Проект участка по ремонту тормозных барабанов с разработкой приспособления для снятия и установки колес




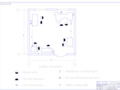

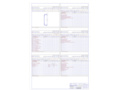
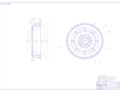
- Добавлен: 25.10.2022
- Размер: 2 MB
- Закачек: 0
Описание
Состав проекта
![]() |
![]() |
![]() ![]() ![]() ![]() |
![]() |
![]() ![]() ![]() ![]() |
![]() ![]() ![]() ![]() |
![]() ![]() ![]() ![]() |
![]() ![]() ![]() ![]() |
![]() ![]() ![]() ![]() |
![]() ![]() ![]() ![]() |
![]() ![]() ![]() ![]() |
![]() ![]() ![]() ![]() |
![]() ![]() ![]() ![]() |
![]() ![]() ![]() ![]() |
![]() ![]() ![]() ![]() |
![]() ![]() ![]() ![]() |
![]() ![]() ![]() ![]() |
![]() ![]() ![]() ![]() |
![]() ![]() ![]() ![]() |
![]() ![]() ![]() ![]() |
![]() ![]() ![]() ![]() |
![]() ![]() ![]() ![]() |
![]() ![]() ![]() ![]() |
![]() ![]() ![]() ![]() |
![]() |
![]() ![]() ![]() |
![]() ![]() ![]() |
![]() ![]() ![]() |
![]() ![]() ![]() |
![]() ![]() ![]() |
![]() ![]() ![]() |
![]() ![]() ![]() |
![]() ![]() ![]() |
![]() ![]() ![]() |
![]() ![]() ![]() |
![]() ![]() ![]() |
![]() ![]() ![]() |
![]() ![]() ![]() |
![]() ![]() ![]() ![]() |
![]() ![]() ![]() ![]() |
![]() ![]() ![]() ![]() |
![]() ![]() ![]() ![]() |
![]() ![]() ![]() ![]() |
![]() |
![]() ![]() ![]() |
![]() ![]() ![]() |
![]() ![]() ![]() |
Дополнительная информация
Чертеж 7.cdw

Ликвидационное сальдо
Коэффициент приведения
Затраты с учетом фонда времени
Экономический эффект
Экономический эффект с наростающим
Технико- экономическое обоснование
Выгоничский ДРСУч с разработкой приспособления для снятия и установки колес
Чертеж 7.cdw

Ликвидационное сальдо
Коэффициент приведения
Затраты с учетом фонда времени
Экономический эффект
Экономический эффект с наростающим
Технико- экономическое обоснование
Выгоничский ДРСУч с разработкой приспособления для снятия и установки колес
дет3 СБ.cdw

Спецификация 2.cdw

Чертеж 1.cdw

Схема технологического процесса
Выгоничский ДРСУч с разработкой приспособления для снятия и установки колес
дет СБ.cdw

дет4СБ.cdw

Чертеж 2.cdw

спецификация.cdw

дет2 СБ.cdw

Чертеж 5.cdw

Б02 Установка ОМ-4276М
А11 030 Сушка порошка
Б08 Ацетон технический ГОСТ 1825263-88
А06 2 Точить поверхность 1 до диаметра
Увеличение внутреннего диаметра
1 Штангенциркуль ШЦ 11-500-0
Выгоничский ДРСУч с разработкой приспособления для снятия и установки колес
Карты технологического
процесса востановления
сб.ед. или материала Обозначение
наименование оборудования СМ Проф Р УТ КР КОИД ЕН ОП Кшт Тпз Тшт
Цех Уч РМ Опер Код наименов. операции Обозначение документа
Маршрутная карта технологического процесса востановления
Эскиз к операционной карте
ОП Операционная карта востановления
КТПД Дефектовочная карта востановления
А03 010 Дефектовочная
Б04 Стол для дефектации ОРГ - 14-6801-90 ГОСНИТИ
Б06 Станок токарно-револьверный 1Д 310
А07 020 Обезжиривание
А09 025 Дроблеструйная обработка
Б10 Установка ДУ-7755
Б12 Электрический шкаф СВЧ-8-3-2
А13 035 Газотермическая напыление
М01 СЧ 18-36 ГОСТ 1412-85
СЧ 18-36 ГОСТ 1412-85
Б14 Установка для напыления 011-1-01
Б16 Станок токарно-револьверный 1Д-310
Б18 Электрический шкаф СВЧ-8-3-2
А01 СЧ 18-36 ГОСТ 1412-85
Б03 Станок токарно-револьверный 1Д 30
Т05 Приспособление для крепления тормозного барабана цеховое
6 2 Точить поверхность 1 до выведения следов износа
Штангенциркуль ШЦ 11-500-01
образец шероховатости
4 1 Установить деталь
А15 040 Механическая обработка
Б03 Станок токарно-револьверный 1Д 310
Т05 Приспособление для крепления тормозного барабана цеховое
штангенциркуль ШЦ 11-500-01
А01 Код наименования дефекта РЧ ДР СТО
Б03 Стол для дефектации ОРГ-14-86-01А ГОСНИТИ Штангенциркуль ШЦ 11-500-0
Кольцевая канавка Недопускается Осмотр
Риски и задиры Недопускается Осмотр
Трещины и сколы Недопускается Осмотр
Б03 Установка для напыления поверхности 011-1-01
Т05 Приспособление установочное цеховое
6 2 Нанести покрытие на поверхность 1
Т07 Горелка ГН-2. Шаблон цеховой
М08 Порошковые композиции ВК-15
ацетелен ГОСТ 54 57-75
кислород ГОСТ 55 83-78
0 Оплавить поверхность
Р11 Установка для напыления поверхности 011-1-01
Т12 Горелка ГН-2. Шаблон цеховой
сборка.cdw

деталей сварные швы по ГОСТ 4771-76-Т3
Выгоничский ДРСУч с разработкой приспособления для снятия и установки колес
Предельные отклонения размеров: Н14;h14
Барабан А1.cdw

Неуказанные предельные отклонения размеров
На рабочих поверхностях не допускается
наличие пор диаметромне более 2 мм
не более 1 мм не более одной на 1 см
чертеж 6.cdw

Проект участка по ремонту
тормозных барабановс разработкой
приспособления для снятия и установки колес
Условные обозначения:
- Слив в канализацию
- Потребитель электроэнергии
- Местный вентиляционный отсос
- Подвод холодной воды
дет3 СБ.cdw

Спецификация 2.cdw

Чертеж 1.cdw

Схема технологического процесса
Выгоничский ДРСУч с разработкой приспособления для снятия и установки колес
дет СБ.cdw

дет4СБ.cdw

Чертеж 2.cdw

спецификация.cdw

Чертеж 5.dwg
Б02 Установка ОМ-4276М
А11 030 Сушка порошка
Б08 Ацетон технический ГОСТ 1825263-88
А06 2 Точить поверхность 1 до диаметра
Увеличение внутреннего диаметра
1 Штангенциркуль ШЦ 11-500-0
Выгоничский ДРСУч с разработкой приспособления для снятия и установки колес
Карты технологического
процесса востановления
сб.ед. или материала Обозначение
наименование оборудования СМ Проф Р УТ КР КОИД ЕН ОП Кшт Тпз Тшт
Цех Уч РМ Опер Код наименов. операции Обозначение документа
Маршрутная карта технологического процесса востановления
Эскиз к операционной карте
ОП Операционная карта востановления
КТПД Дефектовочная карта востановления
А03 010 Дефектовочная
Б04 Стол для дефектации ОРГ - 14-6801-90 ГОСНИТИ
Б06 Станок токарно-револьверный 1Д 310
А07 020 Обезжиривание
А09 025 Дроблеструйная обработка
Б10 Установка ДУ-7755
Б12 Электрический шкаф СВЧ-8-3-2
А13 035 Газотермическая напыление
М01 СЧ 18-36 ГОСТ 1412-85
СЧ 18-36 ГОСТ 1412-85
Б14 Установка для напыления 011-1-01
Б16 Станок токарно-револьверный 1Д-310
Б18 Электрический шкаф СВЧ-8-3-2
А01 СЧ 18-36 ГОСТ 1412-85
Б03 Станок токарно-револьверный 1Д 30
Т05 Приспособление для крепления тормозного барабана цеховое
6 2 Точить поверхность 1 до выведения следов износа
Штангенциркуль ШЦ 11-500-01
образец шероховатости
4 1 Установить деталь
А15 040 Механическая обработка
Б03 Станок токарно-револьверный 1Д 310
Т05 Приспособление для крепления тормозного барабана цеховое
штангенциркуль ШЦ 11-500-01
А01 Код наименования дефекта РЧ ДР СТО
Б03 Стол для дефектации ОРГ-14-86-01А ГОСНИТИ Штангенциркуль ШЦ 11-500-0
Кольцевая канавка Недопускается Осмотр
Риски и задиры Недопускается Осмотр
Трещины и сколы Недопускается Осмотр
Б03 Установка для напыления поверхности 011-1-01
Т05 Приспособление установочное цеховое
6 2 Нанести покрытие на поверхность 1
Т07 Горелка ГН-2. Шаблон цеховой
М08 Порошковые композиции ВК-15
ацетелен ГОСТ 54 57-75
кислород ГОСТ 55 83-78
0 Оплавить поверхность
Р11 Установка для напыления поверхности 011-1-01
Т12 Горелка ГН-2. Шаблон цеховой
дет3 СБ.dwg
дет СБ.dwg
Барабан А1.dwg
Неуказанные предельные отклонения размеров
На рабочих поверхностях не допускается
наличие пор диаметромне более 2 мм
не более 1 мм не более одной на 1 см
Чертеж 1.dwg
Схема технологического процесса
Выгоничский ДРСУч с разработкой приспособления для снятия и установки колес
чертеж 6.dwg
Проект участка по ремонту
тормозных барабановс разработкой
приспособления для снятия и установки колес
Условные обозначения:
- Слив в канализацию
- Потребитель электроэнергии
- Местный вентиляционный отсос
- Подвод холодной воды
дет2 СБ.dwg
сборка.dwg
деталей сварные швы по ГОСТ 4771-76-Т3
Выгоничский ДРСУч с разработкой приспособления для снятия и установки колес
Предельные отклонения размеров: Н14;h14
дет4СБ.dwg
Чертеж 7.dwg
Ликвидационное сальдо
Коэффициент приведения
Затраты с учетом фонда времени
Экономический эффект
Экономический эффект с наростающим
Технико- экономическое обоснование
Выгоничский ДРСУч с разработкой приспособления для снятия и установки колес
Чертеж 2.dwg
дет2 СБ.cdw

