Механизация и электроснабжение очистных работ




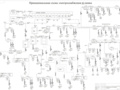
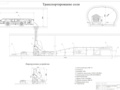
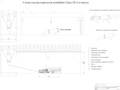
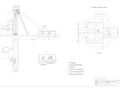
- Добавлен: 24.01.2023
- Размер: 2 MB
- Закачек: 0
Описание
Состав проекта
![]() |
![]() |
![]() ![]() ![]() ![]() |
![]() ![]() ![]() |
![]() ![]() ![]() ![]() |
![]() ![]() ![]() ![]() |
![]() ![]() ![]() ![]() |
![]() ![]() ![]() ![]() |
![]() ![]() ![]() |
![]() ![]() ![]() ![]() |
![]() ![]() ![]() |
Дополнительная информация
Механизация очистных работ (2).dwg

Кафедра ГМ и РТ гр. ГМз-05-1
Самоходный вагон 5ВС-15
Ленточный конвейер 1Л80
Натяжная лебедка ЛВВ-50
Схема отработки камер
Продол- житель- ность
Наименование операций
График организации работ
График выходов рабочего персонала
Машинист комбайна Урал-20
Наименование параметров
Призма возможного обрушения
Угол наклона стакера
Высота надводного борта
Глубина черпания от уреза воды
Макс. ширина забоя по урезу воды
Макс. ширина забоя по плотику
Мин. превышение свай над верхней подушкой
Превышение нижней точки стакера над отвалом
Расстояние между береговыми якорями
Мин. превышение днища понтона над полотном
Подпись лица внесшего изменения
п а р а м е т р ы н а
Глубина черпания (Н)
Призма возможного обрушения (D)
П А С П О Р Т забоя и оптимальные рабочие параметры драги № 116
Т А Б Л И Ц А определения призмы возможного обрушения (D) в зависимости от глубины черпания (Н)
Экономика.dwg
Основные технико-экономические показатели
Калькуляция себестоимости
Объем годовой добычи
Число рабочих дней в году
Число рабочих смен в сутки
Списочная численность
Годовая производительность труда
Уровень рентабельности
Себестоимость продукции
Ремонт горного оборудования
Отчисления на соц.страхование
Вспомогательные материалы
Общерудничные расходы
Полная себестоимость
Рудничный транспорт.dwg

Самоходный вагон 5ВС-15
Устройство загрузочное 1Л100.16.00.000А
Секция разгрузочная Л100.20.00.000Б-01
Привод Л100.13.00.000А
Лебедка натяжная ЛВВ-50
Перегрузочное устройство
Рембаза.dwg

II. Моечное отделение
III. Механическое отделение
IV. Сварочное отделение
V. Агрегатное отделение
VI. Складское отделение
VII. Вспомогательное отделение
VIII. Административное отделение
Камера ремонта горного оборудования
Камера ремонта горного оборудования
Токарно-винторезный станок
Принципиальная схема эл.снабжения.dwg

Надшахтное здание Здание подъёмных машин
Северный вентиляционный штрек
Северный конвейерный штрек
Панельная вентиляционная сбойка №2-з
Разведочный штрек №4
Панельная вентиляционная сбойка №1-з
Панельный вентиляционный штрек
Панельный конвейерный штрек
Панельная вентиляционная сбойка №3-з
Заезд на Главный ствол
Заезд к Главному транспортному штреку №1
Заезд к Главному транспортному штреку №2
Вентиляционная сбойка
Главный транспортный штрек №2
Главный конвейерный штрек
Главный вентиляционный штрек
Главный транспортный штрек №1
Конвейерный уклон №1
Вспомогательный ствол
Панельный разрезной штрек
Вспомогательный уклон №2
Фланговый вентиляционный штрек
Камера подземных гаражей
Схема вскрытия шахтного поля
Кафедра ГМ и РТ гр. ГМз-03-1
Параметры системы разработки
Габариты машины 1ВОМ А
Сечение конвейерного штрека
ИрГТУ ДП 150402.65 09 023
Принципиальная схема электроснабжения рудника
ЗРУ-6кВ ЯЧ.№18 ЯЧ.№24
Л100У№5 ЛВВ-50№4 (90) (7.5)
Л100У№4 ЛВВ-50№3 (90) (7.5)
заряд. станок заточн. устр. сверл станок
ААВ3х120 СБн3х70 400 800
вентилятор ВМЭ-6 (22)
Спуск комбайна.dwg

Схема спуска агрегатов комбайна в шахту
Схема спуска агрегатов комбайна Урал-20 А в шахту
Схема скребкового конвейера комбайна Урал-20 А
Передняя рама конвейера
Задняя рама конвейера
Подвижная часть конвейера
Передняя и задняя рама конвейера
Рама конвейера комбайна Урал-20 А
Диплом Нормоконтроль - копия.doc
Федеральное государственное бюджетное образовательное учреждение
высшего профессионального образования
Кафедра горных машин и электромеханических систем
Заведующий кафедрой ГМиЭМС
МЕХАНИЗАЦИЯ И ЭЛЕКТРОСНАБЖЕНИЕ ОЧИСТНЫХ РАБОТ
Пояснительная записка
Приложение к Заданию
ИНДИВИДУАЛЬНЫЕ ПАРАМЕТРЫ МЕСТОРОЖДЕНИЯ
1 Геологическое строение месторождения11
2 Гидрогеологическая характеристика месторождения13
3 Основные параметры шахты16
4 Вскрытие месторождения17
5 Горнокапитальные и подготовленные выработки19
5.1 Способы проведения выработок19
5.2 Околоствольный двор19
5.3 Протяженные выработки21
5.4 Камерные выработки22
Механизация горных работ24
1 Выбор оборудования и расчёт производительности25
2 Расчёт производительности для комбайна Урал–20 А25
3 Расчёт производительности для комбайна Урал–10 Р27
4 Технико–экономическое сравнение вариантов27
5 Проверочный расчёт мощности привода комбайна Урал–20 А31
Рудничный транспорт34
1 Выбор оборудования и расчёт производительности35
1.1 Расчёт производительности для 5ВС–1535
1.2 Расчёт производительности для 5ВС–10 тгод36
1.3 Технико–экономическое сравнение вариантов37
1.4 Тяговый расчет самоходного вагона 5ВС–1541
1.5 Эксплутационный расчет42
2 Выбор и детальный расчет ленточного конвейера42
2.1 Определение линейного веса отдельных частей груженной и порожней ветвей конвейера43
2.2 Определение сопротивлений при движении ленты44
2.3 Расчет статических натяжений методом обхода по контуру45
2.4 Определение усилий на натяжном устройстве и расчет ленты на прочность46
2.5 Определение тягового усилия и мощности двигателя приводной станции конвейера46
2.6 Выбор и расчет ленточного конвейера 1ЛУ10047
2.7 Определение линейного веса отдельных частей груженой и порожней ветвей конвейера48
2.8 Экономическая часть для конвейерного транспорта49
Стационарные установки54
1 Расчет скиповой подъемной установки55
1.1 Выбор подъемного сосуда55
1.4 Выбор подъемной машины57
1.5 Выбор направляющих шкивов58
1.6 Расположение подъемной машины58
1.7 Вычисление мощности двигателя59
1.8 Определение приведенной массы установки60
1.9 Максимальное ускорение скипа61
1.10 Вычисление времени и расстояний при движении скипа62
1.11 Расчет необходимых усилий в подъемном канате63
1.12 Уточненный расчет мощности электродвигателя65
1.13 Мощности на валу барабана и потребляемые электродвигателем из сети.66
1.14 Определение расхода электроэнергии67
1.15 Техника безопасности при эксплуатации подъемной установки70
2 Расчет водоотливной установки70
3 Проветривание участка горных работ75
Эксплуатация и ремонт78
1 Организация и технология ремонта79
2 Расчет площадей ремонтной базы83
3 Технико–экономические показатели ремонтного участка84
1 Расчет участковых электрических сетей89
1.1 Расчет и выбор кабельной сети напряжением выше 1кВ90
1.2 Расчет и выбор кабельной сети напряжением до 1кВ92
2 Выбор низковольтной аппаратуры уставок реле максимальной токовой защиты и плавких вставок предохранителей100
2.1 Выбор автоматических (фидерных) выключателей100
2.2 Выбор магнитных пускателей100
3 Расчет заземления трансформаторной подстанции101
4 Расчет освещения подземных выработок103
5 Технико–экономические показатели электроснабжения подземных горных работ104
1 Организация труда и структура управления предприятием110
2 Расчет основных технико–экономических показателей112
Безопасность труда114
1 Общие требования безопасности горных работ115
2 Безопасность производственных процессов116
3 План ликвидации117
4 Оценка условий труда121
5 Электробезопасность122
6 Промышленная санитария123
7 Средства индивидуальной защиты работников124
8 Основные мероприятия по обеспечению безопасных и здоровых условий труда125
9 Противопожарная защита128
Специальная часть130
1 Демонтаж и монтаж комбайна Урал–20 А131
1.1 Разгрузка и прием изделия получателем131
1.2 Подготовка комбайна к монтажу131
2.1 Организация работ по спуску137
2.2 Доставка до монтажной камеры138
Перечень условных обозначений символов единиц142
Библиографический список144
Площадь Тыретского месторождения каменной соли административно входит в состав Заларинского района Иркутской области и расположено в 15 км северо–восточнее железнодорожной станции Тыреть Восточно–Сибирской железной дороги и в 240 км к северо–западу от г.Иркутска. Район месторождения электрифицирован от Иркутской ГЭС. Площадь месторождения характеризуется выположенным рельефом слабо расчлененным речной сетью. Абсолютные отметки в пределах контура проектируемого шахтного поля колеблются от 450 до 475м. По южной юго–восточной и восточной окраинами разведанной площади протекает река Унга (левый приток р.Ангары) Климат района резко континентальный. Среднегодовая температура составляет –3ºС. Распределение осадков по временам года неравномерное. Максимальное количество их выпадает в летне–осенний период. Снежный покров невелик и обычно не превышает 400мм. Почва зимой промерзает до глубины 35 м. Полное оттаивание её заканчивается во второй половине июня. Вечная и островная мерзлота в районе отсутствуют. Ветры преобладают северо–западного направления. Средней скоростью 46мсек.
1Геологическое строение месторождения
Тыретское месторождение каменной соли находится в пределах южной части Сибирской платформы на западном крыле Ангарской антеклизы в месте сочленения её с восточным бортом Присаяно–Енисейской синеклизы. В геологическом строении месторождения принимают участие декембрийские кристаллические и метаморфические образования фундамента Сибирской платформы перекрытые мощной толщей кембрийских отложений слагающих платформенный чехол.
Наиболее древними из вскрытых разведочными скважинами отложений являются образования низкого протерозоя Prz. Представленные в серицитизированные магнетито–биотитовые гнейсы в нашей биотитовыми гнейсами.
Нижнепротерозойские породы с утловым несогласием перекрываются отложениями ушаковской свиты нижнего кембрия представленными переслаиванием аргиллитов алевролитов песчаников и глинистых сланцев общей мощностью около 230м.
Породы мотской свиты нижнего кембрия согласно залегают на образованиях ушаковской свиты. Они представлены песчаниками реже глинистыми песчаниками; глинистыми ангидритуированными алевритистыми и песчанистыми доломитами мергелями аргиллитами ангидритами а также ангидрито–доломитами общей мощностью до 550м.
Отложения мотской свиты согласно перекрываются отложениями усольской свиты нижнего кембрия представленной переслаиванием пластов каменной соли мощностью до 70м. и карбонатных пород доломитов и ангидритов реже аргиллитов.
Бельская свита нижнего кембрия согласно залегает на отложениях усольской свиты. По литологическим признакам в ней выделяются три подсвиты: нижне и среднебельская подсвиты отложены доломитами известковыми доломитами доломитовыми известняками реже ангидридо–доломитами. Породы нередко окремненные засолоненные встречаются прослои глин сланцев гипсоангидридов ангидридов. Общая мощность отложений нижне– и среднебельской подсвит достигает 300м.
Верхнебельская подсвита нижнего кембрия является основным объектом изучения. Она характеризуется переслаиванием пластов каменной соли засолоненных доломитов доломито–ангидритов и реже ангидритов. В отложениях этой подсвиты было вскрыто десять пластов каменной соли мощностью от 06 до173м.
Вскрытые пласты соли разделены «межпластовыми перемычками» мощность которых колеблется от 08 до 13м. Кровля верхнебельской подсвиты отбивается по кровле первого пласта каменной соли (на глубинах 4536–49655м) а подошве последнего десятого пласта соли (на глубинах 5745–6046м). Пласты каменной соли имеют пологое моноклинальное падение в северо–восточном направлении. Угол падения не превышает 1º. Общая мощность верхнебельской подсвиты в разведанном контуре находится в пределах 118–123м. Наиболее перспективными для промышленной отработки каменной соли являются V VII VIII пласты имеющие средние мощности соответственно 164; 118; 64м. Глубина залегания верхнего промышленного (V) пласта каменной соли составляет 5004–5426м. Плотность соли колеблется от 208 до 213 тм3. При подсчете запасов принято среднее значение ее равное 21 тм3 . Временное сопротивление сжатию образцов соли взятых из пластов V и VII колеблется в пределах 190–370 кгсм2. Физико–механические свойствам разделяющих пласты соли пород характеризуются следующими величинами: для доломитов плотность варьируется от 22 до 23 тм3 пористость – от 11 до 164% чаще от 52 до 164% временное сопротивление сжатию в воздушно–сухом состоянии изменяется от 520 до 1680 кгсм; для ангидрито–доломитов плотность равна 24–28тм3 пористость варьируется в пределах 55–166% и временное сопротивление сжатию в воздушно–сухом состоянии изменяется от 15 до 855 кгсм2.
Продуктивная соленосная толща согласно перекрывается отложениями булайской свиты нижнего кембрия которая по литологическому составу подразделяется на две подсвиты. Нижнебулайская подсвита сложена слоистыми внизу и массивными вверху доломитами реже мергелистыми и глинистыми доломитами доломито–ангидритами с прослоями в нижней части песчаников и ангидритов Верхнебулайская подсвита представлена однообразной толщей массивных доломтов в верхней части незначительно кавернозной трещиноватой. Общая мощность свиты достигает 150 метров.
Ангарская свита нижнего кембрия согласно перекрывающая на нижне– и верхнеангарские подсвиты. Нижнеангарская подсвита сложена доломитами с прослоями глинистых и известковых доломитов реже известняками. Породы часто перемяты брекчированы с включением гипса и ангидрита нередко окремненные часто кавернозные трещиноватые. Верхнеангарская подсвита представлена доломитами нередко кавернозным и с прослоями глинистых доломитов карбонатных и кремнисто–карбонатных брекчий на глинистом и карбонатнно–глинистом цементе доломитизированных известняков мергелей участками перемятых в верхней части разреза водорослевых известняков и доломитов скорлуповатого строения: реже ангидритов и ангидрито–доломитов. Все породы часто окремнены и трещиноваты. Общая мощность пород ангарской свиты достигает 315м.
На породах ангарской свиты со стратиграфическим несогласием залегают отложения верхоленской свиты верхнего кембрия.Отложения верхоленской свиты не имеют повсеместного распространения в пределах разведанного участка и представлены только осинской пачкой сложенной в нижней части алевролитами а в верхней–мергелями. Изредка встречаются тонкие прослои доломитизированных известняков прожилки и вкрапления гипса реже пирита. Средняя мощность пачки в пределах месторождения 147м
Четвертичные отложения развиты в пределах всего разведанного участка но мощность их невелика около 10м. Они представлены супесью суглинками песчаными глинами в нижней части с примесью обломочного материала в основном карбонатных пород.
2Гидрогеологическая характеристика месторождения
Тыретское месторождение каменной соли расположено в центральной части Иркутского артезианского бассейна. В пределах месторождения выделяются воды приуроченные к четвертичным нижне– и нижне–кембрийскими отложениями.
Подземные воды в четвертичных отложениях приурочены главным образом к аллювиальным образованиям долины р.Унги и наиболее крупных падей а также к отложениям делювиальных шлейфов и имеют распространение. Максимальная мощность водоносного горизонта не превышает 5–7м. На площади распространения закарстованных отложений нижнего кембрия аллювиальным водам свойственно спорадическое распространение. Поэтому в пределах шахтного поля месторождения каменной соли лишь небольшое число скважин обнаружено в аллювий подземные воды. Водообильность пород четвертичного водоносного горизонта очень низкая поэтому на условиях вскрытия они не окажут практически никакого влияния.
Подземные воды в отложениях верхнего кембрия приурочены к трещиноватым мергелям и прослоям доломитизированных известняков. Водообильность пород низкая и находится в прямой связи с трещинноватостью и мощностью отложений. Удельные дебиты скважин пробуренных на верхнекембрийский водоносный горизонт варьируют в пределах 0015–2лс. Коэффициент фильтрации пород изменяется от 02 до 25мсут.
Скважинами пробуренными на верхнекембрийский водоносный горизонт в пределах шахтного поля водопроявлений не обнаружено.
Подземные воды нижнекембрийских отложений.
В породах ангарской свиты выделяют трещинные и трещиннокарстовые воды. Водовмещающими породами являются трещиноватые и кавернозные разности доломитов доломитизированных известняков мергелей и мергелистых доломитов залегающие среди массивных доломитов и мергелей. В отложениях ангорской свиты в процессе разведочного бурения было выделено семь водоносных горизонтов и приконтактовый водоносный горизонт приуроченный к контакту брекчированных мергелей и доломитов в интервале 21–25м; характеризуется интенсивным водопоглощением достигающем 42 лс. Проявляется только в периоды паводков и интенсивных дождей.
I водоносный горизонт залегает на глубине 36–38м и имеют мощность от 5 до 10м. Слабо напорные (напор до 12м) на отдельных участках безнапорные воды приурочены к верхней части разреза пачки брекчированных мергелистых доломитов этой же пачки. Удельные дебиты скважин варьируют в пределах 005–0005 лс. Коэффициент фильтрации 003–07 мсут. реже до 6 мсут.
II водоносный горизонт приурочен к нижней части пачки кавернозных доломитов на контакте с пачкой мергелистых доломитов. Водоупорами служат плотные доломиты. Глубина залегания горизонта от 48 до 63м при мощности 3–5м. Величина напора воды от 155 до 337м. Удельный дебит до 1лс. Коэффициент фильтрации варьирует от 3 до22мс.
III водоносный горизонт приуроченный к сильно трещиноватым слоистым доломитам выделен разведочным бурением на контакте пачки мергелистых доломитов и пачки серых доломитов. Водоупорами этого горизонта служат мергелистые известняки и плотные разности доломитов. Мощность водоносного горизонта колеблется от 20 до 40м при глубине залегания от 62 до71м. Величина напора достигает 42м. Удельные дебеты скважин до 25лс. Коэффициент фильтрации водоносного горизонта составляет 18–58 мсут.
IV водоносный горизонт приурочен к верхней трещиноватой части пачки коричневато–серых доломитов выделенной среди плотных доломитов. Мощность горизонта колеблется от 15 до 29м. Глубина залегания горизонта варьирует в пределах 112–120м. Величина напора достигает 84м. Удельный дебет по данным откачек колеблется от 05 до 25 лс. Коэффициент фильтрации пород составляет 18–58 мсут.
V водоносный горизонт залегает на глубине 164–178м. и приурочен к верхней части интенсивно трещиноватых доломитов. Мощность горизонта колеблется в пределах от 10 до 32м. Величина напора достигает 149м. Удельный дебет из скважин достигает 0.5лс. Коэффициент фильтрации пород составляет 20–29 мсут.
VI водоносный горизонт связан с трещиноватыми и кавернозными породами верхней и средней части пачки брекчированных мергелистых известняков. Водоупорами служат массивные доломиты и плотные мергелистые известняки. Водоносный горизонт залегает на глубине 2455–262м. и имеет мощность от 5 до 35м. Воды горизонта напорные: величина напора достигает 233м. Водообильность горизонта сильно варьирует. Удельные дебиты при откачках достигали 22лсек. Коэффициент фильтрации от 05 до 97 мсут.
VII водоносный горизонт последний в разрезе отложений ангарской свиты приурочен к подошве пачки брекчированных мергелистых известняков на контакте с массивными доломитами булайской свиты. Глубина залегания горизонта 2765м. Удельные дебеты по скважинам достигают 11 лс.
Отложения булайской свиты представлены преимущественно плотными массивными породами. Трещиноватость пород отличается лишь в кровле верхней и нижней подсвит. К этим интервалам приурочены VIII и IX водоносные горизонты.
VIII водоносный горизонт приурочен к трещиноватым доломитам верхнебулайской подсвиты. Водоупорами являются плотные разности доломитов. Глубина залегания водоносного горизонта 335–347м. мощность горизонта 9–19м. Удельный дебет скважин около 0002лс. Коэффициент фильтрации до 01мсут.
IX водоносный горизонт приурочен трещиноватым доломитам верхней части разреза нижнебулайской подсвиты. Глубина залегания водоносного горизонта 431м. при мощности 3–5м. Водообильность горизонта незначительна. Коэффициент фильтрации 0013–0057мсут.
Продуктивная толща и подстилающие породы являются практически безводными. Вскрытые в продуктивной толще рассолы образуют небольшие скопления межкристаллической рапы.
Питание подземных вод развитых в районе месторождения осуществляется за счет атмосферных осадков и поверхностных вод. Область питания соответствует области распространения водоносных горизонтов а также для глубоких горизонтов распространяется до мест выхода водоносных горизонтов на поверхность. По химическому составу подземные воды района месторождения делятся на три зоны.
