Одноступенчатый редуктор





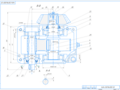

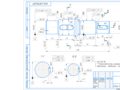
- Добавлен: 24.01.2023
- Размер: 475 KB
- Закачек: 0
Описание
Состав проекта
![]() |
![]() |
![]() ![]() ![]() |
![]() |
![]() |
![]() ![]() ![]() ![]() |
![]() ![]() ![]() ![]() |
![]() ![]() ![]() ![]() |
![]() ![]() ![]() |
![]() ![]() ![]() ![]() |
![]() |
![]() ![]() ![]() |
![]() |
Дополнительная информация
моя пояснилка.doc
Назначение редуктора – понижение угловой скорости и соответственно повышение вращающего момента ведомого вала по сравнению с ведущим.
Редуктор состоит из корпуса в котором помещают элементы передачи – зубчатые колёса валы подшипники и т.д. В отдельных случаях в корпусе редуктора размещают так же устройства для смазывания зацеплений и подшипников или устройства для охлаждения.
Редуктор проектируют либо для привода определённой машины либо по заданной нагрузке (моменту на выходном валу) и передаточному числу без указания конкретного назначения.
Редукторы классифицируют по основным признакам: типу передачи (зубчатые червячные или зубчато-червячные) числу ступеней (одноступенчатые двухступенчатые и т.д.) типу зубчатых колёс (цилиндрические конические коническо-цилиндрические и т.д.) относительному расположению валов редуктора в пространстве (горизонтальные вертикальные) особенностям кинематической схемы (развёрнутая соосная с развёрнутой ступенью и т.д.).
В данном случае редуктор представляет собой прямозубую передачу. Редуктор является одноступенчатым установлен с горизонтальным расположением валов.
Выбор электродвигателя. Определение основных кинематических и энергетических параметров редуктора
Определение КПД привода. Общий КПД привода определяем по формуле:
где h - общий КПД привода;
hп12 – КПД подшипников качения;
hз – КПД зубчатой передачи [1].
Численные значения КПД определяем по таблице приведенной в [2]: hп12 = 099; hм = 098; hз = 096.
Подставив численные значения в формулу получим:
Определение требуемой мощности привода. Требуемая мощность привода определяется по формуле:
где Р - требуемая мощность привода кВт;
nвых – частота вращения выходного вала обмин [1].
Определение требуемой мощности электродвигателя. Требуемая мощность на валу электродвигателя определяется по формуле:
где Рр – мощность на валу электродвигателя кВт;
Р – номинальная мощность на ведомом валу привода кВт;
h - общий КПД привода [3].
По каталогу приведенному в [2] определяем мощность двигателя Рном=75 кВт.
Определение частоты вращения вала электродвигателя. Требуемая частота вращения вала определяется по формуле:
где n1 - требуемая частота вращения вала обмин;
n2 – частота вращения выходного вала обмин [1].
Подставив численные значения в формулу (1.4) получим:
Выбор электродвигателя. Согласно рассчитанным данным выбираем по каталогу двигатель марки 132S41440 асинхронная частота вращения 1440 обмин [1].
Определение передаточного числа редуктора. Общее передаточное число привода определяем по формуле:
где u - общее передаточное число привода;
n1 - частота вращения вала электродвигателя обмин;
n2 - частота вращения выходного вала обмин.
Расчет закрытой передачи
Выбор материала зубчатых колес. Основными условиями для выбора материалов и термообработки колес являются:
) критерии работоспособности условия нагружения и назначение машин. Наиболее типовым критерием работоспособности зубчатых колес является контактная прочность рабочих поверхностей зубьев. Допускаемые контактные напряжения в зубьях пропорциональны твердости материалов а допускаемая нагрузка передач по контактной выносливости пропорциональна квадрату твердости. Износостойкость и противозадирные свойства возрастают с увеличением твердости поверхностей зубьев поэтому целесообразно широкое использование зубчатых колес с высокой поверхностной твердостью зубьев;
) условие равнопрочности зубьев шестерни и колеса. Для обеспечения одинаковой контактной выносливости зубьев шестерни и колеса рекомендуется назначать такое сочетание материалов колес чтобы твердость поверхности зубьев шестерни превышала твердость зубьев колеса на 25 70 НВ;
) при твердости рабочих поверхностей зубьев обоих колес НВ > 350 передачи являются плохо прирабатывающимися при твердости НВ ≤ 350 хотя бы одного из колес возможна приработка зубьев. В связи с этим для колес с твердостью НВ > 350 назначаются марки стали подвергаемые закалке с нагревом ТВЧ цементации азотированию а при НВ ≤ 350 – стали подвергаемые улучшению редко – нормализации;
) технология изготовления зубчатых колес;
) конструкция размеры точность зубчатых колес методы обработки зубьев и виды термообработки [3].
