Очистка коксового газа от сероводорода вакуум-карбонатным методом с получением серной кислоты


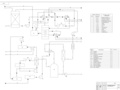
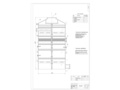
- Добавлен: 25.01.2023
- Размер: 952 KB
- Закачек: 0
Узнать, как скачать этот материал
Подписаться на ежедневные обновления каталога:
Описание
Очистка коксового газа от сероводорода вакуум-карбонатным методом с получением серной кислоты
Состав проекта
![]() |
![]() |
![]() |
![]() ![]() ![]() ![]() |
![]() ![]() ![]() |
![]() ![]() ![]() ![]() |
Дополнительная информация
Контент чертежей
Технол.сх.dwg

Конденсатор-холодильник
Подогреватель паровой
Условное обозначение
Наименование среды в
Исходный коксовый газ
Очищенный коксовый газ
Регенерированный раствор
Вакуум-карбонатный метод очистки коксового газа от сероводорода с получением серной кислоты. Технологическая схема
Курсовая.docx
Федеральное государственное бюджетное образовательное учреждение высшего образования
«Кузбасский государственный технический университет
имени Т.Ф. Горбачёва»
Кафедра химической технологии твёрдого топлива
РАСЧЁТНО-ПОЯСНИТЕЛЬНАЯ ЗАПИСКА
к курсовой работе по дисциплине «Общая химическая технология»
на тему «Расчет и обоснование технологической схемы очистки коксового газа от сероводорода вакуум-карбонатным методом с получением серной
гр. ХТб-131 Андреева Т. А.
Технико-экономическое обоснование выбора вакуум-карбонатного метода очистки коксового газа от сероводорода с получением серной кислоты5
1 Вакуум-карбонатные методы очистки коксового газа5
2 Аммиачный метод очистки коксового газа7
3 Моноэтаноламиновый метод очистки коксового газа от сероводорода ..12
Физико-химические основы вакуум-карбонатного метода очистки коксового газа от сероводорода16
Технологическая схема очистки коксового газа от сероводорода вакуум-карбонатным методом с получением серной кислоты21
1 Материальный баланс контактного окисления сернистого ангидрида29
2 Тепловой баланс контактного окисления сернистого ангидрида32
Очистка коксового газа занимает важное место в коксохимическом производстве т. к. очевидна целесообразность использования в качестве товарного продукта больших количеств серы содержащейся в виде сероводорода в газе. Кроме того выделение сероводорода из коксового газа применяющегося в металлургии позволяет сократить продолжительность плавки в мартеновских печах и улучшить качество стали уменьшив содержание серы в металле. Также коксовый газ применяется в химических синтезах – преимущественно для синтеза аммиака. Такой газ должен быть совершенно свободен от сероводорода т. к. последний является ядом отравляющим катализаторы.
В самом технологическом процессе коксохимического производства сероводород также очень нежелательная примесь газа т. к. вызывает ухудшение качества поглотительного масла коррозию аппаратуры и т. д. [1].
В 1 м3 прямого коксового газа при нормальных условиях содержится в среднем 5-25 г сероводорода 80-120 г смолы 7-10 г аммиака 20-45 г бензольных углеводородов и др. [2]. Содержание сероводорода в газе зависит от сернистости коксуемой шихты; в сероводород переходит 25-30 % от всей серы угля. На заводах коксующих кузнецкие угли содержание сероводорода не превышает 3-4 гм3 на заводах перерабатывающих угли Донецкого бассейна оно достигает 20-25 гм3 [1].
В среднем на 1% серы в исходном угле образуется 360-420 мгм3 органически связанной серы в коксовом газе. На долю сероводорода приходится около 95% от всего количества серы содержащейся в коксовом газе остальные 5% - органические сернистые соединения [3].
Громадные ресурсы серы и значительная стоимость последней делают целесообразным сочетание процесса очистки газа от сероводорода с процессом его утилизации т. е. с получением его в виде серы и серной кислоты.
Серная кислота извлекает из коксового газа аммиак в виде сульфата аммония который используется как минеральное удобрение в сельском хозяйстве.
Коксохимическая промышленность заинтересована в получении серной кислоты из собственного сырья т. к. является значительным ее потребителем. Проблема получения собственной серной кислоты очень важна т. к. в калькуляции производства сульфата аммония стоимость кислоты (в зависимости от дальности ее транспортирования) составляет 40-60 % [1].
При использовании коксового газа для обогрева коксовых печей и в других потребляющих установках коксохимического предприятия глубина очистки регламентируется технологическими нормативами на выброс диоксида серы образующегося в результате сжигания серосодержащих компонентов газа.
Ниже представлены требования к очистке коксового газа от сероводорода [3]:
В газе для металлургических целей мгм3
В очищенном газе для целей синтеза мгм3
При использовании коксового газа для коммунально-бытового потребления мгм3
При вдувании коксового газа в доменные печи мгм3
Содержание органической серы в бытовом газе (не более) мгм3
Технико-экономическое обоснование выбора вакуум-карбонатного
метода очистки коксового газа от сероводорода с
получением серной кислоты
В настоящее время существует ряд методов очистки газа от сероводорода которые отличаются друг от друга применяемыми поглотителями и тем в виде какого продукта извлекают серу.
В мире существует более 15 вариантов технологий очистки коксового газа от сероводорода. При этом промышленный интерес представляют круговые абсорбционно-десорбционные и жидкостные окислительные процессы. Среди действующих сероочисток преобладают круговые: вакуум-карбонатные (содовые поташные) аммиачные (метод комплексной очистки фирмы «Штиль» ФРГ) и аминовые (очистка газа водным раствором моноэтаноламина) способы очистки газа [4].
