Проектирование привода исполнительного механизма




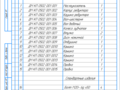
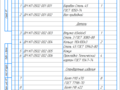
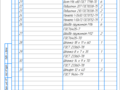
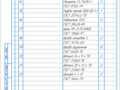
- Добавлен: 24.01.2023
- Размер: 672 KB
- Закачек: 0
Описание
Состав проекта
![]() |
![]() ![]() ![]() ![]() |
![]() ![]() ![]() ![]() |
![]() ![]() ![]() |
![]() ![]() ![]() ![]() |
![]() ![]() ![]() ![]() |
![]() ![]() ![]() ![]() |
![]() ![]() ![]() ![]() |
Дополнительная информация
Спецификация-2.2.cdw

Шайба плоская М22 ГОСТ7798-70
Шайба плоская М10 ГОСТ7798-70
Болт М10 х27 ГОСТ 7798-70
Болт М12 х70 ГОСТ 7798-70
Болт М16 х80 ГОСТ 7798-70
Подшипник 207 ГОСТ8338-75
Подшипник 210 ГОСТ8338-75
Манжета 1-35х50 ГОСТ8752-79
Манжета 1-50х72 ГОСТ8752-79
Спецификация 1.2.cdw

DM.docx
Определение срока службы привода
Определение недостающих геометрических
размеров исполнительного механизма
Определение потребной мощности и выбор
электродвигателя и редуктора
КОНСТРУИРОВАНИЕ ИСПОЛНИТЕЛЬНОГО МЕХАНИЗМА
Предварительный расчет вала и определение размеров вала ИМ
Определение диаметра вала под подшипник.
Конструирование буртика.
Подбор крышек корпуса манжетных уплотнений
Выбор смазки подшипников
Разработка посадочного места под ступицу
Проектирование приводного вала
Определение геометрических размеров вала
Расчет вала на прочность
Расчет подшипника на динамическую прочность
Расчет на прочность сварного шва
Расчёт ступеней быстроходного вала редуктора
Расчёт ступеней тихоходного вала редуктора
Крепление крышки редуктора к корпусу
Выбор смазочного материала
Заданием на курсовой проект по основам проектирования и конструирования является конструирование привода ленточного конвейера который как и любая другая машина включает в себя три основных узла: двигатель – передаточный механизм – исполнительный механизм.
В данном проекте разработке подлежит третий узел машины. В качестве мотора используется стандартный трехфазный асинхронный электродвигатель.
Передаточный механизм содержит редуктор. Исполнительным механизмом в данном проекте является приводной вал конвейера. Для ленточного конвейера – это вал приводного барабана.
В данной пояснительной записке должны быть расчеты: расчет вала на статическую прочность и на сопротивление усталости; расчет подшипников по динамической и статической грузоподъемности; расчет шпоночных соединений.
Цель предварительного расчёта привода заключается в составлении и уточнении кинематической схемы выборе основных элементов привода и проведении его кинематического и силового анализа.
1 Определение срока службы привода
Срок службы (ресурс) ч определяется формулой
где n – число лет работы привода n = 5 лет =0256; =08.
Полученное значение учитывает время на профилактические мероприятия (осмотр обслуживание) привода.
2 Определение недостающих геометрических размеров
исполнительного механизма
В качестве исполнительного механизма задан вал приводного барабана ленточного конвейера поэтому дополнительно определяются ширина ленты транспортера в миллиметрах:
Вб = В + (50 100)(1.2)
где В – ширина ленты транспортера мм (задана в исходных данных)
В = Вб – 50 = 500 – 50 = 450 мм
3 Определение потребной мощности и выбор
Номинальный момент определяется по формуле:
Расчет эквивалентного вращающего момента:
Определение угловой скорости вращения ИМ
Расчет КПД привода. Согласно кинематической схеме изображенной на рис.1 а также с учетом данных табл.4 [ ] получаем
где рем = 095 – КПД ременной передачи
ЦП = 098 – КПД цилиндрической закрытой передачи
ПП = 099 – КПД подшипниковой пары.
