Дозатор тонера


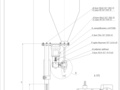
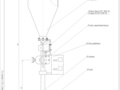
- Добавлен: 19.12.2022
- Размер: 2 MB
- Закачек: 1
Описание
Дипломный проект по проектированию дозатора тонера с перистальтическим насосом
Состав проекта
![]() |
![]() ![]() ![]() |
![]() ![]() ![]() |
![]() |
![]() ![]() ![]() ![]() |
![]() ![]() ![]() ![]() |
![]() ![]() ![]() ![]() |
![]() ![]() ![]() ![]() |
![]() ![]() ![]() ![]() |
![]() ![]() ![]() ![]() |
![]() ![]() ![]() ![]() |
![]() ![]() ![]() ![]() |
![]() ![]() ![]() ![]() |
![]() ![]() ![]() ![]() |
![]() ![]() ![]() ![]() |
![]() ![]() ![]() ![]() |
![]() ![]() ![]() ![]() |
Дополнительная информация
маршрутная карта.doc
Коднаименование операции
Обозначение документа
Код оборудования модель инвентарный номер
ширина расч. длина t i S n V T0 TВ
Токарно-винторезный 16К20Ф3 ток. 4 1 1 500 27 4964
Резец 2112-0031 ГОСТ18871-73 3-кулачковый патрон
Точить выдерживая размеры 3 4
Резец 2101-0559 ГОСТ18870-73 3-кулачковый патрон штангенциркуль ШЦ-1
Точить выдерживая размеры 5 6
Код наименование оборудования
Наименование детали сб. единицы или материала
Точить выдерживая размеры 7 8
Точить выдерживая размеры 8 9
Резец 2120-0503 ГОСТ 18874-73 3-кулачковый патрон
Резец 2221-1287 ГОСТ 18877-73 3-кулачковый патрон штангенциркуль ШЦ-1
Переустановить деталь
Подрезать торец выдерживая размер 10
Точить выдерживая размеры 11 12
Точить выдерживая размеры 13 14
Резец 2101-0045 ГОСТ 18875-73 3-кулачковый патрон
Сверлить отверстие выдерживая размеры 1516
Сверло 2300-2752 ГОСТ 4010-77 3-кулачковый патрон
Калить до твердости HRC 40 45
0 4131 Круглошлифовальная
Круглошлифовальный 3410В шлиф. 4 1 1 1 500 17 292
Шлифовать выдерживая размер 5 71113
Круг ПП 250х20х60 14АСТ1К5 35 мс кл.2А ГОСТ 2424-83 патрон цанговый микрометр рычажный МР ГОСТ 510-71
0 4132 Внутришлифовальная
Внутришлифовальный 3К225В шлиф. 4 1 1 1 500 17 292
Шлифовать выдерживая размеры 15
Круг ПП 10х6х4 14АСТ1К5 35 мс кл.2А ГОСТ 2424-83 патрон 4-кулачковый микрометр рычажный МР ГОСТ 510-71
пз.doc
Описание конструкции дозатора
1. Расчет производительности насоса
2. Процесс дозирования по времени
3. Процесс дозирования по массе
3.1. Режим автоматического дозирования
3.2. Режим ручного дозирования
Расчеты подтверждающие работоспособность.
1. Кинематический расчет
3. Расчет червячной передачи редуктора
4. Предварительный расчёт валов.
5 Выбор типа подшипников.
6. Расчет на точность.
7 Расчет на надежность
8. Расчет шпоночных соединений
9. Расчет подшипников скольжения
Микропроцессорный контроллер.
1 Технические данные
2. Органы управления и индикации
4. Описание меню прибора
5. Настройка параметров контроллера
6. Монтаж прибора на объекте
Технология изготовления вала насоса
1. Назначение служебная конструкторская и технологическая
характеристики детали
2. Описание типа производства
3. Выбор вида исходной заготовки и методы ее получения
4. Выбор технологических баз и схем базирования
5. Расчет параметров резания при точении
6. Нормирование технологического процесса
7. Анализ технологичности детали
Основное назначение дозирующего устройства — обеспечить заданное количество материала по массе (или поддержание заданного расхода компонента) с определенной точностью. Питание компонентов является одной из важнейших операций технологического процесса приготовления теста.
К питателям предъявляются следующие основные требования:
определенная точность питания компонентов;
высокая производительность;
простота конструкции и высокая надежность работы узлов питателя и его системы управления;
По структуре рабочего цикла дозирование бывает непрерывным или порционным а по принципу действия — объемным или весовым.
Для порционного дозирования характерно периодическое повторение циклов выпуска дозы (порции) компонента. При порционном объемном способе дозирующее оборудование обычно отмеривает порцию при помощи мерной камеры заданного объема. Порционное весовое дозирование основано на отмеривании дозы определенной массы. При непрерывном объемном дозировании дозатор подает поток материала с заданным объемным расходом. Объемный способ дозирования конструктивно более прост поэтому дозаторы основанные на этом принципе работы более надежны. Применение объемного метода существенно упрощает процесс дозирования жидких компонентов. Вместе с этим объемное дозирование нередко характеризуется более значительной погрешностью в величине выдаваемых доз что в отдельных случаях может ограничить его применение.
Многокомпонентное дозирование может осуществляться по следующим схемам.
Последовательное дозирование компонентов в одном общем дозаторе.
Параллельное дозирование каждого компонента в отдельном специальном дозаторе (так называемые дозировочные станции).
Первая схема используется как правило при порционном дозировании и является весьма простой и экономичной. Она обеспечивает меньшую металлоемкость и компактность установки. Однако длительность общего цикла дозирования из-за последовательного отмеривания компонентов велика. Это может снижать производительность тестоприготовительного оборудования.
Вторая схема применяется при непрерывном дозировании. Она позволяет наиболее полно приспособить каждый дозатор к особенностям дозируемого компонента и тем самым повысить точность дозирования. Вместе с этим нужно учитывать что дозировочные станции такого типа более громоздки и имеют большую стоимость.
Упрощенная классификация дозаторов по структуре рабочего цикла и конструктивным признакам выглядит так:
Выбор конструкции дозирующего устройства.
1. Оборудование европейских производителей представлено на рынке в основном автоматическими или полуавтоматическими линиями с высокой степенью автоматизации и с очень высокой производительностью. Данные дозаторы предназначены для фасовки большого объема однотипного тонера вследствие чего перенастройка на другой тип тонера или на другой вес порции затруднена. Данные дозаторы более подходят для больших производств специализирующихся на фасовке однотипного тонера и поэтому мы не будем подробно на них останавливаться.
Рисунок 1 –дозаторы европейского производства: автоматическая линия по дозированию (рис.1а) дозатор европейского производства (рис.1б)
Другим полюсом рынка можно считать дозаторы различных китайских производителей.
Дозаторы китайских производителей можно считать другой крайностью в конструкции фасовщиков тонера. Основа популярности китайских моделей их традиционная дешевизна. Дешевизна влечет за собой простоту конструкции вплоть до примитивизма несколько разбавленного китайской электроникой.
2.Точность дозирования осуществляется по весу.
Переход на другой вид тонера затруднен большинство моделей оснащены только одним постом раздачи. Применение в некоторых моделях сменных бункеров с тонером не решает данную проблему полностью. При покупке же нескольких дозаторов каждого под свой тонер пропадает ценовая привлекательность китайских моделей.
Сохранность тонера вполне удовлетворительная. Герметичность достигается применением в качестве бункеров пластиковых мешков и бочек. Слежаться тонеру в бункере тоже не придется в течении дня фасовщик поднимет и перевернет бункер неоднократно. Особенность большинства моделей – пост раздачи в виде мягкой пластиковой трубки через которую самотеком и подается тонер. Остановка подачи тонера осуществляется передавливанием этой трубки. Постепенно тонер в месте сжатия спекается и забивает подающую трубку. Как результат комки спекшегося тонера могут попасть в картридж. Поставщики предлагают считать трубки расходным материалом а испорченный тонер – минимальным злом.
Условия труда фасовщика – вызывают сочувствие фасовщик вынужден в течение смены неоднократно снимать а затем поднимать на высоту 15-2 метров 10-20 килограммовые бункеры.
Цену можно признать минимальной из возможных срок службы тоже.
Основа популярности китайских моделей их традиционная дешевизна.
3.Оценка отечественных разработок дозаторов тонера
Рисунок 2 –дозатор отечественной сборки
Хочется упомянуть появляющиеся время от времени предложения дозаторов от российских компаний разработчиков профессиональной дозирующей и упаковочной техники.
Рассмотрим их на примере «Дозатора тонера 1».
К сожалению все попытки напрямую применить опыт фасовки других сыпучих смесей к фасовке тонера закончились неудачей а конструкции не пошли далее опытных образцов. Объяснение здесь простое производители оборудования не пожелали разобраться в свойствах тонера и не учли потребности ресайклеров.
Что бы ни быть голословными укажем на основные ошибки. Раздача тонера через один пост раздачи нет возможности сменить тонер в бункере до его полной выработки. Не герметичность бункера.
Достоинством можно было бы считать возможность задать нужную порцию в граммах но излишне сложное решение с применением тензодатчиков приводит к высокой стоимости. Высокая стоимость и недостатки конструкций не позволяют окупить данные образцы.