1 Вакуум-карбонатные методы очистки коксового газа
Среди способов мокрой очистки газа от сероводорода основное место занимают обратимые круговые процессы отличительной способностью которых является выделение из поглотителя сероводорода в неизменном концентрированном виде что дает возможность его последующей переработки в серную кислоту. Эти способы основаны на обратимости реакции поглощения сероводорода циркулирующим в замкнутом цикле поглотителем и выделении сероводорода из поглотителя при изменении условий. Поглотитель обычно представляет собой слабощелочной реагент что облегчает улавливание сероводорода и не препятствует его выделению при регенерации.
В качестве поглотителей применяются растворы аммиака углекислых солей натрия и калия фенолята натрия фосфорнокислого калия и органические поглотители – аминоспирты и соли аминокислот. Из всех поглотителей
наибольшее распространение получили углекислые растворы натрия и калия что объясняется их доступностью относительной дешевизной и отсутствием корродирующего действия на аппаратуру.
Любая обессеривающая установка работающая по круговому процессу включает в себя два основных аппарата: абсорбер (скруббер) в котором газ промывается раствором улавливающим сероводород и регенератор в котором происходит выделение поглощенных веществ и восстановление поглотительных свойств раствора.
Вакуум-карбонатные методы основаны на обратимости реакции:
Ме2СО3 + Н2S = MeHCO3 + MeHS.
При улавливании реакция идет слева направо при регенерации насыщенного поглотительного раствора (при нагреве) – справа налево; при этом сероводород выделяется в концентрированном виде а двууглекислая соль переходит в углекислую т. е. раствор восстанавливает свои поглотительные свойства [1].
Технологическая схема очистки коксового (рис.1) газа от сероводорода вакуум-карбонатным методом заключается в следующем [3]. Подлежащий очистке от сероводорода коксовый газ поступает в скруббер заполненный хордовой насадкой орошаемой раствором соды или поташа.
Насыщенный сероводородом поглотительный раствор насосом подается в конденсатор-холодильник где он подогревается за счет тепла конденсации паров выделяющихся при регенерации поглотительного раствора. Затем раствор поступает в теплообменник в паровой подогреватель и в регенератор представляющий собой тарельчатую колонну с циркуляционным подогревателем. Регенерированный раствор из регенератора попадает в сборники откуда насосом подается через теплообменник и холодильник на верх скруббера для улавливания сероводорода.
Выделяющиеся из регенератора пары отсасываются вакуум-насосом и поступают в холодильник а затем в печь для сжигания сероводорода с получением сернистого ангидрида [1].
Рисунок 1. Принципиальная схема очистки коксового газа от сероводорода по вакуум-карбонатному методу
– скрубберы; 2 3 8 18 – насосы; 4 – конденсаторы-холодильники с пародистиллятными теплообменниками; 5 14 – оросительный и газовый холодильники; 6 – теплообменник; 7 16 – сборники; 9 – подогреватель; 10 – регенератор; 11 13 – отбойники; 12 – вакуум-насос; 15 – предохранительный газовый затвор; 17 – бак для приготовления свежего раствора; 19 – циркуляционный подогреватель
Вакуум-карбонатный способ характеризуется простотой аппаратурного оформления и эксплуатации сравнительной дешевизной поглотителя. Фирма «Крупп-Копиерс» на заводах ФРГ и других стран также применяет этот процесс. К недостаткам процесса относятся его энергоемкость дефицит содопродуктов и несовершенство мокрого катализа [4].
2 Аммиачный метод очистки коксового газа
Принципиальная схема очистки коксового газа от сероводорода аммиачным методом не отличается от привычной схемы абсорбционного-десорбционного метода: сероводородный абсорбер – теплообменники – регенератор (раскислитель).
Аммиачный метод очистки разработанный ВУХИН сочетается с фосфатным методом извлечения аммиака из коксового газа или бессатураторным способом получения сульфата аммония. Коксовый газ охлаждают до температуры не выше 33-35 С в массотеплообменных аппаратах непосредственного действия например в скрубберах Вентури. Подготовленный коксовый газ поступает в сероводородный абсорбер где в результате контакта газа с поглотительным аммиачным раствором и парами аммиака происходит извлечение сероводорода и частично цианистого водорода.
После извлечения H2S и HCN коксовый газ направляют в аммиачный абсорбер для улавливания из него аммиака фосфатным методом или в абсорбер бессатураторного процесса производства сульфата аммония.
Регенерацию поглотительного раствора проводят путем десорбции поглощенных из коксового газа газообразных веществ. Из поглотительного раствора в процессе регенерации удаляются до 90% содержащегося в нем H2S 45-50 % HCN около 50 % CO2 и небольшая доля NH3. Перед подачей поглотительного раствора в регенератор часть раствора (около 80%) пропускают через теплообменники где раствор нагревается за счет тепла обратного потока регенерированного раствора. Остальную часть раствора (около 20%) подают непосредственно в регенератор минуя теплообменники. Регенерированный раствор после охлаждения в теплообменниках и холодильниках до 33 С возвращается на орошение абсорбера сероцианоочистки. Для поддержания требуемой концентрации аммиака в циркулирующем поглотительном растворе в испарительную часть регенератора подают парогазовую смесь содержащую аммиак полученную на установке улавливания аммиака из коксового газа. Для предотвращения накопления в циркулирующем растворе роданидов и поддержания водного баланса в системе часть регенерированного раствора непрерывно выводят из цикла в совместную переработку с надсмольной водой на аммиачной колонне.
Очистку сероводородного газа от аммиака производят в отдельном абсорбере раствором моноаммонийфосфата или маточным раствором сульфата аммония. Образовавшийся раствор диаммонийфосфата передают в абсорбер предназначенный для улавливания аммиака из коксового газа или насыщенный аммиаком раствор возвращают в сульфатное отделение. Для поддержания температуры в абсорбере на уровне 35 С часть раствора непрерывно отбирают с нижней части аппарата пропускают через систему холодильников и возвращают в абсорбер. Освобожденный от аммиака сероводородный газ поступает на дальнейшую переработку для получения из него товарной продукции. В условиях обычных температур охлаждающей воды при содержании аммиака в циркуляционном растворе 15 гл очистка коксового газа от серы осуществляется до 07-105 гм3. Для обеспечения содержания аммиака в поглотительном растворе 25 гл используют захоложенную воду.
