Проектирование привода ленточного транспортера




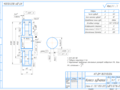
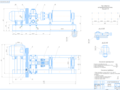
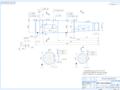

- Добавлен: 04.11.2022
- Размер: 997 KB
- Закачек: 0
Описание
Состав проекта
![]() |
![]() |
![]() |
![]() ![]() ![]() |
![]() ![]() ![]() |
![]() ![]() ![]() |
![]() ![]() ![]() |
![]() ![]() ![]() |
Дополнительная информация
Колесо зубчатое _ КП ДМ 18.01.10.004.cdw
Коэффициент смещения
Степень точности СТ СЭВ 641-77
Сталь 45 ГОСТ 1050-2013
Радиусы скруглений 2 мм.
Неуказанные предельные отклонения размеров отверстия H14
Пояснительная записка.docx
Федеральное государственное бюджетное образовательное учреждение высшего образования
«Сибирский государственный университет науки и технологий
им. академика М.Ф. Решетнева»
Основы конструирования машин
Детали машин и основы конструирования
Проектирование привода ленточного транспортера
Пояснительная записка
КП ДМ 15.03.05.01.10 ПЗ
Проф. д.т.н. Т.Т. Ереско
(ученое звание степень инициалы фамилия)
Руководитель проекта
«Сибирский государственный университет науки и технологий
Рассчитать и спроектировать привод ленточного транспортера
2. Перечень графического материала:
Чертежи деталей: выходной вал редуктора
Технические характеристики привода
Мощность на ведомом валу
Частота вращения ведомого вала
Коэффициент годового использования
Коэффициент суточного использования
Кинематический расчет привода 6
Проектный и проверочный расчет закрытой передачи 10
1. Выбор материала для изготовления зубчатых колес редуктора 12
2 Определение допускаемых контактных и изгибных напряжений .13
3. Проектный расчет закрытой передачи 15
Расчет открытой передачи 21
Расчет валов редуктора 26
1. Нагрузка валов редуктора 26
2. Выбор материала для изготовления валов. 27
3. Выбор допускаемых напряжений на кручение .27
5. Эскизная компоновка редуктора 28
6. Проверочный расчет ведущего вала на статическую прочность 29
7. Проверочный расчет ведомого вала на статическую прочность 33
Расчет шпоночных соединений ..38
Расчет подшипников 40
1. Расчет подшипников ведущего вала редуктора 41
2. Расчет подшипников ведомого вала редуктора 42
Выбор системы смазки и сорта масла редуктора уплотнений 43
Посадки основных деталей и сборочных единиц .45
Конструктивные размеры редуктора 46
Список используемых источников . 48
Привод механизма служит для передачи вращения от вала электродвигателя на исполнительный механизм.
Электродвигатель превращает электрическую энергию в механическую вал двигателя совершает вращательное движение но число оборотов вала двигателя очень велико для скорости движения рабочего органа. Для снижения числа оборотов и увеличения момента вращения и служит данный редуктор.
В данном курсовом проекте разработан одноступенчатый цилиндрический редуктор. Цель работы выучить основы конструирования и получить навыки инженера-конструктора.
К важным требованиям проектирования относятся экономичность в изготовлении и эксплуатации удобство в обслуживании и ремонте надежность и долговечность редуктора.
В пояснительной записке выполнен расчет необходимый для конструирования привода механизма.
Кинематический расчет привода
1 Выбор и проверка электродвигателя
Предварительно определим КПД привода.
В общем виде к.п.д. передачи определяется по формуле:
где - к.п.д. отдельных элементов привода.
Для привода данной конструкции к.п.д. определяется по формуле:
где - к.п.д. подшипников качения; ;
- к.п.д. зубчатой цилиндрической передачи; ;
- к.п.д. ременной передачи; ;
Рассчитаем требуемую мощность двигателя:
Рис.1.1. Эскиз электродвигателя 4АM112MВ6У3.
2 Определение общего передаточного отношения
Находим общее передаточное число для каждого из вариантов:
u = nномnвых= 95060 = 1583.
Принимаем передаточное отношение зубчатой передачи uзцп = 56
тогда uрп = uuзцп = 158356 = 2827.
