Висбрекинг




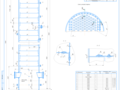
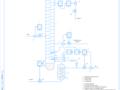
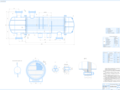
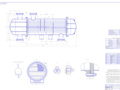
- Добавлен: 25.01.2023
- Размер: 979 KB
- Закачек: 2
Описание
Состав проекта
![]() |
![]() |
![]() ![]() ![]() |
![]() |
![]() ![]() ![]() ![]() |
![]() ![]() ![]() ![]() |
![]() ![]() ![]() ![]() |
![]() ![]() ![]() ![]() |
![]() ![]() ![]() ![]() |
![]() ![]() ![]() ![]() |
![]() ![]() ![]() ![]() |
![]() ![]() ![]() ![]() |
![]() ![]() ![]() ![]() |
![]() ![]() ![]() ![]() |
![]() ![]() ![]() |
Дополнительная информация
Доклад на диплом.doc
В процессе изучения состояния переработки нефти в России было выявлено что несмотря на лидирующие позиции в мире по количеству перерабатываемой нефти глубина ее переработки остается на достаточно низком уровне (647%). По данному показателю наша страна занимает 67-е место. Таким образом на отечественных нефтеперерабатывающих предприятиях необходимо повысить глубину переработки нефти за счет использования дополнительных процессов переработки тяжелого углеводородного сырья.
Для выбора метода переработки тяжелых нефтей был проведен анализ различных методов и было выявлено что одним из преимуществ висбрекинга является его более низкая стоимость в сравнении с другими. Введение этого процесса в производство обусловлено простотой аппаратурно-технологических решений минимально требуемым инвестиционным бюджетом на строительство установки высокой универсальностью по круглогодичному производству всегда востребованной продукции.
Висбрекинг представляет собой процесс термического крекинга; осуществляемый в сравнительно мягких условиях с целью снижения вязкости нефтяных остатков. Это сравнительно простой и не требующий разработки специального дорогостоящего оборудования процесс. Включение висбрекинга в схему переработки нефти позволяет значительно увеличить отбор вакуумного газойля и тем самым увеличить ресурсы сырья для каталитического крекинга.
Как сравнительно простой и не требующий разработки специального дорогостоящего оборудования процесс висбрекинга является одним из перспективных в схемах глубокой переработки высоковязких нефтяных остатков.
Принципиальная технологическая схема установки представлена на плакате «Схема установки». Процесс происходит следующим образом:
Остаточное сырье (гудрон) прокачивают через теплообменники где нагревают за счет тепла отходящих продуктов до температуры 300 °С и направляют в нагревательно-реакционные змеевики параллельно работающих печей. Продукты висбрекинга выводят из печей при температуре 500 °С и охлаждают подачей квенчинга (висбрекинг остатка) до температуры 430 °С и направляют в нижнюю секцию ректификационной колонны К-1.
С верха этой колонны отводят парогазовую смесь которую после олаждения и конденсации в конденсаторах-холодильниках подают в газосепаратор С-1 где разделяют на газ воду и бензиновую фракцию. Часть бензина используют для орошения верха К-1 а балансовое количество направляют на стабилизацию.
Из аккумулятора К-1 через отпарную колонну К-2 выводят фракцию легкого газойля (200 350 °С) и после охлаждения в холодильниках направляют на смешение с висбрекинг-остатком или выводят с установки. Часть легкого газойля используют для создания промежуточного циркуляционного орошения колонны К-1.
Кубовая жидкость из К-1 поступает самотеком в колонну К-3. За счет снижения давления с 04 до 01 005 МПа и подачи водяного пара в переток из К-1 в К-3 происходит отпарка легких фракций. Парогазовая смесь выводимая с верха К-3 после охлаждения и конденсации поступает в газосепаратор С-2. Газы из него направляют к форсункам печей а легкую флегму возвращают в колонну К-1.
Из аккумулятора К-3 выводят тяжелую флегму которую смешивают с исходным гудроном направляемым в печи. Остаток висбрекинга с низа К-3 после охлаждения в теплообменниках и холодильниках выводят с установки. Для предотвращения закоксовывания реакционных змеевиков печей (объемно-настильного пламени) в них предусматривают подачу турбулизатора — водяного пара на участке где температура потока достигает 430 450 °С.
В соответствии с заданием на дипломный проект я спроектировала установку по висбрекингу. На данном предприятии сырьем для переработки является гудрон а получаемой продукцияей – газ бензин керосино-газойлевая фракция и крекинг остаток.
В работе был проведен расчет реакционной камеры мощностьью установки 580000 т в год. В процессе расчета был составлен тепловой баланс установки было рассчитано количество получаемого бензина и газа. Размеры реакционной установки в соответствии с полученными данными должны быть следующими диаметр камеры 1 м высота камеры 146 м.
Была выбрана ректификационная колонна с ситчато-клапанными тарелками (представлена на плакте «Колонна»).
Ректификационная колонна представляет собой вертикальный цилиндр с контактными устройствами внутри. В ректификационную колонну подаются пары перегоняемой жидкости. Они поднимаются снизу а в режиме противотока навстречу парам идёт жидкость сконденсировавшаяся наверху в холодильнике. В случае если разгоняемый продукт состоит из двух компонентов конечными продуктами являются дистиллят выходящий из верхней части колонны и кубовый остаток (менее летучий компонент в жидком виде вытекающий из нижней части колонны).
При ситовой ректификационной колонне самая нижняя тарелка всегда делается с одним центральным колпаком. Сливную трубку погружают в жидкость куба возможно глубже для того чтобы конец ее был погружен в перегоняемую жидкость до самого конца сгонки.
Максимальная производительность ректификационной колонны получается в том случае когда площадь штуцера равна площади всех отверстий ректификационной тарелки этой колонны.
Точно так же крайне важно правильно устроить отвод пара из колонны в дефлегматор и холодильник. Не следует ставить отводящие трубы слишком маленького диаметра так как они требуют повышенного давления и кроме того количество спиртового пара отводимого из колонны и дефлегматора сокращается.
Ректификационная колонна должна быть оборудована следующей арматурой: краном в верхней части колонны для промывки ее водой; паровым вентилем для пропаривания паром; дроссельным клапаном закрывающим отверстие для выхода паров из колонны при пропаривании ее и воздушным клапаном на крышке колонны для автоматического впуска воздуха в случае внезапного образования вакуума внутри ректификационной колонны.
Самыми простыми в тоже время наиболее дешевыми тарелками являются ситовые. Чем длиннее путь проходимый погоном в колонне и чем длиннее линия по которой пары проникают сквозь погон (флегму) тем лучшего качества получается ректификат; при более длинном пути погон отдает большее количество заключающейся в нем фракции а при длинной линии барботажа пара сквозь погон кипение последнего происходит спокойнее без перебрызгивания с нижний тарелок на верхние. Ситовые тарелки имеют плоское дно. Диаметр просверленных отверстий равен 25-35 мм. Для стока погона между ситами расположены сливные трубки.
Пар поднимаясь сквозь отверстия сита вверх не позволяет погону (флегме) собирающемуся на сите протекать через отверстия вниз. Погон остается на сите до тех пор пока уровень его не поднимется выше края сливной трубы и излишек погона не начнет стекать вниз.
Сливная трубка имеет гидравлический затвор. Ее нижний конец спускают в сливную чашку всегда заполненную погоном. Пар проходя сквозь слой погона тонкими струйками конденсируется погон нагревается и начинает кипеть т. е. Происходит собственно ректификация.
Недостатком ситовых тарелок является неудобство в работе так как при остановке аппарата и падении давления все содержимое тарелок стекает через отверстия сит в куб; в связи с этим при возобновлении работы аппарата приходится затрачивать время на приведение колоны в то состояние в котором она находилась перед остановкой.
Достоинством ситовых тарелок является и дешевизна простота изготовления и малый вес по сравнению с тарелками других систем. Коэффициент полезного действия ситовых тарелок колеблется от 06 до08 в зависимости от их размеров и способа изготовления. При работе с ситовыми тарелками особенно важно соблюдать горизонтальность их расположения. Во избежании прогиба тарелок у колонн больших диаметров такие тарелки скрепляют стяжными болтами с расположенными трубками между отдельными тарелками. При прогибе тарелок сильно снижается коэффициент их полезного действия. При установке сита должны плотно прилегать к стенкам корпуса колонны.
Величину ситовых тарелок устанавливают в зависимости от скорости движения пара через отверстия в ситах. В среднем она равна 5-6мсек и больше.
Был проведен также расчет кожухотрубного теплообменника с плавающей головкой. Был составлен тепловой баланс аппарата и в соответствии с ним определана тепловая нагрузка. Это дало возможность определить необходимую поверхность теплообмена и выбрать необходимы теплообменник.
Выбранный теплообменник представлен на плакате «Конденсатор». Теплообменник кожухотрубный горизонтальный с площадью теплообмена 873 м2. Исходя из расчета теплообменников такого типа необходимо 3.
В разделе автоматизации были рассмотрены варианты систем управления которые позволили бы увеличить выход продуктов на действующих установках за счет автоматического контроля и коррекции температуры давления и уровня.
На плакате «Автоматизация »представлена схема регулирования процесса ректификации. Материальный баланс колонны поддерживается путем сохранения равенства между количеством вводимого сырья и выводимыми продуктами. Для этой цели на колонне установлены: регулятор уровня 1 регулятор расхода сырья 2 регулятор отбора промежуточной фракции 3 и регулятор отбора продукта 9. Тепловой баланс колонны поддерживается путем сохранения равенства между количеством вводимого и отбираемого тепла. Для поддержания теплового баланса установлены: регулятор подачи охлаждающей воды 4 в дефлегматор и регулятор подачи пара 6 в кипятильник. Задание регуляторам 7 и 9 корректируется анализаторами качества 8 и 10 задание регулятору 4— прибором 5 измеряющим давление в верхней части колонны.
В разделе охраны труда были рассмотрены особенности промышленной безопасности нефтеперерабатывающих предприятий был проведен анализ существующих вредностей и опасностей на данном производстве и меры по защите работников предприятия от них. Был проведен анализ источников загрязнения и меры по снижению их влияния на окружающую среду.
В экономической части проекта были рассчитаны основные технико-экономические показатели установки численность работающих и себестоимость выпускаемой продукции. На плакате «Экономика» представлены основные технико-экономические показатели проекта. Только досмотрела Срок окупаемости НЕРЕАЛЬНЫЙ нужно подправить хотя бы лет на 5. Установка мощностью 580000 т в год будет обслуживаться 18-ю работающими при этом себестоимость годового выпуска продукции составит 1482 млн. рублей а прибыль – 1704 млн. рублей. При таких показателях проект окупится в течение .. лет.
Таким образом разработанный проект может быть использован при введении процесса висбрекинга на нефтеперерабатывающих предприятих.
Конденсатор_А1+.cdw

РТК.3.24.04.04.01 ПНиГ - 07-33.П.3
Аппарат подлежит действию правил Гостехнадзора России.
Контроль сварных швов 100%
Материал изготовления и сварка по Правилу оборудования и
безопасной эксплуатации сосудов работающих под давлением ОСТ
Все обработанные поверхности
лакокрасочного покрытия
консервируются смазкой ПВК ГОСТ
Чертеж разработан на основе ГОСТ 14249-79
-02-571-77 и отвечает правилам установления и безопасной
эксплуатации сосудов работающих под давлением ОСТ 26-291-75
Аппарат может устанавливаться в районах со средней
температурой наиболее холодной пятидневки не ниже -40°С
деталей крепления теплоизоляции провести в
соответствии с ГОСТ 17314-81.
остановку и испытание аппарата на герметичность
зимой провести в соответствии с "Регламентом" ОСТ 26-291-87.
Схема расположения штуцеров и опор
Соединение с атмосферой
Техническая характеристикай
Колонна.dwg

РТК.3.24.04.04.01 ПНиГ - 07-33.П.3
При изготовлении испытании и поставке аппарата должны
выполнятся требования: Гостехнадзора; ГОСТ 12.2.003-79
Оборудование производственное. Общие требования безопасности";
ОСТ 26-29т-79 "Сосуды и аппараты: стальные сварные. Технические
Материал тарелок - сталь 08Х13 ГОСТ 5632-77 и сталь 20 ГОСТ
Сварные соединения должны соответствовать требованиям ОСТ
-01-82-77 "Сварка в химическом машиностроении
Не указанный вылет штуцеров 150 мм
Наименование и марка
Шайба 12 ГОСТ 11371-68
Вход паров из кипятильника
Выход жидкости из куба
Для измерения давления
Для камеры уровнемера
Выход кубового остатка
Для предохранительного клапана
Аппарат предназначен для отгонки легколетучих примесей.
