Проектирование механизмов автомата для резьбонарезания гаек (М8+М16). Вариант №26



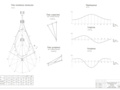
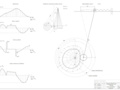
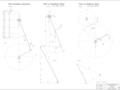
- Добавлен: 24.01.2023
- Размер: 772 KB
- Закачек: 0
Описание
Состав проекта
![]() |
![]() |
![]() ![]() ![]() |
![]() ![]() ![]() ![]() |
![]() |
![]() |
![]() ![]() ![]() ![]() |
![]() ![]() ![]() ![]() |
![]() ![]() ![]() |
Дополнительная информация
TEMP.doc
*********************** Исходные данные ************************
Длина кривошипа L= 0035 м
Начальный угол поворота кривошипа FIO= -90000 (град.)
способ сборки = 1 Х=00000 Y=00000
звено присоединения =0 ХF=15708YF=00000
L1 = 00840;тета1 = 000;L2 = 00000;тета2 = 000
***********************************************************************
В программе приняты следующие обозначения:
AJ - точка А j-ой группы BJ - точка B j-ой группы
FJ - угол FI1 j-ой группы PJ - угол FI2 j-ой группы
V и W - символы аналога скорости и ускорения таким образом:
VXA1 - проекция аналога скорости точки A1 1-ой группы на ось Х
MU1 и MU2 - углы передачи
*********************** Расчетные данные ************************
Векторные кинематические параметры получены в виде проекций на оси координат
Все угловые кинематические характеристики получены в градусах !
Точка M 11 : № группы =1 № звена = 1 ХM= 0042 YM= 0000
XM 1 1 000000 000875 001515 001750 001515 000875 000000 -000875 -001516 -001750 -001516 -000875
YM 1 1 000700 001077 002167 003818 005667 007139 007700 007139 005667 003818 002167 001077
VXM 1 1 001750 001516 000875 000000 -000875 -001516 -001750 -001516 -000875 000000 000875 001516
VYM 1 1 000000 001427 002692 003500 003370 002073 000000 -002073 -003370 -003500 -002692 -001427
WXM 1 1 000000 -000875 -001516 -001750 -001516 -000875 000000 000875 001516 001750 001516 000875
WYM 1 1 002771 002633 002112 000802 -001388 -003429 -004229 -003429 -001388 000802 002112 002633
FI 1 2700 3000 3300 00 300 600 900 1200 1500 1800 2100 2400
XA 1 000000 001750 003031 003500 003031 001750 000000 -001750 -003031 -003500 -003031 -001750
YA 1 -003500 -003031 -001750 000000 001750 003031 003500 003031 001750 000000 -001750 -003031
VXA 1 003500 003031 001750 000000 -001750 -003031 -003500 -003031 -001750 000000 001750 003031
VYA 1 000000 001750 003031 003500 003031 001750 000000 -001750 -003031 -003500 -003031 -001750
WXA 1 000000 -001750 -003031 -003500 -003031 -001750 000000 001750 003031 003500 003031 001750
WYA 1 003500 003031 001750 000000 -001750 -003031 -003500 -003031 -001750 000000 001750 003031
XB 1 000000 000000 000000 000000 000000 000000 000000 000000 000000 000000 000000 000000
YB 1 004900 005185 006084 007636 009584 011247 011900 011247 009584 007636 006084 005185
VXB 1 000000 000000 000000 000000 000000 000000 000000 000000 000000 000000 000000 000000
VYB 1 000000 001104 002354 003500 003708 002396 000000 -002396 -003708 -003500 -002354 -001104
WXB 1 000000 000000 000000 000000 000000 000000 000000 000000 000000 000000 000000 000000
WYB 1 002042 002235 002473 001604 -001027 -003827 -004958 -003827 -001027 001604 002473 002235
F 1 900 1020 1112 1146 1112 1020 900 780 688 654 688 780
VF 1 041667 036893 022338 000000 -022338 -036893 -041667 -036893 -022338 000000 022338 036893
WF 1 000000 -018402 -036759 -045835 -036759 -018402 000000 018402 036759 045835 036759 018402
MU 1 00 120 212 246 212 120 00 3480 3388 3354 3388 3480
Fmax= 011900 Fmin= 004900
Силовой анализ.dwg

План положений механизма
План сил входного звена
(для 5 положения механизма)
Механизм автомата для
резьбонарезания гаек
Кинематический анализ.dwg

(для 5 положения механизма)
Механизм автомата для
резьбонарезания гаек
Кулачок.dwg

Профилирование кулочка
профиль действительный
График изменения угла давления
Механизм автомата для
резьбонарезания гаек
Пояснительная записка по ТММ.doc
Государственное образовательное учреждение высшего профессионального
Образования «Уральский государственный технический университет – УПИ
имени первого Президента России Б.Н. Ельцина»
Факультет: общего специального машиностроения
Кафедра: «Прикладная механика»
Члены комиссии: Филимонов И. Е.
