Проект установки ЭЛОУ-АВТ




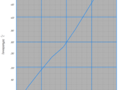
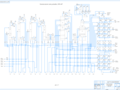
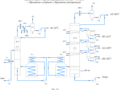
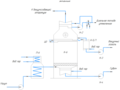
- Добавлен: 25.01.2023
- Размер: 847 KB
- Закачек: 1
- ВКонтакте
- РћРТвЂВВВВВВВВнокласснРСвЂВВВВВВВВРєРСвЂВВВВВВВВ
- Telegram
Описание
Состав проекта
![]() |
![]() |
![]() ![]() ![]() |
![]() ![]() ![]() |
![]() |
![]() |
![]() |
![]() ![]() ![]() ![]() |
![]() |
![]() ![]() ![]() ![]() |
![]() ![]() ![]() ![]() |
![]() |
![]() ![]() ![]() ![]() |
![]() ![]() ![]() ![]() |
![]() ![]() ![]() ![]() |
![]() |
![]() |
![]() ![]() ![]() ![]() |
![]() ![]() ![]() ![]() |
![]() ![]() ![]() ![]() |
![]() ![]() ![]() ![]() |
Дополнительная информация
Кусовая ЧАСТЬ 2.doc
Углеводородный газ. Газ входящий в состав данной нефти состоит в основном из бутанов (739 % мас.) выход газов на нефть составляет 15 % мас. Пропан - бутановая фракция будет использована в качестве сырья газофракционирующих установок с целью производства индивидуальных углеводородов топлива и компонента автомобильного бензина.
Фракция НК-62°С будет использована как сырьё для процесса каталитической изомеризации с целью повышения октанового числа.
Фракция 62-85°С. Данную фракцию называют “бензольной” будет использоваться как компонент товарного бензина и для получения бензола.
Фракция 85-120°С в смеси с фракцией 120-180°С будет использована как сырье для установки каталитического риформинга с целью повышения октанового числа. Предварительно отправляется на гидроочистку.
Фракция 120-180°С будет использована в смеси с фракцией 180-230°С как компонент реактивного топлива. Реактивное топливо не подходит по температуре вспышки поэтому нужно удалить часть лёгких компонентов.
Характеристика нефтяных фракций и реактивных топлив
Реактивные топлива марок
- при 15°С в пределах
Фракционный состав °С
- температура начала перегонки
- 10% отгоняется при температуре
- 50% отгоняется при температуре
- 90% отгоняется при температуре
- 98% отгоняется при температуре
- температура конца кипения
Не нормируется. Определение обязательно.
Кинематическая вязкость мм2с:
Низшая теплота сгорания кДжкг
Продолжение таблицы 2.1
Высота некоптящего пламени
Кислотность мг КОН100см3
Йодное число г I2100г топлива
Температура вспышки °С
Содержание ароматических
углеводородов % мас. (об.)
Содержание общей серы % мас.
Содержание меркаптановой серы% мас.
Фактические смолы мг100г
Часть фракции 180-230°С в смеси с фракцией 230-350°С будут использоваться в качестве компонента летнего дизельного топлива. Отправляется на установку гидроочистки.
Характеристика нефтяных фракций и дизельных топлив
Дизельные топлива марок
Цетановое число не менее
Дизельный индекс не менее
- 96% отгоняется при температуре
Температура застывания °С
Температура помутнения °С
Температура вспышки °С:
Содержание серы % мас.
Фракция 350-500 °С вакуумный газойль с содержание серы 164% мас. и коксуемостью 009% мас. Направляем на установку каталитического крекинга или гидрокрекинга с целью увлечения выработки светлых нефтепродуктов.
Фракция выкипающая при температурах выше 500оС (гудрон). Гудрон используется как сырье установок термического крекинга висбрекинга коксования и производства битума.
ВЫБОР И ОБОСНОВАНИЕ СХЕМЫ ЭЛОУ-АВТ
Установка ЭЛОУ-АВТ является комбинированной и включает в себя блок ЭЛОУ атмосферный блок блок стабилизации вторичной перегонки бензина и блок вакуумной перегонки мазута с вакуумосоздающей аппаратурой.
1 Выбор и обоснование схемы блока ЭЛОУ
Подготовка нефти к переработке осуществляется на блоке ЭЛОУ является важнейшим условием обеспечения работы установки первичной переработки нефти и получения качественных фракций для дальнейшей их переработки или компаундировании.
Данная нефть характеризуется плотностью 842 кгм3 содержание сернокислых смол 14% мас. и селикагельевых 10%мас. следовательно выбирается двухступенчатая схема. Число потоков выбирается исходя из производительности 6 млн. тгод
Объёмная производительность по сырью равна
Исходя из объёмной производительности определяется число электродегидраторов на каждой ступени.
n - число электродегидраторов
Wэдг – мощность электродегидратора Wэдг=450 м3ч
Нагрев нефти на современных установках ЭЛОУ-АВТ осуществляется в 2-4 потока исходя из производительности установки по сырью. На установках производительностью 6 млн. тгод ведется в три потока.
Температура и давление в электродегидраторе выбирается исходя из практических данных Т=140°С Р=16 МПа.
Принципиальная схема блока представлена на рисунке 3.1
2 Выбор схемы блока атмосферной перегонки.
В атмосферном блоке АВТ применяют три схемы разделения нефти:
– схема с одной сложной ректификационной колонной в атмосферном блоке (схема с однократным испарением и однократной ректификацией);
– схема с предварительным испарителем и ректификационной колонной (схема с двукратным испарением и однократной ректификацией);
– схема с предварительной отбензинивающей колонной и основной ректификационной колонной (схема с двукратным испарением и двукратной ректификацией). Выбор схемы определяется содержанием в данной нефти газов бензиновых фракций светлых нефтепродуктов и серы. Смесь Самотлорских нефтей содержит: 15 % газа 254 % бензиновых фракций выкипающих до 180оС или 306 % фракций выкипающих до 200оС и 582 % светлых нефтепродуктов выкипающих до 350оС (табл. 1.1). Содержание в нефти серы составляет 096 % (табл. 1.1). Для переработки такой высокопотенциальной нефти наиболее рационально применить двухколонную схему с двукратным испарением и двукратной ректификацией.
Данная схема имеет следующие достоинства:
- поскольку в колонне К-1 отгоняется часть бензина доля отгона отбензиненной нефти в печи будет меньше по сравнению с другими схемами переработки и тем самым отложение солей на поверхности труб печи уменьшится;
- в теплообменниках и змеевиках печи давление будет более низким;
- имеется возможность получения бензина с низким концом кипения ассортимент получаемых фракций более широк;
- основное количество коррозионно-активных компонентов нефти будет отделяться в колонне К-1 которая дешевле колонны К-2.
Схема имеет недостатки:
- так как самые легкие бензины отбираются в колонне К-1 колонна К-2 работает при более жестких условиях;
- установка имеет большое количество оборудования следовательно нужны более высокие капитальные и эксплуатационные затраты;
- на установке имеет место сравнительно большой расход топлива.
Как видно из рис. 3.2 схема атмосферного блока включает в себя отбензинивающую колонну К-1 две печи (П-1 и П-2) основную атмосферную колонну К-2 с тремя стриппинг-колоннами с помощью которых будут получаться фракции 180-230 230-280 и 280-350оС.
3 Стабилизация и вторичная перегонка бензиновой фракции
Стабилизация предназначена для удаления из бензиновых фракций углеводородных газов в том числе рефлюкса (пропан - бутановой фракции) и сероводорода. Стабилизация проводится при повышенном давлении в колонне оборудованной 32 клапанными тарелками. Стабильный бензин подается на блок вторичной перегонки. На блоке вторичной перегонки широкую бензиновую фракцию (28-180оС) мы в соответствии с заданием разделяем на фракции 28-62 62-85 85-120 и 120-180оС. Разделение предлагается проводить в трёх ректификационных колоннах с 60 клапанными тарелками в каждой. Схема блока стабилизации и вторичной перегонки бензина отражена на рис. 3.3.
