Курсовик по ТММ



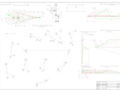
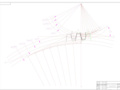
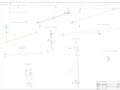
- Добавлен: 25.10.2022
- Размер: 2 MB
- Закачек: 0
Описание
Состав проекта
![]() |
![]() ![]() ![]() |
![]() ![]() ![]() |
![]() ![]() |
![]() ![]() |
![]() ![]() |
![]() |
![]() ![]() ![]() ![]() |
![]() ![]() ![]() ![]() |
![]() ![]() ![]() ![]() |
Дополнительная информация
Курсовая работа по ТММ.docx
1Синтез плоского рычажного механизма по коэффициенту изменения средней скорости ведомого звена3
2Построение повернутых планов скоростей4
3 Приведение внешних сил5
4 Определение работы приведенного момента7
5 Определение величины работы движущего момента8
6 Определение приращения кинетической энергии8
7 Определение приведенного момента инерции8
8 Определение момента инерции маховика10
Динамический анализ рычажного механизма12
1 Определение углового ускорения кривошипа12
3 Определение сил инерции16
4 Структурный анализ16
4.1 Расчёт группы 5417
4.2 Расчёт группы 3218
4.3 Расчёт начальной системы 1018
5 Проверка силового расчёта18
Синтез эвольвентного зацепления20
1 Предварительный расчет и выбор электродвигателя20
2 Расчет закрытой зубчатой передачи23
3 Построение профилей зубьев колес25
Задание 2 вариант 1.
Схема плоского рычажного механизма – рисунок 1.
Коэффициент изменения средней скорости ведомого звена k=12.
Ход рабочего звенаН=120 мм.
Число оборотов кривошипаn=420 обмин.
Сила полезного сопротивленияР=400 Н.
Коэффициент неравномерности движения механизма=.
Коэффициент изменения средней скорости ведущего звена К=1
Соотношение длин в крайнем положении механизма=13
Длина звена ВС lbc=lсd
Масса звеньев m= q·l где l-длина звена в м q- масса 1 мq=20кгм
Масса ползуна в пять раз превышает массу предыдущего стержневого звена.
Рисунок 1 – Схема механизма
Требуется: Провести структурный синтез кинематический анализ механизма динамический анализ механизма синтез эвольвентного зацепления.
Динамический синтез механизма (лист 1 графической части)
1Синтез плоского рычажного механизма по коэффициенту изменения средней скорости ведомого звена
Последовательность построения с учетом заранее выбранного масштаба построения =1:5 плана механизма (рисунок 2).
Рисунок 2 (М 1:5) – Определение размеров звеньев
С помощью К определим угол между крайними положениями шатуна
=180º·=180º·=0º (1.1)
Отложим ход Н при этом ход точки Е равен ходу точки D откуда DC=1802=90 мм. По условию =13 следовательно DC=3· DC=3·90=270 мм. Радиус АВ=DC=90 мм. По условию АВ>АC примем АС=70 мм
Вес звеньев определяется по формуле:
где g - ускорение свободного падения g = 98 мc2.
Расчетные значения длин массы и веса звеньев сведем в таблицу 1.1
Разобьем окружность описываемую точкой В на 12 равных частей. Через каждое положение точки В проведем прямую через точку С до пересечения с дугой описываемой точкой Д. Методом засечек построим положения точки Е на направлении ее хода.
2Построение повернутых планов скоростей
Определим скорость точки В1 (принадлежащую звену АВ) равную скорости В2 (принадлежащую звену ВД).
VВ1 = VВ2 = 1 ·lАВ=·lАВ =·009 =396 (мс)
Из полюса Рi плана скоростей для положения i механизма отложим произвольный отрезок изображающий повернутую на 90° против хода кривошипа скорости точки В1. Пусть рibi>=100 мм тогда масштаб плана скоростей будет
Скорость точки В3 принадлежащей кулисе складывается из движения вместе с кулисным камнем 2 и относительно камня.
где B3 B2 - векторы абсолютных скоростей точек; B2 B3 - вектор относительной скорости.
Уравнение (1.3) решается графическим способом. При этом учитывается что B2АB В3DВ В2В3 DВ после поворота плана скоростей на 90°против вращения кривошипа.
Скорость точки D определяется из теоремы подобия.
При этом pid>= pib3>
Ломаные скобки означают что величина берется с чертежа и выражается в миллиметрах.
Для положения 1 уравнение примет вид p1b3>= 39=165 (мм).
Скорость точки Е4 принадлежащей кулисе складывается из движения вместе с кулисным камнем 5 и относительно камня.
где Е4 - вектор абсолютной скорости точек; Е4Е5 - вектор относительной скорости.
Уравнение (2.2) решается графическим способом. При этом учитывается что Е400 Е5DЕ В2В3 DЕ после поворота плана скоростей.
Значения скоростей E для остальных положений механизма приведены в таблице 1.2.
3 Приведение внешних сил
Приведенный момент Мп представляем в виде пары сил Рп приложенных в точках А и В кривошипа. Приведение выполняется с помощью «Рычага Жуковского».
Силы тяжести звенев 13 и 5 а также одна на составляющих пары сил Рп не будет иметь момента относительно полюса повернутого плана скоростей и поэтому их не показываем.
Величину и направление Рп определим из равенства - по величине и направлению - момента силы Рп сумме моментов сил G2 G4 и Рпс относительно полюса. Например для положения 1 (рисунок 3) это равенство будет иметь вид:
-Рп ·р1b>=Рпc·p1e>+G2·р1В3>-G4·р1g4>(1.5)
Рисунок 3 - Определение приведенной силы с помощью Рычага Жуковского
Знак «минус» показывает что сила направлена в противоположную сторону от указанного направления.
Мп=Рп·lАВ=1781·009=16 (Н·м)(1.6)
Переносом Рп в точку В схемы механизма устанавливаем что момент силы Рп относительно точки А направлен против направления вращения кривошипа. По этой причине Мп в положении 1 будем считать отрицательным. Аналогичным образом определяем Мп для всех остальных положений механизма. При этом учитываем что во время холостого хода сила полезного сопротивления не действует. Результаты приводим в таблице 1.3.
По данным таблицы строим график приведенного Мп (φ) с масштабными коэффициентами
φ=2·180= 0035 радмм;
4 Определение работы приведенного момента
Работу Ап приведенного момента Мп получаем методом графического интегрирования. С этой целью пространства под кривой момента делим на вертикальные полосы и заменяем их равновеликими прямоугольниками. Полки прямоугольников сносим на ось Мп. Точки пересечения сносок с осью Мп соединяем лучами с левым концом отрезка Н.
