Сцепление автомобиля категории М1 полной массой 1400 кг



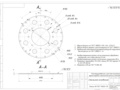
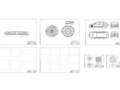
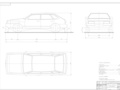
- Добавлен: 04.11.2022
- Размер: 29 MB
- Закачек: 1
Описание
Состав проекта
![]() |
![]() ![]() ![]() |
![]() |
![]() |
![]() |
![]() |
![]() |
![]() |
![]() |
![]() |
![]() |
![]() ![]() |
![]() |
![]() |
![]() |
![]() |
![]() |
![]() |
![]() |
![]() |
![]() |
![]() |
![]() |
![]() |
![]() |
![]() |
![]() |
![]() |
![]() |
![]() |
![]() |
![]() |
![]() |
![]() |
![]() |
![]() |
![]() |
![]() ![]() ![]() |
![]() |
![]() |
![]() |
![]() ![]() |
![]() |
![]() |
![]() |
![]() |
![]() |
![]() |
![]() |
![]() |
![]() |
![]() |
![]() |
![]() |
![]() |
![]() |
![]() |
![]() ![]() ![]() ![]() |
![]() |
![]() |
![]() |
![]() ![]() ![]() |
![]() ![]() |
![]() |
![]() |
![]() |
![]() |
![]() |
![]() |
![]() |
![]() |
![]() |
![]() |
![]() |
![]() |
![]() |
![]() |
![]() |
![]() |
![]() |
![]() |
![]() |
![]() |
![]() |
![]() ![]() ![]() ![]() |
![]() ![]() ![]() ![]() |
![]() ![]() ![]() |
Дополнительная информация
спецификация.doc
Пластинчатая пружина
пластинчатая пружина
Конструирование и расчет наземных транспортно-технологических комплексов
МГТУ им. Н. Э. Баумана Группа СМ10-11М
расчет ведомого диска.docx
Определение диаметра заклепок соединяющих диск со ступицей
где: - средний радиус трения расположения заклепок; - число дисков; – число заклепок; - диаметр заклепок; - коэффициент приспосабливаемости двигателя:
где: – максимальный крутящий момент ДВС; - максимальный момент соответствующий максимальной мощности.
где: - толщина диска.
Исходные данные к расчету
Из двух значений и выбираем большее и округляем до стандартной величины.
Чертеж1.dwg а3.dwg

МГТУ им. Н. Э. Баумана Кафедра СМ10 Группа СМ10-11М
Конструирование и расчет наземных транспортно-технологических комплексов
Общие допуски по ГОСТ 30893.1: H14
±IT142. 2. Общие допуски формы и расположения по ГОСТ 30893.2 - К. 3. Предельные отклонения размеров радиусов скруглений и высот фасок по ГОСТ 30893.1 - m 1. Необразмеренные кромки после машинной обработки притупить или снять фаску 0
мм. 2. Необразмеренные кромки после резки скруглить R0
3. Покрытие: грунтовка ГФ-0121
эмаль МЧ-123 черная ТУ 6-10-979-84.02. 4. Покрытие: Ц15.хр ГОСТ 9.306-85.
макар спецификация.doc
Пластинчатая пружина
пластинчатая пружина
Конструирование и расчет наземных транспортно-технологических комплексов
МГТУ им. Н. Э. Баумана Кафедра СМ10 Группа СМ10-11М
листы.dwg

Сталь 50 ГОСТ 16523-70
Ступица ведомого диска
Общий вид автомобиля Чертеж общего вида
Сцепление Сборочный чертеж
Детали сцепления Электронная модель
МГТУ им. Н. Э. Баумана Группа СМ10-11М
МГТУ им. Н. Э.Баумана Группа СМ10-11М
МГТУ им. Н. Э. Баумана Кафедра СМ10 Группа СМ10-11М
Технические характеристики
Полная масса 1600 кг. 2. Двигатель: Тип: бензин. Объем двигателя
см^3: 1598. Максимальная мощность
л.с.кВт при обмин: при 6000. 3. Максимальная скорость: 185. 4. Трансмиссия: Коробка передач: механика. Количество передач: 5. Тип привода: передний.
