Разработка торсионной подвески прицепа для легкового автомобиля




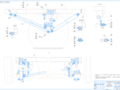
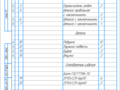
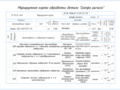
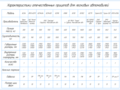
- Добавлен: 25.01.2023
- Размер: 1 MB
- Закачек: 0
Описание
Разработка торсионной подвески прицепа для легкового автомобиля
Состав проекта
![]() |
![]() ![]() ![]() ![]() |
![]() ![]() ![]() |
![]() |
![]() ![]() ![]() ![]() |
![]() ![]() ![]() ![]() |
![]() ![]() ![]() ![]() |
![]() ![]() ![]() |
![]() ![]() ![]() ![]() |
![]() ![]() ![]() ![]() |
![]() |
![]() ![]() ![]() ![]() |
![]() |
![]() ![]() ![]() ![]() |
![]() ![]() ![]() |
![]() |
![]() ![]() ![]() |
![]() ![]() ![]() ![]() |
![]() ![]() ![]() ![]() |
![]() ![]() ![]() ![]() |
![]() |
![]() ![]() ![]() ![]() |
Дополнительная информация
Подвеска торсионная.cdw

кроме размеров в скобках.
Гайки поз.15 и поз. 18 затянуть до указанного размера в скобках.
Неуказанные технические требования к затяжке резьбовых
соединений по ОСТ37.001.031-72
Аннотация.doc
В данном проекте разработана конструкция торсионной подвески прицепа для легковых автомобилей «Сармат-8232» по упругим характеристикам аналогичной пружинной подвески этого прицепа. Разработанная торсионная подвеска отличается меньшей металлоемкостью и трудоёмкостью по сравнению с существующей пружинной подвеской. Снижение себестоимости прицепа от внедрения торсионной подвески составляет 76313 рублей.
1 Отечественная прицепная техника для легковых автомобилей6
2 Характеристика прицепа для легковых автомобилей
3 Подвески применяемые на прицепах для легковых
4 Описание конструкции подвески прицепа для легковых
5 Предложения по изменению конструкции прицепа
Конструкторская часть23
1 Исходные данные для разработки торсионной подвески23
2 Проектировочный расчет подвески прицепа «Сармат-8232»26
3 Описание конструкции модернизированной торсионной
подвески прицепа «Сармат-8232»32
4 Расчет продольного рычага торсионной подвески на прочность35
Технологическая часть40
1 Характеристика детали цапфа рычага40
2 Описание технологического процесса изготовления детали
3 Сборка торсионной подвески прицепа «Сармат-8232»45
1 Техника безопасности при изготовлении деталей
торсионной подвески50
2 Техника безопасности при сборке торсионной подвески56
3 Пожарная безопасность58
4 Охрана окружающей среды61
Экономическая часть65
1 Расчет затрат на материалы65
2 Расчет затрат на электроэнергию68
3 Расчет затрат на заработную плату70
4 Расходы на содержание и эксплуатацию оборудования73
5 Расчет себестоимости изменяемой части проектируемой
и базовой подвески74
Список использованных источников76
Влияние автомобильного транспорта на жизнь современного общества огромно. Помимо выполнения своей прямой транспортной функции он в значительной мере определяет структуру промышленности занимая собой целую отрасль – автомобилестроение изменяет профессиональную ориентацию в обществе в определенной степени формирует психологию людей моды а иногда и нравы.
Особую актуальность ускоренное развитие автомобильного транспорта и автомобилестроения в России приобрело в настоящее время когда увеличивается поток иностранных автомобилей и автомобильной техники на российский рынок ужесточается конкуренция производителей и особенно остро стоит вопрос выживания отечественного машиностроения. Однако успехи достигнутые за предшествующие годы в фундаментальных и прикладных науках позволяют надеяться на скорый выход их кризиса и отечественного машиностроения на появление на дорогах России конкурентоспособных современных автомобилей и автомобильной техники.
Важнейшими направлениями повышения технического уровня автомобильной техники всегда были уменьшение расхода топлива и масел снижение трудоёмкости технического обслуживания расхода материалов на изготовление автомобиля понижение уровня шума и токсичности отработавших газов повышение надежности и безопасности конструкции.
Высокие скорости и полезные нагрузки на современном автомобильном транспорте применение сочлененных автотранспортных средств разнообразие дорожных и климатических условий эксплуатации предъявляют к автомобильной технике особые требования в аспекте безопасности движения надежности транспортных средств. Пытаясь удовлетворить этим требованиям производители автомобильной техники постоянно совершенствуют конструкцию производимых транспортных средств.
Настоящая работа также посвящена этой злободневной теме и в частности вопросу совершенствования подвески прицепа для легковых автомобилей «Сармат-8232». Существующая пружинная подвеска давно уже себя изжила о чем говорит все более и более распространяющаяся на прицепах для легковых автомобилей резиножгутовая подвеска являющаяся видоизменением торсионной подвески. Торсионная подвеска хорошо зарекомендовала себя на военных транспортных средствах и наиболее целесообразна для применения на прицепах для легковых автомобилей. Она может обеспечить не только повышение надежности узла но и значительное снижение металлоемкости прицепа а также снижение трудоемкости его изготовления.
1 Отечественная прицепная техника для легковых автомобилей
Современный этап развития страны характеризуется развитием частного предпринимательства отличительной чертой которого является создание и развитие крупных акционерных обществ средних предприятий частного бизнеса и мелких индивидуальных предприятий. Значительная роль в создании валового национального продукта принадлежит среднему и мелкому частному капиталу. Соответственно промышленность страны должна ориентироваться и на производство товаров удовлетворяющих потребности среднего и мелкого бизнеса. Одним из таких направлений является производство прицепов для легковых автомобилей которые широко используются особенно в мелком бизнесе и не только для пассажироперевозок но и для перевозки мелких партий грузов. Прицепы для легковых автомобилей широко используются также для перевозки малогабаритной техники: катеров лодок мотоциклов и других объектов. В целом применение прицепов для легковых автомобилей существенно повышает функциональные возможности легковых автомобилей.
Спрос на прицепы к легковым автомобилям растет с каждым годом. Предложение - тоже. Прицеп - выбор дачников и туристов оптовиков и ремонтных бригад. Учитывая потребности рынка прицепами занялись многие предприятия России и ближнего зарубежья. По грузоподъемности все производимые прицепы для легковых автомобилей различаются на категории:
– прицепы максимальная масса которых не более 075 т;
– прицепы максимальная масса которых свыше 075 т но не более 35 т.
Тяжелые — прицепы с разрешенной максимальной массой более 750 кг в обязательном порядке оснащаются тормозной системой.
По назначению прицепы к легковым автомобилям делятся на универсальные грузовые предназначенные для перевозки различных грузов и прицепы специального назначения.
К прицепам специального назначения относятся:
- самосвалы для перевозки сыпучих грузов;
- цистерны для перевозки жидкостей;
- прицепы для перевозки техники — лодок гидро- или мотоциклов снегоходов и т.п.;
- прицепы-автовозы для перевозки автомобилей;
- туристические прицепы для багажа и комфортного отдыха туристов;
- прицепы-дачи — с объемным кузовом предназначенные для отдыха и ночлега туристов на стоянках. Обычно оборудуются газовой плиткой емкостями для воды биотуалетом и т.п.;
- коммерческие прицепы — передвижные павильоны для торговли оснащенные необходимым оборудованием (холодильником витриной и т.п.);
- прицепы для перевозки животных (например скаковых лошадей).
Для езды с прицепом достаточно прав с категорией “В” (по действующему законодательству) если разрешенная максимальная масса буксируемого прицепа не превышает 750 кг. Либо если разрешенная максимальная масса прицепа не превышает массу снаряженного автомобиля относящегося к категории “В” а разрешенная максимальная масса такой комбинации транспортных средств не превышает 3 500 кг.
В случае же когда прицеп или состав “автомобиль и прицеп” в эти рамки не вписываются для управления автопоездом требуется категория “Е”.
Прицеп можно использовать практически с любым автомобилем если разрешенная максимальная масса прицепа не превышает массу снаряженного автомобиля относящегося к категории “В”. Что касается прицепного узла – фаркопа то технически его можно поставить на любой автомобиль.
В настоящее время производством прицепов к легковым автомобилям занято около 10 предприятий России которые выпускают прицепы различной грузоподъёмности от 200 до 1500 кг. Характеристика прицепов к легковым автомобилям приведена в таблице 1
К достоинствам прицепов грузоподъёмностью до 300 кг следует отнести их компактность небольшую собственную и полную массу низкую цену. Хранение таких прицепов даже в гараже для автомобиля не вызывает больших проблем. При необходимости можно без труда вручную перевернуть прицеп на бок или установить вертикально. Для буксировки прицепа пригодна даже «ОКА». Невысокая цена обеспечивает возможность приобретения прицепа в любой момент когда возникает необходимость.
Недостатки прицепов малой грузоподъёмности - прямое следствие их достоинств: малые грузоподъемность и объем слабоватые пружинные подвески хилые 10-дюймовые колеса и ступицы. Конструкции не приспособлены к перегрузкам плохим дорогам и высоким скоростям.
Модель 8236 производства «Уралтрансмаша" типична для своей группы. Дополнительные преимущества придает модели наличие штатного запасного колеса. Для хранения дышло можно отвернуть. Открывающиеся передний и задний борта позволяют возить относительно длинные грузы.
Прицепы грузоподъёмностью от 300 до 500 кг наиболее востребованы на рынке и потому они и представлены шире. Типичными конструктивными особенности этой группы прицепов являются вместительные цельнометаллические реже с фанерным полом кузова; обязательное наличие тента Вазовские колеса как правило вынесенные за борта грузовой платформы.
Таблица 1 -Характеристики отечественных прицепов для легковых автомобилей
Ступино Московская обл.
ЭМЗ "Авангард" Арзамас-16
Габаритные размеры мм
Внутрениие размеры платформы мм
Ступицы обычно также "жигулевские" с двумя коническими подшипниками. Запасное колесо в комплект прицепов этой группы не входит что создает определенные неудобства владельцам "волг" "нив" и "москвичей". Модели грузоподъёмностью около 500 кг обычно оснащаются тормозами. Хранение таких прицепов в гаражах для автомобилей представляет определенную трудность поэтому в последнее время в их конструкции появилось шарнирное дышло снижающее остроту проблемы.
В подвесках этих прицепов применяют три типа упругих элементов: пружинные и рессорные упругие элементы соседствуют с современной пришедшей от ведущих европейских производителей резиножгутовой схемой. Ее достоинства - полностью независимая подвеска колес компактность уменьшение неподрессоренных масс возможность отказаться от амортизаторов. При оснащении прицепа резиножгутовой подвеской кузов можно поставить ниже одновременно опустив центр тяжести что очень важно для управляемости автопоезда. Если качество материалов подвески высокое а конструкция просчитана верно резиножгутовая подвеска надежна и долговечна. Это доказано отечественными производителями применяющими импортные узлы. Правда прицепы с деталями именитых фирм дороговаты. Некоторые сетуют на жесткость резиножгутовых подвесок. На практике у груженого прицепа "прыгучесть" не больше чем у моделей с пружинами или рессорами. Особенно если на последних ради удешевления конструкции пожертвовали амортизаторами.
Сегодня почти каждый производитель предлагает несколько модификаций различающихся подвесками высотой тента и бортов другими элементами. Под общим индексом скрывается целое семейство крепких середняков грузоподъемностью 320-500 кг. Их оцинкованные кузова по сравнению с обычными крашеными меньше ржавеют зато стоят дороже. Покупатель может выбрать низкий или высокий тент; остановиться на базовом варианте с единственным откидным бортом - задним - или доплатить 100 рублей за открывающийся передний; предпочесть крашеную или оцинкованную раму. Прицеп с последней обойдется дороже на 3-5%. Помимо версий с резиножгутовой подвеской предлагают более знакомые нашим автомобилистам - с амортизаторами и рессорами от "москвича-2140".
У некоторых прицепов «Трейлер» пол кузова выполнен из водостойкой 12-миллиметровой фанеры. Обслуживание ступицы сведено к нулю: двухрядный передний подшипник от ВАЗ-2108 не требует ни смазки ни регулировки. Дышло складывается у модификаций с резиножгутовой подвеской. "Топ-версии" оборудуют немецкими инерционными тормозами "kнотт". Светотехника прицепное устройство опорная стойка - этой же фирмы. На рынке запчасти к таким прицепам встречаются хотя и не часто. Добротные крепкие и долговечные "Трейлеры" стоят недешево. Вряд ли их купят те кому прицеп нужен два-три раза в год.
Приличные грузоподъемность и вместительность невысокая цена делают «Тонары» лидерами в своей группе. К их недостаткам следует отнести громоздкое нескладывающееся дышло и маленькие 10-дюймовые колеса. Оригинальные фонари на рынках к счастью встречаются. "Тонар-8188" - самая дешевая возможность перевозить 450 кг. Однако следует помнить о маленьких ступицах которые требуют аккуратного обращения.
БОМЗ выделяется немаловажной деталью - проушинами под штатный "жигулевский" или "нивовский" домкрат. Однако расположение проушины следовало предусмотреть пониже так как при вывешивании колеса под домкрат приходится подкладывать доски или кирпич. Прицеп оснащен передним и задним открывающимся бортом и складывающимся дышлом. Фонари закрыты скобами защищающими светотехнику при неаккуратном маневрировании
Продуманная конструкция и невысокая цена - привлекательное сочетание в прицепе "Сармат-8232". Модель Орского завода тракторных прицепов - типичный представитель своей группы. Простой крашеный металлический кузов открываются задний и передний борта остальные довольно легко снимаются. С заменой светотехники проблем не будет - фонари от УАЗа давно не дефицит. Простой с умеренной грузоподъемностью зато цена приемлемая.
У детища электромеханического завода "Авангард" непопулярная ныне конструкция: неудобные колесные ниши вылезли в кузов уменьшив его полезный объем. Подвеска рессорная с гидравлическими амортизаторами. Дышло не складывается. Фонари троллейбусно-автобусные их легко найти на рынках и в магазинах. Не слишком емкий средней грузоподъемности несколько архаичный прицеп купить можно очень дешево.
