Автоматизировать процесс точения фланцев колец


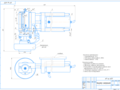
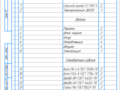
- Добавлен: 24.01.2023
- Размер: 534 KB
- Закачек: 0
Описание
Автоматизировать процесс точения фланцев колец
Состав проекта
![]() |
![]() ![]() ![]() |
![]() |
![]() |
![]() |
![]() ![]() |
![]() ![]() ![]() |
![]() |
![]() ![]() ![]() ![]() |
![]() ![]() ![]() |
![]() ![]() ![]() ![]() |
![]() |
Дополнительная информация
расчёт гидроцилиндра.doc
Определим диаметр поршня перемещающего электромагнит ДКМ010 с закреплённой в нём деталью по вертикали.
Усилие создаваемое гидроцилиндром рассчитывается по формуле:
Р – давление масла в гидравлической системе Р=4 Мпа ();
S – площадь поршня мм2;
F – вес перемещаемый гидроцилиндром Н (F=112 Н – вес электромагнита ДКМ 010 с деталью). Расчётное усилие F1=F×s=112×15=
=170 Н s – коэффициент запаса.
Площадь поршня определяется по формуле:
d – диаметр поршня мм.
Из выше изложенных уравнений определим диаметр поршня гидроцилиндра создающего необходимое усилие:
Исходя из конструктивных соображений (жёсткость и прочность) выбираем Гидроцилиндр 7021-0061 ГОСТ 19898-74.
Пересчитаем тяговую способность выбранного гидроцилиндра с учётом диаметры штока (d=10 мм):
Эффективная площадь гидроцилиндра определяется следующим выражением:
Определим тяговое усилие выбранного гидроцилиндра с учётом эффективной площади поршня (при подаче рабочего давления в штоковую полость):
Определим диаметр штока исходя из прочностных характеристик учитывая вес груза перемещаемого манипулятором (F=112 Н – вес электромагнита ДКМ 010 с деталью).
Для определения диаметра штока воспользуемся следующим выражением:
- допустимое растягивающее усилие для стержня; где
- предел текучести; для стали 45 - =380
n – коэффициент запаса; n=25 – для крепёжных изделий в машиностроении.
Подставляя полученные значения получим расчётный диаметр штока:
Диаметр штока выбранного гидроцилиндра d=10 мм (превышает расчётное в 10 раз) – условие прочности выполняется!
Записка к подрезке торца фланцев++.doc
Государственное образовательное учреждение
высшего профессионального образования
по курсу «Автоматизация производственных процессов»
Тема: «Автоматизировать процесс точения фланцев колец»
Разработка принципиально-структурной схемы устройства
1 Анализ автоматизируемого процесса 4
2 Разработка перечня основных функций устройства.
Функциональный анализ 6
3 Выбор исполнительных механизмов 7
4 Выбор приводов исполнительных механизмов и датчиков 7
5 Цикл работы устройства (автомата) 10
1 Разработка технического задания на проектируемый узел 13
2 Разработка и анализ схемы узла 14
3 Расчёт параметров тягового гидроцилиндра манипулятора. 14
4 Описание конструкций и работы устройства 17
Список литературы 20
Автоматизация производственных процессов есть комплекс мероприятий по разработке новых прогрессивных технологических процессов и проектированию на их основе высокопроизводительного технологического оборудования осуществляющего рабочие и вспомогательные процессы без непосредственного участия человека.
Автоматизация — это комплексная конструкторско-технологическая задача создания принципиально новой техники на базе прогрессивных технологических процессов обработки контроля сборки. Она включает создание таких методов и схем обработки конструкций и компоновок машин и систем машин которые были бы невозможны если бы человек по-прежнему оставался непосредственным участником технологического процесса.
Любую продукцию для получения которой известны методы и маршруты обработки наиболее просто можно получить на универсальном неавтоматизированном оборудовании с ручным управлением при непосредственном участии человека. Автоматизация производственных процессов имеет цель — повышение производительности и качества выпускаемой продукции сокращение количества обслуживающих рабочих по сравнению с неавтоматизированным производством.
