Тарельчатый абсорбер для разделения смеси воздух - пары метанола


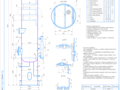
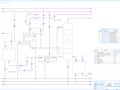
- Добавлен: 25.01.2023
- Размер: 487 KB
- Закачек: 1
Узнать, как скачать этот материал
Подписаться на ежедневные обновления каталога:
Описание
Тарельчатый абсорбер для разделения смеси воздух - пары метанола
Состав проекта
![]() |
![]() ![]() ![]() |
![]() ![]() ![]() ![]() |
![]() ![]() ![]() ![]() |
Дополнительная информация
Контент чертежей
записка.docx
АБСОРБЕР ТАРЕЛКА РАБОЧАЯ ЛИНИЯ РАВНОВЕСНАЯ ЛИНИЯ ГАЗОВАЯ СМЕСЬ ПОГЛОТИТЕЛЬ МАССОПЕРЕДАЧА ДВИЖУЩАЯ СИЛА ТЕПЛООБМЕННИК НАСОС КОМПРЕССОР
Целью данного курсового проекта является проектирования установки для абсорбции паров метанола.
Произведены расчеты и подбор основного аппарата и вспомогательного оборудования составлена технологическая схема установки выполнен чертеж общего вида абсорбера и технологической схемы.
Графическая часть включает:
- чертеж общего вида абсорбера – 1 лист А1;
- чертеж технологической схемы установки – 1 лист А1.
Обоснование и описание технологической схемы6
Описание конструкции и принципа действия абсорбера8
Описание конструкции и принципа действия вспомогательного оборудования9
2 Насос для подачи поглотителя10
3 Компрессор для подачи газовой смеси10
1 Определение условий равновесия процесса12
2 Расчет материального баланса13
3 Определение расхода поглотителя метанола из газовой смеси14
4 Определение концентрации метанола в поглотителе на выходе из абсорбера15
5 Построение рабочей линии абсорбции и определение движущих сил процесса15
6 Расчёт скорости газа и диаметра абсорбера18
7 Высота светлого слоя жидкости20
8 Расчёт коэффициентов массопередачи и массоотдачи21
9 Определение поверхности массопередачи и числа тарелок23
10 Расчет количества тарелок через число единиц переноса23
11 Расчет высоты абсорбера24
12 Гидравлическое сопротивление абсорбера25
13 Расчет штуцеров абсорбера26
Подбор вспомогательного оборудования27
1 Подбор холодильника газовой смеси27
2 Подбор холодильника поглотителя33
3 Подбор насоса для поглотителя35
4 Расчет компрессора38
Список использованных источников42
Абсорбцией называют процесс поглощения газов или паров из газовых или паро-газовых смесей жидкими поглотителями (абсорбентами).
При физической абсорбции поглощаемый газ (абсорбат) не взаимодействует химически с абсорбентом. Если же абсорбат образует с абсорбентом химическое соединение то процесс называется хемосорбцией.
Физическая абсорбция в большинстве случаев обратима. На этом свойстве абсорбционных процессов основано выделение поглощённого газа из раствора – десорбция.
Сочетание абсорбции с десорбцией позволяет многократно применять поглотитель и выделять поглощённый компонент в чистом виде. Во многих случаях проводить десорбцию не обязательно так как абсорбент и абсорбат представляют собой дешёвые или отбросные продукты которые после абсорбции можно вновь не использовать (например при очистке газов).
В промышленности процессы абсорбции применяются главным образом для извлечения ценных компонентов из газовых смесей или для очистки этих смесей от вредных примесей.
Абсорбционные процессы широко распространены в химической технологии и являются основной технологической стадией ряда важнейших производств (например абсорбция окислов азота водой в производстве азотной кислоты; абсорбция аммиака паров бензола сероводорода и других компонентов из коксового газа; абсорбция паров различных углеводородов из газов переработки нефти и т.п.). Кроме того абсорбционные процессы являются основными процессами при санитарной очистке выпускаемых в атмосферу отходящих газов от вредных примесей (например очистка топочных газов от двуокиси углерода и д.р.).
Обоснование и описание технологической схемы
Составление технологической схемы основано на анализе перемещений потоков участвующих в процессе абсорбции монтажных схем насоса и компрессора.
Рисунок 1.1 – Технологическая схема процесса абсорбции
Исходная газовая смесь подается в установку с начальным давлением Р1г = 01 МПа по трубопроводу 12 на технологической схеме. Компрессор К1 осуществляет подачу смеси и ее сжатие до такой степени чтобы с учетом потерь давления она попадала в абсорбционный аппарат ТА под рабочим давлением Ра = 02 МПа. После сжатия смесь последовательно охлаждается холодильниками Х1 и Х2. Одностадийное охлаждение нецелесообразно с экономической точки зрения. В первом охлаждение от tгн1 = 36°С до tгк1 = 29°С проводится оборотной водой (начальная температура tхн =20°С конечная температура tхк =26°С ) которая подается по трубопроводу
В4 и отводится трубопроводом В5. Во втором холодильнике охлаждающим агентом служит речная вода (начальная температура tхн = 15°С конечная tхк =19°С) которая снижает температуру до tгк2 = 29°С. Подача речной воды осуществляется по трубопроводу В7 отвод – по В10. За счет верхнего расположения основных магистральных трубопроводов подача охлаждающих агентов осуществляется самотеком.
Чистый поглотитель находящийся под атмосферным давлением в емкости Е1 перекачивается в аппарат ТА насосом Н1 через холодильник Х3. В холодильнике поглотитель охлаждается речной водой (начальная температура воды tхн =15°С конечная tхк =20°С) от tгн = 30°С до tгх = = 26°С.
Для изменения расходов потоков поглотителя и охлаждающих агентов служат регулировочные вентили.
Очищенная газовая смесь отводится от аппарата по трубопроводу 14 отработанный поглотитель собирается в емкость Е2 и отводится на регенерацию по трубопроводу 13.
Описание конструкции и принципа действия абсорбера
Тарельчатый абсорбер отличается простотой конструкции работой в широком диапазоне нагрузок по жидкости и газу возможностью работы с агрессивными и загрязненными средами высокой интенсивностью возможностью отвода выделяемой теплоты высокими расходами очищаемого газа. Ситчатые тарелки отличаются простотой устройства легкостью монтажа и ремонта имеют невысокое гидравлическое сопротивление. [1]
а – тарельчатый абсорбер; б – две соседние тарелки; 1- корпус; 2 – ситчатые тарелки;
– цилиндрическая опора; 4 – штуцер для ввода газовой смеси; 5 – штуцер для выхода
очищенной газовой смеси; 6 – штуцер для подвода поглотителя; 7 – штуцер для отвода
отработанного поглотителя; 8 - переточные перегородки.
