Шестеренчатый насос для продуктов НРМ – 2


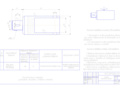
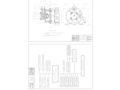
- Добавлен: 25.10.2022
- Размер: 8 MB
- Закачек: 0
Описание
Состав проекта
![]() |
![]() ![]() ![]() |
![]() ![]() ![]() ![]() |
![]() ![]() |
![]() ![]() ![]() ![]() |
![]() ![]() ![]() |
![]() ![]() ![]() |
![]() |
![]() ![]() ![]() |
![]() ![]() |
Дополнительная информация
спецификация.doc
Болт ГОСТ 7805-70 М10 40
группа 544 фак. ТСАПК
Маша 1и2.dwg

Перед сборкой плоскости разьема корпуса покрыть щелочным
Смазка подшипников - "Литол 2Н" ГОСТ 21156-87 или
Солидол - Ж" ГОСТ 1033-79
кисломолочных продуктов
Технические требования
ТОТС.МЭРТО.00 000 СБ
ТОТС.МЭРТО.00 000 Д1
Маша 3.dwg

Принимается на восстановление детали
при износе поверхностей до диаметров
Не принимается на восстановление детали
при наличии трещин и изломов
Шлифованные поверхности вала не должны
иметь рисок и черновин от предыдущей механи-
бочкообразность вала допускается не более 0
Волнистость шлифованных поверхностей
вала допускается не более 0
Технологический маршрут:
Наплавка в среде углекислых
Сталь 45 ГОСТ 4543-71
Технические требования на приёмку в восстановление
Технические требования на выдачу из восстановления
Твёрдость вала должна соответствовать 60 HRC
ТОТС.МЭРТО.00. 011 Р
Cхема базирования детали:
Электроконтактная приварка ленты
Курсовой - ремонт с МОК - рабочий.doc
Таблица 7.1 - Маршрутная карта (МК)
Код наименование операции
Обозначение документа
Код наименование оборудования
Наименование детали сб. единицы или материалы
0 Электроконтактная приварка ленты
Станок токарно-винторезный 1К 62;
Источник питания – трансформатор СТН-500
Установить деталь и закрепить
Трёхкулачковый патрон 7108-002
Отшлифовать поверхность
V=1200 мч; I=10; S=15 ммоб.
Выбор ленты L=90мм a=47мм
V=40 мч; I=1; S=3 ммоб.
V=1400 мч; I=10; S=15 ммоб.
Индикатор многооборотный ГОСТ 9696-82
Маршрутно-операционная карта
Таблица 7.2 - Карта эскизов механической обработки
Основа.doc
В процессе эксплуатации машин и аппаратов происходит потеря их работоспособности главным образом из-за износа и разрушения отдельных деталей. Поэтому необходимо выполнять ряд мероприятий по поддержанию и восстановлению работоспособности оборудования периодичность которых определяется конструктивными особенностями и условиями эксплуатации. Эти мероприятия учитывающие специфику технологий пищевых производств представляют собой систему технического обслуживания и ремонта техники. Такие системы разработаны в каждой отрасли пищевой промышленности.
Одним из основных вопросов ремонтного производства является восстановление изношенных деталей.
Восстановление деталей при ремонте машин и оборудования целесообразно на большинстве ремонтных предприятиях. При этом важным условием является их восстановление до уровня новых при относительно невысокой себестоимости. Это условие является обуславливающим целесообразность процесса восстановления.[2]
Цель данного курсового проекта – ознакомление с основами технологии эксплуатации и ремонта оборудования для переработки продуктов сельскохозяйственного производства с основами технологии восстановления изношенных деталей.[3]
НАЗНАЧЕНИЕ УСТРОЙСТВО И ОПИСАНИЕ РАБОТЫ
Шестерёнчатый насос НРМ-2 с внутренним зацеплением применяют в молокоперерабатывающей промышленности. Применяются в машинах рабочим органам которых является электродвигатель которые применяются для подачи кисломолочных продуктов на заданную высоту.
У шестеренного насоса НРМ-2 с внутренним зацеплением основными рабочими органами являются зубчатый ротор и ведомая шестерня расположенная эксцентрично продольной оси насоса. Часть её зубьев входит в зацепление с зубьями ротора. Шестерня свободно посажена на палец снабженный втулкой.