Принципиальная технологическая схема узла абсорбции аммиака и сероводорода из поглотительного раствора аммиачной сероочистки по технологии «Аммосульф» приведена на «рис.2» [3] узла регенерации поглотительного раствора – на «рис.3» [3].
Рисунок 2. Принципиальная схема узла абсорбции аммиака и сероводорода из коксового газа
– сероводородный скруббер; 2 – аммиачный скруббер; 3 – холодильник; 4 – насос.
Технологические потоки: I – прямой коксовый газ; II – обратный коксовый газ; III – отдутая вода после колонны отгонки летучего аммиака; IV – раскисленная вода; V – насыщенная вода после сероводородного скруббера; VI – щелочь в узле щелочной промывки коксового газа; VII – раствор из щелочной промывки коксового газа в колонну для отгонки связанного аммиака
Основные реакции которые протекают в системе содержащей NH3 H2S CO2 H2O приведены ниже:
NH3(газ) + H2S(газ) = (NH4)2S(водн)
NH3(газ) + H2S(газ) = NH4HS(водн)
NH3(газ) + CO2(газ) + H2O(ж) = (NH4)2CO3(водн)
NH3(газ) + CO2(газ) = NH4CO2NH2(водн)
Рисунок 3. Принципиальная технологическая схема узла регенерации поглотительного раствора сероцианоочистки
– раскислитель; 2 – колонна отгонки связанного аммиака; 3 – колонна отгонки летучего аммиака; 4 – насосы; 5 – теплообменники; 6 – холодильники.
Технологические потоки: I – насыщенная вода из сероводородного скруббера; II – раскисленная вода в сероводородный скруббер; III – отогнанная вода на биохимические установки; IV – отдутая вода в аммиачный скруббер; V – аммиачные пары на каталитическое разложение или в газопровод «хвостовых газов»; VI – кислый газ в узел получения серы или в газопровод «хвостовых газов»
Для эффективного извлечения сероводорода из газа аммиачная вода подаваемая в абсорбер сероводорода должна содержать не только незначительные количества H2S но и минимальное количество углекислоты.
Практическое значение аммиачный метод получил после разработки процесса и аппаратуры для селективного улавливания сероводорода при ограниченном времени контакта между газом и жидкостью. Если требуется максимально достигнуть селективности улавливания NH3 и H2S то применяется разбрызгивающая колонна с относительно коротким временем контакта.
Процесс выделения кислых компонентов из аммиачной воды называют раскислением. При температурах выше 65 С содержащиеся в аммиачной воде соединения углекислого аммония и сульфида аммония полностью диссоциируют. Выделяющиеся газы (NH3 CO2 и H2S) в соответствии с их растворимостью либо остаются в растворе либо отгоняются. Малорастворимые соединения (CO2 и H2S) отгоняются в горячей области колонны значительно сильнее аммиака в холодной области колонны они снова растворяются в воде в соответствии с их растворимостью и константой диссоциации. В верхней холодной области колонны аммиаком связывается преимущественно CO2 т. к. угольная кислота сильнее сероводородной. Если поддерживать температуру паров на выходе из раскислительной колонны на уровне температуры окружающей среды то с определенными потерями аммиака можно добиться отгонки большей части CO2 и H2S.
Повышение степени очистки газа от сероводорода в круговом аммиачном методе со снижением удельного расхода раствора и сокращением расхода пара может быть обеспечено снижением температуры абсорбции повышением селективности извлечения H2S и улучшением регенерации поглотительного раствора.
Аммиачный метод сероочистки коксового газа может применяться в начале газового тракта а образовавшиеся побочные продукты не отличаются от традиционных компонентов в избыточных аммиачных водах и могут быть переработаны совместно [3].
Данный метод очистки коксового газа от сероводорода имеет следующие недостатки: сложность процесса высокие энергетические затраты на охлаждение пароаммиачной смеси и поглотительного раствора высокая коррозионная активность аммиачных паров низкая селективность извлечения сероводорода [5].
3 Моноэтаноламиновый метод очистки коксового газа от
Моноэтаноламин (МЭА) – (C2H7NO или HO-CH2-CH2-NH2) – бесцветная вязкая гигроскопическая жидкость является более сильной щелочью чем аммиак. Ее водный раствор применяется в качестве эффективного поглотителя сероводорода и диоксида углерода. К преимуществам данного поглотителя относятся высокая растворимость при умеренных концентрациях раствора высокая сероемкость по сравнению с содовыми поглотителями способность к отгонке от загрязнителей высокая щелочность. Ограничивает применение МЭА высокая стоимость значительные потери амина коррозия загрязнение аппаратуры вспенивание.
Образование пен в химических аппаратах приносит значительные неприятности. Иногда вследствие образования пены большое количество агрессивной жидкости «выбегает» из аппарата. Это приводит к потерям ценных материалов а иногда к разрушению фундаментов и коммуникаций [6].
Принципиальная технологическая схема аминовой очистки 25-н раствором приведена на «рис.4» [3].
Абсорбция углекислого газа и сероводорода приводится при температуре 25-40 С в аппаратах насадочного или тарельчатого типа при атмосферном или повышенном давлении (15-25 МПа и выше) в зависимости от схемы переработки газа.
Регенерация растворов МЭА проводится при температуре 105-135 С и соответствующем давлении продувкой паром образующимся при кипении растворов в нижней части колонны насадочного или тарельчатого типа. Углекислый газ удаляется из насыщенного раствора труднее чем сероводород поэтому для более полной его десорбции процесс регенерации должен проводиться под давлением до 03 МПа и соответственно при более высокой температуре. Расход пара при регенерации по практическим данным составляет от 55 до 130 кгм3 раствора.