4. Вакуумная перегонка мазута
Мазут – остаток атмосферной перегонки (фракция выкипающая выше 350оС) который выводится с низа колонны К-2 направляется на дальнейшую разгонку. Разгонка мазута осуществляется под вакуумом что позволяет поддерживать относительно низкую температуру (400-420оС на входе в колонну при заданной доле отгона) для предотвращения крекинга сырья. Для разгонки мазута используется вакуумная колонна К-7 в которой предлагается разместить 16 клапанных тарелок. С верха колонны пары отводятся к вакуумсоздающей аппаратуре. С верхней тарелки отводим утяжеленное дизельное топливо часть которого возвращаем в колонну в качестве орошения. Боковым погоном из колонны К-7 выводим вакуумный газойль (350-500оС). Его отбор производится с 10 тарелки. Вакуумный газойль поступает в стриппинг-колонну К-71 в низ которой подается водяной пар. С низа колонны выводим гудрон (остаток выкипающий при температуре выше 500оС). В нижнюю часть колонны подаем водяной пар для снижения парциального давления углеводородов. Избыток тепла в колонне снимаем циркуляционным орошением. Нагрев мазута перед колонной К-7 осуществляется в трубчатой печи П-3.
Схема блока приведена на рис. 3.4.
ПРИНЦИПИАЛЬНАЯ ТЕХНОЛОГИЧЕСКАЯ СХЕМА УСТАНОВКИ И ЕЕ КРАТКОЕ ОПИСАНИЕ
Технологическая схема установки приведена на рис. 4.1.
Нефть и деэмульгатор сырьевым насосом прокачивается через сырьевые теплообменники Т-11 Т-12 Т-21 и Т-22. Нагрев нефти в них осуществляется следующими потоками:
- в теплообменнике Т-11 – отходящей с АВТ фракцией 180-230оС;
- в теплообменнике Т-21 – первым циркуляционным орошением колонны К-2;
- в теплообменнике Т-12 – отходящей с АВТ фракцией 230-280оС;
- в теплообменнике Т-22 – вторым циркуляционным орошением колонны К-2;
Нагретая нефть проходит две ступени электродегидраторов. на каждой ступени – два электродегидратора. На первой ступени к нефти для дополнительного извлечения солей добавляется вода со второй ступени обессоливания на второй ступени – химически очищенная вода.
После электродегидраторов нефть проходит сырьевые теплообменники Т-13 – Т-15 и Т-23 – Т-25. Нагрев нефти в них осуществляется следующими потоками:
- в теплообменнике Т-13 – отходящей с АВТ фракцией 280-350оС;
- в теплообменнике Т-23 – третьим циркуляционным орошением колонны К-2;
- в теплообменнике Т-14 – отходящей с АВТ фракцией 350-470оС;
- в теплообменнике Т-23 –циркуляционным орошением вакуумной колонны К-6;
- в теплообменниках Т-15 и Т-25 – гудроном.
Нагретая нефть поступает на 14 тарелку отбензинивающей колонны К-1.
С верха колонны К-1 отводятся пары легкой бензиновой фракции 28-120оС. Пары бензина конденсируются в аппарате воздушного охлаждения АВО-1 и конденсаторе-холодильнике КХ-1. В емкости Е-1 происходит разделение бензина и газов. Легкая бензиновая фракция насосом Н-3 подается на орошение верха колонны а ее балансовое количество направляется в колонну стабилизации К-3.
С низа колонны К-1 частично отбензиненная нефть насосом Н-2 подается к печам П-1 и П-2. Часть нефти направляется в печь П-1 для создания горячей струи подаваемой в низ колонны К-1 остальная нефть нагревается в печи П-2 и по трубопроводу поступает в основную колонну К-2.
С верха колоны К-2 отводятся пары бензиновой фракции 120-180оС. Они конденсируются в аппарате воздушного охлаждения АВО-2 и конденсаторе-холодильнике КХ-2. В емкости Е-2 бензин отделяется от газов и воды. Далее бензин насосом Н-11 подается на орошение верха колонны а избыток идет на объединение с легкой бензиновой фракцией из колонны К-1 и поступает в стабилизационную колонну К-3.
Из колонны К-2 выводятся боковые погоны и циркуляционные орошения.
- фракция 180-230оС отводится с 32 тарелки и поступает на верхнюю тарелку стриппинг-колонны К-21. Пары из К-21 возвращаются под 33 тарелку колонны К-2 а фракция 180-230оС забирается насосом Н-10 прокачивается через сырьевой теплообменник Т-11 и через аппарат воздушного охлаждения АВО-13 выводится с установки.
- фракция 230-280оС отводится с 22 тарелки и поступает на верхнюю тарелку стриппинг-колонны К-22. Пары из К-21 возвращаются под 23 тарелку колонны К-2 а фракция 230-280оС забирается насосом Н-9 прокачивается через сырьевой теплообменник Т-12 и через аппарат воздушного охлаждения АВО-12 выводится с установки.
- фракция 280-350оС отводится с 12 тарелки и поступает на верхнюю тарелку стриппинг-колонны К-23. Пары из К-21 возвращаются под 13 тарелку колонны К-2 а фракция 280-350оС забирается насосом Н-8 прокачивается через сырьевой теплообменник Т-13 и через аппарат воздушного охлаждения АВО-11 выводится с установки.
Циркуляционные орошения:
- первое циркуляционное орошение забирается из кармана 30 тарелки насосом Н-4 прокачивается через сырьевой теплообменник T-21 и возвращается в колонну на 31 тарелку;
- второе циркуляционное орошение забирается из кармана 20 тарелки насосом Н-5 прокачивается через сырьевой теплообменник T-22 и возвращается в колонну на 21 тарелку;
- третье циркуляционное орошение забирается из кармана 10 тарелки насосом Н-6 прокачивается через сырьевой теплообменник T-23 и возвращается в колонну на 11 тарелку;
С низа колонны К-2 мазут направляется в вакуумную колонну К-5 насосом Н-7.
3 Блок стабилизации и вторичной ректификации бензиновых фракций
Бензиновые фракции НК-120 и 120-180оС с верха колонн К-1 и К-2 объединяются в один поток нагреваются в теплообменнике Т-3 и поступают в колонну стабилизации К-3. Колонна К-3 работает под давлением. В ней происходит освобождение бензина от растворенных газов и сероводорода. С верха К-3 выводится газ который проходит через АВО-3 и КХ-3 где частично конденсируется. Из рефлюксной емкости Е-3 сверху уходит газ а снизу – рефлюкс который насосом Н-16 подается на орошение верха колонны К-3 а избыток выводится с установки.
С низа К-3 выводится стабильный бензин который по трубопроводу поступает в рибойлер Т-4 где нагревается и частично испаряется. Пары направляются в низ колонны К-3 для создания парового потока а жидкость самотеком за счет перепада давления между колоннами К-3 и К-4 проходит через Т-3 и направляется по трубопроводу в колонну вторичной ректификации бензинаК-4.
С верха колонны К-4 отводятся пары фракции НК-70оС которые проходят через АВО-4 и КХ-4 конденсируются и поступают в емкость Е-4. Несконденсировавшиеся пары уходят с верха емкости а жидкая часть фракции НК-70оС выводится снизу и насосом Н-18 подается на орошение верха колонны К-4 а избыток отводится с установки.
С низа колонны К-4 фракция 70-180оС направляется в рибойлер Т-5 нагревается и частично испаряется. Пары подаются в низ колонны К-4 для создания парового потока а жидкость насосом Н-17 подается в колонну К-5.
