Проект энергоблока с турбиной Т-175-130




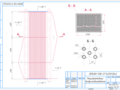
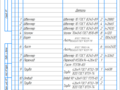
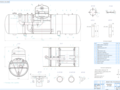
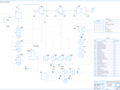
- Добавлен: 24.01.2023
- Размер: 3 MB
- Закачек: 0
Описание
Проект энергоблока с турбиной Т-175-130
Состав проекта
![]() |
![]() |
![]() ![]() ![]() ![]() |
![]() ![]() ![]() ![]() |
![]() ![]() ![]() ![]() |
![]() |
![]() |
![]() |
![]() ![]() ![]() ![]() |
![]() ![]() ![]() ![]() |
![]() |
![]() |
![]() ![]() ![]() |
![]() ![]() ![]() |
![]() ![]() ![]() |
![]() ![]() ![]() |
![]() ![]() ![]() |
Дополнительная информация
Деаэратор ДП-1000.cdw

Подвод основного конденсата
Подвод рециркуляции БЭН
Подвод греющего пара
Подвод пара на барботаж
Подвод рециркуляции впрысков
Подвод дренажа конденсата ПВД (дополн.)
Подвод дренажа конденсата ПВД
Подвод рециркуляции ПЭН
Подвод пара от штоков клапанов
Давление рабочее (избыточное)
Давление пробное при гидроиспытании
Техническая характеристика
* Размеры для справок.
Экспликация штуцеров
Схема 3-х ходового рекуперативного воздухоподогревателя.cdw

Спецификация к деаэратору.spw

ВРБ.ВФ МЭИ.07.140101.06.
Швеллер 10 ГОСТ 8240-89
Уголок 70х45ч5 ГОСТ 8510-89
ВСт3сп5 ГОСТ 14537-79
Переход К530х14-426х12
Круг 10 ГОСТ 2590-88
Тепловая схема энергоблока с турбиной Т-175-130.cdw

Пар нерегулируемого отбора
Цилиндр высокого давления
Цилиндр среднего давления
Цилиндр низкого давления
Охладитель уплотнений
Подогреватель уплотнений
Подогреватель низкого давления
Пиковый водогрейный котел
Тепловой потребитель
Подогреватель сетевой воды
Подогреватель высокого давления
Расширитель непрерывной продувки
Химически обессоленная вода
график к специальной части.cdw

расхода дымовых газов
на воздухоподогреватель
и температуры наружного воздуха
табл.1.1 к бакалавру.DOC
Точка процесса расши-рения
Речь.doc
Вашему вниманию предлагается выпускная работа на тему: «Проект энергоблока с турбиной Т-175-130.
В первой главе РПЗ проведен расчет тепловой схемы энергоблока с турбиной Т-175-130. На основании теплового расчета проведен выбор основного и вспомогательного оборудования. В частности проведен выбор котла Е-820-140 ГМ подогревателей высокого и низкого давления системы регенерации турбины турбогенератора деаэратора сетевых подогревателей питательных насосов конденсатных насосов. Выбрана схема химводоподготовки. Схема ВП включает установки половолоконной ультрафильтрации обратного осмоса установку глубокого дообессоливания на базе ионообменных смол.
Принципиальная тепловая схема энергоблока изображена на плакате 1. Тепловая схема отражает процессы передачи производства и преобразования тепловой энергии в электрическую. Энергоблок мощностью 175 МВт состоит из барабанного парогенератора и одновальной турбоустановки.
Турбина имеет три цилиндра. Свежий пар поступает в цилиндр высокого давления. После ЦВД пар поступает в цилиндр среднего давления. После ЦСД пар поступает в двухпоточный цилиндр низкого давления.
Конденсат турбины подогревается в охладителе уплотнений ОУ подогревателе уплотнений ПУ и охладителе эжектора ОЭ в четырех регенеративных подогревателях низкого давления. После деаэратора вода питательным насосом прокачивается через три подогревателя высокого давления где и осуществляется подогрев питательной воды. Подогрев сетевой воды осуществляется в верхнем и нижнем сетевых подогревателях. Подогрев конденсата питательной и сетевой воды паром отбираемым из проточной части турбины является одним из эффективных способов повышения экономичности тепловых электрических станций.
Турбина имеет 7 регенеративных отборов пара из которых пять нерегулируемых и два теплофикационных отбора для подогрева сетевой воды.
Во второй главе РПЗ проведен конструкторский расчет деаэратора
который включает в себя тепловой и прочностной расчеты.
Деаэраторы в тепловой схеме станции выполняют целый ряд функций: помимо своей основной — деаэрации питательной воды они служат ступенью подогрева в регенеративной схеме подогрева воды аккумулирующей и буферной емкостью между конденсатными и питательными насосами являются источником пара постоянного давления и температуры а также местом ввода в схему разного рода высокопотенциальных дренажей. Однако основной функцией деаэраторов является удаление из питательной воды коррозионно-активных газов. Такими газами являются кислород (02) и углекислый газ (С02).
Сборочный чертеж деаэрационной установки изображен на плакате 2. Установка состоит из деаэрациоиной колонки и бака аккумулятора. Подача деаэрируемой воды осуществляется в верхнюю а греющего пара в нижнюю часть колонки. Поступающая в бак-аккумулятор вода имеет температуру близкую к температуре насыщения. Процесс дегазации воды в основном осуществляется в колонке.
В данной работе был проведён тепловой расчёт деаэратора на основании которого в качестве прототипа был выбран деаэратор повышенного давления струйно-барботажного типа ДП-1000.
В специальной части работы проведен тепловой расчет и компоновка трубчатого воздухоподогревателя для парового котла марки Е-820-140 ГМ. Схематический чертеж воздухоподогревателя изображен на плакате 3. ВП имеет три хода по воздуху один ход по дымовым газам и шахматное расположение трубного пучка. Также была оценочно установлена зависимость между температурой окружающего воздуха и необходимым объемом уходящих газов подаваемых на воздухоподогреватель и обеспечивающих расчетную температуру воздуха перед топкой при различных нагрузках котла. Графики зависимости изображены на плакате 3. Как видно из графиков при повышении температуры воздуха на входе в воздухоподогреватель нужен меньший расход дымовых газов обеспечивающих расчетную температуру воздуха перед топкой. Также были кратко рассмотрены технические решения обеспечивающие регулирование объема уходящих газов подаваемых на воздухоподогреватель.
В разделе природоохранные мероприятия рассмотрены методы очистки сточных вод тепловых электрических.
Доклад окончен. Благодарю за внимание!
содержание.doc
1 Расчет принципиальной тепловой схемы энергоблока с турбиной Т-175-130 6
2 Определение параметров пара и воды 9
3 Выбор основного и вспомогательного оборудования 34
4 Выбор схемы ХВО 46
Конструкторская часть 55
1 Назначение устройство и работа деаэратора 55
2. Исходные данные 57
3. Тепловой расчет деаэратора 58
4. Расчет на прочность элементов деаэратора 64
Специальная часть 66
1. Назначение устройство и работа воздухоподогревателя 66
2. Исходные данные 69
3. Расчетная часть 70
Природоохранные мероприятия 77
Список литературы 89
Приложение А (Деаэратор).
Пояснительная записка.doc
Технологическая часть состоит из расчета принципиальной схемы определения балансов пара и воды энергетических показателей выбора основного и вспомогательного оборудования данного энергоблока выбора схемы химической подготовки питательной воды.
Конструкторская часть заключает в себе тепловой и прочностной расчет деаэратора.
Специальная часть заключает в себе тепловой расчет и компоновку воздухоподогревателя.
Энергетика является важнейшей и необходимой отраслью экономики России. Энергетика переживает в последнее время наиболее сложный период в своем существовании и развитии. Производство электроэнергии является одним из главных показателей экономического уровня страны и отражает общее состояние производственных сил. Энергетика обеспечивает бесперебойную работу промышленности сельского хозяйства транспорта коммунальных хозяйств. Стабильное развитие экономики невозможно без постоянно развивающейся энергетики. Часто электростанции обеспечивают также предприятия и жилые здания паром и горячей водой.
Принципиальная тепловая схема (ПТС) характеризует сущность и совершенство основного и технологического процесса тепловой электрической станции – процесса преобразования тепловой энергии сжигаемого топлива в электрическую и тепловую энергию отпускаемую потребителям. Она определяет тепловую экономичность отпуска потребителям от ТЭС электрической и тепловой энергии.
ПТС включает основное и вспомогательное тепломеханическое оборудование технологического цикла: парогенераторы паровые турбины регенеративные подогреватели питательной воды подогреватели сетевой воды насосы различного назначения деаэраторы испарители расширители.
При составлении ПТС учитываются возможные режимы работы станции. Расчёт ПТС производят с целью определения параметров и величин потоков рабочего тела в различных участках технологического цикла а также мощности и показателей тепловой экономичности.
ТЕХНОЛОГИЧЕСКАЯ ЧАСТЬ
1 Расчет принципиальной тепловой схемы энергоблока с турбиной
Исходные данные для расчета тепловой схемы ТЭЦ:
Тип турбины Т-175-130;
Электрическая мощность 175 МВт;
Давление свежего пара 12.75 МПа;
Температура свежего пара 550 °С;
Температура охлаждающей воды конденсатора 15 °С.
1.1Описание энергоблока с турбиной Т-175-130
Расчёт принципиальной тепловой схемы проведён с целью определения параметров и величины потоков рабочего тела (пара конденсата и питательной воды) в различных участках технологического цикла а также мощности и показателей тепловой экономичности.
Энергоблок мощностью 175 МВт состоит из барабанного парогенератора и одновальной конденсационной турбоустановки Т-175-130 номинальной мощностью 175 МВт с параметрами свежего пара:
давление Р=130 ат. (1275 МПа);
Принципиальная тепловая схема энергоблока приведена на рисунке 1.1
Турбина имеет три цилиндра. Свежий пар поступает в ЦВД включающий регулирующую одновенечную ступень и одиннадцать ступеней активного типа. После ЦВД пар поступает в ЦСД. Цилиндр среднего давления имеет одиннадцать ступеней. После ЦСД пар поступает в двухпоточный цилиндр низкого давления с четырьмя ступенями в каждом потоке.
Конечное давление пара в турбине перед конденсатором Рк=0039 ат. (00039 МПа).
Турбина имеет 7 регенеративных отборов пара из которых пять нерегулируемых и два теплофикационных отбора для подогрева сетевой воды.
Подогрев конденсата и питательной воды паром отбираемым из проточной части турбины является одним из эффективных способов повышения экономичности тепловых электрических станций. Регенеративный подогрев существенно сокращает удельный расход топлива на выработку электроэнергии. Основным преимуществом регенерации является уменьшение расхода пара в конденсатор и потерь тепла в нём. Регенеративный подогрев питательной воды производится последовательно в нескольких подогревателях что существенно повышает тепловую экономичность цикла. В зависимости от начальных параметров и исходной температуры нагреваемого конденсата теплофикационных отборов дополнительная выработка электроэнергии на регенеративных отборах ТЭС составляет 8-35 % от выработки на внешнем теплопотреблении.
Подогрев питательной воды осуществляется в поверхностных и смешивающих (при непосредственном контакте воды с паром) регенеративных подогревателях. Основными подогревателями в тепловой схеме ТЭС являются поверхностные. В качестве смешивающегося подогревателя зачастую используется деаэратор служащий в основном для удаления вредных примесей газов из рабочего тела. В смешивающих подогревателях недогрев равен нулю что обусловливает большую их тепловую экономичность.
Конденсат турбины подогревается в охладителе уплотнений ОУ подогревателе уплотнений ПУ и охладителе эжектора ОЭ в четырех регенеративных подогревателях низкого давления. После деаэратора вода питательным насосом прокачивается через три подогревателя высокого давления. Все ПВД имеют встроенные пароохладители а также снабжены встроенными охладителями дренажа помимо основной конденсирующей поверхности что повышает эффективность регенеративного цикла. Охладитель пара использует теплоту перегрева пара для дополнительного подогрева питательной воды на 2-5 °С выше температуры воды на выходе из основной поверхности. Охладитель конденсата охлаждает конденсат греющего пара ниже температуры насыщения что уменьшает вытеснение пара более низких отборов в случае каскадного слива конденсата из подогревателя. Установка охладителей пара и конденсата даёт экономию топлива до 05-1 %.
Дренажи ПВД сливаются каскадно в деаэратор. Дренажи ПНД4 сливаются каскадно в ПНД5 . Дренажи подогревателей ПНД5 в СМ1 ПНД6 и верхней ступени сетевого подогревателя (СП2) в СМ2 нижней ступени сетевого подогревателя (СП1) в СМ3 а дренажи ПНД7 ПУ ОУ и ОЭ поступают в конденсатосборник конденсатора.
Рисунок 1.1 – ПТС ТЭЦ с турбиной Т-175210-130
2 Определение параметров пара и воды
На рисунке 1.2 показана схема процесса работы пара в HS-диаграмме.