3 Определяем кинематические параметры на каждом валу
n – частота вращения
4 Определяем вращающий момент на каждом валу
Выбор материала передачи
Термическая обработка
Предельные размеры заготовки
Предел прочности при растяжении в МПа
Предел текучести т МПа
Рисунок 2.1 Цилиндрическая зубчатая передача
Исходные данные: Т2 = 1263 Нм; Т3 = 480 Нм;
)Выбор материала зубчатых колёс
)Определение основных параметров и размеров зубчатых венцов
)Назначение степени точности зубчатых колёс
2Критерий работоспособности и расчёта передачи
Зубчатые передачи выходят из строя в основном по причине:
- усталостного выкрашивания рабочих поверхностей зубьев
- усталостной поломки зуба
- возможны статические поломки
Если передача закрытая (работает в редукторе) с не очень высокой твёрдостью рабочих поверхностей зубьев HRC 45 HRC то наиболее вероятной причиной выхода передачи из строя будет усталостное выкрашивание рабочих поверхностей зубьев и основной (проектный) расчёт следует вести из условия ограничения контактных напряжений.
А если передача открытая или закрытая но с высокой твёрдостью рабочих поверхностей зубьев HRC > 55 то наиболее вероятной причиной выхода из строя следует считать усталостную поломку зубьев и основной (проектный) расчёт следует вести из условия ограничения напряжений у ножки зуба (изгибных напряжений).
Во всех случаях необходима проверка на статическую прочность.
1 Выбор материала для изготовления зубчатых колес редуктора
Так как к приводу не предъявляется особых требований по массе и габаритам принимаем материалы со средними техническими характеристиками. С целью обеспечения равной прочности шестерни и колеса и уменьшения задира твёрдость рабочих поверхностей зубьев шестерни должна быть примерно на 10% выше твёрдости рабочих поверхностей колеса. Выбор материалов производим согласно таблицы 2.1 [1 c. 12]
2 Определение допускаемых контактных и изгибных напряжений
2.1 Расчёт допускаемых контактных напряжений
где SH - коэф. безопасности (SH=1.1 т.к. материал с однородной структурой);
KHL - коэффициент долговечности (KHL = 1 так как срок службы передачи не ограниченно долгий).
H lim B = 2ННВ +70 табл. 2.2 [1]
H lim B = 17ННRC +200
H lim B 1= 17475 + 200 = 10075 МПа
H lim B 2= 22855 + 70 = 641 МПа
В качестве расчётных []H для прямозубых цилиндрических колёс принимается значение: 045·([]H 1 + []H2 )= 6069 МПа.
2.2 Определение допускаемых значений напряжений при расчёте зубьев на усталостный изгиб.
SF – коэффициент безопасности (SF=17..22);
SF=175 табл. 4.2 [3]
KFL - коэффициент долговечности (KFL = 1);
F lim B = 1.8 ННВ табл. 2.3 [1]
F lim B2 = 1.8 2855 = 5139 МПа
3 Проектный расчет закрытой передачи
Так как передача закрытая с невысокой твёрдостью рабочих поверхностей зубьев то проектный расчёт ведём из условий ограничения контактных напряжений.
Рассчитаем межосевое расстояние:
где - межосевое расстояние передачи;
u – передаточное отношение передачи;
Т3 – крутящий момент на колесе;
КН - коэффициент нагрузки;
а – коэффициент ширины зубчатого венца;
Принимаем мм [1 c. 20].
3.1 Подбор основных параметров зацепления
3.2.1. Модуль передачи
m = (0.01 0.02) aw B
m = (0.01 0.02) 180 0.9744 = 18 36 мм
принимаем m = 25 [1 c. 22]
3.1.2Определение числа зубьев зубчатых колёс
Определим суммарное число зубьев:
Определим число зубьев шестерни: принимаем = 24.
Число зубьев на колесе:
Уточняем передаточное отношение:
Погрешность не превышает 0% значит принятые параметры принимаются окончательно.
3.2Определение геометрических размеров зубчатых колёс
Определим диаметры делительных окружностей:
Определим диаметры окружностей вершин:
da1 = d1 + 2m = 60 + 225 = 65 мм
da2 = d2 + 2m = 300 + 225 = 305 мм
Определим диаметры окружностей впадин:
df1 = d1 – 2.5m = 60 –25 25 = 5375 мм
df2 = d2 – 2.5m = 300 –25 25 = 29375 мм
Ширина зубчатого венца:
Принимаем b2 = 45мм.
