Инструментальная наладка



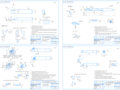
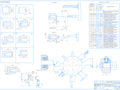
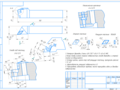
- Добавлен: 25.01.2023
- Размер: 588 KB
- Закачек: 0
Описание
Состав проекта
![]() |
![]() |
![]() ![]() ![]() ![]() |
![]() ![]() ![]() ![]() |
![]() ![]() ![]() |
![]() ![]() ![]() ![]() |
Дополнительная информация
первый лист.cdw

закрепленный в гнезде 1.
Переместить инструмент в исходную
точку перехода на быстром ходу
одновременно по двум осям X и Z.
Установить частоту вращения
Переместить инструмент в точку 1
по двум осям на быстром ходу.
Переместить инструмент в точку 2
по оси X на рабочей подаче.
Переместить инструмент в точку 3
по оси Z на рабочей подаче.
Переместить инструмент в точку 4
Переместить инструмент в точку 5
по двум осям на рабочей подачe.
Переместить инструмент в
исходную точку перехода на быстром
ходу одновременно по двум осям.
Переместить револьверную головку в
точку смены инструмента на быстром
Переместить инструмент в точку 6
Переместить инструмент в точку 7
КП2068998-25-ВМТ-414-02
Инструментальная наладка на
токарно-револьверный станок
Программа на 1-ый переход.
Задать левое вращение шпинделя
Установить рабочую подачу 0.2ммоб
Резец с мех. креп.cdw

Зазор между нижней опорной поверхностью гнезда державки и опорной
плитой не допускается.
кроме опор под режущую пластину
Шероховатость режущей поверхности 6.3.
Маркировать обзначения чертежа
место маркировки-одна из боковых
Механическое крепление
записка.doc
Кафедра: металлорежущие станки и инструменты.
ПОЯСНИТЕЛЬНАЯ ЗАПИСКА К КУРСОВОМУ ПРОЕКТУ.
Тема: проектирование инструментальной наладки на токарно-револьверный станок мод.IB34ОФ30 с ЧП. Расчет и проектирование червячной шлицевой фрезы.
Содержание курсового проекта
Конструкторская доработка чертежа детали .3
1 Номинальные размеры.3
3 Шероховатость поверхности.4
Разработка инструментальной наладки.4
1 План обработки детали.4
3 Проектирование инструментальной наладки ..11
4 Схема установки инструментов в револьверной головке ..11
5 Разработка управляющих программ на переходы 11
Проектирование инструментальной наладки ..12
1 Обоснование выбора инструментального материала .12
2 Проектирование 4-х инструментов из наладки 14
Расчет и проектирование червячной шлицевой фрезы ..18
1 Исходные данные 19
2 Графическое определение профиля 24
3 Конструирование фрезы 25
В данном курсовом проекте производится проектирование инструментов для механической обработки деталей в машиностроении.
В первой части работы производится разработка техпроцесса для изготовления детали из прутка на токарно-револьверном станке с ЧПУ. Производится конструкторская доработка чертежа детали по заданному контуру осевого сечения. Затем разрабатывается техпроцесс изготовления детали (план операций) проектируется инструментальная наладка.
После этого производится проектировка четырех режущих инструментов из наладки.
Конструкторская доработка чертежа детали.
Для детали назначим номинальные размеры допуски шероховатости.
1 Номинальные размеры.
В качестве заготовки для обработки детали будем использовать пруток по ГОСТ 2590-71. Наибольший диаметр детали не должен выходить за пределы значений допустимых по технической характеристике станка т.е. 24 40 мм. Кроме того учитываем припуск на обработку. Поэтому наибольший диаметр детали не выходит за пределы значений 22 38 мм. Руководствуясь этим примем наружный диаметр детали равным - 36 мм. Остальные размеры назначим конструктивно с сохранение конфигурации детали и в соответствии с рядами нормальных линейных размеров по ГОСТ 6639069 (рис. 1).
Точность нарезания внутренней резьбы по квалитету – 7H. Допуски по квалитетам выбираем по таблице в [7] и проставляем вместе с номинальными размерами на детали (рис. 1).
Поля допусков располагаем относительно номинальных размеров следующим образом: в "плюс" - для диаметральных размеров внутренних поверхностей в "минус" - для диаметральных размеров наружных поверхностей симметрично - для остальных размеров.
