Механическое оборудование карьеров


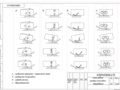
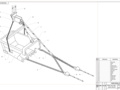
- Добавлен: 24.01.2023
- Размер: 4 MB
- Закачек: 0
Узнать, как скачать этот материал
Подписаться на ежедневные обновления каталога:
Описание
Механическое оборудование карьеров
Состав проекта
![]() |
![]() |
![]() ![]() |
![]() ![]() |
![]() ![]() ![]() ![]() |
![]() ![]() |
![]() ![]() ![]() ![]() |
![]() ![]() ![]() |
Дополнительная информация
Контент чертежей
Схема работы шагающе-рельсового оборудования.dwg

Ось существующего патрубка
Рама насосного агрегата
ДОФПО.19411.00.00.СБ
В-В (повернуто) М 1:40
Г-Г (повернуто) М 1:40
ДОФПО.19407.00.00.СБ
ДОФПО.19411.01.00.СБ
Патрубок всасывающий
Спецификация дана на 4 насосных агрегата. 2. Чертежи фундаментов смотри в строительной части проекта. Чертеж №ДОФПО.19411-КЖ 3. На сечениях А-А
Б-Б патрубок всасывающий условно не показан. 4. Сварные швы по ГОСТ5264-80. Электроды Э42 ГОСТ 9467-75. а) Фланцы приварить сплошным швом. Катет швов 8мм. Контроль методом керосиновой пробы. б) Раму к закладной детали фундамента приварить по периметру прерывистым швом 100х100мм катетом 10мм. 5. Внутренне пространство рамы заполнить бетоном (насос №1 и №2). 6. Покраску оборудования выполнить в соответствии с ГОСТ 12.4.026-80. 7. * Размеры для справок. 8. ** Размеры уточнить при монтаже.
Болт М20х120 Гост 7798-70
Шайба 20 Ст3 ГОСТ10450-78
Гайка М20 ГОСТ 5915-70
ДОФ. Участок №2. Замена агрегатов насосных (1
) с насосами 6НП на агрегаты насосные с насосами WARMAN 8-6 Е-АН.
Согласовано: Главный электромеханик Шпаков Ю.
Главный инженер ДОФ Горбулев А. Главный механик ДОФ Бородин А.
Контур существующего фундамента
ДОФПО.19417.00.00.СБ
Агрегат насосный (с заниженной рамой)
А-А(повернуто) М 1:20
Б-Б(повернуто) М 1:20
ДОФПО.19411.01.00-01.СБ
Шайба 20 65Г ГОСТ6402-70
Болт М20х70 Гост 7798-70
ШГПО.19819.01.00.00.СБ
ШГПО.19819.02.00.00.СБ
Схема работы шагающе-рельсового оборудования
а - кривошипно-шарнирный с треугольной рамой; б - кривошипно-ползункового; в - гидравлического; г - двухкривошипного"
ковш с упряжью драглайна_2007.dwg

Ось существующего патрубка
Рама насосного агрегата
ДОФПО.19411.00.00.СБ
В-В (повернуто) М 1:40
Г-Г (повернуто) М 1:40
ДОФПО.19407.00.00.СБ
ДОФПО.19411.01.00.СБ
Патрубок всасывающий
Спецификация дана на 4 насосных агрегата. 2. Чертежи фундаментов смотри в строительной части проекта. Чертеж №ДОФПО.19411-КЖ 3. На сечениях А-А
Б-Б патрубок всасывающий условно не показан. 4. Сварные швы по ГОСТ5264-80. Электроды Э42 ГОСТ 9467-75. а) Фланцы приварить сплошным швом. Катет швов 8мм. Контроль методом керосиновой пробы. б) Раму к закладной детали фундамента приварить по периметру прерывистым швом 100х100мм катетом 10мм. 5. Внутренне пространство рамы заполнить бетоном (насос №1 и №2). 6. Покраску оборудования выполнить в соответствии с ГОСТ 12.4.026-80. 7. * Размеры для справок. 8. ** Размеры уточнить при монтаже.
Болт М20х120 Гост 7798-70
Шайба 20 Ст3 ГОСТ10450-78
Гайка М20 ГОСТ 5915-70
ДОФ. Участок №2. Замена агрегатов насосных (1
) с насосами 6НП на агрегаты насосные с насосами WARMAN 8-6 Е-АН.
Согласовано: Главный электромеханик Шпаков Ю.
Главный инженер ДОФ Горбулев А. Главный механик ДОФ Бородин А.
Контур существующего фундамента
ДОФПО.19417.00.00.СБ
Агрегат насосный (с заниженной рамой)
А-А(повернуто) М 1:20
Б-Б(повернуто) М 1:20
ДОФПО.19411.01.00-01.СБ
Шайба 20 65Г ГОСТ6402-70
Болт М20х70 Гост 7798-70
ШГПО.19819.01.00.00.СБ
ШГПО.19819.02.00.00.СБ
Чертеж-схема ковша с упряжью драглайна
Проушина тяговой цепи
Проушина цепи подъема
Механическое оборудование карьеров..docx
Государственное образовательное учреждение
Высшего профессионального образования
«Московский государственный открытый университет им.Черномырдина»
по «Механическое оборудование карьеров»
Тема: «Классы машин применяемые на открытых горных работах. Технологическое назначение машин. Конструктивное устройство машин горнотранспортного комплекса.»
Руководитель: Климов В.Н.
Принцин комплексной механизации в горнотранспортном комплексе ..
Структура комплексной механизации ..
Взаимосвязь горнотранспортного комплекса с последующими технологическими процессами переработки полезного ископаемого.. ..
Классы машин применяемые на открытых горных работах
Выемочно-погрузочные машины
Конструктивные схемы одноковшовых экскаваторов .
Ходовое оборудование экскаваторов
Шагающее ходовое оборудование экскаваторов. Схемы механизмов шагания
Назначение. Техническая характеристика. Конструктивное
устройство драглайна ЭШ 40.100
Рабочее оборудование драглайна
Шагающе-рельсовое ходовое оборудование .
