Разработка гильзо-поршневой группы двигателя




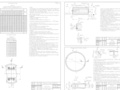
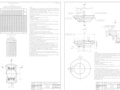
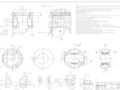
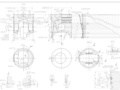
- Добавлен: 25.10.2022
- Размер: 12 MB
- Закачек: 0
Описание
Состав проекта
![]() |
![]() |
![]() ![]() |
![]() ![]() |
![]() |
![]() ![]() ![]() ![]() |
![]() ![]() ![]() ![]() |
![]() ![]() ![]() ![]() |
![]() ![]() ![]() ![]() |
![]() ![]() ![]() ![]() |
![]() ![]() ![]() ![]() |
![]() ![]() ![]() ![]() |
![]() ![]() |
![]() |
![]() |
![]() ![]() ![]() |
![]() ![]() |
![]() ![]() |
![]() ![]() |
![]() |
![]() |
![]() |
![]() ![]() |
![]() |
![]() |
![]() ![]() |
![]() |
![]() |
Дополнительная информация
Лист №1 (диаграммы теплового расчета)_.dwg

Лист №5,6,7 (поршень - продолжение, поршневой палец, кольцо компрессионное)_.dwg

изменения овальности профиля на участке З
в радиальных сечениях
перпендикулярных оси М.
изменения овальности
профиля на участке К.
Отливку поршня после переплава зоны канавки под первое компрессионное
кольцо подвергнуть термической обработке по режиму Т
Допускается вне зоны переплава снижение твердости алюминия до 80НВ
на расстоянии до 45 мм от донышка поршня.
Временное сопротивление разрыву образцов
вырезанных из поршня
менее 170 МПа (17 кгсмм
Зону канавки под первое компрессионное кольцо упрочнить переплавом с
Твердость переплавленного слоя 125 140 НВ.
Размеры для справок.
Неуказанные литейные радиусы 3 мм
Неуказанные предельные отклонения размеров Н14
кл. точности по ГОСТ 23.4.51-73.
Для готовой детали отклонения размеров бочкообразности поршня дол-
мм на участке до 53 мм от донышка поршня;
5 мм на участке от 53 мм до 120 мм;
мм на участке от 120 мм до нижнего торца поршня.
Изменение допуска должно быть только в сторону уменьшения диамет-
Изменение кривизны профиля должно быть плавным.
Поверх. И накатать в линию (совместно с одной стороны).
Угловое смещение маслосливных отверстий относительно номинального
Объем камеры сгорания (87
Разностенность юбки поршня в диаметрально противоположных местах
во всех сечениях не более 0
Ось поршня М определяется центрами сечений
расположенных на рас-
стоянии 44 мм и 123 мм от донышка поршня.
Разность размеров Л не более 0
На поверхности камеры сгорания на радиусе до 10 мм от оси поршня
допускается повышение параметра шероховатости до R
После нагрева поршня до температуры 200 220
С и выдержке в тече-
ние 10 часов увеличение диаметра по головке не должно превышать 0
допустимого чертежом (обеспечивается технологией).
Замеры поршня производить при температуре (20
На обработанных поверхностях поршня забоины
На поверх. И допускается одна риска (след выхода инструмента).
Допускается наличие острых кромок на перемычках между канавками
под поршневые кольца.
Допускается увеличение параметра шероховатости до R
хностей поршня З и К до нанесения покрытия.
64 наружной поверхности. Разность твердости
в одном пальце не более HRC
На внутренней поверхности допускается закаленный це-
ментированный слой h 0
Твердость сердцевины пальца HRC
огранка и изогнутость наружной цилиндриче-
ской поверхности не более 0
При обработке пальца дорнованием допускается внут-
ренний диаметр выполнять (25
Разностенность в одном пальце не более 0
На полированной поверхности пальца риски
волосовины и забоины не допускаются.
Трещины не допускаются.
установленный в призму с углом 90
должен выдерживать нагрузку 1900Н без
Подгонку пальцев по массе производить за счет уве-
личения внутренних фасок до 3
Неравномерность размера фаски Б не более 0
Размер обеспечить инструментом.
98-112 HRB. Разность показаний тв. в одной дет. - не более 4 HRB.
Внутр. напряжения снять
Предел прочности при изгибе - не менее 981 МПа (100 кгсмм
Остаточная деформация при испытании на изгиб - не более 1 %.
Остаточная намагниченнлсть не более 200 Ам.
Размеры обеспеч. инстр.
При снятии заусенцев величина фасок или радиусов не более 0
Колебание радиальной толщины в одной дет. - не более 0
Коробление поверхностей Б - не более 0
мм. Определять при нагружении
сосредоточенными силами.
Покрытие поверх. В ХтВ 120-200. Микротвердость хрома 7840-11760 МПа
Прачность сцепления гальванического хромового пакрытия с основным ме-
таллом проверять разведением концов кольца
методом изгиба до величины
мм. Отслаивание покрытия не допускается.
Зазор в замке S проверять в калибре соответствующем номинальному ди-
Овальность кольца при сжатии гибкой стальной лентой
мм. Максималь. диаметр кольца - по оси У-У.
Деталь показана в состоянии измерения
Лист №9,10 (поршень - продолжение, головка поршня)_.dwg

изменения овальности профиля на участке З
в радиальных сечениях
перпендикулярных оси М.
изменения овальности
профиля на участке К.
Отливку поршня после переплава зоны канавки под первое компрессионное
кольцо подвергнуть термической обработке по режиму Т
Допускается вне зоны переплава снижение твердости алюминия до 80НВ
на расстоянии до 45 мм от донышка поршня.