Оценим «Дозатор тонера 2»
Скорость подачи тонера задается двухскоростным подающим шнеком каждая скорость дополнительно может регулироваться в довольно в широких пределах. Тонкая настройка скорости подачи осуществляется регулировочным винтом переключение скорости с малой на большую вынесено на лицевую панель. На лицевой же панели расположены и таймеры по команде которых происходит отсечка подачи тонера.
Все это сделано в попытке отказаться при фасовке от использования электронных весов и тем самым снизить себестоимость дозатора.
К сожалению электронные весы все равно придется иметь на рабочем месте фасовщика для калибровки дозатора и периодического контроля веса порций.
Производитель настоятельно рекомендует создать таблицы с указанием необходимого времени для получения порции определенного веса определенного типа тонера.
Что бы избежать ошибок и частой замены таблиц винт точной регулировки вынесен на крышку дозатора. Со слов производителя настройка дозатора мастерами на производстве занимало три дня сейчас для ускорения производства дозаторы поставляются без калибровки.
Доступ к различным тонерам решен установкой трех независимых бункеров каждый с индивидуальной регулировкой скорости подачи. Дозатор выполнен в едином корпусе поэтому увеличение количества бункеров невозможно.
Герметичность бункера не вызывает сомнений. Объем бункера позволяет сразу загрузить до 25 кг. тонера. Можно предположить что большой вес тонера и его длительное нахождение в бункере может привести к изменению объемной плотности тонера а как следствие к увеличению веса порции тонера. Хотя данная проблема нивелируется при больших объемах фасовки (свыше 500 порций в месяц каждого типа тонера) или при регулярной калибровке дозатора.
Условия труда фасовщика хорошие. Можно рекомендовать закрепить для работы на данном дозаторе отдельного рабочего обученного и обладающего достаточной внимательностью.
Цена данного дозатора вызывает восторги но она в 2 с лишним раза ниже цен простейших китайских моделей что вызывает некоторую озабоченность.
Производитель объясняет низкую стоимость тем что корпус дозатора выполнена из ДВП. Каким окажется реальный срок работы данной конструкции на практике мы не знаем.
Оценим «Дозатор тонера 3»
Рисунок 3 – Дозатор тонера отечественного производства с 3-мя бункерами
Точность дозирования контролируется в простейшем исполнении дозатора вручную по весу или объему порции. Точность дозирования достигает 1% если применять для контроля электронные весы
Забота о сохранности тонера отличительная черта данной конструкции.
Объем бункера позволяет сразу загрузить в него тонер из стандартного 10 кг. мешка данный объем можно считать оптимальным хотя он и может быть увеличен по требованию.
Герметичность бункера не вызывает сомнений.
Особо обращает на себя внимание наличие в бункере шнека для постоянного перемешивание тонера.
Подача тонера осуществляется отдельным подающим шнеком который обеспечивает равномерность а следовательно и точность подачи.
Данная схема с двумя шнеками исключает попадание в картридж или тубу некондиционного тонера. А это сказывается на качестве выпускаемой продукции и работает на Ваш имидж.
Условия труда фасовщика можно признать хорошими а при установке вытяжки даже отличными.
Цену можно считать адекватной корпуса бункеров и механизмы выполнены из нержавеющей стали что значительно увеличивает срок службы дозатора.
Заканчивая обзор хочется с удовлетворением заметить что на рынке представлена широкая гамма дозаторов и можно подобрать дозатор наиболее полно отвечающий запросам ресайклера.
Описание конструкции дозатора.
На рисунке 2.1 представлена схема дозатора тонера с перистальтическим насосом.
Рис. 2.1. Схема дозатора.
Тонер засыпается в бункер рассчитанный на 20 кг. В верхней части бункера установлен клапан. Из бункера тонер попадает в расширительную камеру к которой подсоединена трубка насоса. Трубка проходит через перистальтический насос.
Вращение ротора насоса осуществляется асинхронным двигателем через червячный редуктор. Двигатель и редуктор выбираются стандартные.
Двигатель однофазный асинхронный общего применения 4ААМТ50В4 мощностью 90 Вт и частотой вращения 1500 обмин. Эскиз электродвигателя представлен на рис. 2.2.
Рис. 2.2. Электродвигатель 4ААМТ50В4.
Рис. 2.3. Редуктор червячный РЧ-25.
Редуктор одноступенчатый червячный РЧ-25 с передаточным отношением 25. Номинальный крутящий момент 10 Нм межосевое расстояние 25 мм.
Эскиз редуктора представлен на рисунке 2.3.
Так как диаметр вала двигателя и входного вала редуктора практически одинаковы то для соединения валов используем стандартную муфту втулочную по ГОСТ 24246-80. Для соединения вала редуктора и вала ротора насоса также используем муфту втулочную по ГОСТ 24246-80.
Дозирование происходит двумя способами: по времени и по массе. Управление работой насоса при объемном дозировании по времени происходит с помощью счетчика дозатора схема которого представлена на рисунке 2.4.
Рис. 2.4. Счетчик дозатор.
Дозирование по массе производится с помощью контроллера Master 210.4 представленного на рисунке 2.5. Предназначен для автоматического управления процессами объемного непрерывного и дискретного дозирования сыпучих и жидких компонентов. Прибор поддерживает заданную производительность управляя исполнительным механизмом подачи продукта аналоговым выходом 0-20mA (0-10V). Контроллер ведет учет текущего расхода порции а также хранит информацию об общем количестве продукта отдозированного с помощью прибора.
Рис. 2.5. Контроллер Master 210.4.
Описание устройства настройки работы и монтажа прибора представлено далее в соответствующем разделе.
Корпус насоса состоит из двух частей. Одна часть в которой находится ротор жестко закреплена на раме установки вторая часть прижимная при помощи винта с маховиком прижимается к первой тем самым фиксирует трубку в насосе. Сделано это для того что бы удобно было менять перистальтическую трубку в случае ее износа или же при смене цвета тонера.
Для дозирования по массе платформа стола 9 оснащено тензодатчиками соединенными с контроллером.
Все эти элементы смонтированы на общей колонне (рис. 2.6).
Рис. 2.6. Дозатор: 1- колонна 2 – консоль 3 – воронка 4 – бункер 5 – электродвигатель 6 – редуктор 7 – насос 8 – трубка 9 – подъемный стол 10 – кнопочный пульт управления.
Рис. 3.1. Принцип действия насоса.
Перистальтический (шланговый) насос является роторной машиной объемного типа. Насос включает в себя металлический корпус в котором на валу установлен стальной ротор с четырмя диаметрально расположенными роликами из алюминиевого сплава. Между внутренней стенкой корпуса и ротором уложен шланг специальной конструкции из полимерной резины с кордом. При вращении ротора ролики обкатывают шланг пережимая его и выдавливают перекачиваемую среду в направлении вращения. Шланг сзади ролика практически сразу восстанавливает свою форму до полного сечения. В результате за роликом создается вакуум обеспечивающий самовсасывание перекачиваемой среды.
Производительность насоса при полном сжатии шланга зависит только от объема витка шланга:
где Vв – объем витка шланга
п – частота вращения ротора насоса (обмин).
Оббьем витка шланга найдем по формуле:
Где d – внутренний диаметр трубки
l – длина витка трубки.
Для определения длины витка составим расчетную схему (рис. 3.2) предварительно задавшись диаметром роликов и ротора насоса.
Рис. 3.2. Расчетная схема.
Из схемы видно что радиус витка равен
Отсюда длина витка равна
И соответственно объем витка:
За один оборот ротора будет происходить дозирование четырех порций тонера объемом Vв. Таким образом конечная производительность насоса будет равна:
Дозирование тонера осуществляется по времени. Т.е. за один оборот роликов редуктора происходит дозирование порции порошка определенного фиксированного веса. Необходимую массу дозы можно определить по формуле:
где - масса порции тонера за один оборот роликов насоса
t – время необходимое для достижения необходимой массы дозы.
2. Процесс дозирования по времени.
Сам процесс дозировки происходит следующим образом. На таймере счетчика выставляется время необходимое для заполнения нужного объема. Нажимаем кнопку ПУСК на выводе PD-6 (рис. 2.4) появляется логическая 1 которая управляет двигателем насоса начинаем процесс дозирования считаются импульсы пересчитываются и выводятся на индикатор счет от заданного времени идет на уменьшение и достигнув значения 0 на индикаторе счетчика одновременно на выводе PD-6 появляется логический ноль что даст команду остановке двигателя.
3. Процесс дозирования по массе.
В контроллере “Master - 210.4” предусмотрены два режима дозирования: ручное (объемное) и автоматическое а также четыре вспомогательных режима – “Продувка” “Сброс расхода” “Сброс порции” и “Стоп дозирования”. Любой из режимов в том числе и режимы дозирования инициируются с помощью соответствующих подменю РежимыУправление”.
Для режима автоматического дозирования можно выделить два варианта работы:
)Дозирование с заданной производительностью “ЗПр-ть” количества продукта “Порция” (остановка дозирования при истечении заданного времени дозирования которое задается в параметре “Время”);
)Непрерывное дозирование с заданной производительностью “ЗПр-ть” (остановка дозирования осуществляется оператором).
Выбор конкретного варианта режима автоматического дозирования определяется опцией “Вариант дозир-я” в меню “РежимыОпции”.