3. Шероховатость поверхности.
Шероховатость поверхностей назначаем в соответствии с видом поверхности и точностью ее обработки (табл. 3 из [7]). Выбранная шероховатость показана на рисунке .
Разработка инструментальной наладки.
1. План обработки детали
При изготовлении детали (рис. 1) на токарном револьверном станке типовой является следующая последовательность обработки: чистовая порезка торца наружная черновая обработка внутренняя черновая внутренняя чистовая нарезания резьбы отрезка. Эту последовательность принимаем за основу. Последовательность обработки детали по показана в таблице 2.
Марка материала режущей части
Центровать торец на размер 5±02
Сверлить отверстие 14+0058 на глубину 45-
-Расточить отверстие 24+027 на глубину 33±03
-Нарезать резьбу М36x15-8g на длине 38 мм
Резец токарный для нарезания резьбы
Отрезать деталь на размер 41 мм
Переход – это часть технологической операции выполняемая одним режущим инструментом. В каждой переходе указывает порядок обработки заготовки поверхность обработки основные размеры предельные отклонения и шероховатости.
Координаты опорных точек траектории
Кодовая запись кадра
Вызвать на рабочую позицию инструмент закрепленный в гнезде 1
Переместить инструмент в исходную точку перехода на быстром ходу одновременно по двум осям
Задать левое вращение шпинделя
Установить частоту вращения шпинделя 400 обмин
Установить рабочую подачу 02 ммоб
Переместить инструмент в т.1 на быстром ходу одновременно по двум осям
Переместить инструмент в т.2 по оси X на рабочей подаче
Переместить инструмент в т.3 по оси Z на рабочей подаче
Переместить инструмент в т.4 на быстром ходу по оси Z
Переместить инструмент в т.5 на быстром ходу одновременно по двум осям
Переместить инструмент в т.6 по оси Z на рабочей подаче
Переместить инструмент в т.7 по оси X на рабочей подаче
Переместить револьверную головку в точку смены инструмента на быстром ходу одновременно по двум осям
Вызвать на рабочую позицию инструмент закрепленный в гнезде 2
Переместить инструмент в исходную точку перехода по оси Z на быстром ходу
Установить частоту вращения шпинделя 900 обмин
Установить рабочую подачу 01 ммоб
Переместить инструмент в т1. по оси Z на быстром ходу
Переместить инструмент в т.2по оси Z на рабочей подаче
Переместить инструмент в и.т. по оси Z на быстром ходу
Переместить инструмент (центр. сверло) в т.3 по оси Z на быстром ходу
Переместить инструмент в т.4 на быстром ходу. Величина перемещения 2200 задана в относительной системе отсчета.
Цикл глубокого сверления с периодически быстрым выводом сверла из заготовки через каждые 10мм пути рабочего хода.
Переместить револьверную головку в точку смены инструмента на быстром ходу одновременно по двум осям.
Вызвать на рабочую позицию инструмент закрепленный в гнезде 3
Установить частоту вращения шпинделя 700 обмин
Переместить инструмент в точку 2 перехода на рабочем ходу одновременно по двум осям
Переместить инструмент в точку 3 рабочем ходу
Переместить инструмент в точку 3по оси Z рабочем ходу
Переместить инструмент в исходную точку перехода на быстром ходу по двум осям.
Вызвать на рабочую позицию инструмент закрепленный в гнезде 4
Переместить инструмент в т.1 на быстром ходу по оси Z
Переместить инструмент в т.2 по оси Z на рабочей подаче
Переместить инструмент в т.3 по оси X на рабочей подаче
Вызвать на рабочую позицию инструмент закрепленный в гнезде 5
Установить частоту вращения шпинделя 700об мин
Установить левое вращение шпинделя
Переместить револьверную головку в точку смены инструмента на быстром ходу по оси Z
3. Проектирование инструментальной наладки
Проектирование наладки осуществляют на основе плана обработки детали. Раздел включает выполнение следующих работ:
составление координатных чертежей на операцию;
составление схемы установки инструментов в револьверной головке;
составление управляющей программы на все переходы.
Начало координат т.О отсчитываем от центра правого торца заготовки горизонтально проводим ось z вертикально –х. Находим координаты каждой точки перехода относительно осей и записываем их дискретной величиной т.е к размеру в мм добавляем два нуля. Значение координат выбираем из имеющихся размеров детали рисунок 1. Например при продольном точении инструмент проводим в к заготовки на 5-10мм больше чем диаметр заготовки при расточки длину растачиваемой поверхности увеличиваем на 1-2 мм и ставим координаты соответствующей точки.
