Переборная коробка



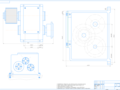
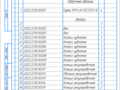
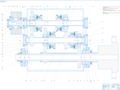
- Добавлен: 24.01.2023
- Размер: 1 MB
- Закачек: 0
Описание
Переборная коробка
Состав проекта
![]() |
![]() ![]() ![]() |
![]() |
![]() ![]() ![]() ![]() |
![]() ![]() ![]() ![]() |
![]() ![]() ![]() ![]() |
![]() |
![]() |
Дополнительная информация
РГР ишмухаметов.doc
Анализ функционального назначения проектируемого модуля определение его подсистем и разработка кинематической структуры5
Определение основных технических характеристик модуля8
1. Основные технологические условия использования станка8
2. Характерные сочетания технологических условий8
3. Определение значений предельных режимов резания и наибольшей (расчетной) эффективной мощности8
4. Определение расчетных значений технических характеристик
5. Анализ технических характеристик модулей аналогичных станковОшибка! Закладка не определена.
Определение компоновок станка и модуляОшибка! Закладка не определена.
Разработка кинематической схемы модуля11
1. Определение кинематики проектируемого модуля12
2. Определение знаменателя ряда регулирования12
3. Уточнение используемых значений частот вращения вала электродвигателя13
4. Определение характерных частот вращения шпинделя13
5. Определение компоновки АПК и построение структурной сетки13
6. Определение передаточных отношений привода.16
7. Определения чисел зубьев зубчатых колес и диаметров шкивов.16
Анализ схем обработки и методов формообразования поверхностей деталей
Таблица 1.1 – Основные переходы обработки для предлагаемых операций
Наименование переходов обработки
Состав исполнительных движений
Равномерное изменение частоты вращения шпинделя с учетом температуры в зоне резания с целью обеспечения производительности и снижения себестоимости обработки
Равномерное изменение частоты вращения шпинделя с учетом температуры в зоне резания и диаметра обработки с целью обеспечения производительности и снижения себестоимости
Равномерное изменение частоты вращения шпинделя с учетом температуры в зоне резания с целью обеспечения производительности и снижения себестоимости
Анализ функционального назначения проектируемого модуля определение его подсистем и разработка кинематической структуры
В качестве двигателя для привода главного движения выбираем двигатель с бесступенчатым регулированием а для увеличения диапазона частот обеспечиваемых с постоянной мощностью разрабатываемым приводом применяем автоматическую переборную коробку (АПК) (рис.2.1.). Для регулирования скорости вращения двигателя необходим датчик скорости (ДС). Решение о выборе двигателя с бесступенчатым регулированием принято также с учетом того что мехатронный станок должен обеспечивать изменение скорости резания с контролем температуры резания для повышения производительности и снижения себестоимости обработки.
Определение функциональных подсистем:
Функциональные подсистемы второго уровня:
обеспечение пуска и останова (ПО);
обеспечение реверсирования движения (РД);
обеспечение скорости движения (СД);
обеспечение перемещения (ПМ).
Функциональные подсистемы третьего уровня:
Пуск и останов (ПО)
Ускорение бесступенчатое (УБ)
Торможение бесступенчатое (ТБ)
Реверсирование движения (РД)
Выбор направления движения (ВН)
Реверсирование бесступенчатое (РБ)
Скорость движения (СД)
Настройка бесступенчатая (НБ)
Стабилизация скорости (СТ): изменение скорости в процессе резания (ИС)
В качестве конструктивного тип модуля главного движения по аналогии со станком модели 800VHT принят простой модуль главного вращательного движения (тип 1).
Таблица 2.1 – Функциональные подсистемы модуля главного вращательного движения
Функциональные подсистемы
Для проектируемого модуля
Простой модуль главного движения
РД1[(ПО1) ВН11РП11)]
СД1[(ПО1)(РД1)НБ11ИС23]
Подсистемы УБ23 и ТБ23 обеспечивают параметры определяющие бесступенчатое изменение скорости движения.
Ввод подсистемы ИС23 необходим для обеспечения необходимых параметров движения повышения производительности изготовления детали и снижения себестоимости обработки. Для реализации работы этой подсистемы необходимы датчик скорости и датчик температуры резания.
С учетом установленного состава функциональных подсистем разработана блок-схема модуля согласно с рисунком 2.1.