За счет реализации этих факторов обеспечивается экономический эффект и окупаемость затрат на автоматизацию. При этом важнейшим определяющим фактором успешного внедрения является надежность автоматизированного оборудования. Если показатели надежности оказываются низкими сложнейшие и технически совершенные автоматические системы машин становятся менее производительными чем неавтоматизированное оборудование; число же рабочих после автоматизации не сокращается а возрастает. Поэтому важнейшим требованием к специалистам работающим в области автоматизации машиностроения является умение правильно оценивать целесообразную степень автоматизации в данных конкретных условиях выбирать и рассчитывать оптимальные варианты построения машин и систем машин. Это не может быть правильно выполнено без наличия специальных знаний которые как правило не даются в общих курсах по технологии и конструированию; поэтому во всех вузах созданы специальные курсы по автоматизации производственных процессов.
Уровень и способы автоматизации зависят от вида производства его серийности оснащенности техническими средствами.
Автоматизация и механизация получили наибольшее распространение в массовом и крупносерийном видах производства.
Автоматизировать процесс точения фланцев колец с подробной разработкой структурной схемы и конструкции манипулятора
1Анализ автоматизируемого процесса
Сущность токарной обработки состоит в формировании цилиндрической поверхности инструментом с одной режущей кромкой при этом как правило происходит вращение заготовки и перемещение резца относительно заготовки. Во многих отношениях этот традиционный метод металлообработки является относительно простым для понимания. С другой стороны этот широко распространённый процесс хорошо поддаётся оптимизации путём тщательного изучения различных факторов оказывающих на него влияние.
В настоящее время всё большее применение находит токарная обработка с применением токарных резцов со сменными неперетачиваемыми твердосплавными пластинами которые позволяют не только повысить режимы обработки стойкость инструмента но и сократить время на размерную подналадку инструмента при смене режущей кромки либо вообще её исключить на операциях чернового и получистового точения (т.к. точность изготовления пластин и точность их позиционирования регламентированная стандартами ISO лежит в пределах ±013 мм).
В разрабатываемом автоматизированном технологическом процессе предполагается использование токарного инструмента со сменными многогранными пластинами; будут применяться резцы токарные проходные (левого исполнения) - державка токарная PSSNL 2525 M12 расточная державка правая – S25T-PCLNR 12 пластина токарная для получистового точения сталей – SNMG 120408 PM 4225 (одинаковая для обеих державок); инструмент изготовлен фирмой Sandvik (Швеция).
Использование данного инструмента позволит не только повысить производительность механической обработки но и облегчит контроль за состоянием режущей кромки (прогнозируемая стойкость) что очень важно в условиях безлюдной технологии.
Предполагается вести токарную обработку на следующих режимах резания:
Скорость резания - V=150 ммин;
Число оборотов шпинделя - n=500 обмин (с учётом диаметра детали 100 мм и скорости резания);
Глубина резания - t=2 мм;
Минутная подача (т.к. предполагается использование привода подачи резца не связанного напрямую с вращением шпинделя) Sм=75 мммин (в переводе на оборотную подачу So=015);
Расчётная стойкость режущей кромки Т=45 мин (с учётом используемых режимов резания).
Схема резания (подрезка торца расточка внутреннего отверстия):
2 Функциональный анализ.
Произведем составление перечня основных функций устройства необходимых для реализации технического процесса. Для каждой функции формулируются требования предлагаются и рассматриваются варианты устройств позволяющих наиболее рационально осуществить заданную функцию производится анализ их относительных преимуществ.
Предлагаемые варианты способы
Подача детали на рабочую позицию
Автоматическая или ручная
)Автоматически толкателем
)автоматически манипулятором
Зажим детали в манипуляторе
Обеспечить надёжный зажим детали при загрузкеразгрузке
)Механический захват
)Электромагнит ДКМ010
Отрывное усилие – 150кг
)Пневматический элемент
Зажим детали на рабочей позиции
Обеспечить неизменное усилие детали при обработке
)Трёхкулачковый патрон
)Специальное зажимное устройство
Обеспечение зажимного устройства
Обеспечить требуемое усилие закрепления(Рз=2000Н)
Привод вращения шпинделя
Обеспечить необходимую скорость резания (v=150 ммин) и крутящий момент
)Трёхфазный асинхронный электродвигатель
)Пневматический привод
Привод рабочей подачи суппорта
Обеспечить необходимую подачу (Sм=75мммин) и усилие резания
)Электодвигатель через пару винт- гайка
Удаление деталей с рабочей позиции
3 Выбор исполнительных механизмов
В результате проведенного функционального анализа производится окончательный выбор исполнительных механизмов.