Номинальная ёмкость 12 м
Производительность 20
Давление в колонне 1
Температура среды в кубе до 150
Среда в аппарате - токсичная коррозионная
Тип тарелок - ситчато-клапанные
Техническая характеристика
Схема расположения штуцеров
Схема ситчатой тарелки
Схема установки.dwg

химически очищенная вода;
остаток висбрекинга;
регенерированный раствор ДЭА;
насыщенный раствор ДЭА
Экономика.dwg

ОСНОВНЫЕ ТЕХНИКО-ЭКОНОМИЧЕСКИЕ
ТЕХНИКО-ЭКОНОМИЧЕСКИЕ
Колонна.cdw

Шайба 12 ГОСТ 11371-68
Вход паров из кипятильника
Выход жидкости из куба
Для измерения давления
Для камеры уровнемера
Выход кубового остатка
Для предохранительного клапана
Аппарат предназначен для отгонки легколетучих примесей.
Номинальная ёмкость 12 м
Производительность 20
Давление в колонне 1
Температура среды в кубе до 150
Среда в аппарате - токсичная коррозионная
Тип тарелок - ситчато-клапанные
Колонна ректификационная
РТК.3.24.04.04.01 ПНиГ - 07-33.П.3
При изготовлении испытании и поставке аппарата должны
выполнятся требования: Гостехнадзора; ГОСТ 12.2.003-79
Оборудование производственное. Общие требования безопасности";
ОСТ 26-29т-79 "Сосуды и аппараты: стальные сварные. Технические
Материал тарелок - сталь 08Х13 ГОСТ 5632-77 и сталь 20 ГОСТ
Сварные соединения должны соответствовать требованиям ОСТ
-01-82-77 "Сварка в химическом машиностроении
Не указанный вылет штуцеров 150 мм
Техническая характеристика
Схема расположения штуцеров
Схема ситчатой тарелки
Автоматизация.cdw

процесса непрерывной ректификации
РТК.3.24.04.04.01 ПНиГ - 07-33.П.3
I - ректификационная колонна;
- регулятор уровня;
- регулятор расхода сырья;
-регулятор расхода промежуточных фракций;
-регулятор подачи охлаждающей воды;
- прибор с пневматическим выходом для измерения давления в
верхней части колонны (задатчик к регулятору 4)
-регулятор подачи пара в кипятильник;
-корректирующий регулятор (прибор с пневматическим выходом
для измерения температуры)
служащий задатчиком к регулятору
- прибор с пневматическим выходом для измерения разности
между температурой насыщенного водяного пара (термометр ТС1) и
температурой на первой тарелке колонны (термометр ТС2);
- регулятор отбора продукта;
-задатчик регулятора 9;
РХ - устройство редуцирования и охлаждения пара до насыщенного
ИМ - исполнительные механизмы с регулирующим органом;
Д - дроссельные сужающие устройства;
С -состав кубового остатка.
Автоматизация.dwg

процесса непрерывной ректификации
РТК.3.24.04.04.01 ПНиГ - 07-33.П.3
- ректификационная колонна;
- регулятор уровня;
- регулятор расхода сырья;
-регулятор расхода промежуточных фракций;
-регулятор подачи охлаждающей воды;
- прибор с пневматическим выходом для измерения
верхней части колонны
-регулятор подачи пара в кипятильник;
-корректирующий регулятор (прибор с
пневматическим выходом
водяного пара (термометр ТС1) и
первой тарелке колонны
- регулятор отбора продукта;
-задатчик регулятора 9;
РХ - устройство редуцирования и охлаждения пара
ИМ - исполнительные механизмы с регулирующим
Д - дроссельные сужающие устройства;
С -состав кубового остатка.
Схема установки.cdw

V - остаток висбрекинга;
VIII - углеводородный газ;
X - регенерированный раствор ДЭА;
XI - насыщенный раствор ДЭА
РТК.3.24.04.04. 01 ПНиГ - 07.33.П.3
Экономика.cdw

РТК.3.24.04.04.01 ПНиГ - 07-33.П.3
технико-экономические
Конденсатор_А1+.dwg

Аппарат подлежит действию правил
Контроль сварных швов 100%
Материал изготовления и сварка по Правилу оборудования и
безопасной эксплуатации сосудов
Все обработанные поверхности
лакокрасочного покрытия
Чертеж разработан на основе ГОСТ 14249-79
и отвечает правилам
установления и безопасной
сосудов работающих под давлением ОСТ 26-291-75
Аппарат может устанавливаться в районах со средней
температурой наиболее холодной
пятидневки не ниже -40°С
деталей крепления теплоизоляции провести в
соответствии с ГОСТ 17314-81.
остановку и испытание аппарата на герметичность
провести в соответствии с
Поверхность теплообмена
Схема расположения штуцеров и опор
Соединение с атмосферой
Техническая характеристикай
Диплом.doc
2 Что является сырьем какие продукты переработки9
3 Актуальность метода производства10
4 Физико-химические основы производства. Химические и физические процессы10
5 Описание технологических схем и режим работы висбрекинга15
6 Характеристика исходного сырья готовой продукции и вспомогательных материалов19
РАСЧЕТ ОСНОВНОГО И ВСПОМОГАТЕЛЬНОГО АППАРАТОВ УСТАНОВКИ ВИСБРЕКИНГА24
1 Материальный баланс установки (мощность установки время работы установки часовая производительность по сырью)24
2 Расчет основного аппарата25
3 Расчет вспомогательного аппарата (теплообменника)29
ОРГАНИЗАЦИОННО-ЭКОНОМИЧЕСКАЯ ЧАСТЬ35
1 Промышленная безопасность50
2 Вредности и опасности на производстве. Техника безопасности56
3 Охрана окружающей среды66
АВТОМАТИЗАЦИЯ И СИСТЕМА АВТОМАТИЗИРОВАННОГО УПРАВЛЕНИЯ ПРОИЗВОДСТВА71
По различным прогнозам следующие два десятилетия нефть сохранит свою доминирующую роль в глобальном потреблении первичных энергоносителей. Общие мировые запасы нефти на сегодня оценивают в 140.88 млрд т (в странах ОПЕК 111.56 млрд т). природного газа - 149.49 трлн. м3 [1]. Нефтяные запасы распределены крайне неравномерно основная их часть (свыше 65 %) сосредоточена на небольшой территории Ближнего н Среднего Востока в Северной Америке - 6 %. в Южной и Центральной Америке - 9 %. в Европе (включая Россию) - 6.5 %. в Африке - 7 %. в Азии - 65 %. Основные запасы природного газа сосредоточены в двух регионах - на Ближнем и Среднем Востоке и в странах СНГ. на страны ОПЕК приходится 44 % запасов.
За год суммарная мировая добыча нефти составляет свыше 3000 млн. т. Основными поставщиками нефти и природного газа в страны мира служат страны Персидского залива и Азиатско-Тихоокеанского региона. В последние годы лидерами по добыче являются Саудовская Аравия США и Россия.
Топливно-энергетический комплекс России - важная составная часть мирового энергетического хозяйства. На территории России сосредоточено около 13 % мировых запасов нефти 33 % разведанных запасов природного газа и более 16 % запасов угля [2].
Современные тенденции мировой нефтепереработки отличаются опережающим ростом мощностей процессов гидроочистки и гидрокрекинга по сравнению с другими процессами а также модернизированных процессов позволяющих увеличить производство нефтехимического сырья [2 3]. Глубина переработки нефти составляет от 87 до 93 %. По количеству перерабатываемой нефти Россия входит в число лидирующих стран мира однако по глубине переработки (647 %.) находится на 67-м месте из 122 стран [2 3]. Структура российской нефтеперерабатывающей отрасли отличается низкой долей каталитических процессов переработки позволяющих получать высококачественные продукты. Так. доли процессов гидроочистки и каталитического крекинга составляют 28 и 93 % от общего объема первичной переработки нефти в то время как в развитых странах они составляют от 30 до 436 % и от 14 до 342 % соответственно. В результате на российских НПЗ из одной тонны нефти в среднем получают всего 16 % бензинов и не менее 30 % мазута в то время как в развитых странах - до 43 % бензинов и не более 5-10 % мазута [2].
Таким образом рациональное использование тяжелого углеводородного сырья как источника энергии и сырья для производства моторных топлив смазочных масел битума кокса и множества нефтехимических продуктов является важнейшей государственной задачей. Повысить глубину переработки возможно за счет более интенсивного развития деструктивных процессов переработки тяжелого углеводородного сырья с получением ценных топливных и нефтехимических продуктов. К таким процессам относятся термические каталитические и гидрогенизационные процессы переработки тяжелого углеводородного сырья в частности мазута гудрона и др.
Основными термическими процессами переработки тяжелого углеводородного сырья являются термический крекинг и висбрекинг.
Термический крекинг в настоящее время утратил свое «бензинообразующее» значение а процесс висбрекинга наоборот приобретает все большее значение в нефтеперерабатывающей промышленности.
Висбрекинг представляет собой процесс термического крекинга; осуществляемый в сравнительно мягких условиях с целью снижения вязкости нефтяных остатков. Как сравнительно простой не требующий разработки специального дорогостоящего оборудования процесс висбрекинга является в настоящее время- одним из перспективных в схемах глубокой переработки высоковязких нефтяных остатков.
Включение висбрекинга в схему переработки нефти позволяет значительно увеличить отбор вакуумного газойля и тем самым увеличить ресурсы сырья для каталитического крекинга.
Как сравнительно простой и не требующий разработки специального дорогостоящего оборудования процесс висбрекинга является одним из перспективных в схемах глубокой переработки высоковязких нефтяных остатков.
В данной работе будут рассмотрены особенности висбрекинга и произведены расчеты установки висбрекинга.
1 Выбор метода производства
При решении задач поиска технологий переработки тяжелых нефтей целесообразно рассматривать процессы и конфигурации технологических схем гарантирующих выработку из тяжелых ингредиентов нефти высококачественных битумов с одновременной максимальной конверсией тяжелых углеводородных ингредиентов не входящих в состав битумов в среднедистиллятные фракции.
Среди «битумных» технологических процессов пригодных к переработке тяжелых нефтей можно рассматривать следующие:
Вакуумная перегонка мазута. Процесс позиционируется как самый известный для производства гудронов и битумов. Общеизвестно что до 80-90% гудронов получаемых вакуумной перегонкой мазута не соответствуют по качественным показателям товарным битумам и гудроны используют в качестве сырья для получения битумов окислением. В большинстве случаев перед окислением гудроны необходимо дополнительно подвергнуть висбрекингу с тем чтобы снизить содержание трудноокисляемых парафиновых углеводородов в битумном сырье. Получаемые при вакуумной перегонке мазута вакуумные газойли не отвечают требованиям легких синтетических нефтей поскольку отличаются высокой плотностью (более 900 кгм3) высокой вязкостью высокими температурами застывания (зачастую выше + 30-40°С). Высоковязкие и как правило высоко-парафинистые компоненты создают проблемы при трубной перекачке нефтей на НПЗ.
Деасфальтизация гудрона. На НПЗ пропановую деасфальтизацию чаще всего применяют в технологиях производства высокоиндексных масел. Деасфальтизацию гудронов бензином используют как процесс наработки сырья для производства битумов компаундированием или окислением. Выделяемая асфальтовая фаза не всегда соответствует свойствам требуемого качества товарных битумов. Поэтому полученный асфальтит либо необходимо дополнительно окислять до битумов либо разбавлять масляной фазой. Легкая фаза процесса деасфальтизации - деасфальтизат имеет еще более тяжелые показатели нежели вакуумный газойль: плотность > 920 кгм3 температура застывания > 40 °С еще более высокую вязкость и также требует дальнейшей квалифицированной переработки. Высоковязкие деасфальтизаты проблемны для перекачки. Самый большой недостаток процесса деасфальтизации - его высокая энергоемкость вследствие чего и капитальные затраты более чем в 2 раза выше чем у процесса вакуумной перегонки.
Висбрекинг мазута. Процесс набирает вторую волну технологической востребованности. Если раньше висбрекинг использовали для снижения вязкости гудронов то теперь для углубления переработки нефти. Ведущие мировые фирмы разработали за последние годы по нескольку оригинальных решений. Основное достоинство новых процессов в том что они предназначены для глубокой переработки тяжелых нефтяных остатков с целью увеличения выхода дистиллятных фракций на 40-60%. Эти процессы применимы и для глубокой переработки тяжелых нефтей с цепью перевода тяжелых углеводородов в светлые бензино-дизельные дистиллятные фракции. В указанных процессах висбрекинга отмечена возможность производства дорожных битумов.
При переработке нефтяных остатков – полугудронов и гудронов – целевым продуктом обычно является котельное топливо получаемое в результате снижения вязкости исходного остатка.
Установка висбрекинга использует тяжелый остаток от процесса вакуумной перегонки часть которого подвергается в ней термическому крекингу. Продукт можно снова разделить на фракции что приводит к уменьшению объема остатка. После этого к остатку добавляют для разбавления дистилятный нефтепродукт чтобы остаток висбрекинга стал пригодным к применению в качестве остаточного (котельного) топлива.
