Расчет и проектирование дисковой фрезы для обработки винтовой фасонной поверхности




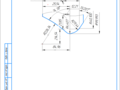
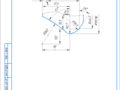
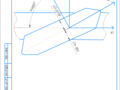
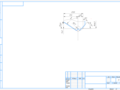
- Добавлен: 24.01.2023
- Размер: 1 MB
- Закачек: 0
Описание
Состав проекта
![]() |
![]() |
![]() |
![]() ![]() ![]() ![]() |
![]() ![]() |
![]() ![]() ![]() |
![]() |
![]() ![]() ![]() |
![]() ![]() ![]() ![]() |
![]() |
![]() ![]() ![]() ![]() |
![]() |
![]() |
![]() ![]() ![]() |
![]() |
![]() ![]() ![]() ![]() |
![]() |
![]() |
Дополнительная информация
Чертеж2.cdw

СОДЕРЖАНИЕ,введение,аннотация,заключение,титульный.docx
Фрезерование является высокопроизводительной технологической операцией. Один из способов получения винтовой фасонной поверхности – фрезерование дисковой двуугловой фрезой.
В данном проекте рассчитана дисковая фреза применением нескольких методов: путем решения прямой задачи профилирования (на ЭВМ) путем аппроксимации теоретического профиля двуугловым линейным решением обратной задачи профилирования. призматический фасонный резец три варианта конструкций шлицевой протяжки с различными конструктивными параметрами и параметрами обработки выбран наиболее оптимальный из них. Выполнены рабочие чертежи фасонного резца выбранного варианта шлицевой протяжки.
Расчет призматического фасонного резца . 5
1Определение расчетных размеров детали . .5
2Выбор переднего и заднего углов 7
3Расчет глубины профиля . . .7
4Расчет криволинейных участков профиля 13
5Пересчет глубин и линейных размеров профиля резца от базовых поверхностей 10
6Пересчет размеров 14
7Длина режущих кромок . .18
8Выбор державки призматического фасонного резца 19
Расчет шлицевой протяжки . .. 20
Библиографический список . .50
Обработка металлов резанием является одним из самых распространенных способов формообразования деталей. Несмотря на значительное развитие способов формообразования без снятия стружки таких как литье ковка штамповка обработка металлов резанием остается ведущим завершающим процессом производства машин и приборов. Широкое распространение этого способа в промышленном производстве объясняется в первую очередь его универсальностью и возможностью достижения высокого класса точности и чистоты образованной поверхности.
В данной курсовой работе были рассчитаны три режущих инструмента – фасонный призматический резец три варианта круглой протяжки дисковый долбяк. Выбран оптимальный вариант протяжки.
Выполнены рабочие чертежи фасонного призматического резца дискового долбяка и оптимального варианта протяжки на форматах А2 А1.
Федеральное агентство по образованию
Южно – Уральский Государственный Университет
Механико–технологический факультет
Кафедра «Станки и инструмент»
Расчетно-пояснительная записка
к курсовому проекту
«Расчет и проектирование дисковой фрезы для обработки винтовой фасонной поверхности»
студент группы МТ-564
БИБЛИОГРАФИЧЕСКИЙ СПИСОК
УДК 621.9.02(076.5) Васькин В.А. Шаламов В.Г. Гаврилов Ю.В. Режущий инструмент: Учебное пособие по курсовому проектированию. - Челябинск: Изд. ЮУрГУ1998-215с.
Грановский Г.И. Панченко К.П. Фасонные резцы. - М.:Машиностроение1975.-310с.
Моргулис Д. К. и др. Протяжной инструмент. – Челябинск: «Металлургия» 1992 – 336с.
Романов В. Ф. Расчет зуборезного инструмента. – М:Машиностроение 1969 – 251с.
Анурьев В.И. Справочник конструктора-машиностроителя: В 3-х т. – 7-е изд. перераб. и доп. –М.: Машиностроение 1992
СТП 04-01. Стандарт предприятия. Курсовые и дипломные проекты. Общие требования к оформлению. – Челябинск ЧГТУ 2001.