Первая зона распространена до глубины 100м где развиты пресные бикарбонатно–кальциево–магневые воды с минерализацией до 1гл.
Вторая зона простирается до кровли первого пласта соли. Воды хлоридно–сульфатно–натоиево–кальциевые слабосолоноватые и соленые с минерализацией 1–10гл характеризующиеся сульфатной агрессией по отношению к бетону.
Третья зона – продуктивная толща. Встречены хлоридно–кальциево–натриевые рассолы с минерализацией до 313гл. В них отмечено большое содержание брома калия хлоридов кальция.
Согласно приведенной гидрогеологической характеристике Тыретское месторождение соли характеризуется сложными гидрогеологическими условиями. Определенные трудности встречаются при проходке стволов шахты в сильно обводненных породах ангарской и булайской свит в связи с чем предусмотрены специальные методы проходки. Помимо этого для исключения проникновения подземных вод в горные выработки проектом проходки стволов предусмотрена изоляция всего обводненного интервала. Условия отработки у пласта соли в пределах которого находится опытный участок простые. Нормальные условия разработки опытного участка обеспечиваются мощной (45–48) вышележащей водоупорной толщей состоящей из четырех верхних пластов соли (I II III IV) и разделяющих их пластов плотных доломитов и доломитоангидритов.
3Основные параметры шахты
На основании проекта в качестве границы шахтного поля принят контур запасов В + С1. Конфигурация запасов всех трех пластов в плане имеет простую форму в виде многоугольников с прямолинейными строками. Пласты каменной соли имеют слабонаклонное залегание. Угол падения пласта с юго–запада на северо–восток составляет 10. Основные параметры шахтного поля приведены в таблице 1.1.
Таблица 1.1 – Основные параметры шахтного поля
Наименование показателей
Размеры шахтного поля
Горизонтальная площадь
Глубина залегания от поверхности почвы
Годовая производительность рудника была установлена утвержденным проектом заданием 1968 года и подтверждена заданием на его корректировку в размере 2 млн. тонн. В соответствии с определенными в проекте размерами общерудничных и эксплутационных потерь соли ниже в таблице 1.2. приведены запасы каменной соли в границах шахтного поля и произведен расчет срока службы рудника.
Таблица 1.2 – Запасы каменной соли в границах шахтного поля
Запасы каменной соли млн. тонн в условиях границы сортности
Продолжительность отработки лет
В том числе высший и первый сорт
Общий срок службы рудника на базе запасов категории В+С2 с учетом развития и затухания горных работ составляет ориентировочно 62 года. Резервом для увеличения срока службы рудника являются запасы категории С2 после их доразведки и перевода в более высокие категории. Режим работы рудника принят в соответствии с заданием на проектирование: количество рабочих дней в году – 305;количество рабочих смен в сутки – 3; продолжительность рабочей смены – 7 часов.
4Вскрытие месторождения
Вскрытие месторождения производится двумя стволами (Главным и вспомогательным). Краткая характеристика стволов приведена в таблице 1.3.
Таблица 1.3 – Краткая характеристика стволов
Наименование характеристик стволов
Вспомогательный ствол
вентиляционный горизонт
– транспортный горизонт
Выдача соли исходящей струи аварийный подъем
Спуск людей материалов оборудования подача свежей струи.
Два скипа 3СНП–1 инспекторская клеть 1КН2–1
Две клети 1КН 3.2–1 лестничное отделение
Пропускная способность ствола по воздуху при скорости 8 мс
Стволы пройдены до промышленного пласта при этом глубина главного ствола (62037) определяется из условий расположения бункера соли комплекса загрузки скипов и горизонта сбора просыпи соли.
В связи с применением комбайнового способа добычи комплекс подземного дробления соли не предусматривается.
Запасы пласта вскрываются и подготавливаются двумя горизонтальными выработками: 1) транспортная расположенная на почве пласта 2) вентиляционная расположенная у кровли пласта.
Главные транспортные вентиляционные и конвейерные выработки вскрывающие шахтное поле делят его на южное и северное крыло с примерно равными запасами каждое крыло шахтного поля разделяется на три участка. Длина участков колеблется в пределах от 1000 до 2000 м ширина определяется длиной камер до 550 м. Запасы каждого участка подготавливаются двумя фланговыми транспортными и вентиляционными штреками. Каждый участок отрабатывается от границы утвержденных запасов к центру шахтного поля. В одновременной обработке будет находиться один участок. Вскрытие запасов VШ и VП пластов предполагается осуществить в конце отработки запасов пласта с помощью конвейерного и транспортного уклонов проходимых от околоствольного двора. Способ проветривания нагнетательный вентиляторно–калориферный установка расположена на поверхности у вспомогательного ствола. Схема проветривания центральная воздух в шахту попадает по вспомогательному стволу далее по горизонтам –81 и –765 м в очистные камеры исходящая вентиляционная струя воздуха поступает в горизонт –71 и далее к главному стволу по которому выдается на поверхность. Температура соли промышленного пласта 15–155 0С.
5 Горнокапитальные и подготовленные выработки
5.1Способы проведения выработок
Горные выработки на соляных рудниках проводят с помощью проходческо–очистных комбайнов (в дальнейшем по тексту – комбайнами) буровзрывных работ или комбинированным способом.
Известно что наибольшая производительность труда рабочего и наименьшая стоимость проходки обеспечивается при проведении выработок комбайнами.
Комбайновый способ проведения выработок характеризуется простотой организацией работ проходческого цикла а так же что проходчики выполняют функции машиниста комбайна т.е. освобождается от многих ручных операций присущих буровзрывному способу проходки.
Для транспортировки горной массы от проходческих работ применяются шахтные самоходные вагоны на пневмошинном ходу 5ВС–15м
5.2Околоствольный двор
Околоствольный двор запроектирован из комплекса выработок транспортного и вентиляционного горизонтов в районе Вспомогательного и Главного стволов предназначенных для создания нормальных технологических условий проходки выработок.
Первоначально на транспортном горизонте (абс.отм.–31м) от сопряжения Вспомогательного ствола с применением буровзрывных работ проходится камера перегрузки и монтажно–перегрузочная камера. На период проходки этих камер от ствола устраивается временный рельсовый путь колеи 750мм. из рельсов Р–24.
В камере перегрузки с помощью монтажной лебедки ЛГРУ–10 грузоподъемностью 10тс. и ручных лебедок грузоподъемностью 5тс. осуществляется монтаж первого комбайна У–20 КСА. Ориентировочные размеры камеры для монтажа комбайна: ширина 6–8м высота 4м длина 15м. Затем производится сборка бункера–перегружателя БП–3А и самоходного вагона 5ВС–15м.
После завершения работ по сборке оборудования первого проходческого комплекса и устройства механизации обмена вагонеток в северо–восточном сопряжении Вспомогательного ствола выполняются работы по сбойке стволов между собой по проектной трассе на горизонте –81м т.е. проходится главная ветвь руддвора и заезд к Главному стволу.
Монтаж вспомогательного транспортного оборудования спускаемого по вспомогательному стволу в разобранном виде предусматривается выполнять в монтажно–перегрузочной камере которая оборудуется электрическим подвесным (однобалочным) краном грузоподъемностью 10тс.
Камера перегрузки предназначена для механизации погрузочных работ материалов оборудования и т.д. спускаемых по Вспомогательному стволу в вагонетках или на платформах. Погрузка их на машины 1ВОМ–А будет осуществляться при помощи электрической тали грузоподъемностью 5тс. (предусматривается два монорельсовых пути с талями).
В состав околоствольного двора включены также следующие выработки проходимые комбайновым способом.
На транспортном горизонте –81м;
-Главная ветвь руддвора;
-Заезд к Главному стволу;
-Обгонная ветвь руддвора;
-Камеры: ожидания ЦПП склад противопожарных материалов;
-Транспортный уклон горизонтов –81–71м (угол наклона выработки составляет 6º).
На вентиляционном горизонте –71м.
-Заезд к Главному стволу (включая сбойки с вентиляционным квершлагом в пределах околоствольного двора)
-Камера участковой подземной электроподстанции №1 (УПП №1).
В выработках непосредственно примыкающих к транспортному уклону гор. –81–71м. разделываются камеры вентиляционных дверей (2камеры) в каждой камере возводится бетонная перемычка с двумя вентиляционными металлическими дверями открывающимися в противоположные стороны. Для уменьшения аэродинамического давления на дверь в период открытия предусмотрены специальные жалюзи; кроме того предусматривается устройство привода для открытия и закрытия дверей с кнопочным управлением. Для предупреждения возникновения короткого замыкания вентиляционной струи запроектировано шлюзование и блокировка дверей.
На транспортном горизонте вблизи сопряжения Главного ствола на участке сбойки сопряжения с заездом к Главному стволу возводятся две бетонные перемычки каждая с двумя деревянными дверями обитыми листовым железом и открывающимися в противоположные стороны в целях предупреждения короткого замыкания вентиляционной струи; эти вентиляционные двери сооружаются по месту производства работ.
Известно что продуктивные пласты каменной соли и вмещающие солевые породы обладают значительной вязкостью. Эти свойства пород позволяют обнажать кровлю на больших площадях проводить и поддерживать без крепления горные выработки проходимые в пределах V пласта каменной соли креплению не подлежат; выработки проходимые по породе в зависимости от физико–механических свойств и степени засоленности необходимо крепить. В соответствии со СНиП II–94–80– «Нормы проектирования подземные горные выработки» п.4.17. и 4.18. – и осадочных пород (исключая каменную соль) расположенных вне зоны воздействия очищенных работ и других выработок в породах I категории устойчивости (величина смещения пород на контуре поперечного сечения выработки за весь срок её службы без крепи до 50мм. – устойчивое состояние I свыше 50 до 200мм. – среднеустойчивое II свыше 200 до 500мм. – неустойчивое III) следует применять анкерную или набрызгбетонную крепь толщиной не менее 30мм; для II категории устойчивости – монолитную бетонную крепь комбинированную из набрызгбетона толщиной не менее 50мм. с анкерами металлическую податливую крепь без обратного свода и т.п.
В выработках проходимых в каменной соли I категории устойчивости (при смещении кровли в однородных породах до 200мм. и в слоистых до 150мм.) допускается поддержание выработок без крепи.
Учитывая что заезд к Главному стволу на горизонте –71м. частично будет пройден комбайном У–20КСА по породе (ангидрид синевато серый) настоящим рабочим проектом предусматривается применить анкерное крепление кровли выработки находящейся непосредственно в породе.
В камере привода магистрального конвейера находящейся вблизи выработки околоствольного двора на абсолютной отметке –65.0м. предусматривается возвести железобетонный ствол по распорной схеме – в связи со значительным сроком службы камеры а также ввиду наличия над соляной пачкой в кровле камеры породы с глинистыми включениями (доломит засолоненный глинистый).
Вблизи околоствольного двора в транспортном квершлаге должны быть сооружены две бетонные перемычки с металлическими противопожарными дверями закрывающимися по ходу вентиляционной струи.
5.3 Протяженные выработки
Транспортные и вентиляционные протяженные выработки предназначенные для вентиляции доставки материалов и оборудования пешеходного сообщения с очистными забоями предусматривается проходить комбайнам У–20КСА. Поперечное сечение выработки (1766м2) определено по условиям вентиляции и обеспечения людей. В этих выработках (квершлагах и штреках) движение машин 1ВОМ–А должно осуществляться со скоростью обеспечивающей безопасность людей но не более 20 кмч; для обозначения свободного прохода для людей в почве выработки устраивается разграничительная рейка. Двухстороннее движение транспортных средств в выработках запрещается.
Конвейерный квершлаг и конвейерный уклон (угол наклона выработки 5º) предназначенные для транспортировки соли в бункер у Главного ствола предусматривается пройти соответственно комбайнам У–20КСА и 4ПП2С. Поперечное сечение выработки после монтажа ленточного конвейера допускает движение машины 1ВОМ–А при исключении возможности нахождения в ней людей не связанных с работой машины и скорости движения не превышающей 10 кмч. В начале этих выработок а также в сбойках примыкающих к ним должны быть установлены освещенные запрещающие знаки.
Конвейерные штреки (площадь сечения 102м2) предназначенные для транспортировки соли скребковыми конвейерами предусматривается движение машины 1ВОМ–А с ограничениями аналогичными для конвейерного квершлага и уклона.
По трасе панельных конвейерных штреков в местах перегрузок соли с конвейера на конвейер предусмотрены так называемые «камеры перегрузки» представляющие местные уширения–ниши; раскоска ниш выполняется комбайном 4ПП2С.
По трассе конвейерного квершлага запроектированы «камеры перехода» – уширения выработки для установки пешеходного моста через конвейер раскоса уширении производится также комбайном 4 ПП 2С.
5.4 Камерные выработки
Для обеспечения технологического звена по выдаче соли из шахты на поверхность запроектированы выработки погрузочного комплекса Главного ствола включающие камеры общего назначения и восстающие выработки:
-Камера питателей на горизонте –99м.
-Бункер соли у Главного ствола;
-Вентиляционно–ходовой восстающий горизонтов – 9965м.;
-Горизонт сбора просыпи соли от скипового подъема на горизонте – 135м. (ходок–сбойка и бункер просыпи) с вентиляционно–ходовым восстающим горизонтов – 135–81м.
Учитывая что соль обладает свойством слёживаемости рекомендуется производить ее полный выпуск из бункера до начала междусменного перерыва а также перед общерудничными выходными и праздничными днями. Для исключения короткого замыкания вентиляционной струи через бункер Главного ствола предусматривается металлическое перекрытие верхней части бункера и специальное шиберное устройство.
Для обеспечения электроэнергией потребителей предусматривается проходка камер центральной подземной подстанции (ЦПП) и участковых подстанций – УПП №1–6.
Камерные выработки намечается проходить в основном комбайном 4ПП–2С. В соответствии и «Инструкцией по безопасному применению самоходного (нерельсового) оборудованию в подземных условиях» камеры располагаются за пределами околоствольного двора по трассе транспортного квершлага. Для обеспечения обособленного проветривания камер предусматривается их сбойка при помощи вентиляционных скважин диаметром 500мм. и специальных подводящих ходков на горизонте –71м. с вентиляционным квершлагом по которому удаляется из шахты исходящая вентиляционная струя.
Для производства добычи соли и дальнейшей эксплуатации рудника запроектированы следующие камеры вспомогательного назначения:
-Камера ремонтного пункта на I пост включающая: ремонтную камеру для сварочных работ участок мойки детали склад запчастей и электросверл; перфораторную;
-Гараж–стоянка для машин 1ВОМ–А и I ВЛГ;
-Камера подземной уборной оборудованная специальной ассенизационной вагонеткой ВАШ–2 на колею 750мм. (транспортировка вагонетки по выработком будет осуществляться на машине 1ВОМ–А);
-Камера склада ГСМ емкостью 3м3 в составе комплекса выработок и камер в том числе склад резервуарного хранения склад тарного хранения пункт заправки насосная;
-Камера диспетчера расположенная вблизи границы околоствольного двора в сбойке между транспортным и конвейерным квершлагами.
По трассе конвейерного уклона и квершлага проходятся соответственно:
-Камера привода магистрального конвейера на абсолютной отметке–65м. (комбайновый и буровзрывной способы проходки);
-Камера натяжной станции магистрального конвейера в районе сопряжения квершлага с главным штреком опытного участка а также «камеры переходов» через конвейер (раскоска участков квершлага комбайном 4ПП 2С).
В конце восточной части панельного конвейерного штрека №2 в целях вентиляции и обеспечения запасного выхода с участка опытных работ предусмотрен вентиляционно–ходовой восстающий №2 горизонтов –81–71м.; вентиляционно–ходовой восстающий №1 запроектирован вблизи склада ГСМ – в целях обеспечения сообщения между транспортным и вентиляционным горизонтами.
Механизация горных работ
Перед началом проведения очистных работ были проведены подготовительные работы комбайном Урал–70 в комплексе с самоходным вагоном
Выбор оборудования и расчёт производительности
Исходя из данных практики для сравнения вариантов принимаем следующие комбайны: Урал–20 А и Урал–10 Р технические характеристики которых приведены в таблице 2.1.
Таблица 2.1 – Технические характеристики комбайнов
Производительность тмин;
Суммарная номинальная мощность двигателей комбайна кВт не более;
Суммарная номинальная мощность двигателей основного исполнительного органа кВт не более.
Расчёт производительности для комбайна Урал–20 А
Для комбайнов роторно–планетарного типа теоретическая производительность определяется по формуле:
где S – площадь сечения проводимой выработки S = 202 м2;
V – скорость подачи комбайна мс;
g – плотность породы (для соли g = 21 тм3)
где Руст – величина устойчивой мощности привода исполнительного органа ( кВт где Р – мощность исполнительного органа комбайна Р = 380 кВт)
В – ширина захвата комбайна В = 51 м;
m – высота выработки m = 37 м;
Нw – средние удельные энергозатраты (определяются в зависимости от P m B g) Нw = 095 МДжт
Техническая производительность определяется по формуле:
где kг – коэффициент готовности комбайна принимаем по обобщённым данным kг = 095
Эксплуатационная производительность определяется по формуле:
где kэ – коэффициент учитывающий все виды простоев комбайна по техническим причинам
где А – коэффициент учитывающий регламентированные перерывы в работе (подготовительно–заключительные операции) А = 1;
tп.к – время простоя за смену (определ. конструкцией) tп.к = 15 мин;
tп.о – время простоя по организационным причинам tп.о = 15 мин;
tр – чистое время работы комбайна за смену
где Тсм – продолжительность смены Тсм = 7 часов
где n – число смен в сутки.
Расчёт производительности для комбайна Урал–10 Р
Расчёт производительности комбайна Урал–10 Р аналогичен расчету производительности комбайна Урал–20 А.
Технико–экономическое сравнение вариантов
Определяем эффективный фонд рабочего времени:
где Тк – количество дней в году; Тк = 365 дн.;
Тв – количество выходных дней Тв =52 дн.;
Тп – количество праздничных дней Тп = 12 дн.;
Тб – количество дней болезни Тб = 3 дн.;
Тс – количество дней на выполнение соцобязанностей Тс =2 дн.
То – количество дней отпуска То =52дн.
Определяем коэффициент списочного состава:
где Nсп – списочная численность состава;
NЯВ – явочная численность рабочих.
Таблица 2.2 – Расчёт рабочей силы и фонда заработной платы
Явочная численность чел.
Коэффициент списочности
Списочная численность чел.
Тарифная ставка руб.смену.
Эффективный фонд времени дней
Премиальные доплаты (40% ФЗП) руб.
Доплаты за работу в вечернее и ночное время (165% ФЗП) руб.
Прочие доплаты (5% ФЗП) руб.
Основной фонд заработной платы руб.
Дополнительная заработная плата
Заработная плата с учётом районного коэффициента (kр =13) руб.
Северные надбавки 30%
Итого основной и дополнительный фонды заработной платы с учётом районного коэффициента северных надбавок и отчислений на социальное страхование руб.
Таблица 2.3 – Расчёт капитальных затрат и амортизационных отчислений
Оптовая цена за единицу руб.
Транспортные расходы (15%) руб.
Заготовительно–складские расходы (12%) руб.
Монтаж оборудования (10%) руб.
Балансовая стоимость руб.
Норма амортизационных затрат %
Сумма амортизации руб.
Таблица 2.4 – Затраты на вспомогательные материалы
(30% от оптовой цены) руб.
Неучтённые материалы (10%) руб.
Расход и стоимость электроэнергии.
Общая сумма затрат на электроэнергию может быть определена по формуле:
где Р – заявленная мощность
где N – установленная мощность кВт;
kуст –коэффициент использования установленной мощности
W – расход электроэнергии
где kим – коэффициент использования мощности kим = 08;
tсм – продолжительность смены tсм = 7 часов;
nсм – количество смен в сутки nсм = 3 смены;
а – тариф за 1 кВт заявленной мощности а = 98 руб.
b – тариф за 1 кВт·ч потребляемой энергии b = 060 рубкВт·ч
Расход и стоимость электроэнергии для комбайна Урал–20 А.
Расход и стоимость электроэнергии для комбайна Урал–10 Р.
Таблица 2.5 – Калькуляция себестоимости добычи полезного ископаемого
Сумма затрат на годовой объём работ руб.
Заработная плата основная и дополнительная руб.
Начисления на зар.плату 34% (социальные начисления) руб.
Материальные затраты:
Вспомогательные материалы руб.
Содержание и эксплуатация оборудования:
Ремонт оборудования
(150% от амортизации) руб.
Услуги на содержание оборудования
(15% от амортизации) руб.
(25% от суммы всех перечисленных затрат) руб.
Цеховая себестоимость руб.
Капитальные затраты К1 = 5296900000 руб.
Эксплуатационные затраты С1 = 6400108405руб.
Производительность комбайна в год:
Удельные капитальные затраты Куд рубт
K уд 1 = К1Qг = 52969000002 019 18024 = 2623 рубт
Удельные эксплуатационные затраты Суд рубт
C уд 1 = С 1 Q г = 64001084052 019 18024 = 3170 рубт
Капитальные затраты К2 = 4395300000 руб.
Эксплуатационные затраты С2 = 5358519150 руб.
Удельные капитальные затраты Куд2 рубт
K уд 2 = К2Qг = 43953000001 50945480 = 2912 рубт
Удельные эксплуатационные затраты Суд2 рубт
C уд 2 = С 2 Q г = 5358519150 1 50945480 = 3550 рубт
Так как Куд1 Куд2 Суд1 Суд2 то следовательно комбайн Урал–20 А эффективнее комбайна Урал–10 Р.
