Обработка пятой части (упорный подшипник)




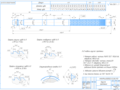
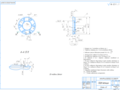
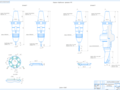

- Добавлен: 24.01.2023
- Размер: 47 MB
- Закачек: 0
Описание
Состав проекта
![]() |
![]() |
![]() |
![]() ![]() |
![]() ![]() ![]() ![]() |
![]() ![]() ![]() |
![]() ![]() |
![]() |
![]() |
![]() ![]() ![]() ![]() |
![]() ![]() ![]() ![]() |
![]() |
![]() |
![]() ![]() ![]() |
Дополнительная информация
Чертеж3.cdw

протяжка.m3d

протяжка.cdw

Чертеж детали.cdw

Рекомендуемые чертежи
- 24.04.2014
- 24.04.2014