Проектирование автомобильного двигателя ВАЗ 2109



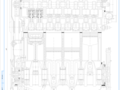
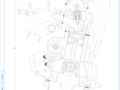
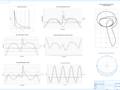
- Добавлен: 25.01.2023
- Размер: 5 MB
- Закачек: 0
Описание
Состав проекта
![]() |
![]() |
![]() |
![]() ![]() ![]() ![]() |
![]() ![]() ![]() ![]() |
![]() ![]() ![]() ![]() |
![]() ![]() ![]() |
Дополнительная информация
Продольный разрез.cdw

Поперечный разрез.cdw

Графики.cdw

Пояснительная записка.doc
1. Обоснование исходных данных 3
2. Тепловой расчет 5
3. Анализ вычисленных параметров 12
1 Кинематика кривошипно-шатунного механизма 15
2.деталей кривошипно-шатунного механизма 17
3. Силы действующие в К.Ш.М. 18
4. Уравновешивание двигателя 22
Расчет основных деталей двигателя
1. Расчет поршневой группы 24
2. Расчет шатунной группы 28
3. Расчет коленчатого вала 34
4. Расчет механизма газораспределения 40
Расчет систем двигателя
1. Система смазывания 44
2. Система охлаждения 45
3. Система питания 46
4. Система пуска. 46
Список литературы 53
Техническое задание на проектирование
Цель разработки и область применения
Спроектировать четырёхтактный четырех цилиндровый бензиновый двигатель с жидкостным охлаждением мощностью Ne = 555 кВт при частоте вращения коленчатого вала n = 5800 мин-1. Двигатель предназначен для установки на легковой автомобиль с улучшенными технико-экономическими показателями.
1. Обоснование исходных данных
Проектируемый двигатель предназначен для установки на легковой автомобиль ВАЗ-2109 и его модификаций.
Номинальная мощность и частота вращения на проектируемом двигателе принимается Ne= 555 кВт и n = 5800 мин1. Отношение SD=095. Отношение радиусу кривошипа к длины шатуна rl=0277.
1.1. Атмосферное давление принимаем P0 = 010 МПа. Температура окружающей среды принимается T0 ≥ 298 K.
1.2. Степень сжатия - отношение полного объема цилиндра к объёму камеры сгорания:
1.3. Коэффициент избытка воздуха - отношение действительного количества воздуха поступившего в цилиндр к количеству воздуха необходимого для полного сгорания 1 кг топлива. Принимаем = 096
1.4. Механический КПД - оценивает механические потери в двигателе. Для бензинового
m = [070 090]. Принимаем m = 0787.
1.5. Подогрев свежего заряда при наполнении цилиндра зависит от скорости вращения коленчатого вала с уменьшением скорости вращение увеличивается приращением температуры и от испарения топлива в процессе смесеобразовании температура свежего заряда уменьшается. Для двигателей с жидкостным охлаждением приращение температуры свежего заряда. Принимаем ΔT = 5°.
1.6. Температура остаточных газов T2 лежит в пределах [900 1100] К. Принимаем T2 = 1000 К.
1.7. Коэффициент сопротивления впускной системы для бензинового двигателя лежит в пределах [0.80 0.90] принимаем Pc P0=087.
Коэффициент вп зависит от сопротивления впускного клапана от наличия изгибов изменений площади поперечного сечения и шероховатости поверхности впускного трубопровода.
1.8. Коэффициент сопротивления выпускной системы; где Pr - давление остаточных газов. Он учитывает потери при выпуске отработавших газов. Для бензиновых двигателей вып = [1.02 1.2]. Принимаем вып =116.
1.9. Коэффициент дозарядки - показывает изменение количества рабочего тела при запаздывании закрытия впускного клапана. Он равен отношению количества свежего заряда находившегося в цилиндре в момент закрытия впускного клапана к тому его количеству которое находится в цилиндре в момент прохождения поршнем НМТ в конце такта впуска. Принимаем φ = 10.
1.10. Коэффициент полноты индикаторной диаграммы учитывает уменьшение теоретического среднего индикаторного давления из-за отличия действительного процесса от расчетного. А именно:
- скругление диаграммы в точке "с" из-за воспламенения смеси до ВМТ;
- в точке "z" из-за разницы конечных скоростей сгорания Pz = 085
- в точке "в" из-за открытия выпускного клапана до того момента когда поршень будет в НМТ φп = [094 097]. Принимаем φп = 096.
2.1. Параметры окружающей среды принимаются в соответствии с ГОСТами.
