Коробка скоростей с неравномерным рядом частот вращения




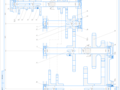
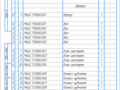
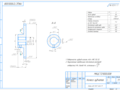
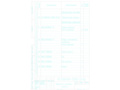
- Добавлен: 25.01.2023
- Размер: 682 KB
- Закачек: 0
Описание
Коробка скоростей с неравномерным рядом частот вращения
Состав проекта
![]() |
![]() ![]() ![]() ![]() |
![]() ![]() ![]() ![]() |
![]() ![]() ![]() ![]() |
![]() ![]() ![]() ![]() |
![]() ![]() ![]() |
Дополнительная информация
Сборки.cdw

Смазка подшипников и зацеплений - масло индустриальное И-20А ГОСТ 20799-88.
Подача смазки от центральной смазочной станции станка.
Вращение в опорах плавное без толчков и вибраций.
На свертке (разрез А-А лист 2) внутренние перегородки корпуса поз. 1
условно не показаны.
Смазка подшипников и трущихся поверхностей - масло индустриальное
И-20А ГОСТ 20799-88. Подача смазки от центральной смазочной станции станка.
Перемещение блоков шестерен по шлицевым валам без заеданий.
Усилие на рукоятке поз 1. при переключении не более 20 кГс
На разрезе А-А элементы конструкции условно развернуты в плоскость чертежа.
Истиное расположение см на главном виде.
Общее передоточное отношение приводных шестерен поз. 1715 и поз. 1617 u = 1.
Вал распределительный
Кольцо А35 ГОСТ 13940-86
Кольцо А18 ГОСТ 13941-86
Кольцо А20 ГОСТ 13941-86
Кольцо А30 ГОСТ 13941-86
Коробка скоростей.spw

Ведомость.dwg

Пояснительная записка
КП-02069964-151002-20-08
Документация текстовая
Детали.cdw

Высота до постоянной хорды
Коэффициент смещения
Поверхности зубьев калить т.в.ч. HRC 50 52.
Неуказанные предельные отклонения размеров:
Зубья и шлицы калить т.в.ч. HRC50 52.
* Размер для справок.
**Размер обеспечивается инструментом.
Шлицы калить т.в.ч. HRC50 52.
С торцев сверлить отв. центр. А2
Предельные отклонения размеров отливок - по ГОСТ 26645-85.
Уклоны формовочные - по ГОСТ 3212-80.
Предельное смещение осей отверстии под крепежные детали
от номинального расположения не более 0
Сталь 40Х ГОСТ 4543-71
Сталь 45 ГОСТ 1050-88
Записка.doc
Расчет силовых характеристик11
Расчет зубчатых передач12
Расчет механизма переключения скоростей40
Список использованных источников43
Создание машин отвечающих потребностям народного хозяйства и промышленности должно предусматривать их наибольший экономический эффект и высокие технико-экономические и эксплуатационные показатели.
Основные требования предъявляемые к создаваемой машине: высокая производительность надежность технологичность ремонтопригодность минимальные габариты и масса удобство эксплуатации экономичность.
Непрерывное совершенствование и развитие машиностроения связано с прогрессом станкостроения поскольку металлорежущие станки вместе с некоторыми другими видами технологических машин обеспечивают изготовление любых новых видов оборудования.
Курсовой проект по металлорежущим станкам является конструкторской работой в результате которой студент приобретает навыки и знания правил норм и методов конструирования. Выполнение проекта базируется на знании физико-математических и общетехнических дисциплин: математики механики сопротивления материалов технологии металлов машиностроительного черчения. В основу методики работы над проектом положено его деление на ряд последовательно решаемых задач: кинематический расчет; определение расчетных нагрузок; расчет и выбор источника механической энергии; проектные и проверочные расчеты элементов привода.
