Модернизация и антикоррозийная защита оборудования цеха улавливания




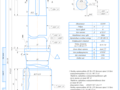
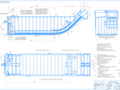
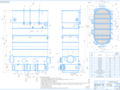

- Добавлен: 25.01.2023
- Размер: 4 MB
- Закачек: 0
Описание
Состав проекта
![]() |
![]() ![]() ![]() |
![]() |
![]() ![]() ![]() ![]() |
![]() ![]() ![]() ![]() |
![]() |
![]() |
![]() ![]() ![]() ![]() |
![]() |
![]() ![]() ![]() |
![]() |
![]() ![]() ![]() |
![]() |
![]() |
![]() ![]() ![]() |
![]() ![]() ![]() |
![]() ![]() ![]() |
![]() |
![]() ![]() ![]() |
![]() ![]() ![]() ![]() |
![]() |
![]() ![]() ![]() ![]() |
![]() |
![]() |
![]() |
![]() |
![]() |
![]() ![]() ![]() |
![]() ![]() ![]() |
![]() ![]() ![]() |
![]() |
![]() ![]() ![]() |
![]() ![]() ![]() |
![]() |
![]() ![]() ![]() |
![]() ![]() ![]() |
![]() |
![]() ![]() ![]() |
![]() ![]() ![]() |
![]() |
![]() ![]() ![]() |
![]() ![]() ![]() |
![]() |
![]() ![]() ![]() |
![]() ![]() ![]() |
![]() |
![]() ![]() ![]() |
![]() ![]() ![]() |
![]() |
![]() ![]() ![]() |
![]() ![]() ![]() |
![]() ![]() ![]() |
![]() |
![]() ![]() ![]() |
![]() ![]() ![]() |
Дополнительная информация
Чертеж халодильника.cdw

Для замера давления
Техническая характеристика
Назначения для первичного охлаждения коксового газа
Номинальная производительность по газу при температуре 293 К (200С) и 0
Объем подаваемой технической воды
Общая площадь поверхности охлаждения
Площадь поперечного сечения по ходам (по ходу воды)
Площадь поперечного сечения по ходам (по ходу газа)
Срок службы холодильник
Сейсмичность места установки холодильника по 12 бальной шкале
Чертеж мехосвитлителя.cdw

Съемные понели и крышки условго не показаны
Опоры под привад условно не показаны
крыши мехоосветлителя
Граница перегиба нижних
направляющих уголков
Граница перегиба верхних
Техническая характеристика привода
Электробвигатель тип 4АХ90l6
Редуктор - тип ц2у -160
Общее передаточное отношение i
Скорость скребкового транспортера V=0
Техническая характеристика
Осветлитнль механизированный предназначен
для осветления габсмольной воды цикла газосблоников
выделения из нее смолы и фусов
для механизированного удаления фусов.
Номинальная производительность
по надсмольной воды м
надсмольная вода - 70%; смола - 25%;фусы - 5%;
в) в подогревателе - водяной пар
а) в осветлителе атмосферное
б) пара поступающего в подогреватель
Емкость бункеров для фусов
Поверхность нагрева подогревателей бункера
механизированный для
Фрагмент3.frw

Фрагмент вид А.frw

Фрагмент Рис1 вид А.frw

Фрагмент5.frw

Фрагмент6.frw

Фрагмент вид А.2.frw

Фрагмент4.frw

Чертеж вал и калисо 2.cdw

величина зерна 5 8 балл
нитроцементировать h 0
Твердость сердцевины нитроцементированного зуба
после закалки не менее HRC 32.
Твердость сердцевины нитроцементованного вала
Поковку нормализовать HB 156 229
Направление линии зуба
Нормативный исходный контур
Коэффициент смешения
Допускается продольная модификация зуба (бочкообразность)
Стрелка прогиба должна быть в пределах 0
Делительный диаметр
ТХ.cdw

Аммиачная вода и смола
- газосборник; 2 - сепаратор; 3 - первичный трубчатый холодильник; 4 - гидравлический затвор; 5 - промежуточный сборник;
- насос; 9 - регулятор уровня жидкости; 10 - промсборник для смолы; 11 - сборник для смолы; 12 - отстойник для воды;
- сборник для избыточной воды; 15 - насос для смолы; 16 - насос для воды; 17 - нагреватель; 18 - электрофильтр;
- гидравлический затвор для отвода смолы; 20 - трубопровод для технической воды.
Тс первичного охлаждения коксового газа
с трубчатым газовым холодильникам
1.1.doc
1.Продукты коксования и их применение
При коксовании каменных углей в результате разложения органической массы выделяются газо- и парообразные вещества смесь которых называется прямым коксовым газом. В состав последнего входят собственно коксовый газ смола бензольные углеводороды аммиак сероводород и другие продукты. Содержание основных компонентов выделяемых при обработке коксового газа в цехах улавливания приведено ниже в гм3 сухого газа:
Пары воды (пирогенетической и влаги шихты) 250-450
Пары бензольных углеводородов 30-40
Цианистый водород ..05-20
Кроме того в состав прямого коксового газа входят сероуглерод сероокись углерода тиофен пиридиновые основания меркаптаны фенолы и др.
Выход и состав продуктов коксования зависят от свойств коксуемых углей конструкции печей и условий коксования. В таблице 1.1 приведены производственные данные о выходе продуктов коксования различных шихт из которых видно что при увеличении выхода летучих веществ шихты растет выход коксового газа смолы бензольных углеводородов аммиака. Значительное влияние на выход и состав химических продуктов коксования оказывает температура процесса.
1.2.doc
Выход летучих веществ
в процентах на сухую массу шихты
Вода пирогенетическая
При ее увеличении растет выход коксового газа и содержание водорода в нем уменьшается выход смолы а ее плотность повышается растет выход сырого бензола при снижении содержания в нем толуола ксилола и непредельных соединений.
Существенное влияние на выход продуктов оказывают также полнота загрузки камер шихтой и режим отсасывания газа. При неполной загрузке камер шихтой увеличивается время пребывания летучих веществ в подводном пространстве при повышенной температуре и степень их пиролиза. Повышение давления в камерах вызывает потерю летучих веществ в атмосферу и отопительную систему а вакуум - сгорание части продуктов из-за подсоса кислорода в систему.
Кокс является основным продуктом коксования углей. Почти 80% производимого кокса используется для выплавки чугуна в доменных печах (металлургический кокс крупностью более 25-40 мм) а примерно 7% для расплавления металлов в вагранках (литейный кокс крупностью более 60 мм). Коксовый орешек крупностью 10-25 мм применяется в качестве восстановителя в электропечах для получения ферросплавов а коксовая мелочь — для агломерации железной руды.
Значительная часть кокса потребляется в цветной металлургии для восстановления свинцовых никелевых медных и других руд в химической промышленности для получения карбида кальция желтого фосфора обжига известняка и для других целей.
Химические продукты коксования используются более чем в 70 отраслях и подотрослях хозяйственного комплекса. Основными потребителями их являются химическая промышленность (35% от общего объема производства) цветная металлургия (30%) сельское хозяйство (более 20%) строительная индустрия и железнодорожный транспорт (около 12%).
В химической промышленности используются водород этилен метан коксового газа бензол и его гомологи сольвент нафталин фенолы пиридиновые основания антрацен аценафтен и пирен индеп-кумароновые смолы каменноугольные масла пек и др. Эти продукты служат исходным сырьем для получения азотных удобрений синтетического фенола этилбензола и циклогексана фгалевого и малеинового ангидридов используемых в производстве полимерных материалов полупродуктов анилиноокрасочной промышленности сажи средств защиты растений синтетических моющих средств лечебных препаратов и пр.
В цветной металлургии перерабатываются сотни тысяч тонн каменноугольного пека и пекового кокса для производства электродов и другой продукции.
Сельскому хозяйству коксохимическая промышленность поставляет азотные удобрения креолин применяемый в животноводстве коллоидную среду для борьбы с вредителями сельскохозяйственных культур антисептики и др. Кроме того ряд коксохимических продуктов используется другими отраслями промышленности для производства гербицидов дефолиантов регуляторов роста растений репеллентов и пр.
В строительной индустрии находят применение инден-кумароно- вые смолы каменноугольные масла и пек для производства строительных материалов.
В строительстве шоссейных дорог применяются дорожные дегги приготовляемые из каменноугольных масел и пека. Большие количества каменноугольных масел используются в железнодорожном транспорте для пропитки шпал.
Большое значение продуктов коксования как сырьевой базы для химической промышленности и других отраслей народного хозяйства обусловливается крупными масштабами коксохимического производства широким ассортиментом продукции и уникальностью многих продуктов. Коксохимическая промышленность является единственным или основным источником нафталина крезолов инден-кумароновых смол пиридиновых оснований мезитилена метаксилола роданистых солей антрацена.
Важнейшее место в ассортименте продуктов коксования занимает коксовый газ. Основным потребителем его (около 53%) является черная металлургия где он используется в качестве топлива в мартеновских и нагревательных печах. 30-35% коксового газа используется коксохимическими заводами для обогрева печей и других нужд. Перспективным направлением использования коксового газа является вдувание его в доменные печи с целью сокращения расхода кокса на выплавку чугуна. В условиях дефицита природного газа и нефтепродуктов коксовый газ может служить сырьем для синтеза аммиака метанола моторных топлив.
Аммиак коксового газа используется для получения азотных удобрений - аммиачной воды и сульфата аммония. Несмотря на относительно низкое содержание азота (211%) сульфат аммония является эффективным удобрением при внесении в известкованные подзолистые почвы и черноземы насыщенные основаниями. Кроме того сера сульфата аммония является необходимым компонентом для ряда сельскохозяйственных культур.
Коллоидная сера получаемая при очистке коксового газа от сероводорода применяется в сельском хозяйстве в качестве средства борьбы с грибковыми возбудителями болезней растений.
Сернистый аммоний находит применение при гидрометаллургическом обогащении руд цветных металлов в производстве тиомочевины ядохимикатов в фармацевтической промышленности. Роданистый аммоний используется в производстве реактивов при крашении тканей для получения лечебных препаратов дефолиантов ингибиторов. Соединения пиридинового и хинолинового ряда являются основой для синтеза лекарственных препаратов и витаминов-противотуберкулезных средств стимуляторов сердечной деятельности бактерицидов витаминов РР1 (никотиновая кислота и никотинамид) В1 (тиамин) В6 (пи- ридоксил) А (ретинол) Д2 и О2 (кальциферолы) Н (биотин и др.). Важной областью применения пиридиновых оснований является также производство пестицидов гербицидов бактерицидов.
Бензол относится к числу важнейших химических продуктов на которых базируется современный органический синтез. Он используется для производства важнейших полупродуктов в промышленности пластических масс синтетического каучука волокон моющих средств красителей фармацевтических препаратов. Основными потребителями бензола являются производства этилбензола фенола и циклогексана.
Толуол используется в производстве консервирующих средств красителей взрывчатых веществ пластических масс и синтетических волокон а также в качестве добавки к моторным топливам для повышения октанового числа растворителя смол и лаков.
Каменноугольный ксилол и сольвент (полиметилбензолы) используются главным образом в качестве растворителя в производстве лаков красок и эмалей.
Инден-кумароновые смолы представляющие собой продукт полимеризации непредельных соединений содержащихся в сыром бензоле применяются для производства асбесто-смоляных плиток пластобетона линолеума искусственной кожи водонепроницаемых тканей клеев изоляционной ленты и т.д.
Каменноугольная смола является важным источником сырья для органического синтеза. При ее переработке получают нафталин крезол антрацен пек и пековый кокс для электродной промышленности каменноугольные масла для пропитки древесины получения сажи выработки ядохимикатов.
Нафталин является одним из основных представителей ароматических углеводородов используемых в качестве сырья для органического синтеза. По масштабам производства и потребления он уступает только бензолу. Главная область его применения - производство фталевого ангидрида используемого для получения пластификаторов алкидных и полиэфирных смол красителей. Нафталин находит применение также в производстве полупродуктов для красителей (-нафтола Аш-кислоты и др.) поверхностно-активных веществ инсектицидов дубильных веществ и других продуктов.
Широкое применение в органическом синтезе получил также фенол главным образом в производстве пластических масс на основе феполформальдегидных смол синтетических волокон типа капрон и нейлон эпоксидных смол на основе дифенилолпропана гербицидов взрывчатых веществ красителей и т.д. В нефтяной промышленности фенол применяется для селективной очистки масел получения присадок к топливам и маслам в легкой промышленности из него получают дубители для кожи а в фармацевтической - салициловые препараты (аспирин и др.).
Технические смеси крезолов используются в производстве смол для лаков пресс-порошков электроизоляционных материалов клеев пластификаторов (трикрезилфосфаты и др.) флотореагентов и присадок к пластмассам и смазкам. Отдельные изомеры крезолов находят применение в производстве гербицидов антиоксидантов витаминов дезинфицирующих и душистых веществ.
Антрацен применяется в производстве синтетических дубителей красителей сажи и для энергетических целей.
В заключение следует сказать что многие компоненты сырого бензола и каменноугольной смолы еще недостаточно изучены и являются потенциальным сырьем для разнообразных производств [1].
2.Основные процессы технологии улавливания химических продуктов коксования
Образующаяся при коксовании смесь парогазообразных продуктов (прямой коксовый газ) выходит из коксовых печей при температуре 650-750°С и содержит большое количество угольной и коксовой пыли. Наличие последней и смолистых веществ склонных откладываться на поверхностях тепло- и массообменных аппаратов исключает или затрудняет в значительной степени разделение этой смеси известными в химической промышленности методами в типовой аппаратуре.
Поэтому первой стадией обработки прямого газа является быстрое охлаждение путем непосредственного контакта с распыляемой форсунками водой в газосборнике представляющем собой горизонтальную трубу диаметром 15-2 м расположенную вдоль коксовой батареи в непосредственной близости от патрубков (стояков) для вывода газа из коксовых камер. При адиабатическом процессе в газосборнике газ охлаждается до температуры близкой к температуре мокрого термометра (82-90°С) одновременно происходит конденсация большей части паров смолы (60-70%) и удаление из газа пыли. Частицы угля и кокса обволакиваются пленкой смолы и образуют так называемые фусы затрудняющие транспортирование конденсата по трубопроводам обезвоживание и переработку смолы. Дальнейшее охлаждение газа до температуры 30-35°С благоприятной для протекания процессов улавливания аммиака сероводорода бензольных углеводородов и транспортирования газа через аппаратуру цеха улавливания химических продуктов производится в холодильниках косвенного или непосредственного действия. При этом происходит пракгически полная конденсация паров воды и смолы поступающих с газом из газосборника в результате чего резко сокращается объем газа и потребность в электроэнергии для его
Несмотря на конденсацию паров смолы в холодильниках значительная часть ее уносится с газом в виде мельчайших капелек.
Туманообразная смола и кристаллы нафталина откладываются в трубопроводах и аппаратуре снижают эффективность процессов улавливания и качество получаемых продуктов. Поэтому следующей важной операцией является очистка газа от туманообразной смолы и нафталина в электрофильтрах или путем промывки его маслами в скрубберах устанавливаемых непосредственно перед газодувками или после них.
Выделение основных химических продуктов из коксового газа производится методами сорбции физической или химической в зависимости от свойств извлекаемых компонентов. Улавливание аммиака может производиться водой с получением концентрированной аммиачной воды в качестве товарного продукта фосфатами аммония с получением жидкого аммиака или серной кислотой с получением сульфата аммония. Поглощение бензола и ею гомологов осуществляется каменноугольными или нефтяными маслами являющимися хорошими растворителями для ароматических углеводородов. Для выделения сероводорода и других кислых газов применяются щелочные растворы различного состава.
Десорбция поглощенных растворителями компонентов при физической сорбции производится путем нагревания при атмосферном давлении или под вакуумом в тарельчатых колоннах. Регенерация щелочных растворов сероочистки может производиться также путем продувки его воздухом в результате чего при наличии в растворе катализаторов происходит окисление сероводорода с образованием элементной серы.
Для разделения конденсатов образующихся при охлаждении коксового газа на водную и органическую фазы применяются процессы осаждения под действием
гравитационных и инерционных сил.
Водный конденсат из холодильников насыщенный аммиаком сероводородом углекислотой перерабатывается методами дистилляции.
Обогащенные аммиаком пары могут конденсироваться с образованием концентрированной аммиачной воды или подаваться вместе с коксовым газом в
абсорберы для поглощения аммиака серной кислотой. Сточная вода после аммиачной колонны подвергается обесфеноливанию методами десорбции водяным паром экстракции жидкими растворителями и биохимической очистки.
На рис. 1.2.1. приведена типичная схема процессов и материальных потоков цеха улавливания химических продуктов коксования.
Получаемые в цехе улавливания сырой бензол и каменноугольная смола представляют собой многокомпонентные смеси нуждающиеся в специальной обработке для выделения узких фракций или индивидуальных веществ получивших широкое применение в качестве сырья для синтезов или готовых продуктов. Поэтому в состав коксохимических заводов кроме цехов улавливания химических продуктов входят также перерабатывающие цехи - цех ректификации сырого бензола и цех переработки каменноугольной смолы.
В цехе ректификации сырой бензол подвергается очистке от непредельных и сернистых соединений серной кислотой или каталитическим гидрированием и последующему разделению на товарные продукты. В смолоперегонном цехе для получения конечных продуктов наряду с дистилляцией и ректификацией применяются процессы кристаллизации фильтрования или фугования прессования а также химическая очистка отдельных фракций смолы от фенолов и пиридиновых оснований. С целью расширения ассортимента продукции в смолоперегонных цехах осваиваются процессы азеотропной и экстрактивной ректификации отдельных фракций. Перспективным направлением переработки каменноугольной смолы и ее фракций можно считать процессы гидрогенизации.
Для выделения из коксового газа водорода метана этилена или узких фракций необходимых для синтезов аммиака метанола моторных топлив могут найти эффективное применение процессы адсорбции с помощью синтетических цеолитов характеризующихся высокой избирательностью действия.
Значительная интенсификация процессов улавливания химических продуктов уменьшение размеров аппаратуры могут быть достигнуты при проведении их под давлением а также с применением малого холода [2].
Рис. 1.2.1. Схема материальных потоков цеха улавливания химических продуктов коксования.
3.Транспортирование газа через аппаратуру цеха улавливания
Для безопасной и эффективной работы коксовых печей требуется поддерживать в них давление близкое к атмосферному во избежание значительных потерь летучих продуктов или подсосов воздуха через неплотности кладки и арматуры. Это достигается путем регулируемого отсоса газа из газосборников при давлении 100-140 Па. При движении газа по трубопроводам и аппаратам цеха улавливания возникают значительные гидравлические сопротивления для преодоления которых необходимо затрачивать энергию.
Отсос коксового газа из печей и транспортирование его через аппаратуру осуществляются с помощью специальных газодувок называемых также эксгаустерами или нагнетателями которые располагаются в машинном отделении после первичных газовых холодильников. Место установки газодувок диктуется не только стремлением сократить расход электроэнергии на транспортировку газа но и необходимостью уменьшения числа газовых аппаратов работающих под разрежением и создающих опасность подсосов воздуха в систему.
Нагнетатели являются наиболее ответственными агрегатами завода от которых зависит работа коксовых печей цеха улавливания и потребителей коксового газа. Количество нагнетателей устанавливаемых в машинном отделении определяется их производительностью по газу и мощностью завода. На типовом заводе включающем четыре батареи коксовых печей устанавливается три нагнетателя из которых два рабочих и один резервный. На случай возникновения перебоев в подаче электроэнергии один или два нагнетателя должны иметь привод от паровой турбины.
Газ из коксовых батарей соединенных попарно поступает через первичные холодильники в общий коллектор расположенный перед машинным отделением из которого двумя нагнетателями подается в аппаратуру цеха улавливания.
Типовые схемы газового тракта коксохимического завода показаны на рисунках 1.3.1. и 1.3.2. с холодильниками непосредственного и косвенного действия соответственно.
По своим параметрам нагнетатели должны обеспечивать отсасывание максимального объема коксового газа с учетом форсирования работы коксовых печей. Необходимый напор нагнетателя определяется общим гидравлическим сопротивлением газового тракта и требованиями потребителей газа.
По опытным данным гидравлические сопротивления отдельных участков газового тракта составляют Па:
Рис. 1.3.1. Схема газового тракта завода с холодильником непосредственного действия
- газосборник; 2 - сепараторы; 3 - холодильники непосредственного действия; 4 - нагнетатели; 59 – электрофильтры; 6 - сатураторы; 7 - конечные холодильники; 8 - бензольные скрубберы; 10 - серные скрубберы; 11 газгольдер.
Рис. 1. 3. 2. Схема газового тракта завода с трубчатыми холодильниками:
- газосборники; 2 - сепараторы; 3 - холодильники; 4 - электрофильтры;
- нагнетатели; 6 - абсорберы; 7 - ловушки; 8 - конечные холодильники;
- бензольные скрубберы; 10 - серные скрубберы.
Газопровод от коксовых печей до нагнетателей 1500-2500
Газовые холодильники .1000-2000
Электрофильтры 400-500
Дроссельные клапаны 500-1000
Всего наличии всасывания .3500-6000
Газопровод от нагнетателей до потребителя 3500-5000
Подогреватели газа .500-600
Сатураторы с ловушками ..5000-6500
Конечные газовые холодильники ..1000-1500
Скрубберы сероводородные ..1500-2000
Скрубберы беззольные 2000-2500
Давление газа в конечной точке газопровода 4000-6000
Всего налинии нагнетания 17500-24100
На современных коксохимических заводах применяются нагнетатели центробежного типа приводимые в движение паровой турбиной (3000- 5000 обмин) или тихоходным высоковольтным электродвигателем (1450 обмин) через зубчатый редуктор увеличивающий скорость вращения до 3000-5000 обмин. Ниже приведена техническая характеристика серийно выпускаемых нагнетателей с электрическими приводами:
Производительность при 35°С и 93200 Па м3мин
Повышение давления Па
Частота вращения ротора с-1
Мощность электродвигателя квт
Регулирование производительности нагнетателя с паровым приводом осуществляется изменением подачи пара в турбину вызывающим соответствующее изменение скорости вращения ротора нагнетателя. Такой способ регулирования является наиболее экономичным.