Координатные чертежи.
4. Схема установки инструментов в револьверной головке.
Схема установки инструментов представляет собой эскиз револьверной головки шпинделя с закрепленной в нем заготовкой и порядок инструментов для обработки заготовки рисунок 2.
5.Разработка управляющих программ на переходы.
Получение формы и размеров на токарных станках с ЧПУ обеспечивается движением инструмента по траектории заданной управляющей программой.
Управляющая программа представляет собой совокупность команд на языке программирования соответствующая заданному алгоритму функционирования станка для обработки конкретной заготовки.
Для составления управляющей программы используют опорные точки.
К опорным точкам согласно ГОСТ 20523-80 относят точки расчетной траектории в которых происходит изменения закона описывающего траекторию или условий траекторий технологического процесса.
Станок 1В340ФЗО оснащен оперативным устройством числового программного управления «Электроника НЦ-31» составления программ обработки для которого не требуется специальной подготовки.
Ввод программы в память станка с ЧПУ как правило осуществляется с пульта управления.
Проектирование инструментов наладки.
1 Обоснование выбора инструментального материала.
Большинство конструкций металлорежущего инструмента изготовляют составными - рабочая часть состоит из инструментального материала а крепежная из обычных конструкционных сталей (сталь 45 50 4ОХ и т.п. в случае тяжело нагруженных корпусов - сталь У10 или 9ХС).
Исключение составляют мелкоразмерные или слесарные инструменты изготовляемые целиком из инструментального материала а также инструменты изготовляемые из углеродистых инструментальных сталей (ГОСТ 1435-74) и легированных инструментальных сталей (ГОСТ 5950-73).
Рабочую часть инструментов в виде пластин или стержней из быстрорежущей стали (ГОСТ 19265-73) соединяют с крепежной частью с помощью сварки. Эксплутационные и технологические свойства и рекомендуемые области применения наиболее распространенных быстрорежущих сталей выбираются из справочников.
В зависимости от режущих свойств и химического состава быстрорежущие стали делят на две группы: нормальной и повышенной красностойкости. К первой группе отнесены стали Р18 Р9 Р6М5 Р12 и др.
Быстрорежущие стали – сложнолегированные. В их состав входят: углерод вольфрам ванадий хром кобальт молибден марганец никель сера фосфор кремний. А у стали Р6М5 кроме того молибден.
Сталь Р18 имеет удовлетворительную прочность и шлифуемость широкий интервал оптимальных температур закаливания но пониженную пластичность. Ее рекомендуется применять для изготовления всех видов режущих инструментов для обработки деталей из обычных конструкционных материалов.
Основной сталью группы нормальной красностойкости является сталь Р6М5. В ее составе: углерод 08-088% вольфрам 5-65% хром 338-44% ванадий 17-21% молибден 5-55%. Эта сталь по режущим свойствам близка к стали Р18 но имеет повышенную склонность к обезуглероживанию при нагреве. Она значительно дешевле стали Р18. Ее широко применяют для изготовления режущих инструментов используемых при обработке деталей из конструкционных материалов.
Вывод: наиболее подходящей маркой твердосплавной пластины для сверла и метчика при обработки данной детали является сталь Р6М5 из-за:
- своей относительной дешевизной по сравнению с другими сталями
- широкой распространенности
- высоких прочностных характеристик и т.д.
Твердые сплавы в виде пластин соединяют с крепежной частью с помощью пайки или специальных высокотемпературных клеев. Многогранные твердосплавные пластины закрепляют прихватами винтами клиньями и т.д.
Применение твердых сплавов позволяет получить большую экономию средств. Твердые металлокерамические сплавы отличаются от быстрорежущей стали большим содержанием вольфрама (до90%) а в некоторых марках также наличием титана (от5 до60%) образующих тугоплавкие карбиды
При правильной эксплуатации инструменты оснащенные пластинками из твердого сплава обеспечивают более высокую эффективность (от 3 до 5 более раз) по машинному времени по сравнению с инструментами из быстрорежущей стали.
