Щековая дробилка СМД-60А




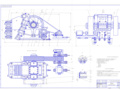

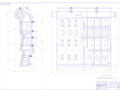

- Добавлен: 25.10.2022
- Размер: 2 MB
- Закачек: 4
Описание
Состав проекта
![]() |
![]() |
![]() |
![]() ![]() |
![]() ![]() ![]() ![]() |
![]() ![]() ![]() ![]() |
![]() ![]() |
![]() |
![]() ![]() |
![]() ![]() ![]() ![]() |
![]() ![]() |
![]() ![]() ![]() ![]() |
![]() |
![]() ![]() ![]() ![]() |
![]() ![]() |
![]() ![]() ![]() ![]() |
![]() ![]() |
![]() ![]() ![]() ![]() |
![]() ![]() |
![]() ![]() |
![]() ![]() ![]() ![]() |
![]() ![]() ![]() ![]() |
![]() ![]() |
![]() |
![]() ![]() ![]() ![]() |
![]() ![]() ![]() ![]() |
![]() ![]() |
![]() ![]() |
![]() |
![]() ![]() ![]() |
![]() ![]() ![]() |
![]() ![]() ![]() |
Дополнительная информация
Спецификация(ГОТОВО).dwg

Эксцентриковый вал в сборе
Механизм регулирования щели
Передняя распорная плита
Задняя распорная плита
Шайба 20.Ст3 ГОСТ 11648-75
Щековая дробилка(многоступ. плита).dwg

Производительность измельчения материала
Наибольший размер загружаемых кусков
Диаметр выходных кусков
Технические требования
В процессе сборки отрегулировать натяжение ремней натяжным
Корпус подшипника заполнить консистентной смазкой
Литол-24-МЛи 412-3 ГОСТ 21150-87
Остальные технические требования по СТБ 1022-96
СМД-60А.01.00.000 СБ
Кожух позиция 7 условно не показан
Перечень.dwg

Шасси агрегата первичного дробления
Агрегат вторичного дробления
Вновь разрабатываемые изделия
СМД-60А.01.00.000 СБ
ПДСУ-60А.00.00.000 ВО
ДСУ(2-ух стад.).dwg

Производительность установки
Тип: двухстадийное дробление
Исходный материал: гранит
Максимальный диаметр загружаемого материала
Диаметр конечного продукта
Степень дробления ДСУ 15
Установочная мощность электродвигателя
Технические требования
Размеры для справок
ПДСУ-60А.00.00.000 ВО
дробильно-сортировочная
Щека подвижная.dwg

Точность отливки 7-8 ГОСТ 26645-85
Неуказанные уклоны 2 5
Неуказанные радиусы 3 5 мм
Остальные технические требования к отливке по ГОСТ 26358-84
Остальные технические требования по СТБ 1014-95
Шатун.dwg

Точность отливки 7-8 ГОСТ 26645-85
Неуказанные радиусы 3 5 мм
Остальные технические требования к отливке по ГОСТ 26358-84
Остальные технические требования по СТБ 1014-95
Ось.dwg

Остальные технические требования по СТБ 1014-95
Распорная плита.dwg

Неуказанные литейные радиусы
Остальные технические требования на отливку по ГОСТ 26358-84
Остальные технические требования по СТБ 1014-95
Шкив.dwg

Неуказанные литейные радиусы
Остальные технические требования к отливке по ГОСТ 26358-84
Остальные технические требования по СТБ 1014-95
Спецификация(испр).dwg

Подвижная щека(ИСПР).dwg

Остальные технические требования по СТБ 1022-96
СМД-60А.01.02.000 СБ
Титульный.docx
Высшего профессионального образования
«Белорусско-Российский университет»
Кафедра ”Строительные дорожные подъемно-
транспортные машины и оборудование
Дробильно-сортировочная установка
«Строительные дорожные и мелиоративные машины»
СМД-60А.01.00.000 ПЗ
Пояснительная записка
Записка(ИСПР).docx
Необходимая интенсификация процесса измельчения может быть достигнута только на основе глубоких знаний как принципа действия и конструкции соответствующего оборудования так и особенностей его эксплуатации.
Целью настоящего курсового проекта является ознакомление с
назначением областью применения и классификацией ДСУ и дробилок а также проектирование и методика расчета щековой дробилки СМД-60А
с простым движением щеки.
Назначение область применения и классификация ДСУ и дробилок
Передвижная дробильно — сортировочная установка (ПДСУ) — комплекс оборудования предназначенного для первичной переработки и подготовки добытой горной массы к промышленному использованию включающее в себя дробилки крупного и среднего дробления грохоты конвейеры и т. д. позволяющее осуществлять поточную технологию и комплексную механизацию открытых и подземных работ.