Временное сопротивление разрыву образцов
вырезанных из поршня
менее 170 МПа (17 кгсмм
Зону канавки под первое компрессионное кольцо упрочнить переплавом с
Твердость переплавленного слоя 125 140 НВ.
Размеры для справок.
Неуказанные литейные радиусы 3 мм
Неуказанные предельные отклонения размеров Н14
кл. точности по ГОСТ 23.4.51-73.
Для готовой детали отклонения размеров бочкообразности поршня дол-
мм на участке до 53 мм от донышка поршня;
5 мм на участке от 53 мм до 120 мм;
мм на участке от 120 мм до нижнего торца поршня.
Изменение допуска должно быть только в сторону уменьшения диамет-
Изменение кривизны профиля должно быть плавным.
Поверх. И накатать в линию (совместно с одной стороны).
Угловое смещение маслосливных отверстий относительно номинального
Объем камеры сгорания (87
Разностенность юбки поршня в диаметрально противоположных метах
во всех сечениях не более 0
Ось поршня М определяется центрами сечений
расположенных на рас-
стоянии 44 мм и 123 мм от донышка поршня.
Разность размеров Л не более 0
На поверхности камеры сгорания на радиусе до 10 мм от оси поршня
допускается повышение параметра шероховатости до R
После нагрева поршня до температуры 200 220
С и выдержке в тече-
ние 10 часов увеличение диаметра по головке не должно превышать 0
допустимого чертежом (обеспечивается технологией).
Замеры поршня производить при температуре (20
На обработанных поверхностях поршня забоины
На поверх. И допускается одна риска (след выхода инструмента).
Допускается наличие острых кромок на перемычках между канавками
под поршневые кольца.
Допускается увеличение параметра шероховатости до R
хностей поршня З и К до нанесения покрытия.
Место испытания твердости
обеспечить при сборе зазор 0
Упрочнение плазменным
переплавом с легированием
Замеры головки поршня производить при температуре (20
На обработанных поверхностях головки поршня забоины
задиры не допускаются.
Лист №8 (гильза цилиндра)_.dwg

Участок до 15 мм от верхнего и до 27 мм от нижнего
торцев допускается не калить. Остаоьные поверхности: HB 170 241.
При проверке твердости поверх. А должно быть произведено не менее пяти измерений. Допускается
снижение твердости по двум измерениям до HRCэ 40.
Гильза не должна быть намагничена. Не допускается величина остаточного магнетизма более 199
Гильза не должна иметь трещин
торонних включений и других дефектов
кроме оговоренных ниже.
На поверх. А допускается наличие течечной пористости величиной до 0
На опорных поверхностях гильзы наличие следующих раковин не допускается:
- на поверх. Е в количестве более 3
мм по наибольшему измерению и глу-
биной более 1 мм при расстоянии их от торцев менее 2 мм;
- на поверх. Б и В в количестве более 2
величиной и глубиной более 1 мм при расстоянии их
от краев менее 2 мм.
На обработанной поверх. Г не допускается наличие более 4
газовых раковин величиной по наиболь-
шему измерению более 3 мм и глубиной более 2 мм при расстоянии между ними менее 30 мм.
На обработанной поверх. Д не допускается наличие более 4
шему измерению более 2 мм и глубиной более 1 мм при расстоянии между ними менее 30 мм.
Допуск круглости и профиля продольного сечения поверх. А-0
На участках до 15 мм от верхнего и до 27 мм от нижнего торцев допуск круглости и профиля про-
на этих участках допускается увеличение параметра шероховатости до
Спиральную канавку на поверх. В допускается выполнять в виде 2
Замеры производить при температуре (20
Клеймить знак ОТК кислотным способом.
Лист №11 (корпус поршня)_.dwg

Упрочнение плазменным
переплавом с легированием
Отливку поршня после переплава зоны канавки под первое компрессионное кольцо подвергнуть термической обработке
Допускается вне зоны переплава снижение твердости алюминия до 80НВ на расстоянии до 45 мм от донышка поршня.
Временное сопротивление разрыву образцов
вырезанных из поршня
не менее 170 МПа (17 кгсмм
Зону канавки под первое компрессионное кольцо упрочнить переплавом с легированием.
Твердость переплавленного слоя 125 140 НВ.
Размеры для справок.
Неуказанные литейные радиусы 3 мм
Неуказанные предельные отклонения размеров Н14
кл. точности по ГОСТ 23.4.51-73.
Для готовой детали отклонения размеров бочкообразности поршня должны быть не более:
мм на участке до 53 мм от донышка поршня;
5 мм на участке от 53 мм до 120 мм;
мм на участке от 120 мм до нижнего торца поршня.
Изменение допуска должно быть только в сторону уменьшения диаметров поршня.
Изменение кривизны профиля должно быть плавным.
Поверх. И накатать в линию (совместно с одной стороны).
Угловое смещение маслосливных отверстий относительно номинального расположения
Разностенность юбки поршня в диаметрально противоположных местах во всех сечениях не более 0
Ось поршня М определяется центрами сечений
расположенных на расстоянии 44 мм и 123 мм от донышка поршня.
Разность размеров Л не более 0
Замеры корпуса поршня производить при температуре (20
На обработанных поверхностях корпуса поршня забоины
задиры не допускаются.
На поверх. И допускается одна риска (след выхода инструмента).
Допускается наличие острых кромок на перемычках между канавками под поршневые кольца.
Не указанные обозначения поясняются в сборочном чертеже.