Твердые сплавы по своему химическому составу подразделяются на две группы:
)вольфрамокарбидные состоящие из карбида вольфрама и твердого раствора карбида вольфрама в кобальте
)титановольфрамокарбидныые состоящие из карбида вольфрама карбида титана и твердого раствора их карбидов в кобальте. С повышением содержания кобальта режущие свойства твердых сплавов понижаются но зато повышается их прочность и вязкость.
Выбирая марку твердосплавной пластины я отдал предпочтение вольфрамокарбидным пластинам а именно сплаву ВК10 по следующим соображениям:
Проведя сравнительный анализ нескольких инструментальных материалов а именно вольфрамокарбидные титановольфрамокарбидные по таким параметрам как твердость теплопроводность ударная вязкость и т.д. я пришел к выводу что:
) Раз теплопроводность вольфрамокарбидных сплавов почти не зависит от содержания кобальта и приближается к теплопроводности малоуглеродистой стали а теплопроводность титановольфрамокарбидиых сплавов значительно ниже (в 2-3 раза) теплопроводности вольфрамокарбидных сплавов и приближается к теплопроводности быстрорежущей стали то для расточного резца для глухих отверстий и отрезного резца лучше всего подходит вольфрамокарбидная пластина ВК10 так как эти резцы работают в условиях с плохим охлаждением особенно расточной резец для глухих отверстий.
)Титановольфрамокарбидные сплавы более чувствительны к трещинам чем вольфрамокарбидные причем с повышением процентного содержания титана склонность к трещинам резко возрастает.
)Твердость является одним из важных свойств твердого сплава так как от нее зависит износоустойчивость. Она у твердых сплавов в 5-8 раз выше чем у быстрорежущей стали и возрастает с увеличением вольфрама или титана и уменьшением кобальта.
)Сплав ВК10 обладает такой же универсальностью как и наиболее распространенный из вольфрамокарбидных ВК8 однако:
а) режущие свойства (по скорости резания) у ВК10 на 30-70% лучше чем у ВК8
б) стойкость в 2-5 раз выше чем у ВК8.
) сплав ВК10 показывает хорошие результаты:
а) при черновом и чистовом точении
) при работе с ударами и с неравномерным припуском
в) при расточных включая алмазное точение и отрезных (отрезные резцы) операциях.
г) при обработке высокотвердых чугунов.
д) при обработке жаропрочных материалов титановых сталей и сплавов.
) Особенностью сплава ВК10 его меньшая склонность к выкрашиванию режущих кромок.
Для резца с механическим креплением выберем сплав ВК10. Он относится к новой группе титановых сплавов в которых карбид вольфрама заменен карбидом титана или карбонитридом а связкой является никель железо молибден.
Этот сплав отличается высокой окалиностойкостью малым коэффициентом трения пониженной твердостью склонностью к трещенообразованию при пайке.
Безвольфрамовые сплавы показывают хорошие результаты при получистовой обработке вязких металлов конструкционных металлов никеля и бронзы
2. Проектирование 4-х инструментов из наладки.
Инструмент №1: Резец с механическим креплением.
Применение многогранных твердосплавных неперетачиваемых пластин на резцах обеспечивает:
-повышение стойкости на 20-25% по сравнению с напаянными резцами;
-возможность повышения режимов резания за счет простоты восстановления режущих свойств многогранных пластин путем их поворота;
-сокращение затрат на инструмент в 2-3 раза потерь вольфрама. и кобальта в 4-5 раз вспомогательного времени на смену и переточку резцов;
-упрощение инструментального хозяйства.
В данном курсовом проекте выбран резец токарный резьбовой 2660-0003 ГОСТ 24996-81 со следующими параметрами:
-режущая пластина 196524 0360 220416- 1 ГОСТ 19046-80
-материал режущей пластины - твердый сплав ВК8 ГОСТ 3882-74;
-материал державки резца СТ 40-ГОСТ 4543-71 40 45HRC
-режущая пластина должна закрепляться плотно без покачивания. Зазор между нижней опорной поверхностью гнезда державки и опорной пластиной не допускается. Зазор между рабочей и опорной поверхностями не допускается. Контролировать на просвет.
- опорная пластина не должна выступать за пределы гнезда больше чем на 05 мм
-шероховатость рабочей поверхности RZ 63
Инструмент №2: Спиральное сверло с коническим хвостовиком.
Спиральное сверло 14 предназначенодля сверления глухого отверстия 14 мм на глубину 45мм в заготовке детали.