Рис. 1.1 Кинематическая схема привода
Расчетная мощность электродвигателя в киловаттах определяется по формуле:
Определение частоты вращения вала ИМ
Возможный диапазон общего передаточного числа кинематической схемы привода.
Uo max=U12 maxU23 max= 45=20 (1.9)
Uo min=U12 minU23 min =225=5(1.10)
Возможный диапазон асинхронной частоты вращения вала электродвигателя.
nэ max=nимUo max=7639420=152789 обмин (1.11)
nэ min=nимUo min=763945=38197 обмин. (1.12)
Определение передаточного числа привода и его разбивка по ступеням передач. В соответствии с расчетной мощностью и полученным диапазоном скоростей выбираем следующие электродвигатели:
100L41430 РТАБ=4 кВт n=20
112МВ6950 РТАБ=4 кВт n=20
132S8720 РТАБ=4 кВт n=22
Для обеспечения заданной скорости движения необходимо чтобы передаточное число привода –(в нашем случае ) принимало следующие значения:
Определяем общее передаточное число редуктора. Принимаем по табл.5 передаточное отношение ременной передачи равным 3 тогда передаточное отношение редуктора:
Выбираем из ряда передаточное отношение одноступенчатого цилиндрического редуктора
Проверяем точность разбивки передаточного числа:
Выбираем электродвигатель 132S8720 так как его погрешность меньше.
Ртаб= 4 кВт п = 22 nтаб=720 обмин
Проверку электродвигателя на перегрузку ведем по условию(12)[1]
п=22 (для выбранного электродвигателя)
а т.к. Ртаб = 4 кВт то условие выполняется т.e. двигатель не будет перегружен.
Рис. 1.2 Эскиз электродвигателя
Номинальная расчетная мощность электродвигателя
Таблица исходных данных
n3= 7619 обмин nим= 7639 обмин n =1%
T3= 4512 Hм T=450 Нм T =1%
Расхождение в скоростях и моментах 1% что допустимо (предел 5%).
1 Предварительный расчет вала и определение размеров вала ИМ
Принимаем диаметр входного конца d = 45 мм (по ГОСТ 12080-66).
Диаметр конца вала d мм
Длина конца вала (исп. 2) мм
Геометрические размеры шпонок зависят от диаметра вала в который вставляется шпонка. Тип шпонки – призматическая (ГОСТ 23360-78).
3 Определение диаметра вала под подшипник.
Рассчитываем диаметр вала под подшипник по формуле:
где t1-размер выступающей части шпонки t1=38 мм;
Принимаем диаметр вала под подшипник мм.
Подбираем подшипник по типу серии и размеру выбираем подшипник 1212 ГОСТ 28428-90.
Внутренний диаметр d мм
4 Конструирование буртика.
Рассчитываем диаметр буртика подшипника по формуле:
dбп = 60 + 3*25 = 675
принимаем dбп = 71 мм.
По найденным размерам диаметра подшипника диаметра буртика подшипника подбираем крышку и корпус.
Корпус УМ 110 ГОСТ 13218.3-80.
Рис. 2.4 Корпус УМ 110 ГОСТ 13218.3-80.
Крышка МН 110*75 ГОСТ 13219.5-81.
Рис. 2.5 Крышка МН 110*75 ГОСТ 13219.5-81.
Выбираем манжетные уплотнения: манжета 1.1-71*95-1 ГОСТ 8752-79.
Рис. 2.6 Манжета 1.1-71*95-1 ГОСТ 8752-79.
5 Выбор смазки подшипников
Пластичные смазки хорошо удерживаются в механизмах и не требуют сложных уплотнений. Вязкость смазок в гораздо меньшей степени зависит от температуры чем вязкость масел на основе которых они сделаны. Применяемая нами смазка - ЛИТОЛ 24.Смазочный материал должен занимать 12 23 свободного объёма полости корпуса.