Лист №5 (поршень)_.dwg

При подгонке по массе
Образующая продольного
Для построения копира
Упрочнение плазменным
переплавом с легированием
Лист №2,3,4 (диаграммы динамического расчета)_.dwg

Расчетно-пояснительная записка к Дипломной работе.doc
Ташкентский Государственный Технический Университет
им. Абу Райхана Беруни
Механико-машиностроительный факультет
Кафедра: “Энергомашиностроение и Профессиональное образование (НТС)”
РАСЧЕТНО-ПОЯСНИТЕЛЬНАЯ ЗАПИСКА
Выпускной квалификационной работы
“Тракторный дизель класса 3.0 с разработкой гильзо-поршневой группы”
Содержание выпускной работы
Пояснительная записка - 112 страниц
Графическая часть - 11 листов
Консультанты по разделам:
Из истории создания ДВС 6
Двигатели внутреннего сгорания 6
Тепловое расширение 8
Основы устройства поршневых ДВС 9
Принцип действия четырехтактного карбюраторного двигателя 11
Принцип действия четырехтактного дизеля 12
Принцип действия двухтактного двигателя 12
Конструкторская часть 14
Назначение характеристика двигателя и разрабатываемого узла 15
Технические экономические и экологические требования предъявляемые к двигателям
внутреннего сгорания 16
Обзор и анализ конструкций материалы Интернета патентное исследование 18
Обзор и анализ конструкций 18
Материалы Интернета 27
Патентное исследование 29
Обоснование темы и описание разрабатываемой конструкции 46
Тепловой и динамический расчет двигателя 48
Динамический расчет 55
Расчет разрабатываемых узлов 60
Расчет поршня дизеля 60
Расчет гильзы цилиндра дизеля 62
Расчет поршневого пальца дизеля 62
Экономическая часть 65
Безопасность жизнедеятельности 72
Размещение санитарно-бытовых помещений согласно нормативным требованиям 73
Меры по предупреждению вредных выделений паров газов и пыли в проектируемом
Промышленная вентиляция 75
Метеорологические условия 78
Мероприятия по борьбе с производственным шумом и вибрацией 79
Мероприятия по борьбе с шумом 79
Мероприятия по устранению вибраций 81
Ограждающие и блокирующие устройства 86
Электробезопасность конструкций 89
Пожарная безопасность 90
Экологическая часть 94
Основные положения экологии экологической безопасности автомобильного
Экология и автомобильный транспорт 95
Состав и токсичность газов автомобильных двигателе 95
Автомобилизация и окружающая среда 99
В Республике Узбекистан внедрение в практику проектирования современных методов в частности автоматизации проектных работ и разработки практических проектных продуктов ведется медленными темпами. Серьезные недостатки в организации проектных работ преграждают инвестиционные процессы которые проводятся в нашей Республике и уменьшают их эффективность. В Указе Президента Республики Узбекистан «О мероприятиях по дальнейшему совершенствованию деятельности проектно-исследовательских организаций» особое внимание уделяется тому что в высших учебных заведениях готовящих специалистов в области проектно-изыскательских работ недостаточное внимание уделяется подготовке молодых перспективных кадров-проектировщиков.
Основными задачами решения этой актуальной проблемы являются:
- используя передовой зарубежный опыт разработка современных и научно обоснованных расчетно-конструкторских решений проектирования;
- проектирование объектов автоматизированным образом;
- высшие учебные заведения должны серьезно пересмотреть учебные планы и программы должны внедрить в учебный процесс автоматизированное проектирование в том числе разработку конструкторских документаций.
Из истории создания ДВС
Автомобильный транспорт создан в результате развития новой отрасли народного хозяйства - автомобильной промышленности которая на современном этапе является одним из основных звеньев отечественного машиностроения.
Начало создания автомобиля было положено более двухсот лет назад (название "автомобиль" происходит от греческого слова autos - "сам" и латинского mobilis - "подвижный") когда стали изготовлять "самодвижущиеся" повозки. Впервые они появились в России. В 1752 г. русский механик-самоучка крестьянин Л.Шамшуренков создал довольно совершенную для своего времени "самобеглую коляску" приводимого в движение силой двух человек. Позднее русский изобретатель И.П.Кулибин создал "самокатную тележку" с педальным приводом. С появлением паровой машины создание самодвижущихся повозок быстро продвинулось вперед. В 1869-1870 гг. Ж.Кюньо во Франции а через несколько лет и в Англии были построены паровые автомобили. Широкое распространение автомобиля как транспортного средства начинается с появлением быстроходного двигателя внутреннего сгорания. В 1885 г. Г.Даймлер (Германия) построил мотоцикл с бензиновым двигателем а в 1886 г.К.Бенц - трехколесную повозку. Примерно в это же время в индустриально развитых странах (Франция Великобритания США) создаются автомобили с двигателями внутреннего сгорания.
Первый двигатель внутреннего сгорания (ДВС) был создан в 1860 г. французским инженером Этвеном Ленуаром но эта машина была еще весьма несовершенной.
В 1862 г. французский изобретатель Бо де Рош предложил использовать в двигателе внутреннего сгорания четырехтактный цикл: 1) всасывание; 2) сжатие; 3) горение и расширение; 4) выхлоп. Эта идея была использована немецким изобретателем Н.Отто построившим в 1878 г. первый четырехтактный двигатель внутреннего сгорания. КПД такого двигателя достигал 22% что превосходило значения полученные при использовании двигателей всех предшествующих типов.
Двигатели внутреннего сгорания
В настоящее время существует большое количество устройств использующих тепловое расширение газов. К таким устройствам относится карбюраторный двигатель дизели турбореактивные двигатели и т.д.
Тепловые двигатели могут быть разделены на две основные группы:
Двигатели с внешним сгоранием - паровые машины паровые турбины двигатели Стирлинга и т.д.
Двигатели внутреннего сгорания.