Для снижения влияний погрешностей монтажа на величину поля зацепления ширина шестерён принимается на 5 мм больше:
Проверка межосевого расстояния:
3.3 Проверочные расчёты
3.3.1. Определение окружной скорости
Рекомендуемая степень точности 8-я табл. 2.5 [1]
Уточняем коэффициенты нагрузки КН КF:
Коэффициенты нагрузки находятся по следующим зависимостям:
при расчёте на контактную выносливость: КН = КН КНV
при расчёте на изгибную выносливость: КF = КF КFV
где КН КF - коэффициенты учитывающие неравномерность распределения нагрузки по длине зуба при расчёте по контактным и изгибным напряжениям соответственно;
КНV КFV – динамические коэффициенты при расчёте по контактным и изгибным напряжениям соответственно.
Рисунок 2.2 Схема закрепления зубчатых колёс
По графическим зависимостям и по заданной схеме закрепления зубчатых колёс находим значения коэффициентов:
КF = 11 рис. 2.7 [1]
Определяем динамические коэффициенты КV:
Определяем коэффициенты КНV и КFV
КНV = 104 табл. 2.6 [1]
КFV = 11 табл. 2.9 [1]
КН = 105 104 = 1092; КF = 11 11 = 121;
3.3.2. Проверочный расчёт по контактным напряжениям
Перегруз передачи не превышает 5% значит находится в пределах допустимого.
3.3.3. Проверочный расчёт по напряжениям изгиба
где YF1 = 396 и YF2 = 3.75 – коэффициенты прочности зубьев шестерни и колеса табл. 2.10 [1]
3.4.1. Силы действующие в зацеплении
Итоговые параметры передачи
Рассчитываемый параметр
Межосевое расстояние
Число зубьев шестерни
Диаметр делительной окружности шестерни
Диаметр делительной окружности колеса
Диаметр окружности выступов шестерни
Диаметр окружности выступов колеса
Диаметр окружности впадин шестерни
Диаметр окружности впадин колеса
Ширина зубчатого венца шестерни
Ширина зубчатого венца колеса
Степень точности передачи
Окружная сила в зацеплении
Радиальная сила в зацеплении
Расчет открытой передачи
Ременная передача — это передача гибкой связью (рис. 3.1) состоящая из ведущего 1 и ведомого 2 шкивов и надетого на них ремня 3. В состав передачи могут также входить натяжные устройства. Возможно применение нескольких ремней и нескольких ведомых шкивов. Основное назначение — передача механической энергии от двигателя передаточным и исполнительным механизмам как правило с понижением частоты вращения и повышением вращающего момента.
Рис. 3.1. Схема передачи
По принципу работы различаются передачи трением (большинство передач) и зацеплением (зубчато-ременные). Передачи зубчатыми ремнями по своим свойствам существенно отличаются от ременных передач трением.
Ремни передач трением по форме поперечного сечения разделяются на плоские клиновые поликлиновые круглые квадратные (рис. 3.2). Клиновые поликлиновые зубчатые и быстроходные плоские изготовляют бесконечными замкнутыми. Плоские ремни преимущественно выпускают конечными в виде длинных лент. Концы таких ремней склеивают сшивают или соединяют металлическими скобами. Места соединения ремней вызывают динамические нагрузки что ограничивает скорость ремня. Разрушение этих ремней происходит как правило по месту соединения.
Рис. 3.2. Сечения ремней
Достоинства ременных передач трением: возможность передачи движения на значительные расстояния; возможность работы с высокими скоростями; плавность и малошумность работы; предохранение механизмов от резких колебаний нагрузки и ударов; защита от перегрузки за счет проскальзывания ремня по шкиву; простота конструкции; отсутствие смазочной системы; низкая стоимость.
Недостатки: значительные габариты; значительные силы действующие на валы и опоры; непостоянство передаточного отношения; малая долговечность ремней в быстроходных передачах; необходимость защиты ремня от попадания масла.
2. Определение параметров передачи.
2.1. Исходные данные.
Рассчитать открытую клиноременную передачу по следующим данным:
P1 = 5587 кВт — мощность на валу ведущего шкива; n = 960 мин-1 — число оборотов ведущего шкива; U = 3 — передаточное число; Л — легкий режим работы. Работа в одну смены. Срок службы привода L = 30905 часов. Конструируемый шкив — ведомый.
