Проект комплекса по перегрузке минеральных удобрений




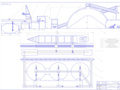
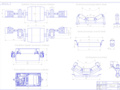
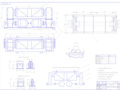
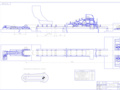
- Добавлен: 25.10.2022
- Размер: 4 MB
- Закачек: 3
Описание
Состав проекта
![]() |
![]() |
![]() ![]() ![]() |
![]() ![]() ![]() |
![]() ![]() ![]() |
![]() ![]() ![]() |
![]() ![]() ![]() |
![]() ![]() ![]() |
![]() ![]() ![]() |
![]() ![]() ![]() |
![]() ![]() ![]() |
![]() ![]() ![]() |
![]() ![]() ![]() |
![]() ![]() ![]() |
![]() ![]() ![]() |
![]() ![]() ![]() |
![]() ![]() ![]() |
![]() ![]() ![]() |
![]() ![]() ![]() |
![]() ![]() ![]() |
![]() ![]() ![]() |
![]() |
![]() |
![]() ![]() ![]() ![]() |
![]() ![]() ![]() ![]() |
![]() ![]() ![]() ![]() |
![]() ![]() ![]() ![]() |
![]() ![]() ![]() ![]() |
![]() ![]() ![]() ![]() |
![]() ![]() ![]() ![]() |
![]() ![]() ![]() ![]() |
![]() ![]() ![]() ![]() |
![]() ![]() ![]() ![]() |
![]() ![]() ![]() ![]() |
![]() ![]() ![]() ![]() |
![]() ![]() |
![]() ![]() |
![]() ![]() |
![]() ![]() |
![]() ![]() |
![]() ![]() |
![]() ![]() |
![]() ![]() |
![]() ![]() |
![]() ![]() |
![]() ![]() |
![]() ![]() |
Дополнительная информация
6Расчет ПМ.doc
1 Описание судопогрузочной машины
Судопогрузочная машина предназначена для загрузки минеральных удобрений в трюм судна и является составной частью специализированного конвейерного комплекса. Машина передвигается вдоль причала по рельсовым путям. Вдоль крановых путей располагается конвейерная галерея в которой находятся магистральные конвейеры подающие груз со склада на судопогрузочную машину. Магистральный конвейер оборудован устройством для промежуточной разгрузки - разгрузочной тележкой которая перемещается вдоль конвейера. Разгрузочная тележка соединена шарнирно с погрузочной машиной и обеспечивает подачу груза на конвейер фронтальной машины. Телескопический конвейер расположенный в подъемной галерее а также телескопическая труба установленная в месте разгрузки конвейера позволяет принимать суда практически всех типов.
Основные технические характеристики судопогрузочной машины приведены в таблице 6.1.
Таблица 6.1 - Технические характеристики судопогрузочной машины
минеральные удобрения
Насыпная плотность груза
Длина галереи от оси вращения
Скорость конвейерной ленты
Ширина конвейерной ленты
Скорость передвижения машины
Скорость подъема галереи
продолжение таблицы 6.1
Максимальный вылет конвейера
Минимальный вылет конвейера
Скорость изменения вылета
Судопогрузочная машина представляет собой металлоконструкцию портального типа установленную на четыре ходовые тележки. Портал представляет собой пространственную жесткую раму коробчатого профиля состоящую из нескольких частей соединенных при монтаже болтами. Колея портала составляет 105м что позволяет расположить под ним двухпутные железнодорожные рельсы. Каждая ходовая тележка входящая в состав механизма передвижения крана имеет 6 ходовых колес и свой привод. На тележках установлены рельсовые захваты с ручным приводом предохраняющие кран в нерабочем состоянии от угона ветром.
К порталу шарнирно прикреплена подъемная галерея выполненная в виде пространственной фермы в которой располагается телескопический ленточный конвейер. Также на портале расположена опорная металлоконструкция для механизма подъема галереи выполненная в виде коробчатой конструкции. На опорной части размещены кабина машинное отделение механизм подъема галереи а также устройства и приборы обеспечивающие работу механизмов крана и управление ими. Портал и опорная конструкция оборудованы лестницами и площадками для обслуживания механизмов и составных частей судопогрузочной машины.
Машинное помещение и кабина управления закреплены на опорной конструкции судопогрузчика. Машинное помещение выполнено из листовой стали и предназначено для размещения механизма подъема и электрооборудования. Съемная крыша установлена для удобства монтажа и демонтажа оборудования. Кабина управления также выполнена из листовой стали передняя и боковые стенки имеют открывающиеся окна для обзора рабочей зоны.
Механизм подъема галереи выполнен в виде барабанной лебедки с двухканатным нарезным барабаном и предназначен для подъема галереи в верхнее положение для закрепления ее «по штормовому» а также для безопасного передвижения судопогрузочной машины вдоль причала при стоянке судна. Закрепление галереи «по штормовому» соответствует нерабочему состоянию машины и используется при силе ветра более 20мс. Для ограничения подъема галереи по высоте а также для ограничения передвижения судопогрузочной машины установлены концевые выключатели.
Ленточный конвейер расположенный в галерее выполнен телескопическим с желобчатой роликоопорой ширина ленты 650мм скорость 125мс. Длина телескопической части составляет 195. Привод конвейера выполнен в виде мотор-барабана для экономии места а также удобного доступа к нему. Разгрузка конвейера осуществляется с помощью телескопической трубы диаметром 300мм длина которой изменяется в пределах от 3 до 10м.
Привод всех механизмов - электрический. Питание судопогрузчика электроэнергией осуществляется гибким кабелем от наземных колонок. Длина кабеля позволяет крану передвигаться на 100м в каждую сторону от колонки. Для наматывания кабеля служит кабельный барабан установленный на портале.
Управление судопогрузчиком осуществляется крановщиком из кабины управления. В комплект крана входят запасные части и инструмент перечни которых включены в состав технической документации поставляемой с краном.
2 Расчет телескопического ленточного конвейера
2.1 Расчет класса использования конвейера расчет и выбор ленты
Принимаем класс использования конвейера по времени В4. В зависимости от класса использования конвейера принимаем весьма тяжелый режим работы конвейера.
Определим коэффициент планового использования конвейера в сутки ч по формуле:
где - время фактической работы конвейера в сутки ч учитывая класс использования конвейера по времени В4 принимаем ();
- количество часов в сутках .
Определим коэффициент планового использования конвейера в год ч по формуле:
где - время фактической работы конвейера в году ч учитывая класс использования конвейера по времени В4 принимаем ();
- количество часов в году .
Определим требуемую ширину ленты м по формуле:
где - производительность конвейера (тч);
- скорость ленты принимаем скорость ленты с учетом режима работы (мс);
- плотность груза (тм);
- коэффициент зависящий от угла естественного откоса груза (= 730) [47 с. 103 таблица 4.6];
- коэффициент зависящий от угла наклона конвейера () [47 с. 102 таблица 4.5].
Выбираем резинотканевую конвейерную ленту ТЛК-100 шириной =650мм с тремя =3 тяговыми прокладками толщиной допускающими рабочую нагрузку =100Нмм с толщиной резиновой обкладки рабочей поверхности =3мм нерабочей поверхности =1мм [7].
Проверим выбранную ширину мм ленты по условию размещения кусков:
где - размер типичного куска мм мм.
Существенное увеличение ленты требует уточнения скорости ленты мс по формуле:
Принимаем скорость ленты из нормального ряда [10].
Определим толщину ленты мм по формуле:
где - количество тяговых тканевых прокладок;
- толщина тяговой тканевой прокладки мм;
- толщина резиновой обкладки рабочей поверхности конвейерной ленты мм;
- толщина резиновой обкладки нерабочей поверхности ленты мм.
Определим нагрузку от массы груза кгм по формуле:
Определим нагрузку от массы ленты кгм по формуле:
где - плотность ленты (кгм);
Определим высоту конвейера м по формуле:
- длина наклонного участка конвейера (м);
- угол наклона конвейера ().
Определим предварительное тяговое усилие в ленте Н по формуле:
где - обобщенный коэффициент местных сопротивлений () [47 с. 118];
- распределенная масса вращающихся частей роликовых опор рабочей ветви (кгм) [47 с. 107];
- распределенная масса вращающихся частей роликовых опор холостой ветви (кгм) [47 с. 107];
- коэффициент сопротивления рабочей ветви () [47 с. 106 таблица 4.9];
- коэффициент сопротивления холостой ветви () [47 с. 106 таблица 4.9];
Определим предварительное максимальное натяжение ленты Н по формуле:
где - коэффициент запаса сцепления ленты с барабаном () [47 с. 46];
- тяговый фактор () [47 с.75].
Проверим необходимое минимальное число тяговых прокладок в ленте z по формуле:
где - принятое число тяговых прокладок (z=3);
- запас прочности ленты () [47 с. 66];
- максимальная допустимая рабочая нагрузка проклади (=200Нмм).
Таким образом произвели расчет и выбор ленты конвейера проверили ленту на прочность а также определили предварительное тяговое усилие и максимальное натяжение ленты.
2.2 Расчет и выбор поддерживающих устройств
Исходя из ширины и скорости ленты выбираем из нормального ряда диаметр роликов желобчатой роликоопоры =89мм и расстояние между роликоопорами рабочей ветви конвейера =1300мм [11].
Определим расстояние между роликоопорами холостой ветви конвейера мм по формуле:
Определим расстояние между роликоопорами в зоне загрузки на выпуклом участке трассы мм по формуле:
Определим наименьший диаметр приводного барабана мм по формуле:
где - коэффициент учитывающий прочность прокладок ленты () [47 с. 74];
- коэффициент зависящий от назначения барабана () [47 с.74].
Из нормального ряда принимаем диаметр приводного барабана =500мм [10].
Определим диаметр отклоняющих барабанов мм по формуле:
где - для отклоняющих барабанов установленных на трассе;
- для натяжных барабанов и отклоняющих установленных рядом с приводным.
Из нормального ряда принимаем диаметр отклоняющих барабанов установленных на трассе =250мм натяжного барабана и отклоняющего установленного рядом с приводным =400мм [10].
Определяем длину приводного и отклоняющих барабанов мм по формуле:
Таким образом произведя расчет выбирали желобчатую роликоопору диаметром =89мм и приняли диаметры приводного барабана =500мм отклоняющего - .
2.3 Подробный тяговый расчет конвейера
Уточненный тяговый расчет проводят с целью более точного определения максимального натяжения тягового элемента натяжения его в характерных точках трассы определения тягового усилия и мощности привода конвейера.
Определим тяговое усилие конвейера методом обхода по его контуру суть которого заключается в том что всю трассу конвейера начиная с точки сбегания тягового элемента с привода разбивают на отдельные участки (рисунок 6.1) сопротивление в которых постоянно по своему характеру. Обход лучше начинать с точки наименьшего натяжения тягового элемента пользуясь общим правилом: натяжение тягового элемента в каждой последующей по ходу контура точке равно натяжению в предыдущей точке плюс сопротивление на участке между этими точками:
где и - натяжения в двух соседних точках контура;
- сопротивление движению тягового элемента на участке между этими точками.
Если место нахождения точки наименьшего натяжения ленты установить невозможно то за начало отсчета можно принять любую из точек.
Рисунок 6.1 - Схема трассы конвейера для определения тягового усилия
Предположим что наименьшее натяжение ожидается в точке сбегания ленты с приводного барабана (точка 1) с которой и начнем тяговый расчет. Наименьшая сила натяжения ленты равна силе предварительного натяжения ленты:
Определим натяжение ленты в точке 2 S2 Н по формуле:
Определим натяжение ленты в точке 3 S3 Н по формуле:
где - коэффициент увеличения натяжения тягового органа от сопротивления при огибании роликовых батарей () [47 с. 47].
Определим натяжение ленты в точке 4 S4 Н по формуле:
Определим натяжение ленты в точке 5 S5 Н по формуле:
где - коэффициент увеличения натяжения тягового органа от сопротивления на поворотном пункте () [47 с. 47].
Определим натяжение ленты в точке 6 S6 Н по формуле:
Определим натяжение ленты в точке 7 S7 Н по формуле:
Определим натяжение ленты в точке 8 S8 Н по формуле:
Определим натяжение ленты в точке 9 S9 Н по формуле:
Определим сопротивление на погрузочном пункте от сообщения грузу скорости тягового органа Sпогр Н по формуле :
Определим сопротивление от направляющих бортов загрузочного лотка Sл Н по формуле:
где - длина лотка ( =3м).
Определим натяжение ленты в точке 10 S10 Н по формуле:
Определим натяжение ленты в точке 11 S11 Н по формуле:
Определим натяжение ленты в точке 12 S12 Н по формуле:
Определим натяжение ленты в точке 13 S13 Н по формуле:
где - постоянные полученные в результате вычислений.
Из условия непроскальзывания ленты на барабане:
Определим натяжение на сбегающей ветви Н по формуле:
Определим натяжение на набегающей ветви Н:
Определим натяжение ленты во всех рассмотренных точках:
По полученным данным строим диаграмму натяжения ленты.
По уточненному значению проверяем прочность ленты:
Определим тяговое усилие конвейера Н по формуле:
Таким образом произвели уточненный тяговый расчет конвейера. Уточнили такие показатели как максимальное натяжение ленты тяговое усилие и количество тканевых прокладок обеспечивающих прочность ленты.
2.4 Расчет мощности электродвигателя
Определим мощность на приводном валу конвейера P0 кВ по формуле:
Определим мощность двигателя P кВ по формуле:
где - коэффициент запаса мощности () [47 с. 121];
- КПД передаточного механизма () [39 с. 52].
Выбираем мотор-барабан серии МБ-5 с электродвигателем мощностью =15кВт [12] со встроенным короткозамкнутым тормозом. Частота вращения барабана =50обмин номинальный крутящий момент максимальное тяговое усилие .
Определим фактическую скорость ленты мс по формуле:
Определим фактическую производительность ленточного конвейера тч по формуле:
Определим допустимое время пуска конвейера с по формуле:
где - допустимое ускорение пуска () [47 с. 123].
Определим время торможения конвейера с по формуле:
где - допустимая длина выбега ленты при торможении () [47 с. 123].
Таким образом произвели расчет мощности электродвигателя.
2.5 Расчет натяжного устройства
Определим усилие натяжного устройства Н по формуле:
где - количество перегибов ленты на натяжном пункте ().
Определим общий ход натяжного устройства Lх м по формуле:
где Lх1 - монтажный ход натяжного устройства (Lх1=01м);
kх - коэффициент удлинения ленты при рабочей нагрузке (kх =002) [40 с. 147].
- длина телескопической части конвейера ().
Выбираем натяжное лебедочное грузовое устройство. Схема запасовки канатов приведена на рисунке 6.2.
Рисунок 6.2 - Схема запасовки канатов
Определим усилие в канате набегающем на барабан Н по формуле:
Определим расчетное разрывное усилие Н в канате по формуле:
где - коэффициент запаса прочности каната () [40 с. 55 таблица 2.3].
В зависимости от расчетного разрывного усилия выбираем стальной канат двойной свивки с одним органическим сердечником типа ЛК-Р конструкции 6x19 (1+6+66)+1 о.с. диаметром 38мм и максимальным усилием на разрыв 9930Н [13].
Определим фактический коэффициент запаса прочности по формуле:
Определим наименьший диаметр барабана мм по формуле:
где e - коэффициент зависящий от типа грузовой машины (e=20) [Кузьмин с. 59 таблица 2.7].
Принимаем диаметр блока из нормального ряда .
Определим количество витков каната наматываемых на барабан по формуле:
где - число неприкосновенных витков требуемых правилами Ростехнадзора для разгрузки деталей крепления каната на барабане ();
- число витков необходимых для крепления каната на барабане ().
Определим шаг канавок мм по формуле:
Определим длину нарезной части барабана мм по формуле:
Определим габаритную длину барабана мм по формуле:
определим необходимую мощность двигателя кВт по формуле:
где - скорость перемещения тележки ();
Выбираем асинхронный электродвигатель с фазным ротором серии АИР 90LB8 [12] мощностью =11кВт при частоте вращения =710обмин. Кратность максимального момента кратность минимального момента .
Определим частоту вращения вала барабана обмин по формуле:
Определим требуемое передаточное число привода по формуле:
Выбираем редуктор цилиндрический горизонтальный двухступенчатый типа ЦД2-60Б с передаточным числом =125 и КПД =096[8].
Для выбора соединительной муфты между двигателем и редуктором определим номинальный крутящий момент двигателя Нм по формуле:
С учетом коэффициента кратности максимального момента двигателя определяем расчетный момент муфты Нм по формуле:
Выбираем упругую втулочно-пальцевую муфту 125-25-1 УЗ [9] с наибольшим передаваемым крутящим моментом =125Н×м.
3 расчет механизма подъема галереи
3.1 Расчет ветровой нагрузки на галерею
Определим динамическое давление ветра на галерею q Па по формуле:
где - плотность воздуха () [6];
- максимальная скорость ветра ( ).
Определим распределенную ветровую нагрузку на галерею Па по формуле:
- коэффициент учитывающий изменение динамического давления по высоте () [6];
- коэффициент аэродинамической силы () [6];
- коэффициент перегрузки для рабочего состояния () [6].
Определим статическую составляющую давления ветровой нагрузки кН по формуле:
где - наветренная площадь галереи (м2).
Определим динамическую составляющую ветровой нагрузки кН по формуле:
где - коэффициент пульсации ветра () [50 с.56 таблица 1.2.17];
- коэффициент динамичности ()[50 с.56 таблица 1.2.18].
Определим ветровую нагрузку действующую на галерею по формуле:
Схема запасовки канатов приведена на рисунке 6.3.
Рисунок 6.3 - Схема запасовки канатов
По схеме запасовки определяем кратность полиспаста и количество витков .