С верха колонны К-5 отводятся пары фракции 70-120оС которые проходят через АВО-5 и КХ-5 конденсируются и поступают в емкость Е-5. Несконденсировавшиеся пары уходят с верха емкости а жидкая часть фракции 70-120оС выводится снизу и насосом Н-20 подается на орошение верха колонны К-5 а балансовое количество отводится с установки через АВО-8.
С низа колонны К-5 отводится фракция 120-180оС которая направляется в рибойлер Т-6 нагревается и частично испаряется. Пары направляются в низ колонны К-5 для создания парового потока а жидкость насосом Н-19 через АВО-7 выводится с установки.
Мазут с низа колонны К-2 насосом Н-7 направляется в радиантную камеру вакуумной печи П-3 он нагревается до температуры 380оС и подается в вакуумную колонну К-6.
С верхней тарелки колонны К-6 отбирается утяжеленное дизельное топливо насосом Н-15 прокачивается через АВО-6 и КХ-6 где охлаждается и по трубопроводу направляется на орошение верха колонны К-6 а балансовое количество утяжеленного дизельного топлива выводится с установки.
С 10 тарелки колонны К-6 выводится вакуумный газойль и направляется на верхнюю тарелку вакуумной стриппинг-колонны К-61. Пары из колонны К-61 возвращаются под 11 тарелку колонны К-6 фракция 350-470оС забирается насосом Н-14 прокачивается через сырьевой теплообменник T-14 аппарат воздушного охлаждения АВО-10 и выводится с установки.
Избыток тепла в колонне К-6 снимается циркуляционным орошением которое забирается из кармана 8 тарелки насосом Н-12 прокачивается через сырьевой теплообменник T-24 и возвращается в колонну К-6 на 9 тарелку.
С низа К-6 выводится гудрон который насосом Н-13 прокачивается по трубному пространству сырьевых теплообменников Т-15 и Т-25 и выводится с установки через АВО-9.
Пары с верха колонны К-6 поступают в конденсатор-холодильник КХ-7. Пары частично конденсируются холодной водой и направляются в вакуумный приемник Е-6 а вода идет на повторное использование. Несконденсировавшиеся пары из конденсаторов-холодильников объединяются в один поток и направляются в пароэжекционный вакуум-насос ЭЖ-1 затем в конденсатор-холодильник КХ-8 где частично конденсируются за счет холодной воды. Несконденсировавшиеся пары поступают на вторую ступень в пароэжекционный вакуум-насос ЭЖ-2 и конденсатор-холодильник КХ-9 а затем на третью ступень в пароэжекционный вакуум-насос ЭЖ-3 и конденсатор-холодильник КХ-10. Несконденсировавшиеся пары после третьей ступени направляются к печам. Для работы пароэжекционных вакуум-насосов ЭЖ-1 ЭЖ-2 и ЭЖ-3 используется водяной пар. Сконденсировавшиеся пары из конденсаторов-холодильников КХ-8 КХ-9 КХ-10 объединяются в один поток и направляются в барометрический ящик Е-7.
В вакуумном приемнике Е-6 происходит разделение паровой и жидкой фаз. Пары направляются в основной поток паров идущих в пароэжекционный вакуум-насос ЭЖ-1. Жидкая фаза с низа Е-6 выводится в барометрический ящик в котором постепенно накапливается утяжеленное дизельное топливо и периодически выводится с установки.
ХАРАКТЕРИСТИКА ОСНОВНОГО ОБОРУДОВАНИЯ
Комбинированная установка ЭЛОУ–АВТ включает в себя: электродегидраторы насосы ректификационные колонны трубчатые печи ребойлеры теплообменники и конденсатор-холодильники.
1 Электродегидраторы
Электродегидраторы используются на установках ЭЛОУ для обезвоживания и обессоливания нефти имеют внутри систему электродов под высоким напряжением интенсифицирующим укрупнение и оседание капель воды. В электродегидраторах обессоливание ведется с добавлением воды деэмульгатора и щелочи. Нефть из резервуара насосом прокачивается через систему теплообменников в последовательно работающие электродегидраторы. Нагрев сырой нефти необходим для достижения необходимой степени очистки.
Выбираем горизонтальный электродегидратор 2ЭГ-160-2М.
Производительность электродегидратора выбранного типа до 450м3ч объем – 160м3 рабочие параметры: давление – 15МПа температура - 140 оС; напряжение между электродами – 30-45кВ.
2 Ректификационные колонны
Ректификационные колонны в зависимости от числа получаемых продуктов при разделении многокомпонентных смесей делятся на простые и сложные.
В зависимости от давления ректификационные колонны делятся на колонны работающие под давлением атмосферные и вакуумные.
Колонны работающие под давлением применяются на АВТ в процессах стабилизации бензиновой фракции. Атмосферными колоннами являются основная колонна и колонны в блоке вторичной ректификации бензинов. Вакуумные колонны применяются при перегонке мазута.
В данной работе используются тарельчатые колонны. Тип тарелок – клапанные дисковые. Клапанные тарелки имеют КПД более 70% гидравлическое сопротивление 49-48 мм. рт. ст.
Колонна К-1 – отбензинивающая колонна. Представляет собой вертикальный аппарат с клапанными тарелками число которых - 32шт. Температура в низу колонны – 270 оС на входе в колонну – 230 оС в верху колонны – 115 оС. Подача тепла в низ колонны осуществляется горячей струей полуотбензиненной нефти циркулирующей через печь П-1 с температурой 370 оС. Давление в колонне составляет 035МПа.
Колонна К-2 – основная атмосферная ректификационная колонна в которой происходит отбор светлых – бензиновых и средних дистиллятов. Температура на входе в колонну- 350 оС в верху колонны – 157 оС давление в колонне – 0169МПа. Число тарелок – 44шт.
Колонна К-3 – стабилизационная колонна. Представляет собой вертикальный аппарат с переменным сечением. Количество ректификационных тарелок 50.
Колонны К-4 К-5 и К-6 – колонны предназначенные для вторичной ректификации широкой бензиновой фракции.
Колонна К-7 – ректификационная вакуумная колонна. Температура на входе в колонну – 380-420 оС в верху колонны – 65-110 оС в низу – 360-400 оС. Давление на входе в колонну – 60-120мм рт.ст. давление в верху колонны – 10-60мм рт.ст. Используются клапанные тарелки – 16
Ректификационные колонны и тарелки необходимо изготовить из материала устойчивого к сероводородной коррозии.
3 Теплообменные аппараты
На высокопроизводительных АВТ применяют укрупненные теплообменники типа «труба в трубе» и «с плавающей головкой».
Теплообменники типа «труба в трубе» применяют для регенерации тепла высоковязких и легкозастывающих гудронов.
Данные теплообменники имеют следующие недостатки:
-малая поверхность теплообмена;
Теплообменники этого типа имеют следующие достоинства:
-позволяют обеспечивать высокие скорости движения теплоносителей что приводит к меньшему отделению загрязнений;
-позволяют обеспечить противоток тем самым увеличивая коэффициент теплоотдачи;
-в аппаратах легко осуществить оребрение труб.
Теплообменники с плавающей головкой наиболее часто используются на АВТ. За счет особенностей конструкции (наличие плавающей головки) в них легко обеспечивается компенсация температурных удлинений корпуса и трубного пучка. Трубный пучок легко вытаскивается вместе с плавающей головкой что облегчает чистку межтрубного пространства. Но эти теплообменники имеют следующие недостатки:
-относительно сложная конструкция;
-большой расход металла на единицу поверхности;
-плавающая головка не доступна для осмотра.