Обоснование выбора материала режущей и хвостовой части сверла.
Для экономии быстрорежущей стали все сверла с коническим хвостовиком более 6 мм изготовляются сварными.
В основном сверла делают из быстрорежущих сталей. Твердосплавные сверла делают для обработки конструкционных сталей высокой твердости (45 56HRC) обработке чугуна и пластмасс. Исходя из твердости обрабатываемого материала – 207 НВ принимаем решение об изготовлении сверла из быстрорежущей стали Р6М5 ГОСТ 19265-73. Крепежную часть сверла изготовим из стали 40Х (ГОСТ 454-74).
Выбор геометрических параметров сверла.
Задний угол . Величина заднего угла на сверле зависит от положения рассматриваемой точки режущего лезвия. Задний угол имеет наибольшую величину у сердцевины сверла и наименьшую величину - на наружном диаметре. Выбираем: .= 12°.
Передний угол. Также является величиной переменной вдоль режущего лезвия и зависит кроме того от угла наклона винтовых канавок и угла при вершине 2. Передняя поверхность на сверле не затачивается и величина переднего угла на чертеже не проставляется.
Угол при вершине сверла. Принимаем: 2125°.
Угол наклона винтовых канавок. Угол наклона винтовых канавок определяет жесткость сверла величину переднего угла свободу выхода стружки и др. Назначаем = 30°.
Угол наклона поперечной кромки. При одном и том же угле определенному положению задних поверхностей соответствует вполне определенная величина угла и длина поперечной кромки и поэтому угол служит до известной степени критерием правильности заточки сверла. Назначаем: = 45°.
Расчет назначение конструктивных размеров сверла.
Спиральные сверла одного и того же диаметра в зависимости от серии бывают различной длины. Длина сверла характеризуется его серией. В связи с тем что длина рабочей части сверла определяет его стойкость жесткость прочность и виброустойчивость желательно во всех случаях выбирать сверло минимальной длины. Серия сверла должна быть выбрана таким образом чтобы
Расчетная длина рабочей части сверла lо равна расстоянию от вершины сверла до конца стружечной канавки может быть определена по формуле:
lо = lр + lвых + lд + lв + lп + lк + lф
lп - запас на переточку lп = l * (i +1) где
lф - величина характеризующая уменьшение глубины канавки полученной при работе канавочной фрезы
lк + lф = 1.5*dсв = 1.5*14 = 21 мм
l0 = 4.2 + 0 +55 + 0 + 41 + 21 = 121.2 мм.
В соответствии с ГОСТ 12121-77 (" Сверла спиральные из быстрорежущей стали с коническим хвостовиком ") уточняем значения l0 и общей длины L :
Положение сварного шва на сверле : lс = l0 + (2 3) = 153 мм.
Диаметр сердцевины сверла dс выбирается в зависимости от диаметра сверла и инструментального материала
dс = 0.15*dсв = 0.15 * 14 = 2.1 мм.
Ширина ленточки fл = (0.45 0.32)*sqrt(dс) = 0.7 мм.
Высота ленточки hл = (0.05 0.025)*dс = 0.4 мм.
Центровые отверстия на сверлах изготовляются в соответствии с ГОСТ 14034-74.
Сверло 2302-0846 ГОСТ 20697-75 - 4мм
Инструмент №3: Резец расточной с пластиной из твердого сплава.
Резец расточной предназначен для обработки ступенчатого глухого отверстия.
В качестве режущей части резца применяется пластинка из твердого сплава. Пластина изготавливается из твердого сплава ВК10 в соответствии с требованиями ГОСТ 25397-82.
Паять пластину ВК8 ГОСТ 2209-69.Паять латунью Ла63 по ГОСТ 15527-70.Рекомендуемая толщина слоя припоя 005-01 мм. Разрыв слоя припоя не допускается.
Материал рабочей части 63 65 HRC державки резца-40 45 HRC.
Материал державки резца Ст 40х-ГОСТ 4543-71.
На рабочей части резца не должно быть трещин и выкрашиваний.
Так же резец должен удовлетворять условию наименьшего растачиваемого отверстия в нашем случае 16
Угол при вершине резца j должен быть равен 8°.
В соответсвии с этими требованиями выбираем –
Резец 2101-0601 ВК10 ГОСТ 18883-73
Инструмент №4: Резец токарный отрезной(прорезной) с пластиной из твердого сплава.
