Анализ работы редуктора




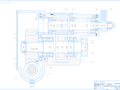
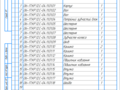
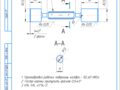
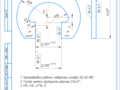
- Добавлен: 24.01.2023
- Размер: 8 MB
- Закачек: 0
Описание
Анализ работы редуктора
Состав проекта
![]() |
![]() |
![]() ![]() ![]() |
![]() ![]() ![]() ![]() |
![]() ![]() ![]() ![]() |
![]() |
![]() ![]() ![]() ![]() |
![]() |
![]() ![]() ![]() ![]() |
![]() ![]() ![]() ![]() |
![]() ![]() ![]() ![]() |
![]() ![]() ![]() ![]() |
![]() ![]() ![]() ![]() |
![]() ![]() ![]() |
![]() ![]() ![]() ![]() |
Дополнительная информация
записка.docx
Крім того якість — це відповідність вимогам стандарту креслення або технічним вимогам.
Підвищення якості машин і механізмів можливе на основі принципів взаємозамінності стандартизації і при впроваджені прогресивних методів і засобів контролю в машинобудуванні.
Мета дисципліни “Взаємозамінність стандартизація та технічні вимірювання” — вивчення основ взаємозамінності стандартизації та метрології здобуття навичок використання і дотримання вимог стандартів виконання розрахунків з вибору посадок типових спряжень метрологічного забезпечення при виготовлені машин.
АНАЛЗ РОБОТИ РЕДУКТОРА
Крутний момент від електродвигуна через клинопасову передачу передається на шків 13 який насаджено на вал 11 за допомогою шпонкового з’єднання. На валу 11 розміщене зубчасте колесо 10 яке з’єднане з валом 11 за допомогою шпонкового з’єднання черв’якам 19 насадженого на валу 1 передається на черв’ячне колесо 5 а отже і на вал 3 на яке це колесо насаджене. Черв’ячне колесо 5 встановлене на шліцьовій частині валу 3. Вал 3 встановлено на двох конічних роликових підшипниках та одному роликовому радіальному підшипнику з короткими циліндричними роликами. Окрім черв’ячного колеса на валу 3 встановлено з натягом зубчасте колесо 15. Воно передає обертальний рух за допомогою шестерні 10 на вал 11 з встановленим на ньому шківом 13. Шестерня та шків 13 встановлені на валу 11 за допомогою шпонкового з’єднання. Сам вал 11 змонтовано у корпусі 6 на двох конічних роликових підшипниках та одному шариковому радіальному.
Зазори А1 А2 забезпечують нормальне функціонування редуктора.
ОБГРУНТУВАННЯ ТА ПРИЗНАЧЕННЯ ПОСАДОК
1 Характеристика та приклади використання посадок з
Посадки з зазором застосовуються для рухомих і нерухомих з'єднань. В таких посадках передбачається гарантований зазор необхідний для забезпечення простоти складання-розбирання взаємного переміщення деталей компенсації теплових деформацій розміщення шару мастила а також компенсації похибок форми і взаємного розташування поверхонь і осей.
Посадки типу He – легкоходові”. Характеризуються значним гарантованим зазором що забезпечує вільне обертання при високих швидкостях та великому навантаженні. Спрощує монтаж при ускладнених умовах - рознесенні опори збільшена довжина з’єднання.
H8e8 – посадки яким надається перевага. Застосовується для підшипників рідинного тертя великих центробіжних насосів блоків зубчастих коліс заднього ходу в вантажних автомобілях стержні вилок переключення передач в автомобілях ходових гвинтів супортів.
1.1 Визначення граничних розмірів валу та отвору для посадки з зазором (D1)
TS = Td + TD = 0021 + 0033 = 0054.
1.2 Схема розміщення полів допусків для посадки з зазором (D1)
1.3 З’єднання в зборі і його деталі для посадки з зазором (D1)
2 Характеристика та приклади використання перехідних посадок (D2)
Перехідні посадки використовують для нерухомих але розбірних з’єднань забезпечуючи при цьому якісне центрування деталей що з’єднуються. В цих посадках можливі як натяги N так і зазори S.
Рисунок 2.1. Приклади призначення посадок з’єднань
Але величини натягів і зазорів малі тому при таких натягах деталі не передають крутні моменти та осьові сили і в основному не потребують перевірки міцності по величині максимального натягу Nmax. При зазорах зміщення осей деталей дуже малі за рахунок чого і забезпечується висока точність центрування.
Перехідні посадки встановлені у відносно точних квалітетах: 5 8 тому що повинні забезпечувати центрування і постійність зусилля при складані.
Посадки типу HjS – щільні”. З перехідних посадок характеризу-ються найбільшою вірогідністю зазора. Призначаються для деталей які потребують частої перестановки тому що при складанні потрібні незначні зусилля (використання дерев’яного молотка).
Приклади використання щільних посадок:
H7jS6 – гільз і стаканів підшипникових вузлів для виробів нормальної
точності невеликих шківів і маховиків.
H7jS5 – підшипникових вузлів підвищеної точності.
H8jS7 – центруючих елементів установки полумуфт двигунів та ін.
2.1 Визначення граничних відхилень розмірів валу та отвору для перехідної посадки (D2)
Ts=TN=TD+Td= 0033 + 002= 0053.
2.2 Схема розміщення полів допусків для перехідної
2.3 З’єднання в зборі і його деталі для перехідної
3 Характеристика та приклади використання посадок з
Посадки з натягом призначені для отримання нероз’ємних і нерозбірних з’єднань. Нерухомість деталей забезпечується за рахунок напружень що виникають в деталях під час складання. Використання цих посадок дозволяє спрощувати конструкцію вузлів.
При складанні таких з’єднань потрібні значні зусилля. Часто для полегшення
складання (особливо при великому натягові і при малій жорсткості
деталі) деталі піддають термічним деформаціям (вал охолоджують а деталь з отвором нагрівають). При цьому підвищується якість з’єднання менше пошкоджуються спряжені поверхні.
Посадки типу Hs і Ht – пресові”. Характеризуються помірними натягами які забезпечують передачу навантажень середньої величини без додаткового кріплення.
Приклади використання пресових посадок.
H7r6 H7t6 – втулки підшипників ковзання при важких и ударних навантаженнях кондукторні втулки постійні шатунні втулки в дизелях зубчасті колеса на проміжному валу в коробці швидкостей вантажних автомашин.