Фрагмент.frw

схема установки.cdw

Чертеж.cdw

записка.DOC
Сущность аналитического расчёта профиля дискового инструмента_
Результаты расчёта дисковой фрезы на ЭВМ и схема установки
инструмента при фрезеровании винтовой стружечной канавки_
Аппроксимация криволинейного профиля фрезы угловым и выбор
расчётных точек профиля_
Решение обратной задачи профилирования_
Графическое решение прямой задачи профилирования_
Определение нормальных и радиальных задних углов затылованной
Определение основных геометрических параметров фрезы_
Винтовые поверхности широко используют в конструкциях различных инструментов например червячных фрез. Форма винтовой поверхности и требования к её точности у различных инструментов различны.
Профиль винтовой поверхности получается как огибающая ряда последовательных положений поверхности инструмента при его относительном движении. Поэтому профиль винтовой поверхности не совпадает с профилем профилирующего инструмента (например дисковой фрезы) и для каждого конкретного случая подлежит определению. Т.е. по заданной форме обрабатываемой поверхности должен определяться профиль инструмента (прямая задача профилирования). Но также можно задавшись профилем инструмента посмотреть какой же профиль получится у обрабатываемой детали (обратная задача профилирования).
Решение вышеприведенных проблем и является основной целью данной курсовой работы.
Исходные данные и эскиз обрабатываемого профиля
Исходные данные согласно варианта задания 1:
Диаметр изделия D = 30 мм.
Число зубьев инструмента z = 3.
Угол наклона зубьев w=30°.
Глубина стружечной канавки h = 02D = 6 мм.
Передний угол в нормальном сечении gN = 15°.
Радиус у основания зуба r = 05h = 3 мм.
Угол скрещивания осей инструмента и заготовки = 685о.
Ориентировочный диаметр фрезы Dф = 1047 мм.
Согласно исходных данных приведенных выше и результатов вычислений на ЭВМ получен эскиз обрабатываемого профиля (рисунок 1).
Рисунок 1 - Эскиз обрабатываемого профиля
Сущность аналитического расчета профиля дискового инструмента
Аналитический метод расчёта профиля дискового инструмента достаточно сложен и громоздок. Для каждой i – ой точки заданного профиля изделия определяется угол контакта инструмента и заготовки. По этому углу определяются координаты точки контакта которые в совокупности дают характеристику т.е. линию касания инструмента и изделия. Поверхность инструмента получается вращением характеристики вокруг оси инструмента.
Данный расчёт выполняется по исходным данным и производится на ЭВМ (см. пункт 3). По полученным в результате расчёта данным строится эскиз теоретического профиля дисковой фрезы с указанием узловых точек профиля точки скрещивания осей инструмента и изделия и всех других параметров указанных в распечатке. Особое внимание при анализе результатов расчёта уделяется параметрам установки дисковой фрезы а особенно положению точки скрещивания осей.
Результаты расчета дисковой фрезы на ЭВМ и схема установки инструмента при фрезеровании винтовой стружечной канавки
Рисунок 2 - Схема установки инструмента и заготовки
Аппроксимация криволинейного профиля фрезы двуугловым и выбор расчетных точек профиля
Полученный теоретический криволинейный профиль фрезы необходимо заменить прямолинейным т.е. аппроксимировать (рисунок 3). Проведенная замена улучшит технологичность изготовления дисковой фрезы. При этом необходимо стремиться к тому чтобы величина вносимой погрешности была наименьшей а на профиле фрезы не было резких переходов. Угловые участки должны плавно сопрягаться с радиусом при вершине фрезы.
Необходимо определить углы y1 и y2 - углы наклона сторон профиля к оси фрезы. Если задаться координатами точек 1 и n как a и b то углы y1 и y2 могут быть определены из следующих соотношений:
где а b – координаты расчетной точки мм
r – радиус на вершине профиля фрезы мм
Для аппроксимации криволинейных участков фрезы прямолинейными использованы результаты распечатки решения прямой задачи:
bп= Т- bл = 2153-175=403 мм.(4.2)
aп= (D12) - x23 - r = мм(4.3)
где х23 – радиус диска инструмента огибающего переднюю поверхность на диаметре изделия мм.
yл1 = 3133о; yл2 = 1467°.
yп1 = 5473°; yп2 = -2875°.
