Расчетно-графическая работа


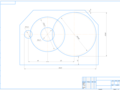
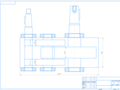
- Добавлен: 24.01.2023
- Размер: 3 MB
- Закачек: 0
Описание
Состав проекта
![]() |
![]() |
![]() ![]() ![]() |
![]() |
![]() ![]() ![]() ![]() |
![]() ![]() ![]() ![]() |
![]() ![]() |
![]() ![]() ![]() |
Дополнительная информация
Моя.doc
ВЫБОР И ОБОСНОВАНИЕ ОПТИМАЛЬНОГО ВАРИАНТА КОНСТРУКЦИИ9
КИНЕМАТИЧЕСКИЙ РАСЧЕТ РЕДУКТОРА13
СТАТИЧЕСКОЕ ИССЛЕДОВАНИЕ РЕДУКТОРА14
1 Определение моментов в зубчатых колесах.14
2 Определение усилий в зацеплении15
3 Определение реакций опор16
ГЕОМЕТРИЧЕСКИЙ РАСЧЕТ ЗУБЧАТЫХ ПЕРЕДАЧ18
РАСЧЕТ ЗУБЧАТЫХ ПЕРЕДАЧ19
1 Выбор материала и термообработка зубчатых колес19
1.1 Допускаемые контактные напряжения20
1.2 Допускаемые изгибные напряжения21
2 Проверочный расчет тихоходной ступени на прочность23
2.1 Проверка зубьев колес по контактным напряжениям23
2.2 Проверка зубьев колес по напряжений изгиба24
ПРОЕКТИРОВАНИЕ ВАЛОВ26
ПОДБОР ПОДШИПНИКОВ ДЛЯ ВАЛОВ30
1 Проверка подбора и определение ресурса подшипников промежуточного вала30
СПИСОК ИСПОЛЬЗОВАННОЙ ЛИТЕРАТУРЫ .34
Привод грузоподъемной машины был сконструирован для передачи крутящего момента на барабан который обеспечивает поднятие груза со скоростью 039мс.
Привод грузоподъемной машины (рисунок 2) состоит из электродвигателя редуктора барабана троса. Электродвигатель и барабан присоединены к редуктору при помощи муфт.
Рисунок 1. Схема привода.
Редуктор состоит из быстроходной шевронной передачи и тихоходной косозубой передачи. Для корпуса редуктора была применена современная конструкция. Все выступающие элементы устранены с наружных поверхностей и введены внутрь. Лапы под фундаментальные болты не выступают за габариты корпуса. Проушины для подъема и транспортировки редуктора отлиты заодно с корпусом.
Для удобства сборки корпус выполнен с разъемом. Плоскость разъема проходит через оси валов.
Ресурс L1000 (час) = 10
Рисунок 2. Схема редуктора №21.
ПОДГОТОВКА ДАННЫХ ДЛЯ ВВОДА В ЭВМ
1 Определение диаметра каната:
2 Определение диаметра барабана:
По ГОСТ 6636-60 принимаем Dбар=160 мм.
3 Частота вращения барабана:
4 Подбор электродвигателя
Мощность электродвигателя:
Определение КПД привода:
где = 09 – КПД барабана лебедки;
= 099 – КПД подшипника;
= 097 – КПД зацепления;
Подбор электродвигателя.
Из таблицы 24.9 [2] определим двигатель с мощностью не менее Pпотр.
По техническим данным двигателей серии АИР подсчитаем передаточное отношение:
nасинх = nсинх (1-x)
По значениям данной таблицы выберем двигатель типа 112MB6 со значением i=2020.
5 Определение крутящегоо момента на барабане лебедки:
6 Определение момент на колесе тихоходной передачи:
7 Определение эквивалентного срока службы
где KHE – коэффициент эквивалентности. Для режима нагружения – 3
KHE = 018 (табл. 8.10 [1]).
Lhe = 10000 × 018 = 1800 час.
ВЫБОР И ОБОСНОВАНИЕ ОПТИМАЛЬНОГО ВАРИАНТА КОНСТРУКЦИИ
Произведем расчет всех вариантов компоновки редуктора с целью нахождения наиболее оптимального из них.