Цель проекта – разработка конструкции коробки скоростей со сложенной структурой и неравномерным рядом частот вращения выходного вала. Исходные данные к проекту: число ступеней регулирования z = 16 минимальная частота вращения выходного вала nmin = 20 обмин знаменатель ряда частот вращения φ = 126 ориентировочная частота вращения ротора электродвигателя nЭЛ = 1450 обмин фактическая мощность двигателя NЭЛ = 24 кВт. При работе над проектом требуется проведение кинематического и силового расчета а также проектирование кулачкового механизма переключения скоростей. В результате проектирования необходимо разработать сборочные чертежи коробки скоростей (развертку свертку механизм переключения) а также рабочие чертежи основных деталей.
Кинематический расчет и выбор электродвигателя
Так как в задании оговаривается неравномерность ряда частот вращения то для начала рассмотрим кинематику коробки скоростей с равномерным рядом.
Для реализации ряда частот вращения n1 n16 при заданном знаменателе φ = 126 и n1 = 20 обмин в качестве прототипа используем структурную формулу
z = 41 × (24 + 1 × 1 × 24) = 16
Равномерный ряд частот вращения выходного вала n1 n16 получим в виде геометрической прогрессии с первым членом n1 = 20 обмин и знаменателем ряда φ = 126
Таблица 1 – Ряд частот вращения множительной структуры обмин
По заданным значениям частоты вращения м мощности на роторе электродвигателя по каталогу подбираем стандартный асинхронный электродвигатель с короткозамкнутым ротором модели АОЛ2-32-4 номинальной мощностью N = 3 кВт и частотой вращения n = 1430 обмин [1 с. 63 таблица 9].
Для формулы с равномерной структурой строим график частот вращения выходного вала (рисунок 1).
Путем изменения характеристик множительных групп можно существенно расширить диапазон регулирования подач при том же числе передач в группах а также добиться более рационального распределения плотность ступеней регулирования в пределах диапазона.
Предполагаем что проектируемая коробка должна отличаться от коробки с равномерным рядом подач увеличенным диапазоном регулирования (за счет увеличения Smax). Вместе с тем предусматриваем более грубое регулирование в верхней и нижней частях диапазона. Таким образом кинематические характеристики коробки будут оптимальными для станка большую часть времени работающего в диапазоне подач S=038 191 ммоб.
Рисунок 1 – График частот вращения для формулы
z = 41 × (24 + 1 × 1 × 24) = 16 с равномерным рядом
Неравномерный ряд частот вращения получим изменив характеристику общей множительной группы 41. В исходной коробке с равномерной структурой характеристика группы X = 1. Это означает что между концами лучей u1 u2 u2 u3 u3 u4 на графике частот вращения винта будет строго один интервал g φ.
Изменяя характеристику множительной группы добиваемся расширения диапазона регулирования: назначаем расстояния между концами лучей u1 u2 – два интервала; u2 u3 – три интервала; u3 u4 – два интервала.
Полученный график частот вращения представлен на рисунке 2.
Рисунок 2 – График частот вращения выходного вала для формулы
z = 42 3 × (24 + 1 × 1 × 24) = 16 с расширенным диапазоном
и более тонким регулированием в середине диапазона
Минимальное общее передаточное отношение при включении низшей скорости
umin = n1 nДВ = 20 1430 = 0014
Далее в соответствии с графиком частот вращений определяем передаточные отношения зубчатых передач множительных групп по формуле
гдеqi – число интервалов g φ пересекаемое лучом ui на графике частот вращений.
u5 =126-45 = 035u6 =126-45 = 035u7 =126-1 = 079
u8 =126-5 = 031u9 =126-2 = 063u10 =126-6 = 025
Передаточное отношение передач группы 41 определим из уравнения кинематической настройки коробки скоростей при n1 = 20 обмин
nЭЛ × u4 × u5 × u6 × u8 = n1 = 20 обмин
u4 = n1 (nЭЛ × u5 × u6 × u8) = 20 (1430 × 035 × 035 × 031) = 036
Определяем числа зубьев зубчатых передач множительных групп
Из справочника для заданных значений передаточных отношений принимаем суммарное число зубьев зубчатых колес Sz = 75 [2 с. 575 приложение 21] тогда:
z1 = 48z2 = Sz – z1 = 75 – 48 = 27;
z3 = 40z4 = Sz – z3 = 75 – 40 = 35;
z5 = 27z6 = Sz – z5 = 75 – 27 = 48.
z7 = 20z6 = Sz – z5 = 75 – 20 = 55.
z9 = 20z10 = Sz – z9 = 77 – 20 = 57;
z11 = 20z12 = Sz – z11 = 77 – 20 = 57.
z13 = 37z14 = Sz – z13 = 84 – 37 = 47;
z15 = 20z16 = Sz – z15 = 84 – 20 = 64.
z17 = 36z18 = Sz – z17 = 93 – 36 = 57;
z19 = 19z20 = Sz – z19 = 93 – 19 = 74.