У нагнетателей с электроприводом число оборотов остается постоянным а регулирование их производительности осуществляется двумя способами:
- прикрыванием (открыванием) задвижки на всасывающем газопроводе;
- путем передачи части газа из нагнетательного газопровода че рез обводной газопровод (байпас) во всасывающий.
Второй способ является более удобным однако как и первый он связан с бесполезной затратой энергии. Недостатком второго способа является также то что температура газа после нагнетателя значительно повышается из-за повторного сжатия части газа. Современные нагнетатели с электроприводом оборудованы автоматическими регуляторами которые действуют с помощью поршневого исполнительного механизма на клапан-бабочку установленный в обводном газопроводе. При турбинном приводе заданное разрежение перед нагнетателем поддерживается путем автоматического изменения числа оборотов турбины.
При автоматическом регулировании производительности нагнетателя колебания давления в газопроводе перед ним не превышают 100- 200 Па. Поскольку такие колебания недопустимы для газосборников коксовых печей то непосредственно за ними на отводных газопроводах устанавливаются автоматически регулируемые дроссели снижающие колебания давления в газосборниках до 10-20 Па.
При работе нагнетателей под действием центробежных сил из газа выделяются смола и водный конденсат которые стекают вниз камеры каждого рабочего колеса. Для непрерывного удаления конденсата в нижней части корпуса нагнетателя имеются спускные отверстия к которым присоединены дренажные трубы погруженные в гидрозатвор и снабженные паровым подогревом.
Большая скорость вращения рабочего колеса нагнетателя обусловливает необходимость непрерывной принудительной смазки подшипников с помощью специального масляного насоса приводимого от главного вала. Этот насос начинает работать при скорости вращения вала более 1500 обмин. Перед поступлением в подшипники циркулирующее масло проходит через специальный холодильник и фильтр [3].
4.Сырьевая база коксования
Выбор углей для коксования имеет важное значение с точки зрения качества и стоимости производимого кокса и химических продуктов. Поскольку в недрах земли имеется сравнительно мало углей пригодных для самостоятельного коксования то обычно для этой цели применяют смеси различных углей - угольные шихты.
В дореволюционной России для коксования применялись почти исключительно донецкие угли однако уже в 30-е годы ка востоке СССР была создана новая угольно-металлургическая база и для коксования начали широко использовать угли других бассейнов. Доля отдельных бассейнов в поставках углей для коксования представлена в таблице 1.4.1.
Таблица 1.4.1. - Степень участия бассейнов в поставках углей для
Резкое сокращение поставок донецких углей для коксования за указанный период объясняется прежде всего состоянием запасов углей в различных бассейнах. В недрах Донбасса запасов коксующихся углей значительно меньше чем в Кузбассе. К тому же глубина шахт в которых добываются угли марок Ж К и ОС здесь превышает 1000 м а резервный шахтный фонд спекающихся углей составляют лишь участки глубиной 1300-1500 м тогда как в Кузбассе глубина шахт не превышает 500 м. Из-за большой глубины залегания и малой мощности пластов строительство и эксплуатация шахт в Донецком бассейне значительно дороже а себестоимость угля примерно в два раза выше чем в Кузбассе.
Угленосная толша Донецкого бассейна содержит около 100 пластов мощностью от 045 до 25 м. Мощность большинства пластов составляет 05-08 м. На глубине до 600 м расположено примерно 33% общих запасов от 600 до 1200 м - около 40% и от 1200 до 1800 м - около 27%.
По петрографическому составу донецкие угли являются блестящими и полублестящими с высоким содержанием витринита. Зольность большинства пластов изменяется от 7 до 15%. В бассейне преобладают среднесернистые угли а высокосернистые (более 25%) составляют треть общих запасов. Содержание фосфора колеблется в пределах от 0001 до 002% что является благоприятным фактором для производства доменного кокса.
К Донецкому бассейну относят также новое месторождение - Западный Донбасс. Здесь имеется около 30 пластов относящихся к категории тонких и очень тонких (мощность не превышает 1 м). Угли Западного Донбасса характеризуются высокой сернистостью (в среднем около 2%) легкой и средней обогатимостью. Зольность их варьирует от 2 до 16% а серность - от 09 до 43%. Для коксования представляют интерес спекающиеся газовые угли Г6 и Г16 запасы которых составляют около 16% от общих запасов бассейна.
Львовско-Волынский бассейн расположен на юго-западе Волынской и северо-западе Львовской областей Украины. Глубина залегания рабочих пластов не превышает 300-500 м. Это малометаморфизированные угли главным образом марки Г (более 99% от балансовых запасов). По петрографическому составу нижиекарбоновые угли этого бассейна менее однородны чем газовые угли промышленного Донбасса. Преобладающим микрокомпонентом является витринит (70-75%). Зольность товарного утля составляет 15-21% сернистостъ от 07 до 55% и более содержание фосфора от 0003 до 014%.
Кузнецкий бассейн представляет собой крупнейшую базу высококачественных углей на территории СНГ. В недрах бассейна залегают угли всех степеней метаморфизма - от бурых и длиннопламенных до антрацитов. Здесь обнаружено около 100 пластов суммарной мощностью свыше 230 м.
Средняя мощность разрабатываемых пластов 22 м.
Около двух третей общих запасов углей находится на глубине более 600 м. Кузнецкий бассейн представлен двумя продуктивными свитами пермского периода- балахонской и кольчугинской. Содержание витринита в утях балахонской свиты обычно ниже 60% а в углях кольчугинской свиты 75-80%. В сравнении с донецкимиутлями аналогичных марок кузнецкие отличаются более низкой спекаемостью и затрудненной обогатимостыю однако имеют меньшую сернистостъ (03-08%) и зольность (до 12% для коль- гушинской свиты и 8-16% для балахонской). Содержание фосфора в кузнецких упиях (001 -02%) более высокое чем в донецких.
По мощности пластов общим геологическим и разведанным запасам углей их доступности для промышленного освоения и высокому качеству Кузнецкий бассейн не имеет себе равных. Добыча углей здесь ведется не более чем на 50 шахтах и разрезах среди которых крупнейшей является шахта «Распадская». Возможность разработки значительной части запасов открытым способом требующим меньших капитальных затрат на освоение месторождений и снижающим себестоимость добываемых углей позволяет считать этот бассейн наиболее перспективным в качестве сырьевой базы для коксохимического производства.
Карагандинский бассейн расположен в северо-восточной части Карагандинской области Казахстана. Более 75% геологических запасов залегает на глубине до 600 м из них половина на глубине до 300 м. Пласты угля рабочей мощности (более 07 м) содержатся в нескольких свитах. Содержание витринита изменяется от 30% в пластах ашлярикской и карагандинской свит до 80% в пластах долинской свиты. В карагандинской свите сосредоточены угли марок К и К2 а в долинской свите угли марок Г КЖ и Ж. Зольность различных пластов колеблется от 8 до 47% а сернистость от 06 до 1 %. Хорошая спекаемость карагандинских углей создает условия использования их для коксования.
Печорский бассейн расположен на северо-востоке европейской части России и простирается вдоль западного склона Урала до Кизеловского угольного бассейна. В этом бассейне установлен непрерывный метаморфический ряд углей - от бурых до антрацитов. Свыше 40% общих запасов углей залегают на глубине до 600 м. Более половины запасов приходится на долю жирных углей технологических групп Ж19 Ж10. Угли Печорского бассейна в основном малосернистые (05- 08%) зольность их колеблется от 11 до 295% при средней и трудной обогатимости а содержание фосфора - от 0002 до 0008%. Печорский угольный бассейн является основной сырьевой базой Череповецкого металлургического комбината.
Кизеловский бассейн расположен в пределах Пермской области России вдоль западных склонов Северного Урала. Залежи здесь представлены среднеметаморфизированными газовыми и жирными углями Г6 Ж13 и Ж18 с меньшей спекаемостью по сравнению с донецкими и печорскими аналогичных марок. Кизеловские угли высокозоль- ны труднообогатимы и высокосернисты. Содержание золы колеблется от 18 до 35% а сернистость составляет в среднем 6%.
Из общей добычи угля в Кизеловском бассейне на коксование направляется около 15%. Основным потребителем этих ушей (марок Г и Ж) является Губахинский коксохимический завод. В связи с высоким содержанием серы кокс из кизеловских углей используется только в цветной металлургии. Из-за отработки значительной части запасов значение Кизеловского бассейна в поставке углей для коксования будет снижаться [4].
5.Размещение и масштабы коксохимических предприятий
В связи с большим количеством перерабатываемого угля и производимого кокса размещение коксохимических заводов возможно на месте добычи угля при шахтах или в составе металлург ических заводов на месте потребления кокса.
Существует также ряд заводов которые располагаются вблизи химических либо металлургических и химических комбинатов.
В процессе развития предприятий коксохимической промышленности определилась тенденция к максимальному укрупнению последних современные заводы имеют мощность в пределах 1-8 млн.тгод. На Украине преимущественное значение имеют коксохимические предприятия связанные с металлургическими заводами и комбинатами при этом существующие заводы могут быть разделены на следующие категории:
—самостоятельные коксохимические заводы расположенные в районе или непосредственно примыкающие к металлургическим заводам;
—коксохимические заводы входящие в состав комбинатов или заводов и получившие в этом случае название коксохимических производств;
—коксохимические заводы связанные с химическими предприятиями использующими коксовый газ для азотно-тукового производства;
—коксогазовые заводы отдающие газ в городские сети промышленного газа.
Для Украины характерно сооружение крупных коксохимических предприятий с блоками из четырех коксовых батарей мощностью 18- 28 млн.тгод кокса для одной очереди и дальнейшее развитие этих предприятий до 8-14 батарей. Сооружение углеобогатительных фабрик предусматривается в составе заводов если они размещены вблизи угледобывающих районов или на расстоянии 400-500 км от последних.
Большие масштабы предприятий Украины определяют районную централизацию переработки основных химических продуктов и организацию в составе крупных заводов цехов ректификации бензола и переработки смолы а также получение пекового кокса.
Малотоннажные продукты (нафталин пиридин фенол и другие) перерабатываются и на более удаленных центральных для данного географического района предприятиях. На отдельных из них также организуется более глубокая переработка химических продуктов.
В своем плановом составе коксохимическое предприятие может состоять из следующих цехов: углеподготовки с угольным складом углеобогатительной фабрики с относящимися к ней сооружениями по шламовому хозяйству сушке продуктов обогащения и породоудалению; коксовых печей с угольной башней и устройствами для тушения сортировки и отгрузки кокса; улавливания химических продуктов — смолы аммиака пиридиновых оснований фенолов бензола и в ряде случаев сероводорода с получением серной кислоты или серы; ректификации бензола с получением чистых бензольных продуктов; переработки смолы и получаемых из них продуктов; пеко-коксовой установки и целого ряда других химических цехов и отделений в зависимости от глубины переработки каменноугольных продуктов.
По характеру зданий и сооружений из основных технологических цехов наибольший объем строительных работ приходится на углеподготовительный цех и углеобогатительную фабрику. В основном все сооружения возводятся в железобетоне. При сооружении коксового цеха применяют железобетон и огнеупорную кладку печей. Химические цехи вследствие выноса большинства аппаратуры наружу имеют ограниченный объем зданий [5].
6.Генеральный план коксохимического завода
Генеральный план коксохимического предприятия оказывает большое влияние на размер капиталовложений в строительство предприятия а также на себестоимость продукции и расходы по эксплуатации. Размещение сооружений коксохимического предприятия на генеральном плане должно обеспечить поточное перемещение сырья полупродуктов и готовой продукции по территории предприятия в процессе производства а также обеспечить максимально возможное объединение вспомогательных сетей сооружений (энергетика водоснабжение канализация транспорт автоматическое и телеуправление бытовые корпуса склады мастерские) и коммуникаций для обслуживания групп технологических цехов.
Подача угля от углеприема на углеподготовку осуществляется ленточными конвейерами. Для сокращения их длины углеподготовительное отделение и углеобогатительная фабрика должны располагаться на минимально допустимом по условиям конвейерной связи расстоянии от сооружений углеприема. Расположение коксового цеха должно обеспечивать удобную связь конвейерами с углеподготовительным отделением и трубопроводами (газопровод аммиакопровод и т.п.) с химическими отделениями. Коксовый блок и в частности коксосортировка должны располагаться на минимально возможном расстоянии от коксоприемных сооружений доменного цеха для сокращения длины тракта кок- сопередачи и сведения до минимума числа перегрузок приводящих к излишнему дроблению кокса. Отделение конденсации и улавливания газа располагается с машинной стороны коксовых печей. При этом газовые холодильники осветлители сборники аммиачной воды и смолы машинное отделение следует располагать против центральной поперечной оси обслуживаемого ими коксового блока. Химические отделения (сульфатное сероочистка и др.) обычно располагаю тся последовательно по ходу газа а цехи смолоразгонный и ректификации бензола - параллельно последним.
При размещении химических отделений связанных с обработкой газового потока необходимо учитывать также место расположения внешних потребителей коксового газа (мартеновские цехи головные сооружения дальнего и бытового газоснабжения азотно-туковые и другие химические предприятия) не допуская возвратных и параллельных потоков газа. Объекты водоснабжения энергоснабжения транспорта склады мастерские и другие вспомогательные помещения располагаются на территориях свободных от технологических объектов но с учетом связей с последними.
В соответствии с санитарными нормами проектирования коксохимические заводы относятся к I классу по санитарной вредности. Стоящие отдельно смолоперегонные заводы и углеподготовительные фабрики относятся ко II классу по санитарной вредности. В соответствии с этим между коксохимическими предприятиями и жилыми районами должна предусматриваться санитарно-защитная зона шириной не менее 500 м. Коксохимические заводы должны располагаться в непосредственной близости к железнодорожным путям МПС.
Химические предприятия относятся к категории предприятий выделяющих значительное количество вредностей и поэтому как правило они располагаются за пределами городской черты.
Противопожарная безопасность предприятия достигается за счет обеспечения разрыва между отдельными сооружениями завода а также за счет оснащения предприятия средствами пожаротушения и профилактики пожаров.
Зона между внешними магистралями и ограждениями коксохимического предприятия должна быть заполнена зелеными насаждениями [6].
7.Оптимизация схемы улавливании химических продуктов коксования
Применяемые на большинстве коксохимических заводов Украины схемы охлаждения и очистки коксового газа при некотором различии их характеризуются одинаковой последовательностью основных процессов обработки газа. После газосборников прямой газ охлаждается в трубчатых холодильниках до 25-35°С а затем проходит последовательно аппаратуру для улавливания аммиака бензольных углеводородов и сероводорода. Практика работы коксохимических заводов показала что такая схема улавливания химических продуктов далека от оптимальной и имеет серьезные недостатки обусловливающие снижение технико-экономических показателей и ухудшение экологической обстановки на прилегающей территории.
Прежде всего следует отметить что установленные в соответствии с проектной схемой электрофильтры (перед нагнетателем или после него) на большинстве заводов не работают и поэтому большое количество туманообразной смолы и нафталина поступает в последующую аппаратуру для улавливания химических продуктов что нарушает нормальное протекание процессов и приводит к образованию различных отходов. Нафталин выпадает в виде кристаллов в трубопроводах и аппаратуре забивает насадку в скрубберах и градирне цикла конечного охлаждения газа конденсационную аппаратуру в цехе ваку ум-содовой сероочистки и в бензольном отделении нарушает работу контрольно-измерительных приборов и регулирующих устройств.
При охлаждении газа в конечных холодильниках нафталин накапливается в охлаждающей воде и для его удаления требуется установка фомоздких отстойников или смолопромывателей. Однако из-за низкой эффективности этих процессов значительная часть нафталина поступает с водой в градирню и выдувается воздухом в атмосферу а другая часть уносится с газом в бензольное отделение и сероочистку.
Наличие нафталина и смолы в оборотной воде конечного холодильника практически исключает возможность закрытия этого цикла из-за быстрого забивания водяных холодильников.
Накапливаемый в поглотительном масле нафталин снижает эффективность работы бензольного отделения а установка дополнительной нафталиновой колонны усложняет технологическую схему и требует значительных капитальных и эксплуатационных затрат.
В цехе вакуум-содовой сероочистки нафталин и смолистые вещества откладываются на насадке в скрубберах а также в конденсаторах-холодильниках. что приводит в конечном итоге к увеличению потерь сероводорода с обратным газом. Вместе с сероводородным газом они поступают в вакуум-насосы и способствуют образованию нагара в цилиндрах и клапанах что снижает эффективное! ь их работы и требует периодических остановок для чистки. При мышьяково-содовой сероочистке нафталин и масла нарушают процесс флотации серы в регенераторах.
Значительные трудности в работе цехов улавливания химических продуктов по традиционной схеме связаны с размещением сероочистки в ее хвосте. Наличие цианистого водорода в коксовом газе обусловливает интенсивную коррозию трубопроводов и аппаратуры образование свищей и. как следствие потери химических продуктов в атмосферу или подсос воздуха в аппараты отделения регенерации работающие под вакуумом. Цианистый водород и кислород способствуют образованию в поглотительном растворе сероочистки нерегенерируемых солей (роданидов ферроцианидов тиосульфатов и др.) для удаления которых требуется выводить часть раствора в отвалы а потери его компенсировать дополнительным расходом соды.
На заводах с открытым водным циклом конечных газовых холодильников значительная часть цианистого водорода растворяется в воде и затем выделяется на градирне в атмосферу что резко ухудшает экологическую обстановку и способствует коррозии металлоконструкций на прилегающей территории.
Закрытие водного цикла конечных холодильников трудно реализуемо в существующих условиях из-за быстрого забивания водяных холодильников нафталином и смолой и кроме того не обеспечивает эффективного решения проблемы вредных выбросов так как приводит к увеличению количества жидких отходов в цехах сероочистки и в бензольных отделениях.
Наличие в коксовом газе цианистого водорода нафталина и смолистых веществ затрудняет работу сульфатного отделения ухудшает качество сульфата аммония способствует образованию кислой смолки.
Недостатками существующей технологии является также низкая степень утилизации вторичных источников тепла большой расход технической воды и значительный объем промышленных сточных вод. Применяемый на коксохимических заводах метод обесфеноливания сточных вод является малоэффективным и неэкономичным.
Таким образом получившая распространение на коксохимических заводах классическая схема улавливания химических продуктов коксования не обеспечивает требуемой очистки коксового газа и получения качественных продуктов обуславливает образование значительного количества вредных жидких отходов и газовых выбросов в атмосферу. Между тем только изменение последовательности улавливания химических продуктов по сравнению с классической схемой может обеспечить значительный экономический и экологический эффект. В связи с обострением экологической обстановки и дефицитом энергоресурсов в Украине выбор оптимальной схемы обработки прямого коксового газа является актуальной задачей.
Возможные варианты размещения установок для улавливания химических продуктов в технологической схеме коксохимического завода показаны на рис. 1.7.1. Варианты 123 представляют разновидности классической схемы улавливания и различаются лишь типом первичных газовых холодильников а также аппаратов для очистки газа от смолы нафталина и аммиака.
Варианты 4 и 5 предусматривают предварительную очистку газа от цианистого водорода непосредственно после нагнетателей что позволяет снизить выбросы сю в атмосферу из градирни цикла конечных газовых холодильников коррозию аппаратуры в бензольном и сульфатном отделениях атакже количество жидких отходов в цехе сероочистки.
По варианту 6 вслед за промывкой газа в циановом скруббере производится очистка от сероводорода что существенно облегчает работу КГХ аммиачного сульфатного и бензольного отделений. Такой же эффект достигается и по варианту 7 предусматривающему размещение аммиачной сероочистки непосредственно после первичных холодильников.
Следует однако отметить что реализация последнего варианта требует тщательной очистки коксового газа от туманообразной смолы и
Рис. 1.7.1. Варианты размещения установок для улавливания химических продуктов:
ХНД - холодильник непосредственного действия; ТХ - трубчатый холодильник;
АВО - аппарат воздушного охлаждения; Н - нагнетатель; СВ - скруббер Вентури; Э – электрофильтр;НП - нафталинопромыватель; СА - сатуратор;
АА - аммиачный абсорбер; ЦС - циановый абсорбер; КГ X - конечный газовый холодильник;БС - бензольный скруббер; ВСО - вакуумная сероочистка;
МСО - мышьяково-содовая сероочистка; АСО - аммиачная сероочистка.
нафталина так как накопление их в поглотительном растворе резко снижает эффективность сероочистки. Кроме того размещение большого числа аппаратов перед нагнетателями связано с опасностью подсоса воздуха через неплотности и образования взрывоопасной смеси в системе. Этот недостаток устраняется при размещении аммиачной сероочистки после нагнетателей однако из-за нагревания газа при сжатии потребуется установка дополнительных газовых холодильников. С этой точки зрения определенные преимущества имеет вариант 6
т.к. эффективность вакуум-содовой сероочистки в меньшей степени зависит от температуры газа. Анализ показывает что вакуум-содовый метод сероочистки представляет более широкие возможности как с точки зрения оптимизации схемы улавливания химических продуктов коксования так и с точки зрения утилизации вторичных источников тепла.
РЕФЕРАТ.doc
В данном дипломном проекте проведена разработка отдела первичного охлаждения коксового газа в условиях ПАО “Евраз ДМЗ им. Петровского”.
Выбранно основное технологическое оборудования. Принята конструкция основных аппаратов – вертикальный газовой холодильник механизированный осветлитель и его редуктор и проведены расчеты на прочность выбранных аппаратов.
