сплавов сталей и алюминиевых сплавов требующих особой частоты однородности и точности химического состава. Эти печи имеют ряд несомненных преимуществ перед другими печами. При малом зеркале металла и большой скорости нагрева плавка характеризуется малым угаром (05 – 10 %). Благодаря тому что атмосфера эл.печей не содержит продуктов сгорания топлива возможно получение сплавов со значительно меньшим чем в пламенных печах уровнем загрязнения неметаллическими примесями (водородом и оксидами) и отказаться например в ряде случаев от применения эффективных но дорогостоящих методов дегазации расплава либо при их применении получить особо высокое качество металла. Пониженная газонасыщенность дает отливки с высокими механическими свойствами.
Печи дают более высокую производительность (в 2-3 раза по сравнению с пламенными и в 5-6 раз по сравнению с электропечами сопротивления).
Затраты на получение тонны расплава литейных алюминиевых сплавов в индукционных тигельных печах значительно ниже чем в пламенных отражательных печах. Меньший расход энергии обусловлен отсутствием потери тепла из рабочего пространства печи продуктами сгорания топлива. Также необходимо отметить еще несколько преимуществ данных печей:
более легкие условия труда;
простое и широкое регулирование мощности и температуры;
сокращение производственной площади из-за малых габаритов печи;
получение чистого расплава благодаря отсутствию источников загрязнения; поглощение водорода на 40% меньше чем в других печах из-за более совершенных условий нагрева;
стойкость тигля более 6 месяцев.
Основным недостатком индукционных печей по сравнению с канальными печами является повышенный расход электроэнергии.
Хорошо зарекомендовали себя для плавки алюминия и его сплавов печи емкостью до 25 тонн. Такие печи снабжены механизированной крышкой шихту можно загружать как вручную так и механизированным способом например мостовым краном. При непрерывной работе с одним сплавом рекомендуется оставлять на дне тигля определенный переходящий остаток и в него загружать свежую шихту.
Расплавленный металл сливается через сливной носок путем наклона печи гидравлическим приводом.
Техническая характеристика плавильной печи УИП-800-10-10х2 представлена в таблице 2.2
Наименование характеристики
Емкость печи по алюминию т
Мощность источника питания кВт
Число фаз питающей сети
Номинальная частота тока контактной сети Гц
Номинальное напряжение питающей сети В
Производительность печи тч
Время расплавления и перегрева до номинальной температуры ч
Удельный расход эл.нергии на расплавление алюминия кВт*чт
Печь питается от однофазного электропечного трансформатора ЭОМН-150010 мощностью 1300 кВА с девятью ступенями переключения напряжения в диапазоне от 116 до 029 кВ (возможно переключение под нагрузкой).
Состояние тигля и наличие утечек на землю контролируется сигнализатором утечки позволяющим своевременно определять сроки ремонтов
3 Склад шихтовых материалов.
Для бесперебойной работы цеха необходимо иметь минимальный но в то же время достаточный запас материалов.
Снабжение цеха песком для изготовления стержневой смеси производится железнодорожным транспортом а флюсами пропиточными смазочными огнеупорными и другими материалами – автомобильным транспортом
Шихта для выплавки сплавов поступает с заводов-поставщиков в виде пакетов чушек весом 15 – 16 кг каждая. Каждый пакет весит в среднем около одной тонны.
Для разгрузки автомобильного транспорта которыми доставляются пакеты с шихтой применяются мостовые краны. На склад пакеты доставляются электропогрузчиками.
Для подачи шихты к плавильным печам предусмотрена система подачи тары и возврата ее по рольгангам. Перед загрузкой в плавильные печи шихта проходит через специальные печи для сушки и подогрева шихты. Эта операция применяется для удаления влаги и увеличения производительности плавильных печей.
В суточные бункера с пластинчатыми питателями шихтовые материалы загружаются при помощи мостового крана.
Возврат собственного производства в виде литников и прибылей поступает на склад шихтовых материалов по системе подземных ленточных транспортеров. На шихтовом дворе для возврата предусмотрено отдельное место хранения.
В проектируемом цехе применяется весовое дозирование шихты. Ее составляющие из суточных бункеров с помощью пластинчатых питателей подаются в бадью с открывающимся дном установленную на весовой тележке.
На шихтовом дворе металлы флюсы материалы хранятся строго по партиям.
Силумин алюминий первичный сплавы хранятся в таре высотой не более чем в два яруса. Марганец металлический хранится в поступающей с завода-поставщика таре (металлических бочках).
Все материалы поступающие на шихтовый двор в цех должны иметь сопровождающие сертификаты качества.
При поступлении влажного и загрязненного материала дают им просохнуть в естественных условиях на шихтовом дворе и производят очистку чушек.
Марганец металлический кусковой перед подачей на плавильный участок размалывают в щековой дробилке до кусков не более 40х40.
Магний режут на летночно-пильном станке на равные части укладывают в тару и подают на плавильный участок.
Возврат производства (литники брак отливок) должен быть сухой чистый без наличия песка и остатков стержней не иметь каркасов и не содержать инородных металлических и неметаллических включений
К шихтовым материалам применяемым в проектируемом цехе предъявляются следующие требования:
все шихтовые материалы должны загружаться в печь сухими и чистыми;
чушки шихты должны соответствовать требованиям ГОСТа;
не допускается перемешивание сплавов разных марок.
4 Характеристика сплавов.
В проектируемом литейном цехе предусматривается производство отливок из сплавов АК9ч. АК9М3-К и АК8М3ч
Химический состав сплавов должен удовлетворять требованиям ГОСТ 1583 – 93. Химические составы приведены в таблице
4.1 Характеристика сплава АК9ч
Сплав АК9ч относится к первой группе литейных сплавов по химическому составу (основа Al-Si-Mg).
Химический состав сплава АК9ч согласно ГОСТ 1583-93 приведен в таблице 2.3.
Массовая доля % основного компонента
Массовая доля % примесей не более
Кремний Si – повышает жидкотекучесть прочность жаростойкость.
Магний Mg – повышает механические свойства увеличивает пористость.
Si и Mg образуют химическое соединение которое при нагреве под термообработку растворяется в твердом растворе выпадает по границам зерен делая структуру мелкозернистой затем фиксируется в этом состоянии в закалочной среде (воде).
Марганец Mn – вводится в сплав для компенсации вредного влияния железа Fe которое в свободном состоянии имеет игольчатое строение и снижает прочностные свойства сплава.
Медь Cu – повышает механические свойства снижает коррозийную стойкость.
Технологические свойства сплава АК9ч согласно ГОСТ 1583-93 приведены в таблице 2.4.
Жидкотеку-честь при 700°С мм
проба прутковая спиральная
Литей-ная усадка eЛИТ %
Объем-ная усадка eV %
Склонность к горячим трещинам мм
Интервал кристал-лизации
Давление газа давление воды
Плотность при 20°С ликвидус
Механические свойства сплава АК9ч согласно ГОСТ 1583-93 приведены в таблице 2.5.
Сопротивление разрыву sВ МПа не менее
Относительное удлинение d % не менее
Твердость по Бринеллю НВ не менее
4.2 Характеристика сплава АК9М3-К
Сплав АК9М3-К относится ко второй группе литейных сплавов по химическому составу (основа Al-Si-Cu).
Химический состав сплава АК9М3-К согласно СТП 37.304.787-2002 приведен в таблице 2.6.
Технологические свойства сплава АК9М3-К согласно СТП 37.304.787-2002 приведены в таблице 2.7.
Литейная усадка eЛИТ %
Объемная усадка eV %
Технологические свойства сплава АК9М3-К согласно СТП 37.304.787-2002 приведены в таблице 2.8.
Предел прочности sВ МПа не менее
4.3 Характеристика сплава АК8М3ч
Сплав АК8М3ч относится ко второй группе литейных сплавов по химическому составу (основа Al-Si-Cu).
Химический состав сплава АК8М3ч согласно ГОСТ 1583-93 приведен в таблице 2.9.
Бериллий Be – способствует рафинированию снижает отрицательное влияние железа на механические свойства.
Бор B - способствует рафинированию измельчает структуру и повышает пластичность.
Цинк Zn – повышает механические свойства и ухудшает литейные.