2.2. Выбираем топливо для двигателя:
2.3. Теоретически необходимое количество воздуха для сгорания топлива:
2.4. Выбор коэффициента избытка воздуха:
На бензиновых двигателях внутреннего сгорания с карбюратором коэффициент избытка воздуха находиться в пределах 08-098. С целью получения приемлемой экономичности и снижения в отработавших газах содержания оксидов азота примем
2.5. Количество свежего заряда:
принимаем молекулярную массу паров топлива
2.6. Давление в конце впуска учитывая отсутствие карбюратора принимаем
2.7. Выбор степени сжатия:
В соответствии с выбранным топливом бензин Аи-92 применением на двигателе жидкостного охлаждения принимаем
2.8. Величина подогрева свежего заряда:
С учетом жидкостного охлаждения принимаем
2.9. Параметры остаточных газов:
Так как на двигателе предусмотрен глушитель учитывая заданную частоту вращения коленчатого вала принимаем коэффициент сопротивления выпускной системы
Температуру остаточных газов принимаем по среднему значению
Коэффициент остаточных газов
так как двигатель без наддува то принимаем и и отношение их теплоемкостей
2.10. Количество рабочей смеси подсчитываются по уравнению:
2.11. Температура рабочей смеси для двигателей без наддува:
2.12. Коэффициент наполнения для двигателей без наддува определяется по уравнению:
2.13. Давление и температуру в конце сжатия вычислим по уравнениям:
С учетом жидкостного охлаждения закрытого типа средней частоты вращения коленчатого вала и испарения бензина принимаем
2.14. Расчет параметров процесса сгорания:
Так как то сгорание будет неполным и продукты сгорания будут включать следующие компоненты:
Количество оксида углерода:
Коэффициент К принимаем равным 05.
Количество водорода:
Количество диоксида углерода:
Количество водяного пара:
Общее количество продуктов сгорания:
Объёмные доли компонентов в продуктах сгорания:
Коэффициенты молекулярного изменения:
Температуру продуктов сгорания в конце сгорания определим по уравнению:
Коэффициент использования теплоты с учетом карбюратора принимаем
Низшая теплота сгорания топлива:
Количество теплоты потерянной вследствие химической неполноты сгорания бензина при :
Температура в конце сжатия:
Мольную теплоемкость воздуха при постоянном объеме в конце сжатия определим методом интерполирования:
Мольную теплоемкость остаточных газов при определим интерполированием по температуре и коэффициенту избытку воздуха при:
Аналогично интерполированием определяется теплоемкость при :
Значение постоянных известных величин в уравнении баланса энергии:
Для определения значения теплоемкостей продуктов сгорания представим в виде формул:
Расчетное давление в конце сгорания:
Действительное максимальное давление в конце сгорания:
Степень повышения давления:
2.15. Расчет параметров расширения:
Средний показатель политропы расширения принимаем по значению показателя адиабаты с учетом поправки:
Показатель адиабаты расширения определим по номограмме.
Проверим правильность принятия и при расчете .
Параметры и приняты правильно.
2.16. Определение индикаторных показателей цикла:
Расчетное среднее индикаторное давление:
Принимаем коэффициент полноты диаграммы
Действительное среднее индикаторное давление:
Индикаторный К.П.Д. при и
Удельный индикаторный расход топлива:
2.17. Расчет эффективных показателей:
С учетом заданной частоты вращения коленчатого вала принимаем среднюю скорость поршня Предварительно приняв отношение хода поршня к диаметру цилиндра определяем среднее давление механических потерь.
Механический К.П.Д.:
Средне эффективное давление:
Удельный расход топлива:
2.18. Определение размеров цилиндра и показатели двигателя:
С учетом частоты вращения и желанием улучшить протекание процессов сгорания топлива примем отношение
Предварительно принимаем .
Средняя скорость поршня:
Окончательно принимаем и
Рабочий объём цилиндра:
Номинальная мощность:
Часовой расход топлива:
Эффективный крутящий момент:
2.19. Построение индикаторной диаграммы:
Объём камеры сгорания:
Полный объём цилиндра:
Давления для построения политроп вычисляем по уравнениям:
Таблица 1 – Давление в цилиндре
Рис.1. Индикаторная диаграмма
3. Анализ вычисленных параметров
3.1. Коэффициент остаточных газов - определяет качество очистки цилиндра от продуктов сгорания характеризуется отношением количества молей остаточных газов Мr к количеству молей свежего заряда М поступившего в цилиндр на такте впуска:
В расчете получено γr = 0054.
Величина γr зависит от степени сжатия: чем больше тем меньше γост.
3.2. Коэффициент наполнения - отношение количества свежего заряда поступившего в цилиндр двигателя к тому его количеству которое могло бы поступить в цилиндр при давлении и температуре заряда перед впускными органами. Для бензиновых двигателей v=[07 09]. В расчете получили v = 0819.
3.3. Давление в начале сжатия.
В расчете получили Pa = 0087 МПа. На Pa влияют вп и ΔT.
3.4. Температура в начале сжатия.
Ta = 339К. Свежий заряд в цилиндре двигателя в начале сжатия подогревается. Для бензиновых двигателей Ta находится в пределах [320 370]К.
3.5. Показатель политропы сжатия.
n1 - характеризует степень теплообмена между рабочим телом и стенками цилиндра.
Величина n1 устанавливается опытным путем в зависимости от частоты вращения коленчатого вала степени сжатия размеров цилиндра теплообмена и других факторов. B расчете получили n1 =136.Для бензиновых двигателей величина n1 находится в пределах[134 137].
