Эксплуатация, ремонт и электроснабжение оборудования инструментального цеха завода Прибор г. Бендеры



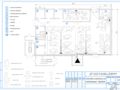
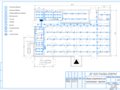
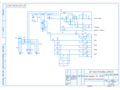
- Добавлен: 25.01.2023
- Размер: 8 MB
- Закачек: 1
Описание
Состав проекта
![]() |
![]() |
![]() ![]() ![]() ![]() |
![]() ![]() ![]() ![]() |
![]() ![]() ![]() ![]() |
![]() ![]() ![]() |
Дополнительная информация
Токарный станок с ЧПУ.cdw

схема электрическая принципиальная
ПГУ им. Т.Г. Шевченко
ДП 13.02.11.140564.2018.
Электроснабжение цеха.cdw

- Заточное отделение
- Резьбошлифовальное отделение
Электроснабжение инструментального цеха
ДП 13.02.11.140564.2018.МЧ1
ПГУ им. Т.Г. Шевченко
- Электропривод раздвижных ворот
- Плоскошлифовальный станок
- Круглошлифовальный станок
- Внутришлифовальный станок
- Заточный станок для фрезерных головок
- Универсальный заточный станок
- Резьбошлифовальный станок
- Заточный станок для червячных фрез
Освещение цеха.cdw

- Заточное отделение
- Резьбошлифовальное отделение
Освещение инструментального цеха
ДП 13.02.11.140564.2018.МЧ2
ПГУ им. Т.Г. Шевченко
ИТОГ ДИПЛОМ.doc
1. Назначение токарных станков с ЧПУ9
2. Техническая характеристика токарного станка СКЕ 6150Z12
3. Техническое описание токарного станка13
4. Инструкция по эксплуатации токарного танка19
РАСЧЕТ ЭЛЕКТРИЧЕСКИХ НАГРУЗОК21
1. Краткая характеристика производства и потребителей электроэнергии21
2. Выбор схемы электроснабжения цеха23
3. Определение расчетной мощности и нагрузок24
4. Нагрузка цеха с учётом освещения29
5. Выбор мощности трансформатора и компенсирующих31
устройств на цеховые ТП31
6. Расчет сети напряжением до 1000 В33
7. Выбор коммутационной аппаратуры и питающих34
кабелей для оборудования34
8. Выбор распределительных конструкций35
9. Выбор защитных автоматических выключателей и питающих кабелей для распределительных шкафов и шинопроводов36
ВЫБОР ОСВЕЩЁННОСТИ СИСТЕМЫ ОСВЕЩЕНИЯ И ИСТОЧНИКА СВЕТА38
1. Выбор типа светильников их размещение и высота подвеса38
2. Расчёт мощности и выбор ламп41
3. Выбор схемы питания типа осветительных щитков46
4. Расчёт и выбор сечений питающей и распределительной сети47
5. Аварийное освещение47
ОРГАНИЗАЦИЯ РЕМОНТА ЭЛЕКТРООБОРУДОВАНИЯ49
1. Расчёт количества рабочих для выполнения работ55
согласно с графиком ППР55
1. Мероприятия по технике безопасности при эксплуатации токарных станков с ЧПУ57
2. Обеспечение электробезопасности при эксплуатации электрооборудования62
3. Организационные требования пожарной безопасности для инструментального цеха64
Завод "Прибор" создан в 1971 году в Бендерах как филиал Московского машиностроительного завода «Салют». Завод возводился как военное производство занятое выпуском корабельных радиолокационных систем и его деятельность носила закрытый характер.
Со временем Бендерский филиал получил статус самостоятельного предприятия в составе ММЗ «Салют» а в апреле 1976 года был преобразован в завод «Прибор». Кроме военной продукции на нём был освоен и выпуск товаров народного потребления.
После распада СССР объём производства резко сократился. Для выхода из кризиса заводом был освоен выпуск оборудования для машиностроительной промышленности и много товаров народного потребления. Во время войны в 1992 году завод "Прибор" сильно пострадал.
Московское основное производство продает газотурбинные авиационные двигатели по всему миру. Именно оно берет на себя заботы по поставке сырья и сбыту продукции. У приднестровского же завода постоянный стабильный план на квартал с разбивкой по месяцам. Здесь не работают на склад только под заказ все строго регламентировано. Все просчитывается в том числе годовой бюджет завода. И неизменно с учетом загрузки рабочих мест по видам работ с целью эффективного использования оборудования.
Задача местного производства – продукцию произвести обеспечив при этом качество той или иной детали (узла) авиадвигателя своевременность их изготовления необходимые объемы. А это уже зависит от профессионализма и компетенции трудового коллектива. Детали и узлы для авиационных двигателей а завод выпускает их более 600 наименований – что может быть сложнее. Отсюда и большая ответственность изготовителя и высокие требования к производимой на заводе продукции. Для этого здесь действует многоступенчатая и многоуровневая система контроля качества – сам работник должен проверить деталь затем мастер контролер отдела технического контроля. Эта система страхует от ошибок которые могут выйти боком исключает массовый брак.
А еще завод сертифицирован по системе менеджмента качества ISO которая подтверждает возможность изготовления. Причем речь идет не о конкретной продукции а о порядке организации производства и обеспечения ее качества. Одним из определяющих факторов этого является удовлетворенность потребителя который всегда прав.
Выпускают здесь и запорно-пломбировочные устройства для запирания и пломбирования железнодорожных вагонов для РЖД. С ними было трудно пробиться на рынок. Направление металлоемкое в приобретении металла нередко возникают сложности связанные с частым изменением ценовой политики поставщиков. Особые требования к качеству изготавливаемых устройств поскольку конкуренция на этом рынке очень жесткая. На этом заказе было создано порядка ста рабочих мест. Главным при этом было не получение прибыли а работа без убытков занятость.
Годами налаживаемый механизм работает как часы без сбоев. Планирование позволяет видеть перспективу иметь возможность для маневрирования производственным процессом.
Для обеспечения качества продукции крайне важно обновлять оборудование. Это необходимо и для повышения производительности труда. Поэтому на заводе взят курс на использование более современного и производительного оборудования. Если раньше станки с ЧПУ были токарные то сейчас они токарно-фрезерные. Но многие виды работ автомат не выполнит только умелые руки человека. Потому что некоторые детали обрабатываются с «полем допуска» до 16 а то и 8 микрон. На старом оборудовании это сделать невозможно. При таком сложном технологическом процессе значение имеет даже температура воздуха в цехе. Когда в цехах не было отопления изготавливать детали с повышенной точностью не было возможности. Первыми в Приднестровье на «Приборе» применили для отопления производственных помещений инфракрасные газовые излучатели. На заводе везде установлены автономные газовые котельные что экономит средства предприятия обеспечивает возможность выпуска качественной продукции ее соответствие предъявляемым заказчиком требованиям.
В 2013 г. была проведена полная реконструкция гальванического участка модернизировано старое и приобретено новое оборудование. К перечню освоенных гальванических процессов добавились хромирование никелирование кадмирование нанесение графита методом электрофореза меднение углеродистых и коррозионностойких сталей и сплавов и деталей из меди и ее сплавов оксидное фосфотирование стальных деталей. Особой гордостью предприятия являются оснащенная самым современным оборудованием линия серебрения участок по изготовлению штампованных заготовок горячештамповочное производство.
Развитие предприятия – это не только приобретение нового оборудования но и освоение новых технологий. Это непрерывный процесс. Изготовление любого изделия требует серьезной предварительной подготовки. К примеру один из выполненных коллективом предприятия заказов обуславливал выпуск 100 с небольшим деталей. Но оснастки для их изготовления необходимо было 500 единиц. Детали настолько сложные что без соответствующего оснащения их не изготовить. В настоящее время на предприятии работают 450 человек (в 2004 г. было 319).
ТОКАРНЫЕ СТАНКИ С ЧПУ
1. Назначение токарных станков с ЧПУ
Токарные станки используются в ремонтных и столярных мастерских механических цехах завода «Прибор» везде где требуется металлообработка. Если нужно обточить поверхности любых форм выполнить сверление нарезать резьбу просто отрезать детали – для всего этого нужен токарный станок.
Для мелкосерийного производства предназначены токарно-винторезные станки. С их помощью обрабатывают конические и цилиндрические внутренние поверхности и конечно нарезают резьбу.
Если производство крупное то и станки нужны с программным обеспечением (ЧПУ). Точность работы и высокая производительность такого агрегата нового поколения обеспечивается программой.
Здесь также применяют еще один вид станков такого же назначения – токарно-револьверный. Он заменяет собой сразу много инструментов так как имеет специальную револьверную головку.
Рис. 1.1. Токарный станок с ЧПУ
Числовое программное управление — это автоматическое управление станком при помощи компьютера и программы обработки.
Токарные станки с ЧПУ функционально идентичны станкам с ручным управлением но перемещение исполнительных органов этих станков управляется электроникой.
Главное преимущество работы на станках с ЧПУ это более высокий уровень автоматизации производства. Поэтому основными задачами оператора становятся подготовительно-заключительные операции: наладка инструмента установка и снятие детали. В результате один работник может обслуживать несколько станков одновременно.
Также плюсом является производственная гибкость. Это значит что для обработки разных деталей нужно лишь заменить программу. Стоит отметить повторяемость и высокую точность обработки. По одной и той же программе можно произвести тысячи практически одинаковых деталей нужного качества. Сама методика работы по программе позволяет точно рассчитывать время обработки партии деталей и значит более полно загружать оборудование.