Механизм автомата для резьбонарезания гаек (М8+М16)
Пояснительная записка
Руководитель: Филимонов И. Е.
Задание на курсовое проектирование 4
Анализ зубчатого механизма 8
Проектирование планетарной передачи 15
Синтез и анализ кулачкового механизма 17
Синтез и кинематический анализ кривошипно-ползунного механизма 23
Силовой расчет кривошипно-ползунного механизма 28
Список литературы 30
В данном курсовом проекте я буду разбирать работу механизмов автомата для резьбонарезания гаек. Рассмотрю принцип действия. Разберусь в необходимости использования кулачкового и кривошипно-ползунного механизмов. Проведя расчеты я установлю может ли такой механизм работать. Такая машина применяется в массово серийном производстве чтобы упростить работу человека. Она полностью автоматизирована проста в изготовлении и не требует особого ухода.
ПРОЕКТИРОВАНИЕ И ИССЛЕДОВАНИЕ МЕХАНИЗМОВ АВТОМАТА ДЛЯ РЕЗЬБОНАРЕЗАНИЯ ГАЕК (М8+М16)
Нарезание резьбы в гайках производится Г-образным вращающимся метчиком8 вложенным в специальную головку 9 закрепляемую на шпинделе 15 (рис.26—1). Заготовки гаек поступают в рабочую зону нарезания по трубке 2 куда подаются посредством кривошипно-ползунного (шиберного) механизма (звенья 1 2 5). При движении шибера 3 вверх (рабочий ход) заготовки забираются его верхней гранью из бункера 10. Ползун 4 при своем рабочем движении (влево) сначала подводит очередную заготовку к метчику 8 с переменной скоростью (рис.26—2а участок 0-4-6) а затем перемещает ее в том же направлении с vрез = сonst на всем участке нарезания резьбы (рис.26—2а участок 6-13). Одновременно ползун 4 принадлежащий рычажно-кулачковому механизму (звенья 4 5 6 7 где кулачок 7 является ведущим при рабочем ходе механизма) запирает зону нарезания от последующей заготовки. После нарезания ползун 4 быстро отводится вправо (рис.26—2а участок 14-19-24) под действием силы Р4 пружины.16. Нарезанные гайки передвигаются вдоль тела метчика к его концу 8 с которого они сбрасываются. Кинематическая цепь привода автомата состоит из электродвигателя 12 редуктора 13 двух зубчатых цилиндрических передач (Z4 Z5) (Z6 Z7) и передачи конической (Z8 Z9).
Цикловые характеристики сил сопротивления (PС3 S3) и знакопеременных сил пружины 16 (P4S4) приложенных соответственно к звеньям 3 и 4 рис.26—1б и рис. 26-1в. Причем на графике (P4S4) совмещена осевая сила Pос действующая на метчик при рабочем ходе в начале врезания метчика 8 в заготовку. На рис.26—2б отмечена фаза действия силы Pос в виде угла ос.