3.1 Визначення граничних відхилень розмірів валу та отвору для посадки з натягом (D3)
TN = Nmax – Nmin = 0068 – 0004 = 0064 мм.
TN = Td + TD = 0039 + 0025 = 0064 мм.
3.2. Схема розміщення полів допусків для посадки з натягом (D3)
3.3. З’єднання в зборі і його деталі для посадки з натягом (D3)
РОЗРАХУНОК ВИКОНАВЧИХ КАЛБРВ КОНТРКАЛБРВ
Виконавчі розміри калібрів розраховують по параметрам: номінальному розміру і квалітету поверхні яку потрібно контролювати вибирають необхідні дані із таблиці. В таблиці прийняті наступні умовні позначення параметрів полів допусків калібрів:
Н (HS) – допуск на виготовлення калібрів для отворів (HS - для калібрів зі сферичними вимірювальними поверхнями);
H1 – допуск на виготовлення калібрів для валів;
Hр – допуск на виготовлення контрольного калібра;
Z Z1 – відхилення середини поля допуску на виготовлення прохідного калібру для отвору (Z) і вала (Z1) відносно граничного розміру виробу;
Y Y1 – допустимий вихід розміру зношеного прохідного калібру для отвору (Y) і вала (Y1) за межу поля допуску виробу;
α α1 – величини для компенсації похибки контролю калібрами отвору (α) і - вала (α1) з розмірами більшими за 180 мм.
1 Визначаємо граничні розміри отвору і вала мм:
2. Визначаємо параметри полів допусків калібрів по таблиці:
- для контролю отвору
Z = 5; Y = 4; α = 0; Н = 4;
- для контролю вала
Z1 = 3; Y1 = 3; α1 = 0; H1 = 4; Hр = 15.
3. Визначаємо виконавчі розміри калібрів за формулами:
а) Калібри для контролю отвору (пробка) мм:
границя зносу ПРз = Dm
б) Калібри для контролю вала (скоба) мм:
границя зносу ПРз = dma
К-З = dmax + Y1 – α1 + 05Hр = 2296+0003–0+000075 = 2296375.
ВИБР РОЗРАХУНОК ПОСАДОК ПДШИПНИКВ КОЧЕННЯ
Підшипники кочення – найбільш розповсюджені стандартні виро-би без яких неможлива робота практично жодної машини. Вони класифікуються по конструкції по тілам кочення по серіям та ін. Якість підшипників довговічність і надійність їх роботи залежить від точності виготовлення самих підшипників та правильного вибору посадок кілець підшипників. Точність приєднувальних розмірів кілець підшипників нормується номінальними D і d та середніми Dm і dm діаметрами.
Вибір посадок кілець підшипників кочення визначається їх типом та характером навантаження кілець. При цьому розрізняють наступні характери навантаження кілець: місцеве циркуляційне і коливальне (рис.4.1).
Рисунок 4.1 Епюра навантаження дорожки кочення при місцевому циркуляційному і коливальному навантаженні.
Місцеве навантаження характеризується постійним по величині і напрямку радіальним навантаженням що передається нерухомому кільцю. Отже під навантаженням знаходиться обмежена ділнка поверхні кільця (рис.4.1.а).
При циркуляційному навантаженні постійне по величині і напрямку навантаження передається кільцю що обертається або обертаюче навантаження сприймається нерухомим кільцем. В цьому випадку послідовно буде навантажена вся поверхня кільця(рис.4.1б).
Коливальне навантаження відбувається коли на кільце діє постійне по величині і напрямку навантаження Pn в поєднанні з обертаючим навантаженням Pb (рис.4.1.в). Отже виникає обертаюче знакозмінне навантаження що сприймається певною ділянкою поверхні кільця. В окремих випадках при певному співвідношенні обертаючого навантаження та постійного можуть виникнути умови що відповідають місцевому або циркуляційному навантаженню.
Для кільця яке має циркуляційне навантаження посадка вибирається по інтенсивності радіального навантаження PR для посадочної поверхні що розраховується із співвідношення:
де R – радіальна реакція в опорі (н); b = B – 2r – робоча ширина посадочного місця; B – робоча ширина підшипника; r – радіус заокруглення кромок посадочних поверхонь підшипника (м); Kn – динамічний коефіцієнт який залежить від характеру навантаження; F – коефіцієнт ослаблення порожнистого вала або тонкостінного корпусу; FA – коефіцієнт нерівномірності розподілу навантаження між рядами роликів в дворядних конічних підшипниках або між здвоєними шарикопідшипниками при наявності осьового навантаження.
1 Призначення та вибір посадок підшипників кочення
Радіальний роликопідшипник №7205 з дод. К.
Конструктивні розміри: d = 25 мм D = 52 мм B = 15 мм r = 15 мм.
Для внутрішнього кільця яке при такій схемі роботи має циркуляційне навантаження розраховуємо інтенсивність цього навантаження на доріжку кочення.
PR = =·1·1·1=6538·103.
Такій інтенсивності навантаження по таблиці дод.М відповідає поле допуску к6. Тоді для внутрішнього кільця підшипника призначаємо наступну посадку
Для зовнішнього кільця підшипникаяке має місцеве навантаження відповідає поле допуску H6. Тоді для зовнішнього кільця підшипника призначаємо посадку.
2 Розрахунок посадок підшипників кочення
Nmin = Dmax – dmin = 25 – 25002 = 0002 мм.
Smin = Dmin – dmax = 52 – 52 = 0 мм.
3 Позначення посадок підшипників кочення
4 Схема розміщення полів допусків кілець підшипників кочення
ПРИЗНАЧЕННЯ ПОСАДОК ДЛЯ ШПОНКОВИХ З’ДНАНЬ
1 Обрунтування вибору посадок для шпонкових з’єднань
Шпонкові зєднання призначенні для зєднання валів між собою за допомогою спеціальних пристроїв (муфт) а також для зєднання з валами осями різних тіл обертання (зубчатих коліс ексцентриків шківів маховиків).
Стандартизовані шпонкові зєднання з призматичними сегментними і клиновими шпонками. Частіше всього застосовується група ненапружених призматичних і сегментних шпонкових зєднань. Використання призматичних шпонок дає можливість більш точно центрувати спряжені елементи і отримувати як нерухомі так і ковзаючі зєднання.
В шпонкових зєднаннях вибір полів допусків шпонки і шпонкових пазів визначається з конструктивних міркувань.