Исходным параметром определяющим размеры составных частей механизма подъема является диаметр каната.
Определим КПД канатной системы:
где - КПД полиспаста (=099)[40 с.54 таблица 2.1];
- КПД направляющих блоков (= 098) [40 с.54 таблица 2.1];
- число направляющих блоков (=9).
Определим наибольшую нагрузку кН действующую на канат по формуле:
где - масса галереи (т);
- расстояние от поворота галереи до оси вращения полиспаста ();
- кратность полиспаста ();
- число ветвей полиспаста (z=8).
Определим по найденной нагрузке S разрывное усилие каната кН по формуле:
где - коэффициент запаса прочности. Для грузовых и стреловых канатов по правилам Госгортехнадзора эту величину выбирают в зависимости от вида привода и режима работы. В данном случае принимаем (=5) [42 с. 55].
В зависимости от расчетного разрывного усилия выбираем стальной канат двойной свивки с одним органическим сердечником типа ЛК-Р конструкции 6x19 (1+6+66)+1 о.с. диаметром 24мм и максимальным усилием на разрыв 380кН [13].
3.3 Расчет геометрических параметров блока
Определим наименьший диаметр блока мм по формуле:
где - коэффициент зависящий от типа грузоподъемной машины и режима ее работы (=22) [42 с.24];
Диаметр блока принимаем =530мм [42 с. 25].
Определим наименьший диаметр уравнительного блока мм по формуле:
Диаметр уравнительного блока принимаем =450мм [42 с. 25].
Диаметр барабана принимаем =560мм [42 с. 29].
где - высота подъема галереи исходя из чертежа ();
- число неприкосновенных витков требуемых правилами Ростехнадзора для разгрузки деталей крепления каната на барабане ();
- число витков необходимых для крепления каната на барабане ( ).
Определим шаг канавок t мм по формуле:
Определяем глубину канавки h мм по формуле:
Определим диаметр барабана по дну канавки мм по формуле:
Определим полную длину нарезанной части барабана мм по формуле:
В качестве материала для изготовления барабана принимаем чугун СЧ-20 [5].
Определим толщину стенки чугунного барабана мм по формуле:
где - допускаемое напряжение сжатия (=200МПа).
3.4 Расчет мощности электродвигателя и выбор тормоза
Определим максимальную суммарную статическую мощность в период установившегося движения при подъеме груза кВт по формуле:
- скорость подъема галереи (ммин);
- кпд редуктора (=094) [40 с. 52];
- кпд барабана (=098) [40 с. 23].
Выбираем 2 асинхронных электродвигателя с фазным ротором серии АИР 180S4 (12) мощностью =225кВт каждый при частоте вращения =1460обмин. Кратность максимального момента кратность минимального момента .
Определим частоту вращения вала приводного барабана обмин по формуле:
Выбираем редуктор цилиндрический вертикальный двухступенчатый типа ЦД2-60Б с передаточным числом =28 и КПД =096[8].
Определим фактическую скорость подъема галереи ммин по формуле:
где - мощность двигателя кВт;
- частота вращения обмин.
Выбираем упругую втулочно-пальцевую муфту 500-40-1 УЗ [9] с наибольшим передаваемым крутящим моментом =500Н×м.
Определяем статический крутящий момент при торможении Нм создаваемый весом галереи на валу на котором устанавливается тормоз по формуле:
Расчётный тормозной момент механизма Нм согласно правилам_Гостехнадзора при условии надежного удержания груза номинальной массы в подвешенном состоянии с определенным запасом торможения определяется по формуле:
где - коэффициент запаса торможения () [50 с.473];
Полученное значение тормозного момента полностью удовлетворяет номинальному значению тормозного момента выбранного двигателя.
Выбираем колодочный тормоз ТКТ-200 с тормозным моментом 400Нм электромагнитом типа МОБ-100 диаметр тормозного шкива 200мм.
Таким образом произвели расчет механизма подъема конвейерной галереи погрузочной машины в ходе чего были определены основные показатели работы механизма такие как усилие в канате наматываемом на барабан исходя из чего выбрали тип свивки и диаметр стального каната диаметры блоков и барабана мощность двигателя определили расчетное передаточное число редуктора выбрали муфту и тормоз.
4 Расчет механизма передвижения судопогрузочной машины
4.1 Расчет ветровой нагрузки на судопогрузочную машину
Определим распределенную ветровую нагрузку на погрузочную машину Па по формуле:
где - наветренная площадь погрузочной машины (м2).
Определим ветровую нагрузку действующую на кран в нерабочем состоянии по формуле:
4.2 Определение сопротивления передвижению судопогрузочной
Определим массу груза т находящуюся на конвейере погрузочной машины во время перегрузки по формуле:
где - распределенная масса груза приходящаяся на метр длины конвейерной ленты ();
- длина конвейера ().
Определим максимальное давление приходящееся на колесо кН по формуле:
где – количество ходовых колес ();
– масса погрузочной машины (т).
В зависимости от максимального давления на колесо определяем его диаметр и тип рельса: выбираем двухребордное колесо диаметром и [14] тип рельса Р-43 [16].
Определим диаметр цапфы мм по формуле:
Определим статическое сопротивление передвижению кН по формуле:
где – сопротивление от трения в ходовых частях кН;
– сопротивление движению от уклона пути кН;
– сопротивление от ветровой нагрузки кН;
– сопротивление сил инерции кН.
Определим сопротивление от трения в ходовой части кН по формуле:
где – коэффициент трения качения колеса по рельсу () [42 с. 40 таблица 2.13];
– коэффициент трения подшипников приведённый к цапфе колеса () [42 с. 40 таблица 2.14];
– коэффициент учитывающий трения реборд ступиц колёс () [42 с. 41 таблица 2.15].
Определим сопротивление движению от уклона пути кН по формуле:
где – уклон подкрановых путей () [42 с. 41].
Сопротивление движению от ветровой нагрузки .
Определим сопротивление сил инерции кН по формуле:
где – коэффициент учитывающий инерцию вращающихся частей механизма () [42 с. 41];
– допускаемое ускорение () [42 с. 41 таблица 2.16].
Определим запас сцепления ходовых колес с рельсами при разгоне на подъем против ветра и при торможении под уклон по ветру по формуле:
где – коэффициент сцепления приводных колес с рельсом (=012) (42 с. 90);
– минимальное значение коэффициента сопротивления передвижению ();
– расчетная нагрузка кН;
– допускаемый коэффициент запаса сцепления () [42 с. 89].
Определим расчетную нагрузку кН действующую на механизм по формуле:
где – коэффициент толчков зависящий от скорости передвижения при ().
Запас сцепления обеспечен.
Таким образом определили статическое сопротивление передвижению погрузочной машины определили диаметр ходовых колес и давление одного колеса на рельс .
4.3 Расчет мощности электродвигателя
Определим статическую мощность одного двигателя в период установившегося движения при передвижении погрузочной машины кВт по формуле:
- скорость передвижения (мсек);
- кпд механизма передвижения () [42 с. 42];
- количество приводных колес ().
Выбираем асинхронный электродвигатель с фазным ротором серии АИР 160S8 [12] мощностью =75кВт при частоте вращения =970обмин. Кратность максимального момента кратность минимального момента .
Определим частоту вращения вала приводного колеса обмин по формуле:
Выбираем вертикальный двухступенчатый редуктор кранового типа В–250 с передаточным числом 63 и КПД =096[8].редуктора 280кг. Крутящий момент .
Определим фактическую скорость передвижения погрузочной машины ммин по формуле:
Выбираем упругую втулочно-пальцевую муфту 250-40-1 УЗ [9] с наибольшим передаваемым крутящим моментом =250Н×м.
Определим расчётный тормозной момент по формуле:
где – коэффициент запаса торможения согласно правилам Ростехнадзора () [42 с. 44];
– момент создаваемый уклоном ;
– момент ветровой нагрузки нерабочего состояния ;
– момент создаваемый силами трения .
- момент создаваемый силами инерции .
Определим момент создаваемый уклоном по формуле:
где – радиус колеса (м).
Определим момент ветровой нагрузки нерабочего состояния по формуле:
Определим момент создаваемый силами инерции по формуле:
Определим момент создаваемый силами трения по формуле:
Принимаем колодочный тормоз с электрогидравлическим толкателем ТКГ–300 с расчетным тормозным моментом 700 и тормозным шкивом 300мм.
Таким образом произвели расчет механизма передвижения погрузочной машины в ходе чего были определены основные показатели работы механизма такие как давление одного колеса на рельс исходя из чего выбрали диаметр ходовых колес сопротивление передвижению погрузочной машины мощность двигателя определили расчетное передаточное число редуктора выбрали муфту и тормоз.
речь.doc
Цель данного дипломного проекта - разработать специализированный комплекс по перегрузке сухих минеральных удобрений
В связи с увеличением объемов добычи апатитонефелиновых руд которые служат сырьем для производства сухих минеральных удобрений применение высокопроизводительного специализированного комплекса поможет избежать высоких расходов на транспортирование их в порты расположенные южнее Мурманска такие как Санкт-Петербург и др.
В ходе подготовки дипломного проекта был произведен анализ исходных данных а также разработаны конвейерная схема механизации (производительность которой 600тч эксплуатационные расходы составили 106млн.у.е. себестоимость перегрузки 53у.е. окупаемость 36лет) и крановая (производительность которой 594тч эксплуатационные расходы составили 143млн.у.е. себестоимость перегрузки 71у.е. окупаемость 115лет).
Таким образом оптимальной является конвейерная схема механизации. В выбранной схеме механизации в качестве фронтальной погрузочной машины используется конвейерный перегружатель который передвигается вдоль причала по крановым путям (его производительность составляет 300тч). Подача груза на судопогрузочную машину осуществляется с помощью причальной конвейерной линии (производительностью 300тч суммарная мощность двигателей 15кВт скорость ленты 125мс). Причальный конвейер оборудован сбрасывающей тележкой(мощность двигателя 15кВт угол наклона 18º скорость передвижения 033мс).
В ходе подготовки дипломного проекта был выполнен расчет основных механизмов судопогрузочной машины: телескопический ленточный конвейер (в качестве привода используется мотор-барабан мощностью 15кВт скорость ленты 125мс) Выполнен чертеж составных частей конвейеров. Рассчитаны механизм подъема галереи (мощность 45кВт скорость подъема 05мс) механизм передвижения судопогрузочной машины (мощность 75 кВт скорость передвижения 033мс).
В качестве элемента привода была выбрана шариковая винтовая пара за счет которой обеспечивается изменение вылета телескопического конвейера. Были выполнены геометрический расчет и расчет на прочность. Параметры передачи следующие: диаметр винта 80мм резьба однозаходная профиль круглый шаг 20мм диаметр шариков 12мм.
Также была рассчитана металлоконструкция подъемной галереи судопогрузочной машины. Металлоконструкция выполнена из равнополочных уголков 70*70мм толщиной 5* в виде пространственной фермы. Был произведен расчет гибкость элементов фермы расчет на прогиб консольного участка фермы выполнена проверка сварных швов и построены эпюры изгибающих моментов и поперечных сил.
В работе также представлены материалы в которых описывается работа электросхемы привода ленточного конвейера описывается охрана труда и обеспечение экологической безопасности на терминале монтаж конвейеров и их техническое обслуживание.
Таким образом модернизация данного терминала позволит повысить грузооборот увеличить степень технической оснащенности терминала и снизить затраты на перегрузку.
5РАСЧЕТ ЛЕНТОЧНОГО КОНВЕЙЕРА.doc
1 Расчет класса использования конвейера расчет и выбор ленты
Принимаем класс использования конвейера по времени В4. В зависимости от класса использования конвейера принимаем весьма тяжелый режим работы конвейера.
Определим коэффициент планового использования конвейера в сутки по формуле:
где - время фактической работы конвейера в сутки ч учитывая класс использования конвейера по времени В4 принимаем ();
- количество часов в сутках ().
Определим коэффициент планового использования конвейера в год по формуле:
где - время фактической работы конвейера в году ч учитывая класс использования конвейера по времени В4 ();
- количество часов в году ().
Определим требуемую ширину ленты м по формуле:
где - производительность конвейера (тч);
- скорость ленты принимаем скорость ленты с учетом режима работы (мс);
- плотность груза (тм);
- коэффициент зависящий от угла естественного откоса груза (= 730) [47 с. 103 таблица 4.6];
- коэффициент зависящий от угла наклона конвейера () [47 с. 102 таблица 4.5].
Выбираем резинотканевую конвейерную ленту ТЛК-200 шириной =650мм с тремя =3 тяговыми прокладками толщиной допускающими рабочую нагрузку =100Нмм с толщиной резиновой обкладки рабочей поверхности =4мм нерабочей поверхности =2мм [7].
Проверим выбранную ширину мм ленты по условию размещения кусков:
где - размер типичного куска мм мм.
Существенное увеличение ленты требует уточнения скорости ленты мс по формуле:
Принимаем скорость ленты из нормального ряда [10].
Определим толщину ленты мм по формуле:
где - количество тяговых тканевых прокладок;
- толщина тяговой тканевой прокладки мм;
- толщина резиновой обкладки рабочей поверхности конвейерной ленты мм;
- толщина резиновой обкладки нерабочей поверхности ленты мм.
Определим нагрузку от массы груза кгм по формуле:
Определим нагрузку от массы ленты кгм по формуле:
где - плотность ленты (кгм);
Определим предварительное тяговое усилие в ленте Н по формуле:
где - обобщенный коэффициент местных сопротивлений () [47 с. 118];
- распределенная масса вращающихся частей роликовых опор рабочей ветви (кгм) [47 с. 107];
- распределенная масса вращающихся частей роликовых опор холостой ветви (кгм) [47 с. 107];
- коэффициент сопротивления рабочей ветви () [47 с. 106 таблица 4.9];
- коэффициент сопротивления холостой ветви () [47 с. 106 таблица 4.9];
Определим предварительное максимальное натяжение ленты Н по формуле:
где - коэффициент запаса сцепления ленты с барабаном () [47 с. 46];
- тяговый фактор () [47 с.75].
Проверим необходимое минимальное число тяговых прокладок в ленте z по формуле:
где - принятое число тяговых прокладок (z=3);
- запас прочности ленты () [47 с. 66];
- максимальная допустимая рабочая нагрузка прокладки (=100Нмм).
Таким образом произвели расчет и выбор ленты конвейера проверили ленту на прочность а также определили предварительное тяговое усилие и максимальное натяжение ленты.
2 Расчет и выбор поддерживающих устройств
Исходя из ширины и скорости ленты выбираем из нормального ряда диаметр роликов желобчатой роликоопоры =89мм и расстояние между роликоопорами рабочей ветви конвейера =1300мм [11].
Определим расстояние между роликоопорами холостой ветви конвейера мм по формуле:
Определим расстояние между роликоопорами в зоне загрузки мм по формуле:
Определим наименьший диаметр приводного барабана мм по формуле:
где - коэффициент учитывающий прочность прокладок ленты () [47 с. 74];
-коэффициент зависящий от назначения барабана () [47 с.74].
Из нормального ряда принимаем диаметр приводного барабана =500мм [10].
Определим диаметр натяжного и отклоняющего барабанов мм по формуле:
где -для натяжного и отклоняющего барабанов.
Из нормального ряда принимаем диаметр приводного барабана =400мм [10].
Определим длину приводного и натяжного барабана мм по формуле:
Таким образом произведя расчет выбирали желобчатую роликоопору диаметром =89мм и приняли диаметры приводного барабана =500мм натяжного .
3 Подробный тяговый расчет конвейера
Уточненный тяговый расчет проводят с целью более точного определения максимального натяжения тягового элемента натяжения его в характерных точках трассы определения тягового усилия и мощности привода конвейера.
Определим тяговое усилие конвейера методом обхода по его контуру суть которого заключается в том что всю трассу конвейера начиная с точки сбегания тягового элемента с привода разбивают на отдельные участки (рисунок 5.1) сопротивление в которых постоянно по своему характеру. Обход лучше начинать с точки наименьшего натяжения тягового элемента пользуясь общим правилом: натяжение тягового элемента в каждой последующей по ходу контура точке равно натяжению в предыдущей точке плюс сопротивление на участке между этими точками:
где и - натяжения в двух соседних точках контура;
- сопротивление движению тягового элемента на участке между этими точками.
Если место нахождения точки наименьшего натяжения ленты установить невозможно то за начало отсчета можно принять любую из точек.
Рисунок 5.1 - Схема трассы конвейера для определения тягового усилия
Предположим что наименьшее натяжение ожидается в точке 1 с которой и начнем тяговый расчет. Наименьшая сила натяжения ленты равна силе предварительного натяжения ленты:
Определим натяжение ленты в точке 2 S2 Н по формуле:
Определим натяжение ленты в точке 3 S3 Н по формуле:
где - коэффициент увеличения натяжения тягового органа от сопротивления на поворотном пункте () [47 с. 47].
Определим сопротивление на погрузочном пункте от сообщения грузу скорости тягового органа Sпогр Н по формуле :
Определим сопротивление от направляющих бортов загрузочного лотка Sл Н по формуле:
где - длина лотка (=4м).
Определим натяжение ленты в точке 4 S4 Н по формуле:
Определим натяжение ленты в точке 5 S5 Н по формуле:
где - сопротивление от разгрузочной тележки .
В зависимости от ширины ленты выбираем барабанный разгружатель типа Б6550 (47 с.88).
Определим сопротивление от разгрузочной тележки :
где - длина подъема ленты () [47 с.88];
- высота подъема ленты () [47 с.88].
где - постоянные полученные в результате вычислений.
Из условия непроскальзывания ленты на барабане:
Определим натяжение на сбегающей ветви Н по формуле:
Определим натяжение на набегающей ветви Н по формуле:
Определим натяжение ленты во всех рассмотренных точках:
По полученным данным строим диаграмму натяжения ленты.