Чертеж 5.cdw

Б02 Установка ОМ-4276М
А11 030 Сушка порошка
Б08 Ацетон технический ГОСТ 1825263-88
А06 2 Точить поверхность 1 до диаметра
Увеличение внутреннего диаметра
1 Штангенциркуль ШЦ 11-500-0
Выгоничский ДРСУч с разработкой приспособления для снятия и установки колес
Карты технологического
процесса востановления
сб.ед. или материала Обозначение
наименование оборудования СМ Проф Р УТ КР КОИД ЕН ОП Кшт Тпз Тшт
Цех Уч РМ Опер Код наименов. операции Обозначение документа
Маршрутная карта технологического процесса востановления
Эскиз к операционной карте
ОП Операционная карта востановления
КТПД Дефектовочная карта востановления
А03 010 Дефектовочная
Б04 Стол для дефектации ОРГ - 14-6801-90 ГОСНИТИ
Б06 Станок токарно-револьверный 1Д 310
А07 020 Обезжиривание
А09 025 Дроблеструйная обработка
Б10 Установка ДУ-7755
Б12 Электрический шкаф СВЧ-8-3-2
А13 035 Газотермическая напыление
М01 СЧ 18-36 ГОСТ 1412-85
СЧ 18-36 ГОСТ 1412-85
Б14 Установка для напыления 011-1-01
Б16 Станок токарно-револьверный 1Д-310
Б18 Электрический шкаф СВЧ-8-3-2
А01 СЧ 18-36 ГОСТ 1412-85
Б03 Станок токарно-револьверный 1Д 30
Т05 Приспособление для крепления тормозного барабана цеховое
6 2 Точить поверхность 1 до выведения следов износа
Штангенциркуль ШЦ 11-500-01
образец шероховатости
4 1 Установить деталь
А15 040 Механическая обработка
Б03 Станок токарно-револьверный 1Д 310
Т05 Приспособление для крепления тормозного барабана цеховое
штангенциркуль ШЦ 11-500-01
А01 Код наименования дефекта РЧ ДР СТО
Б03 Стол для дефектации ОРГ-14-86-01А ГОСНИТИ Штангенциркуль ШЦ 11-500-0
Кольцевая канавка Недопускается Осмотр
Риски и задиры Недопускается Осмотр
Трещины и сколы Недопускается Осмотр
Б03 Установка для напыления поверхности 011-1-01
Т05 Приспособление установочное цеховое
6 2 Нанести покрытие на поверхность 1
Т07 Горелка ГН-2. Шаблон цеховой
М08 Порошковые композиции ВК-15
ацетелен ГОСТ 54 57-75
кислород ГОСТ 55 83-78
0 Оплавить поверхность
Р11 Установка для напыления поверхности 011-1-01
Т12 Горелка ГН-2. Шаблон цеховой
сборка.cdw

деталей сварные швы по ГОСТ 4771-76-Т3
Выгоничский ДРСУч с разработкой приспособления для снятия и установки колес
Предельные отклонения размеров: Н14;h14
Барабан А1.cdw

Неуказанные предельные отклонения размеров
На рабочих поверхностях не допускается
наличие пор диаметромне более 2 мм
не более 1 мм не более одной на 1 см
чертеж 6.cdw