3.6. Температура и давление заряда в конце сжатия.
Зависит от степени сжатия и определяется из уравнения политропы с постоянным показателем n1: Pс = Pa · Tс = Ta · n-1.
Из расчета Pс = 1675 МПа; Tс = 742 K
3.7. Максимальное давление цикла Pz.
Pz находится в пределах [30 65] МПа. Из расчета Tz = 2731 К.
3.8. Показатель политропы расширения.
n2 - характеризует степень теплообмена между рабочим телом и стенками цилиндра в процессе расширения.
В двигателях с наддувом с увеличением степени повышения давления в нагнетателе продолжительность догорания топлива возрастает и значение n2 уменьшается. С ростом нагрузки и увеличением основных размеров цилиндра n2 уменьшается. В расчете получено n2 = 1248. Для бензиновых n2 = [120 13]. Давление и температура конца расширения Pв = 0430 МПа Тв = 1593 К.
3.9. Индикаторные показатели.
Среднее индикаторное давление - условное постоянное избыточное давление при котором работа газов за один ход поршня равна индикаторной работе за цикл. Среднее индикаторное давление представляет собой индикаторную работу за цикл приходящуюся на единицу рабочего объема.
Для бензинового двигателя Pi = [04 14] МПа. В расчете получено Pi =10405 МПа.
Индикаторный КПД - отношение теплоты преобразованной в индикаторную работу ко всей теплоте подведенной в двигатель с топливом:
i = = [025 04]. В расчете получили i = 0361.
3.10. Эффективные показатели.
Среднее эффективное давление - часть среднего индикаторного давления соответствующая работе затраченной на привод потребителей мощности двигателя Pе = Pi – Pм. Из расчета получено Pе = 08185 МПа.
Эффективная мощность - мощность отдаваемая двигателем потребителю. Из расчета Nе = 4512 кВт.
Удельный эффективный расход топлива - количество топлива в граммах израсходованного двигателем при определенном значении эффективной мощности за один час работы. Для карбюраторных двигателей
gе = [260 340] гкВт·ч. В расчете gе = 2910 гкВт·ч.
Эффективный КПД - отношение теплоты эквивалентной эффективной работе ко всей теплоте подводящей в двигатель с топливом e =[025 033]. В расчете получено e = 0281.
1. Кинематика поршня
1.1. Полное перемещение поршня вычисляется по формуле:
Полное перемещение представляет собой сумму перемещений первого
и второго порядка: где
1.2. Полная скорость поршня вычисляется по формуле:
Полная скорость представляет собой сумму скоростей первого и
второго порядка: где
1.3. Полное ускорение вычисляется по формуле:
Полное ускорение представляет собой сумму ускорений первого и
1.4. Обоснование исходных данных для кинематического расчета.
Угловую скорость вращения коленчатого вала определим по формуле:
Кинематический расчет приводился при помощи программы Microsoft Excel. Данные расчета представлены в приложении 1. Графики изображены на рисунках 234.
Рис.2. Полное перемещение поршня
Рис.3. Полная скорость поршня
Рис.4. Полное ускорение поршня
2.деталей кривошипно-шатунного механизма 3.2.1. поршневого комплекта и части шатуна отнесенной к оси поршневого пальца:
Массы деталей КШМ приведены из расчётов программы DINA Алтайского государственного технического университета.
Общая масса поршневой группы Мп = 0417 кг.
Общая масса шатунной группы Мш = 0726 кг.
Поступательно движущаяся масса шатуна Мшп = 0200 кг.
Приведенная к оси шатунной шейки
неуравновешенная масса кривошипа (без противовесов) Mк = 0794 кг.
Приведение масс деталей шатунной группы:
Зная длину шатуна определяем длину от оси нижней головки шатуна до центра тяжести из соотношения:
Длина от оси верхней головки шатуна до центра тяжести:
Заменим массу шатуна на две эквивалентные массы сосредоточенные на концах шатуна. Тогда масса шатуна:
Найдем эквивалентные массы из системы соотношений:
Рис.5. Эквивалентная схема КШМ:
Вычисляем поступательно и вращательно движущиеся массы:
кг – поступательно движущиеся массы;
кг – вращательно движущиеся массы.
3. Силы действующие в КШМ
3.1. Сила давления на поршень (газовая сила):
Силы давления газов в цилиндре двигателя
в зависимости от хода поршня определяются
из индикаторной диаграммы построенной
по данным теплового расчёта.
Рис.6. Схема сил действующих на
кривошипно-шатунный механизм
3.2. Сила инерции возвратно-поступательно движущихся масс:
Pj = - mп.к r2(cos φ+ λcos2 φ)
r – радиус кривошипа;
– угловая скорость коленчатого вала;
– отношение радиуса кривошипа к длине шатуна.
Эти силы действуют по оси цилиндра и так же как силы давления газов считаются положительными если они направлены к коленчатому валу и отрицательными если они направлены от коленчатого вала.