В качестве энергетических установок автомобилей наибольшее распространение получили двигатели внутреннего сгорания в которых процесс сгорания топлива с выделением теплоты и превращением ее в механическую работу происходит непосредственно в цилиндрах. На большинстве современных автомобилей установлены двигатели внутреннего сгорания. Наиболее экономичными являются поршневые и комбинированные двигатели внутреннего сгорания. Они имеют достаточно большой срок службы сравнительно небольшие габаритные размеры и массу. Основным недостатком этих двигателей следует считать возвратно-поступательное движение поршня связанное с наличием кривошатунного механизма усложняющего конструкцию и ограничивающего возможность повышения частоты вращения особенно при значительных размерах двигателя.
Быстрое распространение ДВС в промышленности на транспорте в сельском хозяйстве и стационарной энергетике была обусловлена рядом их положительных особенностей.
Осуществление рабочего цикла ДВС в одном цилиндре с малыми потерями и значительным перепадом температур между источником теплоты и холодильником обеспечивает высокую экономичность этих двигателей. Высокая экономичность - одно из положительных качеств ДВС.
Среди ДВС дизель в настоящее время является таким двигателем который преобразует химическую энергию топлива в механическую работу с наиболее высоким КПД в широком диапазоне изменения мощности. Это качество дизелей особенно важно если учесть что запасы нефтяных топлив ограничены.
К положительным особенностям ДВС стоит отнести также то что они могут быть соединены практически с любым потребителем энергии. Это объясняется широкими возможностями получения соответствующих характеристик изменения мощности и крутящего момента этих двигателей. Рассматриваемые двигатели успешно используются на автомобилях тракторах сельскохозяйственных машинах тепловозах судах электростанциях и т.д. т.е. ДВС отличаются хорошей приспособляемостью к потребителю.
Сравнительно невысокая начальная стоимость компактность и малая масса ДВС позволили широко использовать их на силовых установках находящих широкое применение и имеющих небольшие размеров моторного отделения.
Установки с ДВС обладают большой автономностью. Даже самолеты с ДВС могут летать десятки часов без пополнения горючего.
Важным положительным качеством ДВС является возможность их быстрого пуска в обычных условиях. Двигатели работающие при низких температурах снабжаются специальными устройствами для облегчения и ускорения пуска. После пуска двигатели сравнительно быстро могут принимать полную нагрузку. ДВС обладают значительным тормозным моментом что очень важно при использовании их на транспортных установках.
Положительным качеством дизелей является способность одного двигателя работать на многих топливах. Так известны конструкции автомобильных многотопливных двигателей а также судовых двигателей большой мощности которые работают на различных топливах - от дизельного до котельного мазута.
Но наряду с положительными качествами ДВС обладают рядом недостатков. Среди них ограниченная по сравнению например с паровыми и газовыми турбинами агрегатная мощность высокий уровень шума относительно большая частота вращения коленчатого вала при пуске и невозможность непосредственного соединения его с ведущими колесами потребителя токсичность выхлопных газов возвратно-поступательное движение поршня ограничивающие частоту вращения и являющиеся причиной появления неуравновешенных сил инерции и моментов от них.
Но невозможно было бы создание двигателей внутреннего сгорания их развития и применения если бы не эффект теплового расширения. Ведь в процессе теплового расширения нагретые до высокой температуры газы совершают полезную работу. Вследствие быстрого сгорания смеси в цилиндре двигателя внутреннего сгорания резко повышается давление под воздействием которого происходит перемещение поршня в цилиндре. А это-то и есть та самая нужная технологическая функция т.е. силовое воздействие создание больших давлений которую выполняет тепловое расширение и ради которой это явление применяют в различных технологиях и в частности в ДВС.
Тепловое расширение - изменение размеров тела в процессе его изобарического нагревания (при постоянном давлении).
Тепловое расширение нашло свое применение в различных современных технологиях.
В частности можно сказать о применении теплового расширения газа в теплотехники. Так например это явление применяется в различных тепловых двигателях т.е. в двигателях внутреннего и внешнего сгорания: в роторных двигателях в реактивных двигателях в турбореактивных двигателях на газотурбинных установках двигателях Ванкеля Стирлинга ядерных силовых установках. Тепловое расширение воды используется в паровых турбинах и т.д. Все это в свою очередь нашло широкое распространение в различных отраслях народного хозяйства.
Например двигатели внутреннего сгорания наиболее широко используются на транспортных установках и сельскохозяйственных машинах. В стационарной энергетике двигатели внутреннего сгорания широко используются на небольших электростанциях энергопоездах и аварийных энергоустановках. ДВС получили большое распространение также в качестве привода компрессоров и насосов для подачи газа нефти жидкого топлива и т.п. по трубопроводам при производстве разведочных работ для привода бурильных установок при бурении скважин на газовых и нефтяных промыслах.
Турбореактивные двигатели широко распространены в авиации.
Паровые турбины - основной двигатель для привода электрогенераторов на ТЭС. Применяют паровые турбины также для привода центробежных воздуходувок компрессоров и насосов. Существуют даже паровые автомобили но они не получили распространения из-за конструктивной сложности.
Тепловое расширение применяется также в различных тепловых реле принцип действия которых основан на линейном расширении трубки и стержня изготовленных из материалов с различным температурным коэффициентом линейного расширения.
Как было выше сказано в качестве энергетических установок автомобилей наибольшее распространение получили ДВС в которых процесс сгорания топлива с выделением теплоты и превращением ее в механическую работу происходит непосредственно в цилиндрах. Но в большинстве современных автомобилей установлены двигатели внутреннего сгорания которые классифицируются по различным признакам:
По способу смесеобразования - двигатели с внешним смесеобразованием у которых горючая смесь приготовляется вне цилиндров (карбюраторные и газовые) и двигатели с внутренним смесеобразованием (рабочая смесь образуется внутри цилиндров) – дизели;
По способу осуществления рабочего цикла - четырехтактные и двухтактные;
По числу цилиндров - одноцилиндровые двухцилиндровые и многоцилиндровые;
По расположению цилиндров - двигатели с вертикальным или наклонным расположением цилиндров в один ряд V-образные с расположением цилиндров под углом (при расположении цилиндров под углом 180 двигатель называется двигателем с противолежащими цилиндрами или оппозитным);
По способу охлаждения – на двигатели с жидкостным или воздушным охлаждением.