Конструирование и расчет наземных транспортно-технологических комплексов
Нормальный исходный контур
Число зубьев в длине общей нормали
Общие допуски по ГОСТ 30893.1: H14
±IT142. 2. Общие допуски формы и расположения по ГОСТ 30893.2 - К. 3. Предельные отклонения размеров радиусов скруглений и высот фасок по ГОСТ 30893.1 - m 4. Необразмеренные кромки после машинной обработки притупить или снять фаску 0
мм. 5. Необразмеренные кромки после резки скруглить R0
6. Покрытие: грунтовка ГФ-0121
эмаль МЧ-123 черная ТУ 6-10-979-84.02. 7. Покрытие: Ц15.хр ГОСТ 9.306-85.
±IT142. 2. Общие допуски формы и расположения по ГОСТ 30893.2 - К. 3. Предельные отклонения размеров радиусов скруглений и высот фасок по ГОСТ 30893.1 - m
общий вид.dwg

Полная масс: 1395 кг.
Максимальная скорость 160 кмч.
Объем двигателя 1499 см^3
Максимальная мощность л.с. при обмин 78 при 3000
Коробка передач механника
Количество передач 5
Тип привода передний
Технические требования
Размеры для справок.
Размеры для автомобиля полной массы.
МГТУ им. Н. Э. Баумана
Конструирование и расчет наземных
транспортно-технологических комплексков
пояснительная записка кп Алимова.docx
Федеральное государственное бюджетное образовательное учреждение
«Московский государственный технический университет
(национальный исследовательский университет)»
(МГТУ им. Н.Э. Баумана)
ФАКУЛЬТЕТ «Специальное машиностроение»
КАФЕДРА «Колесные машины»
РАСЧЕТНО-ПОЯСНИТЕЛЬНАЯ ЗАПИСКА
К КУРСОВОМУ ПРОЕКТУ РАБОТА
Сцепление автомобиля категории М1 полной массой
Студент группы СМ10-11МА. М. Алимова
Руководитель курсового проектаЯ. Ю. Левенков
НормоконтролерР. Б. Гончаров
Расчетно-пояснительная записка состоит из 33 стр. 15 рис. 4 источника.
СЦЕПЛЕНИЕ ПРОЧНОСНОЙ РАСЧЕТ РАСЧЕТ РАСЧЕТ В ANSYS ДИАФРАГМЕННАЯ ПРУЖИНА.
Объектом работы является сцепление автомобиля категории М1 полной массой 1400 кг.
Курсовая работа содержит текстовую часть пояснительную записку в которую входят основные сведения о рассматриваемом объекте проектирования и приложение содержащее спецификацию к сборочному чертежу узла сцепления.
Цель работы – выполнить реинженеринг узла краткий анализ конструкции начертить 3D модели изучить назначение и принцип работы агрегатов сцепления.
Объект проектирования6
Анализ конструкций сцеплений8
Классификация сцеплений9
Расчет основных деталей сцепления19
1 Порядок проектирования сцепления19
2 Нажимные тарельчатые пружины20
5 Прочностной расчет диафрагменной пружины25
СПИСОК ИСПОЛЬЗОВАННЫХ ИСТОЧНИКОВ33
Сцепление - это механизм трансмиссии передающий крутящий момент двигателя и позволяющий кратковременно отсоединять двигатель от трансмиссии и вновь плавно их соединять. Конструкция сцепления должна обеспечивать ряд требований: - надежная передача крутящего момента от двигателя к трансмиссии; обеспечение плавного включения; полное выключение таким образом полное отсоединение ведомых деталей от ведущих; надежная работа при нагреве особенно интенсивном в процессе переключения передач в тяжелых условиях эксплуатации высокая износостойкость пар трения; обеспечение возможности снижения динамических нагрузок в трансмиссии особенно при резком включении сцепления минимальные массы и момент инерции ведомых элементов сцепления; возможность применения приводов снижающих усилия водителя при включении и выключении сцепления; гашение высокочастотных колебаний вызываемых работой двигателя.
В данном курсовом проекте выполнен реинжиниринг сцепления и проведен расчет на прочность для диафрагменной пружины.
Объект проектирования
В данном курсовом проектировании будет спроектирован механизм сцепления легкового автомобиля категории М1 полной массой 2000 кг. Будут рассмотрены виды сцепления аспекты работы данного механизма произведены расчеты построены 3D модели данного механизма и рабочие чертежи.
