Механизация и автоматизация поддержания соотношения гипса и песка при производстве ячеистого бетона. Ленточный конвейер.




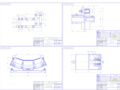
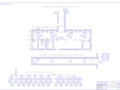
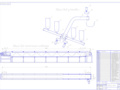
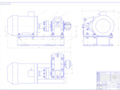
- Добавлен: 25.10.2022
- Размер: 14 MB
- Закачек: 0
Описание
Состав проекта
![]() |
![]() |
![]() |
![]() |
![]() |
![]() ![]() ![]() ![]() |
![]() |
![]() |
![]() ![]() |
![]() |
![]() |
![]() |
![]() |
![]() |
![]() |
![]() ![]() ![]() ![]() |
![]() |
![]() ![]() ![]() ![]() |
![]() |
![]() ![]() |
![]() |
![]() |
![]() |
![]() |
![]() ![]() ![]() ![]() |
![]() |
![]() |
![]() ![]() |
![]() |
![]() ![]() |
![]() |
![]() ![]() |
![]() ![]() |
![]() ![]() |
![]() |
![]() |
![]() ![]() ![]() |
![]() |
![]() |
![]() |
![]() |
![]() |
![]() ![]() |
![]() |
![]() |
![]() |
![]() |
![]() |
![]() |
![]() |
![]() |
![]() ![]() ![]() |
![]() |
![]() ![]() ![]() ![]() |
![]() |
![]() |
![]() ![]() ![]() ![]() |
![]() |
![]() |
![]() |
![]() |
![]() |
![]() |
![]() |
![]() |
![]() |
![]() ![]() ![]() ![]() |
![]() |
![]() |
![]() |
![]() |
![]() |
![]() |
![]() |
![]() |
![]() |
![]() |
![]() |
![]() ![]() ![]() |
![]() ![]() ![]() |
![]() ![]() ![]() |
![]() ![]() ![]() |
![]() ![]() ![]() |
![]() ![]() ![]() |
![]() ![]() ![]() |
![]() ![]() ![]() |
![]() ![]() ![]() |
![]() ![]() ![]() |
![]() ![]() ![]() |
![]() ![]() ![]() |
![]() ![]() ![]() |
![]() ![]() ![]() |
![]() ![]() ![]() |
![]() |
![]() |
Дополнительная информация
ЛИСТ 1 общий вид.dwg

Общий вид ленточного конвейера
Силос хранения песка
Силос хранения гипса
Линейный конвейер гипса
Линейный конвейер песка
Загрузочное устройство
Редуктор лин. конвейера гипса
Двигатель галерейного конв.
Редуктор галерейного конв.
Желобчатая роликоопора
Редуктор одноступенчатый
ЛИСТ 4 сх эл снаб.dwg

Схема электрическая принципиальная
Планировка электрооборудования второго этажа (галереи)
Планировка электрооборудования первого этажа
ЛИСТ 8 алгоритм.dwg

ЛИСТ 6 автоматизация вар 2.dwg

выгружения материала на ленту
Расчетная схема сил
действующих на ленту
действующих на ролик весовой ячейки
ЛИСТ 7 результаты выч. экспериментов.dwg
График расхода гипса (увеличенный)
График расхода песка (увеличенный)
Вычислительная схема
График расхода гипса
График расхода песка
Функциональная схема
ЛИСТ 2 рама, муфта, опора, ролик.dwg

ЛИСТ 3 привод.dwg

ЛИСТ 5 план освещения, заземление.dwg

Схема расположения заземления
Схема расположения освещения 2го этажа (галереи)
ЛИСТ 8 алгоритм .dwg

приложение 1.doc
Рисунок 2 – Общий вид муфты
Рисунок 3 – Роликоопора
Рисунок 5 – Привод конвейера
Рисунок 7 – Планировка электроснабжения
Рисунок 8 – Планировка освещения
Рисунок 9 – Планировка заземления
Реферат.doc
В данном дипломном проекте исходными данными являлся участок по смешиванию гипса и песка. Целью автоматизации является точная дозировка компонентов для бетонной смеси.
Была спроектирована система автоматического управления поддержания соотношения гипса и песка. Также был произведен расчет ленточных конвейеров и выбор двигателей. В электроснабжении был произведен расчет электрических нагрузок и была спроектирована планировка элекроснабжения участка.
Система работает следующим образом: сигнал с пульта управления поступает на линейные конвейера. Включаются питатели силосных банок с песком и гипсом. Материал высыпается на конвейер и взвешивается весовой ячейкой. Далее материал попадает на конвейер галереи который транспортирует его в приемный бункер мельницы мокрого помола
4 Автоматизация.doc
1 Определение объекта автоматизации. Цель автоматизации. Создание системы для поддержания соотношения гипса и песка
В данном дипломном проекте целью автоматизации является исключение человеческого фактора на участке смешивания компонентов: гипса и песка. Это необходимо для того чтобы выпускаемая продукция на этапе проверки соответствовала заданным показателям качества. Песок доставляется на предприятие автосамосвалами и разгружается через колосниновую решетку в приемный бункер. Гипс также может доставляться автосамосвалами или через пневмотранспорт. Из приемного бункера материал по ленточному питателю выгружается на конвейер галереи который поднимает материал для хранения в силоса. Разгрузка материала с ленточного питателя осуществляется при помощи плужковый сбрасывателей которые расположены непосредственно над необходимым силосом песка 3-4 (рис.4.1) или гипса 1-2 (рис.4.1). В каждом силосе находятся датчики слежения уровня материала.
Рисунок 4.1. Схема технологическая. Общий вид
На основании каждого силоса имеется виброконус который необходим для выгрузки материала из силоса. Эту нужно для того чтобы материал не слеживался на стенках конуса. Виброконус оснащен двумя двигателями с дебалансами и двигателем на затворе.
Материал высыпается из силосов когда затвор открывается попадая на ленту конвейера 5 (рис.4.1) и 6 (рис.4.1) которые транспортируют его на конвейер галереи 7. Приводом конвейеров является двигатель 111213 (рис.4.1) соединенный с редуктором 101214 (рис.4.1) через соединительную муфту. На конвейерах установлены натяжные устройства что не позволяет ленте проскальзывать. Также установлены датчики веса для взвешивания материала высыпающегося из силосов датчики скорости ленты датчики наличия материала на ленте и датчики влажности материала. Материал проходя по линейным конвейерам попадает на ленту галерейного конвейера который транспортирует его в приемный бункер мельницы мокрого помола 9 (рис.4.1).
Для создания системы автоматического управления необходимо выявить объект управления. В данном случае объектом управления будет являться линейные конвейера и питатели на силосах. Структурная схема будет иметь вид:
Рисунок 4.2. Структурная схема системы
Задатчиком для системы управления песка является сигнал который задаст оператор на пульте управления. Далее по регламенту работы участка лента конвейера включается за 20 60 сек до включения питателя. Потом происходит включение виброконуса силосов песка и включение питателя.
Сигналом обратной связи служит датчик веса. Расход песка является задатчиком для системы управления гипсом.
2. Объект управления. Его входные и выходные координаты
Для корректной работы системы примем следующие допущения:
Допущения принятые к ленте конвейера:
Не рассматривается переходной процесс при пуске т.к. по регламенту работы участка лента включается за 20 60 секунд до включения питателя к этому времени все переходные процессы закончены;
Лента не растяжима. Упругих свойств нет.
Проскальзывание отсутствует.
Допущения принятые к питателю:
Ленточный конвейер представляет собой классическую транспортную систему в первом приближении ее можно описать звеном запаздывания время запаздывания зависит от размеров установки;
Питатель представляется условно;
Если сравнить время работы установки и время запаздывания выгрузки из питателя от момента его включения то видно что оно существенно мало и транспортным запаздыванием модно принебреч;
3 Математическое описание конвейеров как ОУ
Структура технологического процесса:
Рисунок 4.3. Схема технологического процесса.
На рисунке представлена структура технологического процесса движения материала по ленте в приемный бункер мельницы мокрого помола. На рисунке показано расстояние от центра силосов до центра весовой ячейки (датчика веса). Материал q1 выпадая из силосов попадает на движущуюся ленту конвейера далее материал высыпается на конвейер галереи и отправляется в приемный бункер мельницы мокрого помола. Скорость движения ленты V=16 мс.
Расход материала из силосной банки не равномерна и зависит от следующих условий:
- интенсивность вибрации конуса;
- влажность компонента
- коэффициент слеживаемости
- количество компонента
Сделаем допущение что материал в банке выше уровня 25% загрузки тогда:
Коэффициент слеживаемости будет являться основным возмущающем воздействием приводящем к зависанию материала в силосе.
По результатам наблюдения за установкой включение вибратора конуса увеличивает расход из него.
Численно определить увеличение расхода в данный момент не представляется возможным из за этого делаем предположение что связь между интенсивностью и расходом будет иметь вид:
Связь влажности с находится через коэффициент и носит следующий характер:
Рисунок 4.4. График влажности
На рисунке представлен график влажности материала. Из графика видно что если материал менее влажный то выгрузка его происходит без включения виброконусов.
Полный расход из силоса будет выражатся:
Рисунок 4.5. Расчетная схема выгрузки материала
По визуальному наблюдению за установкой зависимость между подачей напряжения управления на вибратор и расходом из виброзатвора выглядит следующим образом:
Рисунок 4.6. График расхода материала
Для математического описания произведем идентификацию кривой и составим выражение:
Где: К – коэффициент передачи в статическом режиме.
При расходе свыше происходит потеря материала
Рисунок 4.7. Схема потери материала на ленте
Это можно описать ограничением по уровню.
Описание весовой ячейки:
В механических узлах трение отсутствует;
Колебательная система измерения не учитывается;
Рисунок 4.8. Расчетная схема сил действующих на ленту.
Для нахождения силы действующей на ролик весовой ячейки найдем расстояние между роликовыми опорами.
где: - расстояние между роликами;
Найдем силу F действующую на одном погонном метре ленты:
где: v – скорость конвейера;
- время за которое проходит материал по весовой ячейке;
Определим силу действующую на ролик весовой ячейки:
Рисунок 4.9. Расчетная схема сил действующих на ролик весовой ячейки.
где: tk и tн – время начала и окончания действия сил на ролик весовой ячейки
4 Расчетная и вычислительная модели САУ
Функциональная схема управления выглядит следующим образом:
Рисунок 4.10. Структурная схема объекта управления
Управляющим воздействием в функциональной схеме (рис4.10) является сигнал задания который подается на два входа первого объекта управления и на первый вход второго объекта управления. Сигнал на второй вход системы управления гипсом подается с выхода системы управления песком с учетом переводного коэффициента.
Схема работает следующим образом. Сигнал с пульта управления поступает на конвейер песка. Затем включаются вибраторы на силосах и непосредственно питатель. Расход песка будет заданием для включения системы управления гипсом.
Моделирование объекта управления проводилось в программной среде «MATLAB». Построена вычислительная модель для поддержания соотношения гипса и песка (рис4.11).
Рисунок 4.11. Вычислительная модель
Схема работает следующим образом. На пульте управления оператор запускает программу управления процессом. Задает соотношение необходимое для изготовления бетонной смеси. Сигнал с пульта поступает на контроллер который оперирует цифровой сигнал и переводит его при помощи ЦАП в аналоговый сигнал который в свою очередь является сигналом для запуска двигателя конвейера и вибраторов. Затем происходит выгрузка материала на ленту. Расход из вибровыгруза определяется выражением (4.5). Для того чтобы избежать потери материала в системе стоит ограничение. Также установлена задержка по времени пока материал доезжает до весовой ячейки и задержка пока материал проезжает по ней. Материал взвешивается весовой ячейкой которая представляет собой датчик веса выполненный на тензорезисторах. Расход песка является задающим сигналом для расхода гипса.
Графики расхода песка будут выглядеть следующим образом:
Рисунок 4.12. График расхода песка
Рисунок 4.13. График расхода песка (увеличенный)
Из графиков видно что песок из силоса высыпается равномерно
Рисунок 4.14. График расхода гипса
Рисунок 4.15. График расхода гипса (увеличенный)
5 Алгоритм работы участка по поддержанию соотношения гипса и песка.
Работа алгоритма происходит следующим образом:
Первоначальная работа осуществляется включением в сеть автомата (рис4.13. блок 1) далее сигнал поступает на силосы хранения песка (рис4.13. блок 2) осуществляется включение вибровыгруза Р1 (рис4.13. блок 4). Далее сигнал поступает на силосы хранения гипса (рис4.13. блок 5) включается вибровыгруз G3 (рис4.13. блок 7). Потом проиходит включение грохотов (рис4.13. блок 9) на приемном бункере мельницы мокрого помола. В первоначальный момент включение грохота происходит по схеме «звезда».Это необходимо для снижения пусковых токов при включении. Далее включается таймер который действует 5 секунд (рис4.13. блок 10) после чего происходит отключение схемы «звезда» и включение схемы «треугольник» (рис4.13. блок 12). Далее включается таймер (рис4.13. блок 13). Включение таймеров необходимо для корректной работы контроллеров Siemens. После включения таймера происходит включение ленты 5 (рис4.1) конвейера (рис4.13. блок 19) по той же технологии что и включение грохота на приемном бункере мельницы мокрого помола. Сначала включение происходит по схеме «звезда» затем переключается на схему «треугольник» (рис4.13. блок 22). Таким же образом далее включается лента 6 и 7 (рис4.1 рис4.13. блок 25 и 31). Потом происходит включение САУ пропорционального дозирования (рис4.13. блок 34) что приводит к включению вибровыгруза Р2 (рис4.13. блок 35). Далее наполняется приемный бункер до уровня 45 от его объема и вибровыгруз отключается. Включается вибровыгруз G4 (рис4.13. блок 37) и также происходит наполнение приемного бункера в процентном соотношении. После наполнения G4 отключается и происходит отключение САУ (рис4.13. блок 38). Система проверяет количество недогрузившегося гипса. Если оно d>01 (т.е. 100 кг недогруз) то система заново включает САУ (рис4.13. блок 40-42) и вибровыгруз G4 (рис4.13. блок 43) догружает материал до определенного значения. Если материал d01 то происходит поочередное отключение лент 567 (рис4.1) и грохота (рис4.13. блок 45 48 51 54)). Система переходит на непосредственный уровень включения грохота или переключение всей цепи на ручной режим (рис4.13. блок 57).
