Технология поверхностного монтажа печатных плат




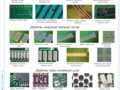
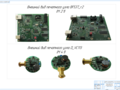
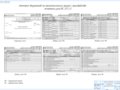
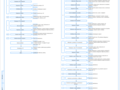
- Добавлен: 24.01.2023
- Размер: 53 MB
- Закачек: 2
Описание
Состав проекта
![]() |
![]() |
![]() |
![]() ![]() ![]() ![]() |
![]() |
![]() ![]() ![]() ![]() |
![]() ![]() ![]() ![]() |
![]() ![]() ![]() |
![]() ![]() ![]() ![]() |
![]() |
![]() |
![]() ![]() ![]() ![]() |
![]() |
Дополнительная информация
Карта техпроцесса.cdw

дефектов маски и пр.
Промывка платы для обезжиривания и активизации поверхности.
Удаление механических загрязнений.
закрепление платы на направляющих
совмещение платы с трафаретом
Нагрев пасты до рабочей температуры
контроль вязкости пасты
контроль посторонних включений.
Использовать паяльную пасту в зависимости от конкретных
требований к монтажу ПУ
Зарядка необходимых компонентов в питатели
установка и закрепление платы на направляющих
Контроль правильности и полноты установки SMD
устранение обнаруженных дефектов
Задание параметров термопрофиля
разогрев печи до рабочей
настройка скорости конвейера.
Контроль качества пайки SMD
устранение обнаруженных
Подготовка необходимой номенклатуры компонентов согласно
Использовать припой и флюс в зависимости от
конкретных требований к ПУ
Контроль правильности и полноты установки компонентов в
устранение обнаруженных дефектов установки и
Использовать для промывки реактивы в зависимости от
применяемой паяльной пасты и флюса
Только при необходимости
при установке микросхем в
Окончательный визуальный контроль
настройка при необходимости
Сборка в соответствии со сборочным чертежом
корпус и пр. при необходимости
Контроль качества нанесения паяльной пасты на контактные
Дополнительной контроль правильности и полноты установки
Испытания на устойчивость к климатическим
Схема адаптированного технологического процесса
производства под нужды опытного производства
Визуальный контроль печатной платы на отсутствие
Промывка платы для обезжиривания и активизации
поверхности.Удаление механических загрязнений.
Предварительная сборка клемников
мех.компонентов и сборочных узлов
Стандартная процедура: 3 цикла
-15 градусов (60минут); +45 градусов (5 минут);
только сушка (1 час)
проверка функционирования
Схема типового технологического процесса
производства печатных узлов
Схема технологического процесса производства
A L - группы отдельных операций
служащие для описания технологического процесса
в технологической документации
Технология поверхностного
монтажа печатных плат
Схема технологического
процесса производства
ВКРМ-02068999-47-15-151.013.ГМ
Входной контроль печатной платы
Очистка печатной платы
Подготовка трафаретного принтера
Нанесение паяльной пасты
Подготовка установщика SMD
Установка SMD-компонентов
Подготовка конвенционной печи
Оплавление паяльной пасты
Подготовка к установке ТНТ-компонентов
Размещение и пайка ТНТ-компонентов
Промывка и сушка печатных плат
Настройка и программирование
Окончательная сборка
Рентгеновский контроль печатных плат
Подготовка паяльной пасты
Соблюдение температурного профиля
Испытания на устойчивость к вибрациям
Нанесение влагозащитных покрытий
Разделение групповых заготовок
Очистка трафаретного принтера
Удаление остатков пасты и флюса с трафарета
Нанесение припойной пасты
Предварительная сборка
Промывка печатной платы
Размещение SMD компонентов
Размещение THT-компонентов
Нанесение защитного покрытия
Правильность установки SMD
Соответствие сборочному чертежу
Комплект документов.cdw

печатного узла BF_537_r2
МК - маршрутная карта
ОК - операционная карта
ВКРМ-02068999-47-15-151.013.ГМ
Технология поверхностного
монтажа печатных плат
Комплект документов на технологический
процесс производства печатного узла BF_537_r2
Типовые дефекты.cdw

выявляемые на различных
этапах технологического процесса производства
Отслоение контактной
Множественные дефекты
расстояние между дорожками
Перемычки между соседними
Вздутие и расслоение
Избыточное количество
Смазывание отпечатков
Растекание отпечатков
Отпечаток пасты больше
Шарики припоя возле
Отслоение влагозащитного
Внешний вид печатного
ВКРМ-02068999-47-15-151.013.ГМ
Технология поверхностного
монтажа печатных плат
Типовые дефекты печатного
выявляемые при входном контроле печатной платы
Волны на паяльной маске
Дефекты нанесения паяльной пасты
Дефекты пайки печатного узла
Дефекты некачественной отмывки печатных узлов
Пояснительная записка.docx
Федеральное государственное образовательное учреждение высшего образования
«ОМСКИЙ ГОСУДАРСТВЕННЫЙ ТЕХНИЧЕСКИЙ УНИВЕРСИТЕТ»
Кафедра «ЭЛЕКТРОНИКИ»
Допускается к защите
Зав. кафедрой электроники
ВЫПУСКНАЯ КВАЛИФИКАЦИОННАЯ РАБОТА
на тему: Технология поверхностного монтажа печатных плат
Студента: Савченко Андрея Анатольевича
Пояснительная записка
Шифр ВКР: ВКРМ-02068999-47-15-151.013.ПЗ
Направление подготовки: 11.04.04 «Электроника и наноэлектроника»
Консультанты: Руководитель:
(подпись дата) (ФИО) (подпись дата)
(название раздела) Савченко А.А.
(подпись дата (ФИО) (подпись дата)
(подпись дата) (ФИО)
на выполнение выпускной квалификационной работы магистра
Студенту:Савченко Андрею Анатольевичу
Факультет: Радиотехнический
Направление: 11.04.04 «Электроника и наноэлектроника»
Код квалификации:Степень или квалификация:
Тема ВКР:Технология поверхностного монтажа печатных плат
Руководитель:Вильшук В.А.
Ученое звание ученая степень руководителя: доцент
Место работы должность руководителя: доцент кафедры «Электроника» Радиотехнический факультет
Срок сдачи полностью оформленной работы на кафедру:
Задание на ВКР (перечень подлежащих разработке разделов): Обзор технологии монтажа печатных плат. Анализ современного состояния технологии поверхностного монтажа. Адаптация типового технологического процесса под опытное производство. Оптимизация термопрофиля оплавления паяльной пасты. Выбор и обоснование выбора технологического
оборудования для поверхностного монтажа оптимальное размещение оборудования. Разработка технологической документации процесса нанесения паяльной пасты.
Перечень графического материала с указанием основных чертежей и (или)
иллюстративного материала: Схема технологического процесса монтажа диаграмма термопрофиля лист технологической документации процесса нанесения паяльной пасты лист типовых дефектов изготовления печатных узлов внешний вид печатного узла.
Задание принял к исполнению:
Выпускная квалификационная работа содержит 142 страниц машинописного текста 73 рисунка 14 таблиц 107 использованных источников.
ПОВЕРХНОСТНЫЙ МОНТАЖ ПЕЧАТНАЯ ПЛАТА ПЕЧАТНЫЙ УЗЕЛ ТЕРМОПРОФИЛЬ ТЕХНОЛОГИЧЕСКАЯ ДОКУМЕНТАЦИЯ МАРШРУТНАЯ КАРТА ОПЕРАЦИОННАЯ КАРТА ТЕХНОЛОГИЧЕСКИЙ ПРОЦЕСС.
Объектом исследования является – технология поверхностного монтажа печатных узлов.
Цель работы – анализ развития технологий поверхностного монтажа адаптация технологического процесса производства печатных узлов выбор оборудования для организации опытного производства адаптация термопрофиля конвекционной пайки разработка пакета технологической документации на печатный узел.
По результатам анализа был определён комплекс технологий удовлетворяющий современному опытному производству.
По результатам выбора технологий произведена адаптация технологического процесса производства под нужды опытного производства выбрано технологическое оборудование.
Для практической проверки правильности выбора технологий а так же сопутствующего оборудования была произведена адаптация термопрофиля конвекционной пайки на примере узла BF_537_r2 произведена практическая сборка узла BF_537_r2 произведён технический контроль печатного узла составлен комплект технологической.
По результатам сборки и технического контроля узла BF_537_r2 можно заключить - адаптация технологического процесса производства выбор технологического оборудования а так же работы связанные с производством и техническим контролем на всех этапах проведены успешно.
ОПРЕДЕЛЕНИЯ ОБОЗНАЧЕНИЯ И СОКРАЩЕНИЯ
BGA - Ball Grid Array – массив из шариков
PLCC - Plastic Leaded Chip Carrier
QFN - Quad-flat no-leads
QFP - Quad Flat Package
SMD (рус. КПМ) - Surface mount device – прибор (компонент) монтируемый на поверхность
SMT (рус. ТМП) - Surface mount technology – технология монтажа на поверхность
THT - Through Hole Technology – технология монтажа в отверстие
ВТ – ведомость оснастки
ГОСТ – государственный стандарт
ЕС – европейский союз
ЕСКД – единая система конструкторской документации
ЕСТД – единая система технологической документации
РЭА – радиоэлектронная аппаратура
TAB - Tape Automated Bonding - монтаж кристаллов интегральных микросхем на ленточные носители
ТД – технологическая документация
ТИ – технологическая инструкция
ИС – интегральная схема
МВ – материальная ведомость
МК – маршрутная карта
НИР – научно-исследовательская работа
ОК – операционная карта
ОПК – оружейно-промышленный комплекс
ЭК – электронный компонент
ЭРИ - электрорадиоизделие
История развития анализ и современное состояние технологии поверхностного монтажа печатных узлов9
1 Исторический обзор развития печатных плат и технологий9
2 Обзор технологий и методов выполнения монтажа13
3 Современное состояние технологии монтажа печатных узлов18
Разработка технологического процесса производства печатных узлов в условиях опытного производства25
1 Технологические особенности опытного производства25
2 Адаптация типового технологического процесса монтажа под условия опытного производства26
3 Оптимизация термопрофиля оплавления паяльной пасты для опытного производства печатного узла BF_537_r256
4 Выбор и обоснование выбора технологического оборудования для организации опытного производства67
5 Разработка пакета документации на технологический процесс нанесения паяльной пасты на печатную плату BF_537_r2112
БИБЛИОГРАФИЧЕСКИЙ СПИСОК125
Основой большинства современных электронных устройств являются узлы выполненные на печатных платах объединяющие в себе электрически и механически значительную часть компонентов входящих в электрическую схему устройства.
Использование технологии поверхностного монтажа и специализированных компонентов при конструировании электронных устройств позволило в значительной мере уменьшить габариты и массу устройств практически полностью автоматизировать и значительно ускорить процесс сборки снизить конечную стоимость и повысить надёжность электронных устройств.
Свыше 50% изготавливаемых в мире компонентов приходится на долю компонентов монтируемых на поверхность. При этом более 80% электронной аппаратуры проектируется изначально с использованием поверхностно монтируемых компонентов.
Прогресс наблюдаемый в развитии электронной техники во многом обязан развитию и совершенствованию как элементарной базы так и методов конструирования и технологии. Наиболее полно это ощущается в области миниатюризации электронной аппаратуры с одновременным расширением её функциональности повышением быстродействия.
Технология поверхностного монтажа появившаяся более 40 лет назад в данное время является основным видом в технологии печатных узлов которые в свою очередь являются основой большинства современных электронных устройств.
История развития анализ и современное состояние технологии поверхностного монтажа печатных узлов
В современном мире монтаж большинства электронных схем выполняются с помощью печатных плат. На основе технологий изготовления печатных плат выполняются и сборные узлы микроэлектроники - гибридные модули которые содержат компоненты различной степени интеграции и различного назначения.
Многослойные печатные платы и электронные компоненты высокой степени интеграции позволяют снизить массогабаритные характеристики узлов электронной и вычислительной техники. На данный момент возраст печатного монтажа начитывает более ста лет [1 2 3].
1 Исторический обзор развития печатных плат и технологий
Прототипом всех современных печатных плат послужила разработка немецкого инженера Альберта Паркера Хансона в 1902 году. Его разработка была связана с быстро развивающейся тогда телефонией и значительно опередила время.
Метод разработанный Хансоном предполагал формирование рисунка на медной или бронзовой фольге путем его вырезания или штамповки. После этого сформированные элементы проводящего рисунка приклеивались к диэлектрику например пропарафиненной бумаге или другому подобному материалу.
Хансон уже тогда понимал важность увеличения плотности монтажа поэтому предложенная им технология предполагала приклеивание проводящего рисунка к диэлектрику с двух сторон. Кроме того изобретатель предусмотрел сквозные проводящие отверстия.
Сам Хансон указывал что проводники можно формировать гальваническим методом или посредством металлического порошка добавленного в подходящий клеящий носитель. Аналогичные идеи так же высказывал и Томас Эдисон.
Отвечая на запрос Франка Спрагу основателя компании Sprague Electric как "нарисовать проводники на бумаге" Эдисон письменно изложил несколько возможных подходов.
Первый из методов – сформировать рисунок посредством адгезивного полимерного материала и пока он не застыл посыпать его мелкодисперсным проводящим порошком (медным графитовым бронзовым и т.д).
Второй метод – нанесение рисунка на диэлектрик нитратом серебра с последующим восстановлением серебра.
Третий метод Эдисона предполагал использование для формирования проводящего рисунка золотой фольги.
Изложенные Эдисоном методы широко используются в современных технологиях. Например первая из них – это основа современных полимерных тонкопленочных технологий вторая описывает принцип современных методов нанесения покрытий путем химического восстановления [1 2 3].
Обобщая сказанное можно сделать вывод о том что все первые методы изготовления печатных плат были аддитивными [45].
В то же время в полиграфии со времен пресса Гутенберга для изготовления матриц применяется субтрактивный процесс – изображение формируется путем удаления ненужных фрагментов [45]. Первоначально это осуществлялось вырезанием на досках затем травлением на металлических пластинах.
Сам термин "печатная плата" – это прямой перевод английского полиграфического термина printing plate – печатная форма (матрица).
Первым запатентовал этот метод Артур Берри в 1913 году. Он предложил покрывать металлическую поверхность резистивным слоем формирующим рисунок а затем вытравливать незащищенные фрагменты поверхности. Вскоре подобный метод описал другой разработчик – Литлфилд [1 2 3].
В 1918 году швейцарский изобретатель Макс Скуп разработал промышленный метод газопламенного напыления металла.
Разработанная Скупом технология позволяла осаждать тонкие высокопроводящие слои через специальную маску снижая тем самым энергоемкость аппаратуры.
Патент американского изобретателя Чарльза Дукаса содержал уже описание и технологии травления и механизма металлизации проводников. Один из подходов Дукаса предполагал формирование проводящего рисунка методом электролитического осаждения меди серебра или золота на низкотемпературный металлический сплав через контактную маску. При нагревании незащищенные фрагменты сплава удалялись.
Другой подход Дукаса предполагал формирование в диэлектрике например воске канавок которые в дальнейшем заполнялись токопроводящими пастами и металлизировались электрохимическим способом. Дукас указывал что его изобретение направлено на формирование отдельных узлов схемы – в частности катушек индуктивности [1 2 3].
В 1933 году Эрвин Е. Франц разработал метод формирования проводящего рисунка на целлофане или другом аналогичном материале. Им использовались полимерные "чернила" с проводящим наполнителем – графитом. Затем на сформированный рисунок осаждалась медь.
Однако Франц прежде всего думал об упрощении изготовления трансформаторов и предполагал использовать вместо их обмоток многослойные конструкции из плат собранных в пакет.
Работы Франца заложили основы современных методов изготовления гибких печатных плат. Однако подлинным изобретателем печатных плат считается австрийский инженер Пауль Эйслер. Он занимался проблемой уменьшения размеров радиоаппаратуры и пришел к выводу что полиграфические технологии применимы и для производства печатных плат. В послевоенные годы он с женой отрабатывал на своей кухне технологию гальванического осаждения медной фольги и ее травления хлорным железом. Изначально Эйслер предполагал что основное применение его технологии – создание электронагревательных элементов расположенных на самых разных материалах и объектах.
В 1948 году он основал фирму Technograph Printed Circuits – предприятие по производству печатных плат после чего начал процесс патентования своей технологии в Великобритании и США.
В этом же году в США были утверждены нормы в соответствии с которыми все авиационное электрооборудование должно быть выполнено на печатных платах. С середины 50-х годов началось массовое внедрение печатных плат как основы всех бытовых электрических приборов. Новая отрасль техники и технологий начала активно развиваться [1 2 3]. Основной бурно развивающейся технологией стала технология поверхностного монтажа печатных узлов.
Технология поверхностного монтажа печатных узлов также называемая ТМП (технология монтажа на поверхность) SMT (surface mount technology) и SMD-технология (surface mount device) появилась в 60-х годах и получила широкое развитие в конце 80-х годов.
Данная технология является самым распространенным на сегодняшний день методом конструирования и сборки электронных устройств на печатных платах.
