Проектирование технологического процесса обработки вал-шестерня


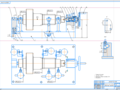
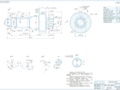
- Добавлен: 04.07.2022
- Размер: 2 MB
- Закачек: 1
Описание
Проектирование технологического процесса обработки вал-шестерня - Дипломный проект
Состав проекта
![]() |
![]() |
![]() |
![]() ![]() ![]() ![]() |
![]() ![]() ![]() ![]() |
![]() ![]() ![]() ![]() |
![]() ![]() ![]() ![]() |
![]() ![]() ![]() ![]() |
![]() ![]() ![]() ![]() |
![]() ![]() ![]() |
![]() |
![]() ![]() ![]() ![]() |
![]() ![]() ![]() |
![]() ![]() ![]() ![]() |
![]() ![]() ![]() ![]() |
![]() ![]() ![]() ![]() |
![]() ![]() ![]() |
![]() ![]() ![]() |
![]() ![]() ![]() |
![]() ![]() ![]() |
![]() ![]() ![]() |
![]() ![]() ![]() |
![]() ![]() ![]() |
![]() ![]() ![]() ![]() |
![]() ![]() ![]() ![]() |
![]() ![]() ![]() ![]() |
![]() ![]() ![]() ![]() |
![]() ![]() ![]() ![]() |
![]() ![]() ![]() ![]() |
![]() ![]() ![]() ![]() |
![]() ![]() ![]() ![]() |
![]() ![]() ![]() ![]() |
Дополнительная информация
1-ЫЙ.cdw

университет гр. ТМА-021
Размеры в скобках-после сборки
Предельные отклонения по ОСТ 37.001.246-82
2-ОЙ!.cdw

университет гр. ТМА-021
* Размеры для справок
** Обработать по сопрягаемым деталям
Неуказанные предельные отклонения по ОСТ
3-ИЙ.cdw

Белорусско-Российский
университет гр. ТМА-021
4-ЫЙ.cdw

Деталь.cdw

Направление линии зуба
Нормальный исходный контур
Коэффициент смещения
Степень точности ГОСТ 1643-81
Средняя лина общей нормали
Обозначение чертежа
Белорусско- Российский
Поковка гр. 2 143 207НВ ГОСТ 8479-70.
м. Поверхность зубьев 57 65 HRC
сердцевина зубьев 32 42 HRC. Резьбу предохранить от
Неуказанные предельные размеры по ОСТ 37.001.246-82.
Допуск непостоянства диаметра в поперечном
ипродольном сечениях поверхностей Ж не более 0
*Боковые стороны шлицев должны быть
прямымиипараллельными между собой до указанного диаметра.
**Допускается отжиг ТВЧ.
После механической обработки допускается глубина
цементационного слоя не менее h 0
Общие допуски по ГОСТ 30893.1: Н14
Остальные технические требования по СТБ 1014-95.
Заготовка.cdw

