Современные технологии сталеплавильного производства


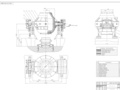

- Добавлен: 24.01.2023
- Размер: 594 KB
- Закачек: 1
Узнать, как скачать этот материал
Подписаться на ежедневные обновления каталога:
Описание
Современные технологии сталеплавильного производства
Состав проекта
![]() |
![]() ![]() ![]() |
![]() ![]() ![]() ![]() |
![]() ![]() ![]() ![]() |
![]() |
Дополнительная информация
Контент чертежей
Курсовик-12.СТ.docx
Федеральное государственное бюджетное образовательное учреждение высшего профессионального образования
«Сибирский государственный индустриальный университет»
Кафедра металлургии черных металлов стандартизации и сертификации
Расчетно-пояснительная записка
к курсовому проекту по учебной дисциплине:
Современные технологии сталеплавильного производства
Руководитель: доцент к.т.н.
Разработать технологию выплавки стали марки 08Ю в конвертере садкой 350 т при верхней кислородной продувке с интенсивностью 30 м3т·мин принять долю чугуна в металлозавалке 80%.
Предусмотреть в процессе плавки использование угля ССО. Расход угля 06%.
Состав чугуна %: S Mn - 041; S - 0013; P - 0086.
Известь: CaO - 896%; ППП - 92%; РСМ - 1:14 мин; РСГ - 80 гр;
Расход электродного боя - 03%.
В соответствии с требованиями утвержденными на заседании кафедры курсовой проект представленный к защите в комиссии должен содержать следующие разделы:
Расчет материального баланса плавки;
Расчет теплового баланса;
Разработка технологии конвертерной плавки с пересчетом расходных коэффициентов полученных в пункте 1 на садку конвертера;
Расчет основных размеров конвертера;
Расчет сопла Лаваля выбор и проектирование кислородной фурмы;
Выбор и обоснование типа и конструкции футеровки способов "горячих" ремонтов;
Выбор и обоснование системы газоочистки;
Графическая часть проекта (1 лист - 3 проекции агрегата 2 лист - разрез по футеровки и головке кислородной фурмы).
Расчет материального баланса7
2 Расчет технологических параметров периода нагрева лома8
3 Расчет технологических параметров плавки13
3.1 Определение среднего состава металлошихты и
количествапримесей окисляющихся к концу продувки13
3.2 Определение расхода извести14
3.3 Определение содержания окислов железа в шлаке15
3.4 Предварительное определение количества и состава
шлака в концу продувки16
3.5 Определение состава металла в конце продувки18
3.6 Определение содержания фосфора в металле19
3.7 Определение содержания серы в металле20
3.8 Определение угара примесей чугуна и количество образовавшихся окислов21
3.9 Уточнение количества и состава конечного шлака22
3.10 Баланс окислов железа в шлаке24
3.11 Расчет технического расхода кислорода24
3.12 Расчет количества и состав газов выходящих из
горловины конвертера25
3.13 Определение жидкого металла в конце продувки26
4 Расчет раскисления и выхода годной стали27
4.1 Расчет необходимого количества ферросплавов для
4.2 Проверка химического состава готовой стали29
Расчет теплового баланса31
1 Общий приход тепла на плавку 32
1.1 Физическое тепло подогретого лома 32
1.2 Физическое тепло жидкого чугуна 32
1.3 Химическое тепло металлошихты 33
1.4 Химическое тепло реакций шлакообразования 33
1.5 Физическое тепло миксерного шлака 34
1.6 Общий приход тепла на плавку 34
2.1 Физическое тепло стали 35
2.2 Физическое тепло шлака 35
2.3 Тепло уносимое отходящими газами 36
2.4 Тепло уносимое выбросами металла 37
2.5 Тепло уносимое пылью отходящих газов 37
2.6 Тепло диссоциации извести 38
2.7 Тепло диссоциации окислов железа внесенных
шихтой и футеровкой 38
2.8 Тепло уносимое корольками 38
2.9 Тепло уносимое отходящими газами периода
2.10 Общий расход тепла39
2.11 Избыток тепла 39
Расчет основных размеров кислородного конвертера 41
Расчет параметров и конструирование кислородной фурмы 45
1 Расчет сопла Лаваля 45
2 Разработка конструкции наконечника и фурмы 48
3 Расчет расхода воды на охлаждение фурмы 49
4 Определение рабочего давления кислорода перед гибким
Разработка технологии конвертерной плавки 52
1 Шихтовые материалы для выплавки стали 52
2 Добавки шлакообразующие материалы и ферросплавы 53
3 Шихтовка плавки и загрузка конвертера 53
4 Режим ведения плавки 54
5 Технология выплавки стали марки 08Ю 55
7 Раскисление стали 58
Футеровка кислородного конвертера 60
1 Материалы применяемые для футеровки конвертера 60
2 Огнеупорные растворы и массы 61
3 Конструкция футеровки конвертера 62
4 Ремонт футеровки конвертера 65
Газоотводящий тракт конвертера 68
1 Охлаждение конвертерных газов 69
2 Установки без дожигания оксида углерода 69
Список литературы 74
Общая схема современного производства стали которая включает в себя технологические этапы подготовки шихтовых материалов выплавки стали в кислородных конвертерах мартеновских или электродуговых печах выпуска и доводки стали в ковше (коррекция химического состава и температуры стали) а также разливку на машинах непрерывного литья заготовок (МНЛЗ) или в слитки в обобщенном виде представляет собой технологический цикл нагрева исходных шихтовых и вспомогательных материалов и последующего охлаждения конечной заготовки.
Кислородно-конвертерный процесс занимает первое место в мировой практике благодаря высоким технико-экономическим показателям и представляет собой сочетание технологий выплавки внепечной обработки и непрерывной разливки.
Преимущества кислородно-конвертерного способа производства стали: более высокая производительность одного работающего агрегата; экологическая чистота; простота управления; низкие удельные капиталовложения мощность производства высококачественной стали широкого сортамента из чугуна различного химического состава; переработка относительно большого количества металлолома. Все это обеспечило его быстрое распространение в мире.
Сочетание конвертеров с установками непрерывной разливки стали позволило снизить расход металла на прокат на 14-15% повысить производительность труда на 5-15% уменьшить затраты условного топлива на 60-70 кгт заготовок.
В будущем предусматривается повысить долю стали выплавляемой в конвертерах значительно увеличить также долю стали разливаемой непрерывным способом и обработанной различными внепечными методами.
РАСЧЕТ МАТЕРИАЛЬНОГО БАЛАНСА
Расчет материального баланса производится на 100 кг металлической завалки (чугун + скрап). Доля чугуна 80%.
Химический состав чугуна скрапа металла перед раскислением и готовой стали приведен в таблице 1.
Таблица 1 - Состав исходных материалов и продуктов
Наименование материала
Содержание элементов %
Металл перед раскислением
На основе практических данных принимаем расход материалов и потери металла (в процентах от веса металлической завалки) значения которых приведены в таблице 2.
Таблица 2 - Расход материала и потери металла
Расход 100 кг металлозавалки кг (%)
Потери железа в виде пыли
Потери железа в виде корольков
Потери железа с выбросами и выдувкой
Расход миксерного шлака
Загрязнения вносимые стальным скрапом
Потери металла в ковше при разливке
Температура чугуна при заливке в конвертер принята равной tчуг = 1380 °С. Температура металла в конце продувки принимается равной = 1641 °С.
Примерный химический состав неметаллической части шихты футеровки конвертера и других материалов приведен в таблице 3.
2 Расчет технологических параметров периода нагрева лома
В последнее время все чаще используется амортизационный лом который является более габаритным чем оборотный в связи с чем при его загрузке приводит к механическим повреждениям футеровки агрегата. Поэтому применение легковесного лома требует пакетировная что не исключается попадания в пакеты посторонних предметов закрытых емкостей и т.д.
Климатические условия нашего региона способствуют попаданию в пакеты воды и снега что приводит не только к технологическим сложностям ведения процесса переработки лома но и значительно ухудшает безопасность производственного процесса в целом.
При заливки жидкого чугуна с температурой 1300-1400°С на металлический лом содержащего закрытые емкости с водой льдом маслами и т.п. происходит взаимодействие расплавленного металла с данными материалами сопровождающееся взрывом.
Для предотвращения взрывом и проводится предварительный подогрев лома в конвертере.
Таблица 3 - Состав исходных материалов
Содержание компонентов %
Загрязнение стального скрапа
С учетом теплотворной способности химического состава угля (см. таблицу 4) их расходами на предыдущей плавке и коэффициента усвоения тепла от топлива определяется тепловой эффект предварительного нагрева лома.
Таблица 4 - Химический состав теплоносителей %
Содержание элементов
В данном расчете расход угля принят равным 06 кг на 100 кг металлической завалки.
Qуголь = (уголь) · Mуголь · К1;
где K1 - коэффициент усвоения тепла угля %;
(уголь) = 28680 кДжкг;
Qнагр = 28680 03 70 100 = 60228 кДж100 кг.
Затем определяется температура лома после нагрева по формуле:
= Qнагр (Мл · Сл) + tл
гдеСл - темплоемкость твердого лома равная кДжкг·град;
Мл - количество лома кг;
- температура лома после нагрева °С;
tл - температура лома до нагрева °C (принимаем равной 0 °C);
= 6022 8 (20 · 07) = 4302 °C
Избыточное тепло чугуна Qизб рассчитывается на 100 кг чугуна. Во время продувки выгорит следующее количество основных примесей чугуна:
Qизб = 103 · [(835 - 01 · B) · Si + 16 · Mn + 38 · C + 2 + 00195 · tчуг] –
– [(044 + 064 · B) · Si + 017 · Mn + 0785 · C + 204] · tм
B - основность шлака (CaO S
C = 445%; Mn = 031 %; S
tчуг - температура заливаемого чугуна °С;
tм - температура металла на выпуске °С;
Qизб = 103 · [(835 - 01 · 3) · 068 + 16 · 031 + 38 · 445 + 2 + 00195 · 1380] –
– [(044 + 064 · 3) · 068 + 017 · 031 + 0785 · 445 + 204] · 1641 =
= 43058199 кДж 100 кг чугуна.
Далее рассчитывается величина охлаждающего эффекта лома которая в зависимости от температуры его нагрева будет иметь разную величину:
где - теплоемкость лома равная 07 кДж кг · град;
- температура плавления лома °С (принимается равной температуре плавления выплавляемой стали);
- температура лома после нагрева;
- скрытая теплота плавления лома равная 2849 кДж кг;
- температура металла в конце продувки °C;
- теплоемкость расплавленного лома равная 084 кДж кг · град;
qл = 07 · (1535 - 4302) + 2849 + (1641 - 1535) · 084 = 11473 кДж кг.