По уточненному значению проверяем прочность ленты:
Определим тяговое усилие конвейера Н по формуле:
Таким образом произвели уточненный тяговый расчет конвейера. Уточнили такие показатели как максимальное натяжение ленты тяговое усилие и количество тканевых прокладок обеспечивающих прочность ленты.
4 Расчет электродвигателя редуктора муфты и тормозного устройства
Определим мощность на приводном валу конвейера P0 кВ по формуле:
Определим мощность двигателя P кВ по формуле:
где - коэффициент запаса мощности () [47 с. 121];
- КПД передаточного механизма () [39 с. 52].
Выбираем 2 асинхронных электродвигателя с фазным ротором серии АИР 132S4 [12] мощностью =75кВт каждый при частоте вращения =1440обмин. Кратность максимального момента кратность минимального момента .
Определим частоту вращения вала приводного барабана обмин по формуле:
где - диаметр приводного барабана м.
Определим требуемое передаточное число привода по формуле:
Выбираем редуктор цилиндрический горизонтальный двухступенчатый типа ЦД2-60Б с передаточным числом =315 и КПД =096[8].
Определим фактическую скорость ленты мс по формуле:
Определим фактическую производительность ленточного конвейера тч по формуле:
Для выбора соединительной муфты между двигателем и редуктором определим номинальный крутящий момент двигателя Нм по формуле:
где - мощность двигателя кВт;
- частота вращения обмин.
С учетом коэффициента кратности максимального момента двигателя определяем расчетный момент муфты Нм по формуле:
Выбираем упругую втулочно-пальцевую муфту 125-25-1 УЗ [9] с наибольшим передаваемым крутящим моментом =125Н×м.
Определим допустимое время пуска конвейера с по формуле:
где - допустимое ускорение пуска () [47 с. 123].
Определим время торможения конвейера с по формуле:
где - допустимая длина выбега ленты при торможении () [47 с. 123].
Определим статический момент инерции на одном валу при торможении Н×м по формуле:
Определим значение потребного тормозного момента Н×м по формуле:
где - коэффициент запаса торможения регламентируемый правилами Ростехнадзора и Регистра ().
Тормоз необходим для предотвращения засыпки узла перегрузки. Расчетный тормозной момент 1875Н×м. Устанавливаем на каждый вал тормоз ТКТ-100 с наибольшим тормозным моментом 200Н×м.
5 Расчет натяжного устройства
Определим усилие натяжного устройства Н по формуле:
Определим общий ход натяжного устройства Lх м по формуле:
где Lх1 - монтажный ход натяжного устройства (Lх1=01м);
kх - коэффициент удлинения ленты при рабочей нагрузке (kх =002) [40 с. 147].
Выбираем натяжное лебедочное полиспастное грузовое устройство. Схема запасовки канатов приведена на рисунке 5.2.
Рисунок 5.2 - Схема запасовки канатов
По схеме запасовки определяем кратность полиспаста и количество блоков .
Определим усилие в канате набегающем на барабан Н по формуле:
- кратность полиспаста;
- КПД блоков () [40 с. 54 таблица 2.1].
Определим расчетное разрывное усилие Н в канате по формуле:
где - коэффициент запаса прочности каната () [40 с. 55 таблица 2.3].
В зависимости от расчетного разрывного усилия выбираем стальной канат двойной свивки с одним органическим сердечником типа ЛК-Р конструкции 6x19 (1+6+66)+1 о.с. диаметром 62мм и максимальным усилием на разрыв 19250 [13].
Определим фактический коэффициент запаса прочности по формуле:
Определим наименьший диаметр блока мм по формуле:
где e - коэффициент зависящий от типа грузовой машины (e=20) [Кузьмин с. 59 таблица 2.7].
Принимаем диаметр блока из нормального ряда .
Определим наименьший диаметр барабана мм по формуле:
Принимаем диаметр барабана из нормального ряда .
Определим количество витков каната наматываемых на барабан по формуле:
где - число неприкосновенных витков требуемых правилами Ростехнадзора для разгрузки деталей крепления каната на барабане ();
- число витков необходимых для крепления каната на барабане ().
Определим шаг канавок мм по формуле:
Определим длину нарезной части барабана мм по формуле:
Определим габаритную длину барабана мм по формуле:
Определим необходимую мощность двигателя кВт по формуле:
где - скорость перемещения тележки ();
Выбираем 1 асинхронный электродвигатель с фазным ротором серии АИР 112МВ8 (12) мощностью =3кВт при частоте вращения =700обмин. Кратность максимального момента кратность минимального момента .
Определим частоту вращения вала барабана обмин по формуле:
Устанавливаем храповой останов для предотвращения обратного движения натяжной тележки.
3.Анализ исходных данных.doc
Анализ исходных данных задания позволит разработать специализированный перегрузочный комплекс а так же позволит выявить факторы влияющие на условия работы выбрать оборудование и компоновочные решения. Для этого необходимо рассчитать грузооборот причала определить вместимость склада дать краткую характеристику используемых на причале машин рассчитать пропускную способность причала.
1 Определение грузооборота причала
Определим число месяцев навигации nмес мес по формуле:
где 305 - средняя продолжительность месяца сут;
Tнав - время навигации сут (Tнав=365).
Определим месячный грузооборот тмес по формуле:
где Qнав - навигационный грузооборот т (Qнав=2000000т);
Кн - коэффициент неравномерности (Кн = 13)
Определим число нерабочих дней Тнр cут по формуле:
где Кн - коэффициент хранения груза принимаем (Кн = 01).
Определим среднесуточный грузооборот тсут по формуле:
Таким образом произвели расчет грузооборота причала получили такие параметры как месячный и суточный грузооборот причала.
2 Краткая характеристика минеральных удобрений
Аммофос или моноаммонийфосфат (NH4H2PO4) - высококонцентрированное гранулированное азотно-фосфорное удобрение азот в котором представлен аммонийной формой. Производится методом нейтрализации фосфорной кислоты аммиаком. Форма выпуска - гранулы.
Аммофос используется на всех типах почв для основного и припосевного внесения под все сельскохозяйственные культуры во всех почвенно-климатических зонах страны. На основе аммофоса можно изготавливать любые марки смешанных удобрений.
Продукт негигроскопичен не пылит и не слеживается. Имеет выровненный гранулометрический состав. Хорошо растворим в воде. Аммофос нетоксичен пожаро- и взрывобезопасен.
Отгружают насыпью или в упакованном виде в мешках по 50кг или одноразовых контейнерах не более 1000кг. Транспортировка осуществляется автомобильным железнодорожным и морским транспортом в соответствии с действующими на них правилами перевозки. Хранение осуществляют в закрытых складских помещениях.
Карбамид (мочевина)(CO(NH2)2) - азотное удобрение производится из аммиака и двуокиси углерода.
Выпускается двух марок:
- марка «А» – применяется в промышленности для производства пластмасс клеев смол. Также используется в качестве кормовой добавки жвачным животным (по кормовой ценности 100г мочевины равноценны 260г протеина или 27кг овса). Карбамид марки «А» высшего сорта применяется в пищевой промышленности.
- марка «Б» – универсальное азотное удобрение применяется в сельском хозяйстве для основного внесения в почву подкормки ранней весной и в период вегетации используется на всех видах почв под любые культуры. Карбамид обеспечивает значительную прибавку урожая сельскохозяйственных культур. Карбамид обрабатывается кондиционирующими добавками обеспечивающими сохранность товарных свойств продукта. Форма выпуска – гранулы кристаллы.
Карбамид - негорюч пожаро- и взрывобезопасен.
Карбамид фасуют в полиэтиленовые и пропиленовые мешки в специальные контейнеры для сыпучих продуктов а также в другие виды упаковки. Для реализации через сеть розничной торговли карбамид фасуют в полиэтиленовые пакеты по 3кг.
Отгружают в упакованном виде и насыпью с принятием мер исключающих попадание продукта в окружающую среду и просыпание продукта. Транспортируют всеми видами транспорта в соответствии с правилами перевозок грузов действующими на данном виде транспорта.
Сульфат аммония (NH4)2SO4 - аммонийная соль серной кислоты аммоний сернокислый представляет собой бесцветные кристаллы. Хорошо растворяется в воде. В лаборатории получают действием концентрированной серной кислоты на концентрированный раствор аммиака:
Эту реакцию как и все другие реакции взаимодействия аммиака с кислотами проводят в приборе для получения растворимых веществ в твёрдом виде.
Среди основных способов получения сульфата аммония которые наиболее часто используются в химической промышленности имеются следующие: процесс нейтрализации серной кислоты синтетическим аммиаком; использование аммиака из газа коксовых печей для его химической реакции с серной кислотой; получение в результате обработки гипса растворами карбоната аммония; получение при переработке отходов остающихся после производства капролактама. Вместе с тем имеются и другие способы производства сульфата аммония например получение этого вещества из дымовых газов электростанций и сернокислотных заводов. Для этого в горячие газы вводят газообразный аммиак который связывает имеющиеся в газе окислы серы в различные соли аммония в том числе и в сульфат аммония.
Применяют как удобрение в производстве вискозного волокна. В биохимии переосаждение сульфатом аммония является общим методом очистки белков. В пищевой промышленности зарегистрирован в качестве пищевой добавки E517.
Используется в технологии хлорирования воды с аммонизацией вводится в обрабатываемую воду за несколько секунд до хлора с хлором образует хлорамины - связывая свободный хлор благодаря чему значительно сокращается образование хлорорганики вредной для организма человека сокращается расход хлора уменьшается коррозия труб водовод.
Сульфат аммония (сернокислый аммоний) формула (NH4)2SO4– азотно-серное минеральное удобрение. Сульфат аммония содержит 21% азота и 24% серы. Это химически нейтральная кристаллическая соль белого цвета хорошо растворимая в воде. Гигроскопичность её слабая поэтому при длительном хранении не слёживается и сохраняет сыпучесть. Значение азота в жизнедеятельности растений трудно переоценить - он занимает первое место среди минеральных соединений поэтому остановимся на значении серы в жизни растений. Сера - является важнейшим элементом питания сельскохозяйственных культур как и азот она входит в состав белков и аминокислот.
Кристаллическое азотносерное удобрение содержит 21% азот в аммонийной форме серы – 24% не слеживается. Сульфат аммония – одно из широкоприменяемых в сельском хозяйстве минеральных удобрений. Используется под все сельскохозяйственные культуры (от картофеля до цитрусовых) на черноземах и сероземах. Аммонийный азот сульфата аммония усваивается растениями. Сера необходима для питания всех культур так как входит в состав некоторых синтезируемых растениями незаменимых аминокислот. Сульфат аммония получают как побочный продукт в производстве капролактама.
Сульфат аммония транспортируют железнодорожным транспортом в крытых полувагонах а также автомобильным и водным транспортом. Хранение осуществляется в крытых складских помещениях специализированных контейнерах защищающих продукт от попадания влаги.
3 Определение грузовой обработки транспортных средств
В качестве расчетного судна выбираем судно для перевозки навалочных грузов проекта ВС 14 «Заполярье» (рисунок 3.1) дедвейтом Дв = 23278т c ледовой категорией ЛУ4. Чистая грузоподъемность Дч =22100т длина судна L = 1805м ширина B = 2286м высота борта H=135м осадка с полным грузом h = 991м.
Рисунок 3.1 - Судно проекта ВС 14
Определим расчетный интервал времени между судами обрабатываемыми в определенный период Тн.с ч по формуле:
Определим норму времени грузовых операций [Tгр] ч по формуле:
где [Ic] - судочасовая норма интенсивности грузовых работ с заданным грузом ([Ic] = 360тч) [45 с. 27 таблица 16].
Определим норму времени стоянки судна у причала [Tc] ч по формуле:
где Твсп - время затрачиваемое на вспомогательные операции (Твсп = 45ч) [45 с. 24 таблица 15].
Определим длину грузового фронта м по формуле:
где минимальное необходимое расстояние предназначенное для безопасности швартовки судов (d=15м);
- длинна судна (=1805м).
По условию погрузочные работы ведутся по прямой схеме (вагон - судно). Выбираем вагон-минераловоз модель 19-953 (рисунок 3.2) грузоподъемностью 70т длиной 132м шириной 326м высотой 512м.
Рисунок 3.2 - Вагон-минераловоз модель 19-953
Определяем расчетное число вагонов подаваемых в разгрузочную галерею в течении суток nвпо формуле:
где Gф - техническая норма загрузки вагонов соответствующим родом груза (Gф= 63т) [45 с. 14 таблица 6].
Определим число вагонов в одной подаче исходя из протяженности грузового фронта по формуле:
где - длина вагона по оси автосцепки (м).
Определим интервал времени между подачами вагонов ч по формуле:
Таким образом произвели расчет грузовой обработки транспортных средств в порту получили такие параметры как время стоянки судна у причала интервал между подачами вагонов.
4 Определение расчетной вместимости склада
Для минеральных удобрений используется склад закрытого хранения. Вместимость оперативного склада на причале зависящая от величины навигационного грузооборота ритмичности перевозок длительности хранения на причале может быть установлена из рассмотрения и анализа ряда выражений для расчета.
Определим расчетную вместимость склада т по формуле:
где Дч - норма загрузки расчетного судна заданным видом груза ( Дч = 22100т).
Определим вместимость склада т по формуле:
где – радиус нижнего основания штабеля (м) [44 c.23];
– радиус верхнего основания штабеля (м) [44 c.23];
– высота штабеля м [44 с. 21]:
Определим количество сформированных штабелей по формуле:
Исходя из проведенного расчета размещаем на территории причала 3 склада общей вместимостью 60000т.
5 Определение расчетной интенсивности обработки транспортных средств
Определим интенсивность грузовой обработки судна тч по формуле:
где пропускная способность оборудования причального фронта тсут;
коэффициент использования перегрузочного оборудования причального фронта;
эффективное время работы оборудования причала в течение суток ч.
Величина расчетной пропускной способности причального фронта принимается из условия:
где норма пропускной способности причального фронта тсут.
Определяем норму пропускной способности причального фронта тсут по формуле:
Принимаем величину расчетной пропускной способности причального фронта равной:
Коэффициент использования перегрузочного оборудования причального фронта принимается из условия:
Определим эффективное время работы оборудования причала в течение суток ч по формуле:
где коэффициент учитывающий подготовительно заключительные операции технологические и обеденные перерывы () [44 с. 9];
время продолжительности рабочей смены.
В порту чаще всего используют двух или трех сменный режим работы.
Продолжительность рабочих смен при двух сменном режиме работы: днем и ночью по 12 часов при трех сменном – утром и вечером 8 часов а ночью 7 часов.
Определяем время продолжительности при трех сменном режиме работы ч по формуле:
Определим эффективное время работы оборудования причала в течение суток ч по формуле:
Определим расчетную интенсивность грузовой обработки вагона тч по формуле:
где расчетная пропускная способность железнодорожного грузового фронта тсут;
коэффициент использования перегрузочного оборудования железнодорожного грузового фронта.
Величина расчетной пропускной способности железнодорожного грузового фронта принимается из условия:
где норма пропускной способности железнодорожного грузового фронта тсут.
Определим норму пропускной способности железнодорожного грузового фронта тсут по формуле:
Принимаем величину расчетной пропускной способности железнодорожного грузового фронта равной:
Определим коэффициент использования перегрузочного оборудования железнодорожного грузового фронта по формуле:
где продолжительность перестановки подачи вагонов (ч).
На основе результатов выполненного анализа исходных данных составляется сводная таблица расчетных показателей (Таблица 3.1).
Таблица 3.1 -Таблица анализа исходных данных
Род груза (наименование)
Минеральные удобрения
Продолжительность перевозок
неравномерности перевозок
Тип склада и способ хранения груза
Норма загрузки транспортных средств
Норма времени обработки
Интенсивность грузовой обработки
Проведя анализ исходных данных были выявлены основные показатели влияющие на работу причала. К ним относятся грузооборот причала длительность навигационного периода необходимая вместимость и размеры складов на причале типы транспортных средств участвующих в перевозках и их характеристики.
Задание.doc
ФГОУ ВПО «Санкт-Петербургский государственный университет
водных коммуникаций»
Кафедра Портовой подъемно-транспортной техники и гидротехнического строительства
(наименование кафедры)
(подпись) (фамилия имя отчество)
Смирнову Алексею Анатольевичу
Тема «Проект комплекса по перегрузке минеральных удобрений в Мурманском морском торговом порту»
Исходные данные к проекту: навигационный грузооборот 2000000 тонн; время навигации 365 суток; прибытие груза - вагон; отправка груза - судно.
Перечень вопросов подлежащих разработке:
Введение. Актуальность темы цели и задачи дипломного проекта.