Длину отрезка примем равной 50 мм. На плоскости Ап (φ) выстраиваем цепочку хорд параллельных лучам. Через точки соединения хорд проводим плавную кривую которая является искомым графиком Ап (φ). Масштабный коэффициент графика по оси Ап при таком способе интегрирования
А=м·φ·Н=1·0035·50=175 (Джмм)(1.7)
5 Определение величины работы движущего момента
Движущий момент Мд будем считать постоянным на всём цикле работы. При этом его работа Ад будет иметь вид прямой идущей из начала координат.
Маховик подбирается для периода установившегося движения машины. Работа всех внешних сил за цикл установившегося движения равна нулю:
Отсюда вытекает что в конце цикла т.е. в положении 12 работы Ап и Ад равны по величине и противоположны пo знаку. Таким образом определяется наклон прямой Ад.
Величину движущего момента определим графическим дифференцированием Ад по φ. Для этого из левого конца отрезка Н проводим луч параллельный прямой Ад. Луч отсекает на оси М искомый момент Мд. В силу постоянства момента Мд его график имеет вид горизонтальной прямой. Величина
Мд= Мд>·М=1923·1=1923 (Н·м).
6 Определение приращения кинетической энергии
Трение в данной задаче не учитывается поэтому работа внешних сил расходуется только на изменение кинетической энергия механизма. Ее приращение равно алгебраической сумме работ Ап и Ад внешних сил. Исходя из этого строим график ΔТ(φ). Для облегчения построений соединим пунктирной прямой начало и конец графика Ап. Искомое ΔТ будет заключаться в промежутке между кривой Ап и пунктирной прямой. Масштабный коэффициент Т= ТА.
7 Определение приведенного момента инерции
Кинетическая энергия приведенного момента инерции должна быть равна кинетической энергии механизма:
где J01= =0097 кг·м2;
Угловые скорости выразим через соответствующие линейные:
= ==4398 мс2; 3= ; 4= .
Истинные скорости заменим изображающими их отрезками тогда:
Вычислим коэффициенты К1 К2 К3 и К4.
Теперь формула для расчёта Iп имеет вид:
Jп = 0097+00000292· +00008333·+00001116· +
Отрезки и берем с повернутых планов скоростей. Результаты расчета по формуле (1.8) сводим в таблицу 1.4.
По данным таблицы строим график Jп(φ) с масштабным коэффициентом I=1 кг·м2мм.
8 Определение момента инерции маховика
По графикам Jп(φ) и ΔТ(φ) строим диаграмму Витенбауэра ΔТ (Jп). Определяем углы наклона касательных к диаграмме:
Момент инерции маховика
где kl> - отрезок на диаграмме ΔТ(φ).
Зная величину момента инерции IМ маховика можно определить размеры маховика.
Исходя из конструктивных соображений выберем диаметр маховика D = 10·r=10·009=09 м где r=009 м-радиус кривошипа.
Воспользовавшись соотношением
JМ=GD2 определим массу G маховика
Изобразим на чертеже эскиз маховика.
Динамический анализ рычажного механизма
(лист 2 графической части)
1 Определение углового ускорения кривошипа
Угловое ускорение i кривошипа определим с помощью дифференциального уравнения движения машины:
Мп+Мд=(Iп+Im)·I+05I2·In’(р)(2.1)
Вместо действительной угловой скорости I кривошипа поставим её среднее значение cp. При этом будет допущена небольшая ошибка в определении I.
Производную In'(φ) определим графически. Для этого проведем касательную к графику In(φ). Поскольку силовой расчёт (динамический анализ) требуется выполнить для 1-г0 положения касательную проводим через точку 1'. Определяем угол наклона касательной его величина α=154°.
In'(φ) =·tgα=·00269= 017 (кг·м2)(2.2)
Тогда искомое угловое ускорение 1 кривошипа в положении 1 механизма
Знак «минус» означает что ускорение направлено против хода кривошипа.
2 Построение планов скоростей и ускорений
На втором листе графической части проекта вычерчиваем схему механизма в заданном положении 1 для которого необходимо выполнить силовой расчёт. Для этого же положения строим план скоростей.
Определим скорость точки В2 равную скорости В1.
VВ2 = VВ1 = 1 ·lАВ=·lАВ =·0039 =227 (мс)
Из полюса Рi плана скоростей для положения i механизма отложим произвольный отрезок изображающий скорость точки В1. Пусть рibi>=100 мм тогда масштаб плана скоростей будет
Необходимые для построения плана ускорений скорости сводим в таблицу 2.1.
Исходными данными для построения плана ускорения являются план положения механизма план скоростей и ускорения точек ведущего звена АВ.
Ускорение точки В2 равно ускорению точки В1
Нормальное ускорение точки В2 равно ускорению точки В1 ведущего звена вращающегося равномерно:
=аВ1= 12·LAB=4392·009=1741 (2.4)
и направлено к центру вращения.
Тангенциальное ускорение:
=1·lАВ=110·009=99 мс2(2.5)
Пользуясь тем же разложением что и при определении скоростей получим следующие уравнения ускорений:
Ускорение Кориолиса в уравнении (2.6)
Угловая скорость звена 3
= = = 249 (с-1 )(2.9)
Подставляя найденное в формуле (2.9) получим :
=2·249· 09=4483 (с-1 )
Направление получим поворотом вектора VВ3В2 в сторону 3 на 90°.
Нормальное ускорение точки В3 в уравнении (2.7)
Расстояние lСB снимаем со схемы механизма:
lВC=p4В>·c=62·25·10-3=0155 (м) (2.11)
Подставляя найденное в (2.10) получим:
По уравнениям строим план ускорений. Отрезок > изображающий ускорение примем равным 200 мм.
При этом масштабный коэффициент плана ускорений
а===087 (м·с2мм)(2.12)
Для определения ускорения точки Е будем иметь следующее уравнение:
Ускорение точки D в этом уравнении определим по теореме подобия. Из теоремы следует что отрезок
d>= B3>=141=82 мм(2.13)
По этой же теореме ускорение точки S3 s3>=9 мм; аS3=8 мс2.
Следующее ускорение из уравнения
Откладываем направление из конца вектора скорости т.D а направление ускорения точки Е из полюса плана ускорений. Пересечение линий направления дает величины ускорений и аЕ.
Ускорение S2 равно В2 ускорение S3 =0 так как по условию задачи в нем находится центр вращения кулисы ускорение S4 найдем соединив точку с центром отрезка ED aS1=0 aS5= aЕ.
Ускорения необходимые для определения сил инерции сводим в таблицу 2.2.
Угловое ускорение звена 3:
Направление 3 - против часовой стрелке.
Угловое ускорение звена 4:
Направление 4 - против часовой стрелке.