Проект участка по ремонту
тормозных барабановс разработкой
приспособления для снятия и установки колес
Условные обозначения:
- Слив в канализацию
- Потребитель электроэнергии
- Местный вентиляционный отсос
- Подвод холодной воды
записка.docx
4 Анализ состояния ремонтно-обслуживающей базы8
5 Обоснование темы выпускной квалификационной работы9
Технологическая часть11
1 Расчет общей трудоемкости ремонтных работ11
2 Распределение трудоёмкости ремонтных работ по технологическим видам и обоснование состава участка12
3 Режим работы сезонного текущего ремонта и фонда времени13
4 Технологический расчёт участка15
4.1 Расчёт штата участка12
4.2 Расчет и подбор технологического оборудования и оснастки12
4.3 Расчёт площадей постов участка по восстановлению тормозных барабанов13
4.4 Компоновка участка по восстановлению тормозных барабанов14
5 Разработка технологических мероприятий по восстановлению тормозных барабанов15
5.1Основные типы и назначение тормозных систем грузовых автомобилей15
5.2Назначение анализ условий работы и основные дефекты восстанавливаемой детали20
5.3 Обзор применяемых способов восстановления21
КОНСТРУКТОРСКАЯ РАЗРАБОТКА30
1 Обоснование разработки30
2 Обзор существующих конструкций31
3 Устройство и принцип работы тележки для снятия и установки колес автомобиля31
4 Меры безопасности при работе с тележкой и монтаже колес31
5 Разработка технологической карты на восстановление тормозных барабанов33
6 Расчет элементов конструкторской разработки33
6.1 Расчёт сварного соединения33
6.2 Расчёт второго сварного соединения35
6.3 Расчёт резьбового соединения36
6.4Расчет подшипников выходного вала40
Безопасность жизнедеятельности42
2.Мероприятия по улучшению условий и охраны труда в ремонтной мастерской44
3 Расчет защитного зануления42
Технико-экономическое обоснование выпускной квалификационной работы46
Выводы ипредложения 60
Основная задача сельскохозяйственного производства—обеспечить население высококачественными продуктами питания а перерабатывающую промышленность—соответствующими видами сырья. Важной составной частью материальной базы для успешного решения актуальной задачи являются совершенствование ремонтной службы предприятия.
Задача ремонтной службы предприятия - обеспечение постоянной работоспособности оборудования и его модернизация изготовление запасных частей необходимых для ремонта повышение культуры эксплуатации действующего оборудования повышение качества ремонта и снижение затрат на его выполнение. Ремонтную службу предприятия возглавляет отдел главного механика предприятия (ОГМ). Функции ремонтной службы предприятия:
- разработка нормативов по уходу надзору обслуживанию и ремонту оборудования;
- планирование ППР (планово-предупредительных ремонтов);
- планирование потребности в запасных частях;
- организация ППР и ППО (планово-предупредительного обслуживания) изготовления или закупки и хранения запчастей;
- оперативное планирование и диспетчирование сложных ремонтных работ;
- организация работ по монтажу демонтажу и утилизации оборудования; - организация работ по приготовлению и утилизации смазочно-охлаждающих жидкостей (СОЖ);
- разработка проектно-технологической документации на проведение ремонтных работ и модернизации оборудования;
- контроль качества ремонтов;
Выгоничский ДРСУч занимается строительством ремонтом и содержанием автомобильных дорог. Основной вид деятельности – содержание автомобильных дорог. На содержании Выгоничского ДРСУч находится 14864 км дорог. Из них 2458 км – III категории; 12045 км – II категории; 364 км – V категории.
2 Цель и задачи работы
Выгоничским ДРСУч на автомобильных дорогах находящихся на содержании в течение всего года выполняются следующие виды работ: зимнее содержание и содержание в осенне-весенний период. Зимнее содержание включает в себя следующие виды работ:
- очистка дорог от снега;
- очистка обочин от снега;
- обработка дорог ПСС от снега и наледи.
В зимний период также приходится выполнять ямочный ремонт автомобильных дорог на «безопасность». Зимой ямочный ремонт выполняется холодной асфальтобетонной смесью «СОМС»-10.
Осенне-весеннее содержание включает в себя следующие виды работ:
- вырубка кустарников;
- окраска обустройства автомобильных дорог;
- установка дорожных знаков;
- ямочный ремонт всей сети дорог.
Ямочный ремонт летом выполняется эмульсией асфальтобетоном.
В таблице 1.1 представлены все виды техники которые используются для содержания и ремонта автомобильных дорог.
Таблица 1.1 Состав машинно-тракторного парка
Газ5201 Бензовоз цистерна
Грейдер прицепной ДС-105
Так как при ремонте дорог техника часто ломается на базе организации находится станция по ремонту машин.
4 Анализ состояния ремонтно-обслуживающей базы
В настоящее время станция занимается ремонтом машин тракторов и специального оборудования. Ремонтная станция является подразделением организации и не имеет своего счета.
Поэтому экономические показатели приводятся согласно данным бухгалтерии.
Согласно данным бухгалтерии организации доход от выполненных работ за год составил – 25 млн. рублей. Из них: затраты по содержанию автомобильных дорог составили – 158 млн. рублей; строительство и ремонт автомобильных дорог – 73 млн. рублей; прочие – 19 млн. рублей. Прибыли как таковой организация не получила.
5 Обоснование темы выпускной квалификационной работы
Выгоничский ДРСУч занимается строительством ремонтом и содержанием автомобильных дорог. Основной вид деятельности – содержание автомобильных дорог. На содержании Выгоничского ДРСУч находится 14864 км дорог.Выгоничским ДРСУч на автомобильных дорогах находящихся на содержании в течение всего года выполняются следующие виды работ: зимнее содержание и содержание в осенне-весенний период. Зимнее содержание включает в себя следующие виды работ:
Текущий ремонт тракторов и машин по ремонту дорог производится своими силами в ремонтноймастерской.
В ней выполняют ремонт оборудования его модернизацию изготавливают новые и восстанавливают изношенные детали сборочных единиц небольшихразмеров осуществляют монтаж и демонтаж отремонтированного оборудования.
Технологическая часть
1 Расчет общей трудоемкости ремонтных работ
Определим по формуле общую трудоёмкость всех работ при ремонте чел.-ч
гдеW программа предприятия;
Туд – удельная трудоемкость ремонта чел.ч;
Туд – принимаем для ремонта тормозных барабанов Туд=30 чел.ч;
Таким образом трудоемкость работ составила 9000 чел.ч.
Для примера определим годовую трудоёмкость операции по наплавке
Результат расчета общей трудоемкости ремонтных работ представлен в таблице 2.1.
Таблица 2.1 – Примерное распределение трудоемкости ремонта машин по видам работ процент от общей годовой трудоемкости
Разборочно-моечный участок
Слесарно-механический
Продолжение таблицы 2.1
Наименование участка
Суммарная трудоемкость
2 Распределение трудоёмкости ремонтных работ по технологическим видам и обоснование состава участка
Распределение общей трудоемкости операций по видам проводится перед технологическим расчетом участка. От точности распределения зависит состав участка т. е. его производственная структура точность последующих расчетов количества рабочих оборудования и производственных площадей постов. В дипломном проекте распределение ремонтных работ по технологическим видам проводят используя принятые посты входящие в проектируемый участок. Структуру участка можно обосновать на основании анализа типовых проектов.
Для восстановления тормозных барабанов в состав участка должны быть включены следующие посты:
- пост наружной мойки;
- дефектовочный пост;
- пост восстановления и контроля тормозных барабанов;
Исходя из принятого участка на посту очистки будет выполнятся мойка ; на дефектовочном посту – разборка дефектовка и сборка; на посту восстановления – ремонт тормозного барабана и его контроль. Результаты распределения приводят в таблице 2.2.
Таблица 2.2 – Распределение трудоёмкости ремонтных работ по технологическим видам
Годовая трудоёмкость
Восстановление и контроль
3 Режим работы сезонного текущего ремонта и фонда времени
Главный корпус предприятия работает по прерывной рабочей неделе в одну смену с одним выходным днем. Продолжительность рабочей недели принимается 40 ч смены 8 в предпраздничные дни 7 в предвыходные 5 ч.
Исходя из принятого режима работы главного корпуса определяют годовые фонды времени работы рабочих оборудования. Различают номинальный и действительный годовые фонды.
Номинальный фонд времени главного корпуса оборудования и рабочих это количество рабочих часов в соответствии с принятым режимом работы без учета возможных потерь
Фн.р.=Драб.tсм nДпродtсок (2.3)
где Др Дп и Дв соответственно количество рабочих праздничных и выходных дней в году (определяют по календарю);
tсм продолжительность смены ч;
tс.п иtс.в сокращение смены соответственно в предпраздничные и предвыходные дни ч;
п число смен (при определении годового фонда времени п = 1;
Годовой фонд времени Фн.р чел.-ч работы рабочих определяется по формуле
Фн.р.=2488171=1977чел.ч
Годовой фонд времени Фн.о чел.-ч работы оборудования и главного корпуса определяется по формуле
Действительный годовой фонд времени Фд.р чел.-ч рабочих определяют по формуле
Фд.р.= (Фн.р Дрtсмn) р (2.4)
гдеДо продолжительность отпуска в рабочих днях;
р коэффициент потерь рабочего времени (р= 096).
Продолжительность отпуска для испытателей двигателей составляет 36 дней для остальных рабочих 28 рабочих дней.
Для испытателейдвигателей
Фд.р.= (1997 3681)096= 1640 чел.ч.
Для остальных рабочих
Фд.р.= (1997 2881)096= 1683 чел.ч.
Действительный годовой фонд времени работы оборудования Фд.орассчитывают по формуле
где0 коэффициент использования оборудования учитывающий потери рабочего времени на проведение ремонта и ТО оборудования (0= 095).
Фд.о= 1977095= 1878 чел.ч.
4 Технологический расчёт участка
4.1 Расчёт штата участка
Число производственных рабочихnр.с и nр.я(явочное и списочное) рассчитывают по каждому участку отдельно