_Toc2164465591 ОБЩАЯ ХАРАКТЕРИСТИКА МУРМАНСКОГО ТОРГОВОГО ПОРТА
1 История возникновения порта
2 Характеристика порта
МЕХАНИЗАЦИЯ И ТЕХНОЛОГИЯ ПЕРЕГРУЗОЧНЫХ РАБОТ
1 Технология перегрузки минеральных удобрений
2 Грузовые операции внутри терминала
АНАЛИЗ ИСХОДНЫХ ДАННЫХ
1Определение грузооборота причала
2 Краткая характеристика минеральных удобрений
3 Определение грузовой обработки транспортных средств
4 Определение расчетной вместимости склада
5 Определение расчетной интенсивности обработки транспортных средств
РАЗРАБОТКА ВАРИАНТОВ СХЕМ МЕХАНИЗАЦИИ
1 Разработка конвейерной схемы механизации
2 Разработка крановой схемы механизации
РАСЧЕТ ПРИЧАЛЬНОГО ЛЕНТОЧНОГО КОНВЕЙЕРА
1 Расчет класса использования конвейера расчет и выбор ленты
2 Расчет и выбор поддерживающих устройств
3 Подробный тяговый расчет конвейера
4 Расчет электродвигателя редуктора муфты и тормозного устройства
5 Расчет натяжного устройства
РАСЧЕТ СУДОПОГРУЗОЧНОЙ МАШИНЫ
1 Описание судопогрузочной машины
2 Расчет телескопического ленточного конвейера
2.1 Расчет класса использования конвейера расчет и выбор ленты
2.2 Расчет и выбор поддерживающих устройств
2.3 Подробный тяговый расчет конвейера
2.4 Расчет мощности электродвигателя
2.5 Расчет натяжного устройства
3 расчет механизма подъема галереи
3.1 Расчет ветровой нагрузки на галерею
3.3 Расчет геометрических параметров блока
3.4 Расчет мощности электродвигателя и выбор тормоза
4 Расчет механизма передвижения судопогрузочной машины
4.1 Расчет ветровой нагрузки на судопогрузочную машину
4.2 Определение сопротивления передвижению судопогрузочной машины
4.3 Расчет мощности электродвигателя
РАСЧЕТ ШАРИКОЙ ВИНТОВОЙ ПАРЫ
1 Определение сопротивления передвижению сбрасывающей консоли
2 Выбор типоразмера шариковой винтовой пары
3 Расчет на статическую прочность Расчет на динамическую устойчивость
4 Расчет коэффициента полезного действия шариковой винтовой пары
5 Расчет геометрии профиля резьбы
6 Расчет стержня винта на прочность
7 Расчет мощности электродвигателя
РАСЧЕТ МЕТАЛЛОКОНСТРУКЦИИ ГАЛЕРЕИ
1 Определение геометрических параметров галереи
2 Определение расчетных нагрузок на галерею и построение эпюр изгибающих
моментов и поперечных сил
3 Расчет металлоконструкции галереи на гибкость
4 Проверка стоек и раскосов на устойчивость
5 Проверка сварных швов стоек и раскосов
ОПИСАНИЕ РАБОТЫ ЭЛЕКТРОСХЕМЫ ПРИВОДА ЛЕНТОЧНОГО КОНВЕЙЕРА
ТЕХНОЛОГИЯ ИЗГОТОВЛЕНИЯ РОЛИКООПОР
ТЕХНИЧЕСКОЕ ОБСЛУЖИВАНИЕ И МОНТАЖ КОНВЕЙЕРА
1 Основные требования предъявляемые к монтажу конвейера
2 Основные операции проводимые при техническом обслуживании и ремонте
ОХРАНА ТРУДА И ЭКОЛОГИЧЕСКАЯ БЕЗОПАСНОСТЬ ПРИ ЭКСПЛУАТАЦИИ
1 Безопасность труда при эксплуатации конвейеров
2 Безопасность труда при эксплуатации специализированного
конвейерного комплекса для навалочных грузов
3 Экологическая безопасность при эксплуатации конвейеров
ЗАКЛЮЧЕНИЕ. Выводы по проекту в целом. Оценка степени решения поставленных задач. Практические рекомендации.
Перечень материалов представляемых к защите:
Пояснительная записка на 144 листах формата А4.
Конвейерная схема механизации - 1 лист формата А1;
Крановая схема механизации - 1 листа формата А1;
Электрическая схема привода ленточного конвейера - 1 лист формата А1;
Общий вид судопогрузочной машины - 1 лист формата А1;
Механизм подъема - 1 лист формата А1;
Механизм передвижения - 1 лист формата А1;
Причальный ленточный конвейер - 1 лист формата А1;
Телескопический ленточный конвейер - 1 лист формата А1;
Составные части ленточного конвейера - 1 лист формата А1;
Разгрузочная тележка - 1 лист формата А1;
Шариковая винтовая пара - 1 лист формата А1;
Металлоконструкция подъемной галереи - 1 лист формата А1.
Консультанты по проекту:
1 ст. преподаватель Катович А.Д. главы №234;
2 ст. преподаватель Данч Р.В. главы №15610;
3 преподаватель Кондрулев К.С. главы №711;
4 преподаватель Реутов В.В. глава №8;
5 к.т.н. доцент кафедры ППТТиГС Капустин А.Н. глава №9;
6 ст. преподаватель Кобылянский И.Г. глава №12.
Руководитель дипломной работы
(должность ученая степень ученое звание фамилия имя отчество) (подпись)
(фамилия имя отчество учебная группа) (подпись)
4 Схема механизации.doc
1 Разработка конвейерной схемы механизации
Величина расчетной интенсивности работы оборудования грузовых фронтов для базового варианта схемы комплекса принимается из условия:
Принимаем величину расчетной интенсивности работы оборудования грузового фронта для базового варианта схемы комплекса равной:
Исходя из расчетной интенсивности работы оборудования грузового фронта разрабатываем механизированный комплекс производительностью 600тч.
Управление перегрузочным процессом централизованно и производится оператором с пульта на который поступает вся информация о работе машин. На всех машинах предусмотрена звуковая и световая сигнализация предупреждающая рабочих о пуске технологического оборудования. Передвижная конвейерная машина для загрузки судов изображена на рисунке 4.1.
Рисунок 4.1 – Передвижная конвейерная машина для загрузки судов
При работе по варианту вагон - судно вагон с минеральным удобрением поступает на вагоноразгрузочное устройство после чего удобрение попадает на конвейерную линию по которой поступает к передвижной конвейерной машине для загрузки судов (рисунок 4.2).
Рисунок 4.2 - Структурно-элементная схема перегрузочного комплекса
Определим число технологических линий по формуле:
где - интенсивность грузовой обработки вагонов (=488тч);
- производительность фронтальной машины (= 300тч).
Для загрузки подающих конвейеров со складов используем ковшовые погрузчики грузоподъемностью 10т с объемом ковша .
Определим массу груза т перемещаемую автопогрузчиком за 1 цикл по формуле:
где - удельный вес груза .
- коэффициент заполнения ковша () [45 с. 17 таблица 9].
Определим продолжительность одного цикла автопогрузчика сек по формуле:
где t1 – время зачерпывания ковшом груза () [45 с. 50 таблица 33];
t2 – время разворота погрузчика при развороте на 180º () [45 с. 50 таблица 33];
t3 – продолжительность перемещения погрузчика с грузом;
t4 – время на разгрузку ковша () [45 с. 50 таблица 33];
t5 – время разворота погрузчика с порожним ковшом () [45 с. 50 таблица 33];
t6 – продолжительность перемещения погрузчика без груза;
φ-коэффициент совмещения рабочих движений ().
Определим продолжительность перемещения погрузчика с грузом и без груза соответственно с по формуле:
где L – путь передвижения погрузчика в метрах принимаем (L=50м);
– скорость передвижения погрузчика (=139мс) с грузом (=222мс) без груза;
tр.з. – время на разгон и замедление (tр.з =1-15с).
Определим производительность автопогрузчика PП тч по формуле:
Определим количество автопогрузчиков занятых на одной технологической линии по формуле:
Для обеспечения заданной интенсивности обработки судна необходимо 3 ковшовых погрузчика для загрузки подающих конвейеров грузом.
Определяем время грузовой обработки судна ч по формуле:
где - фактическая загрузка судна (=22100т).
Определим время занятости причала ч по формуле:
Определим эффективное время работы оборудования причала в течении суток ч по формуле:
где - коэффициент затрат времени на отдых (= 085);
- суммарная продолжительность трех смен (=23ч).
Определим пропускную способность причала тсут по формуле:
Проведем проверку причала с его механовооруженностью освоить расчетный грузооборот:
Определим средний коэффициент занятости причала по формуле:
На основе результатов составляется сводная таблица расчетных показателей (таблица 4.1).
Таблица 4.1 – Таблица исходных данных
Технологическая линия
Время грузовой обработки судна
Время занятости причала
Пропускная способность причала
средний коэффициент занятости
Определим время работы машин в составе технологической линии на грузовых операциях ч по формуле:
Определим трудозатраты на перегрузочную операцию чел.см по формуле:
где – комплексная норма выработки (=550тчел.см.).
Определим списочную численность рабочих чел по формуле:
где – коэффициент списочности (=13);
Состав элементов инженерных сооружений причала и общепортовых систем и сооружений приведены в таблице 4.2.
Таблица 4.2 – Расчет строительной стоимости и амортизационной составляющей эксплуатационных расходов причала
Перегрузочное оборудование
разгрузочная установка
Разгрузочная тележка барабанная
Инженерные сооружения причала
Асфальтовое покрытие
Стоимость вертикальной причальной набережной
Определим эксплуатационные расходы по причалу у.е. по формуле:
где – амортизационная составляющая расходов на перегрузочное оборудование причала (=40184тыс.у.е.);
– амортизационная составляющая расходов по инженерным сооружениям причала (=5383тыс.у.е.);
– суммарные затраты на электроэнергию у.е.;
– суммарные затраты на топливо у.е.;
– суммарные затраты на заработную плату у.е.
Определим суммарные затраты на электроэнергию у.е. по формуле:
где - суммарный расход электроэнергии (кВт);
- стоимость одного кВт электроэнергии (тыс.у.е.)
Определим суммарные затраты на топливо у.е. по формуле:
где - расходы на топливо локомотива тыс.у.е.;
- расходы на топливо вспомогательных машин тыс.у.е.
Определим расходы на топливо локомотива тыс.у.е. по формуле:
где - расход топлива локомотива (лчас) [45 c.39]с;
- время работы локомотива (ч);
- стоимость одного литра топлива ( тыс.у.е.).
Определим расходы на топливо вспомогательных маши тыс.у.е. по формуле:
где - расход топлива вспомогательной машиной (лчас) [45 c.39];
- количество вспомогательных машин ().
Определим суммарные затраты на топливо тыс. у.е. по формуле:
Определим суммарные затраты на заработную плату у.е. по формуле:
где – коэффициент доплаты за работу в ночное время выходные и праздничные дни ();
9 – коэффициент дополнительных расходов на содержание распорядительского и обслуживающего персонала;
- сменная тарифная ставка рабочего бригады:
Определим сменную тарифную ставку рабочего бригады тыс.у.е. по формуле:
где – часовая рабочая ставка рабочего (=0008 тыс.у.е.);
– время рабочей смены (=8ч);
– коэффициент доплаты к тарифной ставке при выполнении сменной нормы перегрузочных работ (=15).
– суммарный баланс рабочего времени:
Определим суммарный баланс рабочего времени челсмен по формуле:
– сменная тарифная ставка рабочего бригады на общепортовых работах:
Определим сменную тарифную ставку рабочего бригады на общепортовых работах тыс.у.е. по формуле:
– коэффициент начислений учитывающий дополнительные расходы на единый социальный налог (=04) [45 с.39].
Определим себестоимость перегрузочных работ С у.е. по формуле:
Определим доход приносимый причалом при переработки навигационного грузооборота D у.е. по формуле:
где d - доход ставки на перегрузку одной тонны груза (d =8у.е.).
Определим прибыль полученную при использовании в данной схеме механизации у.е. по формуле:
Определим срок окупаемости перегрузочного комплекса год по формуле:
где - строительная стоимость перегрузочного комплекса у.е. (19491670у.е.);
- прибыль получаемая от работы перегрузочного комплекса за навигационный грузооборот у.е.
Таким образом разработали комплекс для перегрузки минеральных удобрений рассчитали эксплуатационные расходы по перегрузочным работам и затраты на перегрузку одной тонны удобрений а также установили срок окупаемости перегрузочного комплекса который составил 36года.
2 Разработка крановой схемы механизации
Выбираем крановую схему механизации с использованием козлового крана с подъемной консолью. Погрузка судна будет осуществляться из вагонов в судно. Минеральные удобрения будем хранить навалом и перегружать грейфером.
Выбираем грейфер для сыпучих грузов объемом .
Определим массу груза т перемещаемую краном за 1 цикл по формуле:
где - удельный вес груза ;
- коэффициент заполнения грейфера () [45 с. 17 таблица 9].
Определим производительность фронтальной машины тч по формуле:
где - количество циклов в час.
Определим количество циклов в час фронтальной машины по формуле:
где - продолжительность одного цикла сек.
Найдем продолжительность одного цикла по формуле:
где - время захвата груза грейфером () [45 с.46 таблица 28];
- время подъема груза сек;
- время движения крана с грузом сек;
- время спуска грузозахватного устройства с грузом сек;
- время на высыпку груза из грейфера ( сек) [45 с.47 таблица 29];
- время подъема пустого грузозахватного устройства сек;
- время движения крана без груза сек;
- время спуска пустого грузозахватного устройства сек;
- коэффициент совмещения рабочих движений (φ = 07).
Определим время подъема груза и пустого грузозахватного устройства сек по формуле:
где - высота подъема груза (=15м);
- скорость подъема груза(=12мс);
- время разгона механизма (= 1сек);
- время торможения механизма (= 2сек).
Так как время спуска и время подъема одинаковы то с.
Определим время движения тележки крана с грузом и без груза сек по формуле:
где - перемещение тележки крана ();
- скорость перемещения тележки ().
Определим продолжительность одного цикла сек по формуле:
Определим количество циклов в час фронтальных машин по формуле:
Для обеспечения заданной интенсивности обработки принимаем 3 механизированные линии.
Для формирования штабеля на складе используем ковшовые погрузчики грузоподъемностью 10т с объемом ковша .
где - удельный вес груза ().
Для обеспечения заданной интенсивности обработки судна необходим 1 ковшовый погрузчик на каждую механизированную линию.
Определим время грузовой обработки судна ч по формуле:
где - фактическая загрузка судна =22100т;
- коэффициент снижения интенсивности обработки судна () [45 с. 30].
Определяем средний коэффициент занятости причала тсут по формуле:
На основе результатов составляется сводная таблица расчетных показателей (Таблица 4.3).
Таблица 4.3 – Таблица исходных данных
средний коэффецент занятости
Определим время работы машины в составе технологической линии на грузовых операциях машч по формуле:
где – комплексная норма выработки (=450тчел.смена).
Состав элементов инженерных сооружений причала и общепортовых систем и сооружений приведены в (Таблице 4.4).
Таблица 4.4 – Расчет строительной стоимости и амортизационной составляющей эксплуатационных расходов причала
продолжение таблицы 4.4
где – амортизационная составляющая расходов на перегрузочное оборудование причала (=3492тыс.у.е.);
– амортизационная составляющая расходов по инженерным сооружениям причала (=47907тыс.у.е.);
Определим суммарные затраты на электроэнергию тыс.у.е. по формуле:
- стоимость одного кВт электроэнергии принимаем (тыс.у.е.)
Определим суммарные затраты на топливо тыс.у.е. по формуле:
- расходы на топливо вспомогательных машин тыс.у.е..
Определяем расходы на топливо локомотива тыс. у.е. по формуле:
– коэффициент начислений учитывающий дополнительные расходы на единый социальный налог (=04) [44 с.39].
где d – доход ставки на перегрузку одной тонны груза (d =8у.е.);
где - строительная стоимость перегрузочного комплекса у.е. (18854830у.е.);
Таким образом разработали комплекс для перегрузки минеральных удобрений рассчитали эксплуатационные расходы по перегрузочным работам и затраты на перегрузку одной тонны удобрений а также установили срок окупаемости перегрузочного комплекса который составил 115лет.
12Охрана труда.doc
ПРИ ЭКСПЛУАТАЦИИ КОНВЕЙЕРОВ
1 Безопасность труда при эксплуатации конвейеров
Перед пуском ленточного конвейера в работу необходимо проверить:
чистоту и целостность ленты правильность ее положения и достаточность натяжения;
состояние очистных устройств;
во время работы следить чтобы ролики вращались;
чтобы лоток не истирал ленту материал распределялся по ней равномерно;
чтобы лента не сбегала в сторону;
проследить за работой очистных устройств;
за нагревом подшипников редуктора;
за своевременной приемкой материалов ленточным конвейером.
Окончив работу остановить конвейер после полной разгрузки ленты отключить электропитание осмотреть ленту и все механизмы ленточного конвейера.
От правильной и своевременной смазки узлов оборудования зависит надежность и долговечность работы конвейера. Смазка подшипников барабанов осуществляется через пресс масленки консистентной смазкой. Смазка редукторов путем заливки в картер масла «Индустриального - 50».
Обслуживать ленточный конвейер могут лица прошедшие обучение по программе утвержденной техническим руководителем эксплуатирующей организации прошедшие проверку знаний и получившие допуск к обслуживанию конвейерного комплекса.
Эксплуатирующая организация обязана составить инструкцию по охране труда для лиц обслуживающих ленточный конвейер в соответствии с нормами и правилами действующими в этой организации.
С инструкцией должны быть ознакомлены под роспись все лица занимающиеся обслуживанием и ремонтом конвейерного комплекса.
В указанной инструкции по охране труда должны содержаться следующие требования:
рама ленточного конвейера корпус редуктора и электродвигателя должны быть заземлены. Перед началом работы машинист обязан проверить целостность заземляющих проводов и шин;
перед запуском конвейера машинист должен проверить следующее: убедиться что в непосредственной близости отсутствуют люди; проверить чистоту барабанов и роликов отсутствие на них слоя груза;
проверить уровень масла в редукторе конвейера;
подать предупредительный сигнал.
Произвести пробный пуск конвейера на 2-3 минуты. Во время работы конвейера проверить ленту на отсутствие видимых повреждений на отсутствие посторонних звуков свидетельствующих о ненормальной работе конвейера редуктора роликов электродвигателя. Произвести проверку работоспособности системы экстренной остановки конвейера (трос по всей длине конвейера со стороны свободных проходов) для чего произвести остановку ленточного конвейера с помощью этой системы. Запрещается работать на конвейере при обнаружении повышенной вибрации.
Во время работы ленточного конвейера производить какой-либо ремонт смазку и очистку запрещается. Запрещается перелазить через работающий конвейер становиться на его раму браться руками за нее.