Для колеса и шестерни выбираем материал – сталь 40ХН вид термообработки – улучшение.
Твердость поверхности колеса 235 262 НВ шестерни – 269 302НВ[1].
Определение допускаемых напряжений.
Допускаемое контактное напряжение рассчитывают для каждого зубчатого колеса передачи по формуле:
где [sН12] - допускаемое контактное напряжение МПа;
SН12 – коэффициент безопасности;
ZN12 – коэффициент долговечности [1].
Предел выносливости sНlim12 назначаем по эмпирическим зависимостям в зависимости от вида термообработки:
где - среднее значение твердости материала.
Коэффициент безопасности назначаем в зависимости от вида термообработки (в данной работе – улучшение) и принимаем SН12 = 11 [1].
Коэффициент долговечности ZN12 определяем по формуле:
где NHG12 – базовое число циклов;
NНЕ12 – эквивалентное число циклов до разрушения при расчетном контактном напряжении (при переменных режимах нагрузки) [5].
Эквивалентное число циклов определяем по формуле:
где mН – коэффициент эквивалентности;
NН12 – циклическая долговечность.
Коэффициент эквивалентности определяем в зависимости от режима работы и вида термообработке по таблице приведенной в [1]: mН = 018.
Циклическую долговечность определяем по формуле:
где с – число зацеплений зуба за один оборот (для проектируемого редуктора с = 1);
n12 – частота вращения того зубчатого колеса по материалу которого определяют допускаемые напряжения обмин;
t – время работы передачи (ресурс) ч; t = Lh [1].
Полученные данные подставляем в формулу :
Базовое число циклов NHG перемены напряжений рассчитывают по следующим эмпирическим зависимостям:
Полученные данные подставляем в формулу и определяем коэффициент долговечности ZN12:
По вычисленным данным определяем допускаемое контактное напряжение по формуле :
Из двух значений рассчитанного допускаемого контактного напряжения в дальнейшем для косозубых цилиндрических передач у которых зубья шестерни значительно тверже зубьев колеса за расчетное принимаем:
где [sН]min – меньшее из значений [sН1] и [sН2] [1].
Допускаемые напряжения изгиба [sF]12 вычисляются по формуле:
SF – коэффициент безопасности;
YА – коэффициент учитывающий влияние двустороннего приложения нагрузки;
YN – коэффициент долговечности [1].
Коэффициент безопасности принимаем SF = 11 при односторонней нагрузке YА = 1 [1].
Коэффициент долговечности YN определяем по формуле (при НВ ≤ 350):
где NFG – базовое число циклов;
NFE – эквивалентное число циклов.
Для всех сталей рекомендуют принимать NFG = 4×106 [5].
При переменных режимах нагрузки NFE определяют по формуле:
Коэффициент эквивалентности принимаем по таблице приведенной в [1]: mF = 006 [1].
По полученным данным определяем коэффициент долговечности YN по формуле :
Предел выносливости sFlim12 назначаем по эмпирическим зависимостям в зависимости от вида термообработки:
где - среднее значение твердости материала [1].
По полученным данным определяем допускаемые напряжения изгиба по формуле :
Проектный расчет зубчатой передачи. При проектном расчете прежде всего определяют межосевое расстояние аw мм. Для прямозубой передачи расчет производят по следующей формуле:
где u – передаточное число;
Т2 - вращающий момент на колесе передачи Н×мм;
КНb - коэффициент неравномерности нагрузки по длине контакта;
Епр – приведенный модуль упругости МПа;
[sН] - допускаемое контактное напряжение МПа;
yba – относительная ширина колес [1].