В соответствии со схемой аппроксимации действительными значениями являются yл = yл1 = 3133° ; yп = yп1 = 5473°.
Зная угол y можно определить абсциссу точки касания прямолинейного участка с радиусом при вершине фрезы:
b3 = r*sin yп = 2754* sin 5473° = 224 мм.(4.5)
Длина прямолинейных конических участков измеренная вдоль оси фрезы составляет:
bл= bл – b5 = 175 - 143 = 1607 мм.
bп= Т – bл – b3 = 403 - 224 = 179 мм.
На прямолинейных конических участках выбираются расчетные точки (три на правой стороне профиля и пять на левой) равномерно расположенные по каждой стороне профиля и определяются радиусы Ri дисковой фрезы проходящие через расчетные точки.
R1=4635 мм (из распечатки прямой задачи).
Промежуточные радиусы определяются по выражению:
Рисунок 3 - Аппроксимация криволинейного профиля фрезы угловым.
Решение обратной задачи профилирования
Обратная задача профилирования заключается в определении формы поверхности винтовой канавки аппроксимированной фрезой при принятой выше схеме формообразования.
Расчёт профиля получаемой винтовой поверхности производится на основе решения уравнения контакта для каждой из расчётных точек инструмента. При этом определяется угол контакта для каждой из расчётных точек а зная угол контакта определяем её координаты на профиле инструмента. Потом по уравнениям взаимосвязи систем координат инструмента и заготовки переводят полученные координаты в систему координат заготовки. Далее приравнивая оду из координат заготовки к нулю получаем профиль винтовой канавки в осевом или в торцовом сечении
Для решения уравнения контакта определим координату y0 для каждой расчетной точки:
где Ri – радиус фрезы в I – ой расчетной точке мм.
Rф – минимальный радиус дисковой фрезы на конической поверхности фрезы формирующей винтовую поверхность мм.
– угол между осью фрезы и угловой режущей кромкой град.
с – расстояние от точки скрещивания до рабочей торцевой поверхности дисковой фрезы мм.
Здесь в соответствии с расчетной схемой угол y = yп =5473° берется со знаком минус и величина смещения c со знаком минус.
Для этой группы точек знаки y и c - противоположенные.
Из уравнения контакта определяется угол q. Решение уравнения осуществляется с использованием тригонометрической подстановки по следующему алгоритму:
где y0 - координата расчетной точки.
А – межосевое расстояние А= 53376 мм.(5.2)
– угол между осями уо и у (смотри рисунок 2)
t = 90° - e = 90° - 685о = 215°(5.3)
где – угол скрещивания осей инструмента и детали.
Р – винтовой параметр Р = r tg(w) = 15tg(30) = 25980 мм(5.4)
где r – наружный радиус обрабатываемого изделия мм.
– угол наклона стружечной канавки изделия град.
tgh1= = - 0560;h1= - 29249°.
tgh2= = - 0543;h2= - 28531°.
tgh3= = -0528;h3= - 27845°.
tgh5= = 0952;h5= 43595°.
tgh6= = 1072;h6= 47002°.
tgh7= = 1226;h7= 50816°.
tgh8= = 1433;h8= 55095°.
tgh9= = 07927;h9= 38404°.
cos (h-q)1 = = 0557;±(h-q)1= 5614.
cos (h-q)2 = = 0553;±(h-q)2= 5639.
cos (h-q)3 = = 0548; ±(h-q)3= 5671.
cos (h-q)5 = = 0634;±(h-q)5= 10641.
cos (h-q)6 = = 0408; ±(h-q)6= 10727.
cos (h-q)7 = = 0433; ±(h-q)7= 10821.
cos (h-q)8 = = 0458; ±(h-q)8= 10919.
cos (h-q)9 = = 0347; ±(h-q)9= 11029.
Таким образом для каждой расчетной точки имеются два значения угла контакта q: (Таблица 1).