На pиc.26—2в дана цикловая схема работы основных механизмов автомата. Закон изменения момента сопротивления ( МС77) на метчике 8 (при нарезании резьбы) приведенного к кулачковому валу 07 представлен на рис.26-2б. При проектировании коромыслово-ползунного механизма (звенья 6 5 4) необходимо обеспечить заданный закон изменения скорости ползуна 4 (рис.26—2а). Маховик 14 следует посадить на коленвал 1 выбранный звеном приведения.
Примечание. Перед началом динамического исследования механизмов необходимо для разметки положений точек D4 и D5 на их траекториях найти график изменения (SD4 7) путем графического интегрирования заданного графика (vD4 7) этот материал расположить на листе проекта "Проектирование кулачкового механизма".
Рис. 26-1. Механизм автомата для нарезания гаек.
Рис. 26—2. Цикловая схема.
Наименование параметра
Числовые значения для вариантов
Средняя скорость шибера 3
Отношение длины шатуна 2 к длине кривошипа 1
Передаточное отношение звеньев 1 и 7
Максимальный угловой ход звена 6
Максимальный ход звена 4
Соотношение плеч коромысла 6
Скорость звена 4 на участке нарезания резьбы
Число оборотов шпинделя 15
Сила сопротивления при подъеме шибера 3
Сила сопротивления при опускании шибера 3
Отношение сил Pmax и Pmin
Осевая сила в начале нарезания гаек
Момент сопротивления на метчике приведенный к звену 7
Момент инерции звена 2
Момент инерции зубчатых колес z5 и z6
Момент инерции коленвала 1 и колеса z8
Маховой момент ротора электродвигателя
Маховой момент шпинделя 15 и головки 9
Коэффициент неравномерности вращения вала 1
Передаточное отношение зубчатых колес z6 и z7
Максимально допустимый угол давления в кулачковом механизме
Число сателлитов в редукторе 13
Модуль зубчатых колес z6 и z7
Анализ зубчатого механизма
- угол главного профиля
- коэффициент высоты головки зуба
Выбор коэффициентов смещения:
Делительные диаметры:
Делительное межосевое расстояние:
Межосевое расстояние:
Передаточное число:
Начальные диаметры:
Коэффициент воспринимаемого смещения:
Коэффициент уравнительного смещения:
Диаметры вершин зубьев:
Окружной делительный шаг: (мм)
Окружные делительные толщины зубьев:
Начальные окружные толщины зубьев:
Угол профиля зуба на окружности вершин:
Окружные толщины зубьев по вершинам:
Коэффициенты толщины зубьев по окружности вершин:
Радиусы кривизны эвольвенты на вершине зуба:
Длина линии зацепления:
Длина активной линии зацепления:
Коэффициент перекрытия:
Радиус кривизны эвольвенты в нижней точке активного профиля:
Радиус кривизны эвольвенты в граничной точке эвольвенты:
Вычисление профиля зубьев
Рассчитаем предварительную толщину зубьев по ряду окружностей. Зададимся для этого последовательным рядом значений в пределах и рассчитаем по формуле
Расчетная формула для нахождения ширины зуба:
где Sy – толщина зуба по данной окружности мм; dy – диаметр окружности по которой вычисляется толщина зуба мм; S – толщина зуба по делительной окружности зубчатого колеса мм; d – делительный диаметр зубчатого колеса мм; db – диаметр основной окружности зубчатого колеса мм.
Для примера когда dy=45 мм; S=5.37 мм; d=42 мм; db=39.47 мм; α=200:
Результаты расчетов приведены в таблице 1 для шестерни z6 и в таблице 2 для колеса z7.
Вычисление коэффициентов удельных скольжений для шестерни и колеса
Удельные скольжения λ1 и λ2 характеризуют изнашивание активных профилей зубьев.
Длина линии зацепления: .
Плавность работы зубчатой передачи характеризуется коэффициентом перекрытия - отношением угла перекрытия зубчатого колеса к его угловому шагу. В нашем случае .