Так как в данной работе передача внешнего зацепления то в формуле принимаем знак +.
Коэффициент неравномерности нагрузки по длине контакта КНb выбирают в соответствии с расположением колес относительно опор и твердостью рабочих поверхностей зубьев колес по графику приведенному в [1]: КНb = 105.
Приведенный модуль упругости принимаем Епр = 21 × 105 МПа [1].
В соответствии со схемой расположения колес относительно опор и выбранной твердостью поверхностей зубьев назначаем относительную ширину колес по таблице приведенной в [1]: yba = 04.
Вычисленное межосевое расстояние округляем в большую сторону до стандартного значения: аw = 100 мм [2].
Геометрический расчет закрытой передачи. Модуль зацепления определяем из соотношения (при НВ ≤ 350):
Суммарное число зубьев шестерни и колеса определяем по формуле:
Число зубьев шестерни:
Число зубьев колеса:
Фактическое значение передаточного числа передачи определяем по формуле:
Погрешность значения фактического передаточного числа от номинального значения:
Определяем основные геометрические размеры
Определяем делительные диаметры
Шестерни: d1=z1xm=2x20=40мм
Колеса: d2=z2xm=80x2=160мм
Определяем диаметры вершин зубьев
Шестерни: dа1=d1+2xm=40+2x2=44мм
Колеса: dа2=d2+2xm=160+2x2=164мм
Определяем диаметры впадин
Для прямозубых цилиндрических передач:
Шестерня: df1=d1–25xm=40–25x2=35мм
Колесо: df2=d2–25xm=160–25x2=155мм
Определяем высоту зуба
Определяем ширину венца шестерни и колеса
Рабочая ширина венца b2=04 x 100 = 40 мм
Проверяем величину межосевого расстояния
aw=05(d1+d2)=05(40+160)=100мм
Проверочный расчет закрытой передачи.
Проверка контактной выносливости рабочих поверхностей зубьев колес. Расчетом должна быть проверена справедливость соблюдения неравенства:
Т1 – вращающий момент на шестерне Н × мм;
КНb - коэффициент неравномерности распределения нагрузки по длине контакта;
КНV – коэффициент внутренней динамической нагрузки;
ЕПР – приведенный модуль упругости МПа;
uФ – фактическое передаточное число;
dW – начальный диаметр колеса мм;
bW – рабочая ширина зубчатого венца колеса мм;
aW – фактическое межосевое расстояние мм [1].
bW =yba aW =0.4x100 = 40мм
Величину вращающего момента Т1 на шестерне определяем по формуле:
где h - КПД передачи принимаем h = 096 [1].
Коэффициент неравномерности нагрузки по длине контакта КНb выбирают в соответствии с расположением колес относительно опор и твердостью рабочих поверхностей зубьев колес по графику приведенному в [1]: КНb = 11.
Для определения коэффициента внутренней динамической нагрузки КНV необходимо рассчитать окружную скорость в зацеплении V мс:
В зависимости от значения V по таблице приведенной в [1] назначаем степень точности передачи – 8. Затем определяем коэффициент внутренней динамической нагрузки КНV = 11.
Подставив численные значения в формулу (1.31) получим:
Допускаемое контактное напряжение т. е. неравенство не соблюдается: sН > [sН].
В результате проверки выявилась существенная недогрузка > 10 % то с целью более полного использования возможностей материалов зубчатых колес возможна корректировка рабочей ширины зубчатого венца по формуле:
Проверка прочности зубьев по напряжениям изгиба. Проверяют справедливость соотношения расчетных напряжений изгиба sF и допускаемых напряжений [sF ]:
Ft – окружное усилие в зацеплении колес Н;
КFb - коэффициент неравномерности распределения нагрузки по длине контакта;
КFV – коэффициент внутренней динамической нагрузки;
YF12 – коэффициент формы зуба [1].