Токарный станок с ЧПУ стоит дорого и требует больших затрат на установку и обслуживание чем обычный станок но его высокая производительность перекрывает затраты при грамотном использовании и соответствующих объемах производства.
Осевыми перемещениями токарного станка с ЧПУ руководит компьютер который читает управляющую программу и выдает команды соответствующим двигателям. Двигатели заставляют перемещаться исполнительные органы станка — рабочий стол или колонну со шпинделем. В результате производится механическая обработка детали. Датчики установленные на направляющих посылают информацию о фактической позиции исполнительного органа обратно в компьютер. Это называется обратной связью. Как только компьютер узнает о том что исполнительный орган станка находится в требуемой позиции он выполняет следующее перемещение. Такой процесс продолжается пока чтение управляющей программы не подойдет к концу.
Основные преимущества производства с помощью станков с ЧПУ по сравнению с производством использующим универсальные станки с ручным управлением следующие:
сокращение времени изготовления деталей;
повышение точности обработки;
простота и малое время переналадки;
возможность использования менее квалифицированных рабочих;
возможность применения многостаночного обслуживания;
снижение затрат на специальные приспособления;
сокращение цикла подготовки производства новых изделий и сроков их поставки;
концентрация операций что обеспечивает сокращение оборотных средств в незавершенном производстве а также затрат на транспортирование и контроль деталей;
уменьшение числа бракованных изделий по вине рабочего.
Наибольший экономический эффект дает изготовление на станках с ЧПУ сложных деталей в том числе из труднообрабатываемых материалов повышенной точности требующих выполнения многих технологических операций.
Устройство электродвигателей станка обусловлено особенностями станочного электропривода: повторно-кратковременным режимом работы большой частотой включений широким диапазоном регулирования скорости и частыми реверсами.
Основная особенность станков с ЧПУ состоит в том что программа то есть данные о величине скорости и направлении перемещений рабочих органов задается в виде символов нанесенных на специальный программоноситель. На станке с ЧПУ для того чтобы обработать деталь новой конфигурации часто достаточно установить в УЧПУ новую УП которая содержит определенную задающую информацию (ЗИ). Устройством ввода программы (УВП) программа считывается то есть преобразуется в электрические сигналы и направляется в устройство обработки программы (УОП) которое через устройство управления приводом (УУП) воздействует на объект регулирования – привод подач (ПП) станка. Заданное перемещение подвижных узлов станка связанных с приводом подач контролируют датчики обратной связи. Информация обратной связи с датчика через устройства обратной связи поступает в УОП где происходит сравнение фактического перемещения узла подачи с заданным по программе для внесения корректив в произведенные перемещения. Для исполнения дополнительных функций электрические сигналы поступают с УВП в устройство технологических команд. Происходит включение или выключение различных двигателей муфт электромагнитов и др.
2. Техническая характеристика токарного станка СКЕ 6150Z
Токарные станки с ЧПУ серии CKE 6150Z предназначены для патронной и центровой обработки с высокой точностью в один или несколько проходов наружных и внутренних поверхностей деталей типа тел вращения со ступенчатым и криволинейным профилем различной сложности нарезания резьбы резцом обточки расточки обработки фасонных и конических поверхностей проточки канавок и многих других операций. Обработку можно производить в замкнутом полуавтоматическом цикле одновременно по двум координатам.
Таблица 1.1. Технические характеристики станка СКЕ 6150Z
Наименование параметра
Диаметр обработки над станиной мм
Расстояние между центрами мм
Диаметр обработки над суппортом мм
Диаметр отверстия в шпинделе мм
Диапазон скоростей шпинделя оборотовминуту
Коробка переключения передач вращения шпинделя
Общая мощность двигателя кВт
Быстрые перемещения по осям XZ мм
Точность установки инструмента мм
Точность позиционирования по XZ мм
Время смены инструмента секунд
Диаметр пиноли задней бабки мм
Вращающий момент на шпинделе
3. Техническое описание токарного станка
Устройство токарного станка
CKE 6150Z является аналогом станка 16К20Ф3 (16А20Ф3). Это один из наиболее качественных и популярных станков китайского производства. Популярность этих станков обусловлена в первую не высокой ценой и передовыми и инновационным технологиями.
Рис. 1.2. Устройство СКЕ6150Z
Шпиндельная (передняя) бабка
Револьверная головка (468 - позиционная)
Задняя бабка (гидравлическаямеханическая)
Местное освещение рабочей зоны
Кабинетная защита зоны обработки
Шкаф с электросиловой аппаратурой
Панель управления станком (ЧПУ)
Конвейер для удаления стружки
Изолирующее основание
Трех кулачковый патрон (механическийгидравлический)
На данном станке по заданным параметрам возможно производить обработку материала в патроне: обточку расточку обработку наружных поверхностей подрезку торцов проточку канавок нарезание резьбы обработку деталей типа коротких осей валиков втулок фланцев крышек мелких корпусов стаканов полумуфт обработку внутренних поверхностей центровым инструментом.
Рис.1.3. Система ЧПУ Fanuc Рис.1.4. Гидравлический патрон
Рис.1.5. Револьверная головка Рис.1.6.Зажимный цилиндр гидропатрона
Рис.1.7. Сервопривод подач Fanuc beta Рис.1.8. Гидростанция
Рис.1.9. Электрошкаф Рис.1.10. Сменщик инструмента
Рис.1.11. Механическая задняя бабка Рис.1.12.Гидравлическая задняя бабка
Рис.1.13. Станина Рис.1.14. Система смазки
Рис.1.15. Привод оси Z Рис.1.16. Привод оси X
Описание работы схемы токарного станка
Рис.1.17. Электрическая принципиальная схема токарного станка с ЧПУ CKE6150Z
Управление главным приводом
Пуск электродвигателя осуществляется нажатием одной из кнопок "пуск" SB3 или SB4 (расположенных на пультах каретки и около коробки подач) при выключенном фрикционе. При этом н.з. контакт конечного выключателя SQ1 замкнут. Пускатель КМ1 получает питание и подключает электродвигатель главного движения к сети. Одновременно с пускателем КМ1 получают питание реле времени К1 и К2.
Управление вращением шпинделя осуществляется с помощью фрикциона включаемого от рукоятки.
При отключенном фрикционе н.з. контакт SQ1 остается замкнутым реле времени K1 K2 и тормозная муфта включены. При этом загорается сигнальная лампа HL2. При работе двигателя главного движения на холостом ходу реле времени K1 настроенное на выдержку 25-3 мин отключает катушку магнитного пускателя и соответственно двигатель от сети. Одновременно реле времени K2 настроенное на выдержку 25 сек. потеряет питание и отключит тормозную муфту.
При включении фрикциона н.з. контакт SQ1 размыкается отключает реле времени K1 и обеспечивает работу станка. Остановка двигателя осуществляется нажатием на одну из кнопок "стоп" SB5 или SB6. При этом через н.з. контакт KM1.4 включается реле K1 и тормозная муфта YAT1. Контроль нагрузки электродвигателя осуществляется по амперметру.
Управление приводом подач
Рабочие подачи осуществляются от двигателя главного привода M1 ускоренный ход от двигателя ускоренного хода M3 типа АOЛ2-21-4 (4Ах80А4УЗ) 11 кВт 1400 обмин при 50 Гц 1690 обмин при 60 Гц.
В фартуке станка имеется четыре электромагнитные фрикционные муфты две из которых используются для управления перемещением каретки в продольном направлении и две - для управления перемещением суппорта в поперечном направлении.
Управление муфтами производится рукояткой крестового переключателя установленного на фартуке станка имеющего 5 положений: одно - вертикальное нейтральное и 4 наклонных соответствующих направлению перемещения суппорта и каретки.
Включение электродвигателя ускоренного хода при любом положении рукоятки переключателя обеспечивается пусковой толчковой кнопкой встроенной в головку рукоятки крестового переключателя.
Во избежание одновременного включения маточной гайки и электромагнитных муфт предусмотрен блокировочный конечный выключатель SQ2 установленный внутри фартука который обрывает цепь питания муфт при включении маточной гайки.
Для предотвращения пробоя электромагнитных муфт и уменьшения искрообразования на контакте при отключении катушки предусмотрены разрядные сопротивления R1 R5.
На фартуке станка имеется переключатель режимов работы на три положения который включает муфты соответственно на:
конусное точение (внутреннее)
конусное точение (наружное)
Привод охлаждения осуществляется от электронасоса M2 типа ПА-22 012 кВт 2800 обмин при 50 Гц 3350 обмин при 60 Гц. Пуск и остановка электродвигателя осуществляется включением переключателя установленного на фартуке станка.
Возможные неисправности и методы их устранения
Таблица 1.2. Перечень возможных неисправностей
Необходимые приспособления и материалы
Проверка наличия постороннего шума вибрации температуры работы вентилятора плавности вращения фиксация двигателя к рамке фиксация шкива проверка затяжки электрических соединений эд и вентилятора эд
Керосин для очистки вентилятора и ветошь
Проверка тормоза эд шпинделя
раз в месяц или при появлении посторонних шумов при торможении
Проверка датчиков давления
Проверка электрических соединений (эд гидростанции клеммная коробка разъем к электрошкафу)
раз в 6 мес или при появлении неисправности вибрации
Протяжка всех электрических соединений проверка и закрепление болтов модулей входоввыводов реле контакторов автоматических выключателей очистка от пыли
запрещено использовать сжатый воздух
Очистка фильтра теплообменника вытащить защитную сетку при загрязнении продуть воздухом
Заменить батареи питания сервоприводов (датчиков абсолютных энкодеров)
При появлении сообщения на экране ЧПУ
Очистка вентиляторов: теплообменника частотного преобразователя сервоприводов
ЧПУ пульт управления
Очистка клавиш пульта управления
Ветошь моющее средство на мыльной основе
Проверка наличия запаха или изменение цвета электрических устройств износ поверхностей трения проверка затяжки болтов заземления
Срабатывание всех клавиш управления состояние кабель-канала станины и ЧПУ
4. Инструкция по эксплуатации токарного танка
Техническое обслуживание токарного станка с ЧПУ
Предварительное составление дефектной ведомости станка на комплектность по механической части и электрооборудованию.