При этом расчетный расход лома составит:
гдеqл - охлаждающий эффект лома кДж кг;
По заданию имеем процентное содержание лома 20% разность позволит повысить шлакообразование.
Факел определяется количество кислорода на нагрев (таблица 5) а также состав и объем отходящих газов этого периода (таблица 6). Основываясь на практических данных работы конвертеров принимаем что углерод угля сгорает с образованием 40% CO и 60% CO2. Также необходимо учитывать кислород для сжигания находящегося в угле водорода (окисление происходит по реакции 2H2 + O2 = 2H2O).
Таблица 5 - Количество кислорода и образовавшихся оксидов
Количество окислившегося элемента кг
Потребное количество кислорода кг
Количество образовавшегося окисла кг
1 · 06 100 · 06 · 05 = 0146
1 · 06 100 · 04 · 05 = 0097
11 - 45 · 06 100 = 0684*
* - вычитаем кислород топлива где 45 - кислород угля;
Учитывая тот факт что операция нагрева ограничена по времени (5 - 7 минут) в данном расчете принято что в процессе нагрева сгорают летучие компоненты топлива а также 40 - 70% углерода. Перед заливкой чугуна в конвертере остается не окислившийся углерод топлива и зола. Количество не окислившегося углерода может быть принято 50%.
Таблица 6 - Количество и состав газов
(811 · 06 100 · 06 · 44) 12 · 05 = 0535
(811 · 06 100 · 04 · 28) 12 · 05 = 0227
(4 · 06) 100 · 18 2 = 0216
* - не усвоенный ванной кислород;
С учетом усвоения кислорода ванной равной 95% чистоты технического кислорода 996% а также количества азота поступившего в металл с кислородом определяется его количество на прогрев:
84 · 95 100 = 065 кг или 065 · 224 32 = 0455 м3;
55 996 · 100 = 0457 м3.
Вместе с кислородом поступит азота:
57 - 0455 = 0002 м3 или 0003 кг.
Всего технического кислорода на прогрев требуется:
В процессе продувки образуются газы: CO2 CO N2 H2O от водорода топлива H2O неусвоенный O2.
В итоге за период нагрева выделится 107 кг газов.
Рассчитанные количества кислорода и газов входят в итоговую таблицу материального баланса.
3 Расчет технологических параметров плавки.
3.1 Определение среднего состава металлошихты и количества примесей окисляющихся к концу продувки.
Количество примесей внесенных металлической шихтой приведено в таблице 7.
Таблица 7 - Количество внесенных примесей
Содержание элементов в металлошихте % (кг)
На основе предварительно принятого состава металла перед раскислением и среднего состава металлической завалки можно определить количество примесей окислившихся за время продувки. Так как расчет ведется на 100 кг металлической завалки а состав металла перед раскислением дан в процентах отнесенных к жидкой стали то необходимо внести поправку на изменение количества металла за время продувки (выход жидкого металла к моменту раскисления). Тогда количество окислившихся примесей за время продувки определится величинами представленными в таблице 8.
Таблица 8 - Количество окислившихся примесей
Содержание примесей в шихте
Удаляется за время продувки
3.2 Определение расхода извести
Для определения расхода извести необходимо задаться основностью шлака в конце продувки которая в зависимости от состава чугуна обычно колеблется в пределах 30-45. Принимаю ВК=30.Расчет количества вносимого SiO2 и СaО всеми шихтовыми материалами (кроме извести) и футеровкой конвертера приведен в таблице 9.
Таблица 9 - Количество вносимых SiO2 и CaO
Расход материала на 100 кг шихты кг
Окисление металлошихты
На основе данных таблице 9 получения принятой основности конечного шлака (ВK=30) необходимо иметь в последнем CaO
МСаО = 1871 30 = 5613
Шихтовыми материалами вносится СaО - 0072 кг следовательно присадкой извести необходимо внести окиси кальция:
MСаО = 5613 – 0281 = 5332
Флюсующая способность извести (ФИзв) определяется по формуле:
Тогда расход извести для обеспечения заданной основности шлака:
МИзв = МCaO ФИзв = 5332 0859 = 6207
Однако часть извести будет выносится из конвертера отходящими газами. Количество выдуваемой извести обычно равно 5-10% от ее расхода и зависит от интенсивности продувки фракционного состава присадок сыпучих дутьевого режима плавки и т.д. В расчете принято что потери извести с отходящими газами составляют 5%.
Тогда расход извести на плавку:
3.3 Определение содержания окислов железа в шлаке
При кислородно-конвертерном процессе концентрация окислов железа в шлаке зависит прежде всею от содержания углерода в металле и основности шлака а также от режима продувки (высоты расположения фурмы над уровнем спокойною металла типа фурмы расхода дутья его давления и т.д.) При относительно постоянных условиях продувки содержание окислов железа в конечном шлаке можно определить исходя из содержания углерода в металле и основности шлака используя следующее эмпирическое уравнение:
где (%FeO) - суммарное содержание окислов железа в конечном шлаке;
Вк - основность шлака
[%C]раск - концентрация углерода в металле перед раскислением %;
В зависимости от режима продувки плавки основность конечного шлака и содержания углерода в металле в конце продувки отношение (%FеО) и (%Fе2О3) в конечном шлаке обычно колеблется в пределах 15-30.
В расчете это отношение принято равным 25 т.е.:
(%FeO) = 25 · (%Fе2О3).
Исходя из баланса уравнения:
(%FeO) + 144 160 · (%Fе2О3) = (%FeO)
· (%Fе2О3) + 09 · (%Fе2О3) = 215%
(%Fе2О3) = = 632%(%FeO) = 25 · (%Fе2О3) = 25 · 632 = 158%
3.4 Предварительное определение количества и состава шлака в конце продувки
Количество шлакообразующих окислов получающихся при окислении примесей металлошихты (не учитывая окисление железа) и вносимых шихтовыми материалами миксерным шлаком и футеровкой конвертера приведено в таблице 10.
Из таблицы 10 следует что суммарный вес шлакообразующих (без окислов железа) равен:
31 - 0094 - 017 = 1005 кг.
Эта сумма окислов должна составлять:
0 - 158 - 632 = 7788%
Тогда в конце продувки металла шлака должно образоваться
Таблица 10 - Расчет количества шлака
От окисления примесей чугуна
На основе известного количества шлака и количества поступивших в него компонентов можно рассчитать процентное содержание отдельных окислов:
3.5 Определение состава металла в конце продувки
Содержание углерода. Содержание углерода в металле в конце продувки плавки [%С]К было принято исходя из состава выплавляемой марки стали [%С]К = 0054 %.
Содержание марганца. Распределение марганца в системе металл-шлак в конце плавки приближается к равновесному. Константа равновесия по Керберу и Ользену.
Для температуры конца продувки 1641 °C (1914 K):
тогда константа равновесия марганца составит = 17.
Балансовое уравнение распределения марганца между шлаком и металлом имеет следующий вид:
гдеMnш - количество марганца внесенной всей шихтой кг;
[%Mn]к - содержание марганца в конечном металле;
Ммет - выход жидкого металла принятой равной 900 кг;
Мшл - количество шлака в конце продувки.
металлической шихтой: 045 кг;
миксерным шлаком: кг;
Итого: Mnш = 0469 кг.
Подставляя известные величины в балансовое уравнение получим:
Отсюда содержание марганца в металле в конце продувки:
3.6 Определение содержания фосфора в металле
Значение коэффициента распределения фосфора между шлаком и металлом в конце продувки при температуре близкой к 1641 °С для различных содержаний СаО и FeO может быть определено из уравнения:
Коэффициент распределения фосфора:
Отсюда (%P2O5) = 114074[%P]
Балансовое уравнение распределения фосфора между шлаком и металлом имеет вид:
гдеPш - количество фосфора вносимого всеми шихтовыми материалами кг;
[%Mn]к - содержание фосфора в металле в конце продувки %;
Ммет - выход жидкого металла кг;
Мшл - количество конечного шлака кг.
металлической шихтой: 0074 кг;
Итого: Pш = 0074 кг.
Отсюда содержание фосфора в металле в конце продувки:
3.7 Определение содержания серы в металле
Приближенно считают что вся сера шихты распределяется между шлаком и металлом так как удаление серы в газовую фазу при ЛД-процессе имеет сравнительно слабое развитие (2-4% от общего количества серы шихты).
Значение коэффициента распределения серы между шлаком и металлом можно определить по формуле А.Н.Морозова:
гдеn(CaO)' = n(CaO) - 2n(SiO2) - 3n(P2O5) - n(Al2O3)
n(FeO) = = 02985;n(CaO) = = 0809;
n(MnO) = = 0053;2n(S
n(A3n(P2O5) = = 0022;
Тогда n(CaO)' = 0809 - 0504 - 0022 - 0018 = 0264.
Коэффициент распределения серы S между шлаком и металлом равен:
S = (0536 + 0672) · (1 + ) = 6796
тогда (%S) = S · [%S] = 6796[%S]к.
Балансовое уравнение распределения серы имеет вид:
гдеSш - количество серы вносимой всеми шихтовыми материалами кг;
[%S]к - содержание серы в металле в конце продувки %;
металлической шихтой: 0017 кг;
миксерным шлаком: 0001 кг;
Итого: Sш = 0019 кг.
Отсюда содержание серы в металле в конце продувки:
3.8 Определение угара примесей чугуна и количество образовавшихся окислов
Состав металла перед раскислением:
[C]к = 0054%;[%Mn]к = 015;
Количество примесей оставшихся в металле:
углерода:0054 · 090 = 0049 кг
марганца:015 · 090 = 0135 кг
фосфора:001 · 090 = 0009 кг
серы:0011 · 090 = 000963 кг
где090 - принятый выход жидкого металла.
Следовательно за операцию примесей удаляются:
углерода:4041 - 0049 = 3992 кг
до CO:3992 · 090 = 3593 кг
до CO2:3992 · 010 = 0399 кг
марганца:045 - 0135 = 0315 кг
фосфора:0074 - 0009 = 0065 кг
серы:0017 - 000963 = 000737 кг.
С учетом извести и миксерного шлака серы поступило в шлак:
0737 + 0001 + 0001 = 000937.
В таблице 11 приводится необходимое количество кислорода для окисления указанных примесей и выход окислов.
Таблица 11 - Количество кислорода и образовавшихся окислов
*0003 - количество серы удаленной из металла
3.9 Уточнение количества и состава конечного шлака
Полученные данные о составе металла в конце продувки позволяют уточнить состав и количество шлака в этот момент плавки. С этой целью необходимо внести соответствующие коррективы в таблице 11 в статью учитывающую количество окислов образовавшихся в результате горения примесей металла и переход серы.