В качестве разбавителя можно брать тяжелый крекинг-газойль рециркулирующий газойль или погон полученный на этой же установке.
Висбрекинг напоминает термический крекинг но отличается от последнего по интенсивности. Оборудование в этом случае проще и весь процесс дешевле.
Висбрекинг мазута протекает мягче и глубже нежели для гудрона и процесс надежнее в эксплуатации - исключается закоксовывание оборудования что в случае с гудроном является основным отрицательным фактором.
Таблица 1.1 Новые возможности висбрекинга
Главное достоинство: простота аппаратурно-технологических решений минимально требуемый инвестиционный бюджет на строительство установки высокая универсальность по круглогодичному производству всегда востребованной продукции.
2 Что является сырьем какие продукты переработки
Сырьем установок являются остатки первичной перегонки нефти - мазут выше 350°С и гудрон выше 500°С.
Газ - содержит непредельные и предельные углеводороды и сероводород после очистки от сероводорода может быть использован как сырье газофракционирующих установок или в качестве топливного газа;
Бензин; характеристика: октановое число 66-72 (моторный метод) содержание серы при переработке остатков из сернистых нефтей - 05-12 %; в бензине термического крекинга содержится до 25% непредельных углеводородов (алкенов и алкадиенов) поэтому он обладает низкой химической стабильностью; Может быть использован в качестве сырья риформинга или компонента товарного бензина после процесса гидрооблагораживания. При использовании непосредственно в качестве компонента товарного бензина к бензину термического крекинга добавляют ингибиторы препятствующие окислению;
Керосино-газойлевая фракция является ценным компонентом флотского мазута; после гидроочистки может применяться как компонент дизельных топлив;
Крекинг-остаток используется как котельное топливо имеет более высокую теплоту сгорания более низкую температуру застывания и вязкость чем прямогонный мазут.
3 Актуальность метода производства
Как было сказано выше по количеству перерабатываемой нефти Россия входит в число лидирующих стран мира при этом по глубине переработки (647 %.) находится на 67-м месте из 122 стран. Поэтому необходимо повышать глубину переработки за счет более интенсивного развития деструктивных процессов переработки тяжелого углеводородного сырья с получением ценных топливных и нефтехимических продуктов. К этим процессам относятся термические каталитические и гидрогенизационные процессы переработки тяжелого углеводородного сырья в частности мазута гудрона и др. В нашем случае мы применим висбрекинг.
4 Физико-химические основы производства. Химические и физические процессы
Жидкофазный термолиз имеет место в таких термодеструктивных процессах нефтепереработки как термический крекинг висбрекинг пекование и коксование тяжелых нефтяных остатков.
Основной отличительной кинетической особенностью жидкофазных химических реакций является высокая на два-три порядка выше чем в газофазных концентрация реагирующих веществ в единице объема реактора. В силу этого проведение реакций в жидкофазном состоянии при атмосферном давлении равносильно проведению их в газовой фазе под давлением порядка 10 100 МПа. Это означает что в жидкофазных процессах будет значительно выше вероятность столкновения реагирующих молекул; в результате преимущественно ускоряются вторичные бимолекулярные реакции. При этом однако низкомолекулярные продукты первичного распада высокомолекулярного сырья и алкильные радикалы в зависимости от условий проведения процесса могут «разлетаться» в газовую фазу и не участвовать во вторичных жидкофазных реакциях. В этих условиях цепной процесс жидкофазного термолиза нефтяного сырья будет осуществляться с участием более высокомолекулярных так называемых долгоживущих бензильных и фенильных радикалов. В результате при равных температурах жидкофазный термолиз углеводородов дает значительно больший выход продуктов конденсации и меньший выход продуктов распада.
На суммарный результат жидкофазного термолиза нефтяного сырья существенное влияние оказывает «клеточный эффект». При газофазном распаде молекулы углеводорода образующиеся радикалы мгновенно разлетаются. В жидкой же фазе радикалы окружены «клеткой» из соседних молекул. Для удаления радикалов на расстояние при котором они становятся кинетически независимыми частицами необходимо преодолеть дополнительный активационный барьер равный энергии активации диффузии радикала из клетки. Тем самым клеточный эффект приводит к изменению энергии активации жидкофазной реакции относительно газофазной а также стационарной концентрации радикалов.
Из результатов многочисленных исследований зарубежных и отечественных ученых отметим следующие общепризнанные закономерности жидкофазного термолиза нефтяного сырья.
Термолиз нефтяного сырья в жидкой фазе протекает через последовательные или параллельно-последовательные стадии образования и расходования промежуточных продуктов уплотнения по схеме: легкие масла полициклические ароматические углеводороды смолы асфальтены карбены карбоиды кокс. При этом на каждой стадии образуются газы и менее низкомолекулярные жидкие продукты по сравнению с образовавшимися промежуточными продуктами уплотнения. Так при термолизе смол образуются кроме асфальтенов масла и газы. Это обстоятельство позволяет процесс термолиза рассматривать как обратимый процесс хотя вторичные продукты уплотнения по молекулярной структуре не вполне идентичны исходным нативным компонентам сырья.
При термолизе ТНО имеют место фазовые превращения групповых компонентов. Так при осуществлении процессов термодеструкции с образованием кокса в коксующейся системе происходит несколько фазовых переходов: первый связан с образованием и выделением из раствора фазы асфальтенов а следующий — с зарождением и осаждением не растворимых в ароматических растворителях карбенов которые затем превращаются в карбоиды и конечный твердый продукт — кокс.
Проведенными за последние два десятилетия специальными (спектральными микроскопическими и др.) исследованиями (Брукса Тейлора Уайта Хонда З. И. Сюняева и Р. Н. Гимаева) в продуктах карбонизации органических полимеров нефтяных и каменноугольных пеков ароматизированных дистиллятных нефтяных остатков были обнаружены анизотропные микросферические структуры размером 01 20 мкм обладающие специфическими свойствами жидких кристаллов и получившие название мезофазы. Это открытие имеет исключительно важное научное и практическое значение и позволяет более точно установить механизм жидкофазного термолиза нефтяного сырья. Мезофаза представляет собой слоистый жидкий кристалл состоящий преимущественно из конденсированных ароматических структур с числом бензольных (или нафталиновых) колец от 10 до 15 соединенных посредством алкильных или гетероалкильных групп (метиленовых диариловых аминных амидных и т. д.) имеет примерно на порядок выше парамагнитность. По мнению З. И. Сюняева мезофаза — это ассоциаты асфальтенов образованные за счет межмолекулярных физических сил.
С ростом температуры физические силы переходят в химические и формируется углеродный кристаллит анизатропной структуры. Нерастворимость части мезофазы обусловливается появлением поперечных связей между плоскоконденсированными структурами. В условиях термолиза (пекования или коксования ТНО) микросферы мезофазы растут за счет подвода молекул из карбонизируемой среды и коалесценции мелких сфер с последующим осаждением их за счет разности плотностей анизотропной и изотропной фаз.
На интенсивность (скорость) термодеструктивных превращений ТНО существенное влияние оказывает растворяющая способность дисперсионной среды которая определяет значение так называемой «пороговой» концентрации асфальтенов. Если дисперсионная среда представлена парафино-нафтеновыми углеводородами обладающими слабой растворяющей способностью (т. е. являющимися «плохим» растворителем) асфальтены выпадают из раствора при низких их концентрациях. Наоборот в среде «хорошего» растворителя например полициклических ароматических углеводородов или смол выпадение асфальтенов происходит только при превышении значения их пороговой концентрации (с показателем растворяющей способности тесно связано и такое понятие как «агрегативная устойчивость» сырья или реакционной среды широко применяемое при объяснении причин и разработке способов защиты против расслоения и закоксовывания змеевиков печей и новых сортов высоковязких топлив вяжущих связующих материалов и др.).
При термолизе ТНО растворитель служит не только дисперсионной средой но и является реагирующим компонентом. К тому же сами асфальтены полидисперсны не только по молекулярной массе но и по растворимости в данном растворителе. В связи с этим в ходе жидкофазного термолиза непрерывно изменяются химический состав и растворяющая способность дисперсионной среды. По мере уплотнения и насыщения раствора асфальтенами в первую очередь будут выделяться наиболее высокомолекулярные плохо растворимые асфальтены а затем — асфальтены с более совершенной структурой мезофаза и кокс.
Останавливая процесс термолиза на любой стадии т. е. регулируя глубину превращения ТНО можно получить продукты требуемой степени ароматизации или уплотнения например крекинг-остаток с определенным содержанием смол и асфальтенов и умеренным количеством карбенов кокс с требуемой структурой и анизотропией.
Таким образом можно заключить что термодеструктивные процессы переработки ТНО особенно коксования представляют собой исключительно сложные многофакторные нестационарные гетерогенные и гетерофазные диффузионные процессы со специфическим гидродинамическим массообменным и тепловым режимом.
Исследованиями установлено что по мере увеличения продолжительности (т. е. углубления) крекинга вязкость крекинг-остатка вначале интенсивно снижается достигает минимума и затем возрастает. Экстремальный характер изменения зависимости вязкости остатка от глубины крекинга можно объяснить следующим образом. В исходном сырье (гудроне) основным носителем вязкости являются нативные асфальтены «рыхлой» структуры. При малых глубинах превращения снижение вязкости обусловливается образованием в результате термодеструктивного распада боковых алифатических структур молекул сырья более компактных подвижных вторичных асфальтенов меньшей молекулярной массы. Последующее возрастание вязкости крекинг-остатка объясняется образованием продуктов уплотнения — карбенов и карбоидов также являющихся носителями вязкости. Считается что более интенсивному снижению вязкости крекинг-остатка способствует повышение температуры при соответствующем сокращении продолжительности висбрекинга. Этот факт свидетельствует о том что температура и продолжительность крекинга не полностью взаимозаменяемы между собой. Этот вывод вытекает также из данных о том что энергия активации для реакций распада значительно выше чем реакций уплотнения. Следовательно не может быть полной аналогии в материальном балансе и особенно по составу продуктов между различными типами процессов висбрекинга. В последние годы в развитии висбрекинга в нашей стране и за рубежом определились два основных направления. Первое — это «печной» (или висбрекинг в печи с сокинг-секцией) в котором высокая температура (480 500 °С) сочетается с коротким временем пребывания (15 2 мин). Второе направление — висбрекинг с выносной реакционной камерой который в свою очередь может различаться по способу подачи сырья в реактор на висбрекинг с восходящим потоком и с нисходящим потоком.
В висбрекинге второго типа требуемая степень конверсии достигается при более мягком температурном режиме (430 450 °С) и длительном времени пребывания (10 15 мин). Низкотемпературный висбрекинг с реакционной камерой более экономичен так как при одной и той же степени конверсии тепловая нагрузка на печь ниже. Однако при «печном» крекинге получается более стабильный крекинг-остаток с меньшим выходом газа и бензина но зато с повышенным выходом газойлевых фракций.
5 Описание технологических схем и режим работы висбрекинга
Висбрекинг проводят при менее жестких условиях чем термокрекинг вследствие того что во-первых перерабатывают более тяжелое следовательно легче крекируемое сырье; во-вторых допускаемая глубина крекинга ограничивается началом коксообразования (температура 440 500 °С давление 14 35 МПа).
В последние годы наблюдается устойчивая тенденция утяжеления сырья висбрекинга в связи с повышением глубины отбора дистиллятных фракций и вовлечением в переработку остатков более тяжелых нефтей с высоким содержанием асфальто-смолистых веществ повышенной вязкости и коксуемости что существенно осложняет их переработку. Эксплуатируемые отечественные установки висбрекинга несколько различаются между собой поскольку были построены либо по типовому проекту либо путем реконструкции установок AT или термического крекинга. Различаются они по числу и типу печей колонн наличием или отсутствием выносной реакционной камеры. Принципиальная технологическая схема типовой установки печного висбрекинга производительностью 1 млн т гудрона приведена на рис. 1.1.
Рисунок 1.1. Принципиальная технологическая схема установки висбрекинга гудрона: I — сырье; II — бензин на стабилизацию; III — керосино-газойлевая фракция; IV — висбрекинг-остаток; V — газы ГФУ;
Остаточное сырье (гудрон) прокачивают через теплообменники где нагревают за счет тепла отходящих продуктов до температуры 300 °С и направляют в нагревательно-реакционные змеевики параллельно работающих печей. Продукты висбрекинга выводят из печей при температуре 500 °С и охлаждают подачей квенчинга (висбрекинг остатка) до температуры 430 °С и направляют в нижнюю секцию ректификационной колонны К-1.
С верха этой колонны отводят парогазовую смесь которую после охлаждения и конденсации в конденсаторах-холодильниках подают в газосепаратор С-1 где разделяют на газ воду и бензиновую фракцию. Часть бензина используют для орошения верха К-1 а балансовое количество направляют на стабилизацию.
Из аккумулятора К-1 через отпарную колонну К-2 выводят фракцию легкого газойля (200 350 °С) и после охлаждения в холодильниках направляют на смешение с висбрекинг-остатком или выводят с установки. Часть легкого газойля используют для создания промежуточного циркуляционного орошения колонны К-1.