Основными параметрами для выбора муфты являются:
диаметр конца вала ИМ
передаваемый муфтой крутящий момент
Расчетный крутящий момент
Где К – коэффициент запаса К = 15;
Тогда Тр = 154512 =6768 Нм
Рис. 2.7 Эскиз муфты МЦ
Из каталога на муфты выбираем муфту цепную МЦ 1000–50–1–1 для которой допускаемый крутящий момент [Т] = 1000 Нм
Тр = 6768 Нм [Т] = 1000 Нм
Соединительным элементом в данной муфте является цепь роликовая однорядная Пр-3175-8900:
Диаметр делительной окружности цепи:
где t – шаг цепи z – количество звеньев цепи (число зубьев полумуфты).
7 Разработка посадочного места под ступицу
Диаметр вала под ступицу берем равным 75 мм. Подбираем шпонку по диаметру вала (Шпонка 201270 ГОСТ 23360-78). Так как ВбDб то конструкция вала имеет две ступицы.
Тогда длина каждой ступицы вычисляется по формуле:
где lшп- длина шпонки
Вычисляем основные размеры барабана:
наружный диаметр ступицы
где d – диаметр вала под ступицу;
где Dб – диаметр барабана мм; В – ширина барабана
о=002(300+500)=16 мм;
(0.9 0.8) о =09·16=144 мм;
= (Dст - d)2=(120-75)2=225 мм.
Так как 1 ≤2 то 2 = =144 мм
Рис. 2.8 Эскиз барабана
8 Проектирование приводного вала
Валы – это детали которые служат для поддержания других вращающихся деталей (шкивов зубчатых колес звездочки барабана) а сами опираются на опоры (подшипники). Валы служат для передачи крутящего момента
гладкие или ступенчатые;
с прямой или ломаной осью;
сплошные или пустые.
Чаще всего валы делают из стали углеродистой конструкционной или легированной. Легированная сталь используется только с термообработкой.
Для изготовления вала используем сталь Ст45.
Рис. 2.9 Упрощённая схема приводного вала
– середина конца вала; 25 – середина левого и правого подшипников; 34 – диски барабана;
9 Определение геометрических размеров вала
Рис. 2.10 Приводной вал
Конец вала берем такой же как и у тихоходного вала редуктора l = 82 мм d = 45 мм.
Диаметр в месте посадки подшипника находим по формуле d1 = d + 5 мм. отсюда d1 = 60 мм.
Диаметр d2 определяем по справочнику в зависимости от выбранного под-шипника (d2 равен диаметру буртика подшипника). В нашем случае d2 = 55 мм.
Определяем длины ступеней вала.
L2 берем равным 60 мм.
Рассчитываем L3. От края барабана до середины подшипника взяли 70 мм от края барабана до дисков 100 мм. Отсюда L3 = 170 - Вп2 = 170 - 222 = 159 мм.
L4 составляет (05-06)Bб где Bб ширина барабана. Отсюда L4 = 275 мм.
L5 должно быть меньше ширины подшипника Вп. Вп = 22мм. Откуда принимаем L5=21мм.
1 Расчет вала на прочность
Основными нагрузками на вал являются силы от передач. Силы на вал передают через насажанные на них детали: барабан полумуфты. При расчёте принимаем что насажанные на вал детали передают силы и моменты валу на середине своей ширины. Под действием постоянных по значению и направлению сил во вращающемся вале возникают напряжения изменяющиеся по симметричному циклу.
Основными материалами для валов служат углеродистые и легированные стали. Так как жёсткость вала является определяющим параметром и для её обеспечения диаметр вала должен быть большим материалом для изготовления вала выбираем Сталь 45 прошедшую термическую обработку.
Для расчета по чертежу сборочной единицы вала составляем расчётную схему на которую наносим все внешние силы нагружающие вал. Нагрузка от муфты FМ зависит от точности сборки. Чтобы учесть все возможные неточности крепления муфты выбираем самый худший случай – когда сила от муфты помогает ломать вал. Величину FМ определим по формуле:
Fокр. – окружная сила на элементах муфты
Сила – это сила действующая со стороны конвейера на вал. Её определим из системы
где Ft – окружное усилие на барабане( задано в техническом задании )
S2 - силы натяжения ведущей и ведомой ветвей ленты
Теперь строим расчетную схему.