3 Определение сил инерции
Главный вектор и главный момент сил инерции звена определяют по формулам:
Для звена 1 с маховиком:
Ри4 = m4·аS4 =54·57= 3078 (Н)
Ми4 =IS4 ·4=2642·28=74 (Н·м)(2.16)
На чертеже х4>===96мм
Ри2 = m2·aS2 =9·174 = 1566 (Н) (2.17)
Ри5 = m5·aS5 = 27·57= 1566 (Н)
4 Структурный анализ
Механизм обладает одной степенью свободы. Таким же должно быть число степеней свободы системы с которой начинается образование механизма. В эту систему должны входить стойка и одно из звеньев связанных с ней одноподвижной кинематической парой. Примем в качестве такого кривошип т.к. на него действует неизвестная внешняя нагрузка - движущий момент МД . Этот момент был определен в предыдущем разделе исходя из предложения о том что Мд = const. В этом разделе мы определим его более точно.
Схема образования исследуемого механизма выглядит следующим образом (рисунок 4):
Рисунок 4 – Разделение механизма на группы Ассура.
Силовой расчет ведётся в порядке обратном образованию механизма т.е. сначала будет рассчитана группа 54 затем 32 и в последнюю очередь - 10.
4.1 Расчёт группы 54
Из равновесия звена 4 следует что
=-РИ4 ·hИ4>- ·h34>-G4·hG4>=0(2.18)
Из равновесия звеньев 4 и 5 следует что
+ + + + ++ = 0(2.19)
Графическое решение уравнения (2.19) дает
R05=415 (Н) = 1673 (Н)
4.2 Расчёт группы 32
Звено 2 находится в равновесии под действием двух сил R32 и R12 следовательно R32 =-R12.
Из равновесия звеньев 2 и 3 следует что
=- R43·h43>+G2·hG2>- РИ2 ·hИ2>+ R12·h12>=0(2.21)
Из равновесия структурной группы 3 2 следует что
Отсюда графическим путём находим: R03 = 3199 Н
4.3 Расчёт начальной системы 10
Из равновесия звена 1 следует что
= -R21·h21>+ МУ +G1·hG1>=0
МУ = R21·h21>·l-G1·hG1>·l =3737·35·25·10-3-176·16·25·10-3=321 Н·м (2.22)
5 Проверка силового расчёта
Проверку выполним с помощью «Рычага Жуковского» (рисунок 5). Для этого к повернутому плану скоростей приложим внешние силы механизма и силы инерции. Момент Му представим в виде пары сил Рп приложенных перпендикулярно кривошипу в точках А и В. При этом
План скоростей дополним отрезком
pt4 >= еd >· =272· =158(мм)(2.23)
Этот отрезок изображает скорость точки Т4 пересечения силы PИ4 с кулисой ED. Формула (2.22) вытекает из теоремы подобия.
Рисунок 5 – Определение уравновешивающей силы с помощью рычага Жуковского
Силы проходящие через полюс "Рычага Жуковского» не показываем т.к. они не дают момента относительно этого полюса. Сумма моментов всех
МУ = Pу·lАВ=3314·009=298 Н·м.
Чтобы не путать этот момент с найденным из формулы (2.22) обозначим
его . Ошибка составляет
что приемлемо т.к. допускаемая ошибка составляет 10%.
Синтез эвольвентного зацепления (лист 3 графической части)
1 Предварительный расчет и выбор электродвигателя
Кинематический расчет привода производится одновременно с подбором по каталогу приемлемого по мощности и частоте вращения электродвигателя и сводится к определению общего передаточного числа привода и разбивки его между отдельными узлами и типами передач согласно заданной кинематической схеме (рисунок ). Механизм состоит из открытой и закрытой (редуктора) зубчатых передач.
Скорость вращения входного вала (кривошипа) рычажного механизма задана.
Рисунок 6 - Кинематическая схема механизма
По найденной уравновешивающей силе Рп приложенному к кривошипу определяют вращающий момент на валу кривошипа привода:
=125·3314·009=3728 Н·м
где – уравновешивающая сила
– коэффициент запаса определяемый в зависимости от неучтённых нагрузок степени влияния сил и моментов трения ошибки в положении силового расчета условий эксплуатации и прочего k=12..3
Находят мощность на ведомом валу привода:
где – угловая скорость вала кривошипа 4398 радс.
Определяют мощность на валу электродвигателя:
где – КПД всего привода равный произведению частных КПД передач входящих в привод:
здесь =095– КПД закрытой передачи (редуктора);
=09– КПД цепной передачи;
=099– КПД одной пары подшипников качения;
M=4 - число пар подшипников.
Среднее значение передаточных отношений и КПД различных типов передач взяты из таблицы 1 [5].
общ=095·09·0994=082 тогда =19972 кВт.
По найденной мощности Nдв определяют тип трехфазного асинхронного электродвигателя наиболее подходящего для конкретных условий работы (таблица 2 [5]).
Выбираем двигатель 4АМ80В2Y3 мощностью 22 кВт и частотой вращения 3000 обмин.
Определяют общее передаточное отношение всего привода:
где – частота вращения вала электродвигателя;
=420 обмин – частота вращения вала кривошипа. С учетом скольжения частота вращения двигателя равна 2850 обмин.
После определения общего передаточного числа привода производится его разбивка на передаточные числа отдельных ступеней при этом используются рекомендуемые значения передаточных чисел. При разбивке общего передаточного числа исходим из равенства:
где - частные передаточные числа отдельных передач привода.
Передаточное число закрытой передачи – редуктора выбираем равным 355. Тогда передаточное отношение цепной передачи:
Это число входит в промежуток рекомендуемых передаточных чисел для цепных передач.
Определяют частоты вращения всех валов привода:
быстроходный вал редуктора: n2===1500 обмин.;
тихоходный вал редуктора(вал кривошипа): 4225 обмин.
Угловая скорость валов привода:
где n – частота вращения соответствующего вала.
=2985 об-1; =1571 об-1; =442 об-1.
Находим крутящие (вращающие) моменты всех валов привода:
=1261·355·095=4251 Н·м.
Кинематический расчет привода
Частота вращения обмин
тихоходный вал - вал кривошипа
2 Расчет закрытой зубчатой передачи
Определяем межосевое расстояние и округляем его до стандартного:
где - коэффициент межосевого расстояния (для прямозубых колес принимаем );
=0315- коэффициент ширины принимают в зависимости от положения колес относительно опор.
принимаем а=50 мм по ГОСТ 2185-80.
Определяем модуль зацепления:
Значение модуля зацепления m полученное расчетом округляем в большую сторону до стандартного из ряда чисел и принимаем равным 1.
Произведем геометрический расчет цилиндрической прямозубой передачи составленной из цилиндрических колес. Расчет ведется исходя из условия отсутствия бокового зазора между зубцами. Требуется также обеспечить отсутствие подрезания зубцов во время их нарезания зуборезным инструментом. Для соблюдения этих условий в случае необходимости сдвигают зуборезный инструмент по отношению к оси заготовки.
Сумма коэффициентов сдвигов определяют по формуле
где αр=20° – угол зацепления зуборезного инструмента αсб – угол зацепления колес в сборке равный
Следовательно и [1+2]=0 т.е смещения инструмента при нарезании колес не требуется.
Определяем геометрические размеры зубчатой передачи.