Кубовая жидкость из К-1 поступает самотеком в колонну К-3. За счет снижения давления с 04 до 01 005 МПа и подачи водяного пара в переток из К-1 в К-3 происходит отпарка легких фракций. Парогазовая смесь выводимая с верха К-3 после охлаждения и конденсации поступает в газосепаратор С-2. Газы из него направляют к форсункам печей а легкую флегму возвращают в колонну К-1.
Из аккумулятора К-3 выводят тяжелую флегму которую смешивают с исходным гудроном направляемым в печи. Остаток висбрекинга с низа К-3 после охлаждения в теплообменниках и холодильниках выводят с установки. Для предотвращения закоксовывания реакционных змеевиков печей (объемно-настильного пламени) в них предусматривают подачу турбулизатора — водяного пара на участке где температура потока достигает 430 450 °С.
Висбрекинг с вакуумной перегонкой. На ряде НПЗ (Омском и Ново-Уфимском) путем реконструкции установок термического крекинга разработана и освоена технология комбинированного процесса висбрекинга гудрона и вакуумной перегонки крекинг-остатка на легкий и тяжелый вакуумные газойли и тяжелый висбрекинг-остаток.
Целевым продуктом процесса является тяжелый вакуумный газойль характеризующийся высокой плотностью (940 990 кгм3) содержащий 20 40 % полициклических углеводородов который может использоваться как сырье для получения высокоиндексного термогазойля или электродного кокса а также в качестве сырья процессов каталитического или гидрокрекинга и термокрекинга как без так и с предварительной гидроочисткой. Легкий вакуумный газойль используется преимущественно как разбавитель тяжелого гудрона. В тяжелом висбрекинг-остатке концентрированы полициклические ароматические углеводороды смолы и асфальтены. Поэтому этот продукт может найти применение как пек связующий и вяжущий материал неокисленный битум компонент котельного и судового топлива и сырье коксования.
Для повышения степени ароматизации газойлевых фракций и сокращения выхода остатка процесс висбрекинга целесообразно проводить при максимально возможной высокой температуре и сокращенном времени пребывания. Комбинирование висбрекинга с вакуумной перегонкой позволяет повысить глубину переработки нефти без применения вторичных каталитических процессов сократить выход остатка на 35 40 %.
В табл. 1.2 приведены материальный баланс (в % мас.) комбинированного процесса и висбрекинга гудрона 3 западно-сибирской нефти.
Таблица 1.2 Материальный баланс (в % мас.) комбинированного процесса и висбрекинга гудрона 3 западно-сибирской нефти
6 Характеристика исходного сырья готовой продукции и вспомогательных материалов
В зависимости от состава нефти варианта ее переработки и особых требований к мазуту и топливным фракциям состав продуктов установок висбрекинга может быть различным. На данном предприятии перерабатывается жетыбайская нефть. Характеристика которой приведена в табл. 1.3-1
Таблица 1.3 Физико-химические свойства нефти
- застывания (с обработкой)
- вспышки (в закрытом тигле)-
Давление насыщенных паров при 38 ºС мм.рт.ст.
- температура плавления ºС
- смол сернокислотных
Таблица 1.4. Потенциальное содержание фракций в нефти
Отгоняется до температуры ºС
Таблица 1.5 Характеристика средних дистилятов
Легкий керосиновый дистиллят
Температура отбора ºС
- начала кристаллизации
- вспышки в закрытом тигле
Таблица 1.6 Характеристика вакуумных дистиллятов и остатков атмосферной и вакуумной перегонки
Остаток атмосферной перегонки
(фракция выше 350 ºС)
Температура застывания ºС
Остаток вакуумной перегонки
Температура начала кипения ºС
Наиболее распространенный прием углубления переработки нефти — это вакуумная перегонка мазута и раздельная переработка вакуумного газойля (каталитическим и гидрокрекингом) и гудрона. Получающийся гудрон особенно в процессе глубоковакуумной перегонки непосредственно не может быть использован как котельное топливо из-за высокой вязкости. Для получения товарного котельного топлива из таких гудронов без их переработки требуется большой расход дистиллятных разбавителей что сводит практически на нет достигнутое вакуумной перегонкой углубление переработки нефти. Наиболее простой способ неглубокой переработки гудронов — это висбрекинг с целью снижения вязкости что уменьшает расход разбавителя на 20 25 % мас. а также соответственно общее количество котельного топлива. Обычно сырьем для висбрекинга является гудрон но возможна и переработка тяжелых нефтей мазутов даже асфальтов процессов деасфальтизации.
Технологическую схему установки висбрекинга определяет прежде всего назначение процесса. Существуют схемы позволяющие получать максимальное количество котельного топлива с минимальным количеством газа и бензина; имеются схемы обеспечивающие производство значительного количества легких дистилятов типа дизельного топлива. Одна из простых схем представляет собой нагрев исходного сырья (гудрона) в печи. Выходящий из печи продукт после охлаждения легким газойлем направляют в нижнюю (испарительную) секцию фракционирующей колонны а в верхней (ректификационной) секции пары разделяются на бензин газ и тяжелый газойль.
С начала 80-х годов все более широкое распространение получает вариант с выносными реакционными камерами. Использование указанных камер позволяет снизить глубину превращения сырья в реакционном змеевике и довести ее до нужной глубины в вертикальной цилиндрической камере. Продукт из печи поступает снизу а выходит через верх что позволяет значительно увеличить время пребывания жидкой фазы в зоне реакции.
Применение реакционных камер позволяет использовать нагревательную печь меньшей тепловой мощности что упрощает утилизацию тепла дымовых газов. Компания ABB Lummus G меньший размер печи; меньшие размеры оборудования для утилизации тепла дымовых газов; более низкий перепад давления в печи; меньший расход топлива; большие выходы продуктов и лучшая селективность; большая длительность межремонтного периода; меньшая чувствительность к авариям.
Одним из решающих преимуществ определяющих интенсивное внедрение процесса висбрекинга с реакционной камерой является уменьшение энергетических затрат.
Свойства котельного топлива получаемого висбрекингом в реакционной камере и трубчатом змеевике практически одинаковы но вследствие более высоких температур применяемых при проведении процесса в змеевике и наличия значительных перегревов пристенной пленки жидкости стабильность котельного топлива несколько выше при получении топлива висбрекингом в реакционной камере. Остатки висбрекинга могут также использоваться как компоненты сырья процесса каталитического крекинга производства кокса технического углерода и т.п.
РАСЧЕТ ОСНОВНОГО И ВСПОМОГАТЕЛЬНОГО АППАРАТОВ УСТАНОВКИ ВИСБРЕКИНГА
1 Материальный баланс установки (мощность установки время работы установки часовая производительность по сырью)
Мощность установки 580000 т. в год
Определяем число рабочих дней по формуле
Тэф= 365 – Ткап –Ттек
Тэф – эффективный фонд рабочего времени час.
Тэф= 365 – 30 дн. – 10 дн. = 325
Часовая производительность по сырью
Составляем материальный баланс исходя из практических данных.
Таблица 2.1 Материальный баланс установки висбрекинга
Производительность кгч
2 Расчет основного аппарата
Рассчитываем количество теплоты
Qувг=1264.14*3.4*490=2106057.24
Qб=319743*3.17*490=496656819
Qг=840255*3.02*490=124334094
Qг=6134609*29*490=87172793
Рассчитываем тепловой эффект реакции получения бензина
g – тепловой эффект (-1300 кДж)
Qреакц=319743*0.2*(-1300)=-8313318
Определяем размеры реакционной камеры.
Обычно применяют необогреваемые реакционные камеры в которых происходит углубление реакций
Скорость движения паров принимаем равной 01-03 мс.
Для определения диаметра камеры посчитаем снижение температуры и объем паровой фазы в камер. Высоту камеры определим по времени пребывания в ней паров.
Температура на входе в камеру
В реакционную камеру поступает газ.
Всего поступает Gобщ=743589
Реакция углубления Δх=20%
Критические параметры и молекулярная масса продуктов представлены в табл. 2.2
Таблица 2.2 Критические параметры продуктов висбрекинга
Рассчитываем количество бензина и газа которое образуется с учетом коэффициента углубления
Определяем температуру внизу камеры. Принимаем удельную теплоемкость продуктов крекинга
и составляем тепловой баланс реакционной камеры
где T2 – температура внизу камеры К
t2 = 758.5-273=485.5 ºC
Для определения объема паров продуктов на входе в камеру рассчитаем приведенные параметры
Тпр=763Ткр=763370=206
рпр=196ркр=196421=046
z=1 – коэффициент сжимаемости
Тпр=763Ткр=763558=136
рпр=196ркр=196296=066
Тпр=763Ткр=763721=105
рпр=196ркр=196194=101=1
Объем паров на входе в камеру
Аналогично определяем объем паров продуктов крекинга на выходе из камеры. Рассчитываем приведенные для газа бензина и газойля
zг=1 Тпр=(4855+273)370=209рпр=196421=046
zб=098Тпр=7585558=136рпр=196298=066
zгазойля=055Тпр=7585721=105рпр=196194=101
Принимаем скорость движения паров u=0.1 мс и рассчитываем сечение и диаметр реакционной камеры
Т.к. диаметр получился дробный то округляем его до ближайшего целого числа. Принимаем D=1 м.
Определяем скорость крекинга х2 при средней температуре в камере если известно. что скорость крекинга газойля (х1) при 490 ºС составляет 025% бензина в 1 мин
Продолжительность пребывания первой фазы в камере составит
Определяем высоту камеры
3 Расчет вспомогательного аппарата (теплообменника)
В данном проекте в качестве рассчитываемого аппарата выбран кожухотрубчатый теплообменник с плавающей головкой.
Теплоноситель гудрон (сырье). Висбрекинг остаток - мазут
Начальная температура Т1хол= 200оС = 473 К.
Конечная температура Т2хол = 320оС = 593 К.
Начальная температура Т1гор= 400оС = 673 К.
Конечная температура Т2гор = 250 оС = 523 К.
Плотность гудрона р204 = 0970 кгм3
Плотность гудрона при tгудрон.ср р1515=0970+5×0000541= 0973
Запишем уравнение теплового баланса аппарата в следующем виде:
G×(q1гор – q2гор)× = G×(q2хол – q1хол);
Определение тепловой нагрузки. Тепловую нагрузку рассчитываем по охлаждаемому гудрону.
Q=G×(44896–26536)= 71078.4×(44896–26536)=23100480 кДжч
Определяем ориентировочное значение поверхности теплообмена.
Fор. = Q (Δtср. K)= 23100480 (65 160) = 22212 м2 ;
К – коэффициент теплопередачи. К = 160 Вт(м2К)
Выбранный нами теплообменник имеет поверхность 873 м2. Поэтому для достижения необходимого поверхностного теплообмена мы принимаем 3 теплобменных аппарата со стандартной поверхностью теплообмена.
Диаметр D = 1200 мм;
Диаметр трубок dн = 0020;
Диаметр трубок dвн = 0016;
Поверхность теплообмена F = 873 м2;
Площадь сечение одного хода по трубам Sтруб. = 0049 м2;
Сечение межтрубного пространства Sм.тр. = 0113 м2.
Уточненный расчет состоит из определения требуемой поверхности теплообмена через коэффициент теплопередачи К. Который является функцией коэффициентов теплопередачи а1 и а2 а также термических сопротивлений стенки λ и термических сопротивлений загрязнений.
Коэффициенты теплопередачи αгор и αхол для горячего и холодного теплоносителя вычисляются по критериальному уравнению теплоотдачи в зависимости от числа Re.
Число Re для горячего теплоносителя.
где dвн – внутренний диаметр трубки dв = 0016 м; ср.гор. – средняя кинематическая вязкость ср.гор. = 0003094 Пас; S1 - площадь сечения самого узкого пространства = 0049 м2
dн – наружный диаметр трубки dн = 0020 м; ср.хол – средняя динамическая вязкость ср.неф. = 0017358 Пас
λхол – теплопроводность 0122 ВтмК
Определяем коэффициент теплопередачи αхол
Nuгор. = 024 Reгор.05 Prгор036 (Prгор Prст)025;
где (Prдт Prст) – примем за 1.
Prдт – критерий определяется по формуле:
ср.гор. – теплопроводность 0118 ВтмК
Сумма термических сопротивлений
где r1 r2 – сумма термических загрязнений ; ст λст – термическое сопротивление стенки. ст - толщина стенки трубки 0002 м. λст – коэффициент теплопроводности стенки для стали 168 ВтмК.
Определяем коэффициент теплопередачи.
Определяем требуемую поверхность теплообмена.
Fтр. = 23100480 ( 65 40) = 88848 м2
Гидравлический расчет
Определяем коэффициент трения.
где e = Δd = 0000020016=00125 – относительная шероховатость труб; Δ = 002 мм – высота выступов шероховатости
Определяем скорость в межтрубном пространстве.