В таблице 9 приводится расчет этого уточненного количества образующихся окислов и расход кислорода на горение элементов. Как видно в отличие от таблице 11 изменились только величины поступивших в шлак из металла МnО Р2О5 и S поэтому новая сумма шлакообразующих без окислов железа составит:
05 – (0465 + 0133 + 0002 ) + (0407 + 0149 + 0007) = 10013 кг.
Отсюда уточненное количество шлака в конце продувки:
На основе таблиц 7 и 9 уточненный состав конечного шлака:
Основность шлака: 3.
Коэффициенты распределения:
3.10 Баланс окислов железа в шлаке
Исходными материалами вносится окиси железа (Fe2O3)и.м. = 0176 кг. Следовательно за счет горения железа должно образоваться:
Для этого должно окислится кг и потребуется кислорода
Исходными материалами вносится закиси железа (FeO)и.м. = 0094 кг. Тогда за счет горения железа должно быть получено закиси железа:
Для этого должно окислится 1 кг и потребуется кислорода 1
Итого на образование окислов железа в шлаке должно сгореть железа
5 + 1507 = 1957 кг для чего требуется кислорода 0135 + 0335 = 047 кг.
3.11 Расчет технического расхода кислорода
Для рассчитываемой плавки при [%С]=0054% содержание кислорода может быть принято равным [%О]=0064%.
Тогда всего необходимо кислорода 6946 + 047 + 0064 · 90 100 = 7474 кг.
В зависимости от технологических условий и режима продувки усвоение ванной вносимого дутьем кислорода колеблется в пределах 90 – 98%. В примерном расчете величина принята равной 95%.
Тогда расход кислорода на плавку составит кг или м3.
При чистоте технического кислорода 996% (обычно 985 - 998%) его требуется м3.
Вместе с кислородом поступит азоты 5529 - 5507 = 0022 м3 или = 0027.
Из этого количества азота растворяется в металле 0004 кг (обычно 0003 - 0006%) и уносится из конвертера 0027 - 0004 = 0023 кг.
Всего технического кислорода требуется 7867 + 0027 = 7894 кг.
3.12 Расчет количества и состав газов выходящих из горловины конвертера
В расчете количества и состава газов выходящих из горловины конвертера необходимо учесть режим сжигания углерода металлозавалки и топлива если условия окисления отличаются.
В настоящем расчете принято:
- выделяющийся при нагреве извести СО2 и Н2О не участвуют в окислении примесей металлической ванны;
- углерод металлозавалки окисляется до СО и СО2 соответственно на 90 и 10%;
В процессе продувки образуется газов:
CO2 от горения углерода металлозавалки - 1463 кг;
CO2 от извести - (6207 · 43) 100 = 0267 кг;
где43 - содержание СО2 в извести %.
СО от горения углерода металлозавалки - 8384 кг;
N2 из дутья - 0027 кг;
H2O из извести - (6207 · 1) 100 = 0062 кг;
O2 из дутья - 7867 - 7474 = 0393 кг.
Полученные данные позволяют определить количество и состав газов (таблица 12).
Таблица 12 - Количество и состав газов
3.13 Определение жидкого металла в конце продувки
На основе полученных данных можно определить выход жидкого металла в конце продувки. При определении этого выхода необходимо учесть углерод угля не являющийся углеродом металлозавалки.
Угар и потери металла состоят из следующих статей:
Окислилось примесей металлозавалки - 5555-06-0151-0243=4561 кг.
Унесено железа с пылью - 0600 кг.
Окислилось железа до FeO и Fe2O3 шлака - 1957кг.
Потери железа с выбросами - 1000 кг.
Потери железа в виде корольков в шлаке - 0300 кг.
Количество загрязнений на стальном скрапе - 0400 кг.
Итого угар элементов и потери: 8818 кг.
Растворилось в металле кислорода и азота: 0064 09 + 0004 = 0062 кг.
Тогда выход жидкой стали составит: 100 - 8118 + 0062 = 91244 кг.
На основании произведенного расчета можно составить материальный баланс плавки (таблица 13).
Таблица 13 - Материальный баланс плавки
Технический кислород
Пыль за счет выдуваемой извести
4 Расчет раскисления и выхода годной стали
В конвертерном процессе раскисление и легирование всех марок стали производится в сталеразливочном ковше.
Расчет необходимого количества раскислителей проводится на среднезаданное предусмотренное ГОСТом содержание соответствующих элементов в той или иной марке готовой стали.
В таблице 14 приведен принятый состав ферросплавов.
Таблица 14 - Состав примененных ферросплавов
4.1 Расход необходимого количества ферросплавов для раскисления
Среднезаданное содержание элементов в рассчитываемой стали 08Ю принято равным: [Mn]=035% [Si]=002% [Al]=005%.
Необходимое количество каждого ферросплава определяется по формуле:
гдеМст – выход жидкой стали в конце продувки кг;
[%Э]гот.ст. - содержание соответствующего элемента в готовой стали %;
[%Э]пер.раск - содержание соответствующего элемента перед раскислением %;
[%Э]ферроспл. - содержание соответствующего элемента в ферросплаве %.
Общий расход раскислителей составит:
1 + 0228 + 0035 = 0473 кг.
Количество элементов внесенных раскислителями в металл приведено в таблице 15.
Таблица 15 - Количество элементов внесенных в металл
Вносится марганцем металлическим кг
Вносится ферросилицием кг
Вносится алюминием кг
Тогда выход жидкой стали после раскисления составит:
Мст = 91244 + 02468 = 914908 кг.
Угар раскислителей будет равен:
38 - 02468 = 01912 кг.
4.2 Проверка химического состава готовой стали
Содержание элементов в готовой стали определено по формуле:
где[%Э]гот.ст. - содержание данного элемента в готовой стали после раскисления в ковше кг;
- содержание элемента в металле в конце продувки кг;
- количество элемента внесенного раскислителями кг;
Мст - выход жидкой стали после раскисления кг.
По указанной формуле определен состав готовой стали:
Таким образом проверка показала соответствие полученного состава готовой стали пределам.
Окончательный материальный баланс плавки приведен в таблице 16.
Выход годной стали определяется вычитанием из выхода жидкой стали потерь металла в ковше и в процессе разливки:
4908 - 15 = 899908 кг.
Отсюда расход металлошихты (включая раскислители) на 1 тонну годной стали составит:
(100 + 0438) 899908 = 1116 т или 1116 кг.
Расход технического кислорода на 1 т годной стали:
61 899908 · 100 · 10 = 6068 м3 т.
Таблица 16 - Материальный баланс плавки
РАСЧЕТ ТЕПЛОВОГО БАЛАНСА
Расчет ведем на 100 кг металлической завалки основываясь на данных расчета материального баланса плавки которые приведены в таблице 17.
Таблица 17 - Статьи материального баланса плавки необходимые для расчета теплового баланса.
Доля жидкого чугуна в шихте
Вес жидкой стали перед раскислением
Температура стали перед выпуском
Количество конечного шлака
Окислилось элементов в ходе продувки
Компоненты отходящих газов
[C] = CO2 в том числе и от угля (0146)
Количество Fe2O3 в рез. исп. Fe
Количество CO2 из извести
Содержание окислов в шлаке
Количество Fe2O3 из шихтовых материалов
Количество FeO из шихтовых материалов
Количество миксерного шлака
1 Общий приход тепла на плавку
1.1 Физическое тепло подогретого лома
где К1 - коэффициент усвоения тепла угля.
Qнагр = 28680 · 06 · 05 = 60228 кДж
Тепло оставшейся части неокисленного углерода учитывается при расчете химического тепла реакций окисления элементов металлошихты.
1.2 Физическое тепло жидкого чугуна
Физическое тепло жидкого чугуна можно определить по формуле
гдеGчуг - количество жидкого чугуна в металлической шихте Gчуг = 80 кг;
- теплоемкость твердого чугуна ;
tчуг - температура заливаемого в конвертер чугуна tчуг = 1380 °С
gчуг - скрытая теплота плавления чугуна gчуг = 2179 кДжкг;
- температура плавления чугуна °С;
Cчуг - теплоемкость жидкого чугуна Счуг = 092 кДжкг · град;
1.3 Химическое тепло металлошихты
Значения тепловых эффектов реакций окисления элементов при температурах их окисления приведены в таблице 18.
Таблица 18 - Значение тепловых эффектов реакций окисления
Тепловой эффект реакции окисления на 1 кг элемента кДж
[Fe] + 15O2 = (Fe2O3)
На основании данных таблицы 18 и результатов материального баланса можно определить химическое тепло реакций окисления элементов металлошихты Qхим результаты представлены в таблице 19.
Таблица 19 - Химическое тепло реакций окисления
Выгорело элементов кг
1.4 Химическое тепло реакций шлакообразования
Считаем что все количество SiO2 P2O5 и Fe2O3 в шлаке связано следующими реакциями:
P2O5 + 4CaO = (CaO)4 · P2O5 + 691350 кДжкг·моль
Fe2O3 + CaO = (CaO) · Fe2O3 + 211176 кДжкг·моль
1.5 Физическое тепло миксерного шлака
Среднюю теплоемкость миксерного шлака определяем по формуле:
С0 = 073 + 0003 · Тм.шл.
где 073 - теплоемкость шлака при 0 К кДжкг·град;
003 - приращение теплоемкости шлака на 1° кДжкг·град;
Тм.шл. - средняя температура миксерного шлака К.
Среднюю температуру миксерного шлака попадающего в конвертер из чугуновозного ковша ориентировочно можно принимать на 15-20° ниже температуры заливаемого в конвертер чугуна тогда:
Тм.шл. = (1380 - 20) + 273 = 1633К
С0 = 073 + 00003 · 1633 = 122 кДжкг·град.
Количество вносимого тепла миксерным шлаком определится из выражения:
Qм.шл. = Мм.шл. · (С0 · tм.шл. + qм.шл.)
гдеМм.шл. - количество миксерного шлака на 100 кг металлошихты кг;
tм.шл. - средняя температура миксерного шлака °С;
С0 - средняя теплоемкость миксерного шлака кДжкг·град;
qм.шл. - средняя теплота плавления шлака qм.шл. = 2095 кДжкг.
Qм.шл. = 05 · (122 · (1380 - 20) + 2095) = 93435 кДж
1.6 Общий приход тепла на плавку
Общий приход тепла на плавку рассчитывается следующим образом:
Qприх = 60228 + 103020 + 92675868 + 534102 + 93435 = 207994038 кДж.
2.1 Физическое тепло стали
Физическое тепло стали Q1 можно определить по уравнению
гдеMст - вес жидкой стали перед раскислением кг;
- теплоемкость твердой стали = 07 кДжкг·град;
tпл - температура плавления стали С;
qпл - скрытая теплота плавления стали qпл = 2724 7 кДжкг·град;
tст - температура стали перед выпуском С;
- теплоемкость жидкой стали 084 7 кДжкг·град.
