Автоматизация печи дожига газов


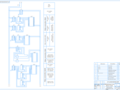
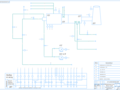
- Добавлен: 24.01.2023
- Размер: 127 KB
- Закачек: 2
Описание
Состав проекта
![]() |
![]() ![]() ![]() |
![]() ![]() ![]() |
![]() ![]() ![]() |
![]() ![]() ![]() |
![]() ![]() ![]() ![]() |
![]() ![]() ![]() |
![]() ![]() ![]() ![]() |
![]() ![]() ![]() |
![]() ![]() ![]() |
![]() ![]() ![]() |
Дополнительная информация
Электрическая схема.doc
На основании функциональной схемы автоматизации с учётом выбранных приборов и средств автоматизации разработана принципиальная электрическая схема регулирования управления и блокировки.
Для регулирования температуры в печи дожига F03 разработана комбинированная система которая работает следующим образом.
Термопреобразователь B1N измеряет температуру верха в печи и преобразует ее в унифицированный электрический сигнал постоянного тока в диапазоне 4 - 20 мА. Питание термопреобразователя осуществляется постоянным напряжением 24 В поступающим от блока питания U2. Сигнал с контактов 1 и 2 блока зажимов термопреобразователя В1N поступает по соединительной линии на контакты 1 и 2 модуля аналогового ввода A1.1Z многоканального цифрового измерительного преобразователя-контроллера. Значение температуры поступает в регулятор температуры который реализован программным путём в программируемом контроллере. С этого регулятора сигнал посредством модуля аналогового вывода A1.2Z поступает на контакты электропневматического преобразователя A1Y который управляет клапаном подачи топливного газа.
Преобразователь расхода B2N измеряет расход остаточных газов и преобразует его в унифицированный электрический сигнал постоянного тока в диапазоне 4 - 20 мА. Питание термопреобразователя осуществляется постоянным напряжением 24 В поступающим от блока питания U3. Сигнал с контактов 1 и 2 блока зажимов преобразователя В2N поступает по соединительной линии на контакты 3 и 4 модуля аналогового ввода A1.1Z многоканального цифрового измерительного преобразователя-контроллера. Значение расхода поступает в компенсатор расхода который реализован программным путём в программируемом контроллере. Этот компенсатор преобразует сигнал и регулятор реализованный в ПЛК выдает управляющее воздействие с учетом этих преобразований.
Рассмотрим системы блокировки.
Для защиты по низкому давлению в линии топливного газа предусмотрена система блокировки. В случае падения давления ниже 35 кгсм2 срабатывает датчик-реле Р1 и замыкает свой контакт. Датчик питается постоянным напряжение 24В от блока питания U5. В результате сигнал идет на контакт 4 модуля аналогового ввода A1.3Z многоканального цифрового измерительного преобразователя-контроллера. Этот сигнал идет далее в программируемый контроллер который выдает сигнал на контакты электропневматических преобразователей (A2Y A3Y A4Y) запорных органов поз. 8-7 8-8 8-9.
1. Описание технологического процесса.doc
Установка предназначена для получения элементарной серы из кислого газа выделенного в процессе сероочистки природного газа на установках У172 У141 установках переработки конденсата а также газа выветривания с установок У-122 У-165.
Установка состоит из:
Отделения Клаус где путем прямого окисления в реакционных печах сероводорода до элементарной серы и SО2 (термическая часть) и дальнейших реакций Н2S и SO2 на слое катализатора (каталитическая часть) получается основной объем серы. В термической части выход достигает 55% а в каталитической части - 40% от общего количества серы.
Отделения Сульфрин где путем доочистки хвостовых газов на катализаторе (активированный глинозем высокого качества) достигается в целом по установке 996% извлечения серы из газа.
Печи дожига остаточных газов где преобразуются в SO2 перед сбросом в атмосферу все сернистые соединения имеющиеся на выходе отделения Сульфрин.
Узла дегазации жидкой серы предназначенного для извлечения сероводорода абсорбированного в сере полученной в отделениях Клаус и Сульфрин.
Производительность установки 2У151 составляет: 7935 тч серы по кислому газу 95000 м3ч - номинальная 96900м3час - максимальная.
Продукцией является сера техническая газовая соответствующая ГОСТ 127-76.
Остаточные газы отделения Сульфрин сжигаются при температуре 520-600 оC в печи дожига F03 работающей на топливном газе. В печь также сбрасываются газы с котлов Н01 и Н11 и газ дегазации с серной ямы Т02. После сгорания образуются дымовые газы которые проходят через теплообменники Е05 и Е07. В Е05 дымовые газы используются для подогрева газа регенерации реакторов Сульфрин и Клаус в Е07 – для перегрева пара.