Корпус насоса с одной стороны закреплен на кронштейне гайкой с другой - закрыт крышкой которая крепится к корпусу четырьмя шпильками. На внутренней стороне крышки имеется серповидный выступ для предупреждения обратного просачивания жидкости с нагнетательной стороны на всасывающую являющийся замыкающей поверхностью переноса порций продукта. В крышке имеются пазы в которых расположены шпильки. Пазы позволяют поворачивать крышку на определенный угол вокруг своей оси и следовательно изменять положение зубьев шестерни находящихся в зацеплении с зубьями ротора относительно входного отверстия. При этом меняется подача насоса. На крышке нанесены риски соответствующие определенной часовой подаче насоса. Таким образом поворот крышки позволяет регулировать подачу насоса в пределах 025 2 м3ч. Между крышкой и корпусом помещены уплотнительные прокладки из картона толщиной 02 мм с помощью которых регулируется необходимый зазор между торцом ротора и крышкой.
Отверстие для ввода жидкости расположено сбоку для вывода—сверху оба заканчиваются патрубками с муфтами для крепления молочных трубопроводов. В случае необходимости корпус с патрубками может быть повернут в нужное положение. При подаче жидкости в рабочую камеру через нагнетательный патрубок необходимо изменить направление вращения ротора.
Длина вала электродвигателя увеличена с помощью наконечника который через сальниковое уплотнение входит в корпус насоса. Уплотнение сальниковой набивки осуществляется гайкой и нажимной втулкой. В качестве сальниковой набивки используют хлопчатобумажный шпур диаметром 5 мм пропитанный животным жиром.
Насос работает следующим образам. Перекачиваемый продукт самотёком поступает в рабочую камеру и заполняет впадины между зубьями ротора и шестерни. Вращаясь зубья переносят перекачиваемый продукт вдоль серповидного выступа а затем начинают входить в зацепление. При этом продукт вытесняется из впадин и поступает в нагнетательный патрубок.
ПОЯСНЕНИЯ К ПРИНЯТОЙ СХЕМЕ РАЗБОРКИ
Для разборки насоса НРМ-2 используют различные инструменты: гайковерты ключи съемники прессы и др.
Разборка насоса начинается:
-после снимается крышка в сборе в следующей последовательности: шестерня 6 втулка 8 палец 7 крышка 5;
-затем снимается прокладка 4;
- затем снимается кронштейн с корпусом в сборе в следующей последовательности: гайка 15 штифт 18; насадка 17; нажимная втулка 16; набивка сальника 14; гайка 13; корпус насоса 2.
Эта самая рациональная схема разборки в которой может быть задействован всего 1 человек. Другой способ невозможен.
ОПИСАНИЕ ВОЗМОЖНЫХ СПОСОБОВ УСТРАНЕНИЯ ДЕФЕКТОВ ШЕЙКИ ВАЛА ПОД ШЕСТЕРНЮ
Вал диаметром 35 мм имеет износ посадочного места под шестерню величина износа – 03 мм на диаметр.
Материал вала – сталь 5. Данный вал находится с насадкой в неподвижном соединении. После восстановления и обработки вал должен иметь наибольшую высоту микронеровностей Rmax = 0032 мкм.
Возможными способами восстановления износа вала с учётом имеющихся установок на ремонтном участке являются: электромеханическая обработка электроимпульсное наращивание наплавка в среде СО2.
Электромеханическая обработка
Электромеханическая обработка- это разновидность способа восстановления деталей давлением отличающийся локальным нагревом восстанавливаемой поверхности с одновременным деформированием разогретого участка.
– высаждающая пластина; 2 – деталь; 3 – сглаживающая пластина; D0 – диаметр после сглаживания; D1 – диаметр после высадки; D2 – начальный диаметр; S – шаг высадки
Рисунок 5 – Схема восстановления деталей электромеханическим способом
Нагревание достигается пропусканием электрического тока через деформирующий инструмент. Высадка увеличивает диаметр детали а последующим сглаживанием получают необходимый (заданный) размер. Для этого деталь устанавливают в центрах токарного станка в суппорте которого закрепляют пружинную державку с твердосплавной пластинкой 1 (рисунок 5). К детали и державке подводят ток силой 300 800 А напряжением 1 ..5 В. При вращении детали и продольной подаче суппорта твердосплавная пластинка 1 деформирует нагретый до температуры 800 900°С металл. В результате чего на поверхности детали образуются спиральные гребни и ее диаметр увеличивается с начального D2 до диаметра Ол. После прохода сглаживающей пластинки 3 получают окончательный диаметр Do. Высаживающие пластины изготавливают из сплава Т15К6 с углом при вершине 60°. Шероховатость рабочей поверхности инструмента (пластины) должна быть не более RA = 004 мм. Сглаживающая пластина изготовляется из того же материала и должна иметь радиус закругления рабочей сферы 80 100 мм.