где Тгi годовой объем работ i-гo технологического вида (таблица 2.2)чел.ч.
Результаты расчета числа рабочих приводят по форме таблицу 2.3.
Списочное число рабочих учитывают при расчете числа остальных работников сезонного текущего ремонта и площади бытовых помещений. По явочному числу определяют число рабочих на участках.
Таблица 2.3 – Число производственных рабочих
Технологический видработ
наименование участка
Восстановление иконтроль
4.2 Расчет и подбор технологического оборудования и оснастки
Оборудование и стандартизованные приспособления принимают в соответствии с технологическими процессами ремонта КПП. Кроме того для организации рабочих мест на участке необходимо предусмотреть организационную оснастку (производственную мебель).
Для наружной очистки машин перед ремонтом принимаем передвижную моечную установку ОМ-22616 и ОМ-5361. Мойка сборочных единиц и деталей при ремонте машин производится в камерных машинах периодического действия. Без расчета принимаем моечную машину ОМ-4610.
Остальное оборудование участка и организационная оснастка подбираются исходя из нужд технологического процесса. Для участка разработан табель оборудования организационной оснастки приспособлений и инструмента.
Принятое технологическое оборудование и организационную оснастку сводят в таблице 2.4. В таблице по каждому участку отдельно подсчитываем суммарную площадь занимаемую оборудованием.
Таблица 2.4 – Ведомость оборудования и организационной оснастки
Шланговый полуавтомат
точильно-шлифовальный
4.3 Расчёт площадей постов участка по восстановлению тормозных барабанов
Площадь участка и капитального ремонта КПП и постов которые он включает рассчитываем по формуле
где Sоб – площади занимаемые оборудованием (таблица 2.4) м2;
– коэффициент учитывающий рабочие зоны и проходы.
Рассчитаем площадь участка по ремонту тормозных барабанов
Площади остальных производственных участков рассчитываются аналогично
Sвсп=(20 40%)Fосн(2.9)
Sвсп=04996=398 м2 (2.10)
Sобщ. рас=996+398=1394 м2
Расчетное значение площади необходимо скорректировать на основании стандартных требований принимаемая площадь должна быть кратна 6 согласно этому принимаем участок площадь Sприн=144 м2 и размерами 12×12.
4.4 Компоновка участка по восстановлению тормозных барабанов
Участок по восстановлению тормозных барабанов было решено разместить в ремонтной мастерской хозяйства. Компоновку проводим на основании расчетов площадей постов. Компоновочный план составляем с учетом рационального расположения производственных участков.
Взаимосвязь между участками должна соответствовать ходу технологического процесса. Участки пожароопасные с выделениями газов и избыточного тепла следует размещать в отдельных помещениях расположенных у наружных стен.
Такое расположение этих участков облегчит устройство вентиляции помещений.
Нами было решено проектируемый участок расположить по левой стороне мастерской и отделить его перегородкой. Посты участка также отделить перегородками друг от друга перегородками.
5 Разработка технологических мероприятий по восстановлению тормозных барабанов
5.1Основные типы и назначение тормозных систем грузовых автомобилей
Тормозная система автомобиля предназначена - для замедления или осуществления полной остановки транспортного средства. В тормозную систему входит ряд составных частей – этотормозные колодки шланги тормозные цилиндры вакуумный усилитель барабаны или диски.
Современные грузовые автомобили оборудованы четырьмя автономными тормозными системами следующих типов: рабочей запасной стояночной и вспомогательной.Рабочая тормозная системаслужит для снижения скорости автомобиля с желаемой интенсивностью вплоть до полной остановки вне зависимости от его скорости нагрузки и величины уклонов дорог для которых он предназначен.
Запасная тормозная системапредназначена для плавного снижения скорости движения или остановки автомобиля в случае полного или частичного выхода из строя рабочей тормозной системы.
Эффективность рабочей и запасной тормозных систем автомобилей с полной массой свыше 12 т оценивается величиной тормозного пути или установившегося замедления при начальной скорости торможения 40 кмч на прямом и горизонтальном участке сухой дороги с твердым покрытием обеспечивающим хорошее сцепление колес с дорогой.
Стояночная тормозная системаслужит для удержания неподвижного автомобиля на горизонтальном участке пути или уклоне даже при отсутствии водителя. Эффективность стояночной тормозной системы должна обеспечивать удержание автомобиля на уклоне такой крутизны который он сможет преодолеть на низшей передаче. Вспомогательная тормозная системапредназначена для поддержания постоянной скорости автомобиля при движении его на затяжных спусках горных дорог и регулирования ее самостоятельно или одновременно с рабочей тормозной системой с целью разгрузки тормозных механизмов последней. Эффективность вспомогательной тормозной системы должна обеспечивать без применения иных тормозных систем спуск автомобиля со скоростью 30 кмч по уклону 7 % протяженностью 6 км.
Каждая тормозная система состоит из тормозных механизмов (тормозов) и тормозного привода. Имея общие элементы тормозные системы работают независимо и обеспечивают высокую эффективность торможения при любых условиях эксплуатации. Кроме того автомобили оснащены аварийной системой растормаживания тормозов стояночной тормозной системы системами контроля и аварийной сигнализации о работе тормозных систем и их приводов а также приводом тормозов прицепа. На грузовых автомобилях зачастую устанавливают такие виды сочетаний барабанных и дисковых механизмов:- четыре барабанные;- по паре барабанные и дисковые;- четыре дисковых.
– опорный диск 2 – колодка тормоза.3 – тормозной барабан 4 – вал разжимного кулака 5 – пробка отверстия для смазки 6 – червячная шестерня 7 – червяк8 – рычаг 9 – шток тормозной камеры 10 – корпус тормозной камеры 11 – крышка тормозной камеры 12 – диафрагма 13 – пружина 14 – кронштейн тормозной камеры 15 – крышка люка 16 – кронштейн осей колодок 17 – эксцентриковые оси колодок
Рисунок 2.1 - Рабочий тормозной механизм автомобиля
5.2Назначение анализ условий работы и основные дефекты восстанавливаемой детали
Во всех грузовых автомобилях используется традиционная тормозная система с пневматическим приводом и тормозными механизмами барабанного типа.Тормозная система грузовиков построена по типичной для грузовых автомобилей схеме: на колесах установлены фрикционные тормозные механизмы барабанного типа привод которых осуществляется с помощью пневматической системы. Тормоза такой схемы наиболее просты и эффективны для грузовиков различной массы.
Колесные тормозные механизмы состоят из трех основных компонентов: тормозного барабана тормозных колодок и привода колодок. Тормозной барабанкрепится на ступице колеса в свою очередь на барабане установлен колесный диск поэтому колесо и барабан вращаются как единое целое. Тормозные колодки и их привод установлены неподвижно. Торможение автомобиля производится за счет трения между колодками и внутренней поверхностью барабана: при необходимости снизить скорость или полностью затормозить грузовик колодки с помощью привода прижимаются к барабану вследствие чего скорость вращения барабана и закрепленного на нем колеса снижается и автомобиль теряет скорость. Для эффективного торможения барабан и колодки изготавливаются из материалов с максимальным коэффициентом трения. В целом тормозные барабаны используемые в автомобилях ЗИЛ различных моделей не отличаются от барабанов других грузовиков но имеют свои особенности конструкции и эксплуатации.
Тормозной барабан - это металлическая цельнолитая деталь цилиндрической формы которую условно можно разделить на две части— собственно барабан с гладкой внутренней поверхностью и фланец с отверстиями под установку шпилек. В частности в ряде моделей тормозных барабанов автомобилей ЗИЛ предусмотрены смотровые отверстия с помощью которых можно производить измерение зазора между колодками и барабаном оценивать состояние колодок и тормозного механизма и т.д. В барабанах для грузовиков ЗИЛ-5301 «Бычок» смотровых окон нет однако это компенсируется особым устройством фланца выполненным в виде приливов с отверстиями для шпилек— производить осмотр тормозного механизма можно через промежутки между этими приливами. Также из конструктивных особенностей барабанов тормозных ЗИЛ стоит отметить двойную функцию отверстий под шпильки— они одновременно служат и для крепления барабана к ступице и для монтажа колеса на барабан. Для этого используются шпильки с левой резьбой которые одной стороной вкручиваются в ступицу а на их другую сторону наворачиваются гайки удерживающие колесный диск.
Тормозные барабаны автомобилей ЗИЛотличаются высокой прочностью и надежностью. Это обеспечивается в первую очередь достаточно большой толщиной стенок а на некоторых барабанах также предусмотрены и ребра жесткости. В частности ребра жесткости есть на барабанах ЗИЛ-5301 поэтому они при своих компактных габаритах имеют высокую жесткость и надежность. На сегодняшний день все тормозные барабаны ЗИЛ изготавливаются только из серого чугуна методом литья с дальнейшей расточкой. Обычно для этого используется серый чугун марок СЧ-20 и СЧ-24. Интересно отметить что на конвейеры ЗИЛ поставляются «родные» барабаны но на рынке присутствуют барабаны и ряда сторонних производителей. Независимо от производителя все тормозные барабаны должны соответствовать ГОСТ 31341-2007 только в этом случае они будут обеспечивать надежное торможение и безопасность автомобиля.
На сегодняшний день выпускается несколько типов тормозных барабанов ЗИЛ которые отличаются конструкцией и применимостью. Но независимо от конструкции все барабаны делятся на две больших категории по внутреннему (рабочему) диаметру:
- с внутренним диаметром 420 мм— все «большие» модели грузовиков ЗИЛ старого и нового производства;