Поковка гр. 2 143 207НВ ГОСТ 8479-70.
Поковка от окалины очищается дробью.
Остальные технические требования по СТБ 1014-95.
Записка1.doc
Использование более совершенных методов изготовления машин имеет при этом первостепенное значение. Качество машины надежность долговечность и экономичность в эксплуатации зависят не только от совершенства ее конструкции но и от технологии ее изготовления.
Инженер-технолог стоит последним в цепи создания новой машины и от объема его знаний и опыта во многом зависит ее качество.
Эти основные предпосылки определяют следующие важнейшие направления развития технологии механической обработки в машиностроении.
Совершенствование существующих и изыскание новых высокопроизводительных методов и средств выполнения резко возросших по объему отделочных операций с целью повышения точности обработки и сокращения их трудоемкости.
Совершенствование существующих и изыскание новых высокопроизводительных процессов выполнения получистовых и чистовых операций металлическим и абразивным режущим инструментом.
Комплексная механизация и автоматизация технологических процессов на основе применения автоматических линий автоматизированных и полуавтоматизированных станков средств активного контроля быстродействующей технологической оснастки групповых методов обработки технологически подобных деталей.
Развитие процессов формообразования пластическим деформированием и применение методов тонкого пластического деформирования для отделочных операций.
Исходные данные для проекта
Исходными данными для проектирования являются задание на дипломное проектирование рабочие чертежи детали указанные в задании технические условия на деталь годовой объем выпуска.
2 Определение типа производства
Тип производства в соответствии с ГОСТ 3.1108-74 характеризуется коэффициентом закрепления операций который показывает число различных операций закрепленных в среднем по цеху за каждым рабочим местом в течение месяца. Коэффициент закрепления операций определяется по формуле:
где - суммарное количество различных технологических операций подлежащих выполнению в течение месяца;
- суммарное количество мест необходимых для выполнения месячной программы.
Предварительно исходя из годового выпуска и массы детали согласно [13] принимаем серийное производство.
В серийном производстве детали изготавливаются партиями размер партии рассчитывается по формуле :
где N – годовой выпуск изделия;
а – количество дней запаса ();
Ф – количество рабочих дней в году ();
По размеру партии детали устанавливаем что производство будет среднесерийным.
Патентные исследования червячных фрез
Развитее машиностроения тесно связано с совершенствованием конструкций технологических машин и в первую очередь металлорежущих станков. Надежная и высокопроизводительная работа оборудования невозможна без компенсации его столь же надежным производительным режущим инструментом и инструментальной оснасткой.
Задачи проектирования состоящие из разработки элементов конструкций рабочей части присоединительной и направляющей частей а также технических требований.
Использование для проектирования хорошо проверенных практикой аналогов или их элементов ускоряем разработку инструмента во многих случаях исключает необходимость выполнения расчетов на прочность жесткость размещение стружки и гарантирует средний уровень качества инструмента однако ограничивает проектировщика известными стереотипами (готовыми решениями) и тормозит производство необходимое для совершенствования старых и создания новых высокоэффективных инструментов.
Далее будут рассмотрены несколько изобретений позволяющих повысить точность и производительность обработки применить более простые более надёжные конструкции зуборезного инструмента.
Первое из рассмотренных изобретений – (SU 1513748 A1 авторы: С.А. Володин и А.С. Крепак) может быть использовано при нарезании зубчатых колёс червячными фрезами. Целью данного изобретения является повышение стойкости инструмента путём гашения вибраций при фрезеровании.
Червячная фреза представленная на рисунке 2.1 выполняется с разнонаправленными чередующимися через одну стружечными канавками угол наклона которых к оси различен канавки попеременно выполнены прямыми 1 и винтовыми 2. Винтовые канавки наклонены к оси фрезы под углом λ = 1-4°.
– прямая стружечная канавка
– винтовая стружечная канавка
Рисунок 2.1 – Червячная фреза
Фреза работает следующим образом. Прямые 1 и винтовые 2 стружечные канавки образуют соответственно прямые и винтовые передние поверхности гребенок поочередно вступающих в резание.
Колебания сопровождающие резание прямыми и винтовыми гребенками находятся в противофазе друг другу вследствие чего достигается снижение их интенсивности способствующее повышению стойкости режущих зубьев фрезы.
Второе изобретение – (SU 1276449 A1 автор: А.Н. Шевченко) представляет конструкцию червячной сборной фрезы для нарезания цилиндрических зубчатых колёс.
Цель изобретения — снижение трудоемкости изготовления червячных фрез. На рисунке 2.2 представлена конструкции фрезы включающая корпус 1 режущие 2 и опорные 3 зубчатые рейки и крышки. В корпусе фрезы выполнены продольные пазы со ступенчатым основанием для размещения реек. При этом ступень предназначенная для размещения опорной зубчатой рейки по глубине превышает ступень для размещения режущей зубчатой рейки на величину выбираемую из соотношения:
где а – величина смещения ступеней мм;
m – модуль фрезы мм.
– режущая зубчатая рейка
Рисунок 2.2 – Сборная червячная фреза
Третье изобретение – (971598 автор: В.М. Браслсвски А.Г. Гладких В.В. Топычканов) представляет инструмент для чистовой обработки зубчатых колёс.
Изобретение относится к металлообработке в частности к инструментам для чистовой обработки зубьев зубчатых колес.
Известна червячная фреза режущие кромки которой выполнены прямолинейными. Однако при работе такими фрезами не обеспечивается необходимое качество поверхности зубьев особенно при нарезании колес из высокопрочных и вязких материалов.
Целью изобретения представленного на рисунке 2.3 является повышение качества обрабатываемых зубьев за счет уменьшения высоты шероховатости.
Цель достигается тем что в инструменте для чистовой обработки зубчатых колес состоящем из корпуса и рабочих элементов последние расположены вдоль прямолинейных образующих представляющих собой однополостные гиперболоиды вращения осевые гиперболические сечения которых совпадают с обрабатываемыми профилями зубьев в расчетных точках при этом рабочие элементы подпружинены относительно корпуса в направлении оси его вращения. Выполнение на рабочих элементах инструмента канавок образующих режущие кромки направленных под острыми углами к радиусам проведенным от оси вращения инструмента в точки их расположения позволяет использовать инструмент в качестве шевинговального.
Рисунок 2.3 – Инструмент для чистовой обработки зубчатых колёс
Четвёртое изобретение – (SU 1181796 A авторы: В.Н. Подураев Е.Д. Баклунов и А.В. Попов) способ обработки передней поверхности зубьев червячной фрезы – рисунок 2.4.
Цель изобретения - повышение точности червячных фрез с разнонаправленными стружечными канавками путем повышения качества обработки передней поверхности и повышения производительности зубофрезерования путем выполнения оптимальных передних углов зубьев фрезы.
Фрезу 1 устанавливают на станке конический шлифовальный круг 2 устанавливают таким образом что касательная и к образующей производящей поверхности круга 2 совмещена с карательной к боковой режущей кромке 3 зуба 4 в точке принадлежащей делительному цилиндру производящего червяка фрезы 1. Круг 2 подворачивают вокруг совмещенных касательных на угол равный положительному значению переднего угла зуба фрезы. Последовательно обрабатывают передние поверхности 5 одноименных левых 4 (или правых 6) зубьев при вращении фрезы 1 вокруг оси в направлении противоположном кругу 2 при вращении последнего вокруг оси. Круг 2 перемещают в направлении и поворачивают вокруг касательных на определённый угол.
После окончания обработки передней поверхности зуба шлифовальному кругу сообщают перемещение выводят из стружечной канавки 7 и останавливают в нерабочем положении. Фрезу в это время вращают в направлении. Шлифовальный круг 2 снова перемещают в направлении и к моменту когда фреза 2 повернется на два угловых шага стружечной канавки 7 обрабатывают следующую переднюю поверхность зуба.
После обработки всех передних поверхностей одного направления производят переналадку на обработку передних поверхностей другого направления. Обработку передних поверхностей другого направления производят в том же порядке.
Рисунок 2.4 – Способ обработки передней поверхности зубьев червячной фрезы
Технологическое проектирование
1 Назначение и конструкция детали
Вал-шестерня 546П-1802086 входит в состав коробки отбора мощности тягача. Коробка отбора мощности предназначена для привода насоса рулевого управления тягача и насосов гидросистемы скрепера а также для передачи крутящего момента от двигателя к сцеплению.
Крутящий момент от маховика двигателя передается через полужесткую муфту уменьшающую пиковые нагрузки на каретку 24 которая свободно вращается на первичном валу 8.
Ведущая шестерня 7 посаженная на шлицы первичного вала 8 приводит во вращение две паразитные шестерни 10. Одна из этих шестерен приводит во вращение ведомую шестерню 16 установленную на вторичном валу 14.
Валы 11 паразитных шестерен имеют внутренние шлицы для привода насосов рулевого управления и гидросистемы скрепера.
Внутренние шлицы втулки 15 установленные в обоих концах вторичного вала приводят во вращение два насоса гидросистемы скрепера.
Вал-шестерня имеет следующие поверхности (конструкторские базы):
)Основные поверхности – определяют положение детали в узле;
)Вспомогательные поверхности – определяют положение присоединительных деталей.
Поверхности 55n6() предназначены для установки подшипников. Точность размеров поверхностей обеспечивается по 6-му квалитету точности т.к. подшипник имеет класс точности 0. Для того чтобы избежать перекоса подшипников при запрессовке и повышенного шума и вибрации при работе допуском Т=005 мм относительно базы А ограничено торцовое биение буртиков прилегающих к этой поверхности.
Шлицы фланца предназначены для крепления ведомой шестерни. Прочность и точность шлиц достигается за счет закалки ТВЧ и последующим шлифованием по наружной поверхности.
Два отверстия М14-6Н предназначены для закрепления стопорной пластины.
Для обеспечения необходимых рабочих параметров в качестве материала для фланца выбрана Сталь 18ХГТ ГОСТ 4543-71. Механические свойства данной стали приведены в таблице 3.1.1.
Таблица 3.1.1- Механические свойства Стали 18ХГТ
Предел текучести МПа
Предел выносливости МПа
Относительное удлинение y%
Химический состав стали приведен в таблице 2.
Таблица 3.1.2 - Химический состав Стали 18ХГТ
Рисунок 3.1.1 – Рабочий чертеж детали
2 Анализ технологичности конструкции вала-шестерни
Отработка конструкции на технологичность представляет собой комплекс мероприятий по обеспечению необходимого уровня технологичности конструкции по установленным показателям направлена на повышение производительности труда снижение затрат и сокращение времени на изготовление изделия при обеспечении необходимого его качества.
Анализ технологичности является одним из важных этапов в разработке технологического процесса от которого зависят его основные технико-экономические показатели: металлоемкость трудоемкость себестоимость.
Оценка технологичности конструкции может быть двух видов: качественной и количественной.
Форма вала-шестерни представляет собой тело вращения. Все поверхности являются доступными для обработки. Конструкция детали позволяет получить заготовку форма и размеры которой будут максимально приближены к форме и размерам детали.
С точки зрения обработки шлицы нетехнологичны так как операция нарезания шлицев со снятием стружки производится в основном малопроизводительными методами.
В остальном деталь достаточно технологична допускается применение высокопроизводительных режимов обработки имеет хорошие базовые поверхности для первоначальных операций и довольно проста по конструкции. Шлифовальные операции выполняются на универсальном широко используемом оборудовании. Технологические и конструкторские базы совмещаются следовательно принцип постоянства баз выполняется.
В соответствии с ГОСТ 14.202-73 рассчитываем показатели технологичности конструкции детали.
Средний квалитет точности обработки детали определяется по формуле:
где – номер квалитета точности
- количество размеров деталей обрабатываемых по - му квалитету.
Для расчета среднего квалитета точности составляем исходную таблицу точности 3.
Таблица 3 - Точность поверхностей вала
Квалитет точности JT
Количество размеров h
Коэффициент точности обработки определяется по формуле:
Средняя шероховатость поверхностей определяется по формуле:
где - значение шероховатости
-количество поверхностей имеющих шероховатость .
Для расчета средней шероховатости составляем исходную таблицу шероховатости детали 4.
Таблица 4 - Шероховатость поверхностей детали
Шероховатость Rа мкм
Количество поверхностей n
Коэффициент шероховатости детали определяется по формуле:
Коэффициент использования материала определяется по формуле:
где - масса детали кг;
- масса заготовки кг.
В целом конструкция вала-шестерни является достаточно технологичной и позволяет сравнительно легко и гарантированно обеспечивать заданные требования известными технологическими способами. При этом на всех операциях обеспечивается соблюдение принципа единства и постоянства баз.
3 Выбор метода получения заготовки
Деталь представляет собой тело вращения размеры которого уменьшаются от торца к торцу. Заготовка вала-шестерни может быть получена горячей штамповкой в закрытом или открытом штампе. Штамповка в закрытом штампе предпочтительнее так как сокращается расход металла (отсутствие заусенец).
Расчет стоимости заготовки полученной горячей штамповкой выполняется по формуле:
где - базовая стоимость одной тонны заготовок;
- стоимость одной тонны отходов;
- коэффициент зависящий от класса точности;
- коэффициент зависящий от степени сложности;
- коэффициент зависящий от массы заготовки;
- коэффициент зависящий от марки материала;
- коэффициент зависящий от объема выпуска.
Экономический эффект достигается за счет сокращения расхода метала:
где - объём выпуска шт.
Следовательно заготовку вала-шестерни целесообразнее получать штамповкой в закрытом штампе так как уменьшается материалоемкость и как следствие уменьшаются экономические затраты на 14328600 рублей.
4 Принятый технологический процесс
В принятом технологическом процессе на всех операциях требующих большой точности изготовления базовыми поверхностями являются центровые отверстия. При этом технологические и конструкторские базы совпадают.
Таблица 3.4.1 - Маршрутный техпроцесс обработки вала-шестерни
Наименование и краткое содержание операции
Технологические базы
Фрезерно-центровальная
Сверлить центровочные отверстия
Фреза торцовая (2шт) 160 мм Т15К6
Сверло центровочное
Поверхности диаметром 80 мм и торец вала-шестерни
Продолжение таблицы 3.4.1
Обточить поверхность по копиру выдерживая размеры 60-074;
(поперечный суппорт) подрезать торцы в размер 101±03 51±03 97-087
Обточить поверхность по копиру выдерживая размеры 555-074; 60-074; 76-074
Резец проходной резец подрезной
Поверхность диаметром 64 мм и центровочные отверстия
Поверхность диаметром 60 мм и центровочные отверстия
Точить фаску 2 30° поверхность 558-013; 14105-016; подрезать торец выдерживая размер 52±03 и 95-087; точить фаску 2545°
Точить канавку 54-074
Точить поверхности 39-01; 558-013;
6-019 фаску 1645° три фаски 245° подрезать торец выдерживая размер 46±03 и 95-087
Точить канавку 54-074 и 69-074
Нарезать резьбу М392
Резец проходной сбор. резец канавочный.
Резец проходной сбор. резец канавочный резец резьбовой
Поверхность диаметром 555 мм и центровоч
Поверхность диаметром 558 мм и центровочные отверстия
Вертикально-сверлильная
Сверлить два отверстия 6+03мм
Зенковать четыре фаски
Поверхности диаметром 558 мм и
Сверлить два отверстие диаметром 119+04 мм
Зенковать две фаски 145° в отверстиях
Поверхность диаметром 706 мм и
Продуть воздухом два отверстия М14 для удаления стружки
Фрезеровать 10 шлицев выдерживая размер 74+2; 706
Зачистить заусенцы острые кромки притупить по всей длине шлица
Торцекруглошлифовальная
Шлифовать поверхность 555-003 на длину 35±02 и торец
Шлифовать поверхность 555-003 на длину 32±02 и торец
Фрезеровать зубчатый венец m=5.5 z=22
Поверхность диаметром 706 мм и торец
Окончание таблицы 3.4.1
Шевинговать зубчатый венец m=55 z=22
Зачистить забоины острые кромки притупить
Шлифмашинка ИП-2009А
Зенковать центровочное отверстие
Шлифовать поверхность 55+002+0039 70+002+0039 начисто и торец
Шлифовать поверхность 55+002+0039 начисто и торец
Колибровать резьбу М14
Расчет необходимого количества операций проведем для поверхности 55n6().
Допуск заготовки согласно ГОСТ 7505-89 составляет 36 мм т.е.
Необходимую величину уточнения определим по формуле:
С другой стороны уточнение определяется как произведение уточнений полученных при обработке поверхности на всех операциях (переходах) принятого техпроцесса:
где - величина уточнения полученного на
n – количество принятых в техпроцессе операций (переходов).
Для обработки данной поверхности в маршрутном технологическом процессе предусмотрены следующие операции:
Промежуточные значения рассчитываются по формулам:
где Т1 Т2 Т3 Т4 – допуски размеров полученные при обработке деталина первой второй и т.д. операциях.
) Шлифование черновое:
Шлифование чистовое:
Тогда по формулам (12) имеем:
Определяем общее уточнение для принятого маршрута обработки:
Полученное значение общего уточнения показывает что при принятом маршруте точность обработки поверхности 55n6() обеспечивается т.к..
5 Расчет припусков на обработку
Рассчитаем припуск на обработку поверхности 55n6()
Заготовка вала-шестерни получена штамповкой в закрытом штампе. Маршрут обработки включает следующие операции (переходы):
На токарной гидрокопировальной токарной с ЧПУ и торцекруглошлифовальной операциях обработка рассчитываемой поверхности ведется в центрах из чего следует что погрешность установки детали в радиальном направлении равна нулю т.е. e=0.
Погрешность заготовки определяем по формуле:
где – погрешность заготовки по смещению мм;
– погрешность заготовки по короблению мм;
- погрешность зацентровки мм.
Согласно ГОСТ 7505-89 = 1 мм.
Погрешность заготовки по короблению определяю по формуле:
где – удельная кривизна заготовки мкммм;
l – расстояние от торца до середины заготовки мм.
Согласно таблице 4.8 [3] DК = 1 мкммм тогда получаем:
Погрешность зацентровки определяем по формуле:
где - допуск на размер поковки мм.
При значении 36 мм получаем:
Тогда по формуле (14) получаем:
Величина остаточных пространственных отклонений:
) после чернового точения
) после чистового точения
) после чернового шлифования
Выписываем параметры шероховатости и глубины дефектного слоя Т [3] для всех операций и заносим их в таблицу 3.5.1.
=150 мкм; Т=250 мкм;
) шлифование черновое
) шлифование окончательное
Расчёт минимальных значений припусков производим по формуле предварительно заполнив расчётную таблицу 3.5.1.
где - высота неровностей полученных на предыдущей операции;
- глубина дефектного слоя полученного на предыдущей операции;
- пространственное отклонение полученное на предыдущей операции;
- погрешность обработки.
Минимальные припуски
)под черновое точение
) под чистовое точение
) под шлифование черновое
) под шлифование окончательное
Определяем расчетный размер путем последовательного прибавления расчетного минимального припуска каждого технологического перехода начиная с минимального размера:
=5502+01432=551632 мм;
= 551632+02864=554496 мм;
=554496+04496=558992 мм;
dзаг=558992+496=608592 мм.
В графу записываем расчётные размеры. Графу «допуск» заполняем в соответствии с достигнутой точностью при обработке деталей на данной операции.
Наибольшие предельные размеры определяем прибавлением допуска к наименьшему предельному размеру:
=5502+0019=55039 мм;
Предельные значения припусков определяем как разность наибольших предельных размеров и - как разность наименьших предельных размеров предыдущего и выполняемого переходов:
Общие припуски Z0max и Z0min рассчитываем суммируя их промежуточные значения и записывая их внизу соответствующих граф:
=140+290+450+4960=5880 мкм;
=151+380+1070+7860=9461 мкм.
Таблица 3.5.1-Расчёт припусков на обработку поверхности 55n6()
Технологические переходы обработки поверхности 55n6()
Элементы припуска мкм
Расчётный припуск мкм
Расчётный размер dp мм
Предельный размер мм
Предельные значения припусков мкм
Окончание таблицы 3.5.1.1
Величину номинального припуска определяем с учётом несимметричности расположения поля допуска заготовки.
где - нижнее отклонение заготовки мм;
- нижнее отклонение размера детали мм.
При значениях =12 мм; Нз=0019 мм получаем:
=588+12-0019=7061 мм.
Номинальный диаметр заготовки
При значениях dm zном=7061 получаем:
Проверку правильности расчётов производим по формуле:
При рассчитанных значениях получаем что 9461-5880=3581; 3600-19=3581 т.е. расчет припусков выполнен верно так как выполняется условие (20).
Строим схему графического расположения припусков и допусков поверхности 55n6() (рисунок 3.5.1).
Рисунок 3.5.1 – Схема графического расположения припусков и допусков на обработку поверхности 55n6() мм
Рассчитаем припуск на обработку торца
Маршрут обработки торца включает следующие операции (переходы):
Фрезерование торцев.
Выбираем значения высоты микронеровностей и глубины поверхностного дефектного слоя [3] и заносим их в таблицу 3.5.2.
Определяем величину суммарного пространственного отклонения мкм:
Определяем погрешность установки при фрезеровании :
где - погрешность базирования .
Расчет минимальных значений припусков производим пользуясь основной формулой:
Определяем расчетный размер мм:
Записав в соответствующей графе расчетной таблицы значения допусков на технологические переходы и заготовку в графе “предельный размер” определяем их минимальные значения для технологического перехода округляя расчетные размеры.
Наибольшие предельные размеры вычисляем прибавлением допуска к наименьшему предельному размеру:
Предельное значение припуска определяем как разность наибольших предельных размеров и – как разность наименьших предельных размеров предшествующего и выполняемого переходов:
Проверка правильности расчетов:
Расчеты выполнены верно.
Расчеты приводим в таблице 3.5.2.
Таблица 3.5.2 – Расчет припусков и предельных размеров по технологическим переходам на обработку поверхности длиной 3085 мм.
Расчетный припуск Zmin мкм
Расчетный размер lр
Предельное значение припуска мкм
Величину номинального припуска определяем с учетом несимметричности расположения поля допуска заготовки:
Номинальный размер заготовки:
Схема графического расположения припусков и допусков на обработку поверхности длиной 306 мм приведена на рисунке 3.5.2.
Рисунок 3.5.2 – Схема графического расположения припусков и допусков на обработку поверхности длиной 3085 мм
На все остальные обрабатываемые поверхности назначаем припуски по ГОСТ 7505-89 и ГОСТ 2590 – 71. Полученные данные приведены в таблице 3.5.3.
Таблица 3.5.3 –Припуски и допуски на обрабатываемые поверхности вала-шестерни
Предельные отклонения
6 Расчет режимов резания
6.1 Расчёт режимов резания аналитическим методом
Операция 005 – фрезерно-центровальная.
Станок фрезерно-центровальный модели МР-71М.
Исходные данные: режущий инструмент - две фрезы торцовых с пластинами из твердого сплава Т15К6 диаметр фрезы глубина резания ширина фрезерования число зубьев фрезы .
Подача при фрезеровании [9 табл. 32 стр.438].
Определяем окружную скорость фрезы м мин:
где и - соответственно коэффициент постоянный и
[4 табл.37 стр. 441];
- период стойкости [4 табл.38 стр. 444 ];
- коэффициент поправочный;
где - коэффициенты учитывающие соответственно качество
обрабатываемого материала состояние поверхности
заготовки инструментальный материал
Определяем частоту вращения фрезы об мин:
Корректируем частоту вращения по паспорту станка .
Определяем действительную скорость резания м мин:
Определяем окружную силу резания Кг:
где и - коэффициенты постоянные и показатели степени
- подача на один оборот фрезы мм об;
- коэффициент поправочный учитывающий качество обрабатываемого материала;
где - показатель степени [4 табл.22 стр. 430].
Определяем крутящий момент на шпинделе Кг м:
Определяем мощность резания кВт:
Проверяем режимы резания по мощности:
где - мощность шпинделя кВт;
где - мощность двигателя кВт.
Установленные режимы резания можно осуществлять на данном станке.
Операция 010(Установ Б) – токарная с ЧПУ. Черновое точение 555-074; 60-074; 76-074. Станок модели 16К20Т1. Резец для контурного точения Т15К6. Расчет приведем для 76-074.
Глубина резания t=2 мм;