Рисунок 2.1 – Устройство колонны с ситчатыми тарелками
Жидкость подается на верхнюю тарелку перетекает с тарелки на тарелку и удаляется из нижней части абсорбера. Переливные устройства на тарелках располагают таким образом чтобы жидкость на соседних по высоте аппарата тарелках протекала в взаимопротивоположных направлениях. Газ поступает в нижнюю часть абсорбера проходит через отверстия в тарелках и затем попадает в слой жидкости на тарелке высота которого регулируется в основном высотой сливного порога. При этом газ в жидкости распределяется в виде пузырьков и струй образуя в ней слой пены в которой происходят основные процессы массо- и теплопереноса. Эта пена нестабильна и при подходе ее к сливному устройству жидкость осветляется. Пройдя через все тарелки газ уходит из верхней части аппарата.
Описание конструкции и принципа действия вспомогательного оборудования
Для охлаждения газовой смеси и поглотителя будем использовать кожухотрубчатые теплообменники. Они достаточно просты в изготовлении отличаются возможностью развивать большую поверхность теплообмена в одном аппарате надежны в работе. [2]
а – одноходовой; б – двухходовой по трубному пространству; I и II – теплоносители;
– кожух; 2- трубные решетки; 3 – трубы; 4 – крышка; 5 – перегородка.
Рисунок 3.1 – Кожухотрубчатый холодильник жесткой конструкции
Для охлаждения поглотителя используется одноходовой теплообменник. Один из теплоносителей I протекает по трубам другой II – по межтрубному пространству. Теплота от одного теплоносителя другому передается через поверхность стенок труб.
В трубное пространство направим поглотитель в межтрубное – охлаждающий агент. При охлаждении газовой смеси будем использовать двухходовой по трубному пространству теплообменник. В этой конструкции трубный пучок разделен на секции с помощью поперечных перегородок установленных в крышке теплообменника. При этом число труб в каждой секции примерно одинаково. В таких теплообменниках при одном и том же расходе теплоносителя скорость его движения по трубам увеличивается кратно числу ходов. Здесь в трубное пространство направим охлаждающий агент в межтрубное – газовую смесь т.к. в этом случае меньше потери давления смеси.
2 Насос для подачи поглотителя
Будем использовать центробежный насос т.к. он обеспечивает плавную и непрерывную подачу перекачиваемой жидкости при достаточно высоких значениях коэффициента полезного действия. Относительно простое устройство обеспечивает его высокую надежность и достаточную долговечность. Отсутствие поверхностей трения создает возможность перекачивания загрязненных жидкостей. [2]
– корпус; 2- рабочее колесо; 3 – лопатка; 4 – всасывающий трубопровод;
– нагнетательный трубопровод; 6 –сальник; 7 – вал.
Рисунок 3.3 – Центробежный насос
Основным рабочим органом центробежного насоса является свободно вращающееся внутри улиткообразного корпуса колесо насаженное на вал. Между дисками колеса соединяя их в единую конструкцию находятся лопатки плавно изогнутые в сторону противоположную направлению вращения колеса. Внутренние поверхности дисков и поверхности лопаток образуют так называемые межлопастные каналы колеса которые при работе насоса заполнены перекачиваемой жидкостью. Всасывание и нагнетание жидкости в центробежных насосах происходит равномерно и непрерывно под действием центробежной силы возникающей при вращении колеса. При переходе жидкости из канала рабочего колеса в корпус происходит резкое снижение скорости жидкости в результате чего кинетическая энергия жидкости превращается в потенциальную энергию давления т.е. происходит превращение скорости в давление необходимое для подачи жидкости на заданную высоту. При этом в центре колеса создается разрежение и вследствие этого жидкость непрерывно поступает по всасывающему трубопроводу в корпус насоса а затем – в межлопастные каналы рабочего колеса. Перед пуском насоса всасывающий трубопровод и корпус необходимо залить жидкостью иначе разрежения возникающего при вращении колеса будет недостаточно для подъема жидкости в насос (вследствие зазоров между колесом и корпусом). Герметизация насоса осуществляется с помощью сальника. Из рабочего колеса жидкость попадает в спиралевидную камеру а затем в нагнетательный трубопровод.
3 Компрессор для подачи газовой смеси
Т.к. давление газовой смеси в аппарате существенно превышает ее давление на входе в установку и расход смеси достаточно большой будем использовать одноступенчатый турбокомпрессор.
- корпус; 2 – рабочее колесо; 3 – направляющий аппарат;
и 5 – всасывающий и нагнетательный патрубки.
Рисунок 3.4 – Турбокомпрессор
В спиралевидном корпусе вращается колесо с лопатками внутри направляющего аппарата в котором кинетическая энергия газовой смеси преобразуется в потенциальную энергию давления. Сжатая газовая смесь выходит через нагнетательный патрубок. Давление нагнетания в центробежных турбокомпрессорах может достигать 25 – 30 МПа. [2]
Исходные данные для расчета:
- поглощаемый компонент (абсорбат) – пары метанола;
- газ-носитель (инертная часть газовой смеси) – воздух;
- поглотитель – вода;
- температура абсорбции t = 26°С
- давление П = 02106 Па;
- начальное содержание абсорбата в исходной газовой смеси сун = 39% об.;
- степень поглощения φ = 095;
- начальное содержание метанола в поглотителе хн = 0005 кмоль(кмоль раствора);
- расход исходной газовой смеси при нормальных условиях Vсм0 = 8000 м3ч = 222 м3с;
- тип аппарата – тарельчатый;
- тип тарелок – ситчатые.
1 Определение условий равновесия процесса
При абсорбции паров метанола водой расчет равновесных концентраций ведут по закону Рауля [3]:
где П – давление в абсорбере Па;
Pн – давление насыщенного пара поглощаемого компонента при рабочей температуре Па;
у – концентрация метанола в газовой фазе кмоль(кмоль смеси).
При t = 26°С Pн = 16000 Па [3].
x* = (20000016000)у = 125у.