Рисунок 3 - Схема редуктора
Данный вид расчета осуществляется по следующим формулам:
B = bwБ + bwТ + 3×a;
L = 05×(da1Б + da2Т) + awБ + awТ ;
где – коэффициент пропорциональности для стальных зубчатых колес можно принять равным 612 кгдм3
А- высота редуктора;
В- ширина редуктора;
V – объем корпуса редуктора;
bwТ – ширина венца тихоходной ступени;
bwБ – ширина венца Быстроходной ступени;
da1Б – диаметр шестерни быстроходной ступени;
da2Б – диаметр колеса быстроходной ступени;
da2Т – диаметр колеса тихоходной ступени;
awБ – межосевое расстояние быстроходной ступени;
awТ – межосевое расстояние тихоходной степени;
a – зазор между корпусом и вращающимися деталями передач (колесами) (одно значение для всех вариантов).
вариант компоновки редуктора
Строим график зависимости V и m от количества вариантов
Оптимальным по массе и объёму является вариант 4
КИНЕМАТИЧЕСКИЙ РАСЧЕТ РЕДУКТОРА
Частота вращения шестерни быстроходной передачи:
Частота вращения колес промежуточного вала:
Частота вращения колеса тихоходной передачи:
На шестерне и колесе быстроходной передачи
На шестерне и колесе тихоходной передачи
СТАТИЧЕСКОЕ ИССЛЕДОВАНИЕ РЕДУКТОРА
Рисунок 4. Составляющие полного усилия в зацеплениях передач.
1 Определение моментов в зубчатых колесах.
На хвостовике быстроходного вала
где uБ = 556 – передаточное число быстроходной ступени.
uТ = 362 – передаточное число тихоходной ступени
На шестерне полушеврона быстроходной передачи
На колесе полушеврона быстроходной передачи
На шестерне тихоходной передачи:
2 Определение усилий в зацеплении
Окружная сила на шестерне быстроходной ступени:
Радиальная сила на шестерне быстроходной ступени:
Осевая сила на шестерне быстроходной ступени:
Усилия действующие на колесо быстроходной передачи:
Окружная сила на шестерне тихоходной ступени:
Радиальная сила на шестерне тихоходной ступени:
Осевая сила на шестерне тихоходной ступени:
Усилия действующие на колесо тихоходной передачи:
3 Определение реакций опор.
Рассмотрим промежуточный вал и действующие на него нагрузки:
Рисунок 5. Действующие нагрузки на промежуточный вал.
Рассчитаем расстояние между колесами и шестернями:
Сумма моментов относительно опоры 3:
R4Y = R3Y = 558532 H;
Сумма моментов относительно опоры 4:
Определим радиальные и осевые реакции опор:
ГЕОМЕТРИЧЕСКИЙ РАСЧЕТ ЗУБЧАТЫХ ПЕРЕДАЧ
Геометрический расчет выполняется в минимальном объеме. Определению подлежат: делительные d1 и d2 и начальные dw1 и dw2 диаметры колес; коэффициенты смещения X1 и диаметры окружностей вершин da1 и угол зацепления коэффициент торцевого перекрытия коэффициент осевого перекрытия eb для косозубых колес. Все колеса нарезаются реечным инструментом или долбяком с исходным контуром по ГОСТ 13755-81 с параметрами: угол профиля a = 20°; коэффициентом головки (ножки) зуба ; коэффициент радиального зазора с* = 025.
Выполним расчет для тихоходной косозубой передачи:
Коэффициенты смещения колес равны нулю т.к. суммарный коэффициент смещения X = X1 + X2 = 0.
Следовательно a W =a =20
– делительные диаметры приводятся в распечатке:
– начальные диаметры:
- коэффициент торцового перекрытия:
- коэффициент осевого перекрытия:
- суммарный коэффициент перекрытия:
РАСЧЕТ ЗУБЧАТЫХ ПЕРЕДАЧ
1 Выбор материала и термообработка зубчатых колес.