Рисунок 4.16. Алгоритм работы
Рисунок 4.17. Алгоритм работы (продолжение)
Рисунок 4.18. Алгоритм работы (продолжение)
Рисунок 4.19. Алгоритм работы (продолжение)
6 Техническая реализация
Для решения задач автоматизации выбираем микроконтроллер серии SIMATIC S7-200 [9 10] предназначенный для решения задач управления и регулирования небольших систем автоматизации. Этот контроллер позволяет создавать как автономные системы управления так и системы управления работающие в общей информационной сети. За счет высокой гибкости конфигураций контроллер SIMATIC S7-200 применяется для решения как простейших задач автоматизации для решения которых в прошлом использовались простые реле и контакторы до задач комплексной автоматизации.
В качестве центрального процессора используем модуль CPU 224 предназначенный для построения компактных систем автоматического управления высокой производительности. Модуль оснащен 14 встроенными дискретными входами и 10 дискретными выходами. Позволяет производить подключение до 7 модулей расширения ввода-вывода.
Технические данные :
Объем встроенной памяти программ - 12288 байт;
Объем встроенной памяти данных - 8192 байт;
Опциональный картридж памяти - 256 Кбайт;
Сохранение данных в памяти при перебоях электропитания - 70 часов;
Количество таймеров - 256;
Количество счетчиков - 256;
Диапазон счета - 0 32767;
Программное обеспечение - STEP 7 M
Языки программирования - LAD FBD
Набор команд основной:
Логические операции адресация результата сохранение счет загрузка; Передача сравнение сдвиг вращение вызов подпрограмм с передачей параметров.
Вибрационные датчики уровня применяются для измерения в жидких и сыпучих веществ различной плотности и вязкости в широком диапазоне давлений и температур. Принцип действия вибрационных датчиков уровня основан на затухании колебаний рабочих пластин резонатора (камертона) датчика в жидкостях или сыпучих продуктах. Достоинством вибрационных датчиков уровня является невосприимчивость к размерам частиц плотности и влажности среды к влиянию электрических и магнитных полей. Вибрационный датчик уровня сохраняет работоспособность даже при значительном налипании контролируемого материала на рабочие поверхности пластин резонатора. На показания вибрационных датчиков уровня не влияет наличие пены пузырьков взвешенных частиц в измеряемой среде.
Вибрационный датчик уровня LVL-A1
Недорогой вибрационный датчик уровня для жидкостей и вязких субстанций. Имеются модификации датчика для высоких температур до 150°С а так же вариант вибрационного датчика уровня для процессов с повышенными требованиями к гигиене.
Таблица 4.1 – Технические характеристики датчика уровня LVL-A1
Диапазон измерений (бар)
Температура процесса [C]
Сигнализатор «Камертон-М» имеет высокую устойчивость к изменениям влажности плотности электропроводности температуры контролируемого материала воздействиям электромагнитных полей и налипанию материала на датчик и стенки сосуда. Сигнализатор «Камертон-М» не критичен к турбулентным потокам пенообразованию и внешним вибрациям.
Конструктивные элементы контактирующие с процессом изготовлены из нержавеющей стали или стали с антикоррозийным покрытием. Допускается использование «Камертон-М» в средах по отношению к которым материал корпуса является коррозионностойким. Допускается электрическое подключение «Камертон-М» к источнику питания и нагрузке через барьер искрозащиты. Сигнализатор имеет повышенную механическую прочность защиту от переполюсовки питания.
«Камертон-М» изготавливается в следующих климатических исполнениях:
УХЛ2 для работы при температуре окружающей среды от минус 40°С до плюс 50°С
«Камертон-М» классифицирован в соответствии с ГОСТ 12997 следующим образом:
- по наличию информационной связи предназначены для информационной связи с другими изделиями (передача информации);
- по виду энергии носителя сигналов в канале связи «Камертон-М» является электрическим:
- в зависимости от эксплуатационной законченности относятся к изделиям третьего порядка С2
- по метрологическим свойствам «Камертон-М» не является средством измерения изделие не имеет точностные характеристики;
- по устойчивости к механическим воздействиям изделие является виброустойчивым.
Таблица 4.2 - Технические характеристики прибора:
Напряжение питания датчика
Выходной коммутирующий элемент (или по заказу)
Два PNP транзистора НО НЗ контакт
Реле перекидной контакт
Напряжение (ток ) коммутации
Электрическое подключение
Температура контролируемой среды
Защита оболочки электронного блока сигнализатора
Размер погружаемой части датчика (регулировка глубины погружения)
Масса датчика не более
Для слежения за уровнем в силосных банках выбираю сигнализатор «Камертон-М». Выбор обусловлен его малой чувствительностью к пыли налипанию материала на датчик и стенки сосуда. Также в случаю попадания кускового материала (гипса) данный датчик не засоряется по сравнению с иностранными аналогами которые имеют две рабочих пластины (так называемые «вилкой»).
Для непрерывного измерения уровня материала выбираю радиолокационный датчик уровня РДУ-Х2. Он предназначен для бесконтактного непрерывного измерения уровня материала (расстояния) в крупногабаритных ёмкостях и бункерах и выдачи информации в аналоговом виде. Датчик уровня размещается на крышах бункеров хранилищ силосов и может использоваться для измерения уровня материалов с различным фракционным составом (в том числе туманообразующих и пылеобразующих). На точность измерения не влияют колебания влажности температуры воздуха и материала. Фторопластовая защита излучателя и приемника радиоволн позволяет использовать измеритель для агрессивных материалов. Типичное применение: цемент зерно уголь шлаки мука песок даламит магнезит гипс зола гранулы вода пищевые жидкости растворы в т.ч. агрессивные и пр.
Таблица 4.3 – Краткие технические характеристики датчика уровня РДУ-Х2
Диапазон измерения уровня м
Зона нечувствительности не более м
Погрешность измерения см
Рабочий диапазон температур °С
Напряжение питания ток потребления
Выходной сигнал токовый мА
Потребляемая мощность Вт не более
Габаритные размеры мм
1 Технология.doc
1Классификация конвейеров.
Ленточные весовые дозаторы используются для непрерывного динамического взвешивания и дозирования сыпучих материалов в технологических потоках металлургической промышленности а также на предприятиях цементной горнорудной угольной строительных материалов и других отраслей промышленности. Дозатор является комплектным оборудованием в системах управления технологическими процессами но может иметь и самостоятельное автономное применение. Дозатор ДВЛ – система состоящая из весового конвейера электропривода микроконтроллера функционирующая на основе принципа непрерывного взвешивания и дозирования.
Конвейер (от англ. convey — продвигать) — такая организация выполнения операций над объектами при которой весь процесс воздействия разделяется на последовательность стадий с целью повышения производительности путём одновременного независимого выполнения операций над несколькими объектами проходящими различные стадии. Конвейером также называют средство продвижения объектов между стадиями при такой организации.
Основной классификационный признак конвейера — тип тягового и грузонесущего органа. Различают конвейера с ленточным цепным канатным тяговыми органами и конвейера без тягового органа (гравитационные инерционные винтовые). Конвейера с тяговым органом могут быть по виду грузонесущего органа ленточными пластинчатыми люлечными скребковыми ковшовыми и пр. Для таких конвейеров характерно общее с рабочим органом движение груза на рабочих участках. Тяговое усилие передается либо грузонесущим элементом либо элементом проталкивающим или тянущим груз по неподвижному желобу трубе настилу и т.п. Для конвейера без тягового органа характерно раздельное движение груза и рабочих органов совершающих круговое вращательное (роликовые винтовые Конвейера) или возвратно-поступательное рабочее движение (например инерционные Конвейера). Конвейера могут иметь машинный привод (наиболее часто электрический реже пневматический) или груз может перемещаться под действием силы тяжести (гравитационные Конвейера).
В зависимости от условий используют конвейера напольные и подвесные. Напольные конвейера могут быть стационарными передвижными или переносными. На конвейерах можно перемещать груз в горизонтальной или близкой к ней наклонной плоскости (ленточные пластинчатые тележечные скребковые роликовые винтовые вибрационные качающиеся); в вертикальной или близкой к ней наклонной плоскости (скребковые ковшовые винтовые вибрационные); в любой плоскости. В последнем случае конвейеры состоят из чередующихся горизонтальных вертикальных или наклонных участков (подвесные ковшовые скребковые люлечные и др.). Кроме того конвейеры могут различаться в зависимости от рода перемещаемых грузов — насыпных или штучных. Конструкция некоторых конвейеров позволяет транспортировать как насыпные так и штучные грузы. Особые группы конвейеров составляют элеваторы вертикальные конвейеры с подвесными ковшами люльками или полками эскалаторы специальные пластинчатые и ленточные. Конвейера для перемещения людей шагающие конвейеры триммеры стакеры для штабелирования брёвен а также комбинированные (например роликоленточные конвейера типа «Рапистан» обеспечивающие удержание штучных грузов на спусках с заданными интервалами) и т.д.
2Основные типы конвейеров.
Рисунок 1.1 – Ленточный конвейер:
– рама конвейера; 2 – моторобарабан; 3 – лента конвейера; 4 – приводной барабан; 5 – натяжной барабан; 6 – роликоопора верхняя желобчатая несущая; 7 – роликоопора нижняя плоская возвратная; 8 – дефлекторный ролик.
Ленточные конвейера используют для перемещения сыпучих кусковых и штучных грузов на расстояния достигающие иногда 10—12 км и больше. Такие конвейеры обычно составляют из отдельных секций. Трасса конвейера в горизонтальной плоскости прямолинейная а в вертикальной может быть наклонной или иметь более сложную конфигурацию. Тяговый и грузонесущий орган — лента которая движется по стационарным роликоопорам огибая приводной натяжной а иногда и отклоняющие барабаны. Груз перемещается на ленте вместе с ней. В зависимости от типа роликоопор лента имеет плоскую или желобчатую форму. Конвейер ленточный с плоской лентой используется преимущественно для перемещения штучных грузов. Необходимое натяжение ленты обеспечивает натяжная станция обычно грузовая а в передвижных конвейерах — винтовая. Привод конвейера (приводная станция) состоит из электродвигателя редуктора барабана и соединительных муфт. Загрузку сыпучего груза на ленту производят через направляющий лоток или воронку а разгрузку — через концевой барабан или при помощи плужкового или барабанного сбрасывателя. Ленточные конвейера имеют высокую эксплуатационную надёжность обеспечивают производительность от нескольких тч до нескольких тысяч тч. Ширина тканевых лент в К. от 300 до 2000 мм скорость движения лент составляет 15—40 мсек. Короткие передвижные ленточные конвейера монтируются на колёсном ходу и используются на погрузочно-разгрузочных работах и в строительстве.
Пластинчатые конвейера
Рисунок 1.2 – Пластинчатый конвейер:
— приводная звездочка; 2 — цепь; 3 — пластина; 4 — каток; 5 — направляющая шина; 5 — станина; 7 — загрузочная воронка; 8 — натяжная звездочка; 9 — натяжное устройство; 10 — разгрузочная воронка; 11 — редуктор; 12 — электродвигатель.
Пластинчатые конвейера предназначены для перемещения в горизонтальной плоскости или с небольшим наклоном (до 35°) тяжёлых (500 кг и более) штучных грузов крупнокусковых в том числе острокромчатых материалов а также грузов нагретых до высокой температуры. Пластинчатые конвейера стационарные или передвижные имеют те же основные узлы что и ленточные. Грузонесущий орган — металлический реже деревянный пластмассовый настил-полотно состоящий из отдельных пластин прикрепленных к 1 или 2 тяговым цепям (втулочно-роликовым). Настил может быть плоским волнистым или коробчатого сечения без бортов или с бортами. Тяговые цепи огибают приводные и натяжные звездочки установленные на концах рамы. Различают пластинчатые конвейера общего назначения (основной тип) и специальные. К последним относятся конвейера с пространственной трассой разливочные машины для металла пассажирские эскалаторы и др. Скорость движения груза небольшая — 03— 10 мсек. Для увеличения производительности конвейера с плоским настилом дополняют неподвижными бортами. Типовые пластинчатые конвейеры имеют производительность до 2000 тч.
Скребковые конвейера
Рисунок 1.3 – Скребковый конвейер:
– станция приводная; 2 – станция натяжная; 3 – секция загрузочная; 4 – секция проходная; 5 – цепь втулочно-роликовая; 6 – секция загрузочная.
