Автоматизация фракционирующей колонны


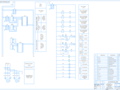
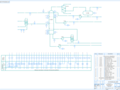
- Добавлен: 24.01.2023
- Размер: 112 KB
- Закачек: 0
Описание
Состав проекта
![]() |
![]() ![]() ![]() ![]() |
![]() ![]() ![]() ![]() |
![]() ![]() ![]() |
![]() ![]() ![]() |
Дополнительная информация
Функциональная схема.cdw

Функциональная схема
Нестандартные средства автоматизации
Технологические потоки
Технологическое оборудование
дистанционное управление
Фракционирующая колонна
Печь подогрева куба К-101
Насос подачи орошения
Неконденсирующиеся газы
Электрическая схема.cdw

бокового погона Н-104
на линии подачи сырья
на линии подачи топливного газа
фракционирующей колонны
Модуль аналогового ввода
Модуль аналогового вывода
Электромагнитные преобразов.
Преобразователи температуры
Электропневматические
Автоматический выключатель
Датчик-реле давления
Автоматические силовые выключатели
Курсовой.doc
Разработка и описание функциональной схемы автоматизации
Выбор технических средств автоматизации
1. Блок питания Метран – 608
2. Термоэлектрический преобразователь Метран – 0553
3. Датчик разности давлений Метран-55-ДД
4. Датчик избыточного давления Метран-55-ДИ
5. Уровнемер буйковый DLC3000
6. Сигнализатор уровня Senshall VHT Sapphire
7. Реле избыточного давления РД-400
8. Электропневматический исполнительный механизм фирмы SAMSON
9. Модульные контроллеры IUC9300
10. CXM-IDAD-16. Модуль аналогового вводавывода 16 – канальный
11. CXM-DIO6. 16 канальный модуль дискретного вводавывода
Разработка принципиальной электрической схемы
В настоящее время все больше возникает потребность в автоматизации как отдельных объектов так и всего производства. Это связано прежде всего с ускорением производственного процесса более точного регулирования и контроля параметров.
Еще одной причиной автоматизации стал тот факт что недорогие переносные компьютеры и большой выбор различных ТСА облегчают сбор передачу и обработку данных в режиме реального времени.
Кроме того многие компании начинают применять интернет-технологии и интранет-сети которые предлагают достаточно простую модель сетевой работы и возможность совместного использования информации. Интранет-сети обеспечивают многие преимущества обработки данных свойственные архитектуре клиент - сервер при более низкой стоимости. Но связь возможна не только через интернет но и с помощью сотовых телефонов как в режиме sms так и в постоянном режиме спутниковой связи.
Не менее важным является применение таких технологий в химической промышленности. Ведь химические процессы являются неустойчивыми со значительными нелинейностями. И даже если известны разгонные характеристики объекта управления то подбор дифференциального уравнения переходного процесса (процессов) может являться делом интуиции что является мало научно - обоснованным но иногда давать лучше результаты чем при наличии уже существующей математической модели. Поэтому применение регуляторов на П ПИ ПИД И и Д законах регулирования либо дает недостаточные показатели качества регулирования либо вообще не оказывает эффекта. А применение регулирования основанного на законах нечетких множеств оптимального адаптивного управления дают хорошие показатели качества переходного процесса и расширяет рамки применения данных ТСА.
Важным фактом является уменьшение роли человека в технологическом процессе т.е. переход от автоматизированного к автоматическому управлению.
В своей работе я разработал функциональную и принципиальную электрическую схемы системы автономного регулирования температуры верха и куба колонны К-101 блока ВТ комбинированной установки У1.731 АГПЗ и произвёл выбор ТСА для реализации этой системы на основе программируемого контроллера.
Блок ВТ он же блок 100 осуществляет вторичную перегонку стабильного гидрогенизата. Сырье блока вторичной перегонки - стабильный гидрогенизат - фракция НК-350 °С поступает по напорному трубопроводу в приемную емкость Е-101 откуда насосом Н-10112 двумя параллельными потоками подается в теплообменники Т-10112.
На общем потоке гидрогенизата установлен счетчик поз. FR-16. Давление в емкости Е-101 поддерживается клапанами-регуляторами давления поз. PRC-1 подводом инертного газа.
Расход подаваемого гидрогенизата регулируется регулятором поз. FRC-6 с коррекцией уровня поз. LRCA-2 в емкости Е-101 клапан которого установлен на выкиде насоса Н-10112.
В теплообменниках Т-10112 происходит нагрев сырья циркуляционным орошением колонны К-51 блока AT. Соотношение расходов гидрогенизата по потокам регулируется регуляторами расхода поз. FRC-45 клапаны которых установлены на линиях подачи сырья перед теплообменниками Т-1011 и Т-1012.