Зубчатые колеса редукторов изготавливают из сталей с твердостью H 350 HB или H > 350 HB. В первом случае заготовки для колес подвергают нормализации или улучшению во втором – после нарезания зубьев различным видам термической и химико-термической обработки: объемной закалке поверхностной закалке ТВЧ цементации азотированию нитроцементации и т.д. обеспечивающим высокую твердость поверхности зуба. Относительно низкая твердость
H 350 HB допускает возможность зубонарезания с достаточной точностью (степень точности 8 и 7 по ГОСТ 1643-81) без отделочных операций что используется как средство для снижения затрат. Применение других видов термообработки вызывает заметное искажение размеров и формы зубьев (коробление). При высоких требованиях к точности такие колеса подвергают отделочным операциям – зубошлифованию притирке на специальных станках обкатке и т.п. что повышает стоимость колес в десятки раз.
Зубчатые колеса с низкой твердостью хорошо прирабатываются особенно если зубья шестерни имеют твердость больше чем у колес на (80 200) HB. У косозубых колес перепад твердости выше. Хорошие результаты обеспечивает закалка ТВЧ зубьев шестерен с HRC 45 55 и термоулучшение колес до 280 350 HB.
При выборе материалов необходимо руководствоваться информацией указанной в табл. 1.10 [1] и стремиться к получению допускаемых напряжений возможно близких к ним величин [sH]Б и [sH]Т.
Материалы и обработку зубчатых колес выбираем по таблице 8.9[3]
Тихоходная ступень редуктора:
Материал шестерни- Сталь35ХМ;
Поверхностная твердость зубьев- HRC 45 55
Улучшение и закалка ТВЧ
Материал колеса- Сталь40Х;
Поверхностная твердость зубьев 350
Термообработка- улучшение.
1.1 Допускаемые контактные напряжения
Допускаемые контактные напряжения рассчитаем по формуле:
где – допускаемые контактные напряжения для колеса тихоходной ступени;
- допускаемые контактные напряжения для шестерни тихоходной ступени;
где - предел длительной прочности соответствующий базовому числу циклов;
SH – коэффициент безопасности.
ZN – коэффициент долговечности.
Для колеса по таблице 89[3] определяем:
=2·350+70=770 (МПа);
Коэффициент долговечности определяем по формуле 861[3].
где NHG1 = 30×HB 24=30×350 24 =3827×10 6;
NHE1 – эквивалентное число циклов;
NHE1 = NH × H = 60 × nw × n1 × Lh × mH =60×1×940×1800×018 = 18×106;
где nw – число зацеплений в которое входит шестерня или колесо за один оборот nw = 1;
n1 – соответствующая частота вращения;
Lh – ресурс привода;
mH – коэффициент режима определяемый по табл. 8.10 [3] в зависимости от категории режима.
Рассчитаем коэффициент долговечности:
Допускаемые контактные напряжения:
Для шестерни по таблице 89[3] определяем:
=17×45+200=965 (МПа);
Коэффициент долговечности.
где NHG2 = 25×10 6- по рисунку 8.40 [3].
NHE2 – эквивалентное число циклов соответствующее
NHE2 = NH × H = 60 × nw × n2 × Lh × mH =60×1×16906×1800×018=33×10 6;
Допускаемые контактные напряжения:
Рассчитаем допускаемые контактные напряжения:
1.2 Допускаемые изгибные напряжения
Допускаемое напряжение изгиба определим по формуле:
YА – коэффициент учитывающий влияние двустороннего приложения нагрузки (при односторонней нагрузке KFC=1);
YR – коэффициент учитывающий шероховатость переходной кривой.(YR = 1 при шероховатости RZ 40 мкм);
YN – коэффициент долговечности;
SF – коэффициент безопасности;
Рассчитаем пределы выносливости для колеса и шестерни (табл.8.9 [3]);
Принимаем значение коэффициентов безопасности для шестерни и колеса
SF = 175 по табл.8.9 [3];
Коэффициент долговечности определим по формуле :
где NFG = 4×10 6 – базовое число циклов;
NFE – эквивалентное число циклов;
Эквивалентное число циклов определим по формуле:
где F – коэффициент эквивалентности по табл.8.10 [3]
для шестерни: F = 0016;
для колеса: F = 0038.