Скорость резания рассчитываем по формуле
где - постоянный коэффициент;
- стойкость инструмента;
-поправочный коэффициент;
- показатели степеней.
=350; =100мин; =02; =015; =035
Поправочный коэффициент рассчитываем по формуле
где - коэффициент учитывающий влияние материала заготовки;
- коэффициент учитывающий состояние поверхности;
- коэффициент учитывающий материал заготовки.
Частоту вращения шпинделя при обработке рассчитываем по формуле:
где – скорость резания ммин;
– диаметр поверхности мм.
Принимаем по паспорту станка
Действительная скорость резания
Силу резания рассчитываем по формуле [12]
где – постоянный коэффициент;
– поправочный коэффициент;
– показатели степеней.
=300; =10; =075; =-015
Поправочный коэффициент рассчитываем по формуле[12]
=086*10*11*10*10=0946
Мощность резания рассчитываем по формуле [12]
где – сила резания Н;
– скорость резания ммин.
Мощность двигателя главного привода станка =10 кВт К.П.Д. привода станка =086. Тогда
Таким образом привод станка обеспечивает обработку при заданных режимах.
6.2 Расчёт режимов резания по нормативам
Операция 035–шлицефрезерная. Фрезерование шлицев z=11. Станок модели 5350. Инструмент фреза червячная специальная из быстрорежущей стали Р6М5.
Длину рабочего хода рассчитываем по формуле
где длина резания мм;
длина подвода врезания и перебега мм;
дополнительная длина вызванная наладкой и конфигурацией колеса.
Подачу на оборот детали назначаем по таблице с.149 [9].
По паспорту станка уточняем подачу
Скорость резания назначаем по таблице с.149 [9].
Частоту вращения инструмента рассчитываем по формуле
где - скорость резания ммин;
диаметр фрезы 100 мм.
По паспорту станка принимаем частоту вращения
Время на операцию определяется по формуле:
величина врезания и перебега мм;
Z- количество шлицев;
подача на оборот ммоб;
Основное время на операцию
Операция 050–торцекруглошлифовальная. Шлифовать поверхность 555-003 на длину 32 мм. Станок модели 3Т161. Инструмент шлифовальный круг.
Назначаем подачу на оборот детали :
Назначаем скорость вращения детали:
Назначаем скорость вращения круга:
Частоту вращения детали рассчитываем по формуле
диаметр обрабатываемой детали 50мм.
Частоту вращения детали принимаем равной n=1712 мин-1 так как станок модели 3Т161 позволяет осуществлять бесступенчатое регулирование.
где апр – припуск на сторону снимаемый на отдельном этапе предварительной подачи мм;
- минутные поперечные подачи мммин;
аок – припуск на сторону снимаемый на этапе окончательной подачи мм;
tвых – время выхаживания мин tвых=011 мин.
где а – общий припуск на сторону
Назначаем минутные подачи =16 мммин; =045 мммин.
Аналогично рассчитываем режимы резания на все остальные операции и записываем в операционные карты и сводную таблицу режимов резания
Таблица 3.6.2.1 – Сводная таблица режимов резания
Фрезерноцентровальная
Продолжение таблицы 3.6.2.1
Точить поверхность выдерживая размеры
Подрезать торец в размер 51±03
Точить поверхность выдерживая размеры 555-074; 60-074; 76-074
Подрезать торец в размер 2075±05
Точить фаску 2 30° поверхность 558-012; 14105-016; подрезать торец выдерживая размер 52±03 и 95-087; точить фаску 2545°
Точить поверхности 39-01; 558-012;
Зенковать четыре фаски 145° в отверстиях
Фрезеровать 10 шлицев выдерживая размер 74+2;
Зачистить забоины острые кромки притупить
Шлифовать поверхность55+002+0039 70+002+0039 начисто и торец
Шлифовать поверхность55+002+0039 начисто и торец
Окончание таблицы 3.6.2.1
Колибровать резьбу М14
7 Расчет точности операции
Расчет точности будем выполнять для токарной чистовой операции на которой производят точение поверхности 558-012.
При расчете технологической операции на точность величина суммарной погрешности обработки не должна превышать величины допуска на получаемый размер Тдет=120мкм.
Величина суммарной погрешности обработки по диаметральным размерам определяется по формуле
где - погрешность обусловленная износом режущего инструмента мкм;
- погрешность настройки станка мкм;
- поле рассеяния погрешностей обработки обусловленных действием случайных факторов мкм;
- погрешность установки заготовки мкм.
Погрешность обусловленную износом режущего инструмента определим по формуле
где - относительный износ инструмента =10 мкмкм;
- путь резания м (3.7.3)
где - диаметр обрабатываемой поверхности
- расчетная длина обработки с учетом длины врезания и перебега режущего инструмента мм;
- количество деталей в настроечной партии;
- подача инструмента.
Погрешность настройки станка определим по формуле:
где - смещение центра группирования размеров пробных деталей относительно середины поля рассеяния размеров мкм
где - мгновенная погрешность обработки =19мкм;
- количество пробных деталей=5.
- погрешность регулирования положения режущего инструмента на станке =15мкм
- погрешность измерения пробных деталей =9 мкм.
Поскольку обработка заготовки производиться в центрах погрешность установки заготовки
Так как Тдет=140 мкм то на данном переходе будет обеспечиваться необходимая точность обработки.
8 Техническое нормирование
Тип производства изготовления вала-шестерни соответствует среднесерийному производству в котором в качестве нормы времени рассчитывается штучно – калькуляционное время мин по формуле:
где - время штучное мин;
- подготовительно-заключительное время мин;
где – основное время мин;
вспомогательное время мин;
время на обслуживание рабочего места и отдых мин.
Основное время рассчитывается по формуле:
где Lрез – длина резания мм;
у – величина врезания и перебега мм;
i – количество рабочих ходов.
Расчет вспомогательного времени проведем по формуле:
где tус – время на установку и снятие детали мин;
tзо – закрепления и открепления заготовки мин;
tуп – время управления станком мин;
tиз – время измерения детали мин.
Для нормирования вспомогательного времени в среднесерийном производстве применяем нормативы приведенные в приложении 5 [3] применяя коэффициент .
Фрезерно-центровальная операция состоит из двух переходов:
Сверление центровых отверстий.
Определяем основное время:
Определяем вспомогательное время:
Определяем оперативное время :
Время на обслуживание и отдых задается в процентах от оперативного времени:
Определяем штучное время:
Подготовительно–заключительное время .
Определяем штучно – калькуляционное время:
Операция 045 – шлицефрезерная.
где – основное время;
вспомогательное время;
время на обслуживание рабочего места;
Основное время мин. рассчитываем по формуле:
Вспомогательное время мин. рассчитываем по формуле
где время на установку и снятие детали мин;
время на приемы управления станком;
время на измерение детали мин.
Время на приемы управления детали состоит из:
)времени включения станка кнопкой – 001мин;
)времени подвода или отвода инструмента к детали при обработке – 003мин;
)время перемещения фрезерной головки в продольном направления – 006 мин.
Вспомогательное время
Время на обслуживание и отдых:
Аналогично рассчитываем нормы времени на все остальные операции и записываем в операционные карты и сводную таблицу норм времени (таблица 3.8.1)
Таблица 3.8.1 – Сводная таблица норм времени
Вспомогатель-ное время tв мин
на обс -лужива-ние и отдых
Подго-тови-тельно–заключи-тельное время
Продолжение таблицы 3.8.1
Обточить поверхность по копиру выдерживая размеры
Обточить поверхность по копиру выдерживая размеры 555-074; 60-074;
Точить фаску 2 30° поверхность 558-012; 14105-016; подрезать торец выдерживая размер 52±03 и
-087; точить фаску 2545°
Окончание таблицы 3.8.1
Шлифовать поверхность
+002+0039 70+002+0039 начисто и торец
Шлифовать поверхность 55+002+0039 начисто и торец
Калибровать резьбу М14
9 Уточнение производства
Тип производства в соответствии с ГОСТ 3.1108-74 характеризуется коэффициентом закрепления операций который показывает число различных операций закрепленных в среднем по цеху за каждым рабочим местом в течение месяца.
Определяем расчетное количество станков m для каждой операции принятого технологического процесса изготовления щита подшипникового.
m (3.9.1)где T– штучно-калькуляционное время мин;
N – годовой объем выпуска деталей шт;
Fд – действительный годовой фонд времени ч.
- нормативный коэффициент загрузки оборудования (=08).
Количество фрезерно-центровальных полуавтоматов:
Принятое число станков nп=10
Коэффициент загрузки
Расчет количества станков сводим в таблицу 3.9.1
Таблица 3.9.1 – Расчет коэффициента закрепления операций
Наименование операции
5 Фрезерно-центровальная
0 Вертикально-сверлильная
5 Вертикально-сверлильная
0 Торцекруглошлифовальная
5 Торцекруглошлифовальная
5 Зубошевинговальная
Кз.о.=11614 по ГОСТ 3.1121-84 соответствует среднесерийному производству.
10 Расчет требуемого количества станков
Определяем расчетное количество станков m для каждой операции принятого технологического процесса изготовления вала-шестерни.
где T– штучно-калькуляционное время мин;
Расчет количества станков сводим в таблицу 3.10.1.
Таблица 3.10.1 – Расчет коэффициента закрепления операций
Наименование оборудования
Фрезерно-центровальный па МР-71М
Токарно-винорезный станок с ЧПУ 16К20Т1
Окончание таблицы 3.10.1
Вертикально-сверлильный танок 2Н150
Шлицефрезерный станок 5350
Круглошлифовальный станок 3А161
Зубофрезерный станок 5К324
Зубошевинговальный станок OS-30
Таким образом на разрабатываемом участке необходимо провести дозагрузку оборудования за счет дополнительных наименований обрабатываемых изделий получившиеся результаты представим в таблице 3.10.2.
Таблица 3.10.2 – Расчет необходимого количества станков после дозагрузки участка.
Количество станков шт
Токарно-винторезный станок с ЧПУ 16К20Т1
Вертикально-сверлильный станок 2Н150
11 Расчет необходимого количества рабочих
В составе персонала участка можно выделить следующие категории работников: рабочие (основные и вспомогательные) линейные руководители специалисты и прочие служащие (исполнители).
Численность основных рабочих Чо определяется по формуле:
где Фр – годовой фонд времени работы рабочего ч;
Кн – коэффициент выполнения нормы выработки (Кн=11-115).
При этом Фр рассчитывается по формуле:
Фр= (8×Дн+7×Дс)×Кнев (3.11.2)
где Дп и Дс – количество полных и сокращенных рабочих дней в году (по календарю);
Кнев – коэффициент невыходов по уважительным причинам (Кнев=09).
При многостаночном обслуживании расчетная численность корректируется и рассчитывается по формуле:
где Ноi – норма многостаночного обслуживания оп i-ой операции.
Расчет численности основных рабочих представлен в таблице 3.11.1.
Таблица 3.11.1– Численность основных рабочих
Годовая трудоемкость ч
Численность принятая чел
5Фрезерно-центровальная
Окончание таблицы 3.11.1
0Торцекруглошлифовальная
0Вертикально-сверлильная
5Торцекруглошлифовальная
Число вспомогательных рабочих Чв определяется делением объема обслуживания на норму обслуживания.
Для рабочих обслуживающих оборудование следует учитывать сменность работы nc.
Расчёт произведём по формуле:
Расчёт сводим в таблицу 3.11.2.
Таблица 3.11.2 – Численность вспомогательных рабочих
Наименование профессии
Объем обслуживания Оо ед.
Норма обслуживания Но ед.
Наладчик оборудования по типам станков:
- агрегатные фрезерные резьбообрабатывающие круглошлифовальные
- токарные сверлильные плоскошлифовальные
Станочник по ремонту оборудования
Электромонтер по межремонтному обслуживанию
Окончание таблицы 3.11.2
Кладовщик-раздатчик инструмента и приспособлений на рабочие места
Стропальщик и крановщик
Уборщик производственных помещений
Произведём расчет численности линейных руководителей.
На участке к ним относятся мастера старшие мастера и начальник участка.
Число мастеров определяется по формуле:
где - количество основных рабочих чел;
- количество вспомогательных рабочих чел;
– норма управляемости для мастеров (=20-25 чел.).
Для старших мастеров норма управляемости – 3 мастера а для начальника участка – 2 старших мастера.
На участке принимаем одного мастера.
Количество специалистов и исполнителей определим исходя из того что их число может быть принято 7-10% от общего числа рабочих.
На участке принимаем одного специалиста.
Таблица 3.11.3–Производственная площадь участка
12 Расчет необходимого количества транспортных средств
При выборе внутрицеховых средств для доставки заготовок на рабочие места и для межоперационной транспортировки следует учитывать тип производства габаритные размеры и вес перемещаемых деталей.
Для выбора межцеховых транспортных средств определяем массу межцехового потока по формуле:
где m- число наименований деталей;
G- годовая масса деталей кг;
N - годовая программа шт;
Масса заготовок поступающих на участок составляет: Q= 317606 кг
Для грузооборота в 317606 тонны в год на расстояние до 400м экономически целесообразно применять электрокары. Для транспортировки заготовок принимаем электротележку типа ЭК202.
- номинальная грузоподъемность- 1500кг;
- скорость передвижения – 671 кмч;
- габаритные размеры – 2790х1140 мм.
Детали транспортируются на электротележках в таре ящичного типа с размерами 1200х800 мм. Допустимый вес загружаемых в тару деталей- 4500кг.
Потребное количество электротележек определяем по формуле:
КТ.Р.= ×( + tЗ + tР) (3.12.2)
где - заполнение электротележек за один рейс q=05 т;
– номинальный годовой фонд времени электротележки при работе в одну смену =2070ч;
- количество смен в сутки;
–коэффициент использования электротележки по времени;
- средний пробег электротележки за один рейс туда и обратно м;
- средняя скорость электротележки кмч;
tЗ- время на загрузку электротележки за каждую операцию мин;
tР- время на разгрузку электротележки за каждую операцию мин:
Подставив все данные в формулу (3.12.2) получим:
Принимаем одну электротележку: КТ.ПР.=1
Определяем коэффициент загрузки электротележки:
Для межоперационного транспортирования принимаем две кран-балки (из расчёта одна-две кран-балки на 30-40 м пролёта) [6].
Площадь склада заготовок определяем по формуле:
где - черновой вес заготовок подлежащих обработке на участке в течение года т;
- количество дней на которые принимается запас материалов;
- количество рабочих дней в году;
- допускаемая нагрузка на площадь пола в тоннах на 1 м2;
При значениях: = 317606 т; t = 1; Ф = 253; = 25 т получаем:
Площадь склада готовых деталей рассчитываем аналогично:
Так как на участке находится линия по обработке деталей и необходим отвод стружки от каждого станка (с учётом догрузки объём стружки получается значительным) то для транспортирования стружки выбираем шнековый конвейер проходящий под станками. Шнековый конвейер выбираем по той причине что он является герметичным и исключает разбрасывание стружки по площади участка.
15 Планировка участка
Производственное здание выполнено с полным каркасом имеет в плане прямоугольную форму и состоит из параллельных однотипных пролетов. Пролеты образованы рядами железобетонных колонн которые являются вертикальными несущими элементами.
Расстояния между осями колонн в поперечном и продольном направлении образуют сетку колонн равную 18×12 м.
Для покрытия здания на колоннах установлены железобетонные сегментные фермы. Покрытие выполнено сборными предварительно напряженными железобетонными плитами размерами 3х12 м и доборными плитами 15х12 м. Стены здания толщиной 380 мм устроены из силикатного кирпича.
Для естественного освещения в стенах устроены оконные переплеты из стеклопакетов а на кровле – фонари прямоугольного сечения с вертикальным остеклением. Для искусственного освещения в верхней зоне здания предусмотрены светильники.
Для отвода дождевой воды с кровли на колоннах здания установлены трубы соединяющиеся с системой водосточной канализации расположенной под зданием.
В основу организации производства на участке положен принцип замкнутого технологического процесса с обеспечением обработки деталей в пределах одного участка.
Подача заготовок на участок и линии осуществляется электрокарами а межоперационное транспортирование – кран–балками.
В конце пролетов самого механообрабатывающего цеха располагаются вспомогательные службы: инструментально-раздаточная кладовая ремонтная служба контрольная лаборатория. Над вспомогательными помещениями на антресолях устроены помещения для администрации цеха и контролеров.
Административно-конторские и бытовые помещения цехов находятся в отдельном здании соединенном с производственным корпусом специальными переходами.
Участок изготовления валов организован по принципу прямоточности движения деталей в процессе обработки т.е. планировка увязана с технологическим процессом. Станки расположены в линию в порядке последовательности технологических операций. В начале участка имеется место для складирования заготовок подвозимых из заготовительного цеха электрокарой. В конце участка находится стол технического контроля.
При проектировании участка было задействовано оптимальное количество станков которое является достаточным для изготовления требуемого количества деталей.
14 Экономическое обоснование принятого варианта технологического процесса.
Определяем экономический эффект от замены токарно-гидрокопировального станка модели 1722 на токарно-винторезный с ЧПУ 16К20Т1.
14.1 Расчет экономического эффекта
Экономический эффект от реализации проектируемого техпроцесса определяется по формуле
Эт = Эз + Эо(3.14.1)
где Эз - экономия (дополнительные затраты) при изменении заготовки тыс.р;
Эо - экономический эффект (дополнительные затраты) при изменении технологии механической обработки тыс.р.
Эт = 32 745 + 900 =33 645 тыс.р.
Экономия затрат на получение заготовки составит
Эз = (Сб – Сн) × Ан (3.14.2)
где Сб Сн - себестоимость (цена) одной заготовки по вариантам тыс.р;
Ан - программа выпуска деталей по новому варианту шт.
Эз = (15444 – 12578) × 5000 = 14330 тыс.р.
Экономический эффект проектируемого технологического процесса механической обработки деталей определяется по формуле
Эо = (Зб – Зн) Ан (3.14.3)
где Зб и Зн - приведенные на единицу продукции затраты по вариантам тыс.р.
Эо = (046– 043) × 5000 = 150 тыс.р.
Приведенные затраты З тыс.р в данном случае равны
З = С +Ен×К (3.14.4)
где С - технологическая себестоимость единицы продукции тыс.р;
К - удельные капитальные вложения в расчете на одну деталь тыс.р;
Ен - нормативный коэффициент экономической эффективности
капитальных вложений (Ен = 015).
14.2 Расчет капитальных вложений
Удельные капитальные вложения определяются по формуле
где Коб и Кзд - капитальные вложения в оборудование и здания по изменяющимся операциям техпроцесса тыс.р;
d - множитель учитывающий другие группы основных фондов
(сооружения инструмент инвентарь) и т.п.. Можно принять d=11 12.;
Кз - коэффициент загрузки оборудования (не учитывается если программа выпуска обеспечивает создание однопредметного участка).
14.3 Капитальные вложения в оборудование
Расчет приведен в таблице 3.14.1.
Таблица 3.14.1 - Стоимость оборудования
Программа выпуска Ашт
Затраты на монтаж тыс.р(10% от цены)
Балансовая стоимость тыс.р.
Проектируемый вариант
Количество оборудования определяем по формуле:
где Np - расчетное число станков шт;
А - программа выпуска шт;
Фд - годовой действительный фонд времени работы оборудования час;
Кн - коэффициент выполнения норм (Кн=105 11).
Nр = 363×5000 (60 × 4029 ×105 ) = 007 шт.
14.4 Капитальные вложения в здания
Капитальные вложения в здания рассчитываются по формуле
где S - площадь занимаемая оборудованием м2;
Цз - стоимость 1 м2 площади тыс.руб. (Цз=150 200у.е.).
Кзд = 2736 × 335 =91566 тыс.р.
Расчет площади представлен в таблице 3.14.2.
Таблица 3.14.2 - Капитальные вложения в здание
Коэффициент дополнительной площади
Площадь на операцию м
Капитальные вложения в здание тыс.р
проектируемый вариант
Расчет общих капиталовложений представлен в таблице 3.14.3.
Таблица 3.14.3 - Удельные капитальные вложения
Всего на операцию Кобтыс.р.
Коэффициент загрузки Кз
Капвложения с учетом загрузки (Коб*Кз) тыс.р.
Удельные вложения тыс.р.
прочие (10-15% от (Кзд+Коб))
14.5 Расчет технологической себестоимости
Технологическая себестоимость по операциям определяется по формуле
С = (Сз+ Сэ) tшт 60(3.14.8)
где Сз - часовая заработная плата с отчислениями тыс.р;
Сэ - часовые затраты по эксплуатации рабочего места тыс.р.
С = (443+52)×72360= 116 тыс.р.
Часовая заработная плата определяется по формуле
Сз = Сч Кпр Кд Кк Кв(3.14.9)
где Сч - часовая тарифная ставка тыс.р;
Кпр - коэффициент премий (Кпр=14);
Кд - коэффициент доплат учитывающий сдельный приработок дополнительную зарплату отчисления на социальные нужды (Кд = 16 17);
Кк - корректирующий коэффициент учитывающий многостаночное обслуживание (при числе обслуживания станков: 1 2 3 4 5 6 7 соответственно - 1; 065; 045; 039; 035; 032; 03).
Кв - коэффициент учитывающий заработную плату вспомогательных рабочих обслуживающих оборудование (наладчиков ремонтников слесарей) (Кв=13 14).
Сз = 152×14×16×1×13 = 443 тыс.р.
При этом часовая тарифная ставка для станочников определяется по формуле
где S1 - тарифная ставка первого разряда тыс.р;
Кт - тарифный коэффициент соответствующего разряда;
Ксл - коэффициент учитывающий сложность работ (Кс=11).
Сч = 150×15711170 = 152 тыс.р.
В составе затрат по эксплуатации рабочего места следует рассчитать амортизацию оборудования по формуле
где Коб - балансовая стоимость оборудования на операции тыс.р;
На - норма амортизации %.
Ам = 22 000×58100 = 1276 тыс.р.
Затраты на содержание производственной площади определяются по формуле
Спл = Рп ×S(3.14.12)
где Рп - расходы по содержанию 1мплощади тыс.р (Рп»10у.е.);
S - площадь занимаемая оборудованием.
Спл = 085×1368 = 11625 тыс.р.
Затраты на ремонт и обслуживание рабочего места принимаем 5-7% от стоимости оборудования.
Силовая энергия рассчитывается по формуле
где Р - мощность оборудования кВт;
Кс - коэффициент спроса (Кс=07).
Цэ – тариф на энергию рубкВт (Цэ =240 руб)
Сэ = 10×4029×07×024=67687 тыс.р.
Затраты на возмещение износа металлорежущего инструмента рассчитываются по формуле
где Ии - часовые затраты на возмещение инструмента тыс.р;
N - количество оборудования.
Си = 0045×4029×2= 36261 тыс.р.
Прочие затраты принимаются 3-5% от суммы предыдущих расходов.
Результаты расчетов сводим в таблицу 3.14.4.
Таблица 3.14.4 – Расходы содержания рабочих мест
Расчет технологичной себестоимости приведен в таблице 3.14.5.
Таблица 3.14.5 – Технологическая себестоимость
Часовая зарплата тыс.р.
Часовые расходы по рабочим местам тыс.р.
Всего расходов тыс.р.
Затраты на деталь тыс.р.
Окончание таблицы 3.14.5
Рассчитанные показатели экономической эффективности сводим в таблицу 3.14.6.
Таблица 3.14.6 – Показатели проекта
Трудоемкость единицы изделия
Коэффициент использования металла
Удельные капиталовложения
Технологическая себестоимость детали
Приведенные затраты: - на деталь; - всего
Экономический эффект по техпроцессу
Экономический эффект на деталь
Экономический эффект с учетом изменения заготовки
15 Параметрическая оптимизация переходов сверления отверстий на вертикально-сверлильном станке.
15.1 Постановка задачи
Задача состоит в определении оптимальных режимов сверления на вертикально-сверлильном станке 2Н150 с помощью ЭВМ что позволяет значительно сократить затраты времени на выполнение расчетов а так же вести обработку с наибольшей экономичностью при заданных требованиях к точности и качеству обрабатываемых поверхностей. Входными данными для расчета являются:
- вид заготовки диаметр и длина
- характеристика заготовки (материал твердость предел прочности)
- диаметр и длина обработки
- технические данные станка (мощность привода предельные значения подач и скоростей)
- технические данные инструмента (материал период стойкости).
В результате автоматизированного решения задачи получаем следующий состав выходных данных: оптимальная частота вращения шпинделя; оптимальная подача; оптимальная скорость резания; период стойкости инструмента; Главная составляющая осевой силы; крутящий момент; мощность затрачиваемая на резание; основное время.
Расчет и оптимизация режимов резания выполняется с использованием математической модели процесса обработки состоящей из целевой функции и ограничений отражающих цели оптимизации и закономерности резания металлов.
Представим схему построения математической модели оптимизации режимов резания технологического перехода сверления выполняемого на вертикально-сверлильном станке 2Н150 при известном экономически выгодным периодом стойкости инструмента. В этом случае модель сверления на станке с ступенчатым рядом частот вращения шпинделя и подач описывается следующей системой соотношений:
где Q – производительность обработки по основному времени;
То – основное время обработки;
Т – период стойкости инструмента;
Те – экономически рациональный период стойкости инструмента;
Ро – осевая сила возникающая при сверлении;
Родоп – допустимое значение осевой силы;
N – эффективная мощность резания;
Nдоп – допустимая мощность привода главного движения станка.
В приведенной модели в качестве критерия оптимизации выбрана наибольшая производительность учтены ограничения по стойкости режущего инструмента осевой силе допустимой приводом главного движения станка мощности резания.