Это означает что 36.5% времени контакта колес в зацеплении будут участвовать две пары зубьев и 63.5% времени — одна.
Удельные скольжения и характеризуют изнашивания активных профилей зубьев.
где— радиус кривизны эвольвенты шестерни в точке контакта k ;
— радиус кривизны эвольвенты колеса в этой же точке;
Для примера когда g=25.99 мм U=2 ρk1=283 мм:
вычисление коэффициента удельных скольжений для колеса :
Для примера когда g=25.99 мм U=2 ρk1=2.83 мм:
Результаты расчетов коэффициентов удельных скольжений для шестерни и колеса приведены в табл3
Определение скорости скольжения в зацеплении
Величину скорости скольжения в зацеплении можно определить по формуле:
где VS – скорость скольжения в зацеплении ммс; PP1– длина отрезка мм; Z6 – угловая скорость шестерни радс; Z7 – угловая скорость колеса радс.
Зная угловую скорость шестерни и передаточное число найдем угловую скорость колеса:
Подставив в исходное уравнение вычисленные значения угловых скоростей а также измерив на чертеже длину отрезка PP1=0.0057 м; PP2=0.0064 м получим:
Вычисление ширины шестерни
Ширину шестерни можно определить по формуле:
где – коэффициент ширины шестерни =03 - 05
аw =64.65 (мм)– межосевое расстояние
Масштабные коэффициенты
Масштабный коэффициент для построения зубчатого зацепления профиля зубьев а также для изображения зоны двухпарного зацепления:
Масштабный коэффициент для построения графика скорости скольжения в зацеплении:
Масштабный коэффициент для построения графика коэффициентов удельных скольжений:
Проектирование планетарной передачи
Подберем числа зубьев колес для планетарной передачи которая должна обеспечить передаточное отношение при одновременном выполнении условий соосности сборки соседства и отсутствии интерференции при числе сателлитов .
Чтобы не было подрезания ножки зуба центрального колеса число его зубьев .
Предварительно принимаем .
Увеличим значение количества зубьев в два раза для того чтобы исключить подрезание ножек зубьев ().
Условие сборки передачи
k – число сателлитов.
получаем целое число т.е. передача собирается без натягов.
Анализ кулачкового механизма
Выбираем закон движения выходного звена если:
Максимальный ход звена 4 H4=85 мм максимальный угловой ход звена 6 соотношение плеч коромысла .Закон движения выходного звена при удалении разбит на два закона – косинусоидальный и линейный при возвращении – косинусоидальный. Кулачек вращается по часовой стрелки допустимый угол давления =40о.
Рассчитаем перемещение Si и значения на графиках аналога скорости Si’ и ускорения Si’’ по соответствующим выбранным законам (формулам).
Найдем максимальное перемещение толкателя h:
По теореме косинусов: (мм)
Составляем закон движения кулачка:
Строим графики по полученным данным.
Масштабные коэффициенты:
Определяем минимальный радиус кулачкового механизма.
Строим для этого новый график на оси ординат которого откладываем ход бокового ползуна а по оси абсцисс в обе стороны значения скорости соответствующие перемещению в данный момент. Но строим все в одном масштабном коэффициенте Кs. К получившемуся графику проводим касательные под углом γmin=500. Расстояние между центром координат и точкой пересечения этих касательных и будет минимальный радиус кулачка. В нижнем треугольнике (ниже точки пересечения касательных) от оси ординат откладываем эксцентриситет по оси абсцисс. Расстояние между получившейся точкой и центром координат будет радиус Rо с которого мы и начнем построение кулачка. Он будет определять на некотором промежутке центровой профиль.
Сроим диаграмму изменения угла передачи при помощи построенного графика для определения минимального радиуса кулачка.
Действительный профиль кулачка: найдем как эквидистантную кривую отстоящую от центрового профиля на расстоянии равном радиусу ролика.
Радиус ролика выбираем наименьший из условия
Rрол≤0.4*Rо=0.4*50=20 мм
Не будем брать большой ролик.