Диаметры делительных окружностей колес:
Диаметры основных окружностей:
db1= d1cosα= 22cos20° = 2067 мм
db2 = d2·cosα =78cos20° = 733 мм.
Диаметры начальных окружностей:
Диаметры окружностей выступов зубчатого колеса.
da1 = d1+2· ha = d1+2· m=22+1·2 =24 мм
da2 = d2+2· ha = d2+2· m=78+1·2 =80 мм.
Диаметры окружностей впадин зубчатых колес равны:
df1 = d1-2· hf = d1-25·m=22-25 =195 мм
df2 = d2-2· hf = d2-25· m=78-25 =755 мм.
Определим шаг зацепления по дуге начальной окружности.
Толщина зуба S и ширина впадины е по дуге начальной окружности равны между собой т.е. S =S1 =S2 е=е1=е2.
S =е= 05·р = 05·314 = 157 мм.
Определим коэффициент перекрытия:
3 Построение профилей зубьев колес
Построение зубчатого зацепления ведется в следующем порядке:
Масштабная высота зуба должна быть не менее 20 мм тогда
Проводим линию центров отмечаем на ней центры О1 и О2 на расстоянии =1000 мм (центры колес О1 и О2 могут выходить за пределы чертежа).
В выбранном нами масштабе вычерчиваем окружности зубчатых колес: основные начальные окружности выступов и впадин.
Через полюс зацепления Р проводим общую касательную к начальным окружностям (перпендикулярно к линии центров) и линию зацепления NN касательную к основном окружностям при этом угол а между этими касательными должен быть равен а = 20° .
Проведем перпендикуляры О1А0 и О2В0 из центров О1 О2 к линии зацепления (длины этих перпендикуляров есть радиусы основных окружностей). Участок А0В0 линии зацепления называется теоретическим участком линии зацепления.
Каждый зуб зубчатою колеса находится в зацеплении не на всем своем пути а только на каком-то участке т.е. в какой-то точке он входит в зацепление а в какой-то выходит из него. Этот участок лежащий на линии зацепления NN и образованный пересечением этой линии с окружностями выступов называется практическим или рабочим участком линии зацепления. На чертеже практический участок линии зацепления обозначен точками А и В.
Строим эвольвентные профили только центральной пары сопряженных зубьев так чтобы они касались в полюсе зацепления Р.
Эвольвентной окружности называется кривая описываемая точкой прямой линии перекатываемой по этой окружности без скольжения. Окружность по которой перекатывается прямая при образовании эвольвенты называется основной окружностью. Следовательно эвольвентные участки зубьев будут находиться в пределах между основными окружностями и окружностями выступов колес.
Построение эвольвенты производим общепринятым методом. Для этого отрезок А0P линии зацепления (второго колеса) разбиваем на равное число частей (допустим на четыре) обозначим точки деления 1 2 3 4 и т.д. продолжив деление по другую сторону точки L.
Отрезок LР линии зацепления играет роль производящей прямой при обкатывании которой без скольжения по основной окружности точка Р опишет эвольвенту.
Полученные отрезки Р-1 1-2 2-3 . . . начиная от точки L отложим по хорде на основной окружности при этом разностью между длинами дуги и хорды пренебрегаем. Полученные точки обозначим 1' 2' 3'
Соединим эти точки с центром колеса и проведем через них касательные к основной окружности которые будут перпендикулярны радиусам.
Отложим на касательных отрезки равные расстоянию до полюса Р от соответствующей точки деления т.е. вдоль первой касательной откладываем отрезок Р-1 вдоль второй касательной — отрезок Р-2 и т.д. Полученные точки обозначим 1" 2" 3" и затем последовательно соединим их плавной кривой. Данная кривая и будет представлять эвольвентный участок профиля зуба. Для сопряженного колеса эвольвентный профиль зуба строится аналогично.
Неэвольвентный участок профилей зубьев т.е. участок в пределах от основной окружности до окружности впадин для случая dfdb очерчивается радиальными прямыми после чего у основания зуба производят их сопряжение с окружностями впадин радиусом ρ =(02-03)m=02·1=02 мм . Для построения симметричного профиля зуба отложим толщину зуба в масштабе ==157 мм; проведем ось симметрии и шаблонов строим профиль зуба.
Аналогично производится построение профилей соседних зубьев.
Обозначим рабочие участки профилей зубьев. Учитывая что в точке А начинается зацепление т.е.в ней контактируются крайняя точка головки зуба второго (большого) колеса и наинизшая точка ножки зуба первого (малого) колеса радиусом О1А сделаем засечку на профиле зуба малого колеса которая определит положение наинизшей точки первого колеса. Делая засечку на профиле зуба второго (большего) колеса радиусом О2В определим наинизшую точку участвующую в зацеплении для этого колеса. Определим длину дуги зацепления по любой из окружностей в пределах которой происходит зацепление зубьев предварительно проведя пунктиром через точки А и В сопряженные профили зубьев в начале и конце зацепления. Дуги сd и ef между положениями соответствующих профилей зубьев в начале и конце зацепления для каждого из колес есть пути проходимые зубьями за время зацепления одной пары зубьев измеренные по начальной окружности.
При работе зубчатых колес необходимо чтобы в любой момент времени зубья находились в зацеплении. Для этого требуется чтобы дуга зацепления была больше шага. В противном случае первая пара зубьев выйдет из зацепления раньше чем войдет в зацепление следующая пара зубьев.
Отношение дуги зацепления к шагу характеризуется коэффициентом перекрытия е.
Определим коэффициент перекрытия графическим и аналитическим методами.
На основании данного выше определения запишем
(величина АВ находится при измерении на чертеже). Для определения коэффициента перекрытия аналитическим методом имеем:
Вычислим процент расхождения
Полученный процент расхождения не превышает допустимой величины.
В курсовом проекте проведен динамический синтез и анализ рычажного механизма синтез эвольвентного зацепления. Результаты проектирования дают возможность оценить кинематического схему механизма по кинематическим и динамическим качествам с тем чтобы определить направление совершенствования кинематических схем подобных механизмов. Совершенные кинематические схемы обеспечивают более экономические в отношении металлоёмкости машины что является одним из основных требований машиностроения.
Более совершенные кинематические схемы механизмов можно получить применяя аналитические методы анализа и синтеза с использованием современной вычислительной техники.
Артоболевский И.И. Теория механизмов и машин И.И. Артоболевский. М.: Наука 1988. -640 с.
Курсовое проектирование по теории механизмов и машин под ред. проф. С.И.Артоболевского. М. :Высшая школа 1960. - 248 с.
Левитская О.И. Курс теорий механизмов и машин О.Н. Левитская Н.И. Левитский. М.: Высш. шк. 1978. -226 с.
С.А. Чернавский К.Н.Боков И.М.Чернин. Курсовое проектирование деталей машин. Учебное пособие для учащихся машиностроительных специальностей техникумов – М.: Машиностроение1988. – 416 с. ил.