В любом случае во время автоматического дозирования выполняются следующие расчеты и операции:
-производится подсчет количества отдозированного продукта (оперативный параметр “О.расход”);
-анализ оперативной ситуации на состояния требующие остановки дозирования (нет разрешения дозирования (дискретный вход “Q1”) емкость пуста (“Q3”) отказостановка соседнего отказ насоса (“Q5”) и т.д.).
Последовательность действий перед пуском дозирования
-проверить при необходимости корректность настроек параметров;
-выбрать вариант дозирования (“РежимыОпцииВариант дозир-я”);
-произвести при необходимости сброс дозирования текущей порции;
-выполнить при необходимости “Продувку”;
-выполнить если надо “Сброс расхода”;
-осуществить запуск дозирования.
Режим автоматического дозирования запускается с помощью меню “РежимыУправление Пуск дозирования”. На случай возможной отмены контроллер выведет диалог подтверждения “Запуск дозир-я?” – требуется подтверждение клавишей «ввод» (нажатие на клавишу «режим» приведет к отмене). После выполнения данных действий произойдет выход в меню “Параметры” на индикацию параметра “Порция”.
При необходимости возможна остановка процесса дозирования путем выполнения команды “РежимыУправлениеСтоп дозирования”.
Последовательность управления выходами при пуске и остановке дозирования при пуске:
-включается выход “Z3” информирующий о начале дозирования и выключается (если был включен) выход “Z4”;
-включаются выходы “Z1” и “Z2” (включение насоса и системы подачи воздуха);
-подается управляющее воздействие с аналогового выхода.
-снимается управляющее воздействие с аналогового выхода;
-выключается выход “Z3” и включается выход “Z4” свидетельствующий об успешном завершении дозирования заданной порции;
-выключается выход “Z1”;
-через 10 секунд выключается выход “Z2”.
Выходной сигнал “Z4” задействован если включена опция дозирования по времени.
Режим ручного дозирования предназначен для объемного дозирования. Т.е. управляющее воздействие задается вручную с клавиатуры контроллера (параметр “ЗПр-ть”). В режиме ручного дозирования выполняются следующие функции:
-включаются выходы “Z1” и “Z2”;
-выдается управляющее воздействие в соответствии со значением оперативного параметра “ЗПр-ть” которое в ручном режиме доступно для изменения с клавиатуры;
-анализ оперативной ситуации на состояния требующие остановки дозирования (нет разрешения дозирования емкость пуста авария насоса и т.д.).
Режим ручного дозирования запускается с помощью меню “РежимыУправлениеРучной режим”. На случай возможной отмены контроллер выведет диалог подтверждения “Ручной режим?” – требуется подтверждение клавишей «ввод» (нажатие на клавишу «режим» приведет к отмене). После выполнения данных действий произойдет выход в меню “Параметры” на индикацию параметра “ЗПр-ть” с помощью изменения значения которого можно задать необходимое управляющее воздействие. При необходимости возможна остановка процесса дозирования путем выполнения команды “РежимыУправлениеСтоп дозирования”.
В установке используется стандартный электродвигатель 4ААММТ50В4 мощностью 60 Вт и частотой вращения 1280 обмин (синхронная частота вращения 1500 обмин). За один оборот роликов насоса будет происходить дозирование 4 порций тонера. Что бы не происходило забивание перистальтической трубки в насосе примем количество порций дозируемых за одну минуту равным 140. Тогда количество оборотов ротора насоса будет равным:
Рассчитаем передаточное отношение редуктора.
Из таблицы 4.1. выберем тип редуктора наиболее подходящий для рассчитанного передаточного отношения
Рекомендуемые передаточные отношения редукторов
Согласно таблице наиболее подходит червячный одноступенчатый редуктор.
Выбираем стандартный червячный одноступенчатый редуктор РЧ-25 с передаточным отношением 36 климатического исполнения У2 по ГОСТ 15150. Параметры редуктора представлены в таблице 4.2.
Определим общий КПД привода.
где чр - КПД червячной передачи
п – КПД отдельных передач и подшипников;
m – кол-во пар подшипников.
Так как передаточное отношение редуктора 36 то при таких параметрах число заходов червяка будет равно 1. Согласно [4] принимаем
Согласно схемы привода m = 2
Мощность передаваемая на валы привода
где P1 – мощность передаваемая на вал 1 (входной) Вт;
P2 – мощность передаваемая на вал 2 (выходной) Вт;
Частота вращения валов привода
Угловые скорости вращения валов
Крутящие моменты на валах
3.1. Схема передачи.
Рис. 4.1 Червячная передача
3.2. Исходные данные передачи.
Обозначение величина ед. измерения
Номинальный вращающий момент на валу колеса
Частота вращения вала колеса
Частота вращения вала червяка
Предварительное значение КПД передачи
Машинное время работы передачи
Расположение червяка относительно колеса
3.3 Ориентировочная скорость скольжения
Скорость скольжения является одним из наиболее сильных факторов влияющих на работоспособность передачи и выбор материалов червячной пары. На данном этапе расчета скорость скольжения мс ввиду отсутствия размеров червяка и колеса находится ориентировочно по эмпирической зависимости:
где n1 — частота вращения вала червяка; Т23 — номинальный вращающий момент на валу колеса.
3.4 Выбор материала для колеса и червяка
Группа материалов для колеса выбирается по таблице 2.14 с.31 1: для соответствует группа материалов I. Из группы I выбираем для колеса марку материала БрО10Н1Ф1 с отливкой центробежной.
Для червяка выбираем марку стали 40ХН
Материалы червячной пары
отливка центробежная
3.5 Допускаемые напряжения
3.5.1 Контактные напряжения
Для колес изготовленных из материалов группы I:
где 09 для червяков с твердостью на поверхности витков 350HВ
3.5.2 Допускаемое напряжение на изгиб
где T и ВР – пределы текучести и прочности бронзы при растяжении; NFE – эквивалентное число циклов нагружения зубьев по изгибной выносливости.
Эквивалентное число циклов нагружения:
Расчет допускаемого напряжения на изгиб:
3.6 Число витков червяка Z1 и предварительное число зубьев колеса Z’2
Число витков червяка назначается в зависимости от передаточного числа передачи U’12: для U’12 = 36 Z1 = 1.
Предварительное число зубьев колеса:
3.7 Межосевое расстояние передачи
Предварительное значение межосевого расстояния:
где Т2 – вращающий момент на валу колеса Н×мм;
[H] – допускаемое контактное напряжение
По ГОСТ 6636-69 Принимаем а’ = 25 мм. Табл.24.1 1
3.8 Осевой модуль зацепления
Предварительное значение модуля зацепления:
Окончательное значение модуля устанавливается по стандарту (ГОСТ 2144-76) из таблицы 4.1 с.55 2: m = 1 мм.
3.9 Коэффициент диаметра червяка
Предварительно определяется по формуле:
Минимальное значение определяется по формуле:
Принимаем стандартное значения из таблицы 4.1 с.55 2: q = 14.
3.10 Коэффициент смещения
3.11 Окончательное значение передаточного числа и межосевого расстояния
Коэффициент смещения х удовлетворяет условию поэтому предварительное значение числа зубьев колеса Z’2 принимаем в качестве расчетного т.е. U12 = 36 и Z2 = 36.
Окончательное значение межосевого расстояния:
3.12 Проверочные расчеты передачи
3.12.1 По контактным напряжениям
Фактическое контактное напряжение в зацеплении:
где d2 – делительный диаметр колеса;
dw1 – начальный диаметр червяка;
Т23 – номинальный передаваемый колесом вращающий момент;
К – коэффициент перегрузки.
Делительный диаметр червяка и колеса:
Фактическое контактное напряжение:
3.12.2 По напряжениям изгиба
Сопротивление зубьев колеса усталостному излому проверяется по условию:
где Ft2 – окружная сила на колесе;
YF – коэффициент формы зуба выбирается по таблице с.39 1 в зависимости от числа зубьев эквивалентного колеса ZV.
Окружная сила на колесе:
Угол подъема линии червяка:
Число зубьев эквивалентного колеса:
КПД червячной передачи
где γ w – угол подъема линии витка червяка на начальном цилиндре;
р’ – приведенный угол трения в зацеплении выбирается из таблицы 11
стр. 24 2: для Vск = 145 мс и твердости венца червячного колеса HRC > 46 р’ = 2°.
3.13 Силы в зацеплении червячной пары
Усилие действующее в полюсе зацепления может быть разложено на три взаимно перпендикулярные составляющие (рисунок 4.2).
Рисунок 4.2 Силы в зацеплении
Окружная сила на колесе или осевая на червяке:
Радиальная сила на колесе и червяке:
Осевая сила на колесе и окружная на червяке:
Предварительные значения диаметров различных участков стальных валов редуктора определяют по формулам 1:
4.1.Для быстроходного (входного) вала-червяка:
–диаметр конца быстроходного вала определяют по приближенному расчету на прочность:
Согласовав диаметр входного конца вала с муфтой (dэд=9 мм) 2 принимаем dВ=8 мм
– ориентировочное значение диаметра буртика вала:
где t – высота буртика
h –высота шпонки h =2 мм
t1–глубина паза ступицы t1=1.3 мм значит t(2–1.3)+0.5 t12 принимаем t=15.