Запрещается работать в случае перекоса и пробуксовывания ленты выбрасывать какие-либо материалы на барабан под движущуюся ленту с целью устранения ее пробуксовывания очищать ленту на ходу вручную и производить уборку под лентой и барабанами при работающем ленточном конвейере.
2 Безопасность труда при эксплуатации специализированного
конвейерного комплекса для навалочных грузов
На комплексе предусматривается широкая механизация и автоматизация перегрузочных и транспортных операций с полным исключением ручного труда. Управление комплексом осуществляется с центрального пульта конструкция конвейеров обеспечивает удобный доступ для осмотра и смазки отдельных частей и узлов. Движущиеся части конвейеров к которым возможен доступ обслуживающего персонала и лиц работающих вблизи конвейеров ограждаются по всей длине легко съемными конструкциями при снятии ограждения на ЦПУ подается сигнал. На всех конвейерах предусмотрены устройства аварийной остановки их с любого места вдоль конвейерной линии. Канаты и грузы натяжных станций ограждаются для исключения прохода людей под грузом. Маршруты передвижения персонала по комплексу регламентируются специально разработанными для комплекса "Правилами техники безопасности" разработанными руководством комплекса.
При ограниченном обзоре зоны загрузки из кабины машиниста судовой погрузочной машины следует назначать сигнальщика. В обязанности сигнальщика входит подача команд машинисту на выполнение тех или иных операций согласно перечню сигналов который должен быть разработан и утвержден портом с учетом конструктивных особенностей машины. В случае если машинист плохо различает сигналы сигнальщика работа судовой погрузочной машины должна быть прекращена.
Перемещение стрелы перегрузочной машины в горизонтальной плоскости допускается только после подъема ее не менее чем на 1м выше встречающихся на пути предметов или на расстоянии по горизонтали не менее 1м от них.
Операции по установке и расцепке вагонов должны производиться только после срабатывания световой и звуковой сигнализаций на вагоноопрокидывателе. При выполнении операции расцепки помощнику машиниста вагоноопрокидывателя следует руководствоваться сводом сигналов применяемом при маневровых работах и помещенным в Инструкции по сигнализации на железных дорогах Российской Федерации. При подаче сигналов допускается пользоваться переносными радиостанциями.
При эксплуатации вагоноопрокидывателя запрещается:
- допускать въезд локомотива на платформу;
- производить разгрузку технически неисправных вагонов а также вагонов не соответствующих технической характеристике вагоноопрокидывателя;
- находиться на вагоне во время его установки в вагоноопрокидыватель;
- находиться между вагоном и привалочной стенкой вагоноопрокидывателя.
Чистку бункеров и надбункерных решеток допускается производить только после установки специальных деревянных мостков предотвращающих падение людей сквозь ячейки надбункерной решетки. При работе перегрузочных машин запрещается: находиться вблизи рабочих органов (под стрелой метателем спускной трубой конвейера) а также в бункерах и на надбункерных решетках на железнодорожных путях надвига и откатки вагонов в зоне опрокидывания вагона вагоноопрокидывателем. Обслуживающий персонал при работе с химически активными грузами (карбамид калийная соль и т.п.) должен руководствоваться "Правилами безопасности морской перевозки незерновых навалочных грузов". Эксплуатация перегрузочных машин разрешается только при исправной системе вентиляции и аспирации. Система вентиляции и аспирации должна эксплуатироваться в соответствии с требованиями заводской (фирменной) документации.
3 Экологическая безопасность при эксплуатации конвейеров
При эксплуатации конвейеров необходимо обеспечивать соблюдение природоохранного законодательства при осуществлении технического обслуживания и производстве ремонта. Для определения количества выбросов от передвижных источников (транспортных средств) необходимо ведение учета количества сожженного топлива и количества часов эксплуатации транспортных средств. Запрещается ремонт заправка топливом мойка машин и транспортных средств складирование отходов в пределах водоохранных зон.
Диапазоны рабочей температуры окружающей среды и силы ветра при которых разрешается работа перегрузочных машин специализированного конвейерного комплекса определяются требованиями заводской (фирменной) документации и устанавливаются приказом по порту.
Специализированный конвейерный комплекс выполнен в соответствии с международными стандартами по охране окружающей среды для перегрузочных комплексов навалочных грузов. Все объекты комплекса выполнены в крытом исполнении таким образом что исключается выход пыли наружу. Специально предусмотрены аспирационные устройства объединенные в единую систему для предотвращения выхода пыли по торцам предусмотрены эластичные шторы. Все помещения оснащены специальными пылесосными установками. Судопогрузочная машина оснащена пылеподавляющей системой которая предотвращает существенное образование пыли в процессе загрузки трюмов судна. В кабинах машин в помещении ЦПУ и других помещениях предусматривается повышенное давление ~40-50мм водяного столба для предотвращения проникновения пыли внутрь помещений и кабин.
10технология изготовления.doc
Ролики применяют в роликовых и ленточных конвейерах в виде отдельных узлов или как составные элементы роликоопор.
Ролики конвейеров изготовляемые по ГОСТ 8324-71 имеют диаметры от 55 до 160мм и длину до 1600мм однако для ленточных транспортеров изготовляют ролики и других размеров. Ролики могут быть по наружной поверхности обрезинены.
Корпусы роликов изготовляют из стальных бесшовных труб [19] в двух вариантах: с обработанной наружной поверхностью и без обработки. Иногда ролики выполняют литыми из стали или чугуна.
Отклонения размеров обработанных роликов по наружному диаметру должны соответствовать 12-му квалитету для необработанных - допускаемым отклонениям для горячекатаных труб повышенной точности. Радиальное биение наружных поверхностей необработанных роликов не должно превышать 15% наружного диаметра (т.е. 09 - 14мм) обработанных роликов - 05% (т. е. 03 - 08мм).
Так как в комплект каждого конвейера входят десятки и сотни роликов объем их выпуска оказывается значительным. Увеличению объема выпуска способствует также высокая степень унификации конструкции роликов.
Все это создает благоприятные условия для применения высокопроизводительной технологии и в частности для эффективного применения групповых методов при обработке и сборке.
Технология обработки корпуса ролика состоит из двух операций - отрезной и расточной. Отрезку заготовки заданной длины выполняют на станке с дисковой пилой по упору. Обработку выточек под подшипники подрезку торцов и снятие фасок выполняют на агрегатном двухстороннем четырехшпиндельном станке при установке заготовок в двухместном приспособлении (рисунок 10.1) и штучном времени менее 1 минуты.
Станок имеет две двухшпиндельные силовые головки 1 и поворотный стол 2 с двумя двухместными приспособлениями 3. Это позволяет во время обработки двух деталей в рабочей позиции снимать и устанавливать две заготовки в загрузочной позиции.
Многорезцовая головка 4 представляет собой разновидность применяемой в массовом производстве быстросменной технологической оснастки. Четыре резца (расточный подрезной и фасочные для наружной и внутренней фасок) устанавливают в корпусе головки вне станка по шаблону обеспечивающему их правильное взаимное положение. Глубина расточки обеспечивается упором ограничивающим длину хода агрегатной головки. Встроенное в станок пневматическое приспособление позволяет закреплять в цанговых зажимах одновременно две заготовки каждую в двух концевых сечениях.
где а - компоновочная схема;
б - схема обработки в одной рабочей позиции.
Рисунок 10.1 - Обработка корпуса ролика на агрегатном четырехшпиндельном станке
Приспособление имеет вал упоров с помощью которого устанавливаемые заготовки ориентируются в осевом направлении путем выравнивания торцов. После закрепления заготовок поворотом рукоятки упоры отводятся освобождая торцы заготовок для обработки.
7РАСЧЕТ ШВП.doc
1 Определение сопротивления передвижению сбрасывающей консоли
Определим количество ходовых колес на телескопическом участке конвейера по формуле:
где - расстояние между роликоопорами рабочей ветви конвейера ().
Определим массу телескопического участка конвейера Н по формуле:
где 15 - коэффициент неучтенных масс участка конвейера;
- распределенная масса груза приходящаяся на метр длины конвейерной ленты ();
- длина телескопического участка ().
Определим максимальное давление приходящееся на колесо Н по формуле:
В зависимости от максимального давления на колесо определяем его диаметр и тип рельса: выбираем двухребордное колесо диаметром [14] тип рельса Р-24 [15].
Определим диаметр цапфы мм по формуле:
Определим статическое сопротивление передвижению кН по формуле:
где – сопротивление от трения в ходовых частях Н;
– сопротивление движению от уклона пути Н;
– сопротивление сил инерции Н.
Определим сопротивление от трения в ходовой части Н по формуле:
где – коэффициент трения качения колеса по рельсу () [42 с. 40 таблица 2.13];
– коэффициент трения подшипников приведённый к цапфе колеса () [42 с. 40 таблица 2.14];
– коэффициент учитывающий трения реборд ступиц колёс () [42 с. 41 таблица 2.15].
Определим сопротивление движению от уклона пути Н по формуле:
где – уклон подкрановых путей для портальных кранов () [42 с. 41].
Определим сопротивление сил инерции Н по формуле:
где – скорость передвижения крана ();
– время разгона механизма до номинальной скорости ().
Определим запас сцепления ходовых колес с рельсами при разгоне на подъем против ветра и при торможении под уклон по ветру по формуле:
где – коэффициент сцепления приводных колес с рельсом (=02) (42 с. 90);
– минимальное значение коэффициента сопротивления передвижению ();
– расчетная нагрузка Н;
– допускаемый коэффициент запаса сцепления () [42 с. 89].
Определим расчетную нагрузку Н действующую на механизм по формуле:
где – коэффициент толчков зависящий от скорости передвижения при ().
Запас сцепления обеспечен.
Таким образом определили статическое сопротивление передвижению погрузочной машины определили диаметр ходовых колес и давление одного колеса на рельс .
2 Выбор типоразмера шариковой винтовой пары
Определим корректирующий коэффициент для вычисления расчетного значения динамической грузоподъемности по формуле:
где - коэффициент точности изготовления передачи () [31 с. 798 таблица 16];
- коэффициент безотказной работы () [31 с. 798 таблица 17];
- коэффициент влияния качества материала () [31 с. 797];
- коэффициент учета числа витков гайки при числе витков () [31 с. 798 таблица 18].
Определим корректирующий коэффициент для вычисления расчетного значения статической грузоподъемности по формуле:
- коэффициент безотказной работы () [31 с. 798 таблица 18];
Определим минимальную базовую динамическую грузоподъемность передачи Н по формуле:
Определим расчетный диметр резьбы мм по формуле:
где - коэффициент высоты гайки () [41 с. 258];
- коэффициент высоты резьбы () [41 с. 260 таблица 15.1.2];
- среднее допускаемое давление между рабочими поверхностями витков винта и гайки () [41 с. 260 таблица 15.1.1].
По значениям минимальной базовой динамической грузоподъемности и расчетного диаметра выбираем типоразмер шариковой винтовой пары исходя из условий (31 с. 792 таблица 12):
Выбираем шариковую винтовую пару номинальным диаметром резьбы винта шагом резьбы винта диаметром шариков базовой динамической грузоподъемностью статической -.
Определим значение скорректированной динамической грузоподъемности Н по формуле:
Определим значение скорректированной статической грузоподъемности Н по формуле:
Определим силу предварительного натяга Н по формуле:
Определим минимальное значение предварительного натяга Н по формуле:
Определим коэффициент учитывающий неполноту рабочего витка вследствии наличия шариков в перепускном канале по формуле:
где - число заходов резьбы () [31 с. 797].
Определим максимально достижимую жесткость выбранного типоразмера ШВП Нмкм по формуле:
- минимальная жесткость выбранного типоразмера ШВП () [31 с791 таблица 10].
Жесткость передачи обеспечена.
3 Расчет на статическую прочность и динамическую устойчивость
Определим силу нагружающую рабочую гайку Н по формуле:
где - осевая сила действующая на рабочую гайку () [31 с. 792 таблица 11].
Определим силу нагружающую нерабочую (правую) гайку Н по формуле:
При расчете на статическую прочность ШВП с натягом расчетной силой Н служит наибольшая из двух нагружающих рабочую и не рабочую гайки:
Определим значение критической силы Н на винт по формуле:
где - модуль упругости () [31 с. 801];
- коэффициент зависящий от способа закрепления винта () [31 с. 801 таблица 19];
- коэффициент запаса прочности () [31 с. 801];
- длина неопорного участка винта ().
Статическая прочность обеспечена.
Определим предельную частоту вращения винта обмин по формуле:
где - предельная линейная скорость шарика () [31 с. 801].
Определим критическую частоту вращения винта обмин по формуле:
где - коэффициент зависящий от способа закрепления винта () [31 с. 801 таблица 19];
- коэффициент запаса по частоте вращения () [Анурьев с. 801].
Определим критическую линейную скорость перемещения гайки ммин по формуле:
где - шаг резьбы винта ().
Динамическая устойчивость обеспечена.
4 Расчет коэффициента полезного действия шариковой винтовой пары
Определим приведенный угол трения в резьбе град по формуле:
где - коэффициент трения качения () [31 с. 801];
- угол контакта () [Анурьев с. 801].
Определим угол подъема резьбы град по формуле:
Определим КПД ШВП по формуле:
где - коэффициент учитывающий влияние натяга () [31 с. 801].
Определим момент холостого хода для передачи по формуле:
Определим наибольший момент завинчивания по формуле:
Таким образом определи КПД передачи.
6 Расчет геометрии профиля резьбы
Рассчитываемые размеры профиля резьбы шариковой винтовой пары отображены на рисунке 7.1
Рисунок 7.1 - Геометрия профиля резьбы
Определим радиус профиля резьбы мм по формуле:
Определим число шариков в одном витке гайки по формуле:
Определим число шариков в канале возврата по формуле:
Определим число рабочих шариков в одном витке по формуле:
Определим расчетное число шариков в гайке по формуле:
Определим нормальную силу нагружающую один шарик Н по формуле:
Определим параметры площадки контакта между телом качения и дорожкой качения по формулам:
Определим радиус галтели винта мм по формуле:
Определим радиус галтели гайки мм по формуле:
Определим наружный диаметр резьбы винта мм по формуле:
Определим смещение центра радиуса профиля мм по формуле:
Определим внутренний диаметр резьбы винта мм по формуле:
Определим наружный диаметр резьбы гайки мм по формуле:
Определим внутренний диаметр резьбы гайки мм по формуле:
Определим диаметр качения по винту мм по формуле:
Определим диаметр качения по гайке мм по формуле:
Таким образом произвели расчет геометрии профиля резьбы.
7 Расчет стержня винта на прочность
Определим допускаемое напряжение на винт МПа по формуле:
где – предел текучести материала винта (МПа) [41 с. 271 таблица 16.2.1].
Определим напряжение растяжения-сжатия МПа по формуле.
Определим напряжение кручения МПа по формуле:
Определим эквивалентное напряжение винта МПа по формуле:
Определим смешение гаек для создания предварительного натяга мкм по формуле:
Определим осевую жесткость винта Нмкм по формуле:
Прочность стержня винта обеспечена.
8 Расчет мощности электродвигателя
Определим статическую мощность одного двигателя в период установившегося движения при передвижении погрузочной машины кВт по формуле:
где - коэффициент запаса мощности () [47 с. 121];
- скорость передвижения (мсек);
- кпд редуктора () [42 с. 42];
Выбираем асинхронный электродвигатель с фазным ротором серии АИР 112МА8 [12] мощностью =22кВт при частоте вращения =2860обмин. Кратность максимального момента кратность минимального момента .
Определим частоту вращения вала приводного колеса обмин по формуле:
Определим требуемое передаточное число привода по формуле:
Выбираем цилиндрический вертикальный одноступенчатый редуктор 1ЦУ 100 с передаточным числом 2 и КПД =096.редуктора 27кг. Крутящий момент .
Определим фактическую скорость подъема галереи ммин по формуле:
Для выбора соединительной муфты между двигателем и редуктором определим номинальный крутящий момент двигателя Нм по формуле:
где - мощность двигателя кВт;
- частота вращения обмин.
С учетом коэффициента кратности максимального момента двигателя определяем расчетный момент муфты Нм по формуле:
Выбираем упругую втулочно-пальцевую муфту 315-18-1 УЗ [9] с наибольшим передаваемым крутящим моментом =315Н×м.
Определим расчётный тормозной момент по формуле:
где – коэффициент запаса торможения согласно правилам Госгортехнадзора () [42 с. 44[;
– момент создаваемый уклоном ;
– момент создаваемый силами трения .
- момент создаваемый силами инерции .
Определим момент создаваемый уклоном по формуле:
где – радиус колеса (м).
Определим момент создаваемый силами инерции по формуле:
Определим момент создаваемый силами трения по формуле:
Устанавливаем на вал тормоз ТКТ-100 с наибольшим тормозным моментом 100Н×м который следует регулировать на нужный тормозной момент.
11ТО.doc
1 Основные требования предъявляемые к монтажу конвейера
Машины механизмы транспортные устройства имеющие небольшие габариты поступают на монтаж отдельными узлами. Поэтому производство монтажных работ всегда включает в той или иной мере выполнение сборочных операций сопровождающихся подгонкой и регулировкой отдельных механизмов. Исходными данными для сборки наладки и пуска отдельных машин являются заводские инструкции сборочные чертежи и технические условия на сдачу машины в эксплуатацию.
Перед сборкой машины необходимо тщательно изучить ее конструкцию условия работы технические условия сборки. При сборке необходимо обеспечить точность положения узлов что достигается регулировкой. Для регулировки отдельных элементов применяются различные компенсирующие устройства. Например прокладки и натяжные устройства передач транспортеров.
При компоновке и размещении оборудования необходимо соблюдать размеры проходов обеспечивающих нормальную эксплуатацию и безопасность. Они должны быть следующими: между движущимися частями смежностоящего оборудования - 1м; между движущимися частями оборудования и стеной - 08м; между неподвижными частями смежного оборудования - 08м; между стеной и неподвижными частями оборудования - 05м; между фронтом оборудования на котором расположены приборы и арматура требующие постоянного обслуживания и стеной или смежным оборудованием - не менее 1м.
