Самоходный скрепер ДЗ-13




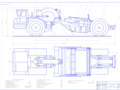
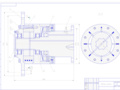
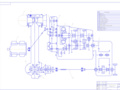
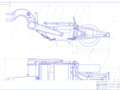
- Добавлен: 25.10.2022
- Размер: 3 MB
- Закачек: 3
Описание
Состав проекта
![]() |
![]() |
![]() ![]() ![]() ![]() |
![]() ![]() ![]() ![]() |
![]() |
![]() ![]() ![]() ![]() |
![]() ![]() ![]() ![]() |
![]() |
![]() |
![]() ![]() ![]() ![]() |
![]() ![]() ![]() ![]() |
![]() |
![]() |
![]() |
![]() ![]() ![]() ![]() |
![]() ![]() ![]() ![]() |
![]() ![]() ![]() ![]() |
![]() |
![]() ![]() ![]() ![]() |
![]() |
![]() ![]() ![]() ![]() |
![]() ![]() ![]() ![]() |
![]() ![]() ![]() ![]() |
![]() |
![]() |
![]() |
![]() ![]() ![]() ![]() |
![]() |
![]() ![]() |
![]() ![]() |
![]() ![]() |
![]() |
![]() ![]() |
![]() ![]() |
![]() ![]() |
![]() ![]() |
![]() |
![]() ![]() |
![]() ![]() |
![]() ![]() |
![]() ![]() |
![]() ![]() |
![]() ![]() |
![]() ![]() |
![]() ![]() |
![]() |
![]() ![]() |
![]() ![]() |
![]() ![]() |
![]() ![]() |
![]() ![]() |
![]() ![]() |
![]() ![]() |
![]() ![]() |
![]() ![]() |
![]() ![]() |
![]() ![]() |
![]() ![]() |
![]() ![]() |
![]() ![]() ![]() |
- Архиватор zip файлов
- AutoCAD или DWG TrueView
- Программа для просмотра изображений
- Компас или КОМПАС-3D Viewer
- Microsoft Word
Дополнительная информация
Чертеж6-1.dwg

Чертеж5(задний мост).dwg

Чертеж3(ГС-1).dwg

Рабочее давление в гидросистеме скрепера 10
Предохранительный клапан
Фильтр с переливным клапаном
Гидрораспределитель с эл.гидравлическим
Гидроцилиндры движения ковша
Дроссели с обратным клапаном
Гидроцилиндры подъема и опускания заслонки
Гидроцилиндры движения задней стенки
Гидрораспределитель с ручным управлением
Наименование Кол-во Прим
Специф-1.dwg

ДП.280340.83-03.01.ВО
Гидроцилиндр поворота
Специф-4.dwg

ДП.280340.83-03.04.01
Гидроцилиндр подъема
Гидроцилиндр заслонки
Гидроцилиндр задней
Задняя ось с колесом
Чертеж0.dwg

С передними управляемыми колесами
С передними ведущими колесами
С элеваторной загрузкой
С поворотом одноосного тягача
Со всеми ведущими колесами
Со средними ведущими колесами
Типы самоходных скреперов
Экономика.dwg

НАИМЕНОВАНИЕ ПОКАЗАТЕЛЕЙ
Капитальное вложение
Эксплуатционные затраты
Годовой экономический эффект
ОСНОВНЫЕ ТЕХНИКО-ЭКОНОМИЧЕСКИЕ ПОКАЗАТЕЛИ ПРОЕКТА
Специф-6-1.dwg

Чертеж3(ГС-2).dwg

с активным задним мостом
Рабочее давление в гидросистеме скрепера 10
Предохранительный клапан
Фильтр с переливным клапаном
Гидрораспределитель с эл.гидравлическим
Гидроцилиндры движения ковша
Дроссели с обратным клапаном
Гидроцилиндры подъема и опускания заслонки
Гидроцилиндры движения задней стенки
Гидрораспределитель с ручным управлением
Дроссель управляемый
Наименование Кол-во Прим
Специф-5.dwg

Чертеж2(КСХ).dwg

Согласующий редуктор
Дополнительная коробка передач
Чертеж1.dwg

Геометрическая емкость ковша
Количество двигателей
Мощность силовой установки
Способ разгрузки ковша Принудительный
Управление рабочим органом Гидравлическое
Максимальная глубина резания
Толщина отсыпаемого слоя грунта
Дорожный просвет под ножами
Колея колес скрепера
Максимальная скорость движения
Чертеж6-2.dwg

Допуски на размеры с неуказаными допусками валов -JT14
Чертеж4(рабочее оборудование).dwg