Титан Ti - способствует измельчению структурных составляющих повышает механическую прочность.
Технологические свойства сплава АК8М3ч согласно ГОСТ 1583-93 приведены в таблице 2.10.
Механические свойства сплава АК8М3ч согласно ГОСТ 1583-93 приведены в таблице 2.11.
5 Описание технологического процесса приготовления сплавов.
5.1 Описание технологического процесса приготовления сплава АК9ч
В состав шихты сплава АК9ч входят следующие компоненты:
алюминий первичный ГОСТ 11069-74 марок А7 А7Э А7Е А6 А5;
силумин ГОСТ 1583-93 марок АК12пч АК12ч АК12оч;
магний ГОСТ 804-93 марки Мг90;
марганец металлический ГОСТ 6008-90 марок Мн997 Мн998;
возврат собственного производства марки АК9ч.
В первую очередь в плавильную печь загружается порция возврата производства. По мере расплавления возврата в отключенную печь загружаются порции свежих материалов в следующей последовательности: марганец ковшом затем чушки алюминия первичного и силумина. Далее производится расплавление шихты в плавильной печи под крышкой.
С целью снижения потерь металла в шлаке при температуре сплава (710±10) 0С производится его обработка рафинирующим флюсом в следующем порядке:
В отключенную плавильную печь на зеркало сплава ковшом засыпается флюс в количестве не менее 02 % от массы сплава в печи.
Производится выдержка сплава под слоем флюса в течение от 8 до 10 минут.
Флюс замешивается в сплав на глубину шумовки шлак снимается с поверхности сплава шумовкой в шлаковню.
После операции обработки сплава при помощи шумовки вводится в сплав навеска магния печь включается на ступень быстрого нагрева.
Не менее чем через 10 минут после ввода магния заливается образец для анализа химического состава сплава образец передается в спектральную лабораторию. Результат анализа передается на плавильный участок телефонограммой. При необходимости производится действия по корректировке химического состава. Сплав сливается из плавильной печи только при положительном результате анализа.
Затем сплав нагревается в плавильной печи до температуры (755±15) °С.
Готовый и годный по химическому составу металл сливается в ковш электропогрузчика транспортируется к установке для дегазации.
При технологическом переливе жидкого металла из плавильной печи в ковш а из него в раздаточную печь происходит рафинирование жидким флюсом
5.2 Описание технологического процесса приготовления сплава АК9М3-К
В состав шихты сплава АК9М3-К входят следующие компоненты:
сплав алюминиевый чушковый СТП 37.304.787-2002 марки АК9М3-К;
возврат собственного производства марки АК9М3-К.
В первую очередь в плавильную печь загружается порция возврата производства. По мере расплавления возврата в отключенную печь загружаются чушки сплава АК9М3-К. Производится расплавление шихты в плавильной печи под крышкой.
С целью снижения потерь металла в шлаке при температуре сплава (710±10) 0С производится его обработка рафинирующим флюсом (процесс обработки сплава рафинирующим флюсом аналогичен процессу обработки сплава АК9ч описанному в п. 2.5.1).
Заливается образец для анализа химического состава сплава образец передается в спектральную лабораторию. Результат анализа передается на плавильный участок телефонограммой. При необходимости производится действия по корректировке химического состава. Сплав сливается из плавильной печи только при положительном результате анализа.
При технологическом переливе жидкого металла из плавильной печи в ковш а из него в раздаточную печь происходит рафинирование жидким флюсом.
5.3 Описание технологического процесса приготовления сплава АК8М3ч
В состав шихты сплава АК8М3ч входят следующие компоненты:
цинк анодный ГОСТ 1180-90 марок Ц0 Ц1;
медь катодная ГОСТ 859-01 марок М0М3;
возврат собственного производства марки АК8М3ч.
В первую очередь в плавильную печь загружается порция возврата производства марки АК8М3ч.
По мере расплавления возврата в отключенную печь загружаются чушки алюминия первичного и силумина. Производится расплавление шихты в плавильной печи под крышкой.
С целью снижения потерь металла в шлаке при температуре сплава (710±10) 0С производится его обработка рафинирующим флюсом (процесс обработки сплава рафинирующим флюсом аналогичен процессу обработки сплава АК9ч описанному в п. 2.1.4).
При помощи шумовки вводятся в сплав навески меди цинка лигатур и позднее магния производится интенсивное замешивание до полного растворения.
Не менее чем через 10 минут после ввода легирующих добавок заливается образец для анализа химического состава сплава образец передается в спектральную лабораторию. Результат анализа передается на плавильный участок телефонограммой. При необходимости производится действия по корректировке химического состава. Сплав сливается из плавильной печи только при положительном результате анализа.
6 Рафинирование и модифицирование
Рафинированием называется процесс очищения металлов и сплавов от нежелательных примесей.
Рафинирование алюминиевых сплавов осуществляется в печи или ковше. В качестве рафинирующих средств используются флюсы состоящие из хлористых и фтористых солей. Наиболее прогрессивным методом рафинирования является рафинирование жидким флюсом посредством технологических переливов жидкого металла из плавильной печи в ковш а из него в раздаточную печь.
Рафинирование металла осуществляется следующим образом: в ковш непосредственно перед выпуском металла наливается определенное количество жидкого флюса затем производится выпуск плавки из печи в ковш. При заполнении ковша за счет интенсивного перемешивания металла с жидким флюсом развиваются значительные поверхности контакта между ними что обусловливает резкое снижение в сплаве неметаллических примесей и газов. Процесс продолжается и при последующем переливе металла с жидким флюсом из ковша в раздаточную печь поскольку в раздаточную печь сначала сливается флюс имеющий удельный вес меньше металла. Большая часть примесей и неметаллических включений реагирует с флюсом и поднимается в виде шлака на поверхность зеркала металла откуда его снимают. После рафинирования металл восстанавливается в течении 5 минут.
Модифицированием принято называть процесс искусственного изменения формы величины и внутреннего строения зерен образующихся при первичной кристаллизации. Модифицирование сплава является необходимой технологической операцией для сплавов с высоким содержанием кремния если он кристаллизуется в виде двойной эвтектики. Пластинчатые частицы кремния снижают механические свойства сплава. Для модифицирования применяют натрий. При содержании 009% - 01% натрия в сплаве кремний кристаллизуется в виде мелких округленных частиц что способствует повышению механических свойств.
Для модифицирования расплава вводится натрий до 008% от массы металла. Натрий может вводится в расплав как в чистом виде так и в виде модифицирующих флюсов содержащих фтористые и хлористые его соли.
В результате модифицирования структура затвердевшего сплава становится весьма мелкозернистой предел прочности увеличивается на 30-40% а удлинение возрастает в 2-3 раза.
Готовый флюс используется для рафинирования и модифицирования жидких алюминиевых сплавов.
Наименование материала
Соль повареная пищевая
Криолит искусственный технический
В состав установки входит ванна выкатная для флюса каркас электродная группа нагреватель для пуска установки используется трансформатор понижающий печной.
Ванная выкатная для флюса представляет собой емкость закрепленную в подшипниках на сварной раме. Рама поставлена на колесо с внутренней стороны ванны. Зафутерована шамотным кирпичом. С наружной стороны наложена изоляция из стекловолокна. Каркас состоит из сварной цилиндрической обечайки закрепленной на стойках. Сверху к обечайке приварен патрубок для подключения к системе вентиляции. На каркасе имеется площадка с окном для крепления электродной группы. С лицевой стороны обечайки имеется другое окно для загрузки и выгрузки флюса закрывается оно откидной дверкой.
Конструкция электродной группы предусматривает возможность перемещения электродов по вертикали по мере их обогревания и для выкатки ванны по горизонтали.
6.1 Дегазация алюминиевых сплавов
Дегазация алюминиевых сплавов проводится с целью очистки от различных включений и загрязнений. Дегазация проводится непосредственно в разливочном ковше или в раздаточной печи.
Дегазация проводится методом продувки жидкого металла инертным газом - азотом ГОСТ 9293-74.
Характеристика азота: бесцветный газ малорастворимый в воде (2.3 мг100г при10 0С; 08 мг100г при 69 0С).