В соответствии с выполненными расчетами вычерчиваем кинематическую схему коробки скоростей с указанием чисел зубьев
Рисунок 3 – Кинематическая схема коробки скоростей
Для расчета силовых характеристик коробки скоростей задаемся расчетной цепочкой при которой выходной вал вращается с частотой вращения n2 = 64 обмин (рекомендуется выбирать из нижней трети диапазона частот вращения). По графику частот вращения находим рассчитываемые передачи (z3z4 ; z9z10 ; z11z12 ; z15z16) и частоты вращения валов
nI = 1430 обмин;nII = 1634 обмин;nIII = 573 обмин;
nIV = 201 обмин;nV = 63 обмин.
Расчет силовых характеристик
Определяем крутящие моменты на валах привода
гдеi – КПД элементов составляющих привод [1 с. 61 таблица 7]
З = 098 – КПД зубчатой передачи;
п = 099 – КПД одной пары подшипников качения.
Расчет зубчатых передач
Исходные данные для расчета передачи z3z4:
-частота вращения шестерни n1 = 1430 обмин
-передаточное число u = 3540 = 088;
-крутящий момент на шестерне Т1 = МI = 16027 Нмм;
-крутящий момент на колесе Т2 = МII = 13606 Нмм.
Выбираем материал колес – сталь 40Х термообработка – закалка токами высокой частоты (т.в.ч.) до твердости на поверхности не менее HRCЭ50 [3 с. 82].
Определяем допускаемые контактные напряжения
гдеsHlimb – предел контактной выносливости для легированных сталей высокой твердости
sHlimb = 17HRC + 70 = 17 × 50 + 70 = 920 МПа
КHL = 1 [3 с. 33] – коэффициент долговечности;
[SH] = 11 [3 с. 33] – коэффициент безопасности.
Определяем предварительное межосевое расстояние исходя из условия обеспечения достаточной контактной выносливости активных поверхностей зубьев
гдеКа = 495 [3 с. 32] – коэффициент учитывающий для прямозубых;
КНb = 135 [3 с. 32] - коэффициент учитывающий неравномерность распределения нагрузки по ширине зуба при несимметричном расположении колес относительно опор валов;
yba = baW = 01 [2 с. 103] – коэффициент ширины венца относительно межосевого расстояния.
По предварительному межосевому расстоянию определяем модуль зацепления
Расчетный модуль зацепления округляем до стандартного значения по ГОСТ9563-60* m = 2 мм [3 с. 36].
Определяем делительные диаметры колес z3 и z4
d3 = mz3 = 2×40 = 80 мм d4 = mz4 = 2×35 = 70 мм
Уточняем межосевое расстояние
Определяем ширину венцов колес
[b] = yba×aw = 01×75 8 мм.
Определим окружную скорость колес
Для прямозубых колес при u = 599 мс рекомендуется назначать седьмую степень точности передачи [3 с. 32].
При модуле m = 2 мм и ширине венца b = 8 мм определяем контактные напряжения на активных поверхностях зубьев
гдеКН – уточненный коэффициент учитывающий неравномерность распределения нагрузки по ширине зуба;
КН = КНb × КНu = 135 × 1 = 135
КНb = 135 [3 с. 32] - при несимметричном расположении колес относительно опор валов
КНu = 1 [3 с. 40] – при окружной скорости передачи u = 599 мс 7-й степени точности и коэффициенте ширины венца yba = 01.
Расчет показывает что sН = 582 МПа [sН] = 837 МПа следовательно передача z3 и z4 удовлетворяют требованиям контактной выносливости.