Скребковые конвейера перемещают груз движущимися по жёлобу или трубе скребками. Такие конвейеры используют для переработки сыпучих или кусковых грузов поступающих в жёлоб через загрузочную воронку. Рабочей ветвью обычно является нижняя реже — верхняя иногда обе ветви. Контур сечения жёлоба и конфигурация скребков должны быть одинаковыми — прямоугольной полукруглой трапецеидальной формы. Скребки бывают штампованными из листовой стали или литыми а желоба изготовляют металлическими реже деревянными. Скребковые конвейеры по сравнению с пластинчатыми имеют меньшую массу могут загружаться и разгружаться в любой точке по всей длине желоба. Применение скребковых конвейеров ограничено из-за измельчения грузов и быстрого износа желоба особенно при перемещении абразивных материалов. Кроме того для скребковых конвейеров характерен большой расход энергии затрачиваемой на преодоление вредных сопротивлений. Скорость рабочего органа скребковых К. 016—05 и реже — 10 мсек производительность 50—350 тч. Скребковые конвейера обычно применяются для перемещения груза на расстояния до 100 м.
Разновидностью скребковых конвейеров являются конвейера с погруженными скребками у которых скребки перекрывают лишь часть сечения желоба а груз заполняет всю рабочую ветвь желоба или большую ее часть. Такие конвейера могут иметь сложную трассу и используются для перемещения грузов (обычно мелкосыпучих) в горизонтальном вертикальном и наклонном направлениях со скоростью 01— 025 мсек. Особую группу скребковых конвейеров составляют трубчатые конвейера тяговая цепь и скребки которых размещены внутри трубы причём скребки заполняют всё её сечение. Такие конвейера также могут иметь пространственную трассу.
Конвейера с несущими и ведущими цепями в отличие от других типов конвейеров не имеют грузонесущего органа и применяются главным образом в поточных линиях при конвейерной сборке. На конвейер с несущими цепями грузы устанавливаются непосредственно на тяговые цепи скользящие в неподвижных направляющих. На конвейер с ведущими цепями грузы передвигаются по неподвижным опорным путям непосредственно по полу цеха или имеют собственный колесный или гусеничный ход. В массовом и серийном производстве на сборочных работах применяют так называемые тележечные конвейеры. Они представляют собой тележки соединенные тяговой цепью и движущиеся по замкнутой трассе. На тележках выполняют основные процессы литейного производства (формовку заливку охлаждение) или сборку машин и узлов.
Рисунок 1.4 – Подвесной конвейер
Подвесные конвейера с цепным тяговым органом служат для непрерывного (реже периодического) перемещения штучных грузов. Трасса таких конвейеров обычно пространственная замкнутая имеет сложный контур. Подвесные конвейера делят на 3 группы: грузонесущие (каретки для груза постоянно соединены с тяговым органом); тянущие (каретки также постоянно соединены с тяговым органом и имеют крюки для присоединения тележек перемещающихся по полу цеха или склада); толкающие (каретки не связаны постоянно с тяговым органом и передвигаются по подвесным путям). Применение подвесных конвейеров позволяет решить проблемы комплексной механизации и автоматизации погрузочно-разгрузочных и складских работ на стыке внутрицехового внутризаводского и магистрального транспорта. Значительная роль им отводится и в создании полностью автоматизированных складов.
Рисунок 1.5 – Винтовой конвейер
Винтовые конвейера служат для перемещения пылевидных и мелкокусковых грузов в горизонтальной или наклонной (до 20°) плоскостях реже в вертикальной плоскости (с быстро вращающимися винтами). Конвейер имеет металлический закрытый жёлоб внутри которого вращается вал с лопастями расположенными по винтовой линии. Лопасти могут быть сплошными (для легкосыпучих грузов) ленточными (для влажных и кусковых грузов) и в виде отдельно укрепленных на валу лопаток (для липких и слеживающихся грузов). При вращении винта лопасти проталкивают груз вдоль желоба. Винтовые конвейера состоят из секций длиной 2—4 м общая длина конвейера не превышает обычно 60 м диаметр жёлоба 100—600 мм. Винтовые конвейера просты по конструкции удобны в эксплуатации особенно при транспортировке пылящих грузов. Однако лопасти и жёлоб конвейера сравнительно быстро изнашиваются груз измельчается и истирается кроме того требуется повышенный расход энергии.
Рисунок 1.6 – Роликовый конвейер
Роликовые конвейера служат для перемещения штучных грузов с плоской ребристой или цилиндрической поверхностью. На неподвижных осях рамы конвейера в подшипниках вращаются ролики. Длина ролика должна быть несколько больше ширины или диаметра груза а расстояние между роликами несколько меньше половины длины груза. Мелкие грузы со сложной конфигурацией перемещают на таком конвейере в ящиках пли на поддонах. Роликовые конвейера бывают 2 типов: гравитационные и приводные. В гравитационных конвейерах устанавливаемых с уклоном в 2—5° ролики свободно вращаются под действием силы тяжести перемещаемого груза. В приводных конвейерах ролики имеют групповой привод от двигателя. Такие конвейера применяют когда нужно обеспечить постоянную скорость движения грузов перемещать их в строго горизонтальной плоскости или поднимать под некоторым углом. Роликовый конвейер состоит из секций каждая длиной 2—3 м. В зависимости от конфигурации трасса может включать в себя криволинейные и откидные секции поворотные круги и стрелочные переводы и т.д.
Инерционные конвейера
Рисунок 1.7 – Инерционный конвейер
Инерционные конвейера служат для транспортирования сыпучих реже мелких штучных грузов на сравнительно короткие расстояния в горизонтальном или наклонном (до 20°) направлениях. В инерционных конвейерах частицы груза скользят по грузонесущему органу или совершают полёты в пространстве под действием силы инерции. Инерционные конвейера делятся на 2 группы: качающиеся характеризующиеся значительными амплитудами и малой частотой колебаний и вибрационные — с малой амплитудой и большой частотой колебаний.
В простейшем качающемся конвейере жёлоб находится на упругих стойках жестко закрепленных на опорной раме под некоторым углом к вертикали. Кривошипный механизм с приводом от электродвигателя сообщает желобу переменные по направлению движения. Желоб при движении вперед немного поднимается а при движении назад опускается (качается). При этом меняется давление груза на желоб. При движении жёлоба назад груз скользит по нему вперёд продвигаясь на некоторое расстояние.
На вибрационном конвейере грузу сообщаются несимметричные колебания. В результате плавного движения трубы К. вверх и резкого движения вниз происходит отрыв частиц груза от поверхности трубы и перемещение их вдоль неё. В зависимости от диаметра жёлоба — 350 500 и 750 мм — производительность вибрационных конвейерах соответственно составляет 50 75 и 150 тч. Наиболее высокая возможная производительность 400 тч наибольшая длина — 100 м. Специальные типы вибрационных конвейеров применяют также для перемещения грузов вверх .
Технико-экономическая характеристика. Эффективность использования конвейера в технологическом процессе любого производства зависит от того насколько тип и параметры выбранного конвейера соответствуют свойствам груза и условиям в которых протекает технологический процесс. К таким условиям относятся: производительность длина транспортирования форма трассы и направление перемещения (горизонтальное наклонное вертикальное комбинированное); условия загрузки и разгрузки конвейера; размеры груза его форма удельная плотность абразивность кусковатость влажность температура и пр.; ритм и интенсивность подачи а также различные местные факторы.
Высокая производительность простота конструкции и сравнительно невысокая стоимость возможность выполнения на конвейерах различных технологических операций невысокая трудоёмкость работ обеспечение безопасности труда улучшение его условий — всё это обусловило широкое применение конвейеров во всех областях народного хозяйства: в чёрной и цветной металлургии машиностроении горной химической пищевой и др. отраслях промышленности. В промышленном производстве конвейера являются неотъемлемой составной частью технологического процесса. Конвейера позволяют устанавливать и регулировать темп производства обеспечивать его ритмичность. Являясь основным средством комплексной механизации и автоматизации транспортных и погрузо-разгрузочных процессов и поточных технологических операций. Конвейеры вместе с тем освобождают рабочих от тяжелых и трудоемких транспортных и погрузочно-разгрузочных работ делают их труд более производительным.
Широкая конвейеризация составляет одну из характерных черт развитого промышленного производства. Это объясняется тем что внедрение загрузочных и разгрузочных дозировочных счетных и взвешивающих автоматов автоматических очищающих и смазывающих устройств разнообразной контрольной защитной и блокировочной аппаратуры средства автоматического управления невозможно без применения конвейеров как одной из основных машин комплектующих систему автоматизированного производства.
7 Техника безопасности.doc
1 Задачи в области обеспечения безопасности труда
Безопасность труда – это система законодательных актов и соответствующих им социально-экономических технических гигиенических и организационных мероприятий обеспечивающих безопасность сохранение здоровья и работоспособности человека в процессе труда.
Главной задачей безопасности труда является уменьшение вероятности поражения или заболевания работающего с одновременным обеспечением комфорта при максимальной производительности труда. Реальные производственные условия характеризуются наличием некоторых опасностей и вредностей.
Производственная опасность – это возможность воздействия на работающих опасных и вредных производственных факторов.
К опасным производственным факторам относятся такие воздействие которых на работающего приводит к травме. К вредным производственным факторам относятся такие воздействие которых на работающего приводит к заболеванию.
Случай с работающим связанный с воздействием на него опасного производственного фактора называют несчастным случаем на производстве. Ухудшение здоровья в результате несчастного случая обычно называют травмой.
Явление характеризующееся совокупностью производственных травм называется производственным травматизмом. Профессиональное заболевание – это заболевание вызванное воздействием на работающего вредных условий труда.
Улучшение условий труда приводит к таким социальным результатам как улучшение здоровья трудящихся повышение степени удовлетворенности трудом укрепление трудовой дисциплины повышение престижа ряда профессий а так же увеличении производительности труда.
Правила и нормы по технике безопасности направлены на защиту организма человека от физических травм воздействия технических средств используемых в процессе труда. Они регулируют поведение людей обеспечивающее безопасность труда с точки зрения устройства и размещения машин строительных конструкций зданий сооружений и оборудования.
Правила и нормы по производственной санитарии и гигиене предусматривают защиту организма от переутомления химического атмосферного воздействия и т. п. Эти правила и нормы устанавливают требования по устройству территорий производственных и бытовых помещений оборудованию рабочих мест и т. п.
2 Обеспечение нормальных параметров микроклимата на участке по поддержанию соотношения гипса и песка
Самочувствие и работоспособность человека зависят от метеорологических условий производственной среды в которой он находится и выполняет трудовые процессы. Под метеорологическими условиями понимают несколько факторов воздействующих на человека: температуру влажность и скорость движения воздуха а также барометрическое давление и тепловое излучение. Совокупность этих факторов называют производственным микроклиматом.
На производстве указанные факторы воздействуют на человека чаше всего суммарно взаимно усиливая или ослабляя друг друга. Например увеличение подвижности воздуха усиливает эффект пониженной температуры и наоборот ослабляет воздействие повышенной температуры на организм человека. Повышение влажности ухудшает самочувствие человека как при пониженной так и при повышенной температуре. Таким образом сочетание метеорологических параметров производственной среды может быть благоприятным и неблагоприятным для самочувствия человека.
Действующими нормативными документами регламентирующими метеорологические условия производственной среды являются ГОСТ 12.1.005-88 «Общие санитарно-гигиенические требования к воздуху рабочей зоны».
Действующими нормативными документами регламентирующими метеорологические условия производственной среды являются ГОСТ12.1.005-88 «Общие санитарно-гигиенические требования к воздуху рабочей зоны» и «Санитарные нормы проектирования промышленных предприятий» (СН 245-71). Этими документами установлены оптимальные и допустимые величины температуры относительной влажности и скорости движения воздуха.
Допустимыми являются такие параметры микроклимата которые при длительном воздействии могут вызвать напряжение реакции терморегуляции человека но к нарушению состояния здоровья не приводят. Оптимальными являются такие параметры микроклимата которые не вызывают напряжения реакций терморегуляции и обеспечивают высокую работоспособность человека.
Температуранормального здорового человека поддерживается на уровне 36.5 – 37°С независимо от метеорологических условий окружающей среды. Она поддерживается на этом уровне с помощью подсознательно действующего механизма терморегуляции. В случае повышения температуры воздуха человек начинает потеть его потеря тепла увеличивается за счет испарения пота. Выделение тепла связано также с тяжестью выполняемой работы. Все работы по степени тяжести делятся на три категории: легкая средней тяжести и тяжелая.
Все производственные помещения в зависимости от величины теплоизбытков подразделяют на помещения с незначительными теплоизбытками.
При перегреве организма увеличивается приток крови к периферийным кровеносным сосудам. Вследствие расширения сосудов количество протекающей по ним крови и теплоотдача увеличиваются.
В случае переохлаждения воздушной среды наблюдается обратное явление. Периферийные кровеносные сосуды сужаются приток крови к ним и соответственно теплоотдача снижаются. У человека появляется стремление к интенсивным движениям которые увеличивают обмен веществ в организме с образованием тепла. Чрезмерное охлаждение организма может привести к различным простудным заболеваниям.
Оптимальная величина температуры воздуха рабочей зоны установленная ГОСТ 12.1.005-88. Как видим она связана с сезоном года и тяжестью выполняемой работы и может колебаться в весьма широких пределах: от 16 до 25 °С.
Влажность воздуха в значительной мере влияет на самочувствие человека и его работоспособность. Влажность воздуха бывает абсолютная и относительная. Абсолютная влажность – это абсолютное содержание водяных паров в воздухе при данной температуре (гм3). Относительная влажность представляет собой процентное отношение абсолютного количества водяных паров в воздухе к их максимально возможному количеству при данной температуре воздуха.
При слишком низкой влажности (менее 20 %) организм человека расслабляется результатом чего является снижение трудоспособности.