Получают азот ректификацией сжиженного атмосферного воздуха. Молекула азота состоит из 2-х атомов. Эти атомы прочно связаны друг с другом чем и объясняется большая инертность азота при обычных условиях.
Азот в химическом отношении отличается большой инертностью. При обычной температуре (20 0С) он почти не способен вступать в реакцию. При нагреве довольно легко соединяется с некоторыми металлами: литием магнием кальцием титаном. При очень высокой температуре азот непосредственно соединяется с кислородом и водородом.
6.2 Описание технологического процесса дегазации Al сплава в разливочном ковше
Подать и установить ковш с металлом под консоль установки типа FDN. Температура металла сливаемого из печи должна быть 760–770 0С. металл в ковше должен быть рафинирован. Плавильщик должен убедиться что ковш находится на полу и графитовый стержень находится по центру ковша. Далее провести следующие операции:
погружение графитового стержня в жидкий металл;
вращение графитового стержня с одновременной подачей азота в жидкий металл;
выгрузка графитового стержня;
Время продувки азотом – 3 минуты при давлении 3 атмосферы.
Подать ковш к контрольному посту заливочных участков.
Выдержать сплав в ковше не менее 6 - 7 минут.
Снять шлак с зеркала металла в ковше.
Замерить температуру металла в ковше. Температура должна быть (700 – 730) 0С.
Примечание. Давление азота измерять манометром ГОСТ 2405-88 предел измерения от 0 до 25 кгссм2 (025 МПа).
6.3 Описание по дегазации в раздаточных печах ИАКр-10
Плавильщику произвести дегазацию сплава в индукционной печи ИАКр-1.0для чего на шкафу управления печи нажать кнопку черного цвета с надписью «Дегазация» (Процесс дегазации происходит в течении 5 минут после чего происходит автоматическое отключение установки).
Выдержать сплав в течении 10 минут. Контроль времени производить по часам электрическим вторичным показывающим ЭВЧ ТУ 25-07.1503-82.
Наладчику заливочного участка установку баллона с аргоном для дегазации производить в следующей последовательности: установить на баллон с селикогелем открыть вентиль баллона при закрытом редукторе. Установить расход газа 8 лмин вращением маховика (винта регулирующего) при этом на указателе расход газа должен быть на 10 единицах.
Наладчику одновременно с заменой использованного баллона с аргоном производить замену патрона селикогелем. Использованный патрон с открытой крышкой просушить на кольце раздаточной печи в течении 1 часа.
7 Расчеты баланса и состава шихты для сплавов.
7.1 Расчеты баланса и состава шихты сплава АК9ч
По данным ведомости объемов производства (таблица 2.1) составляем баланс сплава АК9ч.
Итого жидкого металла
Угар и безвозвратные потери
Всего металлозавалка
Расчет шихты производим на 1000кг жидкого сплава на основании баланса металла и химического состава сплава АК9ч.
Расчет ведем по среднему содержанию компонентов.
Mg = 027 % (берем повышенное содержание из-за большого угара)
7.1.1 Определяем количество металлозавалки:
х - 100 % х = 10363 кг
7.1.2 Определяем количество возврата производства в составе шихты (на основании баланса металла):
85 % + 3 % = 5285 %
х - 5285 % х = 5477 кг
7.1.3 Определяем количество свежих материалов:
363 кг – 5477 кг = 4886 кг
7.1.4 Определяем необходимое количество кремния:
х - 925 % х = 452 кг
Кремний вводится в сплав в составе силумина среднее содержание кремния в котором 117 %. Количество вводимого силумина составит:
х - 100 % х = 3863 кг
Процентное содержание силумина в шихте составит:
63 кг - х х = 3728 %
7.1.5 Определяем необходимое количество магния:
Процентное содержание магния в шихте составит:
7.1.6 Определяем необходимое количество марганца:
Процентное содержание марганца в шихте составит:
7.1.7 Определяем необходимое количество алюминия первичного:
86 кг – (3863 кг + 13 кг + 18 кг) = 992 кг
Процентное содержание алюминия первичного в шихте составит:
Результаты расчетов заносим в таблицу 2.13
Масса на 1 тонну жидкого сплава кг
Масса на тонну годного кг
Возврат производства
7.2 Расчеты баланса и состава шихты сплава АК9М3-К
По данным ведомости объемов производства (таблица 2.1) составляем баланс сплава АК9М3-К.
Расчет шихты производим на 1000кг жидкого сплава на основании баланса металла сплава АК9М3-К.
7.2.1 Определяем количество металлозавалки:
7.2.3 Определяем количество возврата производства в составе шихты (на основании баланса металла):
85 % + 3 % = 5585 %
х - 5585 % х = 5788 кг
7.2.4 Определяем необходимое количество чушкового сплава АК9М3-К:
363 кг – 5788 кг = 4575 кг
Процентное содержание чушкового сплава в шихте составит:
75 кг - х х = 4415 %
Результаты расчетов заносим в таблицу 2.15
Масса на 1 тонну годного кг сплава кг
Чушковый сплав АК9М3-К
7.3 Расчеты баланса и состава шихты сплава АК8М3ч
По данным ведомости объемов производства (таблица 1.2) составляем баланс сплава АК8М3ч.
Расчет шихты производим на 1000кг жидкого сплава на основании баланса металла и химического состава сплава АК8М3ч.
Mg = 035 % (берем повышенное содержание из-за большого угара)
7.3.1 Определяем количество металлозавалки:
7.3.2 Определяем количество возврата производства в составе шихты (на основании баланса металла):
х - 643 % х = 6663 кг
7.3.3 Определяем количество свежих материалов:
363 кг – 6663 кг = 370 кг
7.3.4 Определяем необходимое количество кремния:
х - 775 % х = 287 кг
х - 100 % х = 2453 кг
53 кг - х х = 2369 %
7.3.5 Определяем необходимое количество магния:
7.3.6 Определяем необходимое количество меди:
Процентное содержание меди в шихте составит:
7.3.7 Определяем необходимое количество цинка:
Процентное содержание цинка в шихте составит:
7.3.8 Определяем необходимое количество титана:
Титан вводится в сплав в составе лигатуры Al-Ti в которой содержание титана составляет 5 %. Количество вводимой лигатуры составит:
Процентное содержание лигатуры Al-Ti в шихте составит:
7.3.9 Определяем необходимое количество бериллия:
Бериллий вводится в сплав в составе лигатуры Al-Ве в которой содержание бериллия составляет 5 %. Количество вводимой лигатуры составит:
Процентное содержание лигатуры Al-Ве в шихте составит:
7.3.10 Определяем необходимое количество бора:
х - 005 % х = 019 кг
Бор вводится в сплав в составе лигатуры Al-В в которой содержание бора составляет 3 %. Количество вводимой лигатуры составит:
Процентное содержание лигатуры Al-В в шихте составит:
7.3.11 Определяем необходимое количество алюминия первичного:
0 кг – (2453 кг + 13 кг + 111 кг + 28 кг + 14 кг + 14 кг + 63 кг) = 752 кг
Результаты расчетов заносим в таблицу 2.17
Масса на 1 тонну годного кг
8 Расчет количества оборудования плавильного отделения.
8.1 Расчет количества плавильных печей
Расчет количества печей производим по формулам:
где Р1 – расчетное число единиц оборудования;
К1 – коэффициент неравномерности производства (1.0-1.2) К1 = 12
К2 – коэффициент производительности учитывающий отклонения от паспортных данных (0.8-1.0) К2 = 1
N – часовая производительность тчас
Фд – действительный годовой фонд времени работы оборудования ч
В – годовая потребность в продукте с учетом брака и потерь т
Р2 – принятое в проекте число оборудования
КЗ – коэффициент загрузки оборудования КЗ = 0.8
Расчет производим отдельно для плавки каждого сплава.
8.1.1 Для плавки сплава АК9ч:
Принимаем 3 печи для плавки сплава АК9ч.
8.1.2 Для плавки сплава АК9М3-К:
Принимаем 4 печи для плавки сплава АК9М3-К.
8.1.3 Для плавки сплава АК8М3ч:
Принимаем 1 печь для плавки сплава АК8М3ч.
Всего количество плавильных печей принимаем 8 шт.