Проверочный расчёт мощности привода комбайна Урал–20 А
Рассчитаем среднюю величину глубины стружки снимаемую одним резцом м:
где D – диаметр по резцам м;
Vп – скорость подачи комбайна мс;
Vр – скорость резания мс;
mз – число забойных резцов в одной линии резания.
Средняя ширина среза одного резца м:
tср = tу hср = 25 . 00087 = 002 м
где tуд – удельная ширина среза.
Расчёт коэффициентов:
Определим коэффициент обнажения забоя:
Угол бокового развала борозды резания:
где А – сопротивление соли резанию кНм;
Среднее значение силы резания на передней грани резца кН:
где b – ширина режущей кромки резца м;
kц – коэффициент влияния формы передней грани резца на усилие резания;
kу – коэффициент влияния формы угла резания на усилие резания на передней гране резца;
kот – коэффициент учитывающий степень отжима соли;
kф – коэффициент учитывающий влияние формы передней грани резца;
b - угол наклона резца по направлению подачи.
Коэффициент влияния глубины стружки на усилие подачи:
Временное сопротивление соли одноосному сжатию кНм2:
Проекция площади затупления резца SЗ на плоскость резания м:
где kфр – коэффициент влияния формы резца на площадку затупления:
DU – величина линейного износа на задней грани м.
Коэффициент влияния объемного состояния соли под задней гранью резца на величину усилия подачи:
где а – коэффициент трения при перемещении комбайна.
Сила отжимающая резец от забоя кН:
Суммарное значение силы резания на резце кН:
Мощность затрачиваемая на резание кВт:
где nр – количество резцов находящихся в постоянном контакте с забоем.
кВт что допустимо при установленной мощности в 380 кВт.
Исходя из данных практики для сравнения вариантов принимаем следующие самоходные вагоны: 5ВС–15 и 5ВС–10 технические характеристики которых приведены в таблице 3.1.
Таблица 3.1 – Технические характеристики самоходных вагонов
Скорость движения кмч.
Мощность двигателей кВт.
Вместимость кабельного барабана м.
Расчёт производительности для 5ВС–15
Действительная производительность (тч) самоходного вагона
где Gс – грузоподъемность самоходного вагона т;
kн.с = 085 ÷ 09 – коэффициент наполнения самоходного вагона солью;
nр – возможное число рейсов одного вагона ч.
где tоб – Время одного оборота самоходного вагона с;
где tп – время погрузки самоходного вагона с.;
tдв – время движения самоходного вагона от комбайна до пункта разгрузки и обратно с;
tр – время разгрузки самоходного вагона с.
tп = Gс tц kман k р Qтех kн y
где =115 – коэффициент учитывающий время на отбор негабаритной руды в забое;
kман =11 ÷ 12 – коэффициент учитывающий время маневров самоходного вагона у комбайна;
k р =11 – коэффициент учитывающий время затрачиваемое на техническое обслуживание комбайна;
Qтех – техническая производительность комбайна тмин.
где L – расстояние откатки м;
kдв = 125 ÷ 135 – коэффициент учитывающий время в связи с изменением скорости и остановки самоходного вагона в пути;
vср – средняя скорость движения самоходного вагона мс.
Время разгрузки самоходного вагона у рудоспуска tр – 30 ÷ 60 с.
tдв = 2L kдв vср = 2*270*12519 = 3553 с
tп = Gс tц kман k р Qтех kн y = 115*15*60*11*11 532*09*21 = 1246 с
tоб = tп + tдв + tр = 1246 + 3553 + 30 = 5099 с
nр = 3600tоб = 3600 5099 = 7
Qд = Gсkн.сnр = 15*09*7 = 945 тч
Qсмен = 7*945 = 6615 тсмену
Qсут = 3*6615 = 19845 тсутки
Qгод = Qсут Тр = 19845*301 = 5973345 тгод
Расчёт производительности для 5ВС–10 тгод
где Gс – грузоподъемность самоходного вагона т;
где tоб – время одного оборота самоходного вагона с;
где = 115 – коэффициент учитывающий время на отбор негабаритной руды в забое;
kман = 11 ÷ 12 – коэффициент учитывающий время маневров самоходного вагона у комбайна;
k р = 11 – коэффициент учитывающий время затрачиваемое на техническое обслуживание комбайна;
tп = Gс tц kман k р Qтех kн y = 115*10*60*11*11 532*09*21 = 83 с
tоб = tп + tдв + tр = 3553 + 83 + 30 = 4683 с
nр = 3600tоб = 3600 4683 = 8
Qд = Gсkн.сnр = 10*09*8 = 72 тч
Qсмен = 7*72 = 504 тсмену
Qсут = 504*3 = 1512 тсутки
Qгод = Qсут Тр = 1512 * 301 = 455112 тгод
По техническому сравнению целесообразно применять самоходный вагон 5ВС–15 так как самоходный вагон 5ВС–10 не будет справляться с планируемой годовой производительностью.
ТВ – количество выходных дней ТВ =52 дн.;
Тп – количество праздничных дней Тп = 10 дн.;
То – количество дней отпуска То =52дн
Таблица 3.2 – Расчёт рабочей силы и фонда заработной платы
Итого основной и дополнительный фонды заработной платы с учётом районного коэффициента и северных надбавок руб.
Таблица 3.3 – Расчёт капитальных затрат и амортизационных отчислений
Таблица 3.4 – Расчет затрат на вспомогательные материалы
Смазочные материалы (30% от оптовой цены) руб.
где Р – заявленная мощность
kуст – коэффициент использования установленной мощности
W – расход электроэнергии.
а – тариф за 1 кВт заявленной мощности а = 98 руб
b – тариф за 1 кВт·ч потребляемой энергии b = 060рубкВт·ч
Расход и стоимость электроэнергии для самоходного вагона 5ВС – 15
Р = N ·kуст = 84 · 05 = 42 кВт·ч
W = kим· tсм· nсм· Тр· N = 08 · 7 · 3 · 301 · 84 = 42477120 кВт·ч
Сэ = Р · а + W · b = 42 · 98 + 42477120 · 060 = 25897872 руб.
Расход и стоимость электроэнергии для самоходного вагона 5ВС – 10
Р = N ·kуст = 84 · 05 = 42 кВт
Сэ = Р · а + W · b = 42 · 98 + 42477120 · 060= 25897872 руб.
Таблица 3.5 – Калькуляция себестоимости добычи полезного ископаемого
Ремонт оборудования (150% от амортизации) руб.
Услуги на содержание оборудования (15% от амортизации) руб.
Цеховые расходы (25% от суммы всех перечисленных затрат) руб.
Самоходный вагон 5ВС – 15
Капитальные затраты К1 = 732550000 руб.
Эксплуатационные затраты С1 = 1165607481руб.
Производительность самоходного вагона в год:
Qгод = Qсут Тр = 19845*301 = 59733450 тгод
К уд1 = К1 Qг = 732550000 597 33450 = 1226 рубт
С уд1 = С1 Qг = 1165607481 597 3345 = 1951 рубт
Самоходный вагон 5ВС – 10
Капитальные затраты К2 = 676200000 руб.
Эксплуатационные затраты С2 = 1092692638руб.
Qгод = Qсут Тр = 1512 * 301 = 455 11200 тгод
К уд2 = К2 Qг = 676200000 455 11200 = 1486 рубт
С уд2 = С2 Qг = 1092692638 455 11200 = 2401 рубт
Так как Куд1 Куд2 Суд1 Суд2 то следовательно самоходный вагон 5ВС – 15 эффективнее самоходного вагона 5ВС – 10.
Тяговый расчет самоходного вагона 5ВС–15
Скорость движения самоходного вагона 5ВС – 15;
Fгр = (G + G0) (w – i) = (150 + 160) (80 – 5) = 23250 Н.
где G – грузоподъемность самоходного вагона кН;
G0 – собственный вес самоходного вагона.
По динамической характеристике имеем для параллельно включенных двигателей (Е = 500 В) гр = 85 кмч;
Fпор = G0 (w + i) = 160 (80 + 5) = 13600 Н.
По динамической характеристике имеем (Е = 500 В) пор = 10 кмч;
Проверка мощности двигателей.
Сила тяги на окружности колес при движении
Fк = 3600N гр1 = 3600*80*09 85 = 37090 Н.
где N – Мощность ходовых двигателей кВт; = 09 – к. п. д.:
Сопротивления движения с грузом при установившейся скорости
Wгр = (G + G0) (w – i) = (150 + 160) (80 – 5) = 23250 Н.
Fк > Wк следовательно мощность двигателей достаточна
Проверка возможности буксования при трогании машины по мокрой дорогое.
Наибольшая сила тяги самоходного вагона при всех приводных колесах
Fк = 1000Рсц = 1000*04*310 = 124000 Н
где = 04 – коэффициент сцепления колес с мокрым полотном дороги;
Рсц = G + G0 = 150 + 160 = 310 кН.
Fmax > Wгр следовательно буксирования не будет.
Тормозной путь груженной машины при движении по штреку
Lт = 385²н (1+ kи ) 1000 + w – i + н 36 kиtр = 385*85² (1+ 06)1000*04 + 80 – 5 + 8536*25 = 212 м
что допустимо где н = гр = 85 кмч; kи = 06; tр = 05 с.
Эксплутационный расчет
Время движения самоходного вагона 5ВС – 15
tдв = 3600L( 1vгр + 1 vпор) kдв = 3600*0.27(18.5 + 110)*135 = 286 с.
Время погрузки самоходного вагона 5ВС – 15
tп = Gkн.кtцVлkнnгрγ*kремkман = 15*0.95*20.05*06*2*21*11*125 = 1246 с.
Время оборота самоходного вагона 5ВС – 15
tоб = tдв + tп + tр = 286 + 1246 +30 = 4406 с.
На участке применяется два самоходных вагона с остановкой комбайна.
Производительность самоходного вагона 5ВС – 15 с условиями работы
Qд = nв 3600G kн.вТ tоб = 2*3600*15*095*74406 = 1630 тсмену
Выбор и детальный расчет ленточного конвейера
Выбор ленточного конвейера производится по заданной производительности (грузопотоку) и условиям его эксплуатации.
Расчет ленточного конвейера сводится к определению: ширина ленты сопротивлений при ее движении на прямолинейных и криволинейных участках статических напряжений в ленте тяговой силы и мощности двигателя конвейера.
Расчетный часовой грузопоток необходимый для выбора типа конвейера работающего комбайна принимается равным технической производительности машины. Значение его в этом случае определяется:
где Кн – коэффициент неравномерности грузопотока = 15
Qсм – сменный грузопоток поступающий на конвейер = 1630 тсм
tпо – плановое оперативное время работы конвейерной установки в смену часов
Тсм – продолжительность смены = 7 ч.
tпп – планируемые перерывы в работе конвейера в течении смены = 05 ч.
Qч = 15 1630 65 = 376 тч
Tпо = 7 – 05 = 65 ч.
Перед выбором конвейера по заданной производительности определяется ширина его ленты:
B = Q (160 · К · V · γ · ) Вп
где B – расчетная ширина ленты м;
Q – расчетный часовой грузопоток тч;
0 – коэффициент учитывающий желобчатость ленты;
К = 30 – коэффициент зависящий от угла наклона боковых роликов;
V = 25– скорость движения ленты мс;
γ = 21 – насыпная плотность материала тм3;
= 10 – коэффициент загрузки ленты;
Вп – паспортная ширина ленты выбранного конвейера м.
Ориентировочно выбираем конвейер 1Л80 имеющий ширину ленты 800 мм.
Паспортная ширина ленты проверяется также по крупности транспортируемого материала. Для рядового и сортированного материала соответственно:
где аmax = 300 максимальный размер кусков транспортируемого материала мм.
Определение линейного веса отдельных частей груженной и порожней ветвей конвейера
Линейный вес груза Нм:
где q – вес 1 м. груза на конвейере ;
g – ускорение силы тяжести = 98 м с²
q = 376 · 981 (36 · 2) = 5123 Нм
Линейный вес ленты qл = 150 Н м ;
Линейный вес вращающихся частей роликоопор определяются по формулам Нм:
где mр = 85 и mр = 220 – вес вращающихся частей роликоопор соответственно на груженой и порожней ветвях ленты Н;
lр = 13 и lр = 26 – расстояние между роликоопорами соответственно на
порожней и груженой ветвях ленты м.
qр = 25513 = 1961 Нм
qр = 22026 = 846 Нм.
Определение сопротивлений при движении ленты
Сопротивление на груженой и порожней ветвях конвейера определяется по формулам Н:
Wгр = (q + qп) · L · + qр · L ·
Wп = qп · L · + qр · L ·
где = 003 – коэффициент сопротивления движению ленты;
L = 620 – длина конвейера м;
= 0 – угол наклона конвейера.
Wгр = (5153 + 150) · 620 · 003 + 654 · 620 ·003 = 1353522 Н
Wп = 150 · 620 · 003 + 846 · 620 ·003 = 436356 Н
Сопротивление очистных устройств скребкового и щеточного типа можно определить по формуле Н:
где qоч = 600 и 400 – удельное сопротивление очистки Нм ширины ленты;
Расчет статических натяжений методом обхода по контуру
Таблица 3.6 – Расчет натяжений в ленте
S2 = S1 + W1–2 = S1 + 436356
S3 = 107 · S1 + W1–2 = 107 S1 + 436356
S4 = 107 S1 + 436356
S5 = 107 · (107 S1 + 436356 ) = 114 S1
S6 = 114 S1 + 4669 + 436356 = 114 S1 + 903256
S7 =107 · (114 S1 + 903256) = 122 S1 + 966484
S8 = 122 · S1 + 966484 + 1353522 = 122 · S1 + 2320006
S9 =107 · (122 · S1 + 2320006) = 13 ·S1 + 2482406
S10 =13 ·S1 + 24824 + 480 + 320 = = 13 ·S1 + 2562406
Определяем натяжение в точке 1 используя уравнение Эйлера. В нашем случае это уравнение будет:
где eα =817 – тяговый фактор приводных барабанов;
e = 272 – основание натуральных логарифмов;
=03 – коэффициент ленты о барабан;
α = 400 – угол обхвата лентой приводных барабанов.
S10 = 13 ·S1 + 2562406
·S1 + 2562406 = 817 · S1
Полученное расчетное наименьшее значение натяжения ленты на груженой ветви проверяют по условию допустимого провеса ленты между верхними роликоопорами по формуле:
Sгр. мин 5 · (q + qл) · lр
2152 5 · (5123+150) · 13
2152 430495 что удовлетворяет условию.
Определение усилий на натяжном устройстве и расчет ленты на прочность
Усилие на натяжном устройстве (вес натяжного груза) определяется как сумма натяжений ленты в точках ее набегания и сбегания с натяжного барабана Н:
Fн = Sннб + Sнсб =809336 +835445 = 1644781 Н
Выбранная лента конвейера должна иметь необходимый запас прочности который определяется расчетным путем. Для резинотросовых лент запас прочности определяется по формуле:
mф = Sразр Smax ≥ [m]
mф = 1500 305 = 492 ≥ 7 что удовлетворяет условию.
Определение тягового усилия и мощности двигателя приводной станции конвейера
Тяговое усилие W0 (H) развиваемое приводом конвейера с учетом сопротивления на приводном барабане:
W0 = Sнб – Sсб + fп · (Sнб + Sсб)
где Sнб – натяжение в точке набегания ленты на первый приводной барабан Н;
Sсб – натяжение в точке сбегания с приводных барабанов Н;
fп = 004 – приведенный коэффициент трения в подшипниках вала приводного барабана.
W0 =304728 – 37298 + 004 · (304728+37298) = 281111 Н
Тогда суммарная расчетная мощность двигателя Nдв (кВт) приводной станции конвейера может быть определена:
Nдв = Kp · W0 · V (1020 · )
где Kp = 115 – коэффициент резерва мощности;
V = 2 – скорость движения ленты мс;
= 092 – коэффициент полезного действия механической передачи редуктора.
Nдв = 115 · 281111 · 2 (1020 · 092) = 689 кВт
Принимаются два двигателя типа МА36 – 42 4 мощностью по 375 кВт каждый.
Выбор и расчет ленточного конвейера 1ЛУ100
Где Кн – коэффициент неравномерности грузопотока = 15
Qсм – сменный грузопоток поступающий на конвейер = 3260 тсм
tпо – плановое оперативное время работы конвейерной установки в смену часов
Qч = 15 3260 65 = 7523 тч
V = 2– скорость движения ленты мс;
Ориентировочно выбираем конвейер 1ЛУ100 имеющий ширину ленты
Определение линейного веса отдельных частей груженой и порожней ветвей конвейера
q = 7523 · 981 (36 · 16) = 12813 Нм
Линейный вес ленты qл = 1000 Н м ;
Линейный вес вращающихся частей роликоопор определяются по
где mр = 250 и mр = 500 – вес вращающихся частей роликоопор соответственно на груженой и порожней ветвях ленты Н;
lр = 125 и lр = 25 – расстояние между роликоопорами соответственно на порожней и груженой ветвях ленты м.
qр = 250125 = 200 Нм
qр = 50025 = 200 Нм.
Сопротивление на груженой и порожней ветвях конвейера Н
Wгр = (q + qл ) . L . w + qр . L . w
L = 700 – длина конвейера м;
Wгр = (1281.3 + 1000) . 700 . 003 + 200 . 700 . 003 = 521073 Н
Wп = 1000 . 700 . 003 + 200 . 700 . 003 = 25200 Н
Суммарная мощность двигателей приводной станции конвейера
V = 16 – скорость движения ленты мс;
W0 = Kp . (Wп + Wг)
где Kp – коэффициент неучтенных сопротивлений = 13
W0 = 13 . (521073 + 25200) = 1004995 Н
Nдв = 115 . 1004995 . 16 = 2009 кВт
Принимаем два двигателя типа МА 36 – 42 4 мощностью по 100 кВт каждый.
Экономическая часть для конвейерного транспорта
Таблица 3.7 – Расчёт рабочей силы и фонда заработной платы
Таблица 3.8 – Расчёт капитальных затрат и амортизационных отчислений
Таблица 3.9 Затраты на вспомогательные материалы
Смазочные материалы
Расход и стоимость электроэнергии
Расход и стоимость электроэнергии для ленточного конвейера 1Л 80
Р = N ·kуст = 2 · 375 · 05 = 375 кВт·ч
W = kим· tсм· nсм· Тр· N = 08 · 7 · 3 · 301 · 2 · 375 = 379260 кВт·ч
Сз = Р · а + W · b = 375 · 98 + 379260 · 060 = 23123100 руб.
Расход и стоимость электроэнергии для ленточного конвейера 1ЛУ 100
Р = N ·kуст = 2 · 100 · 05 = 100 кВт·ч
W = kим· tсм· nсм· Тр· N = 08 · 7 · 3 · 301 · 2 · 100 = 1011 360 кВт·ч
Сз = Р · а + W · b = 100 · 98 + 1011 360 · 060 = 61661600 руб.
Таблица 3.10 Калькуляция себестоимости добычи полезного ископаемого
Заработная плата основная и
Начисления на зар. плату (34%) руб.
Цеховые расходы (25% от суммы всех
перечисленных затрат) руб.
Капитальные затраты К1 = 15778 00000 руб.
Эксплуатационные затраты С1 = 2248733135руб.
Производительность конвейера в год:
K уд 1 = К1Qг = 15 778000001 471 890 = 1072 рубт
C уд 1 = С 1 Q г = 22487331351 471890 = 1528 рубт
Капитальные затраты К1 = 18 032 00000 руб.
Эксплуатационные затраты С1 = 25885 65635руб.
K уд 1 = К1Qг = 18 032000002 943 780 = 613 рубт
C уд 1 = С 1 Q г = 25885 656352 943780 = 879 рубт
Итого удельные затраты по принятым двум самоходным вагонам 5ВС–15 конвейеру 1Л80 и конвейеру 1ЛУ100 составляют:
K уд =2·K уд 5ВС–15 +K уд 1Л80 +K уд 1ЛУ100 = 2·1226 + 1072 + 613 = 4137 рубт.
С уд =2·С уд 5ВС–15 +С уд 1Л80 +С уд 1ЛУ100 = 2·1951 + 1528 + 879 = 6309 рубт.
Стационарные установки
1 Расчет скиповой подъемной установки
1.1 Выбор подъемного сосуда
Проектная часовая производительность подъема:
где – плановая годовая производительность подъема т; – коэффициент резерва;
N– число рабочих дней в году;
t – число часов работы подъема в сутки ч.
Ориентировочная высота подъема:
где – глубина ствола шахты до откаточного горизонта
– ориентировочная высота состоящая из глубины загрузки скипа высота скипа высота подъемного бункера превышения днища скипа над бункером м.
Оптимальная масса груза в скипе:
где – продолжительность загрузки скипа (ориентировочно) с.
Необходимая вместимость скипа:
где р – насыпная плотность руды тм3.
Принимаем скип с неподвижным кузовом вместимостью Ес=5 м3 типа СН5–164–25; mс=85т. длина аск=164м. ширина вск=114м. высота с прицепным устройством hc=78м.
Масса груза в скипе при полной загрузке:
где Кз – коэффициент заполнения скипа.
Шкивы находятся на одной оси.
где hб– высота приемного бункера м;
hдб – зазор между днищем скипа и бункером м;
hпер– высота переподъема по ЕПБ[17]м;
Rш – максимальный радиус шкива м.
Принимаем высоту копра 54 м.
Длина отвеса каната:
где hзаг – глубина загрузки скипа м.
Концевая нагрузка на канате:
Принимается стальной канат с – 1800 Нмм2.