3.3. Суммарная сила:
Складывая алгебраические силы действующие в направлении оси цилиндра получим суммарную силу
3.4. Центробежная сила инерции вращающихся масс действующая по радиусу кривошипа и направленная от оси коленчатого вала:
3.5. Нормальная сила действует перпендикулярно оси цилиндра:
- угол отклонения шатуна от оси цилиндра.
Нормальная сила считается положительной если создаваемый ее момент относительно оси коленчатого вала направлен противоположно направлению вращения вала двигателя.
3.6. Сила действующая вдоль шатуна:
Силу S можно разложить на две составляющие:
- нормальную силу К направленную по радиусу кривошипа: ;
-тангенциальную силу Т действующую перпендикулярно кривошипу: .
Строим графики зависимости Рг Рj Р КТ N S от угла поворота коленчатого вала двигателя на номинальном режиме.
В результате динамического расчета получены данные для одного цилиндра (Приложение 2). Интервалы между вспышками в четырёх цилиндровом четырехтактном двигателе:
3.7 Набегающие моменты на коренные и шатунные шейки на режиме Neном. Приведены в таблицах 2 и 3.
3.8 Силы действующие на шатунную шейку.
На шатунную шейку кривошипа действуют: тангенциальная сила T нормальная сила K и центробежная сила Krш=m2r2 возникающая вследствие вращения (в расчетах принимается с постоянной угловой скоростью) части массы шатуна приведенной к оси шатунной щеки.
Следовательно результирующая сила Rшш действующая на шатунную шейку определяется как векторная сумма:
Геометрическое место конца вектора силы Rшш для различных значений угла φ представляет полярную диаграмму этой силы ориентированную относительно продольной вертикальной оси неподвижного кривошипа вращение которого заменяется условно вращением цилиндра ( или всего двигателя) в сторону противоположную вращению коленчатого вала с угловой скоростью . В этом случае силы K и Krш всегда направлены вертикально а Т – горизонтально.
Выберем в прямоугольной системе координат вертикальную ось К с положительным направление сверху вниз горизонтальную Т с положительным направлением слева направо.
Так как сила сама представляет собой вектор суммы двух взаимно перпендикулярных векторов сил К и Т то для построения полярной диаграммы сил Rшш первоначально строят полярную диаграмму силы S откладывая в прямоугольных координатах значения слагаемых К и Т для различных углов φ и получая. Таким образом. Соответствующие точки конца вектора S.
Для получения полярной диаграммы результирующей силы Rшш достаточно в полученной диаграмме силы S полюс О переместить по вертикали на величину вектора Krш в точку Ош что равносильно геометрическому сложению по формуле Krш при принятом нами допущении что =const постоянная и всегда направлена по радиусу кривошипа. Мы тем самым превратим построенную полярную диаграмму сил S в полярную диаграмму нагрузок на шатунную шейку (сил Rшш) с полюсом в точке Ош.
Рис.7. Схема построения полярной диаграммы нагрузки на шатунную шейку.
Результаты сил действующих в КШМ вынесены и значения Rшш для лучей диаграммы износа вынесены в Приложение 3.
4. Уравновешивание двигателя
Двигатель рядный четырёх цилиндровый угол между кривошипами составляет 180° . Порядок работы 1-3-4-2.
В уравновешенном двигателе при установившемся режиме работы силы и моменты сил передаваемые на его опоры постоянны по величине и направлению или равны нулю.
Уравновешивание можно осуществить двумя способами:
)расположение определенным образом цилиндров и выбором такой кривошипной системы коленчатого вала чтобы переменные силы инерции и их моменты взаимно уравновешивались;
)созданием с помощью дополнительных масс (противовесов) новых сил в любой момент времени равных по величине но противоположных по направлению основным уравновешиваемым силам.
Динамический расчёт показывает что на КШМ действуют:
- силы инерции поступательно движущихся масс и
- центробежные силы инерции
- возникают моменты .
Все эти силы и моменты вызывают неуравновешенность двигателя.
Силы инерции первого порядка и их моменты при указанном расположении кривошипов взаимно уравновешиваются:
Силы инерции второго порядка для всех цилиндров равны и направлены в одну сторону. Их равнодействующая:
Силы инерции второго порядка можно уравновесить лишь с помощью дополнительных валов. Суммарный момент этих сил равен нулю:
Центробежные силы инерции для всех цилиндров равны и направлены попарно в разные стороны. Равнодействующая этих сил и момент равны нулю:
Расчет на прочность основных деталей двигателя
1. Расчет поршневой группы
На основании данных теплового и динамического расчета имеем:
Диаметр цилиндра D=78 мм;
Площадь поршня Fп= 04776 дм2;
Действительное максимальное давление сгорания PZ=555 МПа;
Наибольшую нормальную силу N=176 кН;
Масса поршневой группы
В соответствии с существующими двигателями и с учетом рекомендуемых соотношений принимаем:
H=54 мм; hю=16 мм; hГ=20 мм; б=75 мм; s=125 мм; t=3 мм; t=05 мм;
hn= 4 мм; nm=1 мм; b=29 мм; материал поршня – алюминиевый сплав ; материал цилиндра – чугун .