15.2 Функциональная модель процесса
Для определения численных значений переменных и выходных параметров модели процесса сверления можно воспользоваться уравнениями приведенными в справочнике.
Тогда математическая модель процесса сверления будет иметь вид:
где Cv Cp Cm q qh qmyv yn ym Mv Kp - коэффициенты и показатели степеней в формулах для вычисления скорости резания осевой силы крутящего момента.
15.3 Выбор метода решения задачи и схема алгоритма
В данном случае задача нахождения оптимальных режимов резания представляет собой задачу нелинейного математического программирования.
На рисунке 3.15.1 представим схему алгоритма определения оптимальных режимов резания на вертикально-сверлильном станке.
15.4 Анализ результатов оптимизации
Сравнивая данные полученные автоматическим путем и данные полученные неавтоматическим путем делаем вывод что режимы резания полученные в результате автоматического регулирования осуществляются с более высокими скоростями чем полученные в результате неавтоматического проектирования. В результате оптимизации произошло уменьшение основного времени а также времени на аналитический расчет режимов резания что влечет за собой увеличение производительности.
Результаты расчета и программа находятся в приложении.
Технологический эффект от результатов расчета оптимальных режимов резания составит:
где - основное технологическое время при неавтоматизированном проектировании мин;
- основное технологическое время при автоматизированном проектировании мин.
Подставляя все данные в формулу (3.15.12) получим:
Конструирование и расчет приспособлений и инструментов
1 Станочное приспособление
1.1 Назначение и устройство приспособления
Приспособление для сверления отверстия предназначено для базирования и закрепления заготовки а также ориентирование её в системе координат станка.
Проектируемое приспособление используют для сверления отверстия диаметром 6+03 на цилиндрической поверхности вала в кондукторной втулке на вертикально-сверлильном станке модели 2Н150.
По сравнению с базовым вариантом в конструкцию приспособления был внесены усовершенствования.
Пневматический зажим оснащен поворотом при возвратно-поступательном движении поршня пневмоцилиндра что обеспечивает удобную смену заготовки.
Кондуктор состоит из корпуса на который приварены платики на платики устанавливаются две призмы и крепятся винтами и штифтама. Зажимной механизм приспособления состоит из прихвата который является штоком пневмоцилиндра. При нагнетании воздуха в верхнюю пневмокамеру осуществляется прижим детали при сбросе - происходит отжим детали с одновременным поворотом прихвата для облегчения доступа к детали. Также предусмотрен плунжер для фиксации угла в 90°. На корпус приварена стойка с откидной кондукторной втулкой и планкой. Благодаря винту запорному можно откинуть кондукторную втулку для возможности зенкования детали.
Деталь устанавливается в призмы и зажимается прихватом. Производится сверление отверстия деталь отжимается и проворачивается на 90°. В только что просверленное отверстие вставляется плунжер и деталь зажимается. После сверления второго отверстия откидывается кондукторная втулка и производится последовательное зенкование отверстия 145° с четырех сторон. Деталь отжимается и снимается. Обработка следующей детали ведется аналогичным образом.
Базирование приспособления на стол станка осуществляется по плоскости плиты а его крепление к столу станка обеспечивается тремя болтами.
Управление работой приспособления осуществляется при помощи двухходового кранового распределителя.
1.2 Силовой расчет приспособления
В процессе обработки отверстий сверлением обрабатываемая заготовка находится под воздействием крутящего момента М и осевого усилия Рz. Сила подачи и сила зажима действуют в одном направлении прижимая заготовку. Под действием крутящего момента резания М деталь стремится повернуться вокруг оси. Этому противодействует момент трения Мтр создаваемый осевым усилием зажима Q. Расчётная схема приспособления представлена на рисунке 4.1.1
Рисунок 4.1.1 - Расчётная схема приспособления
где М – крутящий момент на сверле;
k – коэффициент запаса;
R – расстояние от центра сверла до центра заготовки мм;
Р0 – осевое усилие кгс;
f – коэффициент трения;
R1 – расстояние от середины опорной площадки до центра заготовки.
Коэффициент запаса рассчитывается по формуле из [9]:
k=k0*k1*k2*k3*k4*k5*k6 (4.1.3)
где k0=15 –гарантированный коэффициент запаса;
k1=12 – коэффициент учитывающий увеличение силы резания из-за случайных неровностей на заготовках;
k2=11 - коэффициент учитывающий увеличение силы резания от затупления сверла;
k3=12 - коэффициент учитывающий условия обработки при прерывистом резании;
k4 =13 - коэффициент учитывающий погрешность зажимного устройства;
k5=1 - коэффициент характеризующий степень удобства расположения рукояток в ручных зажимах;
k6=15 - коэффициент учитывающий только наличие моментов стремящихся повернуть заготовку на опорах;
Определим необходимый диаметр поршня Dрмм.
где D – диаметр поршня цилиндра
p – давление воздуха в цилиндре p = 04 МПа;
– коэффициент полезного действия пневмоцилиндра = 09;
Q – усилия закрепления на штоке пневмоцилиндра
Сравниваем значение диаметра поршня D с расчетным Dр делаем вывод что пневмопривод с диаметром поршня 50 мм позволяет вести обработку на заданных режимах резания.
1.3 Расчет приспособления на прочность
Произведем проверку на прочность болтовых соединений неподвижного корпуса с плитой пользуясь рекомендациями [12]. По формуле 1.32 [12] рассчитаем необходимый внутренний диаметр резьбы d1 мм
где Fр – суммарная нагрузка на болт Н;
допускаемое напряжение = 160 МПа (табл.1.1и 1.2);
Вычислим расчетную суммарную нагрузку на болт по формуле
где Fзат сила затяжки болта Н;
F внешняя нагрузка Н;
где F1 главная составляющая силы резания F2 = 200 Н;
F1 горизонтальная составляющая силы резания F1 = 100 Н;
F3 величина усилия зажима F3 =2474 Н;
n – число болтов крепящих неподвижный корпус n = 4;
где Кзат коэффициент затяжки Кзат = 4 (стр.41 [12]);
Тогда по формуле (4.1.5)
По полученному значению внутреннего диаметра резьбы выбираем болт М10.
1.4 Расчет приспособления на точность
Расчет приспособления на точность будем производить в соответствии с методикой изложенной в [12].
Определяем допуск на изготовление приспособления Тпр мм для обеспечения точности размера 6+03 (диаметр отверстия) по формуле:
где Т – допуск на обработку мм;
Kт – коэффициент учитывающий отклонение рассеяния значений составляющих величин от закона нормального распределения kт = 11;
Kт1 коэффициент учитывающий уменьшение предельного значения погрешности базирования при работе на настроенных станках kт1 = 08;
Kт2 коэффициент учитывающий долю погрешности обработки в суммарной погрешности вызванной факторами не зависящими от приспособления kт2 = 07;
б погрешность базирования заготовки мм;
з погрешность закрепления мм;
у погрешность установки приспособления на станке мм;
и погрешность связанная с износом элементов приспособления мм;
п погрешность от перекоса режущего инструмента мм;
w экономическая точность обработки отверстия w = 015 мм (табл. 10 [12]);
Погрешность базирования заготовки в соответствии с рекомендациями таблицы 3.1 [12] принимаем равной
Погрешность закрепления исключаем из расчетов т.к. пневмопривод обеспечивает постоянное усилие зажима.
Вследствие надежного контакта установочной плоскости приспособления с плоскостью стола станка принимаем погрешность установления приспособления на станке равной
Погрешность связанную с износом элементов приспособления принимаем равной и = 0 так как приспособление предусматривает регулировку которая производится сменными призмами.
Так как в приспособлении присутствуют направляющие элементы то погрешность от перекоса инструмента будет равна
Таким образом по формуле (12.4.1) имеем
Делаем вывод что условие точности для данного приспособления выполняется.
2 Контрольное приспособление
2.1 Назначение и устройство приспособления
Приспособление предназначено для контроля радиального и торцового биений относительно оси детали. Приспособление состоит из основания 1 на котором закреплены две стойки 2 и 3. В стойке 2 закреплен неподвижный центр 4 а в стойке 3-регулируемый который фиксируется фиксатором 20 за счет чего происходит поджим-отжим детали. К основанию 1 крепятся индикаторы которые могут перемежаться в продольном направлении по пазам.
2.2 Порядок выполнения измерений и обработки результатов.
Для измерения радиального биения деталь устанавливают в центра 45. Щуп устанавливают таким образом чтобы он касался измеряемой поверхности сферы а стрелка индикатора сделала 1-2 оборота. После этого стрелка индикатора устанавливается на ноль поворота шкалы. Отклонение стрелки индикатора и покажет биение поверхности относительно оси детали. Затем тоже действие повторяют еще шесть раз и по совокупности всех показаний судят о том годна деталь или нет.
2.3 Расчет приспособления на точность.
В соответствии с ГОСТ 8.051-83 погрешность измерения торцового биения не должна превышать 30% допуска измеряемой величины. Допуск торцового биения Т=005 мм. Тогда допуск погрешности измерения
Погрешность измерения в разработанном приспособлении состоит из трех слагаемых: погрешности базирования и погрешности отсчетного устройства 1 то есть
Погрешность базирования =0 так как установочная база детали и измерительная база совпадают.
Погрешность отсчетного устройства 2 в качестве которого принят индикатор типа ИЧ-10 погрешность измерения которого составляет 001 мм при цене деления шкалы c=001 мм.
Таким образом сумма погрешности измерения в приспособлении
Это означает что сумма погрешности измерения в приспособлении не превышает допускаемой погрешности измерения. Можно использовать для контроля.
3 Режущий инструмент
3.1 Описание конструкции и расчет червячной фрезы
Наиболее распространенными инструментами для обработки изделий с прямолинейным профилем являются червячные шлицевые фрезы. Червячными они называются потому что в основе их лежит исходный червяк. Червячные фрезы изготавливаются из быстрорежущей стали в них профрезеровывают стружечные канавки и затыловывают зубья. После чего термически обрабатывают и шлифуют необходимые поверхности.
В процессе обработки начальная прямая рейки фрезы катится бес скольжения по начальной окружности изделия. Метод обработки червячными фрезами является высокопроизводительным и сравнительно точным так как до полного изготовления детали на донной операции процесс является непрерывным.
Обработка деталей производится на шлицефрезерных станках. Червячная фреза устанавливается в общем случае так что ее ось скрещивается с осью обрабатываемого валика а направление витков совпадает со шлицами валика. Инструменту и изделию сообщается кинематически согласованное вращательное движение относительно своих осей. За один оборот фрезы валик повернется на один окружной шаг.
3.2 Исходные данные:
Червячная шлицевая фреза. Обрабатываемый материал – Сталь18ХГТ; длина шлицевой втулки – 75 мм; Dшл=70n6 мм; dшл=60 мм; bшл=10f9 мм; z=10; с=04.
3.3 Проектный расчет
2.1 Находим предельные отклонения размеров:
2.2 Находим расчетный наружный диаметр шлицевого валика:
Dр=Dmax-2·C=70039-2·04=69.239 мм(4.3.1)
2.4 Расчетная ширина шлица:
bp=bmin+025·E=10941+025·0043=1095 мм(4.3.2)
Е – величина допуска на ширину шлица
2.5 Диаметр начальной окружности валика определяется по формуле:
2.6 Угол шлица находим по формуле:
2.7 Высота профиля валика фрезы:
2.8 Диаметр окружности первой точки:
2.9 Диаметр окружности второй точки:
2.10 Углы α1 и α2 между осью OY и касательной к кривой в точках 1 и 2:
2.11 Абсциссы точек 1 и 2 определяются по формуле:
где α1 α2 γн – углы выраженные в радианах;
Dн – диаметр начальной окружности валика.
2.12 Ординаты точек 1 и 2:
2.13 Абсциссы центра заменяющей окружности вычисляется по формуле:
2.14 Ордината центра заменяющей окружности:
2.15 Радиус заменяющей окружности:
Определение размеров профиля зуба.
2.16 Шаг витков по нормали:
2.17 Толщина зуба фрезы по начальной прямой:
2.18 Угол α для высшей точки профиля фрезы определяется по формуле:
где dp – расчетный внутренний диаметр валика.
2.19 Максимальная высота профиля зуба фрезы:
2.20 Размеры уступа подсчитываются по формуле:
2.21 Толщина зуба фрезы на любой высоте hx от начальной прямой определяется:
2.22 Размеры канавки для облегчения шлифования вычисляются по формулам:
глубина принимаем h4=2 мм;
2.23 Высота шлифованной части профиля зуба:
2.24 Общая высота профиля зуба фрезы:
Определение элементов режущей части.
По рекомендации [2] принимаем:
2.25 Задний угол на боковых сторонах профиля:
2.26 Размеры канавки для выхода стружки:
так как Daи и zи не известны то для определения Hк пользуемся стандартом табл. 9.12 [2]:
- радиус закругления;
2.27 Длина фрезы определяется:
2.28 Диаметр посадочного отверстия:
Рассчитанное значение округляется до ближайшего большего значения из нормального ряда
2.29 Диаметр окружности впадин между зубьями:
2.30 Наружный диаметр фрезы:
2.31 Средний расчетный диаметр фрезы:
2.32 Угол наклона винтовой линии:
2.33 Шаг винтовой линии:
2.34 Осевой шаг витков:
Безопасность и экологичность проекта
1 Идентификация и анализ вредных и опасных факторов в проектируемом объекте
Организация охраны труда на предприятии является одной из важнейших задач и обязанностей администрации. Полностью безопасных и безвредных производств не существует. Задача охраны труда – свести к минимуму вероятность поражения или заболевания работающих с одновременным обеспечением комфорта при максимальной производительности труда. К таким факторам относятся:
) запылённость воздуха оказывающая вредное воздействие на дыхательную систему человека.
) Электрический ток. Воздействие электрического тока может возникнуть при аварийной ситуации в электрической цепи. Ток оказывает на человека термическое воздействие (ожоги) вызывает удушье а так же при длительном времени воздействия значительной силе может вызвать летальный исход.
) шум возникающий при работе оборудования цеха. Вызывает повышенную утомляемость работника снижает работоспособность снижает внимание что повышает вероятность возникновения травматизма.
) вибрация возникает вследствие работы оборудования. Вибрация передающаяся непосредственно на руки работника оказывает вредное воздействие на суставы. Общая вибрация может влиять на организм человека в целом так как её частота может не совпадать с биологической частотой внутренних органов.
) освещение должно быть достаточным для выполняемой работы. Недостаточная освещённость оказывает вредное воздействие на зрение работника приводит к повышенной утомляемости глаз а следовательно и к повышенному травматизму.
) движущиеся части производственного оборудования передвигающиеся изделия и заготовки транспортные средства передвигающиеся по цеху. Это может привести к повреждению работников механического характера и даже к летальному исходу.
) стружка обрабатываемых материалов осколки инструментов ломающихся при работе отказы оборудования. Всё это так же приводит к всевозможным травмам механического характера как во время работы так и после работы при уборке рабочего места.
) высокая температура печей на операции термической обработки высокая температура поверхностей обрабатываемой детали и инструмента. При эксплуатации этот фактор может привести к ожогам различной степени тяжести а так же к возникновению пожаров.
2 Технические технологические организационные решения по устранению опасных и вредных факторов разработка защитных средств
Для защиты человека от механического травмирования применяют два основных способа: обеспечение недоступности человека в опасные зоны и применение устройств защищающих человека от опасного фактора. Опасные зоны механизмов по возможности сделаны недоступными для человека то есть огорожены или закрыты кожухами. В конструкции оборудования в обязательном порядке предусмотрены тормозные и отключающие устройства. При входах в опасные зоны и на самих узлах представляющих потенциальную опасность для человека применяются предупреждающие и запрещающие плакаты и таблички.
Нормативным документом регламентирующим уровни шума для различных категорий рабочих мест является ГОСТ 12.1.003-83 «ССБТ. Шум. Общие требования безопасности». и СН РБ №9-86-98. Уровень шума при частоте F=1000Гц не превышает Lраб=80дБ.
Для снижения уровня шума используются следующие методы: снижение шума в источнике его образования; метод снижения шума на пути его распространения. Используются средства в соответствии с ГОСТ 12.4.051-87 «ССБТ. Средства индивидуальной защиты органов слуха. Общие технические условия». Уменьшение шума в источнике его образования достигается за счет поддержания оборудования в исправном состоянии заменой устаревшего оборудования на новое. Снижение шума на пути его распространения обеспечивается изоляцией источников шума а именно применением кожухов и экранов.
Основные мероприятия направленные на снижение опасности воздействия инфракрасного излучения состоят в следующем: снижение интенсивности источника защитное экранирование источника или рабочего места использование СИЗ лечебно-профилактические мероприятия.
Снижение интенсивности инфракрасного излучения источника достигается выбором технологического оборудования обеспечивающего минимальные излучения; заменой устаревших технологических схем современными (например замена пламенных печей на электрические) национальной компоновкой оборудования с помощью которой обеспечивается минимум нагретых поверхностей.
Наиболее распространенные средства защиты от инфракрасного излучения классифицируемые ГОСТ 12.4.123—83 «ССБТ. Средства коллективной защиты от инфракрасных излучений. Общие технические требования»: оградительные теплоизолирующие средства вентиляции а также средства автоматического контроля и сигнализации. В термических цехах применяют средства защиты работающих в соответствии с ГОСТ 12.4.011 - 89: специальную обувь специальную одежду очки.
Защита работающих от воздействия электрического тока обеспечивается в соответствии с ГОСТ 12.1 030-81 «ССБТ. Электробезопасность. Защитное заземление. зануление». Согласно ПУЭ механическая обработка деталей технологической оснастки ведется в помещении без повышенной опасности. На предприятии для предотвращения несчастных случаев при работе с электрооборудованием применяется: защитное заземление изоляция токоведущих частей оградительные устройства знаки безопасности. Для эффективной работы защитное заземление устроено в соответствии с ГОСТ 12.1.030-81 ССБТ сопротивление заземления не превышает 4 Ом.
Основными видами средств коллективной защиты от воздействия ЭМП токов промышленной частоты являются стационарные заземлённые экранирующие устройства. Экранируют источник излучения. Экранирование источников излучения рекомендуется проводить при помощи замкнутых камер из листового металла.
Средства защиты по отношению к источнику возбуждения вибрации подразделяются на средства снижающие параметры вибрации воздействием на источник возбуждения и средства снижающие параметры вибрации в направлении ее распространения. Согласно требованиям СН РБ №9-89-98 уровень вибрации на рабочем месте не превышает 102 дБ.
Средства динамического виброгашения по принципу действия подразделяются на динамические (пружинные эксцентриковые гидравлические действующие в противофазе к колебательной системе) и ударные. Динамическое виброгашение осуществляется также при установке агрегата на массивном фундаменте.
В качестве индивидуального задания к дипломному проекту было предложено рассчитать защитное заземление металлорежущего станка. Защитному заземлению подлежат металлические нетоковедущие части электрооборудования которые вследствие неисправности изоляции могут оказаться под напряжением и которым возможно прикосновение людей. Принцип действия защитного заземления – устранение опасности поражения людей электрическим током при появлении напряжения а конструктивных частях электрооборудования т. е. при замыкании на корпус.
Принцип действия защитного заземления – снижение до безопасных значений напряжения прикосновения и шага обусловленные замыканием на корпус Это достигается уменьшением потенциала заземленного оборудования а также выравниванием потенциалов за счет подъема потенциала основания на котором стоит человек до потенциала близкого по значению к потенциалу заземленного оборудования.
Область применения защитного заземления – трехфазные трехпроводные сети напряжением до 1000 В с изолированной нейтралью и выше 1000 В с любым режимом нейтрали (рисунок 1).
Рисунок 1 – Принципиальная схема защитного заземления в сети с изолированной нейтралью до 1000 В и выше:
– заземленное оборудование;
– заземлитель защитного заземления.
Мероприятия по защите обеспечивают недоступность токоведущих частей для случайного прикосновения: пониженное напряжение заземление зануление автоматическое отключение индивидуальная защита.
Внутри заводских зданий токоведущие провода подвешивают на высоте не менее 3.5 м.
Ограждения токоведущих частей предусматривается конструкцией оборудования наличие этих ограждений в условиях эксплуатации обязательно.
Пониженное напряжение применяют при использовании ручных машин на участке сборки когда работающий имеет длительный контакт с корпусом этого оборудования.
Для предотвращения поражения электрическим током на участке производим заземление нетоковедущих частей оборудования которые могут оказаться под напряжением (ГОСТ 12.1.030-81 ССБТ).
В качестве заземлителей можно использовать расположенные под землей трубопроводы; металлические конструкции зданий имеющие соединения с землей; обсадные трубы; свинцовые оболочки кабелей проложенных под землей.
Для периодический смены инструментов регулировки и подналадки полуавтоматов и станков с ЧПУ их смазывания и чистки а также мелкого ремонта предусматривается специально выделенное время. Все перечисленные работы производятся при обесточенном оборудовании.
Перед началом работы рабочий должен убедиться в наличии заземления особое внимание уделяется станкам использующим магнитную плиту.
Цель расчета защитного заземления заключается в определении основных параметров заземления (число размеры и размещение одиночных заземлителей и заземляющих проводников) при которых напряжения прикосновения и шага в период замыкания фазы на заземленный корпус не превышает допустимых значений.
При расчете защитного заземления приходится решать целый ряд задач в том числе: определение типа и сложности грунта сезонных изменений сопротивлению растекания грунта (промерзание высыхание повышенная влажность грунта) типа электрозаземлителя (форма размеры) из которого предполагается соорудить проектируемой групповой заземлитель с учетом устройства (размещения) заземлителей (расстояние между электродами конфигурации и т. п.) возможности использования естественных заземлителей (заглубленных в грунт металлоконструкций трубопроводов кабелей) и др.
РАСЧЁТ ЗАЩИТНОГО ЗАЗЕМЛЕНИЯ
Эл. Приемник см. задание
Род тока – переменный
Напряжение в сети В – 380
Место использования – в помещении
Характеристика рабочей зоны – нормальные условия
Класс помещения – с повышенной опасностью
Длина электрода м – 3
Электроды трубчатого сечения
Диаметр электрода м – 005
Схема заземления – 1
Глубина заложения электродов м - 04
Допустимое сопротивление заземлителя Ом – 10
Климатический коэффициент – 195
Расстояние между электродами м – 2
Глубина заложения полосы м – 04
Ширина полосы м – 0016
Сопротивление одиночного электрода Ом – 291
Сопротивление заземляющего устройства Ом – 639
Количество электродов - 6
Заземление удовлетворяет условию R≤Rдоп. т.е. 639≤10 Ом
3 Разработка мер безопасности при эксплуатации объекта проектирования
Общие требования безопасности:
К самостоятельной работе на металлорежущих и заточных станках с сухими абразивными кругами допускаются лица прошедшие медицинское освидетельствование а также обучение и инструктаж по правилам эксплуатации и техники безопасности сдавшие экзамены и получившие соответствующие удостоверения.
При переводе на работу с использованием нового оборудования рабочий обязан ознакомиться с конструкцией методами безопасной работы на нем и пройти внеплановый инструктаж по охране труда.
Рабочие должны работать в спецодежде спецобуви а также использовать при необходимости другие средства индивидуальной защиты (защитные очки и т.п.). Одежда должна быть застегнута на все пуговицы. Кроме того необходимо работать в головном уборе полностью закрывающем волосы. Работать на станках в обуви легкого типа (сандалиях босоножках тапочках и т.д.) запрещается.
Рабочие станочники обязаны содержать в исправности и чистоте оборудование инструмент и рабочее место а работу выполнять стоя на деревянных решетках.
Складировать материалы и готовую продукцию на стеллажах и других приспособлениях в специально отведенных местах. Запрещается размещать материалы и изделия в проходах и проездах на полу вблизи рабочего места.