2.2. Выбор сечения ремня.
Для заданных Р = 5587 кВт n =960 мин-1 по графику [3 с.134] подходят ремни сечением Б с размерами [3 c.91]; Wр = 14 мм; Wз = 17 мм; То = 105 мм; площадь сечения А = 133 мм2; масса 1 м длины ремня - 018 кгм; минимальный диаметр шкива d = 125 мм.
2.3.Определение диаметров шкивов.
С целью увеличения рабочего ресурса работы передачи принимаем . Из стандартного ряда ближайшее большее значение = 140 мм. Расчетный диаметр ведомого (большего) шкива:
Ближайшее стандартное значение d2 = 400 мм. С учетом коэффициента относительного скольжения е =001 уточняем передаточное число:
Отличие от заданного передаточного числа:
что меньше допустимого отклонения 5%.
2.4.Межосевое расстояние ременной передачи.
Принимаем промежуточное стандартное значение а - 500 мм.
2.5.Определяем расчетную длину ремня.
Ближайшее стандартное значение [3 c. 93]: Lp = 1800 мм.
2.6.Уточняем межосевое расстояние.
Принимаем а = 460 мм.
Для установки и замены ремней предусматриваем
возможность уменьшения а на 3% (т.е. на 003·460 = 138 мм).
Для компенсации удлинения ремней во время эксплуатации предусматриваем возможность увеличения а на 55% (т.е. 0055·460= 253 мм).
2.7.Угол обхвата ремнями ведущего шкива.
2.8. Определение числа ремней.
Для определения числа ремней определяем коэффициенты:
угла обхвата Са = 095 [3];
длины ремня CL = 103 [3];
режима работы Ср = 1.1;
числа ремней Сz = 095 (приняв ориентировочно Z= 4 6).
Находим номинальную мощность PQ = 237 кВт [3 c. 132] передаваемую одним ремнем сечением Б с расчетной длиной L = 1000 мм при d1 = 140 мм U = 3 и n = 960 мин-1.
Определяем расчетную мощность передаваемую одним ремнем:
Определяем число ремней:
Принимаем число ремней Z = 4.
2.9.Определение сил действующих на валы.
Окружная скорость ремней:
Начальное натяжение каждой ветви одного ремня:
где = 01 — коэффициент центробежных сил [3].
Силы действующие на валы и опоры:
2.10. Суммарное число ремней необходимое на весь срок службы привода.
где Тср = 2000 ч (ресурс работы ремней по ГОСТ 1284.2-89); К1 = 25 — коэффициент для легкого режима работы; К2 = 1 — коэффициент климатических условий.
Суммарное число ремней Z необходимое на весь
срок службы привода L = 30905 ч (по заданию):
Ремень Б — 1800 Ш ГОСТ 1284.1-80 —ГОСТ 1284.3-80.
Расчет валов редуктора
1 Нагрузки валов редуктора
Определение сил в зацеплении закрытой передачи (рассчитаны в главе 2):
Определение консольных сил.
Определим силы действующие со стороны открытой передачи (рассчитана в главе 3):
Fм = 75=75 = 2049 Н.
Силовая схема нагружения валов редуктора.
Рисунок 4.1. Схема нагружения валов редуктора
2 Выбор материала для изготовления валов
В соответствии с рекомендациями выбираем для шестерни сталь 45 с твердостью 280 НВ термообработка – улучшение. Вал колеса выполнен из аналогичного материала для унификации.
3 Выбор допускаемых напряжений на кручение
Проектный расчет выполняем по напряжениям кручения при этом принимаем [ к]= 15 25Нмм2.
4 Определение геометрических параметров ступеней валов
Схема к расчету представлена на рисунке 4.2.
Диаметр выходного конца ведущего вала находим по формуле
где [к] - допускаемое напряжение на кручение [к] = 15 МПа.
Диаметр шеек под подшипник
Вал колеса редуктора рассчитываем аналогично.
Схема к расчету вала колеса представлена на рисунке 4.3.
Диаметр выходного конца вала
Диаметр вала под колесом 2
Определим конструктивные элементы центра колеса.
Толщина диска центра колеса:
Диаметр центрального отверстия центра колеса:
Наружный диаметр ступицы колеса:
5 Эскизная компоновка редуктора
Определяем размеры для построения эскизной компоновки.
а) зазор между внутренней стенкой корпуса и вращающимся колесом:
Х=8 10 мм принимаем х=10 мм.