Температура плавления стали:
где1539 - температура плавления чистого железа °С;
- снижение температуры плавления стали на 1% углерода в металле °С;
(%С) - содержание углерода в металле перед раскислением.
tпл = 1539 - 65 · 0054 = 1535оС.
2.2 Физическое тепло шлака
Среднюю теплоемкость конечного шлака (как и миксерного) определяем по формуле:
C0 = 073 + 00003 Tшл
гдеТшл - температура конечного шлака К.
Температуру конечною шлака принимаем выше температуры металла в конце продувки на 10°С т.е. 1651°С так как превышение температуры шлака над температурой металла составляет обычно 5-15°С.
С0 = 073 + 00003 · (1651 + 273) = 13 кДжкг·град.
Потери тепла со шлаком определяются по формуле:
Q2 = (C0 · tшл + qшл) · Мшл
гдеqшл - скрытая теплота плавления шлака qшл = 2095 кДжкг·град;
Q2 = (13 · (1641 + 10) + 2095) · 129 = 3038982 кДж.
2.3 Тепло уносимое отходящими газами
Среднюю температуру отходящих газов принимаем равной средней температуре металла за время продувки:
Средними теплоемкостями газов в зависимости от их температуры обычно задаются в соответствии с таблицей 20.
Таблица 20 - Средние теплоемкости газов
Средние теплоемкости газов в кДж(м3·град)
Тепло уносимое отходящими газами кДж:
Q3 = tот.газ. (ССО · VCO + CCO2 · VCO2 + CH2O · VH2O + CN2 · VN2 + CO2 · VO2)
гдеC - теплоемкости соответствующих составляющих газов кДжм3·град;
V - соответственно количество СО СО2 H2O N2 O2 в отходящих газах м3;
Q3 = 1510 · (149 · 6707 + 235 · 0881 + 185 · 0077 + 145 · 0017 + 155 · 0269) = 1909822 кДж.
2.4 Тепло уносимое выбросами металла
Количество тепла уносимого выбросами металла рассчитывается по формуле:
гдеМвыб - потери металла с выбросами кг;
- средняя теплоемкость металла выбросов которую принимаем равной теплоемкости жидкой стали т.е. 084 кДжкг·град;
- средняя температура металла выбросов которую принимаем равной средней температуре металла за период продувки т.е. 1510 °С.
Q4 = 1000 084 1510 = 12684 кДж
2.5 Тепло уносимое пылью отходящих газов
Потери тепла уносимого пылью складываются из потерь тепла уносимого пылью в виде Fe2O3 и пылью извести:
где - количество Fe2O3 образовавшейся в результате испарения и последующего окисления Fе кг;
Спыли - теплоемкость пыли которую принимаем равной теплоемкости шлака при tпыли кДжкг·град;
tпыли - температура пыли которую принимаем равной температуре отходящих газов 1510 оС;
Cпыли=073 + 00003 (1510 + 273) = 126 кДжкг·град
Потерями тепла уносимого известью пренебрегли так как они невелики из-за кратковременного нахождения указанного материала в полости конвертера. Кроме того его нагрев происходит преимущественно за счет тепла отходящих газов которое уже учтено выше
2.6 Тепло диссоциации извести
При диссоциации извести СаСО3 шихтовых материалов по реакции:
CaCO3 СаО + СО2 - 177237 кДжкг·моль
поглощение тепла равно Q6 = 0267 44 · 177237 = 107551 кДж
где039 - количество СО2 выделившегося из извести кг;
- молекулярный вес СО2 кг;
7237 - тепловой эффект диссоциации CaCO3 кДжкг·мольCO2.
2.7 Тепло диссоциации окислов железа внесенных шихтой и футеровкой
При диссоциации Fe2O3 по реакции
Fe2O3 419 (2Fe + 15O2 - 1230) кДжкг
гдеFe2O3 - всего внесено Fe2O3 шихтовыми материалами кг
При диссоциации FeO по реакции:
FeO Fe + 419 (0502 - 895) кДжкг
гдеFeO - всего внесено FeO шихтовыми материалами кг.
Всего поглощается тепла при диссоциации окислов железа
613 + 3525 = 122863 кДж.
2.8 Тепло уносимое корольками
Тепло уносимое корольками металла запутавшимися в шлаке
Температуру корольков принимаем равной температуре шлака т.е. 1651°С. Теплоемкость корольков принимаем равной теплоемкости жидкой стали т.е. 084 кДжкг·град.
Q8 = 0300 084 1651 = 41605 кДж.
2.9 Тепло уносимое отходящими газами периода прогрева лома
В расчете принимается что тепло уносимое отходящими газами перида нагрева лома составляет 65% от прихода тепла прогрева:
Q9 = 60228 65 100 = 39148 кДж.
2.10 Общий расход тепла
Общий расход тепла составит:
Qрасх = 13102091 + 3038982 + 1909822 + 12684 + 163053 + 107551 + 122863 + 41605 + 39148 = 19004287 кДж
Избыток тепла без учета потерь тепла конвертером составит разница между общим приходом тепла за плавку и общим расходом тепла:
Qизб = 207994038 - 19004287 = 17951168
Этот избыток тепла частично расходуется на покрытие теплопотерь конвертера (через поверхность стенок и полость горловины) и охлаждение кислородной фурмы. Теплопотери определяются в зависимости от размеров конвертера длительности перерывов между плавками продолжительности плавки возраста футеровки и т.д. Они могут быть рассчитаны лишь после определения основных размеров конвертера фурмы и продолжительности отдельных операций конвертерной плавки. Обычно потери тепла конвертером ориентировочно можно принимать в пределах 15 - 4% от прихода тепла. В расчете принято 40% тогда потери тепла 207994038 · 004 = 831976.
Избыток тепла составит: 17951168 - 831976 = 9631408 кДж.
Тепловой баланс плавки на 100 кг металлической шихты приведен в таблице 21.
Таблица 21 - Тепловой баланс плавки
Физическое тепло жидкой стали
Физическое тепло шлака
Физическое тепло тходящих газов
Тепло уносимое выбросами
Тепло уносимое пылью
Тепло разложения извести
Тепло диссоциации окислов железа
Теплота шлакообразования
Тепло уносимое корольками металла
Теплота миксерного шлака
Физическое тепло подогретого лома
Потери тепла конвертером
РАСЧЕТ ОСНОВНЫХ РАЗМЕРОВ КИСЛОРОДНОГО КОНВЕРТЕРА
Q – емкость (садка) конвертера 350 т;
qO2 – удельная интенсивность продувки металла кислородом 3 м3т·мин;
Р1 – давление кислорода на входе в сопло 12 атм;
Р2 – давление кислорода на выходе в сопло 11 атм;
Т – температура кислорода перед соплами 293 К.
Критическая скорость истечения кислорода (мс) определяется температурой потока по уравнению:
где R - газовая постоянная для кислорода 265 мК.
Максимальная скорость выхода кислородной струи из сопла:
гдеy - коэффициент учитывающий суммарные потери скорости газа в сопле;
g - ускорение силы тяжести;
k - показатель адиабаты равный для двухатомных газов 14.
Плотность кислорода (кгм3) при входе в сопло:
где ρ0 - плотность технического кислорода состоящего из 995%О2 и 05%
33 - атмосферное давление.
Плотность кислорода истекающего из сопел фурмы:
Удельный объем конверторов:
Vуд = 1 (1 + Q · 10-3) = 1 (1 + 350 · 10-3) = 074 м3т.
Глубина металлической ванны в спокойном состоянии:
Внутренний диаметр конвертера:
Dв = (0599 - 000032 · Q) = (0599 - 000032 · 350) = 6623 м.
Принимаем Dв = 65 м.
Если принять количество шлака равным 10% и при плотности 3000 кгм3 то слой шлака:
Общая глубина ванны в спокойном состоянии:
H1 = H0 + hш = 184 + 035 = 218 м.
Объем металлической ванны:
Vм = Q 7 = 350 7 = 50 м3.
Внутренний диаметр днища конвертера:
путем замены преобразовываем уравнение:
A = ( · H0) 12 = 314 · 184 = 048;
B = ( · H0 · Dв) 12 = 048 · 65 = 312;
C = ( · H0 · Dв2) 12 - Vм = 048 · 652 - 50 = -2969;
В результате получаем
8 · dдн2 + 312 · dдн - 2969 = 0
Принимаем dдн = 45 м.
Диаметр горловины конвертера:
dr = 033 · Q04 = 033 · 35004 = 344 м.
Принимаем dr = 35 м.
Рабочий объем конвертера:
V = Vуд · Q = 074 · 350 = 259.26 м3.
Hг = (Dв · dг · tgα) 2 = 6.5 · 35 · tg60° = 27 м
гдеα - угол наклона горловины принимается 60°.
Высота цилиндрической части конвертера:
Hц = Hг (045 + 0001 · Q) = 27 (045 + 0001 · 350) = 33 м.
Принимаем Hц = 31 м.
Внутренняя (полезная) высота конвертера:
Нв = Нг + Нц + Н1 = 27 + 31 + 218 = 7988 м.
Отношение внутренней высоты к внутреннему диаметру конвертера:
Толщина футеровки в цилиндрической части конвертера:
Толщина футеровки в конической части:
tк = tц - 015 = 10 - 015 = 085 м.
Толщина футеровки днища конвертера:
tдн = tц + 0125 = 10 + 0125 = 1125 м.
Толщина металлического кожуха конвертера в цилиндрической части:
Принимаем бц = 01 м.
Для днища и конической части конвертера толщину металлического кожуха берем на 004 м меньше:
бдн = бк = 01 - 004 = 006 м.
Наружный диаметр конвертера:
Dн = Dв + 2·tц + 2·бц = 875 м.
Полная высота конвертера:
Нп = Нв + tдн + бдн = 8 + 1125 + 006 = 9185 м.
Принимаем Нп = 958 м.
Отношение полной высоты к наружному диаметру конвертера:
Нн Dн = 958 875 = 109
Диаметр выпускного отверстия:
dотв = 01 + 000033 · Q = 01 + 000033 · 350 = 0215 м.
Принимаем dотв = 170 м.
РАСЧЕТ ПАРАМЕТРОВ И КОНСТРУИРОВАНИЕ КИСЛОРОДНОЙ ФУРМЫ
1 Расчет сопла Лаваля
Расчет сопла Лаваля сводится к определению длины сопла и размеров его критического входного и выходного сечений. Исходными данными для этого являются расход кислорода (V0) давление (P1) и температура (T1) его перед соплом в фурме.