Для протекания реакции поглощения сероводорода в оптимальном режиме температура раствора МЭА не должна быть больше 40 С. Рабочий раствор МЭА из нижней части абсорберов через гидрозатворы поступает в сборники насыщенного раствора откуда раствор МЭА по трубной части теплообменника подают в верхнюю часть отгонных колонн где раствор регенерируется до остаточного содержания в нем сероводорода менее 03 гл и углекислого газа менее 5-6 гл. Регенерированный раствор МЭА из нижней части отгонных колонн пройдя межтрубное пространство теплообменников поступает через холодильники на орошение абсорберов. Часть регенерируемого раствора (35-40 м3) выводится из цикла и подается в вакуум-кубы на разгонку. Выделившиеся пары МЭА и воды из вакуум-куба отсасываются в сборник дистиллята. Процесс вакуум-разгонки считается законченным при содержании МЭА в дистилляте более 5 гл. В кубе остаются натриевые соли – кубовые остатки которые утилизируются. Выделившиеся в результате десорбции кислые газы поступают в холодильники-конденсаторы а затем в сборник флегмы №1 где происходит отделение жидкой фазы от газообразной. Жидкая фаза (флегма) поступает в сборники насыщенного раствора а кислые газы – в холодильники-конденсаторы для дальнейшего их охлаждения а затем кислые газы отправляются в сборник флегмы №2. После отделения флегмы кислые газы из сборника флегмы направляются в коллектор кислых газов идущих на участок мокрого катализа для получения серной кислоты. Двухступенчатая схема охлаждения кислых газов позволяет снизить влагосодержание этих газов и повысить концентрацию производимой серной кислоты.
Разгонка раствора МЭА в присутствии щелочи проводится для снижения химических потерь МЭА и коррозии. Периодическую разгонку проводят в специальном аппарате – перегонном кубе. На разгонку поступает небольшая часть раствора чистый дистиллят содержит моноэтаноламин а в кубе накапливаются продукты побочных реакций. При взаимодействии со щелочью часть побочных продуктов разлагается с образованием свободного амина. Кроме того при разгонке раствора из системы выводятся механические примеси (шлам бой керамических колец).
Рисунок 4. Схема очистки коксового газа раствором МЭА
– насос-дозатор; 2 – адсорбер с плоскопараллельной насадкой; 3 – холодильники; 4 – теплообменники; 5 – регенератор; 6 – трубчатая печь; 7 – воздушный конденсатор; 8 – сепаратор газ-жидкость; 9 – емкость раствора щелочи; 10 – куб для моноэтаноламина; 11 – сборник дистиллированного раствора; 12 – сборник для нерегенерированного продукта; 13 14 – соответственно промежуточный сборник и сборник насыщенного раствора моноэтаноламина перед отгонкой; 15 – емкость свежего раствора моноэтаноламина; 16 – фильтры.
Технологические потоки: I III – соответственно исходный и очищенный газ; II – конденсат водяного пара (умягченная вода); IV – сероводородный газ для производства серной кислоты
Перегонные кубы большая часть оборудования и трубопроводов для аминовой сероочистки изготавливается из углеродистой и нержавеющей стали что позволяет использовать высокие концентрации амина при высоком содержании кислых компонентов в растворе и сильнее отогнать кислые газы из раствора [3].
Таким образом выбор вакуум-карбонатного способа очистки коксового газа от сероводорода обусловлен простотой аппаратурного оформления и эксплуатации сравнительной дешевизной и доступностью поглотителя отсутствием корродирующего действия поглотителя на аппаратуру. Также данный метод пригоден для очистки коксового газа при наличии в нем различных примесей (COS O2 HCN и др.) [7].
Физико-химические основы вакуум-карбонатного метода
очистки коксового газа от сероводорода
Вакуум-карбонатный метод основан на поглощении сероводорода из коксового газа в присутствии CO2 водными растворами натрия и калия по быстро протекающей в жидкой фазе обратимой реакции:
H2S + OH- = HS- + H2O. (1)
Химическая реакция абсорбированного CO2 с щелочным раствором проходит по пути гидратации растворенного CO2 с образованием угольной кислоты и ее дальнейшего взаимодействия с ионами гидроксила.
CO2 + H2O = H2CO3 (2)
H2CO3 + OH- = HCO3- + H2O. (3)
Лимитирующей стадией является реакция (2). Скорость реакций может быть увеличена повышением концентрации CO2 OH- или температуры.
При поглощении сероводорода растворами карбоната натрия или калия равновесие в системе H2S – Me2CO3 – MeHCO3 – MeHS – H2O определяется константой:
где pH2S – парциальное давление сероводорода мм рт. ст.
Равновесие в системе с учетом углекислого газа H2S – CO2 – Na2CO3 – NaHCO3 – NaHS – H2O определяется константой Кобщ:
С повышением температуры константа равновесия уменьшается селективность процесса абсорбции карбонатными растворами по отношению к сероводороду возрастает. Однако следует учитывать увеличение скорости реакции гидратации реакции (2) и (3) с повышением температуры:
Величина константы скорости реакции второго порядка может быть определена из уравнения:
где Т – температура К;
I – ионная сила раствора мольл.
В процессе абсорбции CO2 горячими поташными растворами при повышении температуры с 25 до 75 С скорость абсорбции CO2 резко увеличивается.
Повышение содержания углекислоты в очищаемом газе уменьшает сероемкость раствора (см. рис. 5 [3]). Для уменьшения количества поглощаемого из газа CO2 время контакта поглотительного раствора и газа в абсорбере свыше 30 с не рекомендуется.
Рисунок 5. Влияние СO2 на растворимость H2S в 2-н растворе карбонота калия при 25 С
– без CO2 в газе; 2 – 19% объемн. CO2 в газе
Процесс поглощения сероводорода углекислого газа и цианистого водорода в присутствии кислорода сопровождается побочными реакциями с образованием термически стабильных солей которые не регенерируются из щелочных растворов. Также в результате омыления цианидов образуются формиаты [3]. Протекающие при этом процессы следующие [8]:
HS- + 2О2 = S2О32- + Н2О;
CN- + Fe2+ = [Fe(CN)6]4-;
HCN+ 2Н2О = NH3+ HCOOH =
HCOONH4 + К2СО3 = 2НСООК + 2NH3 + СО2 + Н2О.