Окончательно принимаем Rрол=20 мм
При профилировании кулачка все строим в одном масштабном коэффициенте:
К=(действительный радиус Rо)(значение радиуса Rо на чертеже)=5050=1 мммм
Проверка профиля кулачка для фазы удаления.
Центровой профиль кулачка.
Действительный профиль кулачка.
Проверка профиля кулачка на фазе возвращения.
Определение жесткости замыкающей пружины.
Синтез и кинематический анализ кривошипно-шиберного механизма
При предварительном кинематическом расчете получен механизм с неудовлетворительными данными. Поэтому уменьшаем число оборотов коленвала.
Определим основные размеры звеньев:
Определим длину шатуна:
- коэффициент изменения средней скорости выходного звена.
е=0 – эксцентриситет.
Определим длину кривошипа:
Построение плана положений механизма
Определим скорость точек кривошипа к которой присоединена группа Асура типа ВВП.
Построим 12 положений механизма с масштабным коэффициентом
Определим скоростей точек и угловых скоростей звеньев методом плана.
(мс) – скорость точки А кривошипа направлена перпендикулярно кривошипу в сторону его вращения. Построим ее из полюса скоростей Pv и определим масштабный коэффициент.
Составим два векторных уравнения связывающих скорость точки А с известными скоростями.
Направление вектора относительной скорости проводится из конца вектора перпендикулярно шатуну.
Относительная скорость является в данном случае абсолютной скоростью точки А и проводится из полюса скоростей вдоль оси oy до пересечения с направлением скорости .
Измерим и рассчитаем действительные значения полученных скоростей.
Определение ускорений точек и угловых ускорений звеньев.
Ускорение точки А направленно вдоль кривошипа к центру вращения. Построим его из полюса ускорений Ра и определим масштабный коэффициент Ка.
Составим векторное уравнение связывающие ускорения точки А с известными ускорениями.
(мс2) – нормальная составляющая ускорения точки В шатуна относительно точки А направлена вдоль шатуна к точке А.
тангенсальная составляющая ускорения точки В направлена перпендикулярна шатуну. направлена вдоль оси оу до пересечения с .
Данные ТММ ANALYZER:
*********************** Исходные данные ************************
Длина кривошипа L= 0035 м
Начальный угол поворота кривошипа FIO= -90000 (град.)
способ сборки = 1 Х=00000 Y=00000
звено присоединения =0 ХF=15708YF=00000
L1 = 00840;тета1 = 000;L2 = 00000;тета2 = 000
***********************************************************************
В программе приняты следующие обозначения:
AJ - точка А j-ой группы BJ - точка B j-ой группы
FJ - угол FI1 j-ой группы PJ - угол FI2 j-ой группы
V и W - символы аналога скорости и ускорения таким образом:
VXA1 - проекция аналога скорости точки A1 1-ой группы на ось Х
MU1 и MU2 - углы передачи
*********************** Расчетные данные ************************
Векторные кинематические параметры получены в виде проекций на оси координат
Все угловые кинематические характеристики получены в градусах !