В стабилизаторе и колоннах вторичной перегонки для подвода тепла в низ колонны используются подогреватели с паровым пространством. Они позволяют обеспечить любую поверхность теплообмена путем установки необходимого количества подогревателей и малое гидравлическое сопротивление каждого потока. Это позволяет обойтись небольшим объемом жидкости в низу колонны и располагать обогреватель примерно на той же отметке что и колонна. Недостатком их является малый запас жидкости за сливной перегородкой подогревателя.
Конденсаторы и холодильники выполняют в виде змеевиков из гладких или ребристых труб либо в виде одно- и многоходовых кожухотрубчатых аппаратов.
На АВТ используют так же аппараты воздушного охлаждения (АВО) позволяющие сократить расходы воды на НПЗ. Коэффициенты теплопередачи для различных климатических условий при работе аппаратов в качестве конденсаторов и холодильников на АВТ составляют 235-258 Вт(м2 × К).
АВО имеют поверхность охлаждения скомпонованную из секций оребренных труб систему подачи воздуха и регулирующие устройства для изменения расхода воздуха.
В нефтеперерабатывающей и нефтехимической промышленности для нагрева нефти и нефтепродуктов до температур более высоких чем те которые можно достичь например с помощью нагрева водяным паром используются трубчатые печи.
На установке ЭЛОУ-АВТ находят применение трубчатые печи с горизонтальным расположением труб – печи серии ГС-1 – двухкамерная с однозарядным настенным экраном и свободным вертикальным пламенем. Основными характеристиками этого типа печей являются: теплопроизводительность – 15-58МВт средняя теплонапряженность радиантных труб – 406кВтм2 поверхность нагрева: радиантная (трубы 152х8мм) – 265-1050м2 конвективная (трубы 108х6мм) – 450-1785м2; рабочая длина радиантных труб – 6-24м КПД – 08-085; производительность печи – 8000тсут; тепловая мощность – 58МВт; гидравлическое сопротивление змеевика – 05-15МПа.
ТЕХНОЛОГИЧЕСКИЙ РАСЧЕТ
1 Материальные балансы блоков ЭЛОУ-АВТ колонн К-1 и К-2
Материальный баланс блока ЭЛОУ установки АВТ колонн К-1 и К-2 приведен в табл. 6.1 -6.4. Количество рабочих дней в году принимаем равным 340.
Материальный баланс блока ЭЛОУ
Нефть обезвоженная и обезсоленная
Материальный баланс блока АВТ отбензинивающей колонны К-1 и основной атмосферной колонны К-2 представлены в таблице 6.2-6.4.
Материальный баланс блока АВТ
Потенциальное содержание %мас.
Отбор от потенциала в долях от единицы
Фактический отбор %мас.
При составлении материального баланса блока (установки) АВТ принимали во внимание отбор фракций (в долях от единицы) от их потенциального содержания в перерабатываемой нефти. Отбор легких бензиновых фракций (НК-120оС) лежит в пределах 098-10 тяжелых бензиновых фракций (120-200оС) - от 096 до 098 керосиновых фракций (180-280оС) - от 095 до 097 и дизельных фракций - в интервале 080-095.
Отбор светлых дистиллятов = × 100 = 969 % отн.
Материальный баланс колонны К-1
Материальный баланс колонны К-2
Выход на нефть %мас.
Выход на сырьё колонны %мас.
2 Технологический расчет колонны К-2
2.1 Материальный баланс колонны К-2
Материальный баланс колонны К-2 представлен в табл. 6.5. Данные получены с помощью рис. 1.1 и из табл. 6.4.
2.2 Выбор числа и типа тарелок в колонне
Общее число тарелок в основной атмосферной колонне на действующих установках колеблется от 36 до 56. Число тарелок в колоннах при получении бензиновых и керосиновых фракций колеблется чаще всего в пределах 10-16легких дизельных - от 8 до 10 а тяжелых дизельных фракций - от 4 до 10 шт.
В отгонной части колонны принимаем четыре тарелки.
В укрепляющей части колонны - от зоны питания до тарелки вывода фракции 280-3500С принимаем 8 тарелок (с 5 по 12 тарелку считая снизу) n2=8.
От тарелки вывода фракции 280-3500С до тарелки вывода фракции 230-2800С принимаем 10 тарелок (с 13 по 22) n3=10.
От тарелки вывода фракции 230-2800С до тарелки вывода фракции 180-2300С принимаем 10 тарелок (с 23 по 32) n4 = 10.
В верхней части колонны - от тарелки вывода фракции 180-2300С до верха - 12 тарелок (с 33 по 44 тарелку) n5 = 12.
Всего в колонне принято 44 тарелки.
В колонне К-2 используем клапанные тарелки гидравлическое сопротивление которых колеблется в зависимости от типа клапанной тарелки и ее состояния в пределах 4-7 мм рт. ст. Принимаем перепад давления на одну тарелку равным 5 мм рт. ст. (000066 МПа).
2.3 Расчет давления по высоте колонны
Расчет давления по высоте колонны ведем сверху вниз исходя из перепада давления на тарелках. Мысленно делим сложную колонну К-2 на несколько простых.
Принимаем давление в емкости Е-2 равным 01 МПа (РЕ2 = 01МПа). Давление в верху колонны зависит от перепада на участке от верха колонны до емкости орошения. Принимаем Р = 004 МПа.
Давление в верху колонны:
РВЕРХ = РЕ-2 + Р = 01 + 004 = 0140 МПа
Давление на тарелке вывода фракции 180-230оС:
Р180-230 = РВЕРХ + РТ × n5 = 0140 + 12 × 000066 = 0148 МПа
Давление на тарелке вывода фракции 230-280оС:
Р230-280 = РВЕРХ + РТ × (n5 + n4) = 0140 + 000066 × (12 + 10) = 0155 МПа
Давление на тарелке вывода фракции 280-350оС:
Р280-350 = РВЕРХ + РТ × (n5 + n4 + n3) = 0140 + 000066 × (12 + 10 + 10) = 0161 МПа
Давление на входе в колонну:
РВХОД = РВЕРХ + РТ × ( n5 + n4 + n3 + n2) = 0140 + 000066 × 40 = 0166 МПа
Давление по высоте колонны распределяется следующим образом:
Р180-230 = 0148 МПа;
Р230-280 = 0155 МПа;
Р280-350 = 0161 МПа;
2.4 Расчет расхода водяного пара
По заводским данным колебания расхода водяного пара составляют 16 – 23%мас в расчете на сырье основной атмосферной колонны. В среднем это составляет 2%мас на отводимый продукт.
Дальнейший расчет ведем на 100кг сырья.
Расход водяного пара подаваемого в низ колонны:
ZНИЗ = GМАЗУТ× 002 = 503 × 002 = 1006 кг.
Расход водяного пара подаваемого в колонну К-23:
ZК-23 = G280-350 × 002 = 15 × 002 = 03 кг.
Расход водяного пара подаваемого в колонну К-22:
ZК-22 = G230-280 × 002 = 95 × 002 = 019 кг.
Расход водяного пара подаваемого в колонну К-21:
ZК-21 = G180-230 × 002 = 102 × 002 = 0204 кг.
Количество водяного пара на тарелке отбора фракции 280-350 оС:
Z280-350= ZНИЗ = 1006 кг.
Количество водяного пара на тарелке отбора фракции 230-280оС:
Z230-280 = ZНИЗ + ZК-23 = 1006+ 03 =1306 кг.
Количество водяного пара на тарелке отбора фракции 180-230оС:
Z180-230 = ZНИЗ + ZК-23 + ZК-22 = 1006 + 03 + 019 =1496 кг.
Количество водяного пара в верху колонны:
Zверх = Zниз + ZК-23 + ZК-22+ ZК-21 = 1006 + 03 + 019 + 0204=17 кг.
2.5 Расчет расхода флегмы по высоте колонны
Задаемся флегмовым числом и принимаем условно что оно по колонне не меняется. Примем флегмовое число равным 2.