Учитывая связь абсолютных х кмоль(кмоль раствора) у кмоль(кмоль смеси) и относительных Х кмоль(кмоль воды) Y кмоль(кмоль воздуха) мольных долей составим таблицу для построения линии равновесия.
Таблица 4.1. Расчетные данные для построения линии равновесия.
По полученным данным строим линию равновесия.
Рисунок 4.1- Равновесная линия процесса абсорбции
2 Расчет материального баланса
Найдем молярный расход газовой смеси Gсм кмольс:
Gсм = Vcм0224. (4.4)
Gсм = 222224 = 00991 кмольс.
Молярный расход воздуха G кмольс определяется по уравнению:
где ун – исходная мольная доля паров метанола в газовой смеси кмоль(кмоль смеси).
Для газовых смесей объемная доля компонента численно равна его молярной доле. Поэтому ун = 0039 кмоль(кмоль смеси).
G = 00991 (1-0039) = 00952 кмольс.
Относительная мольная доля паров метанола в газовой смеси на выходе из абсорбера Yк кмоль(кмоль воздуха):
где Yн – относительная мольная доля абсорбата в исходной смеси газов кмоль(кмоль воздуха).
Yн = 0039(1-0039) = 00406 кмоль(кмоль воздуха).
Yк = 00406(1-095) = 000203 кмоль(кмоль воздуха).
Рассчитаем конечную мольную долю абсорбата в газовой смеси ук кмоль(кмоль смеси):
yк = 000203(1+000203) = 000202 кмоль(кмоль смеси).
Для определения молярного расхода метанола M кмольс служит следующее уравнение:
M = G(Yн - Yк). (4.9)
M = 00952(00406-000203) = 000367 кмольс.
3 Определение расхода поглотителя метанола из газовой смеси
Для определения минимального молярного расхода чистого поглотителя Lmin кмольс служит следующее уравнение:
где X’к – относительная мольная доля метанола в растворе на выходе из аппарата при минимальном расходе поглотителя кмоль(кмоль воды);
Хн – относительная мольная доля метанола в исходном поглотителе кмоль(кмоль воды).
X’к определим с помощью касательной проведенной к линии равновесия из точки с координатами (ХнYк). X’к = 0667 кмоль(кмоль воды).
АВ – касательная линия; ОС – равновесная линия;
Рисунок 4.2 – Определение X’к
Xн = xн(1-xн).(4.11)
Xн = 0005(1-0005) = 000503 кмоль(кмоль воды).
Т.к. в реальном процессе абсорбции используется не минимальный расход поглотителя а несколько больший (для ускорения процесса) то необходимо пересчитать минимальный расход поглотителя на рабочий расход L кмольс:
где – коэффициент избытка поглотителя.
С увеличением расхода поглотителя увеличиваются размеры абсорбера. Поэтому следует выбирать такое значение расхода поглотителя при котором размеры аппарата будут оптимальными. Примем α = 2.
L = 0005542 = 001108 кмольс.
4 Определение концентрации метанола в поглотителе на выходе из абсорбера
Для определения относительной мольной доли метанола в отработанном поглотителе Хк кмоль(кмоль воды) служит уравнение:
Абсолютная доля метанола в отработанном поглотителе хк кмоль(кмоль раствора):
хк = Хк(1+Хк).(4.14)
хк = 033(1+033) = 0248 кмоль(кмоль раствора).
5 Построение рабочей линии абсорбции и определение движущих сил процесса
Величины движущих сил на входе газовой фазы в абсорбер Δyн кмоль(кмоль смеси) и на выходе газовой фазы из абсорбера Δук кмоль(кмоль смеси) найдем:
где уи у- абсолютные мольные доли абсорбата в газовой смеси равновесной с отработанным и свежим поглотителем соответственно кмоль(кмоль смеси).
Значения у и урассчитаем по формулам:
где Yи Y - относительные мольные доли абсорбата в газовой смеси равновесной с отработанным и свежим поглотителем соответственно кмоль(кмоль воздуха).
Значения Yи Y определим с помощью графика на рисунке 4.3. Y= 002 кмоль(кмоль воздуха) Y= 00004 кмоль(кмоль воздуха).
MN – рабочая линия; ОС – равновесная линия;
Рисунок 4.3 – К определению концевых движущих сил процесса
y= 002(1+002) = 00196 кмоль(кмоль смеси);
y= 00004(1+00004) = 00004 кмоль(кмоль смеси);
Δун = 0039 - 00196 = 00194 кмоль(кмоль смеси);
Δук = 000202 - 00004 = 000162 кмоль(кмоль смеси).
Движущая сила в ходе процесса значительно изменяется поэтому рассчитаем ее значения в нескольких дополнительных точках и осредним значения. Разделим рабочую линию на четыре равных участка точками А В и С.
Величины относительной мольной доли метанола в растворе в точках А В и С ХА ХВ ХС кмоль(кмоль воды) определим как среднее значение по отрезкам:
ХА = (Хн+ХВ)2 (4.20)
ХС = (ХВ+Хк)2. (4.21)
ХВ = (000503+033)2 = 01675 кмоль(кмоль воды).
ХА = (0005+01675)2 = 008625 кмоль(кмоль воды).
ХС = (01675+033)2 = 024875 кмоль(кмоль воды).
Рисунок 4.4 - К определению движущих сил процесса
Переведем полученные значения в абсолютные мольные доли х кмоль(кмоль раствора):
хВ = 01675(1+01675) = 0143 кмоль(кмоль раствора).
хА = 008625(1+008625) = 00794 кмоль(кмоль раствора).
хС = 024875(1+024875) = 02 кмоль(кмоль раствора).
Найдем абсолютные мольные доли у* кмоль(кмоль смеси) равновесные данным х:
уВ* = 0143125 = 001144 кмоль(кмоль смеси)
уА* = 00794125 = 00064 кмоль(кмоль смеси)
уС* = 02125 = 0016 кмоль(кмоль смеси).
Найдем относительные мольные доли паров метанола в газовой смеси в точках А В С YA YB YC кмоль(кмоль воздуха):
YB = (Yн+Yк)2. (4.21)
YA = (YB+Yк)2. (4.22)
YC = (YB+Yн)2. (4.23)
YB = (00406+000203)2 = 00213 кмоль(кмоль воздуха).
YA = (00213+000203)2 = 00116 кмоль(кмоль воздуха).
YC = (00213+00406)2 = 0031 кмоль(кмоль воздуха).