Суммарное содержание нерегенерируемых солей в поглотительном содовом растворе не должно превышать 200 гл поташном и содо-поташном – 250 гл (при температуре окружающего воздуха – 15 и – 20 С соответственно) [3].
Для того чтобы обеспечить селективное поглощение сероводорода растворами соды или поташа регенерацию проводят при температуре 65 - 75°С (остаточное давление в верхней части регенератора 14.5 - 15 кПа). При этом из раствора выделяется преимущественно сероводород и регенерированный раствор селективно сорбирует этот газ.
Концентрация соли подбирается таким образом чтобы исключить выпадение из растворов кристаллов бикарбонатов. Большая концентрация растворов и значит большая сероемкость теоретически могут быть достигнуты при улавливании растворами поташа. Ниже приведены растворимости кислых и средних карбонатов натрия и калия г100 см3 воды [8]:
Таким образом при вакуум-поташной сероочистке можно использовать более концентрированные растворы поглотителя следовательно работать при большей сероемкости раствора и значит при меньшем расходе энергии на перекачку и нагревание растворов. Рекомендуемые концентрации растворов должны быть не более 5 % масс. при улавливании растворами соды и не более 15 % масс. при улавливании растворами поташа.
На коксохимических заводах имеющих вакуум-карбонатные сероочистки применяют переработку сероводорода в серную кислоту.
При использовании этой технологии принципиально подобной получению серной кислоты контактным методом приходится решать несколько специфических задач:
Окисляется сероводород содержащий примеси цианистого водорода. Последний может окислиться либо в оксиды азота либо в элементный азот:
HCN + 7О2 = 2Н2О + 4СО2 + 4NO
HCN + 5О2 = 2Н2О + 4СО2 + 2N2.
Для того чтобы не образовывались оксиды азота окисление (сжигание) сероводорода проводят в две ступени в специальной печи. На первой стадии при недостатке воздуха частично окисляется сероводород а цианистый водород окисляется до азота затем происходит введение дополнительного количества воздуха и дожиг сероводорода и частично образовавшейся серы до диоксида серы.
Другая трудность связана с тем что обычные катализаторы контактного производства серной кислоты снижают активность в присутствии паров воды. Обычно технологические схемы сернокислотных производств включают узел осушки газа перед контактированием. При сжигании сероводорода неизбежно образование смеси диоксида серы и водяного пара поэтому возникла необходимость подбора катализатора устойчивого в присутствии водяных паров. В связи с этим и процесс приготовления серной кислоты из сероводорода получил наименование "мокрый катализ".
Катализатором чаще всего служит ванадиевая контактная масса:
V2О5 12SiО2 05Аl2О3 2Н2О ЗВаО 2КСl.
Наконец особенностью "мокрого катализа" является получение после контактного аппарата в паровой фазе смеси серного ангидрида и водяного пара. При охлаждении газовой смеси конденсируется серная кислота в виде мелкодисперсного тумана. При охлаждении через стенку или при смешении с холодным воздухом в туман переходит все количество образующейся кислоты. Возможным и реализованным решением оказалось охлаждение газов циркулирующей серной кислотой. Образующаяся при конденсации кислота растворяется в циркулирующем продукте (преимущественно). Правда и в этих условиях вместе с газом выносится 30-35% по массе кислоты в виде тумана который улавливается в электрофильтре [8].
Технологическая схема очистки коксового газа от сероводорода
вакуум-карбонатным методом с получением серной кислоты
Процесс очистки коксового газа от сероводорода начинается с его поступления в скруббер оснащенный деревянной хордовой насадкой или плоскопараллельной насадкой из стали 08х13. Скруббер для улавливания сероводорода представляет собой колонный аппарат устройство которого аналогично устройству бензольного скруббера (рис. 6 [3]).
Диаметр скруббера составляет 4-6 м высота – 27-30 м. Деревянная хордовая насадка укладывается внутри скруббера в несколько ярусов.
Скорость газа в скруббере отнесенная ко всему сечению аппарата принимается около 05 мсек [9].
Насадка скруббера орошается 4-5%-м раствором соды или 12-15%-м раствором поташа. При этом происходит поглощение сероводорода цианистого водорода и частично углекислого газа [1].
В ходе поглощения образуются цианиды и гидросульфиды натрия или калия которые впоследствии реагируя с кислородом и сероводородом дают роданиды и тиосульфаты. Реакции образования роданидов и тиосульфатов необратимы и при регенерации раствора не идут в обратном направлении. Затраченные на образование этих солей сода и поташ не восстанавливаются в связи с чем необходимо в производственный цикл непрерывно или периодически вводить определенное количество соды или поташа для пополнения потерь.
Накапливающиеся в поглотительном растворе нерегенерируемые соединения ухудшают улавливание сероводорода из коксового газа. Поэтому до ввода в систему свежего раствора соды (поташа) часть рабочего раствора выводят из цикла. Расход соды при этом составляет около 015 кг на 1 кг извлеченного сероводорода [9].
Рисунок 6. Скруббер для улавливания сероводорода
– плоскопараллельная насадка; 2 – опорные решетки; 3 - распределительные конусы; 4 – штуцер входа газа; 5 – газораспределительное устройство; 6 – струйно-вихревая форсунка; 7 – горизонтальный жалюзийный отбойник; 8 – отбойник циклонного типа.
Насыщенный сероводородом поглотительный раствор насосом подается в конденсатор-холодильник где он подогревается за счет тепла конденсации паров выделяющихся при регенерации поглотительного раствора. Затем раствор поступает в теплообменник в паровой подогреватель и в регенератор представляющий собой колонну с циркуляционным подогревателем и колпачковыми тарелками 1 [1].