Правила устройства монтажной площадки для монтажа горных
Принцип комплексной механизации в горнотранспортном комплексе.
Структура комплексной механизации.
Производственные процессы на открытых горных работах слагаются из основных и вспомогательных операций связанных единой технологической схемой во времени и пространстве и обеспечивающих в общем случае подготовку горных пород к выемке их выемку транспортирование первичную переработку складирование и отгрузку потребителю а также выполнение других необходимых в едином горном производстве процессов. Машины и механизмы выполняющие эти операции соответственно подразделяются на основные(ведущие) и вспомогательные.
Основной (ведущей) машиной в технологически связанной цепочке горных машин (комплексе) является выемочно-погрузочная машина. За операцией выполняемой основной машиной следует другая выполняемая в том же темпе следующей машиной при этом должна быть осуществлена связь второй машины с первой с целью сохранения непрерывности производства технологического процесса. Такая организация технологического процесса соответствует принципам комплексной механизации производства.
Комплексная механизация осуществляется с помощью машин и механизмов различного назначения образующих технологический комплекс.
Комплексная механизация - это технологически связанная совокупность горных и транспортных машин обеспечивающая максимальную производительность основной (ведущей) машины (добычной или вскрышной) и осуществляющая производственный процесс в котором выполняются все операции начиная от подготовки пород к выемке (если она есть) и заканчивая отвалообразованием или переработкой полезного ископаемого.
Комплексная механизация означает что все смежные операции технологического процесса механизированы соответствующем друг другу оборудованием примерно равной производительности; при этом используется наименьшее число механизмов при наибольшей производительности труда. При выборе основной машины цепочка остальных машин и механизмов подбирается такой чтобы обеспечить в конкретных условиях максимально возможную производительность ведущей машины.
Производительность машины или комплекса с течением времени не остается неизменной. Каждая машина создается для усредненных условий работы со сравнительно узкой задачей: бурение погрузка перемещение и др. Поскольку свойства разрабатываемых пород изменяется все горные машины образующие комплекс должны некоторыми резервами повышения производительности.
Комплексная механизация и организация работы на карьерах развивается на основе внедрения поточной технологии а также совмещения или в некоторых случаях разделения производственных процессов.
Поточную технологию легче осуществить при применении машин непрерывного действия. Однако возможно достижение поточности и при использовании экскаваторов цикличного действия а также при рельсовом и автомобильном транспорте. В этом случае комплекс машин (буровые станки зарядные машины экскаватор транспорт с отвалообразующими или перерабатывающими полезное ископаемое машинами) работающих ритмично по жесткой схеме будет являться поточным а технология называться циклично-поточной (ЦТП).
Комплексная механизация должна обеспечиваться по возможности применением машин и механизмов непрерывного действия.
Структуры комплексной механизации в общем случае составляются из следующих звеньев соответственно процессам выполняемым горными и транспортными машинами: подготовки пород к выемке; отвалообразования или складирования; первичной переработки.
Комплект оборудования необходимый для материального обеспечения той или иной принятой структуры комплексной механизации в зависимости от принятой технологии может включать в себя все или часть из указанных звеньев.
Комплекты оборудования соответствующие определенной структуре комплексной механизации предназначены для обслуживания определенных грузопотов и подразделяются на однолинейные параллельные сходящиеся расходящиеся и сложные.
Основное влияние на структуру комплексной механизации оказывают горногеологические условия и в первую очередь крепость пород. Последняя обусловливает в комплексе оборудования наличие или отсутствие буровзрывного рыхления эффективность применения оборудования непрерывного действия на выемочно-погрузочных работах выбор транспорта и способа отвалообразования.
По характеру выполняемой работы комплексы разделяются на:
Непрерывные в которых подготовку горной массы к экскавации выемку погрузку перемещение и отвалообразование или переработку производят машины непрерывного действия;
Дискретные в которых машины цикличного действия осуществляют строго ритмичную работу во всем потоке;
Смешанные в которых подготовку горных пород к выемке выемку и погрузку выполняют машины цикличного действия а перемещение горной масс - машины непрерывного действия или наоборот (рис. 1).
Рис. 1. Экскаваторнотранспортно-отвальный комплекс машин смешанного типа;
-гидравлические лопаты;
-бункер – перегружатель;
-магистральный конвейер.
На современных карьерах обычно стремятся применять однотипные средства механизации что значительно упрощают и облегчает организацию горных работ эксплуатацию ремонт и обслуживание оборудования. Вместе с тем на вскрышных работах как правило стремятся использовать наиболее мощные машины и комплексы.
Взаимосвязь горнотранспортного комплекса с последующими технологическими процессами переработки полезного ископаемого.
Комплексы машин непрерывного действия в общем случае включают в себя следующие технологические звенья: выемочное транспортирующие и отвальное.
В некоторых случаях укладка породы в отвал производится транспортирующей машиной и тогда третье звено отсутствует.
Мощность оборудования составляющего комплекс определяется линейными параметрами карьера объемом добычных и вскрышных работ.
При подборе машин для комплекса соблюдают следующие основные требования:
максимальную поточность процесса производства горных работ с наименьшим числом перегрузочных пунктов и возможностью автоматизации процесса;
соответствие производительности всех машин входящих в комплекс максимальной производительности ведущей машины выполняющей основной процесс (выемку и погрузку породы);
полное использование времени смены при назначении режима работы комплекса машин минимум затрат времени на перерывы в рабочих операциях и маневры машины.
Производительность оборудования определяется технической характеристикой. Коэффициенты использования конкретной машины во времени определяется расчетным путем в соответствии с принятой технологической схемой её эксплуатации.
При поточной технологии определяющим фактором является производительность выемочно-погрузочной машины.
В типажный ряд комплексов машин непрерывного действия для открытой разработки полезных ископаемых входят роторные экскаваторы отвалообразователи и конвейеры.
Состав любого комплекса определяется системой разработки и производственной мощностью карьера. Для образования комплекса непрерывного действия типажом рекомендуется в качестве основных машин роторные экскаваторы и ленточные конвейеры. В состав комплексов также могут входить различные дробильно – сортировочные и загрузочные устройства.(самоходные дробильные агрегаты погрузочно-дозировочные машины бункера самоходные и др.) и перегружатели.