Предложены замены материалов вал-шестерни и зубчатое колеса на 25ХГМ.
Разработанное отделения отвечает всем нормам и стандартам охраны труда обеспечивает работников необходимыми условиями труда.
ОТДЕЛЕНИЯ ОХЛАЖДЕНИЯ СХЕМА ТЕХНОЛОГИЧЕСКАЯ ОСВЕТЛИТЕЛЬ КОКС ХОЛОДИЛЬНИК
6.1.doc
Ремонт крупногабаритных редукторов если о« может быть выполнен без применения огневых работ производится обычно
Рис. 6.1.1. Проверка редуктора.
на месте их установки. Небольшие редукторы целесообразно для ремонта демонтировать заменяя резервными.
Разборку редуктора для ремонта начинают со снятия торцовых заглушек валов и крышек корпуса. Затем не изменяя положения подшипников зажимают их специальными скобами 1 (рис.6.1.1.) и при помощи свинцовой проволоки измеряют боковые и радиальные зазоры между зубьями шестерен. Далее (если валы работают на скользящих подшипниках) замеряют верхние боковые и торцовые зазоры между валами и вкладышами а также между корпусом редуктора и наружными поверхностями вкладышей. Полученные данные анализируют и намечают способы устранения неисправностей и методы ремонта Односторонний износ или местную выработку зубьев шестерен устраняют опиловкой зубьев до равномерной толщины по всей длине контролируя точность опиловки шаблоном имеющим контур соответствующий рабочему профилю зуба.
Валы при работе редуктора смещаются в своих подшипниках в противоположные стороны. В силу этого при неодинаковых боковых зазорах в подшипниках оси шестерен перекашиваются.
6.2.doc
Трещины в корпусе редуктора ликвидируют заваркой или установкой заплат закрепляемы^ на болтах (рис.6.1.2.) плотность достигается при этом при .помощи соответствующих прокладок.
Рис. 6.1.2. Ремонт корпуса -редуктора.
Если корпус редуктора при ремонте снимали то после установки его на место нужно проверить щупом плотность прилегания опорных плоскостей к раме и при наличии зазора осмотреть опорные поверхности чтобы установить причину (заусенцы забоины грязь). Устранять зазор . сильной затяжкой болтов нельзя во избежание деформации корпуса (сварного) отламывания лап редуктора (чугунного). В таких случаях следует применять прокладки с шириною равной ширине опорной плоскости корпуса редуктора.
При сборке редуктора необходимо тщательно уплотнять стыки корпуса и выходных отверстии для валов чтобы предотвратить утечку масла и попадание пыли в редуктор Хорошие результаты но устранению утечек масла в .местах ^разъема корпуса редуктора дает установка отражательных козырьков изготовляемых из стальной полосы толщиной 3—4 ммк и закрепляемых по внутреннему периметру разъема крышек (рис. 6.1.3.).
Причиной нагрева работающего редуктора может быть как недостаток смазки так и ее избыток. В последнем случае перемешиваемое масло интенсивно нагревается за счет внутреннего трения между ело слоями. Излишек масла кроме того затрудняет уплотнение редуктора.
Рис. 6.1.3. Уплотнение редуктора по (разъему.
Изношенные зубья наплавляют при помощи электросварки. Чтобы предотвратить возникновение внутренних напряжений шестерню предварительно равномерно назревают и наплавку ведут не последовательно а через 5—6 зубьев. Охлаждение после наплавки медленное. На'плавку (Производят электродами с качественным покрытием при этом дают небольшой припуск на последующую зачистку опиловку или строжку.
Сломанные зубья восстанавливают либо ввертыванием в обод шпилек и последующей их обваркой либо установкой на место разрушенных зубьев съемных стальных башмаков. Первый способ применим только для работающих без урона малонагруженных передач.
К недостаткам его следует отнести ослабление обода колеса отверстиями под шпильки 'которое может привести
Рис. 6.2.1. Установка стального башмака взамен сломанного зуба.
к разрыву обода а также расшатывание шпилек и разрушение сварочного шва в процессе работы. Ремонт производится следующим образом: подготовляют место под отверстия для шпилек (если сломана часть зуба оставшуюся часть удалять не следует) как можно ближе друг к другу сверлят отверстия и нарезают в них резьбу ставят и обваривают с припуском на обработку (3—5 мм) шпильки наваренный зуб отжигают газовой горелкой для снятия внутренних напряжений и обрабатывают. .
Второй способ применимый для ремонта всех зубчатых колес независимо от материала и условий работы более рационален. Взамен изломанных зубьев после подготовки места на ободе устанавливают съемный стальной башмак (рис. 6.2.1.). Обод колеса при этом ослабляется незначительно в случае поломки или износа башмака его легко заменить новым. Одним башмаком можно восстановить до трех зубьев. При большем количестве дефектных зубьев ставят рядом два башмака или больше.
Лопнувший обод восстанавливают сваркой при этом рекомендуется нагревать шестерни перед сваркой до красного каления и отжигать их после сварки.
Тяжелонагруженные шестерен с трещинами на ободе можно ремонтировать следующим образом. С обеих сторон трещины сеерлят отверстия диаметром 25—40 мм в зависимости от размера обода. Обод шестерни в месте трещины стягивают болтами приварив специальные накладки (или другим способом).
Затем в отверстия вставляют точеные стальные валики и замерив расстояние между валиками из полосовой стали изготовляют две планки с отверстиями.
Расстояние между отверстиями в планках делают меньше чем расстояние между валиками на величину теплового удлинения планки при нагреве ее до 250 - 300°. Нагретые планки свободно надеваются на концы валиков и. остывая надежно стягивают шестерню (рис. 6.2.3.).
Зубчатые колеса шкивы барабаны с трещинами в ступице ремонтируют посадкой на предварительно проточенную ступицу двух стальных бандажей нагретых до 300—400° которые остывая крепко стягивают ступицу.
Рис. 6.2.3. Подготовка к сварке лопнувшей спицы.
Лопнувшие спицы сваривают. Трещину разделывают под Углом 60°. Для предотвращения остаточных напряжений в зазор Между концами спицы перед сваркой забивают клин разжимающий их на 2—3 мм (рис. 30). При заварке клин оплавляется. При усадке наплавленного металла концы опиц сойдутся. При заварке обода и сред соседние участки детали необходимо подогревать.
3. Центробежные насосы
В процессе эксплуатации насосав обычно изнашиваются защитные втулки вала подшипники уплотнительные кольца корпуса и рабочие колеса. Не ремонтируют а заменяют новыми подшипники качения и защитные втулки вала. Целесообразность ремонта и повторного использования остальных -деталей определяется в каждом конкретном случае в зависимости от величины детали ее стоимости и степени износа.
Изношенные детали ремонтируют способами описанными в гл. III.
Рабочие колеса перед сборкой балансируют каждое в отдельности. Ротор многоступенчатого насоса после сборки подвергают дополнительной статической балансировке. Зазоры которые необходимо выдерживать при сборке центробежного насоса приведены ниже мм:
Радиальный зазор между уплотнительнмы кольцом корпуса и проточкой в рабочем колесе
Радиальный зазор между валом или его защитной втулкой и уплотнительным кольцом корпуса
Зазор между валом и вкладышем (если насос
имеет подшипники скольжения)
Зазор между сальниковыми втулками и валом
или его защитной втулкой
Особое внимание при сборке насоса следует обращать на работу деталей служащих для уравновешивания осевого давления возникающего из-за разности давлений на обеих поверхностях рабочего колеса. При плохом уравновешивании осевого давления вал насоса вместе с рабочими колесами сдвигается в сторону всасывания. Вращающиеся детали начинают тереться о неподвижные что вызывает быстрый износ и понижает к. п. д. насоса.
Надежная работа разгрузочного устройства любой конструкции обеспечивается лишь при нормальных зазорах в уплотнениях между колесами и корпусом насоса. При увеличении этих зазоров выше допустимых осевое усилие возрастает в 7—8 раз что приводит к разрушению упорных подшипников или разгрузочных устройств. Максимально допустимыми можно считать зазоры превышающие в 2—3 раза указанные выше.
Разборка для ремонта и сборка многоступенчатых насосов особенно с вертикальным разъемом относительно трудоемка. Одноименные детали таких насосов внешне сходные между собой в осевых (размерах имеют однако как правило неодинаковые отклонения от номинала как по величине так и по знаку. Для облегчения послеремонтной сборки рекомендуется при разборке насоса пронумеровать все детали и записать их осевые размеры (чтобы собирать детали в требуемой последовательности). При замене какого-либо из дисков или направляющих аппаратов ширину новой детали нужно брать обязательно равной ширине детали заменяемой.
Рис. 6.3.1. Сборка многоступенчатого насоса
Оборка многоступенчатых насосов с вертикальным разъемом ведется в следующей1 последовательности. Вал 1 (рис. 6.3.1.) с насаженной на него лолумуфтой 2 и надетой грундбукоой 3 вставляют в крышку всасывания 4. На вал насаживают первое рабочее колесо 5 так чтобы оно торцом уперлось в заточку вала. Колесо 5 (вместе с валом) :при помощи шаблона 6 устанавливают по отношению к крышке всасывания в такое положение при котором ось канала колеса находится от плоскости прилегания направляющего аппарата на расстоянии равном расстоянию от этой плоскости до оси канала направляющего аппарата. На валу против' крышки всасывания делают риску Р. Последовательно собирают направляющие аппараты с прокладками между ними остальные рабочие колеса на шпонках и крышку нагнетания. Стягивают все детали крепежными болтами.
Затягивать болты нужно равномерно во избежание перекоса секций и следить чтобы сопрягаемые плоскости направляющих аппаратов и крышек всасывания и нагнетания плотно прилегали друг к другу. Затем на вал насаживают разгрузочный диск стягивают им до отказа все детали ротора сдвинув весь ротор в сторону крышки всасывания смотрят встала ли риска Р на прежнее место.
Если риска уходит внутрь стакана сальника распорную втулку следует заменить более длинной или поставить дополнительно шайбу соответствующей длины. Если же риска выступает из крышки распорную втулку нужно подрезать. Отрегулировав положение ротора проворачивают его вручную и проверяют отсутствие трения деталей друг о друга и заедания. Если ротор начинает вращаться туго после установки кронштейна со стороны нагнетания то причиной может быть перекос в этом кронштейне который необходимо устранить. После окончательной сборки насоса следует также проверить по риске обратный разбег в сторону разгрузки. Его величина должна быть не менее 3—4 мм. Во время работы необходимо периодически проверять положение установочной риски Р на валу насоса. Сдвиг риски указывает на износ кольца разгрузочного устройства.
Плохое уплотнение зазоров между валом и корпусом насоса ведет к утечкам перекачиваемой жидкости а в (случае перекачки агрессивной жидкости — к ускоренному выходу из строя подшипников насоса как это имеет место например в кислотных насосах сульфатного отделения.
Наиболее распространенным способом уплотнения в насосах коксохимического производства является установка сальников с мягкой набивкой. Сальниковая набивка составляется из отдельных колец с косым срезом в стыке. После тщательной очистки сальниковой коробки 1 (рис. 93 а) от остатков старой набивки и грязи ;в коробку вводят одно за другим кольца новой набивки 2 таким образом чтобы стыки расположенных рядом колец были смещены один относительно другого на 120°. Куски набивки нарезают такой длины чтобы между стыками каждого уложенного в гнездо кольца оставался
Чтобы не испортить шейку вала (или защитную втулку) кольца укладывают деревянными палочками. Недопустима набивка сальника длинным куском шнура наматываемого по спирали на вал так как при этом не обеспечивается хорошая работа уплотнения.
В сальниковую коробку закладывают столько колец чтобы грундбукса 3 при первой затяжке входила в коробку до 13 ее высоты. Для набивки лучше всего применять шнур квадратного сечения толщина которого соответствует промежутку между валом и корпусом коробки. Круглый шнур неплотно заполняет сальниковое пространство.
Грундбуксу 3 следует подтягивать равномерно без перекосов. Чрезмерная и неправильная затяжка сальников приводит к быстрому разогреву вала и к срабатыванию его на участке саль ника. Сальниковая набивка должна быть затянута хорошо но затяжка е должна препятствовать легкому проворачиванию вала от руки. Новая набивка в первое время после установки дает сравнительно большую усадку поэтому в первый период работы при подтяжке сальника добавляют дополнительные кольца набивки.
Грязь и отдельные твердые частицы .попадая в сальник могут повредить вал поэтому нужно тщательно следить за чистотой сальникового уплотнения.
Рис. 6.3.2. Сальник обычный (а) и с фонарем (б).
обнаружив не плотность подтягивать сальник. Если подтяжкой устранить не плотность не удается сальниковую набивку необходимо сменить.
Для улучшения работы сальникового уплотнения рекомендуется между кольцами набивки прокладывать вырезанные по размерам сальника шайбы из паронита или листового свинца толщиной 1—2 мм а конечные кольца устанавливать из сухой хлопчатобумажной пеньковой асбестовой или стеклянной набивки.
Хорошее уплотнение достигается применением сальника с гидравлическим затвором («фонарем») 1 (рис. 6.3.2.б) представляющим собой специальное кольцо в которое через трубку 2 подается нейтральная жидкость под давлением большим на 1—3 ат чем рабочее давление в насосе. Нейтральная жидкость не должна портить перекачиваемую и должна смазывать сальниковое устройство. Фонарь располагают так чтобы при подтягивании грундбуксы последняя не могла перекрыть отверстие для подачи в фонарь жидкости.
Выбор .материала для сальникового уплотнения зависит от конструкции узла и характера его работы. Основные требования предъявляемые к сальниковым набивкам сводятся к химической и тепловой стойкости а для сальников центробежных насосов и других машин с быстровращающимися или перемещающимися возвратно-поступательно деталями необходим кроме того еще низкий коэффициент трения. Наиболее широко применяется асбестовый плетеный прографиченный шнур. Хорошими эксплуатационными свойствами обладают асбестовые волокнистые маслобензостойкие самосмазывающиеся набивки АМБ-1 и АМБ-2. Для уплотнения сальников соприкасающихся с серной кислотой целесообразно применять кислотостойкие сальниковые набивки КНП-4 1-КС-С КСП-1 и набивки из голубого асбеста.
Одним из условий длительной службы сальниковой набивки является гладко отшлифованная без рисок забоин и задирав поверхность соприкасающегося с набивкой участка вала.
В последние годы для уплотнения валов насосов компрессоров и аппаратов начали широко применять торцовые или механические уплотнения.
Герметизация в них достигается за счет постоянного контакта прижимаемых друг к другу при помощи пружин торцовых поверхностей уплотнительных колец одно из которых стальное каленое и хорошо отшлифованное вращается вместе с валом а второе из бронзы или графита неподвижно. Тепло которое -получается при трении работающих частей отводится циркулирующей через коробку уплотнения жидкостью. Давление этой жидкости обычно на 05—15 ат выше давления перекачиваемой среды в рабочей камере насоса.
Торцовые уплотнения при хорошем изготовлении и правильной оборке -обеспечивают чрезвычайно малую утечку рабочей среды при незначительном износе трущихся поверхностей. Для насосов перекачивающих кислоту торцовое уплотнение эффективнее уплотнения с мягкой сальниковой набивкой.
4. Ремонт химической аппаратуры
Аппаратуру коксохимического производства ремонтируют большей частью без ее демонтажа в действующем цехе. Это накладывает особую ответственность на руководителя ремонта и на ремонтников за тщательную подготовку и выполнение всех мероприятий обеспечивающих безопасность работ. Ремонтные работы внутри химических аппаратов и сосудов производятся только при наличии плана работ и специального допуска.
Прежде чем приступить к ремонту аппарата или сосуда необходимо выполнить следующие мероприятия. После прекращения подачи газа или жидкости аппарат опорожняют нейтрализуют (если это необходимо) и пропаривают. Пар додают в один из штуцеров аппарата. Испаряющийся продукт удаляют обычно через свечу а в тех случаях когда аппарат установлен на открытом воздухе и исключены возможность отравления людей и вспышки — через верхний штуцер. После пропарки аппарата открывают люки чтобы при охлаждении в аппарате не образовался вакуум.
При быстром охлаждении закрытого аппарата после пропарки вследствие более низкой температуры наружного воздуха и большой поверхности аппарата и в особенности при подаче в нагретый аппарат воды через разбрызгивающие устройства возможна потеря устойчивости и деформация (сплющивание) его.
Заглушки изготовляют из стальных листов толщиной 3—4 мм к которым с обеих сторон пришивают или приклеивают прокладки из соответствующего назначению трубопровода мате риала. Диаметр заглушки должен быть таким чтобы она свободно поместилась между фланцевыми болтами но не болталась. Для удобства установки или выемки а также для того чтобы было видно место установки заглушки и ее наличие заглушку снабжают хвостовиком выступающим за торцы фланцев.
При отглушении трубопроводов большого диаметра и особенно газопроводов раздвигать фланцы клиньями не следует так как при этом можно погнуть изготовленные из углового железа фланцы трубопровода и повредить чугунные фланцы задвижек и дросселей. К таким трубопроводам возле фланцев между которыми обычно ставят заглушки при ремонте оборудования рекомендуется приваривать кронштейны на расстоянии соответствующем габариту имеющихся в цехе домкратов.
Установка и выемка заглушек при раздвигании фланцев домкратами производятся значительно быстрее чем при пользовании клиньями и менее трудоемки а приваренными однажды кронштейнами можно пользоваться многократно.
Кронштейны располагают так чтобы они не мешали установке заглушки. Толщину заглушки большого диаметра выбирают такой чтобы прогиб заглушки не превышал 5 мм в противном случае вынимать ее будет затруднительно. Заглушки устанавливаемые на газовых линиях и на линиях с ядовитыми и огне-' опасными жидкостями проверяют на герметичность керосином. Недопустима установка в указанных случаях заглушек сваренных из двух кусков листовой стали.
При отсутствии или неисправности отсекающего устройства на газопроводе во время установки заглушки давление газа снижают до 50 мм вод. от. Перед размачиванием фланцев на газопроводе коксового газа для предотвращения загорания фланцы смазывают известковым молоком и к газопроводу подводят острый пар. Для заглушек диаметром более 1000 мм лучше устанавливать прокладки изготовленные из стального кольца толщиной 1 мм обмотанного тонким асбестовым шнуром. Общая толщина такой прокладки должна быть не более 8 мм На газовых линиях и на линиях с ядовитыми и огнеопасными жидкостями устанавливать и вынимать заглушки должны специально обученные рабочие строго соблюдая правила производства опасных и газоопасных работ.
Если имеется возможность то вместо отделения ремонтируемого аппарата от работающего газопровода заглушкой лучше демонтировать на время ремонта одно звено газопровода (патрубок колено).
Установив заглушки на материальных и газовых линиях от-' крьгвают все имеющиеся на аппарате люки проветривают и чистят аппарат.
Непосредственно перед огневыми работами производят испытание на вспышку газо-воздушной смеси отобранной из аппарата. Такое испытание повторяют через каждые 1—2 часа на протяжении всего времени производства огневых работ и кроме того каждый раз непосредственно перед возобновлением прерванных огневых работ.
4.2.doc
бензин бензол бензтерен ксилол сероуглерод толуол фенол.
в) Биологические опасные и вредные производственные факторы:
- Поточенние микроорганизмы (бактерии вирусы риккетсии спирохеты грибы) и продукты их жизнедеятельности.
г) Психофизиологические опасные и вредные производственные факторы по характеру действия подразделяются на:
- Физические перегрузки;
- Нервно-психические перегрузки
Перечень веществ и материалов применяемых в проектируемом производстве - бензольные углеводороды и их производные аммиак аэрозоли серной кислоты серная пыль пиридин фенолы коксовый газ СО промаерозоли сульфат аммония повышенная температура щелочи.
Характеристика вредных веществ
Действие на организм
При концентрации более 1 мгл наблюдаются судороги обморок смерть
Коксохимические заводы добыча природного газа производство искусственного вискозного волокна
Действует на кожу слизистые оболочки дыхательные пути
ТЭС металлургическая и химическая промышленность
Концентрация более 5% (об.) опасна дня жизни
Газы после сгорания органического топлива содового производства процессов брожения
NО - при попадании в организм действует на ЦНС при большой концентрации разрушает гемоглобин крови NО2 - действует на слизистую оболочку легких при концентрации? 5 мгм3 наблюдается тяжелое отравление
Заводы по производству азотной кислоты ТЭС выхлопы ДВС котельные работающие на органическом топливе
Действует на кровь в результате чего кровь теряет способность переносить кислород
Коксохимические заводы производство чугуна и стали выхлопы ДВС
Таблица 4.1.1. - Исходные данные для расчета возможных концентрации вещества в воздухе рабочей зоны.
2. Оценка пожаровзрывоопасности проектируемого объекта
Таблица 4.2.1. - Концентрационные пределы взрыва веществ при начальной температуре 298 К
Состав взрывоопасной смеси% об
Концентрационный предел взрыва% об.
HKM1 НКМ2 НКМn - нижний концентрационный предел взрываемости n-го горючего компонента% об.
ВКМ1 ВКМ2 ВКМn - верхняя концентрационный предел взрываемости n-го горючего компонента% об.
HKMBсум = 100 (852 3 +10 18 +2 150 +2 45 +1 4) = 2307% об.
ВКМВсум = 100 (859 5 +10 91 +2 280 +2 45 +1 75) = 9827% об.
Правила пожарной безопасности.
Вы обязаны соблюдать осторожность и все правила противопожарной безопасности при обращении с огневыми материалами (керосин бензин спирт продукты разгонки каменноугольной смолы и ректификации бензола масла толуола ксилола и др.).
Вы обязаны помнить что эти вещества не только легко воспламеняются но и выделяют воспламеняющие пары.
В огнеопасных местах вывешиваются соответствующие предупредительные знаки или другие указатели.
Запрещается разбрасывать промасленные концы тряпки и другой обтирочный материал.