В верхней части регенератора расположен штуцер 2 с раструбом для подачи раствора на регенерацию. Над штуцером для сепарации паров от жидкости установлен короб 3 Г-образного сечения. Вверху на выходе паров установлен отбойник 4.
Подаваемый на регенерацию насыщенный раствор поступает на верхнюю тарелку и стекает по тарелкам в нижнюю кубовую часть регенератора. Подогрев раствора производят водяным паром в подогревателе при естественной циркуляции раствора. В нижней кубовой части регенератора расположены штуцеры 5 для выхода раствора в подогреватель и 6 для входа парожидкостной смеси из подогревателя. Для сепарации пара от жидкости над штуцером 6 установлен короб 7 Г-образного сечения верхняя полка которого выполнена из просечно-вытяжного листа боковая – из сплошного листа. Над коробом под первой тарелкой установлен отбойник 8. Штуцер выхода паров 9 из регенератора расположен вверху на крышке штуцер выхода регенерированного раствора 10 – в нижней кубовой части. Кроме того регенератор оснащен люками 11 штуцерами для КИП смотровыми окнами и кранами для отбора проб (см. рис. 78) [3].
Технические характеристики регенератора следующие: диаметр составляет 55-7 м высота – 27 м число тарелок – 11-12расстояние между тарелками – 1-16 м [3].
Регенерация раствора осуществляется кипячением его под вакуумом 600-650 мм рт. ст. Температура кипения раствора при таком вакууме 60-63 С [1].
Раствор стекает по тарелкам регенератора выделяя при этом поглощенные при улавливании сероводород циановодород и углекислый газ увлекаемые из регенератора водяными парами. Регенерированный раствор стекает из нижней тарелки регенератора и затем подается на верх скруббера для улавливания сероводорода [1].
Паро-сероводородная смесь отсасывается вакуум-насосом из регенератора через конденсаторы-холодильники где из смеси конденсируется основная масса водяных паров. Верхняя секция конденсатора-холодильника охлаждается холодным насыщенным поглотительным раствором а нижние секции – технической водой.
После охлаждения газовая смесь содержащая сероводород (до 80%) углекислый газ цианистый водород и водяные пары направляется на установку мокрого катализа для переработки сероводорода в серную кислоту [10].
Процесс получения серной кислоты по методу мокрого катализа – каталитического окисления сернистого газа в присутствии водяных паров в реакционных газах – состоит из трех стадий [3]:
)Сжигания сероводорода с получением сернистого ангидрида:
H2S + 3O2 = 2SO2 + 2H2O + 51894 кДжмоль;
)Каталитического окисления сернистого ангидрида в серный ангидрид:
SO2 + 12O2 = SO3 + 9617 кДжмоль;
)Охлаждения серного ангидрида и паров воды и их совместной конденсации с образованием серной кислоты:
SO3(газ) + H2O(пар) = H2SO4(газ) + 12489 кДжмоль;
H2SO4(газ) = H2SO4(жидк) + 5016 кДжмоль.
При сжигании сероводорода получается влажный газ осушка которого потребовала бы сильного охлаждения газа и последующего нагревания перед поступлением в контактный аппарат что неоправданно осложнило бы и удорожило бы технологическую схему и привело бы к потерям некоторого количества сернистого газа. Поэтому газ не охлаждают и не сушат а окисление сернистого ангидрида производят на катализаторе в присутствии большого количества паров воды [11].
Печь для сжигания сероводорода представляет собой стальной цилиндрический котел футерованный огнеупорным кирпичом с колосниковой насадкой из шамотного кирпича. Сероводородный газ поступает в верхнюю часть печи через горелку в которой смешивается с воздухом и сгорает внутри печи в виде факела. Обжиговый газ отводится снизу печи по газоходу где имеется предохранительный взрывной клапан [12].
После обжига газ проходит очистку от вредных для катализатора примесей. Очистка газа освобождает обжиговый газ от механических и химических примесей что необходимо для предохранения контактной массы от порчи. Очистка газа от огарковой пыли осуществляется как в центробежных пылеочистителях – циклонах так и в электрофильтрах [13].
В контактном аппарате происходит процесс окисления сернистого ангидрида в серный ангидрид на трех (или четырех) слоях ванадиевой контактной массы. В контактный аппарат после первого и второго слоев подается холодный воздух для охлаждения газов до заданного режима контактирования (440-450 С) [1].
Гомогенное некаталитическое окисление сернистого ангидрида протекает столь медленно что его нецелесообразно осуществлять в производственных масштабах. На ванадиевом катализаторе в интервале температур 400-600 С который применяется в производственных условиях константа скорости реакции возрастает в сотни миллионов и в миллиарды раз т. е. активность катализаторов Акат = kкатk = 109÷1012 где kкат и k – константа скорости реакции с применением катализатора и без него [14].
Контактный аппарат разработанный Гипрококсом представлен на рис. 9 [3]. Скорость газов в свободном сечении контактного аппарата (объем газов при н. у.) составляет 03 мс. Объем контактной массы на 1 т серной кислоты в сутки – 0135 м3 [3].
Абсорбция серного ангидрида – завершающая стадия производства серной кислоты контактным методом. Специфическая особенность указанного процесса – образование тумана серной кислоты. Присутствие водяных паров вследствие плохой осушки газа и применения для абсорбции кислоты концентрацией ниже 983 % H2SO4 ведет при низких температурах к образованию частиц тумана серной кислоты абсорбция которых очень затруднена т. к. они уже не являются газами. При соприкосновении молекул серного ангидрида и паров воды образуется стойкий туман который почти не поглощается серной кислотой и оказывает существенное влияние на скорость абсорбции [15].