–диаметр вала под подшипники:
– ориентировочное значение диаметра буртика для упора подшипников:
где r–радиус скругления внутреннего кольца подшипника r=1
Червяк конструируем заодно с валом – вал-червяк.
4.2. Для тихоходного вала:
– диаметр конца тихоходного вала:
t1=25 мм значит t(4–25)+0.5 t2 принимаем t=2.
5.1. Для входного вала – подшипники роликовые конические радиальные однорядные средней серии. ГОСТ 27365-87. Обозначение 7202
d =15 мм D = 35 мм B = 1175 мм r = 10 мм Cr = 105 кН Cor = 61 кН.
5.2. Для выходного вала – Подшипники роликовые конические радиальные однорядные легкой серии. ГОСТ 27365-87. Обозначение 7204
d =20 мм D = 47 мм B = 1525 мм r = 10 мм Cr = 21 кН Cor =13 кН.
Рис 4.3. Эскиз подшипников.
На точность дозирования влияют следующие факторы: самосортирование продуктов при поступлении в бункера над дозаторами вызывающее изменение натуры; различная степень уплотнения продуктов в бункерах над дозаторами зависящая от высоты их заполнения и времени нахождения в бункерах; повышенная влажность продуктов способствующая их слёживанию и комкованию.
Также на точность дозирования влияет способ определения необходимого количества тонера для заданных программно значений (по весу по времени и т.д.)
Т.к. любые измерительные устройства имеют свои погрешности а дозаторы достаточно сложные приборы то неизбежно накапливание погрешности дозирования со всех его узлов. На практике погрешность будет возникать в основном при использовании выбранного нами типа дозаторов из за различных характеристик тонера в зависимости от поставки или даже в 1-й поставке (т.к. неоригинальный тонер производят заводы стремящиеся скопировать свойства оригинального и у них это не всегда получается хорошо т.к. тонер - многокомпонентный сложный мелкодисперсный порошок). При изменении состава будут изменяться и его физические характеристики т.е. допустим при отсечке порции по времени за одинаковый промежуток количество тонера может значительно отличаться даже в 1-й партии (т.к. условия хранения и перевозки редко соблюдаются на не крупных организациях занимающихся ресайклингом. А таких большинство)
Под производительностью Q будем понимать вес материала P на выходе из дозатора за определенный промежуток времени т.е.
В силу многих причин производительность постоянно изменяется. Если за бесконечно малый промежуток времени вес материала равен то за промежуток времени вес материала на выходе из дозатора будет равен:
Весовая производительность дозатора в единицу времени будет соответственно равна:
Непрерывное дозирование - случайный процесс Реализация процесса за определенные интервалы времени является функция:
Раскрыв интеграл получим необходимую формулу.
Относительная погрешность будет равна:
Необходимая точность достигнута
7 Расчет на надежность.
Все элементы рассчитываемого устройства делят на условные части с учетом функционального назначения. Наименование всех узлов и элементов записываются в графу 1 таблицы 1. Далее заполняем остальные графы приняв ; ; ; . - коэффициенты учитывающие число переключений механические воздействия и относительную влагоустойчивость. Коэффициент нагрузки определяется по формуле:
- номинальная нагрузка
Коэффициент при числе циклов равных 01.
Интенсивность отказов элементов в реальных условиях эксплуатации будет равна:
Все данные запишем в таблицу 1.
Интенсивности отказов элементов.
Наименование элемента
Интенсивность отказов всей системы
i = 1 m – количество типов групп элементов
Ni - количество элементов в i – ой группе.
Интенсивность отказов всей системы будет равна:
Среднее время безотказной работы механизма определяется формулой:
Вероятность безотказной работы системы в течении заданного времени рассчитывается по формуле:
Вероятность безотказной работы системы в течении 2000 часов:
8. Расчет шпоночных соединений.
Рисунок 4.1 Шпонки призматические ГОСТ 23360-78
Под муфту (хвостовик цилиндрический).
Под зубчатое колесо.
Проверка шпонок на смятие:
где Т – крутящий момент на валу Н×мм2;
d – диаметр участка вала под шпонку мм;
h – высота шпонки мм;
t1 – глубина паза вала мм;
b – ширина шпонки мм;
Хвостовик выходной:
Вывод: выбранные шпонки пригодны для использования.
9. Расчет подшипников скольжения.
Для вала ротора выбираем подшипники скольжения по ГОСТ 1978-81. Характеристики этих подшипников приведены в таблице 4.2.
Расчет подшипников скольжения производится по удельной нагрузке р в подшипнике и величине pv в некоторой мере характеризующей износ последнего и нагрев.
Составим расчетную схему для определения реакций в подшипниках (рис. 4.2).
Консольная сила от действия муфты
Рис. 4.5. Расчетная схема для определения реакций в подшипниках.
Дальнейший расчет производим для подшипника в наиболее нагруженной опоре А
Усилие в подшипнике равно:
Удельная нагрузка в подшипнике
Где d – внутренний диаметр подшипника
Окружная скорость на шейке вала
Допустимые значения и берем по таблице 1 [1т.2 с.33]
Для выбранных подшипников условия и выполнены.
Цикл работы прибора - 01сек.
Точность дозирования - 02% от максимальной производительности при правильной калибровке прибора.
Входы - выходы прибора:
-5 дискретных выходов типа “открытый коллектор” с гальванической изоляцией до 1000В. Питание нагрузки от внешнего источника напряжением до 60В. Максимальный ток 350мА.
-5 дискретных входов типа “сухой” контакт с гальванической изоляцией до 1000В. Питание входов от внутреннего источника напряжением 12В.
-управление исполнительным механизмом подачи продукта - аналоговый выход 020 mA. Индикация значений параметров и режимов производится 32-символьным жидкокристалли ческим русскоязычным индикатором (ЖКИ).
Светодиодная индикация режимов работы.
Коммуникационный порт - RS-485 с гальванической изоляцией до 1000В.
Питание прибора от сети 220В ±10% 50Гц.
Потребляемая мощность - 13Вт.
Диапазон рабочих температур - +5 .. +45 °С.
Контроллер предназначен для щитового монтажа габаритные размеры 96х96х175 мм установочные размеры 90х90 мм вес 07 кг.
Подключение внешних цепей осуществляется с помощью клеммника на задней панели. Схема подключения прибора приведена в приложении. Фирма-изготовитель оставляет за собой право внесения изменений в конструкцию и программу прибора улучшающие его технические характеристики без предварительного уведомления.
Контроллер может оказаться неработоспособным если монтаж системы выполнен без учета требований электромагнитной совместимости и правил заземлений.
Внешний вид лицевой панели прибора приведен ниже на рисунке 5.1.
Рис. 5.1. Лицевая панель.
Дисплей 32-символьный ЖКИ предназначен для индикации режимов работы и параметров контроллера. В зависимости от конкретного меню назначение строк дисплея различно. Примерный вид и назначение строк дисплея для меню “Параметры” приведены на рисунке 2. В верхней строке выводится название текущего режима и может выводиться дополнительная информация (например для режима дозирования – время дозирования). В нижней строке отображаются название параметра его численное значение и единицы измерения (если есть). Список доступных параметров.
Рис. 5.2 Вид дисплея для меню “Параметры”
Примерный вид и назначение строк дисплея для меню “Режимы” и для всех его подменю приведен на рисунке 3. В верхней строке отображаются заголовки меню и подменю. В нижней строке – “строка-подсказка” поясняющая реакцию прибора на нажатия клавиш расположенных под соответствующими надписями. В данном примере нажатие на клавишу «ввод» приведет к выбору подменю “УПРАВЛЕНИЕ” нажатие на клавишу «С» – переход на предыдущее подменю нажатие на клавишу «D» – переход на следующее подменю нажатие на клавишу «режим» – выход из меню “Режимы” и переход в меню «Параметры»
Рис. 5.3 Вид дисплея для меню “Режимы” Индикатор "Дозирование
Данный индикатор индицирует режим работы:
дозатор остановлен – нет свечения;
ручное дозирование – постоянное свечение;
автоматическое дозирование – мигание.
Клавиши на лицевой панели контроллера
«режим» - предназначена для перехода из меню “Параметры” в меню “Режимы” (и обратно) а также для выхода из подменю (в меню “Режимы”).
« С » - предназначена для смены параметров индикации (меню “Параметры”) а при установленном режиме изменения параметра позволяет изменить числовое значение текущего параметра в сторону уменьшения. В меню “Режимы” - для прокрутки (“скроллинга”) его подменю.
« D » - предназначена для смены параметров индикации (меню “Параметры”) а при установленном режиме изменения параметра позволяет изменить числовое значение текущего параметра в сторону увеличения. В меню “Режимы” - для прокрутки (“скроллинга”) его подменю.
«ввод» - предназначена для выбора подменю меню “Режимы” а также для перехода в режим изменения числового значения параметров индикации (меню “Параметры”). После изменения числового значения параметра и нажатия кнопки «ввод» происходит запись значения параметра в энергонезависимую память (EEPROM) и выход из режима изменения параметра.
При одновременном нажатии кнопок «D» и «ввод» происходит включение подсветки ЖКИ если она выключена или выключение если подсветка включена.
3. Описание меню прибора
На рисунке 5.4 приведена диаграмма показывающая реакцию на нажатие клавиш и соответствующие переходы по меню прибора.