Расчетная масса 1м. каната:
где – временное сопротивление разрыву Нм2;
z – коэффициент запаса прочности по ЕПБ [17];
р – плотность стали кгм3;
– коэффициент свивки каната.
По ГОСТ 7668–80 принимается канат Рк=608 кгм; dк=395 мм; усилие разрыва всех проволок в канате
Fпр=1085000Н. (1085тс).
Фактический запас прочности каната:
так как ZфZЕПБ принимаем следующий канат
Рк=84 кгм dк=465 мм Fпр=1500000Н (150 тс).
Рк=994 кгм dк=505 мм Fпр=1775000 Н (1775тс).
Принимается канат 505–Г–В–Ж–1764 (180) ГОСТ 7668–80.
1.4 Выбор подъемной машины
Принимается 2–х барабанная машина.
где dк – диаметр каната м; 78 – минимальное отношение диаметра навивки к диаметру каната по ЕПБ [17].
Стандартный ближайший диаметр барабана 4000 мм.
Ширина барабана необходимая для размещения одной ветви каната:
вт – число витков трения по ЕПБ [17];
– зазор между соседними витками мм.
Принимается подъемная машина 2Ц–6х24; Дб=6 м; Вб=24 м.
Необходимая ширина заклиненной части барабана:
Резервная ширина барабана мм
Технические данные машины:
Допустимое статическое натяжение каната Fсд=320000Н. (32 тс).
Допустимая разность натяжений канатов Fср=240000Н. (24 тс).
Статическое натяжение скипа при загруженном скипе:
Разность статических напряжений канатов:
Степень неуравновешенности подъема:
Навеска уравновешивающего каната не производится так как 07.
1.5 Выбор направляющих шкивов
Диаметр шкива по ЕПБ [17]
Принимается шкив ШК–5 Дш=5м.
1.6 Расположение подъемной машины
Минимальное расстояние между осями подъемной машины и отвесом каната:
Максимальное расстояние между осями подъемной машины и отвесом каната:
Длина струны каната:
где l0 – превышение оси барабана над уровнем земли м.
Угол наклона каната к горизонту:
Угол φ не менее 300 согласно ЕПБ [17].
Расстояние между осями копровых шкивов:
где вск – ширина скипа мм;
Δ – зазор между скипами по ЕПБ [17].
Отклонение каната на барабане к наружной реборде от плоскости шкива:
где вр – расстояние между внутренними ребрами барабанов мм.
Наружный угол отклонения каната от плоскости шкива (наружный угол девиации):
; αн=0о45; αн не>1030 по ЕПБ [17]
Отклонение каната на барабане к внутренней реборде от плоскости шкива:
Внутренний угол девиации:
; αн=0030; αн не>1030 по ЕПБ [17]
1.7 Вычисление мощности двигателя
Продолжительность одного цикла подъема:
Продолжительность движения скипа:
где Тз – продолжительность загрузки скипа по нормам проектирования с.
Средняя скорость движения скипа:
Максимальная скорость подъема (ориентировочно):
где α – множитель скорости.
Мощность двигателя (ориентировочно):
где Квс– коэффициент вредных сопротивлений;
ред – КПД редуктора (ориентировочно);
КД – коэффициент динамического режима.
Частота вращения двигателя при различных передаточных числах редуктора:
где i – передаточное число редуктора.
Принимаем асинхронный двигатель с фазным ротором типа АКН2–18–57–24.
Технические данные двигателя:
Рн=630кВт; nн=245обмин; Vн=6000В; λ=25; ; jрот=2100; н=920%
Крутящий момент на валу барабана подъемной машины создаваемый грузом и канатом:
Крутящий момент от принятого электродвигателя:
Принимаем редуктор ЦО–22 i = 11.5.
Мкр=500000Нм; jред = 70000; = 096
Максимальная скорость подъема с электродвигателем АКН2–18–57–24.
1.8 Определение приведенной массы установки
Длина одной ветви каната:
Масса двух ветвей каната:
Масса поступательно движущихся частей:
Приведенная масса барабанов машины 2Ц–6х24
Приведенная масса редуктора ЦО–22:
Приведенная масса копрового шкива:
Приведенная масса ротора электродвигателя:
Приведенная масса вращающихся частей машины:
Приведенная масса всей установки:
1.9 Максимальное ускорение скипа
Номинальный момент двигателя:
Максимальный момент двигателя:
Момент переключения:
Средний момент двигателя:
Средняя сила тяги в канате создаваемая двигателем:
Тормозная сила при свободном выбеге:
Замедление скипов при свободном выбеге в конце подъема:
Замедление скипов при подтормаживании с усилием 30% от веса груза:
Замедление aз=048 мс2 не более 5 мс2допускаемого ЕПБ [17].
1.10 Вычисление времени и расстояний при движении скипа
Принимаем 5–периодную симметричную диаграмму скорости.
Время движения порожнего скипа в разгрузочной кривой:
где h0–высота загрузочной прямой м;
V0–скорость выхода скипа из кривой мс.
Время движения скипа в загрузочной кривой:
где V4 – скорость движения груженого скипа в кривую мс.
Ускорение скипа в загрузочной кривой:
Замедление груженого скипа в разгрузочной кривой:
Продолжительность движения скипа с ускорением a1=014:
Путь пройденный скипом за время разгона:
Продолжительность движения с замедлением aз=048 мс2:
Путь пройденный скипом за время замедления:
Путь пройденный скипом с равномерной скоростью:
Продолжительность движения скипа с равномерной скоростью:
Фактическая продолжительность движения скипа:
Фактический коэффициент резерва производительности:
1.11 Расчет необходимых усилий в подъемном канате
Общий вид уравнения усилий в канате:
где х – расстояние от точки загрузки до скипа м.
Необходимые усилия в канате по отдельным периодам (точками):
В начало подъема когда один скип загружен другой порожний находится в разгрузочной кривой х=0; а=а0=025 мс2
Груженый скип поднялся х=2 м порожний скип выходит из кривой х=h0=2 м; a=a1=0.25 мс2
а. Груженый скип ускоряется с а=а1=014 мс2 порожний скип вышел из кривой х=h0=2 м.
Груженый скип в конце участка ускорения х=h0+h1=158 м; а=а1=014 мс2
a. Груженый скип в начале участка равномерного движения х=h0+h1=158 м; а=0 мс2
Груженый скип в конце участка равномерного движения х=h0+h1+h2=6212м; а =0 мс2
а. Груженый скип в начале участка замедления х=h0+h1+h2=6212 м; а=a3 = –048 мс2
Груженый скип в конце участка замедления х=h0+h1+h2+h3=667 м; а=a3=–048 мс2
a. Груженый скип на входе в загрузочную кривую х=h0+h1+h2+h3=667 м а=a4 =–025 мс2
Груженый скип в конце разгрузочной кривой х=h0+h1+h2+h3+h4=669м; a =–025 мс2
Таблица 4.1 – Расчет усилий в подъемном канате
1.12 Уточненный расчет мощности электродвигателя
Эквивалентное время цикла:
Эквивалентное усилие:
Эквивалентная мощность двигателя:
Принятый электродвигатель Рн=630кВт имеет запас мощности:
Максимальный момент на валу при Fmax=F3
Перегрузка двигателя при пуске:
Допустимая перегрузка двигателя по справочнику λ=25.
1.13 Мощности на валу барабана и потребляемые электродвигателем из сети
Таблица 4.2 – Мощности на валу барабана и потребляемые электродвигателем из сети
Мощность потребляемая электродвигателем из сети:
1.14 Определение расхода электроэнергии
Расход электроэнергии:
Полезный расход электроэнергии на 1 подъем:
Фактический расход электроэнергии на 1 подъем:
Удельный расход электроэнергии на 1 подъем 1т. груза:
Удельный расход электроэнергии на 1 ткм.:
КПД подъемной установки:
Годовой расход электроэнергии:
Годовая оплата за электроэнергию:
где а – тариф за 1 кВт заявленной мощности а = 98 руб.
Таблица 4.3 – Смета затрат на приоретение оборудовани
Наименование оборудования
Подъемная машина 2Ц–6х24
Электродвигатель АКН2–18–57–24
Канат d = 505 мм = 1325 м
Таблица 4.4 – Расчет штатов и заработной платы
Таблица 4.5 – Расчет капитальных затрат и амортизационных отчислений
Таблица 4.6 – Расчет затрат на вспомогательные материалы
Таблица 4.7 – Калькуляция себестоимости
годовой объём работ руб.
Технико–экономическое обоснование:
Капитальные затраты К1 = 23582291120 руб.
Эксплуатационные затраты С1 = 30981329468руб.
Производительность рудника в год:
Удельные капитальные затраты Куд рубм³
К уд1 = К1 Qг = 235822 91120 500 000 = 47165 рубт
Удельные эксплуатационные затраты Суд рубм³
С уд1 = С1 Qг = 30981329468 500 000 = 61963 рубт
1.15 Техника безопасности при эксплуатации подъемной установки
-Выполнять требования ЕПБ [17 стр. 112–181.]
-Ежесуточно производить осмотр подъемного каната при V=0.3 мс с записью в журнале.
-Еженедельно проводить осмотр подъема (механик подъема).
-Ежемесячно проводить осмотр подъема (главный механик рудника).
-Через каждые 6 месяцев направлять на испытание отрезок каната.
2 Расчет водоотливной установки
Водоприток воды в шахту имеет место только в стволах в виде капежа.
Исходные данные для расчета:
-максимальный водоприток Qma
-высота всасывания Нвс = 15 м;
-длина всасывающего трубопровода Lвс = 8 м;
-длина нагнетательного трубопровода Ln = 570 м;
-температура воды Т = (7–10) 0С;
Требуемая расчетная подача насоса:
Принимаем два насоса (рабочий и резервный) ПТ–1475 с подачей Qn = 4 м3ч и напором Н = 750 м.
Диаметр нагнетательного трубопровода:
где Vn – скорость движения воды мс.
Принимаем нагнетательный трубопровод с внутренним диаметром dвн =30 мм. = 0003 м толщиной стенок Sст = 4 мм наружным диаметром dнн =38 мм.
одного метра трубопровода:
Pн = 00486 . Sст.н (dнн – Sст) = 00486 . 4 (38 – 4) = 63 кг.
Диаметр всасывающего трубопровода:
где Vвс – скорость движения воды во всасывающем трубопроводе мс.
Принимаем всасывающий трубопровод с внутр. диаметром dв.вс = 38 мм толщиной стенок Sст = 2 мм.
Тогда действительные скорости движения воды:
Потери во всасывающем трубопроводе:
Потери в нагнетательном трубопроводе:
где λ – коэффициент гидравлического трения
λвс = 0021dвс03 = 0021003803 = 0056
λн = 0021dн03 = 002100303 = 006
где – коэффициент местных сопротивлений
Суммарные потери напора в трубопроводе:
ΔН = ΔНвс + ΔНн = 051 + 141 = 14151 м
Расчетный напор насоса:
Нр = Нг + ΔН = 558 + 14151 = 69951 м
Характеристика сети строится в соответствии с уравнением Н = Нг + RcQн2 откуда постоянная сети:
Rс = ΔН Qн2 = 14151 42 = 884
Таблица 4.8 – Сводная производительность
По характеристике насоса и сети определим:
Нф = 725 м – фактический напор;
Qф = 44 м3ч – фактическая подача;
Уф = 064 – коэффициент полезного действия.
Увеличение принятого напора Н = 750 м по сравнению с расчетным Нр = 6995 составляет 673 % что вполне допустимо так как не превышает 8% .
НгНо = 558790 = 07 09 – отсутствует неустойчивый режим.
Определим мощность двигателя:
Принимаем двигатель Nдв = 15кВт.
Фактическое время работы в сутки:
Выше перечисленные данные водоотливной установки принимаем для второго ствола.
Суммарный годовой водоприток
Qr = 2 Qmax = 2 . 25 . 24 . 365 = 43800 м3год.
Таблица 4.9 – Расчет капитальных затрат и амортизационных отчислений
Оптовая цена за 4 комплекта руб.
Таблица 4.10 – Расчет затрат на вспомогательные материалы
ПТ–1475 с трубопроводом
Расход и стоимость электроэнергии для насосной установки ПТ–1475.
Так как используется две установки значит сумма затрат на электроэнергию удвоится и составит 7442160 рублей.
Таблица 4.11 – Расчёт рабочей силы и фонда заработной платы
Таблица 4.12 – Калькуляция себестоимости
Технико–экономическое обоснование
Насосная установка ПТ–1475 с трубопроводом
Капитальные затраты К1 = 124150320 руб.
Эксплуатационные затраты С1 = 334728573руб.
Производительность насосной установки в год:
Qгод = 43 800 м³год (откачка воды)
К уд1 = К1 Qг = 124150320 43 800 = 2834 рубм³
С уд1 = С1 Qг = 334728573 43 800 = 7642 рубм³
Qгод = 500 000 тгод (полезного ископаемого)
К уд1 = К1 Qг = 124150320 500 000 = 248 рубт
С уд1 = С1 Qг = 334728573 500 000 = 669 рубт
3 Проветривание участка горных работ
Схема проветривания рудника – центральная подача воздуха осуществляется по вспомогательному стволу а удаление из шахты – по Главному стволу.
Вентиляторно–калориферная установка расположена на поверхности у вспомогательного ствола. Вентилятор главного проветривания (осевой ВОД– 30) может обеспечить подачу в рудник воздуха около 170 м3сек – в случае применения при добыче соли самоходного дизельного оборудования. Изменение количества воздуха обеспечивается изменением угла установки лопаток вентилятора.
Для проветривания участка очистных работ а также камерных выработок технологического и вспомогательного назначения проходческих комбайновых забоев намечается подавать в шахту проектное количество воздуха равное 120 м3сек.
В шахтах предусматривается обособленное проветривание следующих вспомогательных камер: ремонтного пункта гаража подземной уборной и склада ГСМ выдача воздуха из этих камер будет осуществляться на вентиляционный горизонт по специальным вентиляционным скважинам диаметром 05 м. Количество воздуха для их проветривания определено из условий четырехкратного обмена воздуха в течение часа. Количество воздуха для проветривания технологических и вспомогательных камер приведено в таблице 4.13.
Таблица 4.13 – Количество воздуха для проветривания технологических и вспомогательных камер
Количество воздуха м3с
Камера ремонтного пункта
Камера подземного гаража
Камера подземной уборной
Камера вентиляционных дверей (утечки воздуха через шлюзы)
Камера питателей и дозатора
Камера сбора просыпи соли (горизонт – 135 м)
Для проветривания двух проходческих комбайновых забоев которые будут проходиться на транспортном и вентиляционном горизонтах ориентировочно потребуется 12 м3с воздуха из них 6 м3с воздуха от забоя на транспортном горизонте используется впоследствии в общей схеме проветривания рудника.
Таким образом для проветривания очистных камер будет подаваться свежий воздух в количестве:
0 – 20 – 6 = 94 м3с;
Минимальная скорость струи воздуха в очистной камере при отработке 3–х камер составит:
где 2065 м2 – расчетная площадь поперечного сечения очистной камеры после окончания выемки соли.
Регулирование количества воздуха поступающего в конкретную выработку осуществляется силами пылевентиляционной службы рудника путем устройства деревянных вентиляционных дверей в панельном вентиляционном штреке № 2 деревянных ляд в верхних сопряжениях вентиляционно–ходовых восстающих а также шиберных устройств устьях вентиляционных скважин на вентиляционном горизонте. Деревянные вентиляционные устройства должны иметь войлочные или прорезиненные прокладки и плотно обиты герметизирующим материалом.
Главная вентиляционная установка
Скорость вращения: 500; 600обмин.
Мощность: 800; 1250кВт.
Номинальная подача: 125; 160м3с.
Подача в пределах рабочей зоны: m 60. ma 270.
Давление: 2400; 3900Па.
Маховый момент: 128тсм2.
Масса без КСРП и электрооборудования: 2900кг.
Масса с КСРП и электрооборудованием: 48000кг.
Роликоподшипник радиальный опоры ротора:
Радиальный зазор: 002.
Диаметр шейки: 200+006.
Диаметр отверстия в роликоподшипнике до посадки на вал: 200–0035.
Роликоподшипник радиальноупорный опоры ротора:
Радиальный зазор: 003.
Тип: СД ВС 15–49–12У3.
Сопротивление изоляции земли: 4000МОм.
Сопротивление обмотки ротора: 0177Ом.
Сопротивление обмотки статора: 0412Ом.
Мощность двигателя: 800кВт.
Скорость вращения: 500обмин.
Напряжение сети: 6000В.
Частота сети: 50Гц.
Коэффициент мощности: 09.
Питание цепи возбуждения от реверсивного тиристорного преобразователя:
Питающие трансформаторы:
Пульт управления Вентиляторно–калориферной установки: ШУ1–ИЯС.
Трансформаторы: ТТ20–400А; ТТ20–392А.
Блок управления: КФУ–0212.
Эксплуатация и ремонт
1Организация и технология ремонта
На предприятии ремонт машин осуществляется в следующей последовательности:
- Подготовка машин к сдаче в ремонт;
- Сдача–приемка машин в ремонт по акту;
- Очистка от грязи и разборка машины на узлы части и детали;
- Мойка дефектация и маркировка деталей;
- Восстановление изношенных деталей допущенных для повторного использования;
- Сборка выверка настройка и испытание узлов;
- Общая сборка выверка обкатка и испытание машины;
- Устранение недостатков обнаруженных при испытании и сдача машины в эксплуатацию.
Для ремонта машин каждого типа разрабатывается типовой технологический процесс позволяющий заранее провести необходимую конструкторскую технологическую материальную и организационную подготовку обеспечивающую высокое качество и короткие сроки ремонта.
При ценностном методе от полной стоимости оборудования принимается установленный процент отчислений на ремонт. Полученная сумма является годовой стоимостью ремонтных работ и служит исходной величиной при проектировании ремонтных предприятий.
Фонд времени определяем по формуле:
Дм = (365 – В – П) . С . n
где В и П – число выходных и праздничных дней за планируемый период; С – продолжительность смены ч; n – число смен.
Дм = (365 – 52 – 12) . 7 . 3 = 6321 ч.
Проектирование ремонтного участка.
Потребность во всех видах ремонтов по каждому типу оборудования можно рассчитать по формуле:
где Е – потребное число капитальных текущих ремонтов ремонтных осмотров в ремонтном цикле;
О – количество однотипных машин;
Км – коэффициент использования оборудования по машинному времени [18];
Д – общий фонд рабочего времени оборудования в часах:
где А – количество месяцев в планируемом периоде (12 месяцев);
В – количество рабочих часов в смену(7 часов);
Р – количество рабочих смен в месяц(66 смен в месяц при 5–и дневной рабочей неделе;
Л – число капитальных текущих ремонтов осмотров в ремонтном цикле;
У – длительность ремонтного цикла машин.
Д = 12 . 7 . 66 =5544 ч
Потребное число капитальных текущих ремонтов и технических осмотров для машины 1ВОМ А:
Потребное число капитальных текущих ремонтов и технических осмотров для комбайна Урал–20 А:
Потребное число капитальных текущих ремонтов и технических осмотров машины для перевозки людей – Т–32202 «Крот»:
Потребное число капитальных текущих ремонтов и технических осмотров для ленточных конвейеров: 1Л80; 1ЛУ100:
Потребное число капитальных текущих ремонтов и технических осмотров для вагонов шахтных самоходных 5ВС – 15 2шт.:
Таблица 5.1 – График ППР
Таблица 5.2 – Перечень количество и стоимость оборудования
Самоходный вагон 5ВС–15
Машина для перевозки людей Т–32202 «Крот»
Общая стоимость оборудования А (руб.)
где i – число типов машин
n – число однотипных машин
а i – стоимость машин руб.
А = 648432300 + 4700000000 + 1236 60000 + 1400000000 + +1600000000 + 2 . 7 25000000 = 99220 92300 руб.
Годовая стоимость ремонтных и монтажных работ:
где = 009 ÷ 011 – коэффициент учитывающий увеличение стоимости работ в силу удорожания доставки запасных материалов обеспечения рабочей силой
Ар = 01 . 99220 92300 = 992209230 руб.
Полная стоимость работ производимых мастерскими:
Ам = . Ар = 05 . 992209230 = 496104615 руб.
где – коэффициент учитывающий внеплановые работы.
Общий фонд заработной платы производственных рабочих:
Азп = ( . Ам) = 03 . 496104615 = 148831384 руб.
где = 028 ÷ 032 – доля заработной платы в стоимости ремонтных работ
Принимая часовую стоимость производственной заработной платы – Р равный 80 руб.час. из расчета средней тарифной ставки по 5–му разряду определяем общий годовой фонд рабочего времени:
Штат производственных рабочих мастерских рассчитываем по формуле:
где Ц – коэффициент выполнения норм времени ремонтными рабочими [18]
Фр – действительный годовой фонд рабочего времени одного рабочего ч:
Фр = [С (365 – В – П – О)] – С1 . П1 . S.
где С – продолжительность рабочей смены ч;
В – число выходных дней в году;
П – число праздничных дней в году;
О – число отпускных дней в году;
С1 – продолжительность укорочения рабочего дня в праздничные дни
П1 – число предпраздничных дней в году;
S – коэффициент учитывающий болезни общественные обязанности и пр. [18].
Фр = [7(365 – 52 – 12 – 52)] – 1 . 8 . 097 = 16829
Ориентировочно определяется штат производственных рабочих по профессиям[18] :
-Токари–станочники – % – 3 чел.
-Слесари–ремонтники – % – 6 чел.
-Газоэлектросварщики – % – 3 чел.
-Агрегатчики – % – 1 чел.