Характеристики передвижных дробильно — сортировочных установок:
производительность — до 270 тч;
общий вес — от 30000 кг;
размер входного материала — от 80 мм;
размер входного отверстия дробилки — от 900х578 мм;
объем загрузочного бункера — от 4 м3;
диаметр ротора — от 1200 мм;
ширина ротора — от 950 мм;
мощность двигателя — от 220 кВт.
Применение передвижных дробильно — сортировочных установок:
осуществление поточной технологии обогащения породы;
комплексная механизация открытых и подземных горных работ.
Рабочие инструменты передвижных дробильно — сортировочных установок:
дробилки крупного дробления;
дробилки среднего дробления;
Классификация передвижных дробильно — сортировочных установок:
а) по производительности
передвижные дробильно — сортировочные установки малой производительности (до10тч);
передвижные дробильно — сортировочные установки средней производительности (до 50тч);
передвижные дробильно — сортировочные установки большой производительности (от 50тч);
б) по виду исполнения
перемещаемые передвижные дробильно — сортировочные установки;
самоходные передвижные дробильно — сортировочные установки;
сборно — разборные передвижные дробильно — сортировочные установки;
в) по числу агрегатов
одноагрегатные передвижные дробильно — сортировочные установки;
двухагрегатные передвижные дробильно — сортировочные установки;
многоагрегатные передвижные дробильно — сортировочные установки;
г) по виду привода машин
передвижные дробильно — сортировочные установки с электрическим приводом;
передвижные дробильно — сортировочные установки с дизельным приводом;
передвижные дробильно — сортировочные установки с комбинированным приводом.
Дробилка (камнедробилка) — оборудование для дробления то есть механического воздействия на твердые материалы с целью их разрушения.
Пригодны для разрушения материала на куски меньшего размера.
Разделяют в зависимости от крупности дробленного материала на
дробилки крупного среднего и мелкого дробления. Условное деление по крупности выглядит следующим образом:
Таблица 1.1 – Деление дробилок по крупности дробленого материала
Крупность исходного мм
Крупность готового мм
По применению разделяют дробилки для:
твердых горных пород;
мягких горных пород;
продуктов и отходов металлургического производства;
твердых бытовых отходов;
биологических отходов.
В зависимости от назначения и соответственно сложности задачи существуют разные конструкции реализующие следующие принципы дробления (рисунок 1.1):
разрезание или разрыхление;
ударное воздействие (молотки отбойные плиты);
ударное воздействие («свободный удар» удар «камень о камень»).
Рисунок 1.1 – Принципы дробления
Соответствие способов механического разрушения материалов и дробилок в которых применён тот или иной принцип представлено на рисунке 1.2.
Рисунок 1.2 Способы механического разрушения материалов реализуемые в дробилках и мельницах.
По конструкции дробилки делятся на:
молотковая дробилка;
Также к дробильным машинам относятся шаровые мельницы и вибрационные мельницы.
Каждая из этих дробилок также имеет свою классификацию.
Щековые дробилки имеют три разновидности:
щековая дробилка с простым движением щеки;
щековая дробилка со сложным движением;
щековая дробилка с роликом (дробилка серии «ЩЕDR»).
Конусные дробилки делят на:
конусные дробилки крупного дробления в двух исполнениях: с одним приводом с двумя приводами;
конусные дробилки редукционного (вторичного крупного) дробления;
конусные дробилки среднего дробления в двух исполнениях камеры дробления: грубого дробления тонкого давления;
конусные дробилки мелкого дробления в двух исполнениях камеры дробления: грубого дробления тонкого давления.
Молотковые дробилки делят на:
однороторные нереверсивные молотковые дробилки с колосниковыми решётками;
однороторные нереверсивные молотковые дробилки без колосниковых решёток;
двухроторные молотковые дробилки с решётками;
двухроторные реверсивные дробилки с решётками;
двухроторные реверсивные дробилки с решётками.
Валковые дробилки делят на:
валковые дробилки крупного дробления;
валковые дробилки среднего дробления;
валковые дробилки мелкого дробления.
Шаровые мельницы делят на:
шаровые мельницы сухого помола;
шаровые мельницы мокрого помола.
По способу установки и возможности передвижения дробилки различают:
мобильные на колёсном шасси;
мобильные на гусеничном шасси.
Анализ научно-технической литературы и патентный обзор
1 Анализ научно-технической литературы
Щековые дробилки применяют для крупного и среднего дробления различных материалов во многих отраслях народного хозяйства.