Отходы следует хранить в специальных ящиках и каждую смену убирать.
Обтирочные и смазочные материалы должны храниться в плотно закрывающихся специально отведенных ящиках.
Механические передачи металлорежущих станков и другие вращающиеся и движущиеся части станков должны иметь ограждения. Обрабатываемые изделия выступающие за габариты станков должны быть ограждены устойчивыми предохранительными приспособлениями.
На рабочем месте следует хранить только те инструменты и приспособления заготовки и готовые изделия которые необходимы для выполнения работы в эту смену.
1 знать устройство станка уметь определять неисправности;
2 заготовки и детали весом более 16 кг поднимать с применением подъемных механизмов и использованием специальных захватов;
3 соблюдать требования производственной санитарии и гигиены труда;
4 соблюдать правила внутреннего трудового распорядка организации.
Требования безопасности перед началом работы:
Проверить станки на холостом ходу при этом убедиться в исправности:
1 органов управления - электрических кнопочных устройств тормозов фиксации рычагов включения и переключения исключающих возможность самопроизвольного переключения с холостого хода на рабочий;
2 убедиться в том что системы смазки и охлаждения работают бесперебойно.
При установке режущего и сверлильного инструмента проверить:
1 правильность заточки инструмента для обработки данного материала;
2 прочность крепления оправки и фрезы;
3 крепление сверла в патроне и правильность центрирования его с осью шпинделя станка. Применять сверла с правильной заточкой.
Перед началом работы станочник обязан:
1 проверить исправность станка инструментов и вспомогательных приспособлений;
2 проверить наличие и исправность ограждений заземляющих и зануляющих устройств.
Требования безопасности во время работы:
Во время работы станка следить за надежностью крепления оградительных и предохранительных устройств и не снимать их.
Если на металлических частях станка обнаружено напряжение (ощущение тока) электродвигатель работает на две фазы (гудит) заземляющий провод оборван или обнаружены другие неисправности электрооборудования немедленно остановить станок и доложить мастеру или начальнику цеха о неисправностях; без его указаний к работе не приступать.
Не брать и не подавать через работающие станки какие-либо инструменты предметы.
Обязательно остановить станок и выключить электродвигатель:
1 при уходе от станка даже на короткое время;
2 при временном прекращении работы;
3 при уборке смазке чистке станков;
4 при перерыве в подаче электроэнергии;
5 при обнаружении какой-либо неисправности в оборудовании;
6 при подтягивании болтов гаек и других соединительных деталей станка.
Меры безопасности при работе на сверлильных станках:
Во избежание захвата вращающимися частями сверлильного станка запрещается:
надевать ремни передач при включенном электродвигателе;
пользоваться патронами инструментами и приспособлениями установленными в шпинделе станка и имеющими выступающие части;
поправлять патрон и сверло а также снимать с них стружку и прикасаться к ним руками во время вращения.
Сверление тонких планок полос производить с применением соответствующих упоров подкладок из дерева или в машинных тисках.
При сверлении мелких деталей необходимо удерживать их ручными тисками.
Во избежание поломки сверла и ранения рабочего осколками необходимо:
сверло к обрабатываемому изделию подводить только после включения станка так чтобы оно слегка коснулось поверхности обрабатываемого изделия; перед сверлением центр отверстия наметить керном;
при сверлении глубоких отверстий для удаления стружки не останавливая станка периодически выводить сверло из сверлильного отверстия;
при сверлении сквозных отверстий когда сверло подходит к выходу необходимо выключить механическую подачу и досверливать отверстие с замедленной ручной подачей.
Удалять стружку из просверленных отверстий необходимо крючком щеткой или магнитом после остановки станка и отвода инструмента.
При обработке деталей на сверлильном станке не допускается:
-придерживать обрабатываемую деталь руками;
-закреплять сверло или деталь во время работы станка;
-тормозить станок нажимом руки на шпиндель или патрон;
-работать в рукавицах или перчатках;
-проверять пальцем выход сверла снизу детали;
-сдувать стружку со стола станка;
-применять сверла и патроны с забитым или изношенным хвостовиком.
Требования безопасности в аварийных ситуациях:
В случае обнаружения неисправности угрожающей жизни работников необходимо немедленно прекратить работу и доложить об этом руководителю мастеру или механику.
В случае пожаров стихийных бедствий объявления чрезвычайных ситуаций необходимо немедленно прекратить работу обесточить станок и выполнить распоряжения руководства.
При несчастном случае необходимо остановить оборудование оказать помощь пострадавшему вызвать скорую помощь доложить руководителю.
Требования безопасности по окончании работы:
Выключить станок и электродвигатель.
Привести в порядок рабочее место: убрать стружку со станка инструменты и приспособления сложить в отведенное место аккуратно сложить готовые детали заготовки.
Использованные обтирочные материалы необходимо убрать в специальные металлические ящики с крышками.
Организационно-экономическая часть
1Организация службы технического контроля
Руководство заводской службой контроля качества продукции осуществляет заместитель директора по качеству - начальник отдела технического контроля который имеет в своём подчинении не только возглавляемый им ОТК но и ряд оперативных подразделений осуществляющих работу по непосредственному контролю качества продукции.
Основными оперативными подразделениями ОТК завода непосредственно контролирующих качество продукции в цехах является бюро цехового контроля (БЦК). На БЦК возлагаются организация и осуществление технического контроля на всех основных и вспомогательных участках соответствующего цеха начиная от контроля полуфабрикатов заготовок деталей и узлов до контроля отправки продукции другими цехами потребителям включая оформление приёмкой и сопроводительной документации и актов о браке. Сменный контрольный мастер осуществляет организацию технического контроля в своей смене. Он руководит работой контролёров принимающих продукцию на участках.
Контрольный мастер помимо руководства работой подчинённых ему контролёров проводит также непосредственную проверку наиболее ответственных деталей и узлов а в ряде случаев и операций.
Контроль состояния и качества измерительных приборов на заводе осуществляет центральная измерительная лаборатория (ЦИЛ) и её отделения в соответствующих цехах - контрольно-проверочные пункты (КПП). На ЦИЛ возлагается задача по работе единой проверочной схемы проверка и аттестация измерительных приборов на заводе руководство работой КПП разработка методов контроля средств измерения. КПП осуществляет непосредственно контроль средств измерения обращающихся в данном цехе надзор за правильной их эксплуатацией хранением и выдачей. КПП осуществляют принудительное изъятие из эксплуатации изношенных и негодных средств измерения.
Все обращающиеся на заводе измерительные приборы и средства подвергаются государственной обязательной и периодической проверкам. Результаты проверок измерительных средств и приборов отмечаются в их паспортах а также в выписываемых на каждую проверку аттестациях.
Помимо оперативных подразделений ОТК имеет в своём составе функциональный орган - техническое бюро которое должно анализировать причины брака на заводе и у потребителя и разрабатывать технические и организационные мероприятия по внедрению наиболее эффективных способов и методов контроля определить оптимальный уровень качества продукции и методы статистического регулирования технологических процессов. Обычно техническое бюро состоит из нескольких групп:
Учёта и анализа брака
Внешней инспекции и рекламаций
Внедрения статистических методов управления качеством.
2 Расчёт экономических показателей и характеристика участка
2.1 Общая характеристика участка
К исходным данным относятся данные представленные в таблицах 6.2.1 и 6.2.2.
Таблица 6.2.1 – Трудоемкость ведущей детали
Структура трудоемкости%
Окончание таблицы 6.2.1
Структура трудоемкости α характеризуется отношениями норм времени по отдельным операциям tшт к общей трудоемкости изготовления детали Тед :
Таблица 6.2.2 – Годовая трудоемкость и расход материала по участку
Трудоемкость единицы Тi мин
Общая трудоемкость Тгод ч
Общая годовая потребность М т
Таблица 6.2.2 заполняется в результате следующих расчётов где годовая трудоёмкость и расход материала рассчитываются по формулам:
где n – число наименований деталей;
НР – норма расхода материала кг.
Общая трудоемкость по участку должна составлять не менее чем следующее произведение:
где m – число операций по ведущей детали участка;
Фд – годовой действительный фонд времени единицы оборудования ч;
tmax - трудоемкость наиболее трудоемкой операции ведущей детали мин.
2.2 Определение годовой трудоемкости по операциям участка
Трудоемкость по i-ой операции Тгодiч Рассчитывается по формуле:
Аi – программа выпуска шт.
Расчет представлен в таблице 6.2.3.
Таблица 6.2.3 – Трудоемкость по операциям участка
Общая годовая трудоемкость ч
Трудоемкость по операциям ч
2.3 Расчет численности персонала на участке
Фр= (8×Дн+7×Дс)×Кнев (6.2.7)
Расчет численности основных рабочих представлен в таблице 6.2.4.
Таблица 6.2.4 – Численность основных рабочих
Расчёт сводим в таблицу 6.2.5.
Таблица 6.2.5 – Численность вспомогательных рабочих
Количество специалистов и исполнителей определим исходя из того что
их число может быть принято 7-10% от общего числа рабочих.
2.4 Расчет фонда заработной платы
2.4.1 Часовые тарифные ставки по разрядам
Часовые тарифные ставки по разрядам Сч р определяются по формуле:
где S1 – месячная тарифная ставка 1-го разряда тыс.р;
Кт – тарифный коэффициент соответствующего разряда;
Кс – коэффициент учитывающий сложность работ;
Фм – месячный фонд рабочего времени ч (Фм=167-170);
Кк – корректирующий коэффициент.
Расчет тарифных ставок для многостаночного обслуживания представлен в таблице 6.2.6 (тарифные ставки по разрядам приняты по данным предприятия).
Таблица 6.2.6 – Тарифные ставки по операциям и разрядам
Корректирующий коэффициент Кк
Часовая тарифная ставка Сч руб.
Для основных рабочих
Окончание таблицы 6.2.6
Для вспомогательных рабочих
2.4.2 Фонд заработной платы основных рабочих
Расчет фонда заработной платы ФЗПо выполняется по формуле:
где Кпр – коэффициент учета премий (Кпр=14);
Кд – коэффициент дополнительной заработной платы (Кд=108-110).
Результаты расчета сводятся в таблицу 6.2.7.
Таблица 6.2.7 – Фонда заработной платы основных рабочих
Часовая ставка Сч р.
Годовая трудоем-кость Тгод ч
Фонд сдельной зарплаты Сч*Тгод тыс.руб.
Фонд премии Фпр тыс. руб.
Фонд основной зарплаты Фосн тыс.руб.
Основной и дополнитель-ной зарплаты тыс.руб.
2.4.3 Фонд заработной платы вспомогательных рабочих
Расчет фонда заработной платы ФЗПв выполняется по формуле:
где n – число профессий вспомогательных рабочих;
Чв – численность вспомогательных рабочих.
Результаты расчета сводятся в таблицу 6.2.8.
Таблица 6.2.8 – Фонда заработной платы вспомогательных рабочих
Тарифный фонд зарплаты Сч*Фр*Чв тыс.руб.
Фонд основной зарплаты Фосн тыс.руб
Фонд дополни-тельной зарплаты тыс.руб.
зарплаты вспомога-тельных рабочих ФЗПв тыс. руб.
Обслуживающие оборудование
Окончание таблицы 6.2.8
- токарные сверлильные
Не обслуживающие оборудование
Кладовщик-раздатчик инструмента и приспособлений на рабочие места
2.4.4 Фонд заработной платы служащих
Расчет фонда заработной платы ФЗПс выполняется по формуле:
где Д – доплата за квалификацию и качество работы;
Чс – численность служащих.
Результаты расчета сводятся в таблицу 6.2.9.
Таблица 6.2.9 – Фонд заработной платы служащих
Тарифный коэффициент Кт
Тарифный фонд ЗП (S1*KT+Д)*12*Чс тыс. руб.
Фонд премии Кпр тыс.руб
Фонд ЗП служащих тыс.руб
2.4.5 Среднемесячная зарплата персонала
Среднемесячная зарплата каждой категории работающих определяется делением фонда зарплаты на численность работающих и на 12 месяцев.
Результаты расчета сводятся в таблицу 6.2.10.
Таблица 6.2.10 – Среднемесячная зарплата
Среднемесячная заработная
плата ФЗП(12*Ч) тыс. руб.
2.4.6 Расчет отчислений на социальные нужды
Для упрощения расчетов объединим все отчисления на социальные нужды (чрезвычайный налог отчисления в фонд занятости отчисления в фонд социальной защиты) в единый платеж по ставке 35%
Результаты расчета сводятся в таблицу 11.
Таблица 6.2.11 – Расчет отчислений на социальные нужды
Категория работающих
Годовой фонд заработной платы включаемый в себестоимость тыс. руб.
Норма отчислений на социальные нужды%
Сумма отчислений в фонд социальной защиты тыс. руб.
Окончание таблицы 6.2.11
2.5 Расчет основных производственных фондов участка
2.5.1. Расчет стоимости зданий
Расчет стоимости участка определим по формуле:
где Цм2 - стоимость 1м2 здания тыс. руб. (Цм2 = 3655 тыс.руб.);
S – площадь участка м2 (S=247015м2)
Таблица 6.2.12 – Расчет площади участка
Коэффициент дополнительной
2.5.2 Расчет стоимости оборудования
Расчёту предшествует определение потребного количества оборудования по формуле:
где - годовая трудоёмкость
- действительный годовой фонд времени работы единицы оборудования ч;
- коэффициент выполнения норм.
Из [9] принимаем: = 4000 ч; = 11.
Подставим все эти данные в формулу (6.2.16) и заполним таблицу 6.2.12
Таблица 6.2.13 – Расчёт потребности в оборудовании и его загрузки
Годовая трудоёмкость Тгод ч
Действительный годовой фонд Фд ч
Коэффициент выполнения норм
Коэффициент загрузки оборудования
Токарныо-винторезный станок с ЧПУ 16К20Т1
Результаты расчета стоимости технологического оборудования сводим в таблицу 6.2.13.
Таблица 6.2.14 – Стоимость технологического оборудования
Коли-чество станков шт
Мощность двигателя кВт
Затраты на монтаж и транспорти-ровку
Балансо-вая стои-мость тыс. руб.
Технологическое оборудование
Таблица 6.2.15 – Стоимость подъемно-транспортного оборудования
Количество единиц шт
Оптовая цена тыс. руб.
Затраты на монтаж и транспортировку
Балансовая стоимость тыс. руб.
Конвейер для уборки стружки
Таблица 6.2.16 Стоимость основных фондов
Группа основных фондов
Амортизационные отчисления ты сруб.
Силовое оборудование
Производственное оборудование
Транспортные средства
Окончание таблицы 6.2.16
Инструменты и приспособления
2.6 Расчет материальных затрат
В состав материальных затрат включается стоимость основных и вспомогательных материалов комплектующих изделий и полуфабрикатов энергии налогов и отчислений включаемых в себестоимость.
2.6.1 Расчет стоимости основных материалов
Расчет стоимости основных материалов представлен в таблице 15
Таблица 6.2.17- Стоимость основных материалов
Наименование металла
Годовая потребность т
Цена за тонну тыс. руб.
Стоимость тыс. руб.
Таблица 6.2.18 – Стоимость возвратных отходов
Стоимость отходов тыс. руб.
Стоимость основных материалов составляет:
См=272506-1421128685 = 2582931 тыс. руб.
2.6.2 Расчет затрат на энергию
Таблица 6.2.19 - Исходные данные для расчета потребности в энергии
Мощность электродвигателей
Фонд времени работы оборудования
Коэффициент загрузки оборудования по времени
Коэффициент спроса мощности
Количество часов освещения
Удельный расход электроэнергии
Коэффициент использования осветительной нагрузки
Средний расход воздуха на приспособление в час
Количество станков с пневматическим приспособлением
Часовой расход воды на 1 станок для эмульсии
Количество станков работающих на эмульсии
Численность персонала
Дневной расход воды на бытовые нужды на 1 человека
Дневной расход воды на пользование душем.
Доля работников пользующихся душем
Число рабочих дней в году
Удельный расход пара для приготовления эмульсии на 1 м3 охлаждающей жидкости
Удельный расход тепла на 1 м3 объема здания
Удельное количество теплоты
Продолжительность отопления
Расчеты затрат на энергоносители сведем в таблицу 20
Таблица 6.2.20- Потребность в энергии
Окончание таблицы 6.2.20
Силовая электроэнергия
Осветительная электроэнергия
Вода на производственные нужды:
- приготовление эмульсии
Вода для бытовых нужд
Рвб=(25×Чп+03×Чп×50) ×Др1000
Пар на производственные нужды:
Рпо=(рт×Топ×S ×n)(i×1000)
Расход затрат на энергию представлен в таблице 21
Таблица 6.2.21 – Затраты на энергию
Цена за ед. тыс. руб.
Стоимость энергии тыс.уб.
Электроэнергия силовая кВт*ч
Электроэнергия осветительная кВт*ч
Вода для производства м3
Вода для бытовых нужд м3
Пар для производства т
2.6.3 Расчет налогов и платежей
В их составе рассчитывается земельный налог Нз и платежи по страхованию имущества Сстр.
Расчет осуществляется по формуле:
где S –площадь земельного участка занимаемого производственным подразделением м2;
hз – ставка земельного налога тыс.руб.га;
К33 – коэффициент застройки земли (К33=22).
Все необходимые данные были рассчитаны выше подставляя их в формулу (10) получим:
Платежи по страхованию имущества рассчитываются по формуле:
где Фоб – стоимость оборотных средств тыс. руб.;
Фосн –стоимость основных фондов тыс. руб.;
Ао – общая сумма амортизационных отчислений тыс. руб.
hстр – норматив платежей по страхованию имущества % (hстр=015%).
Подставляя все данные в формулу (11) получим:
2.6.4 Определение материальных затрат
Таблица 6.2.22– Материальные затраты
Наименование материальных затрат
Годовые затраты ты сруб.
Вспомогательные материалы
Прочие материальные затраты
2.7 Состав и расчет сметы общепроизводственных расходов
Расчет сведем в таблицу 23
Таблица 6.2.23 - Общепроизводственные расходы
Наименование статей затрат
Амортизационные отчисления на полное восстановление
Текущий ремонт и содержание: - здания
- Оборудования и транспортных средств
Заработная плата вспомогательных рабочих и служащих
Отчисления от заработной платы этих работников
Малоценный инструмент и инвентарь
Расход по охране труда и технике безопасности
Всего общепроизводственные расходы
2.8 Калькулирование себестоимости продукции
2.8.1 Определение полной себестоимости
Себестоимость всей продукции определяется как сумма всех затрат по участку.
Все затраты сведены в таблицу 6.2.24.
Таблица 6.2.24 – Себестоимость продукции
Годовые затраты тыс. руб.
Расходы на оплату труда основных рабочих
Отчисления от заработной платы основных производственных рабочих
Общепроизводственные расходы
Общехозяйственные расходы
Прочие производственные расходы
Итого полная себестоимость
2.8.2 Себестоимость единицы продукции
Расчет прямых затрат на деталь
Затраты на основные материалы рассчитываются по формуле:
где НР – норма расхода кг;
Цм – цена 1кг материала (заготовки) тыс.р.;
mд – масса детали кг;
Цот – цена 1 кг отходов тыс. р.
По данным определённым выше имеем: НР=1466кг; Цм=858тыс.рт;
mд=11 кг; Цот=179 тыс.р.т
Подставляя все значения в формулу (12) получим:
Заработная плата основных рабочих рассчитывается по формуле:
где Сч – средневзвешенная часовая тарифная ставка тыс. р;
Тед– трудоемкость обработки детали ч.
По данным определённым выше имеем: Сч=1486 тыс.р; Тед=1387ч.
Подставляя все значения в формулу (13) получим:
Отчисления от заработной платы рабочих рассчитываются по формуле:
Так как заработная плата основных рабочих посчитана имеем:
Произведем расчёт косвенных расходов на деталь.
Эти накладные расходы распределяются пропорционально зарплате основных рабочих по формуле:
где НРд – сумма накладных расходов подлежащих включению в себестоимость детали тыс.р.;
hнр – процент (норматив) накладных расходов %.
Указанный процент может быть определен по формуле:
где НР – общая сумма накладных расходов тыс. р.
- расходы на оплату труда основных рабочих тыс.р.
По данным определённым выше имеем: НР=18928697 тыс.р; =7416997 тыс.р.
Подставляя все данные в формулу (6.2.23) получаем:
Подставляя все данные в формулу (15) получаем:
Себестоимость единицы продукции рассчитывается по формуле:
где - затраты на основные материалы тыс.р;
- заработная палата основных рабочих тыс.р;
- отчисления от заработной платы рабочих тыс.р;
- косвенные расходы на деталь тыс.р.
Подставляя все данные в формулу (6.2.24) получаем:
Цена детали рассчитывается по формуле:
где Кн – коэффициент учитывающий налоги включаемые в цену;
Сед Пед – себестоимость и прибыль единицы продукции соответственно.
Прибыль на деталь принимается в размере 15% от её себестоимости.
Подставляя все данные в формулу (18) получаем:
Стоимость готовой (товарной) продукции рассчитывается по формуле:
где Цед – цена одной детали тыс.р;
Аi – программа выпуска детали шт.
Так как все данные определены подставим их в формулу (6.2.26) и получим:
В многономенклатурном производстве стоимость готовой продукции рассчитывается по формуле:
где - коэффициент учитывающий налоги включаемые в цену;
Соб и Поб – общая себестоимость и прибыль соответственно тыс.р.
Все данные определены выше; подставим их в формулу (20) и получим:
2.9 Расчет прибыли и показателей эффективности
Прибыль по участку рассчитывается по формуле:
где - стоимость готовой продукции тыс.р;
Соб - общая себестоимость тыс.р
Н – налоги тыс. руб.
Налоги определяются по формуле:
Посчитав налоги подставим остальные данные в формулу (6.2.28) и получим:
2.10 Расчет окупаемости инвестиций в участок
Расчет проведем по методу чистой текущей стоимости (ЧТС). Чистая текущая стоимость – это дисконтированное сальдо денежных потоков по проекту. Дисконтирование денежных потоков выполняется с использованием коэффициента дисконтирования αt который рассчитывается по формуле:
где Ен – коэффициент эффективности.
Исходными данными для расчета являются:
-срок строительства-1 год;
-инвестиции в основные фонды – 41426172;
-инвестиции в оборотные фонды - 41426172
-амортизация- 34966637
Таблица 6.2.25 – Расчет чистой текущей стоимости
Инвестиции(-) доход (+)
Коэффициент дисконтирования αt
Дисконтированный доход и инвестиции
Чистая текущая стоимость
2.11 Итоговые показатели и выводы
Основные технико-экономические показатели участка рассчитанные в организационно-экономической части проекта сведены в таблицу 6.2.26.
Таблица 6.2.26 – Основные технико-экономические показатели участка
Количество единиц оборудования
Производственная площадь
Число наименований деталей
Объем выпуска продукции
-общая себестоимость
Рентабельность продукции
Рентабельность производства
Производительности труда
Затраты на 1 рубль товарной продукции
Материалоемкость производства
Среднемесячная заработная плата
Срок возврата инвестиций
Экономический эффект техпроцесса
Разработанный в соответствии с заданием на дипломный проект технологический процесс обеспечивает изготовление деталей в заданном объёме установленного требованиями чертежа качеством.
В качестве заготовки в разработанном технологическом процессе была принята штамповка на ГКМ. Уменьшение напусков заготовки позволило уменьшить расход металла а также снизить трудоёмкость черновой токарной операции и была достигнута материальная экономия средств которая составила 136890 тыс. руб. Применение токарных станков с ЧПУ обеспечивает более высокую гибкость и производительность по сравнению с базовыми гидрокопировальными станками. Экономический эффект механической обработки детали составил тыс. руб.
На основании типового техпроцесса вала-шестерни был спроектирован участок механического цех по изготовлению валов был проведен его экономический анализ что позволило определить сроки окупаемости и необходимые затраты на реализацию проекта.
Список используемых источников
Антонюк В.Е. Конструктору станочных приспособлений: Справ. пособие.- Мн.: Беларусь 1991.
Горбацевич А.Ф. Курсовое проектирование по технологии машиностроения А.Ф. Горбацевич В.А. Шкред.– Мн.: Выш. шк. 1983.
Горошкин А.К. Приспособления для металлорежущих станков: Справ. - М: Машиностроение 1979.
Проектирование и производство заготовок в машиностроении: Учеб. пособие П.А. Руденко Ю.А. Харламов В.М.Плескач; Под общ. Ред. В.М.Плескача. – К.: Выща шк. 1991.- 247 с.: ил.
Дипломное проектирование по технологии машиностроения Под общ. ред. В.В. Бабука. – Мн.: Выш. шк. 1979.
Общемашиностроительные нормативы времени вспомогательного на обслуживание рабочего места и подготовительно-заключительного для технического нормирования. Серийное производство. – М.: Машиностроение 1974.
Прогрессивные режущие инструменты и режимы резания металлов: Справ. В.И. Баранчиков А.В. Жаринов Н.Д. Юдина и др.; Под общ. ред. В.И. Баранчикова. - М.: Машиностроение 1990.-400с.: ил.
Режимы резания металлов: Справ. Под ред. Ю.В. Барановского - М.: Машиностроение 1972.
Справочник технолога-машиностроителя. Т.1 Под ред. А.Г. Косиловой Р.К. Мещерякова.– М.: Машиностроение 1985.
Справочник технолога-машиностроителя. Т.2 Под ред. А.Г. Косиловой Р.К. Мещерякова.– М.: Машиностроение 1985.
Станочные приспособления: Справ. Т.1 Под ред. Б.Н. Вардашкина и А.А. Шатилова. - М.: Машиностроение 1984.
Технология автоматизированного производства. Т.2 Под ред. А.А. Жолобова. – Мн.: Дизайн ПРО 1997.
Карты контроля.frw

