Проектирование долбёжного станка



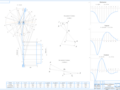
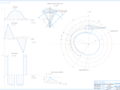
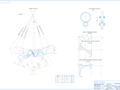
- Добавлен: 24.01.2023
- Размер: 612 KB
- Закачек: 0
Узнать, как скачать этот материал
Подписаться на ежедневные обновления каталога:
Описание
Проектирование долбёжного станка
Состав проекта
![]() |
![]() ![]() ![]() |
![]() ![]() ![]() ![]() |
![]() ![]() |
![]() ![]() ![]() ![]() |
![]() ![]() ![]() ![]() |
Дополнительная информация
Контент чертежей
111111.cdw

Сега2.3.cdw

2й ЛИСТ.cdw

Рекомендуемые чертежи
- 10.08.2016
Свободное скачивание на сегодня
Обновление через: 12 часов 49 минут