Определяем окружную силу действующую в зацеплении z3 z4
Определяем радиальную силу
Fr = Ft tg α = 401 tg 20° = 146 Н
Определяем допускаемые напряжения изгиба
где = 675 МПа [3 с. 44] – предел изгибной прочности;
[SF]’ = 18 [3 с. 44] – коэффициент безопасности для легированных сталей;
[SF]” = 1 [3 стр. 45] – коэффициент учитывающий непостоянство механических свойств материала.
При работе цилиндрической прямозубой передачи при одинаковых материалах и ширинах зубчатых венцов наибольшие изгибные напряжения возникают у зубчатых колес имеющих меньшее число зубьев. В нашем случае у колеса z4 = 35 поэтому проверочный расчет на прочность при изгибе будем проводит для колеса z4.
Определяем действующие изгибные напряжения для колеса z4
гдеKF = 1264 [3 с. 43] – коэффициент учитывающий неравномерность распределения напряжений по ширине зуба;
YF = 3 8 [3 с. 42] – коэффициент формы зуба при числе зубьев z = 35.
Из расчета видно что изгибные напряжения не превышает предельно допустимых для выбранного материала и термообработки sF = 131 МПа [sF] = 386 МПа следовательно рассчитанная передача удовлетворяет требованиям изгибной прочности.
Для остальных рассчитываемых передач принимаем те же материалы и термообработку что и для передачи z3 z4. Методика расчета этих передач аналогична. В таблице 2 представлены исходные данные и результаты расчета передач по расчетной цепочке.
Таблица 2 – Расчет зубчатых передач
Рассчитываемая передача
Число зубьев ведущего колеса
Число зубьев ведомого колеса
Частота вращения ведущего колеса
Продолжение таблицы 2
Частота вращения ведомого колеса
Расположение передачи относительно опор валов
Материал зубчатых колес
Способ получения заготовки
Предел контактной выносливости
Коэффициент безопаснос-ти контактных напряжений
Коэффициент долговечности
Допускаемое контактное напряжение
Предел выносливости при отнулевом цикле изгиба
Коэффициент безопасности напряжений изгиба (от материала)
Коэффициент безопасности напряжений изгиба (от заготовки)
Допускаемое напряжение изгиба
Крутящий момент на ведущем колесе
Крутящий момент на ведомом колесе
Коэффициент для прямозубых передач
Коэффициент (от твердости и расположения относительно опор)
Коэффициент ширины венца относительно межосевого расстояния
Допускаемое межосевое расстояние
Допускаемый модуль зацепления
Принятый модуль зацепления
Принятое межосевое расстояние
Расчетная ширина зуба
Принятая ширина зуба
Поправочный коэффициент для контактных напряжений
Динамический коэффициент для контактных напряжений
Окружная скорость колес
Фактическое контактное напряжение
Окружное усилие в зацеплении
Радиальное усилие в зацеплении
Коэффициент формы зуба
Поправочный коэффи-циент для напряжений изгиба
Динамический коэффи-циент для напряжений изгиба
Коэффициент неравномерности распределения напряжений изгиба
Коэффициент ширины венца относительно делительного диаметра
Фактическое напряжение изгиба
Проверка условия контактной прочности
Проверка условия изгибной прочности
Для остальных передач каждой множительной групп принимаем модуль и ширину венца такие же как и у передач по расчетной цепочке. Определяем геометрические размеры остальных передач множительных групп (таблица 2).
Таблица 2 – Размеры зубчатых колес
Размеры зубчатых колес мм
Делительный диаметр d
Исходными данными для расчета валов являются осевые размеры определяемые по компоновочному эскизу (рисунок 4) и сосредоточенные силы приложенные в зацеплениях.
Рисунок 4 – Схема расположения валов и зацеплений
в плоскости перпендикулярной осям валов
Окружные силы Ft (изображаются удлиненными стрелками) приложены в точке пересечения делительных окружностей и направлены вдоль общей касательной к окружностям. Радиальные силы Fr (изображаются укороченными стрелками) направлены к центрам соответствующих колес.