Наименование оборудования
Белорусско-Российский
Проверить наличие фасок и
отсутствие заусенцев
Проверить шероховатость
Образцы шероховатости
Калибр пробка 120Н11
Индикатор часового типа
Наименование операции
Проверить радиальное биение:
Карты1.frw
Призма 7808-4013; фреза торцовая 2214-0277
14-0278 Т15К6 ГОСТ 26595-86; штангенциркуль ШЦ-
Приспособление сверлильное;сверло 2301-0039 Р6М5 ГОСТ 10903-77;штангенциркуль ШЦ-
Приспособление сверлильное; метчик М14 2620-2773 Р6М5 ГОСТ 3266-81; штангенциркуль ШЦ-
пробка 8221-3053 7Н ГОСТ 17758-72
Центр 7032-0029 ГОСТ13214-79; центр 7032-0079 ГОСТ2576-79; хомутик 7107-0070 ГОСТ16488-70; круг1
0х80х305 24А 40-П С1 7КПГ 35 мс А кл.1 ГОСТ2424-83; скоба 8113 -0142 h7 ГОСТ 18362-73;образец
ГОСТ 9378-75; микрометр МК 50-75 ГОСТ6507-90
Резец 2100-2195 Т15К6 ГОСТ 26611-85;
Резец 212-296 Т30К4 ГОСТ 26611-85;
штангенглубиномер ШГ-160; штангенциркуль ШЦ-
Приспособление сверлильное; сверло
2301-0001 ГОСТ 10903-77 Р6М5 ГОСТ 10903-77;втулка 6100-0142
пробка 8133-0913 ГОСТ 14819-69
Приспособление сверлильное; зенковка 2353-0011 МН725-60;штангенциркуль ШЦ-
Центр 7032-0080 ГОСТ 13214-79; хомутик 706-226-03;фреза червячная шлицевая
оправка 62-162; скоба 8102-6118;микрометр М 30-25 ГОСТ 6507-90
ГОСТ 166-89; образец шероховатостей Ra3
Приспособление фрезерное; фреза 2510-0219 МН 4909-63 m=5
; оправка 6224-0143 МН 3503-62; микрометр
зубомерный МЗ-50-75 ГОСТ 6507-90; образец шероховатости 6
Угол наклона линии зуба
Направление линии зуба
Нормальный исходный контур
Коэффициент смещения
Степень точности ГОСТ 1643-81
Средняя лина общей нормали
Допуск не радиальное биение зубьев венца
Центра при станке; шевер левый m5.5х41х15
ГОСТ 8570-80; микрометр зубомерный МЗ-50-75 ГОСТ 6507-90;
образец шероховатости 2
0х80х305 24А 40-П С1 7КПГ 35 мс А кл.1 ГОСТ2424-83; скоба 8113 -0142 55Г ГОСТ 18362-73;
0х80х305 24А 40-П С1 7КПГ 35 мс А кл.1 ГОСТ2424-83; скоба 8113 -0142 55n6 ГОСТ 18362-73; глубиномер
0х80х305 24А 40-П С1 7КПГ 35 мс А кл.1 ГОСТ2424-83; скоба 8113 -0142 55Г ГОСТ 18362-73;образец
шероховатости 1 ГОСТ 9378-75; штангенглубиномер ШТ-160 ГОСТ160
Фрезерно-центровальная
Наименование операции
Обозначение программы
Сталь 18ХГТ ГОСТ 4543-71
ГОСТ 3.1404-86 Форма 3
Фрезеровать торцы 1 и 2 одновременно
Сверлить центровые отверстия 3 и 4 одновременно
Призма 7808-4013; сверла центровые 2317-0012 Р6М5 ГОСТ 14952-75; штангенциркуль 8734-4051; эталон
Контроль рабочим 100%
Закрепить заготовку в патроне. Установ А.
Патрон поводковый7100-0001 ГОСТ2675-80
Сверлить орверстие 1
Нарезать резьбу выдерживая размеры 3
Приспособление сверлильное; зенковка 2353-0136 Р6М5 ГОСТ 14953-80; набор образцов шероховатости 0
Установить деталь в приспособление для сверлнния отверстий. Установ А
Вертикально-сверлильная
Шлифовать поверхность 1 и торец 2
Торцекруглошлифовальная
Подрезать торец в размер 4
Точить поверхность 1
Закрепить заготовку в патроне. Установ Б.
Точить канавку выдерживая размеры 7
Точить канавки выдерживая размеры 8
Точить резьбу выдерживая размер 15
Резец 216-19 Т15К6 ГОСТ 26611-85;кольцо В211-0132 6g ГОСТ 17763-72
Сверлить отверстие 1
Сверлить отверстие 2
Фрезеровать зубчатый венец 1
Зенковать поверхность 1. Установ А.
Зенковка 232-123 Т15К6; образец шероховатости 2
Зенковать поверхность 2. Установ Б.
Шлифовать поверхность 1
Шлифовать поверхность 2 и торец 3
Маршрутная карта.frw