По виду применяемого топлива - бензиновые дизельные газовые и многотопливные;
По степени сжатия: в зависимости от степени сжатия различают двигатели высокого (e=12 18) и низкого (e=4 9) сжатия;
По способу наполнения цилиндра свежим зарядом:
а) двигатели без наддува у которых впуск воздуха или горючей смеси осуществляется за счет разряжения в цилиндре при всасывающем ходе поршня;
б) двигатели с наддувом у которых впуск воздуха или горючей смеси в рабочий цилиндр происходит под давлением создаваемым компрессором с целью увеличения заряда и получения повышенной мощности двигателя;
По частоте вращения: тихоходные повышенной частоты вращения быстроходные;
По назначению различают двигатели стационарные автотракторные судовые тепловозные авиационные и др.
Основы устройства поршневых ДВС
Поршневые ДВС состоят из механизмов и систем выполняющих заданные им функции и взаимодействующих между собой. Основными частями такого двигателя являются кривошипно-шатунный механизм и газораспределительный механизм а также системы питания охлаждения зажигания и смазочная система.
Кривошипно-шатунный механизмпреобразует прямолинейное возвратно-поступательное движение поршня во вращательное движение коленчатого вала.
Механизм газораспределения обеспечивает своевременный впуск горючей смеси в цилиндр и удаление из него продуктов сгорания.
Система питания предназначена для приготовления и подачи горючей смеси в цилиндр а также для отвода продуктов сгорания.
Смазочная система служит для подачи масла к взаимодействующим деталям с целью уменьшения силы трения и частичного их охлаждения наряду с этим циркуляция масла приводит к смыванию нагара и удалению продуктов изнашивания.
Система охлаждения поддерживает нормальный температурный режим работы двигателя обеспечивая отвод теплоты от сильно нагревающихся при сгорании рабочей смеси деталей цилиндров поршневой группы и клапанного механизма.
Система зажигания предназначена для воспламенения рабочей смеси в цилиндре двигателя.
Рис. 1. Продольный разрез двигателя:
– головка цилиндра; 2 – водяная рубашка блок-картера; 3 – сапун; 4 – шпилька крепления головки цилиндров к блок-картеру; 5 – впускной клапан; 6 – штанга толкателя; 7 – форсунка; 8 – вставка камеры сгорания; 9 – гильза цилиндра; 10 – толкатель; 11 – распределительный вал; 12 – блок-картер; 13 – шестерня распределительного вала; 14 – передняя опора дизеля; 15 – шкив; 16 – шестерня коленчатого вала; 17 – смазочный насос; 18 – коленчатый вал; 19 – маслоприемник; 20 – поддон картера; 21 – шатун; 22 – поршневой палец; 23 – поршень; 24 – картер маховика; 25 – венец маховика; 26 – маховик; 27 – цилиндр
Действие поршневого двигателя внутреннего сгорания основано на использовании работы теплового расширения нагретых газов во время движения поршня от ВМТ к НМТ. Нагревание газов в положении ВМТ достигается в результате сгорания в цилиндре топлива перемешанного с воздухом. При этом повышается температура газов и давления. Т.к. давление под поршнем равно атмосферному а в цилиндре оно намного больше то под действием разницы давлений поршень будет перемещаться вниз при этом газы - расширяться совершая полезную работу. Вот здесь-то и дает о себе знать тепловое расширение газов здесь и заключается его технологическая функция: давление на поршень. Чтобы двигатель постоянно вырабатывал механическую энергию цилиндр необходимо периодически заполнять новыми порциями воздуха через впускной клапан и топливо через форсунку или подавать через впускной клапан смесь воздуха с топливом. Продукты сгорания топлива после их расширения удаляются из цилиндра через выпускной клапан. Эти задачи выполняют механизм газораспределения управляющий открытием и закрытием клапанов и система подачи топлива.
Принцип действия четырехтактного карбюраторного двигателя
Рабочим циклом двигателя называется периодически повторяющийся ряд последовательных процессов протекающих в каждом цилиндре двигателя и обусловливающих превращение тепловой энергии в механическую работу.
Если рабочий цикл совершается за два хода поршня т.е. за один оборот коленчатого вала то такой двигатель называется двухтактным.
Автомобильные двигатели работают как правило по четырехтактному циклу который совершается за два оборота коленчатого вала или четыре хода поршня и состоит из тактов впуска сжатия расширения (рабочего хода) и выпуска.
В карбюраторном четырехтактном одноцилиндровом двигателе рабочий цикл происходит следующим образом:
По мере того как коленчатый вал двигателя делает первый полуоборот поршень перемещается от ВМТ к НМТ впускной клапан открыт выпускной клапан закрыт. В цилиндре создается разряжение 0.07 - 0.095 МПа вследствие чего свежий заряд горючей смеси состоящий из паров бензина и воздуха засасывается через впускной газопровод в цилиндр и смешиваясь с остаточными отработавшими газами образует рабочую смесь.
После заполнения цилиндра горючей смесью при дальнейшем вращении коленчатого вала (второй полуоборот) поршень перемещается от НМТ к ВМТ при закрытых клапанах. По мере уменьшения объема температура и давление рабочей смеси повышаются.