Ленточные конвейеры иногда относят к нестандартизированному оборудованию и изготовляет их монтажная организация. Изготовляют станины собирают приводную и натяжную станции в мастерских монтажных заготовок монтажной организации и доставляют к месту установки транспортабельными звеньями.
До начала монтажа производят проверку механических узлов и комплектуют верхние роликовые опоры с их балочками и стойками. Подшипники роликов не вскрывают и смазку в них не заменяют.
После нанесения продольной монтажной оси транспортера вдоль нее натягивают струну и по ней устанавливают станину методом постепенного наращивания начиная от приводной или натяжной станции выверяя ее по оси.
Проверку горизонтальности положения станины производят монтажным или гидростатическим уровнем а положение ее относительно монтажной оси при помощи шаблона с осевой риской. Шаблон представляет собой деревянную планку длинна которой равна ширине станины. Его кладут между продольными уголками станины а на него от монтажной оси транспортера опускают отвесы. Станина установлена правильно если отвесы по всей ее длине совпадают с риской шаблона. Станину к перекрытию крепят болтами.
После установки и закрепления станины приступают к монтажу приводной и натяжной станций.
По осям приводной и натяжной станций зафиксированных стальной струной под прямым углом к продольной оси транспортера устанавливают опорные металлические конструкции на которых крепят подшипники ведущего и ведомого валов. Далее укладывают валы с барабанами и пришабривают подшипники. Оси валов и барабанов должны быть перпендикулярны продольной оси транспортера. При центровке редуктора с электродвигателем обеспечивают горизонтальность и соосность валов. Радиальное и торцевое биение полумуфт свыше 01мм не допускается.
При установке направляющих натяжного вала обеспечивают параллельность и горизонтальность продольных осей полозков по отношению к продольной оси транспортера на одинаковом от нее расстоянии.
С помощью шаблона для разметки отверстий под болты на станину наносят оси роликовых опор и фиксируют положение отверстий для их крепления. Оси роликов и барабанов должны быть строго параллельны между собой и перпендикулярны оси транспортера. После сверления отверстий устанавливают верхние и нижние роликовые опоры с помощью струн. Поверхности роликов должны находиться в одной горизонтальной плоскости. Допустимое отклонение роликов по высотным отметкам и смещение середины роликов от оси транспортера не должны превышать ±1мм. Регулировка их положения по высоте производится с помощью прокладок.
Заключительными операциями являются натяжение ленты и вулканизация ее стыков. Концы ленты разделывают по ступеням число которых соответствует числу тканевых прокладок ленты. После отделения тканевых прокладок очищают поверхность ступеней от резины. Концы ленты пропитывают резиновым клеем «АН-4» или «АН-425» для горячей вулканизации. Это действие повторяют 3-4 раза. После подсушки последнего слоя клея концы ленты накладывают один на другой и прокатывают от середины к краям. На стыки верхних и нижних тканевых прокладок накладывают полоски из кордовой ленты пропитанные клеем а сверху посыпают тальком. Стык ленты помещают между электронагревательными плитами вулканизационного аппарата.
До испытания транспортера на холостом ходу подтягивают все болты в картер редуктора заливают масло «Индустриальное-30» в пресс-масленки корпусов подшипников валов и роликоопор набивают солидол «УС-2».
Во время испытания транспортера на холостом ходу проверяют правильность положения ленты по ширине барабанов и роликов (лента ее должна выступать за кромки) вращение всех роликов а также центровку приводной станции.
Перед сдачей в эксплуатацию производится общий осмотр устройств: проверяют правильность размещения отдельных агрегатов фактические отметки мест приема и сброса материала углы образуемые горизонтальными и вертикальными участками с наклонными участками и с самотечными устройствами.
Далее установку испытывают на холостом ходу и проверяют правильность хода конвейерных лент действия сигнализации и средств автоматизации. Устанавливают и отмечают потребление электроэнергии двигателями (мощность холостого хода).
Конвейер испытывают под нагрузкой с проверкой характера загружения транспортирующих органов (профиль материала на ленте коэффициент загрузки и т.п.) работы сбрасывающих и перегрузочных устройств действия сигнализации и средств автоматизации. Вновь устанавливают и отмечают потребление электроэнергии двигателями (мощность рабочего хода).
После завершения монтажа и сдаточных испытаний до ввода в эксплуатацию технический отдел порта регистрирует конвейеры в журнале учета перегрузочных машин.
2 Основные операции проводимые при техническом обслуживании и ремонте конвейера
Целью технического обслуживания перегрузочных машин является поддержание их работоспособности или исправности в период между очередными плановыми ремонтами а также увеличение общего срока службы машин.
Техническое обслуживание перегрузочных машин и устройств подразделяется на следующие виды: техническое обслуживание при использовании (ТО-1); техническое обслуживание при ожидании; техническое обслуживание при хранении; техническое обслуживание при транспортировании; периодическое техническое обслуживание (ТО-2).
В состав технического обслуживания ТО-1 входят следующие работы: осмотрово-проверочные крепежные смазочные регулировочно-наладочные уборочно-моечные опробование механизмов и систем машины в действии проверка в действии блокировочных устройств и приборов безопасности снабжение машины топливом смазочными материалами и охлаждающей жидкостью устранение мелких отказов и повреждений.
Техническое обслуживание ТО-1 проводится без вывода машины из эксплуатации ежесменно и через календарные интервалы времени продолжительностью менее месяца (сутки неделя и т.п.).
Ежесменные работы ТО-1 (ежесменное обслуживание ЕО) выполняются при приеме-сдаче смены и во время технологических перерывов в течение смены.
Ежесуточные еженедельные и другие работы ТО-1 выполняются во время технологических перерывов в течение смены.
В состав технического обслуживания ТО-2 входят две группы работ: обязательные содержащие расширенный комплекс работ технического обслуживания ТО-1; по потребности содержащие ремонтные работы небольшого объема по предупреждению и устранению отказов и повреждений узлов и деталей машины.
Работы по потребности могут включать в себя:
- замену быстроизнашивающихся деталей (резьбовых соединений тормозных обкладок пальцев и упругих втулок соединительных муфт канатов манжет и уплотнений гидросистем контактов соединений и пружин командоаппаратов контакторов и реле щеток и щеткодержателей электродвигателей и кольцевых токоприемников и др.);
- восстановление поврежденных элементов металлоконструкций и их соединений изношенных деталей поврежденных устройств и систем механического электрического гидравлического и пневматического оборудования;
- смену масла в редукторах и других узлах;
- ремонт (модернизацию) отдельных узлов который не может быть отложен до ближайшего планового ремонта машин.
Техническое обслуживание ТО-2 производится по план-графикам утвержденным главным инженером предприятия. Отклонение от сроков выполнения ТО-2 предусмотренных план-графиком допускается в исключительных случаях по согласованию с главным инженером.
Перечень работ выполняемых при ТО-1 и ТО-2 на конкретных машинах устанавливает порт на основании инструкций по эксплуатации.
Техническое обслуживание перегрузочных машин при ожидании производственного использования (в периоды неиспользования менее одного месяца - оперативное хранение) включает ежесуточные и еженедельные работы аналогично ТО-1.
Техническое обслуживание перегрузочных машин при ожидании ими ремонта (до одного месяца) не проводится. В период ожидания ремонта необходимо обеспечить сохранность машины и невозможность доступа в ее кабину и машинное отделение посторонних лиц. При ожидании ремонта более месяца машина считается находящейся на хранении.
Техническое обслуживание перегрузочных машин при хранении (в периоды неиспользования свыше одного месяца - длительное хранение) включает работы выполняемые при подготовке к хранению в процессе хранения и при подготовке к использованию после хранения.
Техническое обслуживание при подготовке перегрузочной машины к хранению включает: очистку машины от грязи и мойку выполнение обязательных работ ТО-2 замер изоляции электрооборудования устранение обнаруженных повреждений (восстановление герметичности кожухов крышек и дверей остекление кабины и машинного отделения и т.п.) консервацию.
Консервация машины производятся в зависимости от конструктивных особенностей машины условий и длительности ее хранения.
Техническое обслуживание в процессе хранения перегрузочной машины производится с месячной периодичностью и включает:
- проверку технического состояния путем внешнего осмотра;
- проверку надежности защиты ее от коррозии;
- устранение выявленных повреждений деталей (узлов) с последующей их консервацией.
Техническое обслуживание при подготовке к использованию после хранения включает: расконсервацию; все работы проводимые при ТО-2; проверку сопротивления изоляции электрического оборудования и при необходимости доведение ее до нормы.
Техническое обслуживание при транспортировании машины (перемещение на новое место использования более суток) включает работы выполняемые при подготовке к транспортированию и подготовке к использованию после транспортирования.
Перечень выполняемых при этом работ аналогичен техническому обслуживанию при хранении. Консервация машины производится только при продолжительности ее транспортирования больше месяца. Необходимость демонтажа отдельных частей машины определяется условиями транспортирования.
Техническое обслуживание проводят портовые рабочие осуществляющие управление машинами и члены ремонтно-наладочных бригад. В объеме ТО-1 ежесменно или ежесуточно проверяют: общее состояние и натяжение тягового элемента состояние приводной и натяжной станций блокировочные или защитные устройства а также выполняют крепежные и уборочно-моечные работы.
В объеме ТО-2 через каждые 250ч работы обязательно диагностируют состояние агрегатов и конвейера в целом оценивают выявленные износы. Особое внимание необходимо обращать на состояние стыков и краев конвейерных лент ограждение движущихся частей. Работы по потребности заключаются в регулировке хода ленты ремонте отдельных элементов машин: лент роликов катков металлоконструкций и др. Время выполнения ТО-2 не должно превышать 1 сутки для передвижных установок и 2 суток для стационарных.
В ремонтный цикл конвейеров входят три текущих и один капитальный ремонты. Продолжительность цикла для конвейеров любых типов согласно правил технической эксплуатации должна быть не менее 48тыс.ч. Так у стационарных конвейеров общего назначения ресурс до первого капитального ремонта 10тыс.ч и до списания 32тыс.ч. Технический надзор за конвейерами ведут как и за другими перегрузочными машинами портов. Основной формой периодического надзора являются технические освидетельствования проводимые ответственным по надзору в присутствии лица ответственного за их поддержание в исправном состоянии. Освидетельствования состоят из визуального контроля и опробований машин вхолостую и под нагрузкой; их проводят в следующие сроки: первичные - перед вводом в эксплуатацию периодические - ежегодно внеочередные - после капитального ремонта или модернизации.
В качестве тяговых элементов конвейеров служат конвейерные ленты. Лента является основным и наиболее дорогим элементом ленточных конвейеров. Ее стоимость составляет 50-60 процентов общей стоимости конвейера а срок службы ленты в 2-3 раза ниже чем для конвейера в целом. Наиболее распространены резинотканевые ленты с прокладками на основе бельтинга или синтетического волокна. Ленты подвержены абразивному изнашиванию при взаимодействии с грузом при проскальзывании относительно тяговых поддерживающих и отклоняющих устройств при трении о детали ограждения в случае бокового смещения превышающего допустимую норму.
На практике регулировку хода конвейерной ленты осуществляют следующим образом. На участке конвейера предшествующем началу неустойчивого движения поворачивают одну или несколько роликоопор. Конец роликоопоры противоположный направлению первоначального смешения ленты поворачивают на 1-3° в сторону противоположную направлению ее движения. Максимальное боковое смещение ленты допускается не более 50мм на следующем этапе проверяют ход ленты с номинальным грузом. Если неустойчивость движения появилась снова необходимо выяснить причину возникновения возмущающей силы. Особое внимание нужно обратить на симметричность загрузки ленты качество очистки ленты оказывает большое влияние на долговечность ее обкладок. Частицы груза попадая между роликами барабаном и лентой вызывают интенсивное ее изнашивание. Ремонт ленты сводится к восстановлению стыков за счет запаса ленты в натяжном устройстве или замене изношенных участков различными методами.
Хранят конвейерные ленты намотанными на деревянные катушки или бобины в подвешенном состоянии при температуре 10-20°С в местах исключающих воздействие прямых солнечных лучей.
Основным требованием предъявляемым к роликам и неприводным барабанам является легкость их вращения. При затрудненном вращении или остановке в результате абразивного действия ленты изменяется форма рабочей поверхности: образуются задиры возникает огранка.
В этом случае целесообразно ежедневно определенную часть роликов заменять резервными а снятые - направлять на обслуживание и в ремонт.
При ремонте для исправления формы допускается применять проточку наружных поверхностей если она не вызовет недопустимого снижения прочности стенок. После обработки радиальное биение нефутерованных барабанов в зависимости от диаметра не должно превышать 15-25мм а роликов - 1-15 процента диаметра. Предельное состояние роликоопоры наступает при увеличении радиального зазора в подшипниковом узле до 02мм и износе стенки ролика до толщины 05мм.
Для грузовых натяжных устройств значительное техническое обслуживание не требуется. При обслуживании конвейера необходимо убедиться в том что подвижная каретка свободно перемещается в направляющих отклоняющие блоки проворачиваются от руки поддерживающие канаты не повреждены коррозией ограждения грузового колодца исправны.
Очень важна тщательная очистка ленты. Хотя существуют различные способы и конструктивные решения очистки полностью ликвидировать просыпание и налипание груза на ленту не удается.
В настоящее время наиболее часто применяют скребковые очистные устройства. От резиновых полос скребков в месте контакта лента изнашивается. Поэтому важно чтобы твердость резины этих полос была меньше чем твердость обкладок ленты. По мере изнашивания полосы заменяют.
При непрерывной загрузке конвейера через пересыпную станцию в случае его остановки возможно образование завала. Поэтому при техническом обслуживании контролируют блокировочные устройства отключающие питающий конвейер.
Во избежание просыпания груза необходимо также следить за состоянием бортовых ограждений загрузочной зоны.
Основное требование к работе сбрасывающих устройств заключается в уменьшении загрязнения окружающей среды.
1ОБЩ ХАР-КА ПРЕДП.doc
1История возникновения порта
К началу XX-го века Россия располагала всего лишь двумя портами на северо-западе через которые проходили торговые пути со странами Западной Европы - это Санкт-Петербург и Архангельск. Наиболее дальновидные государственные деятели того времени прекрасно понимали что для развития экономики страны этого явно недостаточно так как Архангельский порт открыт для захода судов лишь семь месяцев в году и его пропускная способность незначительна а замерзающий зимой Финский залив требовал ледокольной проводки судов.
Вступление России в августе 1914 года в войну подтвердило самые наихудшие опасения когда черноморские порты и Санкт-Петербург оказались блокированными противником а с наступлением зимы прекратилась навигация в Архангельске. Единственным выходом было срочное строительство нового порта на севере России. В конце июня – начале июля 1915 года были проведены первые плановые работы на территории будущего порта а уже 1 сентября того же года к временной пристани ошвартовался первый пароход «Дротт» с грузом из Нью-Йорка. Таким образом 1 сентября можно считать днем рождения Мурманского порта. Меньше чем за год был построен участок железной дороги до Кандалакши и по нему пошли первые поезда. В некотором смысле можно сказать что в те годы было «прорублено второе окно в Европу».
Время подтвердило правильность выбора. Благодаря теплому течению Гольфстрим климатические условия в этой части Кольского полуострова относительно мягкие - залив не замерзает даже в суровые зимы что дает возможность осуществлять круглогодичную навигацию без ледовой проводки. Ширина Кольского залива и глубины фарватера позволяют заходить и становиться на якорную стоянку практически любым судам - без ограничений по длине или осадке.
Именно благодаря наличию порта и железной дороги Россия получила возможность освоения природных богатств Кольского полуострова на трассу Северного морского пути и к архипелагу Шпицберген.
После начала Второй мировой войны через порт шли грузы на Испанию а в годы Великой Отечественной войны порт принимал и разгружал караваны судов стран-союзников. В послевоенные годы порт интенсивно развивался. Строились новые причалы подъездные пути и перегрузочные комплексы в порту появлялась новая техника совершенствовалась технология работ.
Широкомасштабное освоение природных богатств Кольского полуострова и регионов Крайнего Севера России которое происходило в то время требовало надежного транспортного обеспечения. И порт всегда успешно справлялся с этой задачей.
2 Характеристика порта
Мурманский морской торговый порт расположен в южной части Кольского залива на расстоянии 22миль от Баренцева моря. Координаты: 68° 58' северной широты; 33°05' восточной долготы. Навигация в порту осуществляется круглосуточно и круглогодично. Примерно каждые шесть часов происходит смена приливов и отливов. Разница в уровне воды между ними составляет 366м. Залив незамерзающий но в особо суровые зимы на короткое время может покрываться льдом; в обычные зимы наблюдается дрейфующий лед. Глубины на рейде - от 20 до 60м. Скорость приливных течений может достигать 25 узлов. В зависимости от приливов и отливов плотность воды в заливе периодически изменяется в пределах 1000 - 1025. Мурманский морской торговый порт - единственный порт на северо-западе России имеющий возможность обрабатывать суда дедвейтом свыше 130000т.
Мурманский порт разделен на три грузовых района. 1-й и 2-й грузовой районы осуществляют перегрузку и хранение генеральных навалочных грузов и грузов в контейнерах. 3-й грузовой район производит хранение и перегрузку на суда апатитового концентрата навалом при помощи спецустановки конвейерного типа.
-цветные металлы и сплавы в пакетах (алюминий медь никель);
-прокат черных металлов;
-апатитовый концентрат навалом;
-металлолом и железорудные окатыши навалом;
-продукция химической промышленности в мешках и биг-бегах;
-строительные материалы;
-продовольственные грузы;
-технологическое оборудование в ящиках и без упаковки;
-различные грузы в контейнерах ИСО-20 и ИСО-40 (в том числе рефрижераторные) МПС и др.