Анурьев В.И. Справочник конструктора – машиностроителя: в 3 – х т. – М.: Машиностроение1978. – т. 12.
Курсовая работа по ТММ.doc
1Синтез плоского рычажного механизма по коэффициенту изменения средней скорости ведомого звена3
2Построение повернутых планов скоростей4
3 Приведение внешних сил5
4 Определение работы приведенного момента8
5 Определение величины работы движущего момента9
6 Определение приращения кинетической энергии9
7 Определение приведенного момента инерции9
8 Определение момента инерции маховика11
Динамический анализ рычажного механизма13
1 Определение углового ускорения кривошипа13
3 Определение сил инерции17
4 Структурный анализ17
4.1 Расчёт группы 5418
4.2 Расчёт группы 3219
4.3 Расчёт начальной системы 1019
5 Проверка силового расчёта19
Синтез эвольвентного зацепления21
1 Предварительный расчет и выбор электродвигателя21
2 Расчет закрытой зубчатой передачи24
3 Построение профилей зубьев колес26
Задание 2 вариант 1.
Схема плоского рычажного механизма – рисунок 1.
Коэффициент изменения средней скорости ведомого звена k=12.
Ход рабочего звенаН=120 мм.
Число оборотов кривошипаn=420 обмин.
Сила полезного сопротивленияР=400 Н.
Коэффициент неравномерности движения механизма=.
Коэффициент изменения средней скорости ведущего звена К=1
Соотношение длин в крайнем положении механизма=13
Длина звена ВС lbc=lсd
Масса звеньев m= q·l где l-длина звена в м q- масса 1 мq=20кгм
Масса ползуна в пять раз превышает массу предыдущего стержневого звена.
Рисунок 1 – Схема механизма
Требуется: Провести структурный синтез кинематический анализ механизма динамический анализ механизма синтез эвольвентного зацепления.
Динамический синтез механизма (лист 1 графической части)
1Синтез плоского рычажного механизма по коэффициенту изменения средней скорости ведомого звена
Последовательность построения с учетом заранее выбранного масштаба построения =1:5 плана механизма (рисунок 2).
Рисунок 2 (М 1:5) – Определение размеров звеньев
С помощью К определим угол между крайними положениями шатуна
=180º·=180º·=0º (1.1)
Отложим ход Н при этом ход точки Е равен ходу точки D откуда DC=1802=90 мм. По условию =13 следовательно DC=3· DC=3·90=270 мм. Радиус АВ=DC=90 мм. По условию АВ>АC примем АС=70 мм
Вес звеньев определяется по формуле:
где g - ускорение свободного падения g = 98 мc2.
Расчетные значения длин массы и веса звеньев сведем в таблицу 1.1
Разобьем окружность описываемую точкой В на 12 равных частей. Через каждое положение точки В проведем прямую через точку С до пересечения с дугой описываемой точкой Д. Методом засечек построим положения точки Е на направлении ее хода.
2Построение повернутых планов скоростей
Определим скорость точки В1 (принадлежащую звену АВ) равную скорости В2 (принадлежащую звену ВД).
VВ1 = VВ2 = 1 ·lАВ=·lАВ =·009 =396 (мс)
Из полюса Рi плана скоростей для положения i механизма отложим произвольный отрезок изображающий повернутую на 90° против хода кривошипа скорости точки В1. Пусть рibi>=100 мм тогда масштаб плана скоростей будет
Скорость точки В3 принадлежащей кулисе складывается из движения вместе с кулисным камнем 2 и относительно камня.
где B3 B2 - векторы абсолютных скоростей точек; B2 B3 - вектор относительной скорости.
Уравнение (1.3) решается графическим способом. При этом учитывается что B2АB В3DВ В2В3 DВ после поворота плана скоростей на 90°против вращения кривошипа.
Скорость точки D определяется из теоремы подобия.
При этом pid>= pib3>
Ломаные скобки означают что величина берется с чертежа и выражается в миллиметрах.
Для положения 1 уравнение примет вид p1b3>= 39=165 (мм).
Скорость точки Е4 принадлежащей кулисе складывается из движения вместе с кулисным камнем 5 и относительно камня.
где Е4 - вектор абсолютной скорости точек; Е4Е5 - вектор относительной скорости.
Уравнение (2.2) решается графическим способом. При этом учитывается что Е400 Е5DЕ В2В3 DЕ после поворота плана скоростей.
Значения скоростей E для остальных положений механизма приведены в таблице 1.2.
3 Приведение внешних сил
Приведенный момент Мп представляем в виде пары сил Рп приложенных в точках А и В кривошипа. Приведение выполняется с помощью «Рычага Жуковского».
Силы тяжести звенев 13 и 5 а также одна на составляющих пары сил Рп не будет иметь момента относительно полюса повернутого плана скоростей и поэтому их не показываем.
Величину и направление Рп определим из равенства - по величине и направлению - момента силы Рп сумме моментов сил G2 G4 и Рпс относительно полюса. Например для положения 1 (рисунок 3) это равенство будет иметь вид:
-Рп ·р1b>=Рпc·p1e>+G2·р1В3>-G4·р1g4>(1.5)
Рисунок 3 - Определение приведенной силы с помощью Рычага Жуковского
Знак «минус» показывает что сила направлена в противоположную сторону от указанного направления.
Мп=Рп·lАВ=1781·009=16 (Н·м)(1.6)
Переносом Рп в точку В схемы механизма устанавливаем что момент силы Рп относительно точки А направлен против направления вращения кривошипа. По этой причине Мп в положении 1 будем считать отрицательным. Аналогичным образом определяем Мп для всех остальных положений механизма. При этом учитываем что во время холостого хода сила полезного сопротивления не действует. Результаты приводим в таблице 1.3.
По данным таблицы строим график приведенного Мп (φ) с масштабными коэффициентами
φ=2·180= 0035 радмм;
4 Определение работы приведенного момента
Работу Ап приведенного момента Мп получаем методом графического интегрирования. С этой целью пространства под кривой момента делим на вертикальные полосы и заменяем их равновеликими прямоугольниками. Полки прямоугольников сносим на ось Мп. Точки пересечения сносок с осью Мп соединяем лучами с левым концом отрезка Н.
Длину отрезка примем равной 50 мм. На плоскости Ап (φ) выстраиваем цепочку хорд параллельных лучам. Через точки соединения хорд проводим плавную кривую которая является искомым графиком Ап (φ). Масштабный коэффициент графика по оси Ап при таком способе интегрирования
А=м·φ·Н=1·0035·50=175 (Джмм)(1.7)
5 Определение величины работы движущего момента
Движущий момент Мд будем считать постоянным на всём цикле работы. При этом его работа Ад будет иметь вид прямой идущей из начала координат.
Маховик подбирается для периода установившегося движения машины. Работа всех внешних сил за цикл установившегося движения равна нулю:
Отсюда вытекает что в конце цикла т.е. в положении 12 работы Ап и Ад равны по величине и противоположны пo знаку. Таким образом определяется наклон прямой Ад.