Количество такелажников подсобных рабочих и обслуживающего персонала устанавливается дополнительно к штату производственных рабочих и составляет 2 чел. а ИТР – 3 чел.
Мобщ = 122 · М = 122 · 14 = 1708 чел.
Потребное число станков определим как:
где Д – действительный годовой фонд рабочего времени станка
S – коэффициент загрузки оборудования для ремонтных мастерских 07.
Д = kтор [ (365 – В – П) . С – П1 . С] = 1994 час.
где kтор = 095 – коэффициент учитывающий продолжительность технического обслуживания и ремонта станка );
Принимаем Нст = 5 станков
Ориентировочно распределяем станки по типам (в % от Нст):
-Токарных 25% – 1 станок
-Сверлильные 20% – 1 станок
-Заточные 15% – 1 станок
-Прочие 40% – 2 станка
2 Расчет площадей ремонтной базы
Общую площадь ремонтной базы определяем по формуле:
где – площадь производственных отделений м2
Ка Кв Кс – процент площади административных вспомогательных и складских помещений от производственной площади принимается 6 12 и 8%.
Площадь производственных отделений Sо определяется по удельной площади Sуд на одного рабочего:
Таблица 5.3 – Величина площадей производственных отделений
Наименование отделения
Удельная площадь Sуд м2
Количество рабочих Nраб чел.
Площадь отделений м²
Общая площадь ремонтной базы:
Sрб = 200 + 026 . 200 = 252м²
Принимаем габариты ремонтной мастерской:
-Длина здания – 24 м
-Ширина здания – 12 м
Sрб = 12 . 24 = 288м²
План расположения помещений и оборудования ремонтной мастерской.
В данной мастерской производят осмотр оборудования и мелкий текущий ремонт с заменой готовыми запасными частями.
В механическом отделении на продольных и поперечных балках подвешена электроталь с грузоподъемностью 5 т.
В этом отделении приемка деталей и машин с последующей разборкой на сборочные единицы. После разборки машин детали очищают промывают и обезвреживают. Качество очистки влияет на их восстановление и дефектацию. Мойку деталей производят ручным способам в специальных растворах или в подогретой воде. После дефектации осуществляют ремонт или замену деталей с последующей сборкой. После сборки деталей и машины испытывают и производят окраску сборочных единиц.
3 Технико–экономические показатели ремонтного участка
Таблица 5.4 – Смета на приобретение монтаж оборудования и расчет амортизационных отчислений
Наименование оборудования станков
Сумма годов. аморт. руб.
Неучтенное оборудование 5 %
Рассчитываем годовой расход электроэнергии по формуле:
W = N . K3 . tсм . Тсм
где К3 – коэффициент загрузки принимаем
Nсм – число смен в год
W = 244 . 07 . 7 . 903 = 1 07962680 кВтч
С3 = W . 031 = 33468431 руб.
Таблица 5.5 – Штат рабочих и фонд заработной платы
Коэффициент спсочности
Списочная численность
Тарифная ставка (руб.см)
Эффективный фонд времени
Премиальная доплата (40% ФЗП) руб.
Доплата за работу в ночное время (165% ФЗП) руб.
Заработная плата с учетом районного коэффициента Кр=13
Северные надбавки 30% руб.
Таблица 5.6 – Расход материалов
Наименование материалов
Годовой расход (нат.вел.)
Таблица 5.7 – Калькуляция себестоимости ремонтных работ
Заработная плата основная и дополнительная
Начисления на зар. плату 34% (социальные начисления)
Ремонт оборудования (150% от амортизации)
Услуги на содержание оборудования (15% от амортизации)
Цеховые расходы (25% от суммы всех перечисленных затрат)
Цеховая себестоимость
Капитальные затраты К1 = 44810745 руб.
Эксплуатационные затраты С1 = 892235814руб.
K уд 1 = К1Qг = 44810745 500 000 = 090 рубт
Удельные эксплуатационные затраты Суд рубт.
C уд 1 = С 1 Q г = 892235814500 000 = 1785 рубт
1 Расчет участковых электрических сетей
Данные расчета нагрузок
Таблица 6.1 Данные расчета нагрузок
Приемники электроэнергии
Коэффици–ент спроса Кс
Проходческо–очистной комбайн Урал–20
Конвейер ленточный 1Л80
Конвейер ленточный 1ЛУ100
Вентилятор шахтный местного проветривания ВМЭ–61
Полная расчетная мощность токоприемников участковой подстанции №1 при Ку.м = 08.
К установке принимаем передвижную участковую понизительную подстанцию (ПУПП) типа ТСВП–6306–069 (трансформатор сухой взрывобезопасный передвижной мощностью 630 кВ·А и напряжением первичной обмотки 6 кВ). С учетом возможности запуска мощного двигателя к установке принимаем трансформатор ТСВП–6306–069 по мощности превышающий утроенную номинальную мощность этого крупного двигателя т.е. Sтн≥3Рнк
Полная расчетная мощность токоприемников участковой подстанции №2
К установке принимаем подстанцию ТСВП–2506–069
Полная расчетная мощность токоприемников участковой подстанции №3
К установке принимаем подстанцию ТСВП–2506–069
Расчет кабельной сети подземного участка
1.1 Расчет и выбор кабельной сети напряжением выше 1кВ
Участок КЛ от УПП до подстанции №1
Рассчитаем сечение и выберем марку высоковольтного кабеля питающего трансформаторную подстанцию ТСВП–6306–069 если длина кабеля L=1200м. Передвижная трансформаторная подстанция питается от высоковольтной ячейки КРУВ–6 установленной в УПП. Мощность КЗ на шинах УПП Sкз³=50 МВ·А
Значение номинального тока трансформатора подстанции принимаем из технической характеристики по справочным данным Iт.вн=606.
Это же значение тока можно определить по формуле:
Iт.вн= Sт.н√3Uн= 630173·6= 607 А
Ток нагрузки высоковольтного кабеля (А) питающего подстанцию ТСВП–6306–069 рассчитываем по формуле:
Расчетное значение тока в высоковольтном кабеле с учетом температурного коэффициента определяем следующим образом. Температурный коэффициент kt=112 по приложению 2.1. Таким образом для рассматриваемой задачи t = 15ºС.
Принимаем кабель марки СБн–6000. Для кабеля этого типа по приложению 2.1 и нормируемой температуры жил 65ºС находим температурный коэффициент Кt = 1112. Тогда Iвн = 66771112=667596 А.
По приложению 2.2 для кабеля СБн–6000 по расчетному току Iвн=6677596 А выбираем сечение жил 25 мм² которое допускает нагрузку Isн=81 А.
Проверка кабеля на термическую стойкость:
Коэффициент загрузки кабеля:
к = Iф.кКt·Isн = 6061·81 = 075
По приложению 2.4 при к = 075 для кабелей с бумажной изоляцией для температуры окружающей среды 15ºС находим коэффициент Кз=111.
Предельно допустимый кратковременный ток КЗ (А) в кабеле:
Iп = Кз·С·S√tп = 111·134·25√017 = 929625 А
Где С = 134 для кабелей с бумажной изоляцией; tп=017 с для КРУВ–6 расположенной в ГПП;
Ток трехфазного КЗ в начале проверяемого кабеля Iкз³ (на шинах ГПП)
Iкз³ = Sk³√3Uc = 50·10³ 173·6 = 4817 А
Iп =929625А > Iкз³ = 4817 А
Выбранное ранее сечение кабеля соответствует условию термической стойкости. Минимальное сечение кабеля соответствующее условию термической стойкости.
S ≥ Iкз³· √tп C = 4817·√017 134 = 148 мм²
Выбранное ранее сечение кабеля 25 мм² > 148 мм²
Сечение кабеля по допустимой потере напряжения:
S = √3· Iн·L·cosφ γ·U = 173·606 ·1200·06 50·150 = 106 мм²
Сечение кабеля соответствует стандартному.
Стандартное сечение (мм²) жилы по экономической плотности тока:
Sэк = Iвн j = 606 25 = 24 мм²
Для шахт время использования максимальной нагрузки Тmax = 4000ч. Для кабелей с медными жилами и пластмассовой изоляцией j = 25 Амм²
Стандартное сечение Sном = 25мм²
Таким образом окончательно принимаем кабель СБн 3х25 с номинальным сечением жил 25мм² и длительно допустимым током нагрузки 81 А.
Участок КЛ от УПП до подстанции №2
Рассчитать сечение и выбрать марку высоковольтного кабеля питающего трансформаторную подстанцию ТСВП–2506–069 если длина кабеля L=600м. Передвижная трансформаторная подстанция питается от высоковольтной ячейки КРУВ–6 установленной в УПП. Мощность КЗ на шинах УПП Sкз³=50 МВ·А.
Iт.вн= Sт.н√3Uн= 250173·6= 2408 А
Ток нагрузки высоковольтного кабеля (А) питающего подстанцию ТСВП–2506–069 рассчитываем по формуле:
Принимаем кабель марки СБн 6000. Для кабеля этого типа по приложению 2.1 и нормируемой температуры жил 65ºС находим температурный коэффициент Кt = 1112. Тогда Iвн = 66771112=6677596 А.
По приложению 2.2 для кабеля СБн 3х25 по расчетному току Iвн=6677А выбираем сечение жил 25 мм² которое допускает нагрузку Isн=81 А.
Iп = Кз·С·S√tп = 111·134·25√017 = 929625А
S = √3· Iн·L·cosφ γ·U = 173·606 ·600·06 50·150 = 6 мм²
Для шахт время использования максимальной нагрузки Тmax = 4000ч. Для кабелей с медными жилами и пластмассовой изоляцией j = 25 Амм². Стандартное сечение Sном = 25мм².
1.2 Расчет и выбор кабельной сети напряжением до 1кВ
Для потребителей ПУПП №1
Рассчитать и выбрать тип и сечение магистрального (фидерного) кабеля от участковой трансформаторной подстанции и кабеля питающего двигатели комбайна УРАЛ–20А если известно что напряжение низковольтной сети 660В длина фидерного кабеля с учетом провисания 90м комбайнового с учетом провисания Lг = 1200м. Комбайн УРАЛ–20А имеет суммарную установленную мощность Σуст = 590 кВт.
Участковая подстанция питается от промежуточного высоковольтного распредпункта УПП–6 напряжением 6 кВ по кабелю СБн 3х70 длиной 1200м. УПП–6 получает питание от ГПП шахты длиной кабеля 1200м. Мощность КЗ энергосистемы на шинах ГПП 42 МВ·А.
Ток нагрузки магистрального (фидерного) кабеля:
Iф = Кс· Σу · 10³ √3·Uн· cosφ = 07 · 590 · 10³ 173 · 660 · 075 = 4823 А
При условии что эксплуатация происходит при tº = 15ºС принимаем поправочный коэффициент на температуру воздуха для токовых нагрузок на кабели равным 112 тогда
Iф = 4823 112 = 4306 А
Для магистрали по приложению 2.2 выбираем кабель из условия Isн ≥ Iф принимаем два параллельно проложенных кабеля типа СБн 3*70 рассчитанных на длительно допустимый ток (см. приложение 2.2)
По приложению 2.2 для комбайна выбираем кабель из условия Isн ≥ Iф. и принимаем два параллельно проложенных гибких кабеля с резиновой изоляцией КГЭШ 3*95+1*10+3*4 сечением силовой жилы 95мм² рассчитанный на максимальный допустимый ток Isн = 290А.
Для проверки фидерного кабеля на термическую стойкость определяем ток трехфазного КЗ в начале кабеля т.е. на зажимах вторичной обмотки трансформатора участковой подстанции. Из технической характеристики подстанции ТСВП–6306–069 по приложению 2.5 находим:
Sтн = 630 кВ·А; Iв.н = 606 А; Iн.н =527 А;
Uк = 35%; Uх.х = 690 В; Рк = 4900 Вт;
Индуктивное сопротивление энергосистемы приведенное к расчетному напряжению сети (базисному напряжению):
Х1 = U²б Sc³ = 690² 42000 = 1134 мОМ
Индуктивное сопротивление кабельной линии напряжением 6 кВ. По приложению 2.2 находим:
Х01 = 0092 Омкм и Х02 = 000021 Омкм.
Хлн = (Х01 · Lгпп – рп–6 + Х02 · Lрп–6 – упп ) · 10³ = ( 0092 · 1 + 000021 · 12 ) · 10³ = 923 мОМ
Индуктивное сопротивление кабельной линии напряжением 6 кВ приведенное к расчетному (базисному) напряжению сети:
Х2 = Хлн · U²б U²ср = 923 · 660² 6300² = 101 мОМ
Активное сопротивление кабельной линии 6 кВ
r01 = 0074 Ом км ; r02 = 000021 Ом км.
rлн = (r01· Lцпп – рп–6 + r02 · Lрп–6 – пупп ) · 10³ = ( 074 · 1 + 000021 · 12 ) · 10³ = 7403 мОм
Активное сопротивление кабельной линии 6 кВ приведенное к базисному напряжению:
r1 = rлн · U²б U²ср = 7403 · 660² 6300² = 81 мОМ
Активное сопротивление трансформатора:
Rт = Рк 3 · Iн² = 4900 3 · 527² = 588 мОм
Индуктивное сопротивление обмотки трансформатора:
Хт = 10 · Uк · U²х.х Sт.н = 10 · 35 · 069² 630 = 265 мОм
Суммарное индуктивное сопротивление до расчетной точки КЗ (вторичной обмотки трансформатора):
ΣХ = Х1 + Х2 + Хт = 1134 + 101 + 265 = 389 мОм
Суммарное активное сопротивление до расчетной точки КЗ (вторичной обмотки трансформатора):
Σr = r1 + Rт = 81 + 588 = 14 мОм
Ток трехфазного КЗ в начале фидерного кабеля (на вторичной обмотке ПУПП)
Iкз³ = Uб · 10³ √3Z = 690 · 10³ 173 √ 389² + 14² = 9647 А
к = Iф Кt·Isн = 4823 1· 590 = 0817
При к = 0817 для кабелей с бумажной изоляцией при напряжении до 3 кВ для температуры окружающей среды 15ºC линейной интерполяцией находим коэффициент загрузки: Кз = 115
Для кабелей с бумажной изоляцией С = 125 ; для подстанции ТСВП – 6306 tп = 005 с.
Предельно допустимый кратковременный ток КЗ для фидерного кабеля:
Iп = Кз·С·S√tп = 115·125·70√005 = 450009 А
Выбранное ранее сечение (S =70 мм ²) фидерного кабеля удовлетворяет условию термической стойкости.
Активное сопротивление фидерного кабеля:
r2 = r0 · L 2 · 10³ = 0074 · 12 · 2 · 10³ = 444 мОм
r0 = 0074 Ом км для СБн 3х70
Индуктивное сопротивление фидерного кабеля:
x3 = x0 · L 2 · 10³ = 0092 · 12 · 2 · 10³ = 552 мОм
x0 = 0092 Ом км для СБн 3х70
Суммарное активное сопротивление сети до начала комбайнового кабеля (сопротивлением коммутационных аппаратов пренебрегаем):
rΣ = 14 + 444 = 584 мОм
Суммарное индуктивное сопротивление сети до начала комбайнового кабеля (сопротивлением коммутационных аппаратов пренебрегаем):
xΣ = 389 + 552 = 941 мОм
Полное сопротивление сети до начала комбайнового кабеля:
Z = √ rΣ² + xΣ² =√ 584² + 941² = 1107 мОм
Ток КЗ в начале комбайнового кабеля:
Iкз³ = Uб · 10³ √3Z = 690 · 10³ 173 · 1107 = 3603 А
Гибкий кабель комбайна проверяем на термическую стойкость.
к = Iдв Кt·Isн = 130 1· 136 = 095
Находим коэффициент загрузки Кз. При 15ºC для кабелей с резиновой изоляцией при к = 09 Кз = 1.
Для кабелей с резиновой изоляцией С = 101 для отключающего аппарата tп = 005
Предельно допустимый ток КЗ Iп (А) комбайнового кабеля:
Iп = Кз·С·S√tп = 1·101· 95√005 = 42910 А
Выбранное ранее сечение кабеля удовлетворяет условию термической стойкости. Фидерный и комбайновый кабели проверяем по допустимой потере напряжения в номинальном режиме.
Потеря напряжения в трансформаторе в номинальном режиме:
Uт.н = т ( Uа · cosφ + Uр· sinφ ) · Ux.x 100
Коэффициент загрузки трансформатора:
к = Sт.р Sт.н = 472630 = 075
Относительное значение активной составляющей напряжения КЗ трансформатора
Uа = Рк Sт.н · 100% = 4900 ·10³ 630·100% = 0777 %
Относительное значение реактивной составляющей напряжения КЗ трансформатора
Uр = √ Uк² – Uа² = √35² – 0777² = 341 %
Cosφ = 06 sinφ = √ 1 – 06 = 08
Uт.н = 075·( 0777 · 06 + 341·08 ) · 690 100 = 1653В
Потери напряжения Uг в гибком кабеле комбайна:
Uг = √3 · Iдв · ( Rг · cosφдв + Xг · sinφдв ) = 173 · 130 ·
( 009 · 085 + 011 · 053 ) = 303 В.
где Rг = r0 Lг = 0074 · 12 = 009 Ом ; Xг = x0 Lг = 0092 · 12 = 011
sinφ = √ 1 – 085² = 053
Общая допустимая потеря напряжения в низковольтной сети:
ΣU = Ux.x – Uдв min = 690 – 0.85 · 660 = 129 В
Потери напряжения в фидерном кабеле:
Uф = ΣU – Uт.н – Uг = 129 – 165 – 303 = 822 В
Сечение фидерного кабеля по допустимой потере напряжения в нормальном режиме
Sф = √3· Iф · · Lф ·cosφ γ·Uф = 173·4823 ·12 · 1200 · 085 50·822
Сечение гибкого кабеля комбайна по допустимой потере напряжения в нормальном режиме:
Sг = √3· Iдв · Lг ·cosφ γ·Uг = 173 · 130 ·1200 · 065 50·303 = 1158 мм²
Выбранные ранее сечения кабелей удовлетворяют условиям напряжения в нормальном режиме.
Фидерный и комбайновый кабели проверяем по пусковому режиму.
Напряжение на распредпункте в номинальном режиме:
Uрп = Uт.н – (Uт.н + Uф) = 690 – (165 + 822) = 5193 В
Активное сопротивление кабельной сети от трансформатора до комбайна:
ΣRн = Rт + Rф+ Rг = 588 + 252 + 90 = 1211 А
Индуктивное сопротивление кабельной сети от трансформатора до комбайна
ΣXн = Xт + Xф+ Xг = 265 + 72 + 110 = 1437 А
Фактическое напряжение на зажимах электродвигателя комбайна при пуске:
Uдв.пф = Uрп 1+ √3 · n · Iдвпн Uн · (ΣRн·cosφ + ΣXн· sinφ) =
0956184 1+ 173 · 1 ·130 660 · (0121 · 085 + 0144 · 053) = 637 В
Допустимый уровень напряжения на зажимах двигателя:
Uд.п ≥ 08 · Uс = 08 · 690 = 552 В
Таким образом фидерный и гибкие кабели с ранее выбранным сечением удовлетворяют условиям допустимой потери напряжения при пуске комбайнового двигателя.
Для потребителей ПУПП №2
Рассчитать и выбрать тип и сечение магистрального (фидерного) кабеля от участковой трансформаторной подстанции и кабеля питающего двигатели ленточного конвейера 1ЛУ100 если известно что напряжение низковольтной сети 660В длина фидерного кабеля с учетом провисания 90м до двигателя Lг = 600 м. . Конвейер 1ЛУ100 имеет 2 электродвигателя суммарная установленная мощность Σуст = 200кВт.
Участковая подстанция питается от промежуточного высоковольтного распредпункта ГПП–6 напряжением 6 кВ по кабелю СБн 3 х 70 длиной 1200м. УПП–6 получает питание от ГПП шахты длиной кабеля 1000м. Мощность КЗ энергосистемы на шинах УПП 42 МВ·А.
Iф = Кс· Σу · 10³ √3·Uн· cosφ = 08 · 200 · 10³ 173 · 660 · 08 = 1752 А
Для магистрали принимаем кабель типа СБн 3х50 рассчитанных на длительно допустимый ток ( см. приложение 2.2 ): 2Isн = 200 А
Isн = 2 · 100 = 200 А. > Iф = 1752 А
Для конвейера выбираем кабель из условия Isн ≥ 2Iн
Принимаем кабель СБн 3х50 сечением силовой жилы 50 мм² рассчитанный на номинальный длительно допустимый ток Isн = 200 А.
Для проверки фидерного кабеля на термическую стойкость определяем ток трехфазного КЗ в начале кабеля т.е. на зажимах вторичной обмотки трансформатора участковой подстанции.
Коэффициент загрузки фидерного кабеля:
к = Iф Кt·Isн = 1752 1· 200 = 086
При к = 086 для кабелей с бумажной изоляцией при напряжении до 3 кВ для температуры окружающей среды 15ºC линейной интерполяцией находим коэффициент загрузки Кз = 115
Iп = Кз·С·S√tп = 115·125·50√005 = 321435 А
Выбранное ранее сечение (50 мм²) кабеля удовлетворяет условию термической стойкости.
т = Sт.р Sт.н = 293250 = 11
Uт.н = т ( Uа · cosφ + Uр· sinφ ) · Ux.x 100 = 11( 0777 · 06 + 341·08 ) · 293 100 = 103 В
Потери напряжения Uг в кабеле конвейера:
Uг = √3 · Iдв · ( Rг · cosφдв + Xг · sinφдв ) = 1 73 · 130 · ( 0156 · 08 + 0036 · 053 ) = 324 В.