Параметры и величины потоков рабочего тела (пара конденсата и питательной воды) в различных участках технологического цикла приведены в таблице 1.1 где приняты следующие обозначения:
Pп Tп hп - давление (МПа) температура ( °С) и энтальпия (кДжкг) пара;
Pп - давление пара перед подогревателями регенеративной установки (МПа);
t'н h'п - температура ( °С) и энтальпия (кДжкг) конденсата при давлении насыщения;
q - недогрев воды в поверхностных теплообменниках на выходе из встроенного пароохладителя (°С);
Pв Tв hв - давление (МПа) температура (°С) и энтальпия (кДжкг) воды после регенеративных подогревателей;
х – степень сухости;
Точка процесса 0' отвечает состоянию пара перед регулирующей ступенью ЦВД.
2.1Давление в конденсаторе
Температура насыщения в конденсаторе:
tо.в = 15 оС - температура охлаждающей воды конденсатора;
t = 8 ° С - нагрев воды в конденсаторе;
tк = 55 °С - недогрев воды до состояния насыщения в конденсаторе;
tк = tо.в. + t + tк =15 + 8 + 55 = 285°С.
По [1] находим давление в конденсаторе: рк = 0.0039 МПа.
2.2 Построение процесса расширения пара в турбине
Параметры свежего пара перед регулирующим клапаном:
Рп = 127 МПа tп =550°C hп = 34745 кДжкг ;
pв = 0045 · р0 = 0045 ·127 = 06 МПа - потери давления на паровпуске;
ро' = р0 – рв =127 – 06 = 121 Мпа.
2.3Давление в нагнетательном патрубке конденсатного насоса
Рkн = Рд + Рнив + pэл (1.1)
где рд = 0.59 МПа - давление в деаэраторе питательной воды;
Рнив = = = 0.294 МПа
ρ = 1000 кг м3 - плотность воды от насоса до деаэратора; Н = 30м - разность уровней в конденсаторе и ДПВ; pэл = 0.15 МПа - потери давления в одном элементе; Рkн = 0.59 + 0.294 + 0.15 · 7 = 0.98 МПа.
2.4Давление в нагнетательном патрубке питательного насоса
Рnн =Рб + Рб + Рpnк + Рэк + Рnвд + Рзап + Рнив (1.2)
где рб = 159 МПа - избыточное номинальное давление в барабане;
Рб = 0.08 · р6 = 0.08 · 15.9 = 1272 МПа - запас давления на открытие
предохранительных клапанов;
Рpnк =16 МПа - перепад давления в регулирующем питательном клапане
Рэк = 0.05 · рб = 0.05 · 15.9 = 0.795 МПа - потери давления в экономайзере;
Рnвд = 0.5 МПа - потери давления в одном ПВД;
Рзап = 0.08 · Рnвд =0.08 ·05 · 3 = 0.12 МПа;
ρ = 822 м3 кг- средняя плотность питательной воды от насоса до барабана;
Н = 30 м - высота уровня воды от оси насоса до уровня в барабане;
рпн = 15.9 + 1.272 + 1.6 + 0.795 + 0.5 · 3 + 0.12 + 0.22 = 21.4 МПа.
рв = рд + - р = 0.6 + - 0.06 = 0.76 МПа –давление
ρ = 908.6 кг м3 - плотность воды от деаэратора до питательного насоса;
Н = 25м - высота столба жидкости от уровня воды в деаэраторе до уровня
р = 006 МПа - потери давления от деаэратора до питательного насоса.
2.5 Определение параметров конденсата и воды на участке регенерации низкого давления
По [1] находим энтальпию пара в i-ом отборе:
р7 = 0.037 МПа х7 = 0906 h7 = 24145 кДж кг;
р6=008 МПа х6 = 0933 h6 = 2513 кДжкг;
р5 = 0.277 МПа х5 = 0984 h5 = 2687 кДжкг;
р4 = 0.576 МПа t4 = 177°С h4 = 2797 кДж кг.
Принимаем потери давления от камеры отбора до ПНД - 5% [2] тогда рнпнд = 0.95 · р
По [1] находим по рнпнд температуру и энтальпию насыщения греющего пара.
рнпнд1 = 0.95 · р7 = 0.95· 0.037 = 0.035 МПа;
tнпнд1 = 73 оС hнпнд1 = 30604 кДжкг;
рнпнд2 = 0.95 · р6 = 0.95 · 0.08 = 0.076 МПа;
tнпнд2 = 92 оС hнпнд2 = 39164 кДжкг;
рнпнд3 = 0.95 · р5 = 0.95 · 0.277 = 0.263 МПа;
tнпнд3 = 12911 оС hнпнд3 = 54259 кДжкг;
рнпнд4 = 0.95 · р4 = 0.95 · 0.576 = 0547 МПа;
tнпнд4 = 15527 оС hнпнд4 = 65503 кДжкг.
Недогрев воды до температуры насыщения принимаем tnнд= 3 °С [2]
тогда температура конденсата:
Давление конденсата:
По [1] находим энтальпию питательной воды при: tвпнд и рвпнд:
hвпнд1 = 2936 кДжкг;
hвпнд2 = 3736 кДжкг;
hвпнд3 = 53021 кДжкг;
hвпнд4 = 64224 кДжкг.
2.6Определение параметров конденсата и воды на участке регенерации высокого давления
р3 =147 МПа t3 =274 °C h3 = 2978 кДжкг;
р2 = 222 МПа t2 = 320°C h2 = 3056 кДжкг;
р1 = 330 МПа t1 = 370°C h1=3156 кДжкг.
Принимаем потери давления от камеры отбора до ПВД - 5% [2] тогда
рнпвд = 0.95 · pi - давление насыщения греющего пара в ПВД.
По [1] находим по рнпвд температуру и энтальпию насыщения греющего пара.
рнпвд5 = 0.95 · р3 = 0.95 · 147 = 1396 МПа;
tнпвд5 = 19493 оС hнпвд5 = 82961 кДжкг;
рнпвд6 = 0.95 · р2 = 0.95· 222 = 2109 МПа;
tнпвд6 = 21508 оС hнпвд6 = 92099 кДжкг;
рнпвд7 = 0.95 · р1= 0.95 · 33 = 3135 МПа;
tнпвд7 = 23631 оС hнпвд7 = 101998 кДжкг.
Недогрев воды до температуры насыщения принимаем tnвд =3 °С [2] тогда температура питательной воды:
Давление питательной воды:
По [1] находим энтальпию питательной воды при: tвпвд и рвпвд:
hвпвд5 = 82546 кДжкг;
hвпвд6 = 91399 кДжкг;
hвпвд7 = 100943 кДжкг.
2.7Балансы пара и воды
Расчёт тепловой схемы ведётся при расходе свежего пара на турбину D0=210 кгc.
2.7.1 Определение параметров пара и воды в установке использования продувки.
Паровая нагрузка парогенератора определяется с учётом потерь на продувку и протечек через уплотнения.
Величину продувки принимаем равной 15% от расхода свежего пара D0 то есть:
Dпр=0015×210=315 кгс.
Величину протечек через уплотнения направляемых в ПВД 6 принимаем Dу=20 кгс.
Величину протечек направляемых в охладитель уплотнений принимаем 1% то есть
Сумма протечек через уплотнения:
Утечки пара подводимого к турбине:
Dут=0016×210=336 кгс.
Паровая нагрузка парогенератора:
Dпг=210+3.36=213.36 кгс.
Расход питательной воды:
Dпв=21336+315=21651 кгс.
Расход пара из уплотнений штоков клапанов:
Dуш=(00008÷0003) ×D0 (1.9)
Dуш = 0003×210 = 063 кгс
Расход пара на концевые уплотнения 0.1% от D0:
Dук=(00015÷0002) ×D0 (1.10)
Dук=00015×210=0315 кгс
Расход пара на эжектор:
Суммарный расход пара на эжектор и уплотнения:
Dэу=252+0315=2835 кгс
Для использования тепла воды продувки парогенератора предусмотрена установка расширителя для сепарации продувочной воды. Параметры рабочих сред в расширителе приведены в таблице 1.2
Таблица 1.2 Параметры пара и воды в расширителе
где Pпр МПа - давление теплоносителей;
tпр °С - температура теплоносителей;
hпр кДжкг - энтальпия теплоносителей.
Определяем выход пара из расширителя . Из уравнения теплового баланса расширителя имеем:
где h=0.98 – коэффициент учитывающий потери тепла в расширителе;
Расход продувочной воды выходящей из расширителя:
D'пр1=Dпр-D''пр1 (1.14)
D'пр1=3.15-1.39=1.76 кгс.
Пар из расширителя поступает в деаэратор питательной воды (ДПВ) а продувочная вода – в охладитель продувки ОП где подогревает воду для водоподготовки.
2.7.2Определение расхода пара на теплофикацию
Параметры пара и воды сетевой подогревательной установки приведены в таблице 1.3. Схема движения рабочих сред в сетевых подогревателях показана на рисунке 1.3.
По графику температуры сетевой воды определяем температуру прямой tпс=84°С и обратной tос=46°С сетевой воды.
Рисунок 1.3 – Схема движения пара и воды в сетевых подогревателях
а) в верхнем; б) в нижнем.
По заданному графику сетевой воды определяем температуру прямой и обратной сетевой воды:°С °С.
Температура сетевой воды после нижнего сетевого подогревателя:
Определяем энтальпии (принимаем МПа):
Принимаем недогрев сетевой воды
Температура насыщения в нижнем и верхнем подогревателях:
По [1] в состоянии насыщения по определяем давление греющего пара в нижнем и верхнем сетевых подогревателях:
Определяем давление в шестом и седьмом отборах с учётом потерь:
Таблица 1.3 Параметры пара и воды сетевых подогревателей
Нижний подогреватель
Верхний подогреватель
Давление в отборе Р МПа
Давление в подогревателе Р` МПа
Отдаваемое тепло q кДжкг
Конденсат греющего пара
Температура насыщения t`°С
Энтальпия при насыщении h` кДжкг
Продолжение таблицы 1.3
Температура на входе tв°С
Энтальпия на входе hв кДжкг
Температура на выходе tв°С
Энтальпия на выходе hв кДжкг
Подогрев в подогревателе tв кДжкг
Расход сетевой воды
где Qт=3198 МВт – отопительная нагрузка;
hпс=3523 кДжкг - энтальпия сетевой воды на выходе из верхнего подогревателя;
hoс=1933 кДжкг - энтальпия сетевой воды на входе в нижний подогреватель.
Тепловой баланс нижнего сетевого подогревателя:
Dнс×qнс=Gсв×tнсhп (1.21)
где Dнс – расход пара на нижний сетевой подогреватель;
qнс=2327 кДжкг- тепло отдаваемое паром в подогревателе;
tнс=794 кДжкг- нагрев сетевой воды в подогревателе;
hп=0995 – коэффициент учитывающий потери тепла в подогревателе.
Тепловой баланс верхнего сетевого подогревателя:
Dвс×qвс=Gсв×tвсhп (1.23)
где Dвс – расход пара на верхний сетевой подогреватель;
qвс=2280 кДжкг- тепло отдаваемое паром в подогревателе;
tвс=796 кДжкг- нагрев сетевой воды в подогревателе;
2.7.3Определение параметров пара и воды на участке линий основного конденсата:
ОЭ – охладитель эжектора;
ОУ – охладитель уплотнения;
ПУ – подогреватель уплотнения;
КРУК – клапан регулятора уровня в конденсаторе;
Узел рециркуляции основного конденсата:
tрецв = tОЭ+tОУ+tПУ = 4+4+85 = 165 (1.24)
tПУв = tк+tрецв = 285+165 = 45 где (1.25)
tПУв – температура воды перед ПНД1.
2.7.4Расчёт группы подогревателей высокого давления
Рисунок 1.4 – Схема включения ПВД
Тепловой баланс ПВД 7 (П-1)
Уравнение теплового баланса ПВД7 :
Dп1(hп1- h'п1) =Dпв(hв1- hв2)п
Dп1= Dпв(hв1- hв2) (hп1- h'п1) п (1.26)
где Dп1- расход греющего пара на ПВД7;
hп1 =3156 кДжкг – энтальпия пара первого отбора;
h'п1=101998 кДжкг – энтальпия конденсата греющего пара;
hв1=100943 кДжкг – энтальпия питательной воды на выходе из П1 (ПВД7);
hв2=91399 кДжкг – энтальпия питательной воды на входе в П1;
Dпв=216.51 кгс- расход питательной воды;
п =0995 – КПД теплообменника.