КМЗ-8136 высоко сидит над дорогой. Помимо модели с пружинной подвеской "Курганмашзавод" выпускает вариант с рессорами. Ступица у обеих модификаций универсальная: подойдет колесо от "Жигулей" "Самар" и заднеприводных "Москвичей". В комплекте - металлические панели для наращивания бортов. Длинномеры курганцу тоже по плечу: передняя и задняя стенки откидываются да и дышло удлиняется. Кузов может выполнять самосвальные функции без "отстежки" от тягача. В гараже КМЗ приживется: в вертикальном положении со сложенным дышлом он занимает не более 1 м2. Курганец - лидер по универсальности. А просят за него относительно не дорого.
Появление на рынке множества моделей прицепов способных перевозить более полутонны обусловлено не дачно-садовыми а коммерческо-торговыми потребностями. К такому "хвосту" тягач нужен серьезный да и управление солидным автопоездом требует навыков. Почти все тяжеловесы оборудованы инерционными тормозами. Много моделей с двумя осями.
Двухосные прицепы семейства "Трейлер-8298" грузоподъемностью от 955 до 1010 кг по конструкции кузова подвески и разнообразию модификаций аналогичны "трейлерам" средней группы (8294). Внушительные размеры и грузоподъемность помогут профессионалам окупить дорогое приобретение.
Тонар-8310". Старший брат и конструктивный аналог модели 8188. Прицеп двухосный но колеса 10-дюймовые. Все борта откидываются. Некоторые пользователи поездившие с этим "Тонаром" жаловались на петли бортов: тяжелый груз их постепенно разгибает. Для большинства дачников 8310 великоват да и в хранении неудобен (дышло не складывается). А для серьезных перевозок скорее подойдут старшие братья на вазовских колесах - 83101 и 83102.
Тонар-86101" хоть и одноосный выглядит солидно. - вазовские вынесенные за габарит кузова колеса удобны для управляемости и погрузки-выгрузки. Открывается только один борт зато кузов меньше "дышит". Версия 86101 м - без тормозов. Подойдет и частникам если гараж для автомобиля достаточно просторный.
Общий вид прицепа «Сармат-8232» приведен на рисунке 1
Одноосный прицеп «Сармат-8232» оснащен кузовом и днищем из металла и тентом из ткани «ТЕЗА».
Прицеп рассчитан на буксировку всеми типами легковых автомобилей оборудованных тягово-сцепными устройствами шарового типа и штепсельной розеткой для подключения вилки электрооборудования прицепа. Тент с прицепа может быть легко демонтирован. Прицеп имеет передний и задний открывающиеся борта. На дышле смонтировано замковое устройство и страховочные тросы для соединения с буксирным устройством автомобиля.дополнительного оборудования (тента дуг противооткатных упоров) составляет 10 кг. Кроме того прицеп имеет вынесенные за борта колеса что позволяет его хранить в гараже перевернув набок и при этом не боясь поцарапать краску на кузове.
Дышло — А-образный горизонтальный рычаг закрепленный на передней стороне рамы прицепа. На дышле находятся узел сцепки страховочные тросы складная подставка (у некоторых прицепов).
Узел сцепки служит для соединения прицепа с тягово-сцепным устройством автомобиля (ТСУ). Для ТСУ шарового типа узел сцепки состоит из "чашки" надеваемой на сцепной шар и запорного механизма фиксируемого рычагом и удерживающего узел на шаре. Некоторые конструкции узла сцепки имеют индикатор износа и механизм регулировки зазора между "чашкой" и сцепным шаром.
Страховочные тросы (цепи) предотвращают полное разъединение прицепа и автомобиля в случае расцепления узла сцепки. Фиксируются в специальных страховочных петлях ТСУ. Эксплуатация прицепа без тросов (цепей) не допускается.
Рисунок 1 – Общий вид прицепа «Сармат-8232»
Складная подставка служит для удобства загрузки и разгрузки прицепа отсоединенного от автомобиля позволяя удерживать его в горизонтальном положении. Для облегчения стыковки прицепа с ТСУ подставка иногда оснащается небольшим колесом. На дышле может размещаться запасное колесо прицепа.
Подвеска- пружинная зависимая отличается от рессорной тем что в качестве упругих элементов используются цилиндрические пружины а балка крепится к кузову двумя продольными и одной поперечной тягами. Аналогична задней подвеске заднеприводных автомобилей ВАЗ.
Ступицы колес прицепа аналогичны ступицам легкового автомобиля (как правило "Жигулей"). На колеса прицепов монтируются как правило камерные шины для которых установлены нормы остаточной высоты рисунка протектора шин аналогичные нормам для шин автомобилей-тягачей (соответственно 16 мм для легковых автомобилей). Не допускается установка на одну ось прицепа диагональных шин вместе с радиальными а также шин с различным рисунком протектора.
Необходимое давление в шинах при разном уровне загрузки прицепа иногда указывается в руководстве по эксплуатации последнего.
Прицеп “Сармат- 8232” оснащается приборами световой сигнализации. К обязательным приборам относятся:
два задних указателя поворота оранжевого цвета;
два задних стоп-сигнала красного цвета;
два задних габаритных фонаря красного цвета;
фонарь освещения номерного знака белого цвета;
один или два задних противотуманных фонаря красного цвета;
два задних треугольных световозвращателя красного цвета (вершины треугольников должны быть направлены вверх);
два передних нетреугольных световозвращателя белого цвета;
два боковых нетреугольных световозвращателя оранжевого цвета.
Питание электроприборов осуществляется от автомобиля через розетку на ТСУ.
Для буксировки прицепа автомобиль-тягач должен быть оснащен специальным тягово-сцепным устройством (ТСУ) и штепсельной розеткой для питания электрооборудования прицепа. Существуют два основных типа ТСУ:
- петля-скоба с фиксатором. Состоит из скобы в которую вдевается кольцо закрепленное на узле сцепки прицепа и пальца фиксирующего кольцо в скобе. Широко распространена на грузовых автомобилях и автомобилях с повышенной проходимостью;
- беззазорное шаровое ТСУ. Состоит из сцепного шара диаметром 50 мм (стандарт в РФ ОСТ 37.001.096-77 международный стандарт ИСО-1103-76) и металлической конструкции с помощью которой ТСУ жестко крепится к задней части кузова автомобиля.
Различные модели ТСУ могут крепиться к кузову автомобиля через кронштейны бампера и(или) непосредственно к силовым элементам кузова и полу багажника. Среди отечественных автомобилей штатные точки крепления ТСУ имеет только семейство ВАЗ-2108—15. При установке устройства на прочие автомобили предполагается самостоятельная разметка и сверление крепежных отверстий. На большинстве автомобилей перед установкой ТСУ как правило приходится снимать задний бампер.
Существуют разборные конструкции ТСУ позволяющие снимать крюк со сцепным шаром.
Штепсельная розетка закрепляется на специальном кронштейне ТСУ. Она подключается к соответствующим проводам заднего жгута проводки автомобиля (в багажнике вблизи фонарей заднего хода). Цвета проводов жгута идущих к соответствующим фонарям указываются в схеме электрооборудования автомобиля. Если прицеп шире тягача и закрывает обзор через штатные зеркала заднего вида то на автомобиле с обеих сторон должны быть установлены зеркала заднего вида на удлиненных кронштейнах. Прицеп должен быть укомплектован двумя противооткатными упорами для установки под колеса при остановке на уклонах.
3 Подвески применяемые на прицепах для легковых автомобилей
Как уже отмечалось прицепы для легковых автомобилей предназначены для перевозки самых разнообразных грузов. Сохранность груза во время перевозки зависит от конструкции подвески сглаживающей динамические воздействия со стороны дороги на груз и гасящей колебания прицепа от такого динамического воздействия. Велико влияние подвески и на автомобиль тягач так как прицеп связан с автомобилем тягово-сцепным устройством.
Основная масса прицепов для легковых автомобилей оснащена подвесками аналогичными подвескам самих легковых автомобилей. Такой подход позволяет при эксплуатации использовать одинаковые запчасти для ремонта подвески автомобиля и прицепа а в некоторых случаях применять для ремонта подвески прицепа не выработавшие ресурса детали подвески автомобиля. Однако конкурентная борьба за потребителя заставляет производителей снижать цены на свои прицепы за счет упрощения конструкции отдельных узлов либо повышать надежность этих узлов. Именно поэтому в последнее время на многих прицепах появились подвески которые не применяются на автомобилях вообще и на легковых автомобилях в частности.
В настоящее время на одноосных прицепах для легковых автомобилей применяются следующие виды подвесок: рессорная зависимая пружинная зависимая рычажно-пружинная независимая торсионная независимая резиножгутовая независимая.
Рессорная зависимая подвеска по устройству и обслуживанию аналогична задней подвеске легковых автомобилей ГАЗ и автомобилей классической компоновки АЗЛК и ИЖ. Схема рессорной зависимой подвески приведена на рисунке 2. Подвеска состоит из балки и продольных полуэллиптических рессор. Как правило снабжается гидравлическими амортизаторами. Рессоры в подвеске выполняют как функцию упругого элемента так и функцию направляющего элемента. Такая подвеска отличается надежностью не требует частого обслуживания.
К недостаткам рессорной подвески следует отнести наличие межлистового трения вызывающего характерный пищащий звук при ходах рессоры преждевременный износ листов рессоры и нечувствительность рессоры к мелким неровностям дороги что для прицепов с 10 дюймовыми колесами особенно актуально.
–балка 2 – рессора 3 – амортизатор
Рисунок 2 – Схема рессорной зависимой подвески
Пружинная зависимая подвеска прицепов для легковых автомобилей по конструкции аналогична подвеске легковых автомобилей ВАЗ классической компоновки. Схема пружинной подвески прицепа показана на рисунке 3.
- балка 3 – амортизатор 4 – реактивные тяги 5 - пружина
Рисунок 3 – Схема пружинной зависимой подвески прицепа
Пружинная зависимая подвеска отличается от рессорной тем что в качестве упругого элемента в ней выступают пружины а в качестве направляющего элемента – две (три) продольные и одна поперечная реактивные тяги. Пружинная подвеска проста в изготовлении однако требует большего обслуживания чем рессорная из-за необходимости частой замены резиновых элементов в шарнирах (сайлент блоках) соединения тяг с кузовом и с балкой моста.
Рычажно-пружинная независимая подвеска схема которой показана на рисунке 4 имеет продольные или поперечные рычаги цилиндрические пружины и гидравлические амортизаторы.
– амортизатор 2 – пружина 3 - рычаг
Рисунок 4 –Схема рычажно-пружинной независимой подвески прицепа
Пружинные упругие элементы подвески имеют большие рабочие ходы чем рессоры и потому обеспечивают более высокую плавность хода. Целесообразность их применения на легковых автомобилях не вызывает сомнения однако необходимость их применения на прицепах пусть даже для легковых автомобилей можно объяснить только простотой изготовления и необходимостью унификации с подвеской автомобиля тягача.
Наиболее целесообразно на прицепах для легковых автомобилей применение торсионной подвески упругий элемент которой не более сложен в изготовлении чем пружина. Схема торсионной независимой подвески прицепа для легкового автомобиля приведена на рисунке 5.
- амортизатор 2 – продольный рычаг 3 – торсионы
Рисунок 5 – Схема торсионной подвески прицепа
Торсионная независимая подвеска имеет установленные поперек кузова упругие металлические элементы работающие на кручение (торсионы).
Один конец торсиона зафиксирован на кузове а к другому крепится маятниковый рычаг со ступицей соединенный с кузовом через амортизатор. Обеспечение необходимого рабочего хода подвески достигается подбором длины торсиона. Чем больше рабочий ход подвески тем длиннее должны быть торсионы. Однако условию сохранности груза транспортируемого на прицепе удовлетворят и небольшие хода подвески способные погасить значительные динамические удары от дороги на груз и не отразится серьезным образом на тягаче. Несомненными преимуществами торсионной подвески перед рассмотренными выше конструкциями являются:
- меньшая величина неподрессоренных масс что обеспечивает комфортную перевозку грузов;
- меньшее пространство между осью и рамой прицепа;
- незначительные затраты на техническое обслуживание или полное отсутствие таковых. Конструктивно такая подвеска похожа на переднюю подвеску автомобиля ЗАЗ-968.
В последнее время на прицепах для легковых автомобилей получили большое распространение видоизменение торсионной подвески – резиножгутовая подвеска. Схема резиножгутовой подвески приведена на рисунке 6.
– продольный рычаг 2 наружная труба 3 –резиновые жгуты
Рисунок 6 – Схема резиножгутовой подвески прицепа
Резиножгутовая подвеска применяется на прицепах имеющих полную массу от 700 до 2500 кг. В качестве торсиона в таких подвесках используется резинометаллическое устройство в котором резиновые упругие элементы работают на сжатие. Оно представляет собой две квадратные или другого профиля трубы между которыми параллельно осям труб расположены резиновые жгуты. При взаимном повороте этих труб жгуты сжимаются за счет чего и происходит упругое действие подвески.
К настоящему времени эта подвеска получила основное применение в европейских странах. Основные элементы этой подвески: наружная труба внутренняя труба три резиновых жгута и рычаг-балансир.
В резиножгутовой подвеске резиновые элементы выполняют две задачи: пружинят и направляют колеса. Поэтому эта подвеска не нуждается в подшипниках и является более дешевой в изготовлении и в техническом обслуживании (не требует смазки и ухода).
Однако такая подвеска имеет и некоторые недостатки в числе которых достаточно небольшой ход то есть резиножгутовая подвеска является короткоходовой что и обусловило её распространение в прицепах. К недостаткам этой подвески следует отнести и проблему изготовления профилированных труб которые могут быть изготовлены только в условиях крупных специализированных предприятий. Не случайно поэтому отечественные производители прицепов для легковых автомобилей в конструкциях прицепов используют резиножгутовые подвески произведенные предприятиями Западной Европы. К достоинствам резиножгутовых подвесок следует отнести:
- высокую удельную энергоемкость не требующую применения амортизаторов;
- высокую долговечность ограниченную только временем службы резиновых жгутов которые в течение очень продолжительного времени не теряют свои свойства;
- незначительные затраты на техническое обслуживание или полное отсутствие таковых.
