Автоматизация технологического процесса производства жевательной резинки



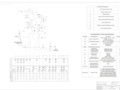
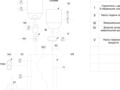
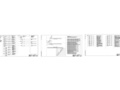
- Добавлен: 24.01.2023
- Размер: 1 MB
- Закачек: 2
Описание
Состав проекта
![]() |
![]() ![]() ![]() |
![]() |
![]() ![]() ![]() ![]() |
![]() |
![]() ![]() ![]() |
![]() ![]() ![]() |
![]() |
![]() ![]() ![]() |
![]() ![]() ![]() |
![]() |
![]() ![]() ![]() |
![]() ![]() ![]() |
![]() ![]() ![]() |
![]() ![]() ![]() |
![]() ![]() ![]() |
![]() |
![]() ![]() ![]() |
![]() ![]() ![]() |
![]() ![]() ![]() |
![]() ![]() ![]() |
![]() ![]() ![]() ![]() |
![]() ![]() ![]() ![]() |
![]() |
![]() ![]() ![]() |
Дополнительная информация
2.Реферат.doc
Поточный вискозиметр единый пункт управления.
В ходе выполнения проекта был произведен подробный анализ объекта управления разработана структурная схема системы управления процессом производства жевательной резинки. Разработан алгоритм управления процессом производства жевательной резинки. На основании алгоритма управления разработана функциональная схема автоматизации процесса производства жевательной резинки. На ее основе выполнены схемы электрические принципиальные системы управления процессом производства жевательной резинки. Был произведен выбор технических средств автоматизации.
Приведено технико-экономическое обоснование проекта от внедрения автоматизации. Решены вопросы техники безопасности и охраны труда.
9.Схема автоматизации.dwg

Цех производства жевательной резинки
Экспликация оборудования
Шнек подачи сахарного песка
Сборник сахарного песка
Сборник основы жевательной резинки
Дозатор основы жевательной резинки
Смеситель с двумя S-образными шнеками
Насос перекачки продукта
Спецификация к схеме автоматизации
ТСМУ – 0552 – 80 – 0 100°С – 0
% - ГП – ТУ 4227-003-13282997-95
Mobrey Measurement (Solartron)
Тензометрические весы
Светодиоды: - с зеленой линзой - с красной линзой - с синей линзой
С503B-GAS (5мм) C503B-RAS (5мм) C503B-BAS (5мм)
Кнопки ручного управления
ABLF-22: - красная - зеленая
Переключатель режимов управления
ПК16-11С0102 (3 положения
Исполнительный механизм клапана
модуль аналогового ввода: 6ES7 431-7QH00-0AB0 (16 входов) модуль дискретного ввода: 6ES7 421-1BL01-0AA0 (32 входа) модуль дискретного вывода (24В): 6ES7 422-7BL00-0AB0 (32 выхода) модуль дискретного вывода (220В): 6ES7 422-1FH00-0AA0 (16 выходов)
10. Выбор технических средств автоматизации.docx
Датчик температуры ТСМУ – 0552 – 80 – 0 100°С – 025%
Термопреобразователи с унифицированным выходным сигналом предназначены для преобразования значения температуры различных (как нейтральных так и агрессивных) сред в унифицированный токовый выходной сигнал. Применяется в системах автоматического контроля и регулирования температуры.
Чувствительный элемент первичного термопреобразователя и встроенный в головку датчика измерительный преобразователь. ИП в виде герметичной «таблетки» преобразует измеряемую температуру в унифицированный токовый выходной сигнал что дает возможность построения систем АСУТП без применения дополнительных нормирующих преобразователей.
Диапазон измеряемых температур °С
Сигнализатор уровня ультразвуковой УЗС-207
Для сигнализации достижения верхнего и нижнего уровней в воронке формовочно-отсадочной машины глазури в приемнике для глазури глазури в распределительных коробках глазировочной машины используются ультразвуковые сигнализаторы уровня:
– АД101 – 100 – Н (для сигнализации достижения верхнего уровня);
– АД101 – 200 – Н (для сигнализации достижения нижнего уровня):
УЗС – 207 – модель прибора;
ОМ – климатическое исполнение: -30 – +50°С;
АД101 – тип датчика;
– расстояние от фланца датчика до номинальной линии срабатывания первого датчика;
0 - расстояние от фланца датчика до номинальной линии срабатывания второго датчика;
Н – вид сигнализации: на наличие для верхнего уровня;
Н – вид сигнализации: на наличие для датчика нижнего уровня.
Погрешность: ± 2 мм при вертикальной установке датчика что отвечает технологическим требованиям (± 5 мм).
Привод шибера - BELIMO NM230ASR
Номинальное напряжение
Диапазон номинального напряжения
Потребляемая мощность
Исполнительный механизм
Механизмы исполнительные электрические однооборотные фланцевые постоянной скорости МЭОФ предназначены для перемещения регулирующих органов в системах автоматического регулирования технологическими процессами в соответствии с командными сигналами автоматических регулирующих и управляющих устройств.
Основные технические характеристики:
Напряжение и частота питания:
для однофазной сети;
допустимое отклонение напряжения;
допустимое отклонение частоты.
0 В с частотой 50 Гц
Индуктивные датчики положения.
или 2 датчика положения выходного органа в виде изменения индуктивности
Реостатные датчики положения.
датчика положения выходного органа в виде изменения активного сопротивления
Токовыйдатчик с унифицированным сигналом.
20 мА (механизмы с токовым датчиком комплектуются блоком питания).
повторно-кратковременный с частыми пусками S4
Продолжительность включений.
до 25 % при нагрузке на выходном органе в пределах от номинальной противодействующей до 0.5 номинального значения сопутствующей
Максимальная частота включений.
0 в час при продолжительности включений до 25 %
При реверсировании интервал времени между выключением и включением на обратное направление.
Поточный вискозиметр Visconic 7829 Mobrey Measurement:
Вискозиметр 7829 предназначен для оперативного измерения вязкости в режиме реального времени и его можно устанавливать непосредственно в ёмкости или трубопроводы или же в специальные байпасные линии. Являясь поточным прибором Вискозиметр 7829 измеряет вязкость в реальных условиях процесса. Программное обеспечение ADView компании Solartron Mobrey позволяет если нужно конфигурировать вискозиметр 7829 с помощью протокола связи RS485.
Технические характеристики:
- диапазон измерений: 100-12500 сПз;
- абсолютная погрешн ость: ±70 сПз;
- напряжение питания: 20-28 В DС;
- выходной сигнал: аналоговый 4 20 мА.
Тензометрические весы SBA ТОКВЕС
Наибольший предел измерения т
Рабочий диапазон температур °С
- с зеленой линзой С503B-GAS (5мм);
- с красной линзой C503B-RAS (5мм);
- с синей линзой C503B-BAS (5мм).
Кнопки ручного управления ABLF-22
Кнопки ручного управления предназначены для оперативного управления магнитными пускателями контакторами и реле автоматики в электрических цепях переменного тока частотой 50Гц напряжением до 660В или постоянного тока напряжением до 400В.
Переключатель режимов управления ПК16-11С0102:
- стандартная ручка;
Контроллер Siemens Simatic S7-400:
Это модульный программируемый контроллер предназначенный для построения систем автоматизации средней и высокой степени сложности. Система ввода-вывода программируемого контроллера S7-400 может включать в свой состав две части: систему локального и систему распределенного ввода-вывода. Система локального ввода-вывода образуется модулями устанавливаемыми в монтажные стойки контроллера.
Центральный процессор: CPU 414-2 – для построения систем управления средней степени сложности с программами большого объема скоростным выполнением инструкций и интенсивным сетевым обменом данными.
Сигнальные модули предназначены для ввода и вывода дискретных и аналоговых сигналов контроллера. Они включают в свой состав:
- модули ввода дискретных сигналов SM 421;
- модули вывода дискретных сигналов SM 422;
- модули ввода аналоговых сигналов SM 431.
Сигнальные модули могут использоваться во всех модификациях программируемого контроллера SIMATIC S7-400.
Модули ввода дискретных сигналов 6ES7421-1BL01-0AA0 – 32 входа.
Модули ввода дискретных сигналов предназначены для преобразования входных дискретных сигналов контроллера в его внутренние логические сигналы. К входам модулей могут подключаться контактные и бесконтактные датчики.