Количество флегмы стекающей с тарелки вывода фракции 280-350 оС:
G280-350= G280-350 × 2 = 15 × 2 = 30 кг.
Количество флегмы стекающей с тарелки вывода фракции 230-280оС:
G230-280 = G230-280 × 2 = 95 × 2 = 19 кг.
Количество флегмы стекающей с тарелки вывода фракции 180-230оС::
G180-230 = G180-230 × 2 = 102 × 2 = 204 кг.
Количество флегмы в верху колонны:
G105-180 = G150-180 × 2 = 15 × 2 = 30 кг.
2.6 Определение температуры нагрева сырья на входе в колонну
Температуру нагрева нефти на входе в колонну К-2 определяем аналитическим методом. Для этого определяем температуру нагрева нефти которая должна соответствовать необходимой массовой доле отгона сырья колонны в зоне питания. Под необходимой долей отгона (теоретической) отбензиненной нефти понимают сумму светлых в долях от единицы которую определяют из материального баланса колонны.
В нашем примере теоретическая доля отгона (ет) будет следующей (см. таблицу 6.5):
ет = (0150+0102+0095+0150) = 0497.
В результате расчета необходимо определить температуру нагрева нефти которая должна обеспечить величину фактической доли отгона равной или на 0001 - 0003 больше теоретической.
Для определения температуры нагрева нефти необходимо рассчитать процесс однократного испарения сырья.
Расчет процесса однократного испарения сырья колонны удобнее вести для условий испарения в трубах печи а не в питательной секции колонны. В этом случае следует принять давление на 003-004 МПа выше чем в питательной секции.
Принимаем расчетное давление следующим:
Рр = Рвход + 003 = 0166 + 003=0196 МПа.
Для удобства продолжаем вести расчет на 100 кг сырья.
Разбиваем сырье колонны - отбензиненную нефть узкие фракции (по 50 градусов).
При принятом давлении задаемся температурой нагрева нефти и с помощью программы ПЭВМ находим молярную долю (ер) методом подбора. Для молярной доли отгона должны соблюдаться соблюдаются равенства:
ер - молярная доля отгона;
Кi - константа фазового равновесия.
Затем рассчитываем массовую долю отгона по формуле:
где - массовая доля отгона (расчетная);
Му - молярная масса паровой фазы;
Мс - молярная масса сырья.
Расчет оформляем в виде табл. 6.6.
Молярную массу сырья находим по формуле
где GС - расход сырья (отбензиненной нефти) кг; Gi = 100 кг (колонка 4).
NС - число молей сырья (колонка 6).
Mi - молярная масса компонента сырья (колонка 5).
Определение молярной доли отгона отбензиненной нефти
на входе в колонну при температуре 350оС и давлении 0196 МПа
Выход фракций (фактический) на сырье установки % мас.
Выход фракций на сырье колонны %мас.
Продолжение таблицы 6.6
Средняя температура кипения фракции оС
Давление насыщенных паров фракции при 350оС 0196 МПа (Рi)
Массовая доля отгона сырья колонны К-2:
= 06917 × (1790 2444) = 05064 ~ 0506.
Массовая доля отгона () сырья основной колонны полученная в результате расчета должна быть несколько больше или равна теоретической доле отгона . В нашем случае это условие соблюдается следовательно температуру нагрева сырья на входе в колонну определили верно.
Проверку правильности расчета проводим определяя плотность сырья колонны из соотношения
Определим плотность сырья по данным табл. 6.6 (колонка 21):
Полученные значения плотностей сырья колонны совпадают.
2.7 Определение температуры в низу колонны
Колонна работает с вводом водяного пара в нижнюю часть колонны где происходит испарение наиболее легкой части углеводородов на что тратится теплота и температура мазута снижается на 10-250С по отношению к температуре входа сырья в зону питания. Принимаем температуру в низу колонны в нашем примере следующей:
tниз = 350 - 10= 340оС.
2.8. Расчет температуры вывода фракций
2.8.1. Расчет парциальных давлений фракций по высоте колонны.
Парциальное давление фракций 105-180 180-230 230-280 и 280-350оС в сечениях их вывода приведено в таблице 6.7 – 6.10.
Парциальное давление фракции 105-180оС в сечении ее вывода
Фракция 105-180 оС + флегма
Парциальное давление фракции 180-230оС в сечении ее вывода
Фракция 180-230 оС + флегма
Парциальное давление фракции 230-280оС в сечении ее вывода
Фракция 230-280 оС + флегма
Парциальное давление фракции 280-350оС в сечении ее вывода
Фракция 280-350 оС + флегма
2.8.2 Определение температуры вывода боковых погонов и температуры в верху колонны
Для определения температур вывода боковых погонов и температуры верха используем данные полученные в ходе построения линий ИТК и ОИ для соответствующих фракций. Эти данные приведены в курсовой работе «Построение кривых ИТК плотности и молярной массы Смеси Самотлорских нефтей».
Кривые ИТК фракций 105-180 180-230 230-280 и 280-350оС приведены на рис. 6.1 - 6.4. Данные на основании которых строились представленные кривые приведены в табл. 6.11 - 6.14.
Исходные данные для построения кривой ИТК фракции 105-180 °C
Температура выкипания °C
Исходные данные для построения кривой ИТК фракции 180-230°C
Исходные данные для построения кривой ИТК фракции 230-280°C
Исходные данные для построения кривой ИТК фракции 280-350°C
Методика построения линий однократного испарения (ОИ) подробно изложена в предыдущей курсовой работе.
Для фракции 105-180оС по кривой ИТК (рис. 1.1) находим температуры выкипания 10 50 и 70 % фракции.
=113оС =144оС =160оС.
Затем находим угол наклона кривой ИТК фракции по формуле
По углу наклона и температуре 50%-ного отгона находим на графике Обрядчикова - Смидович:
% (НОИ) соответствует 315 % по ИТК
0% (КОИ) соответствует 61 % по ИТК.
При атмосферном давлении
Парциальное давление фракции 105-180оС в верху колонны составляет 0111 МПа (см. табл. 6.7). По сетке Максвелла находим
Верхний продукт колонны выводится в паровой фазе поэтому за температуру верха принимают температуру конца однократного испарения (конец линии ОИ). Температура верха колонны составляет 157оС.
Для фракции 180-230оС (см. рис. 6.3):
=182оС =192оС =208оС.
Угол наклона кривой ИТК
По графику Обрядчикова - Смидович
% (НОИ) соответствует 38% по ИТК
0% (КОИ) соответствует 54% по ИТК.
Парциальное давление фракции 180-230оС в сечении ее вывода равно 007МПа (см. табл. 6.8). По сетке Максвелла:
Температура вывода бокового погона соответствует температуре начала линии ОИ соответствующей фракции при ее парциальном давлении. Температура вывода фракции 180-230оС составляет 180оС.
Для фракции 230-280оС (рис. 6.3):
=236оС =252оС =263оС.
% (НОИ) соответствует 37% по ИТК
С помощью сетки Максвелла находим при давлении 0055 МПа (табл. 6.9):
Температура вывода фракции 230-280оС составляет 225оС.
Для фракции 280-350оС (рис. 6.4):
=287оС =314оС =330оС.
0% (КОИ) соответствует 57% по ИТК.
С помощью сетки Максвелла находим при давлении 0062 МПа (табл. 6.10):
Температура вывода фракции 280-350оС составляет 288оС.
Температуры вывода фракций из колонны К-2:
фракция 105-180оС t = 157оС;
фракция 180-230оС t = 180оС;
фракция 230-280оС t = 225оС;
фракция 280-350оС t = 270оС.
2.9 Тепловой баланс колонны К-2
Используя результаты расчетов составляем тепловой баланс колонны К-2. Он приведен в табл. 6.15.