4 Описание конструкции подвески прицепа для легковых
Прицеп для легковых автомобилей «Сармат-8232» как и многие его собратья оснащен подвеской конструкция которой заимствована от семейства вазовских легковых автомобилей классической компоновки. Конструктивно она аналогична задней подвеске этих автомобилей и относится к типу пружинных зависимых подвесок. Конструкция подвески показана на рисунке 7.
Упругим элементом подвески являются две цилиндрические пружины 12 навитые из прутка круглого сечения диаметром 11мм. Материал прутка пружин – высокоуглеродистая сталь 60С2А. Более половины длины каждого из крайних витков пружин поджаты к рабочим виткам формируя опорные витки. Опорными витками пружины опираются на опорные чашки приваренные к раме и к балке оси прицепа. В каждой опорной чашке выполнено кольцо высотой равной высоте опорного витка пружины и диаметром несколько меньшим её внутреннего диаметра. Это кольцо служит для центрирования каждой пружины в чашке и обеспечивает центральное восприятие каждой пружиной динамических воздействий от дороги.
Рисунок 7 – Подвеска прицепа «Сармат – 8232»
Динамический ход пружин подвески ограничивается резиновым буфером 13 служащим в качестве верхнего ограничителя хода. Резиновый буфер имеет специальную форму обеспечивающую ему прогрессивную упругую характеристику. По мере увеличения деформации буфера при ударах в него балки оси прицепа сила его упругое сопротивление возрастает не по линейному закону как у цилиндрических пружин а по закону геометрической прогрессии. Результатом совместной работы пружин и резиновых буферов специальной формы является нелинейная упругая характеристика подвески прицепа в целом обеспечивающая увеличение жесткости подвески в зоне её динамических ходов.
Направляющим элементом зависимой пружинной подвески обеспечивающим передачу усилий в двух взаимно перпендикулярных направлениях продольном и поперечном являются реактивные тяги. В подвеске прицепа «Сармат 8232» таких тяг четыре: три – продольные 5 6 и одна поперечная 7. Продольные тяги предназначены для передачи продольных тяговых и тормозных усилий создаваемых автомобилем буксировщиком от рамы на балку оси прицепа поперечная – для передачи боковых усилий.
По концам к каждой тяге приварены наконечники с механически обработанными отверстиями. Отверстия имеют коническую форму и соединяются с соответствующими пальцами на раме или на балке оси при помощи резиновых втулок. Такой шарнир принято называть сайлент-блоком назначение которого состоит в гашении динамических ударов передаваемых тягой на кузов прицепа. Резиновые втулки такого шарнира под воздействием окружающей среды с течением времени разрушаются и требуют замены. В этом и состоит один из существенных недостатков пружинной независимой подвески по сравнению с другими типами подвесок. Типичная конструкция сайлент-блока прицепа показана на рисунке 8.
Рисунок 8 – Конструкция сайлент-блока прицепа «Сармат-8232»
Характерной особенностью соединения продольных тяг с рамой и балкой оси прицепа является то что две из них 5 крепятся к балке оси сверху и одна 6 снизу. Расположение шарниров тяг подобрано таким образом чтобы при соединении их осей прямыми линиями образовалась трапеция. Такое крепление реактивных тяг необходимо для того чтобы при ходах балки оси вверх или вниз она поворачивалась вокруг своей оси на такой угол при котором пружины сохраняли бы положение обеспечивающее центральную передачу вертикальных усилий от дороги на раму прицепа. В этом и состоит направляющая функция реактивных тяг.
Пружины рассматриваемой подвески являясь упругими элементами сглаживающими динамическое воздействие неровностей дороги на кузов прицепа а в конечном итоге и на груз в тоже время являются источниками колебаний кузова под действием их сил упругости. Для гашения колебаний кузова вызванного силами упругости пружин как и в любой пружинной подвеске в рассматриваемой подвеске прицепа используются устройства гасящие колебания. Таковыми являются гидравлические амортизаторы 33. В подвеске прицепа «Сармат-8232» используются амортизаторы автомобилей ВАЗ. Это амортизаторы телескопического типа двустороннего действия. Гасящее колебания действие амортизаторов основано на использовании гидравлического сопротивления возникающего при перетекании жидкости из одного объёма в другой через отверстия перекрываемые клапанами. Амортизаторы также как и реактивные тяги крепятся к кузову и к балке оси прицепа с помощью сайлент-блоков которые требуют периодического осмотра и замены. Кроме этого периодического осмотра и замены требуют и сами амортизаторы. В результате износа или старения резиновые уплотнения амортизаторов изнашиваются что приводит к вытеканию амортизаторной жидкости. В этом случае амортизатор перестает работать как положено и колебания кузова прицепа увеличиваются что сказывается на сохранности перевозимого груза а также отражается на самом прицепе и автомобиле буксировщике. При выходе из строя амортизатора его следует заменить или отремонтировать.
5 Предложения по изменению конструкции подвески прицепа
Пружинная зависимая подвеска прицепов «Сармат-8232» отличается простотой и достаточно высокой надежностью. Однако наличие таких элементов как сайлент-блоки заставляет владельцев прицепов следить за их состоянием и периодически производить замену резиновых элементов этих узлов. Другим существенным недостатком пружинной подвески прицепа является относительно высокая погрузочная высота. Дальнейшее уменьшение высоты прицепа что необходимо для понижения его центра тяжести и обеспечения высокой устойчивости прицепа при движении по дороге с высокими скоростями практически невозможно. В существующей конструкции подвески пружины уже входят в раму и уменьшение высоты прицепа без изменения высоты пружины невозможно. Такую возможность вполне может обеспечить торсионная подвеска прицепа.
Торсионные подвески широко использовались и используются на транспортных средствах к плавности хода которых не предъявляется серьезных требований. Она используется на военной технике (танки артиллерийские орудия) и может полностью удовлетворить прицепную технику. В недалеком прошлом торсионные подвески применялись и на легковых автомобилях: Фольксваген «Жук» некоторые модели «Рено» «Пежо» и «Ситроен». Среди отечественных автомобилей торсионной подвеской оснащались передние колеса автомобиля ЗАЗ-968.
Основным достоинством торсионной подвески является их компактность. Для легковых переднеприводных автомобилей это свойство особенно ценно так как торсионы не мешают подводить крутящий момент к передним приводным колесам. Для прицепов легковых автомобилей это свойство так же ценно потому что позволяет понизить их центр тяжести и сделать прицепы более устойчивыми на дороге.
Торсионные подвески отличаются и более высокой надежностью. Как показывает опыт эксплуатации военной и гражданской техники торсионы ломаются реже традиционных пружин и рессор даже если транспортное средство работает с перегрузкой. Правда на подобные издевательства стержни реагируют потерей упругости в результате чего кузов начинает просто проседать а сама подвеска становится ощутимо жесткой. Для продления срока службы просевшего торсиона автомобили с торсионной подвеской оснащаются механизмом регулировки угла закручивания торсиона.
В торсионных подвесках применяются различные виды торсионов: сплошные круглого квадратного или шестигранного сечения а также наборные состоящие из нескольких элементов прямоугольного или круглого сечений. Наборные торсионы отличаются большей надежностью чем торсионы сплошного сечения и кроме того они обеспечивают более низкую жесткость чем сплошные. Жесткость наборного торсиона примерно на 20 % ниже жесткости сплошного. Дополнительным преимуществом наборных торсионов перед сплошными является их значительно меньшая длина.
В пользу применения торсионной подвески на прицепах для легковых автомобилей говорит и тот факт что в последнее время на прицепах получило широкое распространение видоизменение торсионной подвески – резиножгутовая подвеска. Эта подвеска рекламируется производителями вообще как вечная. Однако отечественные производители резиножгутовой подвески пока не готовы самостоятельно разработать и даже изготовить такую подвеску. Применяемые на прицепах для легковых автомобилей резиножгутовые подвески как правило импортного производства и потому прицепы оснащенные ими не по карману основной массе отечественных потребителей. Наиболее реальный путь для отечественных производителей стремящихся повысить надежность и качество своих прицепов – это торсионная подвеска с наборным торсионом.
Оснащение прицепа «Сармат-8232» торсионной подвеской позволит понизить погрузочную высоту прицепа понизить расположение центра тяжести прицепа и улучшить его устойчивость на дороге при движении с высокой скоростью снизить металлоемкость прицепа и сделать его более надежным.
пррицеп обший вид.cdw

снаряженного прицепа
Полная масса прицепа
Нагрузка на дышло прицепа в сцепке не более 40 кг;
Максимальная скорость движения тягача с прицепом
* Размеры для справок.
Затяжка резьбовых соединений по ОСТ 37.001.050-73.
Зазоры между бортами и основанием и между бортами не более
производить по сопрягаемой детали.
Технические требования
Подвески прицепов.cdw

Пружинная зависимая подвеска
Рычажно-пружинная независимая подвеска
Торсионная независимая подвеска
Резиножгутовая независимая подвеска
Подвески прицепов для легковых автомобилей
Подушка.cdw

2 Конструкторская часть 2.doc
1 Исходные данные для разработки торсионной подвески
Исходные данные для проектировочного расчета торсионной подвески могут быть получены из технической характеристики прицепа «Сармат-8232». К исходным данным для проектировочного расчета относятся:
- нагрузка на ось груженого прицепа - ;
- нагрузка на ось снаряженного прицепа - ;
- жесткость пружинной подвески прицепа - ;
- максимальный вертикальный ход колеса прицепа -
- вертикальный ход колеса при загрузке прицепа
максимальным грузом (деформация подвески от груза) - .
Из технической характеристики прицепа устанавливаем что нагрузка на ось груженого прицепа составляет = 460 кг =45126 Н нагрузка на шар тягово-сцепного устройства = 40 кг = 3924 Н.
Используя эти данные а также зная полный и снаряженный вес прицепа вес груза можно установить нагрузку на ось снаряженного прицепа.
= 460 кг = 45126 Н; =170 кг = 16677 Н; =330 кг = 32373 Н
Схема нагружения прицепа с размерами точек приложения сил приведена на рисунке 9.
Рисунок 9 – Схема нагружения груженого прицепа
Используя рисунок 9 составим уравнение для определения координаты центра тяжести груженого прицепа
Отсюда определяем координату центра тяжести груженого прицепа
В соответствии со схемой полученная координата центра тяжести груженого прицепа совпадает с координатой центра тяжести груза которая лежит на оси симметрии кузова прицепа. Это может означать только то что центр тяжести снаряженного прицепа также имеет координату
Используя полученную координату центра тяжести снаряженного прицепа и схему нагружения снаряженного прицепа приведенную на рисунке 10 определяем нагрузку на ось прицепа в снаряженном состоянии.
Рисунок 10 – Схема нагружения снаряженного прицепа
Из рисунка 10 следует
Из полученного выражения нагрузка на ось снаряженного прицепа составит
При расчете подвесок учитываются не нагрузки на ось в груженом или снаряженном состоянии а нагрузки от подрессоренных масс. Величина подрессоренных масс прицепа может быть определена после вычета из нагрузок на веса колес и балки оси прицепа.
Вес колеса прицепа составляет =14 кг = 13734
Вес балки оси прицепа = 10 кг = 981 Н
Общий вес неподрессоренных масс прицепа составит
= 2×13734 + 981 = 3728 Н
Подрессоренная нагрузка приходящаяся на пружину подвески груженого прицепа
Подрессоренная нагрузка приходящаяся на пружину подвески снаряженного прицепа
По величинам подрессоренных нагрузок и деформации подвески под действием груза определим жесткость пружинной подвески прицепа . Жесткость пружинной подвески не равна жесткости пружины так как пружина в подвеске установлена под углом к вертикальной оси.
Деформация подвески под действием груза может быть определена на основании данных чертежа общего вида прицепа и составляет 40 мм.
Жесткость пружинной подвески прицепа может быть определена из выражения
Максимальный вертикальный ход колеса прицепа при упоре балки оси в буфер легко определяется по сборочному чертежу подвески и составляет = 72 мм.
На основе определенных исходных данных можно производить проектировочный расчет торсионной подвески прицепа.
2 Проектировочный расчет торсионной подвески прицепа
Как уже отмечалось наборные торсионы собранные из нескольких стержней отличается от сплошных высокой надежностью меньшей жесткостью и длинной. Так как проектируемый торсион предназначен заменить собой пружинный упругий элемент подвески то все перечисленные преимущества наборного торсиона в данном случае как нельзя к стати.
В качестве отдельного элемента наборного торсиона примем пластинчатый элемент прямоугольного профиля. Для наборного торсиона основным видом нагружения которого является кручение наиболее целесообразно сечение квадратной формы состоящее из пластин одинаковой толщины. В этом случае число пластин составляющих торсион должно быть равно отношению сторон одной пластины
где и - толщина и ширина пластины соответственно.
Предполагаемая форма сечения проектируемого торсиона приведена на рисунке 11.
Рисунок 11 – Форма сечения проектируемого торсиона
Пластины наборного торсиона должны изготавливаться из высокоуглеродистой легированной стали 50ХГА или 60С2Х по ГОСТ14959-79. Для повышения усталостной прочности пластины торсиона закаливают обрабатывают дробью и торсион в собранном состоянии подвергают закручиванию в сторону противоположную рабочему ходу. От количества и качества выполнения предварительных мероприятий повышающих усталостную прочность торсиона зависит величина расчетных допускаемых напряжений . Примем в качестве материала для изготовления отдельных пластин торсиона сталь 60С2Х по ГОСТ14959-79 предварительно закаленную без дробеструйной обработки.