Предпосылками к появлению технологии поверхностного монтажа печатных плат явились растущие требования к миниатюризации и технологичности печатных узлов автоматизации процесса сборки узлов электронной техники удешевление производства а так же постоянный рост спроса и объёмов производства электроники.
Технология поверхностного монтажа печатных узлов объединила в себе преимущества различных технологий (планарной гибридных модулей и т.д) позволив тем самым существенно уменьшить массу габариты стоимость и время сборки печатных узлов улучшить электрические характеристики и повысить надёжность сборки устройств на печатных платах [6].
2 Обзор технологий и методов выполнения монтажа
Если рассмотреть все существующие технологии монтажа компонентов электронных устройств то можно выделить 2 основных метода выполнения монтажа – это объёмный монтаж практически не применяющийся в современной электронной технике и монтаж с применением печатных плат.
В свою очередь среди основных методов (способов) установки компонентов на печатные платы можно выделить 2 - это установка компонентов на поверхность печатной платы (SMD ТПМ) и установка компонентов в отверстие (ТНТ).
В современных электронных устройствах очень редко встречается только SMD или THT монтаж поэтому принято выделять так же третий метод (способ) установки – смешанный монтаж печатных плат. Классификация основных методов (способов) монтажа показана на рисунке 1.1.
Рисунок 1.1 – Общая классификация технологий установки компонентов на печатную плату.
Каждый из рассмотренных методов установки компонентов на печатную плату и способ монтажа обладает определёнными достоинствами и недостатками.
Объёмный монтаж в настоящее время применяется преимущественно при присоединении исполнительных механизмов с большой величиной протекающих в цепях токов; при соединении отдельных функциональных блоков иили узлов друг с другом а так же выполнении макетных образцов электроники невысокой сложности. Монтаж как правило выполняется полностью вручную.
Так же данный тип монтажа активно применяется в устройствах и блоках в тех случаях когда к блоку предъявляются жесткие требования в отношении наводок и взаимовлияний. В этом случае монтаж выполняется обычными жёсткими проводниками по кротчайшему пути после чего при необходимости проводники дополнительно закрепляются. Пример выполнения данного типа монтажа представлен на рисунке 1.2 [7 8].
Рисунок 1.2 – Пример выполнения объёмного монтажа
К основным достоинствам объёмного монтажа относятся:
- относительная простота выполнения монтажных работ;
- простота и дешевизна подготовительных операций;
- отсутствие необходимости в специализированном прецизионном технологическом оборудовании;
- относительная наглядность выполненных монтажных соединений;
- возможность построения компактных СВЧ устройств на современной элементарной базе с учётом требований электромагнитной совместимости;
- не требует относительно высококвалифицированного персонала в области обслуживания наладки и работе с применяемым оборудованием (кроме непосредственно монтажников).
К основным недостаткам объёмного монтажа относятся:
- низкая надёжность устройств без специальных мер герметизации и виброзащиты;
- низкая технологичность конечных электронных устройств (низкая плотность монтажа по отношению к более совершенным методам условно малая ремонтопригодность из-за малой наглядности расположения компонентов и сложном поиске необходимых электрических связей относительно высокая стоимость т.к. монтаж выполняется вручную и т.д);
- невозможность автоматизации большинства технологических процессов производства монтажных работ;
- длительный и затратный этап подготовки к выполнению монтажных работ;
- невозможность быстрого и качественного выполнения технического контроля;
- широкая номенклатура различных типов корпусов физических размеров выводов способов правил и требований к установке компонентов;
- нет повторяемости электрических характеристик узлов электронной техники [7].
В противовес объёмному монтажу можно поставить активно развивающийся в последние 4-5 десятилетий монтаж с использованием печатных плат.
Данный тип монтажа в соответствии с названием предполагает использование в качестве несущего основания и электросоединительной основы так называемые печатные платы [4 5 7].
Печатная плата (ПП) – это изделие состоящее из плоского изоляционного основания с отверстиями пазами вырезами и системой токопроводящих полосок металла (проводников) которое используют для установки и коммутации электрорадиоизделия (ЭРИ) и функциональных узлов в соответствии с электрической принципиальной схемой [4].
Монтаж с использованием печатных плат в данное время активно применяется во всех областях электронной техники начиная от мобильных телефонов персональных компьютеров и заканчивая аэрокосмической военной техникой и другой специализированной аппаратурой.
Сущность поверхностного монтажа с использованием печатных плат заключается в том что основная часть элементарной базы специальным образом адаптирована под технологический процесс установки компонентов на поверхность печатной платы (КМП-технология) что значительно повышает плотность монтажа а так же даёт возможность практически полностью автоматизировать процесс сборки и пайки.
В тех случаях когда компоненты установить на поверхность невозможно применяется технология установки компонентов в отверстия. Использование же самой печатной платы в качестве несущего основания совместно с электросоединительным функционалом значительно упрощает и удешевляет процесс конечной сборки и автоматизации производства т.к. нет необходимости в ручном соединении основной части компонентов друг с другом проводниками. Эту роль выполняет проводящий рисунок печатной платы.
К основным достоинствам монтажа с применением печатных плат можно отнести:
- значительное уменьшение габаритов устройства по сравнению с объёмным монтажом;
- повышение уровня автоматизации производства;
- высокая скорость установки компонентов при использовании специализированного оборудования;
- более высокая надёжность конечных устройств при строгом и точном соблюдении технологических процессов на всех этапах производства;
- высокая технологичность конечных устройств;
- возможность относительно быстрого выполнения контроля качества большинства паяных и не паяных соединений;
- высокая повторяемость электрических характеристик узлов электронной техники.
В качестве основных недостатков монтажа с использованием печатных плат можно выделить:
- высокую себестоимость изготовления печатных плат (особенно многослойных);
- сложность выполнения электроконтроля проводящего рисунка печатной платы (требуется специализированное технологическое оборудование. Визуально проконтролировать целостность всех соединений на современных печатных платах практически невозможно);
- необходимость в широкой номенклатуре специализированного технологического оборудования;
- необходимость в высококвалифицированном персонале для налаживания обслуживания и работы со специализированным оборудованием;
- более высокая стоимость оборудования и применяемых материалов.
Таким образом несмотря на присутствие ряда недостатков у монтажа с применением печатных плат данный тип монтажа в данное время является основным типом монтажа электронных устройств. Данные недостатки незначительны по сравнению с достоинствами применения печатных плат. Тем не менее экономически выгодно применять данный тип монтажа только в серийном производстве [7].
На рисунке 1.3а представлен пример выполнения монтажа с применением печатных плат и использованием только компонентов монтируемых на поверхность на рисунке 1.3б показан смешанный монтаж с применением печатных плат.
Рисунок 1.3 – Пример выполнения монтажа с использованием печатных плат.
(а – с использованием только КМП б – смешанный монтаж)
3 Современное состояние технологии монтажа печатных узлов
Узлы современных электронных устройств значительно отличаются от устройств разработки конца 80-х - начала 90-х годов прошлого века.
Поверхностныймонтаж компонентов на печатные платыпришел на смену устаревающей технологии монтажа в отверстия. Если рассмотреть подробно технологию поверхностного монтажа печатных плат то можно заметить что при монтаже установка компонентов производится на поверхность печатной платы что позволяет существенно автоматизировать монтаж увеличить его плотность и значительно сэкономить место. Кроме того существенно повышается технологичность изделия и уменьшается стоимость монтажных работ.
Можно сказать что технология поверхностного монтажа с использованием печатных плат (или просто технология поверхностного монтажа печатных узлов) на данный момент является одной из самых перспективных для производства электронной аппаратуры в особенности высокой степени интеграции. Это связано с тем что:
- новые технологии поверхностного монтажа привели к уменьшению габаритов компонентов в 3–6 и более раз;
- появились новые корпуса интегральных схем с малым шагом между выводами (05–065мм) корпуса с шариковыми выводами (BGA) новые малогабаритные дискретные компоненты и соединители;
- повысилась точность изготовления печатных плат увеличились возможности для разводки сложных устройств в малых габаритах.
- благодаря применению новых компонентов для поверхностного монтажа конечная масса изделия снизилась в 3-4 раза улучшилась помехозащищённость и быстродействие электронных устройств (благодаря уменьшению паразитной индуктивности и ёмкости компонентов);
- повысилась производительность труда на рабочих местах появилась возможность практически полной автоматизации процесса сборки и пайки печатных узлов;
- появление новой элементной базы позволяет говорить о возможности воплощения сложных систем на одной плате и даже на одном кристалле (технология систем на кристалле рис. 1.4).
Рисунок 1.4. – Пример выполнения системы на кристалле
Современное электронное устройство уже невозможно представить без применения технологии поверхностного монтажа печатных узлов.
Первые корпуса для поверхностного монтажа появились ещё в конце 50-х – начале 60-х годов прошлого века. Корпуса типа flat pack представляли собой металлический корпус с двусторонним расположением выводов. Отечественному разработчику такие корпуса известны как корпуса «типа 4» в которых было выпущено огромное количество ИС для применений в специальной технике.
Сегодня применяется огромное число корпусов поверхностного монтажа с шагом между выводами до 05мм и массивами шариковых выводов (BGA рисунок 1.5а).
Рисунок 1.5 – Различные корпуса для поверхностного монтажа высокой степени интеграции (а – BGA корпус б – QFP корпус в – PLCC корпус г – QFN корпус).
К группе поверхностно – монтируемых компонентов относятся пассивные чип-компоненты в корпусах различающихся по размеру и прочие ИС в базовых технологических корпусах PLCC (рис. 1.5в) QFP(рис. 1.5б) BGA (рис. 1.5а) QFN (рис.1.5г) и т.д. Сюда же относят специализированные технологии которые еще не стали стандартом электронной сборки или стали им относительно недавно (TAB flip-chip) и т.д.
Автоматизация процесса установки КМП стала возможной благодаря их корпусной chip структуре и поэтому сегодня практически нет необходимости устанавливать компоненты в отверстия на печатной плате. Традиционные компоненты монтируемые в отверстия - это наиболее узкое место в процессе установки их на плату поскольку практически полностью исключают возможность автоматизации процесса. Гораздо проще и быстрее автоматизировать процесс установки КМП чем монтаж традиционно монтируемых компонентов [9].
Таким образом сегодня методика монтажа компонентов на поверхность печатных плат и связанные с этим технологии продолжают динамично развиваться и совершенствоваться во всех направлениях начиная от миниатюризации компонентов и конечных узлов заканчивая всё время повышающейся степенью интеграции законченных устройств на единый кристалл.
Тем не менее несмотря на активное развитие как методик так и технологий поверхностного монтажа печатных узлов разработчики электронных устройств сталкиваются с рядом технических и технологических проблем. Перечислим кратко основные трудности стоящие на пути разработчиков при использовании КМП и соответствующих технологий и возможные пути их решения.
ТМП в отличии от монтажа в отверстия не предполагает компенсацию расширения ПП при нагреве за счёт выводов компонентов. В связи с этим поверхностный монтаж безвыводных компонентов на стеклотекстолитовые ПП приводит к снижению сроков службы элементов аппаратуры подвергающейся постоянным температурным воздействиям [10]. По этой причине подавляющее большинство отказов ИС при ТМП связано с разрушением сварного контакта между внутренним концом вывода и контактной площадкой на кристалле внутри корпуса ИС. Наиболее очевидным путём решения данной проблемы является переход от ТМП к технологии внутреннего монтажа.
Технология внутреннего монтажа — это монтаж «голых» кристаллов и других чип-компонентов в тело основы функционального радиоэлектронного узла. Корпусирование микросхем в данном случае не требуется так как роль корпуса выполняет сама основа радиоэлектронного узла. Основа исполняет так же и роль печатной платы после того как на ней будут сформированные коммутационные слои схемы радиоэлектронного узла [11 12].
При применении ИС монтируемых на поверхность с малым шагом выводов возникают сложности с проектированием ПП (необходимо спроектировать узкие дорожки с малым шагом) процессом нанесения паяльной пасты на контактные площадки ИС (сложно обеспечить необходимое количество паяльной пасты: если пасты слишком мало – некачественная пайка если слишком много – залипы между соседними выводами) установкой ИС (при недостаточной точности оборудования - смещение компонента) а так же непосредственно процессом пайки ПП (несовершенство термопрофиля пайки приводит к появлению дефектов пайки).
Одним из возможных путей решения проблемы нанесения паяльной пасты для данного типа ИС является применение технологии автоматической каплеструйной печати при нанесении паяльной пасты взамен трафаретной. [13 14]. Другим способом решения является применение многоуровневых разнотолщинных трафаретов [14 15].
Проблема отвода тепла выделяемого при высокой плотности монтажа на единицу площади значительно увеличивается что необходимо учитывать при проектировании ПП а так же при выборе типа паяльной пасты. Для решения проблемы эффективного теплоотвода можно использовать платы на основе металлической подложки например из инвара но в этом случае могут возникнуть трудности с обеспечением равномерной температуры пайки всех КПМ [13].
Брак нанесения паяльной пасты вызванный ошибками оператора является одной из главных трудностей в обеспечении хорошего качества паяного соединения в ТМП технологии. Около 60% всех дефектов пайки обусловлено низким качеством нанесения паяльной пасты на поверхность контактных площадок ПП. Одним из путей решения данной проблемы помимо повышения квалификации рабочего персонала является переход на полуавтоматические и автоматические трафаретные принтеры с одновременным введением в технологический процесс нанесения паяльной пасты средств автоматизированного контроля качества нанесения паяльной пасты [15].
Трудности связанные с точной установкой КПМ (особенно ИС с малым шагом выводов) вызванные несовершенством применяемого технологического оборудования. Основным методом решения данной проблемы является применение более дорогого технологического оборудования обеспечивающего высокую точность установки с автоматическим контролем процесса установки КМП [15 16].
Брак пайки вызванный некорректной установкой параметров температурного профиля печи а также несовершенством технологического оборудования является не менее важной проблемой стоящей на пути получения высокого конечного качества печатных узлов. Данный недостаток можно частично ликвидировать применением более совершенных конвекционных печей с контролем процесса пайки на каждом этапе процесса пайки [15 17].
Если обобщить вышесказанное то можно сделать вывод что несмотря на большой срок существования как самих ПП так и ТМП-технологии в настоящее время остаётся ещё множество нерешённых или частично решённых проблем связанных с технологическим процессом производства и монтажа печатных узлов. Часть данных проблем можно решить применением более совершенного технологического оборудования другую часть совершенствованием применяемых технологических процессов производства печатных узлов а так же повышением квалификации персонала но в реальных производственных условиях данные меры как правило носят комплексный характер.
Разработка технологического процесса производства печатных узлов в условиях опытного производства
1 Технологические особенности опытного производства
Согласно ГОСТ 14.004-83 опытное производство - это производство образцов партий или серий изделий для проведения исследовательских работ или разработки конструкторской и технологической документации для установившегося производства.
Опытное производство - важная стадия создания новых видов продукции или технологических процессов один из основных видов деятельности опытно-конструкторских или научно-исследовательских организаций. Опытное производство играет важную роль в высококачественном завершении опытно-конструкторской или научно-исследовательской работы подготовке проектно-конструкторской документации.
Опытное производство обычно включает: предварительное компьютерное моделирование узлов и технологических процессов в специализированных программных пакетах обеспечение эскизного макетирования для решения отдельных задач создание новых технологических процессов апробирование технической документации оказание технической помощи предприятиям в серийном освоении изделий и процессов.
Особенностями опытного производства является:
- сочетание большого количества одновременно выполняемых опытно-конструкторских и научно-исследовательских работ и как следствие широкая номенклатура различных электронных компонентов (ЭК);
- тесная связь между подготовкой производства и изготовлением конечных узловизделий;
- частые изменения конструкторской документации в особенности состава изделия и отсутствие полноценной технологической документации;
- продукция изготавливается обычно в единичном экземпляре либо небольшой серией;
- процесс разработки новых изделий сопровождается частыми изменениями состава изделияузла которые необходимо учитывать при оперативном планировании.
2 Адаптация типового технологического процесса монтажа под условия опытного производства
Как отмечалось ранее опытное производство обладает рядом специфических свойств в плане организации процесса производства печатных узлов и применяемых техпроцессов не позволяющих в полной мере использовать существующие типовые способы организации производства. В связи с этим произведём адаптацию технологического процесса производства печатного узла показанного на рисунке 2.1 под нужды опытного производства на практическом примере [19].
Данный типовой технологический процесс состоит из отдельных групп операций обозначенных латинскими буквами S P H C Z и служащих для описания полного технологического цикла конкретного изделия в технологической документации. Рассмотрим кратко основные группы операций входящих в типовой технологический процесс производства.
Входной контроль печатной платы. Среди стандартных процедур подготовки сборочно-монтажного процесса одно из важнейших мест занимает входной контроль комплектующих - печатных плат и компонентов. Наиболее полные критерии оценки качества изготовления печатных плат приведены в стандарте IPC-A-600G [21]. Для визуальной оценки отдельных параметров возможно также использование стандарта IPC-A-610D RU [22].