Энтальпию паров рассчитываем по формуле
Энтальпию жидкой фазы вычисляем по формуле
Плотность находится по формуле
где a - средняя температурная поправка на один градус.
Находим дебаланс тепла по следующей формуле
= ((Qприх - Qрасх) Qприх ) × 100 = ((97754 – 85612) 97754)×100 = 124%
Следовательно необходимо циркуляционное орошение.
Материальный и тепловой баланс колонны К-2
Средняя температурная поправка на один градус
Нефть отбензиненая в том числе:
Фракция 105-180 оС + острое орошение
Продолжение таблицы 6.15
2.10 Расчет количества циркуляционных орошений
Принимаем допущение что количество теплоты вошедшее в колонну с водяным паром равно количеству теплоты потерянному через стенки колонны в окружающую среду.
Избыток тепла в колонне который снимается циркуляционными орошениями составляет Q = QПРИХ – QРАСХ = 97754 – 85612= 12141 кДжкг
Число циркуляционных орошений равно 3.
Температуры вывода циркуляционных орошений определим учитывая величины перепада температур на одну тарелку по формуле
t цоi = ti + 2 × Dti
Dti - перепад температуры на одну тарелку оС.
Перепад температуры на одну тарелку между тарелками вывода фракций 180-230 и 230-280оС:
Перепад температуры на одну тарелку между тарелками вывода фракций 230-280 и 280-350оС:
Перепад температуры на одну тарелку между тарелками вывода фракций 280-350 и зоной питания:
Температура вывода первого циркуляционного орошения
t цо1 = 180 + 2 × 45 = 189 оС.
Температура вывода второго циркуляционного орошения
t цо2 = 225 + 2 × 45 = 234оС.
t цо3 = 270 + 2 × 8 = 286оС.
Принимаем для циркуляционных орошений I и II следующие температуры выхода из колонны:
для ЦО1 tвх = 130оС;
для ЦО2 tвх = 160оС;
для ЦО3 tвх = 220оС.
DQ = DQ1 + DQ2 + DQ3
DQ1 = gцо1 × (h189– h130) = gцо1 × (39628 – 258996) = 1372 × gцо1;
DQ2 = gцо2 × (h234 – h160) = gцо2 × (52712– 33872) = 1884 × gцо2;
DQ3 = gцо3 × (h286 – h220) = gцо3 × (69117– 50428) = 1869 × gцо3.
Предполагаем что по массе выводимого из колонны вещества потоки циркуляционных орошений равны между собой.
141 = 1372 × gцо1 + 1884 × gцо2 + 1869 × gцо3 = 5126 × gцо
Отсюда находим среднее значение gцо
gцо1 = gцо2 = gцо3 = 12141 5126 = 236 кг.
DQ1 = gцо1 × (h189– h130) = 236× (39628 – 258996) =3240 кДжкг;
DQ2 = gцо2 × (h234 – h160) = 236× (52712– 33872) =4446 кДжкг;
DQ3 = gцо3 × (h286 – h220) = 236× (69117– 50428) =4410 кДжкг.
2.11 Расчет нагрузки по высоте колонны
Выбираем наиболее нагруженные сечения.
Расчет нагрузки в сечении I-I (под верхней тарелкой).
Составляем материальный баланс по парам и жидкости в сечении I-I.
GI-I = G105-180 + gгоо
где GI-I - поток паров проходящий через сечение I-I кг;
G105-180 - расход паров фракции 105-180оС; G105-180 = 15 кг (см.табл. 6.5).
где gгоо - расход горячего орошения (внутренней флегмы) возникающего от острого орошения кг.
Рассчитаем количество горячего орошения по формуле
где gгоо - расход горячего орошения от острого кг;
Hверх - энтальпия паров в верху колонны кДжкг;
hвход - энтальпия острого орошения кДжкг ;
- энтальпия паров при температуре в сечении I-I кДжкг;
- энтальпия горячего орошения (флегмы) при температуре в сечении I-I кДжкг;
Нагрузка по жидкости:
Температуру в сечении I-I (сечении под верхней тарелкой) найдем из уравнения tI-I = tверха + Dt
где tI-I - температура в сечении I-I оС;
tверха - температура в верху колонны оС;
Dt - перепад температуры на одну тарелку оС.
tI-I = 157 + 2 = 159оC
Определим энтальпии фракции 105-180оС ( = 0768):
Н157 = 649 кДжкг; h30 = 60 кДжкг; Н159 = 653 кДжкг; h159= 355 кДжкг;
GI-I = 15 + 594 = 744 кг.
gI-I = gгоо. = 594 кг.
Расчет нагрузки в сечении II-II – сечении между выводом и вводом
первого циркуляционного орошения.
GII-II = G105-180 + G180-230 + gфл.180-230 + gгцо1
где GII-II - расход паров проходящих через сечение II-II кг;
G180-230 - расход паров фракции 180-230оС;
gфл.180-230 - расход флегмы стекающей с тарелки вывода фракции 180-230оС кг. Принимаем условно что расход флегмы стекающей с тарелки вывода фракции 180-230оС остается постоянным до тарелки вывода фракции 230-280оС изменяется только ее состав. gфл.180-230 = 204 кгч;
Эскиз сечения II - II
gгцо1 – горячее орошение возникающее от первого циркуляционного орошения кг.
gгцо1 – горячее орошение возникающее от циркуляционного орошения I.
где gцо1 - расход ЦО 1 кг; gцо1 = 236 кг.
Условно принимаем что плотность ЦО1 равна плотности фракции 180-230оС ( = 0808). Определим энтальпии паров и жидкости ЦО1:
Н189 = 704 кДжкг; h189 = 39628 кДжкг; h130 = 25899 кДжкг.
GII-II = 15 + 102 + 204 + 105= 561 кг.
gII-II = gфл.180-230 + gцо1 + gгцо1
где gII-II - поток жидкости проходящий через сечение II-II кг;
gII-II = 204 + 236 + 105= 545 кг.
Расчет нагрузки в сечении III-III – сечении между выводом и вводом
второго циркуляционного орошения.
Эскиз сечения III - III
III GIII-III gIII-III III
G III-III = G105-180 + G180-230 + G230-280 + gфл.230-280 + gгцо2
где GIII-III - количество паров проходящих через сечение III-III кг;
G230-280 - количество паров фракции 230-280оС;
gфл.230-280 - количество флегмы стекающей с тарелки вывода фракции 230-280оС кг.
Принимаем условно что количество флегмы стекающей с тарелки вывода фракции 230-280оС остается постоянным до тарелки вывода фракции 280-350оС изменяется только ее состав.
gфл.230-280 = 19 кг;
gгцо2 – горячее орошение возникающее от второго циркуляционного орошения кг.
где gцо2 - расход ЦО 2 кг; gцо2 = 236 кг.
Условно принимаем что плотность ЦО2 равна плотности фракции 230-280оС ( = 0856). Определим энтальпии паров и жидкости ЦО2:
Н234 = 7885 кДжкг; h234 = 52712 кДжкг; h160 = 33872 кДжкг.
GIII-III = 15 + 102 + 95 + 18 + 17 = 697 кг.
gIII-III = gфл.230-280 + gцо2 + gгцо2
где gIII-III - поток жидкости проходящий через сечение III-III кг.
gIII-III = 18 + 236 + 17 = 586 кг.
Расчет нагрузки в сечении IV-IV - сечении между
выводом и вводом третьего циркуляционного орошения.
G IV-IV = G105-180 + G180-230 + G230-280 + G280-350 + gфл.280-350 + gгцо3
где GIV-IV - поток паров проходящий через сечение IV-IV кгч;
G280-350 - количество паров фракции 280-350оС G280-350 = 15 кг;
gфл.280-350 - количество флегмы стекающей с тарелки вывода фракции 280-350оС кг.