При разработке компоновочного эскиза учтена возможность сцепления колес на валу V с колесами на валу IV (длинная кинематическая цепь) и с колесами на валу II (короткая кинематическая цепь). При расчете опорных реакций все внешние силы должны быть разложены на вертикальные и горизонтальные составляющие. Так как по эскизной компоновке два луча соединяющие точки приложения сил зацеплений с центром делительной окружности для валов II IV отличаются от 90 и 180° то для этих валов необходимо учесть перекос осей на углы α1 α2 и α3 (рисунок 4).
Приведем составляющие сил зацеплений на ведущих шестернях к вертикальным и горизонтальным.
В сечении «2» вала II
Fy = –Ft · sin α1 + Fr · cos α1 = –544 · sin 45° + 198 · cos 45° = –245 Н
Fx = –Ft · cos α1 – Fr · sin α1 = –544 · cos 45° – 198 · sin 45° = –525 Н
гдеFt = 544 Н – окружная сила в зацеплении колес z9 z10 ;
Fr = 198 Н – радиальная сила в зацеплении колес z9 z10 ;
α1 = 45° – угол между силой Ft и горизонталью.
В сечении «2» вала III
Fy = –Ft · sin α2 + Fr · cos α2 = –1075 · sin 30°20’ + 391 · cos 30°20’ = –205 Н
Fx = Ft · cos α2 + Fr · sin α2 = 1075 · cos 30°20’ + 391 · sin 30°20’ = 1125 Н
гдеFt = 1075 Н – окружная сила в зацеплении колес z11 z12 ;
Fr = 391 Н – радиальная сила в зацеплении колес z11 z12 ;
α2 = 30°20’ – угол между силой Ft и горизонталью.
В сечении «2» вала IV
Fy = Ft · sin α2 – Fr · cos α2 = 2312 · sin 36°25’ – 841 · cos 36°25’ = 689 Н
Fx = Ft · cos α2 + Fr · sin α2 = 2312 · cos 36°25’ + 841 · sin 36°25’ = 2362 Н
гдеFt = 2312 Н – окружная сила в зацеплении колес z15 z16 ;
Fr = 841 Н – радиальная сила в зацеплении колес z15 z16 ;
α2 = 36°25’ – угол между силой Ft и горизонталью.
Так как силы зацепления парных колес взаимно уравновешены то на ведомые колеса (сечения валов «1») действуют силы зацеплений равные по значению но противоположные по знаку соответствующим силам на ведущих колесах. Запишем вертикальные и горизонтальные составляющие на ведомых колесах в сечениях «1»
В сечении «1» вала III
Fy = 245 НFx = 525 Н
В сечении «1» вала IV
Fy = 205 НFx = –1125 Н
В сечении «1» вала V
Fy = –689 НFx = –2362 Н
Рассмотрим подробно расчет вала I.
Определяем предварительные значения диаметра вала из расчета на чистое кручение по пониженным касательным напряжениям
где[] = 20 МПа [3 с. 161] – допускаемое напряжение при кручении.
На этапе предварительной компоновки выявляем расстояние между опорами и положение зубчатых колес относительно опор для последующего определения опорных реакций и подбора подшипников.
По посадочным диаметрам валов под опоры подбираем стандартные подшипники: подшипник 202 ГОСТ 8338-75 (внутренний диаметр 15 мм).
Исходными данными для расчета являются нагрузки действующие на валы со стороны механических передач(нагрузки от передач были определены при расчете соответствующих передач) а также осевые размеры валов. Ориентировочные размеры валов получим из предварительной эскизной компоновки редуктора с учетом расположения шкивов и цилиндрических зубчатых колес.
Расчетные схемы вала и эпюры моментов представлены на рисунке 5.
Рисунок 5 – К расчету вала I
Для определения реакции опоры RY1 составляем уравнение моментов относительно опоры «2»
гдеFY1 = Fr(Z3Z4) = 146 Н – вертикальная сила в зацеплении колес z3z4 равная радиальной;
= 975 мм; 2 = 535 мм – расстояние от места приложения нагрузки до середин опор вала (размеры выявлены из предварительной компоновки).