Для подвода тока к детали на патроне устанавливают медное кольцо и медно-графитовые щетки. В качестве источника питаний используют обычный сварочный трансформатор имеющий 3.. .4 витка независимой дополнительной обмотки проводов сечением 120 мм2. Этим же проводом подводят ток к детали и державке.
Наложение ультразвука на инструмент при сглаживании повышает качество обработки. При этом обработка ведется без подключения тока. Электромеханический способ целесообразен при увеличении диаметра детали не более чем на 015 мм.
Режимы электромеханической обработки приведены в таблице 2.
Таблица 2- Режимы электромеханической обработки
Давление инструмента Н
для закаленных сталей
Окружная скорость детали ммин
Этот способ применяют для восстановления малоизношенных поверхностей валов и осей а также как финишную упрочняющую обработку (без высадки). Его достоинствами являются простота технологии и оборудования высокие качество и производительность низкая себестоимость отсутствие расхода материалов и коробления деталей и др. Он особенно эффективен в условиях перерабатывающих и небольших ремонтных предприятий. Применяют установку ОР-14136-УСХИ-ГОСНИТИ в комплекте с токарным станком [4].
Электроимпульсное наращивание
При электроимпульсном наращивании используется короткий импульс электрической дуги на ограниченном по площади пространстве в результате чего происходит частичное оплавление металла электрода и приваривание к поверхности детали. Материал электрода имеет повышенную хрупкость. Под действием электромагнита происходит отрыв электрода от детали и частиц электрода приварившихся к поверхности детали. Это и обеспечивает наращивание металла электрода на деталь.
Схема установки УМН-6 для электроимпульсного наращивания приведена на рисунке 3.2.
– насос для подачи охлаждающей жидкости; 2 – наращиваемая деталь;
– электрододержатель; 4 – вибратор; 5 – стойка; 6 – груз; 7 – головка установки;
– автотрансформатор; 9 – силовой трансформатор
Рисунок 3.2 – Схема установки УМН-6 для электроимпульсного наращивания
Для наращивания применяется электроимпульсная установка УМН-6 представленная на рисунке 3.2. Стойка 5 закреплена на поперечном суппорте токарно-винторезного станка с высотой центров 150 170 мм. По стойке перемещается головка 7 свободно подвешенная на тросе и уравновешиваемая грузом 6.головки должна превышать массу противовеса для электрода из чугуна на 1 кг а при электроде из стали ХВГ – на 15 кг. Электрододержатель закреплен в патроне с демпфером. Усилие затяжки пружины демпфера регулируется в пределах 30 35 Н. Для получения толстых наращиваемых слоев (до 1 мм) используют электрод из стали ХВГ диаметром 8 10 мм а для тонких слоев (до 03 мм) – чугун марки АМ-8 того же диаметра. Для поддержания нормального процесса электроимпульсного наращивания и охлаждения конца электрода на последний надевается ванночка из текстолита которая опирается на поверхность вращающейся детали поддерживая высоту слоя жидкости у электрода примерно 15 мм.
Расход жидкости 03 04 лмин. Линейная скорость поверхности детали 10 18 ммин. Подача равна 4 5 ммоб. Производительность 85 см²мин.
Наплавка в среде защитных газов
Разработана в 1952 г в ЦНИИТМАШе. Сущность способа заключается в том что наплавка происходит в защитной среде инертных или углеродистых газов. Из инертных газов широкое распространение получил аргон. Его применяют при наплавке высоколегированных хромоникелевых и коррозионно-устойчивых сталей и сплавов на основе меди алюминия и др. Наплавку ведут короткой дугой на постоянном токе обратной полярности с использованием источников питания с жесткой внешней характеристикой.
Сварку и наплавку в среде защитных газов можно вести как плавящимся (рисунок 3.2 а) так и неплавящимся (рисунок 3.2 б) электродом. В последнем случае дуга горит между деталью и электродом а присадочный материал вводят в зону дуги отдельно.