Модули выпускаются в пластиковых корпусах. На их лицевых панелях установлены:
- зеленые светодиоды для индикации отказов или ошибок (в модулях с расширенным набором диагностических функций);
- разъем для установки фронтального соединителя закрытый защитной дверцей;
- защитная дверца на которую наносится маркировка входных цепей.
Модули вывода дискретных сигналов 6ES7422-7BL00-0AB0 (24В) – 32 выхода.
Модули вывода дискретных сигналов предназначены для преобразования внутренних логических сигналов контроллера в его выходные дискретные сигналы. К выходам модулей могут подключаться реле сигнальные лампы и т.д. Модули выпускаются в пластиковых корпусах. На их лицевых панелях установлены:
- зеленые светодиоды для индикации состояния выходных цепей;
- красный светодиод для индикации внутренних и внешних отказов и ошибок для индикации перегорания предохранителя отсутствия напряжения питания нагрузки;
- паз в защитной дверце для установки этикетки на которую наносится маркировка внешних цепей.
Модули вывода дискретных сигналов 6ES7422-1FH00-0AA0 (220В) – 16 выходов.
Модули вывода дискретных сигналов предназначены для преобразования внутренних логических сигналов контроллера в его выходные дискретные сигналы. К выходам модулей могут подключаться соленоидные вентили реле контакторы небольшие двигатели и т.д. Модули выпускаются в пластиковых корпусах. На их лицевых панелях установлены:
Модули ввода аналоговых сигналов 6ES7431-7QH00-0AB0 – 16 входов.
Модули ввода аналоговых сигналов предназначены для аналого-цифрового преобразования входных аналоговых сигналов контроллера и формирования цифровых величин используемых центральным процессором в процессе выполнения программы. К входам модулей могут подключаться датчики с унифицированными выходными сигналами напряжения или силы тока термопары термометры сопротивления.
Входной сигнал 4 20 мА.
5. Введение.docx
Жевательная резинка (жвачка)— особое кулинарное изделие которое состоит из несъедобной эластичной основы и различных вкусовых и ароматических добавок. В процессе употребления жевательная резинка практически не уменьшается в объеме но все наполнители постепенно растворяются после чего основа становится безвкусной и обычно выбрасывается. Из многих видов жвачки в качестве развлечения можно выдувать пузыри что в англоязычных странах дало ей еще одно название Bubble Gum (то есть что-то вроде «резина для пузырей»). В настоящее время везде можно встретить жующих людей. Жуют в транспорте жуют на занятиях и лекциях жуют дома жуют на работе жуют за рулём автомобиля. Ежедневно по телевидению мы наблюдаем уйму реклам жевательных резинок нас постоянно убеждают использовать жевательную резинку которая не только освежает дыхание но и укрепляет зубы.
Что только не жевали наши древние предки! Греки «чистили зубы» и «освежали дыхание» с помощью смолы мастикового дерева индейцы племени майя жевали высушенный сок гевеи (каучука) англичане – сок елейного дерева древнюю жвачку готовили также из сосновой смолы и пчелиного воска.
Промышленное производство жевательной резинки началось в середине XIX века в США. Первую попытку по изготовлению сосновой жвачки предприняли братья Куртис выпускавшие резинки «Американский флаг» «Сосновая магистраль». Однако популярность хвойной жвачки постепенно падала из-за присутствия в ней не удаленных из смолы примесей. Наибольшую известность приобрели парафиновые жвачки.
Первый патент на производство жевательной резинки был получен 28 декабря 1869 г. американцем Уильямом Финли Семилом. В патенте было написано: «Комбинация каучука с прочими компонентами в любых пропорциях для создания приемлемой жевательной резинки». Однако в итоге сам Семил ничего жевательного так и не произвел. Вероятно дети и взрослые так и остались бы без привычных сегодня резиновых пластиночек и подушечек если бы не экс-президент Мексики генерал Антонио Лопес Санта Анна который очень любил жевать каучук. На столь странную особенность генерала обратил внимание фотограф и по совместительству изобретатель Томас Адамс из штата Нью-Йорк. На собственной кухне Адамс сварил маленький кусочек каучука – прообраз современной резинки. Чуть позже он добавил в жвачку лакричный ароматизатор. Так появилась первая ароматизированная жвачка под названием «Black Jack». В 1871 г. Адамс запатентовал автомат для производства жвачки а с 1888 г. созданная им же жвачка «Tutti Frutti» стала продаваться из автоматов на перронах железнодорожных станций.
Говоря об истории жевательной резинки нельзя не сказать о возникновении компании Wrigley ставшей значимой фигурой на рынке еще в конце XIX в. С 1892 г. он начал торговать своей собственной резинкой с торговой маркой «Wrigley». Первые сорта ее не дошли до наших дней но уже в 1893 г. появились Juicy Fruit и Wrigley’s Spearmint. Так сбылась еще одна американская мечта и возникла старейшая из ныне существующих компаний – производителей жевательной резинки. Резинка от Ригли вскоре пошла на экспорт.
Еще одним представителем кондитерской промышленности занимающихся производством жевательной резинки является «Чупа Чупс». «Чупа Чупс» — испанская компания производящая карамель на палочке но так же в сферу их производства входит производство жевательной резинки «Big Babol». Основана в Испании в 1952 году Энрике Бернатом. Эскиз первоначального логотипа «Чупа Чупса» был нарисован Сальвадором Дали. В 1964 открыта вторая фабрика в Испании. В 1990 году открытие фабрик в Франции Мексике Бразилии Китай. В 1992 году «Чупа Чупс» приходит в Россию. В 1997 году запуск фабрики в России с одной линией. В 2006 году компания вошла в итальяно-нидерландский концерн производящий кондитерские изделия и жевательную резинку «Perfetti Van Melle» которая занимается производством карамели с начинкой «Аlpenliebe» жевательные конфеты «Fruittella» и жевательное драже «Mentos». В 2010 году на заводе насчитывается 6 линий выпускающих 95 видов различной карамели а также линии по производству безсахарной карамели «Sula» и жевательной резинки « Big Babol». С 1967 года по настоящее время карамель «Чупа Чупс» занимает ведущее место в мире по качеству выпускаемого продукта.
Главной составляющей жевательной резинки является так называемая резиновая основа. Однако это вовсе не та резина из которой делают покрышки для автомобилей или коврики для «мыши». В идеале резиновую основу должен составлять сок деревьев каучуконосов который под действием кислоты или вываривания превращается в мягкую но довольно упругую массу. Однако еще не выросло столько деревьев чтобы стало возможным использовать их в массовом производстве. Поэтому сегодня применяются синтетические резиновые основы. Резиновая основа обладает полезной особенностью - под воздействием температуры она размягчается. Именно поэтому приклеившуюся жевательную резинку легче отодрать намочив одежду горячей водой или хорошо ее отпарив.
Основными компонентами современной жевательной резинки являются:
жевательная основа содержание которой колеблется от 20 до 30%;
подсластители составляют до 60% жевательной резинки;
ароматизаторы отдушки или вкусовые добавки (порядка10%);
глазурирующие агенты;
незначительное количество жидкости.
Жевательной основой резинки являются натуральные латексы смолы парафин текстурирующие вещества (тальк карбонат кальция) за счет которых под воздействием имеющейся в полости рта температуры происходит размягчение жевательной резинки. Резиновая основа представляет собой носитель для остальных ингредиентов в то же время оставаясь нейтральной к организму человека в целом. В последние годы натуральные латексы вытесняются синтетическими так резиновую основу составляет прототип чикла но синтезированный химическим путем и являющийся не вулканизированной каучуковой цепочкой.
Подсластители входят в состав жевательной резинки для придания вкусовых свойств. В настоящее время в качестве подсластителей применяют массовые сахарозаменители и интенсивные подсластители. Из массовых сахарозаменителей в состав жевательных резинок обычно вводят: ксилит сорбитол маннитол мальтит. К интенсивным подсластителям выполняющим роль компенсации потери сахара относятся: сахарин аспартам ацесульфам К и др.
К вкусовым добавкам используемым в жевательных резинках относятся: мята обыкновенная мята перечная эвкалипт фруктовые композиции. Однако мятные компоненты предпочитают фруктовым отдушкам в связи с тем что некоторые из них до сих пор готовятся с добавлением сахаров предпочтение чаще всего отдается мятным компонентам. Таким образом для того чтобы не провоцировать потребителей и микроорганизмы полости рта предпочтение чаще всего отдается мятным компонентам.