Комплексы машин непрерывного действия для вскрышных работ составляют по одной из следующих схем:
экскаватор (цепной или роторный) – транспортно-отвальный мост (рис.2а);
экскаватор – консольный перегружатель – отвалообразователь (рис. 2б);
экскаватор – отвалообразователь (рис. 2в);
экскаватор – перегружатель – отвалообразователь (рис. 2г);
экскаватор – конвейерная линия – отвалообразователь (рис. 2д).
Рис.2 Схемы комплексов непрерывного действия для открытых работ
Комплексы машин непрерывного действия для добычных работ составляются по одной из следующих схем:
экскаватор - конвейерная линия - перегружатель;
экскаватор – погрузочное устройство – рельсовый транспорт;
экскаватор – автомобильный транспорт.
Производительная работа комплекса возможна только при высокой надежности и гарантированной долговечности всех входящих в него звеньев.
Классы машин применяемые
на открытых горных работах.
Машины и оборудование используемые на открытых горных работах принято подразделять по роду выполняемой работы т. е. по технологическому признаку на семь классов;
машины для подготовки горных пород к выемке;
выемочно-погрузочные машины;
выемочно-транспортирующие машины;
транспортные машины;
отвалообразующие машины;
сортировочно-обогатительное оборудование;
машины для вспомогательных работ.
Машины каждого класса дополнительно можно подразделить на группы. В каждую группу включаются типы машин отличающиеся друг от друга уже не характером выполняемой работы а только конструкцией отдельных узлов или всей машины в целом.
Каждый тип машины имеет несколько типоразмеров (моделей) совпадающих в основном по конструкции но различающихся между собой производительностью параметрами рабочего оборудования массой и т. д.
Согласно приведенной выше классификации например одноковшовый карьерный экскаватор ЭКГ-10 оборудованный прямой лопатой относится к классу выемочно-погрузочных машин группе одноковшовых экскаваторов и типу прямая лопата типоразмера 10 м3.
Горные машины для открытых работ могут быть также классифицированы по видам используемой энергии ходовому оборудованию способу экскавации массе и конструктивным признакам.
Каждая машина состоит из рабочего исполнительного и силового оборудования непосредственно выполняющего технологические операции; передаточных механизмов связывающих рабочее и исполнительное оборудование с силовым; ходового оборудования обеспечивающего транспортные и технологические перемещения машины; несущих металлоконструкций систем управления и автоматизации.
Рабочее оборудование состоит из рабочего органа и исполнительных механизмов. Рабочий (исполнительный) орган (ковш экскаватора нож бульдозера буровая коронка и др.) предназначен для непосредственного воздействия на рабочую среду (забой). Необходимые движения и усилия сообщаются рабочему органу исполнительными механизмами (например подъемным и напорным механизмами у одноковшового экскаватора типа прямая лопата и др.).
Передаточный механизм служит для передачи движения от двигателя к исполнительным механизмам с трансформацией вида движения скоростей и сил (моментов).
Таким образом рабочее оборудование и передаточные механизмы для машин каждого класса и каждой группы различны и определяются их функциональным назначением (бурение выемка породы погрузка транспортирование и т. д.).
Силовое оборудование а также механизмы управления для большей части горных машин применяемых на открытых разработках однотипны. Так основная часть бурового и выемочно-погрузочного оборудования имеет электропривод тогда как выемочно-транспортирующие машины и экскаваторы работающие в условиях отсутствия линий электроснабжения оборудуются двигателями внутреннего сгорания.
Подробные сведения по каждому из узлов машины даются в паспорте завода-изготовителя где обязательно указываются технические характеристики машины ее кинематическая схема и ряд других данных.
Выемочно-погрузочные машины.
Наиболее характерными представителями выемочно-погрузочных машин эксплуатируемых на открытых разработках являются одноковшовые и многоковшовые экскаваторы.
Экскаватором называется машина предназначенная для черпания (экскавации) горной массы перемещения ее на относительно небольшие расстояния и погрузки на транспортные средства или в отвал.
Рабочий цикл одноковшового экскаватора складывается из четырех последовательных операций:
наполнения ковша (черпания);
перемещения его к месту разгрузки (транспортирования);
перемещения порожнего ковша к месту черпания для воспроизведения нового цикла.
Поэтому одноковшовые экскаваторы являются машинами цикличного (прерывного) действия. В отличие от них многоковшовые экскаваторы у которых все элементы рабочего цикла осуществляются одновременно (совмещенно) являются машинами непрерывного действия.
Существующие типы экскаваторов в общем виде классифицируются типажом по следующим признакам:
назначению и роду выполняемой работы;
вместимости ковша (Е м3 - одноковшовые) или теоретической производительности (Q мзч -многоковшовые);
видам рабочего ходового и силового оборудования.
В свою очередь одноковшовые экскаваторы подразделяются на лопаты:
карьерные прямые напорные механические гусеничные (ЭКГ);
прямые гидравлические (ЭГ);
обратные гидравлические (ЭГО);
прямые вскрышные гусеничные (ЭВГ);
драглайны - шагающие (ЭШ);
драглайны - гусеничные (ЭДГ);
Карьерно-строительные лопаты (преимущественно гидравлические) маркируются как ЭО.
Многоковшовые экскаваторы подразделяются на:
роторные гусеничные - вскрышные (ЭР или ЭРГ);
вскрышные на шагающе-рельсовом ходу (ЭРШР);
добычные гусеничные (ЭРП или ЭР-Д);
добычные на шагающе-рельсовом ходу (ЭРШР-Д);
добычные на цепные гусеничные (ЕRs);
добычные на рельсовом ходу (Еs).
Кроме упомянутых больших классов экскаваторов имеются и некоторые мало распространенные разновидности экскаваторов например прямые лопаты с рабочим оборудованием типа «Суперфронт» и с рабочим оборудованием фрезерного типа (барабан с зубками).