Рисунок 2.1 – Пример типового технологического процесса производства печатного узла
Наиболее распространенные дефекты печатных плат которые могут
быть обнаружены на этапе входного контроля – это механические повреждения печатной платы некоторые дефекты изготовления печатных плат (заполнение монтажных отверстий маской либо припоем смещение паяльной маски образование пустот под паяльной маской неудовлетворительное качество финишного покрытия разрыв проводников под паяльной маской и др.) изгиб и скручивание ПП различной природы неудовлетворительная паяемость различной природы (при условии проведения теста на паяемость) и другие [20]. На рисунке 2.2 показаны типовые дефекты ПП выявляемые при проведении входного контроля.
Рисунок 2.2 – Типовые дефекты ПП выявляемые при проведении входного контроля (а – механическое повреждение ПП б – дефектная металлизация в – разрыв проводников г – неудовлетворительная паяемость).
Таким образом входной контроль ПП является одним из первых важных этапов в технологическом процессе производства печатных узлов позволяющим ещё до начала физического производства исключить часть брака готовых печатных узлов путём проведения первичной отбраковки ПП.
Учитывая специфику опытного производства процесс контроля печатного узла должен производиться как можно более полно и по возможности на каждом этапе производства с привлечением методов автоматической оптической инспекции визуального контроля и методов неразрушающего контроля. Чем более полно будет произведён контроль всего цикла производства тем меньше вероятность появления брака в конечной продукции выше качество готовой продукции выше скорость отладки конечного производства быстрее адаптация применяемых техпроцессов под конкретные печатные узлы и т.д. В связи с вышесказанным следует считать целесообразным введение операций контроля на всех ключевых этапах производства печатных узлов в условиях опытного производства.
Очистка печатной платы. Одним из важнейших факторов влияющих на надёжность печатных узлов и качество пайки является чистота поверхности ПП перед сборочно-монтажным процессом.
В некоторых случаях процесс очистки ПП должен быть тщательно произведён непосредственно перед началом сборочно-монтажного процесса. Данная операция особенно актуальна в тех случаях когда на заводе изготовителе на ПП наносится консервационное покрытие а также когда есть необходимость удалить с поверхности ПП различные органические загрязнители и обезжирить поверхность контактных площадок для лучшего растекания припоя (остатки смазки потожировые отпечатки и т.д) удалить остатки мелких частичек диэлектрика оставшихся после операций механической обработки ПП [23].
Для консервации поверхности ПП обычно применяют аэрозольные распылители на основе флюсующих композиций (например спиртовой раствор канифоли). Нанесенный на поверхность платы консервирующий лак после высыхания образует прочную гладкую пленку которая препятствует окислению ПП не менее полугода в нормальных условиях при отсутствии вакуумной упаковки. Последующая пайка консервированных ПП проходит напрямую по обработанной поверхности без удаления лака. В особо ответственных случаях пайки лак необходимо удалить спиртом (этанолом) [24].
Для удаления остатков мелких частичек диэлектрика оставшихся после механической обработки и других сходных загрязнений возможно применение очистки струёй сжатого воздуха (а также ручное удаление загрязнений безворсовыми салфетками или салфетками из микрофибры) либо специализированным оборудованием очистки встраиваемым в производственную линию.
Производственная компания Teknek предлагает для данной цели линейку встраиваемого в производственную линию оборудования работающего по принципу механического удаления загрязнений подобного типа. По сути ПП прокатывается между парой силиконовых роликов покрытых специализированной клейкой лентой к которой прилипают остатки загрязнений. На рисунке 2.3 показан станок для очистки ПП CM40600UP1223 производства Teknek [25].
Рисунок 2.3 – Встраиваемый в линию станок для очистки ПП CM40600UP1223 производства Teknek
Обобщая вышесказанное подведём итоги:
В условиях опытного производства нецелесообразно применение для очистки ПП перед сборочно-монтажным процессом специализированного производственного оборудования т.к. необоснованно повышается стоимость конечной продукции (нет достаточных объёмов производства для обеспечения окупаемости оборудования; нецелесообразно подготавливать и переналаживать оборудование с учётом небольшого количества плат в партии при опытном производстве).
Для очистки ПП от механических загрязнений целесообразно применить безворсовые салфетки либо салфетки из микрофибры.
Для удаления консервации ПП а также остатков органических загрязнений целесообразно применить отмывку этиловым спиртом.
Применение данных мер очистки будет достаточной мерой в обеспечении необходимой чистоты поверхности перед началом сборочно-монтажного процесса печатных узлов в опытном производстве. Важно отметить что во избежание загрязнения плат в процессе отмывки потожировыми следами а также для защиты рук необходимо применять перчатки устойчивые к действию этилового спирта и остаткам загрязняющих веществ.
Нанесение паяльной пасты. В технологии поверхностного монтажа наиболее ответственным процессом оказывающим наибольшее влияние на дефекты возникающие при сборке печатных узлов является процесс нанесения паяльной пасты. Известно что 65 - 70% дефектов печатного узла возникает на этапе нанесения паяльной пасты или клея на печатные платы. Дефекты могут возникать из-за неточных недостаточных или избыточных отпечатков паяльной пасты недостатка или избытка флюса (неверно подобранная консистенция) неверно выбранной паяльной пасты ошибок в выборе скорости перемещения и силе прижима ракеля относительно трафарета наличия загрязнений на поверхности ПП перед процессом нанесения паяльной пасты [26].
Существует пять основных методов нанесения клеев флюсов и паяльных паст на печатную плату:
нанесение (перенос) материалов с помощью стержней;
дозирование материалов с помощью пульсационного нагнетательного насоса-дозатора;
дозирование материалов с помощью винтового насоса;
дозирование материалов с помощью поршневого насоса [27].
Каждый из перечисленных методов нанесения паяльной пасты на поверхность контактных площадок ПП обладает своими достоинствами и недостатками. Рассмотрим кратко основные особенности каждого метода.
Метод стержней - самый простой метод нанесения клея или флюса на печатную плату. Несмотря на то что один стержень может быть использован для нанесения клея либо флюса только в одном месте за один проход для нанесения материала в нескольких местах можно использовать матрицу стержней.
Метод стержней обычно используют для нанесения клеев и флюсов однако он плохо подходит для нанесения паяльной пасты т.к. стержень погружают в резервуар с материалом который будет наноситься на печатную плату после чего опускают на печатную плату в том месте где нужно нанести точку клея или флюса. Поверхностное натяжение заставляет часть клея или флюса стечь на плату. В процессе нанесения важно чтобы стержень не касался платы поскольку это нарушит форму точки материала. Для этого метода нанесения нужна относительно плоская и ровная подложка. На рисунке 2.4 схематически показан технологический процесс нанесения клея методом стержней. Аналогично производится нанесение паяльной пасты на поверхность контактных площадок ПП.
Рисунок 2.4 – Нанесение клея методом стержней
Главной проблемой метода стержней является использование открытых ванн с клеем или флюсом.
Любой из этих процессов приводит к изменению свойств материала т.к. клеи легко впитывают влагу из воздуха а у флюсов легко испаряется носитель (вода или спирт и др.) что влияет на количество жидкости на стержне и размер точки на ПП.
Трафаретная печать может использоваться для нанесения как клеев так и для паяльной пасты. Тем не менее низкая вязкость большинства флюсов препятствует их успешному нанесению этим методом. Метод трафаретного нанесения материалов на печатную плату основан на том что наносимый материал продавливается через отверстия в трафарете называемые апертурами.
Апертуры трафарета расположены строго над теми местами печатной платы на которые требуется нанести клей или паяльную пасту. Количество клея или паяльной пасты при нанесении способом трафаретной печати зависит от толщины трафарета консистенции наносимого материала скорости движения ракеля и силы прижима ракеля к трафарету. На рисунке 2.5 показан технологический процесс нанесения паяльной пасты методом трафаретной печати.
Рисунок 2.5 – Нанесение паяльной пасты методом трафаретной печати
Трафаретная печать является одним из наиболее широко используемых методов для нанесения паяльной пасты при поверхностном монтаже ПП. Данный метод имеет ряд недостатков:
Метод трафаретной печати должен выполняться за один проход. Если же паста была нанесена неправильно печатную плату тщательно отмывают перед повторным нанесением паяльной пасты;
Технология трафаретной печати подразумевает что поверхность печатной платы должна быть плоской и не иметь неровностей которые могут помешать плотному наложению трафарета на ее поверхность поскольку паста или клей будут продавливаться ракелем в апертуры;
Трафареты изнашиваются с течением времени в результате увеличивается число дефектов печати. Чем прочнее металл или сплав трафарета тем дольше срок его эксплуатации;
К основным достоинствам трафаретной печати можно отнести:
Высокую скорость нанесения клея либо паяльной пасты на ПП;
Более правильную форму отпечатка материала при отлаженном техпроцессе;
Меньшую вероятность заполнения материалом пространства между соседними контактными площадками и как следствие появления замыканий между соседними площадками при небольшом шаге контактных площадок;
Простоту налаживания и обслуживания технологического оборудования для трафаретной печати.
Пульсационный нагнетательный насос-дозатор так же относится к системам дозирования материалов для нанесения на печатную плату и позволяет наносить пасту с помощью приложения к резервуару с материалом импульса давления в течение определенного времени.
Из сопла насоса выбранного диаметра выдавливается точно контролируемое (дозируемое) количество клея или паяльной пасты и наносится на плату. Часто материал поставляется уже расфасованным в шприцы которые вставляют в монтажный автомат. На рисунке 2.6 показан пример шприца-фасовки с паяльной пастой.
Рисунок 2.6 – Шприц-фасовка с паяльной пастой
Как и в случае остальных технологий нанесения материалов свойства клея или паяльной пасты играют важную роль и определяют постоянство размеров точек на различных местах. При эксплуатации насоса-дозатора следует строго придерживаться требований к сроку годности материалов особенно тех что находятся внутри дозатора из-за их быстрого разложения на открытом воздухе в условиях сборочного цеха.
Автоматы с установленными поршневыми насосами-дозаторами способны наносить материалы на одной печатной плате в виде точек различного размера. Один из методов использования насоса-дозатора заключается в установке на одну головку сопел или шприцев различного размера и приложении одинакового импульса давления. Второй подход заключается в предварительном программировании времени и силы давления в насосе-дозаторе чтобы получить точки материала различного размера из одного и того же сопла или шприца. На рисунке 2.7 схематически показано устройство поршневого дозатора [28].
Рисунок 2.7 – Схематическое устройство поршневого дозатора
Основным недостатком данной технологии является более высокое время нанесения материала на все необходимые места по сравнению с трафаретной печатью но тем не менее данная технология обеспечивает большую гибкость с точки зрения строгого контроля количества и расположения точек клея или паяльной пасты.
В винтовом насосе для нанесения паяльной пасты или клея использован архимедов винт который через сопло выталкивает определенную порцию материала. Скорость и продолжительность поворота винта а также размер отверстия определяют количество клея или пасты нанесенной на печатную плату. Основные характеристики поршневого насоса ничем не отличаются от винтового за исключением некоторого различия в конструкции. На рисунке 2.8 схематически показано устройство винтового дозатора [29].
Рисунок 2.8 – Схематическое устройство винтового дозатора
Обобщая вышесказанное можно заключить:
Учитывая что качество нанесения паяльной пасты оказывает наибольшее влияние на дефекты возникающие в процессе пайки печатного узла целесообразно в технологический процесс подготовки паяльной пасты к использованию включить технологическое оборудование для качественной подготовки паяльной пасты к работе а именно оборудование для тщательного перемешивания паяльной пасты и контроля физических параметров паяльной пасты;
Учитывая специфику опытного производства в качестве основной технологии для нанесения паяльной пасты необходимо использовать метод трафаретной печати. Данный метод сочетает в себе высокую точность с высокой скоростью нанесения паяльной пасты и при этом менее требователен к физическим свойствам наносимой пасты. Сам же технологический процесс отладки производства и непосредственно нанесения паяльной пасты так же более прост т.к. количество параметров влияющих на конечный результат меньше (по сравнению с дозированием) обслуживание оборудования проще. В качестве дополнительной технологии возможно использование дозирования в отдельных ситуациях когда трафаретная печать технологически невозможна. В этом случае целесообразно выбирать оборудование для поверхностного монтажа с возможностью установки дополнительной дозирующей головки уменьшив тем самым суммарную стоимость оборудования и конечной продукции.
Установка и пайка КМП. Процессы установки и пайки компонентов монтируемых на поверхность (КМП) – это основные процедуры технологического процесса производства печатного узла. В зависимости от сложности монтажа печатного узла широты номенклатуры устанавливаемых компонентов количества изготавливаемых узлов компоненты на контактные площадки ПП могут устанавливаться либо с применением специализированных автоматических (автоматизированных) установщиков КМП либо вручную с применением монтажного оборудования и инструмента. Рассмотрим каждый способ установки КМП подробно.
Ручная установка КМП применяется в том случае когда необходимо изготовить небольшие партии или отдельные печатные узлы небольшой сложности а так же при проведении ремонта что делает нерентабельной полную автоматизацию техпроцесса производства. В случае ручного монтажа КМП установка и пайка могут производится как полностью вручную (с использованием пинцета специализированных термопинцетов а также монтажных столов увеличителей паяльных станций) так и с привлечением автоматизированного или ручного технологического оборудования (ручных либо автоматизированных манипуляторов для установки и пайки КМП). На рисунке 2.9 показан ручной манипулятор для установки КМП на ПП; на рисунке 2.10 показана ручная пайка КМП с использованием паяльной станции [30 31 32].
Рисунок 2.9 – Ручной манипулятор для установки КМП производства PRECITEC
Рисунок 2.10 – Ручная пайка КМП с использованием паяльной станции
Основным достоинством ручной установки и пайки КМП в штучных изделиях небольшой сложности является высокая скорость сборки печатного узла но при этом монтажники должны обладать достаточной для данного вида работ квалификацией. По мере увеличения сложности монтажа печатного узла широты номенклатуры КМП уменьшения размеров КМП ручная установка становится нерентабельной а иногда и невозможной. В этом случае необходимо применять автоматическую (автоматизированную) установку и пайку КМП. Основным недостатком ручной установки и пайки КМП является необходимость дополнительного высококвалифицированного штата монтажников РЭА и постоянное повышение их квалификации.
Автоматическая (автоматизированная) установка КМП на ПП применяется преимущественно для сложных узлов с широкой номенклатурой устанавливаемых компонентов при большом количестве печатных узлов в партии а так же при применении КМП установка которых вручную затруднительна либо невозможна.
В зависимости от размера применяемой элементной базы установщики КМП должны обладать достаточной для установки точностью при этом учитывая специфику опытного производства производительность станка уходит на второй план.
Основным достоинством автоматической (автоматизированной) установки КМП является высокая скорость и точность установки КМП а также исключение человеческого фактора в процессе установки компонентов. Основным же недостатком является необходимость в высококвалифицированном инженерном персонале т.к. сложное технологическое оборудование требует квалифицированного обслуживания программирования наладки и т.д.
Как известно КМП могут поставляться в специализированных лентах пеналах либо поддонах что накладывает некоторые ограничения на выбор необходимого технологического оборудования для установки КМП. На рисунке 2.11 показан пример автоматизированного установщика КМП; на рисунке 2.12 показаны примеры поставки КМП в различных тарах [5 33].
Рисунок 2.11 – Установщик КМП производства Autotronic
Рисунок 2.12 – Примеры поставки КМП в различных тарах (а – в лентах с намоткой на бобину б – в матричном поддоне)
При использовании в производстве автоматического (автоматизированного) монтажа КМП пайка может производится с использованием преимущественно конвекционных либо инфракрасных печей. После выхода в 2004 году директивы ЕС о запрете применения опасных для здоровья веществ (RoHS) наметился массовый переход на бессвинцовую пайку что так же необходимо учитывать при выборе технологического оборудования для пайки ПП. Данные вопросы будут подробно рассмотрены при выборе технологического оборудования для организации опытного производства. На рисунке 2.13 показана конвекционная печь для пайки ПУ оплавлением.
Рисунок 2.13 – Конвекционная печь для пайки печатных узлов оплавлением производства ESSEMTEC
Обобщая вышесказанное можно сделать следующие выводы:
Учитывая специфику опытного производства в парке технологического оборудования необходимо иметь как оборудование для автоматического (автоматизированного) монтажа и пайки КМП так и для ручной установки и пайки КМП.
Для осуществления качественной пайки печатных узлов различного назначения и сложности целесообразно оснастить производство конвекционной либо инфракрасной печью для пайки оплавлением т.к. данный тип печей позволяет наиболее точно подстроить параметры пайки под применяемые материалы и компоненты.
Для упрощения ручной установки и пайки КМП целесообразно оснастить производство специализированными монтажными столами и ручными манипуляторами для установки компонентов в BGA и им подобных корпусах при ремонте ПУ и невозможности установки компонентов на установщике КМП. При этом пайку данных ПП можно производить в конвекционной либо инфракрасной печи.