На основании данных расчета материального расчета плавки имеем:
удельный расход технического кислорода на 1 т садки 551 м3т;
удельную интенсивность продувки 3 м3т·мин;
давление и температуру перед соплом соответственно Р1=14 атм и Т1=298К;
Количество сопел в головке фурмы принимаем равным 6 шт;
Чтобы исключить возможность истечения кислорода с недостатком давления и возможность отрыва струи от стенок сопла принимаем величину Р2 на 01 атм больше давления окружающей фурму среды.
Площадь критического сечения сопла Лаваля (Fкр) вычисляется по уравнению неразрывности составленному для этого сечения:
G = ρкр · Wкр · Fкр = const
гдеG - массовый расход кислорода кгс;
ρкр - плотность кислорода в критическом сечении кгм3;
Wкр - скорость кислорода в критическом сечении мс.
Массовый расход кислорода можно определить по уравнению:
гдеV0 - объемный расход кислорода м3с;
ρ0 - плотность кислорода при нормальных условиях кгм3.
Тогда ρкр = Wкр · Fкр = V0 · ρ0 откуда
или с учетом количества сопел в фурме
где 350 - емкость конвертера т;
- удельная интенсивность продувки м3т·мин;
- количество секунд в 1 минуте.
При нормальных условиях плотность технического кислорода (кгм3) состоящего из 996% О2 и 04% N2
ρ0 = (32 · 0.0996) 22.4 + (28 · 0.004) 22.4 = 1428
Плотность кислорода в критическом сечении можно определить по уравнению
гдеРкр - давление кислорода в критическом сечении ат;
Tкр - критическая температура.
Определим давление в критическом сечении сопла по формуле:
Ркр = 0528 · Р1 = 0528 · 14 = 739 ат.
Вычислим критическую температуру:
Ткр = (2 · Т1) (к + 1) = (2 · 298) (14 + 1) = 2483 К.
Скорость в критическом сечении определяется по уравнению:
Представляя найденные величины в уравнение получим Fкр в расчете на одно сопло применительно к шестисопловой фурме:
Диаметр сопла в критическом сечении составит:
Принимаем dкр = 47 мм.
Площадь сечения одного сопла на выходе определяется по формуле:
гдеV2 - удельный объем кислорода при Т2 и Р2 м3кг;
W2 - скорость кислорода на срезе сопла Лаваля (на выходе) мс.
Удельный объем кислорода (V2) с учетом параметров (Т2 и Р2) определится по уравнению:
Температура кислорода (Т2) после его расширения до Р2 = 11 ат определяется по формуле:
V2 = RT2 P2 = (265 · 144) 11000 = 0347 м3кг.
Скорость на срезе сопла определим уравнением:
dвых = ринимаем dвых = 73 мм.
Увеличение сечения от Fкр до Fвых происходит на участке lзакр длина которого (мм) при принятом угле раскрытия равном 10° составит:
Длина докритической части сопла (мм):
lдокр = dкр 2 = 47 2 = 235 мм.
Принимаем lдокр = 26 мм. Радиус скругления сопла в докритической части при переходе к критическому сечению принимаем равным диаметру критического сечения (мм):
Обычно на практике Rскр = (065 - 15) · dкр.
Диаметр входного сечения сверхзвукового сопла dвх определяется значениями lдокр и Rскр графически. В данном случае dвх = 58 мм.
Общая длина сопла составит:
l0 = lдокр + lзакр = 26 + 126 = 152 мм.
Принимая во внимание что в практике кислородно-конвертерного процесса наблюдается тенденция расположения фурмы при продувке на выосте (Нф) близкой к длине ядра начальных скоростей струи (Х0) определим рациональную в данных условиях рабочую высоту фурмы над уровнем ванны в спокойном состоянии.
На основании приведенного работе выражения по определению длины ядра начальных скоростей струи и получим:
Нф = 247 · Р1 · dкр = 247 · 14 · 0047 = 165 м
гдеР1 - давление кислорода на входе в сопло атм;
dкр - критический диаметр сопла м.
2 Разработка конктрукции наконечника и фурмы
Толщину стенки сопла берем равной 10 мм (обычно она равна 8-12 мм).
Принимаем угол наклона сопел к вертикальной оси равным 20° при размещении сопел на торцевой части головки в один ряд.
По полученным данным о размерах сопел а также угла наклона их к оси фурмы путем графических построений определяем размеры и проектируем конструкцию коллектора и торцевой части головки фурмы.
В соответствии с полученными размерами выбираем необходимые диаметры кислородоподводящей (Дк) разделительной (Др) и наружной (Дн) труб фурмы по ГОСТ 8732-58 на стальные бесшовные трубы выпускаемые нашей промышленностью. При этом учитывается необходимость обеспечения достаточного расхода воды на охлаждение фурмы а также соотношение сечений каналов для подвода и отвода воды.
В данном случае Дк =325·8 мм Др = 377·9 мм Дн = 426·9 мм.
На основании данных о расстоянии от уровня спокойного металла в конвертере до фурменного окна в камине а также крайнего верхнего положения каретки закрепления фурмы определяем длину последней в 23 м.
С учетом удаления патрубков фурмы от стационарных точек подвода кислорода и воды к агрегату выбираем длину гибкого металлического рукава в 23 м.
3 Расчет расхода воды на охлаждение фурмы
Потери тепла (Qф) на охлаждение кислородной фурмы определяют по формуле:
Qф = 314 · Dн (q1 · ln.к. + q2 · lн.к.)
гдеq1 q2 - соответсвенно величина удельного теплового потока для участка фурмы наводящейся в полости конвертера и для участка расположенного над конвертером МДжм2·ч;
Dн - наружный диаметр фурмы м.
При наружном диаметре фурмы 0426 м и глубине опускания ее в конвертер на 60 (глубина опускания определяется разностью между расстояние от уровня спокойной ванны до среза горловины конвертера и рабочей высоты фурмы над ванной) потери тепла во время продувки при q1 = 2500 и q2 = 3750 МДжм2·ч составит:
Qф = 314 · 0426 (2500·6 + 375·17) = 2859206 МДжч или 2859906·103 кДжч.
При этом весовой расход охлаждающей воды будет равен:
гдеС - теплоемкость воды (419 кДжкг·К);
Твых Твх - температура воды на выходе и входе в фурму К.
Обычный расход воды на охлаждение фурмы
QH2O = GH2O ρH2O = 4549253 1000 = 4549 м3ч.
4 Определение рабочего давления кислорода перед гибким шлангом фурмы
Вначале определяем давление технического кислорода на входе в фурму по формуле:
гдеРв.ф. - давление технического кислорода при входе в фурму атм;
Dк - внутренний диаметр кислородоподводящей трубы см;
ρ0 - плотность технического кислорода при нормальных условиях кгм3;
V0 - расход технического кислорода м3с;
Р1 - давление технического кислорода на входе в сопло (выше принято равным 14 атм);
λф - коэффициент трения принятый для металлической трубы равным 005;
lф - длина фурмы м (выше была принята 23 м).
После подстановки необходимых величин в уравнение получаем:
По аналогии с вышеприведенным расчетом определяем давление технического кислорода перед гибким шлангом фурмы. Давление кислорода перед гибким шлангом определяется по аналогичному выражению:
где λш - коэффициент трения для металлорукавов принятый равным 01;
Dш - внутренний диаметр металлорукава см.
Таблица 22 - Основные размеры и эксплуатационные данные проектируемой фурмы
Условное обозначение
Давление кислорода перед гибким шлангом
Давление кислорода перед соплами
Расход воды на охлаждение фурмы
Количество сопел в фурме
Диаметр сопла в критическом сечении
Диаметр сопла на выходе
Длина сопла в том числе:
длина докритической части
длина закритической части
Угол раскрытия сопла
Угол наклона сопел к вертикали
РАЗРАБОТКА ТЕХНОЛОГИИ КОНВЕРТЕРНОЙ ПЛАВКИ
Для разработки технологии конвертерной плавки необходимо произвести пересчет расходных коэффициентов полученных в пункте 1 на садку конвертера. Для данного расчета производится пересчет на садку конвертера 350 т.
Таблица 23 - Пересчет расходных коэффициентов материального баланса
Также произведем пересчет количества ферросплавов расходуемых на плавку на садку конвертера:
марганец металлический т или 735 кг;
силикомарганец 0035 · 35 = 0122 т или 122 кг;
алюминий т или 798 кг;
1 Шихтовые материалы для выплавки стали
Чугун поставляется следующего химического состава: S Мn – 041%; S – 0013%; Р – 0086%.
Температура чугуна 1380°С.
Стальной лом используемый в конвертерной плавке имеет размеры обеспечивающие свободную его загрузку в конвертер.
Весь лом проверяется и обезвреживается от взрывоопасных и легковоспламеняющихся предметов.
Лом доставляется к конвертерам в совках емкостью 50 м3.
Допускается использование в качестве металлошихты остатков металла в виде "блинов" "козлов" "коржей" очищенных от шлака и огнеупоров. Габаритные размеры остатков металла должны обеспечивать свободную их загрузку в конвертер. Запрещается использовать в шихту промасленную стружку а также лом загрязненный горюче-смазочными материалами вредными примесями (серой или фосфором) неочищенный от цветных металлов (цинка олова свинца меди и др.) неосвобожденный от взрывоопасных и легковоспламеняющихся предметов и материалов а также снега льда и закрытых сосудов.
2 Добавки шлакообразующие материалы и ферросплавы
Для наводки шлака применяется свежеобожженная известь с крупностью кусков 13-70 мм с суммарным содержанием СаО + MgO 896% потери при прокаливании 92%.
Длительность хранения извести в бункерах конвертерного цеха не должна превышать одних суток. Применение некондиционной извести (СаО + MgO менее 86%) и извести-пушонки не допускается.
Применяются в качестве шлакообразующих материалов флюсы содержащие MgO (ФОМИ).
Для корректировки теплового баланса плавки в качестве теплоносителей используется каменный уголь ССО.
Для раскисления и легирования стали при выпуске плавок из конвертера применяются следующие ферросплавы: марганец металлический а также алюминий.
Все раскислители и легирующие материалы должны удовлетворять требованиям соответствующих ГОСТов применяться дробленными в кусках не более 50мм.
3 Шихтовка плавки и загрузка конвертера
После выпуска предыдущей плавки мастером конвертеров вместе со сталеваром производится осмотр футеровки конвертера и сталевыпускного отверстия обращая особое внимание на состояние кладки днища при необходимости производится подварка торкретирование футеровки или ремонт сталевыпускного отверстия. При оголении футеровки днища (просматриваются швы кладки рабочего слоя) на шлак присаживается до 50% извести расходуемой на плавку конвертер покачивают и при наличии жидкой составляющей шлака ее сливают в чашу.
При удовлетворительном состоянии футеровки конвертера после выпуска плавки производится подготовка шлака для нанесения шлакового гарнисажа.