Тепловой баланс ПВД- 6 ( П-2)
Уравнение теплового баланса ПВД6 :
Dп2(hп2- h'п2) + Dп1(h'п1- h'п2) =Dпв(hв2- hв3)п
Dп2= [Dпв(hв2- hв3)п - Dп1(h'п1- h'п2)] (hп2- h'п2) (1.27)
где hп2 =3056 кДжкг – энтальпия пара второго отбора;
h'п2=92099 кДжкг – энтальпия конденсата греющего пара второго отбора;
hв3=82546 кДжкг – энтальпия питательной воды на входе в П2 (ПВД-6);
Dп2 – расход греющего пара;
Тепловой баланс ПВД –5 (П-3)
Подогреватель ПВД5 рассчитывается с учётом нагрева воды в питательном насосе.
Подогрев воды в питательном насосе характеризуется внутренней работой сжатия воды:
tн=103×vср×(Pн-Pв)hн (1.28)
где vср=00011 м3кг – средний удельный объём воды;
Рн=2194 МПа – давления воды в нагнетательном патрубке пит. насоса;
Рв=076 МПа – давления воды во всасывающем патрубке пит. насоса;
hн=0845 – КПД насоса с учётом объёмных и механических потерь.
tпн=103×0.0011×(214-076)0845=2686 кДжкг.
Энтальпия воды после питательного насоса:
hв.пн=66765+2686=69452 кДжкг
Уравнение теплового баланса ПВД5 (П-3) :
Dп3(hп3- h'п3) + (Dп1+ Dп2)(h'п2- h'п3) =Dпв(hв3- hв.пн)п
где hп3 =2978 кДжкг – энтальпия пара третьего отбора
h'п3=82961 кДжкг – энтальпия конденсата греющего пара третьего отбора
Dп3=12.53 кгс – расход греющего пара на ПВД5;
2.7.5 Деаэратор питательной воды (ДПВ)
Рисунок 1.5 - Потоки пара и воды через ДПВ
Искомыми величинами при расчёте деаэратора являются расход пара в деаэратор Dд и расход основного конденсата на входе в деаэратор Dок.
Материальный баланс деаэратора питательной воды
Dок+Dшт+Dп1+Dп2+Dп3+ Dу+ D''пр +Dд = Dпв+Dэу (1.31)
Dок= Dпв+Dэу–Dд–Dшт–Dп1–Dп2 –Dп3- Dу–D''пр
Dок=21651+2835– Dд –063–972–857–1253–2–139
Тепловой баланс деаэратора питательной воды
Dд×h3+(Dп1+Dп2+Dп3+Dу)×h'п3+Dшт×hшт+Dок×hв4+D''пр×h'пр=(Dпв×hв.д+Dэ.у×hд)п (1.32)
где hшт=3474 кДжкг – энтальпия пара из уплотнений штоков клапанов тогда
Dд×2978+(972+857+1253+2)×82961+063×3474+Dок×64224+
+139×2756139=(216.51×66765+2835×2978)0995
Решая систему уравнений получим: Dд=0865 кгс Dок=18364 кгс.
2.7.6 Подогревательная установка низкого давления
Рисунок 1.6 – Схема включения ПНД
Расчёт группы ПНД заключается в совместном решении тепловых и материальных балансов теплообменников.
Тепловой баланс ПНД-4 (П-4)
ТБ: Dп4(hп4- h'п4) =Dк4(hв4- hсм1)п где (1.34)
Dп4 – расход греющего пара на ПНД-4
hп4=2797 кДжкг – энтальпия греющего пара четвёртого отбора
h'п4=65503 кДжкг – энтальпия конденсата греющего пара четвёртого отбора
Dк4 - расход основного конденсата через ПНД-4
hв4=64224 кДжкг – энтальпия основного конденсата на выходе из ПНД-4
hсм1 – энтальпия основного конденсата в точке смешения 1
Dп4× (2797–65503)=18548× (64224 –hсм1)0995
Тепловой баланс ПНД-3 (П-5)
ТБ: Dп5(hп5- h'п5)+ Dп4(h'п4- h'п5) =Dк3(hв5- hсм2)п где (1.35)
Dп5 – расход греющего пара на ПНД-3
hп5=2687 кДжкг – энтальпия греющего пара пятого отбора
h'п5=54259 кДжкг – энтальпия конденсата греющего пара пятого отбора
Dк3 - расход основного конденсата через ПНД-3
hв5=53021 кДжкг – энтальпия основного конденсата на выходе из ПНД-3
hсм2 – энтальпия основного конденсата в точке смешения 2
Dп5× (2687–54259)+ Dп4× (65503–54259)= Dк3 × (53021 - hсм2)0995
Тепловой баланс ПНД-2 (П-6)
ТБ: Dп6(hп6- h'п6) =Dк2(hв6- hсм3)п где (1.36)
Dп6 – расход греющего пара на ПНД-2
hп6=2513 кДжкг – энтальпия греющего пара шестого отбора
h'п6=39164 кДжкг – энтальпия конденсата греющего пара шестого отбора
Dк2 - расход основного конденсата через ПНД-2
hв6=3736 кДжкг – энтальпия основного конденсата на выходе из ПНД-2
hсм3 – энтальпия основного конденсата в точке смешения 3
Dп6× (2513–39164)= Dк2 × (3736 - hсм3)0995
Тепловой баланс ПНД-1 (П-7)
ТБ: Dп7(hп7- h'п7) =Dк1(hв7- hв)п где (1.37)
Dп7 – расход греющего пара на ПНД-1
hп7=24145 кДжкг – энтальпия греющего пара седьмого отбора
h'п7=30604 кДжкг – энтальпия конденсата греющего пара седьмого отбора
Dк1 - расход основного конденсата через ПНД-1
hв7=2936 кДжкг – энтальпия основного конденсата на выходе из ПНД-1
hв=230 кДжкг – энтальпия конденсата перед ПНД-1 (П-7)
Dп7× (24145–30604)= Dк1 × (2936 - 230)0995
МБ: Dк4= Dк3+ Dп4+ Dп5 (1.38)
ТБ: Dк4 ×hсм1 см=(Dп4+ Dп5) × h'п5+ Dк3× hв5 (1.39)
Dк4 ×hсм1 0995=(Dп4+ Dп5) × 54259+ Dк3× 53021
МБ: Dк3= Dк2+ Dп6+ Dвс (1.40)
ТБ: Dк3 ×hсм2 п=Dк2 × hв6+ Dп6× h'п6+ Dвс× h'вс (1.41)
Dк3 ×hсм2 0995=Dк2 × 3736+ Dп6× 39164+ 706× 3845
МБ: Dк2= Dк1+ Dнс (1.42)
ТБ: Dк2 ×hсм3 п= Dк1× hв7+ Dнс× h'нс (1.43)
Dк2 ×hсм3 0995= Dк1× 2936+ 69× 306
Dп4× (2797–65503)=18364× (64224 – hсм1)0995
Dп5× (2687–54259)+ Dп4× (65503–54259)= Dк3 × (53021 – hсм2)0995
Решая систему из семи уравнений получим:
Dп4=9765 кгс Dкз=163539 кгс hсм1=52891 кДжкг
Dп5=10336 кгс Dк2=89889 кгс hсм2=3887 кДжкг
Dп6=305 кгс Dк1=20889 кгс hсм3=3020 кДжкг
2.7.7 Уравнение материального баланса конденсатора. Поток конденсата
Dв.к.= Dк1–Dп1–Dоу–Dэу–Dв (1.44)
Dв.к.=20889–0633–21–2835–512 = 10201 кгс
где Dв – добавочная химически очищенная вода.
2.7.8 Материальный баланс турбины
Паровой баланс турбины представляет собой сравнение потоков пара входящих в конденсатор Dп.к и конденсата выходящего из конденсатора Dв.к.
Поток пара входящий в конденсатор
Dп.к=D0-Dуп-Dуш-SDi (1.45)
где SDi – суммарное количество отобранного пара в i-ых отборах кгс. Расходы пара в отборы приведены в таблице 1.4
Таблица 1.4 Расходы пара в отборы
D1+ D2+ D3+ D4+ D5+ D6+ D7
Подставляя значение SDi получим
Dп.к=210–41–063–195069=10201 кгс.
Погрешность материального баланса
2.7.9 Энергетический баланс турбоагрегата.
Энергетический баланс турбоагрегата заключается в определении полной мощности турбины SWi путём суммирования мощностей выработанных в каждом отсеке Wi.
Электрическая мощность отсека
Hi – действительный теплоперепад в отсеке кДжкг.
Данные по выработке мощности в отсеках приведены в таблице 1.5
Таблица 1.5 Мощность отсеков турбины.
Интервал давлений МПа
Пропуск пара через отсек
Электрическая мощность турбоагрегата
где hэм=0.98 – коэффициент учитывающий электромеханические потери мощности.
Wэ=184465×0.98=180776 МВт.
2.8Энергетические показатели энергоблока
Полный расход тепла на турбоустановку
Qту=D0×(h0-hв7) (1.49)
Qту=210×(3474-100943)=51756 МВт.
Расход тепла на отопление
Q0т=Qт×0.5×(k1+k2) (1.50) Q0т=319.825×0.5×(1.002+1.001)=320.305 МВт.
Расход тепла на турбоустановку по производству электроэнергии
Qэту=Qту-D``пр1×(h``пр1-hпв)-Qт (1.51)
где hпв=hв7 – энтальпия питательной воды кДжкг.
Qэту=51756×103–1.39×(2756.139–100943) –319.825×103=195307 МВт.
Коэффициент полезного действия по производству электроэнергии
hэту=180776195307=0925
Удельный расход тепла на производство электроэнергии
qэту=3600hэту (1.53)
qэту=36000.925=388941 кДж(кВт×ч).
Тепловая нагрузка парогенераторной установки
Qпг=Dпг×(hпг-hпв)+Dпр×(hпр-hпв) (1.54)
где hпг=3502.706 кДжкг–энтальпия пара в парогенераторе (при Рпг=13.8 МПа tпг=565 °С)
Qпг=213.36×(3502.706–1009.43)+3.15×(1598.757–1009.43)=533.822 МВт.
Коэффициент полезного действия трубопроводов
hтр=51756533822=0969
Коэффициент полезного действия ТЭЦ по производству электроэнергии
hэс=hэту×hтр×hпг (1.56)
где hпг=0.92 – КПД парогенератора
hэс=0.925 ×0.969×0.92=0.825
Коэффициент полезного действия ТЭЦ по производству и отпуску тепла на отопление
hтс=hт×hтр×hпг (1.57)
hтс=0.995×0.969×0.92=0.887
Коэффициент ценности тепла отпускаемого из 6-го отбора
hк = 2294 кДжкг – энтальпия пара в конденсаторе при фактической мощности турбоагрегата но при условии работы его в конденсационном режиме;
Коэффициент ценности тепла отпускаемого из 7-го отбора
Увеличение расхода тепла на производство электрической энергии при отсутствии отпуска тепла внешним потребителям из 6-го отбора
dQэ2=Qт×(1-Kцт6) (1.60)
dQэ2=319.825×(1–0.246)=241148 МВт.
Увеличение расхода тепла на производство электрической энергии при отсутствии отпуска тепла внешним потребителям из 7-го отбора
dQэ1=Qт×(1-Kцт7) (1.61)
dQэ1=319.825×(1–0.139)=27535 МВт.
Суммарное увеличение расхода тепла на производство электрической энергии при отсутствии отпуска тепла внешним потребителям
dQэту=dQэ2+dQэ1 (1.62)
dQэту=241.148+27535=5165 МВт.
Коэффициент отнесения затрат топлива энергетическими котлами на производство электрической энергии
Общий расход условного топлива энергетическими котлами
где Qнр=29307.6 кДжкг – теплота сгорания условного топлива;
Расход условного топлива на выработку электрической энергии
Bээ=7127×0.69=4917 кг утс.
Расход условного топлива на выработку тепловой энергии
Bтэ=7127-4917=2216 кг утс.
Удельный расход условного топлива на производство электрической энергии
Удельный расход условного топлива на производство и отпуск тепловой энергии
3Выбор основного и вспомогательного оборудования
3.1 Выбор основного оборудования энергоблока Т-175-130
Выбор оборудования для энергоблока будем производить исходя из теплового расчета принципиальной тепловой схемы турбоустановки Т-175-130 а также рекомендаций по выбору теплообменного оборудования для данной турбины согласно литературным источникам.
3.1.1Выбор турбоагрегата
Турбина Т-175-130 мощностью 175 МВт сконструирована на начальные параметры пара 1275 МПа и 550 ºС. Давление в конденсаторе составляет 39 кПа частота вращения 50 с -1.
Турбина выполнена трехцилиндровой и имеет 7 регенеративных отборов.
Регенеративная система турбоустановки включает три подогревателя высокого давления деаэратор и четыре подогревателя низкого давления. Температура питательной воды 233 ºС.
3.1.2 Выбор парового котла
Выбор типа котлов в основном ограничивается двумя типами: барабанными и прямоточными. При выборе котлов помимо начальных параметров пара учитывают качество исходной воды и величину потерь теплоносителя водный режим стоимость котла график нагрузки станции снижение параметров пара на пути от парогенератора до турбоустановки и многое другое.