Отмывка печатных плат. Отмывка печатных плат как правило является заключительным этапом процесса поверхностного монтажа. Типовой технологический процесс отмывки ПУ можно разделить на несколько этапов:
-й этап - ультразвуковая очистка в отмывочной жидкости нагретой до температуры 60 °С с системой замкнутой механической фильтрации отмывочного раствора от частиц.
После очистки в течении 3-5 минут необходимо извлечь корзину с печатными платами из ультразвуковой ванны выдержать 1–2 минуты на воздухе чтобы дать отмывочной жидкости стечь.
-й этап - предварительное полоскание в дистиллированной воде. Полоскание осуществляется водой нагретой до той же температуры что и раствор для отмывки (60 °С). Эта вода должна меняться регулярно во избежание ее загрязнения отмывочной жидкости. Далее также необходимо извлечь корзину с печатными платами из второй ванны (для полоскания) задержать на 1–2 минуты на воздухе чтобы дать воде стечь.
-й этап - финишное полоскание осуществляется в ванне с воздушным барботажем (агитацией) или методом струйного воздействия в деминерализованной воде с системой замкнутой фильтрации и регенерации воды. Вода должна циркулировать между деионизационными колоннами или в избытке пополняться свежей деминерализованной водой наполняя ванну до краев. Использование горячей деминерализованной воды облегчает сушку но в этом случае необходимо убедиться в том что деионизационные колонны допускают применение горячей воды.
-й этап - сушка горячим воздухом [34].
Следует отметить что этапы отмывки ПУ могут производиться как на одном технологическом оборудовании так и раздельно т.е. ультразвуковая отмывка с отмывочной жидкостью в ультразвуковых ваннах а конечная отмывка например в оборудовании для струйной отмывки ПУ.
При выборе технологического оборудования для отмывки ПУ необходимо помнить что не для всех КМП допустимо использование ультразвуковой отмывки.
Одним из ярких примеров являются кварцевые резонаторы резонансная частота которых лежит в области генерируемых излучателем ультразвуковой ванны частот либо кратна им. В этом случае применение ультразвуковой отмывки недопустимо.
На рисунке 2.14 показана типовая ультразвуковая ванна для отмывки ПУ а также установка для струйной отмывки ПУ.
Рисунок 2.14 - Технологическое оборудование для отмывки ПУ (а - ультразвуковая ванна для отмывки ПУ производства Ultrasonic б – установка для струйной отмывки ПУ)
Необходимость удаления остатков флюсов и других загрязнений с поверхности ПУ вызвано следующими причинами:
Высокая рабочая температура ПУ. Это связано с тем что остатки флюсов на основе природной химически обработанной канифоли или искусственных смол до температуры около 100 °С являются хорошими изоляторами. Если происходит повышение температуры свыше 100 °С остатки флюса сначала размягчаются а потом начинают плавиться приводя к образованию карбоксильных ионов. В результате возникающей ионизации остатки флюса становятся проводником. Таким образом возникает опасность повышенных значений токов утечки и коротких замыканий [35 36 37 38].
Повышенная влажность. Проблема понижения поверхностного сопротивления имеет особое значение в современных условиях развития электроники т.к. уменьшаются расстояния между проводниками и компонентами а полупроводниковые компоненты развиваются от низкоимпедансных цепей к высокоимпедансным имея тенденцию к уменьшению потребляемой энергии. Поэтому уже малые токи утечки существенно нарушают работу элементов логики. Токи утечки могут возникать за счет присутствия ионных компонентов. Однако даже остатки канифольного флюса могут стать проводником при наличии тонкого слоя влаги. Токи утечки могут увеличиваться за счет появления в процессе пайки шариков припоя наличия остатков травильных растворов или солей припоя а также в случае роста металлических нитей.
Металлические нити - это волосоподобные кристаллы которые растут спонтанно без приложения напряжения. Обычно нити растут со скоростью 001–10 мм в год и имеют диаметр в несколько микрометров. Как правило тенденцию к образованию нитей имеют контактные площадки покрытые электрохимическим оловом. Устранение подобных загрязнений достигается путем применения специализированного оборудования отмывки и эффективных промывочных жидкостей [35 36 37 38].
Дендриты. Дендриты тоже представляют собой металлические нити или кристаллы которые растут на поверхности металла но по электролитическому механизму. Для роста дендритов необходимо наличие электролита и электрического напряжения. Скорость роста дендритов на катоде может достигать 01 мм в минуту. Аналогичный рост дендритов происходит и на аноде но значительно медленнее. Рост дендритов наблюдается на проводниках с покрытием из серебра меди олово-свинца золота золото-палладия. Область роста дендритов ограничивается зоной поверхностного ионного загрязнения и наличиея влаги. Внешний вид дендритов показан на рисунке 2.15 [35 36 37 38].
Рисунок 2.15 – Микрофотографии дендритов на контактных площадках и дорожках ПУ
Влагозащитные покрытия. Для предохранения от воздействия влаги и агрессивных сред печатные узлы часто покрываются влагозащитными покрытиями. При этом особое внимание следует уделять совместимости влагозащитных материалов с остатками флюсов. Если остатки флюса несовместимы с влагозащитным покрытием возможно ухудшение адгезии отшелушивание и отслаивание влагозащитных покрытий. Определяющим параметром является количество остатков флюса. Чем больше остатков флюса тем выше вероятность возникновения дефектов влагозащитного покрытия. На рисунке 2.16 показан пример плохой адгезии а так же отслаивания влагозащитного покрытия [35 36 37 38].
Рисунок 2.16 – недостаточная адгезия и отслоение влагозащитного покрытия на поверхности ПУ
Внешний вид изделия. Как правило флюсы не требующие отмывки оставляют малозаметные остатки незначительно ухудшающие внешний вид печатных узлов тем не менее в ряде случаев остатки флюсов приходится удалять по требованию заказчиков в косметических целях. На рисунке 2.17 представлен внешний вид ПУ перед отмывкой под увеличением [35 36 37 38].
Рисунок 2.17 – Внешний вид ПУ перед процедурой отмывки под увеличением
Высокое сопротивление контактов. Не удаленные остатки флюса могут покрывать тестовые площадки и контакты краевых разъемов. Так как канифоль и синтетические смолы при комнатной температуре являются хорошими изоляторами то тестовые точки могут иметь очень высокое сопротивление контактов препятствуя обеспечению электрического контроля [35 36 37 38].
Ручная пайка. Отечественные производители достаточно часто применяют жидкие «безотмывочные» флюсы для ручной пайки полагая что их остатки не требуют удаления. Однако большинство жидких флюсов не требующих отмывки специально разработаны для машинной пайки волной припоя - только этот способ пайки гарантирует выгорание и разложение активаторов флюсов не требуя обязательного удаления остатков после пайки. Зачастую необходимость удаления остатков жидких флюсов при ручной пайке вызвана только частичным выгоранием активаторов. Флюс при ручной пайке как правило наносится кисточкой и попадает не только в места подлежащие пайке но и вокруг них на паяльную маску соседние проводники и компоненты. Нагрев до температуры пайки производится локально только в местах образования паяных соединений. Весь остальной флюс не подвергается термической обработке и сохраняет свою активность [35 36 37 38].
Отмывка ПУ после монтажа а также контроль качества отмывки должны производиться как можно более полно и тщательно т.к. это позволит устранить многие дефекты возникающие при дальнейшей эксплуатации ПУ. ПУ необходимо отмывать всегда вне зависимости от применяемого флюса. Контроль качества отмывки ПУ должен производиться на каждом этапе технологического процесса отмывки ПУ.
Оборудование для отмывки ПУ должно позволять полноценно отмывать ПУ с КМП допускающими ультразвуковую отмывку так и с КМП не позволяющими применять ультразвуковую отмывку но при этом производительность оборудования уходит на второй план уступая место многоцелевому назначению и технологичности.
Нанесение защитного покрытия. Согласно [103] влагозащитные покрытия необходимы для защиты электронных изделий эксплуатируемых в жестких климатических условиях и подвергаемых воздействию влаги и высокой температуры пыли и агрессивных химикатов.
Влагозащитные покрытия предотвращают рост дендритов и образование оксидов приводящих к короткому замыканию и выходу из строя печатного узла. В электронной промышленности существует ряд способов нанесения покрытий которые эволюционировали от ручных способов до автоматических (автоматизированных) систем.
Одним из самых известных и широко используемых методов нанесения влагозащитного покрытия является погружение печатного узла в ванну с материалом. Однако в этом случае требуется чтобы конструкция печатного узла предусматривала возможность нанесения покрытия этим методом.
Компоненты на которые не должны наноситься влагозащитные покрытия (разъемы потенциометры предохранители и т.д.) требуется дополнительно маскировать. Для маскирования могут быть использованы различные материалы: лента латекс защитные колпачки. После полимеризации защитного покрытия маски удаляются.
Маскирование достаточно трудоемкий и ресурсоемкий процесс его сложно назвать удобным и экономичным. И несмотря на то что данный способ прост в использовании и не требует больших капиталовложений такие немаловажные факторы как неравномерная толщина покрытия по площади печатного узла загрязнение материала нестабильность вязкости необходимость маскирования вручную делают этот метод неспособным обеспечить требуемую повторяемость и качество. На рисунке 2.18 показан пример нанесения влагозащитного покрытия методом окунания [39 40].
Рисунок 2.18 – Нанесение влагозащитного покрытия методом окунания
Самый простой и на первый взгляд дешевый подход - нанесение покрытия кистью. Данный метод все еще используется в единичном производстве или при проведении ремонтных работ но недостатков у него гораздо больше чем достоинств: это большая трудоемкость низкая производительность различная толщина получаемого покрытия невозможность использования быстросохнущих материалов проблема нанесения покрытий под микросхемой. Очень часто в лак попадают волоски кисточки снижающие влагостойкость изделий. Волоски образуют в покрытии ПУ капилляры - своеобразные насосы для подкачки влаги к поверхности стеклотекстолита. На рисунке 2.19 показан пример нанесения влагозащитного покрытия кистью [39 40].
Рисунок 2.19 – Нанесение влагозащитного покрытия кистью
Самое широкое распространение получил метод нанесения влагозащитных покрытий распылением. Сущность метода заключается в распылении материала сжатым воздухом на поверхность изделия. Метод требует маскирования незащищенных участков и не отличается высокой повторяемостью так как зависит от квалификации оператора. Метод не безопасен по отношению к оператору и предъявляет жесткие требования к вентиляции помещения. От 20 до 30% лака не попадает на плату а накапливается в воздухе что приводит к вдыханию паров лака оператором. Данный метод затрудняет нанесение покрытий в теневые зоны и под корпуса интегральных микросхем. На рисунке 2.20 показан пример нанесения влагозащитного покрытия методом распыления [39 40].
Рисунок 2.20 – Нанесение влагозащитного покрытия методом распыления
На принципиально новый уровень качества выходит нанесение влагозащитных покрытий с применением автоматического селективного метода.
Наиболее передовые научные достижения были использованы в разработке оборудования селективного пленочного нанесения покрытия по запатентованной технологии американской компании Asymtek. Например высокоточная автоматическая система С-740 выборочно наносит влагозащитный материал на печатный узел который загружается в автомат вручную или по конвейеру.
Преимуществами данного метода нанесения являются:
Высокая точность за счет фирменной технологии пленочного нанесения.
Высокая повторяемость за счет высокоточных приводов и современных подсистем контроля вязкости ширины дозируемой струи и др.
Высокая производительность за счет исключения маскирования и проведения дополнительных подготовительных работ.
Высокая гибкость за счет простоты создания рабочих программ и перепрограммирования возможности использования различных модулей и типов материалов.
Экономичность за счет расходования строго нормированного количества материала.
Безопасность - процесс нанесения изолирован от окружающей среды что предотвращает загрязнение материала и обеспечивает комфорт работы оператора. На рисунке 2.21 показан пример нанесения влагозащитного покрытия селективным методом [39 40].
Рисунок 2.21 – Нанесение влагозащитного покрытия селективным методом
Этап нанесения влагозащитных покрытий является одним из важнейших этапов обеспечения дальнейшей высокой эксплуатационной надёжности и устойчивости ПУ к внешним климатическим и биологическим факторам.
Учитывая особенности опытного производства как основы НИР и фундамента будущих производств в технологический процесс опытного производства ПУ необходимо внести процесс нанесения влагозащитных покрытий и организовать участок нанесения покрытий с использованием специализированного технологического оборудования.
Учитывая что влагозащитные покрытия необходимы для защиты электронных изделий эксплуатируемых в жестких климатических условиях и подвергаемых воздействию влаги и высокой температуры пыли и агрессивных химикатов проектирование и испытание устройств работающих в данных условиях без участка влагозащиты невозможно. Организация данного участка на опытном производстве является целесообразной.
Таким образом ранее были рассмотрены все основные этапы типового технологического процесса производства печатных узлов а также произведена их адаптация под условия опытного производства. Учитывая особенности опытного производства и тот факт что для выполнения широкого спектра НИР в частности военного назначения для проведения испытаний печатных узлов блоков и изделий на устойчивость к климатическим и вибрационным нагрузкам необходимо иметь на производстве специализированный испытательный участок [41 42 43].
Соответственно организация данного участка на производстве целесообразна т.к. позволит расширить спектр выполняемых НИР а также провести самостоятельные испытания (без привлечения сторонних организаций) и повысить надёжность уже имеющихся разработок при необходимости. При выборе испытательного оборудования необходимо руководствоваться его технологичностью и многофункциональностью в ущерб производительности т.к. опытное производство не ставит под собой задачу выпуска больших партий изделий.
Кроме основного оборудования как правило на участке опытного производства присутствует такое вспомогательное оборудование как: установка для разделения групповых заготовок ПП счётчик компонентов принтер штрих-кодов ПК с комплектом оргтехники для выполнения вспомогательных организационных и технических задач ведения технической технологической производственной документации и т.д [44 45].
Обобщая сделанные выводы приведём схему адаптированного типового технологического процесса производства ПУ под нужды опытного производства. Данная схема показана на рисунках 2.22-2.23.
Рисунок 2.22 – Адаптированный технологический процесс производства ПУ под условия опытного производства
Рисунок 2.23 – Адаптированный технологический процесс производства ПУ под условия опытного производства
Рассматривая проектирование опытного производства необходимо принять во внимание что данное производство целесообразно параллельно использовать для выпуска небольших партий изделий для собственных нужд а также для выполнения коммерческих заказов на сборку влагозащиту испытание и контроль качества блоков и узлов РЭА т.к. позволит загрузить производственные мощности более полно и повысит рентабельность производства [46].
3 Оптимизация термопрофиля оплавления паяльной пасты для опытного производства печатного узла BF_537_r2
Создание оптимального температурного профиля оплавления является одним из важнейших факторов в обеспечении качества паяных соединений получаемых на ПП методом поверхностного монтажа. Температурный профиль непосредственно влияет на следующие характеристики готового ПУ:
Распределение температур по площади ПП.
Способность припойной пасты к смачиванию.
Очищающую способность флюса.
Микроструктуру паяных соединений.
Уровень остаточных напряжений в сборке и т.д [47].
Конвекционная пайка проводится в камерных или конвейерных печах. В первом случае отработка профиля пайки осуществляется путем изменения температуры внутри камеры со временем а во втором - перемещением платы по конвейеру через несколько зон печи: зону предварительного нагрева зону пайки и зону охлаждения каждая из которых имеет свою фиксированную температуру.
В ряде случаев используется пайка в инертной среде при которой происходит впуск азота в рабочую область печи для сведения к минимуму процесса окисления.
На формирование температурного профиля пайки оказывают влияние следующие факторы:
Применяемое технологическое оборудование;
Тип и размер используемых компонентов;
Площадь толщина а так же материал ПП.
Температурный профиль пайки состоит из четырех стадий: предварительного нагрева стабилизации (зоны температурного выравнивания) оплавления и охлаждения. Принято выделять традиционный и новый (линейный) профили пайки причем принципиальными отличиями последнего от первого являются большая продолжительность стадии предварительного нагрева и более короткая стадия стабилизации что приводит к более низкой скорости нагрева компонентов. На рисунке 2.24 показан типовой температурный профиль конвекционной пайки ПП оплавлением [48 49].
Рисунок 2.24 – типовой температурный профиль конвекционной пайки ПП оплавлением
При температуре более 90 °Сканифоль (смола) входящая в состав пасты начинает размягчаться а растворитель с высокой точкой кипения - испаряться. Размягчение канифоли приводит к уменьшению вязкости пасты а испарение растворителя - к увеличению вязкости. При высокой скорости нарастания температуры превалирует первый процесс что ведет к расползанию материала. При этом появится типичный для данного случая дефект - шарики припоя по бокам чип-компонентов показанные на рисунке 2.25 [48 49 50].
Рисунок 2.25 – Шарики припоя по бокам чип-компонента
При температуре порядка 150 °С начинается активное испарение растворителя максимально активизируется флюс. При данной температуре расплавляется припой и из отдельных шариков формируется единая масса. При этом припой под воздействием сил поверхностного натяжения растекается по очищенным флюсом металлическим поверхностям. На стадии охлаждения происходит отверждение припоя и канифоли. Рассмотрим каждую стадию более подробно.