Они способны разрушать нерудные материалы практически всех разновидностей. Главным параметром щековых дробилок является размер (ширина и длина В×L) приемного отверстия камеры дробления образуемой подвижной и неподвижной щеками. Отечественная промышленность выпускает дробилки с размерами приемного отверстия B×L (мм): 160×250 250×400 250×900 400×900 600×900 900×1200 1200×1500 1500×2100 2100×2500.
Принцип работы щековой дробилки основан на сжатии рабочими поверхностями (щеками) материала что приводит к возникновению больших напряжений сжатия и сдвига разрушающих материал. На рисунке 2.1 показан принцип работы щековой дробилки.
Рисунок 2.1 – Принципиальная схема щековой дробилки
Одна из щек дробилки делается неподвижной. Вторая щека крепится на шатуне обеспечивающем перемещение верхнего края щеки так что щека совершает качающееся движение. Вал шатуна приводится во вращение через клиноременную передачу от двигателя (электрический дизельный). На этом же валу крепится второй шкив играющий роль маховика и противовеса для основного шкива. Нижний край подвижной щеки имеет возможность регулировки положения в горизонтальном направлении (механический привод или гидравлический привод) которое влияет на ширину минимальной щели определяющую максимальную крупность материала на выходе из дробилки. Щеки образуют клинообразную форму камеры дробления в которой материал под действием силы тяжести и после разрушения продвигается от верхней части в которую загружаются крупные куски до выходной (разгрузочной) щели. Боковые стенки в процессе дробления не участвуют. Сейчас применяют щековые дробилки простого и сложного качения щеки принципиальные схемы которых показаны на рисунке 2.2.
а) - дробилка с простым движением щеки (ЩДП) б) - дробилка со сложным движением щеки (ЩДС).
Рисунок 2.2 Принципиальные схемы щековых дробилок
В дробилках с простым движением щеки движение от кривошипа к подвижной щеке передается кинематической цепью. При этом траектории движения подвижной щеки представляют собой или прямые линии или части дуги окружности.
В дробилках со сложным движением щеки кривошип и подвижная щека образуют кинематическую пару. В этом случае траектории движения точек подвижной щеки представляют собой замкнутые кривые чаще всего эллипсы.
Рассмотрим описания изобретений к патентам (приложение А).
Изобретение относится к дроблению полезных ископаемых а именно к щековым дробилкам и может быть использовано в промышленности стройматериалов и других горнодобывающих отраслях.
Щековая дробилка содержащая корпус неподвижную щеку подвижную щеку привод колебаний последней дробящие плиты с рифлениями отличающаяся тем что с целью повышения производительности дробления мёрзлых и налипающих пород плиты снабжены стержнями вставленными во впадины между рифлениями и кинематически связанными с приводом с возможностью продольных периодических перемещений.
Конструктивная схема изобретения представлена на рисунке 2.3.
– стержни 2 – впадины 3 – коромысло 4 – рычаг 5 – шатун 6 – кривошип 7 – тяга 8 9 – неподвижная и подвижная щёки
Рисунок 2.3 – Схема дробилки
В процессе работы дробилки порода измельчается в камере между дробящими плитами щёк 8 и 9. Когда между ними образуется спрессованный ком примерзающий к щеке 8 при отходе последней стержни 1 перемещаясь во впадинах 2 (как направляющих) нарушают связь массы с дробящей поверхностью плит. В результате предотвращается забивание камеры дробления и связанные камеры дробления и связанные с этим перебои в работе дробилки.
Изобретение относится к технике дробления полезных ископаемых и твердых материалов в частности к щековым дробилкам.
Щековая дробилка включающая сварную раму выполненную заодно с неподвижной щекой с футеровкой и с подвижной щекой с футеровкой установленный в подшипниках вал с эксцентриком и насаженной на эксцентрик головкой шатуна шкивы клиноременной передачи отличающаяся тем что футеровки неподвижной и подвижной щек с тыльной стороны имеют полости для разгрузки продуктов а футеровки обеих щек снабжены сквозными отверстиями для непрерывного выноса в полости из рабочей камеры глинистой массы исключающими её накопление в рабочей зоне дробилки.
Конструктивная схема изобретения представлена на рисунке 2.4.