Гидравлическое сопротивление межтрубного пространства.
где m – число рядов труб омываемых теплоносителем ; n – количество трубок.
Определяем скорость в трубном пространстве.
Гидравлическое сопротивление трубного пространства.
На основании расчетов определяем что выбранный теплообменник удовлетворяет требованиям.
ОРГАНИЗАЦИОННО-ЭКОНОМИЧЕСКАЯ ЧАСТЬ
Расчет себестоимости продукции:
Сс = Зк+Зэ+Зс+Зпр-Зпоб
Зк – капитальные затраты (руб.)
Зэ – эксплуатационные затраты (руб.)
Зс – затраты на сырье (руб.)
Зпр – затраты на внутреннюю перекачку (руб.)
Зпоб – стоимость побочной продукции (руб.)
Расчет капитальных затрат.
Ф - стоимость оборудования (руб.)
А – годовая сумма амортизационных отчислений (руб.)
МР – стоимость монтажных работ составляет 20% от стоимости оборудования (руб.)
КС – капитальное строительство составляет 30% от стоимости оборудования (руб.)
Зк = 13350 000+ 1599 500+(13350 000*20%)+(13350 000*30%)=
= 13350 000+ 1599 500+2 670 000+4005 000=21624 500руб.
Таблица 3.1 Стоимость оборудования
Наименование оборудования
Стоимость за единицу
Количество единиц оборудования
Определяем номенклатуру оборудования согласно технологической схемы и вычисляем общую стоимость.
Таблица 3.2 Годовая сумма амортизационных отчислений
Стоимость за единицу
Количество единиц оборудования шт.
Годовая сумма амортизационных отчислений
Вычисляем согласно формуле:
На – норма амортизации (%)
Т – срок службы оборудования (год)
Ф - общая стоимость оборудования (руб.)
На=(1Т)*100 = (135)*100 = 28 %
А= (На*Ф)100 =( 28*18000000)100 =504 000 (руб.)
На=(1Т)*100 = (115)*100 =6 7 %
А= (На*Ф)100 =( 67*1 000000)100 =67 500 (руб.)
На=(1Т)*100 = (110)*100 =10 0 %
А= (На*Ф)100 =( 100*3 800000)100 =380 000 (руб.)
На=(1Т)*100 = (125)*100 =4 0 %
А= (На*Ф)100 =( 40*3 450000)100 =138 000 (руб.)
А= (На*Ф)100 =( 100*2 400000)100 =240 000 (руб.)
На=(1Т)*100 = (110)*100 =100 %
А= (На*Ф)100 =( 100*2 700000)100 =270 000 (руб.)
Таблица 3.3. Сводная таблица капитальных затрат
стоимость оборудования
годовая сумма амортизационных отчислений
стоимость монтажных работ
капитальное строительство
Расчет эксплуатационных затрат.
Зэ=ФОТ+затраты на воду ээнергию+прочие расходы
ФОТ- годовой фонд оплаты труда (по рабочим специальностям и по окладам ИТР) (руб.)
затраты на воду ээнергию и прочие расходы- данные берутся в соответствии с расходными нормами ценами на данный момент (руб.)
Рисунок 3.1 - Расчет годового фонда оплаты труда
Расчет ФОТ по рабочим специальностям
Для того чтобы сделать расчет фонда оплаты труда по рабочим специальностям необходимо определиться с графиком рабочего времени и составить комплектацию бригад. Для непрерывного производства наиболее распространен 5-ти бригадный 3-х сменный график работы по 8 часов или 6-ти бригадный 4-х сменный график работы по 6 часов так же возможен график работы при работе вахтовым методом. График составляется на 15-30 дней самостоятельно.
При 3-х сменном графике работы.
Смены: 1-я 6.00-14.00
Расчет планового баланса рабочего времени ведется с учетом средней продолжительности отпуска невыходов по болезни невыходов в связи с выполнением государственных и общественных обязанностей внутрисменных потерь времени режимов работы установки. Расчет планового баланса рабочего времени на одного рабочего ведется по форме таблицы.
Таблица 3.4. Плановый баланс рабочего времени
Отпуска очередные и дополнительные Тот дни
Выполнение государственных обязанностей Тог дни
Планируемый эффективный фонд рабочего времени Тэф дни
Планируемый эффективный фонд рабочего времени Тэф час
Коэффициент использования рабочего времени Ки
Далее в расчетах используем данные из таблицы 3.4.
Таблица 3.5. Определение состава рабочей бригады
Наименование профессии
Продолжительность смены
Количество рабочих по сменам
Составление и комплектация рабочей бригады для выполнения работ на изучаемом оборудовании выполняется самостоятельно с учетом видов и специализацией работ.
Таблица 3.6. Определение списочного числа рабочих
Коэффициент использования рабочего времени Ки
Часовая тарифная ставка
Явочное число рабочих - то количество работников которые должны явиться для выполнения определенного задания в течение рассчитываемого периода времени.
Списочное число рабочих вычисляют с учетом явочного числа рабочих и коэффициента использования рабочего времени.
Часовая тарифная ставка берется по рабочим специальностям на данный момент времени (данные берутся по предприятиям изучаемой отрасли).
Определяем тарифный фонд заработной платы
Фтар = Счас*Тэф* Чсп
Счас – часовая тарифная ставка руб.
Чсп – списочная численность рабочих чел.
Определим среднюю часовую тарифную ставку
Счас =( Чсп2* Счас2+ Чсп3* Счас3+ Чсп4* Счас4+ Чсп5* Счас5+ Чсп6* Счас6) Чсп
Счас =( 4* 8926+ 4* 7679+ 7*6682+ 3*5884+ 3*6682) 21=7185руб
Фтар = 7185*1524* 21=2299 48740 руб.
ПР – сумма премий руб.
П – установленный размер премии по действующему положению премирования на предприятии (40%).
ПР=( 2299 48740 *40)100=919 79496 руб.
На долю ночных часов приходится 13 часть отработанного времени за каждый ночной час доплачивается 40 % от тарифной ставки.
D ноч =13* 2299 48740 *04=306 59832 руб.
На долю вечерних часов приходится также 13 часть отработанного времени. За каждый вечерний час доплачивается 20 % от тарифной ставки.
D веч =13* 2299 48740 *02=153 29916 руб.
- за праздничные часы
D пр= Счас* Тпр * Тсм* Псм* Чяв
D пр= 7185* 13 *8* 3* 18=403 50960 руб.
Тпр – число праздничных дней в году
Тсм – продолжительность смены в часах.
Псм – количество смен.
Чяв – явочное число рабочих в смену.
Определяем основной фонд заработной платы
Фосн=Фтар + ПР + D ноч + D веч + D пр
Фосн=2299 48740 + 919 79496 + 306 59832 + 153 29916 + 403 50960 =4082 68944 руб.
- оплата дней отпуска производится из расчета среднемесячной зарплаты за год и рассчитывается по формуле
Dотп= (Фосн Тэф)* Тот
Dотп= (4082 68944 254)* 29=46613383 руб.
Тэф – эффективный фонд рабочего времени дни.
Тот – продолжительность отпуска дни.
- оплата дней выполнения государственных и общественных обязанностей:
Dог=(4082 68944 254)* 1=16 07358 руб.
Тог – планируемые затраты рабочего времени на выполнение государственных и общественных обязанностей дни.
Определим фонд дополнительной заработной платы
Фдоп= 46613383 + 16 07358 =482 20741 руб.
Определим доплаты по району:
Dр=( 4082 68944 + 482 20741)*15=6847 34528 руб.
– доплата по коэффициентам (07 – районный коэффициент 08 – северная надбавка) (для Республики Саха Якутия).
Определяем годовой фонд заработной платы
Фгод= Фосн+ Фдоп+ Dр
Фгод= 4082 68944 + 482 20741 + 6847 34528 =1141224213 руб.
Определяем отчисления в фонд социального страхования который для предприятия отрасли составляет 356 % от годового фонда заработной платы.
Фсоц= (1141224213 *356)100=4062 75820 руб.
Годовой фонд оплаты труда по рабочим специальностям составит
ФОТраб=1141224213 + 4062 75820 =1547500033 руб.
Расчет ФОТ инженерно-технических работников
Фонд заработной платы ИТР и служащих рассчитывается на основе должностных окладов и доплат за вредные условия труда.
Таблица 3.7. Численность ИТР.
Наименование должности
должностной оклад До руб.
Фтар= (10000+8000)*11*11=21780000 руб.
До – месячной должностной оклад руб.
– коэффициент учитывающий вредные условия труда.
– число рабочих месяцев в году мес.
ПР=( 21780000 *60)100=13068000 руб.
П – установленный размер премии по действующему положению премирования на предприятии (60%).
-дополнительная заработная плата
Фдоп= (Фтар+ ПР)(11*245)*Dотп
Фдоп= (21780000 + 13068000)(11*245)*29=3749878 руб.
4 – среднее количество рабочих дней в месяц дни.
Dот – число дней отпуска.
- доплата по району:
Dр=( Фтар+ ПР +Фдоп)*15
Dр=( 21780000 + 13068000 +3749878)*15=57896817 руб.
Годовой фонд заработной платы с учетом районного коэффициента:
Фгод= Фтар+ ПР +Фдоп + Dр
Фгод=21780000+13068000 +3749878 +5789681 =96494695 руб.
Фсоц= (96494695 *356)100=34352111 руб.
Годовой фонд оплаты труда ИТР составит
ФОТИТР=96494695 + 34352111 =130846808 руб.
Определяем фонд оплаты труда производственного персонала установки и ИТР.
ФОТ= 1547500033 +130846808=1678346841 = 16783468 руб.
Расчет затрат на воду ээнергию топливо и прочие
Таблица 3.8 Затраты на электроэнергию воду топливо
Годовой переработки сырья тонн
Потребность на годовую программу
Топливо на технические цели
Расчет ведется по данным материального баланса с учетом цен на данный момент.
Размер эксплуатационных затрат составит
Зэ=16783468 +275038 800=291822268 руб.
Зс=10000*580000= 5800000000 руб.
Ц – оптовая цена за единицу руб.
Q – количество перерабатываемого сырья тонн.
Затраты на внутреннюю перекачку
Зпр= 10*580000 = 8700000000
Спер – себестоимость перекачки 1 тонны сырья (берется по данным предприятия)
Определим стоимость побочной продукции
Споб=1160*8000=9280000
Ц – цена за единицу побочной продукции руб. (берется по данным предприятия).
Q поб – объем производства того или иного вида побочной продукции
Определяем себестоимость продукции всего выпуск
Сс Зк+Зэ+Зс+Зпр-Зпоб Сс=21624500+291822268+5800000000+
+8700000000+9280000= 1482272610.
Расчет основных технико-экономических показателей
Производительность труда
Птр=58000021=276904762
Определяем фондоотдачу
Фо= Q Ф Фо=580000276904762=0.002094582
Ф – среднегодовая стоимость основных производственных фондов руб
Расчетная цена определяется по формуле
Вр=115*1482272610=1704613502
П=Вр - Сс П=1 704 613 502-1 482 272 610=222340892
Рентабельность производства
Р=(П Сс)*100 Р=22234408921482272610*100=15%
Со=капитальные вложенияСо=ВРкапз =
= 170461350213350000 = 130796631
Таблица 2.1. Основные технико-экономические показатели
Наименование показателей
Численность работающих
Себестоимость годового выпуска продукции
Рентабельность производства продукции
1 Промышленная безопасность
Промышленная безопасность опасных производственных объектов – состояние защищенности жизненно важных интересов личности и общества от техногенных аварий и катастроф и последствий указанных аварий.
Для достижения этих целей реализуется комплекс мероприятий направленных на обеспечение безопасности эксплуатации технических устройств.
Организация эксплуатирующая опасный производственный объект обязана проводить данный комплекс мероприятий по выполнению требований Федерального закона “О промышленной безопасности опасных производственных объектов” (116-ФЗ) для того чтобы условия на опасных производственных объектах эксплуатирующихся на предприятии соответствовали всем законодательным нормам принятым на территории Российской Федерации.
В наше время безопасность приобретает особое значение. Всевозрастающее количество опасных объектов и производств возводит проблему безопасности в ранг главных приоритетов для любого собственника. На данный момент во всех промышленно развитых странах принят особый порядок лицензирования строительства проектирования реконструкции эксплуатации и ликвидации опасных объектов что позволяет властям и соответствующим государственным органам осуществляющим контроль в данной сфере деятельности влиять на обеспечение безопасности.
Промышленная безопасность – область в которой действуют жестко установленные стандарты и нормы и ее обеспечение возможно только если все характеристики объекта проходят специальную экспертизу. Промбезопасность подразумевает определенные требования предъявляемые к объекту экспертизы. Экспертиза определяет в какой мере испытуемый объект соответствует этим требованиям.