Толщина пластины наборного торсиона может быть определена по формуле 1 рекомендованной в литературном источнике [1]
где - модуль поперечной упругости материала пластины МПа; для стали 60С2Х по ГОСТ14959-79 =78×104 МПа;
- допускаемое напряжение для материала пластины МПа; для закаленной стали 60С2Х по ГОСТ 14959-79 без дробеструйной обработки = 800 МПа;
- число прямоугольных пластин в наборном торсионе шт.; примем = 4;
- коэффициент характеризующий рациональность использования материала при деформациях кручения некруглых стержней; зависит от величины отношения = при ===4 = 0567;
- длина рабочей части торсиона мм; примем = 250 мм;
Примем = 5 мм тогда = × = 4×5= 20 мм
То есть одна пластина наборного торсиона будет иметь размеры поперечного сечения 5 × 20 квадратное сечение наборного торсиона 20×20 а рабочая длина торсиона = 250 мм.
Допустимый угол закручивания одной пластины торсиона определится по формуле 2 [1]
= = 0641 рад = 294 º
Для определения проектных размеров элементов торсионной подвески необходимо определить угловую жесткость наборного торсиона. Угловая жесткость торсиона расчитывается по формуле 3
где - момент закручивающий торсион Нм;
- угол закручивания торсиона рад.; определяется по формуле 4
где - момент инерции сечения торсиона при кручении мм4; для наборного торсиона состоящего из пластин прямоугольной формы момент инерции определяется по формуле 5 приведенной в литературном источнике [2];
где - табличный коэффициент зависящий от отношения ; при = 5 =0291;
Подставив в формулу 3 вместо его выражение в виде формулы 4 получим формулу 6 по которой и определим угловую жесткость торсиона
Угловая жесткость торсиона составит
Жесткость торсионной подвески с продольными рычагами переменна в связи с тем что при работе подвески изменяется расстояние от оси качания продольного рычага до линии действия нагрузки. При чем наибольшая жесткость подвески отмечается в положении минимальных её деформаций и по мере увеличения угла закручивания торсиона жесткость уменьшается. Минимального значения жесткость торсионной подвески достигает когда продольный рычаг колеса располагается горизонтально. При переходе рычагом горизонтального положения жесткость подвески снова начинает возрастать. Это положение наглядно проиллюстрировано на рисунке 12.
Рисунок 12 – Иллюстрация изменения жесткости торсионной подвески с продольными рычагами.
В связи с изложенным наиболее целесообразным представляется подбор длины продольного рычага подвески таким чтобы обеспечивалось с одной стороны горизонтальное положение рычага при груженом прицепе и наклонное на снаряженном прицепе. При упоре подвески в буфер ограничения динамического хода рычаг также примет наклонное положение но с другой стороны от своего горизонтального положения. Это позволит снизить колебания жесткости подвески и считать её примерно постоянной.
Горизонтальное положение продольного рычага торсионной подвески на груженом прицепе и наклонное на снаряженном при деформации подвески под весом груза = 40 мм используем для определения необходимой длины продольного рычага .
Угол закручивания торсиона при достижении продольным рычагом горизонтального положения на груженом прицепе может быть определен по формуле 7
При длине рычага = 155 мм угол закручивания составит
Деформация пружинной подвески под действием веса груза прицепа составляет =40 мм. Проектируемая торсионная подвеска тоже должна обеспечивать эту величину деформации сохраняя преемственность с пружинной. Угол между горизонтальным рычагом подвески в загруженном прицепе и рычагом в снаряженном прицепе может быть определен по формуле
Тогда угол закручивания торсиона при положении рычага соответствующем снаряженному прицепу составит
Момент закручивающий торсион при рассматриваемом положении рычага
Нагрузка перпендикулярная оси рычага вызвавшая момент такой величины
Вертикальная нагрузка вызвавшая такую деформацию определится по формуле
Полученное значение =579Н отличается от рассчитанного ранее = 581Н (см подраздел 2.1) на 2 Н что незначительно.
Максимальный угол закручивания торсиона подвески соответствующий упору рычага в буфер ограничения динамических ходов можно рассчитать по формуле
Полученное значение угла = 3288 º превышает допустимый угол закручивания торсиона = 294º рассчитанный в подразделе 2.1 по допускаемым напряжениям = 800 МПа также незначительно.
Определим напряжения возникающие в торсионе при упоре рычага подвески в буфер ограничения динамических ходов по формуле 8 приведенной в литературном источнике [3].
где - момент вызывающий закручивание торсиона Нм; при упоре рычага подвески в буфер закручивающий момент будет равен
=153×3288 =503064 Нм
Тогда максимальные напряжения в элементах торсиона будут равны
Перегруз торсиона составит
Перегруз торсиона не превышает 5% что допустимо.
В результате проектировочного расчета торсионной подвески определены размеры рабочей части торсиона и длина продольного рычага подвески. Остальные размеры элементов подвески могут быть определены при её конструировании. По упругим характеристикам разрабатываемая торсионная подвеска аналогична пружинной подвеске прицепа «Сармат -8532»
3 Описание конструкции модернизированной торсионной подвески
прицепа «Сармат -8232»
Модернизированная подвеска прицепа «Сармат-8232» по упругим характеристика является полным аналогом пружинной подвески прицепа так как обеспечивает такие же ходы колес прицепа что и при их пружинной подвеске. Конструктивно торсионная подвеска существенно отличается от пружинной. При пружинной подвеске колес на двух цилиндрических пружинах колеса прицепа устанавливались на цапфах балки оси в торсионной подвеске каждое колесо установлено на цапфе своего продольного рычага. Иначе говоря пружинная подвеска представляет собой зависимую подвеску а торсионная – независимую.
При независимой подвеске колес каждое колесо связано с рамой прицепа посредством своего продольного рычага качающегося относительно своей оси и поэтому ход колеса от действия вертикальных реакций со стороны дороги никак не связан с такими же ходами другого колеса. Продольный рычаг воспринимает и передает на раму прицепа все нагрузки действующие на колесо со стороны дороги: и вертикальные и горизонтальные. Продольный разрез модернизированной торсионной подвески прицепа «Сармат -8232» показан на рисунке 13.
Продольный рычаг подвески 1 представляет собой Г-образную сварную конструкцию двух труб 483×6 и 76×3 в верхней части которой приварена цапфа оси продольного рычага в нижней – присоединительная пластина цапфы колеса прицепа. Цапфа колеса крепится к присоединительной пластине при помощи болтов М10 защищенных от действия сдвигающих усилий специальным замком (по аналогии с соединением цапфы колеса с балкой задней оси ВАЗ 2108). Труба 76×3 обеспечивает простое и прочное сварное соединение с основной трубой рычага 483×6 и кроме того служит для размещения на ней скобы упора буфера и кронштейна крепления нижней головки амортизатора.
Цапфа оси колеса приваренная к трубе 483×6 служит для шарнирного крепления продольного рычага торсионной подвески к раме прицепа и для установки в ней свободного конца торсиона. Шарнирный узел соединения продольного рычага с рамой прицепа конструктивно аналогичен шарнирным узлам крепления рычагов подвески на автомобилях ВАЗ.
На цилиндрическую поверхность цапфы рычага установлена тонкостенная втулка 5 из цветного металла длинной 46 мм. Между тонкостенной втулкой и обоймой кронштейна рамы гайкой 15 зажаты резиновые втулки 7. Сжатые резиновые втулки 7 обеспечивают хорошее центрирование элементов шарнирного соединения продольного рычага друг с другом и способствуют гашению динамических воздействий от дороги на раму прицепа передаваемых продольными рычагами торсионной подвески. Степень сжатия резиновых втулок в шарнире ограничивается длиной тонкостенной втулки 5.
Рисунок 13 – Продольный разрез торсионной подвески
Гайка 15 разрезная и её стопорение от самотворачивания осуществляется с помощью винта 11. Стягивая две половинки разрезанной резьбовой поверхности гайки 15 винт 11 нарушает шаг резьбы и тем самым предотвращает самоотвинчивание гайки 15.
В цапфе оси рычага выполнено квадратное отверстие со стороной квадрата 20 мм предназначенное для свободного конца наборного торсиона. Наборный торсион состоит из четырех пластин толщиной 5 мм и шириной 20 мм. Собранный из четырех пластин пакет закрепляется на кронштейнах рамы с помощью пластин 9 и болтов с гайками. Свободный конец пакета вводится в квадратное отверстие цапфы продольного рычага. Дополнительного соединительного элемента отдельных пластин торсиона в пакет не предусмотрено. При повороте продольного рычага в шарнире под действием вертикальных сил реакций дороги на колесо торсион закручивается относительно своего защемления и создаёт ту упругую силу которая и уравновешивает силы реакции дороги. Как показал расчет для уравновешивания сил реакций дороги приложенных к колесу прицепа достаточно чтобы пакет пластин торсиона имел рабочую длину 250 мм.
Торсион надежно закреплен на раме прицепа и в цапфе оси продольного рычага. В связи с этим не требуется искусственное ограничение хода отбоя подвески подобно тому как это организовано в подвеске с пружинным упругим элементом. При вывешивании колеса прицепа продольный рычаг займет свое исходное положение повернувшись в обратном направлении всего на 6 º что соответствует 15 мм вертикального хода колеса.
Существенных конструктивных отличий торсионной подвески при установке буфера ограничения динамического хода колеса и амортизаторов подвески по сравнению с пружинной подвеской нет. Следует добавить что торсионная подвеска прицепа позволила снизить погрузочную высоту прицепа на 60 мм. В случае возможности установки в подвески амортизаторов с меньшей габаритной высотой возможно снижение погрузочной высоты прицепа на более существенную величину.
4 Расчет продольного рычага торсионной подвески на прочность
Продольные рычаги торсионной подвески являются её направляющими элементами и потому должны выдерживать действие всех нагрузок передаваемых на них со стороны колес прицепа. Продольные рычаги проектируемой торсионной подвески испытывают сложное нагружение и одновременно могут подвергаться действию изгибающих моментов в вертикальной и горизонтальной плоскости а также действию крутящего момента. Схема нагружения продольного рычага торсионной подвески приведена на рисунке 14.
Рисунок 14 – Схема нагружения продольного рычага торсионной
Максимальное значение изгибающего момента в вертикальной плоскости будет равно максимальному моменту создаваемому при максимальном угле закручивания торсиона (упор рычага в буфер ограничения динамического хода подвески). Величина этого момента определена в предыдущем подразделе и составляет Нм.
Продольный рычаг выполнен из трубы 483×6 геометрические характеристики сечения которой могут быть рассчитаны по формулам 9 и 10.
Осевые моменты сопротивления сечения
Полярный момент сопротивления сечения
где - наружный диаметр трубы см; у трубы 483×6 =483 см;
- коэффициент равный отношению внутреннего диаметра трубы к наружному диаметру трубы ; для трубы 483×6 у которой внутренний диаметр =363 мм отношение = = 075;
Осевые моменты сопротивления сечения рычага из трубы 483×6
Полярный момент сопротивления сечения рычага из трубы 483×6
Максимальные нормальные напряжения в сечении продольного рычага из трубы 483×6 от изгибающего момента действующего в вертикальной плоскости определятся по формуле 11
Для расчета нормальных напряжений изгиба в сечении продольного рычага от изгибающего момента действующего в горизонтальной плоскости необходимо определить максимальную величину поперечной силы . Максимальной величины поперечная сила будет достигать при поперечном заносе полностью груженого прицепа. При этом значение силы может быть определено по формуле 12
где - нагрузка от груженого прицепа на колесо Н; в соответствии с исходными данными приведенными в подразделе 2.1 = 22563 Н;
- коэффициент сцепления шин с дорогой; для дорог с асфальтобетонным покрытием =06;
Максимальный момент действующий на продольный рычаг в горизонтальной плоскости может быть определен по формуле 13
где - длина продольного рычага м; в подразделе 2.2 установлена длина =155 мм = 0155 м;
Максимальные нормальные напряжения в сечении продольного рычага из трубы 483×6 от изгибающего момента действующего в горизонтальной плоскости определятся по формуле 14
Суммарные нормальные напряжения изгиба возникающие в сечении продольного рычага рассчитываются по формуле 15
Касательные напряжения от действия крутящего момента на продольный рычаг торсионной подвески определяться по формуле 16
где - крутящий момент возникающий в сечениях продольного рычага Нм; может быть определен по формуле 17
где - смещение продольной оси продольного рычага от оси симметрии колеса (см. рисунок 14) м; в соответствии с выполненным сборочным чертежом торсионной подвески = 0093 м;
Расчетные эквивалентные напряжения от всех видов нагружения продольного рычага могут быть определены по формуле 18
Полученные эквивалентные напряжения не превышают значение допустимого напряжения для стали 3пс из которой изготовлена труба 483×6 составляющее 160 МПа. Прочность продольного рычага торсионной подвески обеспечена.
Спецификация подвески.cdw

Штанга с наконечниками
ГайкаМ12-6Н ГОСТ5915-70
ОГТИ1906.01 11 09. 25 000СБ
Подвеска чертеж.cdw

Болты поз.19 и 20 затянуть до указанного размера в восьми
Неуказанные технические требования к затяжке резьбовых
соединений по ОСТ37.001.031-72
Маршрутная карта.cdw

Фрезерно-центровальная: фрезеровать
торцевые поверхности 2 и 7
выполнить центровочные
Токарная: точить поверхности 1 и 3 окончательно
поверхности 4 и 6 предварительно
Сверлильная: сверлить отверстие 10 на проход
Протяжная: протягивать квадратное отверстие
Спец. приспособление
Токарная: точить поверхности 4 и 6
Сталь 35Л ГОСТ977-75
ОГТИ 1906.01 11 09 25 111
Маршрутная карта обработки детали "Цапфа рычага"
Цапфа рычага 2.cdw

Сталь 35Л ГОСТ977-75
Отливка II класса точности по ГОСТ 2009-55.
Неуказанные литейные уклоны - 7
Литейные радиусы - 3мм
Предельные отклонения размеров
получаемых механообработкой:
валов - остальных -
3 Технологическая часть 2.doc
1 Характеристика детали «Цапфа рычага»
Деталь «Цапфа рычага» является составным элементом продольного рычага торсионной подвески прицепа для легковых автомобилей «Сармат-8232». Она предназначена для перехода от основной трубы продольного рычага к шарниру крепления продольного рычага на раме прицепа. Конструкция и основные рабочие поверхности детали приведены на рисунке 15.