Nк – число циклов перемены напряжений за весь срок службы;
где с – число зацеплений зуба за один оборот колеса;
n – частота вращения;
NFE1 =F1× Nк1 = 60×с× n1×LH ×F1 = 60×1×940×1800×0016 = 16×10 6;
NFE2 =F2× Nк2 = 60×с× n2×LH ×F2 = 60×1×16906×1800×0038 = 07×10 6;
Допускаемые изгибные напряжения равны:
2 Проверочный расчет тихоходной ступени на прочность
2.1 Проверка зубьев колес по контактным напряжениям
Контактные напряжения определяются по формуле:
Коэффициент расчетной нагрузки:
где KHb - коэффициент концентрации нагрузки;
KHV - коэффициент динамической нагрузки;
KHa - коэффициент распределения нагрузки между зубьями.
Коэффициент распределения нагрузки между зубьями при v = 0585 мс KHa=107 по табл. 8.7 [3]).
Коэффициент ширины шестерни относительно диаметра:
Коэффициент концентрации нагрузки при постоянной нагрузке при ybd = 097
KHb = 104 по рис.8.15 [3].
Коэффициент динамической нагрузки определим по табл.8.3[3]:
Коэффициент расчетной нагрузки
KH = KHb×KHV×KHa= 104×102×107 = 114.
Eпр – приведенный модуль упругости. Для стальных колес и шестерен
Т1 – момент на шестерни передачи;
dw1 – начальный диаметр шестерни;
bw – ширина зубчатого венца колеса;
aw – угол зацепления;
u – передаточное число передачи .
Коэффициент ZHb определяется по формуле:
где ea – коэффициент торцевого перекрытия;
b – угол наклона зубьев на делительном диаметре (из распечатки)
Величина контактного напряжения
условие прочности выполняется.
2.2 Проверка зубьев колес по напряжений изгиба
Напряжения в основании зубьев колес определяются по формулам:
sF1 =YF1×ZFb×Ft×KF(bw×m)
YF – коэффициент формы зуба;
Эквивалентное число зубьев:
где z – число зубьев
b – угол зацепления (из распечатки);
Коэффициент формы зуба по рис.8.20 [3]
ZFb – коэффициент вычисляемый по формуле
KFa – коэффициент учитывающий распределение нагрузки между зубьями равный 122 по табл. 8.7 [3];
Yb – учитывает работу зуба как пластины (а не балки) и определяется равенством
Yb = 1 –b°140° = 1-14070140=0899;
ZFb = KFa×Ybea=122×0899164=0668
Коэффициенты расчетной нагрузки
Коэффициент распределения нагрузки между зубьями по табл.8.7[3]:
Коэффициент концентрации нагрузки по рис 8.15 [3]:
Коэффициент динамической нагрузки по табл.8.3[3]:
sF1 = YF1 × ZFb × Ft ×KF(bw×m) = 4×0668×835255×163(525×25) = 2772 МПа;
sF2 = sF1 × YF2 YF1.= 2772 ×3754 = 25987 МПа.
Условия прочности для шестерни и колеса выполняются.
Рассмотренная ступень редуктора обеспечит необходимую долговечность и ресурс при заданных нагрузках.
ПРОЕКТИРОВАНИЕ ВАЛОВ
Рисунок 6. Конструкции валов редуктора.
Диаметры участков валов:
– для быстроходного вала
Диаметр конца выхода вала-шестерни
Диаметр посадочной поверхности под подшипник
Диаметр буртика для упора подшипника
Длина посадочного места:
Длина промежуточного участка:
Наружная резьба хвостовика быстроходного вала имеет диаметр
– для промежуточного вала
Принимаем d2 =dk=42 мм;
Диаметр посадочной поверхности для подшипника
Диаметр буртика для упора подшипника:
Диаметр буртика для упора колеса:
– для тихоходного вала
Принимаем dБК = 64 мм
Длина промежуточного участка тихоходного вала:
LКТ = (08 12) × dП .=(08 12)·50 = 40 60 мм
Наружная резьба хвостовика вала имеет диаметр
Значения переходных радиусов и заплечиков приведены в табл. 1.9[1]
Консольные участки входного и выходного вала выполнены коническими по ГОСТ 12081-72. Конический конец входного вала выполнен с наружной резьбой а конец выходного вала выполнен с внутренней резьбой.
Размеры выходного вала определяются по табл.24.27 [2].