Сцепление – это механизм трансмиссии передающий крутящий момент от двигателя и позволяющий кратковременно отсоединять его от трансмиссии.
Требования предъявляемые ко всем агрегатам и механизмам:
Обеспечение минимальных размеров и массы;
Простота в использовании;
Простота в обслуживании;
Ремонтнопригодность;
Низкий уровень шума;
Анализ конструкций сцеплений
Сцепление предназначено для кратковременного разойденения двигателя и трансмиссии при переключении передач для плавного трогания с места предотвращение воздействия на двигатель черезмерных нагрузок возникающих при перемене различных режимов.
К сцеплениям предъявляются следующие основные требования:
Чистота выключения и включения;
Плавность включения;
Минимальный момент инерции ведомой части сцепления;
Хорошая уравновешенность;
Постоянство осевых усилий и момента трения сцепления независимо от износа накладок;
Гашение высокочастотных колебаний вызываемых работой двигателя;
Нормальный тепловой режим работы;
Обеспечение условий труда водителя легкость и удобство управления;
Высокие технико-экономические показатели;
Безотказность в работе;
Обеспечение охраны окружающей среды.
Классификация сцеплений
По способу передачи крутящего момента сцепления подразделяют на:
Электромагнитные порошковые.
В зависимости от формы поверхности трения различают различают:
По способу создания давления на рабочих поверхностях сцепления различают на:
По числу ведомых дисков:
У первых двух смазка на поверхностях трения отсутствует и сцепление называют «сухим» у последних диски работают в масле т. е. имеет место «мокрое» сцепление.
В большинстве колесных машинах применяют так называемые сухие сцепления имеющие более простые конструкции.
В зависимости от способа управления сцепления бывают:
На большинстве колесных машин установлены неавтоматические постоянно замкнутые сцепления которые большую часть времени включены и выключаются водителем лишь при трогании переключении и торможении.
Типовая конструкция однодискового сцепления показана на рисунке 3.1.
– маховик; 2 – картер сцепления; 3 – ведомый диск; 4 – нажимной диск; 5 – отжимные рычаги; 6 – масленка; 7 – гайка; 8 – подшипник; 9 – вал; 10 – кожух сцепления; 11– пружины.
Рисунок 3.1 - Однодисковое сцепление с периферийными пружинами
Однодисковое сцепление с периферийным расположением нажимных пружин смонтировано на маховике (1). Нажимной диск (4) с кожухом (10) сцепления соединятся посредством выступов проушин за счет чего несколько увеличивается усилие сопротивления выключению сцепления из-за трения которое возникает в процессе осевого перемещения нажимного диска.
Нажимное усилие создается цилиндрическими пружинами (11)б которые расположены по периферии нажимного диска. В зависимости от конструкции машины количество пружин и их жесткость могут варьироваться (со стороны нажимного диска) устанавливаются теплоизолирующие прокладки.
Периферийное расположение нажимных пружин позволяет обеспечить равномерность распредеоения нажимного усилия при износе фрикционных накладок за счет чего усилие сохраняется практически неизменным.
Ведомый диск (3) с кольцевыми фрикционными накладками устанавливаются между маховиком двигателя и нажимным диском (4) на ведущем валу (9) коробки передач. С целью уменьшения динамических нагрузок в трансмиссии машины ведомый диск изготавливают как можно легче.
Схема ведомого диска представлена на рисунке 3.2.
– фрикционная накладка; 2 – волнистые пластины; 3 – ведомый диск; 4 – балансировочный грузик; 5 – фрикционные кольца; 6 – диск; 8 – пальцы; 9 – ступица; 10 – пружины демпфера.
Рисунок 3.2 – Ведомый диск сцепления
Чтобы обеспечить плавное включение сцепления одна из фрикционных накладок прикреплена к стальным волнистым пружинящим пластинам (2) которые присоединены к ведомому диску (3). На фрикционной накладке (1) предусмотрены радиальные канавки для вентиляции трущихся поверхностей а также с целью удаления случайно попавшего масла.
В диске предусмотрен демпфер для гашения крутильных колебаний возникающих при неравномерном вращении коленчатого вала двигателя движении машины по неровным дорогам резких изменениях угловых скоростей валов трансмиссии резком включении сцепления.