где Rг = r0 Lг = 026 · 06 = 0156 Ом ; Xг = x0 Lг = 0061 · 06 = 0036
sinφ = √ 1 – 08 = 053
ΣU = Ux.x – Uдв min = 1200 – 095 · 660 = 63В
Потери напряжения в фидерном кабеле:
Uф = ΣU – Uт.н – Uг = 63 – 103– 324 = 203 В
Сечение фидерного кабеля по допустимой потере напряжения в нормальном режиме:
Sф = √3· Iф · · Lф ·cosφ γ·Uф = 173·1752 ·13 · 90 · 06 50·203 = 363 мм²
Сечение гибкого кабеля конвейера по допустимой потере напряжения в нормальном режиме:
Sг1 = √3· Iдв · Lг ·cosφ γ·Uг = 173 · 130 · 600 · 08 50·324 = 666 мм²
Аналогично рассчитывается кабель для конвейера1Л80 т.к. он подключен к этой же подстанции.
Iф = Кс· Σу · 10³ √3·Uн· cosφ = 08 · 75 · 10³ 173 · 660 · 08 = 66 А
Для магистрали принимаем кабель типа СБн 3х50 рассчитанных на длительно допустимый ток ( см. приложение 2.2 ):
Isн = 2 · 375 = 75 А. > Iф = 66 А
Принимаем кабель СБн–3х50 сечением силовой жилы 50 мм² рассчитанный на номинальный длительно допустимый ток Isн = 90 А.
к = Iф Кt·Isн = 66 1· 90 = 073
При к = 073 для кабелей с бумажной изоляцией при напряжении до 3 кВ для температуры окружающей среды 15ºC линейной интерполяцией находим коэффициент загрузки Кз = 115.
Предельно допустимый кратковременный ток КЗ для фидерного кабеля
Iп = Кз·С·S√tп = 115·125·50√005 = 160717 А
Дальнейшие проверочные расчеты аналогичны расчетам для конвейера 1ЛУ100.
Аналогичным образом проводятся расчеты для ПУПП№3.
2 Выбор низковольтной аппаратуры уставок реле максимальной токовой защиты и плавких вставок предохранителей
2.1Выбор автоматических (фидерных) выключателей
Автоматы выбирают по условиям применения назначению номинальному напряжению сети номинальному току и проверяют по предельному току отключения (коммутационной способности). При этом должны соблюдаться условия:
Uр.н = Uн ; Iн ≥ Iс ; Iо.а ≥ 12 · Iкз³
где Uр.н – номинальное напряжение катушки независимого расцепителя В;
Uн – номинальное напряжение сети В ;
Iн – номинальный ток выключателя А ;
Iс – ток защищаемой сети равный току в фидерном кабеле А;
Iо.а – предельно отключаемый ток автомата А;
Iкз³ – ток трех фазного КЗ на выводных зажимах автомата А.
Uр.н =660 = Uн =660 В; Iн = 200 А ≥ 1037 А; Iо.а = 11000 ≥ 9642 А
2.2 Выбор магнитных пускателей
Пускатели выбирают по условиям применения номинальному напряжению сети номинальному току подключаемой сети а также по мощности и режиму работы электродвигателей для управления которыми выбирается пускатель. При этом должны соблюдаться условия:
Uн ≥ Uс ; Iн ≥ Iс ; Рн ≥ Рдв
где Uн и Iн – номинальное напряжение и ток на которые рассчитан пускатель;
Рн – предельно номинальная мощность двигателя которая может быть подключена к пускателю кВт;
Рдв – номинальная мощность двигателя для которой выбирается пускатель кВт.
При управлении одиночным двигателем:
При управлении группой двигателей
Пускатель проверяют по отключающей способности из условия:
где Iо.п – предельно отключаемый ток пускателя А;
Iкз³max – расчетный максимальный ток трехфазного КЗ на зажимах моторной камеры пускателя А.
Уставка токовой защиты защищаемого пускателя должна быть выбрана по общему правилу и проверена из условия:
Если из выпускаемых пускателей не представляется возможным выбрать пускатель отвечающий условию Iо.п ≥ 12 · Iкз³max то к установке может быть принят пускатель с меньшей коммутационной способностью но при этом защита от токов КЗ должна осуществляться встроенным в ПУПП или установленным на распредпункте автоматически выключателем.
Суммарная мощность комбайновых двигателей составляет
Номинальное напряжение сети Uн =660 В
Ic = Σуст Uн = 590 *10³660 = 456894А
Выбираем 3 пускателя типа ПВИ–350 с номинальным током 350А.
Суммарная мощность комбайнового двигателя составляет Σуст = 200кВт
Ic = Σуст Uн = 200 *10³660 = 192303А
Выбираем 2 пускателя типа ПВИ–250 с номинальным током 250А.
3 Расчет заземления трансформаторной подстанции
Согласно ПБ для подземных электроустановок устраивают общую сеть заземления к которой присоединяют все подлежащие заземлению объекты а также главные и местные заземлители. Для устройства общей сети заземления используют броню и свинец бронированных кабелей заземляющие жилы гибких кабелей заземляющие провода и перемычки.
Главные заземлители устанавливают в зумпфах и водосборниках необходимо устраивать не менее двух главных заземлителей в разных местах резервирующих друг друга на время осмотра чистки или ремонта одного из них.
Для местных заземлителей устраивают искусственные заземлители в штрековых водосборниках или в других пригодных для этого местах.
Заземление корпусов передвижных машин главных конвейеров установленных в лаве и светильников подсоединенных к сети гибкими кабелями осуществляют путем соединения их с общей сетью заземления через заземляющие жилы питающих кабелей. Заземляющую жилу с обеих сторон надо присоединить к внутренним заземляющим зажимам кабельных муфт и вводных устройств.
Заземление в шахтах требуется выполнять в соответствии с инструкцией по устройству осмотру и измерению сопротивления шахтных заземлителей. Общее переходное сопротивление сети заземления измеренное у любых заземлителей не должно превышать 2 Ом. Сопротивление заземляющей цепи предназначенной только для защиты от статического электричества должно быть не более 100 Ом.
Таблица 6.2 – Характеристика заземлителей
Площадь поверхности м2
Общее заземляющее устройство состоит из центрального и местных заземляющих устройств. Центральные заземляющее устройства располагаются у ГПП. Местные заземляющие устройства в виде заземлителей у ППП ПКТП и у других электроустановок.
В соответствии с ЕПБ [17] сопротивление в любой точке общего ЗУ на поверхности не должно превышать 4 Ом в шахте 2 Ом.
Определение расчетного значения наибольшего возможного тока однофазного замыкания на землю.
Iозз = *Uф*(LвлКкл + LклКкл)
Где Lвл;Lкл – суммарная длина ВЛ и КЛ электрически связанных с точкой замыкания на землю км.
Квл Ккл – эмпирические коэффициенты
Квл = 300–400; Ккл = 10
Iозз = *63*(1210) = 131 кА
Определение общего сопротивления сети заземления:
Rзу = 125Iозз = 125131 = 0095 Ом
Так как Rзу намного меньше 4 Ом чего быть не может то расчет ведём исходя из того что Rзу=4 Ом.
Определение сопротивления центрального заземлителя:
Rцз = Rзу – Rпр – Rк
Где Rпр – сопротивление магистрального провода Ом
Rк – сопротивление заземляющей жилы кабеля Ом
Rцз = 4 – 068 = 332Ом
Определение сопротивления растеканию одиночного заземлителя:
Rэ = 0227*r = 0227*200 = 454Ом
где r – удельное сопротивление грунта r = 200Ом*м
Определение числа заземляющих электродов заземлителя:
n = RэRцз*hэ = 454072*332 = 19 шт.
где h – коэффициент использования электродов h=072
4 Расчет освещения подземных выработок
Для освещения рудника принимаются светильники типа РПЛ01 – 20 с люминесцентной лампой мощностью 20Вт и устанавливаются через 15м по всей длине лавы. Осветительная сеть протяженностью 1200м запитывается от своего пускового агрегата типа АПШ – 1.
Количество светильников получающих питание от одного агрегата составит:
где L – протяженность осветительной сети м.
l – расстояние между светильниками м.
Принимаем количество светильников 80 штук на агрегат.
Мощность трансформатора для питания светильников
Sтр.р = РΣЛ ·10³ с · эл ·cosφсв
где РΣЛ – суммарная мощность люминесцентных ламп Вт;
эл = 083 – 087 – электрический КПД светильника учитывающий потери в дросселе;
cosφсв = 06 – коэффициент мощности светильников с люминесцентными лампами;
Sтр.р = 30 · 20 ·10³ 094 ·087 ·cosφ06 = 12 кВА.
Сечение кабеля питающего светильники выбирается так чтобы отклонение напряжения на зажимах ламп наиболее удаленных от светильного трансформатора не превышало 4% номинального.
Сечение жилы магистрального осветительного кабеля:
где М – момент нагрузки кВт · м;
С – коэффициент значение которого для трех фазной линии при равномерной нагрузке принимается равным 85;
U – нормируемая потеря напряжения U = 4%.
Момент нагрузки для линий с равномерно распределенной нагрузкой:
М = 30 ·20 · 12002 · 10³ = 360 кВт · м;
Тогда сечение жилы магистрального осветительного кабеля составит
S =360 85 · 4 = 105 мм²
К установке принимается кабель типа КОГЭШ 3х16+ 1х10+ 3х4
5 Технико–экономические показатели электроснабжения подземных горных работ
Состоят из основной и дополнительной зарплаты рабочих занятых на работах по эксплуатации оборудования его содержанию и ремонту. Затраты на заработную плату персонала занятого на эксплуатации оборудования определяются с учетом численности и принятой системы оплаты труда. Численность рабочих устанавливается явочная и списочная.
Таблица 6.3 Расчет рабочей силы и фонд заработной платы
Необходимые данные для расчета:
– количество рабочих дней в году – 301;
где Ру – установленная мощность потребления;
Кс – коэффициент спроса.
Определим Qp по руднику в целом:
где t – количество рабочих дней в году.
Данные расчета сведены в таблицу 6.4.
Таблица 6.4 – Рассчетные данные
Насосы главного водоотлива
Определим средневзвешанный коэффициент мощности:
Рсрв = Wр Wа =63 22745 673=l38.
Определим среднегодовую активную нагрузку:
Рсрг=Wa Tp= 13 884 592 500 =27 769 кВт.
Определим среднегодовую реактивную нагрузку:
Qcpг=Wр Tp= 19 221 008 500 = 38 442 кВАр
Wа.срг= Wa301 = 45 673301 =13 884 592 Wр.срг= Wр301 = 63 227 301=
Определим затраты на электроэнергию за 1 год:
C = ( Р а + W b ) ( 1 + К )
где Р – заявленная предприятием мощность в часы максимума нагрузки энергоносителей кВт.
Р = Руст Км = 4256 08 = 3 4048 кВт.
а – тариф за 1 кВт заявленной мощности руб
а = Nдв Ц n = 4 256 98 251 = 1 400 руб
Wа – потребление активной энергии предприятием кВт ч
b – плата за 1 кВт ч потребляемой энергии равна 060.
К – коэффициент учитывающий изменение стоимости электроэнергии
С = ( 34048 1 400 + 45 673 060 ) ( 1 + 0 ) = 4 791 84015 руб.
Определим энерговооруженность труда:
Э = Wа N tсм nдн = 13 884 592 730 6 251 = 104 кВт ч чел. ч
где N – среднесписочное число производственных рабочих на руднике 730 чел
tсм – длительность рабочей смены = 7 ч.
nдн – число рабочих дней = 301 дн.
Определим фактический cosq > на руднике:
cosq p = QP Py = 2817 4 256 = 066
Это низкий коэффициент мощности необходим cosq ≥ 097 поэтому дальнейший расчет ведем из этого условия: cosp=097 tg p=025
Q = Py tg p = 4 256 0250=1 064 кВАр.
Определим реактивную мощность до компенсации:
Q = Qр – Q = 2 817 – 1 064 = 1 753 кВАр
Принимаем две конденсаторные батареи УК–63 мощностью 900 кВАр
Таблица 6.5 – Расчёт капитальных затрат и амортизационных отчислений
Таблица 6.6 – Расчет затрат на вспомогательные материалы
Таблица 6.7 – Калькуляция себестоимости добычи полезного ископаемого
Цеховые расходы (25% от суммы всех
Капитальные затраты К1 = 3 94450000 руб.
Эксплуатационные затраты С1 = 1961761554руб.
К уд1 = К1 Qг = 3 94450000 500 000 = 789 рубт
С уд1 = С1 Qг = 1961761554 500 000 = 3924 руб
В данной части дипломного проекта рассматриваются вопросы организации труда структуры управления предприятием производится расчет производственной и полной себестоимости продукции расчет основных технико–экономических показателей проектируемого горного предприятия или участка.
Организация труда и структура управления предприятием
На руднике принимаются следующие режимы работы: на подземных работах работы производятся в 3 смены по 7 часов (две добычных и одна ремонтно–подготовительная); на поверхности по 8 часов.
Таблица 7.1 – Сводный расчет численности трудящихся
Категории работников
Себестоимость продукци – представляет собой стоимостную оценку используемых в процессе производства продукции природных ресурсов сырья материалов топлива энергии основных фондов трудовых ресурсов а также других затрат на ее производство и реализацию.
Таблица 7.2 – Калькуляция производственной и полной себестоимости
Ремонт горного оборудования руб.
Электроснабжение руб.
Подъемная установка руб.
Рудничный транспорт руб.
Очистные работы руб.
Отчисления на соцстрахование
Вспомогательные материалы
Общерудничные расходы
Полная себестоимость
Расчет основных технико–экономических показателей
Определим полную себестоимость:
Сп = (Ср + Вр) × Дг = (1 084+3252) × 500 000 = 558 260 тыс.руб
где Ср – производственная себестоимость рубт.
Вр – внепроизводственные расходы составляют 3% от производственной себестоимости
Дг – годовая производительность проектируемого участка т.
Определим годовой выпуск товарной продукции:
Qт.п. = Дг × Ц = 500 000 × 155 = 775 000 тыс.руб
где Ц – цена одной тонны соли тыс.руб.
Определим сумму общебалансовой прибыли:
nб = Qт.п. – Сп = 775 000 – 558 260 = 216 740 тыс.руб.
Определим уровень общей рентабельности (%):
Ро = nб × 100 Сп = 216 740 × 100 558 260 = 39%
Определим хозрасчётную прибыль:
где Нп – налог на прибыль тыс.руб.
Нп = 024 × nб = 024 × 216 740 = 52 01760 тыс.руб.
Пх = 216 740 – 52 01760 = 164 72240 тыс.руб.
Производительность труда и трудоёмкость работ:
Определим годовую производительность труда:
Пт.г. = Дг Nсп = 500 000 74 = 6 757 тчел.
Определим трудоёмкость работ:
Тсут = 1000 × NявДсут = 1 000 × 62 1 661 = 37 чел×см1000т.
Фо = Дг Qт.п. = 500 000 775 000 000 = 00006труб.
Фе = Qт.п. Дг = 775 000 000 500000 = 1 550рубт.
Определим срок окупаемости:
Ток =кз Пр=33556152185 21674000000= 15 года.
Таблица 7.3 – Технико–экономические показатели предприятия
Объем годовой добычи
Число рабочих дней в году
Число рабочих смен в сутки
Годовая производительность труда
Уровень рентабельности
Себестоимость продукции
Срок окупаемости кап. вложений
Общие требования безопасности горных работ
Объекты ведения подземных горных работ в соответствии с Федеральным законом от 21.07.97 N 116–Ф3 "О промышленной безопасности опасных производственных объектов" отнесены к опасным производственным объектам.
Для решения задач по безопасности труда на руднике существует специальный отдел «Отдел промышленной безопасности» который следит за соблюдением условий труда на руднике. Обучение по промышленной безопасности проходит каждый поступающий на работу в учебном пункте. За соблюдением и выполнением норм безопасности труда на участке следит мастер.
К основным производственным вредностям на предприятии относятся:
Интенсивное пылевыделение в очистном забое при работе комбайна;
Образование шумов при работе механических установок;
Недостаточное освещение.
Условия труда на руднике относятся к тяжелым что обусловлено сложными горно–геологическими условиями предопределяющими высокий уровень опасности и степени риска при ведении подземных горных работ.
Обеспечение безопасности горных работ достигается общей совокупностью технических и технологических решений а также системой специальных мер по защите горных работ и людей в горных выработках.
Главная вентиляторная установка состоит из двух самостоятельных вентиляторных агрегатов причем один из них – резервный. Главные вентиляторные установки обеспечивают реверсирование струи воздуха поступающего в рудник. Перевод на реверсивный режим должен обеспечиваться за время не более 10 мин. а расход воздуха проходящего по главным выработкам при этом должен быть не менее 60 % от расхода воздуха проходящего по ним в нормальном режиме.
Для надежного контроля параметров рудничной атмосферы на главных входящих и исходящих струях горизонтов оборудуются замерные станции стандартной конструкции длиной не менее 4 м. Для измерений требуется соответствующая аппаратура (анемометры пылемеры газоанализаторы) предусмотренная специальными мероприятиями согласованными с Ростехнадзором России. Главные вентиляторные установки оборудуются депрессиометрами и расходомерами.
Для создания более благоприятных условий по фактору производственного микроклимата в зимнее время предусмотрен подогрев воздуха подаваемого в выработки с помощью поверхностной калориферной установки.
Размеры и форма поперечных сечений выработок определены с учетом безопасных проходов между оборудованием и выработкой.
Безопасность производственных процессов
Наряду с обеспечением безопасности в рамках общей подземной горной системы безусловно должно соблюдаться выполнение требований безопасности участковых и локальных объектов подземной горной системы. Эти меры безопасности являются составной частью проектных решений связанных с конкретными видами горных работ (подготовительными очистными горными работами перевозкой людей и доставкой грузов и т.п.) конкретными видами горного горно–шахтного оборудования и локальными ситуациями возникающими в производственном процессе.
Очистная выемка должна вестись в строгом соответствии с проектом и планом развития работ. Параметры забоев размеры и форма целиков и кровли должны выдерживаться в соответствии с рассчитанными в проекте.
Ходовые отделения наклонных и вертикальных выработок перекрываются лядами или решетками; вентиляционные восстающие и рудоспуски – металлическими решетками или другими предохранительными ограждениями для предотвращения падания людей в выработки. Ходовые отделения должны быть очищены от руды и находиться в состоянии пригодном для пользования. Лестницы должны иметь перила.
Очистные и нарезные выработки проветриваются обособленно. Подача воздуха в тупиковые забои осуществляется нагнетательным способом с помощью вентиляторов местного проветривания установленных в выработках со свежей струей.
Учитывая что от вспомогательного ствола до очистного забоя расстояние более 1км. предусмотрена перевозка людей к рабочим местам и обратно.
В выработках предназначенных для движения самоходного оборудования устанавливаются типовые дорожные знаки регламентирующие движение.
План ликвидации аварий (ПЛА) – это документ предусматривающий все мероприятия по спасению людей застигнутых аварией в шахте по ликвидации аварий в начальный период их развития а также определяющий действия инженерно–технических работников рабочих и ГСВ при возникновении аварии.
Согласно Правилам безопасности ПЛА составляется для каждой шахты находящейся в эксплуатации строительстве или реконструкции.
ПЛА разрабатывается главным инженером шахты и командиром ГСВ на каждые 6 мес. и утверждается главным инженером предприятия за 15 дней до ввода плана в действие.
Регулярный (через 6 мес.) пересмотр ПЛА диктуется изменчивостью условий работы в шахте.и дополнения в ПЛА вносятся в течение суток если введен новый или ликвидирован отработанный участок изменены схемы вентиляции или путей вывода людей.
ПЛА находится у главного инженера шахты горного диспетчера и командира обслуживающего шахту ГСВ.
Совместно с командиром ВГСЧ разрабатывает оперативный план ликвидации аварии согласно которому отдает распоряжения по ликвидации аварии.
Любое лицо обнаружившее аварию или пожар обязаны немедленно сообщить об этом лицу технадзора и принять меры к ликвидации аварии или пожара.
Ответственным руководителем работ по ликвидации аварии является главный инженер шахты а до его прибытия – горный диспетчер.
ПЛА составляется для всех возможных мест аварий в шахте. Для удобства каждому месту аварии присваивается номер (позиция) который наносится на схему вентиляции шахты начиная с поверхности по движению свежей струи (надшахтное здание ствол околоствольный двор и т. д.).
ПЛА состоит из оперативной части распределения обязанностей между лицами участвующими в ликвидации аварии и порядка их действий списка должностных лиц и учреждений которые должны быть немедленно извещены об аварии.
Оперативная часть ПЛА состоит из мероприятий по спасению людей и ликвидации аварий и описания маршрутов движения и заданий отделениям ГСВ для каждой позиции аварии.
К оперативной части плана прилагается схема вентиляции шахты; схема горных выработок с указанием мест расположения всех противопожарных средств установки телефонов и средств спасения работающих при авариях план поверхности шахты с указанием всех выходов из нее водоемов и других средств пожаротушения складов аварийных материалов и оборудования подъездных путей; схема электроснабжения шахты планы околоствольных дворов действующих горизонтов с указанием мест расположения вентиляционных устройств и трубопроводов.
При составлении ПЛА должны быть тщательно продуманы пути выхода людей.
При авариях возможны следующие вентиляционные режимы:
режим нормальной вентиляции (расход и направление движения воздуха не меняются);
реверсирование вентиляции (изменяется направление движения воздуха в выработках на противоположное).