Величину движущего момента определим графическим дифференцированием Ад по φ. Для этого из левого конца отрезка Н проводим луч параллельный прямой Ад. Луч отсекает на оси М искомый момент Мд. В силу постоянства момента Мд его график имеет вид горизонтальной прямой. Величина
Мд= Мд>·М=1923·1=1923 (Н·м).
6 Определение приращения кинетической энергии
Трение в данной задаче не учитывается поэтому работа внешних сил расходуется только на изменение кинетической энергия механизма. Ее приращение равно алгебраической сумме работ Ап и Ад внешних сил. Исходя из этого строим график ΔТ(φ). Для облегчения построений соединим пунктирной прямой начало и конец графика Ап. Искомое ΔТ будет заключаться в промежутке между кривой Ап и пунктирной прямой. Масштабный коэффициент Т= ТА.
7 Определение приведенного момента инерции
Кинетическая энергия приведенного момента инерции должна быть равна кинетической энергии механизма:
где J01= =0097 кг·м2;
Угловые скорости выразим через соответствующие линейные:
= ==4398 мс2; 3= ; 4= .
Истинные скорости заменим изображающими их отрезками тогда:
Вычислим коэффициенты К1 К2 К3 и К4.
Теперь формула для расчёта Iп имеет вид:
Jп = 0097+00000292· +00008333·+00001116· +
Отрезки и берем с повернутых планов скоростей. Результаты расчета по формуле (1.8) сводим в таблицу 1.4.
По данным таблицы строим график Jп(φ) с масштабным коэффициентом I=1 кг·м2мм.
8 Определение момента инерции маховика
По графикам Jп(φ) и ΔТ(φ) строим диаграмму Витенбауэра ΔТ (Jп). Определяем углы наклона касательных к диаграмме:
Момент инерции маховика
где kl> - отрезок на диаграмме ΔТ(φ).
Зная величину момента инерции IМ маховика можно определить размеры маховика.
Исходя из конструктивных соображений выберем диаметр маховика D = 10·r=10·009=09 м где r=009 м-радиус кривошипа.
Воспользовавшись соотношением
JМ=GD2 определим массу G маховика
Изобразим на чертеже эскиз маховика.
Динамический анализ рычажного механизма
(лист 2 графической части)
1 Определение углового ускорения кривошипа
Угловое ускорение i кривошипа определим с помощью дифференциального уравнения движения машины:
Мп+Мд=(Iп+Im)·I+05I2·In’(р)(2.1)
Вместо действительной угловой скорости I кривошипа поставим её среднее значение cp. При этом будет допущена небольшая ошибка в определении I.
Производную In'(φ) определим графически. Для этого проведем касательную к графику In(φ). Поскольку силовой расчёт (динамический анализ) требуется выполнить для 1-г0 положения касательную проводим через точку 1'. Определяем угол наклона касательной его величина α=154°.
In'(φ) =·tgα=·00269= 017 (кг·м2)(2.2)
Тогда искомое угловое ускорение 1 кривошипа в положении 1 механизма
Знак «минус» означает что ускорение направлено против хода кривошипа.
2 Построение планов скоростей и ускорений
На втором листе графической части проекта вычерчиваем схему механизма в заданном положении 1 для которого необходимо выполнить силовой расчёт. Для этого же положения строим план скоростей.
Определим скорость точки В2 равную скорости В1.
VВ2 = VВ1 = 1 ·lАВ=·lАВ =·0039 =227 (мс)
Из полюса Рi плана скоростей для положения i механизма отложим произвольный отрезок изображающий скорость точки В1. Пусть рibi>=100 мм тогда масштаб плана скоростей будет
Необходимые для построения плана ускорений скорости сводим в таблицу 2.1.
Исходными данными для построения плана ускорения являются план положения механизма план скоростей и ускорения точек ведущего звена АВ.
Ускорение точки В2 равно ускорению точки В1
Нормальное ускорение точки В2 равно ускорению точки В1 ведущего звена вращающегося равномерно:
=аВ1= 12·LAB=4392·009=1741 (2.4)
и направлено к центру вращения.
Тангенциальное ускорение:
=1·lАВ=110·009=99 мс2(2.5)
Пользуясь тем же разложением что и при определении скоростей получим следующие уравнения ускорений:
Ускорение Кориолиса в уравнении (2.6)
Угловая скорость звена 3
= = = 249 (с-1 )(2.9)
Подставляя найденное в формуле (2.9) получим :
=2·249· 09=4483 (с-1 )
Направление получим поворотом вектора VВ3В2 в сторону 3 на 90°.
Нормальное ускорение точки В3 в уравнении (2.7)
Расстояние lСB снимаем со схемы механизма:
lВC=p4В>·c=62·25·10-3=0155 (м) (2.11)
Подставляя найденное в (2.10) получим:
По уравнениям строим план ускорений. Отрезок > изображающий ускорение примем равным 200 мм.
При этом масштабный коэффициент плана ускорений
а===087 (м·с2мм)(2.12)
Для определения ускорения точки Е будем иметь следующее уравнение:
Ускорение точки D в этом уравнении определим по теореме подобия. Из теоремы следует что отрезок
d>= B3>=141=82 мм(2.13)
По этой же теореме ускорение точки S3 s3>=9 мм; аS3=8 мс2.
Следующее ускорение из уравнения
Откладываем направление из конца вектора скорости т.D а направление ускорения точки Е из полюса плана ускорений. Пересечение линий направления дает величины ускорений и аЕ.
Ускорение S2 равно В2 ускорение S3 =0 так как по условию задачи в нем находится центр вращения кулисы ускорение S4 найдем соединив точку с центром отрезка ED aS1=0 aS5= aЕ.
Ускорения необходимые для определения сил инерции сводим в таблицу 2.2.
Угловое ускорение звена 3:
Направление 3 - против часовой стрелке.
Угловое ускорение звена 4:
Направление 4 - против часовой стрелке.
3 Определение сил инерции
Главный вектор и главный момент сил инерции звена определяют по формулам:
Для звена 1 с маховиком:
Ри4 = m4·аS4 =54·57= 3078 (Н)
Ми4 =IS4 ·4=2642·28=74 (Н·м)(2.16)
На чертеже х4>===96мм
Ри2 = m2·aS2 =9·174 = 1566 (Н) (2.17)
Ри5 = m5·aS5 = 27·57= 1566 (Н)
4 Структурный анализ
Механизм обладает одной степенью свободы. Таким же должно быть число степеней свободы системы с которой начинается образование механизма. В эту систему должны входить стойка и одно из звеньев связанных с ней одноподвижной кинематической парой. Примем в качестве такого кривошип т.к. на него действует неизвестная внешняя нагрузка - движущий момент МД . Этот момент был определен в предыдущем разделе исходя из предложения о том что Мд = const. В этом разделе мы определим его более точно.