Стадия предварительного нагрева. Данная стадия необходима для снижения теплового удара по электронным компонентам и печатным платам. На этой стадии происходит испарение растворителя из паяльной пасты. Температура предварительного нагрева лежит в пределах 95-130 °С а скорость изменения температуры для традиционного профиля пайки составляет от 06 до 40 °Ссек. Заметим что высокая скорость предварительного нагрева может вызывать повреждение компонентов разбрызгивание шариков припоя образование перемычек. Однако если скорость предварительного нагрева низка то может происходить окисление контактных поверхностей и частиц припоя [48 49 50].
Стадия стабилизации. Стадия стабилизации также называемая «стадия температурного выравнивания» позволяет активизировать флюсующую составляющую и удалить жидкость из паяльной пасты. Повышение температуры на этой стадии происходит очень медленно. Максимальная активация флюса происходит при температуре около 150 °С. Время стабилизации обычно лежит в пределах от 30 до 180 сек. В конце зоны стабилизации температура обычно достигает 150-170 °С.
Стадия оплавления. Для исключения чрезмерного роста интерметаллического соединения температура пайки должна не более чем на 30-40 °С превышать точку плавления паяльной пасты. Например для наиболее распространенных сплавов Sn62Pb36Ag2 и Sn63Pb37 температура пайки должна находится в пределах 205-225 °С.
Низкая температура пайки (195-205 °С) обеспечивает слабую смачиваемость особенно для компонентов с плохой паяемостью. Поэтому температуру на стадии оплавления устанавливают немного выше - в пределах 215-225 °С при скорости повышения температуры 2-4 °Ссек. Рекомендуемое время выше точки плавления составляет 30-60 сек. Для массивных плат это время может быть увеличено до 90-120 сек.
Высокая температура (240-260 °С) и время пайки более 120 секунд способствуют росту интерметаллического соединения. Чрезмерный рост интерметаллического соединения увеличивает хрупкость паяного шва и ухудшает его внешний вид [48 49].
С другой стороны согласно [51] температура пайки определяется исходя из оптимальных условий формирования паяного соединения при которых скорость вязкого течения припоя больше скорости поверхностной диффузии. Экспериментально установлено что температура пайки для этого условия должна быть выше температуры плавления припоя на 50 100 °С. Отсюда видно что пайка бессвинцовыми припоями при температуре ниже 280 °С не гарантирует надлежащего качества даже с слабоактивированными флюсами.
Применение таких высоких температур не может положительно сказаться на итоговом качестве образования паяных соединений из-за образования интерметаллических соединений ограниченной стойкости диэлектрика к нагреву снижения адгезии паяльной маски снижения поверхностного сопротивления изоляции из-за пиролиза канифоли а также риска увеличения непредвиденных химических реакций композиции самой пасты которые увеличиваются в 100 раз на каждые 10 °С согласно закону Аррениуса [51].
Таким образом правильный выбор температуры оплавления и длительности нахождения ПП в зоне оплавления является одной из основных задач оптимизации термопрофиля из соображений выбора оптимального баланса между качеством паяного соединения и вероятностью появления серьёзных дефектов ПУ.
Стадия охлаждения. Для обеспечения максимальной прочности паяных соединений скорость охлаждения должна быть максимальной. В то же время высокая скорость охлаждения может вызывать термоудар по электронным компонентам. С другой стороны медленное охлаждение так же приведет к интенсивному росту интерметаллического соединения делающего шов более твердым но хрупким.
Рекомендуется проводить охлаждение со скоростью 3-4 °Ссек. до температуры 130 °С. Ниже 130 °С скорость охлаждения может быть меньше так как она уже не влияет ни на качество паяных соединений ни на электронные компоненты.
Таким образом окончательный выбор режимов пайки проводится технологом исходя из конструкции и материала печатной платы типа и размеров компонентов количества и плотности размещения компонентов на печатной плате а также типа паяльной пасты. При выборе профиля пайки следует учитывать что реальная температура на плате в процессе пайки будет ниже заданной в печи. Разница между реальной и заданной температурами зависит от конструкции печи количества слоев и размера платы размера и плотности размещения компонентов [48 49].
Оптимизацию типового температурного профиля конвекционной пайки произведём на примере ПУ с кодовым шифром BF_537_r2. Оптимизацию произведём для 4-х зонной конвекционной печи BM-W430. На фото 2.26 показан данный ПУ на завершающем этапе сборки. Для проведения оптимизации типового термопрофиля следует выделить некоторые особенности данного ПУ:
На ПУ используется широкая номенклатура КМП различных типоразмеров но основную массу КМП составляют компоненты типоразмера 0603 а так же 12061210;
На ПУ устанавливаются КМП в массивном корпусе (кварцевый резонатор в металлическом корпусе катушка индуктивности);
На ПУ устанавливаются ИС нескольких различных типоразмеров (в том числе BGA);
На ПУ использованы компоненты с различным финишным покрытием (свинцовосодержащими припоями и бессвинцовыми);
Финишное покрытие ПП – ПОС-40;
На ПУ не используются компоненты относящиеся к группе термочувствительных.
Рисунок 2.26 – ПУ BF_537_r2 на завершающем этапе сборки
Так как конечные параметры термопрофиля зависят не только от применяемой элементной базы и особенностей ПП но и от применяемой паяльной пасты целесообразно на данном этапе определиться с типом применяемой паяльной пасты. В качестве паяльной пасты для пайки данного ПУ целесообразно применить пасту WS200 Multicore по следующим причинам :
Паста обладает высокой активностью флюса;
Прозрачные остатки флюса упрощают визуальный контроль паяных соединений;
Отличные клеящие свойства пасты хорошо подходят для удержания компонентов до пайки;
Паста обладает длительным срок жизни на трафарете а так же подходит для нанесения на контактные площадки КМП с малым шагом при высокой скорости нанесения;
Эффективна для разнообразных типов профилей оплавления;
Обладает высокой устойчивостью к растеканию при предварительном нагреве;
Пригодна к применению для пайки компонентов с малым шагом (до 04 мм);
Оставляет отпечатки высокого качества;
Активность флюса паяльной пасты обеспечивает высокую точность параметров технологического процесса и позволяет использовать пасту в крупносерийном производстве с применением компонентов и печатных плат с плохой паяемостью а также избежать появления сопутствующих пайке шариков припоя. [52 53].
Производитель данной паяльной пасты рекомендует использовать для пайки оплавлением термопрофиль показанный на рисунке 2.27.
Рисунок 2.27 – Рекомендуемый производителем термопрофиль для оплавления паяльной пасты WS200 Multicore
Учитывая что на данный ПУ устанавливаются компоненты с бессвинцовым покрытием а также тип финишного покрытия ПП в качестве отсчётной пиковой температуры целесообразно использовать температуру 237.5±2.5 °С что достаточно точно совпадает с рекомендуемой производителем пиковой температурой оплавления для выбранного типа паяльной пасты. Использование данной температуры не приведёт к выходу компонентов из строя т.к. на данном ПУ не используются термочувствительные КМП [52].
Следует учитывать что данная температура оплавления должна обеспечиваться на поверхности ПП а не поверхности нагревателя печи т.к. ПП находится на некотором расстоянии от нагревателя и температура на ПП всегда несколько ниже.
Как показывает практика при снижении скорости охлаждения ПУ с 5 до 3.5 °Ссекунду уровень дефектности ИС снижается с 5 до 0.01%. Учитывая наличие на данном ПУ ИС нескольких различных типоразмеров целесообразно использовать скорость охлаждения не более 3.5 °Ссекунду [52].
При длительном хранении ЭРЭ вне шкафов сухого хранения а ПП - без вакуумной упаковки с влагопоглотителем во внутренних слоях ПП и толще ЭРЭ возможно накопление влаги. Таким образом в процессе пайки при быстром нагреве на стадии предварительного прогрева данная влага может не успеть равномерно испариться что приведёт к «взрыву» ЭРЭ а также короблению ПП и её расслоению. Наиболее сильно данная проблема выражена у танталовых конденсаторов для поверхностного монтажа (которые используются в процессе сборки рассматриваемого ПУ). Кроме того производители и поставщики танталовых конденсаторов не рекомендуют использовать скорость нагрева выше 3°Ссекунду [49].
Согласно [106 107] активная стадия испарения воды происходит при температуре от 80 °С и выше. Соответственно данную температуру необходимо принять за точку перегиба температурного профиля в области 1 зоны нагрева. Нагрев до данной температуры должен производится со скоростью не более 3°Ссекунду. Свыше данной температуры необходимо понизить скорость нагрева для более равномерного испарения накопленной влаги и исключения термоудара КМП.
Как известно конвейер линейной конвекционной печи имеет равномерную скорость движения соответственно для обеспечения надёжной пайки КПМ ПП в зоне оплавления должна находиться около 50 секунд что рекомендовано производителем паяльной пасты [52 53].
Зная граничные рекомендуемые скорости нагрева и охлаждения пиковую температуру и время пайки а так же равномерность перемещения ПУ по конвейеру составим адаптированный температурный профиль для пайки ПУ BF_537_r2. Кроме того данный термопрофиль так же подходит для пайки типовых ПУ аналогичных BF_537_r2 например D_VC113. Адаптированный термопрофиль оплавления показан на рисунке 2.28а. На рисунке 2.28б – типовой ПУ D_VC113.
Рисунок 2.28 – (а - адаптированный температурный профиль для пайки ПУ BF_537_r2 б - типовой ПУ D_VC113)
4 Выбор и обоснование выбора технологического оборудования для организации опытного производства
Выбор технологического оборудования для участка поверхностного монтажа печатных узлов является одним из ключевых этапов при проектировании опытного производства. От выбора данного оборудования и его возможностей в наибольшей степени зависит дальнейшее функционирования будущего производства его рентабельность возможность выполнять широкий спектр НИР и т.д. При выборе оборудования общими основополагающими ключевыми факторами являются:
Технологические особенности опытного производства.
Трудоёмкость изготовления планируемых ПУ с учётом возможности работы в условиях постоянного развития и миниатюризации элементной базы.
Широта номенклатуры устанавливаемых КМП (как по количеству с которым оборудование может работать одновременно так и по геометрическим размерам корпуса).
Технологичность многофункциональность точность оборудования. Учитывая специфику опытного производства данные критерии являются наиболее важными по сравнению с производительностью. В условиях опытного производства производительность – это вторичный фактор не являющийся основополагающим как для крупносерийного производства т.е в соотношении производительность - технологичность точность многофункциональность необходимо выбрать второе.
Необходимость высококвалифицированного персонала для работы с технологическим оборудованием (программирование станков настройка налаживание и т.д.).
Высокая надёжность оборудования.
Наличие сервисной службы в России.
Итоговая стоимость оборудования.
Рассмотрим выбор технологического оборудования для каждого этапа поверхностного монтажа и испытания ПУ подробнее.
Подготовка паяльной пасты. Как отмечалось в главе 2.2 данной работы для подготовки паяльной пасты к работе в парк технологического оборудование целесообразно включить оборудования для перемешивания и контроля физических параметров паяльной пасты.
Необходимость её тщательного перемешивания связана с тем что при хранении происходит расслаивание паяльной пасты с оседанием шариков припоя на дно тары хранения. Необходимость же контроля физических параметров паяльной пасты необходима для определения пригодности паяльной пасты к использованию (как непосредственно готовность пасты к непосредственной работе в данный момент времени так и вообще физическую пригодность пасты) а так же для определения технологических режимов работы другого сопутствующего оборудования.
В качестве оборудования для перемешивания паяльной пасты выберем миксер паяльной пасты т.к. он позволяет перемешивать паяльную пасту сразу после хранения не дожидаясь её полного прогрева до комнатной температуры в течение 1-2 часов.
Основными критериями при выборе миксера паяльной пасты служат:
Возможность перемешивания пасты в стандартных банках;
Наличие дополнительных крепежей для надёжной фиксации банки с пастой и крышки исключающие непроизвольное открытие и загрязнение миксера;
Наличие дополнительного блокирующего замка исключающего травмы;
Возможность программирования времени перемешивания паяльной пасты;
Возможность крепления банок с пастой различной величины;
Конечная стоимость и надёжность оборудования.
В данное время на рынке миксеров паяльной пасты в основном представлены такие фирмы как Ningliante THINKY Genitec.
Фирма Genitec в основном представлена миксерами серии GAM-60 и GAM-60A технические характеристики которых представлены в таблице 1. На фото 2.29 представлен внешний вид миксера GAM-60 [56 57 58].
Таблица 1. Технические характеристики миксеров серии GAM
Скорость вращения кронштейна
Контейнер с паяльной пастой
Обычно загружается два контейнера (зажимы кронштейна приспособлены для разных типов контейнеров. Имеются дополнительные защёлки исключающие непреднамеренное открытие банки с пастой)
Потребление электроэнергии
Рисунок 2.29 – Внешний вид миксера паяльной пасты GAM-60
Миксеры паяльной пасты THINKY представлены на рынке в основном моделями SR-500 и ARE-250. Миксер SR-500 обеспечивает следующие функциональные возможности:
Быстрый нагрев паяльной пасты в процессе смешивания после хранения в холодильнике;
Достижение оптимальной вязкости и консистенции паяльной пасты в течение нескольких минут;
Удаление пузырьков воздуха в массиве пасты являющиеся причиной некоторых дефектов пайки ПУ;
Миксер рассчитан на смешивание стандартных банок пасты массой 500;
Возможно смешивание в миксере паяльной пасты в шприцах при использовании дополнительного адаптера.
На фото 2.30 показан внешний вид миксера паяльной пасты SR-500 [59 60].
Рисунок 2.30 – Внешний вид миксера паяльной пасты SR-500
Миксер модели ARE-250 позиционируется производителем как универсальная модель в линейке продукции которая подходит для исследований в медицине промышленности и научной отрасли. На фото 2.31 показан внешний вид универсального миксера ARE-250.
Данный миксер обеспечивает следующие технические возможности:
Максимальный объем перемешиваемого материала: 500 млили 1.1 кг;
Одновременные процессы смешивания дисперсии деаэрации;
Мембранные кнопки комфортные для пользователя обладающие высокой надёжностью;
Настройки таймера содержащие 5 программируемых шагов длякаждого профиля.
Ускорение 400 G создаваемое скоростью вращения миксера 2000 обмин;
Настраиваемую скорость вращения;
Высокую прочность инадежность узлов [61 62].
Рисунок 2.31 – Внешний вид универсального миксера ARE-250
Миксеры паяльной пасты фирмы Ningliante представлены на рынке в основном моделью NLTGP-848 которая обеспечивает следующие технические и эксплуатационные характеристики:
Применение уникальной технологии двойного перемешивания пастообразного материала (вокруг центра миксера 350 обмин а так же вокруг оси банки 600 обмин);
Угол наклона оси банки по отношению к вертикали 45 градусов;
Установкуу времени перемешивания от 0 до 99 минут;
Масса оборудования 48 кг;
Размеры системы: длина 430мм ширина – 460мм высота - 480 мм;
Электропитание 220 В 50 Гц 40 Вт;
Внутренний диаметр держателя (стакана) - 66мм;
Максимальный диаметр банки с паяльной пастой - 65мм;
Дополнительно возможно увеличение внутреннего диаметра держателя до 72мм.
На фото 2.32 показан внешний вид миксера паяльной пасты NLTGP-848 [63].
Рисунок 2.32 – Внешний вид миксера паяльной пасты NLTGP-848.
Обобщая приведённые технические и эксплуатационные характеристики можно сделать вывод что для нужд опытного производства достаточно возможностей миксера паяльной пасты производства Genitec марки GAM-60.
Несмотря на то что миксеры ARE-250 и NLTGP-848 обладают наилучшими характеристиками данные миксеры больше подходят для нужд медицинских и других подобных исследований. Их функционал будет излишним для опытного производства ПУ и не будет использоваться полностью но тем не менее он отразится на повышенной стоимости данного оборудования и конечной стоимости производства конкретного ПУ и рентабельности производства в целом. К тому же техническом описании данных моделей нет информации об установленных средствах дополнительной защиты банок с пастой от преднамеренного открытия а так же блокировок исключающих непреднамеренный травматизм персонала.
Технические характеристики SR-500 приведённые поставщиками на официальных сайтах недостаточны для полноценной оценки его функциональных возможностей и требуют уточнения у производителя. При наличии системы блокировок от непреднамеренного травматизма а так же наличия дополнительных крепежей исключающих открытие банок с пастой данный миксер может использоваться взамен GAM-60.
Для контроля физических параметров паяльной пасты в частности её вязкости воспользуемся предназначенным для этого специализированным контрольным оборудованием (вискозиметрами).
Рынок оборудования для контроля вязкости паяльных паст в основном представлен портативной моделью PM-2A а так же профессиональным многофункциональным оборудованием типа ВЗ-246 ВУ-М ИР-2 применять которое для условий опытного производства экономически необоснованно т.к. функционал данного оборудования использоваться не будет в полной мере [64].