Для хранения обтирочного материала должны быть металлические ящики с плотно закрывающимися крышками.
3 Профилактические мероприятия по охране труда
3.1. Средства защиты органов дыхания Патрон к респиратору РПГ-67
КД для защиты от аммиака и сероводорода.
3.2. Респиратор РПГ-67
Респиратор в комплекте с двумя патронами. Для защиты органов дыхания от вредных паров и газов присутствующих в воздухе рабочих зон производственных помещений в концентрации не превышающей ПДК более чем в 10 раз. Представляет собой универсальный дыхательный прибор фильтрующего типа имеет трикотажный обтюратор и резиновую полумаску с устройством для установки сменных патронов.
Предназначены для защиты: марка «А» от паров органических соединений (бензин керосин ацетон бензол сероуглерод спирты эфиры анелин галоидоорганические соединения нитросоединения бензола и его гомологи тетраэтилсвинец фосфор и хлор содержащих ядохимикаты) марка «В» от кислых газов и паров (сернистый ангидрит хлор сероводород синильная кислота хлористый водорот фосген фосфор и хлорсодержащие ядохимикаты; марка «КИ» от аммиака и сероводорода.
3.3. Респиратор РУ-60
Для защиты органов дыхания от вредных паров и газов присутствующих в воздухе рабочих зон производственных помещений в концентрации не превышающей ПДК более чем в 10 раз. Представляет собой универсальный дыхательный прибор фильтрующего типа имеет трикотажный обтюратор и резиновую полумаску с устройством для установки сменных патронов. Отличается от респиратора РПГ-67 наличием в патронах противоаэрозольного фильтра.
Предназначены для защиты: марка «А» от паров органических соединений (бензин керосин ацетон бензол толуол ксилол сероуглерод спирты эфиры анилин галоидоорганические соединения нитросоединения бензола и его гомологи тетраэтилсвинец фосфор и хлорсодержащие ядохимикаты); марка «В» от кислых газов и паров (сернистый ангидрит хлор сероводород синильная кислота хлористый водород фосген фосфор и хлорсодержащие ядохимикаты); марка «КИ» от аммиака и сероводорода.
3.4. Коробка Противогазная (А В КД БКФ)
ПРО107 Коробка Противогазная малого габарита (А В КД БКФ)
ПРО108 Коробка Противогазная большого габарита (А В КД БКФ)
Маркировка и назначение противогазных коробок:
А для защиты от паров органических соединений (бензин керосин ацетон бензол и т. д.);
В для защиты от кислых газов и паров (сернистый ангидрид сероводород и т. д.);
КД для защиты от аммиака и сероводорода;
БКФ для защиты от кислых газов и паров паров органических соединений мишьяковистого и фосфористого водорода.
3.5. Малого габарита:
Противогазовые ФГ-5-А2 В2 Е2 К2 А2В2Е2К2 А2В2Е2 В2Е2К2 А2В2К2 с:
- Фильтры марки "в": для защиты от неорганических газов и паров за исключением окиси углерода (диоксид серы хлор сероводород цианистый водород йод озон фосген и др.).
- Фильтры марки "е": для защиты от диоксида серы и других кислых газов и паров (диоксид серы диоксид хлора сероводород синильная кислота йод хлористый водород фосген фосфор и хлорорганические ядохимикаты).
4.1.doc
Основные и вредные производственные факторы подразделяются по природе действия на следующие группы:
а) Физические опасные и вредные производственные факторы подразделяются на:
- Движущиеся машины и механизмы подвижные части производственного оборудования передвигающиеся изделия заготовки материалы разрушающиеся конструкции обрушивающиеся черные породы повышенная запыленность и загазованность воздуха рабочей зоны повышенная или пониженная температура воздуха рабочей зоны повышенный уровень шума и вибрации и т.д. . . д.
б) Химические опасные и вредные производственные факторы подразделяются:
По характеру воздействия на организм человека на:
- Сенсибилизирующие.
Влияющие на репродуктивную функцию:
- По пути проникновения в организм человека через:
органы дыхания желудочно-кишечный тракт кожные покровы и слизистые оболочки.
2.2.doc
Из-за ограниченности поверхности и времени контактирования газа и жидкости в газосборнике не достигается равновесное состояние поэтому температура газа на выходе существенно выше температуры воды а температура точки росы газа несколько ниже температуры воды на выходе то есть газ на выходе из газосборника является ненасыщенным. Разница между равновесной и фактической температурой воды и газа на выходе и температурой точки росы последнего зависит при прочих равных условиях (поверхность и время контактирования) от интенсивности процессов тепло- и массообмена между ними. Скорость этих процессов определяется разностью температур газа и жидкости и гидродинамическими условиями контактирования.
Коэффициент теплоотдачи от газа к жидкости обратно пропорционален градиенту температур в пограничном слое. При наличии массообмена между газом и жидкостью на границе раздела возникает поперечный поток пара вызывающий изменение толщины пограничного слоя и следовательно градиента температур в нем. В работах Лыкова А.В. Исаченко В.П. и других авторов изучавщих теплообмен между газом и жидкостью в контактных теплообменниках показано что при направлении потока пара от поверхности жидкости в газовую фазу (испарение десорбция) толщина пограничного слоя увеличивается а градиент температур в нем и следовательно коэффициент теплообмена между газом и жидкостью уменьшаются. При направлении же потока пара из газовой фазы к поверхности раздела (конденсация сорбция) толщина пограничного слоя уменьшается а градиент температур в нем и коэффициент теплоотдачи возрастают. По ориентировочным оценкам при ламинарном обтекании влажным воздухом поверхности жидкости
и температурном напоре более 260°С снижение коэффициента теплоотдачи от газа к жидкости из-за испарения последней составляет около 10% по сравнению с чистым теплообменом. Для коксового газа в указанных условиях расчетное снижение коэффициента теплоотдачи достигает 50%.
Таким образом охлаждение надсмольной воды подаваемой на орошение газосборника может обеспечить интенсификацию теплообмена в нем однако на практике оно не получило распространения из-за необходимости установки дополнительных теплообменников и возможного увеличения капитальных и эксплуатационных затрат.
Охлаждение надсмольной вода оказалось экономически оправданным на некоторых коксохимических заводах с вакуум-карбонатной сероочисткой при использовании тепла надсмольной воды для нагревания поглотительного раствора в регенераторах.
Наибольшее распространение получили газосборники круглого сечения соединенные внешними клапанными коробками со стояками. На ряде заводов установлены газосборники корытообразного сечения с размещенными в них клапанами. При такой конструкции практически исключается забивание клапанов смолой и фу сами что упрощает их эксплуатацию.
Газосборники устанавливаются на коксовых батареях с машинной стороны то есть со стороны химических цехов. Установка на некоторых батареях двух газосборников (с коксовой и машинной сторон) оказалась не вполне оправданной из-за перетоков газа через подсводовое пространство печей и ухудшения условий труда на них.
Необходимая для охлаждения газа вода подается через форсунки установленные в коленах стояков и в газосборнике. Расход воды принимается 5-6 м3 на 1 т сухой шихты. При удовлетворительной работе форсунок температура коксового газа на выходе из газосборника снижается до 80-85°С а температура точки росы его повышается до 78-82°С в зависимости от влажности шихты.
В результате охлаждения газа в газосборнике выделяется в жидком виде 60-70% смолы а остальное количество ее уносится с газом в парообразном состоянии и в виде мельчайших капелек - туманообразной смолы. Надсмольная вода при контакте с газом насыщается аммиаком и кислыми газами (СО2 H2S HCN SO3 и др.) образующими соли аммония. Одновременно из газа вымывается большая часть угольной и коксовой пыли образующей со смолой фусы - агрегаты твердых частиц со смолой.
Надсмольная вода из газосборника поступает самотеком по трубопроводам в механизированные осветлители где отстаивается от смолы и фусов после чего вновь подается насосом на орошение газосборников. Во избежание чрезмерного накопления солей вызывающих коррозию трубопроводов и затрудняющих процесс отстаивания в осветлителе часть надсмольной воды газосборникового цикла выводится на переработку а убыль ее компенсируется газовым конденсатом из первичных холодильников.
Для охлаждения газа до 25-35°С применяются холодильники непосредственного действия (контактные) и косвенного дейст вия (трубчатые).
К холодильникам непосредственного действия относятся насадочные полочные (каскадные) и низконапорные скрубберы Вентури разработанные ВУХИНом. Процесс охлаждения газа в них осуществляется при непосредственном контакте с водой поэтому изложенное выше о механизме и закономерностях процессов тепло- и массо- обмена в газосборнике справедливо и по отношению к ним.
Особенностью насадочных и полочных холодильников является про- тивоточное движение газа и воды благодаря чему температура воды на выходе может достигать 70°С и более а ее расход значительно ниже чем в скрубберах Вешури. В этих холодильниках снижение температуры газа до 30-35°С может быть достигнуто при одноступенчатом охлаждении тогда как в скрубберах Вентури для этого требуется 2-3 ступени.
Перспективными для охлаждения коксового газа представляются холодильники непосредственного действия колонного типа с провальными тарелками отличающиеся высокой интенсивностью теплообмена при противоточном движении фаз.
Преимуществом холодильников непосредственного действия является более высокая чем в трубчатых холодильниках степень очистки газа от смолы и нафталина. По опытным данным при двухступенчатом охлаждении газа в скрубберах Вентури содержание туманообразной смолы в нем снижается до 0.2-03 г'м3 что соответствует степени очистки 80-90%. Холодильники непосредственного действия отличаются простотой конструкции и низкой металлоемкостью. Общим недостатком их является насыщение охлаждающей воды аммиаком кислыми газами фенолом и другими вредными примесями что исключает возможность ее охлаждения в градирнях и требует установки специальных теплообменников. Применявшиеся ранее для этой цели оросительные холодильники отличаются низкой интенсивностью теплообмена и громоздкостью а их эксплуатация связана с усиленной коррозией металлоконструкций и ухудшением санитарно-гигиенических условий из-за испарения воды и выделения паров в атмосферу. Эти недостатки обусловили отказ от применения газовых холодильников непосредственного действия и замену их трубчатыми при реконструкции цехов улавливания химических продуктов коксования в 50-80-е годы.
В трубчатых холодильниках контакт газа с охлаждающей водой исключается поэтому массообмен между ними отсутствует. Интенсивность теплообмена в них ниже из-за дополнительного термического сопротивления разделяющей стенки и слоя загрязнений на поверхностях со стороны газа и воды. В нашей стране получили распространение две разновидности этих холодильников: с вертикальными трубами и с горизонтальными трубами. В первых газ движется в межтрубном пространстве разделенном вертикальными перегородками на 6 последовательных ходов
вдоль труб противопотоком к воде движущейся в трубах под действием небольшого перепада уровней в смежных водяных камерах. Образующийся газовый конденсат выводится из нижней части межтрубного пространства каждого хода. Из-за малой скорости движения воды в трубах (около 01 мс) а также интенсивного отложения нафталина на внешней поверхности труб последних ходов коэффициент теплопередачи в этих холодильниках незначителен. Для интенсификации процесса требуется периодическая пропарка межтрубпого пространства с целью удаления нафталина.
В холодильниках с горизонтальными трубами газ движется сверху вниз перпендикулярно оси труб а вода проходит снизу вверх последовательно через все трубные пучки соединенные между собой водяными камерами. Во избежание осаждения взвешенных частиц и солей жесткости в трубах скорость воды должна поддерживаться не менее 08-10 мс а температура воды на выходе не более 42°С. Весь газовый конденсат образующийся в холодильнике стекает сверху вниз и смывает нафталин отлагающийся на трубах нижних пучков. С этой же целью в межтрубное пространс тво вводится сверху через разбрызгивающее устройство горячая смола или водо-смоляная эмульсия. Благодаря этому не требуется частая пропарка холодильников а интенсивность теплообмена в них значительно выше чем в холодильниках с вертикальными трубами.
Достоинством холодильников с горизонтальными трубами является также возможность использования тепла коксового газа для нагревания поглотительного раствора сероочистки в верхних трубных секциях с целью регенерации. Недостатками этих холодильников являются сложность конструкции большая металлоемкость недоступность труб для осмотра чистки и ремонта из-за большой высоты аппаратов и сложности снятия крышек водяных камер крепящихся к корпусу с помощью большого числа шпилек.
К трубчатым газовым холодильникам относятся также аппараты воздушного охлаждения в которых коксовый газ движется по трубам
оребренным снаружи и установленным с наклоном к горизонтальной оси для облегчения стока газового конденсата а воздух - в межтрубном пространстве перпендикулярно оси труб с помощью осевого вентилятора. В зависимости от температу ры окружающего воздуха коксовый газ охлаждается в таких аппаратах летом до 67- 70°С а зимой до 59-63°С. Для дальнейшего снижения температуры
Из приведенного выше анализа следует что совершенствование технологии охлаждения газа и конструкций газовых холодильников является актуальной задачей коксохимиков. В последнее время вновь возрастает интерес технологов к применению газовых холодильников непосредственного действия благодаря возможности использования для охлаждения оборотной воды высоко интенсивных спиральных и пластинчатых теплообменников серийное производство которых освоено рядом зарубежных фирм и отечественными заводами химического машиностроения [8].
2. Очистка надсмольной воды от фусов и смолы
Отстаивание надсмольной воды газосборникового цикла от смолы и фусов является важной технологической операцией обеспечивающей нормальную работу форсунок установленных в коленах стояков и газосборнике и удовлетворительное охлаждение коксового газа. Качество смолы также определяется в значительной мере полнотой выделения из нее фусов и воды.
Разделение жидкой смеси основано на различии плотностей ее компонентов и происходит под действием сил тяжести. Надсмольная вода с растворенными в ней солями аммония и другими примесями имеет плотность 1020-1050 кгм3 смола 1120-1220 кгм3 а фусы до 1250 кгм3. Процесс разделения осуществляется в механизированных осветлителях различных конструкций. На отечественных коксохимических предприятиях получили применение осветлители прямоугольной формы объемом 210 м3 и цилиндрической формы объемом 650 м3 . При времени отстаивания 05 часа производительность осветлителей по воде составляет 420 и 1300 м3 час соответственно.
Устройство и техническая характеристика этих осветлителей приведены в учебной и справочной литературе.
Скорость осаждения фусов зависит от вязкости смолы и следовательно от температуры среды в осветлителе. С этой целью днище и нижняя часть корпуса его обогреваются с помощью паровых змеевиков. В процессе эксплуатации обнаружилось что из-за неравномерного обогрева днища в осветлителях возникают конвективные токи препятствующие осаждению частиц и затрудняющие процесс разделения фаз. Серьезным недостатком цилиндрических осветлителей является также неудачная конструкция радиальных скребков при вращении которых фусы перемещаются к стенкам аппарата то есть в противоположном от конвейера направлении что затрудняет удаление фусов и приводит к частым поломкам.
Для устранения этих недостатков Гипрококсом разработана более совершенная конструкция механизированного осветлителя прямоугольной формы объемом 380 м3 . В отличие от упомянутых выше осветлителей в нем вместо парового змеевика предусмотрен обогрев днища осветленной надсмолыюй водой отбираемой из верхней части аппарата. С этой целью днище выполнено двойным а его полость разделена продольными вертикальными перегородками на отдельные каналы по которым последовательно проходит надсмольная вода имеющая температуру 75-80°С. Мягкий и равномерный обогрев теплой водой препятствует локальному загустеванию фусов что облегчает их удаление и обеспечивает равномерное распределение температур во всем объеме аппарата что исключает образование конвективных токов и способствует лучшему осаждению частиц.
Исследования работы новых осветлителей в промышленных условиях подтвердили их высокую эффективность и надежность. При очистке пад- смольной воды содержащей 436 гл смолистых веществ и 067 гл механических примесей (твердых частиц) осветленная вода содержала 022 гл смолистых веществ и 0119 гл взвешенных примесей.
Содержание воды в смоле после осветителей было в среднем равно 303% асвободного углерода 574%. Плотность смолы составляла 1208 аводы 1005 кгм3.
Для разделения газового конденсата образующегося в первичных холодильниках применяются отстойники представляющие вертикальные цилиндрические емкости снабженные штуцерами для ввода жидкой смеси в среднюю часть и вывода осветленной аммиачной воды сверху а смолы снизу через регулятор уровня раздела.
Смола после отстойников и механизированных осветлителей содержит 10-12% воды и поэтому подается для дальнейшего обезвоживания в резервуары - отстойники. Для этой дели применяются также цилиндрические механизированные осветлители служащие хранилищами в которых протекают процессы дополнительного отделения смолы от воды и фусов обеззоливания и обессоливания ее.
На некоторых коксохимических заводах смола газосборникового цикла после отстоя в механизированных отстойниках-осветлителях подвергается двух- трехступенчатой промывке надсмольной водой холодильникового цикла в соотношении 1:1 в шестилопастных смесителях. Образующаяся при этом эмульсия разделяется в механизированных отстойниках при температуре 85-95°С. Экстракт первой ступени отделяющийся от смолы поступает на орошение газосборника а изочная вода на переработку в аммиачное отделение. Очищенная используется для экстракции нафталина из оборотной воды в конечных газовых холодильниках после чего поступает на склад.
В условиях применения бездымной загрузки коксовых печей рассмотренные методы очистки смолы не обеспечивают требуемых показателей ее качества. Для более глубокой очистки смолы от фусов на ряде заводов осваиваются перспективные методы центрифугирования и виброфильтрации. С помощью центрифуги типа 20ГН-2201У-02 содержание минеральных примесей (золы) в смоле снижается от 035 до 0065- 008%
а содержание воды от 30% до 25-35% что позволяет получать из нее пропиточный пек удовлетворяющий требованиям электродной промышленности. Хорошие результаты были получены также при фильтровании смолы с помощью вибросит. При производительности вибросита 5-9м3час зольность смолы снижалась на 40%. Преимуществом этого метода является возможность отделения от смолы пористых фусов которые имеют плотность близкую к плотности смолы и не могут быть выделены на центрифуге. Преимуществом вибросит являются также простота конструкции малые габариты и металлоемкость [9].
3. Технологические схемы первичного охлаждения коксового газа
Применяемые на коксохимических предприятиях схемы охлаждения газа различаются типом газовых холодильников числом ступеней охлаждения конструкцией механизированных отстойников-осветлителей а также способом обезвоживания и очистки от фусов смолы. Первые коксохимические заводы построенные в нашей стране имели отделения конденсации оборудованные газовыми холодильниками непосредственного действия что объясняется простотой конструкции их сравнительно низкой металлоемкостью и высокой интенсивностью теплообмена. Недостатками этой схемы являются громоздкость оросительных холодильников применявшихся для охлаждения оборотной аммиачной воды а также неудовлетворительные санитарно-гигиенические условия и интенсивная коррозия оборудования на прилегающей территории из- за выделения большого количества паров в атмосферу что и обусловило в дальнейшем отказ от этой схемы и замену холодильников непосредственного действия трубчатыми холодильниками.
Схемы охлаждения коксового газа в холодильниках с вертикальными и горизонтальными трубами принципиально не отличаются друг от друга однако первые требуют значительно больше производственных площадей для размещения холодильников с вертикальными трубами.
Образующийся в них газовый конденсат из-за более высокой средней температуры менее насыщен аммиаком сероводородом и другими кислыми газами фенолами что облегчает его переработку.
С целью сокращения расхода технической воды разработаны схемы двухступенчатого охлаждения коксового газа - в первой ступени воздухом с помощью аппаратов воздушного охлаждения а во второй водой в трубчатых холодильниках скрубберах Вентури или насадоч- ных колоннах. Недостатком таких схем является потеря физического тепла прямого коксового газа поэтому они неприемлемы для коксохимических предприятий с вакуум-карбонатной сероочисткой являющейся крупным потребителем низко потенциального тепла.
Бо льшой интерес представляет предложенная УХИНом схема двухступенчатого охлаждения коксового газа отличающаяся тем что после первой ступени газ очищают от туманообразной смолы в электрофильтрах а также от аммиака и цианистого водорода. Это позволяет во второй ступени получать практически чистый конденсат который после обесфеноливания может быть использован в оборотном цикле водоснабжения. При этом отпадает необходимость в аммиачном отделении что является важным преимуществом схемы.
Ниже приведено описание наиболее распространенных и перспективных схем первичного охлаждения коксового газа [10].
3.1. Схема первичного охлаждения коксового газа в холодильниках непосредственного действия
Прямой коксовый газ поступает из подсводового пространства коксовых камер при температуре 650-700сС через стояки в газосборник 1 (рис. 2.3.1.1.) где охлаждается надсмольной водой имеющей температуру 75-80°С распыляемой специальными форсунками в количестве 5-6 м3 на т сухой шихты. В результате тепло- имассообмена между коксовым газом и водой температура газа снижается до 82-87°С а температура воды повышается до 80-83°С.
При этом в газосборнике протекают следующие процессы:
—испарение воды и повышение влагосодержания газа до состояния соответствующего температуре точки росы 79-82°С;
конденсация смолы в количестве 60-70% от ее ресурсов в газе;
—вымывание из газа твердых частичекуптя и кокса которые смешиваясь со смолой образуют фусы.
Количество образующихся в газосборнике фусов колеблется в пределах 001 - 002% от веса сухой шихты.
Охлажденный в газосборниках коксовый газ отсасывается из каждой батареи коксовых печей по газопроводам 2 и поступает вместе с надсмольной водой смолой и фусами в сепаратор 3 где происходит отделение газовой фазы от жидкой. Надсмольная аммиачная вода вместе со смолой поступает по трубопроводу в механизированный освет литель 1.1 а коксовый газ - в первичный холодильник непосредственного действия 4 где при орошении надсмольной аммиачной водой предварительно охлажденной до 25-30°С в оросительных холодильниках 5 температура коксового газа снижается до 30-35°С. При этом в холодильнике непосредственного действия протекают следующие процессы:
—конденсация и выделение каменноугольной смолы в количеств 30-40% от общих ресурсов до остаточного содержания ее 15-2г на 1 м газа (туманообразная смола);
—конденсация водяных паров до состояния насыщения газа пр температуре 30-35°С;
—частичная абсорбция из коксового газа аммиака углекислоты сероводорода синильной кислоты и других компонентов газовым кон денсатом;
—абсорбция нафталина каменноугольной смолой до остаточно го содержания его 18-28 г на 1нм3 газа.