ГОСТ 3.1118-82 Форма 1
Обозначение документа
наименование оборудования
Фрезерно-центровальная
наименование операции
Вертикально-сверлильная
Торцекруглошлифовальная
Кондуктор.cdw

Белорусско-Российский
Допуск перпендикулярности оси кондукторной
втулки к поверхности А 0
Допуск смещения от расположения в одной
плоскотси осей призм 0
Контрольное приспособление.cdw

Белорусско - Российский
*Размеры для справок
Несоосность центров не более 0
Приложение А.doc
на шестерню 40Р.00.00.692
ПРИЛОЖЕНИЯ.doc
Спецификация ДПД.021.42.21.00.СБ
Спецификация ДПД.021.42.31.00.СБ
Комплект документов на технологический процесс
изготовления вала–шестерни 546П–1802086
САПР.doc
Private Sub Ok_Click()
' ***************************************************************
' ПРОГРАММА ОПТИМИЗАЦИИ РЕЖИМА СВЕРЛЕНИЯ
' НА ВЕРТИКАЛЬНО-СВЕРЛИЛЬНОМ СТАНКЕ 2Н150
'*************************************************************
'СВЕДЕНИЯ О ТЕХНОЛОГИЧЕСКОМ ПЕРЕХОДЕ
Dim D As Single ' Диаметр обрабатываемой поверхности
Dim L As Single ' Длина обрабатываемой поверхности
Dim TR As Single ' Глубина резания
Dim LVP As Single ' Величина врезания и перебега инструмента
Dim Ra As Single ' Шероховатость обработанной поверхности
'СВЕДЕНИЯ О МЕТАЛЛОРЕЖУЩЕМ СТАНКЕ
Const k As Integer = 22 ' Количество ступеней частоты вращения шпинделя
Dim n As Variant ' Ряд скоростей вращения шпинделя
n = Array(12.2 16 20 25 31.5 40 50 63 80 100 125 160 200 250 315 400 500 630 800 1000 1250 1600)
Const m As Integer = 22 ' Количество ступеней продольных подач суппорта
Dim S As Variant ' Ряд продольных подач суппорта
S = Array(0.05 0.06 0.075 0.09 0.1 0.125 0.15 0.175 0.2 0.25 0.3 0.35 0.4 0.5 0.6 0.7 0.8 1 1.6 2 2.4 2.8)
Const ND As Single = 5.5 'Мощность двигателя привода
Const KPD As Single = 0.87 'КПД коробки скоростей станка
'СВЕДЕНИЯ О РЕЖУЩЕМ ИНСТРУМЕНТЕ
Const Te As Integer = 25 'Экономически выгодный период стойкости
'КОЭФФИЦИЕНТЫ И ПОКАЗАТЕЛИ СТЕПЕНЕЙ В УРАВНЕНИИ РАСЧЕТА ПЕРИОДА СТОЙКОСТИ
Const Mv As Single = 0.2 Cv = 9.8 qv = 0.4 Yv = 0.5 Kv = 0.8
'КОЭФФИЦИЕНТЫ И ПОКАЗАТЕЛИ СТЕПЕНЕЙ В УРАВНЕНИИ РАСЧЕТА ОСЕВОЙ СИЛЫ РЕЗАНИЯ
Const Cp As Single = 68# qp = 1# Yp = 0.7 Kp = 0.8
'КОЭФФИЦИЕНТЫ И ПОКАЗАТЕЛИ СТЕПЕНЕЙ В УРАВНЕНИИ РАСЧЕТА КРУТЯЩЕГО МОМЕНТА
Const Cm As Single = 0.035 qm = 2# Ym = 0.8 Km = 0.8
Dim V Tij PZ NRij Raij Toij As Single
Dim Nopt Sopt Vopt Topt POopt NRopt Raopt Toopt As Single
pr = Worksheets(5).Range("D16 ").Value 'Количество переходов
For p = 4 To pr + 3 'Цикл определения входных параметров переходов
D = Worksheets(5).Cells(18 p).Value ' Диаметр обрабатываемой поверхности
L = Worksheets(5).Cells(19 p).Value ' Длина обрабатываемой поверхности
LVP = Worksheets(5).Cells(21 p).Value ' Величина врезания и перебега инструмента
Sdop = 0.02 * D ' Подача допустимая прочностью инструмента
Toopt = 1000000 ' Начальное значение критерия оптимизации
For i = 0 To k - 1 ' Цикл по ступеням частоты вращения шпинделя
For j = 0 To m - 1 ' Цикл по ступеням продольных подач суппорта
' Расчет скорости резания
V = 3.14 * D * n(i) 1000
'Проверка ограничения по допустимой прочностью инструмента подаче
If S(j) > Sdop Then GoTo M1
' Расчет периода стойкости инструмента
Tij = ((Cv * D ^ qv * Kv) (V * S(j) ^ Yv)) ^ (1 Mv)
' Проверка ограничения по периоду стойкости инструмента
If Tij Te Then GoTo M1
' Расчет составляющей Po силы резания
PO = 10 * Cp * D ^ qp * S(j) ^ Yp * V ^ Np * Kp
' Расчет крутящего момента
Mkr = 10 * Cm * D ^ qm * S(j) ^ Ym * Km
' Расчет мощности затрачиваемой на резание
NRij = Mkr * n(i) 9750
' Проверка ограничения по мощности привода станка
If NRij > ND * KPD Then GoTo M1
' Расчет величины основного времени (критерия оптимизации)
Toij = (L + LVP) (n(i) * S(j))
' Проверка критерия оптимизации на минимум значения целевой функции
If Toij > Toopt Then GoTo M1
' Сохранение значений режима резания на текущем шаге оптимизации
Nopt = n(i) ' Оптимальная частота вращения шпинделя
Sopt = S(j) ' Оптимальная продольная подача
Vopt = V ' Оптимальная скорость резания
Topt = Tij ' Период стойкости инструмента
POopt = PO ' Осевая составляющая силы резания
NRopt = NRij ' Мощность затрачиваемая на резание
Mkropt = Mkr ' Крутящий момент
Toopt = Toij ' Основное время на выполнение перехода
'ВЫВОД РЕЗУЛЬТАТОВ ОПТИМИЗАЦИИ
Worksheets(5).Cells(27 p).Value = Nopt
Worksheets(5).Cells(28 p).Value = Sopt
Worksheets(5).Cells(29 p).Value = Sopt * Nopt
Worksheets(5).Cells(26 p).Value = Vopt
Worksheets(5).Cells(30 p).Value = Topt
Worksheets(5).Cells(33 p).Value = POopt
Worksheets(5).Cells(32 p).Value = NRopt
Worksheets(5).Cells(31 p).Value = Mkropt
Worksheets(5).Cells(34 p).Value = Toopt
Оптимизация режимов сверления на станке модели 2Н150
Регулирование частоты вращения шпинделя ступенчатое
Регулирование подачи ступенчатое
Обрабатываемый материал
Количество переходов
Диаметр поверхности мм
Длина поверхности мм
Врезание и перебег мм.
Шероховатость Ra мкм
Оптимальные режимы резания
Скорость резания ммин
Частота вращения обмин
Период стойкости мин.
Нормативные режимы резания
Сокращение основного времени по переходам в %
Сокращение основного времени по операции в %
Содержание.doc
2 Определение типа производства5
Патентное исследование червячных фрез6
Технологическое проектирование13
1 Назначение и конструкция детали 13
2 Анализ технологичности конструкции детали 15
3 Выбор метода получения заготовки 17
4 Принятый технологический процесс 18
5 Расчет припусков на обработку 21
6 Расчет режимов резания 31
7 Расчет точности операции 41
8 Техническое нормирование 43
9 Уточнение типа производства 49
10 Расчет требуемого количества станков 51
11 Расчет необходимого количества рабочих 53
12 Расчет необходимого количества транспортных средств 56
13 Планировка участка 58
14 Экономическое обоснование принятого варианта технологического процесса 59
15 Параметрическая оптимизация переходов сверления отверстий на вертикально-сверлильном станке 66
Конструирование и расчет приспособлений и инструментов 71
1 Станочное приспособление 71
2 Контрольное приспособление 76
3 Режущий инструмент 78
Безопасность и экологичность проекта 85
Организационно-экономическая часть 96
1 Организационная часть 96
2 Экономические расчеты. 97
Список используемых источников 122
Приложение А. Оптимизация режимов сверления
Приложение Б. Спецификация ДПД.021.42.21.00.СБ
Приложение В. Спецификация ДПД.021.42.31.00.
Приложение Г. Комплект документов на технологический процесс изготов-ления вала-шестерни 546П-1802086.
Спецификация к кондуктору.spw