В 2009 году грузооборот компании составил 15118227т обработано 510 судов в том числе с углем – 222 с апатитовым концентратом - 91. Погрузка-выгрузка вагонов составила 211057 вагонов в том числе 174712 вагонов с углем 26891 вагон с апатитовым концентратом.
-апатитовый концентрат - 1671593т;
-цветные металлы - 391 989т.
Доля экспортных грузов составила 958% от общего объема грузооборота акционерного общества импорта - 08% каботажных грузов - 34 % .
Особое место занимает перевалка угля. Мурманский морской торговый порт является крупнейшим и практически единственным крупным перевалочным пунктом угля в Северном морском бассейне. Через Мурманский порт сейчас экспортируется больше угля чем через порты Санкт-Петербург Кандалакша Выборг и Высоцк вместе взятые.
Основное направление экспорта – это страны Западной Европы в частности: Испания Нидерланды Бельгия Франция Великобритания и другие.
Заключение.doc
В рамках подготовки настоящего дипломного проекта были рассмотрены следующие вопросы: определен грузооборот причала вместимость склада интенсивность обработки транспортных средств разработаны два варианта схем механизации специализированного комплекса по перегрузке минеральных удобрений и рассчитаны экономические показатели этих двух схем.
В проекте произведен расчет эксплуатационных расходов по перегрузочным работам для конвейерной схемы механизации и крановой а также установлены сроки окупаемости конвейерного перегрузочного комплекса который составил и кранового - .Из вышеперечисленных показателей видно преимущество конвейерной схемы механизации над крановой. Следовательно для перегрузки минеральных удобрений оптимальной является конвейерная схема механизации.
Для загрузки судопогрузочной машины используется причальный ленточный конвейер. Расчет причального конвейера обуславливает технические характеристики судопогрузочной машины. Для обеспечения требуемой интенсивности погрузки производительность судопогрузочной машины должна быть равна производительности причального конвейера. Технические данные причального конвейера следующие: производительность тч ширина ленты =650мм скорость ленты диметр приводного барабана =500мм натяжного - диаметр желобчатой роликоопоры =89мм мощность привода =15кВт для соединения вала двигателя с быстроходным валом редуктора используем упругую втулочно-пальцевую муфту. Технические данные судопогрузочной машины: производительность тч ширина ленты конвейера =650мм диаметр приводного барабана =500мм диаметр желобчатой роликоопоры =89мм мощность привода конвейера =15кВт скорость подъема галереи мощность привода механизма подъема галереи =45кВт скорость передвижения судопогрузочной машины мощность привода механизма передвижения =75кВт скорость изменения вылета телескопического конвейера мощность привода =22кВт.
В расчет судопогрузочной машины входят следующие разделы: расчет телескопического конвейера расчет механизма передвижения и механизма подъема галереи. Также в проект входят расчеты шариковой винтовой пары по средствам которой обеспечивается изменение вылета телескопического конвейера и расчет металлоконструкции галереи.
Помимо этого в работе рассмотрены требования охраны труда и экологической безопасности при эксплуатации и обслуживании специализированного конвейерного комплекса и конвейеров в частности также описаны техническое обслуживание и монтаж конвейеров.
Анализ основных вопросов позволяет сделать вывод о том что невозможно обеспечить устойчивый ритм производства на современной ступени его интенсификации без согласованной и безотказной работы подъемно-транспортных машин. Поэтому для повышения надежности работы перегрузочного комплекса необходимо как минимум две фронтальные машины чтоб обеспечить беспрерывность работы при выходе из строя одной из них.
При правильном и качественном расчете полученные данные можно стандартизировать и унифицировать тем самым получить каталог основных размеров для подбора взаимозаменяемых деталей при выходе их из строя что в свою очередь ведет к снижению простоя машин и перегрузочного комплекса в целом.
Рассчитанный перегрузочный комплекс обеспечивает прогрессивную бесперебойную перегрузку минеральных удобрений в порту с минимальными эксплуатационными расходами и малыми затратами по времени.
Титульный лист.doc
Федеральное государственное образовательное учреждение
высшего профессионального образования
САНКТ-ПЕТЕРБУРГСКИЙ ГОСУДАРСТВЕННЫЙ УНИВЕРСИТЕТ ВОДНЫХ КОММУНИКАЦИЙ
Кафедра Портовой подъемно-транспортной техники и гидротехнического строительства
На тему «Проект комплекса по перегрузке минеральных удобрений в Мурманском морском торговом порту»
ПОЯСНИТЕЛЬНАЯ ЗАПИСКА
Исполнитель: Смирнов Алексей Анатольевич
Руководитель: ст. преподаватель кафедры ППТТиГС
Консультант: ст. преподаватель кафедры ППТТиГС
Консультант: преподаватель кафедры ППТТиГС
Консультант: к.т.н. доцент кафедры ППТТиГС
(ученая степень звание)
9 ОПИСАНИЕ РАБОТЫ ЭЛЕКТРОСХЕМЫ.doc
ЛЕНТОЧНОГО КОНВЕЙЕРА
Принципиальная схема отображена на чертеже 12.
Коммутация первичных цепей электродвигателей конвейера осуществляется двумя индивидуальными масляными выключателями QF2 и QF3 третий общий масляный выключатель QF1 обеспечивает одновременную подачу напряжения на статорные обмотки двигателей М1 и М2 после включения индивидуальных масляных выключателей QF2 и QF3.
Порядок запуска ленточного конвейера следующий. Перед запуском двигателей включаются вспомогательные механизмы (маслосмазка и натяжение конвейерной ленты). Включение привода натяжной лебедки вызывает срабатывание реле натяжения ленты и замыкание его контакта КНЛ в цепи питания реле времени КТ1-КТ6. Далее включаются автоматы цепей управления SА1 SА2 и SАЗ. Включение автомата SА1 приводит к появлению тока в катушке реле времени КТ1 что вызывает его срабатывание и замыкание контакта КТ1.1 в цепи катушки реле времени КТ2. Это в свою очередь приводит к его включению и так до тех пор пока все реле времени не включатся. Все реле времени включившись замыкают контакты КТ1.2 - КТ6.2 и размыкают контакты КТ1 - КТ6.3.
Для запуска двигателей сначала включаются масляные выключатели QF2 и QF3 что приводит к замыканию их контактов QF2 и QF3 в цепях питания контакторов ускорения КМ1 и КМ2. Затем включается масляный выключатель QF1.
Двигатели М1 и М2 получив питание приходят во вращение при полностью включенном сопротивлении пускового резистора. Эта ступень называется предварительной и предназначена для выбора зазоров в передаче и слабины тягового органа. Одновременно с включением масляного выключателя QF1 размыкается его контакт QF1 вызывая обесточивание первого реле времени KT1. Оно с выдержкой времени необходимой для выбора зазоров в передаче и слабины тягового органа замыкает свои контакты KT1.2 и КТ1.3 в цепях катушек контакторов ускорения КМ1.1 и КМ2.1 и размыкает свой контакт КТ1.1 в цепи второго реле времени КТ2. Контакторы ускорения КМ1.1 и КМ2.1 включившись замыкают свои главные контакты КМ1.1 и КМ2.1 шунтирующие первую ступень пускового резистора а размыкающие блок-контакты КМ1.1 и КМ2.1 размыкаются и замыкающие блок-контакты КМ1.1 и КМ2.1 замыкаются.
Переход на вторую пусковую ступень сопровождается бросками токов в двигателях вызывающих включение реле тока КA1 и КА2. Замкнувшиеся контакты КА1 и КА2 этих реле вновь подключают реле времени КТ2 к источнику тока. И только тогда когда токи двигателей М1 и М2 снизятся до значений соответствующих моментам переключений на вторую пусковую ступень контакты реле KA1 и КА2 разомкнутся и разорвут цепь питания катушки КТ2. Реле времени обесточившись замыкает свои контакты КТ2.2 и КТ2.3 вызывая включение контакторов ускорения КМ1.2 и КМ2.2 и размыкает контакт КТ2.1 обесточивая реле времени третьей ступени пускового резистора КТЗ. Но шунтирование второй пусковой ступени резистора контактами КМ1.2 и КМ2.2 вызывает вновь увеличение токов двигателей и включение реле тока КА1 и КА2.
Замыкание их контактов а также контактов КМ1.2 и КМ2.2 создает цепь для питания реле времени КТ3: автомат SA1 - контакт КНЛ - диод VD- катушка реле КТЗ - контакт КМ1.3 (или КМ2.3) - контакты КМ2.2 KM1.2 КМ2.1 КМ1.1 КА1 (или КА2). По мере увеличения частоты вращения двигателей их токи снижаются и при моментах соответствующих моментам переключения контакты токовых реле КА1 и КА2 размыкаются и реле времени КТЗ обесточившись замыкает свои контакты КТ3.2 и КТ3.3 вызывая включение контакторов ускорения КМ1.3 и КМ2.3 и шунтирование третьей ступени пускового резистора.
Аналогично идет процесс шунтирования пусковых ступеней до замыкания последних контактов КМ 1.6 и КМ 2.6 когда двигатели начинают работать на естественных механических характеристиках. К этому моменту все реле времени КТ1-КТ6 и контакторы ускорения КМ1.1 - КМ1.5 и КМ2.1 - КМ2.5 обесточены.
2Механизация и технология перегрузочных.doc
1 Технология перегрузки минеральных удобрений
Минеральные удобрения относятся к навалочным грузам изменяющим свои под влиянием влаги склонным к пылению при перегрузке и поэтому требуют крытого способа хранения транспортировки и перегрузки. Для их транспортировки используют специальные вагоны-хопперы.
Конструкция вагона позволяет производить загрузочные работы механизированным способом через четыре расположенные по оси крыши щелевых загрузочных люка обеспечивающих равномерную загрузку кузова с одной установки. В нижней части кузова по обеим сторонам вагона расположены по два разгрузочных люка. Механизм разгрузки с пневмоприводом обеспечивает как парное открывание и закрывание крышек люков так и одновременное - всех четырех. Специальное блокирующее устройство предотвращает самопроизвольное открывание крышек разгрузочных люков как в пути следовании так и на стоянке.
Хранение минеральных удобрений осуществляется в герметичном крытом складе а перегрузка по герметизированным конвейерным трассам с использованием систем пылеулавливания и локализации распространения пыли.
Пылящие навалочные грузы при переходе из состояния покоя в состояние пересыпания изменяют свою пористость. При этом увеличение порового пространства определяет подсос воздуха а уменьшение при укладке приводит к выделению воздуха с одновременным захватом пылевидных фракций. Учитывая эту особенность необходимо использовать системы локализации замкнутого типа. Система обеспыливания узла переброски груза с одного транспортера на другой и пылеподавляющая насадка для загрузки судов с рециркуляцией воздуха при подсосе и выбросе в струе перегружаемого материала приведена на рисунке 2.1. В пылеподавляющей насадке для загрузки судов система конусов-воронок гасит кинетическую энергию подающей струи а вытесняемый воздух возвращается к месту подсоса в материал в начале падения.
где а - при загрузке трюма;
б - при сбросе с одного транспортера на другой.
Рисунок 2.1 - Системы обеспыливания узлов сброса пылевидных навалочных грузов
Для разгрузки вагонов с минеральными удобрениями используют специализированную вагоноразгрузочную установку которая не только предотвращает попадание влаги на груз и распространение пыли на перегрузочном терминале но и повышают производительность обработки железнодорожных вагонов.
2 Грузовые операции внутри терминала
Перегрузочный комплекс (далее ПК) предназначен для выгрузки минеральных удобрений из железнодорожных вагонов кратковременного хранения груза и погрузки его в суда.
В качестве средств транспортировки минеральных удобрений внутри предприятия приняты ленточные конвейеры с желобчатой роликоопрой. Конвейеры оборудованы целым рядом устройств и приспособлений обеспечивающих надежную и безопасную работу ПК. Сюда относятся приборы контроля схода ленты датчики завалов в узлах переброса с конвейера на конвейер и т.п. Взвешивание груза производится при помощи конвейерных весов.
Технологией предусмотрена работа по вариантам:
Прибывшие вагоны в маршрутах остаются на предпортовой станции откуда локомотив по 15 единиц подает их в порт и устанавливает на технологические железнодорожные пути расположенные рядом с узлом разгрузки вагонов (далее УРВ). На территории порта подача вагонов в УРВ осуществляется маневровым локомотивом. УРВ предназначен для выгрузки вагонов минералловозов и представляет собой 2-х этажное здание. Вагоны в количестве 15 единиц подаются с торцевой стороны здания узла разгрузки по одной железнодорожной линии. УРВ рассчитан на одновременную разгрузку 15 вагонов. Порожние вагоны выводятся локомотивом из УРВ и устанавливаются на технологические железнодорожные пути расположенные рядом со зданием узла разгрузки. Под железнодорожной линией УРВ расположены приемные бункеры. На 1-ом этаже здания под бункерами установлены ленточные питатели предназначенные для равномерной подачи груза из бункеров на магистральные конвейеры транспортирующие минеральные удобрения или в узел погрузки судов (по прямому варианту) или на склад.
Узел погрузки судов включает в себя две погрузочные машины и береговую погрузочную галерею в которой расположены ленточные конвейеры подающие груз на машины для загрузки судна.
Погрузочная машина представляет собой металлоконструкцию портального типа передвигающуюся по рельсам вдоль причала. К порталу шарнирно прикреплена подъемная галерея с установленным в ней телескопическим ленточным конвейером и специальной телескопической трубой через которую происходит сброс груза в трюм судна. Управление работой машины происходит из кабины управления.
В береговой погрузочной галерее минеральные удобрения с конвейеров при помощи двух самоходных сбрасывающих тележек двигающихся по специальным рельсовым путям передаются на погрузочные машины на одну из которых груз со сбрасывающей тележки попадает через отвальный конвейер. Передача груза с конвейеров на погрузочные машины осуществляется через сквозную непрерывную щель предусмотренную конструкцией галереи и имеющую по всей длине укрытие из резиновой ткани.
Для кратковременного хранения минеральных удобрений предусмотрены 3 склада выполненные в виде зданий купольного типа. Диаметр каждого склада 55м высота - 20м емкость каждого - 20000т. Загрузка осуществляется с верхней отметки посредине склада ленточными конвейерами. В нижней части каждого склада расположены по одному ленточному конвейеру с установленными над ними бункерами. С помощью этого оборудования осуществляется самовыгрузка приблизительно 70% груза. Оставшаяся часть груза (приблизительно 30%) перегружается с помощью ковшовых погрузчиков.
Разработанная технология перегрузочных работ обеспечивает эксплуатацию комплекса без отрицательного воздействия на окружающую среду.
Библа.doc
ГОСТ 12.1.005-98 - Система стандартов безопасности труда. Общие санитарно-гигиенические требования к воздуху рабочей зоны.
ГОСТ 12.1.007-06 - Система стандартов безопасности труда. Вредные вещества. Классификация и общие требования безопасности установленные предельно допустимые концентрации пыли в воздухе рабочей зоны в мгм3.
ГОСТ 12.2.022-80 - Конвейеры. Общие требования безопасности.
ГОСТ 12.3.009-06 - Система стандартов безопасности труда. Работы погрузочно-разгрузочные. Общие требования безопасности.
ГОСТ 1412-85 - Чугун с пластинчатым графитом для отливок.
ГОСТ 1451-77 - Краны грузоподъемные. Нагрузка ветровая.
ГОСТ 20-85 - Ленты конвейерные резинотканевые. Технические условия.
ГОСТ 20373-80 - Редукторы и мотор-редукторы. Варианты сборки.
ГОСТ 21424-93 - Муфты упругие втулочно-пальцевые. Основные параметры. Габаритные и присоединительные размеры.
ГОСТ 22644-77 - Конвейеры ленточные. Основные параметры и размеры.
ГОСТ 22645-77 - Конвейеры ленточные. Роликоопоры. Типы и основные размеры.
ГОСТ 2479-79 - Машины электрические вращающиеся. Условные обозначения.
ГОСТ 2688-80 - Канаты стальные. Сортамент.
ГОСТ 28648-90 - Колеса крановые. Технические условия.
ГОСТ 6368-82 - Рельсы железнодорожные узкой колеи типов Р-8 Р-11 Р-18 и Р-24. Конструкция и размеры.
ГОСТ 7174-75 - Рельсы железнодорожные типа Р-50. Конструкция и размеры.
ГОСТ 8324-71 - Конвейеры роликовые стационарные неприводные общего назначения.
ГОСТ 8338-75 - Шарикоподшипники радиальные.
ГОСТ 8509-93 - Уголки стальные горячекатаные равнополочные. Сортамент
ГОСТ 8732-78 - Трубы стальные бесшовные горячедеформированные.
ОСТ 24.848.04-79 - Полумуфты тормозные к муфтам упругим втулочно-пальцевым. Конструкция.
ПБ 10-382-00 - Правила устройства и безопасной эксплуатации грузоподъемных кранов.
ППБ 01-03 - Правила пожарной безопасности в РФ.
РД 24.090.97-98 - Оборудование подъёмно-транспортное. Требования к изготовлению ремонту и реконструкции металлоконструкций грузоподъемных кранов.
РД 31.1.02-04 – Правила технической эксплуатации подъемно-транспортного оборудования морских торговых портов.
РД 31.3.05-97 – Нормы технологического проектирования морских портов.
РД 31.44.01-97 – Правила технической эксплуатации подъемно-транспортного оборудования морских торговых портов.
СН 2.2.42.1.8.562-06 – Шум на рабочих местах в помещениях жилых общественных зданий и на территории жилой застройки.
СНиП 23-05-05 – Естественное и искусственное освещение.