– рама 2 – неподвижная щека 3 5 – футеровки 4 – подвижная щека 6 – ось 7 – вал 8 – шатун
– шкив 10 – клиноременная передача 11 – сухари 12 13 – распорные плиты 14 15 – вкладыши
– упор 17 – винт 18 – сквозные отверстия 19 - полость
Рисунок 2.4 – Схема дробилки
Исходный крупнокусковой материал загружается в рабочую зону дробилки
образованную неподвижной 2 и подвижной щекой 4которые имеют сквозные отверстия18. В процессе дробления глинистые материалы под давлением загружаемого материала и подвижной щеки дробилки выносятся за пределы рабочей камеры через сквозные отверстия18 а дробленый продукт из рабочей камеры выносится через выпускное отверстие. Сохранность переизмельчения ранее раскрытых драгоценных металлов во время интенсивного дробления осуществляется путем получения их через сквозные отверстия на футеровках подвижной и неподвижной щеки на полость 19 с тыльной стороны футеровок. Таким образом предложенное техническое решение позволяет снизить потребляемую энергию и затраты на организацию производства также повысить эффективность дробления при интенсивном дроблении и измельчении высокоглинистых руд для последующего эффективного их извлечения физико-химическими методами обогащения.
Изобретение относится к дробильному оборудованию а именно к щековым дробилкам и может быть использовано при дроблении различных горных пород - руд и нерудных минералов в том числе со слоистой структуройпри циклично-поточной технологии обработки месторождений открытым способом и в подземных условиях.
Щековая дробилка содержащая станину неподвижную и подвижную щеки выполнена с подвижной щекой ступенчатой формы при этом угол захвата верхней ступени камеры дробления принят меньшим допустимой величины отличающаяся тем что нижерасположенные ступени размещены со смещением их верхних кромок в сторону противоположную от неподвижной щеки с углами захвата не превышающими допустимую величину а геометрические параметры камеры дробления определяются следующими соотношениями:
где h - высота переходного участка между смежными ступенями;
а - минимальное расстояние между нижними кромками ступеней и
При этом угол наклона к горизонту переходного участка между
смежными ступенями принят равным углу захвата упомянутых выше ступеней.
Конструктивная схема изобретения представлена на рисунке 2.5.
– станина 2 – неподвижная щека 3- подвижная щека 4 – камера дробления 5 6 – съёмная футеровка подвижной и неподвижной щёк 7 – верхняя ступень камеры дробления 8 9 – нижерасположенные ступени камеры дробления 10 11 – переходные участки между ступенями 12 – куски дробимого материала 13 14 – приёмное и разгрузочное отверстие дробилки.
Рисунок 2.5 – Щековая дробилка с подвижной щекой ступенчатой формы
При движении подвижной щеки 3 и подаче подлежащей дроблению горной породы в дробилку происходит постепенное сокращение поперечных размеров кусков 12 горной породы с ее продвижением вниз по камере дробления 4. При этом при подаче кусков 12 горной породы через приемное отверстие 13 в пространство между неподвижной щекой 2 и верхней ступенью 7 подвижной щеки 3 происходит разрушение куска 12 без его выталкивания вверх. При продвижении раздробленной горной породы вниз под действием собственного веса ее куски 12 попадают в пространство камеры дробления 4 между неподвижной щекой 2 и ступенью 8. При перемещении подвижной щеки 3 в сторону неподвижной щеки 2 происходит следующий этап разрушения кусков 12 с сокращением их поперечных размеров. При этом при сдавливании кусков 12 ступенью 8 (наклоненной под большим углом чем угол α наклона ступени 7) подвижной щеки 3 исключается не только выталкивание кусков 12 вверх но куски 12 дополнительно получают силовой импульс от переходного участка 10 направленный вниз что способствует ускоренному продвижению дробимой породы в сторону разгрузочного отверстия 14 дробилки аналогичным образом происходит дробление горной породы в пространстве камеры дробления 4 между неподвижной щекой 2 и ступенью 9 подвижной щеки 3. Техническим результатом изобретения является увеличение пропускной способности щековой дробилки при гарантированном дроблении и прохождении горной породы в том числе со слоистой структурой в камере дробления без увеличения высоты дробилки.
3Описание принятого решения
На основании проведённого анализа научно – технической литературы и патентного обзора принимаем следующее решение по усовершенствованию щековой дробилки: подвижную щеку дробилки выполним ступенчатой формы что позволит увеличить пропускную способность щековой дробилки при гарантированном дроблении и прохождении горной породы в том числе со слоистой структурой в камере дробления без увеличения высоты дробилки. Принятую разработку представим на рисунке 2.6.
Рисунок 2.6 – Ось в сборе
Выбор основных параметров
1 Определение угла захвата
Со стороны рабочих органов машины на кусок материала
по нормали к контактирующим поверхностям действуют активные
силы Q (рисунок 3.1) равнодействующая которых равна:
где α– угол захвата.