Силовое оборудование мощных экскаваторов преимущественно электрическое на машинах среднего класса и малой мощности применяются также дизель-электрические и дизель-гидравлические и электрогидравлические приводы.
В свою очередь одноковшовые и многоковшовые экскаваторы имеют более узкие классификации отвечающие конкретной специфике конструкций той или иной группы машин.
Любой экскаватор одноковшовый или многоковшовый состоит из рабочего (у одноковшовых экскаваторов оно же и транспортирующее) транспортирующего механического включающего главным образом передаточные механизмы (трансмиссии) ходового и силового оборудования а также механизмов управления металлоконструкций платформы и надстройки кузова.
Конструктивные схемы одноковшовых экскаваторов
Конструктивной схемой в отличие от кинематической называют схематическое изображение всей машины или ее основных узлов с указанием их действительного взаимного расположения и кинематической связи. Одним из главных признаков различия одноковшовых экскаваторов определяющих их назначение и область применения является рабочее оборудование. В зависимости от назначения рабочее оборудование одноковшовых экскаваторов имеет различную конструкцию и кинематику. На универсальных экскаваторах могут применяться до десяти видов сменного рабочего оборудования. Однако экскаваторы используемые на открытых горных разработках имеют как правило один основной вид специализированного рабочего оборудования. Основные виды рабочего оборудования одноковшовых экскаваторов применяемого на открытых работах:
прямая напорная лопата (рис. 3 4):
Рис. 3 Конструктивные схемы прямой напорной лопаты с выдвижной рукоятью.
а. с зубчато-реечным механизмом напора;
б. с канатным механизмом напора с разрезной стрелой;
в. с канатным механизмом напора и неразрезной стрелой;
г. с канатным механизмом напора и неразрезной двухбалочной стрелой.
Рис.4 Конструктивные схемы коленно-рычажных прямых лопат:
а. подача рукоятки в забой с помощью зубчато-реечной системы
б. а. подача рукоятки в забой с помощью системы канатов.
гидравлические прямые и обратные лопаты (рис. 5);
Рис. 5 Конструктивные схемы гидравлических экскаваторов со сменным рабочим оборудованием:
а. прямая напорная лопата с поворотным челюстным ковшом;
б. обратная лопата с поворотным ковшом.
Рис. 6 Конструктивная схема экскаватора драглайна
ковшовые погрузчики.
Драглайн (рис. 6) имеет ковш 1 с упряжью тяговый 2 и подъемный 3 канаты стрелу 4 с направляющими 5 головными 6 блоками и пятой 7. Для перемещения ковша служат лебедки подъема и тяги. Угол наклона стрелы определяется длиной поддерживающего стрелу каната или полиспаста 10. Исполнительный механизм драглайна имеет два гибких звена-каната связывающих ковш с ведущими звеньями механизма. Неподвижным звеном механизма драглайна является платформа экскаватора с двуногой стойкой и стрелой. Подъемный 8 и тяговый 9 барабаны лебедок образуют с неподвижными звеньями в точках O2 О3 О4 или О1 О3 и О4 вращательные пары. Механизм воспроизводит рабочие движения драглайна в результате перемещений подъемного и тягового канатов. Разгрузка ковша осуществляется за счет ослабления тягового каната и поворота ковша имеющего центр тяжести впереди точки А крепления вертикальной подвески. При этом канат упряжи проскальзывает относительно блока 11 давая возможность ковшу опрокинуться.
Рабочее оборудование приспособлено к разработке грунта преимущественно ниже уровня стояния экскаватора хотя вполне успешно может работать и выше этого уровня.
Ходовое оборудование экскаваторов
Ходовое оборудование горной машины - это устройство для ее перемещения и устойчивого опирания на грунтовое основание во время работы. В зависимости от условий работы и назначения горной машины применяют следующие виды ходового оборудования:
колесное (на пневматиках или рельсовое);
Требования предъявляемые к ходовому оборудованию горных машин цикличного и непрерывного действия:
достаточные сила тяги;
скорость передвижения;
способность преодолевать заданные подъемы и уклоны;
небольшая масса при обеспечении заданных давлений на основание (средних и максимальных);
устойчивость машины при всех возможных изменениях положения ее центра тяжести и отсутствие больших динамических нагрузок в конструкции всей машины при передвижении;
малые сопротивления при передвижении;
минимальное число быстроизнашивающихся элементов удобство в эксплуатации и долговечность.
Шагающее ходовое оборудование экскаваторов
Шагающее ходовое оборудование обеспечивает низкие давления на основание (до 01 МПа) небольшую массу (10-12 % массы машины) высокие маневренность и устойчивость машины на базе при работе. Его недостатки - цикличность и малая скорость передвижения необходимость подъема машины при шагании волочение передней части базы по опорной поверхности при шагании сопровождающееся смятием грунта и высокими затратами мощности. Это ограничивает область применения шагающего хода на драглайнах и отвалообразователях работающих на поверхностях (грунтах) с относительно низкой несущей способностью.
Шагающее ходовое оборудование состоит из опорной рамы (базы) и механизма шагания. Последний имеет лыжи (башмаки) механизм перемещения и привод. Схемы механизмов шагания различаются по конструкции механизма шагания и могут быть гидравлическими и кривошипными (рис. 7).
Рис. 7 Схемы механизмов шагания:
а – кривошипно-шарнирный с треугольной рамой;
б - кривошипно-ползункового;
в – гидравлического;
г - двухкривошипного
Они состоят из двух одинаковых синхронно работающих механизмов шагания расположенных симметрично относительно продольной оси экскаватора.
При любом виде шагающего ходового оборудования полный цикл передвижения экскаватора складывается из следующих элементов: подачи лыж на грунт подъема экскаватора передвижения экскаватора опускания экскаватора подъема лыж в исходное положение.
Независимо от вида шагающего ходового оборудования (кроме специального - ЭШ 100.100) в момент непосредственного передвижения экскаватор опирается на две лыжи и на часть опорной базы. Поскольку при этом центр тяжести экскаватора находится впереди оси механизма шагания передвижение машины может быть осуществлено только в направлении противовеса.