Андрианов Е.Н. Металлические конструкции ПТМ [Текст]: метод. указания по курсовому проектированию металлических конструкций ПТМЕ.Н. Андрианов. – СПб.: СПГУВК 2004. – 51с.
Анурьев В.И. Справочник конструктора-машиностроителя. Т2 [в 3-х т.] [Текст]В.И. Анурьев. Под ред. И.Н. Жестковой. – Изд. 8-е перераб. и доп. – М.: Машиностроение 2001. – 912с.; ил.
Бондаровский Ф.П. Корнеев Г.В. Детали машин и подъемно-транспортные машины [Текст]: учеб. пособие для ВУЗовФ.П. Бондаровский Г.В. Корнеев. – М.: Машгиз 1958. – 520с.
Грузовые вагоны колеи 1520мм железных дорог СССР [Текст]: альбом-справочникМинистерство путей сообщения СССР главное управление вагонного хозяйства. – М.: Транспорт 1989. – 176с.
Грузоподъемные машины [Текст]: учеб. пособие для ВУЗовМ.П. Александров Л.Н. Колобов И.П. Крутиков Н.А. Лобов и др.; Под ред. М.П. Александрова. – М.: Высш. шк. 1973. – 473с.; ил.
Давыдов И.В. Смрковский Э.В. Электрооборудование подъемно-транспортных машин [Текст]: учебник для ВУЗовИ.В. Давыдов Э.В. Смрковский. – М.: Транспорт 1991. – 294с.
Евневич А.В. Грузоподъемные и транспортирующие машины на заводах строительных материалов [Текст]: уч. для техникумовА.В. Евневич. – Изд. 3-е перераб. – М.: Машгиз 1962. – 351с.
Зенков Р.Л. Машины непрерывного транспорта. - М.: Машиностроение 1987. - 432с.
Казак А.П. Технология и организация перегрузочных работ на речном транспорте [Текст]: учеб. для ВУЗовА.П. Казак. - 3-е изд. перераб. и доп. – М.: Транспорт 1984. – 416с.
Конвейеры. Справочник. Под. ред. Ю.А. Пертена. - Л.: Машиностроение 1984. - 367с.
Кузьмин А. В. Справочник по расчетам механизмов подъемно-транспортных машин. - Минск: Вышейшая школа 1983. -350с.
Курмаз Л. В. Детали машин. Проектирование: учебн. пособиеЛ. В. Курмаз А. Т. Скойбеда. - 2-е изд. испр. и доп. - Мн.: УП «Технопринт» 2002. - 290с.
Курсовое проектирование грузоподъемных машин: Учеб. пособие для студентов машиностр. спец. вузовС.А. Казак В.Е. Дусье Е.С. Кузнецов и др.; Под ред. С.А. Казака.– М.: Высш. шк. 1989.– 319с.: ил.
Курсовое проектирование деталей машин [Текст]: учеб. пособие для техникумовГ.М. Ицкович В.А. Киселев С.А. Чернавский К.Н. Боков Б.Б. Панич. – Изд. 6-е перераб. – М.: Машиностроение 1970. – 560с.
Макаров В.С. Перегрузочные комплексы и гидрокомплексы. Ч1 [в 2-х ч.]. Перегрузочные комплексы [Текст]: метод. указания по выполнению курсовой работыВ.С. Макаров. – СПб.: СПГУВК 2004. – 48с.
Макаров В.С. Технология и механизация перегрузочных работ: справочные материалы и нормативы технологического проектирования перегрузочных процессовМакаров В.С. – СПб.:СПГУВК 2006. – 59с.
Матвеев В.В. Примеры расчета такелажной оснастки: Учеб. пособие для учащихся монтажных техникумов. - изд. 3-е перераб. и доп. - Л.: Стройиздат 1979. - 240с. ил.
Ромакин Н.Е. Машины непрерывного транспорта.- М.: Академия 2008. - 432с. ил.
Руденко Н.Ф. Александров М.П. Лысяков А.Г. Курсовое проектирование грузоподъемных машин [Текст]: учеб. пособие для ВТУЗовН.Ф. Руденко М.П. Александров А.Г. Лысяков. – Изд. 2-е перераб. и доп. – М.: Машиностроение 1966. – 331с.
Спиваковский А.О. Дьячков В.К. Транспортирующие машины – Изд. 2-е перераб. и доп. – М.: Машиностроение 1968. – 504 с.
Справочник по кранам. Характеристики материалов и нагрузок. Основы расчета кранов их приводов и металлических конструкций. Т1 [в 2 т.] [Текст]В.И. Брауде М.М. Гохберг И.Е. Звягин и др.; Под общ. ред. М.М. Гохберга. – Л.: Машиностроение 1988. – 536с.; ил.
Справочник по кранам. Характеристики и конструктивные схемы их детали и узлы. Техническая эксплуатация кранов. Т2 [в 2 т.] [Текст]М.П. Александров М.М. Гохберг А.А. Ковин и др.; Под общ. ред. М.М. Гохберга. – Л.: Машиностроение 1988. – 559с.; ил.
Эрдеди А.А. Эрдеди Н.А. Детали машин [Текст]: учеб. для машиностр. спец. сред. проф. учеб. заведенийА.А. Эрдеди Н.А. Эрдеди. – 2-е изд. испр. и доп. – М.: Высш. шк. 2002. – 285с.; ил.
8Расчет фермы.doc
1 Определение геометрических параметров галереи
Подъемная галерея выполнена в виде стержня сквозного сечения (фермы).
Определим расстояние между жесткой и гибкой опорами стержня м по формуле:
где - длина фермы ().
Определим высоту стойки м по формуле:
Т.к. по конструктивным соображениям угол наклона раскосов принимают примерно равным 45º то длина панели будет равна высоте стойки .
Определим длину раскосов м по формуле:
Определим ширину стержня м по формуле:
Таким образом был проведен расчет геометрических параметров подъемной галереи.
2 Определение расчетных нагрузок на галерею и построение эпюр
изгибающих моментов и поперечных сил
Вес разгрузочной трубы принимаем .
Определим распределенную нагрузку на ферму от массы конвейера кНм по формуле:
где 15 - коэффициент неучтенных масс участка конвейера;
- распределенная масса груза приходящаяся на метр длины конвейерной ленты ();
- распределенная масса конвейерной ленты ( );
- распределенная масса вращающихся частей роликовых опор рабочей ветви ( кгм);
- распределенная масса вращающихся частей роликовых опор холостой ветви (кгм);
Определим распределенную нагрузку на ферму от собственного веса кНм по формуле:
Определим суммарную нагрузку кНм по формуле:
На рисунке 8.1 показана расчетная схема стержня и эпюры изгибающих моментов и поперечных сил.
Определим опорные реакции и по формулам:
Определим поперечную силу в сечении A по формуле:
Определим поперечную силу левее опоры B по формуле:
Определим поперечную силу правее опоры B по формуле:
Определим поперечную силу в точке С по формуле:
Рисунок 8.1 - Эпюры M и Q
Определим максимальный изгибающий момент между точками A и B по формуле:
Для определения между точками A и B находим при котором :
Определим изгибающий момент в сечении B по формуле:
Таким образом произвели расчет данных для построения эпюр изгибающих моментов и поперечных сил.
3 Расчет металлоконструкции галереи на гибкость
В качестве материала для изготовления ферменной металлоконструкции выбираем сталь 09Г2С расчетное сопротивление при сжатии которой составляет .
Определим сжимающее усилие от действия гибкой оттяжки по формуле:
где - угол наклона гибкой оттяжки ().
Определим необходимую площадь поперечного сечения стержня по формуле:
где - коэффициент продольного изгиба стержня () [Матвеев с.18];
- коэффициент условий работы () [46 с.18].
По необходимой площади поперечного сечения стержня выбираем уголок равнополочный № 4 (40х40х5мм)[19] имеющий радиус инерции площадь сечения уголка момент инерции .
Определим момент инерции стержня относительно оси х по формуле:
где - расстояние от оси центра тяжести до внешней стороны полки уголка () [46 с.213 приложение 4]
Определим момент инерции стержня относительно оси y по формуле:
Определим радиус инерции стержня относительно оси х по формуле:
Определим радиус инерции стержня относительно оси у по формуле:
Определим гибкость стержня относительно свободной оси х по формуле:
Определим гибкость стержня относительно свободной оси у по формуле:
Определим гибкость раскоса по формуле:
Определим гибкость стойки по формуле:
Определим приведенную гибкость стержня по формуле:
где - коэффициент зависящий от угла наклона раскоса () [46 с. 21];
- площадь поперечного сечения раскоса ().
- предельная гибкость элемента фермы () [46 с. 234 приложение 22].
Гибкость раскосов стоек а также стержня в целом обеспечена.
Определим допускаемый прогиб консольного участка стержня по формуле:
Определим прогиб консольной части стержня по формуле:
где - модуль упругости ().
Прочность консольного участка стержня обеспечена.
4 Проверка стоек и раскосов на устойчивость
Определим условную поперечную силу по формуле:
Определим сжимающее усилие в одном уголке стойки по формуле:
Проверим стойку на устойчивость по формуле:
где - коэффициент продольного изгиба стойки () [46 с. 229 приложение 19].
Определим сжимающее усилие в одном уголке раскоса по формуле:
Проверим раскос на устойчивость по формуле:
где - коэффициент продольного изгиба раскоса () [46 с. 229 приложение 19].
Устойчивость раскосов и стоек обеспечена.
5 Проверка сварных швов стоек и раскосов
Проверим прочность шва стойки по формуле:
где - коэффициент учитывающий глубину провара () [46 с. 26];
- толщина углового шва ();
- длина углового шва ();
- сопротивление сварного углового шва () [46 с. 228 приложение 17].
Проверим прочность шва раскоса по формуле:
Прочность сварных швов стоек и раскосов обеспечена.
Содержание.doc
1 История возникновения порта .10
2 Характеристика порта .. .11
МЕХАНИЗАЦИЯ И ТЕХНОЛОГИЯ ПЕРЕГРУЗОЧНЫХ РАБОТ ..14
1 Технология перегрузки минеральных удобрений .14
2 Грузовые операции внутри терминала 15
АНАЛИЗ ИСХОДНЫХ ДАННЫХ ..18
1Определение грузооборота причала .18
2 Краткая характеристика минеральных удобрений 19
3 Определение грузовой обработки транспортных средств 22
4 Определение расчетной вместимости склада 23
5 Определение расчетной интенсивности обработки транспортных
РАЗРАБОТКА ВАРИАНТОВ СХЕМ МЕХАНИЗАЦИИ ..29
1 Разработка конвейерной схемы механизации 29
2 Разработка крановой схемы механизации ..38
РАСЧЕТ ПРИЧАЛЬНОГО ЛЕНТОЧНОГО КОНВЕЙЕРА 49
1 Расчет класса использования конвейера расчет и выбор ленты .49
2 Расчет и выбор поддерживающих устройств .52
3 Подробный тяговый расчет конвейера 54
4 Расчет электродвигателя редуктора муфты и тормозного
5 Расчет натяжного устройства ..60
РАСЧЕТ СУДОПОГРУЗОЧНОЙ МАШИНЫ 64
1 Описание судопогрузочной машины ..64
2 Расчет телескопического ленточного конвейера 66
2.1 Расчет класса использования конвейера расчет и выбор
2.2 Расчет и выбор поддерживающих устройств 70
2.3 Подробный тяговый расчет конвейера ..72
2.4 Расчет мощности электродвигателя ..75
2.5 Расчет натяжного устройства .77
3 расчет механизма подъема галереи .81
3.1 Расчет ветровой нагрузки на галерею 81
3.2 Подбор каната ..82
3.3 Расчет геометрических параметров блока .83
3.4 Расчет мощности электродвигателя и выбор тормоза .85
4 Расчет механизма передвижения судопогрузочной машины 87
4.1 Расчет ветровой нагрузки на судопогрузочную машину .87
4.2 Определение сопротивления передвижению
судопогрузочной машины 88
4.3 Расчет мощности электродвигателя 91
4.4 Выбор тормоза .93
РАСЧЕТ ШАРИКОЙ ВИНТОВОЙ ПАРЫ .95
1 Определение сопротивления передвижению сбрасывающей
2 Выбор типоразмера шариковой винтовой пары 98
3 Расчет на статическую прочность Расчет на динамическую
4 Расчет коэффициента полезного действия шариковой винтовой
5 Расчет геометрии профиля резьбы 103
6 Расчет стержня винта на прочность ..107
7 Расчет мощности электродвигателя ..108
8 Выбор тормоза .109
РАСЧЕТ МЕТАЛЛОКОНСТРУКЦИИ ГАЛЕРЕИ 111
1 Определение геометрических параметров галереи .111
2 Определение расчетных нагрузок на галерею и построение эпюр
изгибающих моментов и поперечных сил 112
3 Расчет металлоконструкции галереи на гибкость 115
4 Проверка стоек и раскосов на устойчивость 118
5 Проверка сварных швов стоек и раскосов 119
ОПИСАНИЕ РАБОТЫ ЭЛЕКТРОСХЕМЫ ПРИВОДА ЛЕНТОЧНОГО
ТЕХНОЛОГИЯ ИЗГОТОВЛЕНИЯ РОЛИКООПОР ..123
ТЕХНИЧЕСКОЕ ОБСЛУЖИВАНИЕ И МОНТАЖ КОНВЕЙЕРА ..125
1 Основные требования предъявляемые к монтажу конвейера .125
2 Основные операции проводимые при техническом
обслуживании и ремонте конвейера 128
ОХРАНА ТРУДА И ЭКОЛОГИЧЕСКАЯ БЕЗОПАСНОСТЬ ПРИ
ЭКСПЛУАТАЦИИ КОНВЕЙЕРОВ ..134
1 Безопасность труда при эксплуатации конвейеров 134
2 Безопасность труда при эксплуатации специализированного
конвейерного комплекса для навалочных грузов ..136
3 Экологическая безопасность при эксплуатации конвейеров 137
БИБЛИОГРАФИЧЕСКИЙ СПИСОК 141
Введение.doc
В связи с разработкой нового месторождения апатитового концентрата и строительством завода по производству минеральных удобрений в Мурманской области применение специализированного конвейерного комплекса поможет избежать больших расходов на перевалку минеральных удобрений через южные порты страны. Кроме того глубины у причалов Мурманского порта позволяют принимать под обработку суда типа «Panamax» что позволяет увеличить грузооборот и производительность причального оборудования снизив тем самым эксплуатационные расходы и срок окупаемости комплекса.
Знание технических возможностей конструкции и основ расчета машин непрерывного транспорта позволит расширить области их применения и более рационально решать вопросы технического перевооружения современных производств.
Цель данного дипломного проекта - разработать специализированный перегрузочный комплекс для перегрузки минеральных удобрений в Мурманском торговом порту.
Для реализации поставленной цели в работе необходимо решить следующие задачи:
- установить географическое месторасположения проектируемого комплекса;
- изучить технологию перегрузки минеральных удобрений что в дальнейшем определит способ их перегрузки.
- произвести анализ исходных данных;
- на основе проведенного анализа разработать конвейерную и крановую схему механизации и выявить преимущества конвейерной схемы механизации над крановой;
- произвести расчет причального конвейера который будет подавать груз на судопогрузочную машину исходя из чего будет произведен расчет машины;
- произвести расчет основных механизмов судопогрузочной машины таких как: механизмы передвижения судопогрузочной машины и подъема конвейерной галереи а также рассчитать телескопический конвейер и передачу за счет которой будет осуществляется изменение вылета конвейера;
- рассчитать и проверить на прочность конвейерную галерею;
Также в дипломном проекте имеется материал по техническому обслуживанию и монтажу конвейеров требования охраны труда и экологической безопасности при перегрузке минеральных удобрений.
Объектом данного дипломного проекта является Мурманский торговый порт.
Предметом исследования является собственно перегрузочный комплекс.
Теоретической основой данного исследования послужили труды известных отечественных ученых В.С. Макарова А.П. Казака М.М. Гохберга Н.Е. Ромакина Е.Н. Андрианова Р.Л. Зенкова В.И. Анурьева и других авторов.
Внедрение данной работы позволит оптимизировать процесс перегрузки минеральных удобрений в Мурманском торговом порту увеличить производительность перегрузки при этом уменьшив эксплуатационные расходы и расходы на перегрузку одной тонны груза.
7разгр. тележка.dwg

8мех подъема.dwg

Вертикальный редуктор
Кинематическая схема механизма подъема галереи
6Сост части.dwg

Желобчатая роликоопора рабочей ветви
Прямая роликоопора холостой ветви
Мотор-барабан телескопического конвейера
Центрирующая роликоопора
Неприводной барабан причального конвейера
12ЭЛЕКТРОСХЕМА.dwg

ленточного конвейера
Масляные выключатели
Контакт реле натяжения ленты
Катушки реле времени
Автоматы цепей управления
Катушки контакторов ускорения
9Мех передвиж.dwg

судопогрузочной машины
Скорость передвижения
Давление колеса на рельс
Вспомогательный балансир
Шестерня открытой зубчатой передачи
Вертикальный редуктор
Привод механизма передвижения
Кинематическая схема механизма передвижения
11металлоконстр.dwg

по незамкнутому контуру
с двусторонним швом без обработки кромок
4конвейер.dwg

Скорость движения ленты
Максимальное натяжение ленты
Минимальное натяжение ленты
Диаграмма натяжения ленты
1Схема механизации.dwg

Галерея магистральных конвейеров
Вагоноразгрузочная установка
Груз (минеральные удобрения)
5 телеск конвейер.dwg

Скорость движения ленты
Максимальное натяжение ленты
Минимальное натяжение ленты
Диаграмма натяжения ленты
3ПМ.dwg

10ШВП.dwg

2схема механизации2.dwg

Груз (минеральные удобрения)
Вагоноразгрузочная установка
Рекомендуемые чертежи
- 30.04.2021
- 07.03.2023
- 24.04.2014