Такт расширения или рабочий ход.
В конце такта сжатия рабочая смесь воспламеняется от электрической искры и быстро сгорает вследствие чего температура и давление образующихся газов резко возрастает поршень при этом перемещается от ВМТ к НМТ.
В процессе такта расширения шарнирно связанный с поршнем шатун совершает сложное движение и через кривошип приводит во вращение коленчатый вал. При расширении газы совершают полезную работу поэтому ход поршня при третьем полуобороте коленчатого вала называют рабочим ходом.
В конце рабочего хода поршня при нахождении его около НМТ открывается выпускной клапан давление в цилиндре снижается до 0.3 -
75 МПа а температура до 950 - 1200 С.
При четвертом полуобороте коленчатого вала поршень перемещается от НМТ к ВМТ. При этом выпускной клапан открыт и продукты сгорания выталкиваются из цилиндра в атмосферу через выпускной газопровод.
Принцип действия четырехтактного дизеля
В четырехтактном двигателе рабочие процессы происходят следующим образом:
При движении поршня от ВМТ к НМТ вследствие образующегося разряжения из воздухоочистителя в полость цилиндра через открытый впускной клапан поступает атмосферный воздух. Давление воздуха в цилиндре составляет 0.08 - 0.095 МПа а температура 40 - 60 С.
Поршень движется от НМТ к ВМТ; впускной и выпускной клапаны закрыты вследствие этого перемещающийся вверх поршень сжимает поступивший воздух. Для воспламенения топлива необходимо чтобы температура сжатого воздуха была выше температуры самовоспламенения топлива. При ходе поршня к ВМТ цилиндр через форсунку впрыскивается дизельное топливо подаваемое топливным насосом.
Впрыснутое в конце такта сжатия топливо перемешиваясь с нагретым воздухом воспламеняется и начинается процесс сгорания характеризующийся быстрым повышением температуры и давления. При этом максимальное давление газов достигает 6 - 9 МПа а температура 1800 - 2000 С. Под действием давления газов поршень перемещается от ВМТ в НМТ - происходит рабочий ход. Около НМТ давление снижается до 0.3 - 0.5 МПа а температура до 700 - 900 С.
Поршень перемещается от НМТ в ВМТ и через открытый выпускной клапан отработавшие газы выталкиваются из цилиндра. Давление газов снижается до 0.11 - 0.12 МПа а температура до 500-700 С. После окончания такта выпуска при дальнейшем вращении коленчатого вала рабочий цикл повторяется в той же последовательности.
Принцип действия двухтактного двигателя
Двухтактные двигатели отличаются от четырехтактных тем что у них наполнение цилиндров горючей смесью или воздухом осуществляется в начале хода сжатия а очистка цилиндров от отработавших газов в конце хода расширения т.е. процессы выпуска и впуска происходят без самостоятельных ходов поршня. Общий процесс для всех типов двухтактных двигателей - продувка т.е. процесс удаления отработавших газов из цилиндра с помощью потока горючей смеси или воздуха. Поэтому двигатель данного вида имеет компрессор (продувочный насос). Рассмотрим работу двухтактного карбюраторного двигателя с кривошипно-камерной продувкой. У этого типа двигателей отсутствуют клапаны их роль выполняет поршень который при своем перемещении закрывает впускные выпускные и продувочные окна. Через эти окна цилиндр в определенные моменты сообщается с впускным и выпускным трубопроводами и кривошипной камерой (картер) которая не имеет непосредственного сообщения с атмосферой. Цилиндр в средней части имеет три окна: впускное выпускное и продувочное которое сообщается клапаном с кривошипной камерой двигателя.
Рабочий цикл в двигателе осуществляется за два такта:
Поршень перемещается от НМТ к ВМТ перекрывая сначала продувочное а затем выпускное окно. После закрытия поршнем выпускного окна в цилиндре начинается сжатие ранее поступившей в него горючей смеси. Одновременно в кривошипной камере вследствие ее герметичности создается разряжение под действием которого из карбюратора через открытое впускное окно поступает горючая смесь в кривошипную камеру.
При положении поршня около ВМТ сжатая рабочая смесь воспламеняется электрической искрой от свечи в результате чего температура и давление газов резко возрастают. Под действием теплового расширения газов поршень перемещается к НМТ при этом расширяющиеся газы совершают полезную работу. Одновременно опускающийся поршень закрывает впускное окно и сжимает находящуюся в кривошипной камере горючую смесь.
Когда поршень дойдет до выпускного окна оно открывается и начинается выпуск отработавших газов в атмосферу давление в цилиндре понижается. При дальнейшем перемещении поршень открывает продувочное окно и сжатая в кривошипной камере горючая смесь перетекает по каналу заполняя цилиндр и осуществляя продувку его от остатков отработавших газов.
Рабочий цикл двухтактного дизельного двигателя отличается от рабочего цикла двухтактного карбюраторного двигателя тем что у дизеля в цилиндр поступает воздух а не горючая смесь и в конце процесса сжатия впрыскивается мелкораспыленное топливо.
Мощность двухтактного двигателя при одинаковых размерах цилиндра и частоте вращения вала теоретически в два раза больше четырехтактного за счет большего числа рабочих циклов. Однако неполное использование хода поршня для расширения худшее освобождение цилиндра от остаточных газов и затраты части вырабатываемой мощности на привод продувочного компрессора приводят практически к увеличению мощности только на 60 70%.