Точка M 11 : № группы =1 № звена = 1 ХM= 0042 YM= 0000
XM 1 1 000000 000875 001515 001750 001515 000875 000000 -000875 -001516 -001750 -001516 -000875
YM 1 1 000700 001077 002167 003818 005667 007139 007700 007139 005667 003818 002167 001077
VXM 1 1 001750 001516 000875 000000 -000875 -001516 -001750 -001516 -000875 000000 000875 001516
VYM 1 1 000000 001427 002692 003500 003370 002073 000000 -002073 -003370 -003500 -002692 -001427
WXM 1 1 000000 -000875 -001516 -001750 -001516 -000875 000000 000875 001516 001750 001516 000875
WYM 1 1 002771 002633 002112 000802 -001388 -003429 -004229 -003429 -001388 000802 002112 002633
FI 1 2700 3000 3300 00 300 600 900 1200 1500 1800 2100 2400
XA 1 000000 001750 003031 003500 003031 001750 000000 -001750 -003031 -003500 -003031 -001750
YA 1 -003500 -003031 -001750 000000 001750 003031 003500 003031 001750 000000 -001750 -003031
VXA 1 003500 003031 001750 000000 -001750 -003031 -003500 -003031 -001750 000000 001750 003031
VYA 1 000000 001750 003031 003500 003031 001750 000000 -001750 -003031 -003500 -003031 -001750
WXA 1 000000 -001750 -003031 -003500 -003031 -001750 000000 001750 003031 003500 003031 001750
WYA 1 003500 003031 001750 000000 -001750 -003031 -003500 -003031 -001750 000000 001750 003031
XB 1 000000 000000 000000 000000 000000 000000 000000 000000 000000 000000 000000 000000
YB 1 004900 005185 006084 007636 009584 011247 011900 011247 009584 007636 006084 005185
VXB 1 000000 000000 000000 000000 000000 000000 000000 000000 000000 000000 000000 000000
VYB 1 000000 001104 002354 003500 003708 002396 000000 -002396 -003708 -003500 -002354 -001104
WXB 1 000000 000000 000000 000000 000000 000000 000000 000000 000000 000000 000000 000000
WYB 1 002042 002235 002473 001604 -001027 -003827 -004958 -003827 -001027 001604 002473 002235
F 1 900 1020 1112 1146 1112 1020 900 780 688 654 688 780
VF 1 041667 036893 022338 000000 -022338 -036893 -041667 -036893 -022338 000000 022338 036893
WF 1 000000 -018402 -036759 -045835 -036759 -018402 000000 018402 036759 045835 036759 018402
MU 1 00 120 212 246 212 120 00 3480 3388 3354 3388 3480
Fmax= 011900 Fmin= 004900
Программа рассчитывает аналоги скоростей ускорений угловых скоростей и угловых ускорений. Для определения действительных значений скоростей соответствующую величину необходимо умножить на .
Определим действительные значения скоростей и ускорений точки В и S2 а также угловой скорости и ускорения шатуна АВ для пятого положения механизма (расчетного положения).
Определим погрешности измерений двумя методами по формуле:
n – значение параметра определенное по плану; а – значение параметра определенное аналитически.
Данные занесем в таблицу на листе.
Силовой расчет кривошипно-ползунного механизма
Силовой анализ выходного звена:
Определяем массы звеньев:
Технологическая нагрузка:
(Н) – сила тяжести кривошипа.
(Нм) – момент сил инерции.
Составляем векторную сумму сил:
Определим неизвестные силы методом плана сил.
Построим силу N01 и определим масштабный коэффициент:
Каждую следующую силу откладываем из конца предыдущей. Построим план сил для шатуна кривошипа и поршня. Из планов сил находим не известные нам силы.
Силовой анализ входного звена:
мм - плечо силы до шарнира О.
мм – радиус основной окружности зубчатого колеса.
Составим векторную сумму сил:
Анурьев В.И. Справочник конструктора-машиностроителя в 3 т.Анурьев В.И. – М.: Машиностроение 2001.
Артоболевский И.И «Теория механизмов и машин» – М.: Наука 1975.
Девойно Г.Н. «Курсовое проектирование по теории механизмов и машин» - Минск В.Школа 1986.
Дунаев П.Ф. Конструирование узлов и деталей машин: учеб. пособие для студ. высш. учеб. заведенийДунаев П.Ф. Леликов О.П. – 9-е изд. перераб. и доп. – М.: «Академия» 2006.
С.А.Попов Г.А.Тимофеев «Курсовое проектирование по ТММ» Москва «Высшая школа» 2004г.
Справочник технолога-машиностроителя в 2-х т. под ред. А.Г. Косиловой и Р.К. Мещерякова. – 4-е изд. перераб. и доп. – М.: Машиностроение 1986.
Рекомендуемые чертежи
- 24.01.2023
- 10.08.2016
- 25.10.2022