- с внутренним диаметром 320 мм— только модели ЗИЛ «Бычок».
При этом большие барабаны имеют восемь отверстий под шпильки малые имеют только шесть отверстий.
Также все тормозные барабаны ЗИЛ делятся на четыре типа по ширине фрикционных накладок колодок:
-70 мм (только передние тормозные барабаны некоторых старых и новых моделей);
- 80 мм (передние и задние тормозные барабаны ЗИЛ «Бычок»);
-140 мм (передние и задние тормозные барабаны средне тоннажных автомобилей); -
0 мм (задние тормозные барабаны большинства новых и старых моделей).
Один и тот же барабан может использоваться в разных моделях автомобилей ЗИЛ на разных осях. Например барабан одинаковой конструкции используется на колесах заднего моста ЗИЛ-433360 и на передней оси ЗИЛ-433180. С другой стороны во многих автомобилях на передней и задней осях используются разные барабаны— на том же ЗИЛ-433180 на передней оси установлены узкие тормозные барабаны (под колодки шириной 140мм) а на заднем мосту— широкие (под колодки шириной 180мм).
Также тормозные барабаны ЗИЛ находят широкое применение на автобусах ПАЗ включая новые модели «Аврора». Наибольшее применение на павловских автобусах находят применение тормозные барабаны под колодки шириной 140мм а в моделях «Аврора» (ПАЗ-4230) на заднем мосту— барабаны под колодки 180 мм. В любом случае при необходимости замены тормозных барабанов необходимо выбирать новые барабаны по их каталожным номерам— это застрахует от ошибки и лишних затрат.
Тормозные барабаныне требуют специального ухода и в процессе эксплуатации практически не доставляют проблем водителю. Однако барабан постоянно подвергается трению поэтому он как и фрикционные накладки колодок подвержен интенсивному износу в результате чего эффективность торможения со временем снижается. Именно этот износ необходимо контролировать и периодически принимать меры для обеспечения надежного торможения. В частности при ТО-2 рекомендуется проверять свободный ход штока пневматической тормозной камеры— в рабочем состоянии ход штока передних тормозов лежит в пределах 15-20мм задних— 20-30мм. При таком ходе штока зазор между фрикционными накладками колодок и внутренней поверхностью барабана достигает 04 мм.
Если ход поршня увеличен до35 и40мм у передних и задних тормозных камер соответственно то увеличен и зазор между колодкой и барабаном — в этом случае необходимо произвести регулировку. В случае если регулировкой не удается достичь нормального хода штока то нужно оценить состояние колодок и барабана на предмет их износа. Толщина фрикционных накладок на колодках должна быть не меньше 1мм в противном случае их необходимо заменить на новые. Если же даже после замены колодок зазор между ними и барабаном слишком велик то это говорит о чрезмерном износе барабана и необходимости его замены.
Очень часто барабан имеет неравномерный износ (приобретает яйцеобразную форму) а на его внутренней поверхности появляются борозды поэтому торможение становится менее эффективным. В данном случае барабан подвергается расточке для придания ему цилиндрической формы и полировки поверхности. Растачивать барабан можно только по так называемым ремонтным размерам максимальный внутренний диаметр до которого допускается расточка составляет 426мм (для барабана ЗИЛ «Бычок»— 324мм). При дальнейшем увеличении рабочего (внутреннего) диаметра барабан эксплуатировать нельзя так как он теряет свои прочностные качества и может стать причиной аварии. Такой барабан должен быть в обязательном порядке заменен новым. При регулярном осмотре расточке и замене тормозных барабанов тормозная система автомобилей будет работать надежно в любых условиях.
Дефекты тормозных барабанов:
-износ по внутренней поверхности;
-износ резьбовых отверстий не допускаются;
-сколы трещины не допускаются.
5.3 Обзор применяемых способов восстановления
Металлическое покрытие при данном способе восстановления детали формируется в результате приварки к ней материала в виде ленты проволоки
порошков или их сочетания используя принцип электроконтактной сварки. Проволоку применяют для восстановления гладких и резьбовых участков валов ленты — наружных и внутренних цилиндрических поверхностей порошки — цилиндрических и конических наружных поверхностей. Приварка осуществляется в результате одновременных теплового и механического воздействий на материалы покрытия и детали импульсами электрического тока и приложением сжимающей нагрузки.Для уменьшения теплового воздействия на деталь и совмещения процессов приварки и закалки применяют охлаждение водой. Процесс формирования покрытия состоит из последовательности тепломеханических циклов включающих: прижатие привариваемого материала к детали; нагревание их в зонах контакта до пластического состояния пропусканием коротких импульсов электрического тока; совместное деформирование привариваемого материала и поверхностного слоя восстанавливаемой детали обеспечивающих электроконтактную сварку в точках их контакта. Прочность соединения покрытия с деталью может достигать 40 ГПа. Метод позволяет создавать покрытия из цветных и черных металлов на стальных и чугунных деталях. Электроконтактная приварка ленты эффективно используется и широко распространена при восстановлении небольших по длине круговых поверхностей.Перекрытие сварочных точек между собой достигается за счет частоты импульсов тока частоты вращения детали и скорости перемещения сварочной головки. Метод электроконтактной приварки имеет определенные преимущества и недостатки. Нагревание заготовки пропусканием тока непосредственно через свариваемые материалы обеспечивает ряд преимуществ рассматриваемого метода восстановления: не происходит выгорания легирующих элементов и разбрызгивания металла; отпадает необходимость в применении защитной среды (флюса газа); благодаря отсутствию характерного для электродуговых методов выделения вредных газообразных веществ обеспечиваются экологически безопасные условия труда и др. Электроконтактная приварка покрытий является энергосберегающим и ресурсосберегающим процессом. Экономия энергии обусловлена прежде всего тем что не требуется расплавление материала покрытия и поверхностного слоя детали а энергия расходуется только
на их нагревание до пластического состояния причем не по всему объему а только в отдельных точках (зонах контакта). Экономия ресурсов (материала покрытия) обеспечивается за счет возможности приварки тонкого слоя материала благодаря чему уменьшается припуск на механическую обработку. При этом сокращаются энергетические материальные и трудовые затраты на ее выполнение.
Это преимущество особенно проявляется при небольшой толщине покрытия необходимой для восстановления размеров детали так как при других методах наплавки большая часть нанесенного слоя металла должна быть удалена резанием. За счет минимизации припусков на механическую обработку и исключения разбрызгивания расход наносимого материала по сравнению с электродуговой наплавкой сокращается в 3—4 раза при повышении производительности труда в 2—3 раза. Всем методам электроконтактной приварки металлических покрытий присущи недостатки характерные для термических методов восстановления деталей машин с нанесением слоя металла. К ним относится прежде всего значительное снижение усталостной прочности. Поэтому данный метод может использоваться при достаточном запасе прочности восстанавливаемых деталей.
При постоянном токе сварка может быть на прямой (изделие присоединено к положительному полюсу источника питания) или обратной (изделие присоединено к отрицательному полюсу источника питания) полярности.
Сварочная дуга плавит металлический стержень электрода с покрытием и металл изделия. Расплавленный металл электрода со шлаком в сварочной ванне смешивается с металлом изделия шлак всплывает на поверхность. После удаления дуги металл в сварочной ванне кристаллизуется и образует шов. На поверхности шва образуется слой застывшего шлака.
Дляручной дуговой сваркииспользуют покрытыеэлектроды представляющие собой металлический стержень с нанесенным на него покрытием. Электродное покрытие - это смесь измельченных компонентов и связующего вещества нанесенная на металлический стержень методом прессования или (реже) окунанием.
Покрытия составляют на базе комбинированной газошлаковой защиты плавящегося металла. В одних видах покрытий имеет место шлаковая защита сварочной ванны а в других газовая. В состав электродных покрытий входят: -стабилизирующие элементы процесса зажигания и горения дуги в виде щелочных и щелочно-земельных металлов: калия натрия цезия кальция; -газообразующие компоненты создающие газовую защиту дуги и сварочной ванны в виде
веществ: крахмала древесной муки декстрина и др; -шлакообразующие составляющие: полевой шпат кремнезем каолин тальк рутиловый концентрат плавиковый шпат и др; -раскислители - вещества способствующие восстановлению окиси железа имеющие большее сродство с кислородом чем железо: ферромарганец ферросилиций ферротитан и др; -легирующие элементы (марганец хром никель молибден ванадий алюминий и др.) для придания шву особых свойств; -пластификаторы - составляющие в виде слюды целлюлозы бетонита каолина и др. для повышения пластичности обмазки; -рафинирующие компоненты (соединения марганца и окиси кальция) выводящие из сварочной ванны серу и фосфор которые являются вредными примесями; -связующие вещества - натриевое калиевое и натриево-калиевое жидкое стекло.
Покрытие может быть основным целлюлозным рутиловым кислым также смешанным и специальным.
Электролитические покрытия (железнение)
Железнение— процессэлектролитическогоосаждения железа из водных растворов его закисных солей.Железоосаждают на катоде; анодом служат прутки или полосы малоуглеродистой стали.
Применяется как средство наращивания металла на изношенную поверхностьстальныхичугунныхдеталей при восстановлении их размеров. Железнение является весьма эффективным способом восстановления деталей; компоненты электролитов недефицитны скорость наращивания слоя высокая толщина слоя может достигать 8 мм.