Полная разборка станка и всех его узлов.
Дефектовка контроль сортировка деталей
Промывка и протирка всех деталей.
Уточнение предварительно составленной дефектной ведомости по деталям требующим восстановления или замены.
Измерение износа трущихся поверхностей перед ремонтом базовых деталей.
Разработка электрических схем и корректировка тех документации
РемонтЗамена электрической части станка: пульта управления электрошкафа разводки шин жгутовки диагностика.
РемонтЗаменаМонтаж ЧПУ с диагностикой электрошкафа и электрических цепей управления станком пайкой разъемных соединений электронных блоков проверкой и регулировкой питающих напряжений контролем программного функционирования проверкой функционирования электронных узлов и каналов связи с интерполяторами наладкой системы управления инструментом наладкой системы обслуживания подключением и наладкой измерительных систем наладкой системы движения наладкой системы диагностики наладкой системы безопасности проверкой работы схемы контроля технологических команд электроприводов и программируемых контроллеров.
Ремонтзамена деталей и узлов имеющих износ или повреждения в соответствии с дефектной ведомостью устранение которых технически возможно и экономически целесообразно
Шлифование и шабрение направляющих всех подвижных узлов плоскости стола столов-спутников поверхностей станины продольного суппорта поперечной каретки задней бабки прижимных планок рычагов кронштейнов вилок.
Замена изношенных подшипников качения.
Замена изношенных зубчатых колес и муфт.
Полная разборка шпиндельного устройства установка новых подшипников шлифовка конуса.
РемонтЗамена комплекта ШВП подшипников опор ШВП. Ремонт коробки подач
РемонтЗамена системы смазки
РемонтЗамена системы охлаждения.
Замена или восстановление и подгонка регулировочных клиньев и прижимных планок
Замена изношенных крепежных деталей.
Ремонт ограждений (щитков кожухов крышек)
Сборка всех узлов станка проверка правильности взаимодействия узлов и механизмов.
Шпаклевка и покраска в соответствии с требованиями к отделке нового оборудования.
Обкатка на холостом ходу станка на разных скоростях и подачах.
Проверка на жесткость и соответствие нормам точности.
ПроверкаИспытания станка по обрабатываемой детали на точность и шероховатость обработанных поверхностей повторяемость размеров.
РАСЧЕТ ЭЛЕКТРИЧЕСКИХ НАГРУЗОК
1. Краткая характеристика производства и потребителей электроэнергии
Инструментальный цех (ИЦ) предназначен для серийного производства деталей по заказу. ИЦ предусматривает наличие производственных служебных вспомогательных и бытовых помещений. Металлорежущие станки различного назначения размещены в станочном заточном и резьбошлифовальном отделениях.
Транспортные операции выполняются кран-балкой и наземными электротележками.
Цех получает электроэнергию от собственной цеховой комплексной трансформаторной подстанции (КТП) пристроенной к заводу. Подводимое напряжение – 10 кВ. Потребители электроэнергии относятся к 2 и 3 категории надежности электроснабжения.
Количество рабочих смен – 3.
Каркас здания сооружен из блоков-секций длиной 6 и 8 м каждый.
Размеры цеха А×В×Н = 50×30×8 м.
У всех вспомогательных помещений высота 4м.
Перечень электрооборудования (ЭО) цеха металлорежущих станков дан в таблице 2.1. Мощность электропотребления указана для одного приемника.
Расположение основного ЭО показано на плане (рис.2.1.)
Рис. 2.1. План расположения ЭО инструментального цеха
Таблица 2.1. Перечень ЭО инструментального цеха
Наименование отделения и оборудования.
Номинальная мощность Pн. кВт.
Коэффициент мощности cosφ
Механическое отделение
Электропривод раздвижных ворот
Круглошлифовальный станок
Токарный станок с ЧПУ
Плоскошлифовальный станок
Внутришлифовальный станок
Универсальный заточный станок
Заточный станок для червячных фрез
Заточный станок для фрезерных головок
Резьбошлифовальное отделение
Резьбошлифовальный станок
Характеристика среды цеха
В помещениях инструментального цеха отсутствует химически активная или органическая среда т.е. не содержаться агрессивные пары газы жидкости не образуются отложения или плесень.
В помещениях по технологическим условиям производства не выделяется технологическая пыль в таком количестве чтобы она оседала на проводах или проникала бы внутрь машин или аппаратов.
Помещения в цеху не относятся к взрывоопасным поскольку объём взрывоопасной смеси не превышает 5 % от свободного объема помещения. Помещения также нельзя отнести к пожароопасным зонам. Поскольку в пространстве внутри и вне помещений не обращаются или мало обращаются горючие вещества в котором они могут находиться в нормальном технологическом процессе или при его нарушении.
Помещения в цеху относятся к сухим помещениям в которых относительная влажность воздуха не превышает 60 %. При отсутствии различных вышеперечисленных агрессивных сред можно отнести помещения в цеху с нормальной средой.
Среда цеха характеризуется как нормальная на основании следующих параметров:
)относительная влажность воздуха не выше 60 % . ПУЭ 1.1.6.
)температура воздуха не выше 350 С ПУЭ 1.1.10.
)технологическая пыль отсутствует ПУЭ 1.1.11.
)агрессивные пары жидкости и газы не применяются ПУЭ 1.1.11
2. Выбор схемы электроснабжения цеха
Схемы электроснабжения приёмников электрической энергии промышленных предприятий зависят от мощности отдельных приёмников их количества распределения по территории и других факторов и должны отвечать следующим требованиям:
Обеспечить необходимую надёжность электроснабжения в зависимости от категории приёмников;
Иметь оптимальные технико-экономические показатели по капитальным затратам расходу цветных металлов эксплуатационным расходам и потерям энергии;
Быть удобными в эксплуатации;
Допускать применение индустриальных и скоростных методов монтажа.
Схемы цеховых сетей бывают радиальные и магистральные.
Выберем радиальную схему электроснабжения.
3. Определение расчетной мощности и нагрузок
Определение электрических нагрузок является первым этапом проектирования любой системы электроснабжения и производится для выбора трансформаторов цеховых ТП токоведущих элементов компенсирующих установок защитных устройств.
Определение электрических нагрузок проводил методом упорядоченных диаграмм. Исходными данными для определения электрических нагрузок являются количество и мощность приемников электроэнергии в цехе категория по степени надежности характеристика помещений по окружающей среде.
Необходимо пронумеровать все электроприемники (ЭП) в цехе.
Все ЭП цеха распределяются по узлам. В узел собираются ЭП расположенные вблизи друг от друга – в линию в одном помещении или просто рядом. Причем если ЭП расположены в линию то лучше запитать их посредством шинопровода а если просто рядом то лучше подключить их к силовому щиту (шкафу). Помимо силовых нагрузок в цехе могут располагаться вспомогательные нагрузки такие как вентиляторы тепловые завесы калориферы обеспечивающие благоприятные условия труда. Запитка этих электроприёмников осуществляется от источников питания – узлов к которым они ближе всего расположены.
В каждом узле выделяются группы однотипных потребителей (в данном случае одинаковые станки). Значение среднего коэффициента использования Ки и коэффициента мощности cosφ для электроприёмников (ЭП) в узлах цеха выбираются по табл. 2.3 [2]. Результаты расчетов заносятся в таблицу 2.2.
Все ЭП работающие в повторно– кратковременном режиме (ПКР) такие как краны – должны быть приведены к длительному режиму работы.
где ПВ– продолжительность включения данного крана в относительных единицах;
Затем поочередно считаются узлы от первого к последнему.
В моем случае всего 6 узлов и ЭП будут запитаны от силовых щитов:
узел: 14 15 16 23 24 29 30 36 37
узел: 17 18 25 26 31 32 33 38 39 40
узел: 1 6 7 12 13 19
узел: 2 3 4 5 8 9 10
Рассмотрим расчет нагрузки на примере узла № 4:
Активная суммарная мощность однотипных ЭП рассчитывается по формуле:
где: Pн – номинальная мощность отдельного ЭП приведенная к продолжительности включения 100% кВт;
n – количество однотипных ЭП
Активная суммарная мощность внутришлифовальных станков кВт:
Активная суммарная мощность однотипных ЭП для остальных узлов определенна аналогичным образом результаты в таблице 2.2.
Активная средняя мощность рассчитывается по формуле:
где: Kи. ср. – средний коэффициент использования для ЭП в узле и цехе по табл. 2.3. [2]
PнΣ– сумма активных мощностей ЭП в узле и цехе кВт;
Активная средняя мощность за наиболее загруженную смену работы внутришлифовальных станков кВт:
Pсм = 60014 = 84 кВт
Реактивная средняя мощность за наиболее загруженную смену работы внутришлифовальных станков кВт 1.3[2]
где: tgφ – коэффициент мощности по 1.7[3]
Qсм = 841333 = 112 кВАр
Активная и реактивная средняя мощность для остальных узлов определенна аналогичным образом результаты в таблице 2.2.