Материал державки Ст 40х-ГОСТ 4543-71
Режущая часть резца ВК8 ГОСТ 3882-74
Паять пластину 13572 ГОСТ 17163-82 ВК6
Паять припоем марки ПрМНМц 68-4-2 или Л63 по ГОСТ 15527-74. Слой припоя толщиной до 02 мм. Разрыв паяного шва между опорными поверхностями рабочей пластины и державки не должны превышать 10%.
Прижоги трещины и сколы на режущей части не допускаются. Контролировать при пятикратном увеличении.
Расчет и проектирование червячной шлицевой фрезы.
Червячные шлицевые фрезы относятся к большей группе режущих инструментов работающих по методу огибания (обкатки).Обкаточные инструменты являются наиболее сложными как по конструированию так и по изготовлению.
В состав задания на проектирование червячной шлицевой фрезы входит:
-графическое определение профиля зуба
-расчет основных конструктивных элементов фрезы
-конструирование фрезы
-составление рабочего чертежа
В задании на проектирование приведено условное обозначение шлицевого вала по ГОСТ 1139-80 (СТ СЭВ 187-75) подлежащего обработки фрезой конструкцию которой предстоит разработать.
Обозначение содержит: букву указывающую поверхность центрирования число зубьев и основание номинальных размеров торцевого сечения вала обозначение полей допусков помещенные после соответствующих размеров.
Число зубьев 10 d внутр. 102 мм по посадке f8 D наруж. 112 мм по посадке e9 ширина зуба в=16 мм по посадке f7.
Основные размеры торцевого сечения и числа зубьев шлицевых валов установленные ГОСТ 1139-80 «Соединения шлицевые прямобочные.»
Боковые стороны каждого зуба вала должны быть оси симметрии зуба до пересечения с окружностью диаметра d.
Предельные отклонения размеров для рекомендуемых полей допусков вала:
*102*112: z=10 число зубьев
c номинальное 05 предельные отклонения +03
Предельные отклонения размеровмкм:
2 (-0036 и -009) 112 (-0072 и -0159) 10(-016 и -0034)
Расчетный наружный диаметр шлицевого вала
Расчетный внутренний диаметр шлицевого вала
Расчетная ширина шлица
Диаметр начальной окружности вала
Минимальное значение углового параметра
Максимальное значение углового параметра
Значение углового параметра для второй точки
Значение углового параметра для третьей точки
. Значение углового параметра для четвертой точки
Абсциссы точек профиля фрезы
Ординаты точек профиля фрезы
Абсцисса центра заменяющей окружности
Ордината центра заменяющей окружности
Радиус заменяющей окружности
Коэффициенты уравнения отклонений заменяющей окружности
Величины углов соответствующие наибольшим отклонениям
Абсциссы точек соответствующие наибольшим отклонениям
. Ординаты точек соответствующие наибольшим отклонениям
Наибольшие отклонения точек заменяющей окружности от теоретической кривой
Суммарная величина отклонений
Шаг витков фрезы по нормали
Толщина зуба фрезы по начальной прямой
Толщина зуба для третьей и четвертой точек профиля зуба
Высота головки зуба фрезы до усика
.Высота головки зуба фрезы
Величина смещения фаски от начальной прямой
Ширина канавки по дну впадины профиля фрезы
Полная высота зуба фрезы
Высота шлифованной части зуба фрезы
Ширина выкружки шлицевого вала
Угловой параметр уравнения проверки ширины выкружки валика
Проверка условия по ширине выкружки валика
Задний угол на вершине зуба фрезы
Угловой параметр уравнения бокового угла
Задний угол на боковых сторонах зуба
Радиус закругления канавки
Величины затылования зуба
2 Графическое определение профиля.
При конструировании червячной шлицевой фрезы определение профиля зуба в нормальном сечении представляет задачу трудоемкую и ответственную.
Предварительные вычисления:
Вычислить расчетный диаметр Dр окружности выступа валика Dр=5699 мм
Вычислить расчетную ширину шлица вр = 10006 мм
вычислить начальный диаметр dw=563 мм
Вычислить высоту ножки зуба фрезы от начальной прямой до основания технологической канавки по формуле
Выбрать масштаб М построения М(30:1) М(50:1)
Ось I расположить посередине чертежа
Полюс Р зацепления расположить ниже верхней границы рамки чертежа на величину Hf + 10 мм.