Для получения износостойких покрытий с повышенными механическими свойствами и улучшенной структурой железнение проводят в электролитах содержащих марганец или никель.
Рассчитаем стоимость восстановления каждого способа по формуле (2.11) учитывая что удельная себестоимость восстановления составляет (руб.см2): электроконтактная приварка ленты – 105; сварка ручная дуговая – 05; электролитическое покрытие (железнение) – 03.
Произведем расчет площадей внутренней поверхности тормозного барабана (Sш) по формуле
Sш==138474 мм2=138474 см2
Рассчитываем стоимость восстановления для электроконтактной приварки ленты
CB1=138474105=145397 руб. (2.12)
Для ручной дуговой наплавки.
CB2=13847405=69237 руб. (2.13)
Для электролитического покрытия (железнения)
CB3=13847403=41542 руб (2.14)
Результаты расчетов сведены в таблицу 2.5
Таблица 2.5 – Себестоимость восстановления тормозного барабана
Метод восстановления
Себестоимость восстановления руб.
Электроконтактная приварка ленты
Сварка ручная дуговая
Электролитическое покрытие
Целесообразность того или иного метода определим из выражения:
- для электроконтактной приварки ленты
- для ручной дуговой сварки
- для электролитического покрытия (железнение)
Из сделанных расчетов видно что самым целесообразным методом восстановления тормозных барабанов будет электролитическое покрытие (железнение).
КОНСТРУКТОРСКАЯ РАЗРАБОТКА
1 Обоснование разработки
От состояния шин зависят тягово-сцепные качества и проходимость трактора и автомобиля их производительность и расход топлива то есть шины во многом определяют экономичную и производительную работу машины. Кроме того шины - быстроизнашивающиеся и дорогостоящие части машины стоимость которых составляет примерно 12% стоимости машины. За срок службы машины шины обновляются три-четыре раза а поэтому затраты относящиеся к эксплуатации шин составляют около 20% общих затрат на эксплуатацию трактора. Доля шин в обшей годовой потребности в запасных частях трактора составляет 40% по стоимости и около 50% по массе. Поэтому к эксплуатации и техническому обслуживанию шин следует относиться особенно внимательно.
На срок эксплуатации шин влияет не только соблюдение правил эксплуатации и технического обслуживания качество их изготовления но и условия в которых они работают: температура и влажность воздуха свойства почвы особенности дорожного покрытия. При использовании трактора на полевых работах срок эксплуатации шин достигает 6000 ч а на транспортных работах они изнашиваются в несколько раз быстрее. В горных районах на каменистых почвах срок эксплуатации шин уменьшается на 25 35% а зимой на снежном покрове наоборот увеличивается на 25 30%.
Для обеспечения наименьшего износа шин рекомендуется выполнять следующие правила.
- строго соблюдать нормы внутреннего давления в шинах в зависимости от действующих на них нагрузок и условий работы трактора.
- при движении на транспортных передачах следить не «ведет» ли трактор в сторону. При «уводе» остановить трактор и проверить состояние шин.
- не оставлять трактор на грунте загрязненном нефтепродуктами.
- не допускать биения и виляния колес для чего необходимо своевременно затягивать крепление дисков колес и рулевой трапеции регулировать осевое перемещение подшипников ступиц колес а также устранять нарушения регулировок гидроусилителя рулевого управления.
Периодически (не реже одного раза в году) переставлять шины с одного борта на другой для более равномерного износа. При перестановках нужно учитывать направленность рисунка протектора ведущих шин: вращение колеса должно совпадать с направлением стрелки на боковине шины. Для передних ведущих и направляющих шин допускается перестановка без учета направленности рисунка протектора когда трактор используется на транспортных работах. Процесс снятия и перестановки колес довольно трудоемкий это связанно с большим весом колёс а также низкой механизацией данного процесса. Из вышесказанного представляется что необходимо разработать устройство для снятия и установки колес которую можно будет применять в любом удобном месте.
Лучше всего к этим требованиям подходит тележка для снятия и установки колес. С помощью данной тележки можно снять доставить на шиноремонтный участок и установить отремонтированное колесо любой грузовой автомобиль и трактор. Для выполнения этих операций достаточно одного слесаря.
2 Обзор существующих конструкций
Тележка П-254 – предназначена для снятия установки и транспортировки одинарных и сдвоенных колес тракторов грузовых автомобилей и автобусов в том числе в сборе со ступицами и тормозными барабанами. Имеет механический привод.
Технические характеристики: грузоподъемность – 700 кг; высота подъема – 180 мм; минимальный диаметр снимаемого колеса – 850 мм; максимальный диаметр снимаемого колеса – 1300 мм; масса тележки – 100 кг. Тележка П-254 имеет относительно простую конструкцию простоту изготовления напри этом плохую устойчивость (из-за трех колесной тележки) и небольшую высоту подъёма.
Рисунок 3.1 – Тележка П-254
Тележка гидравлическая для съема колес BigRed TX12001– предназначена для снятия и установки колес тракторов грузовых автомобилей специального транспорта автобусов. Имеет гидравлический привод подъёма колес обладает относительно высокой грузоподъёмностью (12 т) надежная проста по конструкции и удобная в использовании. Недостаток невысока высота подъёма.
Рисунок3.2 – Тележка гидравлическая BigRed TX12001
Подъемное устройство для сервиса шин WINNTEC (Голандия) – предназначена для снятия и транспортировки автомобильных колёс. Подъём осуществляется мускульной силой человека.
Данное подъёмное устройство имеет простую конструкцию малый вес и низкую стоимость. Недостатками данного устройства является высокая трудоемкость невысокая производительность. . Технические характеристики: грузоподъемность – 250 кг максимальный диаметр снимаемого колеса – 645 мм; масса тележки – 7 кг.
Рисунок 3.3 – Подъемное устройство WINNTEC
Тележка для снятия колес RML600 – предназначена для подъёма и опускания крупногабаритных колёс при их монтаже и демонтаже с транспортного средства а так же транспортировки крупногабаритных шин по территории мастерской. Позволяет работать с колесами карьерных самосвалов гп до 55т. Позволяет транспортировать широкий диапазон типоразмеров колес: 18.00-25; 21.00-33; 21.00-35; 24.00-35. Имеет прочную и устойчивую металлическую конструкцию большой диаметр колес облегчает транспортировки по неровному полу. Простой и надежный механизм подъема посредствам полиспаст.
Рисунок 3.4 – Тележка для снятия колес RML600
3 Устройство и принцип работы тележки для снятия и установки колес автомобиля
Основной несущей частью тележки является П-образная рама (рис. 3.5) с двумя жесткими и двумя самоустанавливающимися колесами. Рама выполнена из труб списанных опор цементовозов. В трубу 1 вварена гайка в которую ввертывается винт 5. Второй конец его крепится в трубе 2. Вращают винт рукояткой 4. Его полный ход допускает сближение опорных труб 6 на 35 см. Тележку за стойки 3 приваренные к трубам подкатывают к колесу. Вращая винт устанавливают базу опорных труб отвертывают гайки крепления колеса и оно вместе со ступицей и тормозным барабанам ложится на тележку. Операцию выполняет один человек.
6 – трубы; 3 – стойка; 4 – рукоятка; 5 – винт; 7– жесткие колеса; 8 – самоустанавливающимися колеса
Рисунок 3.5 - Тележка для снятия и установки колес грузовых автомобилей
4 Меры безопасности при работе с тележкой и монтаже колес
- Требования безопасности перед началом работы:
а) работник должен знать устройство и принцип работы тележки;
б) перед началом убедится в комплектности тележки;
в) убедится в том чтобы все соединения были зашплинтованы;
г) убедится в исправности подъемного механизма тележки;
д) убедится в отсутствии деформаций и трещин основных деталях тележки.
-Требования безопасности во время работы:
а) подложить под колеса противооткатные упоры;
б) убедиться в том чтобы все крепежные соединения снимаемого узла были откручены;
в) перед снятием убедиться в надежном закреплении снимаемого колеса;
д) зафиксировать подъем узла на нужной высоте;
-.Требования безопасности по окончании работы:
а) привести в порядок рабочее место;
б) убедиться в исправности тележки. В случаи неисправности доложить заведующему мастерской;
в) убрать приспособление в отведенное для него место.
- Требования охраны труда в аварийных ситуациях:
а) немедленно прекратить работы и известить руководителя работ.
б) под руководством ответственного за производство руководителя работ оперативно принять меры по устранению причин аварий или ситуаций которые могут привести к авариям или несчастным случаям.
в) при возникновении пожара задымлении:
Немедленно сообщить по телефону «01» в пожарную охрану оповестить работающих поставить в известность руководителя подразделения сообщить о возгорании на пост охраны.
Открыть запасные выходы из здания обесточить электропитание закрыть окна и прикрыть двери.
Приступить к тушению пожара первичными средствами пожаротушения если это не сопряжено с риском для жизни.
Покинуть здание и находиться в зоне эвакуации.
Принять неотложные меры по предотвращению развития аварийной или иной чрезвычайной ситуации и воздействия травмирующих факторов на других лиц.
5 Разработка технологической карты на восстановление тормозных барабанов
Откручивание гаек ступицы
Рисунок. 3.6 - Схема технологического ремонта тормозного барабана
6 Расчет элементов конструкторской разработки
6.1 Расчёт сварного соединения
Рассчитываем стыковое сварное соединение планки со стойками на прочность. Расчёт такого соединения производится по проверке на растяжение.
На растяжение расчёт производится по следующей зависимости
где S толщина соединяемых деталей мм;
[] допускаемое напряжение для сварных соединений для стали 35
[] = 09[]р= 09162 = 1458 Мпа;
F нагрузка на сварное соединение Н.