DZ-13.doc
К ДИПЛОМНОМУ ПРОЕКТУ
на тему: «Разработка активного заднего моста для самоходного скрепера ДЗ-13 с целью повышения тягово-сцепных характеристик»
Специальная часть: «Проектирование и расчет конструкции мотор-колеса»
Дипломный проект выполненный на тему: «Разработка активного заднего моста для самоходного скрепера ДЗ-13 с целью повышения тягово-сцепных характеристик» со специальной частью «Проектирование и расчет конструкции мотор-колеса» представляется для итоговой аттестации автора и присвоения квалификации инженера.
В данном дипломном проекте на основе анализа патентно-литературных источников предложена конструкция мотор-колеса обеспечивающий при простоте конструкции большой крутящий момент и малые габариты а также надежное торможение. Для изменения скорости вращения мотор-колеса при изменении скорости движения скрепера предлагается применить гидропривод с дроссельным управлением. По сравнению с существующими скреперами скрепер предлагаемой конструкции выигрывает в себестоимости единицы работ в 115—13 раза в зависимости от дальности транспортирования породы.
В дипломном проекте определены основные параметры скрепера и рабочего оборудования выполнен тяговый расчет определены усилий на рабочих органах.
В разделе «Безопасность и экологичность работы» освещены вопросы охраны труда техники безопасности защиты о шума противопожарной безопасности машины и экологичности работы.
В разделе «Определение показателей экономической эффективности от внедрения новой техники» определены технико-экономические показатели модернизации погрузчика. Целесообразность модернизации обоснована экономическим эффектом от модернизации который составил 258300 тенге в год при сроке окупаемости 066 года.
Пояснительная записка изложена на 87 страницах графическая часть содержит 8 листов формата А1.
Основные сведения о самоходных скреперах и тенденции их развития
1 Определение назначение основные параметры самоходных скреперов
2 Устройство самоходных скреперов
3 Рабочий процесс скрепера
4 Рабочее оборудование скреперов
5 Обзор существующих моделей самоходных скреперов
6 Технология выполнения земляных работ самоходными скреперами
Расчет и модернизация скрепера ДЗ-13
1 Описание и техническая характеристика скрепера ДЗ-13
3 Улучшение тягово-сцепных характеристик скрепера ДЗ-13
4 Расчет мотор-колеса заднего моста
5 Расчет механизма подъема заслонки
6 Расчет механизма принудительной разгрузки ковша скрепера
Техническое обслуживание и ремонт
1. Общие понятия по системе технического обслуживания и ремонта дорожных и строительных машин
2. Перечни состав и технология работ технического обслуживания дорожных и строительных машин
3. Технология и организация ремонта дорожных и строительных машин
4 Текущий ремонт ходовой части подвески шины
Безопасность и экологичность проекта
1 Безопасность технических систем
2 Разработка мероприятий по улучшению условий труда и ТБ при работе погрузчика. Защита от вибрации
3. Противопожарная устойчивость машины или оборудования
4. Экологичность технических систем и оборудования
Определение показателей экономической эффективности от внедрения новой техники
1 Краткое описание сущность и преимущества проектного решения
2 Расчет годовой эксплуатационной производительности и количества машино-часов работы техники в году
3 Расчет эксплуатационных расходов
4 Определение экономической эффективности
Список использованных источников
Задача строительства развитой сети современных автомобильных дорог различного класса и назначения в Казахстане связано с созданием высокоэффективных и высокопроизводительных строительных и дорожных машин позволяющих существенно повысить производительность труда за счет интенсификации рабочих процессов машин разработки новых прогрессивных конструкций обеспечивающих наименьшие затраты на их изготовление и эксплуатацию. При строительстве сооружений выполняются большие объемы земляных работ для ведения которых используют бульдозеры скреперы грейдеры и автогрейдеры. На долю скреперов приходится до 20 % общего объема земляных работ.
Отличительной особенностью скреперов является возможность выполнения ими всего комплекса землеройных работ в дорожном строительстве (разработка грунта его транспортировка укладка слоем заданной толщины и предварительное уплотнение). Скреперы успешно работают на открытых горных разработках а при дальности транспортирования до 3 5 км успешно конкурируют с комплектом машин: экскаватор и самосвалы. Кроме того колесные скреперы являются экологически наименее вредными при строительстве дорог особенно в лесной зоне.
Развитие тракторостроения в направлении освоения и серийного выпуска промышленностью мощных энергонасыщенных гусеничных и колесных тягачей создало проблему рационального использования мощности двигателя тягача на тяговом режиме при разработке скрепером грунта. Конструкторские разработки в этом направлении привели к созданию скреперных агрегатов с изменяемым сцепным весом которые способны самостоятельно разрабатывать грунт без помощи традиционного трактора–толкача. Практическая реализация таких прогрессивных разработок основана на обобщении результатов современных исследований в области теории копания грунта скреперами тяговой механики землеройно–транспортных машин теории создания и расчета скреперных агрегатов экономико–математическом моделировании их работы уже на стадии проектирования.
Эффективность заполнения ковша скрепера грунтом определяется не только тяговыми качествами трактора но и величиной сопротивления копанию. Увеличение сопротивления заполнению ковша скрепера по мере его заполнения и применяемый в настоящее время способ поддержания тягового баланса за счет уменьшения толщины срезаемой стружки входят в противоречие между собой и снижают эффективность заполнения ковша в его заключительной стадии.
Таким образом повышение эффективности заполнения ковша скрепера грунтом путем улучшения тяговых качеств тягача является актуальной научной и практической проблемой.
ОСНОВНЫЕ СВЕДЕНИЯ О САМОХОДНЫХ СКРЕПЕРАХ И ТЕНДЕНЦИИ ИХ РАЗВИТИЯ
1 Определение назначение основные параметры самоходных скреперов
Самоходный скрепер - самоходная колесная машина имеющая открытый ковш с режущей кромкой расположенный между передними и задними колесами которая режет набирает транспортирует выгружает и распределяет материал при движении вперед.
Самоходные пневмоколесные скреперы широко распространены в различных отраслях промышленности и хозяйства. Благодаря высоким транспортным скоростям (до 40—50 кмч) и хорошей маневренности их производительность в 2—3 раза выше по сравнению с прицепными скреперами к гусеничным тракторам максимальная скорость которых составляет 10—13 кмч.
Скреперы этого типа применяют при перемещении грунта на расстояние до 5 км а иногда на значительно большие расстояния особенно при соответствующих условиях рельефа местности и хорошем состоянии дорог.
При наборе грунта самоходные скреперы загружают с помощью тракторов или колесных тягачей (толкачей) оборудованных специальными толкающими устройствами или отвалами бульдозера. Целесообразно использовать в качестве толкача гусеничный трактор или колесный тягач тяговый класс которых в 15 раза превышает тяговый класс скрепера.
Применение толкачей ниже тягового класса скрепера малоэффективно а применение толкачей тягового класса превышающего более чем в два раза тяговый класс скрепера не рекомендуется по условиям прочности скрепера.
С помощью скреперов можно возводить насыпь земляного полотна из боковых резервов или грунтовых карьеров устраивать выемки с отвозкой грунта в насыпи или кавальеры планировать строительные площадки срезать растительный слой грунта в полосе отвода дороги.
Скреперы различаются параметрами к основным из которых относятся: геометрическая вместимость; грузоподъемность (максимально допускаемая масса груза в ковше); ширина резания; максимальное заглубление; толщина слоя отсыпки или дорожный просвет максимально поднятого ковша под ножами; колесная база колея передних и задних колес; габаритные размеры: длина ширина и высота; масса снаряженного скрепера (полностью заправленного без груза в ковше).
Геометрическая вместимость ковша ограничена боковыми стенками днищем заслонкой и задней стенкой а сверху - плоскостью проходящей через условную среднюю линию выравнивающую верхнюю кромку боковых стенок без уменьшения их общей площади.
В технических характеристиках скреперов часто указывают также номинальную вместимость ковша представляющую собой сумму геометрической вместимости ковша и объема шапки грунта набранного в ковш выше верхних кромок боковых стенок. Это условный параметр характеризующий максимально возможный объем грунта набираемого скрепером. При этом объем шапки может достигать 30 40% геометрической вместимости.
Ширину резания определяют по наружным плоскостям подрезных ножей. Максимальное заглубление - это расстояние от кромки ножа максимально опущенного ковша скрепера до опорной поверхности передних и задних колес. Колесную базу самоходных скреперов измеряют от оси задних колес до оси колес одноосного тягача или оси задних колес трактора. Колея представляет собой колею указанных колес базовой машины.
Кроме перечисленных выше параметров скреперы характеризуются основными параметрами базовых машин - тяговым классом или мощностью двигателя скоростью движения и т.д.
Основные параметры дают представление о производительности технологических возможностях скреперов области их рационального использования. Так при выборе того или иного скрепера для определенного строительного объекта руководствуются вместимостью ковша. На объектах с большими объемами земляных работ целесообразно использовать скреперы с ковшом значительной вместимости несмотря на более высокую их стоимость. На основе ширины резания и величины заглубления планируют число наборов а с помощью толщины слоя отсыпки - число проходов при разгрузке скрепера необходимых для отсыпки грунта заданным слоем. И наконец максимальная скорость передвижения скрепера в заданных условиях наряду с вместимостью ковша позволяет оценить время необходимое для перемещения планируемого объема грунта т.е. производительность скрепера.
В соответствии с принятым у нас в стране типажом предусмотрены типоразмерный ряд скреперов определяемый геометрической вместимостью ковша.
Самоходный скрепер (рис. 1.1) представляет собой двухосную пневмоколесную машину состоящую из одноосного тягача 15 и полуприцепного одноосного скреперного оборудования соединенных между собой универсальным седельно-сцепным устройством 14.
На тягаче смонтированы два гидроцилиндра 1 для его поворота относительно рабочего органа в плане. Седельно-сцепное устройство обеспечивает возможность относительного поворота тягача и скрепера в вертикальной и горизонтальной плоскостях. Для толкания скрепера бульдозером-толкачом в процессе набора грунта имеется буферное устройство 8.
Рис. 1.1 Самоходный скрепер
Основным узлом скрепера является ковш 5 с двумя боковыми стенками и днищем опирающийся на колеса 7. К подножевой плите ковша крепят сменные двухлезвийные ножи 2 — два боковых и средние. Ковш снабжен выдвижной задней стенкой 10 для принудительной разгрузки а в передней части — заслонкой 11 поднимающейся при наборе и выгрузке грунта. Заслонка служит для регулирования щели при загрузке ковша и закрывает ковш при транспортировании грунта. Ковш двумя шарнирами 4 соединен с тяговой П-образной рамой 3 жестко соединенной с хоботом 13. Гидравлическая система управления рабочим оборудованием обеспечивает подъем и опускание ковша 5 заслонки 11 выдвижение задней стенки 10 и возврат ее в исходное положение с помощью трех пар гидроцилиндров 69 и 12. Насосы гидросистемы рабочего оборудования приводятся в действие от коробки отбора мощности базового тягача. Раздельное управление гидроцилиндрами осуществляется золотниковым распределителем установленным в кабине машиниста.
Рабочее оборудование самоходных и прицепных скреперов одинаково по конструкции и максимально унифицировано.
3 Рабочий процесс скрепера
Рабочий процесс скрепера состоит из следующих последовательно выполняемых операций: резание грунта и наполнение ковша транспортирование грунта в ковше к месту укладки выгрузки и укладка грунта обратный (холостой) ход машины в забой. При наборе грунта (рис. 1.2 а) ножи опущенного на грунт ковша 2 срезают слой грунта толщиной к который поступает в ковш при поднятой подвижной заслонке 3. Наполненный грунтом ковш на ходу поднимается в транспортное положение (рис. 1.2 б) а заслонка 3 опускается препятствуя высыпанию грунта из ковша.
При разгрузке ковша (рис. 1.2 в) заслонка поднята а грунт вытесняется принудительно из приспущенного ковша выдвигаемой вперед задней стенкой 5 ковша причем регулируемый зазор между режущей кромкой ковша и поверхностью земли определяет толщину с укладываемого слоя грунта 4 который разравнивается (планируется) ножами ковша и частично уплотняется колесами скрепера. При холостом ходе порожний ковш поднят в транспортное положение а заслонка опущена. Для увеличения тягового усилия скрепера при наполнении ковша в плотных грунтах обычно используют бульдозер-толкач 1 (см. рис. 1.2 а). При наполнении ковша скорость движения скреперов составляет 2 4 кмч при транспортном передвижении - 05 08 максимальной скорости трактора или тягача.
У некоторых моделей скреперов для уменьшения сопротивлений при работе в ковше устанавливают наклонный скребковый конвейер (элеватор) осуществляющий принудительную загрузку срезанного ножом слоя грунта в ковш и его выгрузку. Скреперы с элеваторной загрузкой наиболее рационально используются на сыпучих грунтах при выполнении небольших объемов работ.
Рис. 1.2 – Операции рабочего цикла самоходного скрепера
Рабочее оборудование скреперов разных типоразмеров однотипно по устройству. Состоит это оборудование из передней оси тяговой рамы ковша с заслонкой и задней стенкой в сборе колес и гидросистемы.
Тяговая рама предназначена для передачи силы тяги тягача ковшу и соединения передней оси с ковшом скрепера.
Ковш (рис. 1.3) служит рабочей емкостью для разрабатываемого скрепером грунта а также выполняет роль несущей рамы воспринимающей нагрузки от силы тяги массы машины и грунта. Спереди ковш опирается на переднюю ось и тяговую раму через пальцы 11 а сзади на полуоси колес установленные в цапфу 9. Он представляет собой сварную конструкцию состоящую из двух боковых стенок 1 днища и буферной рамы 6.
- стенка 2 - направляющие полосы 3 - днище 4 16 - связи 5 - балка 6 - рама 7 17 - проушины 8 - буфер 9 - цапфа полуоси 10 - крышка 11 12 - пальцы 13 - подрезной нож 1415 - средний и боковой ножи 18 – подножевая плита
Боковые стенки 1 выполнены из листового проката и усилены продольными и поперечными накладками коробчатого сечения. На стенках 1 размещены пальцы 12 для подвески передней заслонки пальцы 11 тяговой рамы а также лючки закрытые крышками 10 для крепления гидролиний размещенных внутри стенки. Правая и левая боковые стенки связаны между собой передней 16 двумя задними 4 связями коробчатого сечения и днищем 3. По краям передней связи приварены проушины 17 для крепления головки штоков гидроцилиндров подъема-пускания ковша.
На передних нижних кромках боковых стенок изготовленных из полосы более толстого листового проката чем вся остальная стенка крепят ножи 13 для подрезания стружки грунта с боков и уменьшения его потерь в боковые валики. Днище 3 - также коробчатого сечения. Передняя часть днища представляет собой мощную подножевую плиту 18 к которой крепят ножи 14 и 15.
Буферная рама 6 представляет собой сварную пространственную форму из сортового проката. Рама приварена к задним связям ковша и образует с ним единую металлоконструкцию. В раме размещены направляющие балки 5 и проушина 7 для установки толкателя и гидроцилиндра выдвижения задней стенки. Заканчивается рама гнутым листом - буфером 8 в который упирается отвал бульдозера-толкача при толкании скрепера во время набора грунта или выезда из забоя.
Заслонка (рис. 1.4) является передней стенкой ковша и предназначена для регулирования высоты загрузочной щели при наборе грунта. Заслонка - сварной конструкции и состоит из лобового щита 1 двух боковых щек 2 с проушинами 3. Щит 1 выполнен из листа который в верхней части изогнут под большим радиусом. Нижняя часть щита которая воспринимает основную нагрузку от призмы грунта при наборе и перерезает пласт в конце набора усилена накладками 5 образующими вместе с основным листом жесткую конструкцию. Две щеки 2 из стального листа приварены к торцам щита.
Рис. 1.4 – Заслонка:
- щит 2 - щека 3 - проушина 4 - кронштейн 5 – накладки
На свободном конце щек предусмотрены проушины с расточенными отверстиями для шарнирного крепления заслонки с помощью пальцев на боковых стенках ковша. Спереди к щиту приварены кронштейны 4 с проушинами для крепления пальцев тяги заслонки. Лобовой щит со щеками размещен внутри ковша между боковыми его стенками.
Задняя стенка ковша (рис. 1.5) предназначена для выталкивания из него грунта при разгрузке.
Рис. 1.5 - Задняя стенка ковша:
- щит 2 - проушина 3 - раскос 4 - толкатель 5 6 9 - ролики 7 - масленка 8 - шайба
Она представляет собой сварную конструкцию и состоит из щита 1 и толкателя 4. Щит 1 сварен из листовой стали и с задней стороны усилен продольными и поперечными накладками и ребрами жесткости. Толкатель 4 - это балка коробчатого сечения приваренная к тыльной стороне щита. Для усиления стыка толкателя со щитом предусмотрены наклонные и горизонтальные раскосы 3. В месте стыка приварен кронштейн с проушиной 2 для крепления головки штока гидроцилиндра. Направляющие ролики установленные на подшипниках качения снижают сопротивление движению задней стенки а также предотвращают ее перекосы. Нижние 6 и боковые 9 ролики щита своими ребордами катятся по направляющим полосам приваренным соответственно к днищу и боковым стенкам ковша. Сферические ролики 5 установлены попарно в горизонтальной и вертикальной плоскостях.