Основными характеристиками паровых котлов являются их производительность и параметры пара после первичного и промежуточного перегревателей. Производительность выбираемого парового котла должна учитывать увеличение расхода пара на турбину за счет повышения давления в конденсаторе в летнее время утечек пара и конденсата включения сетевых установок для отпуска тепла и других расходов.
В соответствии с этим производительность парового котла выбирается по максимальному пропуску свежего пара через турбину с учетом расхода пара на собственные нужды электростанции и обеспечения некоторого запаса для использования вращающегося резерва и других целей.
С учетом гидравлических и тепловых потерь в паровом тракте блока от котла до турбины давление пара за котлом должно быть выше номинального для турбины на 4-9% а температура на 1-2%.
Для данного расхода пара выбираем котел марки Е-820-140 ГМ (БКЗ-820-140ГМ5) производительностью 820 абсолютное давление пара 13.8 КПД котла масса-3690 .[3 с. 12]
3.1.2Выбор турбогенератора
Выбор турбогенератора производится по характеристикам турбины. Классификация турбогенератора производится прежде всего по системе охлаждения. По принципу охлаждения все турбогенераторы подразделяются на генераторы с косвенным (поверхностным) охлаждением непосредственным охлаждением проводников обмоток статора и ротора со смешанным охлаждением. В качестве охлаждающих агентов применяются воздух водород дистиллированная вода трансформаторное масло и негорючий диэлектрик. Для данной мощности турбины выбираем турбогенератор ТВВ–220–2Е с водородно-водяным охлаждением мощностью 220 МВт 2 – число полюсов Е – единая серия. [3 с. 605]
3.2 Выбор вспомогательного оборудования
3.2.1Выбор подогревателей низкого давления
Подогреватели высокого давления (ПВД) располагаются между котельным агрегатом и питательным насосом используют теплоту пара отбираемого из части высокого и среднего давления турбины. Давление питательной воды в них определяется напором развиваемым питательным насосом.
ПВД предназначены для регенеративного подогрева питательной воды за счет охлаждения и конденсации пара. Все три подогревателя поверхностного типа. Для более полного использования теплоты подводимого пара предусматриваются специальные поверхности нагрева для охлаждения пара до параметров близких к состоянию насыщения (охладители перегрева) и для охлаждения конденсата пара (охладители конденсата).
Выбор ПВД производим исходя из данных расчета тепловой схемы определяя площадь теплообмена (по собственно подогревателю).
ПВД7: Исходные данные берем из расчета тепловой схемы:
Dпв=21651 кгс t н7= 23631 0С; hв1=100943 кДжкг; tв2=21208 0С;
Принимаем что недогрев воды до t н в зоне СП: Δtм=6 0С .
Коэффициент теплопередачи примем k=2.8 кВт(м2 · 0С) [3].
Значение температурного напора при принятых исходных данных равно:
Из уравнения теплового баланса Q= Dпв(hв1 - hв2)= k ·Fто·Dtср находим количество теплоты передаваемое греющим паром в подогревателе:
Выбираем ПВД7 типа ПВ – 800 – 230 – 32 [3 с. 314].
ПВД с площадью теплообмена 800 м2 предельное давление воды 230 кгссм2 расчетный расход воды 850 тч максимальное давление пара 32 МПа.
ПВД6: Dпв=21651 кгс t н6= 21508 0С; hв2=91399 кДжкг; tв3=191930С; hв3=82546 кДжкг.
Значение температурного напора рассчитываем по формуле (1.71):
Из уравнения теплового баланса Q = Dпв(hв2 - hв3) = k ·Fто·Dtср находим количество теплоты передаваемое греющим паром в подогревателе:
Тогда Fто рассчитываем по формуле (1.73):
Выбираем ПВД6 типа ПВ – 800 – 230 – 21 [3 с. 314].
ПВД с площадью теплообмена 800 м2 предельное давление воды 230 кгссм2 расчетный расход воды 850 тч максимальное давление пара 21 МПа
ПВД5: Dпв=21651кгс t н5= 194930С;hв3=82546 кДжкг; tв.пн=158180С;hв.пн=66765 кДжкг.
Из уравнения теплового баланса Q = Dпв(hв3 - hв.пн) = k ·Fто·Dtср находим количество теплоты передаваемое греющим паром в подогревателе:
Выбираем ПВД5 типа ПВ – 760 – 230 – 14 [3 с. 314].
ПВД с площадью теплообмена 760 м2 предельное давление воды 230 кгссм2 расчетный расход воды 850 тч максимальное давление пара 14 МПа.
3.2.2Выбор подогревателей низкого давления
Подогреватели низкого давления (ПНД) располагаются между конденсатором турбины и питательным насосом. Движение конденсата в них происходит под давлением конденсатного насоса.
Рассмотрим подробно расчет ПНД №1.
Исходные данные берем из расчета тепловой схемы:
t н1= 73 0С; hв7=2936 кДжкг; hв=230 кДжкг; tпу в= 450С; Dк1 =20889 кгс.
Коэффициент теплопередачи примем k=3.0 кВт(м2·0С) [3].
Принимаем недогрев воды до t н : Δtм=3 0С.
Из уравнения теплового баланса Q = Dк1(hв7 - hв) = k ·Fто·Dtср находим количество теплоты передаваемое греющим паром в подогревателе:
Из ряда стандартных подогревателей выбираем: ПН-100-16-4-1 с номинальным массовым расходом воды 722 кгс (Dк1=284 кгс) и максимальной температурой 240оС. [3 с. 306]
ПНД№2 – рассчитываем аналогично.
t н2= 92 0С; hв6=3736 кДжкг; hсм3=2936 кДжкг; tв1=70 0С; Dк2 =89889 кгс.
Из уравнения теплового баланса Q = Dк2(hв6 – hсм3) = k ·Fто·Dtср находим количество теплоты передаваемое греющим паром в подогревателе:
Из ряда стандартных подогревателей выбираем: ПН-400-26-7-II с номинальным массовым расходом воды 2083 кгс (Dк2=9084 кгс) и максимальной температурой 400оС. [3 с. 306]
Рассмотрим подробно расчет ПНД№3
t н3=1291 0С; hв5=53021 кДжкг; hсм2=3767 кДжкг; tв2=89 0С;Dк3 =163539 кгс.
Из уравнения теплового баланса Q = Dк3(hв5 – hсм2) = k ·Fто·Dtср находим количество теплоты передаваемое греющим паром в подогревателе:
Из ряда стандартных подогревателей выбираем: ПН-700-29-7-I с номинальным массовым расходом воды 3275 кгс (Dк3=16437 кгс) и максимальной температурой 360оС. [3 с. 306]
ПНД№4 рассчитывается аналогично.
tн4= 15527 0С; hв4=64224 кДжкг; hсм1=5289 кДжкг; tв3=1261 0С; Dк4 =18364 кгс.
Из уравнения теплового баланса Q = Dк4(hв4 – hсм1) = k ·Fто·Dtср находим количество теплоты передаваемое греющим паром в подогревателе:
Из ряда стандартных подогревателей выбираем: ПН-700-29-7-I с номинальным массовым расходом воды 3275 кгс (Dк4=18548 кгс) и максимальной температурой 360оС. [3 с. 306]
Цифры в типоразмере обозначают: первая – площадь теплообменной поверхности м; вторая и третья – рабочее давление кгссм соответственно воды в трубной системе и пара в корпусе; четвертая – номер модификации.
3.2.3Выбор деаэратора
Воздух растворенный в питательной воде содержит агрессивные газы (СО2 О2) вызывающие коррозию оборудования и трубопроводов ТЭЦ. В настоящее время на электростанциях для удаления из питательной воды кислорода углекислого и некоторых других газов применяются термические деаэраторы. В них вода подогревается паром до температуры насыщения. В соответствии с ГОСТ 16860-77 будем производить выбор из деаэраторов повышенного давления (тип ДП).
Исходными данными для выбора деаэратора являются рабочее давление в деаэраторе pд=0.59 МПа а также расход питательной воды DПВ = 21651 кгс.
Выбираем деаэратор струйно-барботажного типа ДП-1000 (изготовитель-ПО «Сибэнергомаш») [3 с. 322].
Таблица 1.6 Характеристики деаэрационной колонки
Номинальная производительность кгс
Бак аккумулятор предназначен для сбора питательной воды и создания ее аварийного запаса не менее чем на 5 минут работы котла в аварийных ситуациях.
Выбираем бак аккумулятор – БД-100-1 его характеристики приведены в таблице 1.7 [3 с. 324].
Таблица 1.7 Характеристика бака БД-100-1
Максимальная длина мм
3.2.4Выбор конденсатора
Конденсатор выбирают по максимальному расходу пара в конденсатор температуре охлаждающей воды по которым определяются давление в конденсаторе расход охлаждающей воды. Поверхность охлаждения конденсатора определяется по формуле:
где Dmaxк – расход пара в конденсатор кгс
hк h-энтальпия отработавшего пара и конденсата кДжкг
k-коэффициент теплопередачи кВтм2 ·°С.
Принимаем k =4 кВт м2·°С [3].
Dtср – среднелогарифмическая разность температур между паром и водой °С
Выбираем конденсатор типа КГ2-12000-1 с поверхностью охлаждения F = 5080 м2 в количестве 2 штук число ходов z = 1 [3 с.282].
3.2.5 Выбор сетевых подогревателей
Сетевые подогреватели служат для подогрева сетевой воды за счет тепла пара отбираемого из турбины. По давлению пара в межтрубном пространстве различают основные работающие на паре с давлением до 025 МПа и пиковые работающие на паре с давлением до 07 МПа.
Расход сетевой воды энергоблока с турбиной Т-175-130 Gсв = 20113 кгс.
Выбираем для подогрева сетевой воды – подогреватели ПСГ-5000-25-8- на верхнем и нижнем отборе с основными техническими характеристиками: площадь поверхности теплообмена – 5000 м рабочее давление в паровом пространстве – 25 кгссм в водяном пространстве – 8 кгссм номинальный расход воды – 1667 кгс число ходов по нагреваемой воде – . [3 с. 341]
3.2.6 Выбор питательных насосов
Выбор питательного насоса осуществляется по обеспечению парогенератора питательной водой максимальное потребление которого определяется максимальным расходом ее парогенераторами с запасом 5-8 %.
Давление которое должен создать насос имеет значение: МПа. Учитывая коэффициент запаса получим:
Pпн= Pн×Y = 214 ×105 = 2247 МПа; (1.75)
Dпв.макс =1.08·Dпв = 108·21651 =234 кгс; (1.76)
где Dп.в. макс=234 кгс (8424 тч).
С учетом запаса воды (и повышения давления) выбираем три питательных насоса с электрическим приводом (два рабочих один резервный) следующей марки: ПЭ-580-200 максимальный расход воды 580 тч. [3 с. 432]
3.2.7Выбор конденсатных насосов
Конденсатные насосы служат для откачки конденсата отработавшего пара из конденсатора и подачи его через подогреватели низкого давления в деаэратор. В качестве конденсатных применяются центробежные насосы. Расчетная производительность конденсатного насоса определяется по формуле:
Напор конденсатного насоса должен быть достаточным для преодоления всех сопротивлений в деаэраторной линии и подачи конденсата в деаэратор и
рассчитывается по формуле:
где НКН – полный напор конденсационного насоса;
hг=30 м – геометрическая высота подъема конденсата (разность уровней в конденсаторе и деаэраторе);
рд= 059 МПа – давление в деаэраторе;
pк=00039 МПа – давление в конденсаторе;
– сумма потерь напора в трубопроводах и подогревателях.
Hкн = 30 + 10(59 – 0039)+10×(835-0039) = 1717 м
В схеме нет подогревателей смешивающего типа поэтому применяем одноподъёмную схему включения конденсатных насосов. Принимая схему включения конденсатных насосов два по 100 % (один рабочий один резервный) выбираем насос КсВ – 500–220. [3 с. 433]
Устанавливаем систему конденсатных насосов:
два насоса (один резервный) КСВ-500-220:
Основной конденсат из конденсатора
Основной конденсат в систему регенерации
Рисунок 1.7- Конденсатные насосы
Допустимый кавитационный запас – 25 м;
Частота вращения – n=1500 обмин.
Надежность работы ТЭС в целом во многом зависит от работы отдельных агрегатов. При этом одним из определяющих факторов надежной работы большинства агрегатов ТЭС является качественная подготовка добавочной воды. В связи с этим требования к качеству добавочной воды непрерывно возрастают. Оборудование современных электростанций эксплуатируется при высоких тепловых нагрузках что требует жесткого ограничения толщины отложений на поверхностях нагрева по условиям температурного режима их металла в течение рабочей компании. Такие отложения образуются из примесей поступающих в циклы электростанций в том числе и с добавочной водой поэтому обеспечение высокого качества водных теплоносителей электростанции является важнейшей задачей. Использование водного теплоносителя высокого качества упрощает также решение задач получения чистого пара минимизации скоростей коррозии конструктивных материалов котлов турбин и оборудования конденсатно-питательного тракта. Для удовлетворения разнообразных требований к качеству воды потребляемой при выработке электрической и тепловой энергии возникает необходимость специальной физико-химической обработки ее.