Якщо матеріал втулки піддається обробці протягуванням або калібруванням то з міркувань економічності вибирають по зовнішньому діаметру D зєднань з прямобічним профілем зубців або по діаметру впадини втулки D зєднань з евольвентним профілем зубців.
Поля допусків вала і втулки по центруючому діаметру визначають із умови точності центрування і довговічності.
Шпонки звичайно спрягаються по ширині з валом по нерухомій посадці а з втулками – по одній з рухомих посадок. Натяг необхідний
для того щоб шпонка не переміщувалась при експлуатації а зазор – для компенсації уникнення неточності пазів і їх перекосів.
2 Поля допусків поверхонь шпонкового з’єднання по ширині шпонки
Основні розміри призматичних шпонок і шпонкових пазів на валах і в втулках приймаємо відповідно до (ГОСТ 23360-78)
Номінальні розміри шпонки
Граничні відхилення параметра b (ширина шпонки).
ширина паза вала 8Н9;
3 Розрахунок характеристик посадок шпонки з пазом вала та з пазом втулки
TB = ES – EI = 0036 – 0 = 0036 мм;
TS = TN = TB + Tb = 0036 + 0036 = 0072 мм.
TB = ES – EI = 0098 + 004 = 0138 мм;
TS = TN = TB + Tb= 0138 + 0036 = 0174 мм.
4 Схема розміщення полів допусків для шпонкового з’єднання
Схема розташування допусків шпонкового з’єднання
ВИБР ПОСАДОК ДЛЯ ШЛЦЬОВОГО З’ДНАННЯ
1 Обрунтування вибору посадок для шліцьових з’єднань
Шліцьові з’єднання призначені для передачі крутячих моментів і осьових сил. Порівняно із шпонковими шліцьові з'єднання забезпечують краще центрування і більшу рівномірність розподілу навантажень по висоті зуба шліця передають більші крутні моменти.
Шліцьові з'єднання бувають з прямим евольвентним трикутним профілем.
Розміри елементів шліцьового з'єднання стандартизовані. Шліцьові з’єднання з прямобічним профілем виготовлять за ГОСТ 1139-80 а з евольвентним - за ГОСТ 6033-60.
Шліцьові з'єднання трикутним профілем широкого поширення не набули.
Основні параметри шліцьового з'єднання з прямобічним профілем показано на рис. 6.1.
Шліцьові з'єднання характеризуються зовнішнім діаметром D внутрішнім діаметром d шириною b шліця числом шліців зубів z. 3'єднання бувають трьох серій : легкої середньої і важкої.
Залежно від експлуатаційних і технологічних вимог центрування вала і втулки досягається одним з трьох методів: за зовнішнім діаметром D; за внутрішнім діаметром d і боковими сторонами b шліців.
Центрування за зовнішнім діаметром D рис.6.2а рекомендується тоді коли твердість втулки дає змогу обробляти протягуванням. Цей спосіб найбільш простий і економічний.
Центрування за внутрішнім діаметром d рис. 6.2б доцільне коли втулка має високу твердість і точний розмір можна дістати при шліфуванні діаметра d .
Вал обробляють на шліцьошліфувальному верстаті.
Центрування за боковими сторонами шліців рис. 6.2 в не забезпечує
точного центрування вала і втулки але дає найрівномірніший розподіл сил між
шліцями. Метод центрування рекомендується для з'єднань у механізмах які передають великі крутячі моменти або знакозмінні навантаження. Він забезпечує найменші зазори між боковими поверхнями зубів і западин.
Допуски та посадки. ГОСТ 1139-80 СТ РЕВ 187-75 і СТ РЕВ 88-75 регламентує допуски на розміри D d b. Повний сумарний допуск рис.6.3 дорівнює сумі похибок розміру форми і розміщень поверхонь.
де - відповідно похибки розмірів форми і розміщень .
Рекомендовані поля допусків:
валів - g6 js6 js7 k7 e8 f9 h9 d9 f9.
2 Визначення розмірів елементів шліцьового з’єднання і розшифровка позначень
Розшифровка позначень посадки:
d спосіб центрування по внутрішньому діаметру:
d = 23 мм внутрішній діаметр шліца;
D = 26 мм зовнішній діаметр шліца;
b = 6 мм ширина шліца.
3 Визначення граничних відхилень і граничних розмірів всіх елементів деталей шліцьового з’єднання
TS = Td + TD = 0008 + 0021 = 004 мм.
TS = Tb + TB = 0030 + 0030 = 006 мм.
4 Схема шліцьового з’єднання і розміщення полів допусків для всіх посадок по спряженим поверхнях шліцьового з’єднання
Схема розташування допусків шліцьового з’єднання
РОЗРАХУНОК ПОСАДОК ДЛЯ РЗЬБОВИХ З’ДНАНЬ
Різьбова поверхня утворюється при гвинтовому переміщенні плоского контуру певної форми по циліндричній або конічній поверхні. Всі різьби можна класифікувати по призначенню профілю числу заходів гвинтових поверхонь та направленню обертання контуру.
В машинобудуванні достатньо поширена метрична різьба. Стандартами передбачено таку різьбу для діаметрів від 1 до 600 мм і поділяється на різьбу з нормальним і з мілким кроком. Метрична різьба використовується в основному в якості кріпильної для різьбових з’єднань. Це пояснюється тим що порівняно з іншими різьбами вона забезпечує найбільш високий приведений коефіцієнт тертя.
Профіль метричної різьби характеризується зовнішнім d (D) внутрішнім d1 (D1) та середнім d2 (D2) діаметрами а також кутом профіля 60º та кроком Р.Номінальні значення діаметрів d1 (D1) і d2 (D2) можна підрахувати по значенню d (D) та Р за наступними формулами:
Вибір вимог до точності виготовлення різьбових поверхонь залежить від класу точності різьби: точний середній і грубий. Вимоги до різьбових поверхонь визначаються з умов забезпечення згвинчування болта і гайки їх міцності та характера різьбового з’єднання та ін.
Слід враховувати що відносна довжина згвинчування нормальна (N) мала (S) або велика (L) визначається співвідношенням абсолютної довжини згвинчування з’єднуємих деталей та їх крока і номінального
1 Призначення допусків та посадок для різьбових з’єднань
Вибір плів допусків для деталей різьбових метричних з’єднань визначається в залежності від класу точності. Вибираємо для нашого з’єднання посаду 6Н6g – це посадка з гарантованим зазором для з’єднання з нормальною довжиною
згвинчування і відповідає середньому класу точності різьби.
2 Визначення номінальних та граничних розмірів різьбового з’єднання
Розрахунок номінальних діаметрів різьби.