При перемещении задней стенки вперед и назад ролики 5 перекатываются по направляющим балкам 5 выполненным в виде швеллеров и фиксируют направленное движение хвостовика толкателя 4.
Основными производителями скреперов вмире являются Volvo Construction Equipment Caterpillar Terex идругие. ВСНГ скреперы производит Могилевский автомобильный заводим. С.М.Кирова и Челябинский завод «Дормаш».
Рассмотрим некоторые модели самоходных скреперов производства СНГ.
Скрепер ДЗ-11П (рис. 1.6) с гидравлическим приводом и принудительной разгрузкой предназначен для послойной разработки грунтов I и II групп и предварительно разрыхленных грунтов III и IV групп.
Рис. 1.6 – Скрепер ДЗ-11П
— тягач МоАЗ-546П; 2 — седельно-сцепное устройство; 3 — дышло; 4 — гидроцилиндр ковша; 5 — заслонка; 6 — ковш; 7 — задняя стенка; 8 — гидроцилиндр заслонки; 9 — заднее колесо; . 10 — буфер; 11 — нож; 12 — гидроцилиндры поворота
Скрепер представляет собой полуприцеппой к одноосному колесному тягачу МоАЗ-546П агрегат на колесах с пневматическими шинами Для установки полуприцепной части тягач оснащен седельно-сцепным устройством с разнесенными по вертикали проушинами обеспечивающим взаимное смещение тягача и полуприцепа на угол 90° в горизонтальной плоскости наклон тягача относительно скрепера на угол до 20°.
Скреперное оборудование состоит из ковша с заслонкой и задней стенкой тяговой рамы (дышла) соединяющей ковш с седельно-сцепным устройством тягача и гидросистемы привода ковша заслонки и задней стенки. Кроме того скрепер оснащен пневмосистемой управления тормозами и электросистемой для световой сигнализации (включения габаритных фонарей указателей поворота и пр.).
Ковш — сварной с наружных сторон боковых стенок усилен балками жесткости и профилями. Сзади ковш оканчивается пространственной фермой из прямоугольных 'балок образующих буфер для использования трактора-толкача при заполнении ковша в тяжелых грунтах.
Днище — жесткой конструкции имеет впереди подножевую плиту с закрепленными на ней режущими ножами. Под буферными балками находится оси задних колес с пневматическими шипами.
Тяговое дышло своей П-образной частью охватывает ковш.
Фиксируют ковш относительно дышла двумя гидроцилиндрами укрепленными на поперечной трубе дышла.
Заслонка крепится шарнирно к боковым стенкам ковша на кронштейнах. Поднимают ее два гидроцилиндра расположенные в плоскости стенок ковша. Задняя стенка приводимая в действие двумя гидроцилиндрами имеет возможность перемещаться вдоль ковша на роликах без перекосов. Сверху она оснащена вертикальной решеткой.
Колеса скрепера и тягача унифицированы. Они оборудованы пневматическими тормозами и шинами размером 21.00—28.
Гидросистема привода ковша заслонки и задней стенки состоит из масляного бака гидронасосов гидораспределителем трех пар гидроцилиндров двойного действия и системы трубопроводов и гибких рукавов.
Одноосный тягач оборудован еще двумя гидроцилиндрами для поворота машины которые установлены по бокам седельно-сцепного устройства.
Ковш заполняется грунтом при поднятой заслонке отодвинутой стенке и опущенном ковше в процессе поступательного движения скрепера. Транспортируется грунт при закрытой заслонке и поднятом ковше а выгружается при поднятой заслонке путем выдвижения задней стенки.
Пневмосистема и электросистема скрепера подобны автомобильной и подключаются к системам тягача
Скрепер ДЗ-13 (рис. 1.7) с гидравлическим приводом и принудительной разгрузкой предназначен для послойной разработки грунтов I—IV трупп (грунты III и IV групп предварительно разрыхляют) без сосредоточенных каменных включений при планировочных работах среднего объема.
Рис. 1.7 – Скрепер ДЗ-13
— тягач БелАЗ-531; 2— седельно-сцепное устройство; 3 — дышло; 4 — заслонка; 5 — ковш; 6 — гидроцилиндр заслонки; 7 — задняя стенка; 8 — заднее колесо; 9 — буфер; 10 — ножи; 11 —гидроцилиндр ковша; 12 — гидроцилиндр поворота
Базовой машиной скрепера служит одноосный колесный тягач БелАЗ-531 снабженный вертикально разнесенным опорным седельно-сцепным устройством.
Скрепер полуприцепного одноосного исполнения состоит из ковша с заслонкой задней стенкой и буфером тягового дышла соединяющего ковш с седельно-сцепным устройством тягача гидросистемы привода ковша заслонки и задней стенки пневмосистемы привода тормозов и электросистемы для управления рабочими органами и световой сигнализации.
Ковш сваренный из листового металла имеет две боковые стенки усиленные гнутыми профилями днище с передней подножевой плитой на которой закреплены средние и крайние ножи (средние — чуть впереди) буферные балки и передние кронштейны к которым крепятся штоки гидроцилиндров подъема ковша. Кроме нижних ножей на боковых стенках закреплены боковые ножи для подрезания стружки грунта.
Полукруглая заслонка перекрывает полость ковша и поднимается двумя гидроцилиндрами двойного действия расположенными в плоскости стенок ковша.
Жесткая задняя стенка выполнена в виде щита и перемещается в полости ковша с помощью гидроцилиндров двойного действия установленных на буфере.
Тяговое дышло через опорные проушины с помощью вертикальных пальцев крепится па седельно-сцепном устройстве тягача а с противоположной стороны П-образной рамой соединяется с ковшом боковыми шарнирами и двумя гидроцилиндрами двойного действия расположенными перед заслонкой. Перемещение штоков гидроцилиндров приводит к взаимному изменению положения -ковша и дышла (опусканию или подъему ковша).
Поворачивается скрепер с помощью двух гидроцилиндров за- -крепленных на дышле с двух сторон. При этом выдвижение штока одного из гидроцилиндров соответствует повороту машины в сторону другого гидроцилиндра и наоборот. Конструкция скрепера предусматривает поворот на 90°.
Скрепер оснащен унифицированными колесами на тягаче и полуприцепном агрегате. Все колеса имеют пневмотормоза приводимые в действие от пневмосистемы тягача.
Тягач оснащен гидромеханической трансмиссией которая в сочетании с пневмогидравлической подвеской тягача обеспечивает высокие транспортные скорости и уменьшает колебания кабины машиниста.
Скрепер имеет электрогидравлическое управление рабочими органами и световую сигнализацию работающую от электрооборудования тягача.
Гидравлическая система скрепера состоит из гидронасосов гидрораспределителей масляного бака запорного клапана установленных на тягаче и трех пар гидроцилиндров для привода ковша заслонки и задней стенки трубопроводов и гибких рукавов расположенных на полуприцепиом агрегате.
Заполняется ковш обычным порядком при поднятой заслонке с опущенным ковшом а разгружается принудительно — выдвижением задней стенки при поднятой заслонке.
Скрепер ДЗ-115 (рис. 1.8) — двухмоторный с принудительной разгрузкой и гидравлическим приводом предназначен для работы в тяжелых грунтовых условиях с крутыми подъемами на максимальных транспортных скоростях. Так как все колеса у него ведущие его используют в ряде случаев без дополнительного тягача при разработке средних грунтов с самостоятельным заполнением ковша.
Рис. 1.8 – Скрепер ДЗ-115
—тягач БелАЗ-531; 2 — седельно-сцепное устройство 3 — дышло- 4 — гидроцилиндр поворота; 5 - гидроцилиндр ковша; 6 - заслонка; 7 - ковш 8 - гидроцилиндр заслонки; 9 - задняя стенка 10 - дополнительный двигатель; 11 — заднее колесо
Скрепер ДЗ-115 изготовлен на базе скрепера ДЗ-13 но имеет более высокую производительность так как снабжен дополнительной силовой установкой с гидромеханической трансмиссией для привода задних колес. Управляют задним двигателем и трансмиссией синхронно с тягачом из кабины тягача.
Скрепер ДЗ-115 отличается от скрепера ДЗ-13 конструкцией заднего _ моста с установленным на нем двигателем и гидромеханической трансмиссией. Наличие всех ведущих колес потребовало выполнить колеи тягача и полуприцепного агрегата равными для лучшей проходимости машины.
Для использования на скрепере толкача сохранено буферное устройство.
Загружается ковш при одновременной работе обоих двигателей. Дополнительный двигатель включается для увеличения скорости при транспортировании или проезда в плохих грунтовых условиях. При выгрузке грунта работает один двигатель тягача.
Скрепер ДЗ-67 (рис. 1.9) с принудительной разгрузкой и гидравлическим приводом предназначен для послойной разработки транспортирования и отсыпки в земляные сооружения грунтов I— IV групп (грунты IV группы предварительно разрыхляют) при производстве земляных работ большого объема.
Скрепер ДЗ-67 состоит из одноосного колесного тягача и полуприцепного агрегата со всеми ведущими мотор-колесами. Наличие всех ведущих колес позволяет скреперу работать без толкача с высокой проходимостью в тяжелых грунтовых условиях.
Рис. 1.9 – Скрепер ДЗ-67
— дизель-электрическая силовая установка; 2— кабина; 3— бак; 4— седельно-сцепное устройство; 5 — переднее мотор-колесо; 6 — тяговая рама; 7 — гидроцилиндр поворота скрепера; 8— шкаф с электрооборудованием автоматики; 9 — рычаги подъема ковша; 10— гидроцилиндр подъема ковша; 11—упряжные тяги тяговой рамы; 12 — ковш; 13 — задняя станка ковша; 14 — вентиляторы для охлаждения мотор-колес; 15 — заднее мотор-колесо; 16 — шкаф тормозных электросопротивлений; 17 — гидроцилиндр задней стенки; 18 — буферная часть
Скрепер оснащен электрической трансмиссией постоянного тока которая обеспечивает автоматическое регулирование скорости движения при изменении сопротивления на ковше или колесах а также равномерное распределение мощности приводной дизель-электрической установки между двигателями мотор-колес независимо от их буксования. Это повышает тяговые свойства скрепера.
Силовая установка находящаяся на тягаче включает дизель М-301 с турбокомпрессором и редуктор отбора мощности. На редукторе отбора мощности установлены гидронасосы привода ковша заслонки и задней стенки а также механизма поворота скрепера компрессор зарядный генератор и шкив привода вентилятора двигателя.
Каждое мотор-колесо скрепера состоит из тягового электродвигателя расположенного по оси колеса редуктора многодискового фрикционного тормоза и обода колеса с пневматической шиной. Корпус электродвигателя служит как бы осью колеса. Он закреплен на остове скрепера.
Электродвигатель питается от генератора постоянного тока установленного на тягаче и приводимого от дизельного двигателя.
Скреперное оборудование состоит из сварного жесткого ковша снабженного сзади балочным буферным устройством заслонки задней передвижной стенки тяговой рамы с П-образными продольными балками для крепления ковша.
Своей концевой частью тяговая рама (дышло) закреплена в вертикально разнесенных опорах седельно-сцепного устройства тягача расположенного за кабиной. Поворачивается скрепер с помощью гидроцилиндров закрепленных с обеих сторон рамы. При этом штоки гидроцилиндров воздействуют на кронштейны опорной части седельно-сцепного устройства и тем самым заставляют тягач поворачиваться относительно полуприцепного агрегата.
Седельно-сцепное устройство допускает поворот тягача относительно полуприцепной части в плане на угол 77° и боковое покачивание на 14° в обе стороны.
Конструкция и установка заслонки на ковше традиционные но ее подъем производится за счет воздействия гидроцилиндра па коромысло закрепленное концом на тяговой раме а от него на тягу подсоединенную к лобовому листу заслонки. В заслонке выполнены прорези для контроля за наполнением ковша.
Изогнутая по сечению задняя стенка с хвостовиком передвигается на роликах в полости ковша под действием телескопического гидроцилиндра расположенного по оси машины за ковшом.
Ковш с заслонкой и задней стенкой поднимается и опускается с помощью двух гидроцилиндров.
Режущие ножи ковша—сменные установлены на подножевой плите в днище ковша. Средине ножи выдвинуты вперед по сравнению с крайними для лучшего резания стружки.
Электродвигатели задних колес расположены в трубе большого диаметра которая вместе с буфером и ковшом создает мощную несущую конструкцию. Электродвигатели охлаждаются специальными вентиляторами. На буферном устройстве помимо гидроцилиндра задней стенки располагается шкаф тормозных сопротивлений.
Пневматическая система скрепера предназначена для управления тормозами мотор-колес привода стеклоочистителя кабины и пневматического сигнала. Она работает от компрессора приводимого то двигателя.
Гидравлическая система скрепера служит для привода механизма поворота тягача ковша заслонки и задней стенки и состоит из трех аксиально-поршневых гидронасосов масляного бака предохранительного клапана золотника управления поворотом гидрораспределителей управления узлами ковша фильтра и двух .гидроцилиндров двойного действия механизма поворота двух гидроцилиндров Двойного действия привода заслонки и одного гидроцилиндра двойного действия привода задней стенки трубопроводов и гибких рукавов.
Электрическая трансмиссия скрепера включает электрические тяговые -машины и систему автоматики для автоматического изменения скорости электрических машин в зависимости от тяги на ведущих колесах.
Ковш заполняется при поднятой заслонке при максимальной тяге на колесах. Грунт выгружается из ковша принудительно с-помощью задней .выдвижной стенки. При загрузке на тяжелых грунтах используют толкач.
6 Технология выполнения земляных работ самоходными скреперами
Применимость скреперов с загрузкой движущим усилием определяется рядом условий: грунтовых транспортных (топографических) и погодно-климатических.
Грунтовые условия. Скреперами можно успешно разрабатывать грунты I и II групп по трудности разработки.
Лучше всего ковши скреперов заполняются при разработке плотных нормально влажных (8 12 %) грунтов. Песчаные сыпучие грунты плохо заполняют ковши скреперов: плотность этих грунтов недостаточна для проталкивания в ковш срезанной его ножами стружки.
Для разработки переувлажненных и заболоченных грунтов скреперы не применяют: на этих грунтах колеса скрепера вязнут что повышает его сопротивление качению а тяговое усилие движителей (гусениц или колес) тягача уменьшается за счет снижения сцепления с грунтом. Уменьшение тяги и увеличение сопротивления качению приводят к плохому заполнению ковша вследствие чего работа скреперного агрегата малоэффективна либо невозможна. При работе на чрезмерно влажных грунтах затруднена разгрузка из-за обильного налипания грунта на щит заслонки боковые стенки и днище ковша.
Отдельные каменные включения не препятствуют разработке грунтов скреперами. Скреперы с ковшам вместимостью 3 4 м3 захватывают и выгружают монолитные камни размером 03 04 м скреперы с ковшом вместимостью 6 15 м3 могут захватывать и выгружать камни размером 06 08 м по наибольшему измерению.
Грунты с массовым включением мелких камней (щебенки гравия размером до 50 мм) можно разрабатывать скреперами. Но вследствие абразивности каменных включений быстро изнашиваются металлоконструкции ковша заслонки и разгружающего устройства. Особенно сильно изнашиваются режущие и боковые ножи ковша. Кроме того мелкие каменные частицы попадая в зазоры между подвижными сборочными единицами машины заклиниваются в них увеличивают необходимые движущие усилия для заслонки или разгружающего устройства и могут вызвать стопорение подвижных сборочных единиц. При этом перегружаются и могут быть повреждены исполнительные механизмы – гидроцилиндры и их приводные насосы а также гибкие шланги.
На очень плотных и сухих грунтах скрепер срезает грунт стружкой малой толщины (3 5 см) вследствие чего путь наполнения скреперов значительно удлиняется. Чтобы облегчить работу скреперов и повысить их производительность увеличив наполнение ковшей предварительно рыхлят грунт. Однако чрезмерное измельчение грунта при предварительном рыхлении нежелательно так как это также снижает наполняемость ковшей. Поэтому целесообразно предварительно экспериментально установить степень разрыхления (измельчения) грунта что впоследствии окупается при скреперных работах. Степень разрыхления зависит от числа рыхлящих зубьев рыхлителя и частоты смежных проходов рыхлителя по одному месту.
Транспортные условия. Дальность транспортирования непосредственно влияет на эффективность скреперных работ: чем больше длина пути между забоем и отвалом тем ниже производительность скрепера и соответственно выше стоимость перемещенного грунта. Но помимо дальности транспортирования на производительность скреперов существенно влияют чисто топографические условия т.е. наличие крутых или затяжных подъемов или спусков а также боковых уклонов путей движения.
Уклоны проходят на пониженных скоростях: на подъемах – из-за снижения свободной тяги расходуемой на буксирование скрепера; на спусках – из-за стремления машинистов обеспечить безопасность движения.
Боковые уклоны (косогоры) опасны для движущихся машин которые могут потерять устойчивость и опрокинуться на бок.
Местные неровности (кочки ухабы) снижают величину преодолеваемого уклона так как при наезде колес на неровности может резко до потери устойчивости измениться положение машины относительно горизонта.
Погодно-климатические условия. Погодные условия существенно влияют на производительность скреперов. Скреперы работают в условиях когда грунт просыхает до нормальной влажности (ранней весной) и не достигает переувлажненного состояния (поздней осенью).