Рисунок 3.1 – Схема для определения угла захвата
Эта сила стремится вытеснить кусок из камеры дробления. Силы
трения между рабочими органами машин и куском должны удерживать его. Таким образом гарантированный захват куска будет обеспечен при условии что силы трения будут больше выталкивающих сил откуда следует что:
Выразив коэффициент трения между куском и рабочей поверхностью через угол трения φ т.е. f = tg(φ) получим что суммарный угол захвата должен быть меньше двойного угла трения:
Следовательно условие захвата справедливо и последующее
дробление возможно когда угол захвата равен или меньше двойного
угла трения. При коэффициенте трения для гравия f=022 получим что угол трения равен: = arctg f = arctg 022=124. Так как 2 то
24 = 248. Принимаем угол захвата =20°.
2 Определение угловой скорости частоты вращения эксцентрикового вала
Для измельчения материала необходимо выполнение условия дробления: ход щеки S в точке контакта с куском должен обеспечить такую его деформацию которая вызывает разрушение куска т.е.
где d максимально допустимый размер куска;
относительная деформация сжатия.
Относительная деформация сжатия определяется по формуле:
где сж предел прочности дробимого материала при сжатии
E модуль продольной упругости.
Вследствие нестабильности физико-механических свойств измельчаемых материалов неопределенности формы кусков и их взаимодействия с рабочими органами дробилки ход сжатия выбирают с
большим запасом по опытным данным.
Ход сжатия определим по формулам 3.6 3.7 и 3.8.
Ход щеки в верхней части камеры дробления равен:
где В – ширина приёмного отверстия.
Ход щеки в нижней части камеры дробления равен:
где b – ширина выходной щели.
Средний ход щеки равен:
Определим угловую скорость эксцентрикового вала по формуле:
Частота вращения эксцентрикового вала будет равна:
Значения частоты вращения эксцентрикового вала следует уменьшить на
75%. Это связано с тем что в исходном материале имеется
значительная доля кусков размером меньшим ширины выходной щели и целесообразно увеличить время отхода щеки чтобы мелкие частицы успели выпасть из верхних зон камеры дробления. Тогда получим:
3 Определение конструктивных параметров загрузочного отверстия
Схема для расчета основных параметров щековой дробилки представлена на рисунке 3.2
Рисунок 3.2 – Схема для расчёта параметров дробилки
Ширина загрузочного отверстия расстояние между щеками определим по формуле:
где - максимальный размер загружаемых кусков
Тогда ширина отверстия равна:
Принимаем ширину отверстия В = 700 мм.
Высота (глубина) загрузочного отверстия равна:
где В – ширина загрузочного отверстия м
Ширина щели определяется по формуле:
где - размер куска после дробления ()
Тогда высота загрузочного отверстия равна:
Принимаем высоту загрузочного отверстия Н = 1200 мм.
Длина загрузочного отверстия (подвижной щеки) равна:
Принимаем длину загрузочного отверстия L = 1600 мм.
Остальные размеры основных элементов механизма щековой дробилки определяются конструктивно.
Расчёт основных параметров
Схема для расчёта мощности дробилки представлена на рисунке 4.1.
Рисунок 4.1 - Схема для расчёта мощности дробилки
Мощность привода дробилки определим по формуле:
где - предел прочности материала ;
L – длина загрузочного отверстия L = 16 м;
n – частота вращения вала n = 253 обс;
Е – модуль упругости материала ;
D – диаметр исходного материала D = 06 м;
d – диаметр готового материала d = 013 м.
Тогда мощность привода равна:
Принимаем к установке защищенный от пыли двигатель мощностью
7 кВт типа АИР 225М4 (1470 обмин).
2 Расчёт производительности
Схема для определения производительности представлена на рисунке 4.2
Рисунок 4.2 – Схема для определения производительности
Производительность дробилки определим по формуле:
где –коэффициент разрыхления готового продукта (=03 065)
L – длина камеры дробления L=16 м;
S – ход подвижной щеки S=006 м;
d - диаметр выходного куска d=013 м;
α – угол захвата α=20;
n- частота вращения вала n=253 с.
Расчёты на прочность
Задача расчета - проверка прочности основных деталей дробилки по усилиям возникающим в деталях во время работы для определения которых исходной величиной является потребная мощность
Расчёт подвижной щеки.
Расчет сил в элементах конструкций щековых дробилок выполняется по нагрузке на подвижную щеку.