Рисунок 15 – Конструкция и основные рабочие поверхности детали
Поверхность 1 – наружная цилиндрическая поверхность установочной шейки предназначена для центрирования детали в основной трубе продольного рычага. Диаметр поверхности 36 мм с допуском по 14 квалитету точности шероховатость не ниже Rа125 мкм Может быть обработана простым точением. Ось поверхности должна быть перпендикулярна оси поверхности 5 в пределах неуказанных допусков на отклонение взаимного расположения поверхностей.
Поверхность 2 - плоская поверхность торца установочной шейки. Не сопрягается с какими либо поверхностями в узле но может использоваться как установочная база при обработке поверхности 1. Обрабатывается подрезкой на токарном или фрезерно-центровальном станке с выполнением центровочного отверстия в установочной шейке. Шероховатость не ниже Rа125 мкм.
Поверхность 3 - поверхность конической фаски необходимой для наложения сварного шва при приварке к трубе продольного рычага. Особых требований к точности выполнения угла конуса к форме и чистоте поверхности нет. Может обрабатываться точением на токарном станке.
Поверхность 4 – наружная не подвергаемая механической обработке поверхность тора переходной части детали. Не сопрягается ни с одной поверхностью в узле. Образуется в заготовке при формообразовании заготовки детали.
Поверхность 5 – внутренняя не подвергаемая механической обработке коническая поверхность необходимая для сокращения длины механически обрабатываемой поверхностей 10. Образуется в заготовке при формообразовании заготовки детали.
Поверхность 6 – плоская поверхность торца шейки оси продольного рычага. В узле сопрягается с поверхностью упорной шайбы и совершает вращение относительно поверхности упорной шайбы. Поверхность должна быть строго перпендикулярна оси поверхности 7 иметь минимальное торцевое биение. Требования к чистоте поверхности высокие не ниже Rа32 мкм. Поверхность может обрабатываться либо тонким точением либо шлифованием.
Поверхность 7 – наружная цилиндрическая поверхность шейки оси продольного рычага. Сопрягается с внутренней поверхностью тонкостенной втулки и совершает вращательные движения относительно неё. Диаметр поверхности 36 мм с допуском по 9 квалитету точности. Достаточно жесткие требования к форме поверхности и чистоте. Шероховатость поверхности не ниже Rа32 мкм Может быть достигнута либо тонким точением либо шлифованием.
Поверхность 8 – наружная резьбовая поверхность для прорезной гайки М36. По точности должна соответствовать полю допуска 7g и по шероховатости не ниже Rа32 мкм. Может обрабатываться нарезанием на токарном станке не менее чем за два прохода.
Поверхность 9 – плоская торцевая поверхность шейки оси рычага. Не сопрягается ни с одной из поверхностей в узле и потому существенных требований к точности чистоте и расположению поверхности нет. Однако может использоваться как установочная база при обработке поверхностей 6.7 и 8. Может обрабатываться подрезкой на токарном или Фрезерно-центровальном станке с выполнением центровочной фаски в отверстии шейки оси.
Поверхности 10 – плоские поверхности отверстия квадратного сечения в шейке оси рычага. Предназначены для образования отверстия некруглой формы служащего для размещения свободного конца наборного торсиона. Точность расположения параллельных поверхностей соответствует 11 квалитету точности соответственно шероховатость поверхностей должна быть не ниже Rа63 мкм. Поверхности должны обрабатываться протяжкой на протяжном станке.
Рисунок 16 – Конструкция заготовки детали «Цапфа рычага»
2 Описание технологического процесса изготовления детали
Механическая обработка заготовки детали «Цапфа рычага» начинается с операций получения установочных баз заготовки. Установочными базами заготовки для обработки поверхностей 1 3 6 и 7 будут являться торцевые поверхности 2 и 3 а также центровые отверстия выполненные в заготовке. Для выполнения операций подготовки установочных баз используем фрезерно-центровальный станок МР-71М и специальное приспособление тисочного типа. В качестве режущего инструмента применяем фрезу торцовую диаметром 45 мм с вставными пластинами Т5К10. Операционный эскиз фрезерно-центровальной операции приведен на рисунке 17
Рисунок 17 – Операционный эскиз фрезерно-центровальной операции
Окончательную обработку рабочих поверхностей 1 и 3 а также предварительную поверхностей 4 и 6 выполняем на токарно-винторезном станке 16К20 при установке заготовки в центрах с поводком. В качестве инструмента используем резцы проходной и подрезной с твердосплавными пластинами Т5К10. Операционный эскиз токарной операции приведен на рисунке 18.
Рисунок 18 – Операционный эскиз токарной операции
Предварительно обработанные поверхности 4 и 6 послужат установочными базами для обработки поверхностей 10 отверстия квадратного сечения. Но для обработки этих поверхностей следует предварительно выполнить внутреннюю цилиндрическую поверхность отверстия диаметром 20 мм в цапфе оси рычага с одновременным выполнением центровых фасок в заходных частях этого отверстия. Фаски послужат установочными базами для окончательной обработки поверхностей 4 и 6. Операцию будем выполнять на радиально-сверлильном станке 2Н135 при закреплении заготовки в специальном приспособлении сверлом диаметром 20 мм и конической зенковкой с углом 90º для выполнения центрирующих фасок. Операционный эскиз сверлильной операции приведен на рисунке 19.
Рисунок 19 – Операционный эскиз сверлильной операции
Внутренняя цилиндрическая поверхность отверстия диаметром 20мм послужит заготовкой для обработки поверхностей квадратного отверстия с размером стороны 20 мм. Обработку квадратного отверстия выполняем на вертикальном протяжном полуавтомате для внутреннего протягивания 7Б64. Установочной базой для выполнения операции послужат предварительно обработанные поверхности 4 и 6. Операционный эскиз протяжной операции представлен на рисунке 20.
Рисунок 20 – Операционный эскиз протяжной операции
После выполнения плоских поверхностей отверстия квадратного сечения необходимо выполнить окончательную обработку поверхностей 45 и 6. Операцию по их обработке будем выполнять на токарно-винторезном станке 16К20 при установке заготовки в центрах с поводком. В качестве инструмента используем резцы проходной и отрезной с твердосплавными пластинами Т5К10. Операционный эскиз токарной операции окончательной обработки поверхностей 45 и 6 приведен на рисунке 21.
Рисунок 21 – Операционный эскиз токарной операции окончательной
обработки поверхностей 45 и 6.
Приведенный маршрут механической обработки основных рабочих поверхностей детали «Цапфа рычага» обеспечит необходимое качество детали. Маршрутная карта технологического процесса механической обработки детали приведена на рисунке 22.
3 Сборка торсионной подвески прицепа «Сармат-8232»
Рисунок 22 – Маршрутная карта механической обработки детали «Цапфа рычага»
Сборка прицепа как в прочем и подвески должна производится из заранее скомплектованных узлов подузлов и деталей которые должны быть поданы на сборочные посты в необходимом количестве. Общая сборка прицепа должна начинаться с установки элементов подвески на раму. Наиболее часто сборка подвески производится когда рама прицепа находится в перевернутом положении. Такое положение рамы позволяет обеспечить доступ ко всем точкам сборки. Однако условием выполнения сборки в таком положении является необходимость в соответствующих подъёмно-транспортных механизмах позволяющих производить кантование как самой рамы перед сборкой так и собранного шасси прицепа для продолжения общей сборки прицепа. Таким образом для сборки торсионной подвески прицепа необходимы сборочные посты оснащенные подъёмно-транспортными устройствами для кантования шасси прицепа и комплект узлов подузлов и деталей поданных на сборочный пост.
В комплект для сборки одной торсионной подвески входят:
рама прицепа – 1 штука
колесо прицепа – 2 штуки;
(цапфа колеса в сборе с подшипниками и ступицей) - 2 штуки;
продольный рычаг подвески левый – 1 штука;
продольный рычаг подвески правый – 1 штука
комплект пластин наборного торсиона – 2штуки
амортизатор – 2 штуки
буфер ограничения динамического хода – 2штуки
подушка оси рычага – 4 штуки
тонкостенная втулка – 2 штуки
упорные шайбы – 4 штуки
гайка разрезная – 2 штуки
планка прижимная – 4 штуки
Крепежные детали подвески подаются на сборку с запасом каждое наименование в отдельной таре.
Процесс сборки подвески начинается с установки продольных рычагов подвески на раму. Для этого необходимо произвести сборку шарнирного узла продольного рычага. Конструкция шарнирного узла показана на рисунке 23.
Предварительно на цилиндрическую поверхность цапфы рычага устанавливаются тонкостенная втулка 1 и упорная шайба 3 а в обойму кронштейна рамы подушки рычага 2. Подсобранная ось цапфы вводится в обойму кронштейна рамы с установленными подушками закрывается с противоположной стороны второй упорной шайбой и зажимается разрезной гайкой 4. Разрезная гайка 4 затягивается специальным ключом до упора после чего стопорится путем заворачивания в резьбовое отверстие гайки винта 5. Винт 5 должен стопориться методом постановки на краску.
Таким же образом производится сборка шарнирного узла правого продольного рычага с рамой.
Рисунок 23 – Конструкция шарнирного узла соединения продольного
рычага подвески с рамой прицепа
После сборки шарниров продольных рычагов с рамой производится установка и закрепление на раме наборных торсионов. Пакет пластин наборного торсиона вводится в квадратное отверстие цапфы продольного рычага на столько чтобы противоположный конец пакета оказался «заподлицо» с краем кронштейна крепления торсиона на раме. Ориентировать наборный торсион следует таким образом чтобы пластины располагались в пакете горизонтально. После установки торсионов необходимо произвести их крепление на раме с помощью болтов и гаек М8 и прижимных планок. Стопорение резьбовых соединений узла крепления торсиона осуществляется с помощью контргаек. Узел крепления торсиона на кронштейне рамы показан на рисунке 24.
Рисунок 24 – Узел крепления торсиона к раме прицепа
К закрепленным на раме и связанным с торсионами продольным рычагам подвески крепят подузел I представляющий сборку подшипникового узла колеса прицепа (цапфа колеса подшипники ступицы колеса и ступица колеса). Подузел I центрируется на присоединительной пластине продольного рычага путем установки буртика цапфы колеса в центрирующее отверстие присоединительной пластины и закрепляется на ней при помощи болтов и гаек М10. Стопорение резьбового соединения осуществляется с помощью граверной шайбы. На установленную с подузлом I ступицу колеса закрепляются колеса прицепа.
Установка амортизаторов и буфера ограничения динамического хода подвески в варианте с торсионной подвеской не имеют существенных отличий от их установки в пружинной подвеске прицепа.
1 Техника безопасности при изготовлении деталей торсионной
При изготовлении деталей торсионной подвески прицепа для легковых автомобилей используются такие технологические операции как: резка заготовок на абразивно-отрезном станке операции механической обработки деталей и сварочные операции.
На машиностроительных предприятиях используется большое количество различного производственного оборудования: машин механизмов и станков. Независимо от их назначения видов и типов обеспечение безопасности при работе возможно лишь при соответствии их конструкции требованиям охраны труда. Для создания безопасных условий труда проектом предусматривается правильное размещение оборудования в помещении оснащение цехов предприятия соответствующими транспортными средствами и подъемными механизмами применение коллективных и индивидуальных средств защиты рациональное устройство рабочих мест.
Необходимо чтобы средства защиты обеспечивали высокую степень эффективности удобство при эксплуатации и отвечали требованиям технической эстетики и эргономики. Все эти требования обобщены в ГОСТ 12.4.011-75 “Средства защиты работающих. Классификация”.
К средствам защиты которые можно считать основными на машиностроительных предприятиях отнесены следующие устройства: оградительные автоматического контроля и сигнализации предохранительные дистанционного управления тормозные и знаки безопасности.
Проектом должно предусматриваться проведение работ в указанных направлениях для устранения производственной опасности под которой понимается возможность воздействия на работающих опасных и вредных производственных факторов. Опасный производственный фактор может привести к травме работающего а вредный производственный фактор -- к профессиональному заболеванию.
Общие требования безопасности к производственному оборудованию установлены ГОСТ 12.2.003-74 где определены требования к основным элементам конструкции органам управления и средствам защиты входящим в конструкцию производственного оборудования любого вида и назначения.
Специфические особенности производственного оборудования учитываются по каждому его виду отдельными стандартами.
Основными из общих требований являются следующие: производственное оборудование должно быть безопасно при монтаже эксплуатации и ремонте как отдельно так и в составе комплексов и технологических схем а также при транспортировании и хранении. Оно должно быть пожаровзрывобезопасным. Все это рассчитывается на обеспечение безопасности в течение всего срока службы оборудования.
Все виды производственного оборудования должны охранять окружающую среду (воздух почву водоемы) от загрязнения выбросами вредных веществ выше установленных норм.
Непременным условием является обеспечение надежности а также исключение опасности при эксплуатации в пределах установленных технической документацией. Нарушение надежности может возникнуть в результате воздействия влажности солнечной радиации механических колебаний перепада давлений и температур агрессивных веществ ветровых нагрузок обледенения и т. п.
Металлообрабатывающее оборудование - основной вид производственного оборудования машиностроительных предприятий. В качестве основного способа обработки металлов используется резание.
Общие требования безопасности предъявляемые к металлообрабатывающему оборудованию определены ГОСТ 12.2.009-75 а дополнительные требования вызванные особенностями их конструкции и условий эксплуатации указываются в нормативно-технической документации на оборудование. К отдельным станкам стандартом обусловлены дополнительные требования безопасности.
Защитные устройства ограждающие зону обработки должны защищать работающего от отлетающей стружки и смазочно-охлаждающей жидкости (СОЖ). Конструкция защитных устройств не должна ограничивать технологических возможностей станка и вызывать неудобства при работе уборке наладке а при открывании - не загрязнять пол смазочно-охлаждающей жидкостью. Во всех случаях крепление защитных устройств должно быть надежным и не допускать самооткрывания.
Автоматы и полуавтоматы по металлообработке оборудуют автоматической блокировкой не допускающей включение рабочего цикла при открытом защитном кожухе если это может привести к травмированию. Поверхности защитных кожухов как и самих станков органов управления станочных принадлежностей и приспособлений не должны иметь острых краев и заусенцев которые могут травмировать работающего.