Демпфер выполнен из пары элементов:
Упруго (резиновый или пружинный);
Фрикционный (стальные кольца 5).
Упругий элемент дает возможность совершать относительное перемещение ступицы и диска помимо этого способствует снижению частоты собственных колебаний трансмиссии. Фрикционный элемент превращает кинетическую энергию колебаний в теплоту которая потом рассеивается.
В окнах ступицы (9) установлены в сжатом состоянии несколько пружин (10). Между фланцем ступицы и дисками (6) и (7) установлены фрикционные кольца (5) и регулировочные стальные прокладки. Диски соединены пальцами (8) утолщенными в средней части и расклепаны по концам. Момент трения устанавливается путем подбора толщины стальных регулировочных прокладок. Перемещение ведомого диска сцепления относительно ступицы (9) ограничивается пальцами (8) которые упираются в края вырезов фланца ступицы.
Ведомый диск в сборе статически балансируется посредством пластинчатых грузиков (4).
Отжимные рычаги (5) стремятся расположится симметрично относительно отжимных пружин. Их крепят к нажимному диску (4) через игольчатые подшипники с целью уменьшения сил трения. Рычаги также через сферические поверхности регулировочных гаек (7) опираются на кожух обеспечивая самоустанвку рычагов (5) при выключении сцеплении. Расположение внутренних рычагов в одной плоскости достигается гайками (7) которые по завершению регулировки раскерниваются.
С целью обеспечения полноты включения сцепления меду внутренними концами отжимных рычагов (5) и подшипников (8) делается зазор который регулируется (в процессе эксплуатации) через привод управления сцеплением. Для отвода от поверхностей трения теплоты нажимной диск изготавливается массивным. Предусмотренные в картере вентиляционные окна способствуют также охлаждению сцеплении.
В большинстве случаев сцепление смазывают только пару точек:
Подшипник(8) через масленку (6);
Внутренний подшипник вала сцепления смонтированный в маховике.
Для лучшего доступа к деталям сцепления нижняя часть картера (2) выполняется съемной.
Типовая схема двухдискового сцепления представлена 3.3.
– нажимной и ведомый диски соответственно; 2 – рычаги; 3 – выжимной подшипник; 4 – нажимные пружины.
Рисунок 3.3 – Двух дисковое сцепление с периферийными пружинами
При увеличении крутящего момента двигателя приходится переходить с однодискового на двухдисковое сцепление. Однако последнее обладает относительно большими осевым размером массой и ходом выключения а кроме того в его конструкции необходимо предусматривать принудительное перемещение среднего диска для обеспечения чистоты выключения сцепления.
В настоящее время на колесных машинах не только малой но и средней грузоподъемности все шире используют диафрагменные нажимные пружины в место цилиндрических периферийно расположенных. В первую очередь это вызвано более приемлемой характеристикой диафрагменных пружин обеспечивающей малую зависимость силы их сжатия от износа накладок ведомого диска.
Преимуществами сцепления с диафрагменной пружиной по сравнению с цилиндрическими являются также меньшая металлоемкость значительно меньшее число деталей и большая долговечность. Различают пружины с «вдавливаемой» и «вытягиваемой» пружинами. Причем по сравнению со сцеплением с «вытягиваемой» диафрагменной пружиной у сцепления с «вытягиваемой» пружиной на 30 40% уменьшаются силы действующие на выжимной подшипник и педаль сцепления при одинаковой нагрузке на нажимной диск а постоянное направление действия силы в рабочем положении пружины и при выключенном сцеплении увеличивает ее долговечность.
На рисунке 3.4 изображена типовая схема однодискового сцепления с диафрагменной «вдавливаемой» пружиной
– нажимной и ведомый диски; 2 – кожух сцепления; 3 – выжимной подшипник; 4 – диафрагменная пружина.
Рисунок 3.4 – Однодисковое сцепление с диафрагменной «вдавливаемой» пружиной.
На рисунке 3.5 изображена типовая схема однодискового сцепления с диафрагменной «вытягиваемой» пружиной
Рисунок 3.5 – Однодисковое сцепление с диафрагменной «вытягиваемой» пружиной.