Рис. 2.3.1.1. Схема первичного охлаждения коксового газа в холодильниках непосредственного действия:
- азосборпик; 2 6 8 10 — газопровод; 3 — сепаратор;
— холодильник непосредственного действия; 5 - оросительный холодильник; 7 - нагнетатель; 9-электрофильтр; 11 - механизированный осветлитель; 12-промежуточный сборник надсмольной воды; 13 15 19 23 25-насос; 16.21 - гидрозатвор; 17 - отстойник; 18-промежуточный сборник конденсата; 20 - промежуточный сборник смолы; 22 24 - сборник надсмольной волы.
Рис. 2.3.1.2. Газосборник круглого сечения:
- седла газосборника;2 - корпус газосборника;3 - отвод из газосборника с тарельчатым клапаном; 4 - чугунный фасонный газоотвод;
- футеровка стояка;6 - отверстие для форсунки.
Из холодильника коксовый газ отсасывается по газопроводу 6 на гиетателем 7 и подается под избыточным давлением 2000-3000 мм вод ст. в электрофильтр 9 в котором выделяется примерно 98% содержг щейся в нем туманообразной смолы. Очищенный от смолы газ на правляется по газопроводу 10 в аппаратуру для улавливания химических продуктов (в сульфатное отделение по традиционной схеме).
В механизированном осветлителе 11 жидкая фаза поступающая и газосборника разделяется путем отстаивания на три слоя:
- верхний слой - надсмольная аммиачная вода плотностью 1010-1020 кгм3 (при 20°С);
—средний слой - каменноугольная смола гшотностью 1170 кгм3
—нижний слой - фусы плотностью 1250 кгм3.
Надсмольная аммиачная вода стекает из верхней части мехосветлителя 11 в промежуточный сборник 12 из которого вновь подается центробежным насосом 13 в газосборник 1 для охлаждения коксового газа.
Таким образом замыкается цикл надсмольной аммиачной воды: газо сборник - сепаратор - механизированный осветлитель - промежуточный сборник - центробежный насос - газосборник. Каменноугольна5 смола содержащая около 2% воды из механизированного осветлителя поступает самотеком в промежуточный сборник 14 из которого насосом 15 подается в резервуары-хранилища где происходит дальнейше отстаивание ее от воды. Обезвоженная таким образом смола передает ся в смолоперерабатывающий цех или потребителям. Фусы из механизированного осветлителя удаляются скребковым конвейером в бункер. из которого периодически выгружаются на платформу и передаются наутилизацию в цех подготовки угольной шихты.
Надсмольная аммиачная вода из холодильника непосредственного действия 4 стекает вместе со смолой через гидрозатвор 21 в отстойный резервуар 17. В этот же резервуар подастся насосом 19 конденсат стекающий из газопроводов нагнетателей и электрофильтров в промежуточный сборник 18.
Отстоявшаяся от воды смола из нижней части резервуара 17 поступает в промежуточный сборник 20 из которого насосом 15 подается в резервуары-хранилища а затем в смолоперерабатывающий цех. Надсмольная аммиачная вода из отстойника 17 перетекает в резервуар 22 из которого центробежным насосом 23 подается в оросительный холодильник 5. Наружная поверхность чугунных радиаторов холодильника орошается технической водой при температуре 20-25 °С. В результате теплообмена надсмольная аммиачная вода охлаждается от 70 до 25- 30ЭС и поступает в холодильник непосредственного действия 4 для охлаждения коксового газа. Таким образом замыкается цикл надсмольной аммиачной воды: газовый холодильник - отстойник - центробежный насос - оросительный холодильник - газовый холодильник.
Часть аммиачной воды из этого цикла соответствующая количеству испаряющейся в газосборнике надсмольной воды перетекает из сборника 22 в промежуточный сборник 12 для поддержания баланса воды в цикле газосборника.
Избыточное количество надсмольной аммиачной воды получающееся в результат е испарения влаги шихты и образования пирогенетической влаги при коксовании перетекает из резервуара 22 в сборник 24 из которого подается центробежным насосом 25 в сульфатное отделение для получения пароаммиачной смеси в аммиачно-известковой колонне [11].
3.2. Схемы первичного охлаждения коксового газа в трубчатых холодильниках
На рис. 2.3.2.1 представлена технологическая схема охлаждения коксового газа в холодильниках с вертикальными трубами. После охлаждения в газосборниках до 80-85°С коксовый газ поступает через сепаратор 2 в межтрубное пространство холодильников 3 с вертикальными трубами по которым движется противотоком техническая вода с начальной температурой 20-25°С. В результ ате теплообмена с водой через стенки труб газ охлаждается до 30-350С и происходит конденсация паров воды и смолы.
Рис. 2.3.2.1. Схема первичного охлаждения коксового газа в холодильниках с вертикальным расположением труб:
I - газосборник; 2 - сепаратор; 3 – первичный трубчатый холодильник;
19- гидравлический затвор; 5 - промежуточный сборник конденсата;
- механизированный осветлитель; 7 - промежуточный сборник;
13 I 5 16 - насосы; 9 - регулятор уровня смолы; 10 - промсборник для смолы; 11 - сборник для смолы; 12 - отстойник для воды; 14 - сборник для избыточной воды; 17 - нагнетатель; 18 - электрофильтр; 20 - трубопровод технической воды.
Рис. 2.3.2.2. Газовый холодильник с вертикальным расположением труб:
- корпус холодильника; 2 - решетки трубные; 3 - трубы теплообменные;
- перегородки; 5 - днище; 6 - вход газа; 7 - выход газа; 8 -- вход воды;
- выход конденсата и подвод пара; 11 - воздушник для пропарок.
Охлажденный газ подается нагнетателем 17 через электрофильтр 18 в сульфатное отделение а конденсат из газовых холодильников стекает через гидрозатвор 4 в промежуточный сборник 5 из которого насосом 13 подается в отстойник 12. Процессы разделения надсмольной воды смолы и фусов из газосборников осуществляются так же как и по рассмотренной выше схеме охлаждения газа в холодильниках непосредственного действия (рис. 2.3.1.1.).
Из отстойника 12 смола поступает через смолоотводник в смоляной сборник 11 из которого насосом 15 откачивается в резервуары склада смолы. Надсмольная вода из отстойника 12 поступаетв сборник 14 из которого часть ее перетекает в промежуточный сборник 7 для пополнения газосборникового цикла а избыток подается насосом 16 для переработки в известково-аммиачную дистилляционную колонну.
При обследовании работы холодильников с вертикальными трубами было установлено что в последней по ходу воды секции возникает рециркуляционный поток в результате чего снижается интенсивность теплоотдачи и увеличивается количество отложений на внутренней поверхности труб из-за перегрева воды. Для устранения этого явления последняя по ходу воды секция была разделена с помощью перегородки на нисходящий и восходящий ходы с отводом воды из холодильника через верхний штуцер. Это усовершенствование позволило уменьшить отложения солей жесткости в трубах и повысить эффективность охлаждения газа.
Как отмечалось выше недостатками газовых холодильников с вертикальными трубами являются низкий коэффициент теплопередачи (50- 90 втм2 К) из-за малой скорости воды в трубах и интенсивного отложения смолистых веществ и нафталина в межтрубном пространстве последних по ходу газа секций и большая производственная площадь занимаемая ими. К достоинствам этих холодильников следует отнести пониженные требования к качеству технической охлаждающей воды.
Схема охлаждения коксового газа в холодильниках с горизонтальными трубами (рис. 2.3.2.3.) принципиально не отличается от предыдущей. Следует лишь отметить что для более полной очистки смолы от фусов по этой схеме предусмотрена установка механизированного хранилища 6 в которое поступает тяжелая смола из механизированного осветлителя 3 и легкая смола из отстойника 16. Очищенная от фусов смола из хранилища 6 подается насосом 19 в конечный газовый холодильник для извлечения нафталина из воды.
Охлажденный в газосборниках 1 до 80-85°С коксовый газ поступает через сепаратор 2 в межтрубное пространство холодильников 9 и движется сверху вниз омывая слегка наклоненные трубы закрепленные в боковых стенках холодильника служащих трубными решетками. По высоте холодильника трубы разделены на отдельные секции (ходы). Охлаждающая вода подается в нижнюю часть холодильника и движется вверх зигзагообразно через все пучки соединенные последовательно с помощью водяных камер.
При тем пературе охлаждающей воды 20-25°С газ охлаждается до 25- 35°С после чего очищается от туманообразной смолы в электрофильтре 10 и подается нагнетателем 11 в сульфатное отделение.
Рис. 2.3.2.3. Схема первичного охлаждения коксового газа в холодильниках с горизонтальным расположением труб:
- газосборник; 2 - сепаратор; 3 - механизированный осветлитель;
- заглубленный промежуточный сборник для смолы; 6 - механизированное хранилище для смолы; 7 - промежуточный сборник для воды; 9 - трубчатые газовые холодильники; 10 - электрофильтры; 11-нагнетатели;
14 - гидрозатворы; 13 - промежуточный сборник для конденсата; 16 отстойник ДЛЯ конденсата; 17 - хранилище для избыточной воды;
Рис. 2.3.2.4. Газовый холодильник с горизонтальным расположением труб:
- трубная решетка; 2 - трубы; 3 - крышка водяной камеры; 4 - прокладка;
- ребра жесткости; 6 - анкерные стяжки; 7 - вход газа; 8 - выход газа;
- вход воды; 10 - выход воды; 12 - люк обслуживающий.
Конденсат из холодильника 9 электрофильтра 10 и нагнетателя 11 поступает через гидрозатворы в сборник 13 откуда подается насосом 15 в отстойник 16. Смола из отстойника поступает в механизированное хранилище 6 а надсмольная вода - в промежуточный сборник 7 для пополнения газосборникового цикла. Избыток надсмольной воды стекает в хранилище 17 откуда передается насосом 18 на переработку в аммиачное отделение.
При разделении водных циклов газосборников и холодильников в первом с течением времени происходит накопление нелетучих солей аммония - хлоридов и роданидов которые вызывают коррозию газосборников трубопроводов и аппаратуры отделения конденсации. Из-за увеличения плотности надсмольной воды ухудшается ее отстаивание от смолы и фусов. При этом происходит увеличение содержания этих солей также в смоле что способствует коррозии аппаратуры в смолоперегонном цехе. Для поддержания концентрации хлористых и роданистых солей аммония в воде цикла газосборников не более 2-6 г л часть ее отводится из промежуточного сборника 7 в отстойник газового конденсата 16 а соответствующее количество газового конденсата перетекает из отстойника 16 в сборник 7.
Следует отметить также что газовый конденсат образующийся в холодильниках с горизонтальными трубами содержит больше летучих солей аммония чем конденсат из холодильников с вертикальными трубами. Это объясняется большим временем пребывания конденсата в Холодильниках с горизонтальными трубами и меньшей температурой его на выходе. По практическим данным в надсмольной воде холодильников с горизонтальными трубами содержится (в гл) аммиака 8-12 сероводорода 2-4 диоксида углерода 3-4 а в надсмольной воде холодильников с вертикальными трубами соответственно 4.4-515-2 и 20.
Практика показала что применение газовых холодильников констру-кции Гипрококса с горизонтальным расположением труб обеспечивает более эффективное охлаждение газа облегчает работу нагнетателей и последующей аппаратуры цеха улавливания. По сравнению с холодильниками с вертикальным расположением труб они имеют следующие преимущества:
—охлаждающая вода движется в трубах под напором создаваемым насосом что позволяет увеличить ее скорость до 08-10 мс уменьшить благодаря этому отложение в трубах взвешенных частип и накипи интенсифицировать теплоотдачу от труб к воде;
—нисходящий поток конденсата смывает с наружной поверхности труб отложения нафталина и смолистых веществ благодаря чему замедляется рост гидравлического сопротивления межтрубного пространства и улучшаются условия теплопередачи от газа к воде;
—наличие самостоятельных трубных секций позволяет разделить поверхность теплообмена на отдельные зоны с различными хладагентами что позволяет использовать тепло коксового газа для нагревания поглотительного раствора в регенераторах и для других целей.
К недостаткам холодильников с горизонтальными трубами следует отнести недоступность теплообменных труб для осмотра очистки и ремонта из-за сложности снятия крышек водамых камер и большой высоты холодильников а также жесткие требования к качеству технической воды [12].
3.3. Схема двухступенчатого охлаждения коксового газа в аппаратах воздушного охлаждения и трубчатых холодильниках
Проведение процесса охлаждения коксового газа в две ступени имеет целью осуществлять раздельный отбор газового конденсата из каждой ступени и рациональную переработку его в зависимости от состава. Конденсат первой ступени содержит больше связанных солей аммиака и поэтому его целесообразно направлять на пополнение газосбор- никового цикла а конденсат второй ступени с большим содержанием летучего аммиака - на переработку в аммиачную колонну.
Применение аппаратов воздушного охлаждения позволяет сократить количество оборотной технической воды и следовательно снизить затраты на строительство и эксплуатацию хозяйства водоснабжения.
Аппараты воздушного охлаждения потребляют меньше электроэнергии требуют меньше производственных площадей чем при охлаждении технической водой поэтому они нашли широкое распространение в химической нефтехимической и газовой отраслях промышленности.
На рис. 2.3.3.1. представлена схема охлаждения коксового газа в аппаратах воздушного охлаждения и холодильниках с горизонтальными трубами внедренная на одном их коксохимических заводов СНГ. После охлаждения в газосборниках 1 как было описано в предыдущих схемах коксовый газ поступает через сепаратор 2 в аппараты воздушного охлаждения 4 типа АВОГ-1 изготовленные Таллиннским машиностроительным заводом по проекту ВНИИнефтемаша.
Аппарат состоит из шести секций с шатровым расположением их. Каждая секция состоит из восьми рядов оребренных труб развальцованных в двух трубных решетках. Газ поступает параллельно во все секции и движется по трубному пространству сверху вниз. При этом происходит охлаждение газа и конденсация из него паров воды смолы и нафталина. Движение газа и конденсата происходит прямотоком благодаря чему внутренняя поверхность труб непрерывно очищается от нафталина и обеспечивается длительная эффективная работа без про парок.
Рнс. 2.3.3.1. Схема двухступенчатого охлаждения газа в АВОГ и ТГХ:
- газосборник; 2 - сепаратор; 3 - осветлитель; 4 - АВОГ; 5 - ТГХ; 6 - электрофильтр; 7 - нагнетатель; 8 - градирня; 9- конденсатоотводчик; 10 - сборник надсмольной воды; 1113 - заглубленный промежуточный сборник; 12 14 15 19. 20 - насосы; 16 - сборник смоло-водяной эмульсии;
- осветлитель конденсата; 18 - смолоотводчик.
При охлаждении коксового газа от 80-85°С до 62-67°С в аппаратах воздушного охлаждения отводится 75-80% тепла и соответственно снижается расход технической воды в трубчатых холодильниках. Пропускная способность одного аппарата составляет 16000 нм7час скорость газа в трубах 10-13 мс коэффициент теплопередачи 25-30 втм2к гидравлическое сопротивление 500-1000 Па расход воздуха 735000 м3час.
В зимний период при температуре наружного воздуха минус 25°С и ниже аппарат работает с отключенным вентилятором и охлаждение газа осуществляется за счет естественной конвекции воздуха. При этих условиях нижние части труб забиваются отложениями нафталина для у даления которых требуются пропарки аппарата.
При пониженной температуре коксового газа на входе в трубчатые холодильники 5 второй ступени снижается накипеобразование в трубах что благоприятно сказывается на работе холодильников однако межтрубное пространство быстро забивается отложениями нафталина и смолистых веществ из-за недостаточного количества стекающего конденсата. При этом уменьшается коэффициент теплопередачи и растет гидравлическое сопротивление холодильников. Для удаления отложений газовое пространство холодильников промывается водно- смоляной эмульсией получаемой смешением газового конденсата (65- 70%) со смолой (30-35%) из механизированных осветлителей 17 в сборнике эмульсии 16. Эмульсия подается насосом 19 в две верхние секции холодильников 5 и выводится вместе с конденсатом через гидрозатвор 9 в сборник 11. Этот способ промывки трубчатых холодильников стабилизирует работу аппаратов но не исключает остановки их для пропарки через каждые 25-30 дней После трубчатых холодильников 5 содержание туманообразной смолы в коксовом газе составляет 2-5 гм3 а после электрофильтров 6 оно снижается до 03-05 гм3.
Расположение электрофильтров перед нагнетателям и 7 предпочтйтельнее так как при работе под разрежением поступление влажного газа в изоляторные коробки и возможность их пробоя снижаются. В электрофильтрах осаждается не только смоляной туман но и уносимые из холодильников капли смолы и кристаллы нафталина. Последний при установке электрофильтров после нагнетателей переходит в парообразное состояние из-за нагревания газа при сжатии и поступает с ним в последующую аппаратуру цеха улавливания.
Тяжелая смола выделившаяся из газа в газосборнике стекает из механизированного осветлителя 3 через регулятор уровня 18 в заглубленный сборник 13 из которого поступает в сборник 16 для приготовления водно-смоляной эмульсии.
Газовый конденсат из аппарата воздушного охлаждения (первая ступень охлаждения) стекает в осветлитель 17 а из трубчатых холодильников 5 электрофильтров 6 и нагнетателей 7 - в отстойник 11. Надсмольная вода из осветлителей 3 и 17 стекает в сборник 10 из которого насосом 14 подается на орошение газосборников 1 а избыток ее подается насосом 20 на переработку в сульфатное отделение.
Рис. 2.3.3.2. Схема двухступенчатого охлаждения коксового газа в АВО и скрубберах Вентурн:
- газосборник; 2 - сепаратор; 3 - осветлитель; 4 - сборник надсмольной воды; 5 19 21 — насосы; 6 - АВО; 7 - сборник смолы; 8 - сборник водно-смоляной эмульсии; 10 - скруббер Вентури: 11 - газоподводящая труба;
- конфузор; 13 - горловина; 14-диффузор; 15- брызгоуловитель;
-оросительное устройство: 17 - центробежный скруббер; 18 - спиральный теплообменник; 20 - градирня с принудительным дутьем;
Рис. 2.3.3.3. Скруббер Вентурн:
I - вход газа; 2 - конфузор; 3 - горловина; 4 - диффузор;
- сборник- брызгоуловитель;6 - выход газа; 7 - устройство оросительное.
Надсмольная аммиачная вода и смола из отстойника 15 поступает в сборники 478 откуда смола подается насосом 21 в смолоперерабаты- ваюший цех а избыточная вода поступает на переработку в сульфатное отделение.
Необходимая для охлаждения коксового газа в скруббере Вентури 10 надсмольная вода подается насосом из брызгоуловителя 15 через спиральный теплообменник 18 те охлаждается технической водой с градирни 20.
Производительность скруббера Вентури по газу составляет 40000 нм3час расход охлаждающей воды 250 м3час суммарное гидравлическое сопротивление двух аппаратов 1000-1500 Па коэффициент теплопередачи отнесенный к общему объему конфузора горловины и диффузора 70000-230000 втм3к.
В таблице 2.1 приведена сравнительная характеристика затрат в относительных единицах при различных вариантах первичного охлаждения коксового газа и очистки его от аэрозолей смолы по данным ВУ- ХИНа. В качестве базового варианта для сравнения принята типовая схема отделения конденсации с охлаждением газа в трубчатых холодильниках с очисткой от смолы в электрофильтрах.
Таблица 2.3.3.1. Сравнительные затраты для различных вариантов схем первичного охлаждения коксового газа
Варианты схем охлаждения и очистки газа от смолы
ХГТ с электрофи- льтром
АВОГ-1 и скруббер Вентури
Приведенные данные свидетельствуют об экономической эффективности применения разработанных схем двухступенчатого охлаждения коксового газа. При этом наиболее благоприятными прогнозными показателями характеризуются схемы охлаждения газа с применением воздушного охлаждения и скрубберов Вентури [13].
3.4. Схема охлаждения коксового газа в двухступенчатых безнасадочных аппаратах
Недостатком насадочных холодильников непосредственного действия является образование отложений смолистых веществ и нафталина на насадке что вызывает рост гидравлического сопротивления снижает эффективность процесса и требует периодических чисток аппаратов. Этого недостатка практически лишены полые аппараты распьливающего типа в которых необходимая поверхность теплопередачи создается путем разбрызгивания большого количества воды с помощью форсунок. В таких аппаратах эффективность теплообмена в нижней части снижается из-за коалесценции капель и соответствующего уменьшения поверхности контакта фаз.
С целью интенсификации работы распыливающих аппаратов их выполняют двухступенчатым и для чего в средней части устанавливается тарелка пропускающая газ из нижней часта в верхнюю а жидкость собирающаяся на тарелке подается насосом через форсунки в нижнюю часть. Благодаря этому а также противоточному движению фаз в таком аппарате обеспечивается достаточно высокая интенсивность и степень теплообмена. Недостатком таких аппаратов является большой расход электроэнергии на циркуляцию и распиливание воды.
Схема охлаждения газа в безнасадочиы.х аппаратах приведена на рис. 2.3.4.1. Коксовый газ поступает параллельными потоками в нижнюю часть безнасадочных холодильников 1 при температуре 80-85°С где охлаждается надсмольной водой до 30-3 5°С и отводится сверху в последующую аппаратуру.
Охлаждающая вода подается в холодильники 1 сверху через распы-лительные устройства и движется противопотоком к газу вниз собирается на разделительных тарелках откуда насосами 2 подается через форсунки в 1шжнюю часть холодильников. Нагретая до 68-72°С охлаждающая вода стекает вместе с газовым конденсатом через гидравлические затворы в механизированные осветлители 3 где происходит разделение фаз по плотности.