Находим реакции в опорах.
Рассчитываем изгибающие моменты.
По полученным результатам строим эпюры.
Находим полные напряжения.
где - напряжение изгиба; - предел выносливости; dч- диаметр вала на чертеже; dp – минимальный рассчитанный диаметр.
Условие выполняется.
2 Расчет подшипника на динамическую прочность
Строим расчетную схему. Определяем реакции в опорах.
Рис.3.2. расчетная схема для расчета подшипника.
Так как обороты вала больше 10 мин-1 расчет проводим только на динамическую нагрузку. Расчет проводим по наиболее нагруженному подшипнику.
Определяем эквивалентную динамическую нагрузку.
Fr Fa- радиальная и осевая нагрузки: Fa =0; Fr=Ra=1660 H;
X Y – коэффициенты радиальной и осевой нагрузок;
V – коэффициент вращения равен 1 т.к. вращается внутреннее кольцо подшипника;
Кб – коэффициент учитывающий характер нагрузок; для ленточного конвеера Кб =1;
Кт – температурный коэффициент равен 1;
Рассчитываем требуемый ресурс подшипника и его фактический ресурс; второй должен быть больше.
Рассчитываем требуемый ресурс подшипника в часах:
Подсчет фактического ресурса работы подшипника:
Условие выполняется подшипник пригоден для использования.
У стандартных шпонок разметы b и h подобраны так что нагрузку соединения ограничивают не напряжения среза а напряжения смятия [6]. Поэтому проводим расчет только на напряжение смятия .
Размеры сечения шпонки: h=9 мм b=14 мм .
Из выражения выражаем получаем:
Выбираем шпонку со стандартной длиной наиболее приближенной к рассчитанной: 14x9x70 ГОСТ 23360-78.
Рис.3.3 Шпонка призматическая
h – высота шпонки; b – ширина шпонки; l – длина шпонки.
4 Расчет на прочность сварного шва
Барабан делают сварным сварка ручная электродуговая электроды обыкновенного качества Э – 42.
Сталь 3 => m = 220 МПа.
где: []р – допускаемое напряжение на растяжение соединяемых деталей
S = 14..16 (запас прочности).
[]р = 220 14 = 157 МПа.
Допускаемое напряжение в швах при срезе
[ср] = 06[]р = 06 157 = 94 МПа.
Расчет напряжений среза возникающих в шве:
где: р – полярный момент сопротивления.
где: К = 3 мм (минимальный размер катета).
d1 – диаметр ступицы 60 мм.
р = 3140062000307 2 = 118710-6
ср = 158 118710-6 = 133 МПа [ср]
Рассчитать длину швов:
l1 = 2000Тн D1 07К[ср] = 2000158 30307394 = 528 мм.
D1 = Dб – 2 s = 315- 2 6 = 303 мм.
s = 6 (толщина листа).
l1 = 2000Тн D2 07К[ср] = 2000158 65607394 =244 мм.
D2 = d1 + 14 К = 60 + 143 = 656 мм.
К = 3 мм (минимальный размер катета).
Для предупреждения преждевременных выходов из строя зубчатых колес из-за поломки зубьев и разрушения их активных поверхностей в результате развития усталостного выкрашивания необходимо уделять большое внимание расчёту на контактную прочность активных поверхностей зубьев и на прочность зубьев при изгибе.
При этом расчёт на контактную прочность является основным так как он в определённой мере способствует предупреждению разрушения не только от пластических деформаций но и от воздействий других видов повреждений вызывающих отказ.
Предположим что диаметр шестерни d1 125 мм. Для её изготовления принимаем сталь Ст45 термическая обработка – улучшение. Назначаем твёрдость рабочих поверхностей зубьев шестерни H1=260 HB. Для изготовления колеса любого диаметра и любой ширины принимаем сталь Ст45 термическая обработка – нормализация. Назначаем твёрдость Н2=210НВ. Для длительно работающей передачи принимаем коэффициент долговечности ZN=1.