Окружное усилие в зацеплении колес Ft определяем по формуле:
Коэффициент неравномерности нагрузки по длине контакта КFb выбирают в соответствии с расположением колес относительно опор и твердостью рабочих поверхностей зубьев колес по графику приведенному в [1]: КFb = 105.
В зависимости от значения окружной скорости V по таблице приведенной в [1] назначаем степень точности передачи – 8. Затем определяем коэффициент внутренней динамической нагрузки КFV = 11.
YF12 – коэффициент формы зуба определяем по графику 8.20[2]
Подставив численные значения в формулу найдем значения расчетных напряжений изгиба sF:
Допускаемые напряжения изгиба: [sF]1 = 1938 МПа; [sF]2 = 212148 МПа неравенство соблюдается.
Расчёт шестерни открытой передачи
Определение модуля открытой передачи
- коэффициент ширины зубчатого венца колеса относительно модуля =9
- коэффициент формы зуба назначаются по рис 8.20 :
- коэффициент концентрации нагрузки по длине зуба. Назначаем по [1 c 136] = 11
Согласно скорости по таблице 2.5[2] степень точности изготовления шестерни Nст=8
Определение основных геометрических размеров шестерни
Делительный диаметр в среднем сечении зуба шестерни рассчитывается по формуле:
По заданному передаточному числу uотк =2 находим угол при вершине делительного конуса
Cреднее конусное расстояние:
Внешнее конусное расстояние рассчитывается по формуле:
Модуль зацепления на внешнем торце
Внешний делительный диаметр шестерни рассчитывается по формуле
Окружное усилие в открытом зацеплении рассчитывают по формуле:
- коэффициент внутренней динамической нагрузки.
Проверка по напряжениям изгиба: должно выполняться бF3 [бF3] 146.63 МПа 243.735 МПа
Проектный расчет валов и подбор подшипников
Определение геометрических параметров ступеней вала
Вал представляет собой ступенчатое цилиндрическое тело количество и размеры ступеней которого зависят от количества и размеров установленных на вал деталей [1].
Тихоходный вал. Диаметры различных участков вала редуктора определяют по формулам:
- диаметр d1 концевого участка вала:
где Т – крутящий момент Н × м;
[t]К – допускаемое напряжение на кручение Нмм2 [1].
Расчет валов редуктора выполняют только по напряжениям кручения то есть при этом не учитывают напряжений изгиба концентрации напряжений и переменность напряжений во времени. Для компенсации этого значения допускаемых напряжений на кручение выбирают заниженными в пределах [t]К = 10 15 Нмм2.
В работе для тихоходного вала выбираем [t]К = 10 Нмм2.
Полученное значение по ряду нормальных линейных размеров округляем до d1 = 40 мм.
Длину ступени вала определяем по формуле:
- диаметр d2 под уплотнение крышки с отверстием и подшипник:
где t – высота буртика мм [1].
Высоту буртика выбираем в зависимости от диаметра ступени d1: t=25мм.
Подставляем численные значения в формулу :
- диаметр d3 под колесо:
где r – радиус скругления мм [1].
Радиус скругления выбираем в зависимости от диаметра ступени d2: r=2мм [1].
Длина ступени вала l3 определяется графически на эскизной компоновке[1].
- диаметр под подшипник d4 = d2 =40мм.
Длина ступени вала l4 равна ширине подшипника В [1].
Быстроходный вал. Диаметры ступеней вала – шестерни определяем по формулам:
- диаметр d1 выходного конца вала соединенного с двигателем через муфту находим по формуле:
где d1 – диаметр выходного конца вала ротора двигателя мм.
Диаметр выходного конца вала ротора двигателя:
Полученное значение по ряду нормальных линейных размеров округляем до d1 = 25 мм.
Длину ступени вала определяем по формуле :
- диаметр d2 под уплотнение крышки с отверстием и подшипник находим по формуле .
Высоту буртика выбираем в зависимости от диаметра ступени d1: t=22мм.
Полученное значение округляем до ближайшего стандартного диаметра внутреннего кольца подшипника d2 = 30 мм [2].
- диаметр d3 под шестерню находим по формуле .