Таблица 8.1 – Оперативная часть. «Очистные камеры – ПОЖАР»
Мероприятия по спасению людей и ликвидации аварии
Ответственные лица и исполнители
Пути и время (мин) выхода людей из аварийного
и угрожаемых участков
Маршруты движения отделений
Маршруты движения отделений ГСВ и задание (отрывная часть)
Вентилятор ВОД – З0М работает нормально.
Подать аварийный сигнал по шахте об аварии и выходе людей на поверхность.
Вызвать ГСВ ВГК. Оповестить лиц по списку (форма №3).
Отключить эл. энергию УПП–3 яч. №1 или ЦПП яч.№10 ЦПП яч. №6 или УПП–6 яч.№1
Использовать подземный транспорт для вывода людей доставка ГСВ материалов средств пожаротушения.
Выставить посты на стволах.
Диспетчер гл. механик шахты.
Диспетчер горный мастер
Горный мастер эл. слесарь
Горный мастер члены ВГК
Диспетчер механик подъема
Люди находящиеся в аварийной камере П–2–З включившись в самоспасатели выходят по ПВШ на ФВШ и движутся на вспомогательный ствол или поднимаются по лестнице на ПВС СВШ через ПВС П–1–3 на ФВШ и движутся к вспомогательному стволу. (51 мин.)
Люди находящиеся в главном стволе в бункере–накопителе включившись в самоспасатели выходят на ГВШ вент. ворота заезд ГВШ клетью выезжают на поверхность вспомогательного ствола. (28 мин.)
Люди находящиеся на ПКШ ПРШ за ПК–80 СКШ за ПК–50
выходят на ФВШ движутся к вспомогательному стволу.(35 мин.) и клетью выезжают на поверхность.
Люди находящиеся на ПРШ до ПК–80 СКШ до ПК–50 через вспомогат. уклон №2 ГТШ №1 движутся к вспомогат стволу
(36 мин.) и клетью выезжают на поверхность.
Люди находящиеся на ГКШ до ПК–70 выходят через заезд ГКШ к вспомогательному стволу а за ПК–70 выходят через уклон гор.–88–81 ГТШ №1 к вспомогательному стволу. (35 мин) и клетью выезжают на поверхность.
I–е отделение ГСВ спускается в шахту клетью по всп. стволу и следует по заезду ГТШ №1 ФВШ ПВС–1–3 СВШ к аварийной камере к очагу пожара для вывода людей и ликвидации пожара
–е отделение ГСВ спускается по вспом. стволу по заезду к транспорт. штреку по ФВШ к аварийной камере к очагу пожара для его ликвидации. Средства пожаротушения находятся в здании АБК (подземный склад ППМ)
Оперативная часть–позиция №17
Таблица 8.2 – Оперативная часть – позиция № 17
Вызвать ГСВ ВГК. Оповестить людей по списку (форма №3)
Выявить количество людей оставшихся за завалом (обрушением)
Отключить эл. энергию на гор.–71м (ТСВП 6660 питающий очистную камеру в которой произошло обрушение).
Вывести людей из очистной камеры через запасной выход на ПВС или по основному заезду на ПВШ
Вентилятор ВОД–30М работает нормально.
Осмотр очистной камеры для выявления места и объёма обрушения.
Выставить посты на стволах
Организация разборки завала
Диспетчер члены ВГК
Горный мастер эл. слесарь дежурный.
Диспетчер гл. механик шахты
Люди находящиеся за завалом выходят через запасной выход на ПВС ( мин.)
Люди находящиеся перед завалом выходят на ПВШ ( мин.)
I–е отделение ГСВ спускается в шахту клетью по всп. стволу и следует по заезду ГТШ №1 ФВШ ПВШ к аварийной камере для вывода людей и разборки завала
–е отделение ГСВ спускается в шахту клетью по всп. стволу и следует по заезду ГТШ №1 ФВШ ПВС–1–3 СВШ к аварийной камере для вывода людей и разборки завала
Оповещение рабочих занятых на подземных работах о немедленном выезде на поверхность производится:
Телефонной связью от диспетчера.
Комплексом аварийного оповещения «СУБР–1П» (многократное отключение света на головных светильниках–8 раз с повторением через 10–20 сек.)
Оценка условий труда
На предприятии произведена аттестация рабочих мест по специальностям и составлены карты аттестация рабочих мест по условиям труда:
машинист ГВМ – по степени вредности и опасности : 34;
– по степени травмобезопасности: 2;
Окончательная оценка тяжести труда – 31.
машинист ПДМ – по степени вредности и опасности : 34;
электрослесарь – по степени вредности и опасности : 32;
по степени травмобезопасности: 2;
Данные условия признаны вредными и опасными. При данных условиях проявляется повышенная усталость больший расход энергии повышенный уровень общей заболеваемости нарушение в работе отдельных органов (в основном обратимые).
На руднике существует много опасных производственных факторов влияние которых на персонал и оборудование может привести к негативным последствиям. На предприятии эксплуатируется большое количество электрооборудования в связи с чем возникает вероятность получения рабочим персоналом электротравм. При обслуживании оборудования прикрепленного к участку электрослесарь может получить электротравму при случайном соприкосновении с токоведущими частями машин. Также причиной электротравм может стать поломка элетрооборудования и повреждение его изоляции.
Для защиты людей от поражения электрическим током предусмотрено защитное заземление. Заземлению подлежат металлические части электротехнических устройств и оборудование нормально не находящиеся под напряжением но которые могут оказаться под напряжением в случае повреждения изоляции а также трубопроводы сигнальные тросы и др. расположенные в выработках с электропроводкой и электроустановками. Заземлению не подлежат металлическая крепь оболочки насосных кабелей металлические устройства для подвески кабеля.
В подземных выработках устраивается общая сеть заземления к которой присоединяются все подлежащие заземлению объекты а также главные и местные заземлители.
На отходящих линиях ЦПП и РПП–6 защита от токов короткого замыкания и утечек должна быть мгновенного действия (без выдержки времени). Для электродвигателей предусматривается также защита от токов перегрузки и нулевая защита.
В подземных установках напряжением до 1140 В также должны использоваться аппараты защиты от утечек токов с автоматическим отключением поврежденной сети.
Центральные подземные подстанции (ЦПП) людские и грузо–людские шахтные подъемные установки вентилятор главного проветривания сетевые и питательные насосы котельных обеспечиваются питанием двумя взаимозаменяемыми кабельными линиями от разных секций поверхностной подстанции а главные водоотливные установки – от ЦПП.
Кабели применяемые в подземных выработках – бронированные с защитными оболочками не распространяющими горение (кроме алюминиевых). Для питания передвижных машин и механизмов для электроустановок в очистных блоках в сетях напряжением 380–660 В применяются гибкие экранированные кабели. Для линий производственной автоматической диспетчерской и аварийной телефонной связи а также прямой телефонной связи подъемных установок используются шахтные телефонные кабели в соответствии с областью применения по действующим техническим условиям.
В подземных выработках допускается применение аппаратов электромашин трансформаторов и приборов только в рудничном исполнении.
Для осветительной сети линейное напряжение – не выше 127 В для стационарного люминесцентного освещения – 220 В; в переносных светильниках – до 36 В. Светильники – только в рудничном исполнении. В сетях связи и сигнализации напряжение питающих сетей – не выше 127 В от осветительной сети аккумуляторных батарей или выпрямительных устройств. Для питания аппаратуры сигнализации допускается напряжение не выше 220 при наличии защиты от токов утечки.
Уровень пола камер ЦПП и главного водоотлива должен быть не менее чем на 05 м выше отметки головки рельсов околоствольного двора в месте его сопряжения со стволом в котором проложены водоотливные трубы.
Камеры подстанций длиной более 10 м имеют по два выхода на противоположных ее сторонах. В камерах предусматриваются свободные проходы для обслуживания монтажа и транспортировки электрооборудования.
Передвижные электроустановки необходимо располагать в хорошо закрепленных местах удобных для обслуживания защищенных от капежа и механических повреждений таким образом чтобы не мешать работе транспорта и передвижению людей. Зазор между электрооборудованием и подвижным составом – не менее 08 м. При размещении электрооборудования в заездах устраивается барьер исключающий заезд подвижного состава на этот участок.
В связи с применением оборудования с вращающимися рабочими органами существует вероятность механической травмы человека.
Промышленная санитария
Мероприятия по защите от вредных газов предусматриваются газовым режимом и учтены в системе вентиляции. Проектом предусматривается также комплекс мер по предупреждению воздействия на людей вредных факторов включающий меры снижения запыленности шума и вибраций на рабочих местах до предельно–допустимых значений установленных санитарными нормами.
Для снижения запыленности воздуха предусмотрена подача свежей струи по выработкам в которых отсутствуют источники пылеобразования (транспортные средства рудоспуски пункты перегрузки и др.). Механическое оборудование применяемое в руднике должно работать с обязательным применением средств снижающих выделение вредностей (пыль вредные газы) уровни шума и вибраций.
Требуемая освещенность в подземных выработках обеспечивается в соответствии с от электросети рудника и светильниками индивидуального пользования.
На руднике существует свой медицинский пункт. В обязанности врачей входит медицинская помощь работникам а также профилактические осмотры всех рабочих рудника. Кроме того каждый год проводится специальное медицинское обучение ИТР и работников технике оказания первой доврачебной медицинской помощи. Для доставки больных в больницы предусмотрен специальный медицинский транспорт. На рабочих местах предусмотрено наличие медицинских аптечек.
На руднике предусмотрен административно–бытовой комбинат с санитарно–бытовыми помещениями в соответствии с нормами строительного проектирования и санитарными нормами. АБК соединяется утепленным крытым переходом с надшахтными зданиями. В АБК оборудуются душевые с раздевалками для чистой и рабочей одежды; комнаты личной гигиены; механическая прачечная; мастерская для починки спецодежды; сушилка для мокрой спецодежды; дезинфекционная камера; мойки и чистки обуви; теплые уборные; кладовую для хранения предметов уборки. Предусмотрены также помещения для хранения чистки и ремонта респираторов; ламповая; помещения для хранения проверки и наладки переносных приборов газового контроля. Здесь же оборудуются пункты питания питьевой воды и здравпункт.
Все санитарно–бытовые помещения имеют вентиляцию обеспечивающую нормативный воздухообмен.
Средства индивидуальной защиты работников
Все работники спускающиеся в рудник должны быть обеспечены индивидуальными аккумуляторными светильниками. Количество исправных светильников должно на 10 % превышать списочное число лиц занятых на подземных работах. Шахтные светильники снабжаются номерами и закрепляются за каждым работником. При получении светильника рабочий обязан убедиться в том что светильник заряжен.
В связи с газовым режимом все работники рудника должны быть обеспечены изолирующими самоспасателями в количестве 11 от списочного состава штата работников занятых на подземных работах. Самоспасатели также закрепляются индивидуально за каждым работником.
В период строительства рудника а также при эксплуатации его для работы в забоях где не могут быть использованы другие средства борьбы с пылью рабочие должны обеспечиваться противопылевыми респираторами типа 3М.
Все работники обеспечиваются касками для защиты головы спецодеждой и обувью.
Для проведения работ на высоте (проведение крепление и ремонтно–профилактическое обслуживание вертикальных выработок) рабочие должны обеспечиваться предохранительными поясами.
Основные мероприятия по обеспечению безопасных и здоровых условий труда
Для решения задач по охране труда на руднике существует специальный отдел «Отдел промышленной безопасности» который следит за соблюдением условий труда на руднике. Обучение по охране труда проходит каждый поступающий на работу в учебном пункте. За соблюдением и выполнением норм охраны труда на участке следит мастер.
Руководство всей работой по охране труда на руднике возложено на генерального директора. Главный инженер заместитель директора по производству главный механик и энергетик возглавляют работу по тем вопросам которые связаны с кругом их деятельности.
Планирование работ по охране труда должно включать разработку мероприятий направленных на предупреждение травматизма на производстве профессиональных заболеваний на улучшение условий труда санитарно–бытового обеспечения работающих. Основные мероприятия по охране труда необходимо оформлять разделом в коллективном договоре или иным соглашением по охране труда между работодателем и профсоюзной организацией или иным представительным органом работников.
Организация обучения и контроля знаний по безопасности труда у рабочих и ИТР.
До назначения на самостоятельную работу или при переводе на другую работу (должность) связанную с обслуживанием электроустановок а также при перерыве в работе свыше 6 месяцев персонал обязан пройти производственное обучение на рабочем месте. Для производственного обучения главным энергетиком (администрацией) предприятия должен быть предоставлен срок достаточный для приобретения практических навыков ознакомления с оборудованием аппаратурой и одновременного изучения;
Обучение должно производиться под руководством опытного работника из числа электротехнического персонала предприятия организации или вышестоящей организации и под контролем административно–технического лица ответственного за эксплуатацию данной установки.
Прикрепление обучаемого к обучающему его работнику должно быть оформлено приказом или распоряжением по предприятию цеху участку.
Обучаемый может производить оперативные переключения осмотры или иные работы в электроустановке только с разрешения и под надзором обучающего.
Ответственность за правильность действия обучаемого и соблюдение им правил ТБ а также правил техники безопасности несет обучающий и сам обучаемый. По окончании сроков обучения обучаемый должен пройти в специальной комиссии проверку знаний по Правилам эксплуатационным и должностным инструкциям техминимуму по обслуживаемому оборудованию.
Объем правил знание которых обязательно тем или иным лицом электротехнического персонала при проверке комиссией устанавливается лицом ответственным за электрохозяйство данного предприятия или вышестоящей организацией.
После проверки знаний каждый работник оперативного и оперативно–ремонтного персонала должен пройти стажировку исполняющего обязанности по рабочему месту (дублирование) продолжительностью не менее 2 недель под руководством опытного работника после чего он может быть допущен к самостоятельной работе. Допуск к стажировке и самостоятельной работе осуществляется для инженерно–технических работников распоряжением по предприятию для рабочих – распоряжением по цеху.
Для ремонтного персонала дублирование не требуется.
Периодическая проверка знаний персонала по ПТБ и производственным инструкциям должна производиться в следующие сроки:
раз в год – для персонала электролабораторий и персонала непосредственно обслуживающих действующие электроустановки или проводящего в них наладочные электромонтажные ремонтные работы или профилактические испытания а также персонала оформляющего распоряжения и организующего эти работы;
раз в 3 года – для ИТР не относящихся к персоналу предыдущей группы. При неудовлетворительной оценке знаний ПТБ повторная проверка может быть произведена в сроки установленные квалификационной комиссией но не ранее чем через 2 недели.
Персонал показавший неудовлетворительные знания при третьей проверке не допускается к работе в электроустановках и должен быть переведен на другую работу не связанную с обслуживанием электроустановках.
Проверка знаний по Правилам должна производиться в комиссии того предприятия где работает проверяемый. В другой какой–либо организации проводить проверку знаний Правил не допускается. За исключением проверки знаний командированных лиц.
Проверка знаний каждого работника должна производиться индивидуально.
Результаты проверки знаний работников заносятся в журнал установленной формы.
Каждому работнику успешно прошедшему проверку выдается установленной формы удостоверение о проверке знания Правил с присвоением квалификационной группы по ТБ.
Допуск к самостоятельному дежурству или самостоятельной работе в электроустановках оформляется специальным распоряжением по предприятию цеху участку.
С целью овладения персоналом наиболее совершенными методами работы повышения знаний по устройству и эксплуатации оборудования должны быть организованы:
курсовое обучение по повышению квалификации;
изучение ПТБ ПУЭ инструкций и других правил относящихся к работе данных установок;
проведение противоаварийных тренировок на рабочих местах для обучения эксплуатационного персонала наилучшим способам и приемам быстрого предупреждения и ликвидации неполадок и аварий;
периодический производственный инструктаж непосредственно на рабочих местах для обучения персонала правильному и безопасному уходу за оборудованием рациональным методам работы и устранению возможных неполадок с оборудованием с оформлением в журнале инструктажа.
Систематическую работу с персоналом обязаны организовать и лично контролировать главные энергетики начальники электроцехов или ответственные за электрохозяйство а также электрики вышестоящей организации группы мелких потребителей.
Рабочие обязаны знать и строго выполнять правила внутреннего трудового распорядка для рабочих и служебных подразделений.
Рабочие должны соблюдать производственную дисциплину выполнять инструкции по технике безопасности охране труда а также распоряжения и указания лиц технического надзора.
Бригадир звеньевой. Рабочие обязаны точно выполнять выданный им наряд в полном соответствии с инструкцией по ТБ техническими документами (паспорт проект) выданными указанием горного надзора с учетом конкретной обстановки в выработке забое.
Без разрешения горного надзора запрещается производить какие–либо работы которые не входят в их постоянные обязанности и которые не связаны с неотложной необходимостью действия для предотвращения аварий или несчастного случая.
Рабочие обязаны следить за своей спецодеждой вовремя сдавать в стирку починку и согласно установленных сроков производить её замену.
Противопожарная защита
Для обеспечения пожарной безопасности рудника предусматривается комплекс мер противопожарной защиты.
Копры и надшахтное здание клетевого ствола по которому подается свежий воздух сооружаются из несгораемых материалов. Башенные копры подъемных установок оборудованы с наружной стороны металлическими лестницами обеспечивающими безопасный выход людей с каждой отметки копра на шахтную поверхность. Все помещения и вентиляционный канал ВГП все калориферные каналы и их сопряжения с выработками на протяжении не менее 10 м выполняются из несгораемых материалов. Вентиляционный канал оборудован двумя клапанами (заслонками) исключающими при их закрытии поступление наружного воздуха. Устье канала выходит в отдельное здание из несгораемого материала с решетками на окнах и металлическими дверями легко открывающимися изнутри. Этот ход служит запасным выходом.
Стволы закрепляются несгораемой крепью на всю глубину. Несгораемая крепь предусмотрена также для всех капитальных выработок.
Устья стволов оборудованы стальными лядами. Управление ими в клетевом стволе может осуществляться как непосредственно из копра так и снаружи надшахтного здания.
Лесные угольные склады склады ГСМ и др. пожароопасные материалы размещены на расстоянии более 100 м от надшахтных зданий и сооружений с учетом господствующих направлений ветров (с подветренной стороны по отношению к ВГП).
На руднике предусматривается наличие технических средств противопожарной защиты запас первичных средств пожаротушения специальных огнетушащих средств (порошковых углекислотных и др.).
Для хранения противопожарных материалов и оборудования организуются склады: 1 – на поверхности; под землей – на каждом действующем горизонте (на первом этапе – 2 подземных склада). Все склады закрываются на замок и пломбируются.
В выработках с входящей струей воздуха и на всех горизонтах вблизи околоствольных дворов устанавливаются двойные легко закрывающиеся по ходу воздушной струи металлические (несгораемые) двери расстояние между которыми не более 10 м.
К чрезвычайным ситуациям на руднике относятся:
затопление выработок;
отключение электроэнергии на особо важных объектах
Источниками пожара на руднике могут стать:
пробой изоляции силовых кабелей
пробой обмоток силовых трансформаторов и т.д.
Причиной затопления выработок может стать:
неисправность аппаратуры управления насосами;
неисправность насосов водоотливной установки.
Причиной отключения электроэнергии может стать:
прямое попадание молнии в ГПП;
обрыв ЛЭП питающей рудник;
неисправность силовых трансформаторов;
Аварийные ситуации возможны в системе водоотведения шахтных вод и при перекачке сточных вод.
Нормальная эксплуатация системы водоотведения шахтных вод осуществляется по одной нити водоводов. При аварии на работающей нити водоотлив переключается на резервную нить. Возможные аварийные ситуации обусловленные превышением нормального водопритока в шахтные выработки ликвидируются включением резервных насосных агрегатов шахтного водоотлива.
Демонтаж и монтаж комбайна Урал–20 А
Разгрузка и прием изделия получателем
Комбайн отгружается с завода на открытых железнодорожных платформах частично разобранным на основные сборочные единицы без специальной упаковки. Запасные части инструмент техническая документация электрический и гидравлический пульт управления гидроцилиндры и другие малогабаритные узлы и детали снимаемые на время транспортирования с комбайна отгружаются упакованными в деревянные ящики.
Перед разгрузкой комбайна с платформы освобождаются его и основные сборочные единицы от растяжек распорных и упорных брусков.
Разгрузку следует начинать с ящиков и демонтированных сборочных единиц.
Грузоподъемность средств используемых при разгрузке комбайна должна быть не менее 25 т.
К месту хранения комбайн и остальной груз доставляется любым транспортом исключающим возможность повреждения грузоподъемностью не менее 25 т. со скоростью не более 20 кмчас.
Получатель принимая комбайн должен проверить комплектность поставки подвергнуть комбайн и демонтируемые сборочные единицы внешнему осмотру с целью выявления возможных повреждений во время транспортировки.
В процессе проверки устанавливается соответствие договору на поставку поступившего комбайна соответствия оборудования упаковочной ведомости наличие предусмотренной технической документации инструмента запасных частей и принадлежностей.
Подготовка комбайна к монтажу
Перед монтажом комбайна необходимо выполнить следующие работы:
Распаковать и освободить оборудование от тары.
Снять защитные заглушки пробки и т. д. с редукторов трубопроводов шлангов и мест их подсоединения.
Очистить все сборочные единицы и детали от пыли и грязи.
Произвести расконсервацию сборочных единиц и деталей для чего снять консервационную смазку промыть и протереть.
Внутренние поверхности редукторов и деталей гидросистемы расконсервации не подлежат.
Осмотреть трубопроводы гидросистемы и при необходимости произвести их промывку.
Тщательно осмотреть все электрооборудование на предмет выявления механических повреждений обратив особое внимание на состояние кабелей и механической защиты блокировок и взрывозащищенных поверхностей.