При затяжных дождях летом или осенью грунты могут оказаться в таком состоянии что скрепер не сможет работать: звенья гусениц трактора будут разрушать размокшую поверхность пути но не развивать тягового усилия достаточного для наполнения ковша и движения груженого скрепера.
Зимой скреперы могут разрабатывать мерзлые грунты при соблюдении следующих условий: после разрушения рыхлителями верхнего мерзлого слоя скреперы должны убрать его и затем работать непрерывно (круглосуточно) чтобы исключить промерзание вскрываемых слоев забоя. Опыт таких работ накоплен некоторыми строительными организациями.
Условия погоды резче сказываются на работоспособности скреперов буксируемых колесными тягачами: простои скреперов с колесной тягой из-за атмосферных осадков вдвое превышают по времени простои по этой же причине скреперов буксируемых гусеничными тракторами.
Виды скреперных работ. Скреперные работы подразделяют на основные и вспомогательные.
Основные работы (табл. 1.1) – это разработка в материковом залегании больших объемов грунтовых масс и их перемещение в земляное сооружение (насыпь дамбу кавальер).
Таблица 1.1 – Виды работ выполняемых скрепером
Указания по выполнению операции
Перемещение грунта из выемки в насыпь
По эллипсу (см. схему ниже)
Набирать грунт по клиновой или гребенчатой схеме особенно в несвязных грунтах; наиболее целесообразна клиновая схема. Во избежание одностороннего изнашивания ходовой части машины менять направление движения 1–2 раза в смену. Ковши наполнять в очередности указанной на эскизе
Продолжение таблицы 1.1
Набирать грунт возможно более толстым слоем. Стремиться набирать грунт при движении скрепера под уклон. Укладывать грунт в насыпь сначала по периметру подошвы а затем ближе к ее оси. При первых проходах возвращаться в забой с ковшом опущенным настолько чтобы нож (при закрытой заслонке) сглаживал неровности на пути следования скрепера
В случае движения на подъем грунт отсыпать тонким слоем. Во время отсыпки толстым слоем использовать толкач. При выгрузке рыхлых и сыпучих грунтов переднюю заслонку поднять на половину зева но не менее чем 400 500 мм. При работе по эллипсу через 15 2 ч работы менять направление движения агрегата во избежание неравномерного изнашивания ходовой части
При работе в широком забое применять шахматно-гребенчатую схему набора (с пропусками между смежными полосами перекрываемыми последующими проходами). При наборе грунта по возможности применять толкач (бульдозер трактор с толкающим устройством). Для самоходного скрепера применение толкача обязательно. Повороты следует делать при пустом ковше. Отсыпать насыпи и дамбы с таким расчетом чтобы со стороны откосов отсыпка была всегда несколько выше чем в середине насыпи во избежание соскальзывания скрепера и для сохранения откосов от разрушений.
При наборе связных грунтов переднюю заслонку поднять на 500 600 мм а после заполнения ковша уменьшить наполовину зазор между заслонкой и ножом. При наборе рыхлых и сыпучих грунтов переднюю заслонку поднять полностью а после заполнения ковша на 23 опустить ее на призму волочения. Ковш попеременно поднимать и опускать.
При выгрузке связных грунтов переднюю заслонку поднять полностью. До полного подъема заслонки заднюю стенку не включать.
В случае остановки задней стенки при выталкивании грунта снизить скорость движения машины заднюю стенку отодвинуть назад и снова включить ее на выталкивание при необходимости затормаживая скрепер
Смягчение профиля трассы строящейся дороги. При этой операции грунт перемещают продольной возкой из выемок разрабатываемых в возвышенностях в насыпи отсыпаемые в понижениях местности (рис. 1.10).
Работы целесообразно организовать так чтобы агрегат скрепер-трактор (или скрепер-тягач) поворачивался в плане на порожнем ходу так как поворот с грузом требует большего времени и большего расхода мощности. На рис. 1.10 а показаны правильная и неправильная схемы движения скреперов. Вторая схема неправильна поскольку приходится выполнять дна поворота в груженом состоянии: на выходе из забоя и на входе в отвал.
Схемы показанные на рис. 1.10 б и в наиболее рациональны так как на два рабочих цикла приходится всего по два поворота т.е. агрегаты перемещаются с минимально возможным числом поворотов и следовательно с наибольшей возможной скоростью причем повороты выполняют на порожнем ходу.
По аналогичным схемам профилируют трассы при строительстве магистральных водных каналов на пересеченной местности планируют большие площади – срезают послойно холмы и бугры и засыпают их грунтом впадины овраги лощины. Так же как и при смягчении профилей дорог и каналов смежное расположение забоя и отвала необязательно. Но средние расстояния между забоями и отвалами должны быть в пределах допускаемых дальностей перемещения грунта для применяемых типоразмеров скреперов.
Возведение дорожных и гидротехнических насыпей из боковых резервов. Для скреперных агрегатов должны быть созданы съезды на откосах резерва и насыпи причем по мере углубления резерва и возведения насыпи съезды и въезды должны сохранять уклоны приемлемые для безотказного движения агрегатов. Съезды и въезды сооружают самими скреперными агрегатами которые срезают излишние массы грунта при порожнем ходе и досыпают по мере надобности при движении с грунтом. При небольшом числе одновременно работающих скреперных агрегатов съезд и въезд часто устраивают в одном месте резерва или насыпи. Места для съездов и въездов выбирает производитель работ.
Рис. 1.10 - Схемы движения скреперов при перемещении грунта:
а – из выемки в насыпь; б – из двух выемок в одну насыпь; в – из одной выемки в две насыпи
Сооружение котлованов. Под крупные гидротехнические и промышленные объекты эту операцию организуют аналогично разработке резервов с обязательным устройством съездов и въездов на откосах котлована и кавальера (если последний отсыпают).
Отсыпка насыпей – подходов к земляным сооружениям (мостам или эстакадам). Сквозной проезд скреперов здесь исключается. Такие насыпи отсыпают «с головы» скреперами с помощью бульдозеров. Постепенно насыпи приближают к земляному сооружению. Скрепер разгружается на некотором удалении от «головы» насыпи а бульдозер смещает выгруженный грунт по поверхности насыпи в ее «голову». При этом должна быть обеспечена возможность разворота скреперного агрегата по насыпи на 180° для обратного хода. Если ширина насыпи не позволяет агрегату развернуться то для него должны быть предусмотрены съезды на откосе насыпи.
Вспомогательные работы. К ним относятся: удаление растительного слоя грунта транспортирование сыпучих грузов и планировочные работы.
Растительный слой удаляют при строительстве любых земляных сооружений со всей площади их основания. Если размеры основания искусственного сооружения в плане большие эту работу выполняют скреперными агрегатами. Скреперы срезают растительный слой грунта и отвозят его за пределы основания сооружения в отвал или в местную естественную впадину (например овраг лощину).
Транспортные работы выполняют скреперными агрегатами в перерывах основных скреперных работ или зимой когда скреперные работы прекращают.
Скреперные агрегаты перевозят грунты щебень гравий и другие сыпучие грузы не вызывающие затруднений при выгрузке. Погружают эти грузы в ковши скреперов экскаваторами одно - или многоковшовыми погрузчиками. Для этого используют также бункера и эстакады. Разгружают скреперы в отвалы или штабеля а при устройстве соответствующих эстакад – и в различную тару.
При планировочных работах срезают мелкие неровности (бугры кочки) и засыпают срезанным грунтом впадины и ухабы. Скреперы могут планировать площади и линейные объекты в том числе и пути для собственного движения по строительному объекту. В последнем случае скреперные агрегаты планируют поверхность перемещаясь порожняком.
Для планирования (рис. 1.11) ножи 1 порожнего скрепера опускают на уровень опорной поверхности заслонку 3 поднимают вверх до отказа а разгружающую стенку 2 устанавливают в крайнее переднее положение.
Приведенный в такое положение скрепер при движении вперед срезает ножами 1 местные выступы или неровности 4 и срезанным грунтом при дальнейшем движении засыпает впадины 5 или ухабы разравнивая (планируя) таким образом поверхность на пути движения. Нож и разгружающая стенка ковша в приданном им положении работают как бульдозерный отвал.
Пути движения скреперы планируют за несколько параллельных проходов (2 – 4 по одному следу) при порожнем движении из отвала в забой. Пониженная скорость порожнего движения компенсируется ускоренным груженым ходом и общим повышением производительности скреперов благодаря улучшению транспортных путей. Планируют пути по мере надобности например после обильных атмосферных осадков разрушения путей колесами движущихся машин.
Рис. 1.11 - Схема планирования грунтовых поверхностей скрепером:
– нож; 2 – разгружающая стенка; 3 – заслонка; 4 – выступающая неровность местности; 5 – засыпаемая впадина
РАСЧЕТ И МОДЕРНИЗАЦИЯ СКРЕПЕРА ДЗ-13
Скрепер ДЗ-13 (рис. 2.1) с принудительной разгрузкой и гидравлическим приводом предназначен для послойной разработки грунтов I-IV групп без сосредоточенных каменных включений при планировочных работах среднего объема. Базовой машиной скрепера служит одноосный колесный тягач БелАЗ-531 снабженный вертикально разнесенным опорным седельно-сцепным устройством.
Рис. 2.1 – Скрепер ДЗ-13
- тягач БелАЗ-531; 2 – седельно-сцепное устройство; 3 – дышло; 4 – заслонка; 5 – ковш; 6 – гидроцилиндр заслонки; 7 – задняя стенка; 8 – заднее колесо; 9 – буфер; 10 – ножи; 11 – гидроцилиндр ковша; 12 – гидроцилиндр поворота
Ковш сваренный из листового металла имеет две боковые стенки усиленные гнутыми профилями днище с передней подножевой плитой на которой закреплены средние и крайние ножи буферные балки и передние кронштейны к которым крепятся штоки гидроцилиндров подъема ковша. Кроме нижних ножей на боковых стенках закреплены боковые ножи для подрезания стружки грунта.
Полукруглая заслонка перекрывает полость ковша и поднимается двумя гидроцилиндрами двойного действия расположенными в плоскостях стенок ковша.
Заполняется ковш обычным порядком при поднятой заслонке с опущенным ковшом а разгружается принудительно – выдвижением задней стенки при поднятой заслонке.
Тяговое дышло через опорные проушины с помощью вертикальных пальцев крепится на седельно-сцепном устройстве тягача а с противоположной стороны П-образной рамой соединяется с ковшом боковыми шарнирами и двумя гидроцилиндрами двойного действия расположенными перед заслонкой. Перемещение штоков гидроцилиндров приводит к взаимному изменению положения ковша и дышла (опусканию или подъему ковша).
Поворачивается скрепер с помощью двух гидроцилиндров закрепленных на дышле с двух сторон. При этом выдвижение штока одного из гидроцилиндров соответствует повороту машины в сторону другого гидроцилиндра и наоборот. Конструкция скрепера предусматривает поворот на 90°.
Тягач оснащен гидромеханической трансмиссией которая в сочетании с пневмогидравлической подвеской тягача обеспечивает высокие транспортные скорости и уменьшает колебания кабины машиниста. Скрепер имеет электрогидравлическое управление рабочими органами и световую сигнализацию работающую от электрооборудования тягача.
Гидросистема управления рабочими органами скрепера (рис. 2.2) состоит из масляного бака двух фильтров трех шестеренных гидронасосов типа НШ-98 переливного золотника трех гидрораспределителей двух гидроцилиндров подъема и опускания ковша двух гидроцилиндров управления заслонкой ковша двух гидроцилиндров управления задней стенкой ковша предохранительного клапана рукавов и трубопроводов гидросистемы
Рис. 2.2 – Схема гидросистемы управления рабочими органами самоходного скрепера ДЗ-13:
– масляный бак 2 –гидронасос 3 – переливной золотник 4 – гидрораспределители 5 – гидроцилиндр управления задней стенкой ковша 6 – гидроцилиндр управления заслонкой ковша 7 – предохранительный клапан 8 – гидроцилиндр подъема и опускания ковша 9 – фильтр
Рабочими органами скрепера управляют из кабины машиниста с помощью рычагов управления гидрораспределителя. В каждым из них трубопроводами и рукавами соединены соответствующие гидроцилиндры управления рабочими органами скрепера.
Техническая характеристика скрепера ДЗ-13 приведена в таблице 2.1.
Таблица 2.1 – Техническая характеристика скрепера ДЗ-13
Вместимость ковша м3
Количество двигателей
Мощность силовой установки кВт
Способ разгрузки ковша
Управление рабочим органом
Наибольшее заглубление мм
Толщина осыпаемого слоя грунта мм
Дорожный просвет под ножами мм
Колея колес скрепера мм
Наибольшая скорость движения кмч
Габаритные размеры мм
Рабочее давление в гидроприводе МПа
Рабочий цикл скрепера состоит из четырех последовательно выполняющихся операций:
-загрузка ковша - ковш опущен заслонка поднята ножи врезаются в грунт и при движении вперед срезают стружку грунта которая наполняет ковш;
-груженый ход - ковш поднят в транспортное положение заслонка опущена и удерживает грунт в ковше;
-разгрузка ковша - заслонка поднята ковш опущен до уровня обеспечивающего заданную толщину отсыпки;
-порожний ход - ковш поднят до образования транспортного положения.
При работе скрепера наиболее неблагоприятным является момент когда ковш скрепера почти полностью загружен грунтом при продолжающемся процессе резания грунта.
Подбор тягача производится по максимальному сопротивлению движению скрепера.
Полное сопротивление движению скрепера при загрузке определяется по формуле:
FΣ=F1+F2+F3+F4+F5 кН(2.1)
где F1 - сопротивление движению скрепера кН;
F2 - сопротивление грунта резанью кН;
F3 - сопротивление движению призмы волочения впереди ковша скрепера кН;
F4 - сопротивление от веса срезаемого слоя грунта движущегося в ковше кН;
F5 - сопротивление от внутреннего трения грунта в ковше кН.
Сопротивление движению скрепера определяется по формуле
где Gc – вес скрепера Gc =334 кН;
Gгр – вес грунта в ковше по максимальной грузоподъемности Gгр=290 кН:
f – коэффициент сопротивления качению колес скрепера по грунту (f=01 015 - для плотных грунтов; f =015 02-для разрыхленных грунтов; f=02 025 - для сыпучих песков) принимаем f =02 ;
α - угол наклона пути движения скрепера к горизонту град знак + принимается при работе на подъем; - при работе на уклон
Сопротивление грунта резанью определяется по формуле
где Кp - удельное сопротивление грунта резанью (Кp=80 120 кПа) принимаем Кp=100 кПа;
b и h - ширина и толщина срезаемого слоя грунта (h=013 04 м) b=312 м принимаем h=025 м.
Сопротивление движению призмы волочения впереди ковша скрепера определяется по формуле
где y - отношение высоты призмы волочения к высоте грунта в ковше (y=05 065 причем большие значения для сыпучих грунтов) принимаем y=06;
Н - высота слоя грунта в ковше м. Ориентировочно Н=06b=06×312=187 м;
ρ - плотность грунта ρ=16 тм3;
g - ускорение свободного падения g=981 мс2;
- коэффициент трения грунта по грунту (=03 05 причем большие значения для песчаных грунтов) принимаем =04.
Сопротивление от веса срезаемого слоя грунта движущегося в ковше определятся по формуле
Сопротивление от внутреннего трения грунта в ковше определяется по формуле
гдех–коэффициент учитывающий влияние рода грунта (для глин х=024 031 для суглинков и супесей х=037 042 для песков х=045 05) принимаем х=04.
Подставляя результаты (2-6) получаем
При загрузке скрепера тягачом должно соблюдаться условие:
где Т – тяговое усилие базовой машины.
Тяговое усилие базовой машины Топределяется по формуле
гдеN-мощность двигателя базовой машины кВт N =265 кВт;
vP-скорость движения скрепера при копании грунта vP=0407 мс принимаем vP =05 мс.
Таким образом условие тягового расчета соблюдено.
Самоходный скрепер ДЗ-13 из-за конструктивных особенностей не может развивать тяговую силу необходимую для набора грунта в ковш и выполняют эту операцию с помощью трактора-толкача. Применение толкача окупается только при работе в скреперной бригаде состоящей не менее чем из трех или четырех скреперов; при этом расходы на содержание толкача раскладываются на все машины.
Однако имеется целый ряд вспомогательных или локальных работ небольших объемов для выполнения которых требуется один или два скрепера. В таких случаях существенным является обеспечение загрузки ковша скрепера без толкача.
В самоходном скрепере ДЗ-13 ведущими являются передние колеса одноосного тягача. Для использования скрепера в ряде случаев без толкача в проекте предлагается усовершенствовать задний мост сделав их активными т.е. установить на заднем мосте скрепера мотор-колеса (рис. 2.3).
Рис. 2.3 – Активный задний мост скрепера ДЗ-13
– Рама; 2 – Мотор-колесо; 3 – Колесо.
Конструкция мотор-колеса должна обеспечивать при простоте конструкции большой крутящий момент и малые габариты а также надежное торможение. Этим требованиям отвечает конструкция мотор-колеса содержащее ступиц опирающуюся посредством подшипников на ось колеса. Мотор-колесо снабжено пластинчатой гидромашиной ротор с пластинами которой соединен со ступицей а расположенный внутри ротора профилированный статор соединен с осью колеса выполненной с каналами подвода и отвода рабочей среды согласно изобретению соединение статора с осью колеса выполнено в виде многогранника с плоскими гранями по углам которого расположены зубья а на плоских гранях в зонах маслоканалов выполнены кольцевые канавки в которых размещены уплотнительные кольца согласно изобретению ось колеса снабжена многодисковым фрикционным стояночным тормозом блокирующим ступицу относительно оси колеса посредством усилий тарельчатых пружин с размещением растормаживающего силового кольцевого гидроцилиндра в теле оси колеса.