Вычертить шлицевый вал в исходном положении 2.
Провести окружности: начальную 3 впадин 4 и 5.
Разделить начальную окружность на 64 части и нанести метки.
Построить из центра вала вспомогательную окружность диаметром равным расчетной ширине шлицевого вала.
Из точек пометок на начальной окружности провести касательные к вспомогательной окружности.
От каждой касательной восстановить перпендикуляр проходящий через (.) Р(полюс зацепления).Точки пересечения пометить. Через эти точки провести лекальную кривую- линия зацепления (профилирования) во взаимном обкаточном движении нач.окр. по нач. прямой.
Определить положение точек профиля зуба фрезы. Точки aibici являются сопряженными.
Через точки ai провести лекальную кривую которая является искомым профилем в нормальной сечении зуба фрезы.
Уточнить ширину и форму усика зуба фрезы путем построения вероятной формы профиля поднутрения состоящих из двух сопряженных удлиненных эвольвент касающихся окружности 5.
Уточнить форму основания зуба фрезы. При этом следует учитывать что профиль зуба следует проложить за точку а3 с тем чтобы не зарезать фаску у вала и что формирование фаски произойдет при обкаточном движении от исходного положения фрезы вправо а вала по часовой стрелке.
3.Конструирование фрезы.
Конструирование фрезы выполняется на основе результатов расчета конструктивных элементов тех. Условий к червячно-шлицевым фрезам по ГОСТ 8027-60.
Конечным результатом конструирования является рабочий чертеж фрезы.
Конструирование зуба фрезы.
Правильно сконструированный зуб чистовой червячно-шлицевой фрезы со шлифованным профилем должен отвечать следующим требованиям:
Обеспечить свободный выход шлифовального круга
отвечать условию достаточного числа переточек фрезы и недолговечности.
Исключить образование седловины при затыловании резцом шлифовальным кругом.
Обеспечить достаточный объем стружечной канавки.
Удовлетворить условию прочности нового и сточенного зуба.
Соответствовать общей компановке фрезы и условиям наибольшего числа зубьев прочности тела фрезы и виброустойчивости.
Допуски на элементы фрезы.
Наибольшая погрешность шага 16 мкм.
Наибольшая накопленная ошибка шага на длине любых двух шагов +-25 мкм
Радиальное биение по наружному диаметру 32 мкм
Отклонение предельного угла от номинального значения 30 градусов
Отклонение шага винтовых стружечных канавок 6% от размера шага винтовой канавки +- 25
Накопленная ошибка окружного шага канавок 100 мкм
Наибольшая разность окружных шагов канавки в пределах одного оборота 63 мкм.
Конусность по наружному D по длине фрезы 50 мкм
радиальное биение буртиков 20 мкм
торцевое биение буртиков 16 мкм
Порядок конструирования фрезы.
Выбрать координатную систему с началом Ои
Определим масштаб М при допущении места положения центра шлифовального круга за пределы рамки чертежа.
Проводим окружность радиусом 05Dеu.
Построим центральный угол Е
Откладываем затылок К вычисленный в таблице.
Проводим хорду через точки ab.
Из середины хорды восстанавливаем перпендикуляр.
Получаем центр окружности О’ заменяющий кривую первого затылка к.
Строим из центра О” окружность проходящую через (.)a и b.
Строим из центра О’ окружность проходящую через (.)g.
Делаем засечку (центр Ок шлифовального круга) дугами радиусом Rk=40 м из центра g’и радиусом равным О’а – hшл.+ Rk из центра О’.
Проводим окружность радиусом Rk.
Пометим точку касания F и точки f и m.
Из центра Ou проводим окружность через точку f.
Откладываем второй затылок к1.
Вычисляем х=(а’m : aa’) к1
Откладываем величину х.
Из центра Ou проводим окружность u отмечаем точку 1.
Проводим две хорды соединяющие точки w и f w и l.
Из середины обоих хорд восстанавливаем перпендикуляр и отмечаем точку O” их пересечения.
Из центра Ou проводим окружность заменяющую второй затылок к1 через три точки lf.w.
Из центра Ou проводим окружность радиусом R5 через точку S.
Из середины дуги проводим окружность радиусом r5.
Касательно к окружности проводим под углом (=20 град.)Линию спинки зуба.
Проводим окружность диаметром du.