Все модели драглайнов УЗТМ и модель 4250-W фирмы «Бюсайрус-Ири» (США) оборудованы гидравлическими механизмами шагания.
Рис. 8 Гидравлический механизм шагания экскаватора ЭШ 15.90
Гидравлический механизм шагания экскаваторов ЭШ 15.90 (рис. 8) ЭШ 25.100 и других состоит из лыж 1 подъемного 2 и тягового 3 гидроцилиндров. Штоки последних сочленяются общим шарниром на траверсе 4 которая также шарнирно с помощью кронштейнов 5 связана с лыжей. Подъемный и тяговый гидроцилиндры шарнирно соединены с металлоконструкциями надстройки 6 и поворотной платформой осями 7 и 8. В верхние и нижние полости гидроцилиндров по трубопроводам 9 и 10 масло или специальная рабочая жидкость подводится от насосной установки под давлением 10-20 МПа (см. рис. 9).
Рис. 9 Схема электрогидравлической системы управления механизмами шагания экскаватора ЭШ 15.90А
Во время работы экскаватора поршни всех гидроцилиндров втянуты внутрь опорные башмаки подняты и занимают крайнее верхнее положение а поворотная платформа при этом опирается на базу 11. При шагании под действием подъемных и тяговых гидроцилиндров опорные башмаки выдвигаются и опускаются на почву уступа. При возрастании давления в подъемных гидроцилиндрох один опорной базы экскаватора приподнимается от почвы уступа затем экскаватор с помощью тяговых гидроцилиндров сдвигается и опираясь на башмаки скользит опорной рамой по почве уступа передвигаясь на величину шага 1 - 25 м после чего база вновь опускается на почву. Затем подъемные гидроцилиндры поднимают опорные башмаки вверх и процесс шагания повторяется.
Достоинства гидравлического шагающего механизма заключаются в плавности его работы и возможности регулирования траектории движения а недостатки - в низком кпд (около 06) и сложности устройства привода требующего квалифицированного обслуживания.
В отличие от описанной выше конструкции на мощном драглайне ЭШ 100.100 применено гидравлическое шагающее устройство с полным отрывом опорной рамы (базы) от грунта. Передвижение экскаватора осуществляется перемещением опорных скользунов (гидростатической опоры) гидроцилиндров по верхней плоскости башмака в направляющих. Шагающее ходовое устройство экскаватора ЭШ 100.100 (рис. 10) состоит из четырех башмаков 1 соединенных попарно шарниром 2 четырех подъемных гидроцилиндров 3 закрепленных в раме поворотной платформы 4 и опирающихся на сферу 5 гидро-статической опоры скользунов двух тяговых гидроцилиндров 6 шарнирно закрепленных в точке А на поворотной платформе и в точке Б - на башмаке и обеспечивающих перемещение гидроста-тической опоры по опорным плитам 7 башмаков. Рабочие поверх-ности гидростатической опоры и опорных плит башмаков закрыты от попадания пыли сложной системой уплотнений и кожухами 8. Во время работы драглайн опирается на базу 9. Минимальный подъем экскаватора - 700 мм максимальная длина шага - до 3 м. Гидравлическая схема управления механизмов обеспечивает три точки опоры машины замыканием пары подъемных цилиндров в гидравлический балансир.
Рис. 10 Положение шагающего ходового устройства экскаватора ЭШ100.100 с полным отрывом базы:
I – начало шагания (лыжи подняты);
II – экскаватор поднят;
III – перемещение экскаватора.
Достоинства данного вида шагающего устройства:
вес машины распределяется между четырьмя точками поворотной платформы вместо двух;
возможность полностью оторвать базу от земли что при передви- жении исключает ее трение о грунт износ и появление поперечных нагрузок на центральной цапфе;
независимость величины выдвижения толкающего цилиндра от величины выдвижения домкратов что позволяет изменять длину шага в различных условиях;
наличие шаровой опоры на нижнем конце подъемного цилиндра в связи с чем устраняются изгибающие нагрузки на штоке и обеспечиваются большие надежность и долговечность соединений.
Недостаток этого шагающего устройства - сложность конструкции гидростатической опоры.
Аналогичный гидравлический механизм шагания с полным отрывом базы отличающийся от механизма шагания экскаватора ЭШ 100.100 удвоенным числом тяговых цилиндров (по одному на каждой опоре) применен на драглайне 4250-W (фирма «Бюсайрус-Ири» США) с рабочей массой 136 тыс. т.
На драглайнах НКМЗ и на всех моделях драглайнов зарубежных фирм применяются кривошипные системы различных видов: кривошипно-шарнирная с треугольной рамой фирмы «Марион» (см. рис. 7 а) кривошипно-ползунковая фирмы «Пейдж» (см. рис. 7 б) двухкривошипная фирмы «Марион» (см. рис.7 г) кривошипно-эксцентриковая НКМЗ и эксцентриковая с тягой фирмы «Марион». Кривошипно-эксцентриковый механизм шагания применялся на ЭШ 4.40 с массой до 4 тыс. т. В настоящее время НКМЗ устанавливается на своих моделях ЭШ 6.45М ЭШ 10.60 ЭШ 10.70А ЭШ 20.55 и ЭШ 15.70 кривошипно-рычажные четырехзвенные механизмы шагания.
Двухкривошипная система шагания (рис. 7.г) применяется на мощных драглайнах фирмы «Марион» массой до 8500 т.
Назначение. Техническая характеристика. Конструктивное устройство драглайна ЭШ 40.100
Шагающий экскаватор-драглайн ЭШ-40.100 (технические характеристики даны в табл.1) используется в горнодобывающей промышленности при добыче полезных ископаемых открытым способом без применения транспорта с укладкой породы в выработанное пространство или на борт разреза. При разработке пород повышенной прочности требуется частичное или сплошное рыхление взрыванием. Простота монтажа оптимальные параметры надежность в ра-боте позволяют эксплуатировать машину с большой эффективностью.