Смягчающие вещества позволяют резинке долго сохранять эластичность. Это глицерин а также эмульгаторы природного происхождения: лецитин камеди (например гуммиарабик-смола некоторых видов акаций). Кроме того в резинку добавляют антиоксидантов по нормам принятым у нас может составлять 750 мгкг а на практике оно редко достигает 200 мгкг.
Для того чтобы сделать вкус и аромат жевательной резинки наверняка достоверным ее приходится подкрашивать. Ведь не может серо-белая резинка пахнуть клубникой! Красители для жевательной резинки тоже обязательно должны входить в международный список разрешенных и безвредных веществ. Этот список постоянно пополняется и перепроверяется.
13. Список использованных источников.doc
Балюбаш В.А. Данин В.Б. Стегаличев Ю.Г. Дипломное проектирование: Метод. указания по организации работы над дипломным проектом для студентов спец. 220301. – СПб.: СПбГУНиПТ 2007. – 37 с.
Патент №2033731 «Способ приготовления жевательной резинки»
Рабочая инструкция OOO «Чупа Чупс Рус» Производство жевательной резинки фруктовых вкусов.
Номенклатурный каталог продукции. Промышленная группа «Метран» Челябинск 1997. – 307 с.
Евдокимов А.А. Безопасность жизнедеятельности. Примеры расчетов: Пособие. – СПб.:СПбГУНиПТ 2007. – 72стр.
ПУЭ 86. Правила устройства электроустановок.
СНиП 23-05-95. Естественное и искусственное освещение.
СанПиН 2.2.4.548-96. Гигиенические требования к микроклимату производственных помещений.
ГОСТ 12.0.003-74 (1999) ССБТ. Опасные и вредные производственные факторы классификации.
ГОСТ 12.1.004-91 (1999) ССБТ. Пожарная безопасность. Общие требования.
ГОСТ 12.1.007-76 (1999) ССБТ. Вредные вещества. Классификация и общие требования безопасности.
Смирнов А.Т. Безопасность жизнедеятельности: Учебное пособие. – М.: Дрофа 2009. – 375 с.
ГОСТ 19.701-90. Блок-схемы алгоритмов программ данных и систем. Условные обозначения и правила выполнения.
Лаврищев И.Б. Кириков А.Ю. Разработка функциональных схем автоматизации при проектировании автоматизированных систем управления процессами пищевых производств: Метод. указания. – СПб.: СПбГУНиПТ 2002. – 51 с.
Лаврищев И.Б. Кириков А.Ю. Добряков В.А. Разработка принципиальных электрических схем управления процессами пищевых производств: Метод. указания. – СПб.: СПбГУНиПТ 2004. – 53 с.
9.Схема автоматизации.docx
Описание функциональной схемы автоматизации.
Изображенная в графической части функциональная схема автоматизации технологического процесса дозирования и перемешивания основных компонентов жевательной резинки выполнена развернутым способом с использованием контроллера.
В системе предусмотрен выбор режима управления. Для этого используются ключи выбора режима. Для каждого привода электродвигателя а также для исполнительных механизмов клапанов и заслонок предусматривается индивидуальный ключ. Ручное дистанционное управление применяется только при аварийных ситуациях. Штатным является автоматический режим.
При достижении предельно допустимого уровня в бункере сахарного песка с первичного преобразователя (поз. 1-1) установленного по месту сигнал поступает на вторичный прибор (поз. 1-3) и засвечивается сигнальная лампа HL2 с зеленой линзой также установленный по месту сигнал с которого идет на дискретный вход контроллера. С его релейного выхода подается сигнал на выключение двигателя М1 шнека I подающего сахар-песок в бункер II и засвечивается сигнальная лампа HL2. При выключении шнека с дискретного выхода контроллера подается сигнал и гаснет сигнальная лампа HL4 с зеленой линзой а при его включении – наоборот. Если уровень сахарного песка ниже нижнего то светится сигнальная лампа HL3 с красной линзой и не светится лампа HL2 с зеленой линзой.
При достижении предельно допустимого уровня в сборнике основы жевательной резинки с первичного преобразователя (поз. 2-1) установленного по месту сигнал поступает на вторичный прибор (поз. 2-3) и засвечивается сигнальная лампа HL8 с зеленой линзой также установленный по месту сигнал с которого идет на дискретный вход контроллера. С его релейного выхода подается сигнал на закрытие клапана К1 подающего основу в сборник IV и гаснет сигнальная лампа HL9 а при его включении – наоборот.
С релейного выхода контроллера осуществляется включение и выключение:
- двигателя М2 ворошителя; при его включении засвечивается лампа HL5 с зеленой линзой с дискретного выхода контроллера и гаснет при его отключении;
- двигателя М3 микромельницы при его включении засвечивается лампа HL6 с зеленой линзой с дискретного выхода контроллера и гаснет при его отключении;
- двигателя М4 насоса подачи патоки; при его включении засвечивается лампа HL16 с зеленой линзой с дискретного выхода контроллера и гаснет при его отключении
- двигателя М5 смесителя; при его включении засвечивается лампа HL16 с зеленой линзой с дискретного выхода контроллера и гаснет при его отключении;
Температура массы жевательной резинки в смесителе VII контролируется первичным преобразователем температуры (поз. 6-1) сигнал с которого поступает на аналоговый вход контроллера. С релейного выхода контроллера поступает сигнал на привод клапана подачи охлаждающей воды (поз. 6-2). Положение клапана подачи пара контролируется указателем %ХРО установленным на щите. При ручном режиме управление осуществляется путем нажатия кнопок SB43 (для уменьшения подачи воды) и SB44 (для увеличения подачи воды).
Текущее значение вязкости контролируется поточным вискозиметром (поз.18) сигнал с которого идет на аналоговый вход контроллера а с дискретного выхода контроллера – сигнал засвечивающий сигнальную лампу HL21 с красной линзой если значение выходит из допустимого диапазона; и гасящий лампу HL21 если значение вязкости вернулось в заданные границы.
7 Анализ объекта.docx
Вырабатываемая продукция
Предприятие специализируется на выпуске карамельных конфет. Карамель - кондитерское изделие полученное увариванием сахаро - паточного сиропа. Карамель приготовляют из одной карамельной массы или с различными начинками. В зависимости от рецептуры карамель может быть молочная витаминизированная лечебная глазированная и других видов.
Class а также жевательная резинка «Big Babol» и жевательные конфеты «Mentos».
Описание производства массы жевательной резинки
Сырье для приготовления массы жевательной резинки.
Сырьем для приготовления массы жевательной резинки являются сахарная пудра патока основа жевательной резинки вкусовые и ароматические добавки краситель. Все ингредиенты перемешиваются в специальной Mix-машине для приготовления массы жевательной резинки.
Сахар-песок хранится тарным способом в мешках на складе. Засыпается вручную в приемный бункер мельницы для помола сахара-песка.
Патока хранится в баках емкостью 35 т снабженных регулируемым электрическим обогревом. Установленная температура в паточном баке составляет 44 oС.
Внимание ! Запрещается изменение температуры нагрева паточных баков.
Основа жевательной резинки приходит в блоках и гранулах. Основа упакована в картонные короба покрытые изнутри воском и хранится на складе при комнатной температуре и относительной влажности не более 75%.
Вкусовые и ароматические добавки влагоудерживающий агент хранятся в заводской упаковке на складе сырья.
Этапы приготовления жевательной резинки.
Подготовка сырья к использованию.
Основа жевательной резинки освобождается от упаковки и вручную загружается в MIX – машину. В MIX – машине основа вымешивается до размягчения;
Патока подается в MIX – машину при помощи насоса;
Параллельно идет приготовление сахарной пудры. Сахарная пудра получается путем размола сахара-песка в мельнице. Для приготовления сахарной пудры на один замес жевательной резинки требуется два мешка сахара-песка. Полученная сахарная пудра порционно вручную засыпается в MIX – машину;
Пищевые кислоты если они предусмотрены рецептурой взвешиваются на весах и засыпаются в MIX – машину;
Глицерин ароматизатор и краситель отмеряются при помощи мерных стаканов и выливаются в MIX – машину.
Этапы приготовления начинки из жевательной резинки.
Масса жевательной резинки готовится в три этапа. Количество ингредиентов добавляемых поэтапно указано в таблице норм сырья на загрузку.