Назначение характеристика двигателя и разрабатываемого узла
Одно из основных достоинств двигателя СМД - его универсальность. Сельскохозяйственные гусеничные и колесные трактора самоходные шасси компрессорные и электрические передвижные станции трелевочные лебедки автогрейдеры и другие подъемные и дорожно-строительные машины - таков диапазон применения двигателей марки СМД. Компактность небольшой вес в сочетании с возможностью изменения мощности при хорошей экономичности обеспечили широкое распространение двигателей СМД. Двигатели оборудуют гидронасосами высокого давления для обслуживания гидросистемы а при установке их на сельскохозяйственные машины - искрогасителями современной конструкции. Двигатели обладают хорошими пусковыми качествами. На двигателях установлены топливные фильтры тонкой очистки которые периодически промываются без разборки что улучшает удобство обслуживания; установлена центрифуга для очистки масла. Производитель Закрытое акционерное общество "Серп и молот" г. Харьков производит дизели для тракторов зерноуборочных комбайнов и другой техники.
Гильзо-поршневая группа вместе с головкой цилиндра образуют замкнутый объем в котором совершается рабочий цикл двигателя. Внутренняя поверхность стенок цилиндра служит направляющей при движении поршня. Эти детали (вместе с поршневыми кольцами) определяют герметичность рабочей полости потери на трение; их конструкция и техническое состояние решающим образом влияют на эффективные показатели и долговечность двигателя.
Технические экономические и экологические требования предъявляемые к двигателям внутреннего сгорания
Автотракторные двигатели – сложные технические устройства. В результате длительного периода развития они в настоящее время обладают достаточно высокой степенью совершенства и приемлемыми мощностными и экономическими показателями а также достаточно надежны в работе. Однако необходимость повышения эффективности использования автомобилей и тракторов требует дальнейшего совершенства как самих машин так и силовых установок.
Особенности конструкций автомобильных и тракторных двигателей и тенденции их развития полностью определяются требованиями к автомобилям и тракторам в соответствии с потребностями народного хозяйства страны. Кроме того эти машины конкурентно способны на мировом рынке.
Основные требования предъявляемые к автомобильным и тракторным двигателям следующие:
развитие необходимой мощности при различных скоростях движения автомобиля (трактора); хорошая приемистость при трогании автомобиля (трактора) и при изменении его рабочих режимов;
максимальная экономичность на всех режимах работы;
низкая себестоимость достигаемая за счет обеспечения технологичности конструкции деталей снижения их массы и применения полноценных заменителей металлов;
высокая удельная мощность и малые габариты без снижения надежности работы;
удобство в эксплуатации а также простота и удобство технического обслуживания и ремонта;
низкие степень токсичности отработавших газов и уровень шума при работе;
перспективность конструкции позволяющая производить ее дальнейшую модификацию путем форсирования мощности двигателя и улучшения ее показателей в соответствии с уровнем развития техники;
быстрая приспособляемость к работе на переменных режимах в зависимости от условий эксплуатации.
Надежность двигателя зависит от условия удельных нагрузок в наиболее ответственных сопряжениях деталей а также от числа кинематических пар входящих в его состав. От числа кинематических пар зависит и механический КПД двигателя.
Износостойкость и долговечность двигателя определяются средней скоростью его поршня механическими и тепловыми нагрузками применяемыми материалами.
Технологичность выбранной схемы характеризуется порядком кинематических пар составляющих конструкцию.
О материалоемкости двигателя следует говорить по его удельной массе – отношению массы двигателя к его номинальной мощности.
Разработка и внедрение новой конструкции автомобильного или тракторного ДВС – трудоемкие и дорогостоящие процессы. Средний срок от разработки новой конструкции ДВС до ее внедрения составляет 5 лет а экологически целесообразное время производства ДВС с учетом последующих модификаций не затрачивающих основные корпусные детали и не требующих коренного преобразования производства зависит от объема последнего и составляет 10 15 лет.
Поэтому уже на стадии проектирования в конструкцию ДВС должны быть заложены решения отвечающие тенденциям развития не только двигателе- и автотракторостроения в целом но и политике общества в вопросах экологии сырьевых и энергетических ресурсов охраны окружающей среды и т. п.
Обзор и анализ конструкций материалы Интернета патентное исследование
Обзор и анализ конструкций
Поршни состоят из двух основных частей: головки I и направляющей части II (Рис. 2 а). Направляющую (тронковую) часть называют юбкой поршня. С внутренней стороны она имеет приливы – бобышки 8 в кот. просверливают отверстие 9 для поршневого пальца. Для фиксации пальца в отверстиях 9 протачивают канавки 10 в кот. размещают детали запирающие палец. Нижнюю кромку юбки часто используют в качестве технологической базы при механической обработке поршня. С этой целью она снабжается иногда точно растачиваемым буртиком 6. С внутреннего торца 5 буртика снимают металл при подгонке поршня по массе в случаях если масса его после обработки превышает норму принятую для данного двигателя. В зоне выхода отверстий под поршневой палец на внешних стенках 7 юбки делают местные углубления 4 вследствие чего стенки этих зон не соприкасаются со стенками цилиндров образуя так наз. холодильники.
Рис. 2. Конструкция поршня и его элементов
Юбка служит не только направляющей (тронковой) частью поршня ее стенки воспринимают также силы бокового давления что увеличивает силу их трения о стенки цилиндра и повышает нагрев поршня и цилиндра. Для обеспечения свободного перемещения поршня в цилиндре прогретого и нагруженного двигателя между направляющей его частью (юбкой) и стенками цилиндра предусматривают зазор величину кот. определяют с учетом линейного расширения материала поршня и цилиндра. Перегрев поршня опасен т. к. приводит к прихватыванию и даже к аварийному заклиниванию его в цилиндре. Однако излишне большие зазоры между поршнем и стенками цилиндра тоже нежелательны т. к. это ухудшает уплотняющие свойства поршневой группы и вызывает стуки поршня о стенки цилиндра.