Портативный компактный вискозиметр РМ-2А предназначен для быстрого определения вязкости технологических материалов различного назначения таких как паяльные пасты лаки компаунды. Вязкость исследуемого материала определяется пересчётом крутящего момента на валу двигателя с погружённой в материал специальной насадкой после чего полученные данные отображаются на ЖК-дисплее. РМ-2А обеспечивает технические характеристики представленные в таблице 2.
Таблица 2. Технические характеристики РМ-2А
Диапазон измерения вязкости Па·с
.500 Па·с (5000..500000 сП)
Диапазон скорости вращения шнека N обмин
Частота измерения 1сек
±10% от отображенного значения
Точность поддержания скорости вращения
±5% (при 10 или 30 обмин)
Аккумулятор с зарядным устройством
Учитывая компактность устройства простоту обслуживания и работы небольшую стоимость по отношению к профессиональным многофункциональным вискозиметрам использование РМ-2А следует считать целесообразным. На рисунке 2.33 показан внешний вид РМ-2А [65].
Рисунок 2.33 – Внешний вид РМ-2А
Нанесение паяльной пасты. Как отмечалось ранее нанесение паяльной пасты – это один из самых важных и ответственных моментов в технологическом процессе изготовления ПУ т.к. около 60% конечного брака пайки ПУ зависит от качества нанесения и подготовки паяльной пасты.
В качестве основного метода нанесения паяльной пасты ранее был выбран метод трафаретной печати. В соответствии с этим учитывая специфику опытного производства сформулируем критерии выбора необходимого по параметрам трафаретного принтера:
Трафаретный принтер должен обеспечивать возможность производить быструю замену трафарета;
Должен обладать возможностью надёжно закреплять трафареты различной площади и толщины;
Система позиционирования рабочего стола и удержания трафарета должна обеспечивать возможность качественного нанесения паяльной пасты на контактные площадки компонентов типоразмера 0201 а так же контактные площадки микросхем с шагом выводов менее 0.5 мм;
Органы управления должны позволять регулировать силу прижима ракелей принтера к трафарету а так же возможность регулировки расстояния между трафаретом и ПП;
Система крепления ПП на рабочем столе должна обеспечивать возможность независимого перемещения платы относительно рабочего стола.
При выборе трафаретного принтера в соотношении функциональностьцена необходимо придерживаться принципа необходимой достаточности функционала т.е. не следует выбирать оборудование с функционалом который не будет использоваться в опытном производстве ПУ или использование которого нецелесообразно. К такому функционалу можно отнести системы автоматического перемещения и регулировки силы прижима ракелей позиционирования печатных плат т.к переналадка и обслуживание данного оборудования в условиях опытного производства вызывает повышенные временные затраты персонала стоимость изготовления каждого ПУ снижая тем самым рентабельность опытного производства.
Рынок трафаретных принтеров в основном представлен такими фирмами как Dec Mechatronic Systems TWS Automation PBT.
Фирма Dec является одной из передовых фирм в разработке автоматического и полуавтоматического встраиваемого оборудования трафаретной печати. Одной из самых известных разработок данной компании является автоматический трафаретный принтер Horizon 03iX. Технические характеристики данного трафаретного принтера представлены в таблице 3.
Таблица 3. Технические характеристики принтера Horizon 03iX.
Время холостого цикла печати
От7до12с (взависимости оттипа конвейера)
Максимальный размер области печати (ДхШ)
Максимальный размер печатной платы (ДхШ)
0×508 или 620×508мм
Минимальный размер печатной платы (ДхШ)
Толщина печатной платы
Внутренние размеры рамы трафарета (ДхШ)
Скорость движения ракеля
Диапазон регулирования давления ракеля
±125 мкм для 20 cpk
Кроме того трафаретный притер данной модели оснащён специализированными ракелями ProActiv системой очистки Cyclone системой поддержки печатной платы Grid-Lok системой автоматического контроля качества нанесения паяльной пасты [66 67].
Рассмотрим кратко принцип работы и назначение функций ProActiv Cyclone Grid-Lok.
ProActiv. При применении функции ProActiv во время нанесения материала ракели со встроенными специализированными электронными блоками активируются и воздействуют на паяльную пасту в области нанесения колебаниями различного типа. Такое воздействие меняет реологию пасты вблизи лезвия ракеля и соответственно внутри апертуры трафарета что способствует лучшему проникновению материала через малые апертуры.
Grid-Lok. Система поддержки печатной платы Grid-Lok активируется после загрузки ПУ в рабочую область и ее поддерживающие штыри с помощью пневматики выдвигаются и подстраиваются под высоту всех установленных с нижней стороны компонентов обеспечивая надежную поддержку печатного узла.
Cyclone. При использовании системы очистки Cyclone в процессе очистки к движению по оси Y добавляются колебательные движения системы по оси Х что значительно увеличивает эффективность очистки трафарета и скорость процесса очистки.
На рисунке 2.34 показан внешний вид автоматического трафаретного принтера Horizon 03iX компании Dec [66 67].
Рисунок 2.34 – Автоматический трафаретный принтер Horizon 03iX
Трафаретные принтеры компании Mechatronic Systems в основном представлены на рынке моделью S30 которая позиционируется производителем как недорогой прецизионный принтер для мелкосерийного производства ответственных изделий. Данная модель обладает техническими характеристиками представленными в таблице 4.
Таблица 4. Технические характеристики принтера Mechatronic Systems S30.
Максимальный размер трафарета
Максимальный размер печатной платы
Скорость движения ракеля
Регулируемый угол наклона ракеля
Регулируемое давление ракеля
Автоматическое опускание стола
Регулируемая скорость отрыва стола
Регулируемое давление стола на трафарет
Расстояние между трафаретом и печатной платой
Диапазон перемещений по осям X Y Theta
Минимальный шаг выводов компонента
Нанесение паяльной пасты в данном принтере производится автоматически с помощью каретки с двойной системой ракелей закрепленной на направляющих. Принтер рассчитан на работу с односторонними и двухсторонними платами с максимальными размерами 400 x 375 мм и позволяет гарантировано наносить паяльную пасту на контактные площадки микросхем с шагом до 03 мм.
На фото 2.35 представлен внешний вид полуавтоматического трафаретного принтера Mechatronic Systems S30 [68 69].
Рисунок 2.35 – Внешний вид принтера Mechatronic Systems S30
Фирма TWS Automation представлена на рынке в основном полуавтоматическими принтерами серии SR-2000 – SR-2700 с близкими техническими характеристиками отличающиеся только степенью автоматизации процесса нанесения паяльной пасты. В таблице 5 представлены технические характеристики младшей модели полуавтоматических трафаретных принтеров TWS Automation SR-2300.
Таблица 5. Технические характеристики принтера SR-2300.
На фото 2.36 представлен внешний вид трафаретного принтера TWS Automation SR-2300 [70].
Рисунок 2.36 – Внешний вид трафаретного принтера SR-2300
Трафаретные принтеры фирмы PBT широко представлены на рынке трафаретным принтером UNIPRINT имеющим несколько схожих модификаций с различными столами. Тип стола зашифрован в названии принтера.
UNIPRINT-M выпускается со столом с магнитными держателями предназначен для работы с двусторонними печатными платами.
UNIPRINT-V выпускается со столом с вакуумным удержанием плат и предназначен для работы с тонкими платами или слайдами.
UNIPRINT-S выпускается с самым простым плоским столом предназначенным для работы с односторонними печатными платами закрепляемыми при помощи ограничителей на липкой ленте.
UNIPRINT-G выпускается со столом оснащенным специальными брусками закрепленными в специальных пазах. Данный стол имеет аналогичное назначение столу “S”.
В таблице 6 представлены технические характеристики полуавтоматического трафаретного принтера UNIPRINT-S.
Таблица 6. Технические характеристики принтеров UNIPRINT-S.
Общий размер рабочего стола
Максимальная область печати с использованием рамок для натяжения трафарета
Максимальная площадь нанесения пасты с использованием направляющих для ракелей
Максимальная толщина платы
Диапазон перемещений стола
Точность позиционирования по осям
Общая длина принтера
Общая ширина принтера
Общая высота принтера
На рисунке 2.37 показан внешний вид трафаретного принтера UNIPRINT-S фирмы PBT [71 72].
Рисунок 2.37 – Внешний вид трафаретного принтера UNIPRINT-S.
Таким образом обобщая вышеприведённые характеристики можно сделать вывод о том что наиболее подходящим для нужд опытного производства является трафаретный принтер фирмы TWS Automation модели SR-2300 т.к. обладает наиболее близкими характеристиками к заданным и при этом не имеет дополнительного излишнего функционала увеличивающего чрезмерно стоимость оборудования и снижающего рентабельность производства.
Наиболее универсальным и функциональным из представленных моделей является автоматический трафаретный принтер Horizon 03iX фирмы Dec. Данный принтер наиболее полно по параметрам удовлетворяет нуждам крупносерийного конвейерного производства. Для нужд опытного производства функционал данного будет излишним. Часть функций автоматизации на практике использоваться не будет т.к либо нецелесообразна в условиях опытного производства либо нереализуема технологически.
В качестве возможной замены трафаретного принтера SR-2300 можно рассматривать принтер Mechatronic Systems S30 обладающий схожими параметрами но являющийся более автоматизированным образцом с широкими техническими возможностями.
Трафаретные принтеры UNIPRINT в основном являются полностью ручными моделями трафаретных принтеров и для наших задач не подходят т.к. не удовлетворяют необходимым техническим характеристикам.
Выше были рассмотрены подробно примеры выбора технологического оборудования на примере выбора трафаретного принтера миксера паяльной пасты а так же оборудования для определения физических параметров паяльной пасты (вязкости).
При дальнейшем выборе технологического оборудования будем приводить только модель оборудования удовлетворяющего поставленным задачам (а так же условиям сформулированным в начале данной главы) и технические характеристики заявленные производителем для данного оборудования. При выборе оборудования в дальнейшем так же будем руководствоваться принципом необходимой достаточности функционала т.е. не следует выбирать оборудование с функционалом который не будет использоваться в опытном производстве ПУ или использование которого нецелесообразно. Кроме того основное предпочтение необходимо отдавать необходимой многофункциональности и точности оборудования в угоду производительности.
Установка КМП. Установка КМП является основной технологической операцией в технологическом процессе производства ПУ. Для нужд опытного производства установщик КПМ должен обеспечивать следующие технические характеристики:
Точностью установки не менее 50 микрон позволяющей устанавливать пассивные компоненты типоразмера 0201 микросхемы с шагом выводов менее 0.5 мм а так же микросхемы в корпусах BGA и ему подобных;
Количество мест под питатели для установки компонентов в стандартных лентах – не менее 80 штук;
Возможность установки не менее 10 различных типоразмеров КМП;
Возможность установки микросхем с матричного поддона а так же пеналов;
Производительность не менее 3500 компонентов в час;
Возможность установки дозатора паяльной пасты либо дозатора клея;
Возможность ручного управления процессом установки КМП;
Возможность работы в автоматическом режиме без реперных знаков на ПП.
Наиболее полно данным техническим характеристикам удовлетворяет установщик КМП фирмы Autotronik марки BS-384V. Технические характеристики заявленные производителем данного установщика приведены в таблице 7. На фото 2.38 показан внешний вид установщика КПМ на фото 8 – внешний вид шпинделя с посадочными местами под инструмент [73].
Таблица 7. Технические характеристики установщика КМП BS-384V.
AUTOTRONIK-SMT GmbH
Производства начального уровня
Установка разнородной элементной базы
Перемещение платы в процессе сборки
Базовое количество мест под инструменты (шпинделей)
Максимальное количество мест под инструменты (шпинделей)
Возможность встраивания в линию
Максимальная скорость комп.ч
Возможность работы с обрезками лент
Максимальное число питателей 8 мм
Опция подачи из россыпи
Опция подачи из паллет
Наименьший компонент
Наименьший шаг выводов мм
Максимальная длина компонента мм
Максимальная ширина компонента мм
Максимальная высота компонента мм
Методы центрирования компонентов
Видеокамера в головке
Стационарная видеокамера
Максимальная погрешность ±мм
Максимальная длина платы мм
Макс. Ширина платы мм
Потребляемая мощность кВт
Рисунок 2.38 – Внешний вид установщика КМП Autotronik марки BS-384V
Рисунок 2.39 – Внешний вид шпинделя с посадочными местами под инструмент
Оборудование для ручной установки КМП должно обладать схожими точностными характеристиками с установщиком КМП за исключением производительности т.к. данное понятие напрямую не применимо к ручным манипуляторам (зависит от навыков оператора). При этом особое внимание необходимо уделить возможности надёжной фиксации органов управления и подвижных частей манипулятора в заданном положении.
Наиболее подходящим по техническим характеристикам манипулятором для ручной установки КМП является манипулятор EASYPLACER V производства CIF. Дополнительным преимуществом данного манипулятора является возможность визуального контроля процесса установки КМП на дисплее под увеличением. Технические характеристики данного манипулятора представлены в таблице 8. На рисунке 2.40 представлен внешний вид данного манипулятора [74].
Таблица 8. Технические характеристики манипулятора производства CIF.
- Макс. Размер печатной платы: 380х295 мм
- Рекомендуется для монтажа компонентов от 0201
- Кол-во 8мм лент: 20(2 магазина по 10 питателей)
- Габариты оборудования: 765 x 390 x 210 мм
- Вес в упаковке: 20 кг
- Пневмопитание не требуется
- Плавное перемещение компонента вручную по 4-м осям: XYZR
- Автоматическое включение вакуума в момент касания выключение в момент установки компонента на плату
Базовое оборудование: манипулятор с одной вакуумной головкой столики под руку с плавным ходом по осям XY
Цветная камера + ЖК монитор 9» для отображения процесса
Рельсы для фиксации печатной платы
Комплект стандартных насадок-игл (4 шт.)
Блок 8 мм питателей (10 шт.)
Держатель катушек для блока V900130
Питатель для пеналов (вмещает 5 пеналов для SO8)
Питатель для пеналов (вмещает 5 пеналов для SO16)
Держатель для установки ячеек подачи из россыпи
Набор из 12 ESD-ячеек для подачи компонентов из россыпи
Рисунок 2.40 – Внешний вид манипулятора для ручной установки КМП производства CIF
Пайка КМП и ТНТ. Конвекционная пайка оплавлением является одним из самых широко распространённый методов пайки ПУ в производстве т.к. обладает рядом преимуществ: высокой гибкостью управления технологическим процессом пайки широкими возможностями задания термопрофиля оплавления возможностью паять ПУ как свинцовосодержащими припоями так и бессвинцовыми возможностью дополнительно создавать инертную среду для пайки отдельных ПУ и т.д.
Существенным преимуществом конвекционного метода нагрева является то что максимально возможной температурой нагрева платы и компонентов является температура воздуха что позволяет не допускать перегрева чувствительных компонентов. При конвекционном нагреве компоненты нагреваются до примерно одной и той же температуры разница температур невелика имеет место лишь разница во времени нагрева [49].
Вторым широко распространённым способом пайки ПУ является пайка ИК-излучением. Нагрев ИК-излучением характеризуется высокой интенсивностью но его главный недостаток состоит в том что излучение различной длины волны неодинаково нагревает разные компоненты и участки платы. Интенсивность нагрева зависит от цвета компонентов.
Компоненты в темных корпусах нагреваются быстро в светлых – медленно. В результате плата нагревается неравномерно причем неравномерность распределения температур на различных участках платы может достигать 40°С. На плате могут возникать теневые зоны если крупные компоненты отбрасывают тень на небольшие.
Отработка режима пайки в таких печах представляет собой довольно сложную задачу. Часто в печах с инфракрасным нагревом задаются не температуры в зонах печи а проценты мощности нагревателей [49].
Учитывая основные существенные достоинства и недостатки в качестве основной технологии пайки в проектируемом опытном производстве выберем метод конвекционной пайки оплавлением.
Основные этапы технологического процесса пайки были рассмотрены ранее при оптимизации термопрофиля пайки под ПУ ОмГТУ_pr13 поэтому приводить их повторно нет необходимости. Конвекционная печи для пайки оплавлением должна иметь следующие технические характеристики:
Количество пар зон нагрева – не менее 4;
Возможность установки температуры нагрева для каждой зоны в отдельности;
Возможность регулировки скорости конвейера в широких пределах;
Возможность полной остановки конвейера;
Возможность экстренной аварийной остановки конвейера;
Отображение параметров термопрофиля и фактических температур нагрева каждой зоны в отдельности;
Индикацию выхода печи на рабочий режим а так же индикацию отклонения фактических параметров от установленных выше заданного порога;
Максимальная температура нагрева не менее 280 градусов;
Время выхода на режим не более 15-20 минут;
Простоту эксплуатации и обслуживания;
Наиболее близкой по техническим характеристикам к заданным является конвекционная печь BM-430W производства Dektec. Производитель заявляет следующие технические характеристики:
- 4 вертикальные физические зоны нагрева;
- 4 верхних нагревательных элемента (принудительная конвекция);
- 1 нижний ИК нагревательный элемент;
- Независимая установка и контроль температуры в каждой зоне нагрева;
- 1 вертикальная физическая зона охлаждения (охлаждение вентиляторами);
- Совместимость с безсвинцовыми паечными процессами (
- Макс. рабочая температура: 350°С;
- Встроенная система контроля и управления;
- Термопары и 5 портов для их подключения (для измерения термопрофилей в печи);
- Точность поддерживаемой температуры: не более 1°С;
- Отклонение температуры: не более 2°С;
- Сетчатый конвейер;
- Макс. ширина ПП: 300 мм (сетчатый конвейер);
- Макс. высота компонента на верхней стороне ПП: 50 мм;
- Время выхода в рабочий режим: не более 10-15 мин [75].