Расчет основных деталей сцепления
1 Порядок проектирования сцепления
Проектирование фрикционного дискового сцепления включает следующие основные этапы:
выбор принципиальной конструктивной схемы сцепления (выбор конструкции нажимного устройства);
определение необходимых размеров фрикционных накладок и числа поверхностей трения;
конструктивную разработку ведомого (ведомых) дисков сцепления;
конструктивную разработку нажимного диска с кожухом в сборе;
выбор привода управления сцеплением и его разработку;
конструирование картера сцепления и согласование его конструкции с конструкцией задней части двигателя и коробки передач;
оформление технической документации на спроектированное сцепление.
2 Нажимные тарельчатые пружины
Исходные данные для расчета следующие.
Сила создаваемая пружиной при включенном положении сцепления
где ; w =015 025 мм для жесткого диска и 10 15 мм – для ведомого диска с осевой податливостью.
Ход пружины соответствующий суммарному линейному износу фрикционных пар. В зависимости от толщины фрикционных накладок принимают для легковых и 4 8 мм – для грузовых колесных машин а для сцеплений с двумя ведомыми дисками у грузовых колесных машин – 8 16 мм.
Материал пружины и допускаемое напряжение изгиба .
В существующих конструкциях тарельчатых пружин (рис. 4.2.1) имеют место следующие соотношения: число лепестков от 8 до 10.
Выбрав размеры в указанных пределах рассчитывают и строят ее характеристику т.е. зависимость действующей на нажимной диск силы P от его перемещения l:
где МПа; ; ; - геометрическое место точек относительно которых происходит поворот поперечного сечения пружины для «вдавливаемой» пружины.
Выбирая параметры пружины необходимо учитывать что при суммарном износе накладок на величину создаваемая пружиной сила должна быть больше или равна а при рабочем ходе - меньше .
Рисунок. 4.1 – Параметры тарельчатой пружины
Далее определяют напряжения изгиба в наиболее нагруженном месте в середине основания лепестка (точка на рис. 6) при достижении максимальной силы действующей на нажимной диск
где и проверяют выполнение условия
В ведущих дисках сцепления на прочность рассчитывают элементы соединяющие их с маховиком или кожухом сцепления. Если этими элементами являются шипы выступы зубья или пальцы то расчет их ведется на деформацию смятия
где - коэффициент учитывающий распределение крутящего момента двигателя по ведущим дискам в зависимости от их количества и расположения: - для нажимного диска однодискового сцепления и для среднего ведущего диска двухдискового сцепления; - соответственно число шипов (выступов пальцев) одного диска средний радиус их расположения и размер площади смятия шипа (выступа пальца); - максимальный динамический момент на первичном валу коробки передач.
где - момент по сцеплению ведущих колес с дорогой приведенный к первичному валу; - коэффициент сцепления колес с дорогой; - передаточное число трансмиссии на 1 передаче; радиус качения колеса и сцепной вес автомобиля.
При зависимость от величины считается линейной.
Если крутящий момент на ведущий диск сцепления передается упругими тангенциальными пластинами то заклепки пластин рассчитывают на срез и смятие а сами пластины – на изгиб и растяжение. Материал ведущих дисков: серый чугун СЧ21 и СЧ24. При расчете по формуле следует принимать .
Определение диаметра заклепок соединяющих диск со ступицей
где: - средний радиус трения расположения заклепок; - число дисков; – число заклепок; - диаметр заклепок; - коэффициент приспосабливаемости двигателя:
где: – максимальный крутящий момент ДВС; - максимальный момент соответствующий максимальной мощности.
где: - толщина диска.
Исходные данные к расчету
Из двух значений и выбираем большее и округляем до стандартной величины.
5 Прочностной расчет диафрагменной пружины
Конечно элементный анализ проводился в Ansys 17.2. Модель была подготовлена в КОМПАС 3D-v18. На рисунке 4.5 приведены параметры 3D модели.
Рисунок 4.5 - Параметры модели пружины
Условимся называть исходно выпуклую поверхность пружины верхней а исходно вогнутую поверхность пружины нижней.
Материал задан как сталь с модулем упругости первого рода E=2*1011 Па и коэффициентом Пуассона =0.3.
Модели были экспортированы в Ansys в формате STEP. Во встроенном редакторе Spaceclaim была построена их срединная поверхность и впоследствии пружина рассматривалась как оболочка толщиной 2 мм.
Ansys Workbench использует для разбиения поверхностей четырёхузловой элемент shell181.