Оснащение мотор-колеса пластинчатой гидромашиной с соединением ротора со ступицей а расположенного внутри ротора профилированного статора с осью колеса позволяет обеспечить большой крутящий момент и значительно уменьшить габариты. Соединение статора с осью колеса в виде многогранника с плоскими гранями по углам которого расположены зубья а на плоских гранях вокруг маслоканалов выполнены кольцевые канавки в которых размещены уплотнительные кольца позволяет передать большой крутящий момент и в тоже время позволяет уплотнить каналы подвода и отвода рабочей среды. Снабжение мотор-колеса многодисковым фрикционным стояночным тормозом с тарельчатыми пружинами и с растормаживающим силовым кольцевым гидроцилиндром размещенным в теле оси колеса позволяет сократить габариты блокировать ступицу относительно оси колеса при длительной стоянке и особенно в аварийном режиме например при разрыве рукава высокого давления когда давление в гидросистеме падает и мотор-колесо становится неуправляемым.
Мотор-колесо (рис. 2.4) содержит пластинчатую гидромашину 1 ротор 2 с пластинами 3 которой соединен со ступицей 4 а расположенный внутри ротора 2 профилированный статор 5 соединен с осью колеса 6. Соединение профилированного статора 5 с осью колеса 6 выполнено в виде многогранника 7 с плоскими гранями 8 по углам которого расположены зубья 9. На плоских гранях 8 вокруг маслоканалов выполнены кольцевые канавки 10 в которых размещены уплотнительные кольца 11. Ось колеса 6 имеет многодисковый фрикционный стояночный тормоз 12 с тарельчатыми пружинами 13 и с растормаживающим силовым кольцевым гидроцилиндром 14 размещенным в теле оси колеса 6. Мотор-колесо крепится к раме машины фланцем 15 оси колеса 6 а колесо монтируется на фланце 16 ступицы 4. Ось колеса 6 имеет каналы 17 подвода и отвода рабочей среды.
Рис. 2.4 – Мотор-колесо
Мотор-колесо работает следующим образом. Среда управления подается в силовой кольцевой гидроцилиндр 14 который воздействует на тарельчатые пружины 13 растормаживая ступицу 4 относительно оси колеса 6. При подаче рабочей среды по каналам 17 через плоские грани 8 многогранника 7 и далее через профилированный статор 5 в рабочие камеры образованные пластинами 3 сила ее давления вращает ротор 2 пластинчатой гидромашины 1 и соединенную с ним ступицу 4 вокруг профилированного статора 5 и оси колеса 6. Зубья 9 передают крутящий момент. Уплотнительные кольца 11 предотвращают утечки рабочей среды.
Для изменения скорости вращения мотор-колеса при изменении скорости движения скрепера целесообразно применения гидропривода с дроссельным управлением (рис. 2.5). При дроссельном управлении часть жидкости подаваемой насосом отводится в сливную линию и не совершает полезной работы. При последовательном включении дросселя предусматривается переливной клапан который поддерживает в нагнетательном трубопроводе постоянное давление путем непрерывного слива рабочей жидкости.
Рис. 2.5 – Схема дроссельного управления скоростью гидромотора
– бак; 2 – насос; 3 – переливной клапан; 4 – управляемый дроссель; 5 – гидрораспределитель; 6 – гидромоторы; 7 - фильтр
Рабочий объем пластинчатого гидромотора двукратного действия
где R1 и R2 –соответственно большая и малая полуоси профиля поверхности статора;
b – ширина пластины;
d - толщина пластины.
Крутящий момент на валу гидромотора
где - перепад давления на гидромоторе =98 МПа
– механический КПД =094.
Расход рабочей жидкости через гидромотор
где п – частота вращения вала.
Частота вращения вала равна скорости вращения колеса
где vP-скорость движения скрепера;
При копании грунта со скоростью движения v =5 кмч.
Принимаем что наибольшие усилия открывания заслонки возникают когда ковш загружен «с шапкой». Следовательно при открывании заслонки приходится преодолевать давление грунта находящегося над заслонкой трение грунта о грунт вес самой заслонки.
Вес грунта находящегося в объеме заслонки зависит от ширины заслонки В высоты Н объема части «шапки» грунта над заслонкой (рис. 2.6) от длины l и от формы заслонки.
Рис. 2.6 – Схема расчета усилий для подъема заслонки
Для приближенных расчетов можно определить площадь проекции заслонки F на вертикальную плоскость. Тогда вес грунта в объеме заслонки V будет равен
гдеk–коэффициент учитывающий конфигурацию заслонки; k=08;
gГ– объемный вес грунта в естественном залегании gГ =19 кНм3.
Для определения сил трения грунта о грунт принимаем что на поднимаемый заслонкой грунт давит объем грунта находящегося в ковше ограниченный поверхностью АС и плоскостью АВ. Вес этого объема грунта
где m2 – коэффициент внутреннего трения грунта m2=036.
Усилие которое должно развивать гидравлическое устройство для подъема заслонки зависит от схемы расположения подъемного устройства. Это усилие определяется из уравнения моментов относительно оси поворота заслонки (точки О).
При гидравлическом управлении заслонка обычно поднимается при помощи двух цилиндров. Для нашей схемы усилие развиваемое каждым цилиндром равно
GЗ – вес заслонки GЗ=10 кН.
Проведем расчет гидравлического цилиндра механизма подъема заслонки. Давление в гидравлической системе р=10 МПа. Определим ориентировочный диаметр поршня из формулы:
Диаметр поршня принимаем dП=115 мм диаметр штока dШ=70 мм. Определяем максимальное усилие развиваемое цилиндром:
где АП и АШ – площади поршня и штока.
Усилие Fmax примерно соответствует значению подъемного усилия SП.
За расчетное положение принимается начало передвижения задней стенки при полной загрузке ковша грунтом и открытой заслонке. Сила F необходимая для выталкивания грунта определяется по формуле
F=Fд+ Fб+ Fк+ Ри(2.20)
где Fд– сила трения грунта о днище ковша;
Fб– сила трения грунта о боковые стенки ковша;
Fк– сила сопротивления качению роликов задней стенки по днищу ковша;
Ри–сила инерции поступательно движущейся массы грунта и задней стенки при включении механизма разгрузки ковша скрепера.
Сила трения грунта о днище ковша
где m1 – коэффициент трения грунта о сталь m1=075m2=075036=027;
q– геометрическая емкость ковша q=162 м3;
kн– коэффициент наполнения ковша kн=08;
kp– коэффициент разрыхления грунта kp=12
Сила трения грунта о боковые стенки ковша
где Еа– активное давление грунта на боковую стенку ковша.
где LK – длина ковша LK=25 м;
Н – высота наполнения ковша грунтом Н=16 м;
j2 – угол внутреннего трения грунта j2=20°.
Сила сопротивления качению роликов задней стенки по днищу ковша
где GCT – вес задней стенки GCT =11 кН;
f–коэффициент сопротивления качению роликов f=012.
где vc– скорость движения задней стенки vc=01 мс;
t– время разгона t=1 с;
g– ускорение свободного падения g=98 мс2;
После подстановки входящих величин окончательно получим
F=554+161+13+22=75 кН.
Проведем расчет гидравлического цилиндра механизма принудительной разгрузки ковша. Давление в гидравлической системе р=10 МПа. Определим ориентировочный диаметр поршня из формулы:
Диаметр поршня принимаем dП=120 мм диаметр штока dШ=70 мм. Определяем максимальное усилие развиваемое цилиндром:
Усилие Fmax примерно соответствует значению cилы F необходимой для выталкивания грунта из ковша.
ТЕХНИЧЕСКОЕ ОБСЛУЖИВАНИЕ И РЕМОНТ
Техническое обслуживание и ремонт машин совместно с их транспортированием и хранением согласно ГОСТ 25866—83 составляют техническую эксплуатацию
Техническое обслуживание (ГОСТ 18322—78) — это комплекс операций или операция по поддержанию работоспособности либо исправности машин при использовании их по назначению а также хранении и транспортировании.
Ремонт — это комплекс операций по восстановлению исправности или работоспособности машин и восстановлению их ресурсов или составных частей.
Процесс определения технического состояния составных частей и машин в целом для выяснения необходимости их технического обслуживания или ремонта а также для контроля качества выполненных работ называют техническим диагностированием. Оно является составной частью технического обслуживания и ремонта машин и организуется в соответствии с требованиями ГОСТ 25044—81.
Совокупность взаимосвязанных средств документации технического обслуживания и ремонта а также исполнителей необходимых для поддержания и восстановления качества машин входящих в эту систему составляет систему технического обслуживания и ремонта машин.
В зависимости от этапа эксплуатации периодичности объема работ условий эксплуатации и других признаков выделяют следующие виды технического обслуживания и ремонта. Техническое обслуживание при использовании машин подразделяется на ежесменное (ЕТО) сезонное (СО) и периодическое техническое обслуживание (ТО). Последнее включает в себя первое (ТО-1) второе (ТО-2) и третье (ТО-3) техническое обслуживание. По объему работ ремонт подразделяется на текущий (Т) и капитальный (К). При текущем ремонте восстанавливают работоспособность машин путем замены и (или) восстановления их отдельных составных частей.
При текущем ремонте восстанавливают исправность и полный (или близкий к полному) ресурс машин заменой или восстановлением большого количества их составных частей включая базовые.
Интервал времени между отдельными видами периодического технического обслуживания (ремонта) называется периодичностью технического обслуживания (ремонта). Периодичность измеряется в моточасах учитываемых по счетчику. Ежесменное техническое обслуживание выполняют на протяжении всего периода смены. Критерием проведения сезонного технического обслуживания является температура окружающего воздуха. При установившейся температуре окружающего воздуха выше 5 °С проводят сезонное техническое обслуживание машин с целью подготовки их к весенне-летнему периоду эксплуатации а при температуре ниже 5 °С — к осенне-зимнему периоду эксплуатации. Проведение сезонного технического обслуживания совмещают с очередным плановым техническим обслуживанием. Затраты труда на выполнение одного вида технического обслуживания (ремонта) машины называются трудоемкостью а время его проведения — продолжительностью технического обслуживания (ремонта). Оба названных показателя являются важными так как по ним оценивается совершенство технического обслуживания и ремонта машин. Показатели технического обслуживания и ремонта скрепера ДЗ-13 приведены в табл. 3.1 (по данным «Рекомендаций по организации технического обслуживания и ремонта строительных машин». — М.. 1993).
Таблица 3.1 - Периодичность трудоемкость продолжительность технического обслуживания и ремонта скрепера ДЗ-13
Тип и типоразмер машин
Вид технического обслуживания и ремонта
Периодичность выполнения технического обслуживания и ремонта ч
Трудоемкость выполнения одного технического обслуживания и ремонта чел.-ч
Продолжительность одного технического обслуживания и ремонта ч
Самоходный скрепер ДЗ-13 с ковшом вместимостью 15 м3
Перечни работ являются основой технического обслуживания машин; их устанавливают для каждого вида технического обслуживания исходя из необходимости обеспечения заданного уровня надежности машин. Каждая из работ включенная в перечень обеспечивает безотказность или долговечность отдельных деталей сборочных единиц или составных частей машин. Все работы входящие в состав технических обслуживании разделены на моечно-очистные крепежные контрольно-регулировочные заправочно-смазочные.
Начальными в обобщенном перечне работ являются операции ежесменного технического обслуживания (ЕТО) машины когда ее очищают от пыли и грунта проверяют герметичность систем питания охлаждения и смазочной системы двигателя крепление деталей а также уровень топлива в баке масла в картере двигателя рабочую жидкость в баке гидросистемы жидкости в системе охлаждения двигателя и смазывают машину в соответствии с таблицей смазки. При необходимости подтягивают крепления устраняют подтекание топлива масел рабочей и охлаждающей жидкостей. В заключение проверяют исправность системы управления машиной сигнализации и освещения.
При первом техническом обслуживании (ТО-1) необходимо: выполнить работы ЕТО и кроме того осуществить наружную мойку машины; проверить натяжение ремней вентилятора и давление в шинах уровень электролита в аккумуляторной батарее и состояние ее зажимов и вентиляционных отверстий; слить отстой топлива из бака и фильтров и конденсат из баллонов пневмосистемы; долить при необходимости масло в отдельные картеры и смазать составные части машин согласно таблице смазки.
В период второго технического обслуживания (ТО-2) необходимо: выполнить работы ТО-1 и при необходимости отрегулировать двигатель сцепление тормоза фрикционы управление натяжение гусеничных лент цепей а также сходимость колес давление открытия предохранительных клапанов гидросистемы и пневмосистемы; измерить плотность электролита и при необходимости подзарядить аккумуляторную батарею; обслужить воздухоочиститель и сапуны; заменить масло в картере двигателя и компрессора; очистить масляную центрифугу и фильтры гидросистемы а также подтянуть крепление деталей и смазать составные части согласно таблице смазки.
При третьем техническом обслуживании (ТО-3) машины необходимо: выполнить работы ТО-2 и кроме того проверить и при необходимости отрегулировать пусковое устройство подшипники направляющих колес и опорных катков гусеничного ходового устройства а также топливный насос и стартер; очистить и промыть фильтр-отстойник топливного бака и карбюратор пускового двигателя топливные фильтры или заменить их фильтрующие элементы.
При сезонном техническом обслуживании машин (СО) в процессе подготовки ихдс осенне-зимнему периоду эксплуатации следует заправить систему охлаждения двигателя охлаждающей жидкостью не замерзающей при низкой температуре; включить предпусковой подогреватель двигателя; установить утеплительные чехлы; отключить радиаторы смазочной системы двигателя и гидросистемы а также перевести винт сезонной регулировки реле-регулятора в положение «3»; довести плотность электролита в аккумуляторной батарее до зимней нормы и заменить зимними сортами масла смазку и рабочую жидкость согласно таблице смазки. При подготовке машин к весенне-летнему периоду эксплуатации во время сезонного технического обслуживания необходимо снять утеплительные чехлы; отключить предпусковой подогреватель; включить радиаторы смазочной системы двигателя и гидросистемы а также перевести винт сезонной регулировки реле-регулятора в положение «Л»; довести плотность электролита в аккумуляторной батарее до летней нормы и заменить летними сортами масла смазку и рабочую жидкость согласно таблице смазки. При необходимости удалить накипь из системы охлаждения двигателя и промыть систему.
Конкретные перечни работ технического обслуживания по каждой марке машин содержатся в руководстве по эксплуатации.
Под технологией понимается совокупность приемов и способов выполнения работ технического обслуживания. Необходимость в проведении указанных работ определяется состоянием составных частей и машины в целом которое оценивается номинальным (начальным) допустимым и предельным значениями показателей. Первое из них характеризует состояние новой или отремонтированной машины второе соответствует исправному техническому состоянию машины (составной части) когда она выполняет свои функции с эксплуатационными показателями в заданных пределах третье представляет собой наибольшее (или наименьшее) допустимое значение показателя за пределами которого дальнейшая эксплуатация машины (составной части) становится неоправданной опасной и может привести к отказу или аварии. Номинальное значение показателей обеспечивается при изготовлении машин (составных частей) на заводе при ремонте или техническом обслуживании. Если техническое состояние остается в пределах допустимых значений показателей то машину (составную часть) можно эксплуатировать. Как только техническое состояние достигнет предельного значения следует выполнять техническое обслуживание.
Техническое диагностирование (ГОСТ 27518—87) проводят для определения технического состояния машины. Плановое диагностирование должно выполняться после того как машина отработает установленное количество часов перед плановым техническим обслуживанием. Диагностирование (заявочное) может быть проведено также при возникновении неисправности для поиска дефекта. Бывает также ресурсное диагностирование целью которого является определение остаточного ресурса сборочных единиц и машины в целом; его проводят при плановом диагностировании.
Технология технического обслуживания двигателей внутреннего сгорания устанавливаемых на дорожных и строительных машинах изложена в руководстве по их эксплуатации поставляемом вместе с машиной. В число наиболее сложных работ технического обслуживания двигателей входит регулирование распределительного и декомпрессионного механизмов натяжения ремней вентилятора давления впрыска топлива форсунками угла опережения подачи топлива а также удаление накипи в системе охлаждения и очистка фильтрующих элементов систем смазывания и питания.