Пределы контактной и изгибной выносливости зубьев:
Определяем допускаемые контактные напряжения принимая для нормализованных и улучшенных зубчатых колес:
для материала шестерни
для материала колеса
Допускаемое контактное напряжение
Определяем допускаемые напряжения изгиба при расчёте на прочность принимая для колес при одностороннем приложении нагрузки и =1 при длительно работающей передаче:
для материала шестерни
Межосевое расстояние определяем из условия сопротивления контактной выносливости рабочих поверхностей зубьев
где – вспомогательный коэффициент (для косозубых колёс =495);
- номинальный вращающий момент на колесе;
– коэффициент учитывающий неравномерность распределения нагрузки по длине контактной линии =11;
- передаточное число редуктора;
– коэффициент ширины венца зубчатого колеса относительно межосевого расстояния =04.
Полученное значение межосевого расстояния округляем до ближайшего большего. Принимаем =160 мм.
Определяем ширину венца зубчатого колеса
Для компенсации неточностей установки колеса в осевом направлении ширину венца шестерни принимают на 3 5 мм больше ширины колеса
Значения и округляем до стандартных и принимаем =63 мм и =67 мм.
Определяем значения модуля для колес из условия сопротивления изгибной усталости
где - вспомогательный коэффициент для косозубых колёс=58.
Округляем до ближайшего стандартного и принимаем =25 мм.
Определяем числа зубьев.
Число зубьев шестерни
Фактическое передаточное число редуктора
Отклонение от ранее принятого стандарта
Делительные диаметры колес
Проверяем межосевое расстояние по делительным диаметрам колес
Находим диаметры вершин зубьев
Вычисляем диаметры впадин зубьев
Определяем окружную скорость в зацеплении
Принимаем 9-ю степень точности изготовления зубчатых колёс.
Силы действующие в зацеплении:
Выполняем проверочный расчёт на контактную прочность рабочих поверхностей зубьев передачи. Силы возникающие в зацеплении колес вызывают деформацию не только зубьев но и валов и опор что приводит к неравномерному распределению нагрузки вдоль контактной линии зубьев а также к динамическим нагрузкам. Такое же влияние оказывают неизбежные погрешности изготовления и монтажа деталей передачи. Для учёта влияния указанных факторов при расчётах номинальную нагрузку умножаем на коэффициент нагрузки. Предварительно находим значения коэффициентов.
Принимаем – коэффициент учитывающий неравномерность распределения нагрузки между зубьями;
5 - коэффициент учитывающий неравномерность распределения нагрузки по длине контактных линей;
- коэффициент динамичности.
Коэффициент нагрузки
Определяем расчётное контактное напряжение
где =270 – для прямозубых колёс.
Недогрузка по контактным напряжениям составляет
1 Расчёт ступеней быстроходного вала редуктора
Первая ступень под элемент открытой передачи
Вторая ступень под уплотнение крышки с отверстием и подшипник
где t=22 мм. (Принимаем в зависимости от диаметра).
Третья ступень под шестерню
Четвертая ступень под подшипник
Принимаем с=16 мм. Длину четвертого вала выбираем исходя из размеров подшипника. Для быстроходного вала выбираем радиальные шариковые однорядные подшипники легкой серии 207 ГОСТ 8338-75. Для тихоходного вала выбираем радиальные шариковые однорядные подшипники легкой серии 211 ГОСТ 8338-75.
Рис. 4.1. Эскиз подшипника шарикового однорядного сферического.
Подшипники шариковые однорядные сферические (из ГОСТ 8338-75) мм
Принимаем l4=186 мм.
2 Расчёт ступеней тихоходного вала редуктора
Первая ступень под полумуфту
Длину первой ступени принимаем стандартную. l1=82 мм.
где =28 мм. (Принимаем в зависимости от диаметра)
Принимаем d2=55 мм.
Длину второй ступени принимаем l2=45 мм.
Третья ступень под колесо
Длину третьей ступени принимаем l3=84 мм.
Принимаем с=25 мм. Длину четвертого вала выбираем исходя из размеров подшипника.
Принимаем l4=235 мм.