На фото 2.41 представлен внешний вид конвекционной печи для пайки ПУ оплавлением BM-430W производства Dektec.
Рисунок 2.41 – Внешний вид конвекционной печи BM-430W
Оборудование же для ручной пайки КМП и ТНТ-компонентов (паяльные станции) должно прежде всего обладать возможностью установки и точного температуры жала в широких пределах а так же иметь достаточный набор жал различной формы.
В качестве дополнительной возможности необходимо рассматривать возможность комплектования паяльных станций так называемым термофеном являющимся функциональным дополнением (либо отдельной паяльной станцией – термовоздушной) облегчающим в некоторых случаях пайку и замену КМП. Номаинальная мощность паяльной станции должна быть не менее 100 Вт предельная температура жала (потока воздуха) не менее 280 градусов. Рынок оборудования для ручной пайки широко представлен различными фирмами в частности Lukey Rexant Ya Xun Element Мегеон и т.д.
Типичным примером комбинированной паяльной станции удовлетворяющей поставленным требованиям является паяльная станция Мегеон 00207. Технические характеристики паяльной станции заявленные производителем показаны на рисунке 2.42. На рисунке 2.43 показан внешний вид паяльной станции Мегеон 00207 [76].
Рисунок 2.42 – Технические характеристики Мегеон 00207
Рисунок 2.43 – Внешний вид паяльной станции Мегеон 00207
Контроль паяных соединений ПУ. Как отмечалось ранее процесс контроля ПУ должен производиться как можно более полно и по возможности на каждом этапе производства с привлечением методов автоматической оптической инспекции визуального контроля и методов неразрушающего контроля.
Чем более полно будет произведён контроль всего цикла производства тем меньше вероятность появления брака в конечной продукции выше качество готовой продукции выше скорость отладки конечного производства быстрее происходит адаптация применяемых техпроцессов под конкретные печатные узлы и т.д.
Основным методом контроля паяных соединений является оптический контроль с привлечением специализированных стереоувеличителей и стереомикроскопов. При невозможности проведения оптического контроля для контроля качества паяных соединений обычно привлекают средства неразрушающего контроля в частности рентгеновский контроль [77 78].
Для проведения оптического контроля ПУ целесообразно воспользоваться стереомикроскопом либо стереоувеличителем обладающим следующими техническими характеристиками:
Суммарное увеличение должно быть достаточным для надёжного контроля компонентов типоразмера 0201 а так же микросхем с шагом менее 0.5 мм;
Стереомикроскопстереоувеличитель должен обладать возможностью установки нескольких объективов одновременно для упрощения оптического контроля ПУ с широкой номенклатурой КМП;
Стереомикроскопстереоувеличитель должен обладать возможностью оперативной замены объектива;
Должен иметь отключаемую подсветку;
Органы управления должны надёжно фиксировать объективы а так же составные части в выбранном положении.
Наиболее близким по характеристикам и зарекомендовавшим себя стереомикроскопом является стереомикроскоп Mantis Elite производства Vision Engineering. Технические характеристики выбранного стереомикроскопа показаны на рисунке 2.44. На рисунке 2.45 показан габаритный чертеж данного стереомикроскопа на рисунке 2.46 – внешний вид стереомикроскопа Mantis Elite [79 80].
Рисунок 2.44 – Технические характеристики стереомикроскопа Mantis Elite
Рисунок 2.45 – Габаритный чертёж стереомикроскопа Mantis Elite
Рисунок 2.46 – Внешний вид стереомикроскопа Mantis Elite
Постоянное повышение требований рынка к расширению функциональных возможностей новых изделий при снижении их размеров веса и энергоемкости заставляет разработчиков использовать электронные компоненты с большим количеством выводов (до 500) и малым шагом (до 100 мкм).
В этих условиях все более популярными становятся интегральные микросхемы в корпусах BGA Flip Chip и QFN так как они позволяют существенно увеличить плотность электронных компонентов на печатной плате.
Очевидно что произвести визуальный оптический контроль большинства микросхем в данных корпусах технически невозможно. В таком случае применяются методы неразрушающего контроля. Самым распространённым методом является рентгеновский контроль [81 82 83 84].
Для проведения качественного рентгеновского контроля в условиях опытного производства рентгеновский аппарат должен обладать следующими техническими характеристиками:
Максимальная мощность излучения – не менее 5 Вт;
Минимальный распознаваемый элемент – 10 микрон и ниже;
Тип рентгеновской трубки – обслуживаемая;
Максимальный угол наклона образца – не менее 45 градусов;
Возможность поворота образца вокруг вертикальной оси;
Максимальный вес исследуемого образца – не менее 1.5 кг;
Соответствие нормам СанПин по уровню побочного излучения.
Наиболее близким рентгеновским аппаратом удовлетворяющим заданным техническим характеристикам является рентгеновский аппарат производства Nikon модели XT V 130. Технические характеристики данного аппарата заявленные производителем представлены в таблице 9. На фото 2.47 представлен внешний вид рентгеновского аппарата Nikon модели XT V 130 [85].
Таблица 9. Технические характеристики рентгеновского аппарата Nikon модели XT V 130.
Максимальный размер тестируемого изделия
Тип рентгеновской трубки
Обслуживаемая со встроенным генератором
Напряжение на рентгеновской трубке
Максимальная мощность трубки
Автоматическая настройка трубки и системы
Минимальный распознаваемый элемент
Увеличение геометрическое
Общее системное увеличение
Максимальный угол контроля исследуемого образца
Вращение исследуемого образца
Максимальный вес исследуемого образца
Соответствие санитарным правилам рентген-безопасности
Да (соответствие с ОСПОРБ-2010). Уровень излучения при максимальной мощности системы 1мкЗвчас
Рисунок 2.47 – Внешний вид рентгеновского аппарата Nikon модели XT V 130
Отмывка печатных узлов. Как отмечалось ранее отмывка ПУ после монтажа а так же контроль качества отмывки должны производиться как можно более полно и тщательно т.к. это позволит устранить многие дефекты возникающие в дальнейшей эксплуатации ПУ. При этом необходимо отмывать ПУ всегда в независимости от применяемого флюса.
Оборудование для отмывки ПУ должно позволять полноценно отмывать ПУ с КМП допускающими ультразвуковую отмывку так и с КМП не позволяющими применять ультразвуковую отмывку но при этом производительность оборудования уходит на второй план уступая место многоцелевому назначению и технологичности.
Соответственно процесс отмывки целесообразно разбить на 2 этапа – ультразвуковую отмывку в специализированных ваннах и окончательную струйную отмывку. При этом оборудование для струйной отмывки целесообразно выбрать с функцией сушки ПУ по установленной программе.
В современных ультразвуковых ваннах источник колебаний жестко закреплен за пределами сосуда благодаря чему сама ванна становится резонансным телом а колебания находящейся в ней жидкости имеют одинаковую интенсивность во всем объеме. Жидкостью чаще всего служит вода или готовый препарат действующий как растворитель жиров преобразователь ржавчины и т. д. (в зависимости от выполняемых работ). Изделие погружают в ванну в свободном подвешенном состоянии или на специальных приспособлениях (подвесные решетки корзины и др.) так чтобы оно постоянно омывалось очищающей жидкостью и подвергалось воздействию ультразвуковых колебаний.
В качестве ванны для ультразвуковой отмывки ПУ можно выбрать любую ванну с геометрическими размерами превышающими максимальные геометрические размеры платы с которыми может работать выбранный установщик КМП. По функциональным возможностям подавляющее большинство ультразвуковых ванн примерно равнозначны. Основное отличие ванн друг от друга заключается в количестве установленных ультразвуковых излучателей а так же возможности двухстороннего либо одностороннего воздействия на ПУ.
В качестве ультразвуковой ванны выберем ванну Vilitek VBS-20H. На рисунке 2.48 показаны технические характеристики ультразвуковых ванн Vilitek серии VBS на рисунке 2.49 – внешний вид ванны VBS-20H [86 87].
Рисунок 2.48 – Технические характеристики ультразвуковых ванн Vilitek серии VBS
Рисунок 2.49 – Внешний вид ультразвуковой ванны Vilitek марки VBS-20H
В качестве установки для струйной отмывки печатных плат с учётом особенностей опытного производства целесообразно применить хорошо зарекомендовавшую себя систему отмывки ОКО 2000МР предназначенную для опытного и мелкосерийного производства. Система отмывки Oko 2000МР с микропроцессорным управлением обеспечивает струйную отмывку печатных узлов в соответствии с заложенной программой производит отмывку горячей или холодной водой ополаскивание и сушку горячим воздухом загруженных в нее изделий. Возможна также промывка с моющими средствами.
В качестве рабочей программы может быть выбрана одна из четырех типовых предлагаемых фирмой или собственная программа пользователя. Весь процесс контролируется встроенным микропроцессором.Таким образом данная система отмывки полностью удовлетворяет поставленным требованиям. В качестве альтернативной замены возможно применение несколько менее производительной системы отмывки ОКО 1000МР. Технические характеристики системы струйной отмывки ОКО 2000МР а так же ОКО 1000МР заявленные производителем приведены в таблице 10 [5 88] На рисунке 2.50 показан внешний вид системы струйной отмывки ОКО 2000МР.
Таблица 10. Технические характеристики системы струйной отмывки ОКО 2000МР ОКО 1000МР.
Продолжительность очистки
Температура ополаскивания
Продолжительность ополаскивания
Количество ополаскивания
Температура сушки горячим воздухом
Потребление воды для наполнения
Размер платы (при использовании лотка)
Размер платы (при использовании рамы)
Рисунок 2.50 - Внешний вид системы струйной отмывки ОКО 2000МР
Испытание ПУ. Как отмечалось ранее для выполнения широкого спектра НИР в частности военного назначения для проведения испытаний печатных узлов блоков и изделий на устойчивость к климатическим и вибрационным нагрузкам необходимо иметь на производстве специализированный испытательный участок.
Оборудование для испытаний на устойчивость к механическим факторам согласно [89] должно соответствовать техническим характеристикам представленным на рисунках 2.51-2.56.
Рисунок 2.51 – Требования к испытательной аппаратуре для обеспечения режима испытаний на воздействие случайной вибрации
Рисунок 2.52 – Требования к допустимым отклонениям для обеспечения проведения испытаний на воздействие случайной вибрации
Рисунок 2.53 – Технические требования для обеспечения проведения испытаний на воздействие случайной вибрации
Рисунок 2.54 – Технические требования для обеспечения проведения испытаний на воздействие случайной вибрации
Рисунок 2.55 – Технические требования для обеспечения проведения испытаний на синусоидальное воздействие
Рисунок 2.56 – Технические требования для обеспечения проведения испытаний на синусоидальное воздействие
Наиболее близкой по техническим характеристикам системой для проведения виброиспытаний является система Dactron-laser в совокупности с вибростендом LDS V721 обладающая техническими характеристиками представленными в таблицах 11-14. На рисунке 2.57 показан внешний вид вибростенда LDS V721 [90 91 92 93].
Таблица 11. Технические характеристики блока контроллера вибростенда
Число каналов управления
Число выходных каналов с постоянной амплитудой
Число измерительных каналов
Диапазоны входного напряжения В
÷ ±01; 0 ÷ ±1; 0 ÷ ± 10
Коэффициент нелинейных искажений канала управления дБ не более
Коэффициент нелинейных искажений канала измерения дБ не более
Отношение сигналшум канала измерения дБ не менее
Пределы допускаемой основной относительной погрешности канала измерения дБ (при 1 кГц синусоидального сигнала)
Взаимное влияние каналов не более дБ
Цифровые фильтры на входном и выходных каналах дБоктаву
Таблица 12. Технические характеристики подсистемы испытаний на воздействие синусоидальных вибраций с качанием частоты.
Диапазоны амплитудного значения входного напряжения В
Пределы допускаемой основной относительной погрешности измерения и установки частоты синусоидальной вибрации %
Пределы допускаемой основной относительной погрешности измерения синусоидального виброускорения виброскорости и виброперемещения дБ
Таблица 13. Технические характеристики подсистемы испытаний на воздействие случайных вибраций.
Диапазон частот формирования спектра Гц
Пределы допускаемой относительной погрешности измерения спектральной плотности мощности ускорения (СПУ) ШСВ дБ
Мгновенное ускорение ШСВ распределено по нормальному (Гауссовскому закону)
Количество линий разрешения
Количество усреднений
Таблица 14. Технические характеристики подсистемы испытаний на ударное воздействие.
Длительность импульса мсек
Количество точек на окно
Количество осреднений
Период повторения сек
ФНЧ с частотой среза устанавливаемой пользователем
треугольник полусинус прямоугольник трапецияколокол
Рисунок 2.57 - Внешний вид вибростенда LDS V721
Технические требования к характеристикам оборудования а так же методикам проведения испытаний на устойчивость к климатическим факторам приведены подробно в [94 95]. Так как предъявляемые требования для проведения испытаний аппаратуры различных типов широки приводить данные технические требования не целесообразно с ними подробно можно ознакомиться в соответствующих ГОСТах.
Наиболее близкой по техническим характеристикам климатической камерой подходящей для проведения большей части испытаний ПУ является камера VCL7006 производства Vtsch Industrietechnik. Технические характеристики климатической камеры VCL7006 заявленные производителем показаны на рисунке 2.58. На рисунке 2.59 показан внешний вид климатической камеры VCL7006 [96].
Рисунок 2.58 – Технические характеристики климатической камеры VCL7006
Рисунок 2.59 – Внешний вид климатической камеры VCL7006
Влагозащита ПУ. Как было отмечено ранее этап нанесения влагозащитных покрытий является одним из важнейших этапов обеспечения дальнейшей высокой эксплуатационной надёжности и устойчивости ПУ к внешним климатическим и биологическим факторам. Согласно требованиям [97] а так же учёте особенностей опытного производства оборудование для нанесения защитных покрытий должно обеспечивать следующие технические характеристики:
Возможность нанесения влагозащитного покрытия на большие участки ПУ;
Возможность нанесения влагозащитного покрытия на отдельные компоненты а так же равномерными узкими участками с шириной от 1 мм;
Возможность нанесения влагозащитного покрытия по ранее заложенной программе;
Возможность задать при программировании скорость перемещения насадки для нанесения покрытий угол наклона а так же высоту размещения насадки над поверхностью ПУ;
Иметь визуальный контроль процесса программирования и нанесения влагозащитного покрытия;
Возможность позиционирования как по реперным знакам так и по центрам выбранных компонентов;
Возможность установки на шпиндель не менее 3-ёх активных головок.
Наиболее близкой по техническим характеристикам к заданным является система нанесения влагозащитных покрытий Anda HD-18. Производитель заявляет следующие технические характеристики данной системы:
Позиционирование по реперам при помощи ПЗС камеры;
Серво-привод ШВП по осям X Y и Z;
Типы функциональных головок: струйная шнековая штыревидная пневматическая;
Система поддержания постоянной температуры головки для обеспечения постоянной текучести материала;
Многофункциональная калибровочная платформа (точность по XY камера лазер размер дозы давление в головке станция автоматической очистки головки);
CAD данные из любого формата P
Измерение высоты платы и компонентов при помощи лазера (опция);
Конвекционный подогрев платы снизу (до 120°С) во входной зоне и зоне дозирования для обеспечения текучести материала при заливке под корпус (опция);
Прецизионное измерение веса дозы с точностью до 01 мг (опция);
Возможность подключения увеличенной ёмкости для материала (опция);
Двойной конвейер (опция);
Вращение (360°)наклон (30°) дозирующей головки (опция).
На фото 2.60 показан внешний вид установки для нанесения влагозащитных покрытий Anda HD-18 [98 99].
Рисунок 2.60 – Установка для нанесения влагозащитных покрытий Anda HD-18
Таким образом в данной главе был подробно рассмотрен процесс выбора технологического оборудования для организации опытного производства с широким спектром возможностей (в том числе проведения НИР в области военной техники) выбрано основное необходимое технологическое оборудование по заданным техническим характеристикам приведены технические характеристики выбранного оборудования заявленные производителем.
5 Разработка пакета документации на технологический процесс нанесения паяльной пасты на печатную плату BF_537_r2
Технологической документацией называют пакет документов либо отдельные документы регламентирующие выполнение технологического процесса изготовления деталей. Технологическая документация служит основой для руководства производственным процессом.
Для того чтобы техпроцесс выполнялся на каждом рабочем месте без задержек и нарушений необходимо провести комплекс специальных подготовительных работ. По этой причине технологическая документация должна содержать исчерпывающие сведения не только для непосредственного выполнения самого технологического процесса но и для подготовки производства в целом.