б) расстояние между дном корпуса и зубчатым колесом:
6. Проверочный расчет ведущего вала на статистическую прочность
6.1 Расчет быстроходного вала
6.1.1 Схема нагружения вала
Рисунок 4.4 – Схема нагружения ведущего вала в плоскости xy:
Рисунок 4.4 – Схема нагружения ведущего вала
Суммарные изгибающие моменты
6.1.2 Уточненный расчет вала
Проверим правильность определения диаметра вала в сечении под червяком.
Эквивалентный изгибающий момент в сечении:
Для вала принимаем сталь 45 ГОСТ 1050-88. Термообработка улучшение – НВ 240 255
Пределы выносливости
Допускаемое напряжение изгиба:
где: - масштабный фактор. При d=45 мм
- коэффициент запаса прочности. Принимаем
- коэффициент концентрации напряжения для шпоночного соединения
Момент сопротивления сечения
Напряжение в сечении меньше допускаемого поэтому окончательно принимаем диаметр вала в месте установки подшипника .
6.1.3 Расчет вала на усталость
Принимаем что нормальные напряжения от изгиба изменяются по симметричному циклу а касательные от кручения – по пульсирующему.
Моменты сопротивления сечения
Амплитуда и среднее напряжение цикла касательных напряжений:
Амплитуда нормальных напряжений изгиба:
Среднее напряжение изгиба
Коэффициенты запаса усталостной прочности по нормальным и касательным напряжениям
где - масштабные факторы
- коэффициенты концентрации напряжений с учетом влияний шероховатости поверхности.
- коэффициенты влияния шероховатости поверхности
- при отсутствии упрочнения вала.
- коэффициенты чувствительности материала к асимметрии цикла напряжений.
Окончательно получим
Так как то вал достаточно прочен.
7. Проверочный расчет ведомого вала на статистическую прочность
7.1. Схема нагружения тихоходного вала
Рисунок 4.5 – Схема нагружения тихоходного вала
Рисунок 4.5 – Схема нагружения
7.2 Уточненный расчет вала
Проверим правильность определения диаметра вала в сечении под коническим колесом.
где: - масштабный фактор. При d=58 мм
Момент сопротивления сечения:
При d=58 мм сечение паза шпонки b=18 мм
- напряжение в сечении меньше допускаемого поэтому окончательно принимаем диаметр вала под колесом .
7.3 Расчет вала на усталость
Наиболее опасным является сечение в месте расположения червяка.
Коэффициенты запаса усталостной прочности по нормальным и касательным напряжениям:
- коэффициенты чувствительности материала к асимметрии цикла напряжений
Расчет шпоночных соединений
Рисунок 5.1 Шпонки призматические ГОСТ 23360-78
Размеры шпонок выбираем в зависимости от диаметра вала [1 c. 476]
Принимаем шпонки призматические по ГОСТ 23360-78. Материал шпонок – сталь 45 нормализованная. Допускаемое напряжение смятия боковой поверхности длину шпонки принимаем на 5 10 мм меньше длины ступицы.
Соединение вала с зубчатым колесом 2 диаметр соединения 58 мм.
Сечение шпонки длина шпонки 60мм.
Расчет остальных шпонок в редукторе представим в виде таблицы 5.1
Расчет шпоночных соединений.
Так как условие для шпонок тихоходного вала не выполняется то устанавливаем по две шпонки под углом 180 градусов считая что каждая принимает половину нагрузки.
Таким образом все шпоночные соединения обеспечивают заданную прочность и передают вращающий момент.
1 Предварительный выбор подшипников
Предварительно намечаем радиальные шарикоподшипники средней серии по ГОСТ 8338-75; габариты подшипников выбираем по диаметру вала в месте посадки подшипников dп1 = 45 мм и dп2= 55 мм. По каталогу подшипников выбираем подшипники (табл. 6.1) [1 c. 459].
Характеристики выбранных подшипников
Условное обозначение подшипника
2 Расчет подшипников ведущего вала редуктора
Эквивалентную динамическую нагрузку подшипника определим по формуле:
где: V – коэффициент вращения кольца. V=1 – при вращении внутреннего кольца. - коэффициент безопасности для редукторов всех конструкций. - температурный коэффициент при t≤100°С.
-осевая нагрузка на валу.