Циркуляционное орошение колонны К-51 проходит двумя параллельными потоками по трубному пространству теплообменников Т-1011 и Т-1012 отдавая свое тепло на нагрев гидрогенизата затем объединяясь в один поток возвращается на установку атмосферной перегонки.
Расход циркуляционного орошения по параллельным потокам регулируется регуляторами расхода поз. FRC-23 клапаны которых установлены на линии подачи циркуляционного орошения перед теплообменниками Т-1011 и Т-1012. Для выравнивания температуры оба потока сырья объединяются и направляются на вторую ступень нагрева.
В соответствии с количеством передаваемого тепла фракция НК - 350 °С разделяется на 2 потока в соотношении 60% и 40% масс. Соотношение расходов гидрогенизата регулируется регуляторами расхода поз. FRC-7 FRC-8 клапаны которых находятся на линии подачи сырья перед теплообменниками Т-102 и Т-103.
Большой поток нагревается в теплообменниках Т-1021 и Т-1022 боковым погоном колонны К-51 блока AT который отдав свое тепло на нагрев сырья возвращается в блок 50.
Меньший поток нагревается в теплообменнике Т-103 отходящим нижним потоком колонны К-101 - фракция 180-350°С. Замер температуры после теплообменников производится прибором TR-5. Нагретый до температуры 200°С гидрогенизат поступает на нагрев в печь П-1011.
Паро-жидкостной поток гидрогенизата с температурой 192 °С двумя потоками поступает на 27 тарелку ректификационной колонны К-101.
Измерение температуры сырья на входе производится термопарой поз. TRC-36. Измерение давления осуществляется прибором PR-4. С верха колонны отбирается фракция НК - 62°С. Пары дистиллята и острого орошения с температурой 76 °С поступают в конденсаторы - холодильники ХВ-1011-7 где конденсируются и охлаждаются до температуры 50 °С и далее поступают на доохлаждение в водяной холодильник X-101.
Для подавления коррозии верхних тарелок колонны К-101 и защиты конденсаторов-холодильников XB-1011-7 в шлемовую линию колонны подается 5% раствор ингибитора коррозии из емкости Е-55 блока AT. Количество ингибитора коррозии измеряется прибором поз. FI-13.
Сконденсированная фракция НК-62°С и неконденсирующиеся газы после водяного холодильника направляются в емкость Е-102 с температурой 40°С откуда продукт забирается насосами Н-10512 и подается на орошение колонны К-101 а балансовое количество фракции НК – 62 °С направляется в колонну К-102.
Количество отбираемой фракции НК – 62 °С регулируется регулятором расхода поз. FRC-12 с коррекцией по уровню поз. LRCA-5 в емкости Е-102 клапан которого установлен на линии подачи сырья в колонну К-102.
Количество подаваемого орошения регулируется регулятором поз. FRC-1 коррекцией по температуре поз. TRC-3 верха клапан которого установлен на линии подачи орошения в колонну К-101.
Давление в системе К-101 Е-102 регулируется регулятором давления поз. PRCAH-2.
Температура верха К-101 замеряется термопарой поз. TRC-3.
Боковым погоном колонны К-101 является фракция 62 – 180 °С которая с температурой 144 °С выводится с 10 (12) тарелки на прием насосов Н-10412 и направляется в блок атмосферной перегонки где отдает свое тепло на нагрев сырья.
Расход откачиваемой фракции регулируется прибором поз. FRC-10 с коррекцией от регулятора уровня на 10-12 тарелках колонны К-101 поз. LRCA-3 клапан которого находится на линии подачи фракции 62 - 180 °С в блок AT. Температура откачиваемого продукта измеряется термопарой поз. TR-6. Из блока атмосферной перегонки фракция 62 – 180 °С возвращается с температурой 72 °С охлаждается в воздушном холодильнике ХВ-103 а затем доохлаждается в водяном холодильнике Х-102.
Охлажденная до 40 °С фракция 62 – 180 °С выводится в промпарк установки каталитического риформинга. Расход фракции 62 – 180 °С на выходе с установки фиксируется счетчиком поз. FR-18.
Качество фракции определяется прибором QR-06.
Поддержание теплового режима в кубе колонны К-101 достигается следующим образом:
Часть фракции 180 – 350 °С с куба колонны К-101 забирается насосами Н-10312 и направляется для нагрева в печь П-1012. Расход горячей струи регистрируется расходомером поз. FR-11. Температура низа регистрируется термопарой поз. TR-7. Давление низа измеряется прибором поз. PR-5.
После нагрева в печи до 300 °С «горячая струя» по трансферной линии направляется в колонну К-101 под 32 ректификационную тарелку.
Основная часть фракции 180 – 350 °С из колонны К-101 насосами Н-10212 направляется в Т-103 где отдает свое тепло на нагрев гидрогенизата.