Таблица 1 - Значение угла контакта
Угол контакта при профилировании должен плавно изменяться при переходе от одной расчетной точки к другой. Поэтому действительным углом контакта является угол q1 . Однако это следует проверить что наиболее просто сделать по 1 расчетной точке профиля фрезы которая профилирует режущую кромку изделия. Следовательно координата y1 на профиле изделия при правильном угле контакта будет равняться радиусу изделия r=15 мм. Координату y1 1 расчетной точки определяется для углов q1 = -79.897о; q2 = 21.398 о. Последовательно определяются величины :
x0 = R*sinq мм.(5.6)
z0= R*cosq - A мм.(5.7)
x1 = x0cost - y0sint + Pj мм.(5.9)
где φ – угол поворота заготовки рад.
y1 = (y0cost + x0sint)cosj + z0sinj мм.(5.10)
Для первой расчетной точки:
x0 = 46.35*sin(-79.897о) = -45.63 мм.
z0= 46.35*cos(-79.897о) - 53.376= -4524 мм.
tgj== -1336; j = -53203°= -0928 рад.
x1 = -4563*cos(215о) + 184*sin(215о) + 2598*(-0928) = -59837 мм.
y1 = (-184*cos(215о) - 45.63*sin(215о))*cos(-79897о) - 45.24*sin(-79897о) = =15.959 мм.
x0 = 46.35*sin(21.398 о) = 16.910 мм.
z0= 46.35*cos(21.398 о) - 53.376= - -10.221 мм.
tgj== -0.935; j = -43.10°= -0.752 рад.
x1 = 16910*cos(215о) +184*sin(215о) -2598*0752 = -9659 мм.
y1 = (-184*cos(215о) +16910*sin(215о))*cos(-4310о) -10221*sin(-4310о) = =-0990 мм.
На основании вышеприведённого расчёта можно сделать вывод что далее в расчётах принимается ряд угла контакта 1. Теперь по формулам 5.6 5.10 рассчитываются координаты осевого профиля получаемой винтовой канавки для остальных точек.
Для второй расчетной точки:
x0 = 4754*sin(-80226о) = - 4685 мм.
z0= 4754*cos(-80226о) - 53376= - 45305 мм.
tgj== -1.291; j = -52.254°= -0.912 рад.
x1 = -46.35*cos(215о) +19.241*sin(215о) - 25.98*0.912 = -60.232 мм.
y1 = (-19.241*cos(215о) - 46.35*sin(215о))*cos(-52.254 о) - 45.305*sin(-52.254 о) = 14.335 мм.
Для третьей расчетной точки:
x0 = 48.73*sin(-80.533о) = -48.066 мм.
z0= 48.73*cos(-80.533о) - 53.376= -45.361 мм.
tgj== -1.249; j = -51.330°= -0.895 рад.
x1 = -48.066*cos(215о) +20.083*sin(215о) - 25.98*0.895 = -60.636 мм.
y1 = (-20.083*cos(215о) - 60.636*sin(215о))*cos(-51.330о) - 45.361*sin(-51.330о) = 12.733 мм.
Для пятой расчетной точки:
x0 = 49.57*sin(-23.744о) = -19.960 мм.
z0= 49.57*cos(-23.744о) - 53.376= - 8.002 мм.
tgj== 0.759; j = 37.199°= 0.649 рад.
Поскольку необходимо получить j 0 то для 5-9 точек введем период и получим j =j -180°
Тогда j = -142801°= -2492 рад.
x1 = -19.960*cos(215о) + 8.002*sin(215о) -25.98*2492 = -19960 мм.
y1 = (19.193*cos(215о) - 19.960*sin(215о))*cos(-142801о) - 8.002*sin(-142801о) = -3.559 мм.
Для шестой расчетной точки:
x0 = 47.11*sin(-18.879о) = -15.243 мм.
z0= 47.11*cos(-18.879о) - 53.376= - 8.800 мм.
tgj== 1.033; j = -134043°= -2339 рад.
x1 = -15.243*cos(215о) - 15.152*sin(215о) - 25.98*2339= -80516 мм.
y1 = (15.152*cos(215о) + 1.102*sin(215о))*cos(-134043) - 8.800*sin(-134043) = 0408 мм.
Для седьмой расчетной точки:
x0 = 44.66*sin(-13.520о) = -10.441 мм.
z0= 44.66*cos(-13.520о) - 53.376= -9.953 мм.
tgj== 1.525; j = -123252°= -2151 рад.
x1 = -10.441*cos(215о) - 11.127*sin(215о) - 25.98*2151 = -69680 мм.
y1 = (11.127*cos(215о) - 10.441*sin(215о))*cos(-123252о) - 9.953*sin(-123252о) = 4745 мм.