Напряжения изгиба в днище поршня
поэтому днище поршня должно быть усиленно рёбрами жёсткости.
Напряжение сжатия в сечении х-х
Напряжения разрыва в сечении х-х:
максимальная угловая скорость холостого хода
масса головки поршня с кольцами расположенными выше сечения х-х:
максимальная разрывающая сила
Напряжения в верхней кольцевой перемычке:
Удельное давление поршня на стенку цилиндра:
Диаметры головки и юбки поршня:
Диаметральные зазоры в горячем состоянии
где приняты с учетом жидкостного охлаждения двигателя.
1.2. Расчет поршневого кольца
Поршневые кольца служат для уплотнения надпоршневого пространства отвода тепла от поршня в стенки цилиндра регулирования несущего масляного слоя. Поршневые кольца работают в условиях высоких температур и значительных нагрузок. Рассчитывают верхнее компрессионное кольцо как наиболее нагруженное.
В проектируемом двигателе кольца изготовлены из серого чугуна
Рис.9. Эпюра давлений поршневого кольца
Среднее давление кольца на стенку цилиндра
Напряжение изгиба кольца в рабочем состоянии
Напряжение изгиба при надевании кольца на поршень
Монтажный зазор в замке поршневого кольца
где - зазор в горячем состоянии.
1.3. Расчет поршневого пальца
Во время работы двигателя палец подвергается воздействию переменных нагрузок приводящих к возникновению напряжений изгиба среза и овализации.
В соответствии с указанными условиями работы к материалам применяемых для изготовления пальцев предъявляются требования высокой прочности и вязкости.
Этим требованиям удовлетворяют малоуглеродистые и легированные стали с цементируемым поверхностным слоем.
В проектируемом двигателе применяют сталь 12ХН3А имеющая
Рис.10. Эпюра напряжений
Расчетная газовая сила действующая на поршень
к – коэффициент учитывающий массу пальца.
Удельное давление пальца на втулку поршневой головки шатуна
Удельное давление пальца на бобышки
Напряжения изгиба в среднем сечении пальца
Касательные напряжения в сечениях между бобышками и головкой шатуна
В проектируемом двигателе палец запрессован в поршневую головку поэтому он не подвержен овализации.
2. Расчет шатунной группы
Геометрические размеры Ш.Г.
d1=21 мм; dшш=46 мм; tв=15 мм;
Lш=134 мм; Lб=63 мм;
hш=27 мм; bш=19 мм; аш=5 мм; tш=5 мм.
При работе двигателя шатун подвергается действию знакопеременных газовых инерционных нагрузок а в отдельных случаях эти силы создают и ударные нагрузки.
Поэтому шатуны изготавливают из углеродистых или легированных сталей обладающих высоким сопротивлением усталости.
Рис.11. Расчетная схема шатуна
В проектируемом двигателе шатун изготовлен из стали 45 имеющей
Для повышения усталостной прочности шатун после штамповки необходимо подвергнуть дробеструйной обработке нормализации закалке и отпуску.
2.1. Поршневая головка шатуна
Натяг от запрессовки пальца
Модули упругости пальца и шатуна
Коэффициент Пуассона Найдем радиальное давление натяга на поверхности соприкосновения пальца с головкой:
Напряжения от натяга на внешней и внутренней поверхностях поршневой головки определяются по формуле Ляме:
Принимается что рассчитываемая на прочность часть головки как брус малой кривизны защемленный в местах перехода проушины в стержень что соответствует центральному углу. В соответствии с расчетной схемой принимается что нижняя часть головки опирающаяся на стержень большой жесткости не деформируется а действие отброшенной правой части головки заменяется нормальной силой и изгибающим моментом.
Рис.12. Эпюра напряжений в верхней головке шатуна
Суммарная сила растягивающая головку достигает максимального значения в В.М.Т.
Средний радиус головки
Нормальная сила и момент заменяющая отброшенную часть головки шатуна
Из эпюры напряжений и из практических наблюдений известно что наибольшее напряжение в поршневой головке при нагружении возникает на её поверхности при угле равном углу заделки и при растяжении и при сжатии. Найдем напряжения
- коэффициент показывающий какая часть нагрузки приходиться на поршневой палец где
площади сечения поршневой головки и поршневого пальца.
- высота поршневой головки шатуна
Рис.13. Эпюра сжимающих напряжений
Суммарная сила сжимающая головку достигает максимального значения после В.М.Т. 10 – 20 угла П.К.В.:
Нормальная сила и изгибающий момент заменяющие отброшенную часть головки при сжатии:
определены по справочным таблицам.
Суммарные напряжения взывающие в сечении А-А газовыми и инерционными силами и запрессованной втулкой изменяются по ассиметричному циклу а минимальным запасом прочности будет обладать наружное волокно для которого:
2.2. Расчет кривошипной головки шатуна
Точный расчет кривошипной головки весьма затруднен из-за невозможности учета всех конструктивных факторов. Приближенный расчет сводится к определению напряжения в среднем сечении С-С (рис.11) крышки головки от инерционных сил.