Для определения реакции опоры RY2 составляем уравнение моментов относительно опоры «1»
Для определения реакции опоры RX1 составляем уравнение моментов относительно опоры «2»
Для определения реакции опоры RX2 составляем уравнение моментов относительно опоры «1»
Определяем суммарные радиальные реакции опор
Рассмотрим наиболее нагруженный подшипник.
Эквивалентная нагрузка
РЭ2 = R2 · V · Кб · КТ = 276 · 1 · 12 · 1 = 3312 Н
где V = 1 [3 с. 212] – коэффициент от вращения внутреннего кольца;
Кб = 12 [3 с. 214 таблица 9.19] – коэффициент от условий работы;
КТ = 1 [3 с. 214 таблица 9.19] – коэффициент от температуры.
Для более нагруженного подшипника вычисляем расчетный ресурс
гдеа1 = 1 [3 132] – коэффициент учитывающий вероятность отказов подшипника;
а2 = 07 [3 132] – коэффициент учитывающий условия работы;
C = 11200 [3 с. 233 таблица 136] - динамическая грузоподъемность.
Рекомендуемое значение расчетного ресурса для заданных условий работы 10000 ч [4 с. 129 таблица 71]. Так как расчетный ресурс подшипников больше требуемого то делаем вывод о достаточной надежности подшипников вала I.
Уточненный расчет вала состоит в определении коэффициентов запаса прочности для опасных сечений и сравнения их с допускаемыми значениями [S] = 25 [3 с. 162].
Определим коэффициенты запаса прочности для предположительно опасных сечений ведомого вала принимая что нормальные напряжения изменяются по симметричному циклу а касательные – по отнулевому (пульсирующему).
Назначаем материал вала – сталь 45 имеющую механические свойства:
-временное сопротивление на разрыв sв =598 Нмм2;
-предел выносливости по нормальным напряжениям s-1 = 309 Нмм2;
-предел выносливости по касательным напряжениям t-1 = 179 Нмм2.
Определяем результирующие изгибающие моменты в середине посадочного места колеса
В качестве концентратора напряжений в середине колеса выступает шлицы. Предварительно намечаем шлицы средней серии (наружный диаметр 20 мм внутренний диаметр 16 мм ширина шлица 4 мм число шлицев 6).
Проверяем вал на усталостную прочность в опасном сечении при одновременном действии изгибающего и крутящего моментов. Для этого определяем коэффициент запаса усталостной прочности
гдеSs – коэффициент запаса усталостной прочности при изгибе
s-1 = 309 Нмм2 [3 с. 200] – предел выносливости стали 35 при изгибе;
k () = 188 [5 с. 554] – эффективный коэффициент концентрации напряжений изгиба;
b – поправочный коэффициент учитывающий качество обработки и состояние поверхности вала (для термообработанных валов с последующим шлифованием);
es – масштабный фактор учитывающий влияние размеров сечения вала на усталостную прочность;
sV – амплитуда цикла изгибных напряжений при симметричном цикле
W – момент сопротивления изгибу шлицевого сечения вала
d = 16 мм – диаметр впадин шлицев;
= 126 – коэффициент учитывающий усиление вала выступами шлицев
St – коэффициент запаса усталостной прочности при кручении
t-1 = 179 Нмм2 [3 с. 200] – предел выносливости при кручении;
k () = 315 [5 с. 554] – эффективный коэффициент концентрации напряжений кручения;
et – масштабный фактор учитывающий влияние размеров сечения вала на усталостную прочность;
tV – амплитуда цикла напряжений при кручения
WКР – момент сопротивления кручению сечения вала
= 01 – коэффициент чувствительности материала вала к постоянной составляющей отнулевого цикла касательных напряжений;
tМ = tV = 79 МПа – постоянная составляющая отнулевого цикла касательных напряжений
Из расчета видно что фактический коэффициент запаса усталостной прочности для опасного сечения вала S = 43 больше предельно допустимого коэффициент запаса [S] = 25 следовательно рассчитанный вал обладает достаточной усталостной прочностью.