Для восьмой расчетной точки:
x0 = 42.21*sin(-7.634о) = -5.607 мм.
z0= 42.21*cos(-7.634о) - 53.376= - 11.540 мм.
tgj== 2.534; j = -111533°= -1.194 рад.
x1 = -5.607*cos(215о) -7.102*sin(215о) - 25.98*1.194 = -58393 мм.
y1 = (7.102*cos(215о) -5.607*sin(215о))*cos(-111533о) - 11.540*sin(-111533о) =9063 мм.
Для девятой расчетной точки:
x0 = 39.76*sin(-31.286о) =-20.648 мм.
z0= 39.76*cos(-31.286о) - 53.376= - 19.398 мм.
tgj== -4.123; j = -100600°= -1.755 рад.
x1 = -20.648*cos(215о) -3.078*sin(215о) – 25.98*1755 = -47540 мм.
y1 = (3.078*cos(215о) -20.648*sin(215о))*cos(-100600о) - 19.398*sin(-100600о) = 12923 мм.
Результаты расчетов сведены в таблицу 2.
Таблица 2 - Расчетные данные профиля изделия
В профилировании винтовой поверхности изделия принимает участие и точка 4 профилирующей окружности. Уравнение контакта для этой точки не решается. Поэтому углом контакта для этой точки задаются. Точка 4 формирует переходную кривую на профиле обрабатываемого изделия и при определенных условиях она может срезать участки поверхности образованные другими расчетными точками. Поэтому для точки 4 задаётся некоторый диапазон применения угла q. Ориентировочным интервалом может служить изменение угла q от точки 3 до точки 5. Особенно важно чтобы точка 4 не срезала поверхность образованную точками 1 3 которые формируют переднюю поверхность на обрабатываемом изделии. С учетом сказанного определяются координаты x1 y1 обрабатываемые точкой 4 в диапазоне угла q = -20 -40°: (брать q в диапазоне
-40 -80 нецелесообразно т.к. полученные при этом координаты не будут соответствовать возможной траектории точки 4)
R4=D2=99.962=49.98 мм
у0 = х49 – G1 = 1759 + 3078 = 20668 мм. (см. пункт 3).
x0 = 4998*sin(-20о) = - 17094 мм.
z0= 40.013*cos(-20о) - 53376= - 6410 мм.
tgj== 0494; j = -153690°= -2682 рад.
x1 = -17094*cos(215о) - 20668*sin(215о) + 25980*0.459 = -93168 мм.
y1 = (20.668*cos(215о) - 17094*sin(215о))*cos(-153690о) - 6410*sin(-153690о) = =-8780 мм.
x0 = 4998*sin(-25о) = -21122 мм.
z0= 40.013*cos(-25о) - 53376= -8078 мм.
tgj== 0703; j = -144885°= -2528 рад.
x1 = -21122*cos(215о) - 20668*sin(215о) - 25980*2528 = -92923 мм.
y1 = (20.668*cos(215о) - 21122*sin(215о))*cos(-144885о) – 8078*sin(-144885о) = -4750 мм.
x0 = 4998*sin(-30о) = - 24990 мм.
z0= 40.013*cos(-30о) - 53376= - 10092 мм.
tgj== 1002; j = -134940°= -2355 рад.
x1 = -24990*cos(215о) - 20668*sin(215о) - 25980*2355 = -92012 мм.
y1 = (20.668*cos(215о) - 24990*sin(215о))*cos(-134940о) – 10092*sin(-134
x0 = 4998*sin(-35о) = - 28667 мм.
z0= 40.013*cos(-35о) - 53376= - 12434 мм.
tgj== 1425; j = -125050°= -2355 рад.
x1 = -28667*cos(215о) - 20668*sin(215о) - 25980*2355 = -90949 мм.
x0 = 4998*sin(-40о) = - 32126 мм.
z0= 40.013*cos(-40о) - 53376= - 15089 мм.
tgj== 2023; j = -116294°= -2030 рад.
x1 = -32126*cos(215о) - 20668*sin(215о) - 25980*2030 = -90198 мм.
y1 = (20.668*cos(215о) - 32126*sin(215о))*cos(-116294о) – 15089*sin(-116294о) =10225 мм.