Дымовые газы пройдя теплообменники Е05 Е07 охлаждаются до 350 оC и направляются в дымовую трубу Д01. Проходя по трубе Д01 дымовые газы охлаждаются отдавая тепло стенкам трубы и выбрасываются в атмосферу.
Топливный газ поступает к F03 по 6" трубопроводу от границы установки. Он сжигается в топке F03 в потоке воздуха подаваемого воздуходувками К02АВ К12 на трех горелках расположенных на фасаде печи. Каждая горелка снабжена основной горелкой пилотной горелкой датчиком наличия пламени электрозапальником.
Воздух для питания F03 подается тремя воздуходувками К02А К02В К12 две из которых в работе одна в резерве. Воздух поступает по 36" трубопроводу в соотношении 10:1 к расходу топливного газа.
Описание существующего уровня автоматизации
В настоящее время в системе автоматизации установки У151 применяется локальная автоматика на основе аналоговых технических средств. Необходимо отметить что применяются устаревшие технические средства построенные на элементах пневмоавтоматики УСЭППА. Технологический процесс рассматривается как набор обособленных параметров управление которыми осуществляется локальными системами автоматического регулирования. Каждый измеряемый параметр с первичного измерительного преобразователя поступает на аналоговое регулирующее устройство установленное на щите в операторной. Индикация и регистрация параметров осуществляется аналоговыми индикаторами и самопишущими регистраторами также установленными на щите в операторной.
Регулирование технологических параметров также может осуществляться в ручном режиме со щита в операторной с помощью кнопок.
3. Описание функциональной схемы автоматизации.doc
В существующей системе автоматизации реализованы следующие основные контуры регулирования:
регулирование температуры в печи F03 осуществляется комбинированной АСР посредством изменения расхода подачи топливного газа в топку;
регулирование температуры дымовых газов после пароперегревателя Е07 осуществляется одноконтурной АСР за счет изменения расхода пара подаваемой в трубное пространство теплообменника;
регулирование расхода технологического воздуха и поддержание соотношения топливный газвоздух осуществляется каскадной АСР с помощью воздействия на соответствующий клапан на линии подачи воздуха;
регулирование температуры перегретого пара нагреваемого в теплообменнике Е07 осуществляется одноконтурной АСР с помощью изменения расхода впрыскиваемой воды клапаном на линии подачи воды.
Также в данной системе автоматизации осуществляется контроль параметров с регистрацией их по месту или на щите в операторной. Наиболее важными из них являются:
содержание SO2 и O2 в дымовых газах после Е07 выбрасываемых в атмосферу (SO2 007-01%об O21%об);
температура дымовых газов после Е07;
давление воздуха подаваемого в печь F03 (01 кгм2);
давление остаточных газов подаваемых в топку печи F03 (003 кгм2);
расход перегретого пара (1478 тч).
В проектируемой АСР также предусмотрена сигнализация достижения ряда параметров предельных значений и срабатывание системы защиты и блокировок для исключения аварийных ситуаций.
Низкое давление топливного газа (35 кгсм2).
Отсутствие пламени на горелках печи – 3 штуки.
Низкая температура в топке печи F03 (520°С).
Высокая температура в топке печи F03 (600°С).
Низкое соотношение воздухтопливный газ (132 кгкг).
Низкий расход воздуха (10000 м3ч);
Неисправность электродвигателя воздуходувок;
Разработана функциональная схема автоматизации системы управления процессом сжигания остаточных газов установки У151.
Остаточные газы отделения Сульфрин подаются в топку печи F03 для сжигания. К этому потоку также прибавляются газы с котлов Н01 и Н11 и газ дегазации серной ямы Т02. Перед входом в печь стоит датчик расхода поз. 6-1. Он посылает сигнал на преобразователь расхода поз. 6-2 с выдачей показаний на ЭВМ. Температура в топке печи измеряется датчиком температуры поз. 7-1. Измеренное значение отправляется на преобразователь 7-2 который посылает унифицированный сигнал на регулятор температуры поз. 7-3. Также на этот регулятор приходит сигнал с преобразователя расхода поз. 6-2. Учитывая влияние этих двух параметров регулятор выдает управляющее воздействие через электропневматический преобразователь поз. 7-5 на исполнительный механизм – клапан поз. 7-6 на линии топливного газа. Так осуществляется регулирование температуры в топке печи F03.