Принимаем что количество флегмы стекающей с тарелки вывода фракции 280-350оС остается постоянным до тарелки ввода сырья в колонну изменяется только ее состав.
gфл.280-350 = 30 кг;
Эскиз сечения IV - IV
gгцо3 – горячее орошение возникающее от третьего циркуляционного орошения кг:
где gцо3 - расход ЦО 3 кг; gцо3 = 236 кг.
Условно принимаем что плотность ЦО3 равна плотности фракции 280-350оС ( = 0917). Определим энтальпии паров и жидкости ЦО3:
Н189 = 88923 кДжкг; h189 = 69117 кДжкг; h220 = 50428 кДжкг.
GIV-IV = 15 + 102 + 95 + 15 + 30 + 222 = 1019 кг.
gIV-IV = gфл.280-350 + gцо3 + gгцо3.
где gIV-IV - поток жидкости проходящий через сечение IV-IV кгч.
gIV-IV = 30 + 236 + 222 = 758 кг.
Расчет нагрузки в сечении V-V.
GV-V = L + gфл.280-350 – gм;
GV-V = 100 + 30 – 503 = 797 кг.
gV-V = gс + gфл.280-350 = L × (1 – р) + gфл.280-350;
gV-V = 100 × (1 – 0504) + 30 = 796кг.
В табл.6.16 представлены нагрузки по парам и жидкостям в различных сечениях колонны.
Нагрузки по парам и жидкостям в различных сечениях колонны
2.12. Определение основных размеров колонны К-2.
Сечение колонны определяем по формуле
где Vп – объемный расход паров в рассчитываемом сечении колонны м3с;
Wдоп – допустимая скорость паров в рассчитываемом сечении колонны мс.
Объем паров в рассчитываемом сечении определяем по уравнению
L - количество водяных паров в рассчитываемом сечении кг;
– молярная масса воды;
t – температура в рассчитываемом сечении оС;
Робщ – общее давление в рассчитываемом сечении МПа;
k – коэффициент пересчета со 100 кг сырья на реальную загрузку колонны.
Коэффициент пересчета k определяем из соотношения
где Gс - массовый расход сырья кгч.
Допустимую скорость паров определяем по формуле
Wдоп = 085 × 10-4 × С ×
где С – коэффициент величина которого зависит от конструкции тарелок и расстояния между ними. Его величину определяем по формуле
С = К×С1 – С2×(l - 35)
где К – коэффициент который зависит от типа тарелок.
Для клапанных тарелок К = 115;
С1 – коэффициент зависящий от расстояния между тарелками.
Примем расстояние между тарелками равным 600 мм. С1 = 750;
С2 - коэффициент равный 4 для клапанных тарелок;
l - коэффициент учитывающий влияние жидкостной нагрузки на допустимую скорость паров. Определим величину этого коэффициента по формуле
где Wc – объемная нагрузка колонны по жидкой фазе в рассчитываемом сечении м3ч.
n - число сливных устройств на тарелке;
Если расчетное значение l10 то принимаем значение l=10. В случае если l>65 следует принять тарелки с большим числом сливных устройств.
Допустимая скорость паров в любой атмосферной колонне составляет 08-10 мс. Однако это не означает что любая меньшая линейная скорость может обеспечить нормальные условия работы колонны. Фактическая линейная скорость паров в колонне должна быть не менее 60 % от допустимой т.е. необходимо обеспечить минимальную скорость паров в колонне не менее 05-06 мс а еще лучше на уровне 07-08 мс.
Нагрузку колонны по жидкой фазе находим из соотношения
где g – массовая нагрузка по жидкости в рассчитываемом сечении кгч;
rж - плотность жидкой фазы при температуре в рассматриваем сечении гсм3.
rп – плотности паров кгм3.
Плотность жидкости находим из выражения
где t - температура в рассматриваемом сечении оС.
Плотность паров определяем из соотношения
где Gп - расход паров в рассматриваемом сечении кг.
Диаметр колонны определяем по формуле
Высоту подпора жидкости над сливной перегородкой рассчитываем по формуле
где Dh - высота подпора жидкости над сливной перегородкой м.
Высота подпора жидкости не должна превышать 50 мм.
- периметр слива (длина сливной перегородки) м.
Длина сливной перегородки может быть рассчитана по формуле
где d - диаметр колонны в рассматриваемом сечении м.
Расчет диаметра колонны в сечении I – I
= 0764 – 0000812 × (157 - 20) = 0654 гсм3 = 654 кгм3.
Wc = × 636029 = 5776 м3ч.
С =115 × 750 – 4 × (293 – 35) = 8853.
WД = 085×10-4× 8853 × = 091 мс.
Расчет диаметра колонны в сечении IV - IV.
G IV-IV = G110-180 + G180-240 + G240-300 + G300-350 + gфл.300-350 + gгцо3
где Nк - количество вещества компонентов находящихся в паровой фазе в рассматриваемом сечении кмоль.
61 × 425875 = 1501 м3с.
= 0858 - 0000647 × (2785 - 20) = 0690751 гсм3 = 6908 кгм3.
Wc = × 425875 = 2848 м3ч.
С =115 × 750 – 4 × (1894 – 35) = 9267.
WД = 085 × 10-4× 9267 × = 0814 мс.
= 0020648 м = 206 мм.
Расчет диаметра колонны в сечении V - V.
GV-V = L + gфл.300-350 – gм;
20 425875 = 148 м3с.
= 0814184 - 0000752 × (3475 - 20) = 0567904 гсм3 = 5679 кгм3.
× 425875 = 566 кгм3.
Wc = × 425875 = 51894 м3ч.
С =115 × 750 – 4 × (3413 – 35) = 86598.
WД = 085 × 10-4× 86598 × = 073 мс.
Расчет высоты колонны.
Общая высота колонны складывается из высот отдельных ее частей на которые она условно разбивается (рис. 6.11). Высоту ее верхней части (над верхней тарелкой) определяем по формуле
где d1 - диаметр верхней части колонны м.
Н1 = 05 × 55 =275 м.
Расчет высоты ведем зная число тарелок по высоте колонны и расстояния между ними. Расстояние между тарелками (Dh) принимается нами равным 05м
H2 = (n1 - 1) × Dh – высота части колонны от тарелки № 37 отбора фракции 180-240оС по 50 тарелку n1 = 13Н2 = (13 - 1) × 05 = 60 м.
H3 = (n2 - 1) × Dh – высота части колонны от тарелки № 5 по 37 тарелку n2 = 32Н3 = (32 - 1) × 05 = 155 м.
Высота зоны питания колонны (Н4) составляет 2-3 расстояния между тарелками:
H4 = (2 – 3) × Dh = 3 × 05 = 15 м.
H5 = (n3 – 1)×Dh = (4 – 1) × 05 = 15 м.
где n3 - число тарелок в отгонной части колонны; n3 = 4 шт.
H6 – расстояние от нижней тарелки до уровня жидкости в низу колонны; H6 = 15 - 2 м. Принимаем Н6 = 20 м.
H7 – высота нижней части колонны определяется в зависимости от объема жидкости в низу колонны. Она равна сумме половины диаметра низа колонны (d) и высоты столба жидкости находящейся в цилиндрической части колонны - величины (h'):
Величину h' находим по формуле
где Vн - общий объем нефти находящийся в низу колонны м3 который должен обеспечивать работу насоса откачивающего жидкость из колонны в течение 10 мин после прекращения подачи нефти на установку. Величину объема нефти находящейся в низу колонны рассчитываем по формуле
где rм - плотность мазута кгм3.
rм = 898 кгм3. В низу колонны мазут находится при температуре 3325оС:
= 0898 - 0000647 × (3325 - 20) = 0695813 гсм3 = 6958 кгм3.
Vполусф - объем нефти находящейся в полусферическом днище колонны м3.