Проверяем на прочность шпоночное соединение выходного конца быстроходного вала с полумуфтой по допускаемым напряжениям смятия [sСМ] = 100 МПа [3 с. 170]
гдеd = 14 мм – диаметр вала
lP = l – b = 40 – 5 = 35 мм – длина рабочей грани шпонки
l = 40 мм – общая длина шпонки
h = 5 мм – высота шпонки
t1 = 3 мм – глубина шпоночного паза на валу;
b = 5 мм – ширина шпонки.
Проверяем на прочность шлицевое соединение блока шестерен с валом по допускаемым напряжениям смятия [sСМ] = 100 МПа [3 с. 175]
гдеz = 6 – число шлицев
АСМ – расчетная площадь смятия
RCP – средний радиус соединения
RCP = 025(D+d) = 025(20+16) = 9 мм
D = 20 мм – диаметр вершин шлицев
d = 16 мм – диаметр впадин шлицев
f = 02 мм – фаска при вершине шлица.
Из расчета видно что напряжение смятия в шлицевом соединении не превышает предельно допустимого т.е. sСМ = 4 МПа [sСМ] = 100 МПа следовательно шлицевое соединение удовлетворяет требованиям прочности при смятии.
Для остальных валов принимаем те же материалы и термообработку что и для вала I. Методика расчета этих валов аналогична. В таблицах 4 7 представлены исходные данные и результаты расчета валов в соответствии с расчетными схемами и предварительной компоновкой коробки.
Рисунок 6 – К расчету вала II
Таблица 4 – Расчет вала II
К расчету реакций опор и выбору подшипников
Осевой размер вала (рисунок 6)
Вертикальная сила в сечении 1
Горизонтальная сила в сечении 1
Вертикальная сила в сечении 2
Горизонтальная сила в сечении 2
Частота вращения вала
Вертикальная реакция левой опоры
Вертикальная реакция правой опоры
Горизонтальная реакция левой опоры
Горизонтальная реакция правой опоры
Суммарная реакция левой опоры
Суммарная реакция правой опоры
Расчетнаяэквивалентная нагрузка
Изгибающий момент в вертикальной плоскости
Продолжение таблицы 4
Изгибающий момент в горизонтальной плоскости
Изгибающий момент в сечении 1
Изгибающий момент в сечении 2
Предварительный диаметр вала из
расчета на чистое кручение
Принятый диаметр вала в межопорном расстоянии
Посадочный диаметр внутреннего кольца
Обозначение подшипника
Динамическая грузоподъемность
Расчетный ресурс подшипников
К расчету запасов усталостной
прочности в сечении 1
Предел прочности материала вала
Предел изгибной выносливости материала вала
Предел выносливости материала вала при кручении
Коэффициент чувствительности постоянной
составляющей отнулевого цикла
касательных напряжений
Концентратор напряжения
Диаметр вершин шлицев
Диаметр впадин шлицев
Момент сопротивления изгибу
Момент сопротивления кручению
Эффективный коэффициент концентрации
Амплитуда цикла нормальных напряжений
Амплитуда цикла касательных напряжений
Постоянная составляющая цикла
Коэффициент запаса усталостной прочности
прочности в сечении 2
Диаметр вала в опасном сечении
Ширина шпоночного паза
Глубина паза на валу
К расчету прочности шпоночного
и шлицевого соединений
Напряжение смятия на боковой поверхности шпонки
Длина шлицевого соединения
Напряжение смятия на боковой поверхности шлицев
Рисунок 7 – К расчету вала III
Таблица 5 – Расчет вала III
Осевой размер вала (рисунок 7)
Продолжение таблицы 5
К расчету прочности шпоночного соединения
Рисунок 8 – К расчету вала IV
Таблица 6 – Расчет вала IV
Осевой размер вала (рисунок 8)
Продолжение таблицы 6
Рисунок 9 – К расчету вала V
Таблица 7 – Расчет вала V
Осевой размер вала (рисунок 9)
Вертикальная сила в опасном сечении
Горизонтальная сила в опасном сечении
Продолжение таблицы 7
Изгибающий момент в опасном сечении
прочности в опасном сечении
Расчет механизма переключения скоростей
В качестве привода управления коробкой скоростей выбираем кулачковый привод. При этом используется только одна рукоятка управления. Коробка скоростей имеет три подвижных блока поэтому используем три цилиндрических кулачка управления (для каждого блока шестерен свой кулачек).