Для подготовки шлака для нанесения шлакового гарнисажа на футеровку конвертера используется сырой обожженный офлюсованный доломит бой шиберных плит известь и каменный уголь (антрацит кокс). Расход материалов зависит от количества и состояния шлака предыдущей плавки и составляет для доломита 05-25 т для каменного угля 01-05 т. Материалы набираются в промежуточный бункер и отдаются одной порцией одновременно с открытием азота. Раздувка шлака азотом производится при максимальном нижнем положении фурмы (0 м по Сельсину) с расходом азота 700-1300 м3мин. Продолжительность наведения шлакового гарнисажа должна быть не менее 2-х минут.
Загрузка шихты в конвертер начинается с завалки металлолома. Во избежание разрушения футеровки конвертера сначала загружается совок с легковесным ломом а затем с тяжеловесным.
После завалки металлолома при необходимости производится его прогрев.
Продолжительность заливки чугуна должна быть не менее 3 мин. Запрещается заливать чугун при попадании в конвертер воды. В зимнее время (без прогрева лома) в целях безопасности заливку чугуна производить не ранее чем через 4 минуты после завалки лома.
После заливки чугуна конвертер устанавливается в вертикальное положение опускается фурма и начинается продувка плавки.
4 Режим ведения плавки
Продувка плавок может вестись по режимам без дожигания с частичным или полным дожиганием отходящих газов в камине.
Основным режимом работы конвертеров является продувка без дожигания отходящих газов.
Для продувки плавки используется кислород чистотой 996% и давлением 14 атм с содержанием азота 04%.
Продувка плавки в режиме отвода газов без дожигания обеспечивается работой автоматического регулирования избыточного давления конвертерных газов в камине котла в пределах 07 - 10 мм.вод.ст. Для запуска системы в работу машинист дистрибутора до начала продувки устанавливает режим управления полузаслонками труб Вентури в "автоматический" и задатчиком устанавливает необходимое избыточное давление под "юбкой" - 07-10 мм.вод.ст.
Продувка осуществляется через 6-ти сопловую фурму.
После "устойчивого" зажигания плавки опускается "юбка". Через одну минуту после опускания "юбки" автоматически или с дистанционного управления включается дожигающее устройство и зажигается факел на свече. На протяжении всей продувки машинист дистрибутора следит за поддержанием заданного давления под юбкой 07 - 10 мм.вод.ст. Если через 3 мин после включения дожигающего устройства факел на свече не загорится то дальнейшая продувка ведется по режиму с полным дожиганием отходящих газов в камине.
В течение первых 2-3 мин продувка ведется при положении фурмы 30-40 м по Сельсину после чего фурма плавно опускается до 08-13 м.
5 Технология выплавки стали марки 08Ю
Известь на плавку отдается: в количестве до 40% от требуемого на плавку через 30-40 с после зажигания плавки еще 40-50% на 2 мин продувки оставшаяся часть извести присаживается по ходу продувки порциями до 500 кг равномерно с весов-дозаторов через открытые шиберные затворы промежуточных бункеров до 10 мин продувки.
Известь присаживается в количестве 2287т для получения жидкоподвижного однородного конечного шлака с основностью 3.
Магнезиальные материалы (ФОМИ) присаживаются в количестве 49т на 1-2 мин продувки вместе с известью.
Электродный бой присаживается в количестве 105т на первых минутах продувки.
Момент окончания продувки определяется по количеству израсходованного кислорода показаниям газоанализаторов и прибора регистрирующего выход дымовых газов по рекомендации АСУ плавкой а также ориентируясь на предыдущие плавки.
Момент окончания продувки определяется по количеству израсходованного кислорода времени продувки и визуально по виду факела. Режим окончания продувки должен обеспечить получение жидкоподвижного уваренного шлака. Общее содержание оксидов железа в шлаке должно быть не более 25% а основность – 3.
По окончании продувки производится повалка конвертера отбор проб металла и шлака и замер температуры металла термоблоком. Ложка для отбора проб металла и шлака должна быть сухой и чистой.
Проба металла раскисляется в ложке чистой алюминиевой проволокой из расчета получения в пробе не более 05% алюминия и заливается в металлический стаканчик. Запрещается присадка в пробу других раскислителей и материалов. Проба не должна иметь шлаковых включений признаков усадочной раковины и трещин. Проба конечного шлака отбирается с ручки ложки. Отобранные пробы охлаждаются и немедленно отправляются в экспресс-лабораторию.
В пробе металла определяется содержание углерода серы фосфора марганца хрома никеля меди при необходимости азота и остаточного кремния.
В пробе шлака определяется содержание кремнезема окиси кальция закиси железа окиси магния.
Режим окончания продувки должен обеспечивать получение достаточно жидкоподвижного без кусков нерастворившейся извести шлака с основностью 3 и содержанием закиси железа до 25%.
В случаях когда продувка прекращена при недостаточной температуре металла высоком содержании углерода фосфора или серы производится додувка плавки. На плавке должно быть не более одной додувки на температуру фосфор серу и шлак продолжительностью не более 2 минут. Количество додувок на углерод и их продолжительность не регламентируется.
Додувка плавки производится при следующем положении фурмы:
а)при додувке на углерод и температуру фурма должна быть в положении конца продувки (10 - 13 м по сельсину);
б)при додувке на фосфор серу и шлак с расходом кислорода 400 м3мин высота фурмы увеличивается на 05 м по отношению к ее положению в конце продувки а при додувке с расходом кислорода 300 м3мин положение фурмы не меняется.
После додувки плавки любой продолжительности отбираются повторно пробы металла и шлака для экспресс-анализа и производится замер температуры металла. Додувки являются отклонением от нормальной технологии процесса и должны отмечаться в паспорте плавки с указанием причин.
При перегреве металла плавка охлаждается присадкой извести доломита известняка или путем выдержки плавки в конвертере с обязательным повторным замером температуры металла.
Плавки с недостаточной температурой металла додуваются до температуры не ниже середины интервала для данной марки стали.
Разрешается при перегреве металла производить охлаждение металла продувкой азотом с присадкой по необходимости извести или доломита.
Ковш для приема стали должен быть тщательно очищен от настылей и остатков металла шлака глины мусора хорошо просушен. Допускается подавать под плавку ковш с незначительными чистыми остатками металла от предыдущей плавки в виде скрапины на дне ковша.
Ковш с новой футеровкой под выпуск углеродистой качественной спокойной и легированной стали подается только после разливки не менее одной плавки других марок стали.
Состояние и чистота ковша проверяются контролером ОТК и мастером конвертеров до начала слива плавки и результаты записываются в паспорт.
Во время выпуска необходимо следить за струей металла и перемещая сталевозную тележку не допускать попадания струи на стенку ковша. Выпуск металла производить через сталевыпускное отверстие обеспечивающее организованную струю и длительность выпуска не менее 3 минут на первой кампании плавок после перефутеровки и 4 минут - на последующих.
Разрешается проводить обработку стали твердым и шлакообразующими смесями на основе извести (отсева извести) — 3 - 6 кгт; плавикового шпата – 06 - 16 кгт. По окончании выпуска плавки осуществляется отсечка шлака шаром либо быстрым подъемом конвертера при появлении шлака.
По окончании выпуска плавки конвертер поворачивается и оставшийся шлак сливается через горловину в шлаковую чашу. Допускается оставление конечного шлака для горячего ремонта.
Раскисление и легирование стали производится марганцем металлическим силикомарганцем и алюминием в ковше.
Раскислители и легирующие добавки расходуются только по весу из расчета получения заданного содержания элементов в готовой стали.
По хим.составу ферросплавы должны удовлетворять требованиям соответствующих ГОСТов и ТУ.
Запрещается применение ферросплавов с неизвестным хим. составом и смешанных между собой.
Вводимые в ковш ферросплавы должны быть сухими в кусках не более 50 мм алюминий - в кусках не более 4 кг.
Присадку ферросплавов начинать после наполнения металлом 15 ковша и заканчивать до наполнения его на 23 высоты при этом особое внимание обращать на равномерность поступления в ковш ферросплавов не допуская их закозления и попадания в шлак. Запрещается присадка ферросплавов через окисленный первичный шлак.
ФУТЕРОВКА КИСЛОРОДНОГО КОНВЕРТЕРА
Футеровка кислородного конвертера подвергается целому ряду разрушающих воздействий. К ним относятся: механические включающие воздействие на футеровку при загрузке шихты; абразивное воздействие движущегося с большими скоростями газового потока несущего твердые и жидкие частицы различных размеров и состава; размывающее воздействие движущегося расплава; химические (включающие коррозионные) воздействия на футеровку различных по составу шлаков расплавов плавильной пыли шлакообразующих материалов; термические воздействия вследствие резких колебаний температур связанных с технологическими операциями а также неравномерность распределения температур по поверхности рабочего пространства.
1 Материалы применяемые для футеровки конвертера
Конвертерные огнеупоры должны отвечать следующим основным требованиям: обладать высокой металлошлакоустойчивостью и термостойкостью иметь повышенную механическую прочность и сопротивляемость истирающему воздействию расплавов и шихтовых материалов при высоких температурах обладать сравнительно низким коэффициентом термического расширения быть недефицитными и иметь сравнительно низкую стоимость.
В настоящее время для изготовления огнеупорных изделий используют обожженные доломит и периклаз а также различные их смеси с получением смоло и пекосвязанных периклазоизвестковых переклазоуглеродистых периклазовых известково-периклазовых огнеупоров. Указанные материалы определенного фракционного состава смешивают с обезвоженной каменноугольной смолой или пеком нагретыми до 130 - 150 °С. Из полученной массы прессуются под давлением (≥130 - 150 МПа) фасонные изделия. Недостатком таких безобжиговых огнеупорных материалов является ограниченный срок их хранения не превышающий в зависимости от состава исходных материалов и качества изготовления 3 - 7 суток.
Периклазоуглеродистые материалы в зависимости от состава исходной шихты содержат 94 - 98% MgO 15% CaO содержание углерода (сверх 100% огнеупорного материала) – 10 - 25% плотность 288 - 306 кгм3 открытая пористость 25 - 7% предел прочности при сжатии 35 - 63 МПа температура начала деформации под нагрузкой может составлять 1700°С.
2 Огнеупорные растворы и массы
Растворы и массы применяют для заполнения швов и неплотностей которые образуют между кирпичами при выполнении футеровки конвертеров подмазки горловины горячего ремонта сталевыпускного отверстия уплотнения стыка между футеровкой днища и корпусом конвертера и т.д. Растворы и массы могут состоять из одного материала или смеси материалов с добавкой связующих веществ. Они должны обладать огнеупорностью приблизительно равной огнеупорности кирпича в кладке хорошей сопротивляемостью разъедающему действию шлака. Материалами для приготовления огнеупорной массы служит магнезитовый или доломитовый порошки. В качестве связующего применяют препарированную смолу сернокислый магний и жидкое стекло.