Полученные данные для удобства построения траектории движения точки 4 сводятся в таблицу 3.
Таблица 3 – Координаты траектории движения точки 4
Взяв из таблиц 3 и 4 значения координат х1 и у1 в графической части работы строится винтовая стружечная канавка в осевом сечении.
(МТ - 557.04.25.00.02).
Графическое решение прямой задачи профилирования
Графическое профилирование инструмента основано на рассмотрении процесса формообразования детали. Позволяет наглядно представить процесс получения огибающей поверхности. На чертеже МТ – 557.04.25.00.02 представлен вариант определения профиля дисковой фрезы формирующей винтовую стружечную канавку. Построение ведётся с изображения профиля обрабатываемого изделия. Заданная винтовая поверхность рассекается плоскостями abcde расстояние между которыми определяется таким образом:
S = (001 003) H(6.1)
гдеH – шаг винтовой поверхности;
ПриD = 30 мм w = 30о H = 16324мм
Каждому осевому положению секущей плоскости соответствует определённое положение профиля в торцовом сечении. Величина смещения профиля будет равна:
Совокупность граничных точек торцовых сечений будет винтовыми линиями 12 пересечения винтовой канавки с наружным цилиндром заготовки.
Для определения точек контакта дискового инструмента с соответствующими винтовыми линиями винтовую поверхность рассекается плоскостями 123 перпендикулярными оси дискового инструмента. Расстояние между плоскостями:
При таком расстоянии между плоскостями сокращается число необходимых линий построения т.к. соответствующие точки пересечения следов плоскостей a b c d e и 1 2 3 будут располагаться на общих прямых параллельных оси заготовки.
Для примера рассматривается построение линии пересечения плоскости 8 с винтовой поверхностью. Плоскость 8 пересекает сечения a b c d e в указанных точках проекции которых указаны на торцовом сечении. В плоскости перпендикулярной оси фрезы эти точки откладываются на соответствующих линиях на расстоянии z i и соединяются плавной кривой. Аналогично строятся линии пересечения с винтовой поверхностью и других поверхностей 1 2 3 После построения всех кривых выбирается радиус дисковой фрезы и расположение оси с учётом следующего положения. В точках контакта нормали к винтовой поверхности изделия и поверхности дискового инструмента совпадают. Нормаль к поверхности вращения пересекает его ось.
Точку касания инструмента к винтовой поверхности можно определить касательным проведением окружности к винтовой поверхности представленной её сечениями плоскостями 1 2 3
Для определения профиля дисковой фрезы от линии проекции оси инструмента восстанавливают перпендикулярные прямые соответствующие плоскостям 1 2 3 на которые проектируются круговые проекции точек контакта окружностей фрезы. Получаемые точки соединяют плавной линией. Полученная рабочая ширина фрезы В р при выполнении рабочего чертежа увеличивается с обеих сторон на 2 5 мм чтобы исключить работу торцовых поверхностей.
Определение нормальных и радиальных задних углов затылованной фрезы
При профилировании режущего инструмента большое влияние уделяется обеспечению нормальных условий резания. Инструмент будет работоспособным если его режущая часть имеет геометрические параметры в соответствии с условиями его эксплуатации. Для определим радиальных и нормальных задних углов затылованного зуба использована расчётная схема (рисунок 4).
гдек – величина затылования к = 3 3;
z – число зубьев фрезы z = 14;
R i – радиус расчётной точки мм.
Рисунок 4 – Схема расчёта задних углов в нормальном и радиальном сечениях
Исходя из расчётной схемы:
Рисунок 5 – Схема расчета угла
Угол φ для расчётных точек 1 2 3 определяется по формуле:
гдеG1- Боковое смещение левого торца фрезы от точки скрещивания осей изделия и инструмента; G1=1418.
А0 – расстояние от левого торца дисковой фрезы до центра окружности с радиусом х31 ( А0 = 21977 мм.
А1 – координата центра окружности с радиусом х33 (х24); А1 = 16939
у0i – координата расчётной точки в системе координат инструмента.