Полученное значение по ряду нормальных линейных размеров округляем до d3 = 36 мм.
- диаметр под подшипник d4 = d2 = 30мм.
Предварительный выбор подшипников
Определение типа серии и схемы установки подшипников. Для опор валов цилиндрических прямозубых и косозубых колес редукторов и коробок передач применяют чаще всего шариковые радиальные подшипники [1].
Из всех стандартных подшипников качения однорядные радиальные шарикоподшипники являются одними из наиболее дешевых имеют наименьшие потери на трение и обладают наибольшей быстроходностью. Кроме того эти подшипники хотя и не являются самоустанавливающимися допускают небольшие (иногда до 05°) перекосы колец и следовательно менее чувствительны к несоосности посадочных мест. Эти существенные достоинства однорядных радиальных шарикоподшипников обеспечили им широкое распространение и наибольшее число конструктивных разновидностей [3].
Предварительно выбираем для тихоходного вала роликовые конические однорядные подшипники средней серии схема установки - враспор. Для вала – шестерни шариковые радиальные однорядные подшипники с защитными шайбами легкой серии схема установки - враспор.
Определение основных параметров подшипников. По каталогу в зависимости от диаметра dП внутреннего кольца подшипника равного диаметру второй d2 и четвертой d4 ступеней вала определяем основные параметры подшипников:
- для тихоходного вала: - d = 45мм;
- грузоподъемность Сr = 1010 кН С0r = 720 кН.
- для вала – шестерни: - d = 30мм;
- грузоподъемность Сr = 281 кН С0r = 146 кН.
Проверочный расчет валов на выносливость
Выбор расчетной схемы вала. Определение опорных реакций построение эпюр изгибающих и крутящих моментов.
Определение реакций в опорах
Реакции в опорах определяем на основании уравнения равновесия
Расчёт реакций в опорах горизонтальной плоскости:
-Ft2*k + Rbx*(k+m) – Ft3*(k+m+n) = 0
-Rax*(k+m) + Ft2*(m) – Ft3*n=0
Расчёт реакций в опорах вертикальной плоскости:
Rby*(k+m) – Fr2*k + Fr3*(k+m+n) +M3=0
-Ray*(k+m) – Fr2*m + Rby*l3 – Fa3* n+ M3=0
Построение эпюр изгибающих и крутящих моментов
Эпюры изгибающих моментов строят в двух плоскостях.
Изгибающие моменты в горизонтальной плоскости:
M(B)x = Rax * l1 = -362321 * 42= -1522 кНм
M(С)x = Ft3 * l3 = -442308 * 87 =-3848 Нм
Изгибающие моменты в вертикальной плоскости:
M(B)y = Ray * l1 = 1394.27*42= 58.6 Нм
M(С)y = Fr3 * l3 - Fa3 * dm32= 143991 * 87 + 71995 * 1042 = 87.8 Нм
M(D)y =- Fa3 * dm32 = 71995 * 1042 =- 3744 Нм
Перерезывающие силы в вертикальной плоскости:
Q(A)x=Rax=-3623.21 H
Q(B)x=Rax-Ft2=-3623.21-1915.67 = -5538.88 H
Q(C)x=Rax-Ft2+Rbx=-3623.21-1915.67+9961.96 = 4423.08 H
Q(C)x=Rax-Ft2+Rbx-Ft3=-3623.21-1915.67+9961.96-4423.08=0 H
Перерезывающие силы в горизонтальной плоскости:
Q(A)y=Ray=1394.27 H
Q(B)y=Ray-Fr2=1394.27-69725= 697.02 H
Q(C)y=Ray-Fr2+Rby=1394.27-69725-213693 = -1439.91 H
Q(C)y=Ray-Fr2+Rby+Fr3=1394.27-69725-213693+1439.91 =0 H
Определение результирующих моментов:
Построение эпюр изгибающих и крутящих моментов
Определение коэффициента запаса усталостной прочности
При расчете коэффициента запаса усталостной прочности принимают что напряжения изгиба изменяются по симметричному циклу а напряжения кручения – по отнулевому. Выбор отнулевого цикла для напряжения кручения основан на том что большинство валов передает переменное по значению но постоянные по направлению вращающие моменты [1].