Показатель силовой сборки для группы ЭП цеха 1.4[2]
Так как в этом узле все ЭП одинаковой мощности то m = 1.
Показатель силовой сборки для группы ЭП для остальных узлов определены аналогичным образом результаты заносятся в таблицу 2.2.
Значение среднего коэффициента использования для группы ЭП: 1.5[2]
где:– суммарная активная средняя мощность нагрузки за наиболее загруженную смену ЭП данной группы кВт;
– суммарная активная нагрузка всех ЭП данной группы кВт.
Средний коэффициент использования для остальных узлов определялся аналогичным образом результаты в таблице 2.2.
Далее определяем эффективное (приведённое) число ЭП. В случае получения не целого числа nэ – оно округляется до целого в ближайшую сторону. Если же nэ получилось больше n то nэ принимается равным n .
Условия определения nэ:
) n 5 – число ЭП в группе; m ≥ 3– показатель силовой сборки;
Kи.ср. ≥ 02– средний коэффициент использования:
) n ≥ 5; m 3; Kи.ср. ≥ 02:
) n ≥ 5; m 3; Kи.ср. 02:
nэ и Кс –не определяется Pр –рассчитывают по коэффициенту загрузки:
(допускается принимать Кз=09 для ЭП длительного режима и Кз=075 для ЭП ПКР)
)n ≥ 5; m ≥ 3; Kи.ср. ≥ 02:
) n ≥ 5; m ≥ 3; Ки.ср ≤ 02:
При этом эффективное число ЭП будет равно:
где: – относительное эффективное число ЭП определяется по таблице 3.11[2] зная и
где: – относительное число наибольших по мощности ЭП:
где: n’– количество ЭП в данной группе ЭП у которых единичная мощность
–относительная суммарная мощность наибольших по мощности ЭП группы:
где: – суммарная мощность тех электроприёмников входящих в узел у которых единичная мощность отвечает условию (1.9).
В данном узле выполняется особое условие т.к. все ЭП одинаковые по мощности в остальных же узлах применялись условия № 1 №2 и №5.
Для подсчета нагрузки группы электроприемников одинакового режима работы определение nэ имеет смысл только в том случае если электроприемники входящие в группу значительно разняться по мощности.
При одинаковой мощности электроприемников входящих в группу
где: n– количество ЭП в группе узле цехе
т. е. эффективное число электродвигателей равно фактическому. Поэтому при одинаковых или мало отличающихся мощностях электроприемников группы определение Кмакс производится по их фактическому числу.
Результаты заносятся в таблицу 2.2.
Зная значения nэ и Kи.ср определяли значение коэффициента максимума Кмакс для первого узла по таблице 2.4[2] используя метод интерполяций
Расчётный максимум активной нагрузки всех ЭП. 1.8[2]
где:Pр.– максимальная расчетная активная мощность ЭП в узле и цехе кВт
– суммарная активная средняя мощность нагрузки за наиболее загруженную смену ЭП данной группы кВт.
Kмакс – коэффициент максимума
Рр. = 84311 = 261 кВт
Расчетный максимум активной нагрузки ЭП остальных узлов определялся аналогичным образом результаты в таблице 2.1.
Если nэ ≤10 то Qp = 11Qсм
Если nэ>10 то Qp = Qсм
где: Qр.– максимальная расчетная реактивная мощность ЭП в узле и цехе кВАр
Qр.= 11112 = 123 кВАр
Расчетный максимум реактивной нагрузки для остальных узлов определяется аналогичным образом результаты заносятся в таблицу 2.2.
Полная расчётная максимальная нагрузка группы всех ЭП: 117[2]
где: Sр. – максимальная расчетная полная мощность ЭП в узле и цехе кВА
Полная расчетная максимальная нагрузка остальных узлов определяется аналогичным образом результаты заносятся в таблицу 3.2.
Расчётный (максимальный) ток потребляемый группой ЭП: 1.18[2]
где: Uном. = 038 кВ – номинальное напряжение которым запитываются ЭП в цехе.
Iр. –расчетный ток потребляемый группой ЭП в узле и цехе А
Расчетный (максимальный) ток для остальных узлов определяется аналогичным образом результаты заносятся в таблицу 2.2.
4. Нагрузка цеха с учётом освещения
Кроме заданной номинальной силовой нагрузки в цехе имеется освещение которое тоже было учтено. Освещение цеха в учебных целях допускается рассчитывать по удельной мощности осветительной нагрузки.
Установленная мощность осветительной нагрузки: 1.19[2]
где: Fц – площадь цеха определяется из задания м2;
Руд.– удельная мощность осветительной нагрузки выбирается по табл. 1.7 [2].
Fц всего= 50 30 = 1500 м2
Руст.о. = 00181500 = 27 кВт
Расчётный активный максимум осветительной нагрузки цеха: 1.20[7]
где: Кс.о=085– коэффициент спроса осветительной нагрузки по табл.24.31 [2]
Ррасч.о. = 27085 = 23 кВт
Расчётный реактивный максимум осветительной нагрузки цеха по 1.21[2]
где: = 173 – коэффициент мощности при использовании люминесцентных ламп;
Qрасч.о. =23173=398 кВАР
Расчётный максимум активной нагрузки цеха с учётом освещения: 1.22[2]
= 210 + 23 = 233 кВт (2.24)
Расчётный максимум реактивной нагрузки цеха с учётом освещения: 1.23[2]
= 122 + 398 = 1627 кВАр (2.25)
Полная расчётная нагрузка цеха с учётом освещения:
Расчётный ток потребляемый ЭП цеха с учётом осветительной нагрузки:
Результаты всех расчётов заносятся в таблицу 2.2.
Таблица 2.2. Нагрузка цеха
5. Выбор мощности трансформатора и компенсирующих
устройств на цеховые ТП
Принял что вся реактивная мощность компенсируется на низкой стороне а выбор трансформаторов проводил по полной мощности равной активной расчётной мощности потребляемой цехом без учёта потерь в трансформаторе. Выбор трансформаторов проводил с учётом того что перегрузка в дневные часы компенсируется недогрузкой в ночные.
Формула для расчёта мощности трансформаторов 2.1[2]
Выбрал для инструментального цеха II категорию
где: SН.Т.– номинальная мощность трансформатора кВА;
Кз =07– коэффициент загрузки трансформаторов для II категории.
n – минимальное количество трансформаторов в зависимости от категории. II категория – 2 КТП;
Sн.т .= 250 кВA ≥ 166кВА
Из таблицы 1 [2] принимаются технические данные трёхфазных силовых масляных трансформаторов общего назначения и сводятся в таблицу 2.3.
Таблица 2.3. Справочные данные трансформатора
Расчётный коэффициент загрузки одного трансформатора: 2.2[2]
где: –суммарная мощность всех тех узлов которые подключены к данному трансформатору кВт.
Нагрузка была разбита наиболее рационально:
Трансформатор 1 – I II III узел = 527+287+261 = 1075 кВт
Трансформатор 2 –IV V VI узел и освещение = 295+333+41+ 23 = 1268 кВт
Расчётный коэффициент загрузки каждого трансформатора
Принимаю параллельную работу двух трансформаторов.
Средний расчётный коэффициент загрузки выбранных трансформаторов при компенсации реактивной мощности на низкой стороне: 2.3[2]
где: – суммарная мощность всех трансформаторов кВА
Компенсация реактивной мощности
Конденсаторные установки устанавливаются в цехе для компенсации реактивной мощности из расчета что вся реактивная мощность компенсируется на низкой стороне трансформатора. Реактивная мощность которую необходимо компенсировать на одном трансформаторе:2.4[2]
где: – Реактивная мощность цеха с освещением кВАр;
SН.Т. – номинальная мощность трансформатора кВА;
SН.Т. – суммарная мощность всех трансформаторов питающих цех кВА;
Выбрал на каждый трансформатор конденсаторные установки типа УКРМ-04-100.
Таблица 2.4.Справочные данные конденсаторных установок
Номинальная мощность кВАр
Число и мощность регулируемых ступеней шткВАр
Проверка условия: = 163 кВАр; QкуΣ=200 кВАр; QкуΣ.
Условие выполняется значит будет перекомпенсация реактивной мощности излишки которой выдаются в систему.
6. Расчет сети напряжением до 1000 В
Все ЭП в цехе защищаются автоматическими выключателями. Номинальные КПД и cosφ необходимые для расчета приведены в табл. 2.5 Рном принимаются из таблицы 2.1 кроме крана. У крана ПВ не учитывается для выбора проводников и защитной аппаратуры.
Таблица 2.5. Значение номинального тока для каждого ЭП
Название электроприёмника
Значение номинального тока для универсального заточного станка по формуле: 5.1[2]
где: Рном – номинальная активная мощность ЭП кВт;
Uном.– номинальное напряжение сети кВ;
н. – номинальный коэффициент полезного действия в относительных единицах;
cosφн – номинальный коэффициент мощности.
Аналогично рассчитываются номинальные токи других ЭП.
7. Выбор коммутационной аппаратуры и питающих
кабелей для оборудования
Выбираю питающие кабели и коммутационную аппаратуру для всех ЭП. Автоматические выключатели выбрал по максимальному рабочему (номинальному) току приемника и количеству полюсов из таблицы 2.10[2] а затем рассчитал необходимое значение тока электромагнитного расцепителя.