Очень высокая влажность (более 80 %) нарушает процесс терморегуляции. Выделяющийся пот не испаряется а лишь стекает по поверхности тела и не отнимает от него излишнего тепла. В особенности неблагоприятно сочетание высокой влажности с высокой температурой при выполнении человеком тяжелой работы.
Оптимальная относительная влажность установленная ГОСТ 12.1.005-88 составляет 40 60 %. Допустимая величина относительной влажности может быть до 75 %) в зависимости от сочетания температуры воздуха со скоростью его движения в помещении.
Источником повышенной влаги в производственных условиях чаще всего являются технологические процессы сопровождающиеся интенсивным испарением жидкостей (различные ванны пропарочные моечные и другие аппараты).
Длительное воздействие влаги в сочетании с низкими температурами может привести к такому заболеванию как туберкулез легких. При значительном содержании влаги и высокой температуре воздуха возникает головокружение тошнота тепловые удары с потерей сознания. В горячих цехах вследствие потери организмом больших количеств солей от чрезмерного потовыделения у работающих может возникнуть судорожная болезнь.
Тепловое самочувствие человека в значительной мере связано с таким метеорологическим параметром как скорость движения воздуха так как она влияет на теплообмен организма с окружающей средой. При высокой температуре воздуха увеличение его подвижности благоприятно сказывается на самочувствии человека при низкой – вызывает неприятные ощущения. Вследствие этого стандартом установлена подвижность воздуха различная для летнего и зимнего периодов года. В теплый период года скорость движения воздуха в рабочей зоне составляет от 0.2 до 1.0 мс а в холодный и переходный периоды – от 0.2 до 0.5 мс.
Следует отметить что слишком низкая скорость воздуха (менее 0.2 мс) неблагоприятно влияет на самочувствие человека в особенности при выполнении однообразной монотонной работы например в условиях конвейерного производства. Человек в этом случае быстро утомляется и заметно теряет трудоспособность. Чрезмерно высокая подвижность охлажденного воздуха в жарких помещениях может вызвать резкие перепады температуры сопровождающиеся простудными заболеваниями работающих.
Из вышеизложенного становится ясным что задача обеспечения наилучших условий труда способствующих его высокой производительности должна решаться комплексно с учетом одновременно трех основных параметров: температуры относительной влажности и подвижности воздуха. Оптимальное сочетание метеорологических параметров производственной среды называют комфортность. Комфортность на рабочих местах должна обеспечиваться применением комплекса современных технических и санитарно-гигиенических мероприятий.
Производственное освещение.
Под производственным освещением понимают систему устройств и мер обеспечивающую благоприятную работу зрения человека и исключающую вредное или опасное влияние на него в процессе труда. Чтобы человек мог выполнять зрительную работу необходимы определенные характеристики света и зрения человека.
Основными количественными показателями света являются световой поток сила света освещенность яркость.
Участок пластического формования керамических кирпичей оснащен дежурным освещением ввиду того что оператор следит за функциональностью оборудования редко появляясь на рабочем месте. Таким образом дежурное освещение предусматривает выделение части осветительных установок обеспечивающих горизонтальную на уровне земли или вертикальную на плоскости ограждения освещенность равную 0.5 лк.
3 Оценка вредности пыли и средства защиты работающего персонала от неё
В процессе труда на человека кратковременно или длительно воздействуют вредные факторы. Эти факторы оказывающие раздельное или совместное вредное воздействие на человека в условиях производства называются производственными вредностями. Результатом их отрицательных воздействий могут явиться профессиональные заболевания.
На производстве керамических кирпичей к физическим вредностям можно отнести повышенная запыленность воздушной среды и высокий уровень шума.
Пыль – это мельчайшие твердые частицы способные некоторое время находиться в воздухе или промышленных газах во взвешенном состоянии. Пыль образуется при транспортировке глиняной смеси и ее дальнейшей загрузке в глиносмеситель.
Пыль представляет собой гигиеническую вредность так как она отрицательно влияет на организм человека. Под воздействием пыли могут возникать такие заболевания как пневмокониозы экземы дерматиты конъюнктивиты и др.
Поведение пылевых частиц в воздухе связано с их скоростью витания. Скоростью витания частиц называют скорость их осаждения под действием силы тяжести в спокойном невозмущенном воздухе. Скорость витания используют в расчетах пылеулавливающих аппаратов как одну из основных характеристических величин.
Поскольку частицы пыли в большинстве своем имеют неправильную форму за размер частиц принимают их эквивалентный диаметр. Эквивалентный диаметр– это диаметр условной шарообразной частицы скорость витания которой равна скорости витания действительной пылевой частицы.
Концентрация пыли в реальных производственных условиях может составлять от нескольких мгм3 до сотен мгм3. Санитарными нормами (СН 245-71) установлены предельно допустимые концентрации (ПДК) пыли в воздухе рабочей зоны. В зависимости от химического состава пылей их ПДК колеблются в пределах от 1 до 10 мгм3.
Измерение концентрации пыли в воздухе чаще всего проводят весовым методом реже — счетным. Весовой метод основан на принципе получения привеса аналитического фильтра при пропускании через него определенного объема исследуемого воздуха. Аналитические фильтры типа АФА изготовленные из нетканого фильтрующего материала имеют высокую эффективность пылезадержания (около 100 %) и считаются «абсолютными». Для просасывания воздуха через фильтр используют специальные приборы — аспираторы.
Счетный метод основан на предварительном выделении пыли из воздуха с осаждением ее на покровные стекла и последующем подсчете числа частиц с помощью микроскопа. Концентрация пыли в этом случае выражается числом частиц приходящихся на единицу объема воздуха.
Весовой метод определения концентрации пыли является основным. Он стандартизован и применяется органами санитарного надзора для контроля качества воздушной среды на промышленных предприятиях.
В зависимости от природы сил действующих на взвешенные в газе пылевые частицы для их отделения от газового потока используют следующие типы пылеулавливающих аппаратов:
- сухие механические пылеуловители (взвешенные частицы отделяются от газа при помощи внешней механической силы);
- мокрые пылеуловители (взвешенные частицы отделяются от газа путем промывки его жидкостью захватывающей эти частицы);
- электрические пылеуловители (частицы пыли отделяются от газового потока под действием электрических сил);
- фильтры (пористые перегородки или слои материала задерживающие пылевые частицы при пропускании через них запыленного воздуха);
- комбинированные пылеуловители (используются одновременно различные принципы очистки).
По функциональному назначению пылеулавливающее оборудование подразделяют на два вида: 1) для очистки приточного воздуха в системах вентиляции и кондиционирования; 2) для очистки воздуха и газов выбрасываемых в атмосферу системами промышленной вентиляции.
Наиболее простыми по устройству и эксплуатации аппаратами являются пылеосадительные камеры в которых отделение частиц пыли от воздуха происходит под действием силы тяжести при прохождении воздуха через камеры. Эти устройства применяют для грубой очистки их эффективность пылеулавливния составляет 50 60 %. Скорость движения воздуха в камере выбирается из условия обеспечения ламинарного движения и обычно составляет 0.2 0.8 мс. Аэродинамическое сопротивление камер невысоко и равно 80 100 Па.
С целью повышения эффективности пылеулавливания камер они иногда разделяются по высоте полками которые могут периодически встряхиваться для очистки от оседающей пыли. Для этой же цели применяют пылеосадительные камеры лабиринтного типа.
Центробежные пылеотделители — циклоны — находят более широкое применение так как при сравнительно простой конструкции обеспечивают высокую степень обеспыливания воздуха (80 90%).
Циклон состоит из цилиндрического корпуса к которому тангенциально подведен входной патрубок; нижней конической части и выхлопного патрубка размещаемого внутри корпуса соосно с ним. Входя в циклон со скоростью 16 20 мс запыленный воздух приобретает вращательное движение и опускается вниз. При этом частицы пыли под действием сил инерции отбрасываются к стенкам аппарата и скользя по ним вниз попадают в бункер. Очищенный поток воздуха поворачивает вверх и через выхлопную трубу выходит из циклона.
Эффективность пылеулавливания возрастает с увеличением скорости входа воздуха в циклон однако при слишком большой скорости возрастает турбулизация воздушной среды и эффективность циклона падает. Максимальную скорость воздуха принимают обычно не более 20 мс. На эффективность этих аппаратов влияет и их диаметр: с его увеличением эффективность падает поэтому диаметр циклонов принимается не более 1 м.
Гидравлическое сопротивление циклонов колеблется в пределах 500 1100 Па. Оно зависит от конструкции аппарата и скорости воздуха на входе в него.
Окончательный выбор того или иного типа циклона должен определяться по технико-экономическим показателям. В тех случаях когда требуется очищать большие объемы воздуха применяют групповые циклоны. В них аппараты подсоединяются параллельно входными патрубками к общему трубопроводу и устанавливаются на один бункер больших размеров. Необходимым условием эффективной работы циклонов в этом случае является исключение возможности перетекания воздуха из одного циклона в другой.
Рукавные фильтры для улавливания сухих неслипающихся пылей нашли широкое применение в промышленности. Основными рабочими элементами этих устройств являются матерчатые рукава подвешиваемые к встряхивающему устройству и размещаемые в герметичном металлическом корпусе. Нижние открытые концы рукавов соединены с бункером. Воздух проходя через ткань рукавов оставляет на их поверхности пыль и удаляется из корпуса фильтра вентилятором. Накапливаясь на поверхности ткани в виде слоя пыль сама становится фильтрующей средой и увеличивает эффективность пылезадержания фильтра. Очистка ткани рукавов от осевшей пыли производится путем их встряхивания для чего устанавливается автоматически действующий встряхивающий механизм. Во многих типах фильтров встряхивание рукавов сочетается с обратной их продувкой с целью лучшей очистки от пыли. Фильтры выполняются многосекционными. При отключении одной из секций для очистки рукавов остальные продолжают работать. Фильтры бывают всасывающего и напорного типов.
Эффективность пылезадержания рукавных фильтров составляет 90 99 %. Воздушная нагрузка на ткань принимается в пределах 50 80 м3(м2ч). Гидравлическое сопротивление фильтра в зависимости от степени запыления рукавов колеблется в пределах 1 25 кПа.
Электрические фильтры находят широкое применение на предприятиях строительной индустрии для очистки воздуха и промышленных газов от пыли. В этих аппаратах отделение пылевых частиц от воздуха производится под воздействием статического электрического поля высокой напряженности. В металлическом корпусе стенки которых заземлены и являются осадительными электродами размещены коронирующие электроды соединенные с источником постоянного тока. Напряжение выпрямленного тока составляет 30 100 кВ.
Вокруг отрицательно заряженных электродов образуется электрическое поле. Проходящий через электрофильтр запыленный газ ионизируется вследствие чего приобретают отрицательные заряды и пылевые частицы. Последние начинают перемещаться к стенкам фильтра и оседая на них образуют плотный слой. Очистка осадительных электродов производится путем их остукивания или вибрации а иногда путем смыва водой.
Эффективность пылеулавливания электрофильтров высокая она достигает 999 %. Причем улавливаются частицы любых размеров включая субмикронные при их высоких концентрациях в газах достигающих 50 гм3. Преимуществами этих аппаратов являются низкое гидравлическое сопротивление 100 150 Па экономичность эксплуатации возможность очищать газы при их высоких температурах (до. 450°С).
Пылеуловители мокрого типа являются аппаратами глубокой очистки и отличаются высокой эффективностью пылеулавливания. Их применение целесообразно в том случае когда улавливаемая пыль хорошо смачивается водой не цементируется и не образует твердых трудно разрушаемых отложений.
При вращении потока из него под действием центробежных сил выделяются пылевые частицы которые удаляются со стенок аппарата стекающей сверху водой. Последняя подается на стенки аппарата через водоподающее кольцо и несколько тангенциально расположенных трубок и стекает по стенкам аппарата в виде сплошной водяной пленки. Образующийся шлам собирается в бункере.
Эффективность пылеулавливания циклонов с водяной пленкой составляет 99.0 99.5 % потери давления в аппарате равны 400 800 Па. При очистке от пыли агрессивных газов разрушающих металлические стенки аппарата последние с внутренней стороны армируются кислотостойкими покрытиями.
Высокими эксплуатационными показателями отличаются также пенные пылеуловители. Аппараты этого типа имеют цилиндрический металлический корпус внутри которого горизонтально размещена решетка. Вода подается на решетку через которую снизу пропускается очищаемый воздух. При этом на решетке образуется слой пены высота которого зависит от высоты сливной перегородки (порога). Обычно она составляет 80 100 мм. С целью снижения капельного уноса влаги в верхней части аппарата размещается каплеуловитель выполненный в виде решетки с лабиринтными каналами.
Для предупреждения загрязнения пылью воздушной среды в производственных помещениях и защиты работающих от ее вредного воздействия проводится следующий комплекс мероприятий.
Использование увлажненных сыпучих материалов. Применяется гидроорошение с помощью поворотной задвижки.
Тщательная и систематическая пылеуборка помещений с помощью вакуумных установок.
Очистка от пыли вентиляционного воздуха при его подаче в помещения и выбросе в атмосферу.
Применение в качестве индивидуальных средств защиты от пыли респираторов очков и противопыльной спецодежды.
Для очистки воздуха от пыли применяются циклоны типа НИИОГАЗ. На заводе по производству керамических кирпичей такие установки позволяют удалять отходы и пыль образующиеся при механической обработке глиняной смеси. Аспирационные установки успешно применяют при процессах размола транспортирования дозирования и смешения глиняной смеси.
4 Электробезопасность
Электротравмы составляют около 1 % от общего числа травм на производстве и 20 30 % от числа смертельных несчастных случаев. При этом большинство (до 80%) смертельных несчастных случаев происходит на электроустановках напряжением до 1000 В которые в основном и применяются в строительстве.