Для передачи крутящих моментов используем призматические шпонки так как соединения с такими шпонками обеспечивают передачу наибольшего крутящего момента. По принятым значениям диаметров концов валов определяем размеры шпоночных соединений по ГОСТ 23360-78. Выбираем:
для конца быстроходного вала: Шпонка 8х7х35 ГОСТ 23360-78;
для конца тихиходного вала: Шпонка 14х9х70 ГОСТ 23360-78;
под колесо: Шпонка 18х11х60 ГОСТ 23360-78.
Рис. 2.1. Эскиз шпонки призматической.
t – глубина паза в вале;
t1 – глубина паза в ступице;
Длина шпонки: Lш=L-10=82-10=72 мм.
Из стандартного ряда длину шпонки принимаем: Lш=70 мм.
3 Крепление крышки редуктора к корпусу
Для соединения крышки с корпусом используем винты с цилиндрической головкой с шестигранным углублением “под ключ”. Диаметр винтов крепления принимаем в зависимости от вращающего момента на выходном валу редуктора.
Высоту прилива в крышке под стягивающий винт принимаем h=9 мм.
Отверстия в подшипниковом гнезде для установки подшипников должны иметь правильную цилиндрическую форму. При сборке редуктора во время затяжки винтов соединяющих корпус с крышкой возможно некоторое смещение крышки относительно корпуса что вызовет деформирование наружных колец подшипников имеющих малую жесткость. Кроме того торцы приливов у подшипниковых гнезд на крышке редуктора и корпусе могут не совпасть что повлечёт перекос крышек подшипников и наружных колец самих подшипников. Следовательно при сборке редуктора нужно точно фиксировать положение крышки относительно корпуса. Для достижения необходимой точности фиксирования применяем штифты. Диаметр штифтов
Кроме фиксирования штифты предохраняют крышку и корпус от сдвига при растачивании подшипниковых отверстий.
Опорную поверхность корпуса выполняем в виде нескольких небольших платиков расположенных в местах установки болтов. Такое расположение снижает расход металла и уменьшает время обработки опорной поверхности корпуса снижает нагрузки на резьбовые детали.
Диаметр винта крепления редуктора к плите
Число винтов принимаем в зависимости от межосевого расстояния.
Места крепления корпуса к плите оформляем в виде ниш расположенных по углам корпуса.
Для заливки масла в редуктор контроля правильности зацепления и для внешнего осмотра деталей делают люки. Чтобы удобнее было заливать масло и наблюдать за зубчатыми колесами люк должен быть как можно больших размеров. Исходя из этого принимаем люк 200х100. Толщину крышки люка принимаем =6 мм.
Для того чтобы внутрь корпуса извне не засасывалась пыль под крышку ставим уплотняющую прокладку из прокладочного картона А толщиной 15 мм. Крышку крепим четырьмя винтами. Диаметры винтов
где - толщина крышки корпуса.
Совокупность устройств обеспечивающих подачу смазочного материала к поверхностям трения а так же его возврат в масляной бак или другую ёмкость называют смазочной системой.
Так как окружная скорость мс то используем картерный способ смазки то есть смазывание погружением зубьев колёс в масло залитое в картер редуктора. Уровень масла в картере редуктора должен обеспечивать погружение венца колеса на глубину до двух высот зубьев но не менее 10 мм.
Для наблюдения за уровнем масла в картере редуктора предусматриваем жезловый маслоуказатель.
Во время работы повышается давление внутри редуктора в связи с нагревом воздуха и масла. Это приводит к выбрасыванию масляного тумана из корпуса через уплотнения и стыки. Чтобы избежать этого в смотровом люке предусматриваем отдушину.
При работе передачи масло постепенно загрязняется продуктами износа. С течением времени оно стареет свойства его ухудшаются. Поэтому масло налитое в корпус редуктора периодически меняют. Отработанное масло нужно слить таким образом чтобы не производить разборку механизма привода. Для этой цели в нижней части корпуса редуктора предусматриваем сливное отверстие закрываемое пробкой.
Внутреннюю поверхность дна корпуса делают с уклоном а у сливного отверстия предусматривается местное углубление. При таком исполнении масло почти без остатка может быть слито из корпуса.