Структура модуля главного движения разработана с учетом блок-схемы и особенностей выполнения переходов обработки показана на рисунке2.2.
Рисунок 2.1 – Блок-схема модуля главного движения
СУ – система управления; ДПТ – двигатель постоянного тока;
АПК – автоматическая переборная коробка; ИО – исполнительный орган;
ДС – датчик скорости; ДТ – датчик температуры.
Рисунок 2.2 – Структура модуля главного движения
РДПТ – регулируемый двигатель переменного тока; СУ – система управления; ЭД-электродвигатель; АПК – автоматическая переборная коробка; ИО – исполнительный орган; ДС – датчик скорости; ДТ – датчик температуры.
Определение основных технических характеристик модуля
1. Основные технологические условия использования станка
К этим условиям относятся:
обрабатываемые материалы и их предельные характеристики – конструкционная сталь с твердостью HB150 по таблице 26 [3] для HB 260 принимаем sв = 530 МПа.
основные переходы обработки – точение продольное и поперечное сверление;
глубиной резания (при токарной обработке) t = 2 мм;
предельные диаметры обработки dmax = 400 мм dmin = 025 × 400 = =100мм.
2. Характерные сочетания технологических условий
К этим сочетаниям относятся условия определяющие vmin Smax и Nэфmax – наиболее тяжелый режим обработки который соответствует черновому продольному точению и условия определяющие vmax – наиболее легкий режим обработки соответствующий чистовому поперечному точению.
3. Определение значений предельных режимов резания и наибольшей (расчетной) эффективной мощности
Наибольшая подача Smax определяется по таблице 1 [6] согласно установленным характерным условиям обработки детали. Для чернового продольного точения конструкционной стали при диаметре обработки dmaх=400мм наибольшие размеры державки резца 16х25мм при использовании твердосплавного резца и наибольшей глубине резания t=2мм – Smax=1ммоб.
Наименьшая подача Smin определяется по таблице 2 [6] согласно характерным условиям обработки детали. С учетом достижения средней чистоты поверхности при чистовом точении вспомогательном угле в плане 5° значении скорости резания > 130 ммин наименьшем радиусе при вершине резца 1 мм Smin = 014 ммоб.
Наименьшая скорость резания с учетом применения твердосплавного инструмента находится по таблице 4 [6]. Для чернового продольного точения конструкционной стали (sв 150 МПа) с учетом глубины резания t = 2 мм с наибольшей подачей 1 ммоб определяется vmin = 121 ммин.
Наибольшая скорость резания также находится по таблице 4 [6]. Для чистового поперечного точения конструкционной стали с учетом глубины резания tmax = 05 мм (по таблице 4 [6] наименьшее значение составляет 14 мм) с наименьшей подачей 017 ммоб (по таблице 4 [6] ближайшее значение составляет 014 ммоб) определяется vmax = 205 ммин.
Расчет для sв 150 МПа
Рисунок 3.1 – Расчет режима резания с помощью ППП «СТАНКИН»
Наибольшее значение эффективной мощности резания определяется при помощи программы «Rezim» [6] для условий обработки соответствующих vmin. При черновом продольном точении заготовки из конструкционной стали диаметром D=400мм твердосплавным резцом с t=2мм S=1ммоб V=130ммин максимальное значение эффективной мощности резания Nэф=5.93кВт.
4. Определение расчетных значений технических характеристик модуля
Предельные значения частоты вращения шпинделя определяются по формулам:
Мощность приводного электродвигателя
где h – к.п.д. привода ориентировочно h=08; kп – допускаемый коэффициент перегрузки двигателя kп=08; при указанных коэффициентах Nэл=Nэф.
Способ регулирования частот вращения шпинделя выбирается с учетом структуры модуля и алгоритмов его работы. В случае бесступенчатого регулирования с учетом плавности регулирования характеризуемой знаменателем геометрической прогрессии ряда частот вращения шпинделя j находится количество ступеней частот вращения шпинделя.
5. Анализ технических характеристик модулей аналогичных станков
Этот этап выполняется с целью уточнения расчетных данных технических характеристик проектируемого модуля с учетом опыта проектирования аналогичного оборудования. В табличном виде приводятся данные по современным станкам такого же типоразмера который определяется по наибольшему диаметру заготовки обрабатываемому на станке D=14×dmax D=560мм.