Основа жевательной резинки
Первый этап. Сначала загружается основа жевательной резинки. Блоки и гранулы основы жевательной резинки разбиваются о шнеки MIX – машины до размягчения в течение 5 минут;
Далее добавляется патока 12 часть глицерина 13 часть сахарной пудры и краситель. Продолжительность вымешивания жевательной резинки в течение первого этапа со всеми добавками - 10 минут;
Второй этап. Загружается остаток глицерина пищевой кислоты и 13 сахарной пудры. Продолжительность вымешивания жевательной резинки в течение второго этапа - 4 минуты;
Третий этап. Вносится ароматизатор и оставшаяся часть сахарной пудры. Продолжительность вымешивания жевательной резинки в течение третьего этапа – 5 минут;
Готовая масса выгружается при помощи насоса. Температура готовой массы жевательной резинки 50 ÷ 55°C.
Определение перечня контролируемых и регулируемых параметров.
В технологическом процессе приготовления жевательной резинки предполагается регулировать:
- уровень сахарного песка в бункере (во избежание пересыпания или недосыпа что может негативно повлиять на работу дозирующих устройств);
- уровень основы жевательной резинки в сборнике;
- уровень сахарного песка в дозаторе;
- уровень основы жевательной резинки в дозаторе;
(Примечание: данные параметры необходимо регулировать для обеспечения ритмичной работы линии.)
- температуру в смесителе (для поддержания температуры 50-55ºС);
Предусматривается регистрация следующих параметров:
- численное значение вязкости жевательной резинки (так как является показателем качества);
- температуры охлаждающей воды в смесителе
Осуществляется визуальный контроль:
- массы дозируемых компонентов (контроль соблюдения рецептуры);
- температуры в смесителе (для поддержания температуры 50-55ºС);
- температуры охлаждающей воды в рубашке смесителя (для осуществления дополнительного контроля);
- численного значения вязкости жевательной резинки (так как является показателем качества глазури);
- положение всех клапанов (для ручного поддержания заданной температуры);
Основным режимом работы системы является автоматический режим работы при котором оператор осуществляет только визуальный контроль параметров а все функции управления возлагаются на систему автоматики. При этом предусматривается резервный режим работы – ручной. Этот режим активируется в аварийной ситуации когда система автоматики не может справиться без вмешательства человека. Для осуществления этого режима установлены кнопки аварийного выключения по месту и кнопки аварийного регулирования на щите.
Автоматизация технологического процесса приготовления жевательной резинки позволит уменьшить себестоимость продукции за счет снижения затрат на заработную плату сотрудникам и снижения количества бракованной продукции повысить ее конкурентоспособность за счет повышения качества достигаемого путем более точного выдерживания технологических режимов.
Для управления технологическим процессом приготовления жевательной резинки предлагается локальная система автоматизации с возможностью передачи необходимой информации на диспетчерский уровень управления. Предполагается использование контроллера имеющего необходимое количество аналоговых и дискретных входов и выходов с возможностью связи по интерфейсу с верхним (диспетчерским) уровнем управления.
8 Алгоритм.docx
Описание блок-схемы алгоритма
В блоке 1 происходит ввод установок уровня температуры и времени.
В блоке 2 происходит включение электродвигателя М1 шнека подачи сахарного песка.
В блоке 3 проверяется достигнут ли нижний уровень в бункере сахарного песка. Если уровень не достигнут то осуществляется переход к блоку 2. Если уровень достигнут то осуществляется переход к блоку 4.
В блоке 4 происходит включение электродвигателя М2 ворошителя.
В блоке 5 проверяется достигнут ли уровень в дозаторе сахарного песка. Если уровень не достигнут то осуществляется переход к блоку 4. Если уровень достигнут то осуществляется переход к блоку 6.
В блоке 6 происходит выключение электродвигателя М2 ворошителя.
В блоке 7 проверяется достигнут ли верхний уровень в бункере сахарного песка. Если уровень не достигнут то осуществляется переход к блоку 2. Если уровень достигнут то осуществляется переход к блоку 8.
В блоке 8 происходит выключение электродвигателя М1 шнека подачи сахарного песка.
В блоке 9 подаётся сигнал на открытие клапана подачи основы жевательной резинки в сборник
В блоке 10 проверяется достигнут ли нижний уровень в сборнике основы жевательной резинки. Если уровень не достигнут то осуществляется переход к блоку 9. Если уровень достигнут то осуществляется переход к блоку 11.
В блоке 11 подаётся сигнал на открытие клапана подачи основы жевательной резинки в дозатор.
В блоке 12 проверяется достигнут ли уровень в дозаторе основы жевательной резинки. Если уровень не достигнут то осуществляется переход к блоку 9. Если уровень достигнут то осуществляется переход к блоку 13.
В блоке 13 подаётся сигнал на закрытие клапана подачи основы жевательной резинки в дозатор.
В блоке 14 проверяется достигнут ли верхний уровень в сборнике основы жевательной резинки. Если уровень не достигнут то осуществляется переход к блоку 9. Если уровень достигнут то осуществляется переход к блоку 15.
В блоке 15 подаётся сигнал на закрытие клапана подачи основы жевательной резинки в сборник.
В блоке 16 подается сигнал на открытие клапана K3 подачи основы. Происходит включение электродвигателя М5 мешалки смесителя и запускается отсчет времени.
В блоке 17 проверяется прошел ли отсчет времени. Если отсчет не прошел то осуществляется переход к блоку 15. Если отсчет прошел то осуществляется переход к блоку 18.
В блоке 18 происходит выключение электродвигателя М5. Подается сигнал на закрытие клапана K3 подачи основы Происходит включение электродвигателя М4 подачи патоки и М3 микромельницы.
В блоке 19 проверяется достигнут ли нижний уровень. Если уровень не достигнут то осуществляется переход к блоку 17. Если уровень достигнут то осуществляется переход к блоку 20.
В блоке 20 происходит выключение электродвигателя М4 подачи патоки и М3 микромельницы. Происходит включение электродвигателя М5 мешалки смесителя.
В блоке 21 запускается отсчет времени.
В блоке 22 осуществляется сравнение текущего значения температуры полученного от датчика с заданным значением. Если текущего значения температуры равно заданному то осуществляется переход к блоку 24. Если текущего значения температуры не равно заданному то осуществляется переход к блоку 23 в котором подается сигнал на открытие клапана подачи охлаждающей воды; затем переход к блоку 24.
В блоке 24 проверяется прошел ли отсчет времени. Если отсчет не прошел то осуществляется переход к блоку 21. Если отсчет прошел то осуществляется переход к блоку 25.
В блоке 25 подается сигнал на закрытие клапана подачи охлаждающей воды.
В блоке 26 происходит выключение электродвигателя М5. Происходит включение электродвигателя М3 микромельницы.
В блоке 27 проверяется достигнут ли средний уровень. Если уровень не достигнут то осуществляется переход к блоку 26. Если уровень достигнут то осуществляется переход к блоку 28.
В блоке 28 происходит выключение электродвигателя М3 микромельницы включение электродвигателя М5 мешалки смесителя и запускается отсчет времени.
В блоке 29 осуществляется сравнение текущего значения температуры полученного от датчика с заданным значением. Если текущего значения температуры равно заданному то осуществляется переход к блоку 31. Если текущего значения температуры не равно заданному то осуществляется переход к блоку 30 в котором подается сигнал на открытие клапана подачи охлаждающей воды; затем переход к блоку 314.
В блоке 31 проверяется прошел ли отсчет времени. Если отсчет не прошел то осуществляется переход к блоку 28. Если отсчет прошел то осуществляется переход к блоку 32.
В блоке 32 подается сигнал на закрытие клапана подачи охлаждающей воды.
В блоке 33 происходит выключение электродвигателя М5 мешалки смесителя. Происходит включение электродвигателя М3 микромельницы.
В блоке 34 проверяется достигнут ли верхний уровень. Если уровень не достигнут то осуществляется переход к блоку 33. Если уровень достигнут то осуществляется переход к блоку 35.
В блоке 35 происходит выключение электродвигателя М3 микромельницы включение электродвигателя М5 мешалки смесителя и запускается отсчет времени.