В процессе сгорания образуются дымовые газы которые направляются через теплообменники Е05 и Е07 в дымовую трубу где выбрасываются в атмосферу. В теплообменнике Е05 газы охлаждаются до 484°С в Е07 – до 343°С. Температура после Е07 измеряется датчиком поз. 1 преобразуется поз. 1-2 и поступает на регулятор поз.1-3. Регулятор управляет клапаном поз. 1-6 посредством электропневматического преобразователя 1-5. Изменение расхода пара в трубах Е07 влияет на температуру газов после Е07.
Перед входом в боров трубы D01 расположен газоанализатор содержания SO2 и O2 поз. 3-1. От него сигнал идет на преобразователь поз. 3-2 который преобразует его в унифицированный сигнал 4-20 мА с выдачей показаний на ЭВМ.
Температура газов на выходе из трубы измеряется датчиком поз. 2-1 сигнал от него приходит на преобразователь поз. 2-2 с выдачей показаний на ЭВМ.
Топливный газ поступает к F03 от границы установки и сжигается в потоке воздуха создаваемого воздуходувками К02 и К12 на трех горелках расположенных на фасаде печи. Каждая горелка снабжена основной горелкой пилотной горелкой электрозапальником и датчиком наличия пламени (поз. 8-1 9-1 10-1). На пилотные горелки газ подается через клапан-отсекатель (поз.8-8). Сигнал от датчика наличия пламени поступает на сигнализацию (поз. 8-2) и далее идет на ПЛК и ЭВМ в операторную. В случае погасания какой-либо из горелок выдается сигнал на ключ управления (поз. 8-3) который через электропневматические преобразователи (поз. 8-4 8-5 8-6) дает команду закрыть клапаны-отсекатели поз. 8-7 и 8-8 открыть поз. 8-9.
Расход топливного газа измеряется расходомером поз. 4-1 далее он посылает сигнал на преобразователь поз. 4-2 который вырабатывает унифицированный сигнал 4-20мА. Тот регистрируется на ЭВМ а также поступает на регулятор соотношения расхода воздуха и топливного газа поз. 5-3. На этот регулятор также приходит сигнал с датчика расхода на линии подачи воздуха поз. 5-1 через преобразователь поз. 5-2. Регулятор соотношения управляет расходом воздуха посредством электропневматического преобразователя поз. 5-5 и клапана поз. 5-6.
На линии топливного газа предусмотрена сигнализация по давлению которая расположена по месту (поз. 12-1) и выводится на ЭВМ в операторную. В случае слишком низкого или высокого давления сигнализация срабатывает и подается сигнал на закрытие клапанов поз.8-7 8-8 открытие поз. 8-9 а также на электродвигатели воздуходувок (через магнитные пускатели поз. 12-3 12-5).
Для обеспечения безопасности здоровья рабочего персонала предусмотрена система контроля состава воздуха рядом с установкой которая обеспечивается датчиком поз. 13-1 и сигнализацией поз. 13-2 сигнал с которых регистрируется на ЭВМ в опереторной.
Список литературы.doc
Ротач В. Я. Теория автоматического управления. – М.: Энергия 2005
Шевченко М. А. Выпускная квалификационная работа. – Астрахань 2009
Технологический регламент установки У251.
Кулаков М. В. Технологические измерения и приборы для химических производств. М.: Машиностроение 1983 – 424 с.
Электрическая схема.cdw

КП 220301.050150.2009
Модуль аналогового ввода
Модуль аналогового вывода
Преобразователь температуры
Электропневматические
Автоматический выключатель
Датчик-реле давления
Преобразователь расхода
Датчик-реле наличия пламени
2. Структура системы управления.doc
Современные системы автоматизации строятся в виде многоступенчатых структур последовательно осуществляющих все необходимые функции контроля и управления.
При этом на первой ступени обеспечивается управление отдельными агрегатами установками и участками преимущественно посредством локальных систем контроля и управления и систем управления с применением микропроцессоров и ЭВМ.
На второй ступени обеспечивается обслуживание самостоятельных производственных комплексов производств линий участков цехов связанных между собой общностью технологического процесса. На этой ступени системы управления с применением ЭВМ обеспечивают координацию работы подчинённых производственных единиц распределение нагрузок между параллельно работающими установками оптимизацию заданных показателей работы посредством воздействия на местные системы управления.
На следующей высшей ступени управления система автоматизации обеспечивает решение сложных задач по координации работы всех производственных и вспомогательных подразделений технологического объекта распределению нагрузок и обеспечению оптимизации работы предприятия. Решение этих задач связано с рациональной организацией текущего и перспективного планирования с учётом и анализом производственной деятельности предприятия и т.д.