Ближайший типоразмер станка характеризуется D=800мм. К станкам-аналогам относятся токарные станки с ЧПУ данного типоразмера;
В качестве станка-аналога для проектируемого модуля был выбран станок 800VHT. Станок токарный сверлильно-фрезерно-расточный с числовым программным управлением (ЧПУ) и автоматической сменой инструмента (АСИ) класса точности П по ГОСТ 8 модели 800VНТ предназначен для комплексной обработки деталей сложной формы. На станке может производиться токарная обработка на вращающемся столе сверление зенкерование развертывание отверстий нарезание резьбы метчиками а также получистовое и чистовое прямолинейное и контурное фрезерование деталей зубофрезерование чистовое растачивание отверстий и шлифовка
На основании сведений полученных для модуля станка-аналога проводится корректировка расчетных значений технических характеристи проектиру-емого модуля. С учетом опыта проектирования современных аналогичных станков и применения прогрессивного режущего инструмента допускается увеличение значения наибольшей расчетной частоты вращения шпинделя на 25%. Уточнение технических характеристик проектируемого модуля представлено в таблице 3.2.
Таблица 3.2 – Уточнение технических характеристик проектируемого модуля
Рисунок 4.2 – Компоновка проектируемого модуля
Компоновка модуля должна быть согласована с компоновкой станка. Приводной электродвигатель целесообразно располагать с учетом обеспечения наименьших габаритов станка.
Согласно заданию курсового проекта выбран модуль с раздельной компоновкой т.е. АКП будет располагаться раздельно от шпиндельной бабки и соединяться с ней с помощью ременной передачи. Движение от двигателя будет передаваться АКП через ременную передачу.
К преимуществам этой компоновки относится разгрузка шпиндельной бабки от значительного веса АКП обеспечение повышенных требований к точности вращения виброустойчивости теплостойкости. Но вследствие применения ременной передачи повышаются нагрузки на шпиндель.
Разработка кинематической схемы модуля
наибольшая частота вращения шпинделя nma
наименьшая частота вращения шпинделя nm
регулирование частот вращения шпинделя – бесступенчатое;
двигатель асинхронный АИР132М6 У2 380 В 50 Гц IM1081 ТУ16-525.571-84;
наибольшая частота вращения электродвигателя nэma
номинальная частота вращения электродвигателя nэном = 1000 обмин;
мощность электродвигателя Pэном = 75 кВт.
1. Определение кинематики проектируемого модуля
Диапазон регулирования привода:
Диапазон регулирования с постоянной мощностью:
где b = 4 для токарных станков
Диапазон регулирования с постоянным моментом:
Диапазон регулирования двигателя по полю с постоянной мощностью:
Для выбранного электродвигателя
2. Определение знаменателя ряда регулирования.
Первоначально знаменатель ряда принимается равным диапазону регулирования двигателя по полю с постоянной мощностью:
Расчетное число ступеней коробки
Т.к. число диапазона регулирования должно быть целым округляем в большую сторону принимаем Zпк = 3.
Знаменатель ряда частот вращения:
При определении знаменателя должны выполняться условия:
Диапазоны регулирования привода уточняются с учетом принятого значения знаменателя
3. Уточнение используемых значений частот вращения вала электродвигателя.
Наибольшая и наименьшая частоты
4. Определение характерных частот вращения шпинделя.
Определяем по рекомендациям
n1 = nP = nmin RПТ = 120 197 = 237250 обмин
n2 = n1 φпк = 250 156 = 390400 обмин
n3 = n2 φпк = 400 156 = 624630 обмин
n4 = n3 φпк = 630 156 = 9821000 обмин
Уточненная наибольшая частота вращения шпинделя
nmax = 102 250 = 1510 обмин
5. Определение компоновки АПК и построение структурной сетки.
Для выбранной структуры привода возможен следующий кинематический порядок привода:
Данный вариант обеспечит возможность построения привода с минимальным числом валов зубчатых колес и подшипников.
Характеристики множительных групп будут иметь значения:
P11 = 2; X11 = 2; P22 = 2; X22 = 2.