R 2 – радиус на правой части профиля ( R2 = 23856 мм.
Угол φ для расчётных точек 5 6 7 8 9 находится по формуле:
где А 3 – координата центра окружности с радиусом на левой стороне профиля (= 43629 мм.
R 3 – радиус на левой части профиля ( R3 = 100392 мм.
= 0483; φ5 = 28877о.
= 0582; φ7 = 35379о.
= 0682; φ9 = 42971о.
Нормальные задние углы находятся по формуле:
= 0176; αN1 = 10005.
= 0188; αN1 = 10646.
По полученным данным строится график изменения задних углов по профилю затылованного зуба в расчётных точках (рисунок 5).
В плоскости наружного диаметра нормальное и радиальное сечения совпадают следовательно задний угол в радиальном сечении будет равен заднему углу в нормальном сечении.
= = 0617(см. пункт 8);
Рисунок 5 – Изменение задних углов по профилю затылованного зуба.
Определение геометрических и конструктивных параметров фрезы
Определение конструктивных параметров профилирующего инструмента необходимо для выполнения рабочего чертежа инструмента без которого в свою очередь невозможно его изготовление. Под конструктивными параметрами инструмента понимают: диаметр фрезы D диаметр посадочного отверстия d0 число зубьев z высота зуба h радиус дна впадины. Под геометрическими параметрами инструмента понимают: угол тела зуба угол впадины углы режущей части фрезы. Данные параметры определяются для двухугловой фрезы с острозаточенными зубьями полученной после аппроксимации теоретического профиля.
Диаметр фрезы В был определен ранее и приведен в распечатке ЭВМ. Диаметр посадочного отверстия d0 находится по зависимости 3
Число зубьев фрезы определяется по формуле:
где: -коэффициент равномерности; =25 3;
- угол контакта град; определяется по отношению
где: t – глубина резания мм; t = 8мм;
R – наружный радиус фрезы мм; R= 40 мм.
Округляем полученное значение в ближайшую меньшую сторону: z=14.
Угол соответствующий шагу зубьев град; определяемый по формуле
Принимаем трапециидальную форму зубьев. Радиус у дна впадины r=1мм. Высота зубьев h принимают равной 05-065 окружного шага зубьев
Передний угол выбирается в зависимости от физико- механических свойств обрабатываемого материала и материала инструмента. Учитывая что мы имеем фрезу из быстрорежущей стали и обрабатываем сталь с В > 1000 Мпа принимаем угол =15 3. Принимаем главный задний угол в нормальном сечении N = 10 3.
В пояснительной записке данного проекта были рассмотрены следующие вопросы: расчёт дисковой фрезы на ЭВМ аппроксимация криволинейного профиля фрезы угловым выбор расчётных точек решение обратной задачи профилирования дисковой фрезы.
В графической части данного проекта представлены: графическое построение профиля фрезы теоретический и действительный профиль винтовой стружечной канавки в осевом и радиальном сечениях рабочий чертёж двухугловой фрезы.
На основании чертежа МТ – 557.04.25.00.02 можно сделать вывод что принятая аппроксимация является правильной т.к. при обработке не будет срезаться соседний зуб заготовки.
Гаврилов Ю.В. Богатенков С.А. Расчёт на ЭВМ “СМ – 3” инструментов для обработки стружечных канавок фрез с винтовыми зубьями: Учебное пособие для курсового и дипломного проектирования Под ред. В.М. Меньшикова. – Челябинск: ЧПИ 1984. – 47 с.
Руководство по курсовому проектированию металлорежущих инструментов: Учебное пособие для вузов по специальности “Технология машиностроения металлорежущие станки и инструменты” Под общ. ред. Г.Н. Кирсанова – М.: Машиностроение 1986. – 288 с.: ил.
Справочник конструктора – инструментальщика: Под. общ. ред. В.И. Баранчикова. – М. : Машиностроение 1994. – 560 с. ил.
Шаламов В.Г. Щуров И.А. Расчёт и проектирование дисковых фрез для обработки винтовых стружечных канавок: Учебное пособие по курсовому и дипломному проектированию. – Челябинск: ЧГТУ 1993. – 31 с.
аппроксимация.cdw

Рекомендуемые чертежи
- 15.04.2024