Нагрузка на сварное соединение равна исходя из эпюры распределения сил на пружину F = 375 H.
Толщина соединяемых деталей равна S = 3 мм.
Длина шва определяется по формуле
где R радиус стойки R = 15 мм.
Тогда длина шва равна
Тогда напряжение будет равно
Это удовлетворяет условию так как [] = 1458 МПа > 013 МПа.
6.2 Расчёт второго сварного соединения
[] = 09[]р= 09162 = 1458 МПа;
где R радиус стойки R = 45 мм.
Это удовлетворяет условию так как [] = 1458 МПа > 004 МПа
6.3 Расчёт резьбового соединения
Рассчитываем на прочность резьбовое соединение гайки с штифтом.
Определяем необходимую силу затяжки резьбового соединения
где внутренний диаметр резьбы для резьбы М20 =17632 мм [21];
напряжение в стержне болта.
Тогда сила затяжки резьбового соединения равна
Рисунок 3.7-Параметры метрической резьбы общего назначения
Проверяем резьбу по условию прочности по напряжениям среза
где F = Fзат= 32097 H;
Н высота гайки мм. H = 8 мм;
К коэффициент полноты резьбы. Для треугольной резьбы К= 087;
Кт коэффициент неравномерности нагрузки по виткам резьбы Кт= 13;
допустимое напряжение среза =04 т = 04220 = 88 МПа.
Тогда напряжение среза будет равно
Это удовлетворяет условию так как [] = 88 МПа > 642 МПа.
6.4Расчет подшипников выходного вала
Выбор типоразмера подшипника
По таблице 7.2 назначаем подшипники радиальные шариковые однорядные типа 213 легкой серии
d=65мм; D=120мм;В=23мм; С=56 кH; C0=34 кН;
Определяем суммарные реакции:
Определяем эквивалентную нагрузку на подшипник
Fпр1 .=R1xKkKТK(3.8)
гдеКт – температурный коэффициент принимаем Кт=1;
Kб – коэффициент безопасности принимаем Кб=13;
Fпр1=384781110513=52522 Н
Определяем требуемую грузоподъемность
Безопасность жизнедеятельности
Охрана труда - это система законодательных организационных технических социально-экономических гигиенических и лечебно-профилактических мероприятий и средств направленных на обеспечение безопасности и сохранения здоровья работающих в процессе труда.
Научно-технический прогресс неоднозначно влияет на условия труда. К сожалению наряду с облегчением он зачастую повышает потенциальную опасность травм и заболеваний. Это связано в первую очередь с появлением более мощной и сложной техники повышением рабочих скоростей производственных процессов внедрением интенсивных технологий возрастанием психологической нагрузки на организм работающих и другими факторами. В связи с этим важно разрабатывать и внедрять в производство более надежные средства защиты человека от вредных и опасных факторов производственной среды научно обоснованные режимы труда и отдыха мероприятия по снижению эмоциональных нагрузок повышать качество их квалификационного обучения.
1 Анализ состояния условий охраны труда вОАО «Брянскавтодор» Выгоничский ДРСУч.
В настоящее время развиваясь хозяйство нуждается в применении все более новой и сложной техники а также технологий ее ремонта с ростом механизированных работ в хозяйстве должна также расти квалификация рабочих участвующих в производстве. Недостаток квалифицированных рабочих сказывается как на производительности труда так и на показателях производственного травматизма на рабочем месте одним из важнейших организационных мероприятий по профилактике производственного травматизма является проведениеинструктажей и обучение персонала безопасным приемам труда.
В организации существует должность инженера по охране труда. При приеме на работу рабочих он проводит вводный инструктаж. Затем первичный инструктаж на рабочем месте проводит непосредственно заведующий мастерскими.
Повторный инструктаж проводят один раз в полгода с целью проверки и повышения уровня знаний правил и инструкций по охране труда. Внеплановый инструктаж проводят при изменении правил по охране труда изменении технологического процесса замене модернизации оборудования и т.д. Например при замене нового оборудования для балансировки шин. Инструктажи проводятся низкого качества из-за отсутствия кабинета уголков и рабочих инструкций по охране труда. Не на всех рабочих местах имеются инструкции по технике безопасности а если имеются то не соответствуют нормативам. Не все опасные зоны отмечены соответствующими знаками безопасности. В течении 5 лет не проводилась проверка токарно-винторезных сверлильных заточных станков а также оборудования для зарядки аккумуляторов и сварочного что является нарушением правил охраны труда. Ряд из этих станков находится в неисправном состоянии. В мастерской имеются два мостовых крана которые в недавнем времени прошли аттестацию. Основное количество травм было получено на участке обкатки двигателей.
Основные причины несчастных случаев были из-за нарушения правил техники безопасности неисправности оборудовании и техники недостаточной освещенности. В мастерской искусственное освещение. В рабочее время включено общее освещение – это люминесцентные лампы обеспечивающие помещение равномерным дневным светом. Кроме этого на каждом станке имеется местное освещение. Оно позволяет легко и быстро различать цвет и размеры обрабатываемого объекта снижает утомляемость глаз и позволяет избежать заболеваний органов зрения снизить травматизм.
Для предотвращения травм глаз рабочие мастерской применяют защитные очки. Основной недостаток нарушающий санитарно-гигиенические условия - значительная загазованность мастерской особенно в период ремонтов и ТО. Отсутствует вытяжная вентиляция на сварочном участке. Нестабильная температура в мастерской особенно в зимний период приводит к снижению трудоспособности ухудшению условий работы и здоровья работников. Не всегда выдаются работникам средства индивидуальной защиты. Есть необходимость в выдаче рабочей одежды и ее периодической стирке. Во избежание поражения электрическим током рабочих станки и стенды заземлены кроме того положены деревянные настилы. Мастерская не обеспечена молниезащитой. Так как работы на участке по проведению ТР связаны с пожароопасностью для предотвращения коротких замыканий на щите установлены предохранители которые отключают станок при коротком замыкании. Помещение обеспечено противопожарным инвентарем: двумя ящиками с песком огнетушителями и подсобным инструментом установлены сигнальные знаки. Хотелось бы отметить что все огнетушители (марки ОХП – 10) перезаряжены в ноябре 2014 года. Место для курения оборудовано должным образом.
2.Мероприятия по улучшению условий и охраны труда в ремонтной мастерской
Инженеру охраны труда и заведующий мастерской необходимо выделить кабинет для проведения инструктажей по технике безопасности обеспеченный инструкциями стандартами наглядными пособиями. Заведующий мастерской обязан контролировать состояние охраны труда на участке. Своевременно выдавать индивидуальные средства защиты спецодежду и спецобувь. Главному инженеру совместно с заведующим мастерскими необходимо выполнить техническое освидетельствование и регистрацию токарно-винторезных сверлильных заточных и т.д. согласно требованиям безопасным приемам труда.
Для мастерской необходимо установить молнезащиту согласно инструкции РД 34.21.122-99. «Инструкция по устройству молниезащиты зданий и сооружений». В мастерской нужно провести капитальный и косметический ремонты. Погрузочно-разгрузочные работы должны выполняться в соответствии с существующими требованиями. В опасных местах рабочей зоны должны быть установлены знаки безопасности в соответствии с требованиями ГОСТ Р 12.4.026-2001 ССБТ «Цвета сигнальные знаки безопасности и разметка сигнальная». На сварочном участке необходимо установить вентиляционную вытяжку предварительно произвести соответствующие расчеты.
3 Расчет защитного зануления
Зануление состоит в соединении корпусов оборудования которое может оказаться под напряжением в результате нарушения изоляции с нулевым защитным проводом. Принцип действия защитного зануления – превращение пробоя на корпус в однофазное короткое замыкание т.е. образование цепи короткого замыкания корпус нулевой провод фазная обмотка трансформатора. В результате однофазного короткого замыкания перегорают плавкие вставки предохранителей и отключается повреждений участка сети.
Известно при срабатывании автомата 25А длина провода 3м. Провод медный. Сопротивление фазного и нулевых проводов соответственно 40м и 40м.
Условие надежного срабатывания защиты
где - ток нормального замыкания А;
- номинальный ток плавкой вставки предохранителя или ток срабатывания автомата А;
- коэффициент кратности защиты; для автоматов защиты =125 14
Активное сопротивление фазного и нулевого проводов определяют по формуле задавая их сечением длиной материалом проводников
где - длина провода м;
- сечение провода м;
- удельное сопротивление проводника ;
Для медных проводов
Сопротивление цепи «фаза-ноль» определяют по формуле
где - сопротивление фазного и нулевых проводов Ом
- индуктивное сопротивление петли «фаза-ноль» Омпринимаем
Расчетное значение тока короткого замыкания находят по формуле
где - фазное напряжение В; =220В
- сопротивление обмоток трансформатора Ом
- сопротивление фазного и нулевого провода Ом
По ожидаемому значению тока короткого замыкания подбираем предохранитель с номинальным током плавкой вставки таким образом чтобы соблюдалось условие надежного срабатывания. Напряжение на корпусах зануленного оборудования относительно земли определяют по формуле
где - сопротивление нулевого провода Ом
Рассчитываем напряжение на корпусах электродвигателей
где - сопротивление повторного заземления Ом;
- сопротивление рабочего заземления Ом
Повторноезаземлениенулевого проводавыполняется для повышения безопасности. Согласно правилам устройства электроустановок сопротивление заземления нейтрали и всех повторных заземлений нулевого провода должно быть не более 8 4 2Ом соответственно при линейных направлениях 220 или 380 и 660В источника трехфазного тока или 127220380В источника однофазного тока.
Определяем ток проходящий через человека
где - напряжение прикосновения