Расход откачиваемой фракции регулируется прибором поз. FRC-9 с коррекцией от регулятора уровня колонны К-101 поз. LRCA-1 клапан которого находится на линии откачки фракции 180 - 350 °С перед теплообменником Т-103. Охлажденная фракция 180 - 350 °С с температурой 125 °С направляется в воздушный холодильник ХВ-102. Температура выхода из воздушного холодильника замеряется термопарой TR-1. Охлажденная до температуры 50 °С фракция 180 – 350 °С (может смешиваться с негидроочищенной фракцией 230 – 350 °С) направляется на склад нефтепродуктов.
Расход фракции 180 – 350 °С на выходе с установки фиксируется счетчиком поз. FR-15. Качество фракции определяется приборами QR-1 QR-2 QR-3 QR-4.
Верхний продукт колонны К-101 - фракция НК – 62 °С поступает с температурой 40 °С в колонну К-102. Экстракционная колонна К-102 предназначена для очистки фракции НК – 62 °С от сероводорода раствором амина с концентрацией не ниже 10%.
Вместе с фракцией НК – 62 °С в колонне К-102 происходит очистка от сероводорода избытка флегмы отпарной колонны К-1 установки каталитического риформинга. Очищаемое сырье подается в нижнюю часть колонны К-102 через распределительное устройство и является «дисперсной фазой».
Регенерированный 10% раствор амина подается в колонну насосом Н-10612 с блока очистки и получения сжиженных газов в верхнюю часть колонны через распределительное устройство и является сплошной фазой.
Постоянство подачи регенерированного раствора амина поддерживается регулятором расхода поз. FRC-14 клапан которого находится на линии подачи амина в колонну К-102.
Уровень вверху колонны регулируется регулятором уровня раздела фаз поз. LRCAHL-7 клапан которого находится на линии откачки амина в блок очистки сжиженных газов.
Измерение уровня внизу колонны производится прибором поз. LRAHL-6.
Измерение давления на верху и внизу колонны производится измерителем давления поз. PR-6 PR-7. Температура колонны измеряется поз. TR-26 TR-27 TR-28.
Очищенная фракция НК – 62 °С с верха колонны поступает в отстойник Е-103 и под собственным давлением направляется в парк на хранение и для дальнейшего использования как компонент для получения товарного бензина
Температура в емкости Е-103 измеряется термопарой поз. TR-9. Уровень регулируется уровнемером раздела фаз поз. LRCAHL-8 клапан которого находится на линии откачки насыщенного раствора амина.
Из емкости Е-103 фракция НК – 62 °С с температурой 40 °С направляется в парк сжиженных газов. Давление регулируется прибором PRC-3. Расход фракции НК – 62 °С на выходе с установки регистрируется счетчиком поз. FR-17. Качество фракции определяется прибором QR-5.
Сброс от предохранительных клапанов всех аппаратов работающих избыточным давлением производится в факельную емкость Е-56 дренаж светлых продуктов - в емкость Е-57 блока AT.
Для управления технологическим процессом возьмем программируемый контроллер предназначенный для построения территориального распределения систем сбора данных и управления обеспечивающий выполнение следующих функций: аналоговый ввод - вывод дискретный ввод – вывод первичное преобразование информации прием команд от удаленной вычислительной системы и передачи в ее адрес преобразованных данных с использованием интерфейса RS – 485 или Ethernet и управление процессом. Программируемый контроллер обозначен на схеме поз. 19-1 на базе ЭВМ поз. 19-2. Все входные сигналы обрабатываются одним программируемым контроллером с передачей данных на ЭВМ для их индикации регистрации печати сигнализации дистанционного управления.
Температура верха колонны контролируется с помощью термопреобразователя поз. 1-1 сигнал которого преобразуется в унифицированный токовый сигнал 4 – 20 мА преобразователем поз. 1-2 с выдачей показаний на ЭВМ. Затем сигнал поступает на регулятор температуры поз. 1-3 реализованный на программируемом контроллере потом управляющий сигнал через электропневматический преобразователь поз. 1-6 поступает на исполнительный механизм поз. 1-7 клапан которого расположен на линии подачи циркуляционного орошения. Также сигнал с преобразователя поз. 1-2 поступает на реализованный на программируемом контроллере компенсатор поз. 1-4 сигнал с которого поступает на регулятор температуры куба колонны поз. 2-3.
Температура куба колонны контролируется с помощью термопреобразователя поз. 2-1 сигнал которого преобразуется в унифицированный токовый сигнал 4 – 20 мА преобразователем поз. 2-2 с выдачей показаний на ЭВМ. Затем сигнал поступает на регулятор температуры поз. 2-3 реализованный на программируемом контроллере потом управляющий сигнал через электропневматический преобразователь поз. 2-6 поступает на исполнительный механизм поз. 2-7 клапан которого расположен на линии подачи топливного газа в печь П-1012. Также сигнал с преобразователя поз. 2-2 поступает на реализованный на программируемом контроллере компенсатор поз. 2-4 сигнал с которого поступает на регулятор температуры куба колонны поз. 1-3.