Діаметру d = 5 мм відповідає нормальний крок різьби Р = 08 мм.
Номінальні розміри середнього і внутрішнього діаметрів метричної різьби визначаємо по формулам:
2.2 Визначаємо граничні відхилення діаметрів різьбових поверхонь.
Визначаємо основні відхилення для діаметру різьби.
верхнє граничне відхилення зовнішнього діаметра esd = – 24 мкм;
верхнє граничне відхилення середнього діаметра esd2 = – 24 мкм;
верхнє граничне відхилення внутрішнього діаметра esd1 = – 24 мкм.
нижнє граничне відхилення зовнішнього діаметра ED = 0 мкм;
нижнє граничне відхилення середнього діаметра EID2 = 0 мкм;
нижнє граничне відхилення внутрішнього діаметра ED1 = 0 мкм.
Визначаємо допуски для діаметрів різьби.
допуск зовнішнього діаметра Td = – 150 мкм;
допуск середнього діаметра Td2 = – 95 мкм.
Допуск внутрішнього діаметра TD1 = 200 мкм;
допуск середнього діаметра TD2 = 125 мкм.
Визначаємо неосновні граничні відхилення для діаметрів різьби.
нижнє граничне відхилення зовнішнього діаметра e
нижнє граничне відхилення середнього діаметра e
нижнє граничне відхилення внутрішнього діаметра eid1 – не нормується.
верхнє граничне відхилення середнього діаметра ESD2 = 118 мкм;
верхнє граничне відхилення внутрішнього діаметра ESD1 = 200 мкм;
верхнє граничне відхилення зовнішнього діаметра ESD – не нормується.
Розрахунок граничних розмірів болта:
Розрахунок граничних розмірів гайки:
3 Схема розміщення допусків профілю та полів допусків для різьбового з’єднання
4 Схема з’єднання в зборі і окремо його деталей з позначенням полів допусків
Розрахунок розмірних ланцюгів
1. Основні положення теорії розмірних ланцюгів.
В будь якій конструкції машини або механізму окремі деталі зв’язані між собою взаємним розміщенням розмірами та допусками на них. Вказаний зв’язок регламентується розмірними ланцюгами.
Розмірний ланцюг сукупність взаємозв’язаних розмірів які утворюють замкнутий контур та визначають взаємне розміщення поверхонь (або осей) однієї або декількох деталей.
Однією з основних властивостей розмірного ланцюга є його замкнутість яка і визначає взаємозв’язок розмірів деталей які входять в розмірний ланцюг.
Кожний з розмірів який утворює розмірний ланцюг називається ланкою. Серед ланок розмірного ланцюга розрізняють одну замикаючу ланку а інші
Замикаюча ланка розмірного ланцюга AΣ безпосередньо не виконується а утворюється автоматично в результаті виконання всіх ланок.
По відношенню до замикаючої ланки складові ланки діляться на збільшуючі із збільшенням яких вихідна ланка збільшується та зменшуюча при збільшенні яких вихідна ланка зменшується.
Вид ланки (збільшуюча або зменшуюча) можна встановити використовуючи правило обходу по контуру. Для цього на схему розмірного ланцюга замикаючій
ланці надають певне направлення яке позначається стрілкою над буквеним
Формулювання задачі:
На рис. 8.1. зображено вузол циліндричного редуктора на валу 4 якого розміщеного в підшипниках кочення 2 розташованих в корпусі 1 розміщений блок зубчастих коліс 3.
Згідно з технічними вимогами до вузла що розглядається необхідно щоб сумарний осьовий зазор між підшипником 5 і кришкою 6 знаходився в межах 03 09 мм.Необхідно визначити допуски та граничні відхилення на розміри тих деталей які визначають величину осьового зазору.
2. Схема розмірного ланцюга.
рис. 8.1. Вузол чотирьох ступінчастого редуктора.
3. Розрахунок розмірного ланцюга методом рівного ступення точності.
3.1. Аналіз конструкції показує що вихідною ланкою є осьовий зазор який залежить від розмірів підшипниківі А5 та розмірів А1 А2 і А4 .
3.2. Будуємо схему розмірного ланцюга ( Рис. 8.1 ).
3.3. Задаємо направлення обходу по контуру і визначаємо зменшуючі та
А1 А2 А4 А6 – зменшуючі;
3.4. Згідно з заданими технічними умовами AΣ = . Тобто номінальне значення вихідної ланки AΣ = 075. Допуск на розмір вихідної ланки ТΣ = AΣmax – AΣmin = 090 – 050 = 040 мм.
3.5. Складаємо рівняння розмірного ланцюга:
AΣі = A5 + (- A1 - A2 + + A3 – A 4 )+ (-AΣ) = 0.
3.6. з конструктивних міркувань прийнято що
Підставляємо прийняті значення розмірів в основне рівняння і дістанемо:
ΣАі =24075+(-20-90-97-7)+(-0.75)=0.
Отже вимога основного рівняння виконана.
Приймаємо що допуск вихідної ланки будемо розподіляти між складовими ланками користуючись методом рівного ступеня точності.
3.7. Визначаємо число одиниць допуску
3.8. По табл. 2 4 ст.14 вибираємо найближче менше число одиниць допуску а = 25 що відповідає Т8 квалітету для цієї ланки ми приймаєм Т9 квалітет він днррівнює ТА5=115мкм.
3.9. По стандарту СТ РЕВ 144-75 призначаємо допуски на всі складові розміри по 9 квалітету
ТA1 = 33 мкм; ТA2 = 54 мкм;
ТA3 = 54 мкм; ТA4 = 22 мкм;
TA5 = 115 мкм; ТA6 = 22 мкм.
3.10. Перевіряємо правильність призначення допусків за формулою:
(33+54+115+54+22+22) ≤ 400;
Отже умова виконується.
3.11. Згідно з рекомендаціями 2 ст. 25 призначаємо відхилення на всі складові розміри. Зокрема на розмір A3 як на ступінчастий відхилення буде симетричним а всі інші розміри як на основний вал тобто в “мінус” тоді:
еs1 = -17.5м км; es2 = -36 мкм;
es3 = -27 мкм; es4 = 0 мкм;
es5 =- 57.5 мкм; es6 = 0 мкм.
3.12. Розраховуємо середні відхилення полів допусків замикаючої та складових ланок за формулою:
3.13. Перевіряємо правильність призначення відхилень за формулою:
=-57.5-(-17.5-27-27-0-0 )=-14;
Отже умова не виконується і тому доцільно ввести “залежну” ланку.