В последние два десятилетия активное развитие получили мембранные методы очистки. Процесс фильтрации на мембране имеет свои особенности. Фильтруемая среда движется по поверхности мембраны и разделяется на два потока – фильтрат и концентрат. Мембранные системы классифицируются в зависимости от рейтинга фильтрации задерживаемых частиц (микро- ультра- нанофильтрация обратный осмос) и задерживают частицы размером от десятков микрон до тысячных долей микрона. В водоподготовке используются мембраны с различными видами пористых структур.
Ультрафильтрация это процесс мембранного разделения растворов высокомолекулярных и низкомолекулярных соединений а также концентрирования и фракционирования высокомолекулярных соединений. Процесс протекает за счет разности давлений до и после мембраны.
Ультрафильтрацию применяют для разделения систем в которых молекулярная масса растворенных компонентов намного больше молекулярной массы растворителя. Например для водных растворов содержащих органические соединения с молекулярной массой 500 и более.
Поскольку осмотические давления высокомолекулярных веществ малы (обычно не более десятых долей МПа) в процессе расчетов движущей силы процесса ультрафильтрации ими как правило можно пренебречь. Поэтому ультрафильтрацию проводят при сравнительно невысоких давлениях (02 - 10 МПа).
Основные преимущества мембранных установок ультрафильтрации с полыми волокнами имеющими селективно проницаемые стенки являются:
Высокая удельная поверхность половолоконных мембран (20000 м2м3);
Отсутствие потребности применения специальных систем дренажа;
Низкие энергозатраты на турбулизацию потока*;
Простота в эксплуатации.
*для стабильной работы системы ультрафильтрации на основе трубчатых мембранных фильтров рекомендуется значение критерия Рейнольдса Rе = 2500-3000 для установок плоскорамного типа Rе = 180200 а для установок с полыми волокнами достаточно значения Rе = 2030. [12]
При обессоливании воды методом обратного осмоса на стадии предварительной очистки обычно используют установки ультрафильтрации с разделительными элементами имеющими центральные опорно-распределительные трубки. Разделяемая жидкость подается в межволоконное пространство через опорно-распределительную трубку. Проникая сквозь стенки полых волокон растворитель (вода) выходит из каналов полых волокон и попадает в сборные камеры образуемые блоком-коллектором и крышкой установки откуда отводится через специальный штуцер. Концентрат отводится по каналу с противоположной стороны установки ультрафильтрации.
Производительность установки определяется числом модулей с половолоконными мембранами и может варьироваться в широком диапазоне.
Обратный осмос это процесс фильтрации водных растворов под давлением превышающее осмотическое через полупроницаемую мембрану. Процесс обратного осмоса как правило протекает под давлением 28-5 МПа.
Рулонные мембранные элементы для мембранных установок обратного осмоса работают по принципу тангенциальной фильтрации. В процессе обессоливания она разделяется на два потока: фильтрат (обессоленная вода) и концентрат (раствор с высоким солесодержанием). Разделяемый поток воды движется в осевом направлении по межмембранным каналам рулонного элемента а фильтрат спиралеобразно по дренажному листу в направлении отвода фильтра. Концентрат выходит с другой стороны мембранного модуля обратного осмоса. Сегодня обратноосмотические мембранные элементы рулонного типа являются наиболее распространенными и наименее дорогостоящими.
Преимущества обратноосмотических аппаратов рулонного типа:
Высокая плотность упаковки мембран в единице объема (300–800 м2м3);
Удобство монтажа и демонтажа мембранного элемента в корпусе мембранной установки обратного осмоса;
Низкая стоимость и простота конструкции напорного корпуса мембранной установки;
Относительно низкие потери давления в установке;
Использование для изготовления разделительных элементов плоской мембраны качество которой может быть предварительно проконтролировано несложными способами.
Работа установок обратного осмоса осуществляется при высоком давлении которое обеспечивается при использовании многоступенчатых насосов высокого давления (насосных станций бустерного типа). Таким образом в примембранном слое происходит концентрирование растворенных веществ содержащихся в питающей воде. Это процесс концентрационной поляризации приводящей к образованию осадка на поверхностях обратноосмотических мембран. Для снижения эффекта концентрационной поляризации в мембранные модулях обратного осмоса производители используют новые сетки турбулизаторы подбирают полимерные материалы сильнее препятствующие отложению солей на их поверхности. Кроме того для снижения осадкообразования производители мембран вводят требования к качеству воды подаваемой на установки обратного осмоса (ограничения по солям жесткости ионам железа общей минерализации взвешенным веществам и свободному хлору). [12]
В рассматриваемой схеме ионный обмен применяют для дообессоливания воды. Подлежащая очистке вода проходит через один или систему фильтров заполненных ионитами подбираемыми в зависимости от требуемой задачи. Иониты удаляют из воды соответствующие ионы и обмениваются с водой эквивалентными количествами других ионов которые первоначально находились в ионите. Обменивающиеся ионы называются противоионами. Иониты состоят из неподвижного каркаса - матрицы и функциональных групп - фиксированных ионов которые жестко прикреплены к матрице и взаимодействуют с противоионами.
Основными характеристиками ионитов являются: селективность рабочая обменная емкость и кинетика ионного обмена.
Работа ионообменного фильтра состоит из следующих операций:
-очистка воды (сервисный режим);
-засос соли из солерастворителя – регенерация ионообменной смолы;
-медленная отмывка ионообменной смолы от регенерационного раствора;
-быстрая отмывка в сервисном режиме;
-заполнение солерастворителя умягченной водой.
Распределительные устройства (дренажи) аналогичны используемым в механических фильтрах. В большинстве случаев ионообменный метод обработки воды обеспечивает удаление ионов оставшихся после установок обратного осмоса.
Для технологического процесса барабанного котла марки Е-820-140 ГМ требуется уровень обессоливания воды который регламентируется соответствующим нормативным документом: РТМ 108.030.130-79. Удельная электропроводность не должна превышать 15 мкСмсм и жёсткость не более 0001 мг-эквл. В технологи водоподготовки реализуется принцип очистки предусматривающий постадийное удаление от крупных коллоидных частиц к более мелким вплоть до молекул солей (от макрофильтрации частиц размером свыше 50 мкм до нанофильтрации и обратного осмоса обеспечивающего задерживание растворённых солей).[11] Это позволяет работать каждому узлу установки в оптимальном для него технологическом режиме. Стадии микро- и ультрафильтрации обеспечивают высококачественную предварительную подготовку воды и позволяют удалить примеси с молекулярной массой опасной для работы обратного осмоса. Непосредственный процесс обессоливания производится на стадии обратного осмоса который в свою очередь может состоять из одной или двух ступеней по фильтрату. Вода прошедшая первую ступень обратного осмоса характеризуется удельной электропроводностью не более 20 мкСмсм и жёсткостью не более 03 мг-эквл после второй ступени – удельная электропроводность составляет не более 2 мкСмсм и жёсткость не более 005 мг-эквл. Обратный осмос одной или двух ступеней по фильтрату позволяет достичь степени обессоливания воды которая соответствует требованиям для водогрейных котлов для подпитки систем горячего водоснабжения и для подпитки оборотной системы охлаждения. Этого уровня обессоливания недостаточно для использования воды непосредственно в парогазовых установках. Для достижения указанного уровня обессоливания используются два варианта технологий глубокого обессоливания:
- дообессоливание на базе электродеионизатора;
-дообессоливание на базе ионообменной технологии;
Принципиальная схема подготовки технологической обессоленной воды с двумя вариантами дообессоливания представлена на рис. №1.8 и № 1.9. [13]
Рисунок 1.8 Принципиальная схема потоков обессоливающей установки
с использованием электродеонизатора
Рисунок 1.9 Принципиальная схема потоков обессоливающей установки
с использованием ионного обмена
В данной работе для достижения указанного уровня обессоливания предлагается использовать вариант №1.9 - дообессоливание на базе ионообменной технологии так как является более дешевым.
КОНСТРУКТОРСКИЙ РАСЧЕТ ДЕАЭРАТОРА
1 Назначение устройство и работа деаэратора
Деаэраторы повышенного давления (ДПВ) в тепловой схеме станции выполняют целый ряд функций: помимо своей основной — деаэрации питательной воды они служат ступенью подогрева в регенеративной схеме подогрева воды аккумулирующей и буферной емкостью между конденсатными и питательными насосами являются источником пара постоянного давления и температуры а также местом ввода в схему разного рода высокопотенциальных дренажей. Однако основной функцией деаэраторов является удаление из питательной воды коррозионно-активных газов. Такими газами являются кислород (02) и свободная двуокись углерода (С02).
На рисунке 2.1 представлена принципиальная схема деаэратора. Установка состоит из деаэрациоиной колонки и бака аккумулятора. Подача деаэрируемой воды осуществляется в верхнюю а греющего пара в нижнюю часть колонки. Поступающая в бак-аккумулятор вода имеет температуру близкую к температуре насыщения. Процесс дегазации воды в основном осуществляется в колонке хотя и в баке-аккумуляторе за счет отстоя происходят частичное выделение мельчайших пузырьков газа и их удаление.
Рисунок 2.1 – Принципиальная схема деаэратора
– деаэраторная колонка; 2 – бак-аккумулятор; 3 – охладитель выпара; 4 – регулятор давления. 5 – регулятор уровня; 6 – гидравлический затвор; 7 – предохранительный клапан: 8—подвод химически очищенной воды; 9 – подвод основного конденсата; 10 – подвод дренажа подогревателей высокого давления; 11 – подвод греющею пара; 12 – отвод деаэрированной воды; 13 – отвод выпара; 14 – выхлоп в атмосферу; 15 – дренаж; 16 – теплообменник для охлаждения проб воды; 17 – водоуказательное стекло.
Эффективность деаэрации воды в деаэраторах зависит от конструкции деаэраторов давления при котором происходит деаэрация а также от режима эксплуатации.
По способу организации контакта воды с греющим паром деаэраторы разделяются на пленочные струйные капельные барботажные и комбинированные сочетающие в себе два или несколько из перечисленных способов увеличения свободной поверхности воды.
Нагрев деаэрируемой воды до температуры насыщения еще не является достаточным условием для качественной деаэрации. Не менее важной задачей является создание условий для быстрой эвакуации выделившихся из воды газов. В деаэраторных колонках газы удаляются паровой продувкой колонки снизу вверх навстречу потоку падающей воды после чего парогазовая смесь удаляется в атмосферу. Этот поток называется «выпаром». Данные эксплуатации показывают что эффективность деаэрации в значительной мере зависит от величины «выпара» (рисунок 2.2). Для деаэраторов повышенного давления эта величина не должна быть ниже 1.5—2 кг пара на тонну воды.
Рисунок 2.2 Зависимость эффективности деаэрации от величины выпара.
На эффективность деаэрации влияет также температура поступающей в деаэратор воды. С повышением температуры воды подводимой к деаэратору вязкость и поверхностное натяжение воды уменьшаются скорость диффузии кислорода в слое воды возрастает и эффект деаэрации улучшается. Однако подавать в колонку воду с температурой близкой к температуре насыщения тоже не рекомендуется поскольку это сокращает расход греющего пара и ухудшает условия вентиляции колонки. Минимальный нагрев воды в деаэраторе должен быть не ниже 5—6°С. Величину нагрева порядка 10—15°С следует считать оптимальной.
В настоящее время в установках высокого давления применяются деаэраторы повышенного давления 06 – 12 МПа. Это позволяет уменьшить число ПВД. а также улучшить условия деаэрации.[4]
Давление в деаэраторе: р = 059 Мпа
Температура насыщения: tн = 158.18 оС
Энтальпия пара по насыщению: h'' = 27554 кДжкг
Удельный объём сухого насыщенного пара (по tн): Vп = 032071 кгм3
Энтальпия жидкости по насыщению: h' = 66765 кДжкг
Расход основного конденсата: Dок = 18364 кгс
Энтальпия основного конденсата: hок = hв4 = 64224 кДжкг
Расход дренажа из вышестоящего ПВД:
DПВД = Dп1 + Dп2 + Dп3 + Dу = 972+857+1253+2 = 3282 кгс
Энтальпия дренажа из вышестоящего ПВД: hПВД = 8296 кДжкг
Расход питательной воды: Dпв = 21651 кгс
Энтальпия питательной воды: hпв = h' = 66765 кДжкг
Расход греющего пара из отбора турбины: Dд = 0865 кгс
Энтальпия греющего пара: hд = 2978 кДжкг
Расход пара из уплотнений штоков: Dшт = 063 кгс
Энтальпия свежего пара: hшт = h0 = 3474 кДжкг
Расход пара из расширителя непрерывной продувки: D''пр = 139 кгс
Энтальпия пара из расширителя: h'пр = h'' = 275613 кДжкг
Расход пара на эжектор и уплотнения: Dэу = 2835 кгс
Удельная теплота парообразования: r = h'' – h' = 275613 – 66765 = 208848 кДжкг
3 Тепловой расчёт деаэратора
Проверка теплового баланса:
Входящие потоки: Di hi =
Исходящие потоки: Dэу hд + Dпв hпв =
Проверка материального баланса:
Расходы входящих потоков = 219345 кгс
Расходы исходящих потоков = 219345 кгс
Суммарный расход воды подающийся в водораспределитель:
Dок = D1 = 18364 кгс
Энтальпия воды в водораспределителе:
hок = hв4 = 64224 кДжкг
Температура воды в водораспределителе:
tв1 = f (р; hв4) = 15227 0С
Горячие потоки (греющий пар и конденсат ПВД) поступают в нижнюю часть колонки деаэратора. При этом за счёт теплоты перегрева греющего пара из потока конденсата ПВД образуется пар в количестве которое может быть определено из уравнений теплового и материального балансов:
где расход насыщенного пара в деаэраторе ниже активной зоны.