В блоке 36 осуществляется сравнение текущего значения температуры полученного от датчика с заданным значением. Если текущего значения температуры равно заданному то осуществляется переход к блоку 38. Если текущего значения температуры не равно заданному то осуществляется переход к блоку 37 в котором подается сигнал на открытие клапана подачи охлаждающей воды; затем переход к блоку 38.
В блоке 38 проверяется прошел ли отсчет времени. Если отсчет не прошел то осуществляется переход к блоку 35. Если отсчет прошел то осуществляется переход к блоку 39.
В блоке 39 подается сигнал на закрытие клапана подачи охлаждающей воды.
В блоке 40 происходит выключение электродвигателя М5 мешалки смесителя.
В блоке 41 происходит включение электродвигателя М6 перекачки продукта.
В блоке 42 проверяется достигнут ли нижний уровень смесителе. Если уровень не достигнут то осуществляется переход к блоку 41. Если уровень достигнут то осуществляется переход к блоку 43.
В блоке 43 происходит выключение электродвигателя М6 перекачки продукта.
В блоке 44 выдается запрос продолжить. Если необходимо продолжить то осуществляется переход к блоку 2. Если необходимо прекратить работу то переходим к блоку «Остановить».
Таблица информационного обеспечения
Температуры в смесителе
Время сбивания основы
Время сбивания на 1 этапе
Время сбивания на 2 этапе
Время сбивания на 3 этапе
Шнека подачи сахарного песка
=1 - двигатель включен;
=0 - двигатель выключен.
Подачи основы жевательной резинки в сборник
= 1 - сигнал на открытие клапана;
=0 - сигнал на закрытие клапана
Подачи основы жевательной резинки в дозатор
Подачи основы жевательной резинки в смеситель
Подачи охлаждающей воды
4.Содержание.doc
Раздел I. Введение 6
Раздел II. Технико-экономическое обоснование проекта автоматизации процесса производства жевательной резинки .12
Раздел III. Анализ объекта управления ..15
Раздел IV. Разработка алгоритма управления процессом производства жевательной резинки . .21
Раздел V. Разработка схемы автоматизации процесса производства жевательной резинки ..27
Раздел VI. Выбор технических средств автоматизации процесса производства жевательной резинки ..30
Раздел VII. Разработка схем электрических принципиальных автоматизации процесса производства жевательной резинки 38
Раздел VIII. Разработка мероприятий по охране труда и технике безопасности 42
Список использованных источников 49ГРАФИЧЕСКАЯ ЧАСТЬ:
Структурная схема системы автоматизации технологического процесса производства жевательной резинки
Параметрическая схема системы автоматизации технологического процесса производства жевательной резинки
Блок-схема алгоритма управления процессом производства жевательной резинки
Схема автоматизации процесса производства жевательной резинки
Принципиальные электрические схемы автоматизации процесса производства жевательной резинки
6. ТЭО.docx
Жевательная резинка наиболее распространенная из всех кондитерских изделий. Темпы ее использования неумолимо растут в настоящее время везде можно встретить жующих людей. Жуют в транспорте жуют на занятиях и лекциях жуют дома жуют на работе жуют за рулём автомобиля. По данным общероссийского Омнибуса Исследовательского холдинга «Ромир» жевательную резинку в большей или меньшей степени жуют почти все социальные группы населения. Пол возраст уровень дохода и образования россиян на востребованность популярного продукта практически не влияют а его потребителями являются 82% граждан. Из них 89% жуют жвачку чаще чем 1 раз в неделю. Если в России будет развиваться малый бизнес вполне вероятны увеличения объемов ее потребления как российского так и импортного производства. Среди крупных фабрик по ее производству: «Wrigley» (Orbit и Eclipse) приходится 49% «Cadbury» (Dirol и Stimorol) - 45% и другие.
Маркетинговое агентство ROIF Expert подготовило аналитический обзор рынка жевательной резинки. В первом квартале 2010 года было выявлено значительное увеличение объемов производства продукции однако аналитики не связывают это с ростом потребления.
В целом статистические данные показывают что динамика объемов производства жевательной резинки в России в 2006-2011 гг. оставалась положительной со средним темпом роста в 31%. В противовес производству Россия снижает объем экспортных и импортных поставок жевательной резинки. В настоящее время внешнеторговые операции не оказывают существенного влияния на рынок.
- единого пункта управления процессом приготовления- нет;
- управление осуществляется с пультов установленных по месту для каждого агрегата отдельно;
- дозирование отдельных компонентов ведется в ручную;
- вязкость глазури измеряют лабораторным способом.
Автоматизация процесса производства жевательной резинки предусматривает создание системы управления реализованной на базе единого пункта оператора. Управление технологическим процессом в этом случае будет осуществляться контроллером для всего процесса.
Кроме того предполагается заменить лабораторный метод определения вязкости жевательной резинки поточным вискозиметром.
Такая автоматизация процесса производства жевательной резинки позволит сократить численность персонала за счет отказа от местных пультов управления и лабораторного измерения вязкости.
3. Задание на квалификационную работу.doc
ВЫСШЕГО ПРОФЕССИОНАЛЬНОГО ОБРАЗОВАНИЯ
«Санкт-Петербургский государственный университет
низкотемпературных и пищевых технологий»
НА ВЫПУСКНУЮ КВАЛИФИКАЦИОННУЮ РАБОТУ
( Фамилия инициалы )
( Фамилияинициалы место работы должность )
Техническое задание и исходные данные к работе
Раздел II. Технико-экономическое обоснование проекта автоматизации процесса производства жевательной резинки
Раздел III. Анализ объекта управления
Раздел IV. Разработка алгоритма управления процессом производства жевательной резинки
Раздел V. Разработка схемы автоматизации процесса производства жевательной резинки
Раздел VI. Выбор технических средств автоматизации процесса производства жевательной резинки
Раздел VII. Разработка схем электрических принципиальных автоматизации процесса производства жевательной резинки
Раздел VIII. Разработка мероприятий по охране труда и технике безопасности
Структурная схема системы автоматизации технологического процесса производства жевательной резинки
Параметрическая схема системы автоматизации технологического процесса производства жевательной резинки
Блок-схема алгоритма управления процессом производства жевательной резинки
Схема автоматизации процесса производства жевательной резинки
Принципиальные электрические схемы автоматизации процесса производства жевательной резинки
Исходные материалы и пособия
Патент №2033731 «Способ приготовления жевательной резинки»
Рабочая инструкция OOO «Чупа Чупс Рус» Производство жевательной резинки фруктовых вкусов.
Консультанты по работе с указанием относящихся к ним разделов работы
Безопасность жизнедеятельности
Наименование этапов выпускной квалификационной работы
Срок выполнения этапов работы
0.Рецензия.doc
ГОСУДАРСТВЕННОГО ОБРАЗОВАТЕЛЬНОГО УЧРЕЖДЕНИЯ
ВЫСШЕГО ПРОФЕССИОНАЛЬНОГО ОБРАЗОВАНИЯ
«САНКТ-ПЕТЕРБУРГСКИЙ ГОСУДАРСТВЕННЫЙ УНИВЕРСИТЕТ
НИЗКОТЕМПЕРАТУРНЫХ И ПИЩЕВЫХ ТЕХНОЛОГИЙ»
Фамилия имя отчество Воронко Павел Павлович -5
Наименование темы дипломного проекта (работы)
Автоматизация процесса производства жевательной резинки -
Квалификационная работа Воронко П.П. посвящена актуальной теме – совершенствованию системы управления процессом производства жевательной резинки.
В структурной схеме проекта приведены все основные компоненты предлагаемой системы управления а на основании анализа технологического объекта управления был разработан алгоритм управления учитывающий все особенности технологического процесса и имеющего технологического оборудования.
На основании алгоритма управления была разработана функциональная схема автоматизации позволяющая вести управление процессом в оптимальном режиме и обеспечивать стабильно высокое качество продукции. Это достигается тем что все параметры технологического процесса контролируются автоматически в течение всех операций производства шоколадной глазури. В качестве устройств управления и регулирования используются современные высокоточные технические средства. Применение поточного вискозиметра позволяет улучшить качество продукции и уменьшить процент брака а использование единого щита управления процессом позволяет сократить число местных пультов управления и обслуживающего их персонала. В схеме предусмотрена возможность перехода с автоматического на операторный режим управления что снижает вероятность возникновения аварийных ситуаций.
Практическая ценность данного проекта заключается в разработанных принципиальных электрических схемах системы управления.