Для опоры В как наиболее нагруженной
Расчетная долговечность подшипника:
Так как срок службы редуктора то подшипник подобран правильно.
3 Расчет подшипников ведомого вала редуктора
где: V – коэффициент вращения кольца. V=1 – при вращении внутреннего кольца.
- коэффициент безопасности для редукторов всех конструкций.
- температурный коэффициент при t≤100°С
Для опоры А как наиболее нагруженной
Расчетная долговечность подшипника
Выбор системы смазки и сорта масла редуктора уплотнений
Смазка зубчатого зацепления производится окунанием зубчатого колеса в масло заливаемое внутрь корпуса до уровня обеспечивающего погружение колес примерно на 15 20мм.
Объем масляной ванны Vм определяем из расчета масла на 1кВт передаваемой мощности.
При внутренних размерах корпуса редуктора: В=415 мм L=96 мм определим необходимую высоту масла в корпусе редуктора:
При окружной скорости зубчатого колеса 2- рекомендуется вязкость масла 59 ссm. При скорости зубчатого колеса 4 рекомендуемая вязкость 118 ссm.
Принимаем масло индустриальное Н100А ГОСТ 20799-75.
При окружной скорости колес более 1мс брызгами масла покрываются все детали передач и внутренних поверхностей стенок стекающие с этих элементов капли масла попадают в подшипники.
Исходя из условий работы данного привода выбираем муфту упругую втулочно - пальцевую со следующими параметрами Т = 100 Нм d = 50 мм D = 220мм L = 288 мм l= 218 мм.
Рис 8.1. Эскиз муфты
Предельные смещения валов:
Посадки основных деталей и сборочных единиц
Зубчатые колёса (легко прессованные): H7r6.
Крышки торцовых узлов на подшипниках качения: H7h8.
Внутренние кольца подшипников качения на валы: k6.
Наружные кольца подшипников качения в корпус: H7.
Шпоночные соединения: P9n6.
Конструктивные размеры привода
Толщина стенки корпуса и крышки:
Толщина нижнего пояса (фланца):
Толщина верхнего пояса (фланца):
Толщина нижнего пояса корпуса:
Толщина рёбер основания корпуса:
Толщина рёбер крышки:
Диаметр фундаментальных болтов:
Диаметр болтов у подшипников:
Диаметр болтов соединяющих основание корпуса с крышкой:
Размеры определяющие положение болтов:
Минимальные диаметры приливов корпуса вокруг подшипников качения:
Ширина лапы при установке винта с шестигранной головкой:
Расстояние от оси винта до края лапы:
Толщина лапы корпуса:
Остальные размеры принимаем конструктивно при построении чертежа.
Список использованных источников
Дунаев П.Ф. Леликов О.П. Конструирование узлов и деталей машин- М.: Высшее профессиональное образование 2006 - 495 с.
Дроздов Н.А. Ереско Т.Т. Смирнов Н.А. Курсовое проектирование по деталям машин и основам конструирования 2008-159 с.
Чернавский С.А. Курсовое проектирование деталей машин.- М.: Машиностроение 1988 - 416 с.
Шейнблит А.Е. Курсовое проектирование деталей машин: Учеб пособие для техникумов. – М.: Высш. шк. 1991. – 432с.
Анурьев В.И. Справочник конструктора-машиностроителя: В 3 т. – М. 1992. – Т. 1
Анурьев В.И. Справочник конструктора-машиностроителя: В 3 т. – М. 1992. – Т. 2
Анурьев В.И. Справочник конструктора-машиностроителя: В 3 т. – М. 1992. – Т. 3
Вал тихоходный.cdw
Неуказанные предельные отклонения размеро:
КП ДМ 15.03.05.01.10
Сталь 45 ГОСТ 1050-2013
Привод.cdw
КП ДМ 15.03.05.01.10 СБ
Технические требования:
Сборку производить на смазке ЛИТОЛ-24 ГОСТ 21500-75.
Несоосность валов электродвигателя и редуктора компенсировать
* Размеры для справок.
Допустимое радиальное смещение валов
Допустимое осевое смещение валов
Допустимый перекос валов 0
Техническая характеристика:
Мощность электродвигателя
Частота вращения вала электродвигателя
Модель электродвигателя 4АМ112МВ6У3
Передаточное число редуктора 5
Рекомендуемые чертежи
- 04.06.2015
- 24.01.2023
- 24.01.2023