Переведем полученные значения в абсолютные мольные доли у кмоль(кмоль смеси):
yВ = 00213(1+00213) = 00208 кмоль(кмоль смеси).
yА = 00116(1+00116) = 00114 кмоль(кмоль смеси).
yС = 0031(1+0031) = 003 кмоль(кмоль смеси).
Найдем движущую силу в каждой точке Δу кмоль(кмоль смеси):
ΔуВ = 00208-001144 = 000936 кмоль(кмоль смеси).
ΔуА = 00114-00064 = 0005 кмоль(кмоль смеси).
ΔуС = 003-0016 = 0014 кмоль(кмоль смеси).
Найдем среднее значение движущей силы Δуср по следующей формуле [4]:
6 Расчёт скорости газа и диаметра абсорбера
Для ситчатых тарелок рабочую скорость wр мс рекомендуется рассчитывать по формуле [3] с.112:
где ρx и ρy –плотности жидкой и газовой фазы соответственно кгм3
С – коэффициент зависящий от типа тарелки и межтарельчатого расстояния hт.
где - массовая доля метанола в растворе кг(кг раствора);
ρмет и ρвод – плотности метанола и воды при рабочей температуре соответственно; кгм3.
где Ммет и Мвод – молярные массы метанола и воды кгкмоль
Х – средняя относительная мольная доля метанола в поглотителе кмоль(кмоль воды).
По [3]: Ммет = 32 кгкмоль Мвод = 18 кгкмоль ρмет = 7866 кгм3 ρвод = 9962 кгм3.
Х = (000503+033)2 = 01675 кмоль(кмоль воды).
Плотность газовой фазы ρу кгм3 при рабочих условиях найдем по формуле:
где Му – молярная масса газовой смеси кгкмоль;
R – универсальная газовая постоянная Дж(мольК);
Mу = Ммету+Мвозд(1-у) (4.32)
где Мвозд – молярная масса воздуха кгкмоль
у – средняя мольная доля паров метанола в газовой смеси кмоль(кмоль смеси).
По [3] Мвозд = 29 кгкмоль; R = 8314 Дж(мольК).
у = (0039+000202)2 = 00205 кмоль(кмоль смеси).
Mу = 3200205+29(1-00205) = 2906 кгкмоль.
По графической зависимости приведенной в [3] с.113 найдем значение коэффициента С. Примем hт = 04 м. Тогда С = 0057.
Диаметр абсорбера Dpм находим по формуле:
где V – объёмный расход газовой смеси при рабочих условиях м3с.
V = 009912906234 = 123 м3с.
По [5] выбираем стандартный диаметр абсорбера d = 12 м. Найдем действительную скорость газа в абсорбере w мс:
w = 4123(314122) = 109 мс.
Согласно диаметру абсорбера выберем ситчатую тарелку типа ТС-Р (ОСТ 26-805 – 73) со следующими характеристиками [5] c.216:
- рабочее сечение тарелки Fрт = 101 м2;
- диаметр отверстия d0 = 5 мм;
- шаг между отверстиями t = 10 мм;
- относительное свободное сечение тарелки Fc = 111%;
- сечение перелива Fпер = 006 м2;
- периметр слива Lc = 0722 м;
7 Высота светлого слоя жидкости
Высоту светлого слоя жидкости на тарелке h0 м находим по [5] (5.49):
где hпер – высота переливной перегородки м;
q – линейная плотность орошения м3(мс) равная q = Q
По данным [3] x = 374 мНм в = 7184 мНм. hпер = 003 м.
m = 005 – 46hпер.(4.38)
m = 005 - 46003 = -0088.
lg x = xlg ж мет+(1-х)lg вод (4.39)
где ж мет и вод – вязкости жидкого метанола и воды при рабочей температуре мПас;
х – средняя мольная доля метанола в растворе кмоль(кмоль раствора).
Из [3] ж мет = 054 мПас вод = 088 мПас.
х = (0005+0248)2 = 01265 кмоль(кмоль раствора).
lg x = 01265lg 054+(1-01265)lg 088 = -0023.
где Мх – молярная масса раствора кгкмоль.
Mx = Мметх+Мвод(1-х).(4.42)
Mх = 3201265+18(1-01265) = 197 кгкмоль.
q = 0000280722 = 000038 м3(мс).
Подставив в (4.30) получим:
Газосодержание барботажного слоя м3м3 определяем из соотношения [5]: (4.43)
где Fr – критерий Фруда.
где wраб – скорость в рабочем сечении тарелки мс.
wраб = 123101 = 122 мс.
8 Расчёт коэффициентов массопередачи и массоотдачи
Коэффициент массопередачи Kyf кмоль(м2с) определяют по уравнению аддитивности фазовых диффузионных сопротивлений [5] (5.38):
где хf и уf – коэффициенты массоотдачи отнесённые к единице рабочей площади тарелки соответственно для жидкой и газовой фаз кмоль(м2с);
m – коэффициент распределения вещества по фазам.
Для жидкой фазы [5]:
– газосодержание барботажного слоя м3м3;
у – динамическая вязкость газовой смеси при рабочих условиях мПас;
U – плотность орошения м3(м2с).
Рассчитаем коэффициент диффузии в жидкости Dх:
Dx = D20[1+002(t-20)](4.49)
где D20 – коэффициент диффузии компонента при 20°С.
По данным [3] D20 =12810-9 м2с.
Dx = 12810-9[1+002(26-20)] = 1410-9 м2с.
где г мет и возд – значения динамической вязкости паров метанола и воздуха при рабочих условиях мПас.
Для нахождения значений вязкости при рабочих условиях воспользуемся формулой пересчета [3] (4.17):
где 0 – вязкость при нормальных условиях мПас;
С – постоянная Сатерленда для данного газа К.
По данным [3] 0возд = 17310-3 мПас 0мет = 8710-3 мПас Свозд = 84 К Смет = 4869 К.
Коэффициент массоотдачи для газовой фазы [5]:
где Dу – коэффициент молекулярной диффузии метанола в газовой фазе м2с.
Dу при рабочих условиях рассчитывается по [3] (4.353):
где D0 – значение коэффициента при н.у.
D0 = 132510-6 м2с. [3].
Т.к. в координатах х-у линия равновесия – прямая то коэффициент m можно найти как тангенс угла наклона равновесной линии к оси абсцисс. Уравнение х* = 125у можно записать в следующем виде: у* = (1125)х = 008х. Отсюда находим тангенс угла наклона равный 008 т.е m = 008.