8.2 Выбор и расчет оборудования для просушки и подогрева шихты
Для просушки и подогрева шихтовых материалов перед загрузкой в плавильные печи выбираем проходные камерные сушила ЭП 0055.00.
8.2.1 Техническая характеристика сушил приведена в таблице 2.18.
Производительность тч
Температура нагрева 0С
Количество зон нагрева
8.2.2 Расчет количества проходных камерных сушил ЭП 0055.00
Для подсушки и подогрева шихтовых материалов применяем камерные сушила ЭП 0055.00.
Расчет количества сушил производим по формулам (1) (2):
Принимаем 2 камерных сушила.
9 Заливочное отделение
В проектируемом цехе литьем в кокиль предусмотрено изготавливать 19 наименования отливок или 7982 тонн годного литья в год литьем под низким давлением предусмотрено изготавливать 2 наименования отливок или 2019 тонн годного литья в год.
9.1 Расчет количества кокильных машин.
Отливки №№ 11 13 (таблица 2.1) изготавливаются на заливочном комплексе. В состав комплекса входит: четырехпозиционных карусельно-кокильные машины 4980 механический заливщик 83М две раздаточные печи ИАКр-10.
Количество ККМ-4980 рассчитываем по формулам (1) (2):
Таким образом для производства данных отливок принимаем три заливочных комплекса.
Машина карусельно-кокильная модели 4980 предназначена для получения отливок из алюминиевых сплавов в кокиль с вертикальной плоскостью разъема с поддоном с правой и левой подвижными плитами с протяжкой торцевого и нижнего стержней и выталкиванием отливок из поддона. Плита поддона снабжена системой принудительного водяного охлаждения. Система управления – комбинированная пневматическая и электрическая и обеспечивает работу в полуавтоматическом режиме.
Техническая характеристика ККМ-4980 представлена в таблице 2.19.
Производительность не менее отлч
Количество позиций шт
Машинное время цикла с
Расход охлаждающей воды м3ч
Расход сжатого воздуха м3ч
Масса дозы заливаемого металла кг
высота над уровнем пола
Механический заливщик модели 83М предназначен для дозирования транспортировки и заливки алюминиевых сплавов в кокиля на кокильных машинах с массой заливаемого металла до 38 кг. Предусмотрена также возможность очистки ковша от окисных плен в камере выбивки при помощи обдува воздуха и вибратора на обратном пути от кокиля к раздаточной печи.
Режим работы заливщика – полуавтоматический. Система управления – программируемый контроллер.
Техническая характеристика механического заливщика модели 83М представлена в таблице 2.20.
Время цикла не более с
Наибольший угол поворота балки град.
Наибольшее вертикальное перемещение ковша мм
Техническая характеристика раздаточных печей ИАКр-10 представлена в таблице 2.19.
Номинальная мощность кВт
Производительность печи при расплавки тч
Точность поддержания температуры 0С
Габаритные размеры печи мм:
Питание печи от трехфазной системы
Расход воды не менее м3ч
Отливки номер 1245 (таблица 2.1) отливаются на заливочном комплексе. В состав комплекса входит: карусельно-кокильная машина модели 4979 механический дозатор модели 139М раздаточные печи САТ-025.
Количество ККМ-4979 определяем по формулам (1) (2):
Таким образом принимаем три заливочных комплекса.
ККМ-4979 предназначена для получения средних отливок из алюминиевых сплавов среднего развеса. Техническая характеристика данной машины приведена в таблице 2.20.
Производительность отлч
Машинное время цикла не более с
Механический заливщик модели 139М предназначен для дозирования транспортировки и заливки алюминиевых сплавов в кокиля на кокильных машинах с массой заливаемого металла до 20 кг.
Техническая характеристика механического заливщика модели 139М представлена в таблице 2.21.
Для сохранения сплава в жидком состоянии в непосредственной близи с заливочной машиной принимаем тигельную электропечь сопротивления САТ-025.
Раздаточно-подогревательная печь САТ-025 выполнена в виде сварного металлического кожуха цилиндрической формы футерованного легковестно-шамотным кирпичом. Нихромовые (Х20Н80) нагревательные элементы печи размещены по боковой поверхности рабочей камеры они закреплены на крючках которые вмонтированы в канавки корундовых полочек. Нагревательные элементы питаются электроэнергией от сети.
В верхней части футеровки вмонтировано литое опорное кольцо выполненное из жаропрочного чугуна. На это кольцо устанавливается литой жаропрочный чугунный тигель. В нижней части печи расположено сливное отверстие.
Во избежание насыщения алюминиевого сплава железом на чугунный тигель наносят специальную обмазку (60% мелкого кварцевого песка 30% огнеупорной глины 10% жидкого стекла)
Техническая характеристика САТ- 025 представлена в таблице 2.22
Количество тепловых зон
Мах рабочая температура
Внутренний размер тигля
Отливки номер: 3 7 8 9 10 14 15 16 17 (таблица 2.1) изготавливаются на заливочном комплексе. В состав входит: четырехпозиционная карусельно-кокильная машина модели 4932 механический заливщик модели 139М раздаточная печь САТ-025.
Количество машин ККМ-4932 определяем также по формулам (1) (2):
В итоге принимаем два заливочных комплекса.
Карусельно-кокильная машина ККМ-4932 предназначена для производства мелких отливок.
Краткая техническая характеристика ККМ-4932 дана в таблице 2.23.
Вес порции заливаемого металла кг
Расход охлаждаемой воды м3ч
Технические характеристики механического заливщика модели 132М и раздаточно-подогревательной печи САТ-025 представлены в таблицах 2.21. и 2.22.
Количество кокильных установок 14МС определяем по формулам (1) (2):
Таким образом принимаем две кокильные установки 14МС.
Данная установка предназначена для изготовления отливок с уменьшенной литниковой системой из алюминиевых сплавов сложной конфигурации и в том числе с металлическим стержнем. Установки наклонного типа применяются для материалов с тенденцией к окислению и пенообразованию. В результате наклона происходит снижение скорости потока металла при заполнении что приводит к снижению пенообразования.
Достоинством данного типа оборудования является:
направленная кристаллизация отливки которая происходит благодаря медленному наклону формы в процессе заполнения;
низкая высота падения металла при заполнении формы та как процедура наклона в то же время выполняет функцию торможения;
низкая высота падения намного сокращает завихрения воздуха в расплаве и способствует плавному заполнению форму;
постоянное статистическое давление в процессе заполнения формы которое особенно важно при производстве тонкостенных отливок;
хорошее распределение и направленная кристаллизация в направлении заливочной чаши что снижает необходимость точного вычисления параметров заливки и системы литников.
Техническая характеристика установки 14МС дана в таблице 2.24.
Количество кокилей шт
Время цикла машинное с
Размер кокильных плит мм
Угол поворота станка град.
Отливка 12 (таблица 2.1) изготавливаются на заливочном комплексе. В состав комплекса входит: шестипозиционная карусельно-кокильная машина 4920 механический заливщик 139М две раздаточные печи ИАКр-10.
Количество ККМ-4920 рассчитываем по формулам (1) (2):
Таким образом для производства данных отливок принимаем три заливочных комплекса.
Техническая характеристика секции ККМ 4920 дана в таблице 2.25.
Технические характеристики механического заливщика модели 132М и раздаточной печи АИКр-10 представлены в таблицах 2.21 и 2.19
Отливки 18 19 заливаются на заливочном комплексе. В состав комплекса входит машина литья под низким давлением мод.03МП и эл.печь нагревательная 4188.
Количество машин ЛНД 03МП рассчитываем по формулам (1) (2):
Таким образом для производства данных отливок принимаем четыре заливочных комплекса.
Машина ЛНД 03МП предназначена для получения отливок головок цилиндров в прессформе с подачей алюминиевого сплава под низким давлением из электрической печи в поддон прессформы.
Техническая характеристика секции машины ЛНД мод.03МП дана в таблице 2.26.
Техническая характеристика и нагревательнаой эл.печи 4188 представлена в таблице 2.27
Тип электронагревателя
Мах рабочая температура 0С
Перед заливкой кокиля очищаются от старой краски нагара при помощи установки «Cold Jet» гранулами сухого льда разогреваются газовой горелкой до температуры 280-350 °С и окрашиваются кокильными краской марки «Ставрол 700К»- рабочая поверхность кокиля краской марки «Ставрол 700П»- литниковая система кокиля.