а – плавящимся электродом; б – неплавящимся электродом; 1 – газовое сопло; 2 – плавящийся электрод;
– электрическая дуга; 4 – защитный газ; 5 – деталь; 6 – присадочный пруток; 7 – неплавящийся электрод
Рисунок 4.2- Схемы способов наплавки в среде защитных газов
Примерные режимы обработки углеродистых сталей наплавкой в среде защитных газов приведены в таблице 3.2.
Таблица 3.2 - Режимы наплавки стальных деталей в среде защитных газов
Толщина наплавляемого слоя мм
Скорость наплавки мч
Расход углекислого газа лмин
Толщина наплавленногослоя мм
На рисунке 3.3 приведена одна из принципиальных схем для наплавки в среде защитных газов. Установка имеет газовую аппаратуру механизм подачи проволоки и источник питания. На предприятиях нашла распространение наплавка в среде углекислого газа. Этим способом устраняют дефекты резьбы осей шеек валов и других деталей. Наплавка проводится на постоянном токе обратной полярности. В зависимости от назначения детали материала и вида термической обработки для наплавки рекомендуются определенные марки электродной проволоки. Для наплавки шлицев и шеек валов используют Нп-30ГСА Св-18ХГСА. Проволока должна обязательно иметь раскислитель (кремний марганец).
– баллон с углекислым газом; 2 – осушитель; 3 – подогреватель газа; 4 – газовый редуктор; 5 – расходомер газа;
– регулятор давления газа; 7 – электромагнитный клапан; 8 – аппаратный ящик; 9 – механизм подачи проволоки; 10 – держатель (горелка); 11 – восстанавливаемая деталь; 12 – источник тока
Рисунок 3.3- Схема установки для наплавки в среде защитных газов
РАСЧЁТ ТОЛЩИНЫ СЛОЯ ПОКРЫТИЯ И ПРИПУСКА НА ОБРАБОТКУ
Толщину слоя Ав который необходимо нанести на изношенную поверхность вала определяют с учётом износа детали и припуска на последующую обработку Zпр:
d – размер изношенного вала мм.
Припуск рассчитывается по формуле:
где Сd – дефектный слой мм;
Δа – компенсация пространственных отклонений мм;
Е – погрешность установки детали при обработке мм.
Выполним расчёт припуска используя формулы (4.1) и (4.2) для всех предварительно выбранных способов восстановления деталей при этом расчёт не будем производить для электромеханической обработки потому что наносимый слой при данном способе как токовой отсутствует.[3]
Электроимпульсное наращивание
Наплавка в среде защитных газов:
ВЫБОР РАЦИОНАЛЬНОЙ ТЕХНОЛОГИИ ВОССТАНОВЛЕНИЯ ДЕТАЛИ
Для расчёта затрат на восстановление по предварительно отобранным вариантам использовали компьютерную базу кафедры ТОТС предварительно заполнив бланк исходных данных по всем операциям (приложение 1).
С учётом того что затраты на материалы составляют незначительную часть а накладные расходы обычно принимаются в процентах к заработной плате то целесообразность применения той или иной технологии определена в данном курсовом проекте по минимуму величины заработной платы. Результаты вычислений представлены в приложении 1.
Частота вращения детали n оборотовминуту определяется по формуле:
где V- скорость вращения детали мч;
D- диаметр детали мм.
Основное время на выполнение операции To минут определяется по формуле:
где L-длина восстанавливаемой поверхности мм;
S-продольная подача ммобороты.
Техническая норма времени Тн минут определяется по формуле:
где α-доля вспомогательного времени минут;
-доля дополнительного времени минут;
Тпз- подготовительно- заключительное время минут;
Z-число деталей в партии штук.
Затраты на заработную плату Сзп рубли:
где tc-тарифная ставка соответствующего разряда рабочего.
Проанализировав полученные результаты выбираем как самую рациональную технологию восстановления деталей способом электроконтактной приварки ленты. При данной технологии затраты на заработную плату минимальные.
Для электроконтактной приварки ленты рассчитаем заработную плату для операции нанесения покрытия:
где V- скорость вращения детали 60 мч;
D- диаметр детали 35 мм.
где L-длина восстанавливаемой поверхности 31мм;
S-продольная подача 5 ммоборот.
где α-доля вспомогательного времени 07минут;
-доля дополнительного времени009 минут;
Тпз- подготовительно- заключительное время14 минут;
Z-число деталей в партии 10 штук.
где tc-тарифная ставка соответствующего разряда рабочего 1274 руб.