Надсмольная вода поступает через промежуточный сборник (на схеме не показан) на всас насоса 4 и вновь подается через спиральные теплообменники 5. где охлаждается от 70 до 25-30°С на орошение холодильников I. Техническая вода подается в теплообменники насосом 6 из градирни 7. Избыток надсмольной воды отводится после насоса 4 В аммиачную установку на переработку. Смола из осветлителя 3 стекает через регулятор уровня в промежуточный сборник откуда подаете) насосом па склад и переработку Удельная поверхность теплообмена оставляет 40-60 м2 на 1ООО м3час газа расход циркулирующей надсмольной воды 10-13 м3 атехнической воды 24-32 м3 на 1000 м3 газа [14].
Рис. 2.3.4.1. Схема охлаждения коксового газа в двухступенчатых безнасадочных аппаратах:
- безнасадочный двухступенчатый холодильник; 2 4 - циркуляционные насосы; 3 - осветители; 5 -теплообменники; б - насос оборотной воды;
2.1.doc
1. Физические основы процесса и аппаратура
В теплообменных аппаратах контактного типа к которым относятся газосборники теплообмен между газом и водой сопровождается массообменом что усложняет механизм и закономерности протекания процессов. Снижение температуры газа при контакте с охлаждающей водой сопровождается изменением его влагосодержания вследствие испарения воды или конденсации водяных паров из газа. Направление переноса влаги при контактном теплообмене зависит от соотношения между температурой воды и температурой точки росы газа.
Если тем пература воды ниже температуры точки росы то охлаждение газа сопровождается конденсацией паров и соответствующим нагревом жидкости. Если же температура воды больше температуры точки росы то газ при охлаждении увлажняется а вода нагревается и частично испаряется. При достаточном времени контактирования газа с жидкостью движущихся прямотоком температуры их стремятся к равновесному значению соответствующему температуре мокрого термометра а относительная влажность газа стремится к единице. При температуре охлаждающей воды равной температуре мокрого термометра газ охлаждается только за счет испарения воды а температура последней остается неизменной.
Параметры газа и жидкости изменяются по длине контактного теплообменника. при этом в различных сечениях аппарата могут создаваться различные условия взаимодействия фаз. В условиях действующих коксохимических заводов температура воды подаваемой на орошение газосборника существенно выше температуры точки росы газа на выходе из печей. При влажности шихты 8-10% температура точки росы газа составляет 68-70°С
с1.doc
1.Продукты коксования и их применение . .. 11
2.Основные процессы технологии улавливания химических продуктов коксования . .. 17
3.Транспортирование газа через аппаратуру цеха улавливания . .21
4.Сырьевая база коксования ..26
5.Размещение и масштабы коксохимических предприятий 30
6.Генеральный план коксохимического завода .. .32
7.Оптимизация схемы улавливания химических продуктов коксования 34
Первичное охлаждение коксового газа . 40
1.Физические основы процесса и аппаратура . .40
2.Очистка надсмольной воды от фусов и смолы . 46
3.Технологические схемы первичного охлаждения коксового газа 49
3.1.Схема первичного охлаждения коксового газа
в холодильниках непосредственного действия . .50
3.2.Схемы первичного охлаждения коксового газа
в трубчатых холодильниках . 56
3.3.Схема двухступенчатого охлаждения коксового газа
в аппаратах воздушного охлаждения и трубчатыххолодильников .. 63
3.4. Схема охлаждения коксового газа в двухступенчатых
безнасадочных аппаратах .. 72
с2.doc
1. Исходные данные . .75
2. Выбор конструкционного материала и допускаемые напряжения 77
3. Расчет толщины стенки корпуса аппарата . ..77
4. Расчет массы аппарата 78
5. Расчет колонны на ветровую нагрузку .79
6. Расчет аппарата на сейсмическую нагрузку .. ..81
7. Расчет опоры аппарата 82
8 Прочностной расчет 85
8.1. Расчет толщины цилиндрической обечайки .. 85
8.2. Расчет толщины днища и крышки ..85
8.3. Расчет и выбор опор аппарата .. ..86
8.4. Расчет на прочность фланцевого соединения .. .87
1. Характеристика негативных факторов проектируемого объекта ..89
2. Оценка пожаровзрывоопасности проектируемого объекта . ..92
3 Профилактические мероприятия по охране труда 93
3.1. Средства защиты органов дыхания Патрон к респиратору РПГ-67 93
3.2. Респиратор РПГ-67 .. 93
3.3. Респиратор РУ-60 94
3.4. Коробка Противогазная (А В КД БКФ) .. 94
3.5. Малого габарита . .95
Антикоррозионная зашита 96
1. Особенности работы конденсационно-холодильного оборудования. Агрессивность оборотных вод . 96
2. Коррозия под действием сточных вод 110
Ремонт оборудования ..120
2. Зубчатые колеса .122
3. Центробежные насосы .124
4. Ремонт химической аппаратуры .130
Список литературы ..134
л2.doc
Литвиненко М.С. Очистка коксового газа от сероводорода. - М.: Металлургиздат 1959.-308 с.
Коуль А.Л. Ризеифельд Ф.С. Очистка газа. - М.: Недра 1968. - 392 с.
Сосуды и трубопроводы высокого давления: Справочник Е.Р. Хисматулин Е.М. Королев В.И. Лившиц и др. – М.: Машиностроение 1990. – 384 с.
Миронов В.П. Фрякин Н.В. Расчет сосудов. Учебное пособие. Иваново. ИХТИ 1981. – 94 с.
А.А. Лащинский А.Р. Толчинский Основы конструирования и расчета химической аппаратуры. Л.: Машиностроение.- 1970
Дытнерский Ю.И. Основные процессы и аппараты химической технологии: Пособие по проектированию. –М.: Химия 1991.- 496 с.
Вихман Г.Л. Круглов С.А. Основы конструирования аппаратов и машин нефтехимических заводов - М.: 1977.-327
.Шицкова А. П. Новиков Ю. В. Гурвич Л. С. Климкина Н. В. Охрана окружающей среды в нефтеперерабатывающей промышленности. М.: Химии 1980. 84 с.
Корразия и защита химической аппаратуры. Т. ЗПод ред. А. М. Сухо тина. Л.: Химия 1970 130 с.
Рейзин Б. Л. Стрижевский И. В. Шевелев Р. А. Коррозия и защита коммунальных водопроводов. М.: Стройиздат. 1979. 398 с.
Отраслевые методические указания по комплексной защите металла конденсационно-холодильного оборудования коммуникаций и градирек от коррозионного воздействия со стороны оборотной воды снижения солеотложений и биообрастаний. М.: МНХП СССР 1985. 140 с.
Юхневич Р. Валашковский Е. Видуховский А. Станкевич Г. Техника борьбы с коррозией. Л.: Химия 1978. 304 с.
Коррозия и защита химической аппаратуры. Т. 9Под ред. А. М. Сухотина А. В. Шрейдера Ю. И. Арчакова. Л.: Химия 1974. 576 с.
Клячко В. А. Апельцин И. Э. Очистка природных вод. М.: Химия 1971. 579 с.
Коррозионная стойкость оборудования химических производств. Коррозия под действием теплоносителей хладагентов и рабочих тел: Справ. изд.А. М. Сухотин А. Ф. Богачев В. Г. Пальмский и др.; Под ред. А. М. Сухотина В. М. Беренблит. Л.: Химия 1988. 360 с.
Розенфельд И. Л. Ингибиторы коррозии. М.: Химия 1977. 350 с.
Поруцкий Г. В. Строменко А. Е. Макаров И. А. и др.Эксплуатация модернизация и ремонт оборудования. М.: ЦНИИТЭНефтехим. 1972. № 5. С. 16—20.
Негреев В. Ф. Фархадов А. А. Абрамов Н. М. Алекперова А. Ю. Коррозия стали в охлаждающих системах и методы защиты. Баку: Азернешр. 1971. 146 с.
Метсик Р. Э. Кальберг А. О.Коррозия и защита в нефтегазовой промышленности. М.: ВНИИОЭНГ. 1979. Вып. 2. С. 3—5.
Шпарбер И. С. Защита от коррозии конденсационно-холодильного оборудования на зарубежных нефтезаводах. М.: ЦНИИТЭНефтехим.1969.76 с.
Гоник А. А. Коррозия нефтепромыслового оборудования и меры ее предупреждения. М.: Недра 1976. 192 с.
Wormwell NurseJ. Appl. Chem. 1952. V. 2. P. 685—692.
Apostolashe S.Rev. corroz. 1972. V. 2 1. P. 22—24.
Тодт Ф. Коррозия и защита от коррозии. Л.: Химия 1967. 710 с.
Строкан Б. В.Коррозия и защита от коррозии. Сер. Итоги науки и техники. 1976. Т. 5. С. 133—161.
Колотыркин Я. М. Пахомов В. С. Паршин А. Г. Усховский А. В.Хим. и нефт. машиностроение. 1980. № 12. С. 20—22.
Андреюк Е. И. Козлова И. А. Литотрофные бактерии и микробиологическая коррозия. Киев: Наукова думка 1977. 162 с.
Разумов А. С. Биологические обрастания и меры борьбы с ними. М.: Наука 1964. 130 с.
Долгополъская М. А.Биологические основы борьбы с биообрастаниями. Киев: Наукова думка 1973. 280 с.
Badiu 2. Constantinescu S. Petrovici P.Luvcar inst. cerc. proect alim. 1970. V. 10. P. 311—321.
Kobrin G.Hydrocarbon Process. 1976. V. 55 8. P 148
Chanterean J.Trlb. CEBEDEAU. 1978. V. 31 417—418. P. 311—315.
Стрижевский И. Б. Некоторые аспекты борьбы с микробиологической коррозией нефтепромыслового оборудования и трубопроводов. М.: ВНИИОЭНГ 1979. 56 с.
Bernard D. . . Haim .6th Eur. Sump. Corrosion Inhibitors. Ferrara 16th —20th Sept. 1985. Proc. V. 2. P. 1465—1481.
Орехов А. И. и др.Эксплуатация модернизация и ремонт оборудования. М.: ЦНИИТЭНефтехим. 1972. № 4. С. 12—14.
Puskorins P. R. Chem. Eng. 1978. V. 85 10. . 171—172 174.
Орехов А. И.Эксплуатация модернизация и ремонт оборудования. М.: ЦНИИТЭНефтехим. 1974. № 1. С. 9—11.
Абдулаев А. Я.Коррозия и защита в нефтегазовой пром. М.: ВНИИОЭНГ 1980. № 1.С. 14—16
Коррозия и зашита химической аппаратуры. Т. 1. Иодобромная промышленность. Производство фтористого водорода солеи и пергидроля: Справ. рукоподствоПод ред. А. М. Сухотина. Л.: Химия 1969. 494 с.
Надежоин Д. С. Гладкий И. Н.. Чмырев Ю. П. Науменко Л. Я.С6. научи тр. У кр НИ И Саль. 1962. Вып. 6 (14).
Падеждии Д. С. Гладкий И. Я.Там же. 1964. Вып. 7 (15) С. 116— 120.
Лупаков И. С. Захаров Ю- В.'Теп.юэнергетика. 196-1 № 6. С. 40.
л1.doc
Белов К.А. Улавливание химических продуктов коксования. - Харьков: М.:Метал лургиздат 1948. -308 с.
Коляндр Л.Я. Улавливание и переработка химических продуктов коксования. - М : Металлургиздат 1962. - 468 с.
Технология коксохимического производства Лейбович Р.Е. Обухопский Я.М. Са- тановский С.Я. Кутовой П.М. - М.: Металлургия 1974. - 421 с.
Технология коксохимического производства.Лейбович Р.Е. Яковлева Е.И. Филатов А.Б. - М.: Металлургия 1982. - 360 с.
Мениович Б.И. Лейбович Р.Е. Аппаратчик коксохимического производства. - М : Металлургия 1987. - 408 с.
Руководство по коксованию. Под ред. О.Гросскинского. Т. П. - М.: Металлургия 1966.-608 с.
Справочник коксохимика. Под ред. А.К.Шелкова. - Т. Ш. - М.: Металлургия. 1966-391 с.
Лазорин С.Н. Стеценко Е.Я. Производство сульфата аммония на коксохимических заводах. - М.: Металлургия 1965. - 158 с.
Петренко Д.С. Производство пиридиновых оснований на коксохимических заводах.-Харьков-М.: Металлургиздат 1961. - 176 с. илл.
Лазорин С.Н. Стеценко Е.Я. Производство сырого бензола - Киев: Техшка 1969. - 224 с.
Гринберг A.M. Обесфеноливание сточных вод коксохимических заводов. - М.: Металлургия 1968. - 212 с.
в2.doc
Дальнейшее совершенствование технологии привело к разработке ульевых печей с плоским подом и полусферическим сводом рабочее пространство которых было полностью закрытым. Загрузка угля в печи производилась через отверстия в своде а выгрузка кокса сбоку на площадку для тушения. Нагревание угля производилось за счет тепла сгорания летучих продуктов коксования. Благодаря меньшему загрязнению атмосферы и возможности механизации трудоемких операций эти печи получили широкое распространение в Европе и в США в середине XIX в.
Общим недостатком стойловых и ульевых печей была низкая скорость нагревания из-за большой толщины угольной загрузки. Время коксования угля достигало нескольких суток. Необходимость ускорения процесса обусловила переход к коксованию угля в узких камерах значительной длины и высоты. Начиная с середины XIX в. в коксовом производстве начали применять печи с горизонтальными камерами расширяющимися в сторону вьирузки кокса. Объединение отдельных печей в батареи позволило уменьшить размеры установок при данной производительности снизить потери тепла механизировать трудоемкие операции.
Важным шагом в развитии коксового производства стало освоение коксовых печей с улавливанием химических продуктов и использованием тепла дымовых газов что обеспечило резкое улучшение экологических и экономических показателей. Первые такие печи появились в начале 80-х годов XIX в. во Франции и Германии.
Зарождение и развитие отечественного коксового производства тесно связано с Донецким угольным бассейном. В 1871-1872 гг. англичанин Дж. Юз построил металлургический завод и 12 стойловых печей для выжига 1100 т кокса в месяц что сыграло существенную роль в становлении современного Донецка. В 1872-1873 гг. в Донбассе имелось 45-50 стойловых печей при 9 рудниках. Разовая загрузка печи составляла 4 т период коксования - 7 суток. В 80-х годах началось строительство коксовых печей с узкими камерами без улавливания химических продуктов. Началом развития коксохимической промышленности в России принято считать 1889 г. когда на Щербиновском руднике в Донбассе были построены 40 коксовых печей и завод для улавливания и переработки продуктов коксования.
Рост производства кокса в дореволюционной России характеризуется следующими данными:
годы .. 1890 1895 1900 1905 1913
производство кокса тыс. т 296 520 2200 2367 4440
Для сравнения объем производства кокса в 1913 г. в США составил 42 в Германии 346 в Англии 13 млн. т. Из этих данных видно что коксохимическое производство дореволюционной России было крайне от сталым как по объему продукции так и по техническому уровню.
За годы советской власти в СССР были построены десятки современных коксохимических предприятий большой мощности. Начиная с 1960 г. по объему производства кокса СССР вышел на первое место в мире причем более 75% его производилось на крупных заводах мощностью более 3 млн. т. в год. Значительная часть мощностей по производству кокса в этот период была размещена в Украине и в частности в Донбассе.
После распада СССР производство кокса во всех бывших республиках стало резко сокращаться что видно из приведенных ниже данных (таблица 1) и объясняется разрывом традиционных производственных связей сокращением спроса на кокс и другие продукты коксования.
Таблица 1. Динамика изменения производства кокса в СНГ
Выполненные в Украине прогнозные разработки показали что производство чугуна будет сокращаться. Если в 1990 г. было выплавлено примерно 45 млн. т. то к 2005-2010 гг. его производство снизится до 33- 34 млн. т в год. Соответственно потребность кокса для металлургического производства уменьшится до 16 млн. т в год в сухой массе. Если даже потребность в коксе остальных потребителей (производство серы обжиг известняка сахарная промышленность литейное производство и др.) сохранится на нынешнем уровне то и в этом случае общая потребность хозяйственного комплекса Украины после 2000 г. снизится до 17 млн. т кокса.
Аналогичная обстановка сложилась и в других государствах содружест ва.
В таких условиях важнейшими задачами коксохимиков являются совершенствование техники и технологии коксования повышение глубины переработки химических продуктов расширение ассортимента продукции улучшение условий труда и экологической обстановки на предприятиях.
в1.doc
Первоначально потребность зарождавшегося металлургического производства в углеродном сырье удовлетворялась почти исключительно за счет древесного угля. Высокие качества последнего как металлургического топлива в особенности почти полное отсутствие минеральных примесей предопределили его применение в металлургических процессах в течение длительного времени. Однако интенсивный рост производства черных металлов в XVIII в. требовал все больше сырья что истощило ресурсы древесины в Англии и других странах развитой металлургии. Закон запрещавший вырубку лесов поставил пред промышленниками задачу использовать в доменной плавке другие виды сырья важнейшим из которых стал впоследствии каменноугольный кокс. Успешную выплавку чугуна на каменноугольном коксе удалось наладить уже в 1735 г. а в конце XVIII в. доменное производство Англии практически полностью перешло на кокс. Первая доменная печь на коксе во Франции была задута в 1785 г.
Технология коксового производства прошла сложный путь развития от коксования в кучах заимствованного из опыта получения древесного угля до современных коксовых печей. Первые попытки коксования угля в кучах относятся к XVI в. и просуществовало оно вплоть до середины XIX в. В кучи засыпали хорошо коксующийся уголь в крупных кусках а необходимое для процесса тепло получали за счет сгорания летучих продуктов коксования и части угля. По окончании коксования кучу разрушали и заливали кокс водой.
5.1.doc
1. Особенности работы конденсационно-холодильного оборудования. Агрессивность оборотных вод
На предприятиях нефтеперерабатывающей и нефтехимической промышленности широко используются системы оборотного водоснабжения. Расход воды в среднем по НПЗ составляет около 90 % общего водопотребления на технологические нужды [20]. В целом по предприятиям нефтеперерабатывающей и нефтехимической промышленности суточный расход оборотной воды превышает 40 млн. м. Металл оборудования и трубопроводов в результате взаимодействия с оборотной водой подвергается интенсивной коррозии солеотложению и биообрастанию.
Основными узлами систем оборотного водоснабжения являются охлаждаемое конденсационно-холодильное оборудование коммуникации сооружения мотоблоков в том числе градирни нефтеотделители камеры холодной и теплой воды насосное оборудование.
Большинство предприятий используют системы водоворота с постоянной продувкой и восполнением потерь воды на капельный унос испарение на градирнях забор воды на технологические нужды и продувку путем подпитки очищенными стоками 1 системы канализации.
Работа систем оборотного водоснабжения осуществляется при температуре воды в среднем 10—40 °С давлении до 05— 07 МПа и температуре охлаждаемых продуктов 45—350 °С.
Присутствующие в воде примеси вызывают процессы коррозии солеотложения и биообрастания металла что приводит к необходимости дополнительных ремонтов увеличению затрат на их проведение снижению качества товарной продукции энергетическим потерям.
В связи с ужесточением требований к охране окружающей среды запрещением сброса неочищенных сточных вод в естественные водоемы системы водоворота переводят на замкнутый цикл с ограниченной продувкой что вызывает рост солесодержания и коррозионной агрессивности вод.
Компонентный состав оборотных вод используемых предприятиями чрезвычайно неоднороден и зависит от источников
5.2.doc
В табл. 5.1.1 представлены обобщенные данные по компонентному составу оборотных вод используемых предприятиями нефтеперерабатывающей и нефтехимической промышленности. Состав оборотных вод классифицирован на три группы по общему солесодержанию. Общее солесо держание с переводом систем водооборотная на бес продувочный режим увеличивается.
—группа-—предприятия использующие оборотную воду с солесодержанием до 2000 мгл. К ней относится до 90 % всех нефтеперерабатывающих предприятии отрасли.
—группа—предприятия использующие оборотную воду с солесодержанием от 2000 до 8000 мгл. Повышенные концентрации солей определяются значительной засоленностью пресноводного источника водоснабжения или концентрированием солей вследствие длительного циркулировали воды при минимальной продувке. К этой группе относится около 8 % предприятий.
—группа (около 2 % предприятий) использует морскую оборотную воду.
Оборотные воды I группы имеют рН изменяющийся в более широком интервале чем для вод II и III групп что определяется большим набором разнообразных производств и
Таблица 5.1.1 Компонентный состав оборотных вод нефтеперерабатывающих и нефтехимических предприятий
* Дли предприятий использующих морскую воду.
кислотно-щелочных загрязнений. Максимальная концентрация сульфидов для оборотных вод 1 группы достигает 60 мгл а для оборотных вод II группы— 1 мгл. Эти существенные различия обусловлены использованием предприятиями 1 группы вод третьей системы оборотного водоснабжения с повышенным содержанием сульфидов. Наряду с увеличением значения общего солесодержания при переходе от оборотных вод I группы к III группе происходит также рост максимальных концентраций хлоридов и сульфатов.
Для всех трех групп предприятий загрязненность оборотных вод взвешенными веществами и нефтепродуктами многократно превосходит проектные нормативы загрязненности которые составляют до 25 мгл по этим компонентам. Это указывает на низкое качество очистки оборотных и пропиточных вод.
Коррозионная "агрессивность оборотных вод определяется следующими основными факторами: величиной рН концентрацией растворенного кислорода диоксида углерода хлоридов сульфатов сульфидов. Нефтепродукты карбонаты механические примеси а также биообрастания отлагаясь на поверхности охлаждаемой аппаратуры способствуют интенсивному развитию различных видов коррозии.