Температура ввода сырья (на 27 тарелке) контролируется с помощью термопреобразователя поз. 3-1 сигнал которого преобразуется в унифицированный токовый сигнал 4 – 20 мА преобразователем поз. 3-2 с выдачей показаний на ЭВМ. Затем сигнал поступает на регулятор температуры поз. 3-3 реализованный на программируемом контроллере потом управляющий сигнал через электропневматический преобразователь поз. 3-5 поступает на исполнительный механизм поз. 3-6 клапан которого расположен на линии подачи топливного газа в печь П-1011.
Температура бокового погона колонны (на 10 – 12 тарелке) контролируется с помощью термопреобразователя поз. 4-1 сигнал которого преобразуется в унифицированный токовый сигнал 4 – 20 мА преобразователем поз. 4-2 с выдачей показаний на ЭВМ.
Уровень в кубе колонны измеряется сенсором уровня поз. 5-1 сигнал с которого поступает на контроллер уровня поз. 5-2 который преобразует его в унифицированный токовый сигнал 4 – 20 мА с выдачей показаний на ЭВМ. Затем сигнал поступает на регулятор уровня поз. 5-3 реализованный на программируемом контроллере потом управляющий сигнал через электропневматический преобразователь поз. 5-5 поступает на исполнительный механизм поз. 5-6 клапан которого расположен на линии отвода фракции 180 – 350 оС из куба насосом Н-102.
Уровень на отборной тарелке измеряется сенсором уровня поз. 6-1 сигнал с которого поступает на контроллер уровня поз. 6-2 который преобразует его в унифицированный токовый сигнал 4 – 20 мА с выдачей показаний на ЭВМ. Затем сигнал поступает на регулятор уровня поз. 6-3 реализованный на программируемом контроллере потом управляющий сигнал через электропневматический преобразователь поз. 6-5 поступает на исполнительный механизм поз. 6-6 клапан которого расположен на линии отвода фракции 62 – 180 оС насосом Н-104 на установку каталитического риформинга.
Уровень во флегмовой емкости Е-102 измеряется сенсором уровня поз. 7-1 сигнал с которого поступает на контроллер уровня поз. 7-2 который преобразует его в унифицированный токовый сигнал 4 – 20 мА с выдачей показаний на ЭВМ. Затем сигнал поступает на регулятор уровня поз. 7-3 реализованный на программируемом контроллере потом управляющий сигнал через электропневматический преобразователь поз. 7-5 поступает на исполнительный механизм поз. 7-6 клапан которого расположен на линии отвода жидкой части фракции НК – 62 оС в блок ГФУ.
Расход стабильного гидрогенизата подаваемого в колонну контролируется с помощью датчика разности давлений поз. 8-2 методом переменного перепада давлений создаваемого диафрагмой поз. 8-1 с выдачей показаний на ЭВМ.
Расход кубового остатка подаваемого на нагрев в печь П-1012 контролируется с помощью датчика разности давлений поз. 9-2 методом переменного перепада давлений создаваемого диафрагмой поз. 9-1 с выдачей показаний на ЭВМ.
Расход ингибитора подаваемого в шлемовую часть колонны К-101 для подавления коррозии колонны и конденсаторов-холодильников ХВ-1011-7 контролируется с помощью датчика разности давлений поз. 10-2 методом переменного перепада давлений создаваемого диафрагмой поз. 10-1 с выдачей показаний на ЭВМ. Затем сигнал поступает на регулятор расхода поз. 10-3 реализованный на программируемом контроллере потом управляющий сигнал через электропневматический преобразователь поз. 10-5 поступает на исполнительный механизм поз. 10-6 клапан которого установлен на линии подачи ингибитора из емкости Е-55 блока АТ.
Давление в системе «верх К-101 – Е-102» измеряется датчиком давления поз. 11-1 выдающим унифицированный токовый сигнал 4 – 20 мА с выдачей показаний на ЭВМ. Затем сигнал поступает на регулятор давления поз. 11-2 реализованный на программируемом контроллере потом управляющий сигнал через электропневматический преобразователь поз. 11-4 поступает на исполнительный механизм поз. 11-5 клапан которого установлен на линии отвода некондесирующихся газов из емкости Е-102 в блок ГФУ.
Давление в кубе колонны контролируется с помощью датчика давления поз. 12-1 который выдает унифицированный токовый сигнал 4 – 20 мА с выдачей показаний на ЭВМ.