Абсорбция протекает в башенном абсорбере орошаемом серной кислотой. В результате охлаждения газовой смеси с 400 до 80 С происходит конденсация серного ангидрида и паров воды т. е. образование серной кислоты. Образовавшаяся в абсорбере серная кислота частично отводится в сборники склада готовой продукции а частично из абсорбера направляется в оросительный холодильник и затем в сборник из которого серная кислота насосом подается в башенный абсорбер [1].
Охлажденные газы из абсорбера направляются в электрофильтр пройдя предварительно брызгоуловитель где происходит улавливание брызг серной кислоты. В электрофильтре отделяется туман серной кислоты. Образующийся в электрофильтре конденсат поступает на склад серной кислоты. Выхлопные газы после электрофильтра выбрасываются в атмосферу [1].
Рисунок 9. Контактный аппарат Гипрококса
– цилиндрическая обечайка; 2 – плоское днище; 3 – система двутавровых балок; 4 – коническая крышка; 5 – ребра; 6 – штуцер; 7 – перфорированный распределительный конус; 8 – распределительная решетка; 9 – слой контактный массы; 10 – подслой из сортированной кварцевой щебенки; 11 – сетка; 12 – защитный слой из крупного кварца; 13 – центральная чугунная колонна; 14 15 – опорные конструкции; 16 – теплообменные элементы с плавающей головкой; 17 – распределительные решетки.
Принципиальная схема получения серной кислоты представлена на рис. 10 [3].
Рисунок 10. Принципиальная схема получения серной кислоты
– печь-котел для сжигания сероводорода; 2 – воздуходувка; 3 – камера смешения; 4 – контактный аппарат; 5 – абсорбер; 6 – холодильник; 7 – электрофильтр.
1 Материальный баланс контактного окисления сернистого
Производительность (G) завода по коксовому газу составляет 110000 м3ч С(H2S) = 4 гм3.
Расчет материального баланса ведем на 1 ч.
Находим массу сероводорода по формуле:
m(H2S) = GC = 4 гм3 110000 м3ч = 440000 гч.
Принимаем степень очистки коксового газа от H2S 90 % [3]:
m(H2S)очист = 440000 г 09 = 396000 гч.
Принимаем выход H2S при регенерации раствора (от поглощенного из газа) 98% [3]:
m(H2S)рег = 396000 г 098 = 388080 гч.
Находим массу сернистого ангидрида образовывающегося при сжигании сероводорода по уравнению реакции:
H2S + 3O2 = 2SO2 + 2H2O. (1)
Из уравнения реакции (1) следует что n(SO2) = n(H2S) тогда:
где M(H2S) = 34 гмоль М(SO2) = 64 гмоль – молярные массы реагирующих веществ.
Принимаем степень контактирования при окислении сернистого ангидрида 98 % [16] и находим массу сернистого ангидрида вступившего в реакцию:
Находим массу непрореагировавшего сернистого ангидрида:
Находим массу серного ангидрида образовывающегося при окислении сернистого ангидрида по уравнению реакции:
SO2 + 12O2 = SO3. (2)
Из уравнения реакции (2) следует что n(SO3) = n(SO2)р тогда:
где М(SO2) = 64 гмоль – молярная масса сернистого ангидрида.
где M(SO3) = 80 гмоль – молярная масса серного ангидрида.
Находим массу кислорода пошедшего на окисление сернистого ангидрида по уравнению (2):
где M(O2) = 32 гмоль – молярная масса кислорода.
Принимаем коэффициент избытка воздуха [17] и находим массу всего кислорода поступившего в контактный аппарат:
Находим массу непрореагировавшего кислорода:
Находим объем кислорода поступившего в контактный аппарат используя молярный объем Vm = 224 лмоль:
Находим объем воздуха поступившего в контактный аппарат при этом принимаем что воздух содержит 79 % объемных долей N2 и 21 % объемных
Находим объем азота содержащегося в воздухе:
Находим массу азота используя молярную массу азота М(N2) = 28 гмоль:
Находим объем сернистого ангидрида поступившего в контактный аппарат:
Находим объем сернистого ангидрида вступившего в реакцию окисления:
Находим объем непрореагировавшего сернистого ангидрида:
Находим объем избытка кислорода используя молярную массу кислорода M(O2) = 32 гмоль и молярный объем Vm = 224 лмоль:
Находим объем серного ангидрида образовавшегося в результате окисления сернистого окисления:
Результаты вычислений заносим в табл. 2.
2 Тепловой баланс контактного окисления сернистого ангидрида
Расчет теплового баланса для контактного аппарата ведем по следующему уравнению реакции [3]:
SO2 + 12O2 = SO3 + 9617 кДжмоль. (3)
Основное уравнение для расчета теплового баланса представлено ниже:
где Q – теплота для вещества; G – количество вещества; С – средняя теплоемкость вещества; t – температура.
Материальный баланс контактного аппарата
Принимаем температуру входящих в контактный аппарат газов равной 440 С; выходящих – 480 С [16].
Рассчитываем теплоты вносимые газами в контактный аппарат.
Принимаем среднюю объемную теплоемкость сернистого ангидрида при 440 С C(SO2) = 2 04 кДж(м3 С) [16] и рассчитываем теплоту вносимую сернистым ангидридом в контактный аппарат:
Рассчитываем теплоту вносимую в контактный аппарат кислородом C(O2) = 139 кДж(м3 С) [16]:
Рассчитываем теплоту вносимую в контактный аппарат азотом C(N2) = 132 кДж(м3 С) [16]:
Рассчитываем теплоты уносимые газами из контактного аппарата при температуре 480 С.