Детали располагаются на конвеере по 50 штук.
Подача детали с конвейера в токарный патрон будет осуществляться специальным манипулятором.
Закрепление детали на рабочей позиции производится в трёхкулачковом патроне оснащённом механизмом автоматического зажима-разжима.
Точение детали (подрезка торца расточка внутреннего отверстия) производится токарным проходным резцом установленным в резцедержателе; направление рабочей подачи – перпендикулярно оси детали от периферии к центру детали (радиальная подача).
Эвакуация готовых деталей производится автоматически манипулятором в поддон.
4 Выбор приводов исполнительных механизмов и датчиков
Для каждого механизма в соответствии с условиями его работы выбираются соответствующие приводы.
)Для приводов перемещения (горизонтальное и вертикальное) манипуляторов выбираем гидропривод т.к. он обеспечивает необходимые величины перемещения скорости и усилия.
)Для привода ленточного конвейера выбираем электродвигатель т.к. он обеспечит необходимую скорость движения полотна.
)Для привода закрепления детали выбираем гидропривод т.к. он обеспечивает необходимую величину усилия закрепления.
)Для привода вращения шпинделя выбираем электрический асинхронный трёхфазный двигатель т.к. он обеспечивает необходимые величины частоты вращения и момента на шпинделе.
)Для привода рабочей подачи суппорта выбираем электрический двигатель постоянного тока который обеспечит необходимую скорость вращения винта ШВП с заданным крутящим моментом.
)Для привода захвата манипулятора выбираем электромагнит т.к. он обеспечивает необходимое усилие захвата детали.
) х1 – датчик работы привода конвейера.
) х2 – датчик нахождения детали на загрузочной позиции.
) х3 х4 – датчики начального и конечного положения привода вертикального перемещения загрузчика.
) х5 – датчик работы электромагнита загрузчика.
) х6 х7 – датчики начального и конечного положения привода горизонтального перемещения загрузчика.
) х8 х9 – датчики начального и конечного положения привода зажима детали в токарном патроне.
) х10 – датчик вращения шпинделя.
) х11 х12 – датчики начального и конечного положения привода рабочей подачи горизонтального токарного суппорта.
) х13 х14 – датчики начального и конечного положения привода рабочей подачи вертикального токарного суппорта.
) х15 х16 – датчики начального и конечного положения горизонтального перемещения съёмника.
) х17 х18 – датчики начального и конечного положения вертикального перемещения съёмника.
) х19 – датчик работы электромагнита съёмника.
5 Цикл работы устройства (автомата)
Условные обозначения устройств (механизмов):
Привод конвейера –(1).
Привод вертикального перемещения загрузчика – (2).
Электромагнит загрузчика – (3).
Привод горизонтального перемещения загрузчика - (4).
Привод закрепления детали в токарном патроне - (5).
Привод вращения шпинделя - (6).
Привод рабочей подачи горизонтального токарного суппорта – (7).
Привод рабочей подачи вертикального токарного суппорта –(8).
Привод горизонтального перемещения съёмника - (9).
Привод вертикального перемещения съёмника - (10).
Электромагнит съёмника - (11).
(2) – крайнее верхнее.
(4) – крайнее левое.
(7) – крайнее правое.
(8) – крайнее верхнее.
(9) – крайнее правое.
(10) – крайнее верхнее.
Циклограмма работы автомата.
После построения циклограммы определяется цикловая производительность:
Таким образом цикловая производительность проектируемого устройства составляет 053 деталей в минуту.
1 Разработка технического задания на проектируемый узел
Задача – разработать конструкцию манипулятора для подачи и удаления
деталей с рабочей позиции.
Цели проектирования:
) Повышение надежности работы механизма перемещения.
) Повышение производительности.
Содержание работы (этапы):
) Анализ и выбор схемы устройства.
) Составление расчетной схемы и определение параметров привода.
) Конструирование узла.
) Описание конструкции и работы устройства
Технические характеристики:
) Рабочее давление 4 МПа
) Грузоподъемность 70 кг.
) ход поршня гидроцилиндра – 0..100 мм.
Технические условия:
) Опресовать до работы при настройке.
) Обеспечить плавность хода механизма.