Определяем амплитуду симметричного цикла нормальных напряжений при изгибе вала в опасных сечениях:
и амплитуду от нулевого цикла касательных напряжений при кручении вала:
где Mоп - результирующий изгибающий момент в рассматриваемом опасном
Т – крутящий момент на валу Н×мм [1].
Mоп определяем по формуле:
Моменты сопротивления изгибу и кручению нетто – сечения вала:
Подставляем численные значения в формулы :
При совместном действии изгиба и кручения запас усталостной прочности определяют по формуле:
где Ss - запас сопротивления усталости только по изгибу;
St - запас сопротивления усталости только по кручению;
гдеs-1 - предел выносливости материала вала при симметричном цикле нагружения;
ks - эффективные концентрации напряжений при изгибе и кручении;
kF и kd - масштабный фактор и фактор шероховатости поверхности;
sа - амплитуда напряжения цикла;
ys - коэффициент учитывающий влияние постоянной составляющей цикла напряжения на сопротивление усталости;
sm – среднее напряжение цикла.
гдеsВ - предел прочности материала вала принимаем sВ=56×108 [2].
Подставляем численное значение в формулу :
Принимаю ks=185 [2].
Принимаю kd=075 [2].
Принимаю ys=015 [1].
Принимаю sm =0 [2]. Для симметричного цикла.
гдеt-1 - предел выносливости материала вала при симметричном цикле нагружения;
kt - эффективные концентрации напряжений при изгибе и кручении;
tа - амплитуда напряжения цикла;
yt - коэффициент учитывающий влияние постоянной составляющей цикла напряжения на сопротивление усталости;
tm – среднее напряжение цикла.
Условие прочности выполняется.
Проверочный расчет подшипников
Выбранный в ходе проектирования узла вала типоразмер подшипника должен быть проверен на работоспособность по динамической грузоподъёмности.
Проверка правильности выбора подшипников может быть проведена двумя способами:
) по сравнению требуемой Cr треб и паспортной Cr пасп динамической грузоподъёмности подшипника когда должно выполняться условие Cr треб Cr пасп;
) по обеспечению заданной долговечности подшипника то есть
Lhзадан Lhфакт где с учётом режима нагрузки Lhзадан = hLh (см. табл. 16.3 [1]).
Здесь фактический срок работы подшипника рассчитывают по зависимости
a1 - коэффициент надёжности обычно принимают a1 = 1 при 90% надёжности;
a2 - обобщённый коэффициент совместного влияния качества металла деталей подшипника и условий его эксплуатации для обычных условий эксплуатации назначают a2 = 0.7 0.8 (для шарикоподшипников) и a2 = 0.6 (для роликоподшипников).
p=3 если подшипник шариковый р=3.3 –если роликовый
Величина эквивалентной динамической нагрузки на проверяемый подшипник рассчитывается в общем случае по формуле
Fr и Fa - соответственно радиальная и осевая силы в опоре
V - коэффициент вращения зависящий от того какое кольцо подшипника вращается; при вращении внутреннего кольца V = 1;
По табл.16.4 [4] Х=1 Y=0
kб - коэффициент безопасности учитывающий характер нагрузки при умеренных толчках kб = 1.3 1.5;
kt - температурный коэффициент для температуры подшипникового узла t 100C kt = 1
Подшипники выбраны верно.
Конструирование элементов корпуса
Определение толщины стенок корпуса.
Крепление крышки к корпусу осуществляется 4 болтами М10 [2].
Толщина стенки крышки корпуса.
для одноступенчатых.
Для соединения корпуса и крышки редуктора по всему контуру плоскости разъёма выполняют специальные фланцы которые располагают внутрь от стенки корпуса.
Размеры конструктивных элементов фланца.
Высота ниши в месте крепления корпуса к раме.
где dф – диаметр винта крепления крышки и корпуса мм.
Смазка зубчатой передачи
Для уменьшения потерь мощности на трение и снижения интенсивности износа трущихся поверхностей а также для предохранения их от “заедания” “задиров” коррозии и лучшего отвода теплоты трущиеся поверхности деталей должны иметь надежную смазку.