В соответствии с принятой структурной формулой составляем принципиальную кинематическую схему привода:
Рисунок 5.1 – Принципиальная кинематическая схема проектируемого привода
В соответствии с этим структурная сетка привода будет выглядеть следующим образом:
Рисунок 5.2 – Структурная сетка
Пользуемся следующими принципами построения графика:
) симметричность графика;
) избегать предельных частичных передаточных отношений.
Рисунок 5.3 – График частот вращения разрабатываемого модуля
n1 = 250 обмин – расчетная цепь
6. Определение передаточных отношений привода.
Используя график определяются значения передаточных отношений всех передач привода:
7. Определения чисел зубьев зубчатых колес и диаметров шкивов.
Представление передаточных отношений в виде простых дробей:
Один из диаметров шкивов принимается в виде стандартного значения .
Затем выполняется проверка кинематического расчета. Определяются фактические частоты вращения с учетом принятых чисел зубьев.
n1ф = nэ min ip i1 i3 = 508 05 = 55 обмин
n2ф = nэ ном ip i1 i3 = 1000 05 = 110 обмин
n3ф = nэ ном ip i2 i3 = 1000 05 = 200 обмин
n4ф = nэ ном ip i1 i4 = 1000 05 = 400 обмин
n5ф = nэ ном ip i2 i4 = 1000 05 = 780 обмин
n6ф = nэ max ip i2 i4 = 1578 05 = 1230 обмин
Как видно из расчетов частоты вращения шпинделя практически совпадают со стандартными. Для обеспечения бесступенчатого регулирования необходимо и достаточно чтобы выполнялись условия
n3ф = nэ max ip i1 i3 = 1578 063 = 202 обмин
n4ф = nэ max ip i2 i4 = 1580 063 = 1231 обмин
При данных соотношениях чисел зубьев обеспечиваются все частоты без разрывов в графике частот.
Отклонения фактических частот вращения шпинделя от стандартных значений находятся в допускаемых пределах (±41 %) cледовательно числа зубьев подобраны правильно обеспечив при этом отсутствие разрывов и бесступенчатое изменение скорости вращения шпинделя. Уточненная схема кинематическая схема представлена на рисунке5.4.
Рисунок 5.4 – Уточненная принципиальная кинематическая схема проектируемого привода
Определение расчетных нагрузок и проектные расчеты деталей.
1. Расчет мощности на валах.
где i - коэффициент потери мощности для i-того вала.
Коэффициенты принимаем по [2 таблица 1.1]
где под – КПД пары подшипников принимаем под = 099
рем – КПД ременной передачи принимаем рем = 097
PI = 75 096 = 72 кВт
где зп – КПД закрытой зубчатой цилиндрической передачи с опорами принимаем зп = 098
II = 096 099 098 = 093
PII = 72 093 = 67 кВт
III = 093 099 098 = 090
PIII = 67 090 = 6 кВт
2 Расчет максимальных моментов на валах.
Момент на i-том валу:
где ni – расчетная частота вращения i-того вала.
3. Расчет минимальных диаметров валов.
Предварительный расчет валов ведется на кручение по передаваемой мощности.
Диаметр выходного конца i-того вала:
Принимаем dI = 35 мм
Принимаем dII = 40 мм
Принимаем dIII = 45 мм
Определение расчетных оборотов для передач:
4 .Выбор электромагнитных муфт.
Выбор муфт произведен по максимальному моменту на валах и максимальной частоте вращения валов.
Номинальный момент муфты на i-том валу вычисляли по формуле
где kм – коэффициент безопасности равный 11.
По полученным результатам принимаем муфты: на оба вала Э1М092-1Н по ГОСТ 21573-76.
5. Проектный расчет зубчатых передач.
Из условия оптимизации габаритов для всех зубчатых колес принимаем сталь 20Х с последующей цементацией (HRC 56-62).
Так как НВ>350 то допускаемые контактные напряжения определяются по формуле
где – предел контактной выносливости по поверхности зуба;
n – коэффициент безопасности n = 11.
Максимальное допускаемое напряжение изгиба равно
где – предел выносливости поверхности зуба по изгибу
- коэффициент долговечности = 1;
- коэффициент реверсивности нагрузки = 1.
6. Расчет зубчатых передач.
6.1. Расчёт передачи i1.
Проектировочный расчет межосевого расстояния по условию контактной прочности:
KH – принимаем равным 12
BA – рекомендуют принимать в промежутке (015 018) принимаем BA=016.