Схема образования исследуемого механизма выглядит следующим образом (рисунок 4):
Рисунок 4 – Разделение механизма на группы Ассура.
Силовой расчет ведётся в порядке обратном образованию механизма т.е. сначала будет рассчитана группа 54 затем 32 и в последнюю очередь - 10.
4.1 Расчёт группы 54
Из равновесия звена 4 следует что
=-РИ4 ·hИ4>- ·h34>-G4·hG4>=0(2.18)
Из равновесия звеньев 4 и 5 следует что
+ + + + ++ = 0(2.19)
Графическое решение уравнения (2.19) дает
R05=415 (Н) = 1673 (Н)
4.2 Расчёт группы 32
Звено 2 находится в равновесии под действием двух сил R32 и R12 следовательно R32 =-R12.
Из равновесия звеньев 2 и 3 следует что
=- R43·h43>+G2·hG2>- РИ2 ·hИ2>+ R12·h12>=0(2.21)
Из равновесия структурной группы 3 2 следует что
Отсюда графическим путём находим: R03 = 3199 Н
4.3 Расчёт начальной системы 10
Из равновесия звена 1 следует что
= -R21·h21>+ МУ +G1·hG1>=0
МУ = R21·h21>·l-G1·hG1>·l =3737·35·25·10-3-176·16·25·10-3=321 Н·м (2.22)
5 Проверка силового расчёта
Проверку выполним с помощью «Рычага Жуковского» (рисунок 5). Для этого к повернутому плану скоростей приложим внешние силы механизма и силы инерции. Момент Му представим в виде пары сил Рп приложенных перпендикулярно кривошипу в точках А и В. При этом
План скоростей дополним отрезком
pt4 >= еd >· =272· =158(мм)(2.23)
Этот отрезок изображает скорость точки Т4 пересечения силы PИ4 с кулисой ED. Формула (2.22) вытекает из теоремы подобия.
Рисунок 5 – Определение уравновешивающей силы с помощью рычага Жуковского
Силы проходящие через полюс "Рычага Жуковского» не показываем т.к. они не дают момента относительно этого полюса. Сумма моментов всех
МУ = Pу·lАВ=3314·009=298 Н·м.
Чтобы не путать этот момент с найденным из формулы (2.22) обозначим
его . Ошибка составляет
что приемлемо т.к. допускаемая ошибка составляет 10%.
Синтез эвольвентного зацепления (лист 3 графической части)
1 Предварительный расчет и выбор электродвигателя
Кинематический расчет привода производится одновременно с подбором по каталогу приемлемого по мощности и частоте вращения электродвигателя и сводится к определению общего передаточного числа привода и разбивки его между отдельными узлами и типами передач согласно заданной кинематической схеме (рисунок ). Механизм состоит из открытой и закрытой (редуктора) зубчатых передач.
Скорость вращения входного вала (кривошипа) рычажного механизма задана.
Рисунок 6 - Кинематическая схема механизма
По найденной уравновешивающей силе Рп приложенному к кривошипу определяют вращающий момент на валу кривошипа привода:
=125·3314·009=3728 Н·м
где – уравновешивающая сила
– коэффициент запаса определяемый в зависимости от неучтённых нагрузок степени влияния сил и моментов трения ошибки в положении силового расчета условий эксплуатации и прочего k=12..3
Находят мощность на ведомом валу привода:
где – угловая скорость вала кривошипа 4398 радс.
Определяют мощность на валу электродвигателя:
где – КПД всего привода равный произведению частных КПД передач входящих в привод:
здесь =095– КПД закрытой передачи (редуктора);
=09– КПД цепной передачи;
=099– КПД одной пары подшипников качения;
M=4 - число пар подшипников.
Среднее значение передаточных отношений и КПД различных типов передач взяты из таблицы 1 [5].
общ=095·09·0994=082 тогда =19972 кВт.
По найденной мощности Nдв определяют тип трехфазного асинхронного электродвигателя наиболее подходящего для конкретных условий работы (таблица 2 [5]).
Выбираем двигатель 4АМ80В2Y3 мощностью 22 кВт и частотой вращения 3000 обмин.
Определяют общее передаточное отношение всего привода:
где – частота вращения вала электродвигателя;
=420 обмин – частота вращения вала кривошипа. С учетом скольжения частота вращения двигателя равна 2850 обмин.
После определения общего передаточного числа привода производится его разбивка на передаточные числа отдельных ступеней при этом используются рекомендуемые значения передаточных чисел. При разбивке общего передаточного числа исходим из равенства:
где - частные передаточные числа отдельных передач привода.
Передаточное число закрытой передачи – редуктора выбираем равным 355. Тогда передаточное отношение цепной передачи:
Это число входит в промежуток рекомендуемых передаточных чисел для цепных передач.
Определяют частоты вращения всех валов привода:
быстроходный вал редуктора: n2===1500 обмин.;
тихоходный вал редуктора(вал кривошипа): 4225 обмин.
Угловая скорость валов привода:
где n – частота вращения соответствующего вала.
=2985 об-1; =1571 об-1; =442 об-1.
Находим крутящие (вращающие) моменты всех валов привода:
=1261·355·095=4251 Н·м.
Кинематический расчет привода
Частота вращения обмин
тихоходный вал - вал кривошипа
2 Расчет закрытой зубчатой передачи
Определяем межосевое расстояние и округляем его до стандартного:
где - коэффициент межосевого расстояния (для прямозубых колес принимаем );
=0315- коэффициент ширины принимают в зависимости от положения колес относительно опор.
принимаем а=50 мм по ГОСТ 2185-80.
Определяем модуль зацепления:
Значение модуля зацепления m полученное расчетом округляем в большую сторону до стандартного из ряда чисел и принимаем равным 1.
Произведем геометрический расчет цилиндрической прямозубой передачи составленной из цилиндрических колес. Расчет ведется исходя из условия отсутствия бокового зазора между зубцами. Требуется также обеспечить отсутствие подрезания зубцов во время их нарезания зуборезным инструментом. Для соблюдения этих условий в случае необходимости сдвигают зуборезный инструмент по отношению к оси заготовки.
Сумма коэффициентов сдвигов определяют по формуле
где αр=20° – угол зацепления зуборезного инструмента αсб – угол зацепления колес в сборке равный
Следовательно и [1+2]=0 т.е смещения инструмента при нарезании колес не требуется.
Определяем геометрические размеры зубчатой передачи.
Диаметры делительных окружностей колес:
Диаметры основных окружностей:
db1= d1cosα= 22cos20° = 2067 мм
db2 = d2·cosα =78cos20° = 733 мм.
Диаметры начальных окружностей:
Диаметры окружностей выступов зубчатого колеса.
da1 = d1+2· ha = d1+2· m=22+1·2 =24 мм
da2 = d2+2· ha = d2+2· m=78+1·2 =80 мм.
Диаметры окружностей впадин зубчатых колес равны:
df1 = d1-2· hf = d1-25·m=22-25 =195 мм
df2 = d2-2· hf = d2-25· m=78-25 =755 мм.