По данным Национального союза страховщиков ответственности (НССО) который проведя оценку ситуации в стране на основании данных фонда деклараций промышленной безопасности Ростехнадзора предприятия нефтепереработки и нефтехимии относятся к группе самых высокорисковых. Проведенный им анализ результатов оценки риска крупых аварий позволил определить что по данным представленным в декларациях наиболее опасными по частоте крупной аварии являются объекты нефтепереработки и нефтехимии. Аварии на таких предприятиях способны нанести ущерб не только нефтяной компании но и превратить регион в зону экологического бедствия.
Исходя из Федерального Закона 116-ФЗ нефтеперерабатывающие заводы относятся к категории опасных производственных объектов поскольку здесь:
) получаются используются перерабатываются образуются хранятся транспортируются уничтожаются следующие опасные вещества:
а) воспламеняющиеся вещества - газы которые при нормальном давлении и в смеси с воздухом становятся воспламеняющимися и температура кипения которых при нормальном давлении составляет 20 градусов Цельсия или ниже;
б) окисляющие вещества - вещества поддерживающие горение вызывающие воспламенение и (или) способствующие воспламенению других веществ в результате окислительно-восстановительной экзотермической реакции;
в) горючие вещества - жидкости газы пыли способные самовозгораться а также возгораться от источника зажигания и самостоятельно гореть после его удаления;
г) взрывчатые вещества - вещества которые при определенных видах внешнего воздействия способны на очень быстрое самораспространяющееся химическое превращение с выделением тепла и образованием газов;
д) токсичные вещества - вещества способные при воздействии на живые организмы приводить к их гибели и имеющие следующие характеристики:
средняя смертельная доза при введении в желудок от 15 миллиграммов на килограмм до 200 миллиграммов на килограмм включительно;
средняя смертельная доза при нанесении на кожу от 50 миллиграммов на килограмм до 400 миллиграммов на килограмм включительно;
средняя смертельная концентрация в воздухе от 05 миллиграмма на литр до 2 миллиграммов на литр включительно;
е) высокотоксичные вещества - вещества способные при воздействии на живые организмы приводить к их гибели и имеющие следующие характеристики:
средняя смертельная доза при введении в желудок не более 15 миллиграммов на килограмм;
средняя смертельная доза при нанесении на кожу не более 50 миллиграммов на килограмм;
средняя смертельная концентрация в воздухе не более 05 миллиграмма на литр;
ж) вещества представляющие опасность для окружающей природной среды - вещества характеризующиеся в водной среде следующими показателями острой токсичности:
средняя смертельная доза при ингаляционном воздействии на рыбу в течение 96 часов не более 10 миллиграммов на литр;
средняя концентрация яда вызывающая определенный эффект при воздействии на дафнии в течение 48 часов не более 10 миллиграммов на литр;
средняя ингибирующая концентрация при воздействии на водоросли в течение 72 часов не более 10 миллиграммов на литр;
) используется оборудование работающее под давлением более 007 мегапаскаля или при температуре нагрева воды более 115 градусов Цельсия;
В результате производственной деятельности предприятий нефтегазодобывающего и перерабатывающего комплекса в окружающую среду поступают:
— углеводороды сероводород оксиды азота сажа оксид углерода сернистый ангидрид — при выбросах в атмосферу;
— нефть нефтепродукты пластовые минеральные воды синтетические поверхностно-активные вещества (СПАВ) ингибиторы коррозии и парафиноотложения деэмульгаторы химреагенты буровые сточные воды и буровой шлам — при сбросе в водные объекты и на рельеф местности.
Нефтеперерабатывающие заводы (НПЗ) являются источниками загрязнения окружающей среды в тех регионах на территории которых они расположены. Основными загрязняющими веществами выбрасываемыми в атмосферу предприятиями нефтепереработки являются летучие органические соединения (углеводороды) диоксид серы оксид углерода оксиды азота. Вклад прочих вредных веществ в валовой выброс невелик однако эти вещества более токсичны. Со сточными водами НПЗ в поверхностные воды поступает значительное количество нефтепродуктов сульфатов хлоридов соединений азота фенолов.
Выбросы вредных веществ отраслью в атмосферу имеют устойчивую тенденцию к снижению. С целью их сокращения на предприятиях отрасли с 2003 года проводятся природоохранные мероприятия что позволило снизить объем сбрасываемых в открытые водоемы загрязненных сточных вод в среднем на 8 % в год. Все производства предприятий нефтепереработки имеют локальные сооружения по очистке сточных вод. В то же время многие предприятия имеют на своем балансе биологические очистные сооружения и осуществляют очистку городских сточных вод.
В 2004 году произошли существенные изменения в структуре государственных органов управления Российской Федерации перераспределены их функции и полномочия. В ходе этой перестройки была сформирована Федеральная служба по экологическому технологическому и атомному надзору которая уполномочена Правительством Российской Федерации осуществлять государственное регулирование безопасности при использовании атомной энергии в области охраны окружающей среды и промышленной безопасности производственных объектов.
На сегодняшний день Служба уделяет особое внимание вопросам государственного регулирования деятельности предприятий нефтегазового комплекса каковыми являются:
- совершенствование нормативной правовой базы Российской Федерации в первую очередь за счет разработки и внедрения технических регламентов пересмотра норм и правил обеспечения безопасности разработки и внедрения системы нормативов в области охраны окружающей среды и т. д.;
- обеспечение функционирования системы государственного экологического контроля;
- совершенствование процедур проведения государственной экологической и иных экспертиз в первую очередь разработку и внедрение в качестве обязательных условий проведения оценок риска и вероятностного анализа безопасности в предпроектной и проектной документации на новую технику технологии вещества;
- совершенствование экономических механизмов стимулирования природоохранительной деятельности разработка нормативных актов по внедрению компенсационных выплат на реализацию природоохранных мероприятий для добросовестных хозяйствующих субъектов;
- внедрение в практику механизмов экологической сертификации товаров и услуг природоохранительного назначения;
- привлечение внебюджетных финансовых средств на решение природоохранительных вопросов в первую очередь платежей за негативное воздействие на окружающую среду остающихся в распоряжении муниципальных образований и субъектов Российской Федерации;
- организация выполнения обязательств Российской Федерации по международным конвенциям и договорам в области охраны окружающей среды в первую очередь по Базельской Стокгольмской конвенциям. Монреальскому и Киотскому протоколам;
- введение обязательных процедур государственной регистрации новых технологий техники химических веществ и т. п. с целью использования административных механизмов по внедрению наилучших технологий в области охраны окружающей среды замещению используемых опасных для окружающей среды веществ альтернативными аналогами внедрению «малоуглеродных» энергоносителей и возобновляемых источников энергии.
В соответствии с действующим законодательством в компетенцию Ростехнадзора входят следующие основные направления деятельности в том числе в областях связанных с недропользованием:
- подготовка проектов нормативных правовых актов и иных документов в сфере охраны окружающей среды в части касающейся ограничения негативного техногенного воздействия на окружающую среду;
- организация и осуществление государственного экологического надзора и контроля в области охраны окружающей среды (государственного экологического контроля);
- организация и проведение государственной экологической экспертизы;
- организация деятельности по исполнению обязательств Российской Федерации в соответствии с международными договорами и соглашениями в области охраны окружающей среды по вопросам относящимся к компетенции Службы;
- координация деятельности территориальных органов Службы по вышеуказанным направлениям.
2 Вредности и опасности на производстве. Техника безопасности
Конкретные проблемы охраны труда и техники безопасности для предприятия должны определяться в процессе анализа безопасности на рабочем месте или комплексной оценки вредности либо риска с помощью принятых методик таких как исследование с целью определения опасности изучение факторов опасности и работоспособности либо количественная оценка рисков. В качестве общего подхода планирование организационной деятельности по вопросам охраны труда и техники безопасности должно включать принятие систематического и структурного подхода для предотвращения и контроля физических химических биологических и радиологических опасных факторов представляющих угрозу для здоровья и безопасности.
Возникающие в процессе эксплуатации нефтеперерабатывающего предприятия вредные и опасные производственные факторы наиболее сильно влияющие на развитие профессиональной заболеваемости в первую очередь включают:
Безопасность производственного процесса
Атмосферу с недостатком кислорода
Химические вредности
Безопасность производственного процесса. Должна быть внедрена программа обеспечения безопасности технологического процесса в соответствии с конкретными характеристиками для отрасли включая сложные химические реакции использование опасных материалов (например токсичных химически активных горючих и взрывоопасных веществ) и многоступенчатые реакции.
Обеспечение безопасности технологического процесса учитывает следующие факторы:
анализ физической опасности материалов и реакций;
исследования по анализу опасности для рассмотрения химических основ технологического процесса и технической практики включая термодинамику и кинетику;
проверка профилактического технического обслуживания и поддержания механической целостности технологического оборудования и инженерных сетей;
обучение работников;
разработка рабочих инструкций и порядка аварийного реагирования.
Атмосфера с недостатком кислорода. Возможность выделения и накопления газообразного азота на рабочих местах может привести к возникновению удушливой атмосферы за счет вытеснения кислорода. Меры предотвращения и контроля для снижения риска выделения удушливого газа включают:
проектирование и установку системы вентиляции азота в соответствии с отраслевыми стандартами;
установку автоматизированной системы отключения которая может обнаруживать неконтролируемое выделение азота и предупреждать о нём (включая наличие атмосферы с недостатком кислорода на рабочих местах) включать принудительную вентиляцию и сводить к минимуму продолжительность выделения. Рабочие места на которых может возникать атмосфера с недостатком кислорода должны иметь свою систему контроля способную определять такие условия. Индивидуальные системы контроля должны быть предоставлены рабочим. Оба типа систем контроля должны подавать предупредительный сигнал тревоги при концентрации O2 в воздухе 195%.
внедрение порядка входа в ограниченное пространство с учетом конкретных опасных факторов на предприятии.
Химические опасные факторы. Выделение фтористоводородной кислоты монооксида углерода метанола и сероводорода может оказывать вредное воздействие на производстве. Утечка сероводорода может возникать с регенерации амина в установках обработки амином и на установках выделения серы. Утечка монооксида углерода может возникать в блоках каталитического крекинга в псевдоожиженном слое и крекинга остатка а также в секции получения синтез-газа установки для производства водорода. Смесь монооксида углерода с воздухом взрывоопасна и в ней может возникать спонтанное и взрывное возгорание. Сероводород представляет непосредственную опасность возгорания при его смешивании с воздухом.
На работников может воздействовать вредность при вдыхании (например сероводорода монооксида углерода летучих органических соединений (ЛОС) полициклических ароматических углеводородов (ПАУ) при обычной работе установки. Опасность для кожи может включать контакт с кислотами паром и горячими поверхностями. Факторами риска химического воздействия следует управлять на основе результатов анализа безопасности на рабочих местах и исследований по промышленной гигиене в соответствии с инструкциями по охране труда и техники безопасности. Меры защиты включают обучение работников систему разрешения на проведение работ использование индивидуальных средств защиты (ИСЗ) и систем обнаружения токсичных газов с тревожной сигнализацией.
Фтористоводородная кислота (HF) может воздействовать на работников в блоке алкилирования. Меры по охране труда включают:
снижение летучести HF с помощью добавления соответствующих присадок для понижения давления паров;
сведение к минимуму удерживания
проведение планировки предприятия таким образом чтобы ограничить площадь подверженную риску воздействия HF и облегчить пути эвакуации для работников;
четкая идентификация участков с риском воздействия HF и указание зон применения ИСЗ;
проведение процедур обеззараживания для работников на отведенных для этого участках;
введение буфера с безопасным расстоянием между блоком HF алкилирования другими технологическими блоками и границей нефтеперерабатывающего предприятия;
использование системы мокрой газоочистки для нейтрализации и удаления HF перед сжиганием в факеле;
использование бассейна для нейтрализации HF в стоках до их сброса в канализационную систему для загрязненных нефтепродуктами стоков нефтеперерабатывающего предприятия;
использование специального резервуара для сбора продуктов алкилирования и проведения регламентных измерений pH перед направлением на производство бензина;
обработка продуктов содержащих бутан и пропан в установках удаления фтора с глиноземом чтобы разрушать органические фториды с последующей обработкой щелочью для удаления всей оставшейся
транспортировка HF на установку и с нее должна осуществляться в соответствии с инструкциями для транспортировки опасных материалов
Пожары и взрывы. Риски возникновения пожара и взрыва создаваемые технологическим процессом включают случайный выпуск синтез-газа (содержащего монооксид углерода и водород) кислорода метанола и газов нефтепереработки. Выпуск газа нефтепереработки может привести к струйному горению если он возгорается в секции выпуска или вызвать взрыв облака топливо-воздушной смеси огненный шар или вспышки в зависимости от количества участвующего горючего материала и степени ограничения облака. Метан водород монооксид углерода и сероводород могут возгораться даже в отсутствие источника возгорания если их температура становится выше температуры самовозгорания составляющей соответственно 580°C 500°C 609°C и 260°C. Разлив горючей жидкости на нефтеперерабатывающем предприятии может вызвать возгорание разлитой жидкости. Опасность взрыва может быть также связана с накоплением паров в резервуарехранилище (например серной кислоты и битума).