При резке листового металла на гильотинных ножницах возможно попадание рук рабочего между режущими кромками. Во избежание этого нижнюю кромку ножниц соединяют со столом и неподвижной предохранительной линейкой не допускающей попадания пальцев работающего под нож и прижимное устройство. Конструкция ножниц такова что исключена возможность самопроизвольного опускания верхнего ножа.
При резании заготовок на ленточных и круглых пилах необходимо устройство подающих приспособлений устраняющих возможность повреждения пальцев рабочего.
На станках сверлильного типа обрабатываемые изделия устанавливают и закрепляют в тиски кондукторы и другие приспособления надежно укрепленные на столе или плите станка. Механизм крепления патронов должен обеспечивать надежный зажим и точное центрирование инструмента.
Автоматическая линия по механической обработке изделий состоит из отдельных но взаимно связанных станков-автоматов.
При разработке монтаже и эксплуатации автоматических линий необходимо выполнение ряда требований. Управление автоматической линией осуществляется с центрального пульта обеспечивающего работу на наладочном и автоматическом режимах. При этом система автоматического управления должна исключать возможность самопереключения линии с наладочного режима на автоматический. При работе на наладочном режиме все станки и агрегаты автоматической линии должны иметь самостоятельные органы управления для их пуска и останова. Обязательно должны быть предусмотрены сигнальные устройства для оповещения о включении линии на наладочный или автоматический режим.
Необходимо также чтобы все станки и агрегаты автоматической линии (как на автоматическом так и на наладочном режимах) во избежание аварий работали в последовательности установленной технологическим процессом и имели исправную систему блокировки для соблюдения этой последовательности.
Движущиеся части станков агрегатов и других устройств автоматической линии а также инструмент и обрабатываемое изделие ограждают надежными кожухами исключающими возможность доступа рабочего к опасной зоне во время работы линии.
Органы управления станками которые обслуживаются сидя располагаются на высоте не ниже 500 мм и не выше 1400 мм от уровня пола (площадки) а при обслуживании стоя соответственно 500 и 1700 мм. Ножные педали органов управления должны иметь рифленую рабочую поверхность (размером не менее 220X80 мм с расположением верхнего конца над полом не выше 100 мм) перемещающуюся в пределах 45--70 мм. Усилие перемещения должно быть не менее 25 Н и не более 40 Н.
Усилия на рукоятках и рычагах (маховиках) органов управления при постоянном ручном управлении не должно превышать 40 Н для фрикционных муфт главного привода в начале и конце перемещения - 80 Н. Усилия на рукоятках и рычагах (маховичках) включаемых не более пяти раз в смену не должны превышать 160 Н включаемых не более 25 раз -- 80 Н. Требуемое усилие рывка на различного рода зажимных рычагах и рукоятках в моменты конца зажима или начала разжима не должно превышать 500 Н. Для перемещения задней бабки усилие в момент трогания не должно превышать 320 Н. При необходимости большего усилия надлежит предусматривать устройство облегчающее перемещение бабки.
В универсальных токарных и токарно-револьверных станках предназначенных для обработки заготовок диаметром до 500 мм время остановки шпинделя с патроном (без закрепленной заготовки) после выключения не должно превышать 5 с а в станках для обработки заготовок диаметром до 630 мм -- 10 с . Это время для сверлильных станков не должно превышать 3 с для расточных станков -- 6с для универсально-фрезерных -- 5с.
На станках или автоматических линиях для установки заготовок массой более 8 кг а также инструментов и приспособлений массой более 20 кг устанавливают подъемные устройства индивидуального типа. Подъемное устройство должно удерживать груз в любом положении даже в случае неожиданного прекращения подачи электроэнергии масла воздуха. Для установки заготовок массой более 250 кг надлежит использовать внутрицеховые подъемные средства.
Для токарных станков толщина материала защитного устройства увеличивается при обработке заготовки со скоростью резания более 5 мс не менее чем в два раза. Смотровые окна в защитных устройствах (экранах) должны изготавливаться из прозрачного специального материала в несколько слоев общей толщиной не менее 10 мм.
Прутковые токарные автоматы и прутковые револьверные станки надлежит по всей длине прутков снабжать ограждениями имеющими шумопоглощающие устройства.
В абразивно-отрезных станках необходимо предусматривать возможность присоединения к ним индивидуальных отсасывающих устройств для удаления продуктов резания из рабочей зоны.
Шлифовальные станки должны иметь повышенную надежность крепления защитного кожуха обеспечивающую удержание его на месте в случае разрыва круга.
Круглошлифовальные станки работающие со скоростью круга 60 мс и выше должны иметь зону обработки (обращенную к рабочему) полностью закрытую защитным устройством. Защитный кожух и его смотровое окно оборудуются в соответствии с требованиями к скоростному резанию.
Ленточные пилы для резания металла ограждают так чтобы открытой оставалась только рабочая часть пилы. Ограждение огибает шкивы по которым проходит лента при этом шкивы дополнительно ограждают с боковых сторон.
Неогражденный привод и движущиеся части станка могут захватить развевающуюся часть одежды и травмировать работающего. Особенно опасны движущиеся столы продольно-строгальных станков и ползуны поперечно-строгальных. Эти части ограждены предохранительным барьером положение которого изменяется при настройке станка.
Несчастные случаи возможны также при заточке резцов на заточных станках. Наибольшую опасность представляет разрыв круга. Причиной разрыва могут быть трещины или раковины в круге превышение предельно допустимой скорости вращения удар тяжелого предмета о круг чрезмерное давление на боковую сторону круга резцом. Для предохранения от разлетающихся кусков при возможном разрыве круга должен быть установлен кожух. Круг перед установкой должен быть испытан в течение десяти минут со скоростью на 50% превышающей нормальную. Круг устанавливают опытные рабочие. Заточку резцов ведут в предохранительных очках.
Все рабочие помимо правил техники безопасности должны также знать основные правила электробезопасности и меры предупреждения несчастных случаев связанных с использованием электрической энергии. Опасность электротравматизма усугубляется тем что электрический ток не может быть обнаружен непосредственно органами чувств человека. Прохождение через организм человека токов величиной 01 а и выше смертельно.
Важнейшим условием электробезопасности является категорическое запрещение рабочим цеха (кроме электриков) самостоятельно производить ремонт наладку вскрытие и осмотр электрического оборудования приборов и проводов. Рабочий обнаруживший неисправности в работе электрооборудования (например искрение и вспышки в электрических приборах нагревание токоведущих частей и аппаратуры обвисшие и оборванные провода и др.) должен немедленно предупредить окружающих и сообщить руководителям цеха. Цеховой персонал не должен иметь доступа к токоведущим частям и деталям находящимся под напряжением.
Для предупреждения поражения электрическим током все станки и механизмы работающие от электродвигателей имеют защитное заземление. При исправном заземлении через тело человека прикоснувшегося к токоведущим частям потечет ничтожный ток не представляющий опасности. Отсюда видно насколько велика роль защитного заземления в обеспечении электробезопасности обслуживающего персонала.
В сварочном производстве к основным видам травматизма относятся:
ожоги от воздействия лучей сварочной дуги;
слезотечение от действия лучей сварочной дуги;
поражение электрическим током.
Для предупреждения поражения сварщика электрическим током соединения сварочных кабелей нужно производить опрессовкой сваркой либо пайкой с последующей изоляцией мест соединений.
Подключение кабелей к сварочному оборудованию следует осуществлять при помощи спрессованных либо припаянных кабельных наконечников. Электросварочная установка (преобразователь сварочный трансформатор и тому подобное) должна быть присоединены к источнику питания через рубильник и предохранители либо автоматический выключатель а при напряжении холостого хода более 70 В должно применяться автоматическое отключение сварочного трансформатора. Металлические части электросварочного оборудования которые не находятся под напряжением а также свариваемые изделия и конструкции на все время сварки следует заземлять а у сварочного трансформатора кроме того заземляющий болт корпуса должен быть соединен с зажимом вторичной обмотки к которому подключается обратный провод. В качестве обратного провода либо его элементов могут быть использованы стальные шины и конструкции в том случае если их сечение обеспечивает безопасное по условиям нагрева протекание сварочного тока. Соединение между собой отдельных элементов которые применяются в качестве обратного провода должно быть надежным и выполняться на болтах зажимах либо сваркой.
При осуществлении прокладки либо перемещения сварочных проводов нужно принимать меры против повреждения их изоляции и соприкосновения с водой маслом стальными канатами и горячими трубопроводами. Расстояние от сварочных проводов до горячих трубопроводов и баллонов с кислородом должно быть не меньше 05 метра а с горючими газами - не меньше 1 метра.
Сварочная дуга излучает яркие видимые световые лучи и невидимые ультрафиолетовые и инфракрасные лучи. Влияние света дуги на незащищенные глаза в течение 10 —20 с в радиусе до 1 м от дуги вызывает сильные боли в глазах слезотечение и светобоязнь. Более длительное воздействие света дуги на незащищенные глаза может привести к серьезным заболеваниям. Свет дуги на открытых частях тела может вызвать в зависимости от длительности времени действия различную степень ожогов. Ультрафиолетовые лучи дуги вызывают ожог кожи.
Для защиты тела от влияния лучей дуги электросварщики и их подручные во время работы должны надевать на руки брезентовые рукавицы шею закрывать специальным шлемом или щитком которые изготовляют из материала не пропускающего ультрафиолетовые лучи малотеплопроводного и не воспламеняющегося от искр. Для изготовления щитков применяют листовую фибру или тонкую фанеру окрашенную в черный цвет огнестойкой краской. В лицевой части щитка и шлема в прямоугольный вырез вставляют специальный светофильтр — защитное стекло ЭС. Для общей защиты работающих рядом от излучения дуги рабочие места сварщиков при сварке открытой дугой в помещении следует отделить от смежных рабочих мест и проходов несгораемыми экранами (ширмами щитами) высотой не меньше 18 метра. При проведении сварки на открытом воздухе ограждения нужно ставить в случае одновременной работы нескольких сварщиков рядом друг с другом а также на участках интенсивного движения людей. Места производства сварочных работ вне постоянных сварочных постов определяются письменным разрешением руководителя либо специалиста который отвечает за пожарную безопасность.
Для защиты сварщика от вредных факторов сварочной дуги ему выдаются средства индивидуальной защиты. Специальная защитная одежда в соответствии с ГОСТ 12.4.011— 89 предусматривает для сварщиков костюмы куртки и брюки с защитными свойствами «Тр» обеспечивающие защиту от искр и расплавленного металла. Обувь для сварщиков — это кожаные ботинки с защитными свойствами «Тр» имеющие наружные металлические носки и предназначенные для защиты ног от теплового излучения контакта с нагретыми поверхностями от окалины искр и брызг расплавленного металла. Для защиты лица и глаз от действия излучения электрической дуги и брызг расплавленного металла сварщики должны пользоваться защитными щитками или масками.
Специальная одежда специальная обувь и другие средства индивидуальной защиты выдаются по установленным нормам занятым на работах связанных с вредными и опасными условиями труда или загрязнением а также производимых в особых температурных условиях. Средства индивидуальной защиты приобретаются работодателем за его счет.
2 Техника безопасности при сборке торсионной подвески.
Сборка торсионной подвески прицепа должна производиться на специально подготовленном для этих целей посту оснащенном необходимым инструментом приспособлениями организационной оснасткой и подъёмно-транспортными устройствами.
При выполнении сборочных работ исполнитель должен обращать особое внимание на содержание в порядке рабочего места и инструмента. Перед началом работы необходимо очистить рабочее место от посторонних деталей и инструментов проверить исправность инструмента и оборудования.
Рабочие инструменты (молотки зубила пробойники и др.) должны отвечать следующим требованиям:
рабочие концы – не иметь повреждений (выбоин сколов);
затылочная часть ударных инструментов – быть гладкой не иметь трещин заусенцев и сколов;
молотки и кувалды – быть надежно насажены а поверхность ручек – быть гладкой без заусенцев и трещин.
Гаечные ключи должны соответствовать размерам болтов и гаек и иметь параллельные неизношенные губки. Запрещается отвертывание гаек ключами больших размеров и подкладыванием металлических пластинок между гранями гайки и ключа а так же удлинение воротка ключа путем присоединения другого ключа или трубы. При вывертывании или ввертывании шлицевых винтов рекомендуется пользоваться отверткой с длиной рабочей части равной диаметру головки винта. При работе раздвижным ключом необходимо прижимать губки ключа вплотную к граням гайки и поворачивать его в сторону подвижной части ключа.
Съемники и приспособления для сборки также должны быть исправны. При сборке узлов и механизмов оснащенных пружинами используют приспособления обеспечивающие невозможность внезапного действия пружины.
Не допускается производить разметку тяжелых деталей на краю верстака или полки стеллажа. Совпадение отверстий при сборке деталей следует проверять только специальными оправками и ломиками.
С целью повышения производительности сборочных работ следует шире заменять ручной резьбозавертывающий инструмент механизированным с электрическим или пневматическим приводом.
Правила безопасности при эксплуатации ручных электрических машин в условиях производства устанавливаются ГОСТ12.2.013-75. К работе с ручными электрическими машинами допускаются лица прошедшие производственное обучение и имеющие квалификационную группу по технике безопасности.
При каждой выдаче ручной электрической машины должны проверяться комплектность и надежность крепления деталей работа выключателя работа на холостом ходу и у машин I класса – исправность цепи заземления. При работе с машинами I класса следует применять индивидуальные средства защиты (диэлектрические перчатки галоши коврики и так далее). При работе машинами II и III класса запрещается их заземление машины III класса нельзя подключать через трансформатор.