Определим шаг зацепления по дуге начальной окружности.
Толщина зуба S и ширина впадины е по дуге начальной окружности равны между собой т.е. S =S1 =S2 е=е1=е2.
S =е= 05·р = 05·314 = 157 мм.
Определим коэффициент перекрытия:
3 Построение профилей зубьев колес
Построение зубчатого зацепления ведется в следующем порядке:
Масштабная высота зуба должна быть не менее 20 мм тогда
Проводим линию центров отмечаем на ней центры О1 и О2 на расстоянии =1000 мм (центры колес О1 и О2 могут выходить за пределы чертежа).
В выбранном нами масштабе вычерчиваем окружности зубчатых колес: основные начальные окружности выступов и впадин.
Через полюс зацепления Р проводим общую касательную к начальным окружностям (перпендикулярно к линии центров) и линию зацепления NN касательную к основном окружностям при этом угол а между этими касательными должен быть равен а = 20° .
Проведем перпендикуляры О1А0 и О2В0 из центров О1 О2 к линии зацепления (длины этих перпендикуляров есть радиусы основных окружностей). Участок А0В0 линии зацепления называется теоретическим участком линии зацепления.
Каждый зуб зубчатою колеса находится в зацеплении не на всем своем пути а только на каком-то участке т.е. в какой-то точке он входит в зацепление а в какой-то выходит из него. Этот участок лежащий на линии зацепления NN и образованный пересечением этой линии с окружностями выступов называется практическим или рабочим участком линии зацепления. На чертеже практический участок линии зацепления обозначен точками А и В.
Строим эвольвентные профили только центральной пары сопряженных зубьев так чтобы они касались в полюсе зацепления Р.
Эвольвентной окружности называется кривая описываемая точкой прямой линии перекатываемой по этой окружности без скольжения. Окружность по которой перекатывается прямая при образовании эвольвенты называется основной окружностью. Следовательно эвольвентные участки зубьев будут находиться в пределах между основными окружностями и окружностями выступов колес.
Построение эвольвенты производим общепринятым методом. Для этого отрезок А0P линии зацепления (второго колеса) разбиваем на равное число частей (допустим на четыре) обозначим точки деления 1 2 3 4 и т.д. продолжив деление по другую сторону точки L.
Отрезок LР линии зацепления играет роль производящей прямой при обкатывании которой без скольжения по основной окружности точка Р опишет эвольвенту.
Полученные отрезки Р-1 1-2 2-3 . . . начиная от точки L отложим по хорде на основной окружности при этом разностью между длинами дуги и хорды пренебрегаем. Полученные точки обозначим 1' 2' 3'
Соединим эти точки с центром колеса и проведем через них касательные к основной окружности которые будут перпендикулярны радиусам.
Отложим на касательных отрезки равные расстоянию до полюса Р от соответствующей точки деления т.е. вдоль первой касательной откладываем отрезок Р-1 вдоль второй касательной — отрезок Р-2 и т.д. Полученные точки обозначим 1" 2" 3" и затем последовательно соединим их плавной кривой. Данная кривая и будет представлять эвольвентный участок профиля зуба. Для сопряженного колеса эвольвентный профиль зуба строится аналогично.
Неэвольвентный участок профилей зубьев т.е. участок в пределах от основной окружности до окружности впадин для случая dfdb очерчивается радиальными прямыми после чего у основания зуба производят их сопряжение с окружностями впадин радиусом ρ =(02-03)m=02·1=02 мм . Для построения симметричного профиля зуба отложим толщину зуба в масштабе ==157 мм; проведем ось симметрии и шаблонов строим профиль зуба.
Аналогично производится построение профилей соседних зубьев.
Обозначим рабочие участки профилей зубьев. Учитывая что в точке А начинается зацепление т.е.в ней контактируются крайняя точка головки зуба второго (большого) колеса и наинизшая точка ножки зуба первого (малого) колеса радиусом О1А сделаем засечку на профиле зуба малого колеса которая определит положение наинизшей точки первого колеса. Делая засечку на профиле зуба второго (большего) колеса радиусом О2В определим наинизшую точку участвующую в зацеплении для этого колеса. Определим длину дуги зацепления по любой из окружностей в пределах которой происходит зацепление зубьев предварительно проведя пунктиром через точки А и В сопряженные профили зубьев в начале и конце зацепления. Дуги сd и ef между положениями соответствующих профилей зубьев в начале и конце зацепления для каждого из колес есть пути проходимые зубьями за время зацепления одной пары зубьев измеренные по начальной окружности.
При работе зубчатых колес необходимо чтобы в любой момент времени зубья находились в зацеплении. Для этого требуется чтобы дуга зацепления была больше шага. В противном случае первая пара зубьев выйдет из зацепления раньше чем войдет в зацепление следующая пара зубьев.
Отношение дуги зацепления к шагу характеризуется коэффициентом перекрытия е.
Определим коэффициент перекрытия графическим и аналитическим методами.
На основании данного выше определения запишем
(величина АВ находится при измерении на чертеже). Для определения коэффициента перекрытия аналитическим методом имеем:
Вычислим процент расхождения
Полученный процент расхождения не превышает допустимой величины.
В курсовом проекте проведен динамический синтез и анализ рычажного механизма синтез эвольвентного зацепления. Результаты проектирования дают возможность оценить кинематического схему механизма по кинематическим и динамическим качествам с тем чтобы определить направление совершенствования кинематических схем подобных механизмов. Совершенные кинематические схемы обеспечивают более экономические в отношении металлоёмкости машины что является одним из основных требований машиностроения.
Более совершенные кинематические схемы механизмов можно получить применяя аналитические методы анализа и синтеза с использованием современной вычислительной техники.
Артоболевский И.И. Теория механизмов и машин И.И. Артоболевский. М.: Наука 1988. -640 с.
Курсовое проектирование по теории механизмов и машин под ред. проф. С.И.Артоболевского. М. :Высшая школа 1960. - 248 с.
Левитская О.И. Курс теорий механизмов и машин О.Н. Левитская Н.И. Левитский. М.: Высш. шк. 1978. -226 с.
С.А. Чернавский К.Н.Боков И.М.Чернин. Курсовое проектирование деталей машин. Учебное пособие для учащихся машиностроительных специальностей техникумов – М.: Машиностроение1988. – 416 с. ил.
Анурьев В.И. Справочник конструктора – машиностроителя: в 3 – х т. – М.: Машиностроение1978. – т. 12.
Лист 1.dwg

Графики работ приведеного и движущего моментов
График приращения кинетической энергии
Графики приведеного и движущего моментов
График силы полезного сопротивления
Приведение сил к звену (определение силы Рп)
Планы положений механизма
Лист 3.dwg

Лист 2.dwg

План сил группы 5-4
План сил группы 2-3
Начальная система 1-0
График силы полезного сопротивления