Проверить соединение обмоток двигателей.
Проверить сопротивление изоляции электрических цепей относительно корпуса мегаометром на 1000 В в течении 1 минуты при этом сопротивление должно быть не менее 05 МОм при сопротивлении изоляции двигателей ниже допустимого их необходимо просушить.
После всех выше перечисленных проверок комбайн сначала собирается на поверхности для точной готовности комбайна для работы в шахте после чего комбайн снова разбирается для спуска в шахту.
Инструкция по ТБ для подземного электрослесаря.
Данная инструкция распространяется на подземных электрослесарей обслуживающих действующие подземное электрооборудование рудников производящих оперативное переключение выполняющих ремонтные монтажные и наладочные или ремонтные работы.
Электрослесарь всегда должен помнить что от правильности выполняемых им методов обслуживания ремонта и монтажа в значительной степени зависит безопасность использования рудничного электрооборудования в рудниках.
Электрооборудование перед спуском должно быть осмотрено и проверено электрослесарем и по возможности опробовано при работе в холостую или даже под нагрузкой в присутствии лица надзора.
Спуск комбайна в шахту производится в клети или под клетью по частям:
На работе по монтажу наладке спуску обслуживанию и ремонту электрооборудования в подземных выработках могут назначаться только электрослесари прошедшие обучение и стажировку на рабочем месте сдавшие экзамены и получившие удостоверения с указанием в нем квалификационной группы по ТБ на право производства этих работ. При необходимости остановки какой–либо подземной машины или механизма с целью их осмотра электрослесарь должен получить на это разрешение лица надзора участка в технологическом цикле которого они используются. Если же машины или механизмы используются в общерудничной технологической цепи то на их остановку электрослесарь должен получить разрешение горного диспетчера (дежурного по шахте).
О всех замеченных неисправностях электрооборудования электрослесарь должен сообщить дежурному надзору участка. А в экстренных случаях – горному диспетчеру.
Спуск негабаритного оборудования по стволу под клетью является наиболее ответственной операцией выполняемой с предельной внимательностью. Для выполнения которой составляют проект организации работ по спуску утверждаемый главным инженером рудника.
Проект состоит из пяти частей: общей; подготовительных работ; организации работ; объема работ; техники безопасности.
Одним из основных и опасных моментов являются ввод груза в клетевое отделение ствола и его вывод так как при этом возможны динамические нагрузки на подвесные устройства и даже внезапный обрыв оттяжного троса а также сопровождение негабаритного груза при спуске так как возможно перекашивание а следовательно и заклинивание в стволе.
С целью четкой организации работ каждый участник должен твердо знать свое местоположений и круг обязанностей.
Начальник участка должен: согласовать с диспетчером работу клетьевого и скипового подъема в период начала и окончания спуска; письменно извещать механика подъема о дате и времени начала и окончания спуска; выдавать наряд на производство работ который должен быть утвержден старшим лицом технического надзора шахты; сообщать диспетчеру рудника об окончании работ по спуску.
Механик подъема обязан выдавать наряд машинисту клетьевого подъема на производство работ по спуску и производить инструктаж по безопасным методам проведения спуска.
Лицо технического надзора смены должно: осуществлять непосредственное руководство работы по спуску; определять местонахождение и обязанности каждого рабочего участвующего в процессе спуска; предупреждать машиниста клетьевого подъема о характере спускаемого груза.
Машинист клетьевого подъема должен остановить клеть и поставить в известность механика подъема о нарушениях при спуске груза и возобновить работу по спуску только после указания главного механика шахты.
Работы по спуску обычно проводит бригада в составе шести человек представленная двумя звеньями. Первое звено под руководством лица технического надзора занято на спуске а второе – под руководством бригадира осуществляет прием груза площадке.
Состав и обязанности звена:
–й рабочий – бригадир (звеньевой) непосредственно руководит работой звена и выполняет работы по строповке и креплению груза производит подачу груза в ствол и извлечение его из ствола; обязан иметь удостоверение и опыт работы машиниста тяговой лебедки и стропальщика;
–й рабочий выполняет работы по строповке груза и извлечению оттяжной стороны подает сигнал первому рабочему при оттяжке груза от ствола к выработкам; обязан иметь удостоверение стропальщика;
–й рабочий выполняет вспомогательные работы.
В период подготовки к спуску ответственное лицо технического надзора совместно с бригадиром обязаны: произвести осмотр площадок – погрузочной на поверхности и приемной на горизонте – с выдачей соответствующих указаний по удалению не нужного оборудования приспособлений и др.: произвести осмотр и проверку вспомогательных механизмов и приспособлений (лебедок блоков грузозахватных средств подвесных устройств стопоров оттягивающих тросов и прицепных устройств) на исправность обращая внимание при этом на тормозные устройства заземление и целостность тросов; удостовериться в наличии и исправности рабочего инструмента вспомогательных материалов (ломы крючья зажимы ключи молотки и т.д.) и предохранительных поясов; проверить чистоту пола клети под которую будет подвешен спускаемый груз; в соответствии с нарядом каждому рабочему указать его рабочее место объем работы и возложенные на него обязанности.
Основные составные части комбайна (вес)
редуктор раздаточный правый с двумя редукторами и режущими дисками (4840 кг.)
редуктор раздаточный левый с двумя редукторами и режущими дисками (4840 кг.)
редуктор исполнительного органа с двигателями левый (6720 кг.)
редуктор исполнительного органа с двигателями правый (6720 кг.)
барабан отбойного устройства (1028 кг.)
редуктор привода отбойного устройства верхний 2 штуки (1260 кг.)
редуктор привода отбойного устройства нижний 2 штуки (932 кг.)
редуктор бермовых фрез 2 штуки (2860 кг.)
шнеки (средняя часть бермового органа 853 кг.)
кронштейн бермового со шнеком 2 штуки (475 кг)
кронштейн (полубланка) правый (1960 кг.)
кронштейн (полубланка) левый (1960 кг.)
элементы системы пылеотсоса (1320 кг.)
рама грузчика передняя (2745 кг.)
рама грузчика задняя (2650 кг.)
баки системы смазки редукторов (295 кг.)
насосная станция (890 кг.)
кабина машиниста (с гидропультом и электропультом управления 1036 кг.)
станция управления (1310 кг.)
бурильная установка (903 кг.)
конвейер скребковый (2859 кг.)
рама гусеничного хода (4000 кг.)
гусеничная цепь 2 штуки (1965 кг.)
редуктор гусеничного хода 2 штуки (1965 кг.)
тележка гусеничная 2 штуки (1265 кг.)
цепь скребковая (568 кг.)
секция щита верхняя 2 штуки (163 кг.)
секция щита нижняя 2 штуки (292 кг.)
проставка исполнительного органа 2 штуки (785 кг.)
рама гусеничного хода
редуктор раздаточный с двумя редукторами резцовых дисков
редуктор исполнительного органа
Перед клетью под которой спускаю груз перекрывают ствол стволовой лядой.
Рабочие выполняющие эту работу должны быть оснащены предохранительными поясами.
Работу по подготовке комбайна ведет бригада слесарей под руководством механика внутришахтного транспорта. С целью уменьшения массы комбайн разбирают и каждая его составная часть не должна превышать 1 т.
Руководитель спуска обязан проконтролировать подготовку комбайна и принять его у механика ВШТ. Все работы по спуску комбайна Урал–20 А должны производиться в соответствии с инструкцией по спуску и подъему длинномерных и негабаритных грузов и оборудования по стволу рудника.
Инструкция по спуску и подъему длинномерных и негабаритных грузов и оборудования по стволу рудника.
Составлена в соответствии с требованиями «Единых правил безопасности при разработке рудных нерудных и россыпных месторождений полезных ископаемых подземным способом»
Спуск–подъём грузов по стволу является работой с повышенной опасностью. Небрежное отношение и нарушение правил безопасности может привести к крупной аварии с подъёмной машиной армировкой ствола.
Лицом ответственным за спуск–подъём длинномерных и негабаритных грузов и оборудования по стволу рудника является механик подъёма.
Перед началом работы по спуску–подъему грузов рабочие должны получить письменный наряд на спуск грузов по стволу (информацию о спускаемых грузах специальный инструктаж – в зависимости от сложности спускаемого груза) от механика подъёма. После этого расписаться в журналах за получение письменного наряда инструктажа
О спуске–подъёме грузов и оборудования ставятся в известность машинист подъёма рукоятчик стволовой.
Негабаритными грузами оборудованием являются оборудование узлы оборудования материалы которые по своим габаритным размерам не помещаются в клеть и транспортируются под клетью.
Подготовка негабаритных грузов к спуску производится на нулевой площадке.
Перед началом работы по спуску–подъёму должна быть проверена исправность инструмента приспособлений чалок предохранительных поясов очищено рабочее место от ненужного оборудования материалов.
Стропы для подвески грузов должны быть подобраны по весу груза
Рабочие бригады должны внимательно следить за сигналами и распоряжениями старшего и выполнять их.
Во время подъёма или спуска грузов не допускать рывков или толчков.
При работах по спуску–подъёму около ствола не должны находиться посторонние люди.
После затаскивания материала под клеть и расчаливания его стволовые двери должны быть немедленно закрыты.
Работы вблизи ствола при открытых дверях должны производиться рабочими с надетыми предохранительными поясами и прицепленными к конструкции копра здания.
Предупреждение вращения или раскачивания груза под клеть регулируется расчаленными пеньковыми канатами катанкой с противоположных сторон или другими приспособлениями.
Рельсы спускаются специальной стропой согласно схеме строповки.
Круглый и пиленый пиломатериал сверлить сверлом 40 мм отступая от начала комля не менее 05м и крепить специальной стропой согласно схеме строповки.
Вес спускаемых грузов не должен превышать грузоподъёмность подъемной машины.
Приём грузов в шахте и складирование их должно производиться бригадой во главе со старшим рабочим.
Для удобства и безопасности производства работ при завозке грузов в ствол и выдаче из ствола к нижней части длинномерных материалов и грузов необходимо привязывать специальные верёвки с помощью которых и производится удержание от качки.
Спуск грузов под клетью должен производиться со скоростью не более 2 мсек. а громоздких грузов– не более 03м сек.
Вывоз и прием груза из ствола должен производиться с помощью верёвки привязанной к грузу тягальной лебёдкой электротолкателем соблюдая при этом соответствующие кодовые сигналы. Вытащенный груз должен убираться от ствола и складироваться в стороне соблюдая габариты для прохода людей.
При возникшей опасной ситуации во время подготовки к спуску или в процессе спуска–подъёма необходимо немедленно прекратить работу и сообщить лицу технического надзора.
Рабочие занятые на спуске–подъёме грузов несут ответственность:за качество выполненных работ и сохранность спускаемых и поднимаемых грузов;
за строгое соблюдение правил ТБ и нарушение настоящей инструкции;
за нарушение трудовой и производственной дисциплины.
Организация работ по спуску
На подготовительной площадке:
В клети на пол укладывают трубу размером 168*8 мм. и приваривают её к полу клети.
Спускаемую деталь (на примере показана рама конвейера) с помощью мостового крана подают к стволу на расстояние не более 5 м. от клети и укладывают её на ствольную ляду.
Два несущих каната диаметром 31 мм. заводят за трубу а свободные концы через монтажные люки в полу клети выводят из клети и закрепляют за раму конвейера.
По указанию ответственного лица машинист поднимает клеть с грузом и рама конвейера находится в висячем положении.
По указанию ответственного лица двое рабочих закрепляют два троса с одного и другого бока клети а другие концы за бока рамы конвейера (это нужно для того чтобы рама при спуске не раскачивалась).
После того как ответственное лицо убедилось что груз надежно закреплен подает команду убрать стволовую ляду.
Связь с участниками спуска осуществляют по телефону или рации.
Машинисту клетьевого подъема подается команда о проведении спуска.
Скорость спуска не должна превышать 05 мc.
Сигнал «стоп» свидетельствующий об окончании спуска подают тогда когда уже возможно захватить крюком лебедки раму.
На приемной площадке
Рабочий застрахованный предохранительным поясом подцепляет раму крюком лебедки и отцепляет боковые поддерживающие канаты.
По соответствующему сигналу машинист подъема опускает рабочий с помощью каната тяговой лебедки вытягивает раму из ствола устанавливает на приемную площадку
Несущий канат отсоединяют от рамы конвейера и убирают из клети.
Опускаемую раму конвейера с помощью машины 1ВОМ–А с крановой установкой (до 1 т.) грузят на несущую тележку (до 35 т.) этой же машины перевозят в монтажную камеру.
Доставка до монтажной камеры
При доставке должны быть приняты все меры исключающие повреждение сборочных единиц и деталей. При этом необходимо чтобы трубы гидросистемы подсоединительные штуцера а также открытые полости редукторов были заглушены как во время транспортирования так и при монтаже.
На месте сборки комбайна необходимо подготовить монтажную камеру которая должна иметь размеры не менее: по ширине 10 м. по высоте 5 м. по длине не менее 20 м. Кровля камеры должна быть закреплена в соответствии с утвержденным паспортом.
Монтаж комбайна производиться лебедками с тяговыми усилиями не менее 10 т. через блоки подвешенные к кровле выработки в нашем случае имеется мостовой кран. На месте сборки должен находиться необходимый слесарный инструмент ветошь ванна с соляровым маслом. Камера должна быть хорошо освещена оборудована противопожарными средствами.
На месте монтажа комбайна должен быть обеспечен безопасный проход персонала производящего монтаж.
Перед началом монтажа необходимо проверить исправность подъемных средств безопасность ведения работ и правильность расстановки людей.
В данном дипломном проекте все расчеты проводились в соответствии с нормативами учебного пособия для дипломного проектирования по специальности 15.04.02 «Горные машины и оборудование».
В разделе «Горная часть» данного проекта был рассмотрен Тыретский солерудник его горно–геологическая характеристика способ вскрытия система разработки.
В разделе «Механизация очистных работ» было произведено технико–экономическое сравнение двух вариантов комбайнов: Урал–20 А и Урал–10 Р . На основании технико–экономического сравнения двух вариантов принят комбайн Урал– 20 А. Данный комбайн характеризуется большей производительностью. Приведен детальный расчет мощности привода исполнительного органа данного комбайна.
В разделе «Механизация транспортных работ» было произведено технико–экономическое сравнение двух самоходных вагонов: 5ВС–15 и 5ВС–10 . На основании технико–экономического сравнения двух вариантов принят самоходный вагон 5ВС–15. Данная машина характеризуется большей производительностью чем самоходный вагон 5ВС–10 который не будет справляться с планируемой годовой производительностью.
Так же в разделе «Механизация транспортных работ» был произведен технико–экономический расчет двух конвейеров: 1Л100У и 1Л80. Данные конвейера удовлетворяют планируемой производительности рудника. Приведен детальный расчет данных конвейеров.
В разделе «Стационарные установки» дано описание и произведен расчет подъемной машины водоотлива вентиляционной установки.
В разделе «Электроснабжение» выполнен расчет освещения мощности трансформаторных подстанций расчет кабельной сети конвейерных линий и заземления.
трансформатор ТСВП 6306
трансформатор ТСВП 2506
для кабельной сети выбран кабель СБн–6000
В разделе «Ремонт горного оборудования» произведен расчет ремонтной базы для ремонта горных машин и оборудования а так же рассмотрены вопросы планирования планово–предупредительного ремонтов их количество продолжительность и объемы работ по каждому виду ремонтов. Составлен годовой график ППР. Произведено определение мощности механических мастерских произведен расчет капитальных и эксплуатационных затрат по оборудованию ремонтной базы.
В специальном вопросе горной части рассмотрена тема: «Демонтаж–монтаж комбайна Урал–20 А» В данном разделе рассмотрены схемы разборки комбайна и его спуск в шахту посредством клетьевого подъема доставка до монтажной камеры для дальнейшей сборки и эксплуатации.
В разделе «Экономика» приведены таблицы:
штат управления предприятия;
калькуляция производственной и полной себестоимости;
технико–экономические показатели предприятия;
расчеты технико–экономических показателей;
рентабельность продукции составила 39%.
Перечень условных обозначений символов единиц
m м – мощность пласта;
Q м3с м3мин – объемный расход подача насоса;
fед.– крепость руды;
Q – производительность;
WкВт*час – электроэнергия;
градус – угол бокового развала борозды резания;
ZnкН – среднее значение силы резания на передней грани резца;
Gт – грузоподъемность;
gмс2 – ускорение силы тяжести;
qлНм – линейный вес ленты;
Нм2 – разрывное усилие;
втед.– число витков трения;
мм – зазор между соседними витками;
αнград.– внутренний угол девиации;
Тзсек.– время загрузки скипа;
iед.– передаточное число
Библиографический список
Библиографический список:
Горные машины и оборудования подземных разработок. Методическое указания к дипломному проектированию. Составители Я.Н. Долгун Д.Е. Махно. – Иркутск: Изд–во ИрГТУ 2001 – 28 с.
Электрификация горных работ. Методическое пособие по выполнению курсового и дипломного проектов. Составители А.И. Найденов Е.А. Дмитриев. Издательство ИрГТУ 2002. – 68 с.
Н.В. Тихонов. Транспортные машины горнорудных предприятий. Учебник для вузов. 2–е изд. перераб. И доп. М.: Недра. 1985 336 с.
Б.Н Неклепаев И.П. Крычков Электрическая часть электроподстаний и подстанций: Справочные материалы для курсового и дипломного проектирования: Учебник. Пособие для вузов. – 4–е изд. перераб. И доп. – М.: Энергоатомиздат 1989. 608с.:ил.
Ю.М. Коледин Я.Н. Долгун. Транспортные машины при разработке месторождений полезных ископаемых подземным способом: Учебное пособие. – Иркутск: Изд–во ИрГТУ 2004. – 123 с.
Под ред. Г.Я. Пейсаховича. Справочник. Подземный транспорт шахт и рудников. – М.: Недра 1985.
В.И. Щуцкий и др. Электропривод и электрификация подземных горных работ. Учебник – М.: Недра 1981. – 319 с.
В.И. Щуцкий Н.И. Волощенко. Электрификация подземных горных работ. – М.: Недра 1986. – 364 с.
М.С. Бинус и др. Новые виды электрооборудования в нормальном рудничном испытании. – М.: Недра 1987. – 89 с.
Под ред. В.А. Гребенюка Я.С. Пыжьянова И.Е. Ерофеева. Справочник по горнорудному делу. – М.: Недра 1983. – 816 с.
М.П. Александров Л.Н. Колобов Н.А. Лобов и др. Грузоподъемные машины. – М.: Машиностроение 1986. – 400 с.
П.М. Шилов. Технология производства и ремонт горных машин. – М.: Недра 1971. – 384 с.
Л.М. Щербакова. Методические указания по дипломному проектированию для студентов специальностей 17.01. и 21.05. Экономика организация и менеджмент. – Иркутск.: ИрГТУ 2006. – 29 с.
Д.Е. Махно Н.Н. Страбыкин В.Н. Кисурин Горные машины и комплексы. Краткий курс лекций. Часть 2. – Иркутск.: ИрГТУ 1996. – 202 с.
К.З. Ушаков Б.Ф. Кирин Н.В. Ножкин. Охрана труда. – М.: Недра 1986. – 616 с.
Д.Е. Махно Н.Н. Страбыкин С.С. Леоненко А.И.Шадрин Я.Н. Долгун Эксплуатация горных машин и оборудования.– Иркутск.: ИрГТУ 2001.–550с.
Положение о планово предупредительном ремонте оборудования и транспортных средств угольной и горнорудной промышленности.–М.: Недра 1965. – 112 с.
Единые правила безопасности при разработке рудных нерудных и рос-сыпных месторождений полезных ископаемых подземным способом. (ПБ-0-553-03). –М.:НТЦ 2004. – 198с.
В.Ф.Замышляев В.И.Русихин Е.Е.Шешко. Эксплуатация и ремонт карьерного оборудования: Учеб.пособие для вузов.–М.:Недра1991.–285 с.: ил.
А.П. Макаров В.М. Горячкин С.Ю. Красноштанов. Методические указания по выполнению курсового проекта для студентов специальности 150402. Основы эксплуатации горных машин и оборудования. – Иркутск.: ИрГТУ 2008. – 32 с.
С.С. Тимофеева Ю.В. Шешуков. Безопасность жизнедеятельности. Учебное пособие. Издание 2–е переработанное и дополненное – Иркутск.: ИрГТУ 2007. – 353 с.
Подъемная установка.dwg

Скип в точке загрузки
Скип в точке разгрузки
Схема вскрытия шахтного поля.dwg
Надшахтное здание Здание подъёмных машин Вентиляторно-калориферная
Надшахтное здание Здание подъёмных машин
Северный вентиляционный штрек
Северный конвейерный штрек
Панельная вентиляционная сбойка №2-з
Разведочный штрек №4
Панельная вентиляционная сбойка №1-з
Панельный вентиляционный штрек
Панельный конвейерный штрек
Панельная вентиляционная сбойка №3-з
Заезд на Главный ствол
Заезд к Главному транспортному штреку №1
Заезд к Главному транспортному штреку №2
Вентиляционная сбойка
Главный транспортный штрек №2
Главный конвейерный штрек
Главный вентиляционный штрек
Главный транспортный штрек №1
Конвейерный уклон №1
Вспомогательный ствол
Панельный разрезной штрек
Вспомогательный уклон №2
Фланговый вентиляционный штрек
Камера подземных гаражей
Габариты машины 1ВОМ А
Сечение конвейерного штрека
Схема вскрытия и подготовки шахтного поля
Параметры системы отработки
Сечение скипового ствола
Рекомендуемые чертежи
- 12.06.2019