Разрабатываемая АСУТП будет выполнять задачи характерные для первой и второй ступеней управления.
Возможно несколько вариантов реализации АСУТП.
АСУТП реализующая ручной режим при котором комплекс технических средств выполняет информационные функции централизованного контроля и вычисления комплексных технических и технико-экономических показателей. Выбор и осуществление управляющих воздействий производит человек (оператор).
АСУТП реализующая режим «советчика» при котором комплекс технических средств на основе анализа исходной информации разрабатывает рекомендации (советы) по управлению и осуществляет поиск оптимальных решений а решение об их использовании принимается и реализуется оперативным персоналом.
АСУТП реализующая автоматический режим при котором комплекс технических средств реализует управляющие функции. Целью этих функций является автоматическая выработка и выдача управляющих воздействий на технологический объект управления. При этом различают режим супервизорного управления когда средства управляющего вычислительного комплекса автоматически изменяют уставки и параметры настройки локальных регулирующих устройств вблизи точки оптимального ведения процесса и режим прямого непосредственного цифрового управления когда управляющий вычислительный комплекс формирует воздействие непосредственно на исполнительные механизмы а регуляторы вообще исключаются из схемы управления.
Для проектируемой АСУ ТП основными задачами являются:
экономия топлива сырья и материалов;
понижение степени вреда окружающей среды;
достижение оптимальной загрузки технологического оборудования;
обеспечение безопасности функционирования объекта;
оптимизация режимов работы технологического оборудования.
Разрабатываемая система будет работать в автоматическом режиме и иметь следующую структуру.
Первый уровень АСУТП составляют локальные средства автоматизации включающие измерительные преобразователи устройства управления и исполнительные механизмы расположенные непосредственно на технологическом оборудовании и коммуникациях или вблизи них.
Второй уровень составляют программируемые логические контроллеры (ПЛК). На этот уровень возложены следующие функции:
сбор данных об управляемом процессе
прием и передача данных во внешнюю промышленную сеть по соответствующему интерфейсу
первичная обработка (преобразование) сигналов измерительной информации
формирование регулирующих воздействий в соответствии с программно реализованными алгоритмами регулирования
выдача регулирующих воздействий на устройства управления.
Таким образом ПЛК осуществляет непосредственное управление технологическими параметрами процесса без участия ЭВМ верхнего уровня.
На третьем уровне располагается ЭВМ реализующая следующие функции:
вторичная обработка сигналов измерительной информации
индикация и регистрация регулируемых и контролируемых параметров процесса
идентификация предельных и аварийных значений параметров процесса и их сигнализация
обеспечение для оператора возможности ручного управления процессом за счет создания автоматизированного рабочего места (АРМ) оператора.
Указанные уровни АСУТП образуют промышленный уровень автоматизированной системы управления предприятием (АСУП). Подключение ЭВМ оператора к локальной заводской сети позволяет взаимодействовать с другими АСУТП и функционировать в составе АСУП.
Использование в проектируемой системе управления ПЛК осуществляющего непосредственное регулирование технологических параметров позволяет высвободить ресурсы ЭВМ вышестоящего уровня для создания и хранения истории процесса резервирования информации.
Использование ЭВМ позволяет осуществлять индикацию регистрацию и сигнализацию технологических параметров в одном пункте – АРМ оператора – что снижает загруженность оператора и повышает эффективность его работы. Кроме того АРМ позволяет реализовать дублирование автоматического управления за счет введения ручного управления что повышает безопасность и надежность функционирования всей АСУТП.
В качестве дополнений для данной АСУТП предложим комбинированную АСР для регулирования температуры в топке печи F03 с учетом расхода газов поступающих в печь. В зависимости от расхода поступающих на сжигание газов будет меняться расход топливного газа что обеспечит более точное поддержание заданной температуры.
Автоматизация печи дожига.cdw

Функциональная схема
дистанционное управление
остаточный газ с R03
параметр - наличие пламени
Содержание и заключение.doc
Структура системы управления
Описание функциональной схемы автоматизации .
Выбор технических средств автоматизации .
Разработка принципиальной электрической схемы ..
В данном проекте была реализована система автоматизации печи дожига остаточных газов выбраны технические средства для данной АСУ построены электрические схемы. Особенностями данной системы является наличие агрессивной среды а также взрыво- и пожароопасное производство. Предложена комбинированная система регулирования температуры в печи.
Структурная схема комбинированной АСР
4. Выбор технических средств автоматизации.doc
На основании существующей функциональной схемы выберем технические средства для проектируемой системы управления дожига остаточных газов.