Виды установленных технологических документов подробно описаны в [100] а правила оформления документации общего назначения в [101]. Наиболее широко распространёнными на производстве технологическими документами являются: маршрутная карта (МК) операционная карта (ОК) карта эскизов (КЭ) технологическая инструкция (ТИ) материальная ведомость (МВ) ведомость оснастки (ВТ).
Маршрутная карта (МК) представляет собой документ содержащий описание технологического процесса изготовления изделия по всем операциям в технологической последовательности с указанием соответствующих данных по оборудованию оснастке материальным трудовым и другим нормативам.
Операционная карта (ОК) - документ содержащий описание операций технологического процесса изготовления изделия с расчленением операций по переходам и с указанием режимов работы расчетных норм и трудовых нормативов.
Карта эскизов и схем (КЭ) является документом в котором содержится графическая иллюстрация технологического процесса изготовления изделия и отдельных его элементов дополняющая или поясняющая содержание операций.
Технологическая инструкция (ТИ) представляет собой документ содержащий описание специфических приемов работы методики контроля технологического процесса правил пользования оборудованием и приборами мер безопасности а также описание физико-химических явлений происходящих при выполнении отдельных операций технологического процесса.
Материальная ведомость (ВМ) представляет собой документ содержащий предварительные данные для подготовки производства. Она составляется на материалы применяемые при выполнении технологического процесса изготовления изделия. ВМ является подетальной и сводной ведомостью норм расхода материалов.
Ведомость оснастки (ВТ) - документ содержащий перечень специальных и стандартных приспособлений и инструментов необходимых для оснащения технологического процесса изготовления изделия. Эту ведомость составляют на основании карт технологического процесса [100 102].
Рекомендованная ЕСТД комплектность ТД для единичных ТП приведена на рисунках 2.61-2.63 [104 105].
Рисунок 2.61 - Рекомендованная ЕСТД комплектность ТД для единичных ТП
Рисунок 2.62 - Рекомендованная ЕСТД комплектность ТД для единичных ТП
Рисунок 2.63 - Рекомендованная ЕСТД комплектность ТД для единичных ТП
Учитывая тот факт что около 60% возникающих дефектов пайки конечного ПУ появляется по причине некачественного нанесения паяльной пасты целесообразно для данного технологического процесса разработать пакет технологической документации сведя тем самым к минимуму возникающие дефекты связанные с данным этапом технологического процесса производства ПУ.
Для оформления технологического процесса производства ПУ воспользуемся рекомендованным комплектом технологической документации №5 показанный на рисунке 2.62. Данный комплект позволяет описать технологический процесс производства ПУ BF_537_r2 с акцентированием внимания на технологический процесс нанесения паяльной пасты. На рисунке 2.64 показан титульный лист на рисунках 2.65-2.67 – маршрутная карта технологического процесса производства ПУ BF_537_r2 на рисунках 2.68 2.69 – операционная карта нанесения паяльной пасты на печатную плату BF_537_r2.
Рисунок 2.64 – Титульный лист комплекта документов на технологический процесс изготовления ПУ BF_537_r2
Рисунок 2.65 – Первый лист маршрутной карты на технологический процесс изготовления ПУ BF_537_r2
Рисунок 2.66 – Второй лист маршрутной карты на технологический процесс изготовления ПУ BF_537_r2
Рисунок 2.67 – Третий лист маршрутной карты на технологический процесс изготовления ПУ BF_537_r2
Рисунок 2.68 – Первый лист операционной карты нанесения паяльной пасты па печатную плату BF_537_r2
Рисунок 2.69 – Второй лист операционной карты нанесения паяльной пасты па печатную плату BF_537_r2
В данной выпускной квалификационной работе был проведён углубленный анализ развития технологий поверхностного монтажа печатных узлов в исторической перспективе а так же современное состояние данных технологий.
Основными целями работы ставились:
- адаптация технологического процесса производства печатных узлов под условия опытного производства с возможностью проведения НИР в области ОПК;
- выбор и обоснование выбора основного а так же вспомогательного технологического оборудования для организации участка опытного производства с возможностью выполнения работ в области ОПК;
- адаптация термопрофиля конвекционной пайки под конкретный печатный узел и выбранное технологическое оборудование;
- разработка пакета технологической документации на наиболее ответственный технологический процесс производства заданного печатного узла.
В результате всестороннего анализа современного состояния технологии поверхностного монтажа печатных узлов был определён комплекс технологий удовлетворяющий современному опытному производству печатных узлов с учётом перспектив развития на ближайшие 5 лет.
Основываясь на результатах выбора применяемых технологий с учётом особенностей опытного производства была произведена адаптация технологического процесса производства под нужды опытного производства а так же выбрано основное и вспомогательное технологическое оборудование. Результаты проведённой работы были частично внедрены и используются в НИИРП ОмГТУ.
Для практической проверки правильности выбора технологий поверхностного монтажа печатных узлов а так же сопутствующего технологического оборудования были произведены следующие работы:
- произведена адаптация термопрофиля конвекционной пайки оплавлением печатного узла на примере узла BF_537_r2 для выбранной конвекционной печи BM-
- произведён комплекс подготовительных мероприятий к производству печатного узла;
- произведена практическая сборка печатного узла BF_537_r2 в полном объёме;
- произведён технический контроль печатного узла в полном объёме предусмотренный адаптированным технологическим процессом производства;
- составлен комплект технологической документации на процесс производства данного печатного узла с акцентированием внимания на процессе нанесения паяльной пасты.
По результатам сборки и технического контроля печатного узла BF_537_r2 можно сделать вывод о том что адаптация технологического процесса производства выбор технологического оборудования а так же работы связанные с производством и техническим контролем на всех этапах производства проведены успешно.
Слабым местом спроектированного опытного производства является низкая степень автоматизации процесса контроля тех или иных технологических процессов на различных этапах производства.
Таким образом можно заключить - поставленные первоначально цели и задачи были реализованы в полном объёме.
БИБЛИОГРАФИЧЕСКИЙ СПИСОК
Кен Джиллео. Из истории технологий печатных плат Электроника: наука технология бизнес. – 2004. - №5. – С. 38-39
Пирогова Е.В. Проектирование и технология печатных плат: учебник Е.В.Пирогова. – М.:ФОРУМ: ИНФРА-М 2011. – 560 с
Леухин В.Н. Радиоэлектронные узлы с монтажом на поверхность: конструирование и технология: учебное пособие В.Н.Леухин. – Йошкар-Ола: МарГТУ 2006. – 248 с
Соболев С.Ф. Технология электромонтажа: методические указания по разработке курсового проекта и подготовки к занятиям по технологии электромонтажа С.Ф.Соболев. – СПб.: СПбГУ ИТМО 2008. – 88 с
Бурлянд В.А. Хрестоматия радиолюбителя В.А. Бурлянд И.П. Жеребцов. – 5-е изд. – М.: Энергия 1971. – 512 с
Назаров Е. Недостатки поверхностного монтажа электронных блоков: как от них избавиться навсегда Компоненты и технологии. – 2003. - № 6. – С. 14-15
Назаров Е. Внутренний монтаж функциональных радиоэлектронных блоков Электроника: Наука Технология Бизнес. – 2008. - № 3. – С. 36-39
Мэнгин Ч.Г. Технология поверхностного монтажа Ч.Г. Мэнгин С. Макклелланд.– М.: Мир 1990. – 276 с
Зотова О. Решение главной проблемы технологии поверхностного монтажа: повышение качества нанесения паяльной пасты Технологии в электронной промышленности. – 2009.- №7. – С. 19-23
Вотинцев А. Технология поверхностного монтажа шаг за шагом А. Вотинцев С.Борисенков Электроника: Наука Технология Бизнес. –2005. – №1. – С. 48-55
Джерон де Гроот. Уменьшение уровня дефектов установки компонентов до 10 dpm в непрерывном процессе производства Производство электроники: технологии оборудование материалы.- 2008.- № 2. - С. 59-62
Общие рекомендации по процессу сборки и пайки печатных плат К.Силиг [и др.].- СПб:Авантех бг.- 30 с
Шохин В. Типовой технологический процесс монтажа печатных плат с применением SMD-компонентовВ.Шохин.- СПб.: СПбГУ ИТМО 2000. – 6 с
Ефремов А. Входной контроль – важнейший этап подготовки производства Производство электроники: технологии оборудование материалы.- 2009.- №1.- С. 19-24
IPC-A-600G. Критерии приёмки печатных плат. – Введ. 2002-02-12.- Нортбук.: IPC 2004. – 124 с
IPC-A-610D RU. Критерии качества электронных сборок. – Введ. 2002-02-12.- Нортбук.: IPC 2005. – 396 с
Кузнецова Т. Технология очистки печатных плат Т. Кузнецова К. Кайдалова Технологии в электронной промышленности.- 2010.- №5.- С. 24-25
Медведев А. Иммерсионные покрытия Технологии в электронной промышленности.- 2013.- №7.- С. 40-43
ГОСТ IEC 61188-5-2-2013. Печатные платы и печатные узлы. Проектирование и применение. Часть 5-2. Общие требования. Анализ соединений (посадочные места для монтажа компонентов). Дискретные компоненты.- Введ. 2013-11-14 .— М.: Стандартинформ 2014.— 37 с.
Вахрушев О. Отмывка печатных плат и трафаретов. Всё что вы хотели знать но боялись спросить Технологии в электронной промышленности.- 2008.- №1.- С. 48-56
Ефремов А. Отмывка печатных плат. Часть 1. Надуманная потребность или необходимость Компоненты и технологии.- 2004.- №6.- С. 174-176
Медведев А. Надёжностно-ориентированное производство аппаратуры специального назначения Технологии в электронной промышленности.- 2007.- №7.- С. 60-64
Ковенский В. Влагозащита и отмывка печатных узлов: где связь? Технологии в электронной промышленности.- 2008.- №3.- С. 42-43
Биксенмэн М. Определение качества отмывки в производстве бессвинцовых печатных плат Производство электроники: технологии оборудование материалы.- 2008.- №5.- С. 1-6
Поверхностный монтаж: информационный бюллетень ostec-group.- 2008.- №1. - С. 1–52.
Стахуров А. Влагозащитные лаки: базовые знания для правильного выбора материала Технологии в электронной промышленности.- 2010.- №4.- С. 36-37
ГОСТ РВ 0027-009-2008. Надежность военной техники. Методы оценки соответствия требованиям к надежности.- Введ. 2008-09-29.- М.: Стандартинформ 2009.- 32 с.
ГОСТ РВ 15.105-2001. Система разработки и постановки продукции на производство. Военная техника. Порядок выполнения научно-исследовательских работ и их составных частей. Основные положения.- Введ. 2001-06-20.- М.: Госстандарт России 2009.- 35 с.
ГОСТ РВ 15.203-2001. Система разработки и постановки продукции на производство. Военная техника. Порядок выполнения опытно-конструкторских работ по созданию изделий и их составных частей. Основные положения- Введ. 2001-12-02.- М.: Госстандарт России 2009.- 124 с
Кантер А. Деликатное разделение групповых заготовок печатных плат А. Кантер О. Вахрушев Технологии в электронной промышленности.- 2009.- №3.- С. 22-27
Клочков В.В. Анализ эффективности и оптимизация уровня мощностей опытного производства в наукоёмкой промышленности В.В. Клочков В.А. Вдовенков С.С. Критская Финансовая аналитика: проблемы и решения.- 2014.- №42 (228).- С. 2-15
Исследование процесса конвекционной пайки ЧИП-компонентов
свинецсодержащими и бессвинцовыми материалами [Электронный ресурс] :
лабораторный практикум Минобрнауки России Самар. гос. аэрокосм. ун-т им. С. П.Королева (нац. исслед. ун-т). – сост. А. В. Архипов Б. Н. Березков Электрон. текстовые и граф. дан. (053 Мбайт). - Самара 2011. - 1 эл. опт. диск (CD-ROM)
Парфенов А. Температурный профиль конвекционной пайки. Что это такое? Технологии в электронной промышленности.- 2009.- №2.- С. 29-30
Гафт С. Современные технологии. Актуальные проблемы пайки печатных узлов С.Гафт П. Агафонов Производство электроники: технологии оборудование материалы.- 2010.- №3.- С. 31-35
Шмаков М. Участок поверхностного монтажа для мелкосерийного многономенклатурного производства сложных печатных узлов М. Шмаков Д. Милишников Т. Каспина Технологии в электронной промышленности.- 2007.- №5.- С. 50-56
Моисеенко А. Лучшее решение для трафаретной печати Печатный монтаж.- 2006.- №6-декабрь.- С. 26-29
Лисов В. Оборудование фирмы TWS Automation для поверхностного монтажа Технологии в электронной промышленности.- 2005.- №1.- С. 62-64
ГОСТ 24715-81. Соединения паяные. Методы контроля качества.- Введ. 1981-04-29.- М.: Государственный комитет СССР по стандартам 2009.- 12 с.
Ланин В. Контроль паяных соединений при поверхностном монтаже СБИС В. Ланин С. Волкенштейн Технологии в электронной промышленности.- 2009.- №4.- С. 34-36
Гафт С. Рентгеновский контроль – мощное средство для диагностики и локализации дефектов современных печатных узлов Компоненты и технологии.- 2004.- №6.- С. 182-184
Лавданский А. Оптический и рентгеновский контроль печатных плат при помощи одной системы Технологии в электронной промышленности.- 2005.- №6.- С. 52-54
Петров С. Современный рентгеновский контроль электронных узлов Печатный монтаж.- 2009.- №4-5.- С. 37-40
Бернард Д. Рентгеновский контроль печатных узлов Печатный монтаж.- 2008.- №2.- С. 20-23
Патрушев С. Ультразвуковая очистка печатных плат: продукция компании «ПСБ-ГАЛС» Электроника: наука технология бизнес.- 2007.- №2.- С. 106-107
ГОСТ РВ 20.57.305-98. Комплексная система контроля качества. Аппаратура приборы устройства и оборудование военного назначения. Методы испытаний на воздействие механических факторов.- Введ. 1998-07-09.- М.: Госстандарт России 2001.- 50 с.
Метрический вибратор серии V500-V700: информационный бюллетень LDD-Group.- 2006.- №6. - С. 1–5.
Расширение области применения систем вибростендов: информационный бюллетень LDD-Group.- 2008.- №11. - С. 1–7.
Система управления виброиспытаниями. Электродинамический вибратор V721. Формуляр ОмГТУ.- 2014.- С. 1–34.
ГОСТ РВ 20.57.306-98. Комплексная система контроля качества. Аппаратура приборы устройства и оборудование военного назначения. Методы испытаний на воздействие климатических факторов.- Введ. 1999-01-01.- М.: Госстандарт России бг.- 30 с.
ГОСТ РВ 20.39.304-98. Комплексная система общих технических требований. Аппаратура приборы устройства и оборудование военного назначения. Требования стойкости к внешним воздействующим факторам.- Введ. 1998-07-09.- М.: Госстандарт России бг.- 55 с.
Беседин В. Испытания радиоэлектронной аппаратуры. Испытательное оборудование фирмы Votsch Электроника: наука технология бизнес.- 2003.- №8.- С. 62-67
ГОСТ Р МЭК 61191-1-2010. Поверхностный монтаж и связанные с ним технологии. Общие технические требования.- Введ. 2010-12-23.- М.: Стандартинформ 2011.- 35 с.
0.ГОСТ 3.1102-2011. Единая система технологической документации. Стадии разработки и виды документов. Общие положения.- Введ. 2011-05-12.- М.: Стандартинформ 2011.- 8 с.
1.ГОСТ 3.1105-2011. Единая система технологической документации. Формы и правила оформления документов общего назначения.- Введ. 2011-05-12.- М.: Стандартинформ 2012.- 24 с.
3.Кушнарев К. Современная технология нанесения влагозащитных покрытий Технологии в электронной промышленности.- 2006.- №6.- С. 54-57
4.Трусов А.Н. Оформление технологической документации по стандартам ЕСТД: методические указания к курсовому проектированию А.Н. Трусов. – К.:КазГТУ 2014. – 38 с
5.Ясинский В.Б. Разработка технологической документации: методические указания В.Б. Ясинский. – К.:СФУ 2007. – 52 с
Внешний вид ПУ.cdw

Внешний вид печатного узла D_VC113
ВКРМ-02068999-47-15-151.013.ГМ
Технология поверхностного
монтажа печатных плат
Внешний вид печатных узлов
Термопрофиль.cdw

пайки печатного узла BF_537_r2
Зона №1 - зона предварительного нагрева
Зона №2 - зона стабилизации
Зона №3 - зона оплавления
Зона №4 - зона предварительного охлаждения
Зона №5 - зона окончательного охлаждения
Типовой температурный профиль конвекционной
Традиционный" профиль
Технология поверхностного
монтажа печатных плат
Температурный профиль
ВКРМ-02068999-47-15-151.013.ГМ
Температура плавления
Рекомендуемые чертежи
- 24.04.2014