Тепловой конструкторский расчет нагревательной (термической) печи


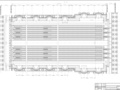
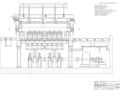
- Добавлен: 25.10.2022
- Размер: 3 MB
- Закачек: 1
Узнать, как скачать этот материал
Подписаться на ежедневные обновления каталога:
Описание
Тепловой конструкторский расчет нагревательной (термической) печи
Состав проекта
![]() |
![]() ![]() ![]() |
![]() ![]() ![]() ![]() |
![]() ![]() ![]() ![]() |
Дополнительная информация
Контент чертежей
Termicheskaya_pech_s_shagayuschim_podom1_ispr.dwg

Termicheskaya_pech_s_shagayuschim_podom2_ispr.dwg

Рекомендуемые чертежи
Свободное скачивание на сегодня
Обновление через: 13 часов 44 минуты