Регулирование технологических параметров в каждом отдельном контуре осуществляется при помощи контроллера IUC9300 для работы в стандартных промышленных сетях.
IUC9300 - модульные контроллеры компании PEP Modular Computers на основе мезонинной шины CXC обладают многими возможностями систем VME при заметно меньшей стоимости. Это делает их применение весьма привлекательным для решения многих задач автоматизации производства. Однопроцессорная шина CXC обеспечивает скорость передачи данных до 10 Мбайтсек. В крейте CXC контроллера может устанавливаться до 7 модулей вводавывода. Применение мезонинной технологии CXC позволяет создавать как мощные локальные VME подсистемы так и автономные интеллектуальные контроллеры. IUC9300 способны обрабатывать до 250 каналов вводавывода. Малые геометрические размеры CXC-модулей (100 х 115 мм) обеспечивают наилучшие эксплуатационные характеристики: микропотребление высокую виброударопрочность компактность. Базируясь на технологии «открытых магистрально-модульных систем» IUC9300 полностью программно совместим с системами VME9300 SMART IO и SMART2 сочетая в себе возможности мощного управляющего компьютера реального времени и программируемого логического контроллера - PLC.
Базовое программное обеспечение:
стандартные операционные системы реального времени: OS-9 V
промышленные сети F сетевые протоколы: TCPIP DECnet Prof
промышленные языки программирования PLC-контроллеров IEC-1131.
Средства программирования:
средства разработки для OS-9 V
ISaGRAF - система программирования PLC-контроллеров на промышленных языках в соответствии со стандартом IEC1131-3 для MS-Windows.
Интерфейс промышленной локальной сети ProfiBus позволяет создавать распределенные системы объединяющие интеллектуальные контроллеры различной мощности: VME9300 IUC9300 SMART а также контроллеры других производителей интеллектуальные датчики и исполнительные устройства с интерфейсом ProfiBus.
Фирма PEP Modular Computers (Германия) образованная в 1975 году имеет 26-тилетний опыт в обеспечении высоко-технологичных решений для промышленной автоматизации особенно для рынка встоенных систем реального времени.
Продукция имеет два исполнения: с рабочим температурным диапазоном 0 - 70°С и -40°С - +85°С. Компания сертифицирована по ISO9001. Оборудование имеет сертификат Госстандарта России как средство измерения и Разрешение Госгортехнадзора для применения в автоматизации опасных объектов.
Применение оборудования РЕР можно найти в таких областях как промышленная автоматизация управление движением транспорта автомобильной промышленности транспорте телекоммуникации автоматизации производства тестировании и измерении автоматизации зданий управлении энергетическими установками. Благодаря высокой вибро- и удароустойчивости РЕР оборудование идеально подходит для применения в мобильных приложениях таких как летательные аппараты железнодорожный транспорт в морской аэрокосмической или военно-морской области.
Выбираем контроллер СХМ-SIO6 оснащенный двумя интерфейсами RS232485 для процессорных последовательных портов и четырьмя последовательными каналами (2*MC68681) с интерфейсом RS232422485.
Для микроконтроллера СХМ-SIO6 необходимо дополнительно выбрать модули ввода - вывода для преобразования аналоговых входных сигналов поступающих с первичных преобразователей в цифровые для работы микроконтроллера и обратного преобразования которое осуществляет модуль вывода.
В комплекте с указанным контроллером используются следующие модули вводавывода и модули специального назначения.
CXM-IDAD-16 - 16 – канальный модуль аналогового вводавывода. Модуль оснащен 16-ти канальным АЦП разрядность - 16 разрядов время преобразования - 25 мкс входной сигнал – унифицированный токовый в диапазоне 4 – 20 мА или напряжение постоянного тока в диапазоне 0 – 5 или 0 – 10 В. Ввывод осуществляется через 8-ми канальный ЦАП разрядность - 12 разрядов выходной сигнал - унифицированный токовый в диапазоне 4 – 20 мА или напряжение постоянного тока в диапазоне 0 – 5 или 0 – 10 В. Модуль оснащен встроенным таймером разрядность – 24 разряда.
CXM-DIO6 - 16 канальный модуль дискретного вводавывода. Модуль имеет 16 дискретных каналов ввода максимальное напряжение 60 В максимальный ток 6 мА и 8 дискретных выходов номинальное напряжение 24 В номинальный ток – 1 А. Входы и выходы гальванически развязаны.
Исходя из количества и номенклатуры требуемых каналов вводавывода выбираем следующие модули ввода-вывода и модули специального назначения:
-ти канальный модуль аналогового ввода-вывода CXM-IDAD-16 – 3 шт.;
-ти канальный модуль дискретного ввода-вывода CXM-DIO6 – 3 шт.;
Для питания контроллера внутренней электроники модулей вводавывода и выходных цепей используется первичный импульсный источник питания встроенный в крейт.