9 Определение поверхности массопередачи и числа тарелок
Поверхность массопередачи в абсорбере рассчитывается по уравнению [5]:
Тогда требуемое число тарелок:
Округлим с запасом требуемое число тарелок до n1 = 16.
10 Расчет количества тарелок через число единиц переноса
Число единиц переноса по газовой фазе на одну тарелку Ny найдем по формуле [4]:
где hпен – высота пены на тарелке м.
Число единиц переноса по жидкой фазе на одну тарелку Nх найдем по формуле:
Общее число единиц переноса по газовой фазе на одну тарелку N0y найдем по формуле:
где А – абсорбционный фактор.
Общее число единиц переноса по газовой фазе n0y найдем:
Число тарелок n2 найдем как:
Округлив до целого числа тарелок примем n2 = 10. В дальнейших расчетах будем использовать число тарелок n = n2 = 10.
11 Расчет высоты абсорбера
Высота тарельчатой части абсорбера Нтч м рассчитывается [5]:
Нтч = (n-1)hт.(4.63)
Нтч = (10-1)04 = 36 м.
Общая высота абсорбера Н м находится как:
Н = Нкч+Нтч+Нсч+Нд+Н0+hшт+lшв(4.64)
где Нкч – высота кубовой части м;
Нсч – высота сепарационной части м;
Нд – высота днища м;
Н0 – высота цилиндрической опоры м;
hшт – высота штуцера м;
lшв – высота сварного шва м.
Для абсорбера диаметром d = 12 м по [6] находим значения данных параметров: Нкч = 28 м; Нсч = 16 м; Н0 = 2 м; hшт = 02 м; lшв = 008 м.
Hд = 025d+004.(4.65)
Hд = 02512+004 = 034 м.
Н = 28+36+16+034+2+02+008 = 1062 м.
12 Гидравлическое сопротивление абсорбера
Гидравлическое сопротивление абсорбера ΔPa Па определяют по формуле [5]:
где ΔР – гидравлическое сопротивление орошаемой тарелки Па.
ΔР = ΔРс+ΔРп+ΔР(4.67)
где ΔРс – гидравлическое сопротивление сухой тарелки Па;
ΔРп – гидравлическое сопротивление газожидкостного слоя (пены) на тарелке Па;
ΔР – гидравлическое сопротивление обусловленное силами поверхностного натяжения Па.
где с – коэффициент сопротивления сухой тарелки.
Для ситчатых тарелок с = 15 [5].
ΔPп = 981ρxh0.(4.69)
ΔPп = 98193900153 = 1409 Па.
где dэ – эквивалентный диаметр отверстий для прохода газа м.
Для ситчатых тарелок принимаем dэ = d0 = 0005 м.
ΔР = 40071840005 = 575 Па.
ΔР = 1692+1409+575 = 3676 Па.
ΔРа = 367610 = 3676 Па.
13 Расчет штуцеров абсорбера
Основными технологическими штуцерами являются штуцера для подвода и отвода газовой смеси для подвода и отвода поглотителя.
Расчетный диаметр штуцеров для газовой смеси dгс м находится по формуле [5]:
где wрек гс – рекомендуемая скорость газовой смеси в штуцере мс.
Примем wрек гс = 14 мс.
Примем стандартный условный диаметр штуцеров для газовой смеси dгс = 350 мм [6].
Расчетный диаметр штуцеров для поглотителя dп м находится по формуле [5]:
где wрек п – рекомендованная скорость поглотителя в штуцере мс.
Примем wрек п = 2 мс.
Примем стандартный условный диаметр штуцеров для поглотителя dп = 20 мм [6].
Подбор вспомогательного оборудования
1 Подбор холодильника газовой смеси
Составим температурную схему процесса охлаждения оборотной водой.
tгн = 36°С tгк = 29°С
tхк = 26°С tхн = 20°С
Здесь tгн и tгк – начальная и конечная температуры горячего теплоносителя (газовой смеси) °С;
tхн и tхк – начальная и конечная температуры холодного теплоносителя (воды) °С.
Среднюю разность температур Δtср °С найдем по формуле [3]:
Δtcp = (Δtб+Δtм)2(5.1)
где Δtб и Δtм – большее и меньшее значения разности температур на концах теплообменника °С.
Δtб = tгн – tхк. (5.2)
Δtм = tгк - tхн.(5.3)
Δtб = 36 – 26 = 10°С.
Δtcp = (10+9)2 = 95°С.
Поверхность теплопередачи F м2 найдем:
где Q – тепловой поток Вт;
К – коэффициент теплопередачи Вт(м2К).
Q = GсмМуcy(tгн-tгк)(5.5)
где су – удельная теплоемкость газовой смеси Дж(кгК).
су = сп мет+свозд(1-) (5.6)
где сп мет и свозд – удельные теплоемкости паров метанола и воздуха при средней температуре газовой смеси Дж(кгК)
- массовая доля паров метанола в газовой смеси кг(кг смеси).
По [3]: сп мет = 1525 Дж(кгК); свозд = 1007 Дж(кгК).
су = 152500226+1007(1-00226) = 10187 Дж(кгК).
Q = 00991290610187(36-29) = 20536 Вт.
Ориентировочно примем значение К = 55 Вт(м2К) [5].
Подберем кожухотрубчатый теплообменник по данной площади. Его параметры:
- диаметр кожуха D = 04 м;
- наружный диаметр труб dн = 002 м;
- толщина стенки трубы т = 0002 м;
- число ходов по трубному пространству а = 2;
- поверхность теплообмена F = 42 м2;
- площадь сечения одного хода по трубам f = 1710-2 м2.
- общее число труб n = 166
- длина труб l = 4 м.
В трубное пространство направим воду в межтрубное – газовую смесь.
Определим среднюю температуру горячего теплоносителя t1 °C:
t1 = (tгн+tгк)2.(5.8)
t1 = (36+29)2 = 325°С.
Коэффициент теплоотдачи от горячего теплоносителя стенке α1 Вт(м2К) найдем:
где Nu1 – критерий Нуссельта характеризующий процесс теплоотдачи для газовой смеси;
λ1 – коэффициент теплопроводности горячего теплоносителя при его средней температуре Вт(мК);
dэ – эквивалентный диаметр межтрубного пространства теплообменника.