Параметры сетки (Рис.4.5.1) были выбраны с учётом специфики решаемой задачи: большие перемещения определяют необходимость применения параметра Nonlinear Mechanical для формы элементов наличие геометрических концентраторов напряжений и близких элементов обусловила выбор параметра Adaptive который измельчает сетку в соответствующих местах модели.
Рисунок 4.5.1 - Параметры создания конечно элементной сетки
Остальные параметры оставлены по умолчанию.
На все варианты пружин наложены только кинематические граничные условия (Рис. 4.5.2):
A.По внешней окружности —перемещения вдоль оси z равны нулю.
B.В геометрическом центре пружины находится remote point связанная с краями лепестков. Задано перемещение вдоль оси z равное -20 мм остальные линейные и угловые перемещения заданы равными нулю. Поведение связи — деформируемое. Это значит что линии по которым приложено перемещение могут перемещаться друг относительно друга в ходе приложения перемещения.
Рисунок 4.5.2 - Граничные условия
Данные настройки обусловлены тем что сцепление — это кинематический механизм и для его правильной работы требуется обеспечить правильное смещение диска сцепления за что и отвечает данная пружина.
Кроме того предполагается потеря устойчивости в ходе приложения нагрузки что усложнит вычисления при задании силовых граничных условий. Таким образом задание нагрузки в перемещениях также и снижает сложность решения задачи.
Заданное перемещение на порядок превосходит толщину оболочки что является большим перемещением и требует соответствующей настройки решателя: включен параметр Large deflection.
Кроме того чтобы построить упругую характеристику пружины разобьём процесс решения на 20 подшагов. Так мы получим значения всех интересующих параметров в 20 точках и сможем построить зависимость силовой реакции от смещения лепестков.
При решении вычислялись эквивалентные напряжения по Мизесу и силовая реакция в связи A. По полученным данным построены упругие характеристики.
Конечно элементная сетка на первый вариант пружины с v93=5° и v95=5 мм изображена на рисунке 4.5.3. Поверхность была разбита на 4129 конечный элемент и в ней 4637 узлов.
Рисунок 4.5.3 - Конечно элементная сетка для первого варианта пружины: 4129 элементов 4637 узлов
На рисунках с 4.5.4 по 4.5.8 представлены результаты прочностного расчета диафрагменной пружины в программе ANSYS.
Рисунок 4.5.4 - Эквивалентные напряжения на верхней поверхности пружины при перемещении 20 мм
Рисунок 4.5.5 - Эквивалентные напряжения на нижней поверхности пружины при перемещении 20 мм
Рисунок 4.5.6 - Верхняя поверхность пружины. Серым показаны области где эквивалентные напряжения менее 1000 МПа
Рисунок .4.5.7 - Нижняя поверхность пружины. Серым показаны области где эквивалентные напряжения менее 1000 МПа
Рисунок 4.5.8 - Упругая характеристика (зависимость силы от перемещения) пружины
В результате выполнения данного курсового проектирования были выполнены следующие задачи:
Изучено назначение устройство и принцип работы агрегатов сцепления ;
Выполнен краткий анализ конструкций сцеплений;
Выполнены 3D модели деталей узла;
Был выполнен расчет ступицы ведомого диска на прочность методом конечных элементов.
СПИСОК ИСПОЛЬЗОВАННЫХ ИСТОЧНИКОВ
Проектирование полноприводных колесных машин: Учебник для вузов В3 т. Т.2 Б. А. Афанасьев Л. Ф. Жеглов В. Н. Зузов и др.; Под редакцией ред. А. А. Полунгяна. – М.: Изд-во МГТУ им. Н. Э. Баумана 2008. – 528 с.: ил.
Проектирование автомобиля: конспект лекций для направления подготовки специалистов 1900109 – специализация «Автомобильная техника в транспортных технологиях» А. М. Иванов В. И. Осипов. – М.: МАДИ 2014. – 40с.
Технические и инженерно – психологические основы проектирования машин: Овсянников В. Е.: Учебное пособие В. Е. Овсянников Г. Н. Шпитко В. И. Васильев. – Курган: Изд-во Курганского гос. Ун – та 2014. – 115 с.
Рекомендуемые чертежи
- 09.07.2014
- 25.10.2022
- 04.11.2022