Квалификационная работа состоящая из пояснительной записки и графического материала выполнен в соответствии с заданием на проектирование на высоком техническом уровне а его автор Воронко П.П. достойна присвоения ему квалификации бакалавра.
Фамилия имя отчество место работы и должность рецензента
Ф.И.О. рецензента Колосов Михаил
12. БЖД.docx
Задачей охраны труда является снижение до минимума вероятности поражения или заболевания работающего создание необходимых условий труда для работы.
В данном дипломном проекте рассматривается процесс производства жевательной резинки. Разрабатываемая система автоматизации процесса сбивания жевательной массы должна обеспечивать безопасные условия труда и стабильность работы оборудования. В ходе внедрения средств автоматизации появляется возможность осуществления процесса производства быстрее качественнее и с наименьшим вмешательством обслуживающего персонала что обеспечивает безопасную работу с минимальным использованием физического труда. Для этого предполагается заменить лабораторный метод измерения вязкости поточным вискозиметром что с точки зрения охраны труда исключит вероятность получения травм при отборе проб лаборантом. В разрабатываемой системе автоматики предложен ряд блокирующих устройств обеспечивающих безопасную работу персонала и предотвращающих непреднамеренную порчу оборудования. Также система автоматизации позволяет частично устранить физическую работу на участке. Путем введения мероприятий совершенствуется система управления процессом производства шоколадной глазури путем перехода от индивидуальных пультов управления за которыми обязательно стоял оператор к локальной системе управления на базе контроллера для которого достаточно одного оператора.
Анализ опасных производственных факторов.
В данном дипломном проекте рассматривается цех приготовления жевательной массы при котором наибольшую опасность как для обслуживающего персонала так и для потребителей представляет мойка оборудования. Оборудование моют 5-8% раствором соляной кислоты. При этом вероятно попадание паров в воздух рабочей зоны где предельно допустимая концентрация (ПДК) паров соляной кислоты - 5 мгм3 класс опасности - 2 (вещества- высокоопасные). Кроме того соляная кислотатоксична вызывает сильные ожоги слизистых оболочек удушье и разрушает зубы.
Затем кислоту нейтрализуют щелочным раствором после чего тщательно ополаскивают. Оборудование на данной технологической линии имеет сложную конструкцию потому нельзя исключать вероятность того что не все труднодоступные места будут промыты как от химикатов так и остатков продукта. Отсюда может возникнуть химическое и бактериальное заражение продукта.
При производстве шоколадной глазури используется такое оборудование как сборники смеситель снабженные мешалками а также микромельница для получения сахарной пудры. При недостаточно правильной сборке мешалки и валки могут цеплять за корпуса аппаратов снимая металлические частицы которые непременно попадут в продукт. Это неизбежно приводит к механическому заражению продукта.
Производство патоки в жидком виде то есть при температуре 44ºС поэтому сборники обогреваются электрическим током; сбивание происходит при температуре 50-55ºС. Вследствие таких высокотемпературных технологических режимов возможны термические ожоги персонала.
Для питания электродвигателей используется трехфазный ток 380В. Электродвигатели имеют мощность лежащую в пределах от 12кВт (насосы) до 55 кВт (мешалки).
Цех производства жевательной массы относится к помещениям с повышенной опасностью характеризующимся наличием высокой температуры (более 35ºС). [1]
Анализ пожаро- и взрывоопасности.
Цеху производства жевательной резинки на фабрике «Chupa Chups» присвоен класс пожаро- взрывоопасности П-IIа как помещению где располагаются твердые горючие вещества такие как ветошь и смазочные материалы которые могут самовоспламениться при нарушении технологического режима. Кроме того потенциальными источниками огня может стать искрение контактных разъемов в электроприборах нормального исполнения а также воспламенение проводки при коротком замыкании.
В цехе располагается громоздкое оборудование транспортеры и подвесные пути которые усугубляют пожарную опасность для обслуживающего персонала. Помимо этого на путях эвакуации складируют тару и готовую продукцию.
Фабрика «Chupa Chups» работает в две смены по 12 часов с 7.00 до19.00 и с 19.00 до 7.00 . При этом оборудование находится в постоянно включённом состоянии поэтому возможность возникновения пожара в присутствие персонала минимальна.
Анализ вредных производственных факторов.
Источниками поступлений в атмосферу цеха теплоты являются электродвигатели технологических аппаратов трубопроводы горячей воды паропроводы и рубашки аппаратов.
Источниками вибрации и шума являются электродвигатели насосов мешалок валков мельницы транспортеров. По характеру воздействия - вибрация общая категории 3а на постоянных рабочих местах производственных помещений предприятий. Спектр шума при работе данного оборудования - сплошной. Уровень шума на рабочем месте регламентирует ПС-80 и не превышает допустимых норм ( 80 дБ).
Органолептический контроль качества продукции осуществляется в соответствии с планом контроля качества.
Зрительные работы относится к разряду 7 (общее наблюдение за ходом производственного процесса). Тяжесть работ в цеху - легкие физические работы (категория Iб). Вредные пары и пыль отсутствуют.
Мероприятия по обеспечению безопасных условий труда.
Для устранения возможности химического и бактериального заражений рекомендуется контроль качества мойки применение безразборной CIP-мойки проведение регулярной дезинфекции технологических аппаратов.
Во избежание механического заражения продукта целесообразно производить контроль качества сборки аппаратов и допускать к сборке только квалифицированный персонал.
Применение тепловой изоляции может устранить возможность термического ожога у обслуживающего персонала.
Мероприятия по пожарной профилактике.
Пожарная профилактика включает в себя профилактику возгораний мероприятия по локализации возникающих очагов пожара мероприятия по эвакуации людей при пожаре пожарную сигнализацию и связь с пожарной охраной технические средства пожаротушения.
Профилактика возгораний базируется на поддержании температуры горючих смесей ниже температуры воспламенения недопущения инициирования процесса горения или искрения.
Мероприятия позволяющие реализовать эти принципы:
- защита электрических сетей от воспламенения при перегрузке и коротком замыкании;
- соблюдение режима смазки;
- применение смазочных материалов с температурой воспламенения более 170ºС;
Мероприятия направленные на локализацию очагов пожара:
- создание надежных преград на пути распространения огня(огнестойких стен перекрытий покрытий дверных тамбуров водяных завес);
- складирование паллетов и картонных коробок в отдельном помещении;
- использование дренчерных систем локализации огня и спринклерных (тушение).
Мероприятия для обеспечения своевременной эвакуации людей при пожаре:
-размещение технологического оборудования с обеспечением проходов для людей и проезда цехового транспорта;
- размещение цехового оборудования вблизи строительных конструкций здания;
- размещение трубопроводов и электрокоммуникаций так чтобы они не мешали свободному перемещению (вертикальные участки – вблизи строительных конструкций здания горизонтальные – выше 25м или заглублены ниже уровня пола);
- обеспечение достаточного количества эвакуационных выходов;
- использование негорючих материалов для дверей на путях эвакуации;
- обеспечение аварийного освещения на путях эвакуации;
- поступление свежего воздуха в помещение и удаление дымовых газов при эвакуации людей;
- использование сигнализации о пожаре и необходимости эвакуации;
- применение индивидуальных средств защиты. [6]
В комплект первичных средств пожаротушения в производственном помещении входят углекислотные огнетушители (ОУ-2 ОУ-8) мешки с песком совковые лопаты топоры.
В помещении цеха предусмотрены планы эвакуации персонала на случай пожара. В цехе размещены пожарные щиты и огнетушители в специально отведённых для них местах.
Мероприятия по обеспечению безвредных условий труда.
Размещение постоянных рабочих мест должно отвечать санитарным требованиям к производственным помещениям к которым относятся обеспечение чистоты воздуха рабочей зоны и комфортных метеоусловий соблюдение установленных норм вибрации интенсивности электромагнитных полей и шума. Для этого рекомендуется изоляция и экранирование горячих поверхностей устройство общеобменной вентиляции отопления кондиционирования воздуха. Этот комплекс мер сможет обеспечить эффективное и экономичное достижение требуемых норм.
Нормальные условия зрительной работы обеспечиваются устройством общего равномерного освещения.
Для снижения общих вибраций характеризующихся широким спектром частот предполагается использовать автономные фундаменты виброгасящие массивные основания виброизоляцию.