С участка заливки по подвесному конвейеру отливки проходят период охлаждения и поступают на участок выбивки для удаления песчаных стержней. Далее отливки поступают на обрезной участок где происходит обрубка литников обрезка прибылей зачистка заливов. После данных операций производится термическая обработка отливок по режиму Т6 (закалка плюс искусственное старение).
10 Участок смесеприготовления и изготовления стержней.
Выбор смесей и способов получения стержней в значительной мере определяется их размерами сложностью и серийностью производства. При определении годового количества и массы стержней следует учитывать потери которые имеют место из-за брака отливок форм и из-за поломки стержней и т.п. эти потери обычно составляют около 10 %.
В базовом цехе стержни в основном изготавливаются при помощи ручной формовки или на стержневых автоматах работающих на горячей оснастке.
Так как изготовление стержней по горячей оснастке становится все менее популярным то в проектируемом литейном цехе стержни будем изготовлять из холодно-твердеющих смесей (ХТС).
Для изготовления стержней из холодно-твердеющих смесей применяем оборудование германской фирмы «Laempe».
Использование холодно-твердеющих смесей по сравнению со смесями приготовляемыми на горячей оснастке дает следующие значительные преимущества:
повышение точности стержней;
изготовление сложных стержней без склейки;
низкий брак (отверждение по всему объему);
короткий цикл производства;
значительное удешевление оснастки (в частности отсутствие электронагревателей и защитных кожухов для них);
экономия энергоресурсов.
Процесс изготовления стержней из холодно-твердеющих смесей основан на способности сыпучей песчано-смоляной смеси заключенной в стержневой ящик отверждаться при комнатной температуре.
Быстрое развитие процесса началось после внедрения специальных синтетических связующих.
Главное преимущество процесса – высокая точность в сочетании с высоким качеством стержней.
В отличии от стержней из песчано-глинистых смесей стержни из холодно-твердеющих смесей не нуждаются в сушке.
Холодно-твердеющие смеси позволяют изготавливать стержни в ящиках из любого материала (дерева металла пластмассы); увеличивать плотность стержня (так как отсутствует преждевременное отверждение смеси в процессе надува); сокращать время на изготовление смесей (15 – 20 с) и повышать пластичность.
Применение ХТС экономически оправдано даже в условиях единичного и массового производства.
Для производства стержней по «Cold-Box-Amin» - процессу применяют стержневую смесь состоящую из формовочного кварцевого песка и связующей композиции которую отверждают продувкой газовым катализатором. Катализатор подводят под давлением при комнатной температуре или в предварительно подогретом состоянии через уплотненную в модельной оснастке стержневую смесь. Во время продувки стержневой смеси катализатор находится в парообразном состоянии причем катализатор разбавляют воздухом. Отверждение стержневой смеси наступает мгновенно. Свою окончательную прочность стержни достигают приблизительно через час. Относительные значения прочности стержня зависят от качества применяемых компонентов.
Связующая композиция состоит из полиуретановой смолы и полиизоцианата.
В качестве катализаторов при процессе Coldbox применяют амины.
Температура окружающей среды в зоне расположения смесителя LVM 50 должна быть не ниже +18 °С.
Помещение для хранения исходных компонентов должно быть оборудовано механической общеобменной вентиляцией по ГОСТ 12.4.021.
Связующее представляет собой композицию состоящую из трех компонентов фирмы «Perstorp Ferguson Limited» г. Санкт-Петербург:
раствор формальдегидной смолы – Pol
раствор полиизоцианата – Pol
третичный амин – Politec G89.
Для приготовления холодно-твердеющих смесей используются материалы:
песок формовочный кварцевый Балашейского ГОК марок 2К2О3О2 и 2К2О3О3;
связующие фирмы «Perstorp Ferguson Limited» г. Санкт-Петербург (см. таблицу 2.28.).
Характеристики составляющих стержневой смеси указаны в таблице 2.28.
Наименование материала марка
Песок формовочный кварцевый Балашейский
Марка 2К2О3О2 и 2К2О3О3
Составляет основу стержневой смеси
Паспорт качества фирмы «Perstorp»
Умеренно вязкая жидкость светло-желтого цвета
Феноло-формальдегид-ная смола
Умеренно вязкая жидкость темно-коричневого цвета
Триэтиламин – катализатор ускоритель отверждения связующего
Физико-механические свойства смеси представлены в таблице 2.29.
Состав стержневой смеси
Физико-механические свойства смеси
Песок Балашейский % (кг)
Полиизоциа-нат % (кг)
Сухая прочность не менее кгсм2
Газотворная способность не более гсм3
В проектируемом цехе для приготовления стержневой смеси и стержней применяем оборудование германской фирмы «Laempe». В комплект поставляемого оборудования входят: вертикальный смеситель типа LVM 50 пескострельные автоматы для производства стержней моделей LB50 и LL5 и скруббер для очистки воздуха.
Вертикальный смеситель LVM 50 предназначен для приготовления холодно-твердеющей смеси
Все операции связанные со смесеприготовлением например выбор рецептуры дозировка компонентов продолжительность дозировки и освобождение рабочего пространства смесителя задают в диалоге с управляющим компьютером. Для ввода значений параметров оператор не нуждается в особых знаниях по программированию. Режим работы смесителя контролируют непрерывно ошибки опознаются автоматически.
вертикального смесителя с приводом;
резервуара для свежего песка с объемным дозатором;
системы объемной дозировки связующего;
вертикального блока.
Смесители располагаются непосредственно над стержневыми автоматами.
Техническая характеристика смесителя LVM 50 представлена в таблице 2.30.
Емкость трубки смесителя л
Производительность стержневой смеси тч
Мощность смесителя кВт
Рабочее давление сжатого воздуха атм
Расход воздуха при постоянной работе и давлении
В качестве стержневых автоматов выбираем стержневые автоматы фирмы «Laempe» типа LB50 и LL5.
Стержневая смесь на данных автоматах уплотняется в модельной оснастке пескострельным способом.
Программа стержневого участка представлена в таблице 2.31.
Количество стержней в одной отливке шт.
Количество стержней в ящике шт.
Программа стержней штгод
Годовая программа стержней с учетом брака
62.1008015 "Труба впускная
61.1307015 "Корпус водяного насоса
63.1008015 "Труба впускная
4.1008015 "Труба впускная
4.1307015 "Корпус водяного насоса
6.1003015 "Головка цилиндров
21.1003015 "Головка цилиндров
4.1003015 "Головка цилиндров
4.1111450 "Кронштейн
Преимущество технологии фирмы «Laempe» состоит в применении вакуума и пневматических фиксаторов частей стержневого ящика. За счет этого затраты времени на замену комплекта модельной оснастки уменьшаются до минимума.
Потребное количество стержневых автоматов LB50 определяем по формуле (1)
Таким образом принимаем четыре пескострельных автомата типа LB50.
Техническая характеристика данного автомата приведена в таблице 2.32.
Потребное количество стержневых автоматов типа LL5 также определяем по формуле ( 1 ):
Таким образом принимаем два пескострельных автомата типа LL5.
Максимальный вакуум атм
Максимальная ширина ящиков мм
Максимальная высота ящиков мм
Максимальная глубина ящиков мм
Среднее машинное время с
Время замены ящиков мин
Максимальное количество стержней в ящике шт
Максимальный вес ящика кг
Быстрота действия вакуумного насоса м3ч
Общий вес установки кг
В комплект поставки скруббера входит:
массообменная колонна;
устройство автоматической дозировки реагентов;
емкость для кислоты;
фильтр для устранения твердых фракций;
Техническая характеристика скруббера для очистки воздуха приведена в таблице 2.34.
Несмотря на ощутимые и неоспоримые преимущества способ изготовления стержней на основе ХТС имеет весьма существенные недостатки. При изготовлении стержней выделяется значительное количество токсичных веществ.
Эту проблему в проектируемом цехе решаем при помощи скруббера для очистки воздуха.