Коммутационная аппаратура и питающие кабели для универсального заточного станка.
где: Iном. - номинальный ток ЭП А;
Iн.а.–номинальный ток автомата А;
Iэм. – ток электромагнитного расцепителя А;
Iпуск – наибольший кратковременный (пусковой) ток приёмника А.
Наибольший кратковременный (пусковой) ток ЭП А 3.4[2]
где: Кпуск. – пусковой коэффициент ЭП
Кпуск. =5- 75 для двигателей работающих в обычных условиях и для приемников работающих в тяжелых пусковых условиях (мостовой кран) соответственно.
Iпуск = 6 4527 = 272А
Ток электромагнитного расцепителя автомата записывается как: 3.5[2]
где: К – кратность тока которая записывается в виде букв В С D
буквы В С D- означают тип кривой отключения
где: Iном.авт – номинальный ток автоматического выключателя А.
Принимаем тип кривой отключения С - 5÷10 Iн.а
Исходя из полученных данных выбрал автомат S200.
Iн.а = 50АIном = 4527 А
Проводник питающий станок выбирал из условия:
Iдоп.Iн.а.;70 А50 А (2.38)
Выбираю для всех ЭП алюминиевый кабель типа АВВГ проложенный в трубе.
Аналогично выбрал защищающую аппаратуру и проводники для других станков. Результаты занес в таблицу 2.6
Таблица 2.6. Выбор защитной аппаратуры и проводников сети напряжением до 1000 В
8. Выбор распределительных конструкций
По полученному расчётному току Iр выбираем по справочнику кабеля питающие распределительные пункты СП1-СП6
Для приема и распределение электроэнергии к группам потребителей трехфазного переменного тока промышленной частоты напряжением 380В применяют силовые распределительные шкафы и пункты.
Для цехов с нормальными условиями окружающей среды изготавливают шкаф серии ПР11М-107-21УХЛЗ защищенного исполнения.
Для ПР11М-107-21УХЛЗ: 96А 100 А
Аналогичные действия производим для остальных распределительных пунктов полученные расчётные данные заносим в таблицы 2.7.
Таблица 2.7. Типы распределительных шкафов
Тип распределительного шкафа
ТМ-160-РУНН1 (ВА 52-35)
ТМ-160-РУНН2 (ВА 52-35)
9. Выбор защитных автоматических выключателей и питающих кабелей для распределительных шкафов и шинопроводов
Выбор автоматов защищающих все приемники в узле.
Максимальный пиковый ток для группы ЭП при выборе автоматов:
Iр.гр– расчётный ток узла А
Ки – коэффициент использования данного ЭП;
Км – коэффициент максимума данного узла.
Максимальный пиковый ток для группы ЭП при выборе автоматов :
где: =25– коэффициент зависящий от условий пуска электроприемника.
Питающий кабель для узла при защите его автоматом по табл.1 [2] из условий (3.18)(3.24).
Iкр.гр.1 = 394+(96-563)01422 = 406 А
Iкр.гр.РУНН1 = 394+(192-563)014253 = 44216 А
Аналогично рассчитал и для остальных узлов данные ввел в таблицу 2.8.
Выбор защищающих автоматов и питающих кабелей для распределительных шкафов и шинопроводов произвел так же как и для приёмников в отдельности.
Для секций трансформаторов цеха следует учитывать то что защищающий автомат и питающий кабель должны быть рассчитаны на возможность нести нагрузку всего цеха в аварийной ситуации либо в случае ремонта одного из питающих трансформаторов.
Также следует не забывать что защищающий аппарат и питающий кабель с помощью которых будет выполнено резервирование трансформаторов должны быть рассчитаны на ток наиболее загруженной из секций.
Результаты вычислений занес в таблицу 2.8.
Таблица 2.8. Выбор автоматов и кабелей по узлам
№ узла наименование группы
Автоматический выключатель плавкий предохранитель
5×Iпуск.гр А Iпуск.a А
ВЫБОР ОСВЕЩЁННОСТИ СИСТЕМЫ ОСВЕЩЕНИЯ И ИСТОЧНИКА СВЕТА
В настоящее время действует СНиП 25-05-95 «Естественное и искусственное освещение». Эти нормы охватывают естественное и искусственное освещение промышленных предприятий работ на открытом воздухе и др. Нормы промышленного освещения построены на основе классификации работ по определённым количественным признакам.
Таблица 3.1. Наименование освещённости на рабочих поверхностях в производственном помещении
Характеристика зрительной работы
Контраст объекта с фоном
Систему освещения выбираем – общую равномерную.
1. Выбор типа светильников их размещение и высота подвеса
Расчет размещения светильников в станочном отделении:
Высота подвеса – это есть расстояние от рабочей поверхности до центра источника света.
Высоту подвеса светильника над рабочей поверхностью h м определили по [1]
где: Н – высота помещения м;
hс – свес т.е. расстояние от потолка м;
hр – высота рабочей поверхности от пола м.
Высоту свеса светильника приняли
Высоту рабочей поверхности от пола приняли
Расстояние между светильниками L м определили согласно [1]
где l - наивыгоднейшее отношение расстояний между светильниками и расчётной высоте подвеса светильника.
Наивыгоднейшее отношение расстояний между светильниками и расчётной высоте подвеса светильника приняли
Расстояние между светильниками приняли
Наибольшая равномерность освещения имеет место при размещении светильников по углам квадрата. Поэтому принимаем такое размещение светильников в производственном помещении.
Расстояние м от стен до крайнего ряда светильников определили согласно [1]
Расстояние от стен до крайнего ряда светильников приняли
Количество светильников по длине помещения паопределили согласно [1]
где А – длина помещения м;
Количество светильников по ширине помещения пbшт определили согласно [1]
где В – ширина помещения м;
Общее количество светильниковв помещении определили согласно [1]
Расчет размещения светильников в заточном отделении:
Расчет размещения светильников в резьбошлифовальном отделении:
Расчет размещения светильников в вентиляционной:
Так как высота помещения 4 м то берем светильники потолочного типа учитывается только высота рабочей поверхности (hс=0м).
Расчет размещения светильников в санитарном узле:
Расчет размещения светильников в кладовой:
Расчет размещения светильников в инструментальной бытовке складе и комнате отдыха:
2. Расчёт мощности и выбор ламп
Для станочного отделения:
По таблице 5.55 [1] находим коэффициент использования светового потока.
Индекс помещения i определяем согласно формуле
Коэффициент использования светового потока приняли
Световой поток одной лампы Фрасч Лм определили согласно [1]
где Е – нормируемая освещённость цеха;
kз - коэффициент запаса для открытого пространства 13;
S – освещаемая площадь м2;
z – поправочный коэффициент учитывающий неравномерность освещаемой поверхности
Поправочный коэффициент учитывающий неравномерность освещаемой поверхности приняли
Освещённость принимаем согласно [1]
По световому потоку выбираем светодиодный светильник поток которой не отличается от расчётного потока более чем на минус 10 плюс 20 процентов. Данные занесли в таблицу.
С учётом требований к светораспределению условиям среды экономичности по таблице 12.3 [1] выбираем светильник GigaTera SEGA 130.
Таблица 3.2.Основные данные светильника.
Фактическую освещённость определили согласно [1]
где ФЛ – световой поток одной лампы Лм;
Мощность осветительной установки определили согласно [1]
где N – количество ламп шт;
РЛ – мощность одной лампы Вт;
Для заточного отделения:
Таблица 3.3. Основные данные светильника
DURAY Енисей 120.26250.
Для резьбошлифовального отделения:
Таблица 3.4. Основные данные светильника
DURAY Енисей 160.35000.
Таблица 3.5.Основные данные светильника
Для санитарного узла:
Таблица 3.6. Основные данные светильника
LEDVANCE (OSRAM) SURFACE-C LED 350 18W
Таблица 3.7. Основные данные светильника
LEDEL L-industry АЗС 48
Для инструментальной бытовки склада и комнаты отдыха:
Таблица 3.8. Основные данные светильника
Ферекс ДСО 05-24-50Д
Мощность освещения всего цеха с подсобными помещениями будет равна:
3. Выбор схемы питания типа осветительных щитков
Все светильники распределили на 6 групп. Из них 5 расположены в станочном отделении и в каждой такой группе 10 ламп мощностью 130 Вт и мощность группы 13 кВт. Все остальные цеха включены в 6 группу общая мощность которой 35 кВт.
По количеству групп выбрали щиток освещения. Данные занесли в таблицу.
Таблица 3.9. Данные щитка освещения
Тип вводного автомата
Тип линейных автоматов
Количество линейных автоматов
Рабочий ток групповой линии определили по формуле
где N – количество ламп в одной групповой линии шт;
РЛ – мощность лампы Вт;
UС – напряжение сети В.
Линейный автомат для первых пяти групп выбрали [1] на номинальный ток 63 А.
Согласно [1] ток уставки Iуст А расцепителя автомата групповой линии
где Iр – рабочий ток групповой линии А.
Для шестой группы рабочий ток будет равен:
Линейный автомат для шестой группы выбрали на номинальный ток 16 А.
Вводной автомат выбирали по [1] на номинальный ток 50А.
Определили место расположения щитка освещения.
Щиток освещения от которого начинаются групповые осветительные сети располагается в помещении удобном для обслуживания и с нормальными условиями среды.
4. Расчёт и выбор сечений питающей и распределительной сети
После расчёта в групповой линии выбрали провод АПВ 4 мм2 с допустимым током 27А согласно [1] таблица 11.1.