Максимальная сила инерции
Момент сопротивления расчетного сечения
- внутренний радиус кривошипной головки.
Моменты инерции вкладыша и крышки
Напряжение изгиба крышки и вкладыша
2.3. Расчет стержня шатуна
Стержень шатуна рассчитывают на усталостную прочность в среднем сечении В-В (рис.11) от действия знакопеременных суммарных сил возникающих при работе двигателя. Запас прочности сечения определяется в плоскости качания шатуна и в перпендикулярной плоскости.
Условием равнопрочности стержня шатуна в обеих плоскостях является .
Из динамического расчета
Момент инерции сечения В-В относительно оси х-х
Момент инерции относительно оси у-у
Площадь среднего сечения шатуна
Длина стержня шатуна между поршневой и кривошипной головкой
Минимальное напряжение возникающие в сечении В-В от растягивающей силы определяется в плоскости качания шатуна в перпендикулярной плоскости:
От сжимающей силы в сечении В-В возникают максимальные напряжения сжатия и продольного изгиба:
в плоскости качания шатуна
в плоскости перпендикулярной плоскости качания
Среднее напряжения и амплитуды цикла:
Запасы прочности в сечении В-В определяются по пределу усталости:
2.4. Расчет шатунного болта
В проектируемом двигателе болты стягивающие половинки кривошипной головки шатуна подвергаются растяжению от действия сил инерции поступательно движущихся масс поршня и шатуна и вращающихся масс расположенных над плоскостью разъёма кривошипной головки. Кроме того болты испытывают растяжение от предварительной затяжки.
Шатунные болты должны обладать высокой механической прочностью и надёжностью. В проектируемом двигателе они изготовлены из стали 40ХНМА
При работе двигателя силы инерции стремятся разорвать болты. В связи с этим они должны быть затянуты настолько чтобы не была нарушена плотность соединения при действии этой силы.
Так как разрывает два болта то один болт будет воспринимать нагрузку равную
Найдем силу предварительной затяжки
- коэффициент запаса надёжности стыка;
- коэффициент основной нагрузки резьбового соединения.
Суммарная сила растягивающая болт:
Максимальные и минимальные напряжения возникающие в болте определяем в сечении по внутреннему диаметру резьбы:
где мм –номинальный диаметр болта; - шаг резьбы.
- площадь сечения болта.
Среднее напряжение и амплитуда цикла:
3. Расчет коленчатого вала
Коленчатый вал – наиболее сложная в конструктивном отношении и наиболее напряженная деталь двигателя воспринимающая периодические нагрузки от сил давления газов сил инерции и их моментов. Действие этих сил и моментов приводит к возникновению в материале вала значительных напряжений скручивания изгиба и растяжения-сжатия. Кроме того периодические изменяющиеся моменты вызывают крутильные колебания вала которые создают дополнительные напряжения кручения.
Таким образом из-за исключительно сложных и тяжелых условий работы вала предъявляются высокие и разнообразные требования к механическим свойствам материалов применяемых для изготовления валов. Материал должен обладать высокой прочностью и вязкостью большой сопротивляемостью износу и усталостным напряжениям сопротивлением действию ударных нагрузок и твердостью. Такими свойствами обладают правильно обработанные углеродистые и легированные стали а также высококачественный чугун. Коленчатый валы отечественных автомобилей и тракторных двигателей изготовляют из сталей 40 45 45Г2 50 специального чугуна а для форсированных двигателей из высоколегированных сталей 18ХНВА
ХНМА. В проектируемом двигателе применяют сталь 40Х имеющей:
Сложная форма коленчатого вала многообразие действующих на него сил и моментов характер изменения которых зависит от жёсткости вала и его опор а также ряд других причин не позволяют провести точный расчет на прочность. В связи с этим используют различные приближённые метода расчета позволяющие получить условные напряжения и запасы прочности в отдельных элементах коленчатого вала. Общепринятой расчетной схемой коленчатого вала является схема разрезной двухопорной балки с одним с пролётом между опорами (рис.14).
При расчете коленчатого вала принимается что:
- кривошип свободно лежит на опорах;
- опоры и точки приложения сил проходят через средние плоскости шеек;
- весь пролёт между опорами представляет собой абсолютно жёсткую
Рис.14. Расчетная схема
3.1. Расчёт коренной шейки
Коренные шейки рассчитывают только на кручение. Максимальные и минимальные значения скручивающих моментов определяют с помощью таблиц набегающих моментов последовательно подходящих к отдельным коренным шейкам.
Таблица 2 – Набегающие моменты на коренные шейки
Найдем наиболее нагруженную коренную шейку.
Наиболее нагруженная пятая коренная шейка
Осевой момент сопротивления шейки кручению:
Максимальное и минимальное касательное напряжения переменного цикла:
Среднее значение и амплитуда напряжений:
Запас прочности коренной шейки по пределу усталости:
Крутильные колебания учитываем коэффициентом . Так как двигатель
четырёхцилиндровый рядный то .