3.14. Нехай залежною ланкою буде A6. Тоді зберігаємо прийняті вище відхилення для всіх ланок крім ланки A6. Враховуючи що ланка A6 – зменшуюча її середнє відхилення визначаємо за формулою:
= EС3 = 0 – 57.5 +44.5+(-0.05) =- 0102 мкм;
3.15. Граничні відхилення залежної ланки визначаються за формулами:
= - 0102 + (54 2 ) = 26.898;
=- 0102 - (54 2 ) =-27.102 .
Таким чином можна записати що
Перевіримо ще раз правильність призначення відхилень за формулою: Таким чином виконані розрахунки дозволили уточнити номінальні значення всіх розмірів які входять у розмірний ланцюг і обрунтовано призначити на них допуски та граничні відхилення.
У цій курсовій роботі:
проаналізовано роботу коробки передач охарактеризовано окремі з'єднання.
Обрунтовано та призначено посадки для D1 D2 38 D3 30 відповідно з зазором перехідну та натягом також зображено для них поля допусків.
Призначено посадку для підшипника кочення
Для внутрішнього кільця –
Для зовнішнього кільця – зображено схеми полів допусків.
Призначено посадки для шпонкового з'єднання шпонка 10х8х35
Розраховано посадку для шліцьового з'єднання та зображено відповідну схему полів допусків.
Розраховано посадку для різьбового з'єднання М8–6H6gта зображено відповідну схему полів допусків та позначення з'єднання в зборі.
Розроблено складальне креслення редуктора специфікація до нього креслення вала гладкого із зазначенням розмірів посадок допусків форми та розташування поверхонь креслення зубчастого колеса
СПИСОК ВИКОРИСТАНО ЛТЕРАТУРИ
Допуски і посадки: Довідник під редакцією Мягкова В.Д. Л. Машинобудування 1982.
Глушич В. О. Переяславський О.М. та ін. «Взаємозамінність стандартизація і технічні вимірювання: методичні рекомендації щодо виконання курсового проекту». В.: Вінницький державний університет 2006 р.
Анурьєв В.. “Справочник конструктора – машиностроителя”
том 1 і 2 М.: “Машиностроение”1982р.
А.О. Желєзна В.О. Кирилович: «Основи ВСТВ». К.:КОНДОР 2004р.
Редуктор.cdw

Калібр-пробка.cdw

Specific2.cdw

Робоче креслення Вала .cdw

Specific1.cdw

Ланцюг 2.cdw

Зубчасте колесо.cdw

поле допуску калібрів.cdw

Зміст.docx
Обрунтування та призначення посадок
1. Характеристика та приклад використання посадки з зазором D1
1.1. Визначення граничних відхилень розмірів валу та отвору для посадки з зазором (D1)
1.2. Схема розміщення полів допусків для посадки з зазором D1
1.3. З’єднання в зборі та його деталі для посадки з зазором D1 ..
2. Характеристика та приклад використання перехідної посадки D2.
2.1. Визначення граничних відхилень розмірів валу та отвору для перехідної посадки D2 .
2.2. Схема розміщення полів допусків для перехідної посадки D2 .
2.3. З’єднання в зборі та його деталі для перехідної посадки D2
3. Характеристика та приклад використання посадки з натягом D3..
3.1. Визначення граничних відхилень розмірів валу та отвору для посадки з натягом D3
3.2. Схема розміщення полів допусків для посадки з натягом D3
3.3. З’єднання в зборі та його деталі для посадки з натягом D3 ..
Розрахунок калібрів для контролю гладких циліндричних поверхонь
Вибір і розрахунок посадки підшипників кочення ..
1. Призначення та вибір посадки підшипників кочення
2. Розрахунок посадки підшипників кочення
3. Позначення посадок підшипників кочення
4. Схема розміщення полів допусків кілець підшипників кочення .
Призначення посадок для шпонкових з’єднань
1. Обрунтування вибору посадок для шпонкових з’єднань
2. Поля допусків поверхонь шпонкових з’єднань по ширині
3. Розрахунок характеристик посадок шпонки з пазом вала та з
4. Схема розміщення полів допусків для шпонкових з’єднань
Вибір посадок для шліцьового з’єднання ..
1. Обрунтування вибору посадок для шліцьових з’єднань .
2. Визначення розмірів шліцьового з’єднання і розшифровка позначень ..
3. Визначення граничних відхилень і граничних розмірів всіх елементів деталей шліцьового з’єднання .
4. Схема розміщення полів допусків для всіх посадок по спряженим поверхнях шліцьового з’єднання
Розрахунок посадок для різьбових з’єднань .
1. Призначення допусків та посадок для різьбових з’єднань ..
2. Визначення номінальних та граничних розмірів різьбового з’єднання ..
3. Розрахунок граничних розмірів болта
4. Розрахунок граничних розмірів гайки
5. Схема розміщення допусків профілю та полів допусків для різьбового з’єднання
6. Схема з’єднання в зборі і окремо його деталей з позначенням
Розрахунок розмірних ланцюгів 22
1. Основні положення теорії розмірних ланцюгів 22
2. Схема розмірного ланцюга 22
3. Розрахунок розмірного ланцюга методом максимуму - мінімум ..23
Список використаної літератури 43
В основу сучасного промислового виробництва покладено масовість. А в умовах масового виробництва широко застосовується спеціалізація і кооперування. Лише таке виробництво здатне задовольняти зростаючі потреби народного господарства підвищити продуктивність праці ефективність і якість вітчизняним та зарубіжним зразкам. Якість — це сукупність властивостей і показників які визначають придатність виробу задовольняти вимоги народного господарства чи населення.
Крім того якість — це відповідність вимогам стандарту креслення або технічним вимогам.
Підвищення якості машин і механізмів можливе на основі принципів взаємозамінності стандартизації і при впроваджені прогресивних методів і засобів контролю в машинобудуванні.
Мета дисципліни “Взаємозамінність стандартизація та технічні вимірювання” — вивчення основ взаємозамінності стандартизації та метрології здобуття навичок використання і дотримання вимог стандартів виконання розрахунків з вибору посадок типових спряжень метрологічного забезпечення при виготовлені машин.