В меню “Параметры” доступно для просмотра и (или) изменения 11 параметров. Чтобы установить режим изменения параметра необходимо выбрать редактируемый параметр и нажатием кнопки «ввод» перейти в режим редактирования параметра. О переходе в режим редактирования свидетельствует мигание курсора. Для изменения значения параметра необходимо пользоваться клавишами «С» и «D». Выйти из режима редактирования можно нажатием кнопки «ввод» до пропадания мигающего курсора.
Рис. 5.4 Диаграмма переходов по меню прибора
Меню “Режимы” имеет в своем составе четыре подменю с помощью которых можно задавать необходимые настройки просматривать текущее состояние дискретных входов и выходов а также давать команды контроллеру. На рисунке 5.5 приведена структура меню “Режимы” и соответствующие функции выполняемые с помощью подменю.
В различных режимах работы доступ к некоторым меню может быть запрещен что будет сопровождаться соответствующим технологическим сообщением. В режиме автоматического дозирования запрещены переходы в меню “Пуск дозирования” “Продувка” “Ручной режим” “Сброс расхода” “Калибровка”.
Рис 5.5 Структура меню “Режимы”
Контроллер «Master - 210.4» поддерживает семь режимов работы и настроечный режим:
– дозирование ручное;
– дозирование автоматическое с заданием времени дозирования и веса порции (дискретное дозирование);
– дозирование автоматическое с заданием производительности (объемное непрерывное дозирование);
– продувка системы дозирования;
– сброс текущего расхода;
– сброс текущей порции;
– остановка дозирования.
– калибровка максимальной производительности.
Активация меню режимов работы производится кнопкой «режим». Выбор конкретного режима производится кнопками «С» и «D». Запуск выбранного режима на исполнение производится кнопкой «ввод».
Настройку параметров контроллера можно разделить на несколько этапов которые перечислены ниже в рекомендуемом порядке их выполнения:
выбор положения десятичной точки;
задание номера прибора;
настройка опций дозирования;
калибровка максимальной производительности;
настройка параметров дозирования (порция время плотность заданная производительность задержка).
Максимальная производительность настраивается с помощью режима “Калибровка”. Остальные параметры настраиваются вручную с клавиатуры контроллера.
Подключение прибора нужно выполнять в соответствии со следующими рекомендациями и схемами:
Питание прибора осуществляется от источника не связанного непосредственно с питанием мощного силового оборудования. Во внешней цепи следует установить выключатель питания и предохранители на ток 1 А.
Питание каких-либо других устройств от сетевых контактов прибора запрещается.
Кабели для соединения прибора с внешними устройствами должны быть медными многожильными сечением не более 1 мм2 и снабжены наконечниками для подсоединения к прибору.
6.1 Подключение входов
Частотный вход F=020 кГц Потенциал входов Uq+17 В. Iвх6 mA.
Рис. 5.6 Схема подключения входов
6.2 Подключение дискретных выходов
Рис. 5.7 Схема подключения дискретных выходов
Uпит≤+60 В Iнагр≤300 mA
При использовании шести реле НН54Р потребляемый максимальный ток300 mA. Рекомендуемые диоды типа 1N4007 или 1N5399.
6.3 Подключение аналоговых выходов
Рис. 5.8 Схема подключения аналоговых выходов
При использовании токового выхода 4-20 mA выход напряжения не работает.
6.4 Подключение интерфейса RS-485
Рис. 5.9 Схема подключения интерфейса RS-485
Кабель связи с конвертером-«витая пара».На конец кабеля связи подключается нагрузка 220 .
6.5 Подключение питания прибора
Рис. 5.10 Схема подключения питания прибора
Потребляемая мощность 13 Вт.
При прокладке кабели располагают отдельно от силовых кабелей а также кабелей создающих высокочастотные и импульсные помехи.
Подключение тензодатчиков производится экранированным кабелем. Длина линии не более 100 м.
Приборы нельзя монтировать в одном щите с оборудованием создающим высокочастотные или импульсные помехи (пускатели частотные преобразователи и т.д.)
Размер окна в щите 91*91 мм. глубина щита: для Master 110.х - 100 мм. для Master -210.х — 200 мм. Расстояние до соседнего прибора не менее 20 мм.
Технология изготовления вала насоса.
Вал – это элемент машин и механизмов назначение которого заключается в передаче крутящего момента между отдельными деталями и узлами машины посредством шпоночного либо шлицевого соединения его с деталью на которую передается вращение в некоторых случаях применяется соединение с натягом.
В данном случае вал передает крутящий момент посредством шпоночного соединения.
Для облегчения монтажа деталей расположенных на валу последний выполняют ступенчатой формы. В данном случае вал конструктивно представляет собой объект цилиндрической формы длиной 95 мм со ступенчатыми переходами: первый - с 20 мм на 22 мм второй – с 22 мм на 24 мм третий - с 24 мм на 28 мм четвертый - с 28 мм на 24 мм пятый - с 24 мм на 22 мм.
Поверхности 20 мм поверхность 22 мм поверхность 24 мм имеют шероховатость . Поверхность шпоночного паза имеет шероховатость . Все остальные поверхности имеют шероховатость .
На валу имеются шесть канавок предназначенные для выхода инструмента при обработке. На торце ступени 20 мм соосно оси ступени просверлено отверстие 12 мм на глубину 15 мм.
Вал изготовлен из стали 45 ГОСТ 1050-88 заготовка выполнена из круглого сортового проката.
1.1. Характеристика материала детали
Сталь является наиболее универсальным и широко используемым в машиностроении материалом. Достоинством сталей является возможность получения нужного комплекса свойств путем изменения их состава и термической обработки.
Вал выполнен из стали марки 45 ГОСТ 1050-88 отличающейся повышенной прочностью и средней вязкостью и применяемой для изготовления подвесок шатунов шестерен осей и валов.
Сталь – это сплав железа с углеродом и неизбежными примесями марганца кремния серы фосфора и других элементов. Обычные сорта стали применяемые в машиностроении содержат от 005 до 15% углерода. Основная характеристика стали определяющая его марку - это механические качества предел выносливости при изгибе предел выносливости при растяжении и при кручении предел текучести временное сопротивление.
Примерный химический состав Стали 45 следующий:
Рассмотрим влияние химического состава на физико-механические свойства легированной конструкционной стали.
Механические свойства зависят главным образом от содержания углерода. Углерод является вторым основным элементом определяющим как структуру так и свойства стали ее прочность и поведение при эксплуатации и в производстве. С увеличением содержания углерода в стали увеличивается количество цементита и соответственно уменьшается количество феррита т.е. увеличиваются прочность и твердость и уменьшается пластичность. Прочность повышается только до 1% С а при более высоком содержании углерода она начинает уменьшаться.
Кремний способствует выделению углерода в соответствии со стабильной системой железо—графит; незначительно изменяет характер превращений по сравнению с превращениями в соответствующих марках углеродистой стали; несколько повышает устойчивость аустенита в перлитной и особенно в средней области; понижает чувствительность к закалке и повышает устойчивость против отпуска; кремнистая сталь отличается особым видом устойчивости против отпуска; повышает сопротивление износу что ухудшает обрабатываемость конструкционной стали особенно при сверлении; стабилизирует аустенит; повышает упругость стали. Практически не растворяется в цементите.
Марганец. Каждый процент марганца понижает концентрацию углерода в перлите на 005—006%. Марганец повышает устойчивость аустенита в перлитной и в промежуточной областях; увеличивает степень его переохлаждения; увеличивает межпластинчатое расстояние в перлите; понижает температуру мартенситного превращения; увеличивает прокаливаемость стали за счет снижения критической скорости закалки; стабилизирует аустенит; повышает механические свойства стали особенно упругие свойства; обладает незначительной склонностью к обезуглероживанию. В отличие от других элементов марганец способствует сильному росту зерна аустенита при перегреве стали.
Марганец и кремний вводят в процессе выплавки в сталь для ее раскисления т. е. для удаления закиси железа поэтому их называют технологическими примесями. Кроме того марганец способствует уменьшению содержания сульфида железа FeS в стали. Марганец и кремний растворяются в феррите повышая его прочность; марганец может также растворяться и в цементите.
Сера - вредная примесь попадающая в сталь главным образом с исходным сырьем - чугуном. Сера нерастворима в железе она образует с ним соединение FeS-сульфид железа. При взаимодействии с железом образуется эвтектика (Fe + FeS) с температурой плавления 988°С. Поэтому при нагреве стальных заготовок для пластической деформации выше 900°С сталь становится хрупкой. При горячей пластической деформации заготовки разрушаются. Это явление называется красноломкостью. Одним из способов уменьшения влияния серы является введение марганца. Соединение MnS плавится при 1620°С эти включения пластичны и не вызывают красноломкости.
Содержание серы в сталях допускается не более 006%.
Фосфор попадает в сталь главным образом также с исходным чугуном использованным для выплавки стали. До 12% фосфора растворяется в феррите уменьшая его пластичность. Фосфор обладает большой склонностью к ликвации поэтому даже при незначительном среднем количестве фосфора в отливке всегда могут образовываться участки богатые фосфором. Располагаясь вблизи границ зерен фосфор повышает температуру перехода в хрупкое состояние т. е. вызывает хладноломкость. Поэтому фосфор как и сера является вредной примесью содержание его в углеродистой стали допускается до 0050%.
Чем больше углерода в стали тем сильнее влияние фосфора на ее хрупкость.