Электрическая ручная машина должна быть отключена от сети при смене рабочего инструмента установке насадок и регулировке при переносе машины с одного рабочего места на другое при перерыве в работе по окончании работы или смены. По окончании работы или смены машина должна быть очищена от пыли и грязи и сдана лицу отвечающему за её исправность. При работе с ручными электрическими запрещается:
оставлять без надзора машину присоединенную к питающей сети передавать лицам не имеющим права пользоваться ею;
натягивать и перекручивать кабели (шнуры) подвергать их нагрузкам ставить на них груз;
снимать средства виброзащиты и управления рабочим инструментом;
эксплуатировать машину при возникновении хотя бы одной из следующих неисправностей: повреждении штепсельного соединения кабеля или его защитной трубки; повреждении крышки щеткодержателя нечеткой работе выключателя; искрении щеток на коллекторе сопровождающимся появлением кругового огня на его поверхности; вытекании смазки из редуктора или вентиляционных отверстий; пояалении дыма и запаха характерного для горящей изоляции; появлении повышенного шума стука вибрации; поломке или появлении трещин в корпусной детали рукоятке защитном ограждении; повреждении рабочего инструмента.
Требования к эксплуатации ручных пневматических машин устанавливаются ГОСТ12.2.010-75. Шланг к ручной пневматической машине должен присоединяться при помощи при помощи ниппелей штуцеров и хомутов. Не допускается крепление шлангов проволокой. На воздухоподводящем трубопроводе или гибком шланге на расстоянии не более 3 метров от рабочего места должно быть расположено запорное устройство или устройство для дистанционного управления запорным краном.
При эксплуатации ручных пневматических машин не допускается:
менять рабочий инструмент при наличии в шланге сжатого воздуха;
снимать с машины средства виброзащиты и управления рабочим инструментом а также глушитель шума.
3 Пожарная безопасность
Пожары на производстве представляют большую опасность для работающих и причиняют значительный материальный ущерб. Поэтому вопросы пожарной безопасности в нашей стране рассматриваются как имеющие государственную важность.
С необходимостью обеспечения противопожарной защиты инженерно-технические работники машиностроительных предприятий постоянно сталкиваются при рассмотрении проектов строительства и реконструкции цехов и предприятий при эксплуатации существующих объектов; в процессе разработки новых конструкций машин механизмов технологических процессов при эксплуатации действующего оборудования и выполнении существующей технологии производства.
В производственных условиях самыми распространенными источниками воспламенения являются:
а) искры образующиеся при коротких замыканиях и нагревания участков электросетей и электрооборудования возникающие при их перегрузках или при появлении больших переходных сопротивлений.
Токи коротких замыканий могут достигать больших величин. Они способны образовать электрическую дугу что приводит к плавлению проводов воспламенению изоляции а также сгораемых предметов веществ и материалов находящихся поблизости. Короткие замыкания могут возникать при неправильном подборе и монтаже электросетей и электрооборудования износе старении и повреждении изоляции электропроводов и оборудования.
Перегрузки электрических сетей машин и аппаратов возникают при токовой нагрузке которая в течение длительного времени превышает величины допускаемые нормами. Перегрузки возникают также в результате нарушения нормативных требований при проектировании электроснабжения и несоблюдения правил эксплуатации;
б) тепло выделяющееся при трении во время скольжения подшипников дисков ременных передач а также при выходе газов под высоким давлением и с большой скоростью через малые отверстия;
в) искры образующиеся при ударах металлических деталей друг о друга или об абразивный инструмент как например удары лопастей вентилятора о кожух образование искр при обработке металлов абразивным инструментом и т. п.;
г) тепло выделяющееся при химическом взаимодействии некоторых веществ и материалов например щелочных металлов с водой окислителей с горючими веществами а также при самовозгорании веществ например промасляной обтирочной ветоши или спецодежды;
д) искровые разряды статического электричества;
е) пламя лучистая теплота а также искры образующиеся например при плавке металла и заливке литейных форм при работе термических печей закалочных ванн;
ж) искры образующиеся при электро- и газосварочных работах.
Возникновение пожара возможно предотвратить путем осуществления соответствующих инженерно-технических мероприятий при проектировании и эксплуатации технологического оборудования энергетических и санитарно-технических установок а также соблюдением установленных правил и требований пожарной безопасности.
Важнейшими пожарно-профилактическими мероприятиями являются:
правильный выбор электрооборудования и способов его монтажа с учетом пожароопасности окружающей среды систематический контроль исправности защитных аппаратов и устройств на электрооборудовании постоянный надзор за эксплуатацией электроустановок и электросетей предупреждение перегрева подшипников трущихся деталей и механизмов путем своевременной и качественной смазки контроля за температурой и т. д.;
оборудование эффективной вентиляции исключающей возможность образования в помещении взрывоопасной смеси и обеспечение нормальной работы вентиляции в окрасочных и сушильных камерах и других аппаратах;
создание условий обеспечивающих пожарную безопасность при работе с нагретыми до высокой температуры изделиями и расплавленным металлом при сварочных и других огневых работах;
изолирование огнедействующих производственных установок и отопительных приборов от сгораемых конструкций и материалов а также соблюдение режима их эксплуатации;
обеспечение надежной герметизации производственного оборудования и трубопроводов с огнеопасными продуктами и немедленное устранение неисправностей при выявлении утечек продуктов в окружающую среду;
запрещение хранения транспортирования и содержания на рабочих местах огнеопасных жидкостей и растворов в открытых емкостях (в ведрах открытых баках и т. п.);
изоляция самовозгорающихся веществ от других веществ и материалов выполнение правил безопасного их хранения и систематическое контролирование состояния этих веществ;
предупреждение появления искровых разрядов статического электричества при обработке материалов или использовании жидкостей склонных к электризации;
своевременное удаление промасленных обтирочных материалов и огнеопасных производственных отходов в специальные отведенные для этого места;
проведение разъяснительной работы среди рабочих и служащих по соблюдению правил пожарной безопасности.
При разработке и осуществлении мероприятий по устранению причин возникновения пожаров особое внимание следует уделять пожароопасным производственным цехам и участкам (лакокрасочных покрытий деревообработки и др.). В этих цехах и на участках необходимо широко применять приборы и аппараты автоматического регулирования параметров которые влияют на снижение пожарной опасности технологического процесса производства.
Цеха и участки предприятия занятые изготовлением узлов и деталей торсионной подвески по пожароопасности относятся к категориям Г и Д . Производства категории Г характеризуются наличием веществ и материалов в горячем раскаленном или расплавленном состоянии процесс обработки которых сопровождается выделением лучистого тепла искр и пламени; твердых жидких и газообразных веществ которые сжигаются или утилизируются в качестве топлива. Из цехов и участков предприятия на котором будет изготавливаться торсионная подвеска к помещениям категории Г следует отнести сварочные участки.
Производства категории Д характеризуются наличием несгораемых веществ и материалов в холодном состоянии. Цеха и участки по механической обработке деталей торсионной подвески относятся к категории Д.
Основными профилактическими мероприятиями по предупреждению пожаров в помещениях категории Г и Д будут являться мероприятия по контролю за техническим состоянием электрооборудования и по изоляции горючих и самовозгорающихся материалов от источников воспламенения.
Однако профилактические мероприятия по предотвращению пожаров на производстве не должны затмевать собой мероприятия по снижению ущерба от возникновения пожаров. Эта система мероприятий носит название противопожарной защиты. Система защиты от пожаров обеспечивается максимально возможным использованием в производственном помещении негорючих и трудносгораемых строительных материалов возможностью эвакуации людей из зоны загорания постоянным обеспечением возможности подъезда пожарной техники к местам возгорания применением средств пожаротушения. Для обеспечения пожарной защиты в производственных помещениях цехов по изготовлению торсионной подвески необходимо не загромождать проезды для пожарной техники и эвакуационные выходы из помещений технологической тарой иметь несколько эвакуационных выходов и в соответствии с ГОСТ12.4.009-75 «ССБТ Пожарная техника для защиты объектов» укомплектовать участки первичными средствами пожаротушения.
4 Охрана окружающей среды
Предприятия машиностроения и металлообработки наряду с другими промышленными предприятиями вносят свой "вклад" в загрязнение окружающей среды. Вредные вещества отходы производства попадают не только в атмосферу но и в водную среду почву оказывают влияние на растительный и животный мир. Охрана окружающей среды должна иметь для отрасли важное значение.
Используя продукцию металлургии и химической промышленности машиностроение и металлообработка участвуют в формировании общей ауры загрязнения промышленных районов. Производственный цикл построен таким образом что чаще всего отходы не перерабатываются вторично а просто выбрасываются. А с учетом объемов производства предприятий машиностроения и металлообработки можно себе представить огромные масштабы воздействия на окружающую среду.
Отрасли следует позаботиться о переработке и утилизации отходов очистке воздуха воды сточных вод. Необходимость совершенствовать этапы рабочего цикла делать их более безопасными экономичными (что уменьшает количество отходов). Энергосбережение ресурсосберегающие технологии использование энергии от альтернативных источников могут улучшить экологическую ситуацию и состояние природы.
Однако не все готовы вкладывать в это средства. К решительным действиям могут подтолкнуть законодательные меры обязывающие не только совершенствовать рабочий процесс но и регулярно проводить природно-восстановительные мероприятия.
Само производство торсионной подвески для легкового прицепа будет более экологически чистым чем производство пружинной подвески уже потому что на её изготовление потребуется меньше количество цветного и черного металла меньшее количество сварочных материалов. Однако изготовление даже такого ресурсосберегающего узла не возможно без образования отходов производства.
Основными отходами при производстве торсионной подвески прицепа для легкового автомобиля являются отходы черных и цветных металлов отходы резинотехнических изделий отходы смазочно-охлаждающих жидкостей.
Утилизация отходов металлов в настоящее время по экономическим причинам становится обычным явлением и как правило на большинстве предприятий машиностроительного комплекса решается успешно. Отходы металлов подвергают сортировке брикетированию и отправляют на предприятия занимающиеся скупкой металлолома.
В меньшей степени успешно решается проблема утилизации резинотехнических изделий в связи с наличием в них различного рода армирующих элементов. Такими армирующими элементами обычно являются кордовые ткани или металлический армирующий каркас. В конструкции торсионной подвески прицепа применяются не армированные резинотехнические изделия что позволяет использовать отходы резины без дополнительной обработки как вторичное сырьё даже на самом предприятии изготовителе.
Важное место в рассматриваемой проблеме занимают жидкие отходы машиностроительных предприятий – смазочно-охлаждающие жидкости. Ежегодно предприятиями машиностроения и металлообработки сбрасывается около 600 млн. м3 отработанных СОЖ.
Практически все технологии обезвреживания СОЖ (отстаивание флотация центрифугирование выпаривание) недостаточно эффективны. Это связано со стойкостью эмульсии большим количеством химических соединений различного класса механическими загрязнениями.
Одним из наиболее перспективных направлений в решении указанной проблемы является создание комплекса установок по очистке и регенерации СОЖ восстановлению отработанных масел и переработке металлосодержащих нефтешламов. Кроме механических и физико-химических методов очистки нефтешламов все большее значение приобретают биологические способы их утилизации.
Наиболее часто используемым комплексным методом утилизации СОЖ с предварительной очисткой от механических примесей является реагентный метод разложения отработанных эмульсий. В настоящее время разработан и успешно опробован сорбционный метод утилизации СОЖ. Его основным достоинством является простота реализации технологического процесса доступное оборудование и материалы.
Для комплексной утилизации СОЖ по этому методу используются гидрофобизированные порошки (ГФП) на основе природных сорбентов Ульяновской области (диатомита опоки). Установлена возможность и эффективность их применения как для разрушения отработанной эмульсии так и для очистки водной и масляной фаз. Предлагаемый сорбционный метод разрушения эмульсий обладает рядом преимуществ по сравнению с реагентным методом:
- снижение себестоимости разложения 1 м3 отработанной СОЖ на 80-90%;
- большая эффективность разделения эмульсии на водную и масляную фазу;
- остаточное содержание основного загрязняющего вещества в водной фазе нефтепродуктов не превышает 1 2 мгл вместо 10 50 мгл для реагентного метода;
- более эффективное удаление анионов катионов (до норм предельно допустимого сброса установленных для предприятия);
- применение природного сырья при изготовлении гидрофобизированных порошков сокращает затраты и предотвращает загрязнение окружающей среды при осуществлении технологического процесса разложения СОЖ;
- получаемые продукты разложения СОЖ вода и масло соответствуют требованиям предъявляемым для дальнейшего использования их в техпроцессах;
- значительное снижение отходов с переработки 1 м3 отработанной СОЖ кроме того сами загрязненные порошки могут подвергаться термической регенерации либо использоваться в дорожном строительстве в качестве заменителя гудрона.
Для реализации комплексной утилизации отработанных СОЖ с применением ГФП применяется технологическая схема состоящая из модулей:
Модуль приготовления ГФП;
Модуль отработанной СОЖ;
Модуль очистки водной фазы;
Модуль утилизации осадков;
Модуль очистки масляной фазы;
Модуль регенерации ГФП.
Модуль приготовления ГФП предназначен для приёма природного порошкового сорбента и его гидрофобизации. В модуле накопления отработанной СОЖ происходит предварительная очистка эмульсии от механических примесей и удаление свободного масла
В реактор осуществляется подача отработанной СОЖ и ГФП с установленным расходом. Предварительно установленный расход ГФП составляет около 10 кгм3. В реакторе образуется водная фаза и осадок ГФП содержащий масляную фазу.
Водная фаза направляется в модуль очистки воды. Здесь может быть использован негидрофобизированный природный сорбент для глубокой очистки воды от загрязняющих компонентов до требуемой степени в зависимости от варианта дальнейшего использования.
Осадок содержащий ГФП попадает в модуль утилизации осадков где происходит разделение ГФП и масляной фазы. Порошок направляется в модуль регенерации ГФП а отделённое масло в модуль очистки масляной фазы.
В модуле очистки масляной фазы происходит удаление примесей из масла и его обезвоживание обработка масла осуществляется сорбентом.
В модуле регенерации отработанный ГФП накапливается и очищается от остаточного загрязнения повторно гидрофобизируется для восстановления исходных свойств. После этого ГФП направляется на подачу в реактор.
Комплексная утилизация отработанных СОЖ реализуется в данной технологической схеме в полной мере с полным или частичным возвратом в производство продуктов её разложения.
Удельная стоимость переработки 1м3 СОЖ значительно уменьшается до 100-200 руб.м3 за счёт возврата в производство сырьевых ресурсов - воды и масла. Себестоимость переработки 1 м3 отработанной СОЖ реагентным методам достигает 800-1000 руб.м3.