Модуль из расчета по контактным напряжениям
Модуль из расчета по напряжениям изгиба:
где – коэффициент распределения нагрузки между зубьями и коэффициент динамической нагрузки =112 =101;
– коэффициент формы зуба =405.
Принимаем ближайшее стандартное значение по СТ СЭВ310-76 mn = 25.
Уточняем межосевое расстояние:
Определение геометрических параметров передачи.
Делительный диаметр:
По таблице П.37 выбираем восьмую степень точности изготовления зубчатых колес.
6.2. Расчёт передачи i2.
Принимаем значение по передаче i1 mn = 25
Определение геометрических параметров передачи:
По таблице П.37. выбираем восьмую степень точности изготовления зубчатых колес.
6.3. Расчёт передачи i3.
6.4.Расчёт передачи i4
Определение геометрических параметров передачи:
7 Проверочный расчет зубчатых передач
Допускаемые контактные напряжения [H]=1296МПа. Допускаемые напряжения изгиба [F]=572МПа.
Проверочный расчет произведем по программе «Комплекс инженерных расчетов». В меню программы выберем «расчет зубчатой передачи».
Расчет передач представлен на рисунках 5.1 – 5.4
Рисунок 5.1 – Результаты проверочного расчета передачи i1
Рисунок 5.2 – Результаты проверочного расчета передачи i2
Рисунок 5.3 – Результаты проверочного расчета передачи i3
Рисунок 5.4 – Результаты проверочного расчета передачи i4
8.Расчет ременной передачи.
Проверочный расчет ременной передачи произведен по программе «Комплекс инженерных расчетов» приведены на рисунках 5.5 и 5.6.
8.1.В меню программы выберем «расчет ременной передачи с клиновым ремнем».
Рисунок 5.5 – Результаты проверочного расчета ременной передачи с клиновым ремнем.
8.2.В меню программы выберем «расчет ременной передачи с поликлиновым ремнем».
Рисунок 5.6 – Результаты проверочного расчета ременной передачи с поликлиновым ремнем.
В целях уменьшения габаритных размеров проектируемого модуля выбираем поликлиновую ременную передачу с меньшим геометрическим показателем.
Рисунок 5.7.-Эскиз первого вала.
Рисунок 5.8-Эскиз второго вала.
10. Схема свертки валов.
Необходимость в свертке валов возникает в связи со стремлением уменьшить габаритные размеры коробки. Данная схема является более приемлемой с точки зрения зацепления зубчатых колес.
Рисунок 5.9 Схема свертки валов.
11.Проверочный расчет 2 вала
Рисунок 5.10. Схема развертки валов.
Рисунок 5.11Схема сил действующих на вал
l1 = 51 мм l2 = 343 мм l3=391мм
Реакции опор определяются следующим образом:
Сумма моментов относительно точки А в горизонтальной плоскости:
Горизонтальная составляющая реакции опоры В:
Горизонтальная составляющая реакции опоры А:
Сумма моментов относительно точки A в вертикальной плоскости:
Вертикальная составляющая реакции опоры B:
Вертикальная составляющая реакции опоры A:
Изгибающие моменты в плоскостях:
В горизонтальной плоскости:
В вертикальной плоскости:
Суммарные моменты в характерных точках определяется по формуле:
Эпюры изгибающих моментов представлены на рисунке 5.12.
Рисунок 5.12 Эпюры изгибающих моментов.
12 Проверочный расчет подшипников 2 вала.
Выбираем подшипники для второго вала 12208 ГОСТ 83328-75
- ресурс в часах =20000 часов
а - коэффициент учитывающий качество материала и условия
n - номинальная частота вращения промежуточного вала n= 400обмин
Данный подшипник при заданном режиме нагружения обеспечивает необходимую долговечность.
13. Проверочный расчет шпоночных соединений.
Назначаем допуск напряжения смятия []=80 .120
Второй вал ( шпонка на передаче )
Назначим шпонку b=12 h=8
Округлим по ряду до ближайшего значения
Шпонка 12x8x40 ГОСТ 23360-78
Шпиндельный вал ( шпонка на передаче )
Назначим шпонку b=14 h=9
Шпонка 14x9x45 ГОСТ 23360-78
Расчет шпиндельного узла.
Выбор и расчет параметров шпиндельного узла производим с помощью системы «Шпиндель».