расход воды в деаэраторе ниже активной зоны.
Принимаем диаметр отверстий в днище тарелки d=0.005 м и высоту подпора воды на тарелке при расчетной нагрузке h=0.05 м [5].
Скорость истечения воды из отверстий тарелки:
Необходимое число отверстий в тарелке:
Площадь тарелки занятая отверстиями размещёнными в шахматном порядке с шагом S = 15d0 = 00075 м.
Принимаем наружний диаметр размещения отверстий в тарелке 2 м тогда внутренний диаметр[5]:
Площадь живого сечения для прохода по внутренней границе струйного отсека при длине струй l = 06 м:
Площадь живого сечения для прохода по внешней границе струйного отсека:
Скорость пара на входе в струйный отсек:
Скорость пара на выходе из струйного отсека:
Средняя скорость пара в струйном отсеке:
Температурный подогрев воды в струйном отсеке:
A=0.05–коэффициент зависящий от теплофизических свойств воды и пара [5].
Количество пара конденсирующегося в струйном отсеке пара.
Концентрация кислорода в потоке воды поступающем в водораспределительное устройство СисхО2 = 100 мкгкг. Концентрация кислорода в потоке воды поступающем на барботажную тарелку определяется по выражению:
откуда С2 = 155 мкгкг
Расход пара поступающего на барботажную тарелку:
Dп.барб. = Dд = 0865 кгс
Общий расход воды через барботажную тарелку:
Принимаем ширину порога барботажной тарелки b=2м при диаметре колонки dк = 24 м [5]
Расход воды через 1 м ширины водослива барботажной тарелки:
Высота слоя воды над порогом водослива:
Высота слоя воды на барботажной тарелке
h0=hп+hв=0.1+0.17=0.27 м(2.17)
Минимально допустимая скорость пара в отверстиях барботажной тарелке:
Принимаем расчетную скорость пара в отверстиях барботажного листа wп=3.5wмин=3.5 11.67=4084 мc [5].
Живое сечение для прохода пара в барботажном листе:
Необходимое число отверстий при d0 = 0005 м
Высота паровой подушки под барботажным листом. При коэффициенте гидравлического сопротивления дырчатого барботажного листа =1.8 и поверхностном натяжении воды =0.0454 Hм.
Из конструктивных соображений принимаем ширину и длину барботажной области равными ширине водослива. Диаметр пароперепускного патрубка гидрозатвора dвых принимаем равным 045 м. Тогда площадь барботажной области (площадь тарелки занятой отверстиями)
Приведённая скорость пара при барботаже:
Высота динамического слоя жидкости на тарелке:
Количество кислорода подлежащего удалению при барботаже (СвыхО2 = 10 мкгкг)
Скорость течения воды на барботажном листе:
Коэффициент массопередачи на барботажной тарелке:
Среднелогарифмический концентрационный напор:
Необходимая площадь барботажной тарелки:
4 Расчет на прочность элементов деаэратора
Расчет толщины стенки деаэратора:
где: P=0.59 МПа – расчетное избыточное давление.
Dв=3 м – внутренний диаметр днища.
[]=128 Мпа – номинально допускаемое напряжение для материала колонки. [6]
Сталь15К – материал днища.
φ=0.85 – ослабление цилиндрических элементов продольным сварным швом.
С=0.002 м – прибавка к расчетной толщине стенки.
Принимаем номинальную толщину стенки деаэратора: Sном=0.02 м.
Расчет толщины днища корпуса с учетом крепления отверстия штуцером.
Минимальная толщина стенки днища при φ=1 С=0.
Минимальная расчетная толщина стенки штуцера при φ=1 С=0.
где: d=0.092 м – внутренний диаметр штуцера.
[]ш=130.23 МПа – номинально допускаемое напряжение для материала штуцера. [6]
Сталь20 – материал штуцера.
Высота укрепляющего участка штуцера расположенного снаружи днища.
где: dн=0.108 м – наружный диаметр штуцера.
Sш=0.008 м – номинальная толщина стенки штуцера.
Сш=0.002 м – прибавка на коррозию к расчетной толщине стенки штуцера.
Площадь укрепляющего сечения штуцера на участке расположенном снаружи днища.
Высота укрепляющего участка штуцера расположенного внутри днища.
Площадь укрепляющего сечения штуцера на участке расположенном внутри днища.
Сумма компенсирующих площадей укрепляющих деталей.
Σf=fн.ш.+fв.ш. (2.37)
Σf=0.000284+0.00016=0.00044 м²
1 Назначение устройство и работа воздухоподогревателя
Теплообменный аппарат – это устройство в котором осуществляется передача теплоты от горячего теплоносителя холодному (нагреваемому). Теплоносителями могут быть газы пары жидкости. В зависимости от назначения теплообменные аппараты используют как нагреватели и как охладители. Теплообменники широко применяются в энергетике: подогреватели высокого давления подогреватели низкого давления экономайзеры пароперегреватели конденсаторы подогреватели в паросиловых установках а также и в других целях.
По способу передачи теплоты теплообменники подразделяют на рекуперативные регенеративные и смесительные. В данной работе рассматривается воздухоподогреватель который относится к рекуперативным.
В рекуперативных теплообменниках каналы по которым движутся горячий и холодный теплоносители теплота передается через разделяющую их стенку. При неизменных параметрах теплоносителей на входе остаются постоянными во времени и параметры теплоносителей в любом из сечений каналов т.е. процесс теплопередачи имеет стационарный характер. Поэтому рекуперативные теплообменники называют также стационарными.
Часть теплообменника в которой происходит процесс передачи теплоты называют теплопередающей матрицей. Подвод теплоносителей к матрице и отвод их осуществляется по входному и выходному коллекторам. В зависимости от направления движения теплоносителей рекуперативные теплообменники могут быть прямоточными при параллельном движении теплоносителей в одном направлении противоточными при параллельном встречном движении и перекрёстными при взаимно перпендикулярном движении.
В матрице теплоносители могут совершать один или несколько ходов. В соответствии с этим теплообменники называют например одноходовым по горячему теплоносителю и двухходовым по холодному теплоносителю. При увеличении количества ходов возрастает скорость движения теплоносителя что ведет к интенсификации теплообменника. Однако при этом растут гидравлические потери и затраты энергии на обеспечение движения теплоносителя. В зависимости от назначения производственных процессов в качестве теплоносителей могут применятся различные газообразные жидкие и твердые тела.
Дымовые газы могут применятся в теплообменниках для нагрева выпарки и термической обработки газообразных жидких и твердых веществ. Достоинство дымовых газов как теплоносителя является возможность достижения высокой температуры при атмосферном давлении недостатками – громоздкость аппаратуры обусловленная низкой теплоотдачей от газов к стенке сложность регулирования рабочего процесса в теплообменном аппарате пожарная опасность и сравнительно быстрый износ поверхностей теплообменника отложениями серы или золы а также при чистке аппаратов.
Воздухоподогреватели в паровых котла предназначены для подогрева поступающего в топку воздуха для интенсификации радиационного тепловосприятия экранов и снижения потери от химического и механического недожогов топлива охлаждения продуктов сгорания до технически и экономически оправданного предела. Увеличение температуры подогрева воздуха на 100°С повышает примерно на 50°С температуру горения топлива что способствует уменьшению необходимых поверхностей нагрева. Снижение температуры уходящих газов на 20°С повышает КПД котла примерно на 1%.
Экономически выгоднее повышать температуру воздуха именно перед зоной горения. Чем выше температура воздуха тем интенсивнее идут процессы смесеобразования и сжигания. Воздух в данном случае – не балластный теплоноситель а смесь газов участвующая в процессе сжигания углеводородов. Воздух нужно подогревать для снятия тепла уходящих газов именно в зоне после экономайзера - это экономичнее чем воздух греть в водяном или электрическом калорифере или же использовать теплый воздух помещения. Температура насыщения среды в испарительных поверхностях нагрева при давлении более 1 МПа выше требуемой температуры продуктов сгорания уходящих из котла поэтому при завершении в них теплоиспользования нельзя обеспечить должную тепловую экономичность установки. Поэтому в современных котлах использование теплоты продуктов сгорания завершается в экономайзере и воздухоподогревателе. В экономайзере подогревается питательная вода и иногда происходит ее частичное испарение.
Наличие экономайзера и воздухоподогревателя при температуре поступающих в них воздуха и питательной воды меньшей чем температура насыщения обеспечивает возможность охлаждения продуктов сгорания до технически и экономически оправданного предела.
Температура питательной воды для энергетических котлов с давлением пара более 393 МПа согласно ГОСТ 3619-89 принимается равной 150 215 и 230 °С в зависимости от развития регенеративного подогрева воды осуществляемого с целью повышения экономичности работы электростанции. Для котлов производственного назначения температура питательной воды после ее термической деаэрации составляет 104 °С. Таким образом для энергетических котлов температура питательной воды должна быть выше температуры уходящих из котла продуктов сгорания и по условиям организации теплообмена необходимо применение теплоносителя с более низкой начальной температурой которым и является воздух. Следовательно тепловосприятие в энергетических котлах должно завершаться в воздухоподогревателе.
Экономически выгоднее чтобы температура подогрева воздуха была выше чем температура питательной воды после экономайзера. Увеличение поверхности нагрева воздухоподогревателя при повышенной температуре подогрева воздуха компенсируется уменьшением более дорогой и ответственной поверхности нагрева экономайзера.
Конечная температура подогрева воздуха в воздухоподогревателе выбирается в зависимости от вида сжигаемого топлива и типа топочного устройства. Температуру подогрева воздуха при сжигании природного газа и мазута рекомендуется принимать 200—300 °С а при слоевом сжигании топлива 200—250 °С. Этим определяется возможность применения одноходовой компоновки экономайзера и воздухоподогревателя для котлов работающих на указанных топливах. Для котлов работающих на влажном пылевидном твердом топливе целесообразен подогрев воздуха до 350—400 °С и для таких установок применяется двухступенчатая компоновка. Дальнейшее повышение температуры подогрева воздуха ограничивается необходимостью применения при tв''>450 °С легированных металлов или специальных материалов или специальных сложных конструкций воздухоподогревателей. Температура продуктов сгорания на входе в трубчатый воздухоподогреватель по условиям окалинообразования трубных досок не должна превышать 530 °С.
Таким образом можно сделать вывод для поддержания стабильного и качественного процесса горения необходима оптимальная и стационарная температура подогретого воздуха. Температура воздуха после воздухоподогревателя зависит от температуры (холодного) воздуха подаваемого в воздухоподогреватель и от расхода дымовых газов через воздухоподогреватель.
2 Исходные данные для расчета воздухоподогревателя:
Диаметр труб – dн = 004 м
Толщина стенки труб – ст = 00015м
Пучок – шахматный – s1 = 006 м s2 = 0042м
Скорость газов – wг = 11 мс
Скорость воздуха – wв = 77 мс
Температура воздуха – на входе t'в = 50оС на выходе t"в = 250оС
В данном разделе бакалаврской работы проведен тепловой расчет и компоновка воздухоподогревателя для котла марки Е-820-140 ГМ а также установлены зависимости температуры подогретого воздуха от температуры (холодного) воздуха подаваемого в воздухоподогреватель и от расхода дымовых газов через воздухоподогреватель.
Геометрические параметры ВП и газохода
Тепловосприятие ВП:
Qвп= αтV0Вr(h"в – h'в) (3.1)
где: Вr-расчетный расход топлива (м3с);
V0-действительные объемы продуктов сгорания (м3 м3);
αт-коэффициент избытка воздуха;
на входе – h'в =(1287+12012·10-4·50) 50 =6465 кДжкг;
на выходе – h"в =(1287+12012·10-4·250) 250 = 32926 кДжкг;
Qвп= 105·9 81·756· (32926– 6465) = 206022 кВт.