Содержание серы и фосфора в стали зависит от способа ее выплавки.
Хром повышает температуру перлитного эвтектоидного превращения; перлитное превращение независимо от явлений перегрева и переохлаждения протекает в некотором интервале температур. Хромистая сталь характеризуется повышенной устойчивостью при отпуске что вообще характерно для стали легированной карбидообразующими элементами; уменьшает скорость коагуляции содержащего хром цементита и специальных хромистых карбидов. Хром относительно слабо воздействует на механические свойства в отожженном состоянии; стабилизирует аустенит; повышает прокаливаемость; способствует получению высокой и равномерной твердости износостойкой поверхности. При высоком содержании хрома (13% и выше) сильно увеличивается сопротивление стали коррозии и окислению. Основным недостатком является склонность к отпускной хрупкости. Никель понижает температуру мартенситного превращения; за счет снижения критической скорости закалки увеличивает прокаливаемость что и определяет применение никелевой машиностроительной стали для массивных деталей; никелевая сталь значительно менее чувствительна к перегреву чем марганцовистая; в отожженном состоянии никель незначительно повышает прочность наиболее сильно и надежно уменьшает склонность к хрупкому разрушению закаленной и отпущенной стали увеличивает дисперсность карбидов но способствует развитию процесса их роста и коагуляции; стабилизирует аустенит; способствует сохранению вязкости при температурах ниже 0°С (до 150— 80°С) и плавному распределению углерода в цементованном слое. Повышает сопротивление стали окислению при нагреве и ее прочность при высоких температурах (особенно при наличии аустенитной структуры). После термической обработки имеет тонкую структуру позволяющую получить при повышенной прочности высокие свойства пластичности и вязкости.
1.2. Механические свойства стали 45
Относительное удлинение
Относительное сужение
1.3. Технологические свойства
Свариваемость является сложной комплексной характеристикой стали под которой следует понимать способность материала образовывать при рациональном технологическом процессе сварки прочное соединение без существенного снижения свойств в эксплуатационных условиях.
Сталь по свариваемости условно можно разделить на четыре группы: свариваемая без ограничений; ограниченно свариваемая; трудно свариваемая; не применяемая для изготовления сварных конструкций.
Сталь 1-й группы сваривают без подогрева и последующей термической обработки. Сварку толстостенных изделий ответственных конструкций рекомендуется вести с подогревом и подвергать их после сварки термической обработке.
При сварке стали 2-й группы следует применять предварительный и сопутствующий подогревы промежуточную и последующую термическую обработку назначаемые в зависимости от толщины свариваемых элементов жесткости конструкции химического состава стали и требований предъявляемых к сварным соединениям.
При сварке стали 3-й группы для получения качественных соединений применяют специальные технологические приемы (подогрев проковку промежуточную термическую обработку и т. д.). При ручной или автоматической дуговой сварке подогрев применяют для углеродистой стали с содержанием углерода выше 025%. а для легированной при эквивалентном содержании углерода (Сэ) — более 05.
Сталь 45 – ограниченно свариваемая.
Обрабатываемость резанием в отожженном состоянии составляет 70% обрабатываемости холоднотянутой автоматной стали марки А12.
Практически не подвержена отпускной хрупкости.
Температура начала ковки 1200–1250°С. Температура конца ковки 800–850°С. Охлаждение после ковки на воздухе.
1.4. Термическая обработка
На требуемую твердость
Теплая вода или масло
В машиностроении в зависимости от производственной программы выпуска изделий и характера изготовляемой продукции различают три основных типа производства: единичное серийное и массовое.
Единичное производство характеризуется широтой номенклатуры изготовляемых или ремонтируемых изделий и малым объемом их выпуска. Объем выпуска — количество изделий определенных наименований типоразмера и исполнения изготовленных или ремонтируемых объединением предприятием или его подразделением в течение планируемого интервала времени.
В машиностроении на предприятиях единичного производства количество выпускаемых изделий и размеры операционных партий заготовок исчисляются штуками и десятками штук; на рабочих местах выполняются разнообразные технологические операции повторяющиеся нерегулярно или не повторяющиеся вообще; используется универсальное точное оборудование которое расставляется в цехах по технологическим группам (токарный фрезерный зубонарезной сверлильный и т. д. участок); специальные приспособления и инструменты как правило не применяются (они создаются только в случае невозможности выполнения операций без специальной технологической оснастки); исходные заготовки — простейшие (прокат литье в землю поковки) с малой точностью и большими припусками; требуемая точность достигается методом пробных ходов и промеров с использованием разметки; взаимозаменяемость деталей и узлов во многих случаях отсутствует широко применяется пригонка по месту; квалификация рабочих очень высокая так как от нее в значительной мере зависит качество продукции; технологическая документация сокращенная и упрощенная; технические нормы отсутствуют; применяется опытностатистическое нормирование труда.
Единичное производство характеризуется широким ассортиментом продукции и малым объемом выпуска одинаковых изделий зачастую не повторяющихся. Особенности этого типа производства заключаются в том что рабочие места не имеют глубокой специализации применяются универсальное оборудование и технологическая оснастка большая часть рабочих имеет высокую квалификацию значительный объем ручных сборочных и доводочных операций здесь высокая трудоемкость изделий и длительный производственный цикл их изготовления значительный объем незавершенного производства.
Разнообразная номенклатура делает единичное производство более мобильным и приспособленным к условиям колебания спроса на готовую продукцию.
Выбор заготовки для дальнейшей механической обработки во многих случаях является одним из весьма важных вопросов проектирования процесса изготовления детали. От правильности выбора заготовки ее формы размеров припусков на обработку точности размеров (допусков) и твердости материала зависящих от способа изготовления заготовки обычно весьма сильно зависит число операций или переходов трудоемкость и в итоге стоимость процесса обработки и изготовления детали в целом. Вид заготовки в большинстве случаев предопределяет в значительной степени дальнейший процесс обработки детали. Если заготовка будет достаточно точно и хорошо изготовлена с припусками не более чем это необходимо для обработки то механическая обработка детали может быть сведена к минимальному числу операций минимальной трудоемкости и стоимости но при этом процесс изготовления заготовки естественно усложняется и удорожается. Грубое и не точное изготовление заготовки с излишне большими припусками удлиняет и удорожает процесс обработки детали хотя в некоторых случаях упрощает и удешевляет процесс изготовления заготовки.
Таким образом при разработке процесса изготовления деталей могут быть два принципиальных направления:
а) получение заготовки наиболее приближающейся по форме и размерам к готовой детали когда на заготовительные цеха приходится как бы значительная доля трудоемкости изготовления детали и относительно меньшая доля приходится на механические цехи;
б) получение грубой заготовки с большими припусками.
В зависимости от типа производства будет более правильным то или иное из указанных направлений или какой-либо промежуточное между ними. Первое направление соответствует как правило массовому производству т.к. дорогостоящие современное оборудование заготовительных цехов экономически оправдывается лишь при больших масштабах производства. Второе направление типично для единичного или мелкосерийного производства когда применение дорогого оборудования в заготовительных цехах неэкономично.
Учитывая все вышеизложенные а также материал детали делаем вывод что наиболее целесообразным будет использование заготовки в виде проката сортового круглого сечения изготовленного из стали 45 ГОСТ 1050-88.
Определяем коэффициент использования материала:
где mд = 4407 г – масса детали;
mз – масса заготовки определяемая по формуле:
ρ – плотность стали: ρ = 785 гсм3;
Vз – объем заготовки:
Большую роль в точности изготовления заготовок играет их базирование на станке. Если не соблюдаются некоторые условия то возникают погрешности базирования понижающие точность обработки заготовки.
Базирование – это придание заготовкам на станке определенного положения (ориентация заготовок) относительно их рабочих органов или относительно выбранной системы координат.
Рабочий орган – это патрон для токарного станка стол для фрезерного станка приспособления суппорт с резцами шпиндель со сверлами и т.д.
В процессе базирования используются поверхности линии точки заготовки или их совокупность которые называются базами.
База – это поверхность линия или точка принадлежащая заготовке относительно которой обрабатываются другие поверхности линии или точки.
По назначению базы бывают:
- конструкторские: основные и вспомогательные;
Конструкторской называется поверхность линия или точка относительно которой формируются другие поверхности заготовки в процессе проектирования.
Основной конструкторской называется поверхность линия или точка которая определяет рабочее положение детали в узле или механизме.
Вспомогательной конструкторской называется поверхность линия или точка которая определяет положение присоединяемых к детали других деталей.
Технологическая база – это поверхность линия или точка которой заготовка устанавливается при обработке.
Измерительная база – это поверхность линия или точка относительно которой происходит отсчет размеров.
Схемы базирования зависят от формы поверхностей обрабатываемых заготовок.
Погрешность базирования не возникнет если будут соблюдаться следующие принципы базирования: принцип постоянства баз принцип совмещения баз принцип единства баз.
Принцип постоянства баз состоит в том что для выполнения всех или большинства операций технологического процесса механической обработки используют одни и те же технологические базы. Желательно использовать этот принцип на всех операциях но особенно это важно при окончательных операциях.
Принцип совмещения баз состоит в том что для выполнения технологического процесса механической обработки одной или нескольких поверхностей в качестве измерительной базы используют технологическую.