Экскаватор состоит из рабочего (у экскаватора-драглайн ЭШ-40.100 оно же и транспортирующее) транспортирующего механического включающего главным образом передаточные механизмы (трансмиссии) ходового и силового оборудования а также механизмов управления металлоконструкций платформы и надстройки кузова.
Вместимость ковша м3
Концевая нагрузка(Max.) кH
Продолжительность рабочего цикла (грунт первой категории) с
Расчетная производительность (грунт первой категории) м3ч
Удельное давление на грунт при работе и передвижении МПа
A – Угол наклона стрелы град
B – Высота выгрузки м
C – Радиус выгрузки м
D – Глубина черпания м
E – Радиус выгрузки м
F – Просвет под платформой м
G – Расстояние от оси вращения до пяты стрелы м
H – Расстояние от пяты стрелы до грунта м
Поворотная платформа
Среднее удельное давление на грунт МПа
Роликовый круг средний диаметр м
Ролик средний диаметр х количество мм х шт.
Зубчатый венец диаметр м
Ширина по башмакам м
Опорная площадь башмаков м2
Среднее давление на грунт при передвижении МПа
Скорость передвижения мч
Рабочее оборудование драглайна
Рабочее оборудование драглайна состоит из стрелы ковша и направляющих блоков.
Стрела драглайна может иметь различное конструктивное исполнение. По основным конструктивным признакам стрелы драглайнов можно объединить в четыре группы:
трехгранные жесткие;
ферменные (как с дополнительной двуногой стойкой и промежуточными подвесками так и без них);
Вантовые стрелы до 1972 г. применялись на драглайнах УЗТМ: ЭШ10.75 ЭШ 14.75; ЭШ 15.90 и ЭШ 25.100А. Вантовая стрела состоит из одной вертикальной и двух наклонных вантовых ферм имеющих один центральный сжатый пояс трубчатого сечения надвое разветвляющийся книзу. Элементы работающие на растяжение выполнены из канатов что делает стрелу легкой и достаточно прочной.
Вантовая стрела экскаватора ЭШ 15.90 (рис. 11) составлена из трубчатых элементов: первый от пяты стрелы представляет собой пространственную жесткую конструкцию образованную элементами 1 2 и 3 а три остальных являются вантовыми фермами. Сжатый пояс 4 стрелы образован трубой свальцованной и сваренной из листов низколегированной стали 10ХСНД. Растянутые пояса вертикальной и горизонтальной вантовых ферм выполнены из канатов 5 6 7 закрытого типа. Канаты 6 верхнего пояса предварительно напряжены с усилием превышающим усилие растяжения от концевой нагрузки. В вершине 8 жесткой конструкции установлен узел крепления подвески стрелы. Трубчатые стойки 9 вместе с канатами б и 7 образуют вертикальную вантовую ферму а профильные боковые стойки 10 и канаты 5 - две боковые вантовые фермы. Диагональные оттяжки 11 увеличивают жесткость стрелы препятствуя ее скручиванию. Канаты 5 боковых вантовых ферм имеют натяжные устройства. Неравномерное натяжение канатов вызывает значительную перегрузку отдельных частей стрелы и может привести к аварии. Вверху центральный стержень заканчивается рамой 12 на которой установлены блоки для подъемных канатов.
Жесткая часть стрелы разделена на две панели причем в качестве элементов жесткости применены крестовые раскосы из предварительно натянутых вант 13. Это позволило увеличить высоту стрелу и тем самым разгрузить ее пояса. Стойки вертикальных ферм соединены с трубой шарнирно что предохраняет их от изгиба а трубу от скручивания при неточном монтаже. Канаты работающие на кручение соединяют наклонные стойки с вершиной 8 жесткой части стрелы.
Рис 11. Вантовая стрела экскаватора драглайна ЭШ 15.90 (УЗТМ)
Трехгранные жесткие стрелы (рис. 12) применяются на отечественных драглайнах ЭШ 15.90А; ЭШ 20.90; ЭШ 40.85 и ЭШ 100.100 (УЗТМ) и других. Такая стрела выполнена из трех жестких трубчатых поясов 1 2 4 образующих с головной частью трехгранную пирамиду с вертикальными трубчатыми стойками 3 и вантовыми диагональными связями 5. Верхний трубчатый пояс 4 стрелы предварительно напряжен системой вантовых канатов до суммарного усилия равного усилию растяжения пояса от концевой нагрузки и веса стрелы что увеличивает выносливость последней. Стрелу на жестких серьгах 6 подвешивают к стойке 7 поворотной платформы. На верхнем поясе стрелы также располагают ролики для подъемных канатов. Последние касаются роликов при ослаб-лении натяжения например во время копания. Трехгранная трубчатая стрела с канатными раскосами тяжелее чем вантовая (масса 1 м стрелы соответственно 13-14 и 11-12 т) но имеет большую эксплуатационную надежность. Комбинированные шарнирно-сочлененные стрелы приме-няют на драглайнах средней мощности (ЭШ 10.70А; ЭШ 20.55 и ЭШ 15.70) производства НКМЗ. Стрела драглайнов ЭШ 20.55 и ЭШ 15.70 (рис. 10.16) пред-ставляет собой пространственную ферменную конструкцию вы полненную из уголков и состоящую из верхней 5 и нижней 7 частей связанных шарниром. Раскос 2 поддерживает нижнюю секцию. Подвеска стрелы 3 канатная обеспечивает удержание стрелы через блок 1 укрепленный на стойке машинного отделения. На правой стороне стрелы установлены лестницы 6. Наличие излома геометрической оси нижнего пояса в вертикальной плоскости исключает запрокидывание верхней части стрелы относительно шарнира.
Рис. 12. Трехгранная жесткая стрела экскаватора-драглайна ЭШ100.100
Головные блоки 4 на драглайнах средней и большой мощности установлены в подвижной раме (люльке) которая позволяет им следовать за отклонением подъемных канатов. Это устраняет трение канатов о боковые поверхности ручьев блоков и уменьшает износ как канатов так и блоков.