В технологии технического обслуживания ходового устройства трансмиссии системы управления основными работами являются: регулирование сцепления натяжение гусеничных лент а также накачивание шин воздухом и диагностирование механизма управления. Регулировочными показателями сцеплений являются: зазор между отжимными рычагами и отжимной муфтой свободный ход педали. Давление воздуха в шинах колес машин с пневмоколесным ходовым устройством проверяют с помощью шинных манометров или приспособления КИ-8903; правильность натяжения гусеничных лент проверяют по значению их провисания. Правильность действия механизма управления поворотом машин на гусеничном ходу определяют по свободному и полному ходу рычагов управления а исправность действия тормозов ходовой части — по ходу педалей. Правильность регулирования механизма управления поворотом машин на пневмоколесном ходу проверяют по свободному ходу рулевого колеса с помощью прибора К-402 колесных тормозов — по ходу штоков а стояночных — по зазору между лентой (колодкой) и барабаном. К основным работам по техническому обслуживанию гидросистемы относятся: очистка фильтрующих элементов регулирование предохранительных клапанов промывка гидроборудования и замена рабочей жидкости. Если давление в сливной линии замеренное манометром ниже номинального то необходимо очистить фильтрующие элементы гидросистемы удалить пыль с корпуса фильтров фильтрующие элементы опустить в ванну с дизельным топливом и тщательно промыть а затем продуть сжатым воздухом подаваемым от компрессора через специальный наконечник. Правильность регулировки предохранительных клапанов гидросистемы проверяют при нормальной температуре рабочей жидкости: открывают кран напорной линии и поворачивают рукоятку до полного выдвижения штока ее гидроцилиндра. В таком положении фиксируют показания манометра. Клапан считается работоспособным если давление в системе находится в пределах нормального. При падении давления более чем на 05 МПа от нормального предохранительный клапан регулируют вращением регулировочного винта.
Техническое обслуживание гидравлического оборудования машин проводят на стационарном посту эксплуатационной базы или с помощью передвижной станции. В пост обслуживания гидросистем входят: оборудование для очистки рабочей жидкости и контроля ее чистоты средства диагностирования технического состояния гидросистемы и помещение для обслуживаемой машины.
Особое внимание уделяют промывке фильтрующих элементов компрессоров как сосудов работающих под давлением. Фильтрующий элемент помещается на 15 20 мин в раствор моющих веществ или стиральных порошков бытового назначения при температуре теплой воды 40 50°С. Концентрация моющих веществ составляет 20 25 г на 1 л воды. Промывка производится последовательным погружением и вращением после чего элемент прополаскивают в чистой теплой воде и тщательно просушивают теплым воздухом температурой не выше 60 °С.
На дорожных и строительных машинах техническое обслуживание электрооборудования заключается во внешнем осмотре источников электропитания сети освещения и сигнализации а также входящих в них приборов.
При всех видах технического обслуживания необходимо проверить работоспособность колесного и ручного тормозов ходовой части машины и замерить ход тормозной педали при работающем двигателе во время нахождения машины на стоянке. Также следует осмотреть гидроусилитель тормозов а при ТО-1 замерить тормозной путь машины. Действие ручного тормоза нужно проверять тогда когда машина установлена на сухую и чистую бетонную поверхность с уклоном 15 %; при регулировании тормозов следует устранить обнаруженные неисправности.
При выявлении трещин и обломов выходящих на рабочие поверхности тормозных шкивов и подходящих к отверстиям под заклепки тормозных накладок а также при износе рабочей поверхности обода шкива более 25 % первоначальной толщины и тормозной накладки по толщине до появления головок заклепок или более 50 % первоначальной толщины машина должна быть снята с дальнейшей эксплуатации. Шкивы и накладки при этом необходимо заменить на исправные. Машинисты должны проводить техническое обслуживание в соответствии с инструкцией определяющей их обязанности и порядок безопасного производства работ.
При проверке состояния кабин необходимо следить за тем чтобы стекла не имели трещин а стеклоочистители перемещались и обеспечивали тщательную очистку лобового стекла. Для предотвращения самопроизвольного открывания дверей кабин следует проверить исправность замков. Двери кабин должны плотно закрываться так как через отверстия просачивается пыль и загрязняется воздух. Особое внимание нужно обращать на наличие чехлов в местах прохождения рычагов и педалей. Подушку и спинку сиденья необходимо содержать в хорошем техническом состоянии и следить за тем чтобы не было провалов выступающих пружин и острых кромок.
Для поддержания органов управления в исправном состоянии их необходимо периодически проверять смазывать и регулировать. Операции технического обслуживания органов управления связаны с осмотром очисткой и устранением неисправностей их сборочных единиц и деталей. Управление муфтами нужно отрегулировать так чтобы они надежно включались и выключались. Во избежание самовключения или самовыключения механизмов рычаги управления должны надежно фиксироваться во всех положениях. Шарниры рычагов следует систематически смазывать для снижения усилий по их включению а следовательно и снижения утомляемости машиниста в процессе работы.
Совокупность действий персонала эксплуатационной базы по восстановлению работоспособности машин с помощью средств технического обслуживания и ремонта называется производственным процессом ремонта машин. Совокупность приемов и способов выполнения работ по восстановлению работоспособности машин составляет технологический процесс. Различают технологический процесс текущего и капитального ремонта машины составной ее части сборочной единицы и детали (ГОСТ 2.602—55).
Технологический процесс текущего ремонта машин включает в себя: их приемку от потребителя; очистку и мойку; оценку технического состояния; снятие с машины составных частей требующих ремонта разборку их на детали; мойку и дефектацию деталей; комплектование годных к применению деталей; сборку составных частей; обкатку; испытание; установку на машину. При проведении текущего ремонта агрегатным методом технологический процесс ремонта машины упрощается. Исключается разборка составных частей их дефектация комплектование деталей сборка а также обкатка и испытание.
Участок эксплуатационной базы мастерской или ремонтного завода оснащенный оборудованием необходимым для выполнения определенной операции одним рабочим звеном или бригадой называют рабочим местом. Так на одном из рабочих мест машины очищают от грунта и пыли моют их используя для этого моечную установку пароводоструйные очистители и другое оборудование. На следующем рабочем месте с машин снимают составные части требующие ремонта.
При необезличенном методе ремонта машин снятые с них составные части направляют на рабочие места для ремонта где их разбирают используя для этого стенды подставки съемники и другие приспособления. После мойки деталей проверяют наличие дефектов результаты проверки заносят в ведомость дефектов; по ней затем определяется объем ремонтных работ и количество запасных частей. Годные новые и восстановленные детали комплектуют по составным частям и сборочным единицам согласно спецификации приведенной в картах на сборку или комплектовочным картам.
Плановое диагностирование должно быть организовано перед плановым ремонтом или совместно с ним. Обычно машины диагностируют на тех же постах эксплуатационных баз или ремонтных предприятий где осуществляется непосредственно ремонт деталей и сборочных единиц для чего эти посты оснащаются соответствующими средствами технического диагностирования. Диагностирование машин на месте их использования выполняют с помощью оборудования и приборов размещенных в передвижных мастерских. Для уточнения сроков постановки машин на текущий ремонт или отправки их в капитальный ремонт проводят ресурсное диагностирование.
При текущем ремонте заменяют детали срок службы которых равен межремонтному периоду. Такие детали к концу межремонтного периода как правило изнашиваются. Фрикционные накладки сцеплений тормозов муфт поворота если они изношены заменяют новыми а также заваривают трещины в металлоконструкциях правят. Кроме того при текущем ремонте проверяют размеры посадочных мест ответственных соединений; замеряют зубья зубчатых зацеплений; заменяют уплотнения где обнаружена течь масла; проверяют корпуса редукторов и при выявлении дефектов ремонтируют их или заменяют; а также проверяют подшипники и штифтовые соединения рамы опорно-поворотное устройство.
Текущий ремонт организуют одним из трех способов: индивидуальным агрегатным и смешанным.
Индивидуальный способ применяется при небольшом числе эксплуатируемых однотипных машин (например катков или автокомпрессоров) когда сборочные единицы снимаемые с машины ремонтируются и вновь устанавливаются на нее сохраняя принадлежность к отремонтированным составным частям.
Агрегатный способ заключается в замене на ремонтируемой машине неисправных сборочных единиц новыми или заранее отремонтированными в условиях эксплуатационной базы и строительной площадки. Дорожные и строительные машины предпочтительно ремонтировать агрегатным методом так как их легко расчленить на сборочные единицы которые имеют свойства полной взаимозаменяемости легкой отделяемости от составных частей независимой сборки без сложных регулировочных операций. Агрегатный ремонт машин целесообразен и на месте их использования. При очередном техническом обслуживании машин выявляют сборочные единицы требующие ремонта комплектуют их за счет обменного фонда и в установленный планом день привозят их на передвижной мастерской к месту работы машины и устанавливают на нее вместо изношенных сборочных единиц. Тут же выполняют ТО-3 заменяя при этом те составные части машины которые требуют регулирования и испытания в стационарных мастерских. Для ремонта машин агрегатным методом на месте их использования применяются передвижные мастерские грузовой автомобиль и автомобильный кран если на грузовом автомобиле отсутствует крановая установка. Для выполнения ремонта агрегатным способом необходим оборотный фонд исправных деталей и сборочных единиц а также ремонтное предприятие.
Смешанный способ ремонта применяется при небольшом парке машин и наличии оборотного фонда деталей и сборочных единиц. Сущность смешанного способа ремонта состоит в том что все сборочные единицы с одинаковыми ресурсами группируют в ремонтные комплекты на заводах а их установку на машине взамен неисправных проводят на эксплуатационных базах.
Перед установкой машины на текущий ремонт машинист вместе с механиком устанавливает по фактическому техническому состоянию а также по записям в журнале учета ремонта перечень необходимых ремонтных работ определяет потребность в запасных частях материалах и дополнительной рабочей силе.
Текущий ремонт выполняют специализированные бригады с участием машиниста что обеспечивает высокое качество ремонтных работ. После текущего ремонта машину испытывают.
Капитальный ремонт выполняемый по ремонтной документации для восстановления исправности и полного или близкого к полному восстановления ресурса машины предусматривает полную разборку машины дефектацию восстановление и замену деталей сборку регулирование и испытание. В капитальный ремонт машины направляют на основании тщательного анализа их предельного технического состояния. Критериями предельного состояния служат: усталостные трещины зазоры по посадкам подшипников деформации люфты износ а также выработка поверхности катания обломы удлинение детали и уменьшение диаметра детали. Поступающие в капитальный ремонт машины на ремонтных предприятиях не обезличивают. Отремонтированные машины поступают к тем же владельцам от которых они прибыли в ремонт. Сборочные единицы и детали в них при капитальном ремонте могут обезличиваться за исключением базовых составных частей сборочных единиц механической гидравлической и электрической систем а также зубчатых колес колец разобранных подшипников взаимно приработанных и совместно обработанных. Все составные части приборы и детали должны быть закреплены как это предусмотрено конструкцией.
Основным методом ремонта является организация специализированных постов которые располагаются в определенной технологической последовательности выполнения работ: чистки и наружной мойки разборки на основные сборочные единицы разборки и мойки сборочных единиц и деталей определения дефектов деталей и сборочных единиц а также ремонта и восстановления деталей ремонта рам ремонта рабочего оборудования сборки и испытания сборочных единиц сборки и испытания гидрооборудования. Собранные после ремонта сборочные единицы подвергают стендовой обкатке и испытанию. Сборочные единицы выдержавшие испытания и принятые ОТК заправляют свежим маслом и подают на пост общей сборки где их устанавливают на составные части. Отремонтированная машина поступает на пост стационарных испытаний в объеме определяемом специальной программой испытаний. Испытанную машину комплектуют ЗИП и передают на площадку готовой продукции.
При ТР ходовой части колесных машин (с зависимой подвеской) устраняют повреждения балки передней оси восстанавливают радиальный зазор между шкворнем и его втулками заменяют уплотнения и роликовые подшипники ступиц передних колес.
Цилиндрические винтовые пружины практически не ремонтируют. Неисправные или имеющие признаки усталости пружины выбраковывают.
Для листовых рессор характерны поломка и трещины одного из листов потеря упругости и износ листов рессор по толщине поломка хомутов срез или обрыв центрального болта и др.
При замене хомутов и ушек срубают заклепки. Новые крепления выполняют с помощью заклепок нагретых до 800 1000°С. Разборку и сборку рессор выполняют на стенде или винтовых приспособлениях. Peмонт рессор заключается в разбор замене изношенных и поломанных деталей. Перед сборкой ты рессоры смазывают графитовой смазкой. Сборка рессоры считается правильной если ее листы касаются друг к другу концами. В средней части рессоры максимально допустимый зазор без нагрузки составляет 1 мм и он должен уменьшаться к концам и центральному болту.
Основными неисправностями шин и камер являются прорывы проколы износ протектора обрыв и отслоение корда потеря упругости трещины и др. При снятии колес используют подъемники для вывешивания машины гайковерты для отвинчивания гаек колес тележки для снятия установки и перевозки колес. Демонтаж колес выполняют на специальных установках. Проколы камеры и небольшие повреждения покрышек устраняют горячей вулканизацией при температуре 140 150°С и давлении 06 12 МПа которое создается в пресс-формах струбцинами и с помощью другого специального оборудования. В ЭП при ТР обычно применяют электровулканизаторы. Для выявления повреждений камеру наполненную воздухом погружают в резервуар с водой. Ремонтируемые места подвергают шерохованию очищают от пыли и покрывают два раза клеем (просушивая каждый слой). Одновременно с этим подготавливают заплату которая должна перекрывать прорыв по окружности на 20 30 мм. После полного высыхания клея заплату накладывают на поврежденное место прикатывают роликом и устанавливают вулканизационный аппарат на 15 20 мин. При ремонте камер могут использоваться самовулканизирующиеся материалы.
Своевременный ремонт местных повреждений покрышек (пробоев порезов трещин) предупреждает дальнейшее разрушение шин в эксплуатации повышая их пробег на 5 10%. Способ ремонта определяется степенью повреждения и используемыми материалами. Обработка поврежденных мест выполняется различными способами. Для удобства доступа к внутренней части покрышки при вырезании сквозных повреждений применяют борторасширители. Участки покрышки подготовленные к ремонту подвергают шерохованию в соответствии с намеченным способом ремонта. Подготовленные поверхности покрышки и пластырь промазывают два раза клеем затем заделывают повреждения вулканизируют. Размеры пластырей и число слоев корда в них выбирают в зависимости от характера и размера повреждений нормы слойности покрышки и вида применяемых материалов. Вулканизацию покрышек проводят на специальном оборудовании при одностороннем или двустороннем обогреве поврежденного места. Восстановление шин наложением (наваркой) нового протектора выполняют специализированные ремонтные предприятия. Практика показывает что более 10% повреждений шин проводит в результате нарушения технологии монтажно-демонтажных операций. Монтажу подлежат только исправные чистые сухие соответствующие по размерам и типам шины камеры ободные ленты ободья и их элементы. Новые шины и шины восстановление методом наложения протектора должны укомплектовываться новыми камерами и ободными лентами.
Ободья и их элементы должны быть правильной формы без механических повреждений (погнутостей острых кромок и т. п.) и очищены от ржавчины. Рекомендуется проверять осевое (торцевое) и радиальное биения обода которые не должны превышать соответственно 20 25 мм и 25 30 мм (в зависимости от размера обода). Перед монтажом покрышку внутри камеру и ободную ленту припудривают тальком по всей поверхности. При монтаже шин на ободья необходима учитывать направленность рисунка протектора и место установки колеса. Колеса машин с большими скоростями движения балансируют на специальных стендах.
БЕЗОПАСНОСТЬ И ЭКОЛОГИЧНОСТЬ ПРОЕКТА
Общие требования безопасности к строительным и дорожным машинам изложены в ГОСТ 12.3.033-84 «Система стандартов безопасности труда. Строительные машины. Общие требования безопасности при эксплуатации».
Работа скреперов всегда связана с некоторой опасностью как для самой машины и ее оператора так и для работающих рядом с ними людей. Это особенно справедливо для машин зачастую эксплуатируемых в сложных стесненных условиях строительных площадок карьеров складских и заводских территорий.
Как правило повреждения машин и травмирование людей являются следствием несоблюдения требований и правил составленных для работы различных машин в специфичных для них эксплуатационных условиях.