Найдем значение критерия Рейнольдса Re1 для выбора зависимости для расчета Nu1.
где w1 – скорость газовой смеси в межтрубном пространстве мс.
где Sмт – площадь сечения межтрубного пространства теплообменника м2.
w1 = 12300735 = 167 мс.
где Пмт – смоченный периметр межтрубного пространства м.
Пмт = 31404+166314002 = 1168 м.
dэ = 4007351168 = 0025 м.
Re1 = 167002523400000181 = 53975.
Nu1 = 024Re106Pr1036(Pr1Prст1)025(5.15)
где Pr1 и Prст1 – критерии Прандтля рассчитанные при температуре ядра потока горячего теплоносителя и стенки с его стороны соответственно.
Для газовой смеси значениями Pr и Prст можно пренебречь приняв их равными 1. Тогда формула (5.11) примет вид:
Nu1 = 024Re106.(5.16)
Nu1 = 0245397506 = 1658.
По [3]: λ1 = 0026 Вт(мК).
α1 = 165800260025 = 1724 Вт(м2К).
Зададим температуру стенки со стороны горячего теплоносителя tст1 = 28°С. Тогда значение удельного теплового потока от ядра потока к стенке q1 Втм2 найдем [3]:
q1 = α1(t1-tст1).(5.17)
q1 = 1724(325-28) = 7758 Втм2.
Значение температуры стенки со стороны холодного теплоносителя tст2 °С найдем по формуле [7]:
tст2 = tст1-Σrα1(t1-tст1)(5.18)
где Σr – сумма термических сопротивлений стенки и загрязнений м2КВт.
где λст – коэффициент теплопроводности материала трубы Вт(мК);
r1 и r2 – среднее значение тепловой проводимости загрязнений внутренней и внешней поверхностей стенок Вт(м2К).
По [3]: материал труб – Сталь 15Х λст = 44 Вт(мК) примем r1 = 2800 Вт(мК) r2 = 2900 Вт(мК).
tст2 = 28-0000751724(325-28) = 274°С.
Значение удельного теплового потока от стенки к ядру потока холодного теплоносителя q2 Втм2 найдем [3]:
q2 = α2(tст2-t2)(5.20)
где α2 - коэффициент теплоотдачи от стенки холодному теплоносителю Вт(м2К);
t2 – средняя температура холодного теплоносителя °С.
где Nu2 – критерий Нуссельта характеризующий перенос тепла от стенки к холодному теплоносителю;
λ2 – коэффициент теплопроводности воды при ее средней температуре Вт(мК);
dв – внутренний диаметр труб теплообменника м.
dв = dн - 2т. (5.23)
dв = 002 - 20002 = 0016 м.
Найдем значение критерия Рейнольдса для охлаждающей жидкости:
где w2 – скорость охлаждающей жидкости в трубах теплообменника мс;
– динамическая вязкость воды при t2 Пас;
ρ2 – плотность воды при t2 кгм3.
где V2 – объемный расход охлаждающего агента м3с.
где Q2 – тепловой поток от стенки трубы к холодному теплоносителю Вт;
с2 – удельная теплоемкость воды при t2 Дж(кгК).
По [3]: 2 = 09410-3 Пас; ρ2 = 998 кгм3; с2 = 41854 Дж(кгК).
Примем Q2 = Q = 20536 Вт.
w2 = 0000821710-2 = 0048 мс.
Re2 = 0048001699809410-3 = 819.
Так как режим ламинарный (Re22300) найдем значение Gr2Pr2 для дальнейшего выбора расчетной зависимости [5]:
где λ2 – коэффициент теплопроводности воды при t2 Вт(мК);
t – коэффициент температурного расширения для воды при температуре t2 К-1.
По данным [3]: λ2 = 06023 Вт(мК); t = 02610-3 K-1.
Полученное значение Gr2Pr2 = 7932 5105 [5] в данном случае влияние свободной конвекции можно не учитывать. Тогда необходимо рассчитать значение выражения Re2Pr2dвl предварительно найдя значение критерия Прандтля для холодного теплоносителя Pr2:
Pr2 = 09410-34185406023 = 653.
Re2Pr2dвl = 81965300164 = 214.
Т.к. полученное значение Re2Pr2dвl = 214 > 12 то критерий Нуссельта Nu2:
Nu2 = 161[Re2Pr2(dвl)]13(2ст2)014(5.29)
где 2ст – динамическая вязкость воды при температуре t2ст мПас.
По [3]: 2ст = 085 мПас.
Nu2 = 161[819653(00164)]13(09410-308510-3)014 = 453.
α2 = 453060230016 = 1706 Вт(м2К).
q2 = 1706(274-23) = 7506 Втм2.
q = (7758+7506)2 = 7632 Втм2.
Найдем точное значение коэффициента теплопередачи К Вт(м2К):
К = 763295 = 80 Вт(м2К).
Уточним величину поверхности теплообмена F м2 по формуле (5.4):
По [5] подбираем кожухотрубчатый теплообменник. Он имеет параметры:
- поверхность теплообмена F = 31 м2;
- длина труб l = 3 м.
Рассчитаем гидравлическое сопротивление выбранного теплообменника по межтрубному пространству ΔР1 Па:
где Σмт – сумма коэффициентов местных сопротивлений в межтрубном пространстве.
где 1 – коэффициент местного сопротивления на входе в межтрубное пространство и выходе из него;
– сопротивление пучка труб.
где m – число рядов труб.
Округлим полученное значение до m = 8.
Рассчитаем второй холодильник для газовой смеси. При охлаждении речной водой будем использовать воду с начальной температурой tхн = 15°С. Проведем приближенный расчет пользуясь формулами (5.1) – (5.6).
Составим температурную схему процесса:
tгн = 29°С tгк = 26°С
tхк = 19°С tхн = 15°С
Δtб = 26 – 15 = 11°С.
Δtм = 29 – 19 = 10°С.
Δtcp = (11+10)2 = 105°С.
Примем К = 40 Вт(м2К) [5].
t1 = (29+26)2 = 275°C.
По [3]: при t1 = 275°C смет = 15107 Дж(кгК); свозд = 1007 Дж(кгК).
су = 1510700226+1007(1-00226) = 1018 Дж(кгК).
Q = 0099129061018(29-26) = 8795 Вт.
По [3] выбираем кожухотрубчатый теплообменник со следующими параметрами:
- поверхность теплообмена F = 21 м2;
- длина труб l = 2 м.