- сопротивление тела человека =1000 Ом
Ток равный 65МА вызовет фибрилляцию сердца. Опасность возникновения фибрилляции возрастает при прохождении тока через сердце во время Т-фазы кардиоцикла когда заканчивается сокращение желудочков и они переходят в расслабленное состояние. Наименьшее значение такого тока (100МА при частоте 50 Гц) называют пороговым фибрилляционным током.
Технико-экономическое обоснование выпускной квалификационной работы
Выводы и предложения
Выполнение выпускной квалификационной работы на тему « Участка ремонта тормозных барабанов грузовых автомобилейс разработкой технологии восстановления» позволяет сделать следующие выводы:
Технико-экономическая оценка деятельности предприятия выявляет что данное предприятие имеет хорошую базу для правильной организации ремонтных работ
Внедрение науки и передового опыта по ремонту и обслуживанию оборудования позволит рационально организовать мероприятия по ним и в тоже время сократить оборудования по причине выхода из строя узлов или деталей
Составление годового плана обслуживаний и ремонтов позволяет определить их количество в текущем году по каждой машине и затем распределить трудозатраты.
Анурьев В.И. «Справочник конструктора – машиностроителя» Т I – III –М : Машиностроение. 1973.
Баранов Л.Ф. Техническое обслуживание и ремонт машин: Учеб.пособие. (Сер.«Учебники ХХI века»). Ростов нД: Феникс 2001.-416с.: ил.
Волкова Н.А. Экономическое обоснование инженерно-технических решений в дипломных проектах: Учебное пособие.–2-е изд. перераб. и доп.–Пенза 2000.–168 с.
Ерохин М.Н. Детали машин и основы конструирования. –М.: -Колос 2004. -462 с
Кузнецов С.Н. «Охрана труда на предприятиях автомобильного транспорта» - М: Транспорт. 1986 – 539 с.
Купреенко А.И. Расчет технологических норм и экономических показателей при курсовом и дипломном проектировании Брянск.: Брянская ГСХА 2003-62с.
Курчаткин В.В. Надежность и ремонт машин В.В. Курчаткин Н.Ф. Тельнов К.А. Ачкасов и др.; Под ред. В.В. Курчаткина.–М.: Колос 2000.–776 с.: ил.
Кухарев О.Н. Организация и управление производством О.Н. Кухарев–Пенза: РИО ПГСХА 2007- 82с.
Спичкин Г.В. Третьяков А.М. Либин Б.Л. Диагностирование технического состояния автомобилей: Учеб.пособие для средн. сел. проф.-техн. училищ.–2-е изд. перераб. и доп.–М.: Высшая школа 1983.–368с.: ил
Справочник инженера по техническому сервису машин и оборудования в АПК.-М.:ФГНУ «Росинформагротех»2003.-604 с.
Суханов Б.Н. Борзых И.О. «Техническое обслуживание и ремонт автомобилей: пособие по дипломному проектированию». – М: Транспорт. 1991. – 209 с.
Техническая эксплуатация автомобилей: Учебник для вузов Е.С. Кузнецов В.П. Воронов А.П. Болдин и др.; Под ред. Е.С. Кузнецова.–3-е изд. перераб. и доп.–М.: Транспорт 1991–413 с.: ил.
Экономическая оценка инженерных проектов (методика и примеры расчетов на ЭВМ) Н.А. Волкова В.В. Коновалов И.А. Спицын А.С. Иванов: Учебное пособие.–Пенза 2002.–242 с.
Аннотация.doc
« Участок ремонта тормозных барабанов грузовых автомобилей с разработкой технологии восстановления» состоит из расчетно-пояснительной записки на страницах машинописного текста на 63 страницах и графической части на 7 листах формата А1.
Пояснительная записка состоит из 5 разделов и включает аннотацию введение предложения а также таблицы схемы рисунки выводы. Список использованных источников составляет 15 наименований.
Во второй части дано описание технологической части.
В третьей части пояснительной записки представлена конструкторская разработка
В четвертом разделе «Безопасность жизнедеятельности» представлены рекомендации по технике безопасности и охране труда при ремонте оборудования а также проведен расчет защитного зануления.
В пятом разделе пояснительной записки представлена технико – экономическое обоснование выпускной квалификационной работы.
Пояснительная записка заканчивается списком использованных источников.
экономика.docx
При определении экономического эффекта от внедрения разработанного технологического процесса ремонта автомобиля необходимо исходить из следующих положений:
начало и конец проектирования планируется осуществить в 2015 г.
новая технология и оборудование для нее рассчитана на функционирование в течении 5 лет начиная с 2016 года.
планируемая программа ремонта тормозных барабанов– 300в год.
амортизационный срок восстановленных деталей 5 лет.
Расчет единовременных капитальных вложений
Капитальные вложения на организацию участка по ремонту тормозных барабанов
где ЦОПТ – стоимость приобретенного оборудования руб.;
МН – затраты на монтаж и наладку оборудования руб.;
ТС – затраты по доставке.
МН = (02 025) ЦОПТ (5.2)
ТС = (01 02) ЦОПТ. (5.3)
Расчет капитальных вложений представляется на примере токарно-винторезного станка 1Д310.
МН = 022 447 = 983 тыс. руб.
ТС = 015 447 = 67 тыс. руб.
К = 447+ 983 + 67 = 6123 тыс. руб.
Аналогично производится расчет капитальных вложений на остальное оборудование. Перечень необходимого оборудования и рассчитываемые показатели представлены в таблице 5.1
Таблица 5.1 – Капитальные вложения на организацию участка по ремонту тормозных барабанов
Наименование оборудования
Стоимость приобретения тыс.руб.
Затраты на монтаж тыс. руб.
Затраты на доставку тыс. руб.
капитальные вложения тыс. руб.
Станок токарно-винторезный 1Д310
Шкаф электрический сушильный
Шланговый полуавтомат
Набор инструментов и приспособлений
Верстак мастера наладчика
Расчет суммарного экономического эффекта
Суммарный экономический эффект по годам расчетного периода
где РТ – стоимостная оценка результатов руб.;
ЗТ – стоимостная оценка затрат на осуществление мероприятий за расчетный период руб.
Суммарная оценка результатов за расчетный период
где tн – начальный год расчетного периода (2012 г.);
tк – конечный год расчетного периода (2017 г.);
t – коэффициент приведения к расчетному году результатов и затрат;
Аt – программа ремонта в t-м году расчетного периода шт.;
Ц – цена реализации услуги по ремонту автомобиля Ц = 23 тыс. руб.
Стоимостная оценка результатов по годам расчетного периода
Рt2016 = 23 250 09091 = 5227 тыс. руб.
Рt2017 = 23 250 08264 = 4752 тыс. руб.
Рt2018 = 23 250 07513 = 423 тыс. руб.
Рt2019 = 23 250 06830 = 392 тыс. руб.
Рt2020 = 23 250 06209 = 357 тыс. руб.
Рт = Pt2016 + Pt2017 + Pt2018 + Pt2019 + Pt2020 =
= 5227 + 4752 + 423 + 392 + 357 = 21789 тыс.руб.
Стоимостная оценка затрат для осуществления мероприятий за расчетный период рассчитывается по формуле:
где Иt – текущие издержки ремонтного предприятия при ремонте автомобилей.
где Сtв – себестоимость ремонта в году t руб.
Себестоимость ремонта автомобиля
СВ = СЗ + СМ + СЭ + СН + СРФ (5.9)
где СЗ – заработная плата производственных рабочих руб.;
СМ – стоимость основных материалов руб.;
СН – накладные расходы руб.;
СЭ – стоимость электроэнергии руб.;
СРФ – стоимость ремонтного фонда руб.
Зарплата основных производственных рабочих с начислениями определяется по формуле:
СЗ = СЧС Д.З. tВ. (5.10)
где СЧС – средняя часовая тарифная ставка для сдельщиков СЧС = 60 руб.час.
Д.З. – коэффициент учитывающий дополнительную плату рабочим Д.З. = 115;
tВ – норма времени затрачиваемая на ремонт автомобиля.
Согласно хронометражу норма времени на восстановление тормозного барабана составляет 205 часов. Заработная плата на восстановление тормозного барабана
Сз = 60 115 72 = 1587 руб.
Стоимость основных материалов
СМ = НМ ЦМ руб. (5.11)
где НМ – норма расхода на один тормозной барабан;
ЦМ – цена материала.
СМ = 003 2520 =756 руб.
Стоимость электроэнергии
где QЭ – расход электроэнергии кВтч.;
ЦЭ – стоимость 1 кВтч электроэнергии равная 708 руб.
СЭ = 475 708 = 336 руб.
Накладные расходы принимаются в процентном отношении к заработной плате рабочих
где RН – процент накладных расходов принимается по фактическим данным.
Стоимость ремонтного фонда вычисляется в согласии с ценами на металлический лом
где ЦЛ – цена металлического лома ЦЛ = 32 руб.кг;
Р – масса ремонтной дополнительной детали(втулки) Р = 028 кг.
СРФ = 12 08 = 96 руб.
Себестоимость ремонта тормозного барабана составит
СВ = ( 1587 2) + 756 + 336 + ( 1111 2 ) +96 = 6584 руб.
Иt = 06584 372 = 245 тыс. руб.
Единовременные затраты и ликвидационное сальдо реализуются в 2015 году.
Зt2015 = Кt – Лt (5.15)
где Кt – единовременные затраты тыс. руб.;
Лt – остаточная стоимость (ликвидационное сальдо) основных фондов ремонтного предприятия выбывающих в году t тыс. руб.
Зt2015 = 270 – 18 = 230 тыс. руб.
Стоимостная оценка затрат по годам составит
Зt2016 = 270 09091 = 2227 тыс. руб.
Зt2017 = 245 08264 = 204 тыс. руб.
Зt2018 = 245 07513 = 184 тыс. руб.
Зt2019 = 245 06830 = 1673 тыс. руб.
Зt2020 = 245 06209 = 1521 тыс. руб.
Стоимостная оценка затрат за расчетный период
Зt = 2227 + 204 + 184 + 1673 + 1521 = 9031 тыс. руб.
Экономический эффект по годам расчетного периода
Эt 2016 = 5227– 2227 = 300 тыс. руб.
Эt 2017 = 4752 – 204 = 271 тыс. руб.
Эt 2018 = 432 – 184 = 248 тыс. руб.
Эt 2019 = 392 – 167 = 2247 тыс. руб.
Эt 2020 = 357 – 1521 = 2049 тыс. руб.
Срок окупаемости капитальных вложений
где Эt – годовой экономический эффект в t году руб.
Суммарный экономический эффект за 5 лет равен
Эт = 21789 – 9031 = 12758 тыс. руб.
При единовременных капитальных вложениях на освоение технологии восстановления тормозных барабанов равных 8231 тыс. руб. и затратах с учетом пятилетнего срока применения технологии внедрение мероприятий окупится за 13 года.
Таблица 2 – Показатели экономической эффективности
Единовременные затраты Кt тыс. руб.
Ликвидационное сальдо Лt тыс. руб.
Текущие издержки Иt = Сt Аt тыс. руб.
Коэффициент приведения
Затраты с учетом фактора времени Зt = Иt t тыс. руб.
Экономический эффект по годам Эt тыс. руб.
Экономический эффект нарастающим итогом за период тыс. руб.
Итог за 5 лет тыс. руб.
Срок окупаемости лет
Таким образом для внедрения проекта необходимы дополнительные капитальные вложения 230 тыс. руб. при этом экономический эффект составит 1276 тыс. руб. срок окупаемости затрат 13 года.