Значение рН является важным фактором влияющим на скорость коррозии в водных средах. В интервале значений рН 65—95 наиболее характерных для оборотных вод скорость коррозии сталей практически постоянна. Контролирующим фактором коррозии в этих условиях является диффузия растворенного кислорода к поверхности металла. При низких значениях рН скорость коррозии увеличивается вследствие водородной деполяризации металла при разряде ионов водорода. При рН > 10 скорость коррозии сталей незначительна [21].
При значениях рН оборотной воды 7 коррозия оборудования равномерна. Образующиеся продукты смываются с металла потоком воды. В интервале рН от 7 до 10 коррозия приобретает локальный характер. На отдельных участках поверхности металла при этом образуются осадки продуктов коррозии способные закупоривать трубки трубных пучков. рН оборотной воды — один из основных факторов определяющих возможность образования на металле карбонатной пленки [22]. Значение рН оборотной воды рекомендуется поддерживать в интервале 65—88 [23]. Нижний предел является оптимальным для применения ряда ингибиторов коррозии а верхний — назначается с учетом максимального естественного повышения рН воды в оборотной системе.
Растворенный кислород — один из наиболее агрессивных компонентов оборотных вод. Процесс взаимодействия кислорода с металлом в водной среде описывается уравнением: Me + 12nО2 +12nН2OМеОn + 12nН2O.
До концентрации 7 мгл скорость коррозии возрастает пропорционально концентрации растворенного кислорода [24].
В дальнейшем снижение скорости коррозии обусловлено пассивацией металла. В присутствии хлоридионов достижение пассивного состояния затруднено а в некоторых случаях даже невозможно.
При эксплуатации коиденсационно-холодильного оборудования постоянно имеет место ситуация когда скорость движения охлаждающей воды на различных участках поверхности металла неодинакова. Это определяет различия в поступлении кислорода и обусловливает функционирование на поверхности металла аэрационных пар приводящих к развитию наиболее опасной язвенной коррозии оборудования. Интенсивной коррозии при этом подвергаются участки с низкой скоростью движения воды. Образующиеся объемные отложения гидроксида железа препятствуют току воды и затрудняют работу оборудования и трубопроводов систем оборотного водоснабжения [21].
В тех случаях когда вода обладает способностью образовывать на поверхности оборудования защитную карбонатную пленку увеличение концентрации кислорода способствует торможению процесса коррозии и повышению защитных свойств пленки [22]. Это объясняется тем что в процессе электрохимической коррозии с кислородной деполяризацией при восстановлении кислорода накапливаются гидроксильные ионы
которые приводят к значительному увеличению рН воды у поверхности металла что стимулирует осаждение карбонатного осадка.
Диоксид углерода в оборотной воде может присутствовать в растворенном виде в форме моногидрата — угольной кислоты гидрокарбонатных и карбонатных ионов или в свободной форме. Растворенный в воде диоксид углерода несколько снижает рН способствуя увеличению ее коррозионной агрессивности.
Присутствующий в воде диоксид углерода дополнительно вызывает от 110 до 17 коррозионных потерь по сравнению с потерями от такого же количества
Следует отметить снижение растворимости газов с ростом концентрации солей в воде и увеличением температуры.
Из оборотной воды возможно осаждение на металле мало7 растворимого СаСОз- Плотвая пленка осадка защищает металл от коррозии но нарушает теплопередачу а при значительном количестве отложении препятствует току воды и усложняет эксплуатацию оборудования. Поэтому коррозионная агрессивность оборотной воды во многом определяется способностью к осаждению пленки карбоната кальция. Каждой определенной концентрации ионов НСОз в оборотной воде соответствует равновесная концентрация свободной СО2 [26]. Если концентрация свободной СО2 в воде выше раввовесной то избыток ее вступает в реакцию с карбонатом кальция
Т. е. происходит растворение карбонатной пленки. В случае когда концентрация свободной СО2 ниже равновесной реакция идет в противоположном направлении с образованием на стенках трубных пучков толстых карбонатных слоев уменьшающих пропускную способность трубок и ухудшающих теплообмен. При равновесной концентрации свободной СО2 вода является стабильной и не способна ни отлагать ни растворять карбонатную пленку.
Из существующих методов оценки способности воды образовывать карбонатные отложения используются расчеты показателей стабильности по методам Ланжелье Ризнера [222627] СНиП 2.04.02—84 и др. Поддержание стабильного состояния воды при эксплуатации систем оборотного водоснабжения чрезвычайно важно для успешной работы оборудования.
Сероводород в воду может поступать из барометрических конденсаторов через пропуски в конденсацнонно-холодильвом оборудовании из атмосферы а также в результате жизнедеятельности микроорганизмов при этом увеличивается скорость процессов восстановления растворенного кислорода и окисления металла что приводит к усилению коррозии углеродистых низколегированных
высоколегированных хромистых и хромо- никелевых сталей При концентрациях сероводорода до 2 мгл образующаяся в результате взаимодействия с углеродистой сталью сульфидная пленка обладает защитными свойствами которые теряются с ростом концентрации сероводорода [2829].
Структура сульфидной пленки на поверхности металла весьма существенно влияет на скорость коррозии сталей в воде. Сульфид железа но отношению к углеродистой стали является катодом и образует с ней гальваническую пару разность потенциалов между полюсами может достигать 02—03 В что способствует усилению коррозии сталей. Структура сульфидной пленки и ее свойства зависят от парциального содержания сероводорода. При концентрациях HaS до 2 мгл сульфидная пленка состоит главным образом из пирита и троилита. Диффузия катионов железа через эту пленку затруднена и скорость коррозии мала. По мере роста содержания H2S сульфидная пленка на поверхности металла обогащается канситом который не препятствует диффузии катионов железа и скорость коррозии увеличивается.
Высокая агрессивность сероводорода и сульфидов требует некоторых мер по снижению их концентраций в оборотных водах. В этой связи при реконструкции предприятий барометрические конденсаторы смешения должны заменять поверхностными а III систему водоснабжения характеризующуюся повышенными концентрациями сероводорода следует аннулировать.
Хлориды и сульфаты повышают коррозионную агрессивность оборотной воды. Адсорбируясь на поверхности металла они образуют соединения обладающие хорошей растворимостью что приводит к увеличению скорости коррозии сталей. Наиболее агрессивны хлор ид-ионы способные легко проникать через защитные поверхностные пленки металла. Скорость коррозии углеродистой стали в воде содержащей хлориды при температуре 80 °С
Рис. 5.1.1.Зависимость скорости коррозия стали Ст3 от концентрации хлорил-ионов в дистиллированной воде [30].
растет до 26 г(м2-ч) при увеличевии концентрации хлоридов до 180 мгл и далее она остается практически постоянной (рис.5.1.1). При температуре 40 °С скорость коррозии равномерно увеличивается до 2 г(м2-ч) при росте концентрации хлоридов примерно до 5500 мгл.
Скорость коррозии в зависимости от концентрации сульфат- ионов возрастает в интервале концентраций 50-—500 мгл и в дальнейшем существенно не изменяется [30] (рис. 5.1.2).
Хлориды и сульфаты стимулируют образование рыхлых пористых осадков продуктов коррозии слабо тормозящих
Рас. 5.1.2. Зависимость скораста коррозии стала СтЗ от концентрации сульфт-ионое в дистиллированной воде (температура 40 °С) [30].
коррозионный процесс и легко смываемых потоком воды. Продукты коррозии углеродистой стали утрачивают защитные свойства при концентрации хлоридов 75 мгл а защитное действие карбонатных пленок ухудшается при концентрации сульфат-ионов более 100 мгл [2227]. Хлориды и сульфаты в оборотной воде способствуют возникновению локализованных коррозионных поражений на поверхности стали.
Общее солесодержание является суммарной косвенной характеристикой коррозионной агрессивности. Так в пределах одной величины солесодержания в зависимости от концентраций составляющих минеральных солей возможно наличие вод различной степени агрессивности. В зависимости от количества солей кальция и магния воды разделяются на жесткие и мягкие. В мягких водах скорость коррозии максимальна в то время как в жестких из-за образования отложений карбонатов кальция и магния скорость коррозии незначительна. Однако в целом с ростом солесодержания воды при отсутствии на металле защитных пленок наблюдается увеличение скорости коррозии углеродистых и низколегированных сталей вследствие увеличения электрической проводимости среды влияния растворимых газов хлоридов и сульфатов. Максимум отвечает суммарному и наиболее агрессивному проявлению этих факторов и зависит от их взаимного сочетания. При содержании в охлаждающей воде до 100 мгл солей в большинстве случаев серьезных коррозионных проблем не возникает. Положение становится более сложным при концентрации солей до 2000 мгл и выше [25]. При этом усиленной коррозии подвержены не только углеродистые и низколегированные стали но и ряд более коррозионно-стойких материалов.
Органические вещества (нефтепродукты продукты органического синтеза гуминовые кислоты и др.) попадают в оборотные воды через дефекты соединений и сквозные коррозионные поражения металла технологического оборудования из почвы в результате жизнедеятельности микроорганизмов. Ряд органических веществ имеет кислый характер и снижает рН воды увеличивая при этом скорость коррозии. Присутствие в воде нефтепродуктов увеличивает
транспорт кислорода к поверхности металла [31]. Это обусловлено возникновением на границе раздела фаз нефтепродукт — иода сил межфазного натяжения способствующих турбулизации потока и усилению перемешивания воды. Скорость коррозии в результате этого увеличивается.
Механические примеси частицы песка продукты коррозии карбонатные отложения водоросли ил — при движении воды способны разрушать поверхностную пленку и усиливать разрушение металла в 2—3 раза [32]. При повышенных скоростях потоков для углеродистых сталей сталей марок 20X13 12Х18Н10Т чугуна СЧ21-40 и других материалов существуют предельные концентрации взвешенных веществ (150—600 мгл) при превышении которых стойкость металла в воде резко понижается [33].
При малых скоростях потоков механические примеси отлагающиеся на поверхности металла приводят к снижению эффективности работы конденсационно-холодильного оборудования вызывают закупоривание трубок пучков усиливают локальные коррозионные процессы вследствие возникновения пар дифференциальной аэрации.
Хлор и медный купорос вводимые в оборотную воду для предотвращения развития биообрастаний могут быть при определенных концентрациях коррозионно-агрессивными. Хлор в оборотной воде связанный в гипохлорит в концентрациях до 04 мгл не вызывает коррозии оборудования при дальнейшем увеличении концентрации коррозия углеродистой стали и латуней становится значительной [34].
При периодическом хлорировании оборотных вод с содержанием остаточного хлора 05 мгл определенные виды бактерий и водорослей приобретают иммунитет к слабой дозировке хлора поэтому возникает необходимость более интенсивного (ударного шокового) хлорирования чтобы содержание остаточного хлора составляло 20—100 мгл. Исследования коррозионной агрессивности таких сред выполнены [35] с использованием углеродистых сталей и нержавеющей хромоникелевой стали типа 18—8. Установлено
что при концентрациях 5 мгл и температуре 40 °С хлор не оказывает отрицательного влияния на коррозионную устойчивость нержавеющей стали в то время как скорость коррозии углеродистых сталей возрастает в 15— 2 раза [35].
Действие хлора в наибольшей степени проявляется при рН 7. При хлорировании шоковым методом с увеличением концентрации остаточного хлора скорость коррозии сталей возрастает в 3—7 раз.
Обработка оборотных вод медным купоросом должна осуществляться в соответствии со СНиП 204.02—84 3—4 раза в месяц с поддержанием концентрации ионов меди в воде 1 — 2 мгл в течение 1 ч. Ионы меди являются окислителем и способны стимулировать коррозию углеродистых сталей в концентрациях 03 мгл и более при концентрации 003 мгл коррозионных поражений обычно не наблюдается [36].
Скорость движения и температура оборотной воды существенно влияют на коррозию металла оборудования. Для нефтеперерабатывающих и нефтехимических предприятий скорость потока оборотной воды в аппаратах изменяется от 01 до 25 мс: рост скорости потока существенно увеличивает скорость коррозии.
При повышении температуры до 80°С наблюдается рост скорости коррозии сталей обусловленный ускорением диффузии кислорода к поверхности металла [24]. При более высоких температурах в закрытых системах каковым в большинстве случаев является оборотное водоснабжение происходит дальнейшее увеличение скорости коррозии а в открытых — из-за уменьшения растворимости кислорода скорость коррозии снижается. Для теплопередающих поверхностей трубных пучков скорость коррозии может существенно отличаться от коррозии в изотермических условиях. Увеличение скорости коррозии теплопередающей стенки является следствием ускорения диффузионных и электрохимических процессов изменения пассивного состояния; термических напряжений температурной неоднородности отложения на металле солей жесткости. Доля влияния каждого фактора различна и зависит от условий эксплуатации оборудования [3738].
Биокоррозия является одной из причин выхода из строя оборудования и трубопроводов в водных средах [39].
Микроорганизмы участвуют в образовании биообрастаний при этом их развитию способствует адсорбция отрицательно заряженных микроорганизмов на поверхности металла и накопление на этих участках более высоких концентраций питательных веществ чем в окружающей среде [4041]. В коррозионных процессах преимущественно принимают участие следующие основные группы микроорганизмов: сульфатвосстанавливающие кислотообразующие железобактерии плесне- и слизеобразую- щие углеводородные.
Действие на металл сульфатвосстанавливающих бактерий (СВБ) является одним из главных факторов биокоррозии [394243]. СВБ анаэробны и в системах охлаждения развиваются под рыхлыми отложениями накапливающимися вблизи подъемов и изгибов труб в зонах застоя воды. В условиях отсутствия кислорода активность этих бактерий тем выше чем больше в среде сульфатов и органических соединений [44]. Роль СВБ в коррозионном процессе заключается в том что они облегчают катодный процесс что приводит к усилению коррозии металла [45]. Кроме того при бактериальном восстановлении сульфатов происходит накопление в среде сероводорода и сульфидов в результате чего имеет место сульфидная коррозия металла. В присутствии СВБ протекают следующие реакции [4546]
В присутствии растворенного в воде кислорода гидроксид Fe(II) окисляется до гидроксида Fe(III).
Fe(OH)2 + 02 + 2Н2О 4Fe(OH)3.
В продуктах коррозии стали в присутствии СВБ содержатся сульфиды гидроксиды железа [47]. Под отложениями находятся глубокие язвы и питтинги. Разрушение чугуна сопровождается графитацией поверхность его покрывается непрочной пленкой состоящей из смеси сульфидов железа с графитом [3645].
Коррозия под действием СВБ в системах охлаждения может протекать с очень высокой скоростью. Сквозное разрушение стального образца толщиной 04 мм произошло через 60 сут при скорости коррозии 25 ммгод [48]. Нержавеющая сталь никель и другие сплавы используемые для изготовления теплообменников и емкостей вышли из строя через 60—90 сут. Скорость питтинговой коррозии при этом изменялась от 13 до 51 ммгод. В оборотных водах ПО «Нижнекамскнефтехим» скорость коррозии углеродистой стали в присутствии СВБ превышает скорость коррозии в воде без бактерий в 3—6 раз [49]. По результатам обследований семи НПЗ концентрация СВБ в оборотных водах достигает 25-105 клетокмл [50]. Коррозионно-опасными считаются водные среды с содержанием СВБ более 100 клетокмл [39].
В группу кислотообразующих входят микроорганизмы тио- новые бактерии грибы дрожжи и другие продуктами метаболизма которых являются органические и неорганические кислоты. Тионовые бактерии окисляют сульфиды элементарную серу сераорганические соединения с образованием сульфатов и серной кислоты при этом рН среды может снижаться до 06 и даже ниже стимулируя процесс коррозии с водородной деполяризацией. Реакции окисления протекают следующим образом [45].
Концентрации тионовых бактерий в оборотных водах НПЗ составляют от 25-Ю2 до 25-10'5 клмл при этом их количества выше 2500 клмл коррозионно-опасны.
Тионовые бактерии увеличивают скорость коррозии углеродистой стали в 2—3 раза [50].
Железо бактерии окисляют Fe(II) до Fe(III) с образованием объемистых осадков гидроксида Fc(III) [45] под которыми облегчается развитие анаэробных микроорганизмов в том числе СВБ. В продуктах коррозии присутствуют оксиды гидроксиды сульфиды железа сероводород уксусная кислота элементарная сера и др.
Слизи- и пенообразующие микроорганизмы создают на поверхности металла плотные желатинообразные колонии обусловливающие функционирование пар дифференциальной аэрации и приводящие к развитию локальной коррозии трубопровода емкостей аппаратов.
В целом биокоррозия металлов вносит значительный вклад в процесс разрушения оборудования и трубопроводов в водных средах. В настоящее время этот вид коррозии изучен недостаточно.
Качественный состав оборотных вод. Нормативные требования к составу оборотных и подпнточных вод нефтеперерабатывающих и нефтехимических предприятий представлены в табл. 5.1.2 [23]. Оборотные воды коррозионно-агрессивны в связи с чем необходима зашита оборудования от коррозии
Таблица 10.2. Нормативные требования к составу подпиточной в оборотной воды с солесодержанием до 2000 мгл для нефтеперерабатывающих и нефтехимических предприятий
2. КОРРОЗИЯ ПОД ДЕЙСТВИЕМ СТОЧНЫХ ВОД
Экологические проблемы наиболее остро проявившиеся в последние годы ставят перед предприятиями нефтеперерабатывающей и нефтехимической промышленности новые задачи.
Одной из наиболее актуальных проблем в нефтеперерабатывающей промышленности является утилизация и обезвреживание сточных вод.
Разработано несколько методов обезвреживания сточных вод нефтеперерабатывающих заводов содержащих большое количество минеральных солей и других примесей.
Один из методов обезвреживания стоков ЭЛОУ-АВТ заключается в их упаривании до сухого остатка. Процесс упаривания состоит из двух каскадов. В первом каскаде стоки упариваются от 05 до 5 %-го содержания солей при температуре 60—210°С и давлении 25 МПа. Стоки нагреваются в теплообменниках до 70—170°С и в печи—до 210 °С. Испарение стоков происходит в ряде испарителей за счет перепада давлений и температур. Упаренный до 5% солесодержащий сток—рапа (в основном с установок ЭЛОУ-АВТ) направляется на умягчение и доупаривание во втором каскаде до солесодержания
Таблица 5.2.1. Скорость коррозия (ммгод) различных конструкционных материалов в 5 %-й рапе
Титановый сплав ВТ5-1
% при 60— 160 °С и давлении 03 МПа. Подогрев умягченной рапы производится в теплообменниках до температуры 140 °С и в печи — до 160 °С при давлении 12—15 МПа. Испарение рапы до 20 %-го солесодержания происходит в испарителях за счет перепада давлений и температур.
В табл. 10.6—10.9 приведены данные по коррозионной стойкости ряда конструкционных материалов в условиях различной степени упаривания стоков из которых следует что при повышении температуры стоков и концентрации в них солей их агрессивность возрастает. Так при максимальных температурах 200—250 °С скорость коррозии углеродистой стали возрастает до 4—5 ммгод.
Таблица 5.2.2. Скорость коррозия ммгод материалов в 20 %-й рапе (умягченной)
Таблица 5.2.3. Результаты испытании образцов различных сталей в кипящей (102 °С) 20 %-й рапе
Скорость коррозии ммгод. при времени выдержки
Характеристика поверхности
Поверхность покрыта сплошной темной ржавчиной
Точечная коррозии глубиной 005—015 мм; 3—8 точек на 1 см2
Точечная коррозия глубиной 005—02 мм; 5—8 точек на 1 см2 02-03 мм
Точечная коррозия глубиной 002—015 мм2 1—2 точки иа 1 см2
Редкие мелкие точки глуби
ной 005—02 мм; 1—2 точки на 1 см5 02 мм
Редкие мелкие точки глубиной 005—02 Mir 1—2 точки на 1 см2
Редкие мелкие точки глубиной до 01 мм; но 1 точке на см2
Таблица 5.2.4. Скорость коррозии различных сталей я сплавов в аппаратах пилотной установки упаривания стоков ЭЛОУ (температура 102 0С; время акспозиции 1070 ч)
Приведенные результаты относятся к стационарным условиям. Первый же опыт эксплуатации полупромышленной установки показал что в потоке значение скоростей коррозии значительно выше. Так при скоростях потока 01 мс скорость коррозии углеродистой стали возрастает втрое. Дальнейшее повышение скоростей потока до 2 мс и более приводит к еще большим разрушениям углеродистой стали с образованием глубоких язв. Отмечены скорости коррозии углеродистой стали до 11 ммгод при испытании в 5 % рапе при температуре 150 °С и скорости потока 64 мс при рН стока 45—5.
Лабораторные испытания также свидетельствуют о существенном влиянии движения среды на коррозию в солесодержа- щих растворах.
Ниже приведены значения скорости коррозии (ммгод) углеродистой и нержавеющей сталей полученные при испытании в 20 %-й рапе при 800 °С в течение 200 ч:
Как видно из этих данных коррозия углеродистой стали при перемешивании возрастает в 4—5 раз.
В стационарных условиях для углеродистой стали отмечено что более высокая концентрация хлоридов обеспечивает образование плотной оксидной пленки приводящей к торможению коррозии.
В слабых растворах хлоридов часть корродирующей поверхности остается не покрытой пленкой и коррозия принимает локальный язвенный характер.
Легированные стали как видно из приведенных данных корродируют в солевых растворах сточных вод с невысокой скоростью. Однако их коррозия носит опасный локальный характер. Так хромистые и хромоникелевые стали подвергаются точечной коррозии а стали типа 12Х18Н10Т при наличии растягивающих напряжений весьма чувствительны к хлоридному коррозионному растрескиванию; местом зарождения трещины в таких растворах обычно является питтинг.
Хорошо известно что легирование молибденом тормозит питтинговую коррозию нержавеющих сталей в хлоридных средах. Однако при наличии питтинга для предупреждения КР требуется чтобы содержание молибдена в стали было не менее 4—6 %.