На линии подачи сырья установлен датчик давления поз. 13-1 который в случае падения давления сырья подает дискретный сигнал с сигнализацией на ЭВМ на дискретный электропневматический преобразователь поз. 13-3 и запирает отсекатель на линии подачи сырья поз. 13-5 и отсекатель на линии подачи топливного газа в печь П-1011 посредством электропневматического преобразователя поз. 13-4.
В кубе колонны установлен сигнализатор низкого уровня поз. 14-1 выходной сигнал которого подается на преобразователь поз. 14-3 формирующий дискретный сигнал с сигнализацией на ЭВМ. В случае падения уровня в кубе колонны до критических значений подается сигнал на магнитный пускатель поз. 14-4 и останавливается насос Н-102 на линии отвода фракции 180 – 350 оС. Насос включается при срабатывании датчика нормального уровня поз. 14-2.
На отборной тарелке установлен сигнализатор низкого уровня поз. 15-1 выходной сигнал которого подается на преобразователь поз. 15-3 формирующий дискретный сигнал с сигнализацией на ЭВМ. В случае падения уровня на отборной тарелке до критических значений подается сигнал на магнитный пускатель поз. 15-5 и останавливается насос Н-104 на линии отвода фракции 62 – 180 оС. Насос включается при срабатывании датчика нормального уровня поз. 15-2.
Выбор технических средств автоматизации.
Для работы (электрического питания) каждого из приборов необходимы блоки питания. Т.к. они работают в том числе и контроллер (см. ниже) при напряжении 24 или 36 В то для них возьмем блок питания Метран серии 600 (например: Метран - 608) концерна «Метран».
Общие характеристики блока питания Метран - 608:
количество каналов - 8.
каналы гальванически развязаны.
каждый канал имеет схему электронной защиты от перегрузок и коротких замыканий.
светодиодная индикация включения блока питания по каждому каналу.
блоки питания для монтажа на шине DIN выполнены в европейском стандарте DIN 43700.
Данные блоки питания предназначены для преобразования сетевого напряжения 220В в стабилизированное напряжение 24В или 36В и питания датчиков с унифицированным выходным сигналом. Имеют взрывозащищенное исполнение. Работоспособность при температуре окружающей среды - 20 + 50 0С относительной влажности 45 - 80 % давлении 84 - 107 кПа.
2. Термоэлектрический преобразователь Метран –0553
Для получения значений температуры непосредственно с технологического объекта возьмем преобразователь термоэлектрический Метран серии 055 (например Метран-0553) концерна «Метран».
Назначение: преобразователь термоэлектрический Метран-0553 предназначен для измерения температуры жидких и газообразных химически агрессивных и неагрессивных сред. Чувствительный элемент первичного преобразователя и встроенный в головку датчика измерительный преобразователь преобразуют измеряемую температуру в унифицированный выходной сигнал постоянного тока что даёт возможность построения АСУТП без применения дополнительных нормирующих преобразователей.
Технические характеристики:
возможность измерения в агрессивных средах.
количество чувствительных элементов 1.
диапазон измеряемых температур: 0 + 500 0С.
рабочий спай: изолированный.
климатические условия: до значения температуры воздуха 85 0С.
зависимость: линейная.
выходной сигнал - унифицированный токовый в диапазоне 4 – 20 мА
взрыво- пожаробезопасен.
Назначение: коррозионностойкие датчики давления «Метран-55» предназначены для работы в системах автоматического контроля регулирования управления технологическими процессами и обеспечивают непрерывное преобразование значения измеряемого параметра в унифицированный аналоговый токовый выходной сигнал иили цифровой сигнал в стандарте протокола HART. Датчики работают со вторичной регистрирующей и показывающей аппаратурой регуляторами и другими устройствами автоматики воспринимающими стандартный токовый сигнал. Датчик имеет: непрерывную самодиагностику встроенный фильтр радиопомех внешнюю кнопку установки «нуля».
Для измерения расхода ингибитора и кубового остатка через печь по методу переменного перепада давлений будем применять датчик разности давлений Метран-55-ДД и диафрагму.
измеряемые среды: агрессивные среды с высокой химической активностью (газ с содержанием сероводорода кислоты щёлочи нефтепродукты сырая нефть морская вода).
напряжение питания =24 В.
избыточное давление в трубопроводе до 10 МПа.
предел относительной погрешности 05%.
ряд верхних пределов измерений кПа: 4; 63; 10; 16; 25; 40; 63.
температура окружающего воздуха - 20 + 70 0С.
относительная влажность окружающей среды до 95 %.
устойчив к вибрации и магнитным полям.
Для измерения давления верха и куба колонны применим датчик избыточного давления Метран-55-ДИ.