Вода составляет порядка 90-95 % от общего объёма поступающей на утилизацию эмульсии. При осуществлении дополнительной очистки до требуемых норм вода может быть использована в других технологических процессах.
При разложении СОЖ масло образуется в объёме 3-5% от исходного объёма. При дополнительной очистке его можно применять следующим образом:
в качестве технологических смазочных материалов в литейном производстве; в виде топлива для котельных и ТЭЦ; как закалочные среды; добавка к битумам; сырьё для обмасливания металлургических порошков в сталелитейном производстве; в качестве сырья для производства керамзита; как смазочные материалы для форм при производстве железобетона.
Шламы и осадки после просушки и прокаливания можно добавлять к строительным материалам при большом содержании металлических частиц проводить магнитную сепарацию и извлечённые ферромагнитные частицы прессовать в брикеты для дальнейшей переплавки.
Таким образом реализация сорбционного метода разрушения эмульсии с использованием ГФП доочистки водной и масляной фаз после разложения СОЖ с применением изученных материалов позволит перейти на более эффективный технологический процесс утилизации что существенно снизит нагрузку предприятия на окружающую среду.
Множество проблем охраны окружающей среды от загрязнений машиностроительных производств могут быть решены только комплексным подходом в том числе законодательными актами и их исполнением.
5 Экономическая част1.doc
Разработанная в проекте торсионная подвеска прицепов для легковых автомобилей «Сармат-8232» отличается от применяющейся в настоящее время пружинной подвески меньшей металлоемкостью и трудоёмкостью изготовления. Общий вес деталей разработанной подвески составляет 12 кг тогда как вес деталей пружинной подвески 15 кг. Однако следует заметить что проектируемая подвеска не предполагает наличия в конструкции прицепа такого металлоёмкого узла как балка оси прицепа. С учетом этого обстоятельства общее снижение металлоёмкости прицепа может достигнуть более 10 кг. Для расчета предполагаемого экономического эффекта от внедрения торсионной подвески прицепа «Сармат-8232» произведем расчет затрат на материалы и на изготовление изменяющихся частей конструкции подвески прицепа.
Любая подвеска транспортных средств состоит из трех основных элементов: упругого элемента направляющего устройства и устройства гасящего колебания. Из перечисленных трех элементов подвесок при внедрении торсионной подвески прицепа изменения коснутся только упругого элемента и направляющего устройства. Исключаемую из конструкции балку оси прицепа при внедрении торсионной подвески отнесем к направляющему устройству.
1 Расчет капитальных затрат на производство торсионной подвески
В состав капитальных затрат на производство торсионной подвески включаются затраты на приобретение (изготовление) доставку монтаж нового оборудования. Новым оборудованием необходимым для организации производства торсионной подвески является вертикально-протяжной полуавтоматический станок 7Б64. Сумма капитальных вложений определяется по формуле 19
где - стоимость нового оборудования руб.; стоимость станка 6Б64 составляет = 90000 руб.
- затраты на монтаж нового оборудования руб.; затраты на монтаж нового оборудования составляют 5 ÷ 15% стоимости оборудования примем затраты на монтаж равными 7% от стоимости оборудования;
= 90000× = 6300 руб.
- затраты на транспортировку оборудования руб.; принимаются равными 5% от стоимости нового оборудования;
Капитальные затраты на производство торсионной подвески составят
2 Расчет затрат на материалы
Эта статья расходов учитывает стоимость материалов которые вещественно входят в состав конструкции подвесок а также вспомогательных материалов используемых при изготовлении подвесок. Затраты на основные материалы определяются по формуле 20
где – масса наименования материала используемого для изготовления
элемента подвески кг;
- коэффициент использования материала данного наименования;
– стоимость материала данного наименования рубкг.
Расчет затрат на основные материалы а также значения и для материалов используемых при изготовлении элементов подвесок сведем в таблицу 2.
Таблица 2 –Расчет затрат на материалы для элементов подвесок
Упругие элементы подвесок
Проектируемый вариант
Наименование и количество элементов
два наборных торсиона из 4-х пластин;
две цилиндрические пружины сжатия
Коэффициент использования материала
Стоимость материала руб.кг
Затраты на материал руб.
Направляющие элементы подвесок
Наименование и количество
два продольных рычага
четыре реактивные тяги
направляющего устройства
Коэффициент использования материала
Шарниры направляющих элементов подвесок
два резинометаллический
восемь резинометаллический
Материал элемента шарнира
Стоимость материала рубкг
К вспомогательным материалам используемым в процессе изготовления подвесок относится сварочная проволока для сварки узлов подвесок. Затраты на сварочную проволоку определяются по формуле 21
где - масса сварочной проволоки затраченной на сварку узлов подвесок кг; принимается равной массе наплавленного металла;
- стоимость сварочной проволоки руб.кг; для проволоки диаметром 12 мм – 713 руб.кг; для проволоки диаметром 16 мм – 645 руб.кг
Потребное количество сварочной проволоки определяется по формуле 22
где - длина сварного шва в узле см;
- катет сварного шва см;
Расчет затрат на сварочную проволоку при изготовлении узлов проектируемого и базового вариантов подвесок приведен в таблице 3
Таблица 3 – Расчет затрат на сварочную проволоку
Проектируемый вариант
Длина сварных швов с катетом: L см
Масса проволоки диаметром: тпр кг
Стоимость проволоки диаметром: руб.кг
Затраты на сварочную
Общие затраты по статье материалы составят:
по проектируемому варианту - = =7347 +85 = 7432 руб.
по базовому варианту - = =116412 +42 = 11682 руб.
2 Расчет затрат на электроэнергию
Эта статья расходов учитывает затраты на топливо и все виды энергии используемой на изготовление подвесок. Основным видом энергии используемой при изготовлении подвесок является электроэнергия которая потребляется оборудованием при выполнении технологических операций изготовления деталей подвесок. Этот вид энергии потребляет металлорежущее оборудование а также сварочные аппараты используемые при сварке узлов подвесок.
Затраты на электроэнергию потребляемую станками определяются по формуле 23
где - мощность электродвигателей единицы оборудования кВт;
- суммарное основное время операций при выполнении которых была задействована данная единица оборудования мин;
- коэффициент загрузки электродвигателей оборудования по мощности; =05094; для всех единиц оборудования принимаем = 07;
- коэффициент учитывающий потери электроэнергии в сети = 095;
- коэффициент полезного действия привода станка = 09
- стоимость электроэнергии руб. кВт×ч; = 16 руб.кВт×ч
Расчет затрат на электроэнергию потребляемую металлорежущим и прессовым оборудованием при изготовлении подвесок по проектируемому и базовому вариантам приведем в таблицах 4 и 5
Таблица 4 – Расчет затрат на электроэнергию потребляемую станками по проектируемому варианту
Механическая обработка деталей
Фрезерно-центровальный
Вертикально-сверлильный
Вертикально-протяжной 7Б64
Затраты на электроэнергию потребляемую станками руб
Таблица 5 – Расчет затрат на электроэнергию потребляемую станками по базовому варианту
Назначение оборудования
Наименование и марка
Суммарная мощность электро
Суммарное время обработки деталей мин
Резка заготовок деталей
Автомат для горячей навивки пружин АБ 5424
Фрезерно-центровальный
Затраты на электроэнергию при выполнении сварочных работ определяются по формуле 24
где - расход электроэнергии при выполнении сварочных работ кВтчкг; при сварке на постоянном токе = 354; примем = 4 при сварке проволокой диаметром 16; = 35 при сварке проволокой диаметром 12;
- масса наплавленного металла кг; см. таблицу 3;
Затраты на сварочную электроэнергию по проектируемому варианту
= 4 × 0131 = 0524 руб.
Затраты на сварочную электроэнергию по базовому варианту
= 35×0009 +4×0055 = 025 руб.
Общие затраты по статье электроэнергия составят:
по проектируемому варианту = 947 + 0524 = 10 руб.
по базовому варианту = 2608 +025 = 2633 руб.
3 Расчет затрат на заработную плату
В затраты на заработную плату включают затраты на основную и дополнительную заработную плату производственных рабочих и выплаты предусмотренные законодательством.
Основная заработная плата производственных рабочих при тарифной системе оплаты труда определяется по формуле 25
где - часовая тарифная ставка рабочего соответствующего разряда руб.ч;
- суммарное штучное время на выполнение операций одного
Расчет основной заработной платы производственных рабочих при изготовлении изменяемой части подвески по проектируемому и базовому варианту приведем в таблицах 6 и 7.
Таблица 6 – Расчет основной заработной платы производственных рабочих по проектируемому варианту.
Основная заработная плата
по проектируемому варианту
Таблица 7 – Расчет основной заработной платы производственных рабочих по базовому варианту
по базовому варианту
Дополнительная заработная плата основных производственных рабочих составляет 10% от основной.
Дополнительная заработная плата основных производственных рабочих при изготовлении подвески по проектируемому варианту
= 01×111.1 = 111 руб.
Дополнительная заработная плата основных производственных рабочих при изготовлении подвески по базовому варианту
= 01×2216 = 222 руб.
Премиальная заработная плата основных производственных рабочих составляет 35% от основной.
Премиальная заработная плата основных производственных рабочих при изготовлении подвески по проектируемому варианту
= 035×1111 = 389 руб.
Премиальная заработная плата основных производственных рабочих при изготовлении подвески по базовому варианту
= 035×2216 = 7756 руб.
Заработная плата с начислениями (учетом уральского коэффициента) рассчитывается по формуле 26
где - уральский коэффициент =015;
Заработная плата с начислениями при изготовлении подвески по проектируемому варианту
= (1111+111+389)×(1+015) = 18526 руб.
Заработная плата с начислениями при изготовлении подвески по базовому варианту
= (2216+222+7756)×(1+015) = 3696 руб.
Отчисления на социальные нужды составляют 26% процентов от заработной платы с начислениями
Отчисления на социальные нужды при изготовлении подвески по проектируемому варианту
= 026×18526 = 4816 руб.
Отчисления на социальные нужды при изготовлении подвески по базовому варианту
= 026 × 3966 = 10312 руб.
Общие расходы на заработную плату составят:
= 18526 + 4816 = 233 42 руб.
по базовому варианту
= 3696 +10312 = 49972 руб.
4 Расходы на содержание и эксплуатацию оборудования
Данный вид расходов рассчитывается по формуле 27
где - коэффициент учитывающий износ оборудования; = 4555%;
Расходы на содержание и эксплуатацию оборудования при изготовлении подвески по проектируемому варианту
Расходы на содержание и эксплуатацию оборудования при изготовлении подвески по базовому варианту
Накладные расходы принимаются в размере 7% от суммы затрат по всем предыдущим статьям расходов.
5 Расчет себестоимости изменяемой части проектируемой
Расчет себестоимости изготовления изменяемых частей торсионной и пружинной подвесок прицепа «Сармат – 8232» для легковых автомобилей выполним в виде таблицы 8.
Таблица 8 – Расчет себестоимости изготовления изменяемой части подвески прицепа «Сармат-8232»
Содержание и эксплуатация оборудования
Накладные расходы Н
Внедрение предлагаемой конструкции торсионной подвески на прицепе для легковых автомобилей «Сармат-8232» позволит снизить себестоимость прицепа на =76313 рубля.
6 Расчет технико-экономических показателей проекта
где - годовая программа выпуска прицепов шт; = 300 шт;
При рассчитанной величине годовой прибыли срок окупаемости мероприятия составит
Технико-экономические показатели проекта сведем в таблицу 9
Таблица 9 – Технико-экономические показатели проекта
Капитальные затраты руб.
Себестоимость изготовления изменяемой части руб.; в том числе:
3 Заработная плата З
4 Содержание и эксплуатация оборудования
5 Накладные расходы
Годовая программа выпуска шт.
Годовая прибыль предприятия руб.
Срок окупаемости лет
Существенно снизить трудоёмкость и металлоёмкость прицепа можно за счет изменения конструкции его подвески заменив применяемую в настоящее время пружинную зависимую подвеску на торсионную независимую. Этот путь снижения трудоёмкости и металлоёмкости прицепа в настоящее время выбран многими производителями широко применяющих в конструкции видоизменение торсионной подвески – резиножгутовую подвеску. Основные элементы резиножгутовой подвески приобретаются у европейских производителей что существенно сказывается на цене прицепа.
Торсионная подвеска широко применяющаяся на военных транспортных средствах и отличающаяся простотой и высокой надежностью позволит существенно повысить конкурентоспособность прицепа «Сармат-8232».
Список использованных источников
Кузнецов В.А. Дьяков И.Ф. Конструирование и расчет автомобиля. Подвеска автомобиля: Учебное пособие. – Ульяновск: УлГТУ 2003. – 64 с
Рампель Й. Шасси автомобиля: Элементы подвески Пер. с нем.
А.Л. Карпухина под ред. Г.Г. Гридасова. – М.: Машиностроение 1987. – 288с
Осепчугов В.В. Фрумкин А.К. Автомобиль. Анализ конструкций элементы расчета: Учебник для студентов вузов по специальности « Автомобили и автомобильное хозяйство». – М.: Машиностроение 1989. – 304с
Анурьев В.И. Справочник конструктора-машиностроителя: В 3-х т. Т.1 – 6-е изд. перераб. и доп. – М.: Машиностроение 1982. – 576 с.
Салов А. И. Охрана труда на предприятиях автомобильного транспорта. М. Транспорт 1970 392с.
Пластина присоединительная.cdw

*Размер для справок.
Неуказанные предельные отклонения размеров
Экономические показатели проекта.cdw

и базовой пружинной подвески прицепа "Сармат-8232
Материалы основные и
Содержание и эксплуатация
Себестоимость изменяемой
Проектируемый вариант
Характеристика прицепов.cdw

Лист торсиона.cdw

Сталь 60С2Х ГОСТ14959-79
Деформация концов листа не допускается
Неперпендикулярность реза концов листа не более 0
Рекомендуемые чертежи
- 09.06.2022
Свободное скачивание на сегодня
Другие проекты
- 29.07.2014