Для быстроходного вала:
Рисунок 7. Окончание быстроходного вала
Для тихоходного вала:
Рисунок 8. Окончание тихоходного вала
ПОДБОР ПОДШИПНИКОВ ВАЛОВ
) Для быстроходного вала-шестерни выберем шариковый радиальный однорядный подшипник №207 по ГОСТ 8338-75 (табл. 24.10):
) Внутренний диаметр подшипников промежуточного вала определим по формуле:
где r=25 (мм) – переходной радиус( по табл.19[3]);
По ГОСТ 8338-75 выбираем шариковый радиальный однорядный подшипник 207 (легкая серия).
) Внутренний диаметр подшипников тихоходного вала:
По ГОСТ 8338-75 выбираем шариковый радиальный однорядный подшипник 210 (легкая серия).
1 Определение ресурса подшипников промежуточного вала
Рассчитаем подшипник по динамической грузоподъемности по формуле:
где а1 = 1 – коэффициент надежности;
а2 = 1 – обобщенный коэффициент совместного влияния качества металла и условий эксплуатации;
α = 3 (для шариковых подшипников);
– эквивалентная нагрузка;
X Y – коэффициенты радиальной и осевой нагрузок (по табл.16.5 [1])
V – коэффициент вращения зависящий от того какое кольцо вращается (при вращении внутреннего кольца V = 1);
ks – коэффициент безопасности учитывающий характер нагрузки ( при умеренных толчках ks = 13)
kT – температурный коэффициент (при температуре до 100 С 0 kT = 1).
По табл. 24.10 [2] определим параметры подшипника:
Динамическая грузоподъемность С = 255 (кН);
Статическая грузоподъемность С0 = 137 (кН).
е = 034 (табл.16.5 [1];
Эквивалентная нагрузка:
17 > 1800 условие выполняется.
Рисунок 9. Соединение шпонкой.
Подбор шпонок произведем по таблицам стандартов ГОСТ23360-78 для соединений типа вал-ступица. Принимаем величину допускаемых напряжений смятия [sсм] = 120 (МПа).
Определим рабочую длину шпонки:
)Для колеса быстроходного вала:
Для соединения быстроходного вала диаметром вала d =32 мм выбираем по табл.24.29 [2] призматическую шпонку имеющую следующие параметры:
l1 = lр1 + b=1457+10=2457 (мм)
согласуем со стандартным числовым рядом l=25 (мм).
где h – высота шпонки;
) Для колеса тихоходного вала:
Для соединения тихоходного вала диаметром вала d = 45 мм выбираем по табл.24.29 [1] призматическую шпонку имеющую следующие параметры:
l3 = lр3 + b=5967+14 = 7367 (мм)
согласуем со стандартным числовым рядом l = 70 (мм).
) Для промежуточного вала вала:
Для соединения промежуточного вала диаметром d=42 мм с колесом выбираем призматическую шпонку имеющую следующие параметры:
l4 = lр4 + b = 2242+8 =3042 мм
согласуем со стандартным числовым рядом l = 32 (мм).
В ходе выполнения расчетно-графической работы был разработан редуктор с рациональными показателями массы размеров и себестоимости отвечающий требованиям по безотказной работе и ресурсу.
СПИСОК ИСПОЛЬЗОВАННОЙ ЛИТЕРАТУРЫ
Анурьев В.И. «Справочник конструктора - машиностроителя» том 1. - М.: Машиностроение 1978 - с. 728.
Анурьев В.И. «Справочник конструктора - машиностроителя» том 2. - М.: Машиностроение 1979 - с. 559.
Дунаев П.Ф. Леликов О.П. «Конструирование узлов и деталей машин» - М.: Высшая школа 1985 - с.416.
Решетов Д.Н. «Детали машин» - М.: Машиностроение1989 - с. 496.
Иванов М.Н. «Детали машин»- М.: Высшая школа 1991 - с.383.
Вид2.cdw

Вид1.cdw

1лист.doc
Уфимский Государственный Авиационный Технический Университет
Кафедра основ конструирования механизмов и машин
Пояснительная записка
к расчетно-графической работе
по дисциплине ”Детали машин и основы конструирования ”
Рекомендуемые чертежи
- 24.01.2023
- 18.12.2020