Предназначен для непрерывного измерения уровня в небольших диапазонах. Буйковые уровнемеры широко применяются в разлиных отраслях промышленности. Конструктивно уровнемер состоит из сенсора уровня серии 249 и электронного контроллера уровня DLC3000. Уровнемер выпускается в различных исполнениях отличающихся материалом деталей сенсора уровня. Поскольку среда в которой работает уровнемер коррозионно активна выберем исполнение из нержавеющей стали 316. Рабочая температура для данного исполнения составляет от –198 до 427 оС. Совместно с сенсорами серии 249 используется контроллер марки DLC3010 характеризующийся герметичным коррозионностойким и взрывобезопасным исполнением. Верхний предел измерения уровня может составлять от 35 до 80 см. Выходной сигнал уровнемера – стандартный токовый в диапазоне 4 – 20 мА и цифровой по протоколу HART. Наличие цифрового выхода существенно облегчает использование уровнемера в АСУ ТП. Прибор оснащен внутренним температурным сенсором для компенсации влияния колебаний температуры окружающей среды. Допускаемая основная погрешность не более 025%. Питание осуществляется постоянным током напряжением 12 – 30 В что положительно сказывается на искробезопасности прибора.
В качестве датчиков реле уровня выберем высокотемпературный сигнализатор уровня жидкости Sensall VHT Sapphire. Датчики Sensall VHT Sapphire идеально функционируют в аэрированных жидкостях вязких коррозионных средах средах с сильным затуханием и в более жестких условиях.
Датчик оснащен системой подавления ложных срабатываний от бурления и вспесков жидкости. Выход реле можно выбрать как нормально замкнутый (НЗ) или нормально разомкнутый (НР).
Рабочая температура сенсора: от -190°С до +160°С.
Максимальное рабочее давление: от -69 кПа до 6895 кПа.
Исходя из значения максимального давления технологического процесса (350 кПа) выберем датчик-реле избыточного давления контактного типа РД-400 фирмы «Метран» назначение и технические данные которого приведены ниже.
Реле давления РД-400 (однопредельные двухпредельные) предназначены для работы в системах контроля регулирования сигнализации избыточного давления и обеспечивают замыкание - размыкание электрической цепи при достижении заданного значения давления уставки.
Преимущества - чувствительный элемент (мембрана) и диски контактирующие с контролируемой средой изготовлены из сплавов 36НХТЮ и 12X18Н10Т соответственно что обеспечивает высокую коррозионную стойкость реле.
Диапазон уставок кПа
Давление перегрузки в течении 1 мин. кПа
Пост. ток коммутируемый контактами А
Напряжение при индуктивной нагрузке В
Напряжение при активной нагрузке В
Температура окружающей среды °С
Относительная влажность
до 95% при температуре 35°С
Вибрация Гц и амплитуда перемещения мм
до 25 Гц не более 01 мм
Диаметр приемной полости мм
В качестве исполнительного механизма я выбираю клапан фирмы SAMSON типового ряда 250. Регулирующие клапаны типового ряда 250 на большие условные проходы иили высокие давления применяются в технологических установках энергетической технике и системах теплоснабжения.
Клапаны выпускаются на условные диаметры от 15 до 500 мм (от 12" до 16") и номинальные давления от 16 до 400 (от класса 150 до класса 2500).
В стандартном исполнении клапаны пригодны для температур от -10 до +220 0С в исполнении с подтягиваемыми высокотемпературными уплотнительными набивками - для температур от -10 до +350 °С с сильфонной или изолирующей частью - для температур от -200 до +550 °С. Наиболее подходящим клапаном для работы в данной среде является проходной клапан типа 254.
Проходной клапан типа 254
Исполнительный клапан для технологических процессов по нормам DIN или ANSI.
корпус клапана из теплоустойчивого холодовязкого или коррозионностойкого стального литья.
условный диаметр от 80 до 500 мм (3" 16")
условное давление от 16 до 400 (класс ANSI 150 .. 2500)
диапазон температур от –200 до 550 оС
конус клапана металлоуплотняющий мягкоуплотняющий или металло-пришлифованный.
Также выпускаются исполнения с дополнительным металлосильфонным уплотнением изолирующей частью обогревательной рубашкой делителем потока для снижения шума или с разгруженным по давлению конусом клапана.
Так как клапан пневматический а у регулятора выходной сигнал токовый мне необходимо на клапан поставить позиционер. В качестве позиционера я выбрал электропневматический позиционер типа 4763 взрывобезопасного исполнения фирмы «Samson». Позиционер обеспечивает заданную координацию положения клапана (регулируемая величина x) и командного сигнала (задающая величина w). Он сравнивает командный сигнал поступающий от регулирующего или управляющего устройства с ходом исполнительного механизма и выдают в качестве выходной величины (y) пневматическое давление исполнительного импульса.