В редукторе применяем картерную систему смазки.
Для того чтобы выбрать необходимую марку масла нужно вычислить окружную скорость:
В зависимости от контактного напряжения и окружной скорости колёс по таблице 11.1 [2] принимаем рекомендуемую вязкость34×10 –6 м2с;
По таблице 11.2 [2] принимаем масло индустриальное И-Г-А-32.
Уплотнительные устройства применяют для предохранения от вытекания смазки из подшипниковых узлов а так же для предотвращения попадания пыли и влаги извне. В проектируемом редукторе в качестве уплотнительных устройств используем манжетные уплотнения.
Объем масла И-Г-А-32 требуемый для заливки в редуктор составляет 15 литра.
Выбор способа и типа смазки подшипников
Подшипники смазывают тем же маслом что и детали передач. Другое масло применяют лишь в ответственных изделиях.
При картерной смазке колес подшипники качения смазываются брызгами масла. При окружности вращения колес V>1мс брызгами масла покрываются все детали передач и внутренние поверхности стенок корпуса. Стекающее с колес валов и стенок корпуса масло попадает в подшипники.
Так как смазка жидкая для предохранения от ее вытекания из подшипниковых узлов а так же для их защиты от попадания извне пыли грязи и влаги торцовые крышки установим с жировыми канавками которые заполним густой консистентной смазкой.
Расчет крышки подшипника.
В данном курсовом проекте принимаю для установки 4 крышки закладного типа из них 2 глухие а 2 другие с отверстием для выходного конца вала.
Диаметры вала колеса:
Диаметры вала шестерни:
l=lp+b=12+16=28 округляем в большую сторону до стандартного значения: l=45.
На d1 вала шестерни.
«Методические указания к выполнению расчетной части курсового проекта по прикладной механике» УГАТУ.
ИвановМ.Н. Детали машин. Высшая школа 2000 г.
П.Ф.Дунаев О.П.Леликов. Детали машин. Курсовое проектирование. Высшая школа 1984 г.
АнурьевВ.И. Справочник конструктора машиностроителя. М.2001г. Т.I II III.
П.Ф.Дунаев О.П.Леликов «Конструирование узлов и деталей
машин». Высшая школа.2004
мое колесо.cdw

Нормальный исходный контур
Степень точности ГОСТ 1643-81
сталь ХН ГОСТ1050-88
Радиусы скругления 2 мм max
Неуказанные пред. откл.размеров: отверстий +t
Мой чертеж!.cdw

Чертеж.cdw

* Размер обеспечить инструментом.
Неуказанные предельные отклонения размеров валов- t
Документ Microsoft Word.doc
Расчет закрытой передачи4
Расчёт шестерни открытой передачи14
Проектный расчет валов и подбор подшипников16
Проверочный расчет валов на выносливость20
Определение коэффициента запаса усталостной прочности22
Проверочный расчет подшипников25
Конструирование элементов корпуса27
Смазка зубчатой передачи28
редуктор.cdw

Момент на выходном валу
Частота вращения выходного вала
Передаточное число редуктора 3
ТЕХНИЧЕСКИЕ ТРЕБОВАНИЯ
Плоскость разъема покрыть герметиком при окончательной
Необработанные поверхности красить малостойкой краской
снаружи серой эмалью
Обкатать редуктор без нагрузки 2 часа
Спецификация к редуктору.doc
Болт М6х18 ГОСТ 7786-70
Болт М10х65 ГОСТ 7796-70
Винт М6х16 ГОСТ 17473-80
Манжета 1-30х52-3 ГОСТ 8752-79
Манжета 1-45х65-3 ГОСТ 8752-79
Шайба 10 ГОСТ 6402-70
Шайба 16 ГОСТ 6402-70
Шпонка 6х6х16 ГОСТ 23360-78
Шпонка 8х12х36 ГОСТ 23360-78
Шпонка 16х10х45 ГОСТ 23360-78
Штифт 4х12 ГОСТ 3128-70
Штифт 10х35 ГОСТ 3129-70