Предупреждение электротравм является важной задачей охраны труда которая на производстве реализуется в виде системы организационных и технических мероприятий обеспечивающих защиту людей от поражения электрическим током.
Степень опасного и вредного воздействия на человека электрического тока электрической дуги и электромагнитных полей зависит от:
- рода и величины напряжения и тока;
- частоты электрического тока;
- пути тока через тело человека;
- продолжительности воздействия электрического тока или электромагнитного поля на организм человека;
- условий внешней среды.
Нормы на допустимые токи и напряжения прикосновения в электроустановках должны устанавливаться в соответствии с предельно допустимыми уровнями воздействия на человека токов и напряжений прикосновения и утверждаться в установленном порядке.
Требования электробезопасности при воздействии электрических полей промышленной частоты по ГОСТ 12.1.002-91 при воздействии электромагнитных полей радиочастот по ГОСТ 12.1.006-91.
Электробезопасность должна обеспечиваться:
- конструкцией электроустановок;
- техническими способами и средствами защиты;
- организационными и техническими мероприятиями.
Электроустановки и их части должны быть выполнены таким образом чтобы работающие не подвергались опасным и вредным воздействиям электрического тока и электромагнитных полей и соответствовать требованиям электробезопасности.
Требования (правила и нормы) электробезопасности к конструкции и устройству электроустановок должны быть установлены в стандартах Системы стандартов безопасности труда а также в стандартах и технических условиях на электротехнические изделия.
Технические способы и средства защиты обеспечивающие электробезопасность должны устанавливаться с учетом:
а) номинального напряжения рода и частоты тока электроустановки;
б) способа электроснабжения (от стационарной сети от автономного источника питания электроэнергией);
в) режима нейтрали (средней точки) источника питания электроэнергией (изолированная заземленная нейтраль);
г) вида исполнения (стационарные передвижные переносные);
д) условий внешней среды:
- особо опасные помещения
- помещения повышенной опасности
- помещения без повышенной опасности
- на открытом воздухе.
е) возможности снятия напряжения с токоведущих частей на которых или вблизи которых должна производиться работа;
ж) характера возможного прикосновения человека к элементам цепи тока:
- однофазное (однополюсное) прикосновение
- двухфазное (двухполюсное) прикосновение
- прикосновение к металлическим нетоковедущим частям оказавшимся под напряжением;
з) возможности приближения к токоведущим частям находящимся под напряжением на расстояние меньше допустимого или попадания в зону растекания тока;
и) видов работ: монтаж наладка испытание эксплуатация электроустановок осуществляемых в зоне расположения электроустановок в том числе в зоне воздушных линий электропередачи.
Требования безопасности при эксплуатации электроустановок на производстве должны устанавливаться нормативно-технической документацией по охране труда утвержденной в установленном порядке.
Требования безопасности при пользовании электроустановками бытового назначения должны содержаться в прилагаемых к ним инструкциях по эксплуатации предприятий-изготовителей.
Для обеспечения защиты от случайного прикосновения к токоведущим частям необходимо применять следующие способы и средства:
- защитные оболочки;
- защитные ограждения (временные или стационарные);
- безопасное расположение токоведущих частей;
- изоляция токоведущих частей (рабочая дополнительная усиленная двойная);
- изоляция рабочего места;
- защитное отключение;
- предупредительная сигнализация блокировка знаки безопасности.
Для обеспечения защиты от поражения электрическим током при прикосновении к металлическим нетоковедущим частям которые могут оказаться под напряжением в результате повреждения изоляции применяют следующие способы:
- защитное заземление;
- выравнивание потенциала;
- система защитных проводов;
- изоляция нетоковедущих частей;
- электрическое разделение сети;
- контроль изоляции;
- компенсация токов замыкания на землю;
- средства индивидуальной защиты.
Технические способы и средства применяют раздельно или в сочетании друг с другом так чтобы обеспечивалась оптимальная защита.
Требования к техническим способам и средствам защиты должны быть установлены в стандартах и технических условиях.
Провода и кабели применяемы на заводе относятся к серии ВВГ (кабели силовые с медной жилой с ПВХ изоляцией) ГОСТ 16442-80. Применяются для передачи и распределения электроэнергии в стационарных установках на номинальное переменное напряжение 660 В и 1000 В частоты 50 Гц.
Для прокладки в сухих и влажных производственных помещениях на специальных кабельных эстакадах в блоках а также для прокладки на открытом воздухе. Кабели не рекомендуются для прокладки в земле (траншеях).
Изоляция – ПВХ пластикат. Изолированные жилы кабелей имеют отличительную расцветку. Изоляция нулевых жил выполняется голубого цвета. Изоляция жил заземления выполняется зелено-желтой расцветки. Жила – медная класса 1 или 2. Оболочка – ПВХ пластикат без защитного покрова.
Кабели предназначены для эксплуатации в стационарном состоянии при температуре окружающей среды от -50 до +50 °С относительной влажности воздуха до 98% при температуре до 35 °С в том числе для прокладки в земле и на воздухе.
Кабели марки ВВГ не распространяют горение при одиночной прокладке.
Прокладка и монтаж кабелей без предварительного подогрева производится при температуре не ниже: – 15 °С.
Основными методами защиты персонала от поражения электрическим током являются: защитное заземление зануление и защитное отключение.
Защитное заземление – преднамеренное электрическое соединение с землей или ее эквивалентом металлических нетоковедущих частей которые могут оказаться под напряжением вследствие замыкания на корпус и по другим причинам (индуктивное влияние соседних токоведущих частей вынос потенциала разряд молнии и т. п.).
Тип заземляющего устройства – выносное.
Выносное заземляющее устройство характеризуется тем что заземлитель вынесен за пределы площадки на которой размещено заземляемое оборудование или сосредоточен на некоторой части этой площадки. Поэтому выносное заземляющее устройство называют также сосредоточенным.
Зануление – это преднамеренное электрическое соединение открытых проводящих частей электроустановок с глухозаземленной нейтральной точкой генератора или трансформатора в сетях трехфазного тока с глухозаземленным выводом источника однофазного тока с заземленной точкой источника в сетях постоянного тока выполняемое в целях электробезопасности.
Для соединения открытых проводящих частей потребителя электроэнергии с глухозаземленной нейтральной точкой источника используется нулевой защитный проводник.
Зануление необходимо для обеспечения защиты от поражения электрическим током при косвенном прикосновении за счет снижения напряжения корпуса относительно земли и быстрого отключения электроустановки от сети.
В качестве максимальной токовой защиты обеспечивающей быстрое отключение электроустановки в аварийном режиме используются автоматические выключатели устанавливаемые для защиты от токов короткого замыкания магнитные пускатели со встроенной тепловой защитой контакторы в сочетании с тепловыми реле осуществляющие защиту от перегрузки.
Защитным отключением называется автоматическое отключение электроустановок при однофазном (однополюсном) прикосновении к частям находящимся под напряжением недопустимым для человека и (или) при возникновении в электроустановке тока утечки (замыкания) превышающего заданные значения.
Назначение защитного отключения – обеспечение электробезопасности что достигается за счет ограничения времени воздействия опасного тока на человека. Защита осуществляется специальным устройством защитного отключения (УЗО) которое работая в дежурном режиме постоянно контролирует условия поражения человека электрическим током.
Принцип работы УЗО состоит в том что оно постоянно контролирует входной сигнал и сравнивает его с наперед заданной величиной (уставкой). Если входной сигнал превышает уставку то устройство срабатывает и отключает защищенную электроустановку от сети. В качестве входных сигналов устройств защитного отключения используют различные параметры электрических сетей которые несут в себе информацию об условиях поражения человека электрическим током.
Неизолированные токоведущие части (провода) закрепленные на изоляторах располагают на определенной высоте где они недоступны для случайного прикосновения или их закрывают крышками кожухами например в местах соединительных зажимов электродвигателей в распределительных устройствах. Если ограждения изготовляют из диэлектриков или металла то их располагают на определенном расстоянии от неизолированных токоведущих частей величина которого зависит от напряжения установки. Наименьшее расстояние для установок напряжением до 1000 В составляет 50 мм; 6000 В – 120 мм 10000 В – 150 мм.
5 Требования безопасности при обслуживании конвейеров
Общие требования техники безопасности к конструкции размещению конвейеров всех видов и назначений применяемых в любой отрасли народного хозяйства регламентированы ГОСТ 12.2.022-80. Особое внимание уделяется следующим требованиям:
Движущиеся части конвейеров (приводные натяжные и отклоняющие барабаны натяжные устройства опорные ролики ременные и другие передачи) к которым возможен доступ обслуживающего персонала и лиц работающих в близи конвейеров должны быть ограждены;
При обрабатывании все конвейеры следует пускать незагружаемыми. Если при этом не обнаружится каких либо недостатков начинают их постепенную нагрузку. Во время пробного пуска должна быть проверена правильность работы всех частей и механизмов и все обнаруженные недостатки необходимо устранить;
Запрещается останавливать конвейеры до их полного освобождения от транспортируемого материала за исключением аварийных ситуаций;
Запрещается очистка ремонт и регулировочные работы во время работы конвейеров и пуск без предварительного сигнала;
Электродвигатели и металлические конструкции работающих конвейеров должны быть надежно заземлены;
Для обеспечения нормальной работы ленточных конвейеров необходимо:
- Систематически вести наблюдение за работой роликоопор периодически смазывать их подшипники неисправные и не вращающиеся ролики немедленно заменить;
- Систематически осуществлять регулирование движения ленты и не допускать ее смещения в сторону;
- Постоянно наблюдать за работой натяжных устройств очищать направляющие подвижных подшипников натяжных барабанов регулярно осматривать загрузочные воронки разгрузочные и очищающие устройства.
Запрещается остановка ленточных конвейеров до полного опорожнения (за исключением аварийных случаев) очистка и ремонт во время движения пуск без предварительного сигнала попытка предотвращения сбегания ленты на сторону установкой упоров и буксования ленты на приводном барабане подсыпанием канифоли песка и прочее;
Перемещение передвижных конвейеров должно осуществляться под руководством производителя работ или мастера;
Ленточные конвейеры предназначенные для транспортирования влажных и липких грузов должны иметь устройства для очистки от налипшего материала с обеих сторон.
Требования безопасности при монтажных ремонтных и очистных работах
На все виды работ при текущем и капитальном ремонте монтаже демонтаже и очистке оборудования связанных с пребыванием работающих в газоходах пылеосадительных камерах холодильниках сушильных барабанах грохотах вращающихся печах грануляторах вакуум-фильтрах должен быть разработан проект производства работ (ППР) с указанием схемы строповки деталей узлов оборудования и выдан наряд-допуск на их выполнение.
Прием вращающихся печей и сушильных барабанов после монтажных работ должен производиться в соответствии с требованиями «Строительных норм и правил. Правил производства и приемки работ» и технической документации предприятия-изготовителя.
Ремонтные и очистные работы внутри пылеосадительных камер газоходов сушильных барабанов вращающихся печей должны производиться при температуре воздуха в них не выше 33°С. Для увеличения воздухообмена применять переносные вентиляционные установки.
При внутреннем осмотре и ремонте газоходов пылеосадительных камер и оборудования должны применяться переносные электрические светильники в пыленепроницаемом исполнении напряжением не выше 12 B.
Пылеосадительные камеры и бункера должны быть оборудованы механическими ворошителями шуровками электровибраторами.
Обрушение наростов пыли и шлама должно производиться без допуска людей внутрь камер и бункеров.
Администрация предприятия должна обеспечить рабочих выполняющих очистные работы комплектом приспособлений и инструментов.
Погрузочно-разгрузочные работы связанные с монтажом и демонтажом оборудования должны производиться в соответствии с требованиями «Правил устройства и безопасной эксплуатации грузоподъемных кранов» утвержденных Госгортехнадзором России ГОСТ 12.3.009-82 ГОСТ 12.3.020-89.
Сварочные работы связанные с ремонтом оборудования должны выполняться в соответствии с требованиями ГОСТ 12.3.003-89 и «Правил пожарной безопасности при проведении сварочных и других огневых работ на объектах народного хозяйства».
6 Требования к средствам защиты
Движущиеся части конвейеров (приводные натяжные и отклоняющие барабаны натяжные устройства канаты и блоки натяжных устройств ременные и другие передачи муфты и т. п. а также опорные ролики и ролики нижней ветви ленты) должны быть ограждены в зонах постоянных рабочих мест связанных с технологическим процессом на конвейере или по всей трассе конвейера если имеет место свободный доступ или постоянный проход вблизи конвейера лиц не связанных с обслуживанием конвейера.
Защитные ограждения должны быть снабжены приспособлениями для надежного удержания их в закрытом (рабочем) положении и в случае необходимости быть сблокированы с приводом конвейера для его отключения при снятии (открытии) ограждения.
Ограждения следует изготовлять из металлических листов сетки и других прочных материалов. В сетчатых ограждениях размер ячейки должен быть выбран таким чтобы исключался доступ к огражденным частям конвейера.
В зоне возможного нахождения людей должны быть ограждены или защищены:
- смотровые люки пересыпных лотков бункеров и т. п. установленных в местах загрузки и разгрузки конвейеров периодически очищаемые обслуживающим персоналом;
- проходы (проезды) под конвейерами сплошными навесами выступающими за габариты конвейеров не менее чем на 1 м;
- участки трассы конвейеров (кроме подвесных конвейеров) на которых запрещен проход людей при помощи установки вдоль трассы перил высотой не менее 10 м от уровня пола.