Рассчитываем теплоту уносимую из контактного аппарата непрореагировавшим сернистым ангидридом C(SO2) = 206 кДж(м3 С) [16]:
Рассчитываем теплоту уносимую из контактного аппарата избытком кислорода C(O2) = 140 кДж(м3 С) [16]:
Рассчитываем теплоту уносимую из контактного аппарата азотом C(N2) = 133 кДж(м3 С) [16]:
Рассчитаем теплоту уносимую из контактного аппарата серным ангидридом C(SO3) = 7094 Дж(мольК) [18]. Переводим температуру из градусов Цельсия в Кельвины Т = 480 + 273 = 753 К:
Рассчитаем теплоту выделяющуюся в ходе экзотермической реакции окисления сернистого ангидрида используя уравнение реакции (3); n(SO3) = =n(SO2)р =1118584 моль:
Рассчитываем суммарный приход теплоты в контактный аппарат:
Qприх = Q(SO2) + Q(O2) + Q(N2) + Qреакц =
= 22949837 кДж + 11493187 кДж + 41059656 кДж + 107574223 кДж = 1830769 03 кДж.
Принимаем потери тепла в окружающую среду 5 % [19] от прихода теплоты:
Рассчитываем суммарный расход теплоты уносимой из контактного аппарата:
Qрасх = Q(SO2(ост)) + Q(O2(ост)) +Q(N2) + Q(SO3) + Qпот =
= 505277 кДж + 4209408 кДж + 45131688 кДж + 59752319 кДж +
+ 9153845 кДж = 118752537 кДж.
Реакция окисления сернистого ангидрида является экзотермической поэтому необходимо отводить тепло из аппарата:
Qотв = Qприх – Qрасх = 183076903 кДж – 118752537 кДж =
Результаты вычислений заносим в табл. 3.
Тепловой баланс контактного аппарата
В данной курсовой работе была рассмотрена технологическая схема очистки коксового газа от сероводорода вакуум-карбонатным методом с получением серной кислоты.
Выбор данной схемы обусловлен следующими преимуществами:
В качестве поглотителей используются растворы карбонатов натрия и калия которые характеризуются относительной дешевизной и доступностью.
Отсутствует корродирующее действие поглотителя на аппаратуру.
Способ характеризуется простотой аппаратурного оформления и эксплуатации.
Данный метод пригоден для очистки коксового газа при наличии в нем различных примесей (COS O2 HCN и др.).
Кроме того был описан процесс получения серной кислоты методом мокрого катализа который включает в себя 3 стадии:
)Сжигание сероводорода с получением сернистого ангидрида
)Каталитическое окисление сернистого ангидрида в серный ангидрид
)Охлаждение серного ангидрида и паров воды и их совместная конденсация с образованием серной кислоты.
Также в курсовой работе был выполнен расчет материального и теплового балансов контактного окисления сернистого ангидрида при содержании в коксовом газе 4 гм3 H2S.
Коляндр Л. Я. Улавливание и переработка химических продуктов коксования Л. Я. Коляндр. – Харьков: Металлургиздат 1962. – 472 с.
Агроскин А. А. Химия и технология углей А. А. Агроскин. – М.:«Недра» 1969. – 237 с.
Справочник коксохимика. В 6-и томах. Т.3. под ред. Е. Т. Ковалева. – Харьков: Издательский Дом «ИНЖЭК» 2009. – 432 с.
Рамм В. М. Абсорбция газов: 2-е издание В. М. Рамм. – М.: «Химия» 1976. – 656 с.
Кауфман А. А. Технология коксохимического производства: учебное пособие А. А. Кауфман Г. Д. Харлампович. – Екатеринбург: ВУХИН-НКА 2005. – 288 с.
Гомельский А. З. Аппаратчики коксохимических производств: 2-е издание А. З. Гомельский. – Харьков: Металлургиздат 1953. – 384 с.
Сысков К. И. Коксохимическое производство К. И. Сысков Ю. Г. Королев. – М.: «Высшая школа» 1969. – 152 с.
Бернштейн И. М. Автоматизация управления сернокислотным производством И. М. Бернштейн Б. Т. Васильев А. И. Голант и др. – М.: «Химия» 1975. – 248 с.
Позин М. Е. Расчеты по технологии неорганических веществ М. Е. Позин Б. А. Копылов Г. В. Бельченко и др. – М.: «Химия» 1966. – 638 с.
Основы химической технологии под ред. И. П. Мухленова. – М.: «Высшая школа» 1983. – 336 с.
Катализ в кипящем слое под ред. И. П. Мухленова. – Л.: «Химия» 1971. – 312 с.
Исследования в области абсорбционных процессов под ред. Б. А. Черткова. – М.: издательство НИУИФа 1970. – 132 с.
Амелин А. Г. Производство серной кислоты А. Г. Амелин. – М.: «Химия» 1967. – 472 с.
Игнатенков В. И. Примеры и задачи по общей химической технологии: учебное пособие для вузов В. И. Игнатенков В. С. Бесков. – М.: ИКЦ «Академкнига» 2005. – 198 с.
Грошева Л. П. Принцип составления энергетического (теплового) баланса и тепловые расчеты химико-технологических процессов: учебное пособие Л. П. Грошева. – Великий Новгород: Новгородский государственный университет имени Ярослава Мудрого 2006. – 14 с.
Контактный ап..dwg

Выход серного ангидрида
Техническая характеристика
Технические требования
Производительность по серной кислоте 10 тч. 2. Концентрация сернистого ангидрида в газе 10 %. 3. Концентрация кислорода в газе 63
%. 4. Объем газа 2270 куб. м.ч. 5. Конечная степень контактирования 0
6. Температура газа на входе 713 К. 7. Температура газа на выходе 753 К. 8. Рабочее давление 0
Аппарат испытать на прочность и герметичность пневматическим пробным давлением 0
МПа не менее 5 мин. 2. Аппарат красить в соответствии с ОСТ 95.884-81 лаком пентафталевым ПФ-170 с алюминиевой пудрой ГОСТ 15907-70. 3. На месте монтажа аппарат установить на изоляторы.
Аппарат контактный. Чертеж общего вида
Наименование и марка материала
Слой контактной массы
Промежуточный теплообменник
Проход услов- ный Dy
Давле- ние ус- ловное Py
Рекомендуемые чертежи
Свободное скачивание на сегодня
Обновление через: 7 часов 9 минут