Проверку на нормируемое отношение между допустимым током проводника и номинальным током аппарата защиты осуществили по [1] таблица 10.2
где Iд – допустимый ток А;
Iз – номинальный ток аппарата защиты А.
Необходимое условие выполняется перегрева кабеля не произойдёт.
Длину кабеля от щита освещения к распределительному пункту цеха приняли
Момент нагрузки М2 кВт×м определили согласно [1]
где Росв – мощность осветительной установки кВт;
Ргр – мощность групповой линии кВт.
Необходимое сечение Sрасч2 мм2 определили согласно [1]
Коэффициент для четырёх проводной линии приняли С=77
Кабель для запитки щита освещения от распределительного пункта цеха выбрали марки АПВ (56) мм2 с допустимым током 46 А.
5. Аварийное освещение
Освещенность от источников аварийного освещения определили согласно [1]
где Ен – нормируемая освещённость по цеху Лк.
Необходимый световой поток определили согласно [1]
где S – площадь помещения м2.
Таблица 3.10. Технические характеристика лампы накаливания
Необходимое количество ламп nав определили согласно 1 с.333 по формуле
где Фл – световой поток лампы Лм.
К установке приняли 18 ламп. Лампы подключения через щиток аварийного освещения запитанный от другого ввода.
По [1] таблице 11.17 выбрали щиток аварийного освещения
Таблица 3.11. Данные щитка аварийного освещения
Тип линейного автомата
Количество автоматов
Необходимый ток уставки автомата Iуст А определили согласно [1]
По расчётному току уставки выбрали автомат с комбинированным расцепителем с Iуст=25 А.
Необходимое сечение аварийной групповой сети определили согласно [1]
Мощность нагрузки P3 кВт определили согласно [1]
где Рав – мощность аварийного освещения кВт.
По таблице 11.1 [1] выбрали двухжильный провод ПРТО с Sн=10 мм2.
ОРГАНИЗАЦИЯ РЕМОНТА ЭЛЕКТРООБОРУДОВАНИЯ
Сущность системы планово-предупредительных ремонтов (ППР) заключается в том что каждый агрегат станок электромашина трансформатор и вся электроаппаратура подвергаются через определенные промежутки времени плановым профилактическим осмотрам и различным видам ремонта. Длительность этих промежутков определяется особенностями конструкции агрегата его техническим значением и условиями эксплуатации.
Система ППР включает в себя два вида работ: периодическое выполнение плановых ремонтов и межремонтное обслуживание.
За ремонтный цикл принимают цикл между двумя капитальными ремонтами состоящий из нескольких текущих и одного капитального ремонта для электрооборудования находящегося в эксплуатации.
Для вновь установленного электрооборудования – период работы от ввода его в эксплуатацию до первого капитального ремонта.
Межремонтным периодом называется время работы электрооборудования от одного вида ремонта до следующего ремонта.
Структурой ремонтного цикла называется чередование ремонтов в определенной последовательности и через определенные промежутки времени.
Таблица 4.1. Нормы продолжительности ремонтного цикла межремонтного периода электрических машин
Условия работы электрических машин
Расчетный коэффициент спроса (Кс)
Продолжительность ремонтного цикла
Продолжительность межремонтного периода tтабл мес.
Сухие помещения (цеха холодной обработки металла и им подобные)
Количество часов плановых ремонтов всех видов (РК и РТ) в течение ремонтного периода определяется по формулам:
Капитальные ремонты
где ТК – время затрачиваемое на капитальный ремонт единицы оборудования
N – количество единиц оборудования
где Тт – время затрачиваемое на капитальный ремонт единицы оборудования
Так как я рассчитываю часы ремонтов за период в один года то для капитального ремонта формула примет следующий вид:
где РК1 – количество часов на капитальный ремонт в течение всего межремонтного периода
Ттабл – продолжительность ремонтного цикла
Для асинхронных двигателей работающих в сухих помещениях продолжительность ремонтного цикла составляет 12 лет. Между текущими ремонтами – 12 месяцев.
Для АД мощностью 16-3 кВт капитальный ремонт с перемоткой обмоток – 13ч без перемотки обмоток – 7 часов. Условно принимаем что 1 двигатель перематывается а 2 нет. Исходя из этого количество часов капитального ремонта составляет:
Так как капитальный ремонт проводится раз в 12 года следовательно время необходимое для капитального ремонта в год составляет:
Для АД мощностью 31-55 кВт капитальный ремонт с перемоткой обмоток – 15ч без перемоток – 8ч. Условно принимаем что 2 двигателя перематываются а 2 нет. Исходя из этого количество часов капитального ремонта составляет:
Так как капитальный ремонт проводится раз в 12 лет следовательно время необходимое для капитального ремонта в год составляет:
Для АД мощностью 56-10 кВт капитальный ремонт с перемоткой обмоток – 20ч без перемоток – 11ч. Условно принимаем что 1 двигатель перематывается а 2 нет. Исходя из этого количество часов капитального ремонта составляет:
Для АД мощностью 101-17 кВт капитальный ремонт с перемоткой обмоток – 27ч без перемоток – 14ч. Условно принимаем что 9 двигателей перематываются а 9 нет. Исходя из этого количество часов капитального ремонта составляет:
Для АД мощностью 171-22 кВт капитальный ремонт с перемоткой обмоток –32ч без перемоток – 17ч. Условно принимаем что 5 двигателей перематываются а 6 нет. Исходя из этого количество часов капитального ремонта составляет:
Для АД мощностью 221-30 кВт капитальный ремонт с перемоткой обмоток – 40ч без перемоток – 21ч. 1 двигатель перематывается. Исходя из этого количество часов капитального ремонта составляет:
Масляные выключатели ток до 1000А ВМ-10 количество 2шт. Продолжительность ремонтного цикла для масляного выключателя составляет – 12 лет продолжительность межремонтного периода – 3 года. Норма времени на капитальный ремонт – 136 часов на текущий – 44 часа.
Так как текущий ремонт проводится раз в 3 года следовательно время необходимое для текущего ремонта в год составляет:
Продолжительность ремонтного цикла для силовых трансформаторов на напряжение 10 кВ мощностью 160 кВА составляет – 12 лет продолжительность межремонтного периода – 3 года. Норма времени на капитальный ремонт – 919 часов на текущий – 85 часов. Мы имеем 2 трансформатора.
РК1 = 9192:12=153 часа
РТ = 285:3=56 часов.
Продолжительность ремонтного цикла для силовых щитков составляет – 144 месяца продолжительность межремонтного периода – 12 месяцев. Имеются 2 распределительных шкафа с 10 автоматическими выключателями 1 с 8 1 с 6 и 2 с 4. Норма времени на капитальный ремонт – 50 40 30 и 20 часов соответственно на текущий – 16 14 10 и 8 часов соответственно. Так как капитальный ремонт проводится раз в 12 лет следовательно время необходимое для капитального ремонта в год составляет:
РК1 = (250+140+130+220) :12=1752 часов
РТ = 162+14+10+82) :1=72 часа.
Продолжительность ремонтного цикла для щитков освещения составляет – 144 месяца продолжительность межремонтного периода – 12 месяцев. Норма времени на капитальный ремонт – 18 часов на текущий – 6 часов.
РК1 = 118:12=15 часа
Капитальный ремонт сетей силовых в сухих помещениях проводят раз в 144 месяцев текущий – раз в 12 месяцев. Норма времени на каждые 100 м линии АВВГ(5х25) при текущем ремонте – 35 часа при капитальном – 11 часов.
РК1 = 600:10011:12=55 ч
Время необходимое для текущего ремонта составляет:
Капитальный ремонт сетей силовых в сухих помещениях проводят раз в 144 месяцев текущий – раз в 12 месяцев. Норма времени на каждые 100 м линии АВВГ(3х95+2х20) при текущем ремонте – 42 часа при капитальном – 14 часов. Так как капитальный ремонт проводится раз в 12 лет следовательно время необходимое для капитального ремонта в год составляет:
РК1 = 600:10014:12=7 ч
Ремонты осветительных сетей проводят в те же промежутки времени. Норма времени на каждые 100 м линии при текущем ремонте – 6 часов при капитальном – 20часов. Так как капитальный ремонт проводится раз в 12 лет следовательно время необходимое для капитального ремонта в год составляет Время необходимое для капитального ремонта в год составляет:
РК1 = 600:10020:12=10ч
Капитальный ремонт светильников светодиодных не проводится. Меж ремонтный период 6 месяцев. Норма времени – 2 часа на 10 светильников.
Количество часов в год:
РК1 = 127:1022=51чгод
На основании данных вычислений создал график ППР и таблицу 4.2. Таблица 4.2.Трудоемкость ремонтов и продолжительность межремонтных периодов
1. Расчёт количества рабочих для выполнения работ
согласно с графиком ППР
Расчет численности вспомогательных рабочих
Количество рабочих необходимое для выполнения всех работ мы определяли на каждый вид оборудования по формуле:
где Т – общее количество часов необходимое для ремонта данного вида оборудования-53865ч ;
Е – годовой эффективный фонд рабочего времени 1664ч.
N = 53865:1664 = 033
Сложив все полученные результаты определили что для выполнения всех работ нужен 1 электромонтера 5 разряда.
Расчет фонда заработной платы вспомогательных рабочих
Расчёт годового фонда заработной платы дежурного персонала рассчитывали с учетом часовой тарифной ставки электромонтера 5 разряда – 1753р; Дополнительно к тарифному фонду заработной платы полагаются премии в размере 50%.