Технические характеристики:
выходное напряжение: пост. 24 В;
номинальное напряжение: перем. 220 В;
диапазон входного напряжения: перем. 85 В – 132 В176 В – 264 В;
время задержки выхода: > 20 мс;
входной ток (тип.): 28 А при перем. 220;
пусковой ток (тип.): 30 Ас;
выходной ток: пост. 10 А;
окружающая температура эксплуатации: 0 – 50 °С;
В качестве ЭВМ используется станция технологического управления Advantech IPC-510-SYS2-1.
процессор: Intel Pent
процессорная плата: Advantech PCA-6186 (чипсет Inte
ОЗУ: 512 Мбайт DDR SDRAM
видеоконтроллер: Intel E
жёсткий диск: 40 Гбайт U
дисковод 144 Мбайт 35";
звуковой контроллер: кодек AC-97 6 – канальный;
сетевой интерфейс: Ethernet 10100
разъёмы: 7 ISA 4 PCI 32 бит33 МГц;
интерфейсы: 6 USB 1.1 2 RS–232 1 LPT 1
температурный режим: 0 – 40 °С (работа) -20 – +60 °С (хранение);
влажность: 10 – 85% при 40 °С (работа) 10 – 95% при 40 °С (хранение) без образования конденсата;
размер: 177 х 482 х 450 мм.
Для измерения температуры применим датчик ТХАУ Метран271МП.
Назначение: преобразователь термоэлектрический Метран-276 предназначен для измерения температуры жидких и газообразных химически агрессивных и неагрессивных сред. Чувствительный элемент первичного преобразователя и встроенный в головку датчика измерительный преобразователь преобразуют измеряемую температуру в унифицированный выходной сигнал постоянного тока что даёт возможность построения АСУТП без применения дополнительных нормирующих преобразователей.
возможность измерения в агрессивных средах;
тип термопары: ТХА (К);
количество чувствительных элементов 1;
схема соединений: двухпроводная;
диапазон измеряемых температур: -40 + 800 0С;
рабочий спай: изолированный;
климатические условия: до значения температуры воздуха 85 0С;
зависимость: линейная;
выходной сигнал - унифицированный токовый в диапазоне 4 – 20 мА;
взрыво- пожаробезопасен вид взрывозащиты: 1E
степень защиты от внешних воздействий:
условное давление: 16 МПа;
материал защитной арматуры: 12Х18Н10Т;
средний срок службы: не менее 8 лет.
В зависимости от значения измеряемой температуры и параметров измеряемой среды используются датчики со следующими диапазонами измерения:
температура в топке печи F03 520°C: диапазон измерения -40 – 800°C;
температура дымовых газов после Е07 350°C: диапазон измерения -40 – 800°C;
температура дымовых газов на вершине трубы D01 320°C: диапазон измерения -40 – 500°C;
температура перегретого пара 380°C: диапазон измерения -40 – 500°C;
Для измерения расхода кориолисовым методом применим датчик Метран Micro Motion.
Назначение: кориолисовые расходомеры предназначены для прямого измерения объемного расхода газов жидкостей и взвесей. Все измерения выполняются в реальном времени.
измеряемые среды: агрессивные среды с высокой химической активностью (газ с содержанием сероводорода кислоты щёлочи нефтепродукты сырая нефть морская вода).
напряжение питания =24 В.
избыточное давление в трубопроводе до 10 МПа.
предел относительной погрешности 05%.
ряд верхних пределов измерений кПа: 4; 63; 10; 16; 25; 40; 63.
температура окружающего воздуха - 20 + 70 0С.
относительная влажность окружающей среды до 95 %.
устойчив к вибрации и магнитным полям.
выходной сигнал - унифицированный токовый в диапазоне 4 – 20 мА
взрыво- пожаробезопасен.
В зависимости от диаметра трубопровода в месте измерения расхода величины расхода и параметров измеряемой среды выбираем расходомеры со следующими диапазонами измерения:
расход газов подаваемых в печь F03: давление 003кгсм2 диапазон измерений 0-43000 (м3ч);
расход топливного газа: 2000 (м3ч) давление 35 кгсм2 диапазон измерений 0-13000 (м3ч);
расход воздуха: 20000 (м3ч) давление 01 кгсм2 диапазон измерений 0-43000 (м3ч);
Для измерения содержания SO2 и O2 в дымовых газах применим универсальный газоанализатор Гамма-100.