Производительность м3ч
Рабочая температура воздуха °С
Максимальная концентрация амина мгм3:
11 Участок регенерации отработанных смесей.
С целью сокращения расхожа формовочных материалов отработанные смеси после разрушения подвергают регенерации.
Регенерация – обработка использованной смеси с целью возврата песков в производство повторное применение которых не должно снижать качества смеси.
При регенерации отработанных смесей содержащих связующие материалы органического и неорганического происхождения восстанавливается лишь их огнеупорная основа. Конечным продуктом регенерации в этом случае является формовочный песок (регенерат) используемый в качестве заменителя свежего песка при изготовлении формовочных и стержневых смесей.
Регенерации подвергаются отработанные смеси с участков выбивки стержней а также отвальные смеси из различных точек литейного цеха. К числу основных операций процесса регенерации отработанных смесей относят: дробление комьев смеси отделение металлических включений отсев спекшихся комочков смеси отделение инертных наслоений с поверхности зерен песка удаление пылеобразных веществ.
Применение регенерированного песка в приготовлении стержней методом ХТС дает возможность заменить до 95% свежего песка регенератом и уменьшить ввод связующего. Простота процесса регенерации и компактность оборудования при вели к широкому распространению установок механической регенерации LKZ-15 ф. Lampe
После регенерации песок с помощью системы пневмотранспорта подается в бункер для стержневой смеси над смесителями.
12 Участок выбивки стержней.
Во избежание механических повреждений каждый вид отливок выбивается согласно технологии.
С заливочного участка отливки изготавливаемые с применением стержней подаются на участок выбивки подвесным толкающим конвейером. Выбивные комплексы отгорожены от остального цеха для уменьшения воздействия шума на работающих в других отделениях.
Выбивка стержней производится на выбивных комплексах «Fill» Австрия.
Комплекс предназначен для выбивки стержней отливок из алюминиевых сплавов массой до 90 кг.
свингмастер (наклонная выбивная решетка с изменяющейся амплитудой колебания)
маятниковые станции ( две штуки)
крепежное приспособление
электрошкаф с пультом управления
манипулятор для загрузки отливок (для крупных отливок)
Открывается защитное ограждение и при помощи манипулятора отливка загружается на рабочее приспособление свингмастера. Закрываются раздвижные дверки кабины. Производится выбивка отливок на свингмастере по заданной программе.
Затем отливка подается к маятниковой станции где продолжается выбивка молотками с измененной частотой колебания.
После цикла выбивки отливка манипулятором (или вручную) вынимается из кабины.
Песок просыпается в нижнюю часть и по направляющим отводится на ленточный транспортер.
Расчет количества выбивных станков производим по формулам (1 ) (2):
В результате принимаем шесть выбивных комплексов.
Техническая характеристика выбивного комплекса представлена в таблице 2.35.
Габаритные размеры мм
Рабочее давление гидросистемы МПа
Суммарная мощность двигателя кВт
Максимальный вес заготовок кг
Размер рабочего приспособления
Род тока переменный трехфазный частотой напряжение
13 Обрубное отделение
На участок обрубки литников и прибылей отливки поступают на подвесном толкающем конвейере.
Для удаления литниковой системы технологических припусков и зачистки по линии разъема отливок применяем роботизированные обрабатывающие центры.
Вышеуказанные центры применяют для отливок из алюминиевых сплавов весом до 30 кг с твердостью от 50-80 до 120 НВ.
Обрабатывающий центр состоит из:
робот – установщик (у LCC-120)
поворотный портал со съемными приспособлениями
обрабатывающий робот
инструментальный шкаф
система уборки литников и стружки
шаговые накопительные устройства (для LCC-120)
Работа обрабатывающего центра.
Установленная отливка подается по накопительному устройству к позиции загрузки. Роботом-загрузчиком отливка устанавливается на рабочее приспособление и при помощи гидравлических зажимов производится фиксация отливки в приспособлении (на приспособлении имеется «метка» для распознавания заготовки и в зависимости от этого запускается нужная программа обработки).
Портал поворачивается на 900 и заготовка подается в зону обработки. Обрабатывающий робот согласно заданной программы инструмента обрабатывает заготовку. Удаленные литники по подземной системе подаются на склад возврата.
Портал возвращается в исходное положение робот-загрузчик вынимает отливку из рабочего приспособления и устанавливает на шаговый накопитель. Отливки подаются к месту разгрузки.
Для обрезки литников и прибылей отливок номер 11 12 13 18 19 (таблица 2.1.) принимаем механизированную линию LCC 120
Потребное количество механизированных линий LCC 120 определяем по формулам (1) (2)
Таким образом принимаем четыре механизированных линий LCC 120.
Техническая характеристика механизированных линий LCC 120 приведена в таблице 2.36.
Min расход воздуха при min давлении 06 Мпа м3час
Манипулятор. усилие на руку кг
Кол-во манипуляторов
Для обрезки литников и прибылей отливок номер 1 2 4 5 (таблица 2.1.) принимаем механизированную линию LCC 350
Потребное количество механизированных линий LCC 350 определяем по формулам (1) (2)
Таким образом принимаем две механизированные линии LCC 350.
Техническая характеристика механизированных линий LCC 350 приведена в таблице 2.37.
Для обрезки литников и прибылей отливок номер 3 6 7 8 9 10 14 15 16 17 (таблица 2.1.) принимаем механизированную линию LCC 420
Потребное количество механизированных линий LCC 420 определяем по формулам (1) (2)
Таким образом принимаем одну механизированную линию LCC 420.
Техническая характеристика механизированных линий LCC 420 приведена в таблице 2.38.
14 Участок термической обработки
Термическая обработка литых деталей из алюминиевых сплавов способствует их значительному упрочнению в ряде случаев улучшению обрабатываемости резанием повышению коррозионной стойкости и т.д. [12 стр. 156].
Отливки из алюминиевого сплава АК9ч проходят термическую обработку по режиму Т6: закалка и искусственное старение (максимальное упрочнение). Назначение режима в получении максимальной прочности за счет некоторого снижения пластических свойств деталей. Искусственное старение осуществляется в условиях повышенных температур (175 – 185 °С) и продолжительной выдержки (5 часов и более). При старении происходит процесс распада твердого раствора обусловливающий высокое дисперсионное твердение.
Сочетание закалки с последующим искусственным старением обеспечивает получение наиболее высокой прочности деталей.
Детали подлежащие термической обработке должны быть рассортированы по сплавам и габаритным размерам (в нашем случае сплав один).
Параметры режима термообработки Т6 даны в таблице 2.39.
Отливки подвергаемые термообработке имеют высокие механические свойства. Высокая температура повышает растворимость упрочняющих компонентов в сплаве. Максимальный переход упрочняющих компонентов в твердый раствор дает необходимые прочностные характеристики. Закалка способствует равномерному распределению атомов легирующих элементов в кристаллической решетке твердого раствора.
Закалка отливок в проектируемом цехе производится в полуавтоматической горизонтальной толкательной печи модели ОКБ 2020. Печь имеет пять тепловых зон служащих для нагрева и выдержки деталей и закалочный бак для их охлаждения. Нагрев осуществляется постоянно циркулирующим горячим воздухом подогретым в калориферах. Заданная температура каждой зоны контролируется от индивидуальных термопар. Нагруженные два ряда поддонов с отливками проталкиваются последовательно через все зоны печи.
Температура нагрева °С
Охлаждаю-щая среда и температу-ра °С
Техническая характеристика термической печи ОКБ 2020 представлена в таблице 2.40.
Рабочая температура °С
Число тепловых зон шт
Производительность при рабочей температуре штч
Размеры рабочего пространства мм:
Расчет количества печей для проектируемого цеха ведем по формуле (1) (2):
В итоге принимаем пять закалочных печей типа ОКБ 2020 .
Старение производим в печах марки ОКБ 4023 которые предназначены для производства операции отпуска (старения) алюминиевых отливок в атмосфере нагретого воздуха. Основной несущей частью печи является каркас на который монтируется шахта. Внутри шахта разделена на два канала перегородкой. По одному каналу происходит подъем отливок на этажерках. В этот момент идет нагрев отливок до технологической температуры. По второму каналу этажерки с отливками опускаются вниз. Печь оборудована рециркулярной вентиляционной установкой с воздухоотводом.