Позиционер имеет следующие особенности:
компактное исполнение требующее минимального технического обслуживания;
любое монтажное положение;
устойчивость к воздействию вибрации;
изменение направления действия;
благоприятная динамическая характеристика;
работа в нормальном диапазоне или в режиме разбивки диапазона;
пропорциональная зона регулирования;
регулируемая подача воздуха;
минимальное потребление вспомогательной энергии.
Общие характеристики:
задающая величина: унифицированный токовый сигнал 4 – 20 мА.
давление воздуха питания: 14 - 6 бар;
диапазон давления исполнительного импульса: 0 - 6 бар.
исполнение для взрывоопасных производственных помещений: искробезопасная цепь с видом взрывозащиты EExiaIICT6 по CENELEC.
диапазон хода с удлиненным рычагом 75 - 90 мм;
направление действия: реверсируемое;
рабочая температура: до 800С.
Данный клапан я выбираю с целью взрыво- пожаробезопасности т.е. проходной клапан типа 254 является пневматическим. Он непосредственно преобразует аналоговый сигнал 4 - 20 мА в пневматический. Он так же подходит под условия измеряемой и окружающей среды (температура кубового остатка 290 0С давление 25 кгссм2 диаметр трубопровода 80 мм).
Управление параметрами будем осуществлять посредством промышленных контролеров IUC9300 компании PEP Modular Computers.
IUC9300 - модульные контроллеры компании PEP Modular Computers на основе мезонинной шины CXC обладают многими возможностями систем VME при заметно меньшей стоимости. Это делает их применение весьма привлекательным для решения многих задач автоматизации производства. Однопроцессорная шина CXC обеспечивает скорость передачи данных до 10 Мбайтсек. В крейте CXC контроллера может устанавливаться до 7 модулей вводавывода. Применение мезонинной технологии CXC позволяет создавать как мощные локальные VME подсистемы так и автономные интеллектуальные контроллеры. IUC9300 способны обрабатывать до 250 каналов вводавывода. Малые геометрические размеры CXC-модулей (100 х 115 мм) обеспечивают наилучшие эксплуатационные характеристики: микропотребление высокую виброударопрочность компактность. Базируясь на технологии «открытых магистрально-модульных систем» IUC9300 полностью программно совместим с системами VME9300 SMART IO и SMART2 сочетая в себе возможности мощного управляющего компьютера реального времени и программируемого логического контроллера - PLC.
Базовое программное обеспечение:
стандартные операционные системы реального времени: OS-9 V
промышленные сети F сетевые протоколы: TCPIP DECnet Prof
промышленные языки программирования PLC-контроллеров IEC-1131.
Средства программирования:
средства разработки для OS-9 V
ISaGRAF - система программирования PLC-контроллеров на промышленных языках в соответствии со стандартом IEC1131-3 для MS-Windows.
Интерфейс промышленной локальной сети ProfiBus позволяет создавать распределенные системы объединяющие интеллектуальные контроллеры различной мощности: VME9300 IUC9300 SMART а также контроллеры других производителей интеллектуальные датчики и исполнительные устройства с интерфейсом ProfiBus.
Фирма PEP Modular Computers (Германия) образованная в 1975 году имеет 26-тилетний опыт в обеспечении высоко-технологичных решений для промышленной автоматизации особенно для рынка встоенных систем реального времени.
Продукция имеет два исполнения: с рабочим температурным диапазоном 0 - 70°С и -40°С - +85°С. Компания сертифицирована по ISO9001. Оборудование имеет сертификат Госстандарта России как средство измерения и Разрешение Госгортехнадзора для применения в автоматизации опасных объектов.
Применение оборудования РЕР можно найти в таких областях как промышленная автоматизация управление движением транспорта автомобильной промышленности транспорте телекоммуникации автоматизации производства тестировании и измерении автоматизации зданий управлении энергетическими установками. Благодаря высокой вибро- и удароустойчивости РЕР оборудование идеально подходит для применения в мобильных приложениях таких как летательные аппараты железнодорожный транспорт в морской аэрокосмической или военно-морской области.
Выбираем контроллер СХМ-SIO6 оснащенный двумя интерфейсами RS232485 для процессорных последовательных портов и четырьмя последовательными каналами (2*MC68681) с интерфейсом RS232422485.
Для микроконтроллера СХМ-SIO6 необходимо дополнительно выбрать модули ввода - вывода для преобразования аналоговых входных сигналов поступающих с первичных преобразователей в цифровые для работы микроконтроллера и обратного преобразования которое осуществляет модуль вывода.
-ти канальный АЦП разрядность - 16 разрядов время преобразования - 25 мкс входной сигнал – унифицированный токовый в диапазоне 4 – 20 мА или напряжение постоянного тока в диапазоне 0 – 5 или 0 – 10 В.