Для снижения шума на постоянном рабочем месте предлагается размещать шумное оборудование в отдельных помещениях разделять источники шума и постоянное рабочее место звукоизолирующими перегородками размещать рабочие места далеко от источников шума использовать звукопоглощающую облицовку для уменьшения отраженного шума.
Рабочее место оператора подвергается эргономической проработке.
Предметом проработки являются:
- форма и размеры информационных щитов;
- расстояние и взаимное расположение приборов индикаторов;
- интенсивность выполняемых операций;
- форма и скорость поступления информации;
- положение тела рабочего;
- освещение рабочего места.
Речь для защиты.doc
Вашему вниманию предоставляется доклад на тему:
Автоматизация процесса производства жевательной резинки.
Актуальность выбранной темы определяется темпами использования жевательной резинки которые неумолимо растут поэтому производители стараются выпускать как можно больше жевательной резинки. Жевательная резинка (жвачка)— особое кондитерское изделие которое состоит из несъедобной эластичной основы и различных вкусовых и ароматических добавок. В нашем городе основными производителями являются кондитерские фабрики «Чупа Чупс Рус» и «Wrigley»
В данном проекте технология производства жевательной резинки рассмотрена на примере фабрики OOO «Чупа Чупс Рус». «Чупа Чупс» — испанская компания производящая карамель на палочке но так же в сферу их производства входит производство жевательной резинки.
В процессе анализа существующей системы были выявлены следующие недостатки:
Отсутствие единого пункта управления процессом приготовления жевательной резинки
Что повышается надежность системы
Измерение вязкости жевательной резинки лабораторным способом путем измерения вязкости в потоке что приводит к повышению качества готового продукта.
Сырьем для приготовления массы жевательной резинки являются сахарная пудра патока основа жевательной резинки вкусовые и ароматические добавки красители. Все ингредиенты перемешиваются в специальной Mix-машине для приготовления массы жевательной резинки. Основными этапами производства жевательной резинки являются:
Первый этап. Сначала загружается основа жевательной резинки. Блоки и гранулы основы жевательной резинки разбиваются о шнеки MIX – машины до размягчения в течение 5 минут. Далее добавляется патока 12 часть глицерина 13 часть сахарной пудры и краситель. Продолжительность вымешивания жевательной резинки в течение первого этапа со всеми добавками - 10 минут;
Второй этап. Загружается остаток глицерина пищевой кислоты и 13 сахарной пудры. Продолжительность вымешивания жевательной резинки в течение второго этапа - 4 минуты;
Третий этап. Вносится ароматизатор и оставшаяся часть сахарной пудры. Продолжительность вымешивания жевательной резинки в течение третьего этапа – 5 минут; Готовая масса выгружается при помощи насоса. Температура готовой массы жевательной резинки 50 ÷ 55°C.
По результатам анализа технологического объекта управления был разработан алгоритм управления блок-схема которого приведена на листе 3.
На основании алгоритма управления была разработана СА представленная на листе 4
Изображенная в графической части функциональная схема автоматизации технологического процесса приготовления шоколадной глазури выполнена развернутым способом с использованием контроллера.
При достижении предельно допустимого уровня в бункере сахарного песка с первичного преобразователя (поз. 1-1) установленного по месту сигнал поступает на вторичный прибор (поз. 1-3) и засвечивается сигнальная лампа HL2 с зеленой линзой также установленный по месту сигнал с которого идет на дискретный вход контроллера. С его релейного выхода подается сигнал на выключение двигателя М1 шнека I подающего сахар-песок в бункер II и засвечивается сигнальная лампа HL2. При выключении шнека с дискретного выхода контроллера подается сигнал и гаснет сигнальная лампа HL4 с зеленой линзой а при его включении – наоборот. Если уровень сахарного песка ниже нижнего то светится сигнальная лампа HL3 с красной линзой и не светится лампа HL2 с зеленой линзой.
При достижении предельно допустимого уровня в сборнике основы жевательной резинки с первичного преобразователя (поз. 2-1) установленного по месту сигнал поступает на вторичный прибор (поз. 2-3) и засвечивается сигнальная лампа HL8 с зеленой линзой также установленный по месту сигнал с которого идет на дискретный вход контроллера. С его релейного выхода подается сигнал на закрытие клапана К1 подающего основу в сборник IV и гаснет сигнальная лампа HL9 а при его включении – наоборот.
С релейного выхода контроллера осуществляется включение и выключение:
- двигателя М2 ворошителя; при его включении засвечивается лампа HL5 с зеленой линзой с дискретного выхода контроллера и гаснет при его отключении;
- двигателя М3 микромельницы при его включении засвечивается лампа HL6 с зеленой линзой с дискретного выхода контроллера и гаснет при его отключении;
- двигателя М4 насоса подачи патоки; при его включении засвечивается лампа HL16 с зеленой линзой с дискретного выхода контроллера и гаснет при его отключении
- двигателя М5 смесителя; при его включении засвечивается лампа HL16 с зеленой линзой с дискретного выхода контроллера и гаснет при его отключении;
Температура массы жевательной резинки в смесителе VII контролируется первичным преобразователем температуры (поз. 6-1) сигнал с которого поступает на аналоговый вход контроллера. С релейного выхода контроллера поступает сигнал на привод клапана подачи охлаждающей воды (поз. 6-2). Положение клапана подачи пара контролируется указателем %ХРО установленным на щите. При ручном режиме управление осуществляется путем нажатия кнопок SB43 (для уменьшения подачи воды) и SB44 (для увеличения подачи воды).
Текущее значение вязкости контролируется поточным вискозиметром (поз.18) сигнал с которого идет на аналоговый вход контроллера а с дискретного выхода контроллера – сигнал засвечивающий сигнальную лампу HL21 с красной линзой если значение выходит из допустимого диапазона; и гасящий лампу HL21 если значение вязкости вернулось в заданные границы.
На основании СА были разработаны схемы принципиальные электрические представленные на листах 5 – 7. В этих схемах предусмотрена защита электродвигателей производственных механизмов от токов короткого замыкания (с помощью автоматических выключателей QF) и от токов перегрузки (с помощью тепловых реле КК) а также защита цепей измерения сигнализации и управления при помощи входного предохранителя FU. Выбор режима управления осуществляется при помощи ключа SA1 – SA11. При их нейтральном положении отключаются все производственные механизмы. А также предусматривается функция предварительного опробования сигнальных светодиодов. Диоды VD1 – VD22 осуществляют развязку цепи сигнальных ламп.
В процессе разработки квалификационной работы была разработана система в которой
Основным режимом работы системы является автоматический режим при котором оператор осуществляет только визуальный контроль параметров а все функции управления возлагаются на систему автоматики. При этом предусматривается резервный режим работы – ручной. В целом статистические данные показывают что динамика объемов производства жевательной резинки в России в последние годы оставалась положительной поэтому целью данной работы является совершенствование системы управления уже существующей технологической линии. Для управления технологическим процессом приготовления жевательной резинки предлагается локальная система автоматизации с возможностью передачи необходимой информации на диспетчерский уровень управления.
Доклад окончен спасибо за внимание!
1.Титульник.docx
Федеральное государственное бюджетное образовательное учреждение высшего профессионального образования
«Санкт-Петербургский государственный
университет низкотемпературных и пищевых технологий»
ФакультетПищевой инженерии и автоматизации
Направление220200.62- «Автоматизация и управление»
КафедраАвтоматика и автоматизация производственных процессовГруппа4А
Пояснительная записка
к выпускной квалификационной работе
Санкт-Петербург 2012 г.
11. Разработка схем электрических принципиальных автоматизации процесса производства.dwg

Контроллер SIMATIC S7 - 400
AI (4 20мА) 6ES7 431-7QH00-0AB0
АиАПП - 12 - КР - 175
Цех производства жевательной резинки
Управление клапаном подачи пара в рубашку сборника какао-тертого: - автоматическое - ручное
Вязкость глазури после темперирования
Уровень сахарного песка в бункере: -верхний;
Управляющий сигнал на привод шнека
Управляющий сигнал на открытие клапана подачи охлаждающей воды в рубашку 1 секции темперирующей машины
Уровень сахарного песка в бункере ниже нижнего
Сигнализация нижнего уровня в сборнике основы
Сигнализация положения заслонки подачи сахарной пудры в смеситель
Управление приводом шнека: - ручное -автоматическое
Управление приводом ворошителя: - ручное -автоматическое
Управление приводом микромельницы: - ручное -автоматическое
Управление приводом подачи патоки: - ручное -автоматическое
Примечание: на схеме показано подключение электродвигателя М1; подключение электродвигателей М2-М6 - аналогично.