Проверяем соответствия:
B=(065 07)H и n> 05B
Если соответствие выполняется это означает что конструирование провели правильно.
Таким образом приходим к выводу что использование метода получения деталей машин обработкой резанием по сравнению с другими методами (литье горячая и холодная штамповка и т. д. Обеспечивает наибольшую гибкость производственного процесса.
Обработка резанием позволяет осуществлять быстрый переход от обработки деталей(заготовок) одного размера и конфигурации к обработке деталей (заготовок) другого типа.
Также обработка резанием очень эффективна благодаря применению универсальной оснастки то есть металлорежущего инструмента особенно инструмента со сменным механическим креплением.
Бергер И. И. «Справочник молодого токаря». Минск: Высшая школа 1972 С.320.
ГОСТ 20697-75. «Сверло».
«Металлорежущий инструмент. Каталог. Часть 1 .Резцы и фрезы». Под редакцией Я.А. Музыканта и др:НИИмаш1983 С.446.
Методические указания к выполнению курсового проекта по проектированию и производству металлорежущих инструментов. Составители: Попов А. Ю. Чирков В.НЧерных Н.А.Омск: ОмПИ 1981
Семенченко И.И. Матюшин В.М. Сахаров Г.Н.:
«Проектирование металлорежущих инструментов».М.:Машгиз 1963
Сахаров Г.Н. Арбузов О.Б.Боровой Ю.П.:
«Металлорежущие инструменты» М. Машиностроение 1989.
Методические указания по курсовому проектированию:
«Проектирование инструментальной наладки на токарно-револьверный станок модели 1В340ФЗО с ЧПУ». Составители:
Попов А.Ю. и др.. Омск-1993.
второй лист.frw

Режущая часть резца ВК8 ГОСТ 3882-74.
Паять пластину 13572 ГОСТ 17163-82 ВК6.
Паять припоем марки ПрМНМц 68-4-2 или латунью Л63 по ГОСТ 15527-74. Слой припоя толщиной
мм. Разрывы паяного шва между опорными поверхностями рабочей пластины и державки не
должны превышать 10%.
трещины и сколы на режущей части не допускаются. Контролировать при пятикратном
Маркировать марку сплава
шифр.. Место маркировки - одна из боковых поверхностей резца.
Рабочая часть сверла Р6М5 по ГОСТ 19265-73.
Материал хвостовика Ст 40х ГОСТ 4543-71.
Твердость рабочей части сверла 63 65 HRC
хвостовика 40 45 HRC.
Обратная конусность рабочей части 0
В месте сварки раковины
трещины и другие дефекты не
Сверла должны быть заточены. Забоины
выкрашивания и прижоги на рабочих кромках не допускаются.
Материал державки резца Ст 40х ГОСТ 4543-71.
Паять пластину ВК8 по ГОСТ 2209-69
Твердость рабочей части 63 65 HRC
державки резца - 40 45 HRC.
Паять латунью Ла 63 по ГОСТ 15527-70. Рекомендуемая толщина слоя припоя 0
слоя припоя не допускается.
На рабочей части резца не должно быть трещин и выкрашиваний.
Несоосность оси хвостовика с осью рабочей части не более 0
Маркировать марку сплава. Место маркировки - одна из боковых поверхностей.
Режущая пластина 08116-170405R30 по ГОСТ 19062-73.
Материал пластины - твердый сплав марки ВК8 по ГОСТ 3882-74.
Материал державки резца Ст 40х ГОСТ 4543-71 40 45 HRC.
Режущая пластина должна закрепляться плотно
без покачивания. Зазор между нижней опорной
поверхностью гнезда державки и опорной пластиной не допускается. Зазор между рабочей и
опорной поверхностями не допускается. Контролировать на просвет.
Опорная пластина не должна выступать за пределы гнезда больше
Шероховатость рабочей поверхности Rz 6
Маркировать обозначение резца. Место маркировки - одна из боковых поверхностей резца.
-державка; 2- режущая пластина по ГОСТ 19062-73;
-опорная пластина по ГОСТ 19079-80; 4-прихват;
Пластина 13572 ГОСТ 17163-82 M 2:1
КП-206998-ВМТ-414-02-08
КП 206998 ВМТ 414 02 08
Гнездо под пластинку
Пластина по ГОСТ 2209-69 М2:1
Пластина опорная по ГОСТ 19079-80
Пластина 08116-170405 по ГОСТ 19062-73