Эту величину находим по формуле
Vн = × 425875 = 508 м3.
Vполусф = = 4353 м3.
H7 = 55 2 + 031 = 306 м.
Общая высота колонны равна
H = Н1 + Н2 + Н3 + Н4 + Н5 + Н6 + Н7 + Н8.
Н = 275 + 60 +155+15+15+20+306+4 = 3631 м.
БИБЛИОГРАФИЧЕСКИЙ СПИСОК
Нефти СССР. Справочник т. III. Нефти Кавказа и Западных районов Европейской части СССР. Под ред. Г.Г. Ашумова Е.С. Левченко и А.С. Журба. М.: Химия 1972 - 616 с.
Проектирование установки ЭЛОУ-АВТ (Методические указания) Самарский. гос. техн. универ.; Сост. В.Г. Власов И.А.Агафонов. Самара 2003.
Гуревич И.Л. Технология переработки нефти и газа. Ч. 1. М.: 1972 360 с.
Касаткин А.Г. Основные процессы и аппараты химической технологии. М.: Химия 1973 750 с.
Скобло А.И. Трегубова И.А. Молоканов Ю.К. Процессы и аппараты нефтеперерабатывающей промышленности. М.: Химия 1982 584 с.
Расчеты основных процессов и аппаратов нефтепереработки (справочник). М.: Химия 1979 566 с.
Рудин МГ Драбкин А.В Краткий справочник нефтепереработчика. Л.: Химия 1980.
Справочник нефтепереработчика. Под ред. Ластовкина Г.А. Л.: Химия 1986.
Сарданашвили А.Г. Львова А.И. Примеры и задачи по технологии переработки нефти и газа. М.: Химия 1980 256 с.
Курсовая ЭЛОУ-АВТ.doc
ГОСУДАРСТВЕННОЕ ОБРАЗОВАТЕЛЬНОЕ УЧРЕЖДЕНИЕ
ВЫСШЕГО ПРОФЕССИОНАЛЬНОГО ОБРАЗОВАНИЯ
«САМАРСКИЙ ГОСУДАРСТВЕННЫЙ ТЕХНИЧЕСКИЙ УНИВЕРСИТЕТ»
Кафедра «Химическая технология переработки нефти и газа»
ПРОЕКТ УСТАНОВКИ ЭЛОУ-АВТ
Характеристика нефти и фракций из нее
Обоснование ассортимента получаемых фракций
Выбор и обоснование схемы ЭЛОУ-АВТ
1. Выбор схемы блока ЭЛОУ
2. Выбор схемы блока атмосферной перегонки
3. Стабилизация и вторичная перегонка бензиновой фракции.
4. Вакуумная перегонка мазута
Принципиальная технологическая схема установки и ее краткое описание
Основное оборудование установки
1. Электродегидраторы
3. Теплообменные аппараты
Технологический расчет
1. Материальный баланс блока ЭЛОУ блока АВТ и атмосферных колонн К-1 и К-2
2. Технологический расчет колонны К-2
Библиографический список
Нефть представляет собой маслянистую жидкость темного (иногда черного) цвета текучую иногда малоподвижную. Сырая нефть состоит из огромного количества органических соединений. В ней содержатся все виды насыщенных углеводородов (парафиновые нафтеновые ароматические). Олефины в природной нефти отсутствуют так как в условиях характерных для залегания нефтяных пластов (высокое давление повышенная температура) олефины превращаются в другие органические соединения. В нефтях также содержатся разнообразные гетероорганические соединения включающие в молекулы атомы кислорода серы и азота.
В силу сложности химического состава нефти для переработки нефть сначала разделяют на относительно узкие фракции химический состав которых более однородный. Критерием разделения служат температурные пределы выкипания этих фракций – начало кипения и конец кипения. Первичная переработка нефти на заводе начинается с разделения нефти на фракции по температным пределам выкипания. Затем эти фракции направляются на другие установки с целью получения товарных нефтепродуктов или их компонентов. Разделение нефти на фракции осуществляется на комбинированных установках атмосферно-вакуумных трубчаток (сокращенно АВТ). Эти установки включают обычно блок ЭЛОУ на котором происходит отделение от нефти воды и солей. Комбинирование установок АВТ и блоков ЭЛОУ значительно сокращает расход топлива электроэнергии пара и капитальных затрат то есть является экономически выгодным.
Также в состав комбинированной установки ЭЛОУ-АВТ входят блок атмосферной перегонки (одна или две колонны для разгонки фракций выкипающих до 350оС) блок стабилизации предназначенный для отделения от бензиновых фракций растворенных в них углеводородных газов и сероводорода вакуумный блок на котором происходит разделение на фракции мазута - тяжелой части нефти выкипающей при температуре выше 350оС и блок вторичной ректификации бензиновых фракций.
Выбор схемы установки ЭЛОУ-АВТ определяется характеристиками нефти которая будет перерабатываться на ней мощностью установки по сырью и ассортиментом получаемых на ней нефтепродуктов.
ХАРАКТЕРИСТИКА НЕФТИ
Общая физико–химическая характеристика нефти
Кислотное число мг КОН на 1 г нефти
вспышки в закрытом тигле
температура плавления °С
Состав газов растворенных в нефти
Содержание индивидуальных углеводородов % мас.
Характеристика фракций выкипающих до 2000С
Фракционный состав0С
Октановое число (ММ)
Давление насыщенных паров
Групповой углеводородный состав фракций выкипающих до 2000С
Содержание углеводородов % мас.
нормального строения
Характеристика фракций служащих сырьем для каталитического риформинга
Содержание серы % мас.
Характеристика легких керосиновых фракций
Температура отбора 0С
Выход на нефть % мас.
Фракционный состав 0С
Теплота сгорания (низшая) Джкг
Высота некоптящего пламени мм
Содержание ароматических углеводородов % мас.
Кислотность мг КОН на 100 см3
Йодное число мг йода на 100 г
Фактические смолы мг на 100 см3 фракции
начала кристаллизации
вспышки в закрытом тигле
Характеристика дизельных топлив и их компонентов
Фракционный состав °С
Кислотность мг КОН на 100 см3 топлива
Характеристика сырья для каталитического крекинга
сернокислотных смол % мас.
Содержание парафинонафтеновых углеводородов
Содержание смолистых веществ % мас.
Характеристика остатков
Потенциальное содержание базовых дистиллятных и остаточных масел
Выход дистиллятной фракции или остатка на нефть % мас.
Характеристика базовых масел
Выход базовых масел % мас.
на дистиллятную фракцию или
Разгонка (ИТК) смеси Самотлорских нефтей в аппарате АРН-2 и характеристика полученных фракций
Температура выкипания фракций при 760 мм рт. ст. °С
Продолжение табл. 1.11
По данным таблицы 1.11 строим кривые ИТК плотности и молярной массы приведенные на рис. 1.1.
Дадим классификацию нефти согласно ГОСТ Р 51858-2002.
Данная нефть содержит 096%мас. серы она относится ко второму классу нефтей (содержание серы 061-180 % мас.) то есть является сернистой.
Относительная плотность нефти составляет 08426; содержание парафинов – 230 % мас.; до 200оС выкипает 306 % мас. до 350оС – 582 % мас. (см. табл. 1.1).
Следовательно нефть является легкой и относится к типу № 1.
рис 6.7.frw

орошений и нагруженнных
рис 6.2.frw

рис 6.3.frw

С.рис 6.8.frw

рис 3.4.frw

вакуумного газойля - по схеме с однократным испарением и однократной
рис 6.1.frw

С.рис 3.3 сТАБИЛИЗАЦИЯ.frw

рис 3.1.frw

рис 3.2.frw

с двухкратным испарением и двухкратной ректификацией
рис 4.1.cdw

Технологическая схема установки ЭЛОУ-АВТ