-ти канальный ЦАП разрядность - 12 разрядов выходной сигнал - унифицированный токовый в диапазоне 4 – 20 мА или напряжение постоянного тока в диапазоне 0 – 5 или 0 – 10 В.
встроенный таймер разрядность – 24 разряда.
дискретных каналов ввода максимальное напряжение 60 В максимальный ток 6 мА.
дискретных выходов номинальное напряжение 24 В номинальный ток – 1 А.
входы и выходы гальванически развязаны.
Разработка принципиальной электрической схемы.
На основании функциональной схемы автоматизации с учётом выбранных приборов и средств автоматизации разработана принципиальная электрическая схема регулирования управления и блокировки.
Для регулирования температур верха и куба колонны К-101 используется автономная система автоматического регулирования которая работает следующим образом.
Термопреобразователь BК1N измеряет температуру верха колонны и преобразует ее в унифицированный электрический сигнал постоянного тока в диапазоне 4 - 20 мА. Питание термопреобразователя осуществляется постоянным напряжением 24 В поступающим от блока питания U2. Сигнал с контактов 1 и 2 блока зажимов термопреобразователя ВК1N поступает по соединительной линии на контакты 1 и 2 модуля аналогового ввода A1.1Z многоканального цифрового измерительного преобразователя-контроллера. Значение температуры поступает в регулятор температуры который реализован программным путём в программируемом контроллере. С этого регулятора сигнал посредством модуля аналогового вывода A1.2Z поступает на контакты электропневматического преобразователя A2Y который управляет клапаном подачи циркуляционного орошения.
Термопреобразователь BК2N измеряет температуру в кубе колонны и преобразует ее в унифицированный электрический сигнал постоянного тока в диапазоне 4 - 20 мА. Питание термопреобразователя осуществляется постоянным напряжением 24 В поступающим от блока питания U3. Сигнал с контактов 1 и 2 блока зажимов термопреобразователя ВК2N поступает по соединительной линии на контакты 3 и 4 модуля аналогового ввода A1.1Z многоканального цифрового измерительного преобразователя-контроллера. Значение температуры поступает в регулятор температуры который реализован программным путём в программируемом контроллере. С этого регулятора сигнал посредством модуля аналогового вывода A1.2Z поступает на контакты электропневматического преобразователя A1Y который управляет клапаном подачи топливного газа в печь П-1012.
Автономность системы обеспечивается программно реализованными компенсаторами один из которых преобразует сигнал термопреобразователя BK2N и корректирует сигнал поступающий на преобразователь A2Y а второй осуществляет аналогичную операцию для датчика BK1N и преобразователя A1Y.
Рассмотрим цепи блокировок и сигнализации. Для разделения режимов ручного и автоматического управления предусмотрен ключ управления SA1. Эти цепи питаются от блока питания U4 постоянным напряжением 24 В.
Для реализации блокировки по падению давления сырья используется реле давления P5. Сигнал с его контактов P5.1 поступает на реле напряжения KV5 которое посредством реле KV6 подает питание на электропневматический преобразователь отсекателя на линии сырья YA1 и отсекателя на линии подачи топливного газа в печь П-1011 YA2. Ручное управление реализовано также с участием KV6 кнопками SB3.1 и SB3.2. Кроме того реле KV6 и сигнальная лампа HL5 образуют цепь сигнализации положения отсекателя.
Все модули ввода и вывода питаются от блока питания U1 встроенного в программируемом контролере преобразующего переменное напряжение 220В в постоянное 24 В. Остальные блоки питания (U2 – U4) преобразуют переменное напряжение 220В в постоянное 24В для работы соответствующих устройств. Блок питания U4 питает все цепи блокировок и сигнализации.
В данной работе решена задача выбора технических средств автоматизации фракционирующей колонны К-101 блока ВТ комбинированной установки У1.731. Особенностью выбора является наличие агрессивной среды в технологическом объекте и обеспечение взрыво- и пожаробезопасности каждого из ТСА. Разработаны функциональная и электрическая схемы автоматизации. Предложена автономная система регулирования температуры верха и куба колонны К-101.
У. Болтон. Справочник инженера - метролога. - М.: «Додэка-21» 2002 г.
Постоянный технологический регламент установки У1.731 книга 3. Астрахань-ГАЗПРОМ 1997 г.
Молоканов Ю.С. «Процессы и аппараты нефтегазопереработки» 1978 г.
Кузнецов А. А. «Расчеты процессов и аппаратов нефтеперерабатывающей промышленности» 1974 г.
Титульный лист.doc
Специальность автоматизация технологических процессов и производств
по дисциплине «Проектирование систем управления»
«Разработка системы автоматизации фракционирующей колонны К-101 комбинированной установки У1.731»
Пояснительная записка
студент группы ДХА-51
Рекомендуемые чертежи
- 20.08.2014
- 20.08.2014
- 20.08.2014