Т.к. второй холодильник отличается от первого длиной труб и поверхностью теплообмена от величины которых не зависит гидравлическое сопротивление межтрубного пространства теплообменника то примем сопротивление второго холодильника ΔР2 = ΔР1 = 1860 Па.
2 Подбор холодильника поглотителя
В качестве горячего теплоносителя выступает поглотитель в качестве холодного – речная вода. Температурная схема процесса:
tгн = 30°С tгк = 26°С
tхк = 20°С tхн = 15°С
Приближенный расчет проводим аналогично предыдущему.
Δtм = 30 – 20 = 10°С.
Q = Qx ρxcx(tгн-tгк)(5.36)
где сx – удельная теплоемкость поглотителя при его средней температуре t1 Дж(кгК).
Т.к. содержание метанола в поглотителе мало то используем теплоемкость чистой воды при данной температуре свод Дж(кгК).
t1 = (30+26)2 = 28°C.
По [3]: при t1 = 28°C свод = 41844 Дж(кгК).
Q = 000028 93941844(30-26) = 4400 Вт.
Примем К = 800 Вт(м2К) [5].
По [5] выбираем кожухотрубчатый теплообменник со следующими параметрами:
- диаметр кожуха D = 0159 м;
- число ходов по трубному пространству а = 1;
- общее число труб n = 19;
- поверхность теплообмена F = 1 м2;
- площадь сечения потока в вырезе перегородок fв = 0310-2 м2;
- площадь сечения потока между перегородками fп = 0510-2 м2;
- площадь сечения одного хода по трубам f = 0410-2 м2.
В межтрубное пространство направим охлаждающую воду в трубное – поглотитель. Рассчитаем гидравлическое сопротивление холодильника ΔР3 Па:
где dв – внутренний диаметр труб теплообменника м;
Σт – сумма коэффициентов местных сопротивлений трубного пространства;
w2 – скорость поглотителя в трубах мс;
λ’ – коэффициент трения.
где Reт – число Рейнольдса для поглотителя в трубах
е – относительная шероховатость труб.
Reт = w2dвρхх.(5.39)
w2 = 0000280004 = 007 мс.
dв = 002-20002 = 0016 м.
Reт = 0070016939000083 = 1267.
где Δ – высота выступов шероховатостей м.
По [5]: Δ = 00002 м.
е = 000020016 = 00125.
где 1 - коэффициент местного сопротивления на входе в камеру и выходе из нее;
- коэффициент местного сопротивления на входе в трубу и выходе из нее.
По [5]: 1 = 15; 2 = 1.
3 Подбор насоса для поглотителя
Насос перекачивает поглотитель из емкости с давлением р1 = 01 МПа при температуре 30С в аппарат работающий под давлением П = 02 МПа. Процесс осуществляется в соответствии с монтажной схемой:
Рисунок 5.1 – Монтажная схема насоса
Найдем диаметр трубопровода d м по формуле [7]:
где w – рекомендуемая скорость перемещения среды мс.
По [5] примем w = 15 мс для всасывающего и нагнетательного участков трубопровода.
Согласно [5] выбираем стальные трубы из нержавеющей стали которые имеют наружный диаметр 20 мм и толщину стенки 2 мм. Внутренний диаметр труб dв = 16 мм = 0016 м. Тогда расчетная скорость среды в трубе wp мс:
Потери напора на трение и местное сопротивление Δhп м найдем по формуле:
где λ’ – коэффициент трения;
L – общая длина трубопровода м;
Σ – сумма местных сопротивлений.
Рассчитаем критерий Рейнольдса Re:
где ρ – плотность перекачиваемой жидкости при рабочей температуре кгм3;
– вязкость перекачиваемой жидкости при рабочей температуре Пас.
Т.к. концентрация метанола в поглотителе незначительна воспользуемся значениями ρ и для воды при 30°С. По [3]: ρ = 995 кгм3; = 0000801 Пас.
Re = 1400169950000801 = 27825.
По [3] выберем стальные трубы с незначительной коррозией для которых Δ = 00002 м
Рассчитаем значение λ’ по формуле (5.34):
Длину трубопровода L определим из рисунка: L = 102 м.
Местные сопротивления на всасывающем участке [5]:
- вход в трубу с острыми кромками 1 = 05;
- внезапное расширение 3 = 036;
- запорный вентиль 4 = 096;
- внезапное сужение 5 = 03.
Местные сопротивления на нагнетательном участке [5]:
- колено - 36 = 011;
- внезапное расширение – 37 = 036;
- запорный вентиль – 38 = 096;
- внезапное сужение – 39 = 03;
- внезапное расширение 10 = 016;
- регулировочный вентиль 11 = 8;
- внезапное сужение 12 = 02.
Σ = 1+2+ 3+ 4+ 5+3 (6+ 7+ 8+ 9)+ 10+ 11+ 12.(5.48)
Σ = 05+011+036+096+03+3 (011+036+096+03)+016+8+02 = 1568.
Напор насоса найдем:
где Нг – геометрическая высота подъема жидкости м.
Полезную мощность затрачиваемую на перекачивание жидкости Nп Вт определим:
Nп = 995981000028231 = 631 Вт.
Мощность N Вт которую должен развивать электродвигатель на валу при установившемся режиме работы:
где н пер – коэффициенты полезного действия насоса и передачи от электродвигателя к насосу соответственно.
По [5]: н = 065; пер = 1.
По [5] выберем насос марки Х28042 с электродвигателем типа АО2-92-4.
Высота всасывания насоса Нвс м не должна превышать допустимого значения рассчитываемого по формуле:
где pt – давление насыщенного пара перекачиваемой жидкости при рабочей температуре Па;
hп вс – потеря напора во всасывающей линии м;
hз – запас напора необходимый для исключения кавитации м.
По [3]: при 30°С pt = 4240 Па.
где Lвс – длина всасывающего участка трубопровода м.
h3 = 03(Qn2)23(5.54)
где n – частота вращения вала с-1.
По [5]: n = 2415 с-1.
h3 = 03(00002824152)23 = 009 м.
Требуемое условие соблюдается т.к.насос расположен ниже чем позволяет максимально допустимая высота всасывания.
4 Расчет компрессора
В установку газовая смесь подается под абсолютным давлением Р1г = 01 МПа. Давление в абсорбере Ра = 02 МПа.