Рекомендуемые меры для предотвращения и контроля рисков пожара и взрыва за счет технологического процесса включают:
Проектирование строительство и эксплуатацию нефтеперерабатывающего предприятия в соответствии с международными стандартами для предотвращения и контроля пожаро- и взрывоопасности включая обеспечение изоляции производственных помещений хранилищ инженерных сетей и безопасных участков. Безопасное расстояние можно определить на основе конкретного анализа безопасности для предприятия и с помощью использования международно признанных стандартов пожарной безопасности;
Обеспечение раннего обнаружения выпуска например контроль давления газа и жидкости в системе подачи в дополнение к обнаружению пожара по дыму и нагреву;
Оценку возможности скопления паров в резервуарах-хранилищах и введение методик профилактики и контроля (например азотная подушка для хранения серной кислоты и битума);
Исключение возможных источников возгорания (например путем такой конфигурации прокладки трубопроводов чтобы разлив не мог произойти на горячую трубу оборудование иили ротационные машины);
Обеспечение пассивных мер пожарной защиты в пределах моделируемой зоны пожара которые способны выдерживать температуру в течение времени достаточного для того чтобы оператор смог принять меры пожаротушения;
Ограничение участков на которых может происходить разлив следующими способами:
определение зон пожара и оборудование их дренажной системой для сбора и подачи случайных разливов горючих жидкостей на безопасный огражденный участок включая вторичное ограждение резервуаров-хранилищ;
установка пожарных и взрывных перегородок на участках где невозможно соблюсти соответствующее расстояние разделения;
проектирование системы канализации для загрязненных нефтью стоков так чтобы избежать распространения пламени.
Профилактика профессиональных интоксикаций начинается с выбора технологической схемы производства и аппаратурного ее оформления размещения оборудования (в здании или под открытым небом) планировки предприятия и отдельных производственных и бытовых зданий выбора методов очистки промышленных выбросов и удаление их в атмосферу канализацию и водоемы. В процессе эксплуатации производства проводится повседневная профилактика интоксикаций. При этом большое значение придается систематическому контролю воздушной среды который проводят центральные заводские лаборатории и санитарио-химические лаборатории санитарно-эпидемиологических станций. Полученные данные используются для принятия соответствующих мер и оценки опасности профессиональных интоксикаций в отдельных производствах.
Меры безопасности при ведении технологического процесса
Четкое ведение технологического процесса в соответствии с нормами технологического режима.
Постоянный контроль за герметичным состоянием оборудования трубопроводов фланцев сальников за работой приборов контроля и автоматики.
Четкое знание технологической схемы процесса внимательность при обслуживании установки.
Грамотная эксплуатация оборудования.
Знание и безусловное выполнение инструкций по охране труда и промышленной безопасности производственных инструкций инструкций по эксплуатации оборудования и должностных инструкций.
Соблюдение пpи pаботе с растворителем аммиаком следующих требований безопасности:
-нельзя допускать pазлив растворителя лотки и канализацию надо содержать в чистоте и исправности;
- вентиляция должны быть всегда в исправном состоянии и работать бесперебойно;
- все работники установки должны быть обеспечены соответствующей спецодеждой спецобувью защитными очками наушниками каской противога-зом. Спецодежда и средства защиты должны быть исправны. Стирка спецодежды должна производиться в прачечной по мере загрязнения;
-pаботы по pазбоpке фланцевых и pезьбовых соединений трубопроводов аппаратов набивке сальниковых уплотнений насосов производить имея при себе средства индивидуальной защиты. Во избежание попадания растворителя аммиака и МЭКа в глаза и лицо пpи pазбалчивании фланцевых соединений необходимо надеть очки защитные шпильки отпускают с противоположной стороны от работающего;
-все пpодувки и дpениpование pаствоpителя аммиака должны производиться c противогазом в положении «Наготове»;
-pазлитый pаствоpитель нужно немедленно убpать засыпать песком с последующей его утилизацией;
-пpи несчастных случаях обслуживающий пеpсонал должен уметь оказать пеpвую помощь постpадавшему до пpиезда медицинского пеpсонала или pаботников газоспасательного отpяда.
В случае аварии пожара на установке необходимо действовать согласно "Плана локализации аварийных ситуаций".
Индивидуальные средства защиты предназначены для предохранения органов дыхания и тела человека от вредного воздействия паров и жидкостей растворителя и нефтепродуктов от нежелательных влияний среды (температура влага).
Обслуживающий персонал установки должен пользоваться следующими средствами индивидуальной защиты выдаваемыми в соответствии с «Каталогом бесплатной выдачи специальной одежды специальной обуви и других средств индивидуальной защиты».
-для защиты органов дыхания от воздействия углеводородных газов аммиака паров нефтепродуктов используются фильтрующие противогазы с фильтром ДОТ;
-для защиты кожи тела используется спецодежда и спецобувь;
-для защиты головы от возможных травм используется защитная каска
Кроме того установка комплектуется:
-шланговыми противогазами ПШ-1 с комплектом масок и спасательным поясом с сигнально-спасательной веревкой для работ внутри аппаратов приямках колодцах;
-защитным щитком для защиты глаз при розжиге печей;
-аварийным запасом фильтрующих противогазов с фильтром ДОТ и шланговым противогазом ПШ-1;
-медицинской аптечкой с необходимым набором медикаментов для оказания первой помощи пострадавшему.
Всем работникам установки в соответствии со статьей 222 Трудового кодекса РФ выдается молоко по установленным нормам либо компенсируется денежной выплатой в размере стоимости молоко
Таблица 4.1 Средства индивидуальной защиты работающих
Профессии работающих
Средства индивидуальной защиты
Наименование и номер НТД
Срок службы защитных средств
Периодичность стирки химчистки
Оператор технологической установки
Общезаводской перечень норм бесплатной выдачи рабочим и служащим
спец.одежды спецобуви и
загрязнения средств защиты
Куртка хб на утепляющей прокладке
Брюки хб на утепляющей прокладке
Плащ непромокаемый (деж.)
Машинист технологических насосов (горячих холодных)
Костюм хб на утепляющей прокладке
Рукавицы комбиниров.
Фартук прорезиненный
Согласно ГОСТ 12.4.011 на установке средствами коллективной защиты работающих являются:
-средства нормализации воздушной среды производственных помещений и рабочих мест: Приточная и вытяжная вентиляция во всех помещениях; аварийная вытяжная вентиляция в помещениях насосной аммиачной компрессорной в кристаллизаторном и фильтровальном отделениях. На случай возникновения пожара у эвакуационных выходов перусмотрено дистанционное отключение (единой кнопкой) всех обслуживающих эти отделения систем вентиляции. Подача в помещения теплого воздуха подогреваемого калориферами; паровые приборы отопления;
-средства нормализации освещения производственных помещений и рабочих мест (естественное освещение через световые проемы и световые фонари в производственных помещениях искусственное освещение электрическими лампами накаливания люминесцентными лампами ртутными лампами типа ДРЛ);
-средства защиты от поражения электрическим током от вторичных проявлений молнии (защитное заземление молниеотводы установленные на крышах производственных зданий);
-средства защиты от статического электричества (заземляющее устройство).
Требования пожарной безопасности – специальные условия социального и (или) технического характера установленные в целях обеспечения пожарной безопасности законодательством Российской Федерации нормативными документами (ППБ-01-03).
3 Охрана окружающей среды
Промышленные предприятия топливно-энергетического комплекса в том числе химической нефтеперерабатывающей и нефтехимической промышленности а также автомобильный транспорт в настоящее время являются одним из наиболее крупных источников загрязнения природы: атмосферы почвы водоемов и морей.
По характеру влияния на природу все загрязнители можно разделить на химические механические тепловые биологические акустические (шумовые) электромагнитные и радиоактивные; по физическому состоянию — на газообразные жидкие твердые; по происхождению — на естественные (природные) и антропогенные.
Загрязнение атмосферы. Больше всего загрязняют окружающую среду металлургическая топливно-энергетическая нефтехимическая и химическая промышленности. Эти загрязнения весьма разнообразны и их состав зависит от качества сырья и технологии переработки.
Загрязнители в атмосфере (как и в гидро- и литосфере) распределяются неравномерно и имеют локальный характер. Загрязнения в воздушной среде распределены: над промышленными комплексами — 80 % над городами — 129 и над сельской местностью — 1. Характер распределения выбросов обусловлен излишней концентрацией производственных объектов в некоторых городах плохой техникой и технологией.
В местах сильного очагового загрязнения атмосферы при неблагоприятных погодных условиях в результате взаимодействия загрязнений и кислорода воздуха под действием ультрафиолетовых лучей может образоваться токсичный туман — «фотохимический смог». При этом наблюдается синергетический эффект — два загрязняющих компонента в результате реакции образуют более ядовитые вещества.
Загрязнение гидросферы. Исключительно сильное отрицательное влияние на природу оказывают также жидкие или растворимые в воде загрязнители попадающие в виде промышленных коммунальных и дождевых стоков в реки моря и океаны. Объем сточных вод сбрасываемых в водоемы мира ежегодно составляет ~ 1500 км3. Как правило для нейтрализации стоков требуется их 5 12-кратное разбавление пресной водой. Следовательно при современных темпах развития производства и непрерывно растущем водопотреблении (5 6 % в год) в самом ближайшем будущем человечество полностью исчерпает запасы пресных вод на Земле. К наиболее крупным источникам загрязнения водоемов относят химическую нефтехимическую нефтеперерабатывающую нефтяную целлюлозно-бумажную металлургическую и некоторые другие отрасли промышленности а также сельское хозяйство (например для целей орошения). Со сточными водами НПЗ в водоемы попадают соленая вода ЭЛОУ ловушечная нефть нефтешламы нефтепродукты химические реагенты кислые гудроны отработанные щелочные расворы и т. д. С талыми и дождевыми стоками в водоемы сбрасывается в огромных количествах практически вся гамма производимых в мире неорганических и органических веществ: нефть и нефтепродукты минеральные удобрения ядохимикаты тяжелые металлы радиоактивные биологически активные и другие загрязнители. В мировой океан ежегодно попадает в том числе более 15 млн т нефти и нефтепродуктов 200 тыс. т свинца 5 тыс. т ртути; 1 т нефти образует на поверхности воды пленку диаметром около 12 км. Нефтяная пленка существенно ухудшает газообмен и испарение на границе атмосфера-гидросфера в результате гибнут планктон водная флора рыбы морские животные и т. д. В последние годы участились аварии морских транспортных судов газовых и нефтяных скважин нефте- газо- и продуктопроводов железнодорожных поездов на промышленных предприятиях. Состояние гидросферы катастрофически ухудшается. Обостряется проблема водоснабжения населенных пунктов и городов (например фенольное загрязнение питьевой воды в количествах в десятки и сотни раз превышающих предельно допустимые концентрации и массовое отравление миллионного населения г. Уфы в марте-апреле 1990 г.). Загрязнение многих рек и водоемов достигает опасного критического состояния.
Загрязнение литосферы. В результате хозяйственной деятельности человека происходит непрерывное сокращение площадей земель пригодных для сельскохозяйственного использования а также их загрязнение промышленными и бытовыми отходами. Годовой объем таких отходов в мире составляет 35 млрд т из них 2 млрд т — в сельском хозяйстве 1 млрд т — в промышленности и 05 млрд т — коммунальный мусор. Из извлекаемых ежегодно из недр около 100 млрд т горных пород 98 % составляют отходы (в виде отвалов терриконов) занимающие огромные площади плодородных земель.
В районах интенсивной добычи нефти в ряде случаев наблюдаются существенное оседание поверхности земли (например в Мексике на 7 м) засоление почвенных вод и другие вредные воздействия.
Наиболее традиционно применяемый сегодня подход при организации борьбы против загрязнения окружающей среды — строительство очистных сооружений. Однако это целесообразно лишь для приспособления существующих производств к новым требованиям экологии поскольку приводит к значительному увеличению капитальных и эксплуатационных затрат и мало снижает реальные отходы. Главным направлением решения проблемы экологической безопасности следует считать экологизацию химических производств т.е. создание экологически чистых безотходных точнее малоотходных технологических производств в которых наиболее рационально и комплексно используются все компоненты сырья и энергии и не нарушаются нормальное функционирование окружающей среды и природное равновесие.
Можно выделить следующие основные направления в осуществлении экологически чистых технологических процессов в том числе нефтехимических:
Комплексное использование и глубокая переработка сырья. Производство должно быть как можно менее ресурсоемким (ресурсосберегающие технологии) осуществляться с минимумом затрат сырья и реагентов на единицу продукции. Образующиеся полуфабрикаты должны передаваться в качестве сырья другим производствам и полностью перерабатываться. Пример такого подхода — технология глубокой переработки нефти.