Для заделки сталевыпускного отверстия и подмазки горловины конвертера применяют смесь состоящую из 80% и более периклазошпинелидного или магнезитового кирпича 15% огнеупорной глины и 5% графита. Массу затворяют водой до тестообразного состояния.
Для горячего ремонта сталевыпускного отверстия применяют водный раствор изготовленный из магнезитового порошка фракции 4 мм с добавлением 5-6% сернокислого магния или жидкого стекла.
3 Конструкция футеровки конвертера
Корпус кислородного конвертера состоит из днища нижнего усеченного
конуса цилиндрического пояса и конической горловины. У основания верхней конической части кожух конвертера имеет сталевыпускное отверстие которое предназначено для лучшего отделения стали от шлака во время её выпуска в ковш после каждой плавки. Кожух конвертера имеет симметричную горловину.
Днище кислородного конвертера предлагается выполнить вставным. Вставное днище представляет собой металлическую футерованную крышку вмонтированную заподлицо в люк определенного диаметра. Относительно небольшие размеры такого днища и его центральное положение позволяют сохранить жесткость и прочность корпуса обеспечивая при этом быстрое охлаждение футеровки во время ремонта и организацию подачи огнеупорных материалов с уровня пола цеха. Однако при ремонте такого днища футеровка разрушается и выполняется вновь.
В соответствии с профилем конвертера его футеровку подразделяют на следующие основные части: днище цилиндрическую часть и горловину. Кладка этих частей имеет некоторые особенности как вследствие своего расположения так и условий службы. Для огнеупоров горловины конвертера характерны специфические условия службы: налипание металла на футеровку в результате его выбросов и резкие термические удары. Футеровка нижней конической части и днища контактирует с бурлящим металлом и в меньшей степени со шлаком. Футеровка цилиндрической части разрушается преимущественно в результате химического взаимодействия с бурлящим шлаком нагретым до высокой температуры с последующим смыванием прореагировавшего рабочего слоя газовым потоком металлом и шлаком. Служба огнеупоров во всех зонах усложняется значительными термическими ударами и воздействием переменной газовой среды. Завалочная сторона футеровки разрушается механически при загрузке скрапа и чугуна. Футеровка сталевыпускного отверстия находится в чрезвычайно жестком тепловом режиме: во время выпуска плавки рабочая поверхность кладки нагревается от 400 - 700 до 1590 - 1680 оС и подвергается истирающему воздействию жидкого металла и шлака. В связи с этим важно чтобы футеровка этой части обладала хорошей термической стойкостью и высокой прочностью. В большинстве случаев наибольший износ наблюдается в районе шлакового пояса и загрузочной стороны. Интенсивно разрушается также кладка сталевыпускного отверстия.
Футеровка конвертера должна иметь высокую прочность и плотность. Для обеспечения прочности и плотности кладки большое значение имеет правильный расчет и распределение температурных швов в огнеупорной кладке так как недостаточное их число ведет к вспучиванию разрушению кладки и деформации металлического кожуха а избыточное их количество – к проникновению металла и шлака в футеровку. Материалом для температурных швов служат дерево картон толь. Они закладываются между кирпичами в виде пластин соответствующих размерам плоскостей укладываемого кирпича. Температурные швы огнеупорной кладки футеровки делают рассредоточенными что позволяет обеспечить равномерный рост кладки и исключает проникновение металла и шлака в кладку.
Футеровка конвертера выполняется из нескольких слоев различных огнеупорных материалов. В настоящее время в эксплуатации находится двухслойная футеровка состоящая из арматурного и рабочего слоев.
Арматурный слой предназначен для защиты металлического кожуха конвертера от непосредственного воздействия расплава. Поэтому арматурный слой изготавливается из обожженных высококачественных огнеупорных материалов (периклазового кирпича) и выкладывается толщиной 115 230 мм. Зазоры между стальным корпусом и кирпичом заполняют периклазовым порошком без использования раствора. Обычно арматурный слой выдерживает несколько кампаний без замены.
Рабочий слой обеспечивает технологический процесс ведения плавки. Как правило в настоящее время он изготавливается из периклазоуглеродистых огнеупоров. Кладку ведут без раствора с перевязкой швов кольцами или по винтовой линии.
Кладка по толщине рабочего слоя выполняется как правило из двух кирпичей (блоков) различной длины. Стойкость рабочего слоя стен определяет длительность кампании конвертера и его технико-экономические показатели.
Футеровка рабочего слоя верхней конической части выполняется горизонтальными рядами. В отечественной практике три - десять верхних рядов выкладываются из периклазошпинелидных обожженных огнеупоров на соответствующих растворах. Плохая стойкость огнеупоров обусловлена повышенным износом кладки на этом участке вследствие ударных и абразивных воздействий загружаемых твердых шихтовых материалов окисления углерода связки огнеупора за счет контакта с окислительной атмосферой и взаимодействия воды с материалом кирпича попадаемой при подтекании фурмы или охладителя конвертерных газов.
Профиль футеровки днища может иметь сферическую или плоскую форму. Во всех случаях на металлический кожух укладываются листовой асбест и выравнивающий слой периклазовой массы на сернокислой магнезии или доломитовой массы на смоляной связке. Рабочий слой выполняется из периклазоуглеродистого кирпича поставленного на торец обычно в два слоя или в один слой. Вся кладка выполняется без раствора с перевязкой швов каждого слоя путем поворота последующего слоя на 45 90°. Швы кладки заполняются тонкомолотым периклазовым порошком размером частиц менее 02 мм.
В районе границы верхней конической и цилиндрической частей конвертера находится сталевыпускное отверстие.
Угол наклона канала отверстия к горизонтали может изменяться в широких пределах от 0 до 45° и определяется удобством горячих ремонтов отверстия его стойкостью зависящей от гидродинамики струи расплава изменением траектории струи в процессе слива требующего точной центровки относительно сталеразливочного ковша исключением возможности совместного слива металла и шлака.
Учитывая большие скорости металла и его размывающие воздействия на огнеупоры при прохождении через сталевыпускное отверстие последнее выкладывают из специальных блоков изготовленных на основе плавленых периклазовых огнеупоров сравнительно неплохо противостоящих размывающему действию расплава. Однако стойкость сталевыпускного отверстия пока остается самой низкой по сравнению с другими элементами футеровки конвертера.
Длина выпускного отверстия обычно составляет 1200 - 1500 мм и его футеровка выступает за корпус конвертера на расстояние 500 - 700 мм в зависимости от угла наклона отверстия что обеспечивает необходимую траекторию струи металла. Внутренний конец блоков закреплен в рабочем слое футеровки. Остальная часть блоков крепится в арматурном слое который выполняется из периклазовых огнеупоров.
Как уже упоминалось износ огнеупорной кладки в кислородных конвертерах имеет сложный характер и зависит как от качества огнеупорных материалов так и от технологии плавки. Основным фактором является воздействие газошлакометаллической эмульсии. Это подтверждается тем что наиболее интенсивный износ футеровки наблюдается как правило в средних и верхних участках футеровки. Общий характер износа футеровки наиболее полно характеризуется топографией ее рабочей поверхности в конце кампании.
4 Ремонт футеровки конвертера
В процессе службы футеровка изнашивается слои огнеупоров смываются и переходят в шлак в кладке образуются местные прогары и углубления а на верхних рядах горловины – настыли. Для восстановления изношенной футеровки применяют ремонт.
Ремонты делятся на горячие когда ремонтируется какой-то наиболее изношенный участок футеровки и холодные в процессе которых заменяется обычно вся рабочая часть футеровки.
В отечественной практике для горячего ремонта или восстановления части футеровки наибольшее распространение получил так называемый метод факельного торкретирования.
Сущность процесса заключается в создании в полости конвертера высокотемпературного факела нагруженного торкрет – массой из тонкомолотого огнеупорного порошка и топлива. Благодаря высокой температуре факела (1800 – 2000 оС) достигаемой в результате сжигания топлива в струе одновременно подаваемого кислорода мелкодисперсные частицы огнеупорного порошка переходят в пластическое состояние поэтому формирование торкрет – слоя происходит почти мгновенно. Факел обеспечивает транспортировку и нагрев частиц аэродинамикой факела обусловлена сепарация частиц высокая температура факела обеспечивает формирование торкрет – покрытия.
Особенностью этого способа торкретирования является очень быстрый нагрев частиц в факеле топливно-кислородной горелки. Зерна периклаза подвергаются в факеле термическому удару и попадают на футеровку в высокоактивированном состоянии.
В качестве торкретмассы на металлургических заводах применяются двухкомпонентные смеси состоящие из 70 - 75% периклазового порошка и 25 - 30% порошка кокса или угля.
Периклазовые порошки содержат 85 - 90% MgO и имеют размер частиц ≤03 мм содержание фракции 01 составляет ≥ 85 - 90%. Помол топлива осуществляется до зерен крупностью ≤ 1 мм. Кокс и угли используемые для торкретмасс не должны иметь зольность выше 17% и влажность не более 05%.
Качество торкрет – покрытия зависит от температуры процесса. Торкретирование необходимо начинать через 3 - 5 минут после слива шлака с предварительным разогревом футеровки не менее трех минут. Для исключения скалывания торкрет – покрытия нужно после торкретирования не допускать простои длительностью больше 30 минут.
Для повышения стойкости футеровки конвертера возможно использование технологии нанесения шлакового гарнисажа.
Сущность технологии заключается в том что после выпуска металла в конвертере оставляют весь шлак образующийся в ходе плавки за исключением того количества которое уходит в сталеразливочный ковш самотеком. Шлак подготавливают к раздуву на рабочую поверхность футеровки подавая шлакообразующие (известь известняк доломит и т.д.). Производят кратковременное перемешивание расплава смесью нейтральных газов для ассимиляции введенных материалов. После начинают раздувать полученный шлак на футеровку конвертера в процессе чего шлак меняет свою структуру цементируется на футеровке образуя огнеупорную арматурную массу.
Операцию нанесения шлакового гарнисажа производят после выпуска предыдущей плавки.
ГАЗООТВОДЯЩИЙ ТРАКТ КОНВЕРТЕРА
Независимо от типа конструкции конвертера и технологического процесса тракт должен состоять из систем отвода охлаждения очистки и утилизации конвертерных газов. Это обусловлено тем что в процессе продувки из конвертера выделяются газы в количестве 60 - 80 м3т стали с температурой 1500 - 1700°С и содержащие пыли от 50 до 350 гм3 (а в ряде случаев и более). Газ как правило содержит до 90% оксида углерода.