Выбираем конструкцию шпинделя с фланцевым концом для токарных станков. Максимальный диаметр обработки выбираем 400 мм. Максимальная частота вращения шпинделя выбираем исходя из пункта 5.3. равное 800 обмин.Выбранная конструкция представлена на рисунке 6.1. с указание всех размеров.
Рисунок 6.1 Выбор конструкции шпинделя.
Далее выбираем опоры шпинделя как показано на рисунке 6.2.
Рисунок 6.2. Выбор опор шпинделя.
Дунаев П.Ф. Леликов О.П. Конструирование узлов и деталей машин – М.: Высш. шк. 1985 – 416с.
Чернавский С.А. Курсовое проектирование деталей машин М.: Машиностроение. 1988г.
Анурьев В.И. Справочник конструктора-машиностроителя. В 3-х томах. - 6-е издание переработано и дополнено. - М.: Машиностроение 1982. -736 с.
Проников А.С. Металлорежущие станки и автоматы – М.: Машиностроение. 1981г – 479с.
Справочник технолога-машиностроителя. В 2-х томах. Т. 2. Под редакцией А.Г. Косиловой и Р. К. Мещерякова. 4-е изд. - М.: Машиностроение 1986 год. 496 с.
Пакеты прикладных программ к подсистемам САПР металлорежущих станков. ЭНИМС СТАНКИН. М. 1985 – 2002.
«Справочник технолога-машиностроителя». В 2-х томах. Т. 2. Под редакцией А.Г. Косиловой и Р. К. Мещерякова. 4-е изд. - М.: Машиностроение 1986 год. 496 с.
«Проектирование приводов главного движения и подачи металлорежущих станков» Методические указания Составители: Куликов Кудояров и др. Уфа УАИ 1988 42 с
Пуш В.И. «Проектирование металлорежущих станков». М.: Машиностроение 1987 г. 293 с. ил.
Чертеж.cdw

Биение конусных рабочих поверхностей канавок шкива не более 0
Обкатку производить в течение 2 часов.
Время обкатки при установившейся температуре 1 час при 2500 обмин.
Неравномерный шум и чрезмерный нагрев при работе переборной коробки не допускаются.
редуктор 1.cdw

маслостойкой краской.
Биение конусных рабочих поверхностей канавок шкива не
Обкатку производить в течение 2 часов.
Время обкатки при установившейся температуре 1 час при 2500
Неравномерный шум и чрезмерный нагрев при работе переборной
коробки не допускаются.
Спецификация.cdw

Кольцо регулировочное
ПКольцо регулировочное
Пояснительная записка
Муфта Э1М111-2Н ГОСТ21573-76
Винт М 6 х 25 ГОСТ 1491-80
Винт М 8 х 20 ГОСТ 1491-80
Винт М 8 х 25 ГОСТ 1491-80
Винт М 8 х 40 ГОСТ 1491-80
Винт М 8 х 50 ГОСТ 1491-80
Винт М1 0 х 40 ГОСТ 1491-80
Гайка М 60 ГОСТ 11871-88
Гайка М 70 ГОСТ 11871-88
Прокладка регулировочная
Кольцо А 32 ГОСТ 13943-86
Кольцо А 36 ГОСТ 13943-86
Манжета 1-70х95ГОСТ 8752-79
Подшипник 36915 ГОСТ 7634-75
Подшипник 1000909 ГОСТ 8338-75
Подшипник 1000910 ГОСТ 8338-75
Кольцо А 65 ГОСТ 13943-86
Кольцо А 48 ГОСТ 13943-86
Кольцо А 60 ГОСТ 13943-86
Кольцо А100 ГОСТ 13943-86
Подшипник 208 ГОСТ 8338-75
Манжета 1-90х120ГОСТ 8752-79
Кольцо А 42 ГОСТ 13943-86
Манжета 1-35х78ГОСТ 8752-79
Подшипник 207 ГОСТ 8338-75
Подшипник 36912 ГОСТ 7634-75
Шайба 6 Н ГОСТ 6402-70
Шайба 8 Н ГОСТ 6402-70
Шайба 10 Н ГОСТ 6402-70
Штифт 8 х 35 ГОСТ 3128-70
Рекомендуемые чертежи
Свободное скачивание на сегодня
- 29.08.2014
- 25.01.2023
Другие проекты
- 14.02.2017