Направляющие блоки (наводка) тяговых канатов устанавливают между опорами стрелы на платформе экскаватора для обес-печения постоянного направления входа тягового каната на барабан лебедки. На экскаваторах малой мощности наводка состоит из двух вертикальных и двух горизонтальных блоков объединенных общей поворачивающейся обоймой.
Рис. 13. Стрела экскаваторов-драглайнов ЭШ-20.55 и ЭШ15.70 (НКМЗ) 1 - стойка поворотной платформы;
- подвеска передняя;
- блоки головные следящие;
и 7 - секции верхняя и нижняя;
На мощных экскаваторах (рис. 14) тяговые канаты от ковша проходят через нижние поворотные вокруг вертикальной оси блоки 8 с которых идут на верхние неповоротные 7 и далее на барабан лебедки 5.
Ферменные решетчатые стрелы с дополнительной стойкой и промежуточной подвеской характерны для экскаваторов фирм «Марион» и «Бюсайрус-Ири». На экскаваторах фирмы «Марион» четырехгранная ферменная стрела имеет рыбоооразную форму с расширяющимся основанием. Ее пояса выполнены из уголков а раскосы и стойки - из труб. Стрела подвешена к мачте являющейся продолжением верхнего строения и двуногой стойки на вантах идущих от головного блока и от серединного сечения стрелы.
Рис. 14. Схема навески канатов экскаватора ЭШ 100.100:
- барабан лебедки подъема стрелы;
- блоки двуногой стойки;
- блоки поддержки стрелы;
5 - барабаны подъемной и тяговой лебедок;
7 - блоки тяговые и подъемных лебедок;
9 - блоки наводки и головные;
Фирмой «Марион» из алюминиевых сплавов изготовлены и испытаны экспериментальные образцы ферменных стрел драглайнов длиной до 78 м имеющие на 30 °о меньшую массу по сравнению со стрелами аналогичной длины выполненными из стального проката.
На экскаваторах фирмы «Бюсайрус-Ири» применяют трехгранные стрелы с поясами раскосами и стойками из труб в основные элементы которых накачан под давлением азот. Специальные датчики установленные на стреле позволяют машинисту по падению давления (по утечке газа) определять наличие в ней трещин и предупреждать поломки стрелы.
Ковш драглайна (рис. 15) состоит из сварного корпуса 1 козырька 2 отлитого заодно с основаниями зубьев и арки 3. Последняя служит для придания боковой жесткости ковшу и крепления разгрузочных канатов 4.
Рис. 15. Ковш драглайна
– разгрузочный канат;
– проушина тяговой цепи;
– проушина цепи подъема;
Наибольшей жесткостью обладают литые арки однако они тяжелее сварных. К передней части ковша (щекам) приваривают проушины 5 для тяговых цепей 6 а к боко-вым стенкам приклепывают проушйны 7 для цепей 8 подъема. Через траверсу 9 и балансир 10 цепи 8 соединяются с подъемными канатами 15. В основание козырька 2 вставляют зубья 11.
Чтобы защитить днище ковша от изнашивания к нему приваривают стальные полозья 12 внутри и снаружи. Для предохранения подъемных цепей 8 от истирания о ковш предусмотрена распорная балка 13. Центр тяжести ковша с грузом находится между подъемными цепями и аркой. Вследствие этого при ослаблении тяговых 14 и разгрузочных 4 канатов последние проскальзывают по блоку 16 ковш поворачивается вокруг осей крепления подъемных цепей и порода свободно выгружается через открытое пространство под аркой и между тяговыми цепями. В транспортном положении (при поворотах) ковш удерживается в горизонтальном поло-жении с помощью натянутых тяговых (тягового) и разгрузочного канатов. Совокупность деталей соединяющих ковш с тяговыми и подъемными канатами называется упряжью ковша.
Для сравнения ковшей применяют характеристики металлоемкости пустого ковша представляющие собой отношение массы ковша к его вместимости. Эти характеристики для ковшей тяжелого типа вместимостью 14-100 м3 именяются в пределах 154-123 тм3 составляя в среднем 14 тм3. За рубежом ковши драглайнов в зависимости от назначения подразделяют на легкие средние тяжелые и сверхтяжелые с удельной металлоемкостью от 07 до 16 тм3. Как правило с ростом вместимости ковша его металлоемкость падает. Так у ковша вместимостью 168 м3 экскаватора 4250-W этот коэффициент равен 072 тм3. Ковши безарочной конструкции драглайнов отличаются низкой металлоемкостью (около 1 тм3). Безарочный ковш имеет расширение в области режущей кромки в результате чего облегчаются заполнение и его разгрузка уменьшается возможность образования пустот в ковше при черпании. Зубья ковшей драглайнов отливают из высокомарганцовистой стали. Их конструкции аналогичны применяемым на прямых лопатах.
Шагающе-рельсовое ходовое оборудование
Шагающе-рельсовое ходовое оборудование было впервые разработано на НКМЗ и применено на отвалообразователях и мощных роторных экскаваторах.
Схема работы шагающерельсового ходового оборудования приведена на рис. 16.
Рис. 16 Схема работы шагающе-рельсового ходового оборудования
Ходовое оборудование включает в себя четыре соединенные сферическим шарниром 1 лыжи 2 (лыжа может быть неразрезная) на которых имеются верхние 3 и нижние 4 рельсы. Верхняя часть экскаватора 5 через четыре гидродомкрата 6 опирается на ходовые тележки 7. В рабочем положении машина опирается через гидродомкраты и ходовые тележки на нижние направляющие лыж. База вместе с верхней частью приподнята над землей (положение 1). Для передвижения верхней части машины включают тяговые лебедки 8 которые с помощью полиспастов перемещают машину по лыжам в нужном направлении. Когда тележки достигнут крайнего положения на лыжах (положение II) производятся опускание машины на базу и последующий подъем лыж через верх ние направляющие рельсы до упора катков 9 в раму машины (положение Ш). Далее происходит отключение гидравлической системы домкратов и включение тяговых лебедок которые перемещают лыжи вперед на величину шага после чего тяговые лебедки отключаются с помощью гидросистемы происходят опускание лыж на грунт подъем машины и базы на величину обеспечивающую необходимый зазор между базой и грунтом. Далее цикл шагания может быть повторен. Изменение направления движения машины осуществляется поворотом стоящей на базе 10 машины по роликовому кругу 11 при поднятых лыжах так же как у машин с шагающим ходовым оборудованием.