Из конструктивных соображений принимаем: величину эксцентриситета r=25 расстояние от центра оси подвеса подвижной щеки до точки касания с дробимым куском а1=50 мм и от оси подвеса до точки приложения силы Т действующей вдоль распорной плиты l1=130 мм. Также необходимо учесть что при дроблении прочных материалов нагрузку на единицу активной площади дробящей плиты следует принимать q 27 МПа. Нагрузка на поверхность дробящей плиты распределяется приблизительно равномерно поэтому равнодействующую сил дробления Q можно приложить к станине и подвижной щеке в точках соответствующих середине высоты камеры дробления (рисунок 5.1). Для предотвращения ложного срабатывания предохранительных устройств коэффициент превышения номинальной нагрузки принимают равным 15. Расчетная нагрузка действующая на подвижную щеку определяется по формуле:
где Н и L – соответственно высота и длина камеры дробления м;
q – нагрузка на единицу активной площади дробящей плиты МПа.
Тогда расчетная нагрузка действующая на подвижную щеку будет равна:
Рисунок 5.1 – Схема сил действующих на подвижную щеку дробилки
Подвижную щеку дробилки с простым движением рассчитывают
на изгиб от действия силы Q и растяжение от силы N.
Сила N рассчитывается по формуле:
При переходе шатуна из нижнего положения в верхнее когда подвижная щека оказывает давление на дробимый материал в шатуне возникает растягивающее усилие Р. Это усилие изменяется от нуля при нижнем положении шатуна до максимального значения Рmax в верхнем положении. Можно считать что усилие в шатуне возрастает по закону прямой пропорциональности. Среднее значение этого усилия
Работа выполняемая этой силой за один оборот вала
А = Рср2r =2 r = Рmaxr Дж (5.4)
Мощность равна работе деленной на время пол-оборота:
Зная что Nэл.дв=45 кВт при КПД передачи =075 мощность потребляемая щековой дробилкой Nдр=45075=3375 кВт.
Находим Рmax по формуле:
Учитывая ударный характер нагрузки и возможность попадания в дробилку недробимых предметов принимаем (по практическим данным) величину расчетного усилия для шатуна в 34 раза больше чем Рmax т. е.
Ppасч =35249723=874030 Н
Чтобы уменьшить неуравновешенность дробилки вес шатуна должен быть как можно меньше. Для изготовления шатуна берем высококачественную сталь.
Площадь поперечного сечения шатуна при [р]=110 МПа будет равна:
S 79510-3 м2=79457 мм2.
По конструктивным соображениям принят шатун с поперечным сечением 8000 мм2 имеющий значительно больший запас прочности. Длину головки шатуна принимаем 150 см.
Крышку подшипника охватывающего эксцентриковый конец вала крепим к шатуну шестью болтами из стали Ст5 с допускаемым напряжением на растяжение [р]130 МПа.
Диаметр валов определяем из выражения:
Выражаем из формулы 5.9 диаметр вала:
где k1=135 – коэффициент учитывающий наличие напряжения от затяжки болтов;
k2=15 – коэффициент учитывающий неравномерность распределения нагрузки на болты.
Расчет распорных плит.
Усилия Т действующие вдоль распорных плит достигают максимальной величины когда плиты находятся в крайнем верхнем положении:
Схема для расчёта распорной плиты представлена на рисунке 5.2
Рисунок 5.2 – Схема сил действующих на распорную плиту
С увеличением угла возрастает усилие Т а при =90 cos 90=0 т.е. при горизонтальном положении распорных плит усилие Т неограниченно возрастает. Следовательно в щековой дробилке распорные плиты не должны располагаться в одну линию. Угол принимают равным не менее 1012°. Сечения плит выбирают такими чтобы они передавали нормальные расчетные усилия и при попадании недробимых предметов ломались раньше чем какая-либо другая деталь дробилки.
В дробилке с простым движением подвижной щеки распорные плиты работают на сжатие поэтому их сечение S можно определить из формулы
Принимая =80 определяем усилие действующее вдоль распорных плит:
Распорные плиты обычно изготавливают из чугуна. Необходимая площадь поперечного сечения плиты:
Для чугуна принимаем [сж]=685 МПа.
Расчет оси подвижной щеки.
Ось подвижной щеки рассчитывают как балку на двух опорах. Так как ширину подшипников принимаем равной 180 мм реакции располагаем на 13 их ширины от края а усилие передаваемое на ось распределяется равномерно в двух местах на расстоянии 200 мм.
Нагрузка действующая на ось определяется по формуле:
Максимальный изгибающий момент
Mmax = R1026- (5.16)
Mmax =76838026-=12294 Нм.
Определим изгибающий момент от веса щеки вместе с броневой плитой которая примерно равна Gп=37210-3 МН.
M1max=026-=29710-3 МНм=2970 Нм.
Если считать что моменты Mmax и M1max действуют во взаимно перпендикулярных плоскостях то результирующий момент равен:
Принимая диаметр оси подвижной щеки равным 0165 м получим
Размеры маховика определим из уравнения махового момента:
где m – масса маховика кг;
D – диаметр маховика м;
N – мощность потребляемая щековой дробилкой кВт;
– угловая скорость эксцентрикового вала радс;
– коэффициент неравномерности (=001003).