ЗП = 1 · 1753 · 1664 · 15 = 43 755р
Годовой фонд заработной платы составит 43 755 рублей.
Расчет годового расхода электрической энергии
Годовой расход электроэнергии на освещение Эосв кВт определяли согласно
где Р – мощность одной лампы Вт;
Т – годовое количество часов использования максимального освещения нагрузки 3200ч;
N – количество ламп шт.
Эосв = 10000 · 32001000 =32000 кВт · ч
Годовой расход энергии потребляемой электродвигателями Ээ.д. кВт определяли согласно формуле:
где Рн – мощность электродвигателя;
Кс – коэффициент спроса 075;
Т – эффективный фонд работы оборудования 1664ч;
nс – коэффициент одновременной работы электродвигателей 096;
эд – КПД электродвигателя 098.
Ээ.д. = 555 · 075 · 1664096 · 098 = 707 070 кВт · ч
Общий расход электроэнергии
Эобщ = 32000 + 707070 = 739 070
Общий расход электроэнергии составляет 739 070 кВтч.
1. Мероприятия по технике безопасности при эксплуатации токарных станков с ЧПУ
Современные станки обычно имеют личный электропривод. Почти всегда электродвигатели реле и другие электронные аппараты расположены либо на самом станке либо в раздельно стоящем шкафу.
Работу по наладке эксплуатации и ремонту электрического оборудования станков делят на четыре категории:
работы при полном снятии напряжения
работы с частичным снятием напряжения
работы без снятия напряжения вблизи токоведущих шин
работы без снятия напряжения вдали от токоведущих шин.
Работой при полном снятии напряжения считается работа которую делают в электроустановке где со всех токоведущих частей снято напряжение и где нет незапертого входа в соседнюю электроустановку находящуюся под напряжением.
К такому виду работ относятся:
а) прозвонка цепей силовой схемы
б) ремонт либо замена электронной аппаратуры конкретно на станке
в) проверка величины сопротивления изоляции токоведущих частей.
Работой с частичным снятием напряжения считается работа которую проводят на отключенных частях электроустановки в то время как другие ее части находятся под напряжением либо напряжение снято стопроцентно но есть незапертый вход в соседнюю электроустановку находящуюся под напряжением.
а) регулировка характеристик срабатывания реле
б) регулировка и очистка контактов аппаратов
в) смена ламп освещения в шкафу и на станке.
Работой без снятия напряжения вблизи и на токоведущих частях считается работа которая просит принятия технических и организационных мер и делается на не отключенной электроустановке с применением защитных средств.
К такому виду работ относятся: измерение величин тока и напряжения при помощи измерительных клещей.
Работой без снятия напряжения вдалеке от токоведущих частей считается работа при которой исключено случайное приближение работающих людей и применяемых ими ремонтной оснастки и инструмента к токоведущим частям на опасное расстояние и не требуется принятия технических и организационных мер для предотвращения такового приближения.
а) протирка пультов и шкафов управления с внешней стороны
б) протирка электродвигателей станка
в) измерение частоты вращения движков тахометром
Работу по наладке электрического оборудования станков должны делать более чем два лица старший из которых — производитель работ — обязан иметь квалификационную группу не ниже третьей а второй — член бригады — не ниже второй.
Наладочные работы создают по устному либо письменному распоряжению ответственного управляющего работ (начальника электролаборатории механика мастера эксплуатации либо старшего электромонтера) который инспектирует наличие у производителя удостоверения на право допуска к работам на электрическом оборудовании дает задание на наладку и обеспечивает его технической документацией (принципиальной электронной схемой и спецификацией к ней).
Конкретно перед допуском бригады к работе допускающий (дежурный электромонтер либо ответственный управляющий работ) инспектирует:
а) наличие у членов бригады удостоверений на право работы
б) познание производителем работ «Правил технической эксплуатации электроустановок потребителей» «Правил техники безопасности при
эксплуатации электроустановок потребителей» и электронной схемы настраиваемого оборудования
в) обеспечение безопасного производства работ на рабочем месте.
До работы производитель работ подготавливает рабочее место: выключатель пульта управления станком устанавливает в положение «Отключено» и вывешивает плакат «Не включать — работают люди» осматривает техническое состояние пульта шкафа с электрическим оборудованием: подготавливает защитные средства - коврики диэлектрические перчатки монтерский инструмент подготавливает электроизмерительные и другие приборы нужные при наладке.
После проведения предварительных работ производитель разрешает бригаде приступить к работе. Во время наладки электрического оборудования бригаде разрешается делать последующие работы:
а) проверку правильности выполнения монтажа
б) включение и отключение оборудования
в) манипуляции элементами управления (клавишами тумблерами командоаппаратами на станке и щите управления
г) выявление изъянов оборудования методом его осмотра
д) замену дефектных мест монтажа вторичной коммутации и силовой схемы
е) замену дефектного оборудования
ж) измерение характеристик схемы переносными измерительными устройствами
з) испытание электрического оборудования станка завышенным напряжением
и) измерение сопротивления изоляции катушек аппаратов и обмоток электронных машин мегомметром
к) испытание электрического оборудования станка при холостом ходе и под нагрузкой.
Проверку изъянов монтажной схемы разрешается проводить лишь на стопроцентно отключенном оборудовании. Осмотр электрического оборудования с целью выявления его изъянов можно создавать без снятия напряжения производителем работ через открытую дверь в присутствии второго лица из состава бригады.
Замену вышедших из строя аппаратов проводят при полном снятии напряжения при всем этом на ручке вводного автомата либо рубильника должен быть вывешен плакат «Не включать — работают люди».
При подаче напряжения на отдельные участки схемы по временным перемычкам должны быть обеспечены условия безопасной работы для других членов бригады занятых на наладке аппаратуры установленной на станке либо в другом шкафу. При подаче напряжения на всю схему нужно поставить ограждения в местах доступных для проникания посторонних лиц и вывесить плакат «Стой! Опасно для жизни!».
При замене предохранителей измерениях переносными устройствами и мегомметром нужно воспользоваться защитными средствами. Перед применением защитных средств нужно убедиться в том что срок использования ими не истек (для диэлектрических перчаток он составляет 6 месяцев для диэлектрических ковриков 2 года для монтерского инструмента с изолированными ручками 1 год.) Сразу нужно убедиться в механической целостности диэлектрических перчаток. При обнаружении прорывов и других механических повреждений использовать защитными средствами воспрещается.
Исходя из вероятности травматизма более ответственными и небезопасными являются тесты работы станка вхолостую и под нагрузкой потому что в процессе ремонта либо наладки могут быть не выявлены и не устранены некие недостатки оборудования действующие на безопасность работы на станке. Потому проверку работы станка вхолостую и под нагрузкой нужно проводить с большой осторожностью.
Перед проверкой работы станка убирают с него посторонние предметы вместе с механиком убеждаются в правильной работе кинематической схемы инспектируют крепление всех аппаратов электронных машин состояние и работу предохранительных и блокировочных устройств действие остановочных пусковых и реверсирующих устройств переключающих рукояток фрикционных муфт путевых выключателей.
Перед запуском станка уясняют последовательность операции включения и отключения головного привода и приводов подач убеждаются в правильном подключении электродвигателей их направление вращения должно соответствовать требованиям паспорта.
Первоначальное опробование станка под нагрузкой необходимо производить на самых низких оборотах и при самых легких режимах с постепенным повышением загрузки станка. При испытании станка под нагрузкой следует строго следовать правилам техники безопасности относящимся к выполняемой на нем работе и вытекающими из его конструктивных особенностей.
Техническую эксплуатацию электрического оборудования станков необходимо производить руководствуясь действующими «Правилами технической эксплуатации электроустановок потребителей» и «Правилами техники безопасности при эксплуатации электроустановок потребителей».
2. Обеспечение электробезопасности при эксплуатации электрооборудования
Электрозащитные средства (ЭЗС) – это переносимые и перевозимые средства служащие для защиты людей работающих с электроустановками от поражения электрическим током от воздействия электрической дуги и электромагнитного поля.
Электрозащитные средства для электроустановок напряжением до 1000 В.
Основные электрозащитные средства в электроустановках напряжением до 1000 В.
Основными электрозащитными средствами в электроустановках напряжением до 1000 В являются диэлектрические перчатки изолирующие штанги изолирующие и электроизмерительные клещи слесарно-монтажный инструмент с изолирующими рукоятками и указатели напряжения.
Наиболее широкое применение находят диэлектрические перчатки изготовленные из резины. Перед применением перчатки необходимо проверить на герметичность. Применять негерметичные перчатки запрещается.
Слесарно-монтажный инструмент с изолирующими рукоятками применяют при выполнении работ под напряжением 220380 В. Обычно используют односторонние гаечные ключи отвертки плоскогубцы кусачки ножи с изолирующими рукоятками. Изоляция рукояток инструмента изготовленная из пластмассы является основным средством зашиты.
Для проверки наличия или отсутствия напряжения на токоведущих частях без определения его значения служат указатели напряжения: двухполюсные работающие при активном токе— для электроустановок переменного и постоянного тока напряжением до 500 В и однополюсные работающие при емкостном токе — для электроустановок переменного тока напряжением до 380 В. Сигнализатором служит газоразрядная индикаторная лампа. Двухполюсные указатели напряжения имеют два щупа соединенные гибким проводником.