Рисунок 5.2 – Монтажная схема компрессора
По [5] примем w = 15 для всасывающего и нагнетательного участков трубопровода.
Согласно [5] выбираем стальные трубы из нержавеющей стали имеющие внешний диаметр 377 мм и толщину стенки 10 мм. Внутренний диаметр труб dв = 357 мм = 0357 м. Тогда расчетная скорость среды в трубе wp мс:
Суммарные потери давления на трение местные сопротивления и в аппаратах ΔРп Па найдем по формуле:
где ρг – плотность перекачиваемой газовой смеси при рабочей температуре кгм3;
г – вязкость перекачиваемой газовой смеси при рабочей температуре Пас.
Т.к. содержанием паров метанола в смеси в данных расчетах можно пренебречь используем значения ρг и г для воздуха при средней температуре 31°С и 02 МПа. По [3]: ρ = 26 кгм3; =00000187 Пас.
Re = 12303572600000187 = 610527.
Длину трубопровода L определим из рисунка: L = 36 м.
- задвижка – 33 = 015;
- колено – 34 = 011.
Σ = 1+2+ 33+34.(5.59)
Σ = 05+015+3015+3011 = 143.
Давление Р Па которое должен создавать компрессор найдем:
Р = Ра-Р1г+ΔРп.(5.60)
Р = 200000-100000+8030 = 108030 Па.
Nп = 108030123 = 132877 Вт.
Мощность N Вт которую должен развивать электродвигатель на валу при установившемся режиме работы найдем по формуле (5.47).
По [5]: н = 07; пер = 1.
По [8] выберем компрессор марки ТГ-170-17-В1 с электродвигателем типа BAO2-280L2. Давление создаваемое компрессором Рн = 159900 Па; мощность электродвигателя Nн = 200 кВт.
В ходе расчетов были подобраны:
- колонный аппарат тарельчатый цельносварной диаметром 1200 мм;
- ситчатые тарелки типа ТС-Р;
- кожухотрубчатый теплообменник для охлаждения поглотителя имеющий диаметр кожуха D = 0159 м; 19 труб 20х2 длиной 1 м; поверхность теплообмена F = 1 м2;
- кожухотрубчатый теплообменник для охлаждения газовой смеси имеющий диаметр кожуха D = 04 м; 166 труб 20х2 длиной 3 м; поверхность теплообмена F = 31 м2;
- кожухотрубчатый теплообменник для охлаждения газовой смеси имеющий диаметр кожуха D = 04 м; 166 труб 20х2 длиной 2 м; поверхность теплообмена F = 21 м2;
- насос марки Х28042 с электродвигателем типа АО2-92-4.
- турбокомпрессор марки ТГ-170-17-В1 с электродвигателем типа BAO2-280L2.
Список использованных источников
Дытнерский Ю.И. Процессы и аппараты химической технологии: учеб. пособие для вузов в 2 ч. Ю.И.Дытнерский. – 2-е изд. – М.: Химия 1995. – Ч. 2: Массообменные процессы и аппараты. – 368 с.
Дытнерский Ю.И. Процессы и аппараты химической технологии: учеб. пособие для вузов в 2 ч. Ю.И.Дытнерский. – 2-е изд. – М.: Химия 1995. – Ч. 1: Теоретические основы процессов химической технологии. Гидромеханические и тепловые процессы и аппараты. – 400 с.
Калишук Д.Г. Процессы и аппараты химической технологии: учеб.-метод. пособие Д.Г.Калишук Н.П.Саевич А.И.Вилькоцкий. – Минск: БГТУ 2011. – 426 с.
Рамм В.М. Абсорбция газов 2-е изд. – М.: Химия 1976. – 656 с.
Основные процессы и аппараты химической технологии. Пособие по проектированию Под ред. Ю.И.Дытнерского.- 2-е изд. – М.; Химия 1991. – 496 с.
Вилькоцкий А.И. Процессы и аппараты химической технологии. Курсовое проектирование: учеб. пособие для студентов химико-технологических специальностей А.И.Вилькоцкий В.А.Марков Л.В.Новосельская. – Минск; БГТУ 2011. – 288 с.
Процессы и аппараты химической технологии. Методические указания к курсовому проектированию по одноименной дисциплине для студ. очного и заочного обучения Д.Г.Калишук С.К.Протасов В.А.Марков – Минск: Ротапринт БГТУ 1992.
SECTION_ID=147. –доступа: 05.11.2012.
абсорбер.cdw

Аппарат предназначен для абсорбции паров метанола с
их начальным содержанием в смеси 3
Производительность 1
с (при рабочих условиях.)
Давление в колонне 0
Температура абсорбции 26
Тип тарелок - ситчатые.
Среда в аппарате - токсичная
взрыво- и огнеопасная.
Технические требования
испытании и поставке аппарата должны выпол-
а) ГОСТ 12.2.003 - 74 "Оборудование производственное. Общие
требования безопасности";
б) ОСТ 26.291 - 79 "Сосуды и аппараты стальные сварные. Техни-
Материал деталей колонны
соприкасающихся с разделяемыми жид-
- сталь Х18Н10Т ГОСТ 5632-72
остальных - сталь Ст3
Аппарат испытать на прочность и плотность гидравлически в го-
ризонтальном положении давлением 0
в вертикальном положе-
Сварные соединения должны соответствовать требованиям
ОСТ 26-01-82-77 "Сварка в химическом машиностроении".
Сварные швы в объеме 100% контролировать рентгенопросвечи-
Действительное расположение штуцеров
Неуказанный вылет штуцеров - 120 мм.
Поскольку аппарат эксплуатируется под давлением 0
должен соответствовать требованиям Госпроматомнадзора РБ.
Устройство поворотное
Цилиндрическая опора
Приспособление для выверки
Для регулятора уровня
Для камеры уровнемера
Для замера температуры
Колонна абсорбционная
СХЕМА.cdw

Вода оборотная (подача)
Вода оборотная (возврат)
Вода речная (подача)
Вода речная (возврат)
Канализация производственная
Загрязненная газовая смесь
Отработанный поглотитель
Очищенная газовая смесь
Тарельчатый абсорбер
Холодильник газовой смеси (I ступень охлаждения)
Холодильник газовой смеси (II ступень охлаждения)
Холодильник поглотителя
Вентиль регулировочный
Технологическая схема.
Рекомендуемые чертежи
- 25.01.2023
Свободное скачивание на сегодня
Обновление через: 15 часов 55 минут