Принцип единства баз состоит в том что для выполнения технологического процесса механической обработки одной или нескольких поверхностей в качестве технологической и измерительной баз используют комплект конструкторских баз.
Измерительной и конструкторской базами является правый торец заготовки технологической - наружная поверхность 30 мм (заготовка устанавливается на ножовочное полотно).
5. Токарно – винторезная
Правый торец заготовки является измерительной базой конструкторской базой является ось заготовки технологической базой – поверхность 22 (заготовка устанавливается в 3-х кулачковый патрон).
Конструкторской базой – ось вращения заготовки. Технологической - левый торец и наружная поверхность заготовки.
Измерительная база – правый торец заготовки. Технологической базой является левый торец и наружная поверхность 20. Конструкторская база – ось заготовки
Измерительная база – правый торец заготовки. Технологической базой является левый торец и наружные поверхности. Конструкторская база – ось заготовки
Измерительная база – ось вращения заготовки. Конструкторская база – ось вращения заготовки. Технологическая база – центровочные отверстия.
5.1. Исходные данные
Тип станка – токарно-винторезный 16К20
Вид обработки – получистовое точение вала диаметром мм до на длине мм.
Общая длина вала L=95±05 мм.
Тип заготовки – прокат круглый ГОСТ 2590-71
Материал заготовки – сталь 45 ГОСТ 1050-88 с
Способ крепления заготовки – в трёхкулачковом патроне
Шероховатость обработанной поверхности
Выбор резца и его геометрические параметры.
Принимаем токарный упорный проходной резец прямой правый из быстрорежущей стали Т15К6.
Сечение державки h × b = 16 × 25 мм
Длина резца L = 120 мм
Обозначение: резец 2101-0567 ГОСТ 18870-73
Геометрические параметры:
Форма передней грани – криволинейная с фаской
Величина переднего угла фаски γ2= 0°
Ширина фаски f = 06 мм
Радиус выемки R = 6 мм
Выбор режима резания.
Рассмотрим участок вала диаметром 20 мм и длиной 39 мм.
Припуск на обработку удаляем за один проход т.е. глубина резания равна припуску на сторону:
Подача назначается как доля от глубины резания:
S = (015 025) t – при черновой обработке
S = (0.05 0.15) t – при чистовой обработке
S = 0.15 5 = 075 ммоб
Полученная подача корректируется по паспортным данным станка.
Принимаем S = 18 ммоб.
Период стойкости резца.
Из справочных данных имеем Т =60 мин.
Допустимый износ резца по задней поверхности hз = 1 14 мм.
Cv = 350 – эмпирический коэф.
x=0.15 – эмпирический коэф.
y=035 – эмпирический коэф.
m=02 – эмпирический коэф.
– коэф. учитывающий влияние материала заготовки инструмента и состояние поверхности.
Knv=0.9 – коэф. учитывающий состояние поверхности заготовки
Kuv =1.0 – коэф. учитывающий влияние материала инструмента
Кv = 1.28 0.9 1.0 = 1.152
Частота вращения шпинделя станка.
D = 30 мм – диаметр обрабатываемой поверхности
В соответствии с паспортными данными станка 16К20 принимаем частоту вращения nр = 1250 обмин.
Основное (машинное) время обработки.
L = l + y + Δ – путь инструмента в направлении рабочей подачи
i = 1 – количество проходов
y = 0 – величина врезания (при величине главного угла в плане φ0 = 90°)
Δ = 1 2 мм – величина перебега
l = 39 мм – длина обрабатываемой поверхности
S = 04 ммоб – подача
n = 1250 обмин – частота вращения шпинделя
мин что составляет примерно 5 с.
Рассмотрим участок вала диаметром 28 мм и длиной 42 мм.
S = 0.15 1 = 015 ммоб
В соответствии с паспортными данными станка 16К20 принимаем частоту вращения nр = 1600 обмин.
Рассмотрим участок вала диаметром 22 мм и длиной 11 мм.
S = 0.15 4 = 06 ммоб
мин что составляет примерно 12 с.
Под техническим нормированием понимается установление нормы времени на выполнение определенной работы или нормы выработки в штуках в единицу времени.
Правильное нормирование затраты рабочего времени на обработку деталей сборку и изготовление всей машины имеет весьма большое значение для производства. Величина затраты времени на изготовление той или иной продукции при надлежащем качестве ее является одним из основных критериев для оценки совершенства технологического процесса.
Норму времени определяют на основе технического расчета и анализа исходя из условий возможно более полного использования технических возможностей оборудования и инструмента в соответствии с требованиями к обработке данной детали или сборке изделия.
В машиностроительном производстве при обработке деталей на металлорежущих станках определяется норма времени на отдельные операции (комплекс операций) или норма выработки деталей (изделий) в штуках в единицу времени (час смену).
Итак под технической нормой времени понимают время (в минутах или долях минуты) устанавливаемое на выполнение данной операции при определенных организационно-технических условиях и наиболее эффективном использовании всех средств производства с учетом передового производственного опыта.
Техническая норма времени определяющая затрату времени на обработку (сборку или другие работы) служит основой для оплаты работы калькуляции себестоимости детали и изделия. На основе технических норм рассчитываются длительность производственного цикла необходимое количество станков инструментов и рабочих определяется производственная мощность цехов (или отдельных участков) производится все планирование производства.
При выборе оптимальных вариантов технологических процессов обработки деталей или сборки изделий наряду с другими технико-экономическими показателями пользуются нормой времени для оценки технологического процесса.
При установлении нормы времени необходимо обеспечить следующие условия:
) работа должна выполняться рабочим соответствующей квалификации;
) должны быть применены наиболее эффективные для данной работы приспособления и инструменты;
) должны быть установлены оптимальные режимы резания исходя из возможности рационального применения одновременной обработки нескольких деталей одновременной работы несколькими инструментами и в тех случаях где это возможно одновременного обслуживания одним рабочим нескольких станков;
) припуски на обработку должны быть оптимальными сорт и качество материала — нормальными для данного завода; станок должен быть исправным а качество инструмента нормальным;
) в норму времени не должны быть включены те ручные приемы которые могут быть выполнены одновременно с работой станка т. е. перекрыты машинным временем;
) в норму времени не должно включаться время на исправление забракованных деталей или на изготовление взамен их новых;
) организация рабочего места должна предусматривать заблаговременную доставку к нему чертежей и нарядов на работу материалов инструментов приспособлений а также сдачу их по окончании работы вспомогательными рабочими;
) заточка инструмента должна быть централизованной т. е. инструмент должен затачиваться в заточном отделении цеха специальными рабочими — заточниками. Инструмент заменяется через установленные промежутки времени (принудительная смена инструмента) или по требованию станочника. Каждое рабочее место должно быть обеспечено дополнительным комплектом инструмента. Заточенный инструмент подается к рабочему месту в готовом виде;
) в норму времени не должны входить потери времени из-за каких-либо организационных неполадок; к числу этих неполадок относятся: перерыв в подаче электроэнергии задержка в доставке материала приспособлений инструмента задержка транспортных средств наряда на работу или сдачи работы неисправность электродвигателя и т. д.; следовательно должно быть предусмотрено непрерывное и своевременное обслуживание рабочего места всем необходимым для выполнения бесперебойной работы;
) норма времени должна устанавливаться в расчете на нормальные условия работы и какие-либо потери времени связанные с отклонениями от нормальных условий как зависящие от рабочего так и не зависящие от него не входят в норму.
Техническая норма времени – время необходимое для выполнения операций или определенного вида работ при нормальной интенсивности с применением передовых средств и приемов труда.
Технологичность конструкции – это свойство конструкции проявляемое в наименьших затратах труда средств и материалов по сравнению с базовыми вариантами на всех этапах: проектирование изготовление сборка монтаж ремонт эксплуатация.
Рациональные конструкции деталей обеспечивающие необходимые эксплуатационные требования не могут быть созданы без учета трудоемкости и материалоемкости их изготовления. Соответствие конструкции детали требованиям минимальной трудоемкости и материалоемкости определяет технологичность конструкции.
На стадии проектирования рассматриваются следующие аспекты технологичности:
- безопасность жизнедеятельности человека.
Рассмотрим технологические аспекты. Их соблюдение отмечаем знаком «+» несоблюдение «-». В конце определим относительную технологичность детали в целом.
) сокращать протяженность механически обрабатываемых поверхностей до конструктивно необходимого минимума «+»
Т. е. если возможно шероховатость неответственных поверхностей не понижается.
) уменьшать количество металла снимаемого при обработке «+»
Т. е. припуски на механическую обработку назначаются как можно меньшими но в то же время достаточными для получения требуемых шероховатостей поверхностей.
) предусматривать изготовление детали или ее отдельных поверхностей наиболее производительными методами (чеканкой штамповкой) «+»
Заготовка – прокат более приближена к форме и размерам готовой детали.
) шире применять сортовой и профильный прокат с сохранением наибольшего числа черных поверхностей «+»
) предусматривать изготовление детали из заготовок с формой близкой к форме детали «+»
Форма проката наиболее приближена к форме детали.
) избегать излишней точности механической обработки «+»
) применять в каждом отдельном случае наиболее грубую точность обеспечивающую правильную работу узла и удовлетворяющую условию взаимозаменямости «+»
) обеспечить возможность применения наиболее производительных способов механической обработки «+»
) предусматривать возможность обработки напроход являющуюся главным условием повышения производительности получения более высокой точности «+-»
Т. е. не все поверхности возможно обрабатывать напроход.