Управление приводом мешалки смесителя: - ручное -автоматическое
Управление приводом насоса перекачки продукта: - ручное -автоматическое
Уровень сахарного песка в бункере: -верхний; -нижний.
Управление заслонкой подачи основы жевательной резинки в сборник: - ручное -автоматическое
Управление заслонкой подачи основы жевательной резинки в дозатор: - ручное -автоматическое
Управление заслонкой подачи основы жевательной резинки в смеситель: - ручное -автоматическое
Управление заслонкой подачи сахарной пудры в смеситель: - ручное -автоматическое
Управление клапаном подачи охлаждающей воды в рубашке смесителя: - ручное -автоматическое
Управляющий сигнал на привод ворошителя
Управляющий сигнал на привод микромельницы
Управляющий сигнал на привод подачи патоки
Управляющий сигнал на привод смесителя
Управляющий сигнал на привод насоса перекачки продукта
Управляющий сигнал на открытие заслонки подачи основы жевательной резинки в сборник
Управляющий сигнал на закрытие заслонки подачи основы жевательной резинки в сборник
Управляющий сигнал на открытие заслонки подачи основы жевательной резинки в дозатор
Управляющий сигнал на закрытие заслонки подачи основы жевательной резинки в дозатор
Управляющий сигнал на открытие заслонки подачи основы жевательной резинки в смеситель
Управляющий сигнал на закрытие заслонки подачи основы жевательной резинки в смеситель
Управляющий сигнал на открытие заслонки подачи сахарной пудры в смеситель
Управляющий сигнал на закрытие заслонки подачи сахарной пудры в смеситель
Управляющий сигнал на открытие клапана охлаждающей воды в рубашку смесителя
Управляющий сигнал на закрытие клапана охлаждающей воды в рубашку смесителя
Измерение температуры жевательной массы
Измерение вязкости жевательной массы
Уровень достиг верхнего уровня в бункере сахарного песка
Уровень достиг нижнего уровня в бункере сахарного песка
Уровень достиг верхнего уровня в сборнике основы
Уровень достиг нижнего уровня уровня в сборнике основы
Уровень достиг верхнего уровня в дозаторе сахарного песка
Уровень достиг верхнего уровня в дозаторе основы
Сигнализация работы щита
Сигнализация верхнего уровня в бункере сахарного песка
Сигнализация нижнего уровня в бункере сахарного песка
Сигнализация работы работы шнека
Сигнализация работы работы ворошителя
Сигнализация работы работы мельницы
Сигнализация верхнего уровня в дозаторе сахарного песка
Сигнализация положения заслонки подачи основы в сборник
Сигнализация верхнего уровня в дозаторе основы
Сигнализация положения заслонки подачи основы в дозатор
Сигнализация положения заслонки подачи основы в смеситель
Сигнализация готовности к первому этапу сбивания
Сигнализация готовности к второму этапу сбивания
Сигнализация готовности к третьему этапу сбивания
Сигнализация работы работы насоса подачи патоки
Сигнализация работы работы смесителя
Сигнализация положения клапана подачи воды в рубашку
Сигнализация работы работы насоса перекачки продукта
Сигнализация выхода из пределов вязкости
Сигнализация верхнего уровня в сборнике основы
Схема принципиальная электрическая
1.Технологическая схема.dwg

Смеситель с двумя S-образными шнеками
Дозатор основы жевательной резинки
Насос перекачки продукта
11. Разработка схем электрических принципиальных автоматизации процесса.docx
Описание принципиальной электрической схемы автоматизации
технологического процесса производства жеваетлной резинки.
Кнопкой SB26 осуществляется проверка работоспособности сигнальных ламп. При нажатии этой кнопки ток проходит через диодную развязку и засвечивает все лампы. При отжатии кнопки все лампы гаснут. Эта проверка позволяет до начала работы технологической линии заменить отказавшие лампы.
Ключи SA имеют три режима: автоматический «А» ручной «Р» и нейтральный «0». При выключенной технологической линии ключи находятся в нейтральном режиме. Если ключ установить в положение «А» то всей системой будет управлять контроллер. Если же ключ установить в положение «Р» то включение выключение агрегатов и поддержание необходимых температур осуществляется вручную путем нажатия соответствующих кнопок SB.
Электродвигатели М1 – М20 питаются трехфазным переменным током напряжением 380В маркировка фаз ABC. В цепь двигателей включены автоматический выключатель QF1 – QF20 контакты магнитных пускателей КМ1 – КМ20 нагревательные элементы трехфазных тепловых реле КК1 – КК20 соответственно.
Питание системы осуществляется от фазы С1 через предохранители FU с одной стороны и от нулевого провода с другой.
Все электродвигатели М1 – М6 имеют индивидуальные переключатели режимов SA1 – SA6. Это необходимо для предотвращения аварийного останова всей технологической линии.
Запуск технологической линии производства жевательной резинки в автоматическом режиме осуществляется контроллером по сигналу оператора. При нажатой кнопке SF ток идет в наш щит управления и питает все его комплектующие и засвечивается сигнальная лампа HL1. Затем контроллер по заданной программе запускает электродвигатели технологического оборудования.
Запуск электродвигателей осуществляется аналогично поэтому целесообразно рассмотреть запуск одного электродвигателя например включение шнека подачи сахарного песка в бункер. С модуля дискретного вывода поступает сигнал 220В на катушку реле К1. Нормально разомкнутый контакт этого реле замыкается и ток идет на магнитный пускатель КМ1. При этом замыкается нормально разомкнутый контакт КМ1 а также замыкается нормально разомкнутый контакт К1 и засвечивается сигнальная лампа HL4.
При положении переключателя режимов SA1 «Р» запуск электродвигателя осуществляется оператором путем нажатия кнопки SB2. При этом ток идет на катушку магнитного пускателя КМ1 замыкается его нормально разомкнутый контакт двигатель запускается.
Поддержание заданного уровня например в бункере с сахарным песком осуществляется следующим образом. При опускании уровня в бункере до нижнего подается сигнал с дискретного выхода контролера запитывает реле К1 одним замыкающим контактом запитывает цепь управления приводом шнека нагнетает сахар в бункер а вторым включает сигнальную лампу HL4. Шнек нагнетает продукт в бак II до верхнего уровня. При достижении верхнего уровня с ультразвукового сигнализатора уровня идет на катушку реле К17 замыкается контакт и сигнал поступает на соответствующий дискретный вход контроллера. С дискретного выхода контроллера сигнал идет на катушку реле срабатывает и размыкает контакты реле К1 следовательно заснет сигнальную лампу HL4. Аналогично происходит поддержание уровня в заданных пределах в сборнике основы жевательной резинки а также в дозаторах сахарного песка и основы жевательной резинки только с той разницей что вместо шнека или насоса там поддерживается уровень путем открытия и закрытия заслонок.
Система стабилизации температуры в сбивателе жевательной массы реализована следующим образом. При положении ключа выбора режима SA11 – «А». К аналоговому входу контроллера подключен датчик температуры с аналоговым выходом 4 20мА. При достижении нижней уставки с релейного выхода контроллера поступает сигнал на катушку реле К15 его нормально разомкнутый контакт замыкается клапан начинает открываться При этом с замыкается нормально-разомкнутый контакт и засвечивается HL19. При достижении верхней уставки с релейного выхода контроллера поступает сигнал на катушку реле К16 его нормально разомкнутый контакт замыкается клапан начинает закрываться. При положении ключа «Р». Оператор вручную поддерживает температуру в сборнике какао-тертого путем нажатия на кнопки SB24 для уменьшения подачи пара и SB25 для увеличения подачи пара в рубашку сборника наблюдая на цифровом табло за изменением значений температуры и положением рабочего органа клапана.
ТаблицаVIII.Перечень элементов схемы электрической принципиальной.
Выключатель автоматический
Предохранитель плавкий
Электротепловое реле
Выключатель кнопочный
Электромагнитное реле
Переключатель режимов
Путевой выключатель (концевой)
Сигнальный светодиод
Конденсатор керамический
Рекомендуемые чертежи
- 24.01.2023
- 15.04.2015