) Привод гидравлический.
) Использовать в качестве рабочей жидкости масло индустриальное И-20А ГОСТ 5326-82.
) Утечки масла не допускается.
2 Разработка и анализ схемы узла
Нашей задачей является проектирование манипулятора для подачи и удаления деталей. Для заданной детали простой кольцевой формы имеющей достаточно большую плоскую опорную поверхность целесообразно использовать ленточный конвеер. Ленточный конвейер — один из наиболее прогрессивных видов транспортировки обеспечивающий высокую производительность и технико-экономическую эффективность при больших грузопотоках. В современном массовом и крупносерийном производстве ленточные конвейеры являются неотъемлемой частью технологического процесса. Ленточные конвейеры регулируют темп производства обеспечивают его ритмичность способствуют повышению производительности труда и увеличению выпуска продукции.
В качестве привода используется гидроцилиндр.
Работают на давлении до 160 кгссм2 что позволяет значительно уменьшить их габариты. Плавны и бесшумны в работе имеют малую инерцию срабатывания.
3 Расчёт параметров тягового гидроцилиндра манипулятора.
Определим диаметр поршня перемещающего электромагнит ДКМ010 с закреплённой в нём деталью по вертикали.
Усилие создаваемое гидроцилиндром рассчитывается по формуле:
Р – давление масла в гидравлической системе Р=4 Мпа ();
S – площадь поршня мм2;
F – вес перемещаемый гидроцилиндром Н (F=112 Н – вес электромагнита ДКМ 010 с деталью). Расчётное усилие F1=F×s=112×15=
=170 Н s – коэффициент запаса.
Площадь поршня определяется по формуле:
d – диаметр поршня мм.
Из выше изложенных уравнений определим диаметр поршня гидроцилиндра создающего необходимое усилие:
Исходя из конструктивных соображений (жёсткость и прочность) выбираем Гидроцилиндр 7021-0061 ГОСТ 19898-74.
Пересчитаем тяговую способность выбранного гидроцилиндра с учётом диаметры штока (d=10 мм):
Эффективная площадь гидроцилиндра определяется следующим выражением:
Определим тяговое усилие выбранного гидроцилиндра с учётом эффективной площади поршня (при подаче рабочего давления в штоковую полость):
Определим диаметр штока исходя из прочностных характеристик учитывая вес груза перемещаемого манипулятором (F=112 Н – вес электромагнита ДКМ 010 с деталью).
Для определения диаметра штока воспользуемся следующим выражением:
- допустимое растягивающее усилие для стержня; где
- предел текучести; для стали 45 - =380
n – коэффициент запаса; n=25 – для крепёжных изделий в машиностроении.
Подставляя полученные значения получим расчётный диаметр штока:
Диаметр штока выбранного гидроцилиндра d=10 мм (превышает расчётное в 10 раз) – условие прочности выполняется!
4. Описание конструкции и работы устройства
Описание работы автомата для подрезки торцев деталей «Фланец».
Автомат предназначен для подрезки торца и расточки отверстия детали представленной на рис.1:
Материал детали: Сталь 20 ГОСТ 1050-88
Автомат состоит из ленточного конвейера загрузчика токарного шпинделя двух токарных суппортов (горизонтального и вертикального) и съёмника для снятия готовых деталей.
Цикл обработки начинается с подачи детали ленточным конвейером на позицию загрузки (на ленте конвейера через равные промежутки расставлены ориентирующие пальцы на которых располагаются детали). После того как деталь доставлена на позицию загрузки конвейер останавливается.
Загрузчик с захватным устройством в виде электромагнита захватывает деталь и переносит её к разжатым кулачкам токарного патрона (ось шпинделя располагается вертикально). Электромагнит отключается и деталь (с небольшой высоты) падает в разжатые кулачки токарного патрона. Загрузчик возвращается в начальное положение.
Деталь зажимается включается вращение шпинделя затем следует рабочая подача горизонтального токарного суппорта. После того как подрезка произведена суппорт отводится в начальное положение. Затем включается рабочая подача вертикального токарного суппорта. По окончанию расточки суппорт отводится в начальное положение. Вращение шпинделя отключается кулачки патрона разжимаются.
Затем к детали подводится съёмник который захватывает её перемещает к бункеру готовых деталей над которым электромагнит съёмника отключается и деталь под воздействием собственного веса падает в бункер-приёмник.