Отечественные молибден со держащие аустенитные стали с 2—3 % Мо не могут обеспечить стойкости к хлоридному коррозионному растрескиванию в сточных водах содержащих хлориды.
Аустенитно-ферритные стали с пониженным содержанием никеля более стойки к коррозионному растрескиванию чем аустенитные стали типа 18—8 в растворах хлоридов [51-54]. Однако их стойкость к КР в значительной степени зависит от содержания ферритной фазы и термообработки. Наиболее восприимчивы к КР аустенитно-ферритные стали с повышенным содержанием феррита (20—40 %) после оптимальной термообработки и закалки с 1100СС.
Аустенитно-ферритные стали 08Х22Н6Т и 08Х21Н6М2Т при испытаниях в лабораторных и промышленных условиях производства поваренной соли [52] проявили высокую стойкость как к общей коррозии (0005 ммгод) так и к коррозионному растрескиванию благодаря чему были рекомендованы в качестве конструкционного материала для работы в среде хлорида натрия.
Аустенитно-ферритная сталь содержащая молибден ОX21H6M2T в этих же условиях подвергалась коррозионному растрескиванию как и сталь 12Х18Н10Т.
В настоящее время принята схема очистки сточных вод на установке в три ступени:
первая ступень—предочистка стоков (содо-известковое умягчение);
вторая ступень — предварительное упаривание стоков;
третья ступень — концентрирование стоков и выделение солей.
При работе установки стоки из буферного пруда проходят последовательно через теплообменники расположенные во втором отделении в которых нагреваются до 60 °С и поступают на первую ступень обработки —в осветлитель с фильтрующим осадком. В осветлитель подаются из реагентного хозяйства известковое молоко растворы кальцинированной соды и коагулянта—хлорида железа. В осветлителе стоки умягчаются до конечной жесткости 1 мквл и осветляются.
Стоки после содо-известковой обработки представляют раствор с общим солесодержаиием порядка 2000—3000 мгл в основном это хлориды натрия и в значительно меньших количествах— сульфат натрия.
Умягченные стоки собираются в емкости а выделившийся шлам солей жесткости (кальция и магния) из бункера насосом откачивается в шламоотвал. Из емкости стоки подаются на вторую ступень обработки — в вакуумный деаэратор.
Из деаэратора стоки насосом прокачиваются через систему теплообменников где нагреваются до 124—128 °С и с этой температурой поступают на упаривание в первый выпарной аппарат. По мере упаривания стоки последовательно перетекают из корпуса в корпус в направлении движения греющего пара. Для предотвращения накипеобразования при глубоком упаривании стоков последнее производится в присутствии «затравочных» кристаллов мела вводимых в отстойник и циркулирующих по замкнутому контуру вместе с упариваемыми стоками. Из шестого выпарного аппарата стоки при температуре порядка 60 °С сливаются в отстойник для улавливания меловой затравки и возврата ее в первый выпарной аппарат.
Конденсат выпарного аппарата через самоиспаритель самотеком поступает в деаэратор атмосферного типа для химически очищенной воды. Конденсат от остальных выпарных аппаратов и подогревателей перетекает из аппарата в аппарат (греющие камеры) и сливается в испарители и затем в емкость а из емкости насосом через подогреватель химически очищенной воды — во внешние сети завода.
Воздух и другие несконденсировавшиеся газы попадающие в паровую систему удаляются из аппаратов работающих под вакуумом с помощью пароэжекторных блоков (ПЭБ) а из аппаратов работающих под избыточным давлением— непосредственно в атмосферу.
Из отстойника предварительно упаренные и освобожденные от меловой затравки стоки переливаются в емкость из которой далее насосом подаются на третью ступень обработки — в седьмой выпарной аппарат. Здесь стоки упариваются до состояния перенасыщения по NaCI суспензия из этого аппарата сливается в емкость и из последней насосом подается в отстойник с перемешивающим устройством. Стоки с очень мелкими кристаллами соли переливаются через верх отстойника в следующую емкость а основной поток суспензии с более крупными кристаллами соли NaCI Поступает на центрифугу. На центрифуге извлекается чистый хлорид натрия по качеству удовлетворяющий ГОСТ 13830—84. Маточный раствор после центрифуги сливается в емкость.
Сухой остаток солей после центрифуги и испарителя подается в промежуточный склад где упаковывается в тару. Товарная соль поступает на реализацию а нетоварная — на захоронение в соленакопитель
Анализ рабочих условий основного оборудования работающего по такой схеме предусматривающей деаэрацию повышение рН до 10—11 и температуры в указанном интервале позволяли рассмотреть возможность материального оформления оборудования этих установок без привлечения остродефицитных материалов.
Характеристика исходных стоков одного из нефтеперерабатывающих заводов приведена в табл. 5.2.5.
Поскольку наибольшую опасность для работы оборудования в условиях упаривания стоков представляет коррозионное растрескивание под воздействием горячих хлоридов основное внимание при выборе материального оформления должно уделяться этому вопросу.
Анализ всех имеющихся результатов исследований поведения материалов в условиях имитирующих работу выпарных
Таблица 5.2.5. Состав (гл) исходных. к умягченных стоков н раствора выпарных аппаратов
установок и в условиях других производств близких к описанным (например производство поваренной соли и т. п.) свидетельствуют о том что в качестве конструкционных материалов для оборудования установок термического обезвреживания стоков могут быть приняты стали 08Х22Н6Т 08X2LH6M2T (для температур ниже порога возможного возникновения КР) латунь марки ЛАМш77-2-006 и углеродистая сталь с оптимальной прибавкой на коррозию.
Так тонкостенное теплообменное оборудование и трубки в греющих камерах выпарных аппаратов целесообразно изготовлять из указанной латуни корпусные детали выпарных аппаратов — из аустенитно-ферритной стали 08Х22Н5Т емкости могут выполняться либо с эмалированным покрытием
либо из сталей 08X22Н6Т 08Х21Н6М2Т для условий средней агрессивности может быть использована и углеродистая сталь с прибавкой на коррозию не менее 3 мм.
Трубопроводы это легкозаменяемое оборудование также рекомендуется изготавливать из углеродистой стали с максимальной прибавкой на коррозию (от 3 до 5 мм).
Вывод.doc
3.1.doc
Диаметр корпуса – 2400 мм;
Высота корпуса – 20000 мм;
Узел соединения рассчитываемый на малоцикловые нагружения –
днище – опора – кольцо жесткости
Число циклов нагружения:
аварийных остановок – 12
технологических остановок – 30
гидравлических испытаний – 15
срабатываний КИП – 25
3.2.doc
Рассчитать кожухотрубчатый теплообменный аппарат с компенсатором на корпусе исходя из следующих условий:
Поверхность теплообмена F= 200 м2.
Диаметр и толщина стенки труб dн×SТ = 38×2мм.
Рабочая среда: трубное пространство – газ межтрубное – жидкость.
Давление в трубном пространстве РТ = 12 МПа.
Давление в межтрубном пространстве РМ= 08 МПа.
Температура в трубном пространстве: вход tНТ = 200 ºС выход tКТ = 120 ºС.
Температура в межтрубном пространстве: вход tНМ = 20 ºС выход tКМ = 95 ºС.
Скорость коррозии V= 002 ммгод.
Срок службы = 30 лет.
Коэффициент прочности сварного шва φ= 08.
Материал аппарата ВТ 1-0.
Расположение аппарата – горизонтальное.
Крышка – торосферическая тип ТС-В
2. Выбор конструкционного материала и допускаемые напряжения
Расчетное давление Р = 20 МПа.
Принимаем расчетную температуру внутри аппарата t = 150 °С.
Материал аппарата – сталь 20 для которой
в = 325 МПа т = 163 МПа [15].
Нормативное допускаемое напряжение:
nв = 26; nт = 15 – коэффициенты запаса прочности
* = m 16315=109 МПа) = 109 МПа
Допускаемое напряжение:
[] = * = 09·109 = 98 МПа
= 09 – поправочный коэффициент при отсутствии данных о рабочей среде.
С = ПТа =00001·10 = 0001 м
где П = 00001 мгод – скорость коррозии
Та = 10 – срок службы аппарата
Давление гидравлических испытаний
Рги = 125Р[]20[]500 = 125·20·10698 = 27 МПа
3. Расчет толщины стенки корпуса аппарата
Толщина стенки по методу максимальных упругих напряжений.
Расчетный коэффициент толстостенности:
= = [98(98 – 312·20)]12 = 1244
Расчетный коэффициент толстостенности в условиях гидроиспытаний:
= = [98(98 – 312·27)]12 = 1383
Исполнительная толщина обечайки:
s > 05D( – 1) = 05·2400(1383– 1) = 460 мм
Принимаем s = 480 мм тогда коэффициент толстостенности:
= (D+2s)D = (2400+2·480)2400 = 1400
Допускаемое рабочее давление:
[p] = [](2 – 1)312 = 98(14002 – 1)312 = 54 МПа
Условие р [p] выполняется
Проверка условия прочности
= Р(2+1)(2 – 1) = 20(14002+1)(14002 – 1) = 62 МПа
и = Р(2 – 1) = 20(14002 – 1) = 21 МПа
[(62 – 21)2+(62+20)2+(21+20)2]12 = 71 МПа
Условие экв [] = 98 МПа выполняется
Проверка по условию пластичной деформации
Допускаемое давление
[Р] = []φln = 98·10ln1400 = 330 МПа
Условие [Р] > Рг.и = 27 МПа выполняется
Проверочный расчет с учетом температурных напряжений при Δt = 50°С.
Для стали 20: α = 124·10-6 1ºС; = 03; Е = 186·105 МПа
Вспомогательный коэффициент k1:
k1 = = 124·10-6·186·105[(14002–1)2ln1400– 1](1 – 03) = 141
Эквивалентное напряжение
экв = = (3·202+3·20·141·50+1412·502)05(14002 – 1) =106 МПа
экв =106 т11 = 16311 = 148 МПа выполняется
4. Расчет массы аппарата
Масса корпуса аппарата
mк = 0785(Dн2-Dвн2)Нρ
где Dн = 336 м – наружный диаметр корпуса;
Dвн = 240 м – внутренний диаметр корпуса;
Н = 182 м – высота цилиндрической части корпуса
ρ = 7800 кгм3 – плотность стали
mк = 0785(3362-242)182·7800 = 616211 кг
Общая масса аппарата. Принимаем что масса вспомогательных устройств (штуцеров фланцев и т.д.) составляет 10% от основной массы аппарата тогда
m = 11(mк + mд + mкр) = 11(616211+25130+18440) = 725759 кг = 711 МН
Масса аппарата заполненной водой при гидроиспытании.
Масса воды при гидроиспытании
mв = 1000(0785Dк2Hц.к + Vд) = 1000(0785·242·182 + 235) = 84643 кг
Максимальный вес аппарата
mmax = m + mв = 725759 + 84643 = 810402 кг = 794 МН
5. Расчет колонны на ветровую нагрузку
Отношение HD = 21336 = 63 15 следовательно расчетная схема принимается в виде упругозащемленного стержня. Условно разбиваем по высоте аппарат на 3 участка по 7 метров вес участка принимается сосредоточенным в середине участка; ветровая нагрузка равномерно распределенная по высоте аппарата заменяется сосредоточенными силами приложенными в середине участка:
Период собственных колебаний для максимального и минимального веса колонны. При HD 15
где Н = 21 м – высота колонны;
G – максимальный или минимальный вес колонны;
J – момент инерции верхнего поперечного сечения корпуса аппарата относительно центральной оси;
Е – модуль упругости;
где Dcp – средний диаметр корпуса
Dcp = D + (S-C) = 24 + (048-0001) = 2879 м
J = 28793(048-0001)8 = 4498 м4
φ0 = 1СфJф = 150·212 = 0009 1МН·м
где Сф = 50 МНм3 – коэффициент неравномерности сжатия грунта;
Jф – момент инерции подошвы фундамента относительно центральной оси
Jф = 1 3Jк = 13·163 = 212 м4
где Jк - момент инерции фундаментного кольца
Jк = D3l8 = 243·038 = 163 м4
где l = 03 м – ширина кольца
Тmax = 179·21[794(21186·105·4498 + 4·0009)98]05 = 642 c
Тmin = 179·21[711(21186·105·4498 + 4·0009)98]05 = 608 c
Нормативный скоростной напор для II географического пояса q = 0035·10-2 МНм2 [16]
Поправочный коэффициент к нормативному скоростному напору для участков аппарата высотой Н > 10 м = 14 [16]. Расчетный скоростной напор по участкам
q1 = q2 = q = 14·0035·10-2 = 0049·10-2 МНм2
Коэффициент динамичности определяем по графику [16]:
для Т = 642 с – = 33
для Т = 608 с – = 32
Коэффициент пульсации скоростного напора определяем по графику [16]:
для участка 1 - m1 = 034
для участка 2 - m2 = 035
для участка 3 - m3 = 035
Коэффициент увеличения скоростного напора
при максимальной массе аппарата
при минимальной массе аппарата
Сила от ветровой нагрузки действующей на каждый участок аппарата
при максимальной силе тяжести аппарата
Р1 = 06·2122·0049·10-2 ·336·7 = 00147 МН
Р2 = 06·2155·0049·10-2 ·336·7 = 00149 МН
Р3 = 06·2155·0035·10-2 ·336·7 = 00106 МН
при минимальной силе тяжести аппарата
Р1 = 06·2088·0049·10-2 ·336·7 = 00144 МН
Р2 = 06·2120·0049·10-2 ·336·7 = 00147 МН
Р3 = 06·2120·0035·10-2 ·336·7 = 00105 МН
Изгибающий момент от ветровой нагрузки на аппарат относительно основания при максимальной силе тяжести аппарата
Мв1 = 00147·175 = 0257 МН
Мв2 = 00149·105 = 0156 МН
Мв3 = 00106·35 = 0037 МН
Мв1 = 00144·175 = 0252 МН
Мв2 = 00147·105 = 0154 МН
Мв3 = 00105·35 = 0037 МН
6. Расчет аппарата на сейсмическую нагрузку
Величина сейсмической силы в середине i-го участка.
где Кс = 005 – сейсмический коэффициент при 8 балах [16];
= 055 - коэффициент динамичности;
Gi – сила тяжести i-го участка.
Принимаем что масса аппарата распределена по высоте равномерно тогда
α0 = хiН – относительные координаты центров тяжести.
К1= 21·0723·186·105·4498 + 0009·083 = 000748 1МН·м
К2= 21·0313·186·105·4498 + 0009·050 = 000450 1МН·м
К3= 21·0043·186·105·4498 + 0009·017 = 000153 1МН·м
Предварительно рассчитываем суммы
GiKi = 265(000748+000450+000153) = 003580
GiKi2 = 265(0007482+0004502+0001532) = 2081·10-4
Сейсмическая сила в середине каждого участка
Р1 = 005·055·265·0.00748·0.035802081·10-4 = 00938 МН
Р2 = 005·055·265·0.00450·0.035802081·10-4 = 00564 МН
Р3 = 005·055·265·0.00153·0.035802081·10-4 = 00191 МН
Расчетный изгибающий момент в нижнем сечении опоры аппарата от сейсмической нагрузки при учете первой формы колебаний
938·175+00564·105+00191·35 = 2301 МН·м
Расчетный изгибающий момент в том же сечении опоры с учетом влияния высших форм колебаний
Мс1 = 125Мс = 125·2301 = 288 МН·м
Суммарный расчетный изгибающий момент от сейсмической и ветровой нагрузок
Мсум = Мс1 + 03Мв = 288+03·045 = 3015 МН·м
Поскольку ветровая нагрузка на колонну меньше суммарной то расчет опоры ведем по суммарной нагрузке.
7. Расчет опоры аппарата
Аппараты вертикального типа с соотношением НD > 5 размещаемые на открытых площадках оснащают так называемыми юбочными цилиндрическими опорами конструкция которых приводится на рисунке.
Принимаем толщину цилиндрической стенки опоры S= 20 мм.
Материал опоры сталь Ст 3 ГОСТ 380-88
в = 380 МПа; т = 220 МПа; Е = 210·105 МПа; = 146 МПа
Диаметр опоры равен наружному диаметру аппарата 336 м.
Размеры опорного кольца.
Внутренний диаметр кольца
D2 = D – 006 = 336 – 006 = 330 м
Наружный диаметр кольца
D1 = D + 2S + 02 = 336+ 2·0020 + 02 = 360 м
Принимаем D1 = 360 м
Опорная площадь кольца
F = 0785(D12 – D22) = 0785(362 – 3302) = 1625 м2
Момент сопротивления опорной площади кольца
W = (D14 – D24)32D1 = (364 – 3304)32·36 = 135 м4
Напряжение сжатия в стенке опоры с учетом отверстия для лаза d = 05 м
с = Gmax[(D+S) – d](S-C) = 794[(336+0020) – 05](0020-0001) = 391 МНм2
Напряжение на изгиб в стенке опоры
и = М(D+S)2(S-C) = 0450(336+0020)2(0020-0001) = 07 МНм2
D2(S – C) = 3362(0032– 0001) = 54
по этой величине по графику [16] находим коэффициенты:
Kc = 875тkcE = 875·220·00521·105 = 0046
Kи = 875тkиE = 875·220·00421·105 = 0037
Допускаемые напряжения на сжатие и изгиб в обечайке опоры
сд = КсЕ(S-C)D = 0046·210·105(0020 – 0001)336 = 55 МПа
ид = КиЕ(S-C)D = 0037·210·105(0020 – 0001)336 = 44 МПа
Устойчивость цилиндрической опоры
= 39155 +0744 = 073 1
устойчивость обеспечена
Максимальное напряжение на сжатие в сварном шве соединяющем цилиндрическую опору с корпусом аппарата при коэффициенте сварного шва φш = 07
407(336+0020)(0020 – 0001) + 4·045007(336+0020)2(0020– 0001) = 326 МПа сд
Максимальное напряжение сжатия на опорной поверхности кольца
41625+ 045135 = 52 МПа 10 МПа
Номинальная расчетная толщина опорного кольца при l = 01 м
3·01(52146)05 = 0033 мм
с учетом прибавки на коррозию принимаем округляя размер s = 0040 м
Наименьшее напряжение на опорной поверхности кольца:
при максимальной силе тяжести аппарата
41625– 0450135 = 455 МПа
при минимальной силе тяжести аппарата
11625– 0443135 = 405 МПа
Расчетным является наибольшее по абсолютной величине значение – при максимальной силе тяжести аппарата а знак минус указывает на необходимость установки фундаментных болтов.
Общая условная расчетная нагрузка на фундаментные болты
Рб = 0785(D12 – D22) = 0785(3602 – 3302)455 = 739 МН
Принимаем количество фундаментных болтов z =24 тогда нагрузка на один болт
Рб1 = 73924 = 031 МН
Расчетный внутренний диаметр резьбы фундаментных болтов
(4·031146)05 + 0001 = 0052 м
Диаметр болтовой окружности
Dб = D + 012 = 336+ 012 = 348 м
8 Прочностной расчет
8.1. Расчет толщины цилиндрической
Выбор расчетных величин принимаем материал аппарата сталь 20к с допускаемым напряжением при t=20 0c МПа.
Принимаем коэффициент прочности сварного шва и поправку на коррозию в размере с =2мм [19].
Расчет толщины цилиндрических обечаек проводим согласно ГОСТ 14249-80 по формуле:
где расчетная толщена обечайки мм;
- диаметр обечайки м;
- расчетное давление. МПа;
Определим расчетное давление в аппарате:
Здесь кгм3 плотность воды при гидроиспытании при 200С;
Согласно ГОСТ356-68 [19]принимаем ближайшее большее значение Рр=0.4 мПа;
Определим толщину цилиндрической обечайки .
Тогда с учетом поправки на коррозию получим:
8.2. Расчет толщины днища
Толщину эллиптических обечаек определяем по формуле:
Тогда толщина эллиптической обечайки с учетом поправки на коррозию составит:
8.3. Расчет и выбор опор аппарата
Рассчитаем массу аппарата в рабочем положении т.е. заполненным водой при гидравлическом испытании.
где -масса аппарата в рабочем положении кг;
- масса пустого аппарата кг;
- объем трубного и межтрубного пространства соответственно м3;
Рассчитаем нагрузку действующую на опору.
где -нагрузка действующая на опору Н;
По рассчитанной нагрузке согласно ОСТ 26-665-70 принимаем опоры-лапы к вертикальным аппаратам с основными размерами таблица 6.1 рисунок 6.1. [19]
Основные размеры опоры аппарата
Опоро1-2500 ОСТ 26-665-70
Проверим сварной шов на касательное напряжение среза.
Допускаемое напряжение на срез составляет:
Расчетное напряжение на срез составит:
где - расчетное напряжение на срез мПа;
к- катет сварного шва м;
условие выполняется.
8.4. Расчет на прочность фланцевого
Расчет на прочность фланцевого соединения ведем по ОСТ 26-373-78 [18]
В качестве прокладки принимаем асбестовый картон с шириной bn=15 мм
Наружный диаметр прокладки: Dn=DБ – e
где е=30 безразмерный коэффициент [19]
Средний диаметр прокладки: Dn ср.= Dn – bn=650-15=635 мм.
Эффективная ширина прокладки составляет при bn ≤ 15 мм
be=05 be=05 15=75 [19]
Нагрузка действующая на фланцевое соединение составляет:
Qy=0.785 D2n ср. Pp=0.785 06352 025=0079 МПа м2.
Реакция прокладки в рабочих условиях:
где m=2.5 – для асбестового картона [18]
Болтовая нагрузка в условиях монтажа: ;
Где α=1.45 – безразмерный коэффициент [19]
Болтовая нагрузка в рабочих условиях:
Условия прочности болтов:
м2 – площадь сечения болтов [19]
=160 МПа – допускаемое напряжение для материала болтов при 200С МПа [18]
Условие выполняется.
Рекомендуемые чертежи
- 24.01.2023