Подставляя в вышеприведенную формулу числовые значения получим:
Диаметр маховика определим из формулы
Принимая v=15 мс находим диаметр
Масса обода маховика:
А с учетом массы спиц:
mоб = 1225611=1348 кг.
На эксцентриковом валу устанавливают два маховика. Площадь сечения обода каждого из маховиков найдем из уравнения:
где – плотность металла =7 100 кгм3.
Принимая что один из маховиков является шкивом тогда ширину маховика-шкива берем равной 005 м а толщину обода
Расчет эксцентрикового вала.
Эксцентриковый вал рассчитывают как балку свободно лежащую на двух опорах. Схема для расчёта представлена на рисунке 5.3.
Рисунок 5.3 – Схема сил действующих на эксцентриковый вал
На вал действуют нагрузки:
б) на консолях – сила тяжести маховиков
в) на одной консоли кроме веса маховика сила Тр от натяжения ремня.
Для определения силы Тр найдем крутящий момент на маховике-шкиве:
Окружное усилие на маховике:
Натяжение ремня можно принять приближенно равным утроенному окружному усилию:
Тр =356926 =17078 Н.
Для упрощения вычисления допустим что сила Тр направлена вертикально вверх. По чертежу а2=081 м – расстояние между осями подшипников b2=025 м – расстояние от оси подшипника до оси маховика.
Находим реакцию RA. Сумма моментов всех сил относительно опоры В:
G м (b2+a2)-RAa2 - Pрасч- Gмb2 - Трb2=0 (5.27)
Максимальный изгибающий момент на середине эксцентрикового вала:
Mmax = - 906444(- 0155)+(-12545350405) = - 5066817 Нм.
Кроме изгибающего эксцентриковый вал подвергается действию крутящего момента:
Мкр = 25166700025 = 6291675 Нм.
Результирующий момент будет равен:
Принимаем диаметр эксцентрикового вала dв=04 м тогда
и = = 798106 Па = 798 МПа
Вполне допустимо так как эксцентриковый вал изготовляют из хромистой стали с в=8090 МПа.
Для определения диаметра коренной шейки вала определяют изгибающий момент относительно опоры В:
МВ=(Gм - Tр)b2 (5.32)
МВ =(906444 - 2516670) 025 = - 6269014 Нм.
Так как изгибающий момент незначительный то шейку вала рассчитывают на кручение.
Диаметр шейки вала принимают dш=025 м тогда:
Что для принятой стали вполне допустимо.
Определяем диаметр шейки вала из расчета на удельное давление. Допустимое удельное давление для стали по битуму р=900 МПа тогда:
где l – длина шейки коренного подшипника l=450 мм.
При дроблении каменных материалов необходимо соблюдать следующие требования:
загружаемый материал должен соответствовать размеру загрузочного отверстия дробилки;
не допускается проталкивать камень в загрузочное отверстие рукой ногой а также лопатой или ломом; для извлечения заклинивших кусков материала следует использовать крюки не допускается извлечение материала руками;
регулировать загрузочную щель необходимо только после полной остановки дробилки и очистки ее от дробимого материала;
при нарушении нормальной работы дробильно-сортировочной установки необходимо немедленно остановить ее выяснить и устранить причину неисправности.
Работа на установках не допускается при:
отсутствии защитных ограждений;
ослаблении шпонок у зубчатых колес шкивов или маховиков а также ослаблении крепежных болтов;
повреждении пружин натяжения щековых дробилок;
ослаблении крепления дробящих плит.
Все движущиеся или представляющие опасность части машин должны иметь ограждения исключающие доступ к ним во время работы.
Передвижение работников в зоне работы дробильной установки осуществляется только по предусмотренным обозначенным и оборудованным проходам лестницам площадкам местам.
Не разрешается хождение под ленточным транспортером а также перелезать через него во время остановки и на ходу.
Перед запуском дробильно-сортировочной установки необходимо подать предупредительный звуковой сигнал. В местах с повышенным уровнем шума необходимо предусмотреть дублирующую световую сигнализацию.
С порядком подачи сигналов должны быть ознакомлены все работающие. Схема подачи сигналов должна быть вывешена на видном месте.
Для создания нормальных санитарно-гигиенических условий труда на дробильно-сортировочных установках необходимо предусмотреть:
дистанционное управление установкой;
оборудование кабины оператора шумозащитными материалами кондиционером обмена воздуха;
оборудование увлажнения перерабатываемого материала.