ДПД.021.42.21.00.01.00
Втулка 7051-555812f7
Спецификация контрольного.spw

Титульник на карты.cdw

ГОСТ 3.1404-86 Форма5
Министерство образования Республики Беларусь
Технологический процесс механической обработки
Министерство образования и науки Российской Федерации
Белорусско-Российский университет
Кафедра "Технология машиностроения
Государственное учреждение высшего профессионального образования
Фреза.cdw

Белорусско-Российский
Накопленная погрешность окружного шага не более F
Радиальное биение дуртиков не более f
Угол наклона стружечной канавки
Маркировать: параметры шлицевого валика
диаметр посадачного отверстия
инструментальный материал
товарный знак изготовителя
ЦЕХ-х.cdw

Белорусско-Российский
университет гр. ТМА-021
ДПД 011.37.81.00.000
Место складирования заготовок
Местный вентиляционный отсос
Условные обозначения
Рабочее место станочника
Место для готовых деталей
Конвейер для уборки стружки (шнековый)
Фрезерно центровальный
Вертикально-сверлильный
Наименование оборудования
Экономика1.cdw

экономические показатели
ДПД.021.42.75.00.000
Количество едениц оборудования
Производственная площадь
Число наименований деталей
Объём выпуска продукции
Рентабельность продукции
Рентабельность производства
Производительность труда
Затраты на 1 рубль товарной продукции
Материалоёмкость производства
Среднемесячная заработная плата
Срок возврата инвестиций
Экономический эффект техпроцесса
- общая себестоимость
- с учетом изменения заготовки
Эскизы - 2.cdw

Направление линии зуба
Нормальный исходный контур
Коэффициент смещения
Степень точности ГОСТ 1643-81
Средняя лина общей нормали
Допуск не радиальное биение зубьев венца
Белорусско - Российский
Операция 065 - Шлицефрезерная
Операция 050-Торцекруглошлифовальная
Операция 040 - Вертикально - сверлильная
Операция 045 -Торцекруглошлифовальная
Операция 060 -Зубошевинговальная
Операция 055 -Зубофрезерная
Эскизы - 1.cdw

Фрезерно - центровальный
полуавтомат МР - 71М
Белорусско - Российский
Операция 010 - Токарная с ЧПУ
Эскизы - 3.cdw

Операция 015 - Токарная с ЧПУ
Белорусско - Российский
Операция 020 - Вертикально - сверлильная
Операция 065 - Шлицефрезерная
Рекомендуемые чертежи
- 24.01.2023
- 05.01.2022
- 24.01.2023
- 04.06.2017
Свободное скачивание на сегодня
Другие проекты
- 20.08.2014