Многокомпонентный стационарный газоанализатор ГАММА-100 предназначен для непрерывного автоматического измерения от 1-го до 3-х компонентов из следующего набора газов СО СО2 SО2 H2 N2 CН4 NO О2 при контроле различных технологических процессов.
Газоанализатор ГАММА-100 изготавливается как в трех- двухкомпонентном так и в однокомпонентном варианте и используется в составе автоматизированных систем управления технологическими процессами в черной цветной металлургиинефтяной и газовой промышленности цементной и стекольной промышленности предприятиях производства кирпича и керамики в химической и нефтехимической промышленности ТЭЦ ГРЭС котельных и т.д.
Принципы измерения: оптико-акустический термомагнитный термокондуктометрический;
Диапазоны измерения SO2 гм3: 0 – 2 0 – 5 0 – 10 0 – 20 0 – 60;
Способ измерения SO2: оптико-акустический;
Дипазоны измерения O2 объемная доля %: 0 – 1 0 – 2 0 – 5 0 – 10 0 – 20 0 – 30 0 – 60;
Способ измерения O2: термомагнитный;
Количество измерительных каналов: 1 – 3;
Среднее время наработки на отказ: 120 000 часов;
Габаритные размеры: длина – 435 мм ширина – 485 мм высота – 280 мм масса - 20 кг.
Для контроля пламени в печи F03 применим прибор контроля пламени «Пламя-М».
Приборы Пламя-М предназначены для применения в схемах защиты и сигнализации газотурбинных установок печей и котлов.
Приборы Пламя-М можно также использовать в системах защиты газотурбинных установок от последствий самопроизвольного погасания пламени в газовой нефтяной химической и других отраслях промышленности.
Освещенность фотодатчика: не более 20000 лк;
Инерционность: не более 2 с;
Выходные параметры: 3 переключающие группы контактов реле;
Напряжение питания: 12 или 24 В.
Потребляемая мощность: не более 45 ВА;
Длина линии связи: не более 300 м.
Использование для контроля инфракрасных датчиков гарантирует высокую чувствительность приборов во всем диапазоне освещенности.
При выходе температуры воздуха окружающего датчик за пределы установленных значений мы можем поставить дополнительный корпус для охлаждения (обогрева).
В приборах предусмотрена сигнализация при обрыве линии связи.
В качестве контактора давления на линии топливного используем реле избыточного давления однопредельные Метран РД.
Реле имеют следующие характеристики:
контролируемая среда: газ пар жидкость;
тип уставки: при понижении давления;
способ срабатывания реле: на замыкание;
постоянный ток коммутируемый контактами: 001 – 05 А;
коммутируемое напряжение:
- при индуктивной нагрузке: 5 – 36 В
- при активной нагрузке: 5 – 100 В;
коммутируемая мощность:
- при индуктивной нагрузке: 06 ВА
- при активной нагрузке: 10 ВА;
пределы допускаемой основной погрешности срабатывания реле: не более ±1% от верхнего предела диапазона уставки;
зона возврата: регулируемая от 1 до 10% от верхнего предела диапазона избыточного давления соответствующей уставки;
параметры окружающей среды:
- температура: -30 – +50 °С
- относительная влажность: до 95% при температуре 35 °С
- вибрация частотой до 25 Гц амплитудой перемещения не более 01 мм;
- дисков контактирующих с контролируемой средой: 12X18Н10Т;
Для связи контроллера с пневматическими ИМ регулирующих клапанов используются электропневматические преобразователи для сигналов постоянного тока Samson 6126.
вход: 4 – 20 мА; мин. ток 36 мА; напряжение при полном сопротивлении 6 В (соответствует 300 Ом при 20 мА);
выход: 02 – 1 кгссм2 расход воздуха: 2 м3ч;
вид взрывозащиты: ЕЕх
питание: 14 кгссм2 макс. 15 кгссм2 без регулятора преддавления расход воздуха 008 нм3ч при 14 кгссм2;
передаточное соотношение: графическая характеристика линейная гистерезис 03 % от конечного значения;
температура окружающей среды: -20 – +60 °С;
Для связи контроллера с пневматическими ИМ отсекателей используются электропневматические реле типа ЭПР-4.
Это реле предназначено для преобразования электрических импульсов в пневматические управляющие пневматическим ИМ.
питание пневматическое: очищенный и осушенный воздух давлением 14 кгссм2;
питание электрическое: 24 В пост. тока;
потребляемая мощность: 10 Вт;
условия окружающей среды: температура 5 – 50 °С относительная влажность до 80 %;
габаритные размеры: 240 195 90 мм;
Для питания стабилизированным напряжением и искрозащиты датчиков применим блок питания PSM-36-24 24 В (15 А).