В процессе выполнения работы был проведен анализ автоматизируемого технологического процесса. Затем был произведен функциональный анализ т.е. разработка перечня основных функций будущего устройства. С помощью анализа были выбраны исполнительные механизмы и датчики с подробным описанием их действия.
В дальнейшем был разработан цикл работы устройства и циклограмма работы автомата с помощью которых была определена цикловая производительность.
Во второй части работы был спроектирован манипулятор произведён расчёт потребного усилия закрепления детали в руке манипулятора на основании которого выбран гидроцилиндр привода захвата. Были проанализированы основные схемы устройства произведен расчет привода и был разработан сборочный чертеж.
Разработана и проанализирована принципиально – структурная схема автоматического устройства и автоматизируемого процесса подрезки торца детали «Фланец» которая осуществляется на основе компоновки проанализированных и выбранных исполнительных механизмов приводов и датчиков контроля состояния исполнительных механизмов и параметров технологического процесса и составлено описание цикла работы.
Ансеров М. “Приспособления для металлорежущих станков”. Изд-е 4-е исправл. и доп. Л. “Машиностроение” ( Ленингр. отд-ние ) 1975 г. 656 с.
Справочник технолога-машиностроителя. В 2-х т. Т.2 Под ред. А.Г.Косиловой и Р.К.Мещерякова. – 4-е изд. перераб. и доп. – М.: Машиностроение 1986. 496 с. ил
Справочник технолога-машиностроителя. В 2-х т. Т.1 Под ред. А.Г.Косиловой и Р.К.Мещерякова. – 4-е изд. перераб. и доп. – М.: Машиностроение 1986. 656 с. ил.
Промышленные роботы в машиностроении: Альбом схем и чертежей: Учеб. пособие для технических вузов Ю.М. Соломенцев К.П. Жуков Ю.А. Павлов и др.- М.: Машиностроение 1986. – 140 с.: ил.
Кузнецов М.М. Проектирование автоматизированного производственного оборудования: Учеб. пособие для вузов.- М.: Машиностроение 1987. – 288 с.: ил.
Владзиевский А.П. Белоусов А.П. Основы автоматизации производства в машиностроении. Изд. 2-е перераб и доп. Учебник для техникумов. М. "Высш. школа" 1974.
новый Манипулятор.cdw

.Грузоподьёмность 70 кг
Ход поршня гидроцилиндра-0 100мм.
Рабочее давление - 4МПа
Технические условия:
Опресовать до работы при настройке.
Обеспечить плавность хода механизма.
Использовать в качестве рабочей жидкости масло
индустриальное И-20А ГОСТ 5326-82.
Температура окружающей среды от +5 до +25
Утечки масла не допускаются.
Манипулятор с электормагнитом
122.doc
Грузоподъемные электромагниты ДКМ (круглые) аналоги М22 М42 М62. Грузоподъемные электромагниты ДПМ (прямоугольные) аналоги ПМ15 ПМ26. Грузоподъемные электромагниты ДПМА (аккумуляторная серия).
Основные особенности круглых электромагнитов серии ДКМ:
- новые заново спроектированные литые корпуса имеют сильное оребрение и высокую износостойкость.
- усиленное магнитное поле.
- улучшенный теплообмен что позволяет уменьшить нагрев электромагнитов в процессе работы.
- дополнительное ограждение защищает коробку выводов и подводящий электрический кабель от механических повреждений.
- сама коробка выводов закрывается толстостенной литой крышкой которая надежно защищает ее от возможных ударов в процессе работы в то же время выводы электромагнита позволяют легко выполнить подключение питающего кабеля.
- новые литые рельефные брони электромагнитов имеют высокие износостойкость и жесткость меньшую восприимчивость к ударам о грузы. Они увеличивают срок службы изделий и обеспечивают надежную защиту катушки электромагнита.
Грузоподъемные электромагниты ДКМ
Круглые грузоподъемные электромагниты
новая Спецификация.cdw

Гидроцилиндр поршневой ГОСТ 19898-74
Болт М8 х 8 ГОСТ 15589-70
Болт М12х 8 ГОСТ 7796-70
Шайба 8Н ГОСТ 6402-70
Шайба 6Н ГОСТ 6402-70
Гайка М6 ГОСТ15521-70