Конвейеры передвигающиеся по рельсам если они не закрыты специальными кожухами и конвейеры установленные в производственных зданиях ниже уровня пола должны быть ограждены по всей длине перилами высотой не менее 10 м от уровня пола.
Перила ограждающие конвейеры установленные ниже уровня пола должны быть закрыты на высоту не менее 015 м от уровня пола.
На конвейерах входящих в автоматизированные транспортные или технологические линии должны быть предусмотрены устройства для автоматической остановки привода при возникновении аварийной ситуации.
На технологической линии состоящей из нескольких последовательно установленных и одновременно работающих конвейеров или из конвейеров в сочетании с другими машинами (питателями дробилками и т. п.) приводы конвейеров и всех машин должны быть сблокированы так чтобы в случае внезапной остановки какой-либо машины или конвейера предыдущие машины или конвейеры автоматически отключались а последующие продолжали работать до полной разгрузки транспортируемого груза.
Конвейеры малой протяженности (до 10 м) в головной и хвостовой частях должны быть оборудованы аварийными кнопками для остановки конвейера. Конвейеры большой протяженности должны быть дополнительно оборудованы выключающими устройствами для остановки конвейера в аварийных ситуациях в любом месте. При оснащении всей трассы конвейеров тросовым выключателем дающим возможность остановки конвейеров с любого места аварийные кнопки для остановки конвейера в головной и хвостовой частях допускается не устанавливать.
В схеме управления конвейерами должна быть предусмотрена блокировка исключающая возможность повторного включения привода до ликвидации аварийной ситуации.
На участках трассы конвейеров находящихся вне зоны видимости оператора с пульта управления должна быть установлена двусторонняя предупредительная предпусковая звуковая или световая сигнализация включающаяся автоматически до включения привода конвейера. Двусторонняя сигнализация должна обеспечивать не только оповещение о пуске конвейера лиц находящихся вне зоны видимости с пульта управления конвейером но и подачу ответного сигнала на пульт управления с участков трассы невидимых оператору о готовности конвейера к пуску. При отсутствии постоянных рабочих мест на трассе конвейера предусматривать подачу ответного сигнала не требуется.
На рабочих местах должны быть помещены таблички поясняющие значения применяемых средств сигнализации и порядок управления конвейером.
Конвейеры транспортирующие горячие грузы должны иметь средства защиты обслуживающего персонала от ожогов.
Конвейеры предназначенные для транспортирования пылевидных пыле- паро- и газовыделяющих грузов должны снабжаться пылеподавляющими или пылеулавливающими системами в местах выделения пыли отводами к местной вытяжной вентиляции в местах выделения пара или местными отсосами для подключения абсорбционных устройств в местах выделения газа.
Конвейеры предназначенные для транспортирования мокрых грузов должны быть закрыты кожухами или щитами в местах возможного брызгообразования.
Места периодической смазки конвейеров должны быть доступны без снятия защитных устройств.
7 Контроль выполнения требований безопасности
Контроль выполнения требований безопасности должен проводиться:
- при проверке конструкторской документации на конвейеры и их размещение;
- после изготовления конвейеров транспортируемых в собранном виде предприятием-изготовителем при приемочных испытаниях;
- после окончания монтажа наладки и обкатки вновь устанавливаемых конвейеров;
- после аналогичных работ вызванных переносом на другое место конвейера или расширением конвейерной линии;
- после капитального ремонта и реконструкции конвейеров.
Контроль должен включать проверку конвейеров внешним осмотром и замером контролируемых параметров как в нерабочем так и в рабочем состоянии.
Методы определения шумовых характеристик конвейеров — по ГОСТ 12.1.026-80 — ГОСТ 12.1.028-80.
Измерение вибрации — по ГОСТ 12.1.012—90.
6 Технико-экономический расчет.doc
Расчет капитальных вложений по базовому варианту [15]:
Объем капитальных вложений рассчитывается по формуле:
где КМ – капитальные вложения на монтаж и установку оборудования; КОБ – капитальные вложения на оборудование рассчитывается по формуле:
где ЦОБ = 15000 – цена оборудования в год приобретения руб.; КВО = 2685 – коэффициент пересчета цен на дату проекта; СПР = 1 – принятое число комплексов.
где а = 12 – коэффициент учитывающий затраты на доставку и монтаж оборудования.
Расчет издержек производства по базовому варианту:
где ИЗ – годовая зарплата рабочих по обслуживанию установки руб; ИР – годовые затраты на ремонт основных фондов руб.; ИЭ – затраты на электроэнергию комплекса руб.
где ЗСМ = 12000 – среднемесячная зарплата рабочих руб.; Р = 2 – общее число рабочих на установке чел.
ИЗ = 12000 12 2 = 288000 руб.
где ТЭ = 232 – тариф за 1 кВт в час руб.; WГР – годовой расход электроэнергии кВт находится по формуле:
где РА = 23 – активная мощность кВт; ФЕ = 3840 – действительный фонд времени работы участка ч.; КМ = 075 – коэффициент загрузки по времени; КВ = 08 – коэффициент загрузки по мощности.
WГР = 23 3840 075 08 = 52992 кВтч.
ИЭ = 232 52992 = 1229414 руб.
ИП-ВА = 288000 + 8055 + 1229414 = 4189964 руб.
Амортизационные отчисления:
где Р = 0053 – коэффициент амортизационных отчислений.
А = 0053 40275 = 213457 руб.
Найдем приведенные общие эксплуатационные затраты
где ПБ = 35856 - годовая производительность(в 2010 году 249 рабочих дней).
Удельные капитальные вложения определяем по формуле
ИЭ = 232 68400 = 158688 руб.
ИП-ВА = 144000 + 1166528 + 158688 = 4193408 руб.
А = 0053 583264= 3091299 руб.
где П = 48000 - годовая производительность шт.
Расчет экономической эффективности проекта:
Для установления эффективности проектируемого производства сравниваем показатели рассчитанные выше:
Величина издержек производства проекта и базового варианта определяется по формуле:
Годовой экономический эффект от реализации проекта в производство определяется по разности приведенных затрат:
Срок окупаемости проекта:
ТОК = (КБ - КП) Эг = (6415904 – 48330)114720 = 39 (5.7.13)
Таблица 5.7.1 – Технико-экономические показатели базового и проектного варианта
Наименование показателей
Объем капитальных вложений
Затраты энергоресурсов
Амортизационные отчисления на оборудование
Приведенные общие эксплуатационные затраты
Годовой экономический эффект
5 надежность.doc
К технологическим методам повышения долговечности деталей машин относятся мероприятия по улучшению свойств материалов при формообразовании применение термической и химико-термической обработки. В таблице 5.1 указаны причины выхода деталей машин из строя и способы повышения их долговечности.
Качество детали от которого зависит ее долговечность начинает формироваться еще на стадии получения заготовки и продолжает изменяться при дальнейшем изготовлении. Долговечность деталей работающих в условиях циклических нагрузок имеющих их концентраторы напряжений значительно повышается в результате поверхностного наклепа. Например при обработке дробью рессор транспортных машин полуосей автомобилей зубчатых колес и других деталей срок их службы увеличивается в 25 раза; при обкатке роликами усталостная прочность коленчатых валов из высокопрочных чугунов повышается до 200% а предел выносливости зубчатых колес тепловозов – на 50%; при чеканке галтелей достигается равнопрочность участков ступенчатых валов в результате чего их долговечность повышается в 15 раза. Повышение предела выносливости деталей с концентратором напряжений а также повышение износостойкости достигается в процессе гидроструйного наклепывания. Механические свойства всего объема металла повышаются при упрочнении взрывом.
Таблица 5.1 – Причины выхода деталей машин из строя и способы повышения их долговечности
Наименование деталей
Омновные виды повреждения в процессе эксплуатации
Способы повышения долговечности
Изгиб зубьев деформации контактного сжатия и сдвига рабочих поверхностей зубьев трение
Излом зуба (усталостный или из-за кратковременной перегрузки) усталостное выкрашивание изнашивание или пластическая деформация рабочих поверхностей
Корригирование улучшение сплошная или поверхностная закалка зубьев цементация азотирование нитроцементация рабочих поверхностей
Червяк и червячное колесо
Скольжение витков червяка по рабочим поверхностям зубьев червячного колеса
Заедание изнашивание рабочих поверхностей пластическая деформация и излом червячного колеса
Корригирование зубьев червячного колеса. Повышение класса чистоты закалка или цементация рабочих поверхностей витков червяка
Звёздочки цепных передач
Удары и трение рабочих поверхностей звёздочек об элементы цепи
Изнашивание рабочих поверхностей зубьев
Применение звёздочек с вогнутым профилем зубьев повышение класса чистоты закалка или цементация рабочих поверхностей зубьев
Деформация изгиба и кручения трение скольжения между цапфой и опорой
Усталостные изломы изнашивание и задиры цапф заедание
Уменьшение влияния концентраторов напряжений шлифование цапф поверхностный
наклёп галтели поверхностная закалка азотирование
Качение шариков (роликов) по наружному и внутреннему кольцам
Разрушение тел качения и излом колец изнашивание заедание усталостное выкрашивание поверхностей деталей подшипника
Обеспечение податливости корпуса в нагруженной части подшипника
Болты и шпильки резьбовых соединений
Статические напряжения от предварительной затяжки переменные во времени напряжения перегрузок
Усталостные изломы деформация
Повышение прочности стали уменьшение концентрации напряжений жёсткости болта повышение класса чистоты поверхности болта накатка резьбы болта роликами
Рассчитаем интенсивность отказов компонентов системы автоматического управления для этого изобразим устройства входящие в систему управления:
Рисунок 5.1 – Структура для расчета надежности автоматической системы
Зададимся начальными данными:
- интенсивность отказов задатчика (кнопки);
- интенсивность отказов регулятора;
- интенсивность отказов контакоров;
- интенсивность отказов двигателей;
- интенсивность отказов датчиков.
Интенсивность отказов находится по формуле:
Рассчитаем вероятность отказов системы для этого зададимся интервалом времени
Рисунок 5.1 – Вероятность отказов системы
Рассчитаем время наработки на отказ:
2 Механизация.doc
1 Расчет и выбор механического оборудования для линейных конвейеров
Для расчета механического оборудования зададимся исходными данными:
Расчетная производительность ;
Плотность материала:
Угол наклона конвейера ;
Скорость транспортирования ;
1.1 Определение ширины ленты и округления до ближайшего стандартного значения.
Предварительно ширину ленты можно получить из следующего выражения:
- производительность конвейера кгс;
- коэффициент производительности зависящий от формы поперечного сечения грузового потока для желобчатой ;
- коэффициент уменьшения производительности в зависимости от угла наклона конвейера при (таблица 7)
- насыщенная плотность груза
- скорость конвейера мс
Выбираем стандартную ленту шириной .
После выбора ширины ленты уточняем скорость конвейера по формуле:
1.2Определение распределенных нагрузок при работе ленточного конвейера
Расчетные распределения массы приходящей на 1 м длины ленты и вращающих частей роликовых опор груженой и холостой ветвей определяем ориентировочно по таблице 4.
Для гипса и песка одиноковые.
Распределенная масса груза рассчитывается по формуле:
1.3 Тяговый расчет ленточных конвейеров
Контур трассы конвейера разбиваем на отдельные участки которые имеют характерный вид изменения сопротивления перемещению ленты и груза.
Тяговый расчет выполнен методом обхода по контуру конвейера начав расчет натяжений ленты с точки сбегания ленты с приводного барабана.
Предположим что минимальная сила натяжения ожидается в точке 1 с которой и начинаем тяговый расчет. Наименьшая сила натяжения ленты равна предварительному натяжению ленты по формуле:
В ленточных конвейерах невозможно задать предварительное натяжение так как оно зависит от тяговой силы на ведущем барабане которая находится только после тягового расчета. Оставим пока численное значение неизвестным и будем выражать натяжение ленты в последующих точках.
Сила натяжения ленты в точке 2 (набегания холостой ветви на отклоняющий барабан) будет складываться из силы натяжения и сопротивлений движения ленты по холостым роликовым опорам на участке 1-2 длинной по формуле:
где - коэффициент сопротивления движению ленты при тяжелых условиях работы ;
Сила натяжения ленты в точке 3 (схода ленты с отклоняющего барабана)
где - коэффициент увеличения силы натяжения при огибании барабана при угле обхвата менее 90°;
Натяжение ленты в точке 4
Сопротивление включает составляющие связанные с преодолением силы трения на роликовых опорах и веса ленты на участке 3-4 :
Знак «+» ставится при движении ленты на подъеме а знак «–» при движении ленты на спуск.
Сила натяжения в точке 5 (сбегания ленты с концевого барабана)
где - коэффициент увеличения силы натяжения при огибании барабана при угле обхвата менее 180°.
Сила натяжения ленты в точке 6 (точке загрузки материала на ленту)
Сопротивление при загрузке материала на ленту зависит от производительности Q скорости ленты начальной скорости груза и других факторов. При выборе и проектировании загрузочного устройства следует стремится к тому чтобы тогда и в этом случае:
Сила натяжения ленты в точке 7
Сила натяжения ленты в точке 8
где - коэффициент увеличения силы натяжения при огибании барабана при угле обхвата менее 90°.
Сила натяжения в точке 9 набегания ленты на приводной барабан:
Для получения натяжения используют формулу Эйлера
она связывает натяжение набегающей и сбегающей ветви ленты:
1.4 Расчет приводов конвейеров
Привод представлен в приложении 1 рис. 5.