Техническая характеристика термической печи искусственного старения ОКБ 4023 представлена в таблице 2.41.
Расчет ведем по формуле (1) (2):
Принимаем пять печей старения ОКБ 4023 .
Максимальная температура °С
Время термообработки ч
Производительность штч
Для придания отливкам товарного вида применяют очистку отливок дробью гидроабразивную вибрационную ультразвуковую химическую электрохимическую и другие виды обработки.
Наибольшее распространение нашла очистка отливок дробью. Для очистки дробью используют дробеструйные камеры периодического и непрерывного действия проходные дробеметные камеры в которых проводится очистка отливок подвешенных на подвесках с несколькими крюками вращающихся вокруг своей оси при движении через камеру и на них направляется поток дроби. Дробь может выбрасываться сжатым воздухом или лопатками вращающихся турбин. Последний способ выбрасывания дроби применяется чаще так как он примерно в 10 раз эффективнее дробеструйного а его энергоемкость также в 10 раз меньше.
Для обработки отливок в проектируемом цеха применяем проходные дробеметные камеры ф. «Schlik».
Расчет количества дробеметных камер для отливок номер 1 2 3 4 5 6 9 11 12 13 18 19 (таблица 2.1.) производим по формулам: (1) (2)
Принимаем три дробеметных камеры производительностью 220 отлч
Технические характеристики дробеструйной установки представлены в таблице 2.42.
Производительность кгмин
Мощность привода квт
Максимальная нагрузка кг
Максимальный вес детали кг
После термообработки отливки подвергаются проверке на твердость специальным прибором. Затем отправляются на склад готовой продукции который находится в непосредственной близости от участка термической обработки и зачистки деталей что позволяет без дополнительной транспортировки доставлять контейнерами продукцию на склад. Со склада отливки вывозятся потребителю.
15 Контроль отливок.
15.1 Контроль химического состава.
В цеховой лаборатории проверку химического состава сплава производят методом спектрального анализа. Химическому анализу подвергаются составные части шихты сплава расплавы всех плавок. Проверяют основные элементы сплава и количество вредных примесей.
Спектральный анализ основан на рассмотрении спектра излучения при воздействии дугового разряда на поверхность материала. По спектру определяют качественный и количественный состав сплава.
15.2 Контроль исполнителем при заливке.
Заливщик в процессе работы производит контроль качества внешнего вида отливок согласно установленным требованиям. Не допускаются: неспаи трещины раковины рыхлоты утяжины. Наружная и внутренние поверхности отливок должны быть чистыми без включений.
15.3 Контроль исполнителем после обрубки.
Обрубщик производит визуальный контроль отливок на соответствие требований технической документации. Не допускаются сколы зарезы отпечатки от прижимов и упоров в теле отливки.
15.4 Контроль геометрии отливок.
Контроль линейных размеров отливок производится:
при сдаче новой оснастки;
после ремонта и доводки действующей оснастки;
контроль один раз в неделю с каждой работающей формы.
15.5 Приемочный контроль по внешнему виду.
На контрольный пост ОТК предъявляются партии отливок с маршрутной картой. Контроллер ОТК проверяет визуально внешний вид отливок на выявление дефектов литья согласно требованиям чертежа отливки.
16 Вспомогательные службы проектируемого цеха.
В проектируемом цехе предусмотрены следующие вспомогательные службы:
участок ремонта индукторов;
участок ремонта тиглей и ковшей;
участок ремонта и обслуживания кокильной оснастки;
участок ремонта и обслуживания пресс-форм;
участок ремонта погрузчиков;
производственно-диспетчерская служба;
лаборатории (химико-спектральная механических испытаний формовочных материалов ЦЛЛ);
пирометрический пункт;
зарядная аккумуляторов для электропогрузчиков.
В ремонтных мастерских служб механика энергетика и ШИХ ведутся следующие работы:
периодический осмотр и наладка оборудования;
замена режущего инструмента.
текущий и средний ремонты оборудования;
частичное изготовление запчастей к оборудованию;
ремонт вентиляции и промразводок.
Технологическая часть.
1 Анализ технологичности конструкции детали.
Исходными данными при проектировании технологического процесса изготовления отливки являются программа ее выпуска чертеж детали технические условия обусловливающие требования к ее качеству.
Проектирование технологического процесса начинают с анализа технологичности конструкции детали возможности и целесообразности ее изготовления тем или иным способом литья. Анализ технологичности конструкции детали включает сравнение различных способов изготовления: литьем сваркой штамповкой механической обработкой и т.д. и заключается в установлении ее соответствия требованиям литейной технологии с учетом последующей технологии обработки резанием и сборки.
Деталь отвечает следующим требованиям по технологичности:
деталь имеет компактную конфигурацию и сравнительно небольшие габариты;
стенкам детали приданы равномерные сечения во избежание образования усадочных раковин и других дефектов.
Минимально возможная толщина стенок отливок зависит от свойств заливаемого сплава температуры заливки размеров и конструкции отливки а также от температуры и состояния поверхности формы. Правильно выбранная толщина стенки обеспечивает расчетную прочность герметичность и другие
Деталь 514.1008118 «Ресивер» имеет компактную конфигурацию и габаритные размеры 220х270х90 мм массу 149 килограмма. Стенкам детали приданы равномерные сечения во избежание образования усадочных раковин и других дефектов. Преобладающая толщина стенки детали 4 мм. Деталь «Ресивер» относится к пятой группе сложности.
Учитывая большую производственную программу – 35000в год необходимость выполнения внутренней конфигурации отливки песчаным стержнем выбираем в качестве метода литья – литье в кокиль. Этот способ наиболее прост технологически и экономически выгоден и рентабелен. Литье в кокиль обеспечит высокую производительность и точность размеров.
2.Выбор положения отливки в форме.
Исходя из выбранного метода литья и конструкции детали имеющей поднутрения выполнить которые возможно только песчаным стержнем в качестве способа заливки отливки 514.1008118 «Ресивер» выбирается литье в кокиль на кокильной машине мод.14МС.
Внутренняя полость образуется стержнем и в связи с этим к полости предъявляют следующие требования:
Полости отливки должны допускать удаление стержня без особых затруднений.
Полости отливки должны иметь выходные отверстия обеспечивающие свободный выход газов образующихся при заливке.
Для предупреждения дефектов таких как: усадочные раковины горячие трещины в горячих узлах необходимо установить прибыли которые бы в достаточной мере обеспечили бы подпитку горячих узлов.
Положение отливки в форме определяет конструкцию (тип) литниковой системы размещение на отливке прибылей и промывников.
При выборе положения отливки в форме необходимо учитывать:
Возможность направленного удаления воздуха и газов из формы при заполнении ее сплавом:
Удобство размещения литниковой системы при кратчайшем пути прохождения металла до отливки;
Расположение в одной полуформе поверхностей отливки являющихся базами для изготовления и контроля отливки и обработки резанием.
Выполнять литниковую систему в соответствии с принципом последовательного затвердевания.
Положение отливки в форме и разъем формы должны обеспечивать высокое качество отливки минимальные затраты на ее изготовление и на механическую обработку минимальный расход металла и возможность применения механизации и автоматизации технологического процесса.
В нашем случае отливка располагается вертикально.
При решении вопроса о количестве отливок в форме необходимо брать во внимание конструкцию отливки (вес отливки ее геометрические размеры степень сложности) характер производства тип оборудования показатель металлоемкости формы и экономическую целесообразность принятого решения.
Деталь имеет средние габариты и массу поэтому в данном случае отливка в форме одна.
Разъем кокиля вертикальный. При этом учитывается расположение отливки в форме. На чертеже поверхность разъема обозначается в соответствии с ГОСТ 3.1125-88.
Для лучшего извлечения отливки из кокиля применяем выталкиватели.
Для выхода газов и воздуха из формы применяем вентиляционные пробки.
3 Выбор плоскости разъема формы
Оптимальный вариант разъема формы должен способствовать:
повышению геометрической точности отливки и в целом ее качества;
уменьшению вероятности образования дефектов;
снижению себестоимости отливки;
минимальному количеству стержней.