АНАЛЗ РОБОТИ МЕХАНЗМУ
Обертальний рух від валу електродвигуна передається на шків 16 що закріплений на конічному кінці валу 7 за допомогою шпонки 21. Вал 7 змонтовано в корпусі редуктора на підшипниках ковзання 15. На шліцовій частині валу 7 встановлений зубчастий блок 11. При зачепленні зубчастого блоку попарно валу 7 встановлений зубчастий блок 11.При зачепленні зубчастого блоку попарно з зубчастими колесами 9 або 10 змінюються частота обертання валу 7 та насадженої на ньому з натягом зірочки 8. Зубчасті колеса 9 та 10 встановленні на валу 6 за допомогою шпонок. Для запобігання осьового зміщення зубчастих коліс 9 та 10 встановленні втулки 4 12 і 13. Зазорами АΣ1 і АΣ2 забезпечують компенсацію теплових деформацій.
ОБГРУНТУВАННЯ ПРИЗНАЧЕННЯ ПОСАДОК
1 Характеристика та приклади використання посадок з
Посадки з зазором застосовуються для рухомих і нерухомих з'єднань. В таких посадках передбачається гарантований зазор необхідний для забезпечення простоти складання-розбирання взаємного переміщення деталей компенсації теплових деформацій розміщення шару мастила а також компенсації похибок форми і взаємного розташування поверхонь і осей.
Посадка типу Нf – «ходові». Характеризуються помірним гаран –
тованим зазором достатнім для вільного обертання в підшипниках
коввзання при легких та середніх режимах роботи (швидкість до 150 радс) вільного лінійного переміщення деталей та вузлів.
H9f9 H8f8 – підшипники ковзання при великих швидкостях обер–
тання для направлення поршнів і штоків гідроциліндрів центрування кришок циліндрів вал барабана молотилки.
1.1 Визначення граничних розмірів валу та отвору для посадки з зазором (D1)
TS = Td + TD = 0039 + 0039 = 0078.
1.2 Схема розміщення полів допусків для посадки з зазором (D1)
1.3 З’єднання в зборі і його деталі для посадки з зазором (D1)
2 Характеристика та приклади використання перехідних посадок (D2)
Перехідні посадки використовують для нерухомих але розбірних з’єднань забезпечуючи при цьому якісне центрування деталей що з’єднуються. В цих посадках можливі як натяги N так і зазори S.
Рисунок 2.1. Приклади призначення посадок з’єднань
Але величини натягів і зазорів малі тому при таких натягах деталі не передають крутні моменти та осьові сили і в основному не потребують
перевірки міцності по величині максимального натягу Nmax. При зазорах зміщення осей деталей дуже малі за рахунок чого і забезпечується висока точність центрування.
Перехідні посадки встановлені у відносно точних квалітетах: 5 8 тому що повинні забезпечувати центрування і постійність зусилля при складані.
Посадки типу Нk - напружені". Найбільш характерні для перехідних посадок. Характеризуються однаковою вірогідністю отримання натягів і зазорів в з'єднаннях. Забезпечують точне центрування у вузлах з середніми навантаженнями.
Приклади використання напружених посадок.
Н7k6 - посадка якій надається перевага. Застосовується для установки зубчастих коліс на валах редукторів верстатів шківи підшипникові втулки в корпусах втулки в головках шатунів тракторного двигуна.
Н6k5 - поршневий палець в бобишках поршня шестерні на валах прецизійних механізмів.
2.1 Визначення граничних відхилень розмірів валу та отвору для перехідної посадки (D2)
TD = ES – EI = 0030 – 0 = 0030;
TS=TN=TD+Td= 0030 + 0019 = 0049.
2.2 Схема розміщення полів допусків для перехідної
2.3 З’єднання в зборі і його деталі для перехідної
3 Характеристика та приклади використання посадок з
Посадки з натягом призначені для отримання нероз’ємних і нерозбірних з’єднань. Нерухомість деталей забезпечується за рахунок напружень що виникають в деталях під час складання. Використання цих посадок дозволяє спрощувати конструкцію вузлів.
При складанні таких з’єднань потрібні значні зусилля. Часто для полегшення складання (особливо при великому натягові і при малій жорсткості деталі) деталі піддають термічним деформаціям (вал охолоджують а деталь з отвором нагрівають). При цьому підвищується якість з’єднання менше пошкоджуються спряжені поверхні.
Посадки типу Hр – легкоходові”. Характеризуються мінімальним граничним натягом. Застосовується у випадках: 1) для передачі руху при малих навантаженнях; 2) для тонкостінних деталей; 3) для центрування важко навантажених деталей з додатковою фіксацією від відносного зміщення.
Приклади використання пресових посадок.
H7р6 – посадка якій надається перевага. Застосовується для установки зубчастих коліс на валах редукторів (з шпонкою) установчі кільця на валах електродвигунів втулки в корпусі для підшипників ковзання при невеликих навантаженнях.
3.1 Визначення граничних відхилень розмірів валу та отвору для посадки з натягом (D3)
TN = Nmax – Nmin = 0085 – 0036 = 0049 мм.
TN = Td + TD = 0030 + 0019 = 0049 мм.
3.2. Схема розміщення полів допусків для посадки з
3.3. З’єднання в зборі і його деталі для посадки з натягом (D3)
ВИБР РОЗРАХУНОК ПОСАДОК ПДШИПНИКВ КОЧЕННЯ
Підшипники кочення – найбільш розповсюджені стандартні виро-би без яких неможлива робота практично жодної машини. Вони класифікуються по конструкції по тілам кочення по серіям та ін. Якість підшипників довговічність і надійність їх роботи залежить від точності виготовлення самих підшипників та правильного вибору посадок кілець підшипників. Точність приєднувальних розмірів кілець підшипників нормується номінальними D і d та середніми Dm і dm діаметрами.
Вибір посадок кілець підшипників кочення визначається їх типом та характером навантаження кілець. При цьому розрізняють наступні характери навантаження кілець: місцеве циркуляційне і коливальне (рис.4.1).
Рисунок 4.1 Епюра навантаження дорожки кочення при місцевому циркуляційному і коливальному навантаженні.
Місцеве навантаження характеризується постійним по величині і напрямку радіальним навантаженням що передається нерухомому кільцю. Отже під навантаженням знаходиться обмежена ділянка поверхні кільця (рис.4.1.а).
При циркуляційному навантаженні постійне по величині і напрямку навантаження передається кільцю що обертається або обертаюче навантаження сприймається нерухомим кільцем. В цьому випадку послідовно буде навантажена вся поверхня кільця(рис.4.1б).