Рис.5.1. Индивидуальные электрозащитные средства:
Для их работы необходимо одновременное прикосновение к двум фазам или к одной фазе и нулевому проводу. Однополюсные указатели напряжения выполняют в виде авторучки. Для их работы достаточно прикоснуться щупом к одной токоведущей части электроустановки и рукой — к металлическому контакту в верхней части конструкции. При этом ток протекает через тело человека и землю. Однополюсные указатели рекомендуется применять при проверке схем вторичной коммутации определения фазного провода при подключении электросчетчиков патронов выключателей предохранителей и т. п.
Изолирующие клещи применяют для операций со вставками трубчатых предохранителей а также для надевания на ножи однополюсных разъединителей и снятия колпаков. Изолирующие клеши выполняют из пластмассы.
Дополнительные электрозащитные средства в электроустановках напряжением до 1000 В.
Дополнительными электрозащитными средствами являются диэлектрические галоши (боты) сапоги диэлектрические резиновые коврики дорожки и изолирующие подставки.
Диэлектрические боты галоши и сапоги применяют для изоляции человека от основания на котором он стоит. Боты применяют в электроустановках любого напряжения а галоши и сапоги — только при напряжении до 1000 В.
Диэлектрические коврики и дорожки — это изолирующие основания. Их применяют в закрытых электроустановках любого напряжения.
Изолирующие подставки также изолируют человека от грунта или пола. В электроустановках напряжением до 1000 В изолирующие подставки выполняют без фарфоровых изоляторов а выше 1000 В — обязательно на фарфоровых изоляторах.
3. Организационные требования пожарной безопасности для инструментального цеха
Настоящая инструкция устанавливает требования пожарной безопасности для инструментального цеха и является обязательной для исполнения всеми рабочими служащими и инженерно-техническими работниками.
Ответственность за пожарную безопасность производственного цеха (участка) несет должностное лицо установленное соответствующим приказом. Весь персонал работающий в цехе должен быть проинструктирован о мерах пожарной безопасности знать основные требования «Правил пожарной безопасности» порядок действий при обнаружении пожара и эвакуации людей расположения средств пожаротушения сообщения о пожаре и уметь ими пользоваться.
Каждый работающий (независимо от занимаемой должности) обязан знать строго соблюдать и поддерживать установленный противопожарный режим не допускать действий которые могут привести к пожару докладывать обо всех нарушениях требований пожарной безопасности своему руководителю.
Лица нарушающие требования инструкций по пожарной безопасности несут ответственность в установленном законом порядке.
Требования пожарной безопасности к помещениям
На дверях всех производственных и складских помещений расположенных в производственном цехе (электрощитовые вентиляционные камеры и т.д.) надлежит обозначить категории пожарной и взрывопожарной опасности а также класс зоны по правилам устройства электроустановок. Определение категории осуществляется расчетом.
Противопожарные системы и установки (средства пожарной автоматики системы противопожарного водоснабжения противопожарные двери другие защитные устройства в противопожарных стенах перекрытиях и т.п.) помещений должны постоянно содержаться в исправном рабочем состоянии. Использование данных систем не по прямому назначению запрещено.
При пересечении противопожарных преград различными коммуникациями зазоры между ними и конструкциями преград (на всю их толщину) должны быть герметично заделаны негорючим материалом.
Наружные пожарные лестницы и ограждения на крышах здания должны содержаться в исправном состоянии и не менее двух раз в год испытываться на прочность с оформлением актов.
Во всех помещениях на видных местах должны быть вывешены таблички с указанием номера вызова пожарной охраны 101.
Спецодежда лиц работавших с маслами лаками красками и другими ЛВЖ и ГЖ должна храниться в подвешенном виде в металлических шкафах установленных в специально отведённых для этой цели местах.
Ежедневно по окончанию работы помещения необходимо тщательно осматривать рабочие места - убирать электрооборудование и электросети – обесточивать (за исключением оборудования которое должно работать круглосуточно по функциональному назначению и (или) предусмотрено требованиями инструкции по эксплуатации).
В здании производственного цеха должны быть разработаны и на видных местах вывешены поэтажные планы эвакуации людей в случае пожара а также предусмотрена система оповещения людей о пожаре. К плану эвакуации людей при пожаре в дополнение разрабатывается инструкция определяющая действия персонала по обеспечению быстрой и безопасной эвакуации людей.
Требования пожарной безопасности к электроустановкам
Лицо ответственное за состояние электроустановок определяется соответствующим приказом.
Эксплуатацию электрических сетей электроустановок и электротехнических изделий а также контроль за их техническим состоянием необходимо осуществлять в соответствии с требованиями нормативных документов по электроэнергетике и правилам пожарной безопасности.
Электроустановки и бытовые электроприборы в помещениях в которых по окончании рабочего времени отсутствует дежурный персонал должны быть обесточены за исключением дежурного освещения установок пожаротушения и противопожарного водоснабжения пожарной и охранно-пожарной сигнализации. Другие электроустановки и электротехнические изделия могут оставаться под напряжением если это обусловлено их функциональным назначением и (или) предусмотрено требованиями инструкции по эксплуатации.
Проверка электрических сетей электроприемников замер сопротивления изоляции и другие измерения должны производиться не реже 1 раза в год специализированной организацией имеющей лицензию.
Световые указатели «ВЫХОД» должны находиться в исправном состоянии и постоянно быть включенными. Проверка исправности световой и табличной аварийной индикации должна осуществляться не реже 1 раза в квартал.
Переносные электрические светильники должны быть выполнены с применением гибких электропроводок оборудованы стеклянными колпаками а также защищены предохранительными сетками и снабжены крючками для подвески.
При эксплуатации электроустановок запрещается:
Использовать приемники электрической энергии (электроприемники) в условиях не соответствующих требованиям инструкций организаций-изготовителей или приемники имеющие неисправности которые в соответствии с инструкцией по эксплуатации могут привести к пожару а также эксплуатировать электропровода и кабели с поврежденной или потерявшей защитные свойства изоляцией;
Пользоваться повреждёнными розетками рубильниками и другими электроустановочными изделиями.
Эксплуатировать электролампы и светильники со снятыми колпаками предусмотренными конструкцией светильника
Применять нестандартные (самодельные) электронагревательные приборы использовать некалиброванные плавкие вставки или другие самодельные аппараты зашиты от перегрузок и короткого замыкания.
Пользоваться электроплитками электрочайниками и другими электронагревательными приборами не имеющими устройств тепловой защиты без подставок из негорючих теплоизоляционных материалов исключающих опасность возникновения пожара;
Размещать у электрощитов электродвигателей и пусковой аппаратуры горючие (в том числе легковоспламеняющиеся) вещества и материалы.
Рис.5.2. Запасный выход Рис.5.3. Номер вызова Рис.5.4. Наружная пожарная
пожарной охраны лестница
В дипломном проекте я рассмотрел виды назначение и технические характеристики токарных станков с ЧПУ в целом в частности - токарно-винторезного станка с ЧПУ CKE6150Z изучил его схему и принцип действия технологию ремонта а также инструкцию по эксплуатации.
Была спроектирована и рассчитана система технической эксплуатации и обслуживания электротехнического и электромеханического оборудования инструментального цеха завода «Прибор».
В ходе расчёта были детально рассмотрены вопросы электроснабжения цеха и его освещение была выбрана питающая сеть цеха: кабели провода условия их прокладки. Для осветительной сети были выбраны типы ламп и светильников разработаны схемы питания освещения.
Выполнен расчет графика ППР согласно которому рассчитана численность вспомогательных рабочих и фонд их заработной платы. Составлены инструкции по эксплуатации электрооборудования. Разработаны мероприятия по технике безопасности при их эксплуатации.
Также были рассмотрены мероприятия пожарной безопасности.
В результате проектирования была разработана простая и надёжная система технической эксплуатации и обслуживания электротехнического и электромеханического оборудования инструментального цеха и выполнены монтажные чертежи освещения и силовых сетей.
Для расчетов была использована литература указанная в перечне.
Кнорринг Г.М. Фадин И.М. Сидоров В.Н. Справочная книга для проектирования электроосвещения. -2-е изд. перераб. и доп. - Санкт-Петербург: Издательство «Энергоатомиздат» 1997.-448с
.А.В. Кабышев С.Г.Обухов «Расчет и проектирование систем электро-снабжения: справочные материалы по электрооборудованию» Томск 2005
Сибикин Ю.Д. Техническое обслуживание ремонт электрооборудования и сетей промышленных предприятий. В 2 кн. Кн 1: учебник для нач проф. образования Ю.Д.Сибикин. -4-е изд. перераб. И доп. - М.: Издательский центр «Академия» 2012.-208с
Сибикин Ю.Д. Техническое обслуживание ремонт электрооборудования и сетей промышленных предприятий. В 2 кн. Кн 2: учебник для нач проф. образования Ю.Д.Сибикин. -4-е изд. перераб. И доп. - М.: Издательский центр «Академия» 2012.-256с.
Сибикин Ю.Д. Электробезопасность при эксплуатации электрических установок промышленных предприятий: учебник для нач проф. образования Ю.Д.Сибикин М.Ю.Сибикин - М.: Издательский центр «Академия» 2012.-240с
«Система технического обслуживания и ремонта энергетического оборудования» справочник под ред. А.И. Ящура -2-е изд. испр. - М.: Издательский центр «Академия» 2008.-368с
Шеховцов В.П. Электрическое и электромеханическое оборудование: учебник В.П. Шеховцов -2-е издание - М.: ФОРУМ: ИНФРА - М. 2013.-416с.
Рекомендуемые чертежи
- 24.05.2017
- 16.06.2019
- 27.11.2021