) при невозможности обработки напроход обеспечить выход инструмента (канавки) на расстоянии достаточном для получения точных поверхностей «+»
) обеспечить удобный подход к обрабатываемой поверхности «+»
) предусматривать возможность обработки максимального числа поверхностей на одной операции на одном станке с одного установа одним и тем же инструментом (принцип концентрации операций) «+»
) обеспечить возможность обработки точных соосных и параллельных отверстий с одного установа облегчающую получение точных межосевых расстояний «+»
) предусматривать четкое разделение поверхностей обрабатываемых различным инструментом и с различной точностью «+»
) избегать совместной обработки деталей в сборе нарушающей непрерывность производственного цикла и затрудняющей смену детали в эксплуатации «+»
) сокращать номенклатуру обрабатывающего инструмента путем унификации размеров и формы поверхностей «+»
) в единичном и мелкосерийном производстве сводить к минимуму применение специального режущего инструмента «+»
) придавать обрабатываемым участкам поверхности высокую и равномерную жесткость «+»
Те поверхности при удалении припусков с которых снижается жесткость заготовки (отверстия) обрабатывают в последнюю очередь.
) предусматривать удобные измерительные базы для контроля размеров с применением универсального измерительного инструмента «+»
) сокращать машинное время за счет увеличения скорости резания подачи и глубины резания «+»
Т. е. глубину резания подачу и скорость резания назначают предельно возможными.
) сокращать вспомогательное время за счет применения быстродействующих приспособлений для установки закрепления и снятия заготовки «+»
Т. е. применяют стандартные приспособления (патроны электромагнитную плиту) которые способствуют быстрой установке закреплению и снятию заготовки. Проектируют же такие приспособления которые по возможности будут максимально быстродействующими и удобными в эксплуатации.
Качественная оценка технологичности (путем рассмотрения процентного отношения технологичности к нетехнологичности) показывает что технологичность изготовления вала – 82% – достаточно высокая.
Исходная деталь – ступенчатый вал-шестерня.
Материал Сталь 45 ГОСТ 1050-88
Заготовка – прокат горячекатаный
Производство – среднесерийное
0 – Операция заготовительная
Отрезание заготовки нужной длины
Оборудование – круглокопировальный автомат 8Г642
Режущий инструмент – резец отрезной
0 – Операция: токарно-подрезная
Черновая чистовая обработка наружных цилиндрических поверхностей с припуском под шлифовку подрезание торцов фасок.
Оборудование: Станок токарно-винторезный 16К20Ф3
Оснастка: Трехкулачковый самоцентрирующийся патрон 7100-0009 ГОСТ 2675-80
Центр вращающийся А-1-4-НП ЧПУ ГОСТ 8742-75
Резец проходной с механическим креплением пластины из твердого сплава правый 2103-0713 ГОСТ 20872-80
Резец проходной с механическим креплением пластины из твердого сплава левый 2103-0714 ГОСТ 20872-80
Резец проходной φ = 45 с механическим креплением пластины из твердого сплава правый 2102-0191 ГОСТ 21151-75
Резец проходной φ = 45 с механическим креплением пластины из твердого сплава левый 2102-0192 ГОСТ 21151-75
Резец токарный для проточки угловых канавок с механическим креплением пластины из твердого сплава правый К.01.4528.000
Резец токарный для проточки угловых канавок с механическим креплением пластины из твердого сплава левый К.01.4528.000-01
Измерительный инструмент: штангенциркуль ШЦ-2-160-005 ГОСТ 166-90
Точить диаметр 20 мм на длине 39 мм с припуском под шлифовку 02 мм.
Точить диаметр 22 мм на длине 11 мм с припуском под шлифовку 02 мм.
Точить диаметр 24 мм на длине 5 мм с припуском под шлифовку 02 мм.
Точить диаметр 28 мм на длине 21 мм.
Нарезание фаски 10х45
Нарезание фаски 05х45
Выполнить проточку длиной 3 мм на глубину 1 мм
Точить диаметр 22 мм на длине 13 мм с припуском под шлифовку 02 мм.
0 – Операция: сверлильная
Сверление отверстия диаметром 12 мм на глубину 15 мм.
Сверло диаметром 12 мм с коническим хвостовиком. ОСТ 2 И41-14
произвести сверление глухого отверстия диаметром 12 мм на глубину 15 мм. Размер отверстия обеспечивается размером интсрумента.
Операция 040 – шпоночно-фрезерная
Нарезание шпоночного паза под призматическую шпонку по ГОСТ 23360-78
Оборудование: Станок консольный вертикально-фрезерный ВМ-127М
Оснастка: Головка делительная УДГ-Д250
Фреза шпоночная по ГОСТ 9140—68 диаметр 4 мм
Измерительный инструмент: штангенциркуль ШЦ-2-160-005 ГОСТ 166-90 микрометр.
Выполнить нарезание шпоночного паза глубиной 55 мм и длиной 34 мм.
Операция 050 – Шлифование диаметров 22к6 24к6 с подшлифовкой торца Ra08.
Оборудование: круглошлифовальный станок модели 3151.
Инструмент: круг шлифовальный.
Операция 060 – Моечная
Оборудование: машина моечная.
Операция 070 - Контрольная
Оборудование: стол ОТК.
Контроль размеров вала на всех этапах изготовления производится следующими приборами.
Наружные диаметральные размеры 20 и 24 мм измеряются штангенциркулем ШЦ-2-160-005 ГОСТ 166-90 (рис. 2.1).
Внутренние диаметральные размеры 12 мм измеряются стандартным трехточечным метрическим нутромером (рис. 2.2)
Контроль глубины отверстия 15 мм осуществляется стандартными глубиномерами (рис. 2.3).
Измерение наружных линейных размеров осуществляется механическим вертикальным длинномером
Контроль цилиндрических поверхностей на наличие биений осуществляется при помощи индикаторов часового типа.
Диаметры подшипниковых шеек 22 мм измеряются более точными инструментами – микрометрами.
В ходе выполнения дипломного проекта была разработана конструкция дозатора для тонера основным дозирующим механизмом которого является перистальтический насос.
Была получена зависимость производительности насоса от внутреннего диаметра трубки диаметра роликов и ротора насоса.
Рассмотрены два метода дозирования – по времени и по массе. И в соответствии с этими методами описаны конструктивные особенности дозатора.
Анурьев В.И. Справочник конструктора-машиностроителя: т. 1- 5- е изд. перераб. и доп. - М.: Машиностроение 1980.
Решетов Д.Н. Детали машин: Учебник для студентов машиностроительных и механических специальностей вузов М.: Машиностроение - 4- е изд. перераб. и доп 1989. - 496 е.: ил.
Курсовое проектирование деталей машин: Учебное пособие. Чернавский С.А. и др. М.: Машиностроение 1979.
3D.cdw

вал ротора.cdw

дозатор.cdw

редуктора и электродвигателя - 0
Осевое смещение валов не более редуктора и вала насоса - 0.5 мм
редуктора и электродвигателя - 1 мм
Перекос валов не более редуктора и вала насоса - 1 мм
насос перистальтический
болт М8х50 ГОСТ 7805-70
гайка М8 ГОСТ 5915-70
болт М8х40 ГОСТ 7805-70
болт М5х40 ГОСТ 7805-70
гайка М5 ГОСТ 5915-70
винт М5х15 ГОСТ 17475-80
винт М5х6 ГОСТ 50383-92
муфта втулочная ГОСТ 24246-80
электродвигатель 4ААМТ50В4
Технические характеристики
Мощность эелектродвигателя 60 Вт
Частота вращения входного вала 1280 обмин
Частота вращения выходного вала 35
Крутящий момент на выходном валу 11
Технические требования
корпус.cdw

* Размер обеспеч. инстр.
Общие допуски по ГОСТ 30893.1- m.
крестовина.cdw

крышка корпуса.cdw

* Размер обеспеч. инстр.
Общие допуски по ГОСТ 30893.1- m.
насос.cdw

Перед окончательной сборкой болты больших крышек
установить на герметик УТ-34 ГОСТ 24285-80.
Операционные карты1.cdw

Ролик.cdw

* Размер обеспеч. инстр.
Общие допуски по ГОСТ 30893.1- m.
Спецификация насос.spw

Спецификация.spw

Насос перистальтический
Болт М8х50 ГОСТ 7805-70
Болт М8х40 ГОСТ 7805-70
Болт М5х40 ГОСТ 7805-70
Винт М5х15 ГОСТ 17475-80
Гайка М8 ГОСТ 5915-70
Гайка М5 ГОСТ 5915-70
Винт М5х6 ГОСТ 50383-92
Муфта втулочная ГОСТ 24246-80
Электродвигатель 4ААМТ50В4
технологический маршрут.cdw

Установить и закрепить заготовку в патроне
Подрезать торец в размер 2*
Центровать в размер 1
Установить и закрепить заготовку в патроне и
Выполнить проточку 7
Выполнить проточку 8
Выполнить проточку 5
Сверления отверстия 1
Нарезать шпоночный паз под призматическую
шпонку ГОСТ 23360-78
Произвести шлифование подшипниковых шеек
маршрут изготовления
Электросхема.cdw