Основной задачей проектирования кулачкового механизма является определение диаметра цилиндрического кулачка (барабана).
Согласно графику частот вращения и ходам подвижных блоков вычерчиваем развертки кулачков управления (рисунок 10).
Диаметр кулачка определяется исходя из обеспечения угла подъема профиля α ≥ 30°. При таком угле подъема исключается заклинивание кулачкового механизма и снижаются потери на трение толкателя о поверхность паза кулачки.
Определяем диаметр кулачка
гдеz = 16 – число ступеней регулирования;
Н = 44 мм – максимальный ход блока (тройной блок шестерен)
h = 10 мм – ширина паза кулачка.
При профилировании кулачка необходимо учесть что в множительной группе 41 имеются два блока шестерен следовательно кулачек управления данной группой имеет два рабочих паза в каждом из которых предусмотрены нейтральные положения. Таким образом исключается одновременное включение зацеплений и поломка зубьев. При правильном профиле кулачка и достаточном зазоре между сцепляемыми колесами в нейтральном положении дополнительных устройств блокировки не требуется.
При настройке коробки на скорости n7 n11 – n16 движение с вала II передается сразу на вал V минуя валы III и IV и множительную группу длинной кинематической цепи. Для устранения холостого вращения неиспользуемых блока и валов в профиле кулачка двойного блока также предусмотрено нейтральное положение.
Нейтральные положения на развертках профилей кулачков (рисунок 10) показаны заштрихованными кружками. Для проверки соблюдения условия α ≥ 30° на рисунке указан угол подъема при переключении скоростей с n6 на n7 когда имеет место наибольший ход тройного блока.
Рисунок 10 – Развертка кулачков управления коробки скоростей
При выполнении курсового проекта я научился: производить кинематический расчёт множительных структур коробок скоростей (строить график частот вращения используя графоаналитический метод определять передаточные отношения механических передач определять числа зубьев зубчатых колёс разрабатывать кинематическую схему коробки скоростей); производить расчёт основных силовых характеристик коробки скоростей (определять крутящие моменты на валах и передаваемые мощности); выполнять прочностной расчёт геометрических размеров элементов механических передач (зубчатых колёс); производить предварительный (без учёта изгиба) и уточнённый (на усталостную прочность) расчёты валов выполнять подбор и проверочный расчёт опорных подшипников и шпоночных соединений а также рассчитывать на прочность по допускаемым напряжениям смятия шлицевые соединения.
Кроме этого были выполнены сборочные чертежи коробок скоростей и рабочие чертежи основных деталей.
В результате работы над проектом сконструирована коробка скоростей со следующими характеристиками:
Число ступеней регулирования
Диапазон частот вращения
Тип множительных структур
Сложенная с неравномерным
рядом частот вращения
Частота вращения ротора электродвигателя
Номинальная мощность приводного электродвигателя
Список использованных источников
Курсовое проектирование по деталям машин и подъемно-транспортным машинам: Методические указания и задания к проектам и работам для студентов-заочников технических специальностей высших учебных заведений П. Г. Гузенков А. Г. Гришанов В. П. Гузенков. – М.: Высш. Шк. 1990. – 111с.: ил.
Расчет и конструирование коробок скоростей и подач Ю.И. Свирщевский Н.Н. Макейчик – Минск: Вышейш. школа 1976 - 590 с.: ил.
Курсовое проектирование деталей машин: Учеб. Пособие для учащихся машиностроительных специальностей техникумов С.А. Чернавский К.Н. Боков И.М. Чернин и др. – 2-е изд. перераб. и доп. – М.: Машиностроение 1988 - 416 с.: ил.
Анурьев В. И. Справочник конструктора – машиностроителя Т.2. М.: Машиностроение 1978 – 784 с.
Расчет на прочность деталей машин: Справочник И.А. Биргер Б.Ф. Шор Г.Б. Иосилевич – 3-е изд. перераб. и доп. – М.: Машиностроение 1979 - 702 с.: ил.
Рекомендуемые чертежи
- 18.05.2024
- 21.05.2024
- 29.05.2024
- 04.06.2024