Периодический контроль содержания пыли на рабочих местах необходимо проводить не реже 1 раза в год а также при изменении технологического процесса после реконструкции и ремонта оборудования.
Содержание пыли в воздухе рабочей зоны не должно превышать предельно допустимых концентраций.
Метрология и стандартизация
Метрология — наука об измерениях методах и средствах обеспечения их единства и способах достижения требуемой точности. Предметом метрологии является извлечение количественной информации о свойствах объектов с заданной точностью и достоверностью; нормативная база для этого — метрологические стандарты.
Цели и задачи метрологии заключаются в следующем:
создание общей теории измерений;
образование единиц физических величин и систем единиц;
разработка и стандартизация методов и средств измерений методов определения точности измерений основ обеспечения единства измерений и единообразия средств измерений (так называемая «законодательная метрология»);
создание эталонов и образцовых средств измерений поверка мер и средств измерений. Приоритетной подзадачей данного направления является выработка системы эталонов на основе физических констант.
Стандартизация — деятельность по разработке опубликовании и применении стандартов; также деятельность по установлению норм правил и характеристик в целях обеспечения безопасности продукции работ и услуг для окружающей среды жизни здоровья и имущества технической и информационной совместимости.
Стандартизация направлена на достижение оптимальной степени упорядочения в определенной области посредством установления положений для всеобщего и многократного применения в отношении реально существующих или потенциальных задач.
Целями стандартизации являются:
повышение уровня безопасности с учётом риска возникновения чрезвычайных ситуаций природного и техногенного характера повышение уровня экологической безопасности безопасности жизни и здоровья животных и растений;
обеспечение конкурентоспособности и качества продукции (работ услуг) единства измерений рационального использования ресурсов взаимозаменяемости технических средств (машин и оборудования их составных частей комплектующих изделий и материалов) технической и информационной совместимости сопоставимости результатов исследований (испытаний) и измерений технических и экономико-статистических данных проведения анализа характеристик продукции (работ услуг) исполнения государственных заказов добровольного подтверждения соответствия продукции (работ услуг);
содействие соблюдению требований технических регламентов;
создание систем классификации и кодирования технико-экономической и социальной информации систем каталогизации продукции (работ услуг) систем обеспечения качества продукции (работ услуг) систем поиска и передачи данных содействие проведению работ по унификации.
1 Метрологическое обеспечение при сборке оси в сборе
При сборке оси необходимо использовать следующие инструменты:
динамометрический ключ (для затяжки болтов с определённым моментом);
угломер (для установки заданной величины углов наклона ступеней подвижной щеки и дробящих плит).
В процессе выполнения данного курсового проекта была спроектирована щековая дробилка СМД-60А с простым движением щеки содержащая станину неподвижную и подвижную щеки. Особенностью дробилки является то что она выполнена с подвижной щекой ступенчатой формы что дало возможность увеличить пропускную способность щековой дробилки при гарантированном дроблении и прохождении горной породы в том числе со слоистой структурой в камере дробления без увеличения высоты дробилки.
Также были произведёны расчёты её основных параметров мощностной расчёт расчёт производительности и расчёты на прочность.
Борщев В. Я. Оборудование для измельчения материалов: дробилки и мельницы В. Я. Борщев Тамбов: Издательство Тамбовского Государственного Технического Университета 2004. 75 с. : ил.
Клушанцев Б. В. Дробилки. Конструкция. Расчёт. Особенности эксплуатации Б. В. Клушанцев А. И. Косарев Ю. А. Муйземнек. – М: Машиностроение 1190. – 319 с. : ил.
Анурьев В.И. Справочник конструктора-машиностроителя: в 3 т. В.И.Анурьев. – М: Машиностроение 2001. – Т. 2. – 8-е изд. – 912 с. : ил.
Охрана труда в химической промышленности. Г.В. Макаров А.Я
[и др.]. – М.: Химия 1989. – 496 с. : ил.
Содержание.doc
Анализ научно-технической литературы и патентный обзор 10
1 Анализ научно-технической литературы ..10
2 Патентный обзор .12
3 Описание принятого решения 17
Выбор основных параметров 18
1 Определение угла захвата ..18
2 Определение угловой скорости и частоты вращения
эксцентрикового вала 19
3 Определение конструктивных параметров загрузочного отверстия20
Расчёт основных параметров 23
1 Мощностной расчёт 23
2 Расчёт производительности 24
Расчёты на прочность 25
Метрология и стандартизация ..37
1 Метрологическое обеспечение при сборке оси в сборе .38
Список литературы 40
Рекомендуемые чертежи
Свободное скачивание на сегодня
- 23.02.2023