Применительно к роторным экскаваторам лыжи шагающе-рельсового ходового устройства с двумя поворотными рамами располагаются вдоль оси движения машины к забою (рис. 17).
Рис. 17. Шагающе-рельсовое оборудование с двумя поворотными рамами.
Передвижение машины осуществляется на лыжах 1 при поднятой базе 2. Гидродомкраты 3 для подъема машины и лыж установлены в нижней раме 4 которая при стоянке машины на базе опирается на последнюю с помощью поворотного круга 5 используемого для изменения направлений движения. Поскольку процесс экскавации у роторных машин осуществляется поворотом верхней части 6 экскаватора то последняя устанавливается на нижнюю раму через второй поворотный круг 7. Образование каждой новой стружки осуществляется передвижением машины на ходовых тележках 8 по лыжам переход с подуступа на подуступ и от блока к блоку осуществляется перестановкой лыж и перемещением всей машины. Поворот верхней части 6 относительно нижней рамы 4 и базы 2 обеспечивается поворотными механизмами через венцовые шестерни 9 и 10.
Правила устройства монтажной площадки
для монтажа горных машин.
Оборудование для открытых горных работ поступает на предприятия отдельными деталями и узлами масса которых достигает 40 – 60 т а в уникальных машинах – 120 т.
Для укрупненной сборки узлов и монтажа машин сооружают специальные монтажные площадки.
Монтажные площадки подготавливаются на территории горного предприятия. Оборудование монтажной площадки должно обеспечивать минимальные сроки монтажных работ при высоком их качестве. Размеры монтажной площадки зависят от числа и типа одновременно монтируемых машин и интенсивности монтажа. Проект монтажной площадки разрабатывается проектно-техническими организациями и согласуется с поставщиком оборудования.
Для монтажной площадки используется не слишком пересеченная с плотными не обводненными грунтами с удалением от места будущей работы собранных машин на 15 – 3 км. При этом учитывается необходимость строительства подъездных железнодорожных и автомобильных дорог подвода высоковольтной линии электропередачи связи возможности использования грунтовых вод для хозяйственных нужд и противопожарных мероприятий.
Площадка должна быть достаточно ровной и иметь плотный естественный или насыпной грунт. Часть площадки предназначенной для установки экскаватора и размещения узлов накладываются щебнем или гравием высотой 100 – 120 мм с последующей утрамбовкой а для мощного оборудования площадка покрывается бетонными плитами. Для стока поверхностных вод площадка должна быть спланирована с небольшим уклоном в стороны от центра стоянки экскаватора.
Габариты площадки должны позволять свободное и удобное размещение узлов экскаватора и монтажных приспособлений нормальную работу грузоподъемных и транспортных машин (табл. 1).
Тип монтируемого оборудования Размеры площадки м
Одноковшовыеэкскаваторы длина ширина
ЭКГ – 46А Э– 2505ЭКГ– 5А ЭКГ– 4У
ЭКГ – 63УС; ЭКГ– 46Б ЭВГ– 4И
ЭКГ – 8 ЭКГ– 8И ЭШ – 645М; ЭКГ– 5У;
ЭШ– 2060; ЭКГ– 125; ЭКГ– 15И; ЭКГ– 63У
ЭШ– 1060; ЭШ – 1350; ЭВГ– 6; ЭГ – 12А
ЭКГ – 20 ЭШ – 2090А; ЭГ - 20 90 – 160 60 – 80
ЭШ– 1070А; ЭШ – 1590; ЭВГ– 15
ЭШ– 2075Б; ЭШ – 1475
ЭШ– 4085; ЭВГ– 3565; ЭШ – 25100;
ЭШ– 80100 ЭШ – 100100
Многоковшовые экскаваторы массой т
00 200 –300 150 –180
00 –6000 350 –500 200 –300
На монтажной площадке заранее сооружаются необходимые фундаменты якоря и углубления. После их закладки грунт вокруг них утрамбовывается механическими трамбовками.
Трасса соединяющая монтажную площадку с забоем должна быть удобной для передвижения экскаватора своим ходом и проходить по плотным грунтам причем путь не должен иметь продольных уклонов более 120 и пересекаться с оврагами руслами рек и ручьев высоковольтными линиями электропередачи.
На должно обеспечивать хорошую видимость в зоне монтажа в любое время суток. Площадка оборудуется отдельным распределительным устройством необходимыми грузоподъемными средствами приспособлениями материалами необходимыми для производства сварочных работ сжатым воздухом для работы пневмоинструмента.
К концу монтажа экскаватора на площадку подается напряжение 6кВ для испытания и окончательной наладки электрооборудования экскаватора.
Прибывшие на монтажную площадку узлы и агрегаты экскаватора нужно располагать так чтобы дополнительные работы по транспортированию их на монтируемый экскаватор были минимальными. Необходимо учитывать последовательность монтажа и возможности грузоподъемных средств.
В качестве грузоподъемных средств необходимо использовать краны на железнодорожном и гусеничном ходу. Для правильного выбора грузоподъемных средств учитываются массы и размеры наиболее крупных монтируемых узлов а также высота их подъема в процессе монтажа. Кроме основных грузоподъемных средств (кранов) на монтажной площадке необходимо иметь: электрические лебедки гидравлические домкраты и автокраны грузоподъемность которых зависит от типа монтируемого оборудования и массы отдельных узлов и деталей. На монтажной площадке необходимо иметь в достаточном количестве стальные и пеньковые канаты стропы и другие такелажные приспособления а также слесарный инструмент. Для изготовления различных стоек подкладок шпальных клеток необходимо иметь от 400 до 1000 железнодорожных шпал в зависимости от типа монтируемого оборудования.
Рекомендуемые чертежи
- 22.08.2014
- 22.08.2014
Свободное скачивание на сегодня
Обновление через: 23 часа 15 минут
- 23.08.2014