Энтальпия газов на выходе из воздухоподогревателя:
h"г =(15645+1967·10-3·120) 120 = 19067 кДжкг.
Энтальпия газов на входе в воздухоподогреватель:
h'г= h''г+ Qвп(φВr) (3.4)
h'г = h''г+ Qвп(φВr)= 19067+424644( 09992·756)= 46336 кДжкг.
Температура газов на входе в ВП:
Средняя температура в ВП:
газов – г = 05('г + "г) = 05(28589+ 120) = 20295оС;
воздуха – tв = 05(t'в+ t"в) = 05(50+250) = 150 оС.
«Живое» сечение ВП для прохода газов:
«Живое» сечение ВП для прохода воздуха:
Общее количество труб в пакете ВП:
где - поперечное сечение трубы пучка ВП:
Число труб в поперечном ряду:
n1=(aвп- s1) s1 (3.9)
где aвп – ширина воздухоподогревателя
n1 =(129-006)006=214 шт.
Высота одного хода ВП:
где kз=1 – dнs1 = 1 – 004006 = 0333 – коэффициент загромождения;
kт = 1 – технологический коэффициент.
Коэффициент теплоотдачи от газов для шахматных пучков:
где s— поправочный коэффициент зависящий от шага труб в пучке; λ= λ'·Мλ= 00385 — теплопроводность продукта сгорания при средней температуре потока кВт(м K); = 'М=30·10 -6 — кинематическая вязкость продуктов сгорания при средней температуре потока м2с; Рr = Рr'МРr = 0698— число Прандтля. dэк –эквивалентный диаметр определяется как:
U=2·( aвп+h1)+2· n1· h1=2·( 129+295)+2· 214· 295=1296
Значения λ и Рr определяются по графическим зависимостям МУ.
Коэффициент теплоотдачи от стенки трубы к рабочему телу α2 определяется следующим образом.
Поправки Ct Cd и С ='М = 30·10 -6 — кинематическая вязкость воздуха при средней температуре потока м2с; Рr = Рr'МРr = 0672— число Прандтля.
Расчет коэффициента теплопередачи:
где = 095 — коэффициент тепловой эффективности;
Температурный напор — усредненная по поверхности нагрева разность температур между теплообменивающимися средами — определяется по формуле:
где Δtb = ух – t'вп = 120 – 50 =70оС; ΔtM = 'вп – t''вп =28589 – 250= 3589 оС — больший и малый перепады температур между средами на концах поверхности нагрева;
Расчетная поверхность нагрева:
Поверхность одной трубы:
Количество ходов ВП:
Действительная скорость газов:
wгд = wг·( Z' Z) (3.19)
wгд = 11· (334)=97 мс.
Высота одного хода ВП:
h'1=h1· (Z Z' ) (3.20)
h'1=295· (34 3)=334 м.
Высота первого хода ВП:
Высота следующего хода ВП:
hII= (L - hI)( Z' – 1) (3.22)
hII= (1056 - 25)( 3 – 1)=4 м.
Определение числа труб в одном ряду вдоль течения воздуха:
n'2= 128217214= 599 59 шт.
bвп = n'2·s2+s2 (3.24)
bвп = 59·0042+0042=252 м.
Аналогичным образом в программе Mathcad были произведены расчеты
воздухоподогревателя для котла работающего с расходом пара D0=500 D0=580 D0=660 D0=740 D0=820 . На рисунке 3.1 приведен график зависимости подаваемого расхода дымовых газов на воздухоподогреватель и температуры наружного воздуха.
Из графика видно что при снижении температуры наружного воздуха для поддержания стационарной температуры воздуха на выходе из воздухоподогревателя следует повышать расход дымовых газов.
Для регулирования расхода дымовых газов используется система поворотных шиберов.
ПРИРОДООХРАННЫЕ МЕРОПРИЯТИЯ
Сточные воды энергообъектов и их очистка
Предотвращение загрязнения общественных водоемов сточными водами тепловых энергообъектов металлургических предприятий очистка и повторное использование этих вод являются в настоящее время в соответствии с принятыми законами по охране окружающей среды важнейшими задачами проектирования и эксплуатации тепловых энергообъектов и их водоподготовительных установок.
Используются следующие основные способы очистки сточных вод:
Сброс в циклы в которых требования к воде позволяют использовать сбрасываемую воду;
Окисление вредных примесей;
Разбавление и сброс в водоемы;
Удаление вредных примесей и повторное использование.
1 Сбросные воды после прямоточного охлаждения конденсаторов турбин
Сбросные воды после прямоточного охлаждения конденсаторов турбин воздухоохладителей и маслоохладителей с температурой на 8—15 °С выше температуры воды в водоеме с биохимической точки зрения считаются "условно чистыми". Единственным "загрязнителем" этих вод является вносимое ими в водоем тепло нарушающее во всем водоеме (при небольших его размерах) или в отдельных частях его тепловой и биохимический режимы. Повышение температуры воды в водоеме на 5 °С и более особенно в летнее время усиливает жизнедеятельность микроорганизмов рост водорослей и снижает содержание в воде кислорода необходимого для жизнедеятельности рыб и других высших организмов. Процессы эти усиливаются если сбрасываемая в водоем вода содержит биологически активные вещества (РО43- NO3 К+). Усиленный рост микроорганизмов и водорослей в водоеме отмирание водорослей и гниение их ухудшают процессы известкования коагуляции отстаивания и фильтрования воды на предочистках что приводит к забиванию ими труб и конденсаторов паровых турбин. Рост водяных растений вызывает заболачивание прибрежных участков водоема сокращение его активной водоохлаждающей поверхности повышение температуры охлаждающей воды и в конечном счете ухудшение вакуума и перерасход топлива. Борьба с усиленным ростом микроорганизмов водорослей растений ведется путем хлорирования воды применения медного купороса гербицидов дефолиантов а также разведением в водоемах травоядных теплолюбивых рыб — белого амура толстолобика и др.
Количество сбрасываемой теплой воды при прямоточном водоснабжении достигает 60—100 кг воды на 1 кг пара конденсируемого в конденсаторах турбин.
Продувочная вода сбрасывается в количестве 1—2 % от часового расхода оборотной воды. В ряде случаев при невысокой минерализованности продувочная вода оборотных циклов энергообъектов может поступать на ВПУ и в оборотные циклы конвертерных и прокатных цехов газоочисток и других производств не предъявляющих к воде повышенных требований. Это уменьшает сброс продувочных вод в общественные водоемы и нарушения биохимического режима их.
2 Сточные воды от мазутных хозяйств энергообъектов
Количество этих вод невелико (2-10 м3ч) загрязненность мазутом - от 10-15 до 1000 мгл. Причиной попадания мазута в сточные воды является смыв разлитого мазута с поверхности почвы вследствие неровностей площадки а также из-за плохого качества (проницаемости) стенок железобетонных мазутохранилищ и разрыва трубок подогревателей. К этой же группе сточных вод примыкают воды от охлаждения подшипников вращающихся механизмов и смыва полов в помещениях электростанций а также от маслохозяйств станций. Количество их также невелико — до нескольких десятков кубических метров в час загрязненность маслами — до 10—15 мгл. Общее количество масел попадающее в сточные воды практически равно количеству масла доливаемого в масляные системы охлаждения (трансформаторы масляные выключатели подшипники и др.) если не организовано его улавливание.
Сточные воды и конденсат мазутных хозяйств и станций загрязненные нефтепродуктами должны сначала отстаиваться в мазутоловушках. Там мазут и масла удаляются на 98—99 % от содержания их в первичных стоках при остаточном содержании 10—50 мгл. Отстой продолжается в проточных ловушках не менее 2 ч в ловушках периодического действия 6-8 ч. Загрязненную мазутом воду для улучшения расслаивания мазутных эмульсий следует подогревать до 50-60 °С. После ловушек воду содержащую мазут или масла преимущественно в эмульгированном состоянии следует направлять во флотомашины. Во флотомашины должен подаваться раствор коагулянта (50-70 мгл А12(SO4)3·18H2O) для коагуляции частичек нефтепродуктов. В напорных флотомашинах сжатым воздухом насыщают находящуюся под давлением воду из которой при последующем снижении давления выделяются мельчайшие пузырьки воздуха увлекающие за собой на поверхность жидкости капельки масла и хлопья коагулянта образующие прочную пену. При исходном содержании нефтепродуктов в воде до 200 мгл содержание их после флотации снижается до 8-10 мгл т.е. в 10—20 раз. При безнапорной флотации воздух в воду подается при помощи импеллеров (турбинок) или водовоздушных эжекторов.
Многоступенчатая флотация в 2—4 ступени позволяет обходиться без ловушек и более полно удалять нефтепродукты (до 5—8 мгл). После ловушек и флотомашин полуочищенные масла воды (или конденсат) должны направляться на механические (зернистые целлюлозные или тканевые) фильтры. Скорость фильтрования через безнапорные зернистые фильтры с размером зерен 05-2 мм 01-03 мч через напорные 5 мч через тканевые 1 мч через намывные напорные целлюлозные фильтры при одновременном обезжелезивании до 20 мс. Оптимальное содержание мазута или масел перед механическими фильтрами 5—10 максимум 30 мгл. Конечное содержание (1—3 мгл) зависит от исходного содержания и свойств масел высоты слоя и размеров зерен загрузки. Конечная ступень очистки замасленных вод (конденсатов) — фильтрование через одну или две ступени сорбционных фильтров загруженных обезмасливающим активированным углем. Перед сорбционными фильтрами содержание масел не должно превышать 3-5 мгл. После одной ступени фильтрования остаточное содержание масел ~10 мгл после двух — не более 05 мгл. При нецелесообразности глубокой очистки загрязненные мазутом воды после ловушек и флотомашин следует направлять на осадительную предочистку ВПУ или смешивать с водой гидрозолоудаления и направлять на золоотвалы или в грязные циклы газоочисток металлургических цехов. В результате дополнительной очистки частичками золы и разбавления содержание мазута и масел в воде сливаемой с золоотвалов обычно не превышает норм.
3 Сбросные воды систем гидрозолоудаления
В сбросных водах систем гидрозолоудаления (ГЗУ) тепловых электростанций отапливаемых зольными твердыми топливами (углем сланцами торфом щепой) в зависимости от месторождения и сорта топлива меняются количество и состав золы содержание в ней нерастворимых и водорастворимых соединений в том числе свободных щелочей (CaO NaOH Na2CO3 и др.). При содержании в золе более 10 % водорастворимых свободных щелочей обычно имеют место цементация частичек золы и обрастание золопроводов в результате реакции щелочей золы с Са2+ и Mg2+ содержащимися в транспортирующей воде. При значительном содержании в топливе серы зола может иметь кислую реакцию вследствие содержания в ней H2SO4 Н2SО3 и их кислых солей. К этой же категории относятся воды после обмывки поверхностей нагрева которые также могут быть и кислыми и щелочными в зависимости от сорта топлива. Обмывочные воды наружных поверхностей нагрева теплоутилизационных парогенераторов а также сточные воды газоочисток предприятий черной металлургии в зависимости от состава горючих газов и вида процесса содержат:
а) после котлов-утилизаторов за мартеновскими печами и охладителями конвертерных газов - оксиды железа и частички унесенного шлака (SiO2 CaO МgО Аl2О3 Fе2О3). Они имеют обычно щелочную реакцию.
б) после котлов-утилизаторов за вращающимися печами для обжига извести и доломита — взвешенные частицы (CaO СаСО3 МgО МgСО3). Они имеют щелочную реакцию.
При наличии достаточного количества щелочной золы и транспортирующей воды ГЗУ кислые воды после обмывки мазутных котлов целесообразно нейтрализовать щелочными водами ГЗУ. Нейтрализацию кислых вод ГЗУ и обмывочных вод мазутных котлов можно осуществлять кроме известкового молока (обычно получаемого с ВПУ) шламом продуваемым из осветлителей [СаСО3 + Мg(ОН)2 + Fе(ОН)3] и щелочной продувочной водой котлов и испарителей. Продувочную воду можно применять для обмывки наружных поверхностей нагрева непосредственно из котлов или после выделения из нее пара и охлаждения (из сборных резервуаров с помощью насосов). Возможно также применение сбросных вод после анионитных фильтров непригодных вследствие большого содержания в них Nа2SiO3 Na2SO4 NaCl для других целей. При сбросе в систему ГЗУ сбросных вод после щелочения химических промывок и консервации котлов состав вод особенно поступающих в шлаконакопители ГЗУ а также сбрасываемых из них очень сильно меняется (соли щелочи кислоты органические вещества). Смешивание обмывочных вод с водами после химических промывок недопустимо. Сливаемые с золоотвалов воды разомкнутых систем ГЗУ обычно имеют нейтральную или щелочную (рН 10—12) реакцию. Общее солесодержание их повышено содержание взвеси после нескольких суток отстоя не превышает 20—50 мгл после зернистых фильтров — до 10 мгл.