Окружная (тяговая) сила на приводном барабане конвейера:
Применив предварительное значение КПД привода конвейера определим потребляемую мощность двигателя конвейера по формуле:
Для конвейеров с гипсом и песком выбираем два одинаковых двигателя АИР80А2 с мощностью Вт и частотой вращения .
Диаметр приводного барабана при использовании резинотканевой ленты рассчитывается по формуле:
где – коэффициент зависящий от типа барабана для приводного для натяжного для отклоняющего
– коэффициент зависящий от прочности тканевых прокладок (таблица8)
ммшт (меньшее значение применяется для лент малой ширины)
Диаметр барабана округляем до мм.
Диаметр натяжного барабана при принимаем равным 420 мм.
Производим кинематический расчет. Определяем частоту вращения приводного барабана по формуле:
Передаточные числа привода для каждого табличного значения частоты вращения электродвигателя находим по формуле:
Вращающий момент на валу приводного барабана конвейера:
где - тяговая сила кН;
Выбираем типоразмер редуктора характеристика которого соответствует требуемому передаточному числу и вращающему моменту с учетом 25% запаса т.е.:
Для обоих конвейеров выбираем редуктор Ц2У-125 с передаточным числом ; вращающий момент на тихоходном валу 500 Нм.
Уточняем скорость ленты
что вполне допустимо.
1.5 Расчет натяжных устройств
В качестве натяжного устройства используем грузовые тележечного типа расчет который сводиться к определению веса груза подвешенного к натяжному барабану конвейера.
где Кн- коэффициент запаса силы натяжения учитывающий сопротивление передвижению тележки; Кн= 12 .15;
- натяжение соответственно набегающей с натяжного барабана ветвей ленты.
Величину полученного груза обеспечат 12 единичных чугунных грузов размерами в плане 730×140мм общей высотой 840мм
Ход натяжного барабана
где В- ширина ленты м
Z- общая длина конвейера
2 Расчет и выбор механического оборудования для галерейного конвейера
Плотность материала ;
2.1 Определение ширины ленты и округления до ближайшего стандартного значения.
где - производительность конвейера кгс;
2.2Определение распределенных нагрузок при работе ленточного конвейера
2.3Тяговый расчет галерейного конвейера
Рисунок 2.2.1 – Схема трассы ленточного конвейера
где - коэффициент сопротивления движению ленты при тяжелых условиях работы (таблиц 5).
2.4Расчет (выбор) привода конвейера
Выбираем двигатель АИР112МВ6 с мощностью Вт и частотой вращения .
где – коэффициент зависящий от типа барабана для приводного для натяжного для отклоняющего
Диаметр натяжного барабана при принимаем равным 480 мм.
где - тяговая сила кН
Из приложения выбираем типоразмер редуктора характеристика которого соответствует требуемому передаточному числу и вращающему моменту с учетом 25% запаса т.е.:
Редуктор Ц3У-160 с передаточным числом ; вращающий момент на тихоходном валу 1000 Нм.
Уточняем скорость ленты:
2.5 Расчет натяжного устройства.
Величину полученного груза обеспечат 12 единичных чугунных грузов размерами в плане 730×140мм общей высотой 840мм (таблица 8)
Список используемых источников.doc
Алиев И.И. Справочник по электротехники и электрооборудованию. Ростов нД: Феникс 2004. - 480 с.
Анурьев В.И. Справочник конструктора-машиностроителя. Том 123. М.: Машиностроение 1979. – 727 с.
Белов М.П. Новиков В.А. Рассудов Л.Н. Автоматизированный электропривод типовых производственных механизмов и технологических комплексов. М.: Академия 2004. - 576 с.
Галицков С.Я. Галицков К.С. Масляницын А.П. Динамика асинхронного двигателя. Учебное пособие. Самара: СГАСУ 2002. – 104 с.
Герман-Галкин С.Г. Компьютерное моделирование полупроводникоковых систем в MATLAB 6.0. СПб.: КОРОНА принт 2001. – 320 с.
Строительные материалы: Справочник А.С. Болдырев П.П. Золотов А.Н. Люсов и др. – М.: Стройиздат 1989. – 567 с.: ил.
Детали машин. Проектирование: учебное пособие. Л.В.Курмаз А.Т.Скойбеда - 2-е издание испр. и доп. – Мн.: УП Технопринт” 2002. - 290 с.
Титульный.doc
РОССИЙСКОЙ ФЕДЕРАЦИИ
САМАРСКИЙ ГОСУДАРСТВЕННЫЙ
АРХИТЕКТУРНО - СТРОИТЕЛЬНЫЙ УНИВЕРСИТЕТ
Факультет: СТРОИТЕЛЬНО – ТЕХНОЛОГИЧЕСКИЙ
Кафедра: МЕХАНИЗАЦИЯ АВТОМАТИЗАЦИЯ и ЭНЕРГОСНАБЖЕНИЕ СТРОИТЕЛЬСТВА
УТВЕРЖДАЮДОПУСТИТЬ К ЗАЩИТЕ
Декан СТФ Зав. кафедрой
Д И П Л О М Н Ы Й П Р О Е К Т
«Механизация и автоматизация поддержания соотношения гипса и песка при производстве ячеистого бетона»
ПОЯСНИТЕЛЬНАЯ ЗАПИСКА
СГАСУ 270113 – 10.20.01
ПодписьДатаИнициалы фамилия
Заключение.doc
В данном дипломном проекте была рассмотрена автоматическая система управления по поддержанию соотношения гипса и песка при производстве ячеистого бетона. Данная система позволяет смешивать компоненты бетонной смеси в той пропорции необходимой для выпуска качественной отвечающей всем требованиям продукции.
Целью этой работы является создание системы которая позволяла бы управлять участком смешения компонентов бетонной смеси без участия человеческого фактора и повышения выпуска готовой продукции.
Содержание .doc
2 Классификация конвейеров
2 Основные типы конвейеров
Раздел № 2. Механизация участка поддержания соотношения гипса и песка
1 Расчет и выбор механического оборудования для линейных конвейеров
1.1 Определение ширины ленты и округления до ближайшего стандартного значения.
1.2Определение распределенных нагрузок при работе ленточных конвейеров
1.3 Тяговый расчет ленточных конвейеров
1.4 Расчет приводов конвейеров
1.5 Расчет натяжных устройств
2 Расчет и выбор механического оборудования для галерейного конвейера
2.1 Определение ширины ленты и округления до ближайшего стандартного значения.
2.2 Определение распределенных нагрузок при работе конвейера
2.3 Тяговый расчет галерейного конвейера
2.4 Расчет привода конвейера
2.5 Расчет натяжного устройства
Раздел № 3. Энергоснабжение
1 Начальные данные для расчета электрических нагрузок групп цеха.
2 Проектирование осветительных установок
4 Расчет электрических нагрузок освещения
5 Расчет схемы силовой сети цеха
6 Выбор сечений кабелей питающих отдельные электроприемники
7 Расчет токов короткого замыкания
8 Расчет заземляющего устройства
9 Схема электроснабжения планировка участка
Раздел № 4. Автоматизация участка поддержания соотношения гипса и песка
1 Определение объекта автоматизации. Цель автоматизации. Создание системы для поддержания соотношения гипса и песка
2. Объект управления. Его входные и выходные координаты
3 Математическое описание конвейеров как ОУ
4 Расчетная и вычислительная модели ОУ
5 Алгоритм работы участка по поддержанию соотношения гипса и песка
6 Техническая реализация
Раздел № 5. Надежность
1 Меры по повышению надежности
Раздел № 6. Технико-экономическое обоснование
Раздел № 7. Техника безопасности
1 Задачи в области обеспечения безопасности труда
2 Обеспечение нормальных параметров микроклимата на участке по поддержанию соотношения гипса и песка
3 Оценка вредности пыли и средства защиты работающего персонала от неё
4 Электробезопасность
5 Требования безопасности при обслуживании конвейеров
6 Требования к средствам защиты
7 Контроль выполнения требований безопасности
Раздел № 8. Охрана окружающей среды
Список используемых источников
8 Охрана окружающей среды.doc
Меры и средства защиты окружающей среды на заводах ЖБИ регламентируют санитарные правила и нормы СанПиН 2.2.12.1.1.1200 – 03 устанавливают гигиенические требования к размеру санитарно-защитных зон в зависимости от санитарной классификации предприятий сооружений и иных объектов требования к их организации и благоустройству основания к пересмотру этих размеров.
Санитарные правила предназначены для органов государственной исполнительной власти и органов местного самоуправления предприятий организаций учреждений специалистов деятельность которых связана с проектированием строительством и эксплуатацией объектов а также осуществлением государственного экологического контроля и государственного санитарно-эпидемиологического надзора.
Предприятия их отдельные здания и сооружения с технологическими процессами являющимися источниками выделения в окружающую среду вредных и (или) пахучих веществ а также источниками шума вибрации инфразвука электромагнитных волн радиочастот статического электричества необходимо отделять от жилой застройки санитарно-защитными зонами.
Санитарно-защитная зона является обязательным элементом любого промышленного предприятия и других объектов которые могут быть источниками химического биологического или физического воздействия на окружающую среду и здоровье человека.
Санитарно-защитная зона — территория между границами промплощадки складов открытого и закрытого хранения материалов и реагентов предприятий сельского хозяйства с учетом перспективы их расширения и селитебной застройки.
Санитарно-защитная зона предназначена для:
)обеспечения требуемых гигиенических норм содержания в приземном слое атмосферы загрязняющих веществ уменьшения отрицательного влияния предприятий транспортных коммуникаций линий электропередач на окружающее население факторов физического воздействия — шума повышенного уровня вибрации инфразвука электромагнитных волн и статического электричества;
)создания архитектурно-эстетического барьера между промышленностью и жилой частью при соответствующем ее благоустройстве;
)организации дополнительных озелененных площадей с целью усиления ассимиляции и фильтрации загрязнителей атмосферного воздуха а также повышения активности процесса диффузии воздушных масс и локального благоприятного влияния на климат.
Складское помещение относится к предприятиям класса размер санитарно-защитной зоны которых должен составлять не менее 300 м.
Санитарно-защитная зона составляет около 300 м площадь озеленения санитарно-защитной зоны составляет почти 60 % ее территории. Зеленые насаждения являются биофильтром обогащают воздух кислородом отфильтровывают вредные примеси частично нейтрализуют вредные промышленные выбросы поглощают шум неприятные запахи и др. Растительность санитарно-защитной зоны представлена травой кустарниками деревьями (тополь клен ясень береза). Древесная растительность задерживает пыль очищая воздух от нее. На листве оседает до 72 % взвешенных в воздухе частиц. В течение вегетационного периода деревья уменьшают запыленность на 42 % а в остальной период - на 375 %. Подсчитано что 1 га леса очищает в год 18 млн. м3 воздуха. В санитарно-защитной зоне расположены гаражи складские и торговые помещения.
Производства строительных материалов представляют собой сложные технологические процессы связанные с превращением сырья в разные состояния и с различными физико-механическими свойствами а также с использованием разнообразной сложности технологического оборудования и вспомогательных механизмов. Во многих случаях эти процессы сопровождаются выделением больших количеств полидисперсной пыли вредных газов и других загрязнений. Когда отдельные технологические аппараты надежно герметизированы выделения вредных веществ в производственную атмосферу можно избежать. В противном случае необходимы дополнительные эффективные средства например местные отсосы системы обще обменной вентиляции и др. к технологическим процессам связанным с повышенным выделением пыли и вредных газов относятся погрузка перегрузка и разгрузка сыпучих материалов их сортировка дробление транспортировка смешивание формирование и упаковка.
На заводах по производству цемента бетона где в воздухе выделяется пыль надо систематически исследовать воздушную среду. Это делают в сроки согласованные с санитарно-эпидемиологической службой но не реже одного раза в месяц.
В смесительном цехе пылевыделение не превышает предельно допустимые концентрации. В цехах успешно применяются аспирационные камеры с аспирационным патрубком в местах интенсивного выделения пыли для улавливания пыли.
Так как завод по производству ячеистого железобетона находится на весьма удаленном расстоянии от населенных пунктов то шум не приносит вреда здоровью окружающим.
3 Энергоснабжение.doc
1 Начальные данные для расчета электрических нагрузок групп цеха.
Таблица 3.1 – Начальные данные
Наименование электроприемника
Двигатель на приемном бункере
Двигатель конвейера галереи
Двигатель на вентилятор
Двигатель питателя приемного бункера
Приводы плужковых сбрасывателей и линейных конвейеров
Вибраторы на приемном бункере
Вибраторы на силосах и на вибровыгрузах
Определение электрических нагрузок производится методом упорядоченных диаграмм как обладающим меньшей допустимой погрешностью при расчетах.
Целесообразно отдельно определить расчетные активные и реактивные нагрузки для групп потребителей с коэффициентом использования и .
Групповую номинальную мощность определяют как сумму номинальных мощностей электроприемников.
Для группы электроприемников одного режима работы среднюю активную
и реактивную мощность нагрузки за наиболее загруженную смену находят по формулам:
- значение соответствующее средневзвешенному коэффициенту характерному для электроприемников данного режима работы;
- коэффициент использования соответствующий данному электроприемнику;
- активная мощность данного приемника; - количество приемников в группе:
При наличии в одной группе электроприемников с разными режимами работы средняя активная и реактивная мощность определяется:
Средневзвешенный коэффициент использования группы приемников с одинаковым режимом работы характеризует использование активной мощности и представляет собой отношение средней активной мощности группы приемников за наиболее нагруженную смену к номинальной мощности:
- средняя активная мощность за смену приемников с одинаковым режимом работы;
- номинальная мощность приемников с одинаковым режимом работы.