Запас прочности с учетом крутильных колебаний:
3.2. Расчет шатунных шеек
Шатунные шейки рассчитывают на кручение и изгиб. Скручивание шейки происходит под действием набегающего момента а изгиб под действием изгибающих моментов в плоскости кривошипа и в перпендикулярной плоскости. Так как максимальные значения скручивающего и изгибающих моментов не совпадают по времени запасы прочности шейки от кручения и изгиба определяют независимо друг от друга а затем их суммируют определяя общий запас прочности.
Таблица 3 – Набегающие моменты на шатунные шейки
Найдем наиболее нагруженную шатунную шейку.
Наиболее нагруженная четвертая коренная шейка
Момент сопротивления кручения шатунной шейки
Так как наибольшие напряжения возникают у краёв масляного отверстия то определяем изгибающий момент действующий в плоскости оси масляного отверстия:
В проектируемом двигателе
Максимальное и минимальное значение определяем на основе динамического расчета путем выявления и :
Момент сопротивления шейки изгибу определим по формуле:
По полученным значения определим экстремальные значения напряжений изгиба в шатунной шейки:
Среднее напряжение и амплитуда напряжений:
Общий запас прочности шатунной шейки:
Щёки коленчатого вала воспринимают сложные переменные напряжения: касательные от кручения и нормальные от изгиба и растяжения сжатия. Наибольшие напряжения возникают в местах перехода шейки в щеку в галтелях. Максимальный и минимальный момент скручивающий щеку:
Максимальные и минимальные касательные напряжения знакопеременного цикла щеки:
Запас прочности щеки от касательных напряжений по пределу усталости:
Максимальное и минимальное нормальное напряжение щеки:
Запас прочности щеки от нормальных напряжений:
Суммарный запас прочности:
4. Расчет механизма газораспределения
Для газообмена в существующих автомобильных и тракторных двигателях применяются клапанные механизмы. При конструировании М.Г.Р. необходимо стремиться к максимально возможным удовлетворению двух противоположных требований:
- получению максимальных проходных сечений обеспечивающих хорошее наполнение и очистку цилиндров;
- сокращению до минимума массы подвешенных деталей газораспределения для уменьшения инерционных нагрузок.
Расчёт кулачка выполнен с помощью программы «Расчет безударного профиля кулачка»
Выбор и расчет сходных данных.
Угол предварительного открытия впускного клапана п.к.в. до В.М.Т. угол запаздывания закрытия выпускного клапана п.к.в. после Н.М.Т.
Угол участка сбега принимаем равным 200 п.р.в.
Продолжительность впуска .
Так как кулачек симметричный то угол Рис.15. Диаграмма фаз
положительных ускорение на участке подъёма и на участке опускания клапана равны между собой и равны:
Диаметр горловины определяем при условии неразрывности потока несжимаемого газа по условной средней скорости при максимальном подъёме клапана на режиме номинального числа оборотов:
Рис.16. Расчётная схема клапана
где - средняя скорость поршня; ; - число впускных клапанов.
Максимальный ход клапана:
- угол фаски клапана.
Радиус начальной окружности
где - диаметр начальной окружности.
4.2. Расчет пружины клапана
Пружина клапана должна быть обеспечивать при всех скоростных режимах двигателя:
Плотную посадку клапана в седле и удержании его в закрытом состоянии в течении всего периода движения рокера по начальной окружности.
постоянную кинематическую связь между клапаном рокером и кулачком во время движения клапана с отрицательным ускорением.
По статистическим данным аналогичных клапанных механизмов
- масса М.Г.Р. приведенная к оси клапана и отнесенная к площади горловины. Найдем :
Сила инерции приведенная к оси клапана при движении толкателя с отрицательными ускорениями:
- минимальное ускорение (приложение 4).
Максимальная сила упругости пружины:
где -коэффициент запаса.
Материал пружины – пружинная сталь
Приминаем - коэффициент учитывающий наличие среза и касательных напряжений.
Найдем диаметр пружинной проволоки
Рис.17. Расчетная схема пружины
Отношения диаметров:
Момент от силы упругости пружины скручивающей пружину:
Момент сопротивления кручению сечения пружинной проволоки:
Максимальные и минимальные напряжения:
Средние напряжения и амплитуды напряжений:
Найдем число витков пружины:
Максимальная деформация пружины
- рабочее число витков
Полное число витков .
Проверка пружины на резонанс
Пружина рассматривается как прямой брус имеющий те же параметры по габаритам и массе.
4.3. Расчёт распределительного вала
Распределительный вал изготовляют из углеродистых или легированных сталей и легированных чугунов. При работе двигателя на распределительный вал со стороны клапанного привода действуют: сила упругости пружин сила инерции деталей клапанного механизма и сила давления газов приведённая к толкателю.
Материал – легированный чугун
Упругая сила пружины:
при п.р.в. когда ускорение максимально
- давление в конце расширения.
Условно принимается что .