При замкнутых (оборотных) системах ГЗУ возвращается вода с тем же содержанием взвеси и той же величиной рН обычно до предела насыщенная растворимыми солями (CaSO4 Na2SO4 и др.). Солесодержание ее достигает 2500—3500 мгл.
Чтобы не допустить загрязнения воды в водоеме (особенно в месте ввода) сброс воды с золоотвалов необходимо проводить рассосредоточенно и разбавлять ее водой водоема. При содержании в золе СаО + МgО + Na2O > 16% сливаемую воду следует разбавлять в 200 раз при сухих золоуловителях и в 100 раз при мокрых. При содержании этих примесей 10 и 15 % - соответственно в 50—100 раз а при содержании щелочей 10 % — в 50 раз при любых видах золоуловителей.
4 Продувочные воды парогенераторов испарителей и паропреобразователей
Эти воды содержат все соли присутствовавшие в питательной (химически обработанной) воде и введенные в нее: NaOH Na2СО3 Na3PO4 и другие фосфаты а также Na2SO4 NaCl NaNO3 Na2SiO3 и в небольших количествах комплексоны. Общее содержание этих солей в продувочной воде от 500-1000 мгл (парогенераторы высокого давления) до 30000-50000 мгл (испарители).
Продувочную воду стремятся полностью использовать выделить из нее тепло и пар в расширителях тепло в теплообменниках. Ее используют для питания парогенераторов более низкого давления испарителей для подпитки закрытых теплосетей фосфатирования циркуляционной воды (при невысокой щелочности и большом содержании в ней фосфатов) для растворения соли (при невысоком содержании сульфатов). Количество продувочной воды 1—5 % от паропроизводительности. После выделения пара в расширителях количество продувочной воды уменьшается на 15—25 % и настолько же возрастает концентрация солей. При сбросе в канализацию горячей щелочной продувочной воды котлов и испарителей и расхолаживании ее жесткой (>7—10 ммольл) водой канализация может зарастать отложениями СаСО3 Са3(Р04)2.
5.Сбросные воды водоподготовительных установок
Эти воды обычно загрязнены взвесью кислотами щелочами и нейтральными солями и образуются на одной и той же ВПУ на разных этапах обработки воды. Количество сточных вод зависит как от схемы обработки воды так и от количества содержащихся в исходной воде и удаляемых при обработке ее загрязнений от качества реагентов (коагулянта извести поваренной соли) и наличия в них балласта.
Ниже приводятся краткие сведения о сточных водах ВПУ ориентировочных количествах их содержащихся в них загрязнениях и способах очистки или утилизации с целью сокращения сброса этих вод и загрязнения ими водоемов.
Сбросные воды реагентного хозяйства содержат примеси реагентов применяемых на водоподготовительных установках (CaO FeSO4 Аl2(SO4)3 NaCl Н2SO4 NaOH СаСО3) и песок содержащиеся в извести нерастворимые остатки содержащиеся в реагентах. Концентрация примесей может быть значительна но количество этих вод невелико (01—05 % от количества обработанной воды). Поступление этих вод периодическое не регулярное. Целесообразно направлять их в систему ГЗУ или на иловые площадки. Перед сбросом в водоемы взвешенные примеси должны быть удалены а содержание растворенных примесей доведено до допустимых значений путем разбавления технической водой.
Продувочные воды осветлителей получаются более или менее постоянно ежесуточно в количестве 1-3 % от объема обработанной воды. Они содержат 05-20 % (по массе) сухого шлама (СаСО3 Мg(ОН)2 Аl(ОН)3 Fе(ОН)3) и направляются в специальные уплотнители для увеличения концентрации сухого вещества в шламе до 5 % и более (отстой в течение 1—2 сут). Осветленная вода должна подаваться обратно в осветлители или на механические фильтры а уплотненный шлам — на вакуумные рамные или другие фильтры или на фильтрпрессы. Фильтрат после специальных фильтров для обезвоживания шлама должен возвращаться на механические зернистые фильтры ВПУ. Утилизация продувочных вод предочисток должна быть полная.
Сбросные воды после промывки механических зернистых фильтров или при спуске первого фильтрата получаются периодически; за одну промывку 40-100 м3 при общем расходе 2-5 % от количества обрабатываемой воды. Они загрязнены взвесью того же состава что и продувочная вода осветлителей но в меньшем количестве. В среднем - 500-1000 мгл. Эти воды должны быть после отстаивания (до содержания взвеси 50—100 мгл) полностью возвращены на фильтры или в осветлители а неотстоенные или при большем содержании взвеси — только в осветлители.
Сбросная вода после взрыхления предочищенной или умягченной водой всех ионитных фильтров и не засоленная вода после их опорожнения содержат небольшое количество взвеси и продуктов распада ионитов. Эти воды должны использоваться вместе с промывочными водами механических фильтров - хуже с продувочными водами осветлителей. Количество их 2—5 % от объема профильтрованной воды. Воды указанные в пп. 2—4 обработки реагентами не требуют.
Сбросные воды после регенерации Na- H H-Na-катионитных фильтров состоят из двух видов: отработанного раствора с содержанием регенерирующих реагентов NaC
отмывочных вод с содержанием тех же загрязнений от 10-05 % до нуля. Объем 3—5 % от количества профильтрованной воды.
Хотя содержание NaC CaSO4 MgSO4 MgC содержание NН4+ не должно превышать 5 мгл. С целью сокращения сброса NaCl CaCl2 MgCl2 на 30-50 % рекомендуются повторное пропускание части отработанного регенерационного раствора не насыщенной Са2+ и Мg2+ через истощенный Na-катионит предварительно перед пропусканием свежего раствора (что сокращает расход регенерирующего реагента на 30-50 %) и обработка дважды отработанного раствора соли содой и известью для осаждения СаСО3 и Mg(OH)2.
В отдельных случаях более целесообразны возврат отработанного раствора соли и отмывочных вод после Na-катионитных фильтров и обработка их известью и содой в осветлителях вместе с исходной водой в схемах подготовки воды для нетребовательных потребителей. При этом сброс сточных вод с ВПУ практически прекращается (~1 %) но возрастают солесодержание питательной воды и количество продувочной воды котлов. Общее количество сбросных вод энергообъекта при этом сокращается. Мягкие продувочные воды котлов могут использоваться для подпитки закрытых тепловых сетей питания испарителей растворения реагентов или для других целей.
Значительно сложнее утилизация или очистка сбросных вод после Н- или Н—Na-катионитных фильтров. Отработанный регенерационный раствор серной кислоты после регенерации и первые порции отмывочной воды содержат значительное количество (100—140 ммольл) CaSO4 и свободную (неизрасходованную для обмена на Са2+) серную кислоту. CaSO4 содержится в количествах в 2-4 раза превышающих предел насыщения воды при 20—25 °С. При таком пресыщении раствор очень нестабилен и склонен к выделению CaSO4 в дренажных системах на стенках труб резервуаров фильтров и т.д. что приводит к увеличению времени отмывки и перерасходу воды.
Содержащиеся в отработанном растворе и промывочной воде остатки кислоты должны пропускаться через предвключенный Н-катионитный фильтр (для "голодной" регенерации). Пройдя через фильтр отработанный раствор теряет кислоту приобретает нейтральную реакцию и содержит большие количества Са2+ + Мg2+. После разбавления технической водой до содержания Са2+ 20 ммольл этот раствор может быть сброшен в систему ГЗУ городскую канализацию или в водоем.
Отработанный раствор кислоты после Н-катионитных фильтров II—III ступеней содержащий большие количества свободной кислоты и немного Са2++ + Мg2+ должен подаваться для регенерации фильтров I ступени или предвключенных фильтров с "голодной" регенерацией (сдвоенные последовательные регенерации.
Нейтрализация отработанных растворов кислоты и промывочной воды Н-катионитных фильтров допускается только первыми порциями отработанного раствора щелочи после регенерации анионитных фильтров преимущественно I—II ступеней насыщенных Na2SiO3 Na2SO4 NaCl которые не могут быть использованы более целесообразно. Применение для нейтрализации кислых стоков свежей щелочи запрещается.
Как правило все кислые воды должны нейтрализоваться известковым молоком молотой известью магнезитом хуже молотым мелом и доломитом. Возможно применение шлама из осветлителей содержащего СаСО3 (мел мрамор) + Мg(OН)2. Шлам содержащий только А1(ОН)3 или Fе(ОН)3 для нейтрализации непригоден так как соли Fе2(SO4)3 или Al2(SO4)3 сами имеют кислую реакцию.
Отработанные регенерационные растворы (щелочи) и отмывочные воды после регенерации анионитных фильтров из-за их большого объема (15—20 м3м3 анионита) должны быть использованы внутри самой водоподготовительной установки по следующей схеме:
а) первые порции отработанных растворов насыщенные Na2SO4 NaCl Na2S
б) следующие порции содержащие меньшие количества NaCl Na2SO4 Na2S
в) отмывочные воды также должны использоваться последовательно для отмывки фильтров а в случае невозможности такого использования — для растворения щелочи соли (щелочность раствора соли 2—3 ммольл) для питания парогенераторов не требующих высокого качества питательной воды для подпитки закрытой теплосети (не имеющей бойлеров с латунными трубками и не используемой для подогрева воды систем горячего водоснабжения);
г) отмывочные воды анионитных фильтров с невысоким содержанием Na2SO4 NaCl Na2SiO3 могут подаваться в осветлители взамен СаО и Na2CO3.
В технологической части работы произведен расчет принципиальной тепловой схемы энергоблока с турбиной Т-175-130 определен баланс пара и воды осуществлена оценка экономичности энергоблока и произведен выбор основного и вспомогательного оборудования в соответствии с принятой тепловой схемой была выбрана схема водоподготовки для котла марки Е-820-140 ГМ.
Результаты расчетов показали что выбранный тип основного и вспомогательного оборудования сходится с типом комплектующего оборудования данной турбины.
Данные полученные в результате расчетов свидетельствуют что основные показатели соответствуют типовым требованиям для проектирования ТЭЦ.
В конструкторской части работы был осуществлен тепловой и прочностной расчет деаэратора ДП-1000 цель которого – определение гидравлических сопротивлений по воде и по пару и установление характера зависимости этих сопротивлений от диаметра трубок деаэратора и скорости движения охлаждающей воды в них. В результате были получены соответствующие прототипным данным основные характеристики деаэратора и его геометрические размеры. Итоги расчета показали соответствие деаэратора современным стандартам.
В специальной части работы проведен тепловой расчет и компоновка воздухоподогревателя для котла марки Е-820-140 ГМ а также установлены зависимости температуры подогретого воздуха от температуры (холодного) воздуха подаваемого в воздухоподогреватель и от расхода дымовых газов через воздухоподогреватель.
В части природоохранные мероприятия были рассмотрены сточные воды и методы их очистки.
Александров А.А. Григорьев Б.А. Таблицы теплофизических свойств воды и водяного пара. Справочник. М.: Издательство МЭИ 1999 г.
Рихтер Л. А. Елизаров Д. П. Лавыгин В. М. Вспомогательное оборудование тепловых электростанций: Учебное пособие для вузов. – М.: Энергоатомиздат 1987. – 216 с.
Клименко А. В. Зорин В. М. Теплоэнергетика и теплотехника. – 3-е изд. перераб. и доп. Книга третья. – М.: Издательство МЭИ 1999.
Капелович Б.Э. Эксплуатация паротурбинных установок – «Энергия» Москва 1975. – 246 с.
Назмеев Ю.Г. Лавыгин В.М. Теплообменные аппараты ТЭС. – 4-е изд. М.: Издательский дом МЭИ 2007. – 61 с.
Клименко А. В. Зорин В. М. Теплоэнергетика и теплотехника. – 3-е изд. перераб. и доп. Книга первая. – М.: Издательство МЭИ 1999. – 424 с.
Григорьев В.А. Зорин В.М. Тепловые и атомные электрические станции: Справочник – 2-е изд. перераб. М.: Энергоатомиздат 1989.
Абрамов А.И. Елизаров Д.П. Повышение экологической безопасности ТЭС – М.: Издательство МЭИ 2001. – 143 с.
Маликов Е.А. – Методические указания по оформлению пояснительной записки выпускной работы на степень бакалавра –ВФ МЭИ (ТУ) Волжский 2001.
Бойко Е. А. Котельные установки и парогенераторы (конструкционные характеристики энергетических котельных агрегатов) Е. А. Бойко Т. И. Охорзина. Красноярск: ИПЦ КГТУ 2004. 228 с.
Кострикин Ю. М. - Водоподготовка и водный режим энергообъектов низкого и среднего давления. Справочник. - М.: Энергоатомиздат 1990.
Копылов А.С. Лавыгин В.М. Очков В.Ф. Водоподготовка в энергетике: Учебное пособие для вузов М.: Издательство МЭИ 2003.