ПРИНЯТАЯ ТЕХНОЛОГИЯ. РРЕМОНТНЫЙ ЧЕРТЁЖ ДЕТАЛИ
1 Износ отверстия под штифт крепления на валу электродвигателя
После восстановления и обработки оно должно иметь наибольшую высоту микронеровностей Rmax = 008 мм.
Возможными способами восстановления износа вала с учётом имеющихся установок на ремонтном участке является полная заварка места где крепится штифт и установка его на другое место.
2 Износ шпоночной канавки по ширине
Величина износа- 06 мм.
Возможными способами восстановления износа шпоночных пазов с учётом имеющихся установок на ремонтном участке являются: фрезерование шпоночного паза с другой стороны под углом 90°.Можно заварить ручной сваркой и потом профрезеровать.
В данном курсовом проекте были приняты рациональные схема разборки и технология восстановления шейки вала под шестерню вала износа шпоночной канавки и отверстия под штифт крепления.
Решение по схеме разборки было принято исходя из факторов ремонтного производства таких как: недорогое ремонтное оборудование сокращённое время работы и невысокая квалификация рабочих. Все данные факторы прямопропорционально снижают себестоимость ремонта наконечника.
Принятая схема разборки приводит кратчайшую последовательность разделения деталей насоса при этом используются самые простые инструменты такие как гаечный ключ вороток съёмник шпилечный ключ.
Рациональная технология восстановления шейки вала была продиктована производственными обстоятельствами выполнения ремонтных работ: на ремонтном участке имеются установки для электромеханической обработки электроимпульсной наплавки и наплавки в среде СО2.
Рациональной с экономической точки зрения оказалась электромеханическая обработка.
Принятая ремонтная технология обеспечивает восстановление шейки вала с применением минимального колличества оборудования и технологической оснастки. Целесообразность применения электромеханической обработки была определена в курсовом проекте по величине заработной платы. Из всех трёх видов ремонтных работ только у выбранной технологии затраты на заработную плату минимальны.
Исходя из принятых схемы разборки и технологии восстановления шейки вала была составлена технологическая документация в виде маршрутной карты (МК) и карты эскизов механической обработки.
Воловик Е.Л. Справочник по восстановлению деталей. - М.: Колос 1981. – 351 с. ил.
Методические указания. Монтаж эксплуатация и ремонт технологического оборудования. ЧГАУ 2000.
Батищев А.Н. и др. Монтаж эксплуатация и ремонт технологического оборудования перерабатывающих отраслей АПК. Справочник. М.: Информагротех 1997.
Монтаж эксплуатация и ремонт машин в животноводстве. М.: ВО Агропромиздат 1996.
Стандарт предприятия. Проекты (работы) курсовые и дипломные. Общие требования к оформлению СТП ЧГАУ 2-96. Челябинск 1996.
Справочник по машиностроительному черчению. – 14-е изд. перераб. и доп. Под ред. Г.Н. Поповой. – Л.: Машиностроение Ленингр. отд-ние 1981. – 416 с. ил.
Справочник техника-конструктора. – 3-е изд. перераб. И доп. Под ред. Я.А. Самохвалова М.Я. Левицкого В.Д. Григораша - Киев: Технiка 1978 592 с.
Справочник техника-машиностроителя. Под ред. В.В. Данилевского. – М.: Высшая школа 1962. – 645 с. ил.
Бланки исходных данных для расчета на восстановление детали
Наплавка в среде СО2
Окончате-льная обработка
Длина поверхности L мм
Скорость вращения деталиV мч
Продольная подача S обмин
Доля вспомогательного времени α
Доля дополнительного времени
Количество штук в партии Z
Подготовительно- заключительное время Тпз мин
Коэффициент ресурса Кр
Диаметр электродной проволоки d мм
Скорость подачи проволокиVпр ммс
Толщина наращиваемого слоя h мм
Тарифная ставка tc рубличас
Частота вращения деталиn обмин
Основное время на выполнение операции То мин
Техническая норма времени Тн мин
Затраты на заработную плату Сзп рубли
Затраты на восстановление детали Св рубли
Окончательная обработка
Скорость вращения детали
Затраты на восстановление детали Св рубли
Содержание.doc
Схема разборки узла 6
Описание возможных способов устранения деффектов 7
Расчет толщины наращиваемого слоя при восстановлении деталей 13
Выбор рациональной технологии восстановления 15
Принятая технология . Ремонтный чертеж. 18
Технологическая документация 26
Список литературы 20
Рекомендуемые чертежи
Свободное скачивание на сегодня
- 24.01.2023