В соответствии с требованиями санитарных норм выброс в окружающую атмосферу таких газов недопустим. В то же время конвертерные газы могут служить источником вторичных энергоресурсов для утилизации физической и химической теплоты. Учитывая что оксид углерода в смеси с воздухом является взрывоопасным в интервале концентраций 125 - 745% СО система отвода газа должна быть взрывобезопасной. Отсутствие технической возможности очистки от пыли отходящих высокотемпературных газов обусловило разделение системы отвода газов на два самостоятельных участка участок охлаждения и участок очистки.
Устанавливаем за конвертером установку без дожигания оксида углерода. В качестве котла-охладителя используем радиационно-конвективный котел типа ОКГ – 100-3 соответствует расчетному количеству отходящих конвертерных газов (по расчетам это количество равно 58 тыс. м3ч). Установленный за конвертером котел-охладитель имеет Г-образную компоновку. ОКГ включает барабан где собирают вырабатываемый пар циркуляционные насосы систему водо и пароподводящих труб и расположенный над конвертером газоход.
1 Охлаждение конвертерных газов
Для охлаждения конвертерных газов используются разнообразные по конструкции и принципу действия котлы-утилизаторы получившие название охладителей конвертерных газов (ОКГ).
Учитывая что высокотемпературные отходящие газы имеющие большую запыленность способны интенсивно излучать теплоту охладитель имеет в своем составе котел радиационного действия в котором газ охлаждается до температуры 1000 900°С Дальнейшее охлаждение может осуществляться либо с утилизацией теплоты в конвективных котлах либо путем подачи воды непосредственно в газовый поток.
Радиационная часть ОКГ представляет собой подъемный газоход внутренняя часть которого выполнена из трубчатых экранных панелей. Вода циркулирующая в этих трубках отбирая теплоту поступает в виде пароводяной смеси в бак-сепаратор. Все ОКГ работают с принудительной циркуляцией что требует сооружения специальной насосной станции.
Котел охладитель конвективного действия представляет собой пакеты труб расположенных в определенном порядке по которым циркулирует охлаждающая вода. При просачивании дымовых газов между трубками их температура снижается до 200 - 250° С. Располагается такой охладитель как правило в опускном газоходе.
Необходимое дальнейшее охлаждение газов осуществляется путем прямой подачи воды в наклонную или опускную часть газохода.
2 Установки без дожигания оксида углерода
Предлагается установить в конвертерном цехе установку работающую без дожигания оксида углерода с применением чисто радиационных котлов-охладителей и использованием только физического тепла конвертерных газов. В этом случае количество газов следовательно и размеры газового тракта в 3 - 5 раз меньше. Газ прошедший очистку может быть направлен в газгольдер с последующим использованием в качестве топлива.
Вследствие отсутствия процессов горения в газоотводящем тракте химический и дисперсный составы пыли выходящей из конвертера изменяются мало что благоприятнее для процессов очистки. Концентрация пыли в газе может достигать 200 гм3 а иногда и более.
Сокращение размеров газоотводящего тракта значительно облегчает компоновку и эксплуатацию оборудования в конвертерном цехе поэтому я предлагаю эту установку.
При работе установок без дожигания оксида углерода увеличивается возможность образования в газоотводящем тракте взрывоопасных смесей кислорода и оксида углерода. Взрывобезопасная работа газового тракта обеспечивается тем что в начале и после окончания кислородной продувки на границе раздела кислорода и оксида углерода автоматически образуется тампон из нейтрального газа (CО2+N2) надежно отделяющий одну среду от другой и не позволяющий им смешиваться.
Образование тампона обеспечивает нависающий над конвертером колпак (юбка) опускающийся и частично перекрывающий зазор во время продувки и автоматически поднимающийся в начале и конце продувки. В моменты подъема колпака зазор полностью открыт в него устремляется воздух и происходит дожигание с образованием СО2 т. е. образуется тампон из нейтральных газов как и в случае установок с частичным дожиганием СО. В отличие от последних в установках без дожигания СО концентрация последнего в конвертерных газах во время продувки значительно выше что делает их вполне пригодными для использования в качестве топлива.
При проектировании газоотводящего тракта установок без дожигания СО особое внимание нужно уделять его аэродинамической форме (отсутствию газовых мешков) и тщательному уплотнению стенок газоходов. Широкое распространение в крупных конвертерных газоочистках работающих без дожигания СО получили прямоугольные трубы Вентури с регулируемым сечением горловины. Положение регулирующих створок в них автоматически изменяется и соответствует давлению газа над конвертером и следовательно количеству газов выходящих из него. Регулируемые трубы Вентури обеспечивают эффективную очистку отходящих газов независимо от колебаний их расхода и запыленности поддержание необходимого давления разрежения над конвертером использование при пленочном орошении воды с повышенной концентрацией вредных веществ. Типичная схема газоотводящего тракта конвертера работающего без дожигания СО приведена на рисунке 2.
– конвертер; 2 – котел-охладитель; 3 – орошаемый газоход; 4 – Бункер орошаемого газохода; 5 – трубы Вентури первой ступени; 6 – бункер первой ступени; 7 – соединительный газоход; 8 – регулируемая труба Вентури второй ступени; 9 – бункер второй ступени; 10 – каплеуловитель; 11 – подвод воды к орошаемому газоходу; 12 – гидрозатвор; 13 – отвод шлама; 14 – отвод газов к дымососу.
Рисунок 2 - Схема очистки со скрубберами Вентури за конвертером
Газы выходящие из конвертера пройдя котел-охладитель радиационного типа при температуре 750 - 1000°С поступают в орошаемый газоход. Вода к орошаемому газоходу подводится из оборотного цикла. Впрыскиваемая вода охлаждает газы до 250 - 300°С. К бункеру орошаемого газохода примыкают две трубы Вентури являющиеся первой ступенью очистки. Из бункера труб Вентури газы делая поворот поступают на вторую ступень очистки - в регулируемую трубу Вентури а затем после бункера направляются в каплеуловитель из которого по газоходу отсасываются дымососом и выбрасываются в дымовую трубу где дожигаются на свече.
В последнее время на отдельных предприятиях с целью повышения надежности эксплуатации в газоотводящие тракты конвертеров внесены некоторые изменения и дополнения основными из которых являются: впрыскивание с помощью форсунок тонкого распыливания в верхнюю часть подъемного газохода мелкодиспергированной воды с тем чтобы быстрее охладить частицы пыли и перевести их из жидкого состояния в твердое во избежание зашлаковывания верхней крышки котла-охладителя; замена орошаемого газохода и первой ступени труб Вентури полым форсуночным скруббером что упрощает газоотводящий тракт снижает его гидравлическое сопротивление позволяет освободиться от крупной пыли и кусков настылей отделившихся от поверхностей нагрева уменьшает абразивный износ и предохраняет отводящие шламопроводы от засорения; установка второго каплеуловителя перед дымососом для защиты последнего от капель образующихся в результате охлаждения насыщенных влагой газов при прохождении достаточно длинных в большинстве случаев неизолированных металлических газоходов между мокрой очисткой и дымососом.
Регулирование работы газоотводящего тракта может производиться двумя способами: изменением положения лопаток в направляющих аппаратах дымососов и изменением проходного сечения горловины трубы Вентури или плотности его орошения. Наилучшие результаты дает комбинированное регулирование с использованием обоих способов. Дымососы следует выбирать с возможно меньшей зоной помпажа и наиболее крутой характеристикой в рабочем диапазоне.
Для выравнивания колебаний выхода пара после котлов-охладителей обычно устанавливают паровые аккумуляторы представляющие собой большие горизонтально установленные резервуары заполненные водой.
Значительным вторичным энергоресурсом конвертерного производства является теплота сгорания конвертерного газа которая в моменты максимального газовыделения достигает 9 МДжм3; как правило она не используется. Это связано с цикличностью выхода конвертерного газа что требует установки газгольдера вносящей усложнение в эксплуатацию в связи с повышенной взрывоопасностью конвертерного газа.
Методические указания к дипломному и курсовому проектированию по расчету материального баланса кислородно-конвертерной плавки Сост.: Е.В. Протопопов Г.И. Веревкин: СибГИУ.-Новокузнецк 2000.-29с.
Методические указания к дипломному и курсовому проектированию по расчету теплового баланса кислородно-конвертерной плавкиСост.: А.Л. Николаев:СибГИУ.-Новокузнецк2000.-18с.
Раскисление и легирование стали: Методическое указание Сост.: Е.В. Протопопов Г.И. Веревкин К.М. Шакиров: СибГИУ.- Новокузнецк 2001.-20с.
Определение размеров кислородного конвертера: Методическое указание Сост.: А.Г. Чернятевич Г.И. Веревкин: СМИ.- Новокузнецк 1984.-13с.
Проектирование кислородной фурмы для кислородно-конвертерного процесса: методическое указание Сост.: И.П. Герасименко: СМИ.- Новокузнецк1984.-24с.
Выбор основных параметров шихтовки и материальный баланс теплотехнического периода современного мартеновского скрап-рудного процесса (7-9с.): Методическое указание Сост.: И.П. Герасименко Г.И. Веревкин: СМИ.- Новокузнецк 1989.-25с.
Конструкции сталеплавильных агрегатов: Методическое указание Сост.: И.П. Герасименко: СМИ.-Новокузнецк 1980.-22с.
Выплавка внепечная обработка стали на УВОС и разливка стали
в изложницы в конвертерном цехе №2. Технологическая инструкция
ТИ 107-СТ. ККЦ2-01-07 Новокузнецк 2007 г.
Конструкции и проектирование сталеплавильного производства. В.П. Григорьев Ю.М. Нечкин А.В. Егоров Л.Е. Никольский.- Москва: “МИСИС” 1995.-562с.
Газоочистные аппараты и установки в металлургическом производстве. Старк С.Б.: Учебник для вузов. Изд. 2-е переработанное и дополненное.- М.: Металлургия 1990.-400с.
Курсовик-12.СТ.Разрез.dwg

Уровень металлической ванны
Конвертер емкостью 350 т
СибГИУ 2012.150101.08006 КП
Разрез по футеровке и головке
СибГИУ 2012.150101.08006. КП
Периклазоуглеродистый
Периклазоуглеродистые
Курсовик-12.СТ.Три-проекции.dwg

Быстроходный редуктор
Периклазоуглеродистый кирпич
Уровень рабочей площадки
УСЛОВНЫЕ ОБОЗНАЧЕНИЯ:
Конвертер емкостью 350 т
СибГИУ 2012.150101.08006 КП
Три проекции агрегата
СибГИУ 2012.150101.08006. КП
Рекомендуемые чертежи
- 24.10.2015
Свободное скачивание на сегодня
Обновление через: 19 часов 34 минуты
- 23.02.2023