Коливальне навантаження відбувається коли на кільце діє постійне по величині і напрямку навантаження Pn в поєднанні з обертаючим навантаженням Pb (рис.4.1.в).Отже виникає обертаюче знакозмінне навантаження що сприймається певною ділянкою поверхні кільця. В окремих випадках при певному співвідношенні обертаючого навантаження та постійного можуть виникнути умови що відповідають місцевому або циркуляційному навантаженню.
Для кільця яке має циркуляційне навантаження посадка вибирається по інтенсивності радіального навантаження PR для посадочної поверхні що розраховується із співвідношення:
де R – радіальна реакція в опорі (н); b = B – 2r – робоча ширина посадочного місця; B – робоча ширина підшипника; r – радіус заокруглення кромок посадочних поверхонь підшипника (м); Kn – динамічний коефіцієнт який залежить від характеру навантаження; F – коефіцієнт ослаблення порожнистого вала або тонкостінного корпусу; FA – коефіцієнт нерівномірності розподілу навантаження між рядами роликів в дворядних конічних підшипниках або між здвоєними шарикопідшипниками при наявності осьового навантаження.
1 Призначення та вибір посадок підшипників кочення
Радіальний шарикопідшипник №212 з дод. Ж.
Конструктивні розміри: d = 60 мм D = 110 мм B = 22 мм r = 25 мм.
Для внутрішнього кільцяяке при такій схемі роботи має циркуляційне навантаження розраховуємо інтенсивність цього навантаження на доріжку кочення.
PR = =·1·1·1=906·103.
Такій інтенсивності навантаження по таблиці дод.М відповідає поле допуску js6. Тоді для внутрішнього кільця підшипника призначаємо наступну посадку
Для зовнішнього кільця підшипникаяке має місцеве навантаження відповідає поле допуску Js7. Тоді для зовнішнього кільця підшипника призначаємо посадку.
2 Розрахунок посадок підшипників кочення
S = Dmax – dmin = 60 – 599905 = 00095 мм.
Smax = Dmax – dmin = 110017 – 109985 = 0032 мм.
3 Позначення посадок підшипників кочення
4 Схема розміщення полів допусків кілець підшипників кочення
ПРИЗНАЧЕННЯ ПОСАДОК ДЛЯ ШПОНКОВИХ З’ДНАНЬ
1Обрунтування вибору посадок для шпонкових з’єднань
Шпонкові зєднання призначенні для зєднання валів між собою за допомогою спеціальних пристроїв (муфт) а також для зєднання з валами осями різних тіл обертання (зубчатих коліс ексцентриків шківів маховиків).
Стандартизовані шпонкові зєднання з призматичними сегментними і клиновими шпонками. Частіше всього застосовується група ненапружених призматичних і сегментних шпонкових зєднань. Використання призматичних шпонок дає можливість більш точно центрувати спряжені елементи і отримувати як нерухомі так і ковзаючі зєднання.
В шпонкових зєднаннях вибір полів допусків шпонки і шпонкових пазів визначається з конструктивних міркувань.
Якщо матеріал втулки піддається обробці протягуванням або калібруванням то з міркувань економічності вибирають по зовнішньому діаметру D зєднань з прямобічним профілем зубців або по діаметру впадини втулки D зєднань з евольвентним профілем зубців.
Поля допусків вала і втулки по центруючому діаметру визначають із умови точності центрування і довговічності.
Шпонки звичайно спрягаються по ширині з валом по нерухомій посадці а з втулками – по одній з рухомих посадок. Натяг необхідний для того щоб шпонка не переміщувалась при експлуатації а зазор – для компенсації уникнення неточності пазів і їх перекосів.
2 Поля допусків поверхонь шпонкового з’єднання по ширині шпонки
Основні розміри призматичних шпонок і шпонкових пазів на валах і в втулках приймаємо відповідно до (ГОСТ 23360-78)
Номінальні розміри шпонки
Граничні відхилення параметра b (ширина шпонки).
3 Розрахунок характеристик посадок шпонки з пазом вала та з пазом втулки
TB = ES – EI = – 0018 – (– 0061) = 0043 мм;
TS = TN = TB + Tb = 0043 + 0043 = 0086 мм.
TD = ES – EI = 0021 – (– 0021) = 0042 мм;
TS = TN = TB + Tb= 0042 + 0043 = 0085 мм.
4 Схема розміщення полів допусків для шпонкового з’єднання
Схема розташування допусків шпонкового з’єднання
ВИБР ПОСАДОК ДЛЯ ШЛЦЬОВОГО З’ДНАННЯ
1 Обрунтування вибору посадок для шліцьових з’єднань
Шліцьові з’єднання призначені для передачі крутячих моментів і осьових сил. Порівняно із шпонковими шліцьові з'єднання забезпечують краще центрування і більшу рівномірність розподілу навантажень по висоті зуба шліця передають більші крутні моменти.
Шліцьові з'єднання бувають з прямим евольвентним трикутним профілем.
Розміри елементів шліцьового з'єднання стандартизовані. Шліцьові з’єднання з прямобічним профілем виготовлять за ГОСТ 1139-80 а з евольвентним - за ГОСТ 6033-60.
Шліцьові з'єднання трикутним профілем широкого поширення не набули.
Основні параметри шліцьового з'єднання з прямобічним профілем показано на рис. 6.1.
Шліцьові з'єднання характеризуються зовнішнім діаметром D внутрішнім діаметром d шириною b шліця числом шліців зубів z. 3'єднання бувають трьох серій : легкої середньої і важкої.
Залежно від експлуатаційних і технологічних вимог центрування вала і втулки досягається одним з трьох методів: за зовнішнім діаметром D; за внутрішнім діаметром d і боковими сторонами b шліців.
Центрування за зовнішнім діаметром D рис.6.2а рекомендується тоді коли твердість втулки дає змогу обробляти протягуванням. Цей спосіб найбільш простий і економічний.
Центрування за внутрішнім діаметром d рис. 6.2б доцільне коли втулка має високу твердість і точний розмір можна дістати при шліфуванні діаметра d .
Вал обробляють на шліцьошліфувальному верстаті.
Центрування за боковими сторонами шліців рис. 6.2 в не забезпечує
точного центрування вала і втулки але дає найрівномірніший розподіл сил між шліцями. Метод центрування рекомендується для з'єднань у механізмах які передають великі крутячі моменти або знакозмінні навантаження. Він забезпечує найменші зазори між боковими поверхнями зубів і западин.
Допуски та посадки. ГОСТ 1139-80 СТ РЕВ 187-75 і СТ РЕВ 88-75 регламентує допуски на розміри D d b. Повний сумарний допуск рис.6.3 дорівнює сумі похибок розміру форми і розміщень поверхонь.