5 Выбор смазочного материала
Выбор смазочных масел для передачи редуктора производим по кинематической вязкости которая характеризует сопротивление отдельных слоев жидкости относительному сдвигу.
Для повышения стойкости зубьев против заедания желательно применять масла высокой вязкости. Однако это связано с заметным увеличением потерь на перемешивание масла. Поэтому вязкость масла выбираем в зависимости от окружной скорости нагрузки и материала зубьев. Вязкость смазочного материала
где - рекомендуемая кинематическая вязкость смазочного материала при температуре 50°;
- средняя окружная скорость;
=170 мм2с для стальных передач.
Выбираем масло марки ИРП-75.
Объем масляной ванны принимают таким чтобы обеспечить отвод выделяющейся в зацеплении теплоты к стенкам корпуса. В данном случае объем масляной ванны принимаем таким образом чтобы на 1 кВт передаваемой мощности приходилось 035 07 л масла. Так как передаваемая мощность составляет порядка 4 кВт то объем ванны можно взять в пределах от 14 до 28 л. Принимаем 2 литра.
При выполнении курсового проекта был рассчитан привода ленточного конвейера от электродвигателя марки АИР с использованием цилиндрического редуктора и ременной передачи. В предварительном расчёте привода был выбран двигатель и определены крутящие моменты на валах. На основе этого был рассчитан вал исполнительного механизма. Также был спроектирован одноступенчатый цилиндрический редуктор определены характеристики его работы. Проведены проверочные расчёты подтверждающие работоспособность выбранных элементов привода.
Анурьев В.И. Справочник конструктора-машиностроителя: В 3 т. Т. 1. –8-е изд. перераб. и доп. Под ред. И. Н. Жестковой. – М.: Машиностроение 2001. – 920 с.: ил.
Дунаев П.Ф.Конструирование узлов и деталей машин: учеб. пособие для техн. спец. вузов. – 7-е изд. испр. – М.: Высш. шк. 2001. – 447 с.: ил.
Основы конструирования деталей и сборочных единиц машин: учеб. пособие В.Н.Бельков Н.В.Захарова. – Омск: Изд-во ОмГТУ 2007. – 256с.
Предварительный расчёт привода: методические указания. Омск: Изд-во ОмГТУ 2005. – 44 с.
Приводы конвейеров с гибким тяговым элементом: учеб. пособие В.П.Добровольский. – Омск: Изд-во ОмГТУ 2009. - 112 с.
Проектирование приводного вала конвейера: методические указания. Омск: Изд-во ОмГТУ 2006. – 25 с.
Чернилевский Д.В. Детали машин. Проектирование приводов технологического оборудования: учебное пособие для студентов вузов. 3-е изд. исправл. – М.: Машиностроение 2004. – 560 с. ил.
Лист 2 .cdw

Вращающий момент на ведомом валу Т
Частота вращения ведомого вала n
Передаточное число U = 4
Технические требования
Внутреннюю стенку корпуса и крышки покрасить
маслостойкой краской
снаружи серой нитразмалью.
Перед окончательной сборкой стыки фланцев
корпуса покрыть пастой "Герметик".
литра масла марки ИРП-75.
Лист 1 .cdw

Техническая характеристика:
Вращающий момент на валу барабана 315 Hм.
Частота вращения вала барабана 121
ехнические требования:
Подшипники качения посадить на вал нагрев их в масле
Корпуса подшипников заполнить на 23 объема
внутренней полости смазкой литол 24 (ГОСТ 1631-61).
После сборки проверить вал на легкость вращения в опорах.
Вращение должно быть свободным без толчков и остановок.
кроме опорных поверхностей корпусов и посадочного
отверстия в муфте окрасить в 2 слоя нитраэмалью
(ГОСТ 9825-73) в красный цвет по грунту.
Спецификация-2.1.cdw

Спецификация 1.1.cdw

Сталь 45 ГОСТ 13940-80
Прокладка Технический
ДМ КП 0502 000 000СБ
Рекомендуемые чертежи
- 09.11.2023
- 25.10.2022