Цель обеспечения безопасности работы — полное исключение случаев производственного травматизма увечий и потери трудоспособности людей а также сбережение производственной техники от повреждений и поломок.
Безопасную для себя и окружающих работу может обеспечить каждый работник хорошо изучивший приемы работы и соблюдающий правила техники безопасности.
Для обеспечения безопасной работы разработана и непрерывно совершенствуется специальная отрасль техники — техника безопасности. Техника безопасности — совокупность всех мероприятий по обеспечению безопасной работы людей и машин в промышленности строительстве и других областях народного хозяйства. Техникой безопасности установлен ряд правил и запретов для работы самоходных строительных и дорожных машин в том числе и погрузчиков. Неукоснительное соблюдение правил и запретов техники безопасности является основой для полной ликвидации производственного травматизма людей и аварий машин. Правила и запреты техники безопасности для работы на автогрейдерах в некоторой части являются общими для всех самоходных строительных и дорожных машин.
1.1. Анализ потенциально опасных и вредных факторов. При работе на скреперах на организм работающего оказывают вредное влияние различные факторы. Анализ потенциально опасных и вредных факторов приведен в таблице 4.1.
Таблица 4.1 – Анализ потенциально опасных и вредных факторов
Опасные и вредные факторы
Нормируемое значение параметра
Возможные воздействия
Установка устройства
Снижение слуха головные боли
СНиП РК 4.02-05-2001
Нарушение терморегуляции
СНиП РК 2.04-05-2002
Снижение работоспособности ухудшение зрения
Нарушение функций дыхательных путей
Спазма сосудов отложение солей
СНиП РК 1.02-0.11-94
Отравление генетические нарушения
Электроофтальмия электротравма удар и термические ожоги
1.2 Требования безопасности при земляных работах. Общие требования. Безопасности людей и машин предотвращению аварий и несчастных случаев в нашей стране придается большое значение. С этой целью постоянно совершенствуются конструкции машин улучшаются условия труда машиниста разработаны специальные требования и правила безопасности которые машинист должен знать и выполнять неукоснительно. Залогом безопасной работы являются отличное знание машинистом устройства и правил работы на машине и ее исправность.
При эксплуатации скреперов необходимо руководствоваться правилами приведенными в СНиП РК-1.03-05-2001 и системе стандартов ССТБ.
При перемещении машин своим ходом или на транспортном средстве особенно с выездом на автомобильные дороги необходимо строго выполнять требования правил дорожного движения. Особую осторожность следует проявлять при переездах через железнодорожные пути мосты и искусственные сооружения с учетом указанных на них допускаемых нагрузок и габаритов.
На рабочей площадке должны быть приняты меры предотвращающие опрокидывание или сползание машин. Откосы и косогоры на которых предстоит работать машине не должны превышать значений допускаемых техническим паспортом.
В случае расположения рабочей площадки около линии электропередач (ЛЭП) необходимо учитывать требования электробезопасности. В этих зонах можно работать только при письменном разрешении и под наблюдением лиц ответственных за безопасность.
При работе в темное время суток следует периодически очищать от грязи и пыли отражатели фар и плафонов.
Во время перерывов и по окончании работ машина должна быть установлена на ровной площадке и заторможена. Рычаги органов управления ставят в нейтральное положение а кабину запирают. Не допускается оставлять машину с работающим двигателем. Во время осмотра машины рабочий орган (отвал ковш) должен быть опущен на грунт двигатель выключен или отключен привод.
Чтобы предотвратить несчастные случаи запрещается:
допустить к работе необученных рабочих и посторонних лиц;
приступать к работе или продолжать ее при обнаружении любой неисправности;
устанавливать машину на свеженасыпанном неутрамбованном грунте;
переезжать через кабели трубопроводы без специальных защитных укрытий;
перевозить посторонних людей в кабинах;
запускать двигатель используя движение под уклон;
останавливать машину на уклонах; в случае вынужденной остановки на уклоне необходимо выключить двигатель затормозить машину ручным тормозом или подложить под колеса (гусеницы) упоры;
находиться под поднятым рабочим органом (отвалом ковшом заслонкой) удерживаемым гидроцилиндром или канатом;
пользоваться открытым огнем для ускорения пуска двигателя и или разогрева масла в картерах коробок передач и ведущих мостов а также эксплуатировать машину при течи в топливных и масляных системах.
2 Разработка мероприятий по улучшению условий труда и ТБ при работе погрузчика. Защита от вибрации
2.1. Действие вибрации на организм человека
Под вибрацией понимают движение точки или механической системы при котором происходит поочередное возрастание и убывание во времени значений какой-либо величины.
Тело работающего человека условно рассматривают как своеобразную колеблющуюся систему поскольку под воздействием вибрации части тела человека перемещаются относительно друг друга с амплитудами в зависимости от источника колебаний и массы органов. Относительные перемещения частей тела приводят к напряжениям в связках между частями тела и взаимному соударению и надавливанию.
Продолжительные колебания человека с частотой f=3 5 Гц вредно отражаются на вестибулярном аппарате сердечно-сосудистой системе и вызывают синдром укачивания. Колебания с частотой f=5 11 Гц вызывают расстройства вследствие резонансных колебаний головы желудка кишечника в конечном счете всего тела. При колебании с частотой f==11 45 Гц ухудшается зрение возникают тошнота рвота нарушается нормальная деятельность других органов. Колебания с частотой f³45 Гц вызывают повреждение сосудов головного мозга; происходит расстройство циркуляции крови и высшей нервной деятельности с последующим развитием вибрационной болезни.
Тело человека рассматриваемое как вязкоупругая механическая система обладает собственными частотами и достаточно выраженными резонансными свойствами. Резонансные частоты (Гц) отдельных частей тела человека следующие: головы — 12 27 горла — 6 27 грудной клетки— 2 12 йог и рук — 2 8 поясничной части позвоночника— 4 14 живота — 4 12.
Степень вредного воздействия колебаний на организм человека зависит от частоты продолжительности и направления действия вибрации.
Характерные случаи в области механизации строительства передачи вибрации телу человека показаны на рис. 4.1: через сиденье 1 от неровностей дороги 2 и неуравновешенности двигателя 3 (рис. 4.1 а). Эта вибрация возникает на скреперах бульдозерах автогрейдерах грузовых автомобилях тракторах и других самоходных машинах; через сиденье кабины управления 1 подвешенной к башне 3 вследствие колебания крана при подъеме или опускании груза 2 (рис. 4.1 б). К таким кранам относят самоходные башенные и стреловые самоходные; через пол 1 рабочего места от вибрации стенда 2 (рис. 4.1 в) на котором испытывается генерирующий вибрации механизм (например двигатель внутреннего сгорания или вибрационная площадка для уплотнения бетона в железобетонных конструкциях); через пол 1 рабочего места расположенного на формующем агрегате бетоноукладчика 2 (рис. 4.1 г); от пневматической или электрической ручной машины (рис. 4.1 д) и от органов управления самоходной машины (рис. 4.1 е).
Действующие гигиенические оценки вибрации изложены в СанПиН РК 1.02.012-94 – «Санитарные нормы вибрации рабочих мест». По способу передачи на человека вибрацию делят на общую передающуюся через опорные поверхности на тело сидящего или стоящего человека и локальную передающуюся через руки человека. Направление действия общей вибрации принято оценивать вдоль осей ортогональной системы координат X Y Z. Общую вибрацию в зависимости от источника ее возникновения подразделяют на следующие категории: 1—транспортную (от подвижных машин и транспортных средств: тракторы автомобили грузовые скреперы грейдеры бульдозеры); 2 — транспортно-технологическую (экскаваторы краны промышленные и строительные); 3 — технологическую (станки металлообрабатывающие кузнечно-прессовое оборудование литейные машины).
Гигиеническую оценку вибрации производят одним из трех методов: частотным (спектральным) анализом; интегральной оценкой по частоте и дозой вибрации. При частотном анализе нормируемыми' параметрами являются средние квадратические значения виброскорости V (и их логарифмические уровни Lv) или виброускорения а для локальной вибрации в октавных полосах частот а для общей вибрации — в октавных или 13 октавных полосах частот.
Рис. 4.1 – Примеры передачи вибрации телу человека
Измерение вибрации производится приборами-измерителями вибрации (виброметрами). В зависимости от назначения и измеряемой величины приборы подразделяют на измерители ускорений скорости и перемещения. Приборы основаны на пьезоэлектрическом магнитоэлектрическом индуктивном тензометрическом и других методах.
2.2 Методы и средства вибрационной защиты
Под вибрационной защитой имеют в виду совокупность средств и методов уменьшения вибрации воспринимаемой защищаемыми объектами. Под уменьшением вибрации понимают уменьшение значений каких-либо определенных величин характеризующих вибрацию.
Методы и средства вибрационной защиты изложены в ГОСТ 12.4.064—78. Этот стандарт устанавливает классификацию методов и средств предназначенных для уменьшения вредного воздействия вибраций на оператора ручных стационарных самоходных и транспортных машин. Ниже приведена краткая классификация методов и средств вибрационной защиты.
Методы вибрационной защиты: по виду реализации снижающие передачу вибрации при контакте оператора с вибрирующим объектом (использование дополнительных устройств встраиваемых в конструкцию машины; демпфирующие покрытия); по принципу действия (виброизоляция динамическое виброгашение); по использованию дополнительного источника энергии (активная виброизоляция); пассивное и активное динамическое виброгашение.
Средства вибрационной защиты подразделяют на: пассивные и активные; динамическое виброгашение (ударные и динамические виброгасители); по конструктивному признаку (металлические полимерные волокнистые пневматические гидравлические электромагнитные); по виду демпфирования (с сухим или вязким трением); средства индивидуальной защиты (для рук ног и тела оператора).
2.3 Расчет пассивной виброизоляции сиденья погрузчика
Пассивная виброизоляция (виброзащита)—это виброизоляция не использующая энергию дополнительного источника.
Рассмотрим для примера виброизоляцию сиденья водителя. Сиденья в самоходных строительно-дорожных машинах грузовых автомобилях и тракторах должны обеспечивать санитарно-гигиенические условия для длительной работы водителей. Сиденье должно смягчать толчки и удары и часть вибрации превышающую гигиенические характеристики и нормы вибрации по ГОСТ 12.1.012—78*. Типовая схема подрессоривания сиденья водителя (рис. 4.2) состоит из следующих элементов: направляющего механизма 1 состоящего из параллелограммных рычагов и обеспечивающего стабильность вертикального положения корпуса водителе при колебании машины. Направляющий механизм соединяющий посадочное место водителя с рамой ходовой части машины выполняет роль кинематической и силовой связи; пружины 3 снижающей амплитуду колебаний сиденья от колебания машины при передвижении по неровностям дороги; регулировочного винта 4 для изменения жесткости пружины в зависимости от массы тела водителя; гидроамортизатора 2 поглощающего колебания сиденья при передвижении машины по неровностям дороги.
Рис. 4.2 - Схема подрессоренного сиденья
При переезде препятствий на неровностях пути возникают резкие колебания рамы ходовой части в результате чего сопротивление гидроамортизатора возрастает. Это сопротивление вызвано тем что жидкость в нем не успевает проходить через отверстия 1 в поршне 2. В результате возникающего гидравлического торможения колебания сиденья гасятся.
Требования к виброизоляции сиденья водителя изложены в следующих стандартах: ГОСТ 12.2.011—75* «Машины строительные и дорожные»; ГОСТ 12.2.019—76 «Тракторы и машины самоходные сельскохозяйственные»; ГОСТ 12.2.023— 76 «Кабина. Рабочее место водителя»; ГОСТ 20062—74 «Сиденье тракторное»; ГОСТ 21398— 75 «Автомобили грузовые».
В соответствии с ГОСТ 25571—82 «Вибрация. Основные положения методов расчета виброизоляции рабочего места операторов самоходных машин» излагается порядок поверочного расчета линейной системы виброизоляции при гармоническом возбуждении.
Расчетную схему системы виброизоляции принимаем по рис. 4.1 а.
Характеристикой кинематического возбуждения является например виброскорость основания сиденья (пола кабины) изменяющаяся по гармоническому закону (dydt)a и частота f Гц. Характеристикой возбуждения может быть также виброускорение сиденья.
подрессоренной части сиденья (тс=10 кг) является суммой масс элементов конструкции перемещающихся в процессе работы относительно основания сиденья.
водителя (тч) приходящаяся на сиденье принимается (70± 10) кг; часть массы сидящего водителя также приходящаяся на сиденье составляет 57 его массы а на ноги водителя — 27.
Коэффициент жесткости пружины — с=50000 Нм; коэффициент сопротивления демпфера — b=5000 Нсм.
Определить Кэфф — коэффициент эффективности виброизоляции; Sа — амплитуду гармонического колебания м; vа — абсолютную скорость сиденья мс; аа— абсолютное ускорение сиденья мс2; v() — среднеквадратическую абсолютную скорость сиденья для октавы со среднегеометрической частотой п; () — среднеквадратическое абсолютное ускорение сиденья для октавы со среднегеометрической частотой п; Lv(п)—логарифмический уровень ;
Сравнить аа; L (n) с нормами вибрации по ГОСТ 12.1.012—78* и сделать выводы об эффективности виброизоляции.
водителя приходящаяся на сиденье —
тч = 8057 = = 57 кг.
подрессоренной части сиденья с сидящим на нем водителем
Собственная угловая частота (С-1) системы виброизоляции без демпфирования
Относительное демпфирование
Угловая частота гармонического возбуждения
Относительный коэффициент передачи при виброизоляции
Абсолютный коэффициент передачи при виброизоляции
Коэффициент эффективности виброизоляции
Полученные результаты соответствуют нормам вибрации по СанПиН РК 1.02.011-94 т.е. жесткость и коэффициент сопротивления демпферу сидения достаточны.
Пожарная безопасность – это такое состояние объекта при котором исключается возможность пожара а в случае возникновения предотвращается его опасное воздействие на людей и обеспечивается защита материальных ценностей.
Пожарная безопасность обеспечивается системами предотвращения пожара и пожарной защитой. Под системой предотвращения пожара имеется ввиду комплекс организационных мероприятий и технических средств направленных на исключение возможности возникновения пожара. Под системой пожарной защиты понимают комплекс организационных мероприятий и технических средств направленных на предотвращение воздействия на людей опасных факторов пожара и ограничение материального ущерба от него.
При эксплуатации строительно-дорожных машин в пожары в большинстве случаев возникают по следующим причинам: у строительных машин с электроприводом – из-за перегрузки электродвигателей электрооборудования электропроводов и электросетей в результате чего они нагреваются свыше допустимых норм или искрят; у машин с двигателями внутреннего сгорания – из-за воспламенения оставшейся внутри двигателя горючей смеси; неправильного расположения баков с горюче-смазочными материалами масло- и топливопроводов по отношению к трубопроводу выхлопных газов и глушителю; применение открытого огня для запуска двигателей при низких температурах; самовоспламенение различных масел и горючего под картером двигателя; отсутствие искрогасителей на выпускных трубах; курение при заправке машин топливом.
Пожары возникают также в случаях утечки горючего из топливопроводов и приборов; утечки отработанных газов в выпускных трубах; неисправности кранов перекрывающих топливопроводы; неисправности карбюратора и самовозгорание использованных обтирочных материалов.
Пожарная защита обеспечивается: ограниченным применением горючих и трудногорючих веществ и материалов; предотвращением распространения пожара с использованием средств его тушения строительных конструкций с необходимыми пределами огнестойкости и горючести; эвакуацией людей; системой противодымной защиты; средствами пожарной сигнализации или извещением о пожаре а также организацией пожарной охраны объекта.
В целях пожарной безопасности работать на погрузчики оснащают положенными средствами огнетушения (например углекислотными огнетушителями в которых огнегасящее вещество не является электропроводным)
При обнаружении даже незначительных подтеканий топлива из бака топливопроводов или других агрегатов топливоподачи работу на погрузчиках прекращают.
При работе необходимо следить за тем чтобы на машине или в непосредственной близости от места ее стоянки не было замасленной или пропитанной топливом ветоши и других обтирочных материалов. Выполнять регулировочные сборочно-демонтажные ремонтные и другие работы на погрузчике вдали от источников открытого огня (горящих факелов спичек).
Заправлять топливом машины допускается только при заглушенном двигателе и выключенном зажигании.
При возникновении пожара машины или около нее водитель в первую очередь перекрывает краники топливопровода. Затем для быстрого прекращения горения при пожарах необходимо выполнить два основных условия: прекратить доступ воздуха (кислорода) в зону горения так как горение возможно при содержании кислорода в воздухе не менее 14% (всего в воздухе содержится до 21% кислорода); охладить зону горения ниже температуры самовоспламенения тогда процесс горения прекращается даже при наличии достаточного доступа воздуха.