де - відповідно похибки розмірів форми і розміщень .
Рекомендовані поля допусків втулок : H7 F8 D9
валів: g6 js6 js7 k7 e8 f9 h9 d9 f9.
2 Визначення розмірів елементів шліцьового з’єднання і розшифровка позначень
Розшифровка позначень посадки:
D спосіб центрування по зовнішньому діаметру:
d = 56 мм внутрішній діаметр шліца;
D = 62 мм зовнішній діаметр шліца;
b = 10 мм ширина шліца.
3 Визначення граничних відхилень і граничних розмірів всіх елементів деталей шліцьового з’єднання
TS = Td + TD = 0030 + 0019 = 0049 мм.
TS = Tb + TB = 0022 + 0022 = 0044 мм.
4 Схема шліцьового з’єднання і розміщення полів допусків для всіх посадок по спряженим поверхнях шліцьового з’єднання
Схема розташування допусків шліцьового з’єднання
РОЗРАХУНОК ПОСАДОК ДЛЯ РЗЬБОВИХ З’ДНАНЬ
Різьбова поверхня утворюється при гвинтовому переміщенні плоского контуру певної форми по циліндричній або конічній поверхні. Всі різьби можна класифікувати по призначенню профілю числу заходів гвинтових поверхонь та направленню обертання контуру.
В машинобудуванні достатньо поширена метрична різьба. Стандартами передбачено таку різьбу для діаметрів від 1 до 600 мм і поділяється на різьбу з нормальним і з мілким кроком. Метрична різьба використовується в основному в якості кріпильної для різьбових з’єднань. Це пояснюється тим що порівняно з іншими різьбами вона забезпечує найбільш високий приведений коефіцієнт тертя.
Профіль метричної різьби характеризується зовнішнім d (D) внутрішнім d1 (D1) та середнім d2 (D2) діаметрами а також кутом профіля 60º та кроком Р.Номінальні значення діаметрів d1 (D1) і d2 (D2) можна підрахувати по значенню d (D) та Р за наступними формулами:
Вибір вимог до точності виготовлення різьбових поверхонь залежить від класу точності різьби: точний середній і грубий. Вимоги до різьбових поверхонь визначаються з умов забезпечення згвинчування болта і гайки їх міцності та характера різьбового з’єднання та ін.
Слід враховувати що відносна довжина згвинчування нормальна (N) мала (S) або велика (L) визначається співвідношенням абсолютної довжини згвинчування з’єднуємих деталей та їх крока і номінального
1 Призначення допусків та посадок для різьбових з’єднань
Вибір плів допусків для деталей різьбових метричних з’єднань визначається в залежності від класу точності. Вибираємо для нашого з’єднання посаду 6Н6g – це посадка з гарантованим зазором для з’єднання з нормальною довжиною згвинчування і відповідає середньому класу точності різьби.
2 Визначення номінальних та граничних розмірів різьбового з’єднання
2.1 Розрахунок номінальних діаметрів різьби.
Діаметру d = 20 мм відповідає нормальний крок різьби Р = 25 мм.
Номінальні розміри середнього і внутрішнього діаметрів метричної різьби визначаємо по формулам:
2.2 Визначаємо граничні відхилення діаметрів різьбових поверхонь.
Визначаємо основні відхилення для діаметру різьби.
верхнє граничне відхилення зовнішнього діаметра esd = – 42 мкм;
верхнє граничне відхилення середнього діаметра esd2 = – 42 мкм;
верхнє граничне відхилення внутрішнього діаметра esd1 = – 42 мкм.
нижнє граничне відхилення зовнішнього діаметра ED = 0 мкм;
нижнє граничне відхилення середнього діаметра EID2 = 0 мкм;
нижнє граничне відхилення внутрішнього діаметра ED1 = 0 мкм.
Визначаємо допуски для діаметрів різьби.
допуск зовнішнього діаметра Td = 335 мкм;
допуск середнього діаметра Td2 = 170 мкм.
Допуск внутрішнього діаметра TD1 = 450 мкм;
допуск середнього діаметра TD2 = 224 мкм.
Визначаємо неосновні граничні відхилення для діаметрів різьби.
нижнє граничне відхилення зовнішнього діаметра e
нижнє граничне відхилення середнього діаметра e
нижнє граничне відхилення внутрішнього діаметра eid1 – не нормується.
верхнє граничне відхилення середнього діаметра ESD2 = 224 мкм;
верхнє граничне відхилення внутрішнього діаметра ESD1 = 450 мкм;
верхнє граничне відхилення зовнішнього діаметра ESD – не нормується.
3 Розрахунок граничних розмірів болта
4 Розрахунок граничних розмірів гайки
5 Схема розміщення допусків профілю та полів допусків для різьбового з’єднання
6 Схема з’єднання в зборі і окремо його деталей з позначенням полів допусків
У цій курсовій роботі:
проаналізовано роботу коробки передач охарактеризовано окремі з'єднання.
Обрунтовано та призначено посадки для D1 D260 D3 відповідно з зазором перехідну та
натягом також зображено для них поля допусків.
Призначено посадку для підшипника кочення
Для внутрішнього кільця –
Для зовнішнього кільця – зображено схеми полів допусків.
Призначено посадки для шпонкового з'єднання шпонка 18х11х100
Розраховано посадку для шліцьового з'єднання та зображено відповідну схему полів допусків.
Розраховано посадку для різьбового з'єднання М20–6H6gта зображено відповідну схему полів допусків та позначення з'єднання в зборі.
Розроблено складальне креслення редуктора специфікація до нього креслення вала гладкого із зазначенням розмірів посадок допусків форми та розташування поверхонь креслення зубчастого колеса
СПИСОК ВИКОРИСТАНО ЛТЕРАТУРИ
Допуски і посадки: Довідник під редакцією Мягкова В.Д. Л. Машинобудування 1982.
Глушич В. О. Переяславський О.М. та ін. «Взаємозамінність стандартизація і технічні вимірювання: методичні рекомендації щодо виконання курсового проекту». В.: Вінницький державний університет 2006 р.
Анурьєв В.. “Справочник конструктора – машиностроителя”
том 1 і 2 М.: “Машиностроение”1982р.
А.О. Желєзна В.О. Кирилович: «Основи ВСТВ». К.:КОНДОР 2004р.
Калібр - Скоба збіль.cdw

Рекомендуемые чертежи
- 24.01.2023
- 04.06.2023
- 09.04.2021
Свободное скачивание на сегодня
- 23.08.2014