Напряжение смятия возникающие в местах контакта рабочих поверхностей кулачка и толкателя:
1. Система смазывания
Масляная система обеспечивает смазку деталей двигателя с целью уменьшения трения предотвращения коррозии удаления продуктов износа и частичное охлаждение его отдельных узлов. В зависимости от типа и конструкции двигателей применяют систему смазки разбрызгиванием под давлением комбинированную. Проектируемый двигатель имеет комбинированную систему смазывания. Одним из основных элементов системы смазки является масляный насос.
Масляный насос служит для подачи масла к трущимся поверхностям движущихся частей двигателя. В проектируемом двигателе установлен шестерёнчатый насос. Он отличается простотой конструкции компактностью надёжностью в работе.
1.1. Расчет масляного насоса
Расчёт насоса заключается в определении размеров его шестерён исходя из расчётного циркуляционного расхода масла в системе.
Количество тепла выделяемое топливом за 1с:
По данным теплового расчета
Количество отводимого маслом от двигателя тепла:
Циркуляционный расход масла:
-средняя теплоёмкость масла;
- температура нагрева масла в двигателе.
Для стабилизации давления масла в системе двигателя циркуляционный расход масла увеличивается в 2 раза:
В связи с утечкой масла через торцовые и радиальные зазоры насоса расчётную производительность его определяем с учётом объёмного коэффициента подачи
Рассчитываем геометрические размеры шестерён:
Частота вращения насоса:
- окружная скорость вращения шестерни на внешнем диаметре
- диаметр внешней окружности шестерни;
- модуль зацепления
число зубьев зацепления
При расчёте насоса принимают что объём зуба шестерни равен объёму впадины между зубьями.
- диаметр начальной окружности шестерни;
Тогда расчетная производительность насоса будет равна:
откуда зуба будет равна:
Мощность затрачиваемая на привод масляного насоса:
-рабочее давление масла в системе;
- механический К.П.Д. масляного насоса.
2. Система охлаждения
Охлаждение двигателя применяется в целях принудительного отвода тепла от нагретых деталей для обеспечения оптимального теплового состояния двигателя и его нормальной работы. В зависимости от рода используемого теплоносителя в автомобильных и тракторных двигателях применяют систему жидкостного и воздушного охлаждения каждая из которых имеет свои преимущества и недостатки.
В проектируемом двигателе с учетом особенности условий его эксплуатации применяют жидкостную систему охлаждения. Основным элементом системы охлаждения является жидкостный насос (помпа). Он служит для обеспечения непрерывной циркуляции жидкости по системе охлаждения.
Расчет системы сводиться к определению основных размеров помпы поверхности радиатора и подбору вентилятора.
Для осуществления рабочего цикла двигателя внутреннего сгорания нужна горючая смесь – смесь топлива с окислителем. В результате сгорания горючей смеси скрытая химическая энергия топлива переходит в тепловую а затем в механическую которая и приводит в движение автомобиль или трактор.
Проектируемый двигатель – двигатель с внешним смесеобразованием и воспламенением смеси от постороннего источника. В таких двигателях используют легкоиспаряемое топливо а горючую смесь как правило приготовляют за пределами основного рабочего объёма двигателя в специальном приборе – карбюраторе.
Карбюратор – основной прибор системы питания проектируемого двигателя. Он имеет ряд систем и устройств обеспечивающих выполнение требований предъявляемых к системе питания:
Главную дозирующею систему с корректировкой подачи топлива обеспечивающую получение заданных составов смеси на всех эксплуатационных режимах работы двигателя.
Систему холостого хода для обеспечения устойчивой работы двигателя на малых нагрузках.
Систему обогащения смеси при переходе к максимальным нагрузкам для получения максимальной мощности.
Устройства обеспечивающие хорошую приёмистость двигателя.
Приспособления и устройства обеспечивающие надежный пуск двигателя
Дополнительные устройства обеспечивающие надежность и стабильность работы карбюратора.
При проведении расчетов карбюратора как правило ограничиваются расчетом элементов главной дозирующей системы определяя основные размеры диффузора и жиклеров.
Для пуска проектируемого двигателя применяется электростартерная система пуска. На двигатель устанавливается стартер СТ-221 питающейся от аккумуляторной батареи 6СТ-55П номинальной ёмкостью и напряжением 55 Ач и 12 В соответственно.
Перемещение скорость и ускорение поршня
Список используемой литературы
Двигатели внутреннего сгорания. Теория рабочих процессов поршневых и комбинированных двигателей Орлин А.С. Алексеев В.П. Ивин В.И. Под ред. проф. Орлина А.С.-М.: Машиностроение 1970.
Расчет автомобильных и тракторных двигателейКолчин А.И.
Демидов В.П.-М.: Высшая шкала 1980.
Кинематика и динамика кривошипно-шатунного механизма поршневых
поршневых двигателей Гоц А.Н.-Владимир: ВлГУ 2005.
Проектирование автотракторных двигателей Зейнеидинов Р.А.
Дьяков И.Ф. Ярыгин С.В.-Ульяновск: УгТУ 2004.
Федеральное агентство по образованию
Владимирский государственный Университет
Кафедра «Двигатели внутреннего сгорания»