Поэтому при выборе поверхности разъема формы нужно стремиться к тому чтобы форма состояла из минимального количества частей. Желательно располагать всю отливку в одной полуформе число плоскостей разъема должно быть минимальным; при этом необходимо избегать сложных криволинейных разъемов.
Для отливки “РЕСИВЕР” предпочтительней является горизонтальная поверхность разъема формы при заливке. Выбираем плоскость разъема вертикальной. При этом обеспечивается:
-минимальное количество стержней;
-условие направленного затвердевания отливки;
-снижается вероятность образования различных дефектов.
Выбор разъема стержневого ящика
Для получения внутренней поверхности отливки применяются песчаные стержни. В данном случае выбираем для изготовления автомат изготовления стержней методом ХТС мод.LB50. Так как габариты песчаного стержня составляют 220х280х125мм а программа производства 45000отливок возможно применить многогнездный стержневой ящик и расположить в стержневом ящике 4 стержня
Для обеспечения удаления стержня из стержневого ящика совпадения литейных уклонов отливки и стержня выбираем разъем ящика – горизонтальный.
4 Расчет литниковой системы.
Литниковая система - система каналов и устройств для подвода в определенном режиме жидкого металла в полость литейной формы отделения неметаллических включений и обеспечения питания отливки при затвердевании. Литниковую систему размещают по разъему литейной формы и вне разъема.
Правильная конструкция литниковой системы должна обеспечивать непрерывную подачу расплава в форму по кратчайшему пути; спокойное и плавное ее заполнение; улавливание шлака и других неметаллических включений; создание направленного затвердевания отливки; минимальный расход металла на литниковую систему; не вызывать местных разрушений формы вследствие большой скорости и неправильного направления потока металла.
При выборе конструкции литниковой системы необходимо учитывать сплав размеры отливки толщины ее стенок и конструктивные особенности.
Рассчитать литниковую систему – это значит установить соотношения между всеми ее элементами и определить их сечения. Расчет делают приближенно так как явления имеющие место в форме при заливке многообразны и поэтому практически не удается учесть все факторы влияющие на заполнение формы жидким металлом. Существующие методы расчета литниковых систем основаны на законах гидравлики с использованием данных полученных опытным путем.
Литниковая система состоит из питателя и прибыли.
В нашем случае выбираем литниковую систему с заливкой расплава сверху.
Выбрав тип литниковой системы и место подвода металла к отливке рассчитываем площадь поперечного сечения и определяем размеры элементов:
Расчет элементов литниковой системы ведется из следующего соотношения суммарных площадей поперечных сечений стояков коллекторов и питателей: При литье алюминиевых сплавов в кокиль применяют расширяющуюся литниковую систему т. е.:
Продолжительность заливки можно определить по формуле Дубицкого:
где d - отношение периметра опасного сечения отливки к ее площади мм;
S – коэффициент зависящий от конфигурации отливки S= 24 – для отливок из алюминиевых сплавов массой от 2 до 5 кг.
Средний металлостатический напор определим по формуле Дитертта:
=330 мм. (поскольку заливка производится в прибыль)
где Hо – напор металла над питателями;
Р – высота отливки (включая прибыль) от места подвода металла до верхней части ;
Так как в данном случае заливка отливок производится сверху :
Так как в данном случае отливка заливается через прибыль основание прибыли имеет размер 66х84 мм принимаем его за размеры питателя
Fпит = (6.6*84)-r2= 469 см2
Для питания верхней части отливки как наиболее массивной принимаем открытую прибыль прямого действия округлого сечения.
Существует упрощенный метод расчета прибылей. Такой метод основан на следующих положениях:
для обычных отливок изменение массы узла питания в довольно широких пределах мало влияет на высоту прибыли;
высота прибыли мало возрастает с увеличением высоты отливки.
Так для легких сплавов при малой высоте отливки отношение высоты прибыли к высоте отливки без прибылей
Для отливки 514-1008118 «Ресивер» высотой 220 мм принимаем высоту прибыли -120мм габариты прибыли – 115 х 95 мм.
Проверяем принятую прибыль расчетом. Расчет прибылей проводится по методу Пржибыла ( для алюминиевого литья и для малого развеса отливок).
Для расчета необходимо знать:
Объем горячего узла – в данном случае горячим узлом является вся отливка (масса узла 15 кг объем 0000681 м3).
Безразмерные коэффициенты – для алюминиевого сплава (характеризуют усадку металла).
Принятая прибыль имеет массу 25 кг а расчетная масса прибыли примерно 1 кг. Условие выполняется.
5 Выбор режима заливки и охлаждение отливки.
Для обеспечения хорошей заполняемости формы и получения качественных отливок необходимо выдерживать определенную температуру заливаемого расплава которую выбирают в зависимости от вида сплава и характера отливки.
Для алюминиевых отливок со стенками толщиной 4-6 мм температура расплава: при выпуске из печи 750 о С при заливке форм 690-710О С.
Для заливки отливок выбираем ручной ковш емкостью 5 кг так как масса заливаемого металла 42 кг.
Регламентирование времени охлаждения отливок в формах диктуется необходимостью обеспечения полного затвердевания расплава исключения образования некоторых усадочных дефектов получения требуемой структуры металла отливок.
Время охлаждения отливки в форме определяется по формуле:
t1 – время отвода теплоты перегрева Т зал. Т ликв.
t2 – время отвода скрытой теплоты кристаллизации Т лик. Т сол.
t3 – время охлаждения Т сол. Т выб.
где G- металлоемкость формы
коэффициент теплоотдачи
F – площадь поверхности отливки
Тн – средняя температура кокиля
Тп- температура отливки в момент ее извлечения
= 2406+4387+13888=20682 с.
6 Специфические виды брака для отливки «Ресивер»
Специфические виды брака при производстве отливки «Ресивер» даны в таблице 3.1.
Газовая раковина газовая пористость
Повышенное содержание водорода не до конца проведена дегазация. Захват воздуха при заливке.
Заменить способ дегазации. Понизить скорость заливки. Применение смазок уменьшающих выделение газов.
Турбулентное поступление металла в форму. Прерывание струи металла при заливке.
Применение чистых материалов. Изменение литниковой системы.
Малая скорость заполнения формы расплавом. Низкая температура заливки. Недостаточный нагрев формы.
Повысить температуру металла или кокиля.
Недостаточное питание жидким металлом.
Организация направленного затвердевания.
Несовершенства литниковой системы. неравномерная заливка металлом.
Не допускать разрыва струи металла. Усовершенствовать технологию.
Ранняя выбивка. Высокая температура заливки
Соблюдение технологии. Снизить температуру заливки.
Заключение.doc
В спроектированном цехе используются автоматизированные комплексы литья под давлением карусельно-кокильные машины с механическими заливщиками автоматизированные обрубные и выбивные комплексы что снижает трудоемкость работы заливщиков и обрубщиков численность рабочих повышает культуру производства.
Применение прогрессивных технологий исключает необходимость использования формальдегидных смол это удешевляет процесс получения отливок снижает трудоемкость работы позволяет экономить металл делает производство экологически чистым.
Внедрение новых технологий способствует снижению брака в отливках улучшению их механических свойств.
В спроектированном цехе для транспортировки отливок и возврата применяются подвесные конвейеры и ленточные транспортеры что приводит к снижению аварийных ситуаций из-за повышенной загруженности проездов для электрокар и автотранспорта уменьшению использованных площадей.
Планир цеха 2.dwg

ДП-НГТУ-110400-(ЛП-1104)-11-2005
Участок регенерации
Центральная литейная лаб.
Стоянка и подзарядка
Службы механика и энергетика
Участок ремонта оснастки
Разрез цеха1.dwg

грунт уплотненный щебнем
бетонная подготовка 15см
железобетонная ферма L=18м
железобетонная плита (12х3х0.45)
пароизоляция 1сл. пергамина
утеплитель j=400кгм3 14см
цементная стяжка 3см
-х слойный рубероидный ковер
ДП-НГТУ-110400-(ЛП-1104)-12-2005
бетонная подготовка 12см
ДП-НГТУ-110400-(ЛП-1104)-11-2005
Рекомендуемые чертежи
- 09.06.2018
Свободное скачивание на сегодня
Другие проекты
- 30.08.2014