Расширенный входной диапазон переменного (AC 85 – 264 В) и постоянного (DC 120 -370 В) напряжения
Выходной ток до 15 А
Широкий диапазон температуры эксплуатации (-30 . +50 °С)
варианта крепления: на DIN-рейку и панель
Дублированные выходные разъемные клеммы
Автоматическое восстановление нормального функционирования после устранения причин срабатывания защит.
Преобразование сетевого переменного напряжения в диапазоне 85 - 264 В и постоянного напряжения в диапазоне 120 - 370 В в стабилизированное постоянное напряжение 24 В
Защита от перегрузки по току
Защита от короткого замыкания
Защита от повышенного и пониженного входного напряжения
Индикация напряжения на выходе «24 V» - зеленый
Индикация аварийных ситуаций «Error» - красный
Для защиты цепей подключения дискретных датчиков используются барьеры БИ-005.
Для обеспечения искрозащиты датчиков используются барьеры искробезопасности БИ-005 на стабилитронах. Они обеспечивают вид взрывозащиты «искробезопасная электрическая цепь». Характерными особенностями барьеров искробезопасности серии БИ являются простая и быстрая установка (наличие разъёмных колодок позволяет заменить барьер без отсоединения проводов от клемм барьера) монтаж на направляющей типа DIN обеспечивает высокую скорость монтажа при технологической простоте и минимальных трудозатратах.
максимальное выходное напряжение U0: 36 В;
максимальный выходной ток I0: 50 мА;
максимальная внешняя индуктивность L0: 1 мГн;
максимальная внешняя емкость С0: 05 мкФ;
максимальная выходная мощность Р0: 048 Вт;
максимальное выходное напряжение переменного тока (эффективное значение) Um: 250 В;
габаритные размеры: 114 99 125 мм;
средняя наработка на отказ: не менее 150000 ч.;
масса: не более 025 кг.
В качестве регулирующих клапанов выберем клапаны регулирующие запорные дисковые «Импульс-КРЗд».
Поворотные запорно-регулирующие дисковые клапаны КРЗд предназначены для качественного регулирования параметров рабочей среды в различных тепловых и других технологических системах.
Условный проход: до 65мм;
Рабочее давление: до 40 МПа;
Рабочая среда: конденсат пар газ мазут и другие среды;
Температура: до 650°С;
Эти клапаны будут использоваться на линиях топливного газа технологического воздуха пара воды.
В качестве отсечных клапанов выберем клапаны регулирующие запорные дисковые «Импульс-КОг100».
Клапаны электромагнитные отсечные быстродействующие с дистанционным управлением предназначенные для автоматического перекрытия подачи рабочего продукта (газа пара) при нарушении технологических параметров в системе.
Условный проход: 100мм;
Рабочее давление: до 2.5 МПа;
Рабочая среда: конденсат пар газ;
Длина – 560мм; высота – 640мм;
Эти клапаны будут стоять на линии подачи топливного газа на основные и пилотные горелки.
Введение.doc
Предприятия нефтяной и газовой промышленности относятся к классу объектов с повышенной техногенной опасностью поэтому важнейшим требованием к системам автоматизации является повышенная надежность (здесь недопустимы даже мелкие аварии из-за возможного значительного экологического и материального ущерба). На выполнение этого требования ориентируются при выборе программно-аппаратных средств используемых на всех уровнях автоматизации.
Автоматизированные системы управления отдельными технологическими процессами предназначены для: повышения эффективности управления и учета нефтепродуктов; сокращения количества аварийных ситуаций и времени простоя оборудования для достижения его оптимальной загрузки; снижения затрат на ремонт оборудования за счет оперативного выявления его неисправностей и уменьшения трудоемкости эксплуатации оборудования; повышения производительности и улучшения условий труда персонала занятого управлением сбором и анализом информации; оперативной передачи данных технологического процесса в экономические процессы организации производства.
В данной работе рассматривается автоматизация печи дожига остаточных газов установки получения серы У251. Данная печь является одним из наиболее важных элементов всей установки. В случае ее неправильной работы или выхода из строя вся установка будет отключена поэтому необходимо вести тщательный контроль за ее параметрами.
Астраханский государственный Технический Университет
Кафедра Автоматизация технологических процессов
Курсовой проект по дисциплине: «Проектирование автоматизированных систем»
Автоматизация печи дожига газов
выполнил: ст. гр. ДИА-51
проверил: доц. Прохватилова Л. И.
Рекомендуемые чертежи
- 24.01.2023