Для группы электроприемников с разными режимами работы групповой коэффициент использования:
Эффективным (приведенным) числом приемников называют число однородных по режиму работы электроприемников одинаковой мощности которые дают такую же величину расчетного максимума что и группа электроприемников различных по мощности и режиму работы. Эффективное число группы электроприемников определяется по формуле:
Коэффициент служит для перехода от средней нагрузки к максимальной. Расчетная нагрузка учитывает потребляемую за смену мощность с учетом коэффициента максимума и рассчитывается по формуле:
Планировка электроснабжения представлена в приложении 1 рис.7.
2 Проектирование осветительных установок
Проектирование осветительных установок решает следующие задачи: выбираются типы источников света и светильников намечают наиболее целесообразные высоты установки светильников и их размещение определяют качественные характеристики осветительных установок. Расчет освещения выполняется методом коэффициента использования. Предварительный расчет осветительной нагрузки производится по удельной мощности на единицу производственной площади.
Таблица 3.2 – Исходные данные для светотехнического расчета
Расстояние светильника от перекрытия м
Высота светильника над полом м
Высота расчетной поверхности над полом м
Нормированная освещенность Е лм
Коэффициент запаса к
Коэффициент отражение от потолков
Коэффициент отражение от стен
Коэффициент расчетной плоскости
Коэффициент минимальной освещенности
Расстояние между светильниками по длине:
Расстояние от крайних светильников или рядов светильников до стены:
Расстояние между светильниками по ширине участка:
а=1÷5 принимаем а=15;
Число светильников по длине:
Принимаем число светильников .
Число светильников по ширине:
Общее количество светильников на участке:
Индекс помещения определяется как:
На основании индекса помещения применяемого типа ламп и определяем световой поток:
где - коэффициент использования светового потока
По световому принимаем люминесцентную лампу дневного света улучшенной светопередачи СДЦ с номинальным световым потоком лм и мощностью Вт.
Определим значение тока для выбора кабеля питания ламп:
Выбираем кабель ПХВ сечением 15 мм² I=19 А.
Рассчитаем значение тока для проводов питающие отдельные лампы:
Выбираем провод ТПРФ сечением 15 мм² I=19 А.
Планировка освещения представлена в приложении 2 рис.8.
4 Расчет электрических нагрузок освещения
Предварительный расчет осветительной нагрузки производится по удельной мощности на единицу производственной площади активная нагрузка освещения:
Втм² - удельная мощность на единицу производственной площади;
Реактивная нагрузка освещения:
- значение соответствующее средневзвешенному коэффициенты . Для механического участка .
Суммарная расчетная и активная нагрузка участка определяется как сумма всей активной мощности потребляемой на участке:
и - потребляемая активная и реактивная мощности;
и - активные и реактивные осветительные мощности.
Полная расчетная мощность участка:
По полной расчетной мощности цеха кВА выбираем герметичный силовой трансформатор масляного типа с гофрированным корпусом марки ТМГ номинальной мощностью кВА мощностью холостого хода Вт током холостого хода % мощностью короткого замыкания Вт и напряжением короткого замыкания %.
5 Расчет схемы силовой сети цеха
Исходными данными для формирования схемы силовой сети являются план расположения оборудования на участке с указанием порядкового номера (числитель) и номинальной мощности приемника (знаменатель).
Возможны два основных варианта выбора - выполнить схему электроснабжения комплектными распределительными шинопроводами либо с помощью силовых пунктов. В данном случае необходимо привести таблицу разбиения исходных данных электрических приемников для каждого распределительного шинопровода или силового пункта (СП). Выполняем схему электроснабжения магистральным шинопроводом.
Магистральный шинопровод выбирается по току исходя из полной мощности участка:
Так как трансформатор находится на расстоянии 50 м от участка поддержания соотношения гипса и песка необходимо выбрать кабель для питания данного участка. По току определим марку кабеля: АПР сечением 25 мм² и А.
Выбираем магистральный шинопровод марки ШРМ73УЗ со следующими параметрами:
Таблица 3.3 – Технические характеристики магистрального шинопровода марки ШРА73УЗ
Сопротивление на фазу мОмм:
На основании исходных данных выбираем самый мощный приемник на
участке для данного распределительного шинопровода. В большинстве случаев
этим потребителем является станок но также им может являться пресс. Для него рассчитываем номинальный ток по формуле:
Для этого потребителя рассчитываем пусковой ток:
– кратность пускового тока;
Пиковый ток для выбранного магистрального шинопровода:
– коэффициент использования характерный для двигателя имеющего наибольший пусковой ток;
– расчетный ток группы приемников.
Ток плавкой вставки для выбранного магистрального шинопровода:
– коэффициент плавкой вставки;
Выбираем предохранитель НПН-60 с номинальным током плавкой вставки А номинальным током предохранителя А.
Рисунок 3.1 – Схема включения двигателей
На рис 3.1. показана схема включения двигателей. От трансформатора который находится за 50 м от цеха смешения компонентов тянется кабель на вводной автомат QF1 далее на распределительный пункт РП1. После чего по шинопроводу ШРМ73У3 питаются приемники первого этажа. Распределительный пункт РП2 питается от этого же шинопровода который поднимается на второй этаж. От шинопровода двигатели питаются кабелями ПХВ.
Рисунок 3.2 – Схема электрическая принципиальная
6 Выбор сечений кабелей питающих отдельные электроприемники
Линии с двигателями мощностью 055 кВт:
По длительному току подбираем 3-жильный кабель с медными жилами ПХВ сечением 15 мм² для которых допустимая токовая нагрузка А.
Линии с двигателями мощностью 09 кВт:
Линии с двигателями мощностью 1 кВт:
Линии с двигателями мощностью 2 кВт:
Линии с двигателями мощностью 25 кВт:
Линии с двигателями мощностью 75 кВт:
Линии с двигателями мощностью 9 кВт:
7 Расчет токов короткого замыкания
Для установок до 1 кВ при расчетах КЗ считаем что мощность питающей системы не ограничена и напряжение на стороне высшего напряжения цехового трансформатора является неизменным.
Приведение сопротивления элементов схемы электроснабжения высшего напряжения к схеме низшего напряжения:
= 440 мОм и = 340 мОм – сопротивления элементов схемы электроснабжения высшего напряжения;
Сопротивление цехового трансформатора (относительно в единицах):
– мощность короткого замыкания выбранного трансформатора;
– установленная мощность трансформатора.
- напряжение короткого замыкания трансформатора приведенное в процентах;
Сопротивление цехового трансформатора (в мОм):
– напряжение питания на низкой стороне трансформатора.
Определение токов короткого замыкания:
Рисунок 3.1 – Расположение точек для расчета короткого замыкания
Определение токов короткого замыкания.
Суммарное сопротивление на вводе низшего напряжения цеховой трансформаторной подстанции с учётом добавочного активного сопротивления для распределительных устройств подстанции мОм.
Определяем тока короткого замыкания:
Ударный ток короткого замыкания:
– ударный коэффициент для трансформаторов;
Суммарное сопротивление на второй точке короткого замыкания:
– активное и индуктивное сопротивление шинопровода на участке короткого замыкания которые определяются по формулам:
– активное и индуктивное сопротивление выбранного шинопровода;
l –длинна шинопровода от трансформатора до самой удаленной точки.
- ударный коэффициент определяемый по кривым в зависимости от отношения равный:
Суммарное сопротивление в третьей точке короткого замыкания:
– активное и реактивное сопротивление кабеля на участке короткого замыкания которые определяются по формулам:
Rк Xк – активное и реактивное сопротивление выбранного кабеля;
– длина кабеля от шинопровода до дальнего станка.
8 Расчет заземляющего устройства
Таблица 3.4 – Исходные данные для расчета заземляющего устройства:
Грунт в месте сооружений
Удельное сопротивление грунта Ом·м
Повышающие коэффициенты для:
горизонтальных электродов
вертикальных электродов
Коэффициенты использования:
Диаметр стержневого электрода d м
Длина стержневого электрода l м
Глубина заложения электрода tм
Сопротивление электрода
Расчетные удельные сопротивления грунта для горизонтальных и вертикальных заземлителей:
Сопротивление растеканию одного вертикального электрода стержневого типа:
d – диаметр стержневого электрода;
t – глубина заложения электрода.
Примерное число вертикальных заземлителей:
– сопротивление одного электрода;
Предварительно принимаем число вертикальных заземлителей .
Расчетное сопротивление растекания горизонтальных электродов:
t1 = 07 – глубина закладки горизонтального электрода;
L=24 м–длина горизонтального электрода.
Уточненное сопротивление вертикальных электродов:
Окончательное число вертикальных электродов:
Окончательно принимаем число вертикальных электродов .
Планировка заземления представлена в приложении 1 рис.9.
Введение.doc
Надёжность и достоверность технологического контроля и автоматического управления во многом определяются качеством наладки контрольно – измерительных приборов средств автоматизации систем и устройств технологической сигнализации защиты и блокировки.
Измерительные приборы и автоматические устройства обеспечивают оптимальное протекания технологического процесса недоступное ручному управлению. Поэтому автоматизация позволяет наиболее эффективно использовать все ресурсы производства улучшить качество выпускаемой продукции и значительно повысить производительность труда.
Автоматизированные системы управления технологическим процессом (АСУТП) представляет собой организационно техническую систему управления технологическим процессом. В целом в соответствии с принятым критериям управления в котором для сбора и обработки информации используется вычислительная техника. Роль человека сводиться к содержательному участию в выработке решений там где задачи могут быть формализованы и их выполнение не может быть полностью автоматизировано.
В соответствии с существующей терминологией автоматические системы управления принадлежат к той же области АСУТП но являются высшей ступенью их развития на которой человек полностью выведен из процесса непосредственного управления.
Комплекс технических средств АСУТП включает и средство локального контроля сигнализации регулирования которые могут функционировать автономно.
Автоматизация производства – непрерывно развивающийся процесс причём истинностью его развития является то что переход к более высокой ступени не означает помимо исчезновения характерных черт развития на лучшей ступени так как каждая последующая ступень является продолжением и развитием низшей ступени. Анализ структурных схем автоматической системы регулирования (АСР) показывает что основным элементом системы является объект управления без которого какой либо разговор о системе управления теряет всякий смысл.
Объект управления (регулирования) – это промышленная установка в которой есть необходимость управлять технологическим процессом автоматически следовательно без участия человека. Очевидно что при создании АСР свойства объекта управления будет играть существенное значение при выборе элементов для реализации этой системы а также на свойства системы в целом. При этом надо отменить что если характеристиками элементов можно как-то варьировать то свойства объекта управления остаются практически неизменными. Поэтому изучение характеристик объекта управления относятся к одной из основных задач теории автоматического управления и регулирования.
Развитие всех областей техники в настоящее время характеризуется широкой автоматизацией различных производственных процессов. При этом освобождается труд человека повышается точность и скорость выполнения операций что значительно повышает производительность производства.
Автоматизация обеспечивает работу таких объектов непосредственное обслуживание человеком которых невозможно из-за вредности отдаленности или быстрого протекания процесса. В настоящее время резко увеличивается производство различного оборудования для автоматизации промышленности а также внедряются новые типы автоматических устройств основанные на последних достижениях науки и техники.
Наиболее ответственным этапом при проектировании систем автоматизации является их синтез расчет и последующий анализ которые на сегодняшний день базируются на теории управления.
Технологический процесс производства ячеистого бетона состоит в следующем:
- подготовка сырьевых компонентов;
- смешивание сырьевых компонентов;
- добавление газообразователя;
- заливка формы раствором и транспортировка формы с помощью крана на отстой для набора определенной прочности;
- транспортировка формы с массивом для разбора формы и разрезки массива;
- формирование массивов на тележках с помощью автоклавного крана для помещения их в автоклав;
- автоклавная обработка в течение 12 часов для набора положенной прочности бетоном;
- разгрузка автоклава и перемещение массива с помощью автоклавного крана на цепной транспортер который перемещает массив к цанговому крану;
- цанговый кран производит разделение блоков и перемещение блоков на упаковку.
Пористый бетон изготовляется с применением вяжущих песка и воды. Вяжущие известь и цемент содержат СаО который имеет решающее значение для процесса. Песок вводит в процесс SiO2. Из компонентов СаО Н2О SiO2 в автоклаве при твердении образуются новые минералы гидросиликаты кальция. Так что в конце пористый бетон состоит приблизительно из 60% гидросиликатов кальция и 40% остатков песка. Для того чтобы этот процесс протекал должным образом необходимо сырьевые материалы иметь в тонкомолотом виде. Добавленный ангидрид служит в первую очередь для регулирования реакций в автоклаве дополнительно влияет на процесс вспучивания и набора пластической прочности. В смесителе сырьевые материалы перемешиваются. Причем на качество смешивания могут влиять как время смешивания так и последовательность смешивания. Затем смесь заливают в предварительно смазанную форму. Высоту заливки смеси измеряют специальным шаблоном. Температура смеси в момент заполнения форм не должна быть ниже 35°С.
В производстве ячеистого бетона участвуют разборные формы: большая часть отсоединяется от массива после набора им необходимой прочности и остается на участке набора бетоном прочности а поддон (меньшая часть) уходит с массивом на разрезку автоклавную обработку и упаковку. Так как процесс производства ячеистого бетона непрерывный требуется чтобы поддонов было в два раза больше. Это объясняется тем что в то время как массив газобетона бетона с поддоном находятся в автоклаве необходимо чтобы форма была в собранном виде и участвовала в технологическом цикле производства.
Рекомендуемые чертежи
- 24.01.2023
- 25.10.2022
Свободное скачивание на сегодня
Другие проекты
- 23.08.2014