Оптимальное использование энергии и топлива. Производство должно осуществляться при минимальных затратах энергии и топлива на единицу продукции (энергосберегающие технологии) и следовательно тепловые загрязнения окружающей среды также минимальны. Энергосбережению способствуют укрупнение и энерготехнологическое комбинирование процессов; переход на непрерывные технологии; совершенствование процессов разделения; применение активных и селективных катализаторов позволяющих проводить процессы при пониженных температуре и давлении; рациональная организация и оптимизация тепловых схем и схем рекуперации энергетического потенциала отходящих потоков; снижение гидравлического сопротивления в системах и потерь тепла в окружающую среду и т. д. Нефтеперерабатывающие и нефтехимические предприятия являются крупными потребителями топлива и энергии. В их энергетическом балансе на долю прямого топлива приходится 43 45 % тепловой энергии — 40 42 % и электрической — 13 15 %. Полезное использование энергетических ресурсов не превышает 40 42 % что приводит к перерасходу топлива и образованию тепловых выбросов в окружающую среду.
Создание принципиально новых малоотходных технологических процессов. Этого можно добиться совершенствованием катализаторов техники и технологии производств. Малоотходные процессы более эффективны чем процессы с дорогостоящими очистными сооружениями. Экономичнее получать небольшое количество сильно концентрированных отходов которые можно перерабатывать или ликвидировать по специальной технологии чем большой объем сильно разбавленных отходов сбрасываемых в биосферу.
Создание и внедрение замкнутых систем водопользования включающих (или сводящих к минимуму) потребление свежей воды и сброс сточных вод в водоемы.
Обеспечение высокой эксплуатационной надежности герметичности и долговечности функционирования оборудования и всех систем производств. Сведение к минимуму или исключение вероятности аварий взрывов пожаров и выбросов отравляющих веществ окружающую среду. Разработка автоматизированных систем обеспечения экологической безопасности производств и комплексов.
Обеспечение высокого качества целевых продуктов используемых в народном хозяйстве. Экологически чистыми должны быть не только сами технологические процессы но и выпускаемые в них товарные продукты. Так моторные топлива должны удовлетворять возросшим экологическим требованиям по содержанию сернистых соединений ароматических углеводородов вредных присадок например этиловой жидкости и т. д.
Использование новых экологически чистых продуктов из альтернативных источников сырья например нефтяного и природных газов кислородсодержащих углеводородов (спиртов эфиров) и водорода в автомобильном транспорте.
АВТОМАТИЗАЦИЯ И СИСТЕМА АВТОМАТИЗИРОВАННОГО УПРАВЛЕНИЯ ПРОИЗВОДСТВА
Основной задачей автоматического управления процессом висбрекинга является обеспечение заданных показателей качества продуктов при минимальных энергетических затратах. Применение эффективных и надежных систем управления позволяет заметно повысить качество и увеличить выход продуктов на действующих установках без увеличения производственной мощности.
Измеряемыми величинами являются температура давление расход и уровень. На них приходится около 80 % всех измерений. Остальную часть занимают электрические оптические и другие измерения.
При измерениях используются различные измерительные приборы которые классифицируются по ряду признаков. Общей градацией является разделение их на приборы для измерения: механических электрических магнитных тепловых и других физических величин.
Классификация по роду измеряемой величины указывает какую физическую величину измеряет прибор (давление Р температуру Т расход F уровень L количество вещества Q и т.д.).
Исходя из признака преобразования измеряемой величины измерительные приборы разделяют на приборы:
а) непосредственной оценки;
По характеру измерения: стационарные и переносные.
По способу отсчета измеряемой величины: показывающие регистрирующие суммирующие.
Функциональные схемы автоматизации (ФСА) представляют собой технологическую схему с нанесенными на нее обозначениями контрольно-измерительных приборов. Технологическое оборудование чертится обычными линиями контрольно-измерительное – тонкими.
При этом первичные преобразователи (датчики) ХЕ (для упрощения буквой Х обозначен произвольный технологический параметр; вместо него может быть любое обозначение из принятых: температура Т расход F и т.д.) показывающие приборы установленные по месту XI (TI LI FQI PI и т.д.) и исполнительные устройства (клапаны задвижки и др.) показываются непосредственно на схеме. Существует несколько наиболее распространенных вариантов ФСА.
Вариант 1. Измерение и индикация технологического параметра по месту (XI). Обычно эта функция возлагается на один прибор в конструкцию которого входят датчик преобразователь и шкала (индикатор). Прибор отображает значение измеренного параметра непосредственно в месте измерения и часто не имеет возможности вывода сигнала на щит. К таким приборам относятся градусники стеклянные уровнемеры расходомеры-счетчики и т.д. Прибор обозначается одной окружностью (рис. 5.1 а).
Датчик измеряет технологический параметр преобразует его в какой-либо сигнал удобный для дальнейшей передачи (напряжение ток давление и т.д.) и передает его вторичному преобразователю. Вторичный преобразователь усиливает этот сигнал преобразует его в один из унифицированных сигналов и передает далее. Вторичный преобразователь может отсутствовать если например с выхода датчика уже поступает унифицированный сигнал. Показывающий прибор (XI) на щите у оператора получив сигнал отображает его на шкале (индикаторе). Если унифицированный сигнал токовый то показывающий прибор – амперметр если напряжение – вольтметр или потенциометр если пневматический – манометр.
Вариант 3. Измерение с индикацией и регистрацией (XIR или XR рис. 5.1 в). Принцип действия схемы аналогичен предыдущему варианту но вместо показывающего прибора на щите устанавливается регистрирующий. Как правило регистрирующие приборы одновременно показывают на шкале или индикаторе текущий регистрируемый параметр т.е. выполняют одновременно функцию индикации. Цепочка передачи сигнала:
Вариант 4. Сигнализация технологического параметра (XIA рис. 5.1г). Существуют показывающие приборы которые позволяют сигнализировать звуковым или световым сигналом факт выхода контролируемого параметра за допустимые пределы. Схема в этом случае будет аналогична варианту 2 но с выводом сигнала на лампочку или звуковой сигнал. Цепочка передачи сигнала:
Вариант 5. Измерение с индикацией регистрацией и сигнализацией на щите (XIRA рис. 5.1д и е). Для реализации перечисленных функций либо на щит устанавливается прибор одновременно выполняющий их либо используется комбинация схем из вариантов 3 и 4. В первом случае цепочка передачи воздействий:
Во втором производится ветвление сигнала с первичного или вторичного преобразователя на два прибора: на регистратор (XIR) и на прибор с сигнализацией (XIA):
Вариант 6. Регулирование (XIC рисунок 5.2а). Регулирование подразумевает наличие регулятора и управляющего воздействия на объект. На предприятиях нефтеперерабатывающей газовой и химической промышленности для реализации управляющих воздействий на объект управления в основном используются задвижки клапаны и другие устройства дроссельного типа. Принципы построения современных систем управления требуют при регулировании отображения регулируемого параметра для контроля за процессом регулирования поэтому дополнительно реализуется функция индикации:
Вариант 7. Регулирование регистрация индикация и сигнализация технологического параметра (XIRCA рис. 5.2б). Функции также реализуются с помощью единого устройства которое позволяет это сделать (например с помощью пишущего потенциометра КСП-4 со строенными блоками регулирования и сигнализации) либо с помощью нескольких устройств установленных на щите и реализующих каждое свою функцию. Ветвление сигнала также идет после первичного или вторичного преобразователя.
Далее несколько схем рассматривается более подробно.
Рисунок 5.3 Индикация и регистрация температуры
Индикация и регистрация температуры (TIR рис.5.3)
1-1 Термоэлектрический термометр тип ТХА гр. ХА пределы измерения от –50 °С до 900°С материал корпуса Ст0Х20Н14С2 марка ТХА-0515
1-2 Преобразователь термоЭДС в стандартный токовый сигнал 0 5 мА гр. ХА марка Ш-72
1-3 Миллиамперметр показывающий регистрирующий на 2 параметра марка А-542
Другие виды амперметров А-502 А-503 – показывающие А-542 А-543 – регистрирующие (последняя цифра – число параметров); А-100 – показывающий на 1 параметр.
Рисунок 5.4 Индикация регистрация сигнализация и регулирование температуры с помощью потенциометра
Индикация регистрация сигнализация и регулирование температуры с помощью потенциометра (моста) (TIRС электрическая ветвь рис. 5.4)
4-2 Автоматический электронный потенциометр на 1 точку со встроенными устройствами регулирования и сигнализации тип КСП-4 (или автоматический электронный мост типа КСМ-4 и т.д.)
4-3 Лампа сигнальная Л-1
4-4 Регулирующий клапан для неагрессивных сред корпус из чугуна предельная температура Т=300°С давление Ру = 16 МПа условный диаметр Dу = 100 мм тип 25нч32нж3
Рисунок 5.5 Индикация регистрация и регулирование давления
Индикация регистрация и регулирование давления (PIRC пневматика рис. 5.5)
3-1 Пневматический первичный преобразователь давления предел измерения 0 16 МПа выходной сигнал 002 01 МПа марка МС-П-2 (манометр сильфонный с пневмовыходом)
3-2 пневматический вторичный прибор на 3 параметра со станцией управления марка ПВ 10.1Э (с электроприводом диаграммной ленты)
3-3 пневматический ПИ-регулятор ПР 3.31
3-4 Регулирующий клапан для неагрессивных сред корпус из чугуна предельная температура Т=300°С давление Ру = 16 МПа условный диаметр Dу = 100 мм тип 25нч32нж
Наиболее распространенный прием углубления переработки нефти - это вакуумная перегонка мазута и раздельная переработка вакуумного газойля (каталитическим и гидрокрекингом) и гудрона. Получающийся гудрон особенно в процессе глубоковакуумной перегонки непосредственно не может быть использован как котельное топливо из-за высокой вязкости. Для получения товарного котельного топлива из таких гудронов без их переработки требуется большой расход дистиллятных разбавителей что сводит практически на нет достигнутое вакуумной перегонкой углубление переработки нефти. Наиболее простой способ неглубокой переработки гудронов - это висбрекинг с целью снижения вязкости что уменьшает расход разбавителя на 20 - 25 % масс а также соответственно общее количество котельного топлива. Обычно сырьем для висбрекинга является гудрон но возможна и переработка тяжелых нефтей мазутов даже асфальтов процессов деасфальтизации. Висбрекинг проводят при менее жестких условиях чем термокрекинг вследствие того что во-первых перерабатывают более тяжелое следовательно легче крекируемое сырье; во-вторых допускаемая глубина крекинга ограничивается началом коксообразования (температура 440-500 °С давление 14-35 МПа).
В данной работе для установки висбрекинга была выбрана реакционная камера. Применение реакционных камер позволяет использовать нагревательную печь меньшей тепловой мощности что упрощает утилизацию тепла дымовых газов приводит к меньшему количеству вырабатываемого водяного пара. По данным расчета была получена реакционная камера диаметром 1 м и высотой 14.6 м.
Преимущество процесса висбрекинга с реакционной камерой по сравнению с обычным: снижение капитальных затрат на 10-15%; меньший размер печи; меньшие размеры оборудования для утилизации тепла дымовых газов; более низкий перепад давления в печи; меньший расход топлива; большие выходы продуктов и лучшая селективность; большая длительность межремонтного пробега — до 1 года (время работы установки на потоке 330 дней); меньшая чувствительность к авариям; меньшее количество пара от утилизации тепла.
Одним из решающих преимуществ определяющих интенсивное внедрение процесса висбрекинга с реакционной камерой является уменьшение энергетических затрат.
В качестве наиболее эффективной конструкции зарекомендовали себя вертикальные цилиндрические реакционные камеры. Применение указанных камер позволяет снизить глубину превращения сырья в реакционном змеевике и довести ее до нужной глубины в камере.
Байков Н.М. Состояние мировых запасов нефти и газа и объемы их добычи Н.М. Байков Нефтяное хозяйство.- 2001.- № 2. -С. 96-98.
Левинбук М.И. О некоторых стратегических проблемах развития российского нефтегазового комплекса М.И. Левинбук. С.Д. Нетесанов. А.А. Лебедев. А.В. Бородачева. Е.В. Сизова Перспективы развития химической переработки горючих ископаемых: материалы конференции. - СПб. - 2006. - С. 11-23.
Дуплякин В.К. Современные проблемы российской нефтепереработки и отдельные задачи ее развития В.К. Дуплякин Рос. хим. журнал. -2007. -Т. № 4. - С. 11-22.
Ахметов С.А. Технология и оборудование процессов переработки нефти и газа: Учебное пособие С. А. Ахметов Т. П. Сериков И. Р. Кузеев М. И. Баязитов; Под ред. С. А. Ахметова. — CПб.: Недра 2006. — 868 с.
Ахметов С.А. Технология глубокой переработки нефти и газа: Учебное пособие для вузов. - Уфа: Гилем 2002. - 672 с.
Кирюшин О.В. Управление техническими системами: курс лекций. – Уфа: Изд-во УГНТУ 2004. – 116 с.
Александров И. А. Перегонка и ректификация в нефтепереработке. М.: Химия 1981 — 352 с.