Гасить пламя следует огнетушителем песком землей или надо накрыть его брезентом или войлоком чтобы прекратить доступ воздуха к пламени. При воспламенении топлива на машине или под ней запрещается заливать пламя водой так как это может вызвать взрыв. Если потушить пожар машины своими силами невозможно необходимо вызвать ближайшую пожарную команду частыми звуковыми сигналами по телефону радио или любыми другими средствами связи.
Склад горюче-смазочных материалов размещают вдали от производственных помещений и стоянок машин. Территорию склада отделяют от других сооружений полосой противопожарной безопасности шириной не менее 10 м. Емкости горюче-смазочных материалов заземляют для отвода от них статического электричества и возможного удара молнии.
Промышленность и транспорт создают мощную техногенную нагрузку на окружающую среду. В ряде случаев живая и неживая природа испытывают на себе воздействия промышленных и транспортных объектов. Эти обстоятельства дают возможность говорить о возникновении новой научной ветви – промышленно-транспортной экологии т.е. промышленно-транспортная экология изучает различные аспекты воздействия объектов промышленности и транспорта на окружающую среду.
Жизненный цикл объекта транспорта – хронологически выраженная последовательность этапов создания производства использования восстановления работоспособности и утилизации техники или сооружений.
Основными видами воздействия транспортного комплекса на окружающую среду являются:
- отчуждение площадей территорий под дороги и объекты транспортной инфраструктуры эрозионные процессы осушение рубки лесов карьерная
разработка строительных материалов;
- изъятие природных минеральных водных энергетических ресурсов;
-технологическое и транспортное загрязнение вредными веществами шумом вибрациями теплотой электромагнитными и ионизирующими излучениями окружающей среды (воздуха воды почвы биоты) предприятиями транспорта и дорожного хозяйства дорогами как линейными сооружениями (транспортными потоками).
При строительстве автомобильных дорог обычно не захватываются большие территории однако линейная протяженность сооружений оказывает на окружающую среду значительные воздействия специфического характера.
Для сооружения 1 км земляного полотна современных магистральных дорог даже в слабопересеченной местности необходимо разработать и переместить до 200 тысяч м3 грунта. Учитывая объективные ограничения отвода земель особенно в сельскохозяйственных районах технико-экономические соображения разработку грунта стараются концентрировать. Устройство сосредоточенных резервов приводит подчас к резким изменениям местного рельефа. Кроме того со временем на территории автомобильной дороги происходят следующие нарушения среды: оползни; образование очагов эрозии; загрязнение воды; изменение водной фауны; перенос грунта; нарушение биогеоценоза; осушение местности.
При выполнении технологических процессов погрузчиками происходит загрязнение окружающей среды проявляющееся в загрязнении атмосферы почвы поверхности и грунтовых вод повышении шумового фона и вибрации что вызывает серьезные негативные изменения во всех компонентах окружающей среды.
Загрязнение воздуха создается отработавшими газами машин летучими соединениями вяжущих материалов растворителей а также пылью тонкодисперсных грунтов каменных материалов и отходов промышленности которые образуются при работе погрузчиков.
Основную массу загрязняющих воздух веществ составляют отработавшие газы. В настоящее время в отработавших газах двигателей внутреннего сгорания обнаружено около 1200 компонентов из которых расшифровано не более 200. Токсичность отработавших газов дизельных двигателей а именно они используются на погрузчиках обуславливается главным образом содержанием в них окислов азота и сажи.
Объем отработавших газов и содержание в них вредных веществ в основном зависят от количества потребляемого топлива и технического состояния двигателя главным образом системы питания. Количество воздуха потребляемое двигателем и соответственно объем отработавших газов составляет в среднем 24 кг на 1 кг топлива. Например за 1 час работы расход топлива базового тягача БелАЗ–531 скрепера ДЗ–13 составляет 80 литров.
Полностью исправные погрузчики расходуют меньше на 40% по сравнению со среднестатистическими данными топлива а значит и меньше загрязняют воздух.
Дымность отработавших газов дизельных двигателей скреперов определяется в соответствии с требованиями ОСТ 23.1.441 – 76 и не должна превышать 40% в режиме свободного ускорения.
При работе с частой сменой нагрузочных режимов работы двигателя токсичность дизелей увеличивается причем как при снижении рабочей нагрузки так и при ее повышении. Установлено что минимальную удельную токсичность отработавших газов имеют дизельные двигатели при 60 – 70% рабочей нагрузке. Исходя из этого можно определять оптимальный режим работы машины при выполнении земляных работ.
Образование пыли при работе скреперов обуславливают недостаточная влажность перегружаемых грунтов наличие в них дисперсных пылеватых и глинистых частиц а также ветровые воздействия. Для исключения загрязнения воздуха пылью превышающего предельно допустимые нормы необходимо проводить мероприятия по пылеподавлению и снижению пылимости.
Технологический процесс работы погрузчиков является источником интенсивного шума который отрицательно воздействуют на здоровье людей непосредственно принимающих участие в технологических процессах а также на флору и фауну окружающей среды. Так при работе скрепер создает шум с эквивалентным уровнем 80 дБ. Мероприятия по снижению уровня шума сводятся главным образом к снижению шума в его источнике т.е. к снижению шума скрепера и применению звукоотражающих или звукопоглощающих экранов на пути распространения звука. Для снижения шума двигателей можно применять усовершенствованные конструкции глушителей значительно снижающие уровень звука при выпуске отработавших газов (лабиринтные реактивные многозвенные и т.д.).
В конструкции скреперов используются в основном гидравлические системы приводов рабочих органов. В результате недостаточно плотного упплотнения гидравлических шлангов рукавов маслопроводов и различной гидравлической аппаратуры возможно загрязнение почвы и грунтовых вод гидравлическими маслами которые могут просочиться на землю и сквозь почву попасть в грунтовые воды.
Вредное влияние на растения и животных от погрузчиков проявляется в механическом повреждении растений замедлении или прекращении биохимических процессов под действием отработавших газов продуктов сгорания испаряющихся веществ пыли при непосредственном соприкосновении с горюче-смазочными материалами гидравлической жидкостью и другими веществами и материалами.
Мероприятия позволяющие снизить воздействие транспорта на окружающую среду:
-совершенствование нормативно-правовой базы для обеспечения экологической безопасности (устойчивого развития) промышленности и транспорта;
-создание экологически безопасных конструкций объектов транспорта эксплуатационных конструкционных строительных материалов технологий их производства;
-разработка ресурсосберегающих технологий защиты окружающей среды от транспортных загрязнений;
-совершенствование системы управления природоохранной деятельностью на транспорте.
Мероприятия по снижению загрязнения окружающей среды со стороны погрузчиков это:
-совершенствование (модернизация) систем питания увеличение полноты сгорания топлива; ужесточение технологических допусков при изготовлении деталей формирующих камеру сгорания систему подачи топлива улучшение конструкции поршневых колец использование микропроцессорного управления;
-повышение качества моторных топлив. Отказ от использования тетраэтилсвинца в бензинах снижение содержания серы в дизельном топливе ароматических углеводородов;
-рециркуляция отработавших газов;
-нейтрализация отработавших газов фильтрация твердых частиц;
-поддержание технического состояния (теплового режима регулировок) в пределах допусков заводов-изготовителей;
-использование новых рабочих процессов и видов энергоресурсов (природный газ синтез-газ водород спирты электропривод).
В отличие от транспортной техники экологические нормативы (предельные уровни токсичности шума) строительно-дорожных машин пока не разработаны. Нет предельных уровней выбросов при осуществлении технологических процессов при строительстве ремонте дорог и мостов. Но устанавливается предельное содержание вредных веществ в отдельных видах строительных материалов. В дорожном хозяйстве как и в автомобильной промышленности широко используются методы санитарно-гигиенического нормирования.
ОПРЕДЕЛЕНИЕ ПОКАЗАТЕЛЕЙ ЭКОНОМИЧЕСКОЙ ЭФФЕКТИВНОСТИ ОТ ВНЕДРЕНИЯ НОВОЙ ТЕХНИКИ
Модернизация скрепера заключается в установке на заднем мосте скрепера мотор-колеса с целью улучшения тяговых возможностей скрепера. Установка мотор-колеса обеспечить загрузку ковша без толкача в вспомогательных или локальных работах небольших объемов где использования толкача неэффективно.
По сравнению с существующим скрепером без активного заднего моста скрепер предлагаемой конструкции выигрывает в производительности и себестоимости единицы работ в 115—13 раза в зависимости от дальности транспортирования породы.
Эксплуатационная производительность скрепера (м3ч) в плотном теле определяется по формуле
где п – число циклов в час (п=3600Тц где Тц – продолжительность одного рабочего цикла скрепера с);
q – вместимость ковша скрепера q =162 м3;
Кн – коэффициент наполнения ковша грунтом (Кн=06 12) принимаем до модернизации Кн=07 после модернизации Кн=09;
Кр – коэффициент разрыхления грунта в ковше скрепера (Кр=11 13) принимаем Кр=12;
Кв – коэффициент использования машины по времени (Кв=08 09) принимаем Кв=085.
Продолжительность одного рабочего цикла скрепера
vз vт vрз vп.х – скорости скрепера соответственно при заполнения ковша транспортировке грунта разгрузке и порожнем ходе принимаем vз=05 мс vт=7 мс vрз=1 мс vп.х=10 мс;
tп – время на переключения передач тягача принимаем tп=10 с;
tпов – время на один поворот принимаем tпов=20 с;
Длина участка набора грунта
Разгружается скреперы на участках длиной 5 15 м принимаем lрз=10 м.
Подставляя значения в формулу (2.10) получим
Таким образом эксплуатационная часовая производительность скрепера до модернизации
Эксплуатационная часовая производительность после модернизации
Годовая эксплуатационная производительность техники
где ТГ – количество машино-часов работы скрепера в году маш-часгод;
kПР– коэффициент учитывающий простои в работе техники по организационным причинам kПР =09.
Определяем количество машино-часов работы техники в году:
где ТФ – годовой фонд рабочего времени скрепера ТФ=247 дней;
tСМ – продолжительность смены tСМ=8 час;
kСМ – коэффициент сменности работы техники kСМ =1;
DР – простои в днях во всех видах плановых техобслуживаниях и ремонтах приходящиеся на один машино-час работы техники днеймаш.-час;
dП – продолжительность одной перебазировки техники с объекта на объект dП=1 день;
ТОБ – средняя продолжительность работы техники на объекте ТОБ=4000 маш.-час.
Число простоев в днях во всех плановых видах техобслуживаний и ремонтов приходящиеся на один машино-час работы техники определяется по формуле:
Tp – средний ресурс до первого капремонта Tp=7200 мото-часов;
kr – коэффициент перевода мото-часов в машино-часы;
n – число разновидностей ТО и Р (n = 4).
Коэффициент перевода мото-часов в машино- часы определим по формуле:
где kдв–коэффициент использования двигателя машины по времени определяется как отношение суммарного времени работы двигателя к общей продолжительности смены kдв=09;
kдм–коэффициент использования двигателя по мощности показывает отношение средней мощности развиваемой двигателем в процессе работы к ее номинальному значению kдм=08.
Определяем количество ТО и ремонтов за ремонтный цикл:
где tpi – периодичность проведения соответствующих ТО и ремонтов мото-час.
Годовая эксплуатационная производительность техники до и после модернизации
П=267166608=3558576 м3год;
П=323166608=4304944 м3год;
Определим коэффициент изменения производительности:
Технико-экономическим показателем работы скрепера являются расходы на его эксплуатацию т.е. годовые эксплуатационные расходы.
Эксплуатационные расходы определяются по формуле:
Рэ = Аг+Р+В+Э+З(5.12)
где Аг – годовые амортизационные отчисления тг;
В – затраты на износ сменной оснастки вспомогательных материалов смазочных материалов;
Э – расход энергоресурсов;
З – заработная плата машиниста.
Балансовая стоимость активного заднего моста скрепера равна:
где м – масса металлоконструкции заднего моста 4 т;
Ц – цена одной тонны рабочего оборудования 194 тыс.тг.
С=4194 = 776 тыс.тг.
Затраты на монтаж рабочего оборудования принимаем в размере 15% от балансовой стоимости.
См = 015776 = 1164 тыс.тг.
Затраты на транспортировку рабочего оборудования принимаем в размере 7% от балансовой стоимости.
Стр = 007776 = 543 тыс.тг.
Балансовая стоимость усовершенствованной конструкции заднего моста скрепера составит:
С=776+1164+543 = 9467 тыс.тг.
Годовая сумма амортизационных отчислений:
Аг=776008=6208 тыс.тг.
Аг=9467008=7574 тыс.тг.
Затраты на ремонты составят:
Р=946701(1–01)=852 тыс.тг
Годовой фонд оплаты труда машинистов:
З = ЧсписЗср12(5.14)
где Чспис – списочная численность машинистов;
Зср. – средняя месячная заработная плата машинистов.
Списочная численность при непрерывном режиме работы:
Чср. = (С+1)Кприв(5.15)
где С – сменность работы ( число смен в сутки);
К – коэффициент приведения штатной численности к списочной с учетом резерва на подмену.
Чср. = (1+1)113 = 226 ставок
З=З=2263512 = 9492 тыс.тг.
Н=Н=949202 = 18984 тыс.тг.
Общая сумма эксплуатационных затрат составит:
Рэ=6208+776+9492+18984=127872 тыс.тг.
Рэ=7574+852+9492+18984 =129998 тыс.тг.
Сравнительный экономический эффект определяют по формуле
где Zy Zy – удельные приведенные затраты до и после модернизации.
где ЕН – нормативный коэффициент эффективности ЕН =015.
Срок окупаемости капитальных вложении:
На основании произведенных расчетов составим таблицу сводных технико-экономических показателей
Таблица 5.1 – Основные технико-экономические показатели проекта
Наименование показателей
Значение показателей
Капитальные вложения
Эксплуатационные затраты
Производительность скрепера
Годовой экономический эффект
В выполненном дипломном проекте посвященной модернизации самоходного скрепера с целью повышения тягово-сцепных характеристик скрепера ДЗ-13 на основании выполненного анализа конструкций машин патентно-литературного обзора расчетов основных параметров скрепера расчета экономической эффективности от внедрения новой техники в производство можно сделать следующие выводы:
При выполнении целого ряда вспомогательных или локальных работ небольших объемов для выполнения которых требуется один или два скрепера существенным является обеспечение загрузки ковша скрепера без толкача. Для использования скрепера ДЗ-13 без толкача в таких работах предложена усовершенствование заднего моста сделав их активными т.е. установить на заднем мосте скрепера мотор-колеса
Предложена конструкция мотор-колеса обеспечивающий при простоте конструкции большой крутящий момент и малые габариты а также надежное торможение. Для изменения скорости вращения мотор-колеса при изменении скорости движения скрепера предлагается применить гидропривод с дроссельным управлением.
Выполненные расчеты показывают работоспособность и эффективность предлагаемой конструкции заднего моста.
По сравнению с существующими скреперами скрепер предлагаемой конструкции выигрывает в себестоимости единицы работ в 115—13 раза в зависимости от дальности транспортирования породы.
Годовой экономический эффект от внедрения сменного рабочего органа составил 301350 тенге в год при сроке окупаемости 24 года.
СПИСОК ИСПОЛЬЗОВАННЫХ ИСТОЧНИКОВ
Дорожно-строительные машины и оборудование. – М: «Наука» 1986. – 186с.
Забегалов Г.В. Ронисон Э.Г. Бульдозеры скреперы грейдеры. – М.: «Высшая школа» 1991. – 332с.
Плешков Д.И. Хейфец М.И. Яркин А.А. Бульдозеры скреперы грейдеры. – М.: «Высшая школа» 1980. – 271с.
Рейш А.К. и др. Машины для земляных работ. – М.: «Стройиздат» 1981. – 352с.
Алексеева Т.В. Артемьев К.А. Бромберг А.А. и др. Дорожные машины. Часть I. Машины для земляных работ. – М.: «Машиностроение» 1972 504 с.
Добронравов С.С. Строительные машины и оборудование. Справочник. . – М.: «Высшая школа» 1991. – 456с.
Шестопалов К.К. Подъемно-транспортные строительные и дорожные машины и оборудование. - М.: «Мастерство» 2002. – 320 с.
Баловнев В. И. Моделирование процессов взаимодействия со средой рабочих органов дорожно-строительных машин. - М.: Высшая школа 1981. - 335 с.
Справочник конструктора дорожных машин. Под. ред. И.П. Бородочева. – М.:Машиностроение 1973. – 504с.
Абрамов Н.Н. Курсовое и дипломное проектирование по дорожно-строительным машинам. –М.: Высшая школа 1972. -120с.
Кузьмин А.В. Чернин И.М. Козинцов Б.С. Расчеты деталей машин: Справ. пособие. – Минск: «Вышэйшая школа» 1986. – 400 с.
Писаренко Г.С. Яковлев А.П. Матвеев В.В. Справочник по сопротивлению материалов. - Киев «Наукова думка» 1988. -736 с.
Гидравлика гидромашины и гидропневмо привод под. ред. С.П. Стесина - М.: Изд. центр «Академия» 2007. – 336 с.
Филиппов Б.И. Охрана труда при эксплуатации строительных машин. – М.: «Высшая школа» 1984 – 247 с.
Рекомендуемые чертежи
Свободное скачивание на сегодня
Другие проекты
- 22.08.2014