Головка поршня состоит из днища 1 и образующих ее стенок 11 в кот. протачивают канавки 2 под поршневые кольца разделяемые друг от друга перемычками 12. Нижнюю канавку снабжают дренажными отверстиями 3 через кот. отводят смазочное масло с тем чтобы предотвратить его проникновение (подсос) в камеру сгорания. Диаметр дренажных отверстий составляет примерно 25 – 3 мм. При меньшем размере они быстро загрязняются и выходят из строя.
Днище головки поршня является одной из стенок камеры сгорания и воспринимает поэтому давление газов омывается открытым пламенем и раскаленными до температуры 1500 – 2500 газами. Для увеличения прочности днища и повышения общей жесткости головки ее стенки 11 снабжаются массивными ребрами 13 связывающими стенки и днище с бобышками 8. Оребряют иногда и днище но чаще всего его делают гладким с переменным сечением постепенно утолщающимся к периферии как показано на Рис. 2 а. При таком сечении улучшается теплоотвод от днища и уменьшается его нагрев.
Днища поршней в двигателях автомобильного тракторного и мотоциклетного классов изготовляют плоскими выпуклыми вогнутыми и фигурными (Рис. 2 а г - к). Формы их выбирают с учетом типа двигателя камеры сгорания принятого смесеобразования и технологии изготовления поршней. Самой простой и технологически целесообразной явл-ся плоская форма днища. Головка поршня имеет при этом относительно малые массу и поверхность соприкосновения с раскаленными газами что способствует снижению ее тепловой напряженности. Поэтому плоская форма днища применяется в различных двигателях и особенно широко ее используют в автомобильных.
Сравнительно несложную геом. форму имеют также выпуклые и вогнутые днища (Рис. 2 г д). Выпуклая форма придает днищу большую жесткость и уменьшает возможное нагарообразование (масло проникающее в камеру сгорания с выпуклого днища легко стекает но выпуклое днище всегда бывает горячее плоского). Вогнутая форма днищ облегчает общую компоновку сферических камер сгорания но создает благоприятные условия для повышенного нагарообразования поэтому в четырехтактных двигателях выпуклые и особенно вогнутые днища находят ограниченное применение. Однако в двухтактных двигателях с контурной продувкой где выпуклые и вогнутые формы днищ облегчают организацию продувки цилиндров их широко используют. В двухтактных двигателях используют также фигурные днища с козырьками-отражателями или дефлекторами (Рис. 2 е) обеспечивающими заданное направление потоку при продувке цилиндров. Фигурные днища с различного рода вытеснителями (Рис. 2 ж) применяют и в четырехтактных бензиновых двигателях в том числе и фигурные днища позволяющие полностью или частично размещать камеру сгорания в головке поршня (Рис. 2 з).
Головка поршня по сравнению с юбкой в любом случ. имеет более высокую рабочую температуру а следовательно и больше чем юбка увеличивается в размерах поэтому диаметр головки всегда делают меньше диаметра юбки на 05 – 07 мм (по расчету) и придают ей форму цилиндра или усеченного конуса с малым основанием у днища или же выполняют ступенчатой с определенными размерами жарового пояса 14 (Рис. 2 а). Выбирают головки так чтобы ее стенки в горячем состоянии на режиме максимальной мощности двигателя не соприкасались со стенками цилиндра. Тем не менее головку считают уплотняющей частью поршня имея в виду что стенки ее вместе с поршневыми кольцами образуют уплотняющий лабиринт.
На днище поршня в точке 15 прежде делали технологическую центровку и предусматривали для нее специальный прилив снизу. В настоящее время внешний выступ с центровкой срезают при обработке или же поршень крепят с использованием отверстий 9 в бобышках. Базовой поверхностью в обоих случаях является точно обработанный буртик 6 или просто поясок 18 растачиваемый непосредственно в стенках 7 юбки (Рис. 2 б). Для этих же целей бобышки снабжают приливами 16 и технологическими отверстиями 19 (Рис. 2 в). При отсутствии буртика 6 поршни подгоняют по массе за счет снятия металла с торцов 17 приливов 16 на бобышках.
Являясь базовой деталью поршневой группы и наиболее напряженным элементом кривошипно-шатунного механизма поршень должен обладать высокой прочностью теплопроводностью износостойкостью и при этом иметь возможно малую массу. С учетом этого выбирают и конструкцию и материал поршней. Для двигателей автотракторного типа поршни изготавливают из алюминиевых сплавов и чугуна но применяют иногда сталь и магниевые сплавы.
Поршни из чугуна прочны и износостойки. Благодаря небольшому коэффициенту линейного расширения чугуна они могут работать с относительно малыми зазорами обеспечивая хорошее уплотнение цилиндра даже в двигателях имеющих большую тепловую напряженность (двухтактные и др.). Однако чугун имеет большую плотность (73 ) что приводит к переутяжелению изготовленных из него поршней. Чугун имеет также низкую теплопроводность поэтому нагрев днища у чугунных поршней достигает 400 .
Рис. 3. Профилирование тронковой части поршней компенсационные вставки и прорези в их стенках
Подавляющее большинство быстроходных бензиновых двигателей и дизелей автотракторного типа снабжают поршнями из алюминиевых сплавов. Основу их составляет алюминий сплавленный с медью (6 – 12 %) или кремнием (до 23 %). Большим достоинством алюминиевых поршневых сплавов явл-ся то что они примерно в 26 раза легче чугуна обладают в 3 – 4 раза большей теплопроводностью и хорошими антифрикционными свойствами. Благодаря этому изготовленные из этих сплавов так наз. алюминиевые поршни примерно на 30 % легче чугунных хотя стенки их по соображениям прочности делаются толще последних. Нагрев днища алюминиевых поршней обычно не превышает 300 что способствует лучшему наполнению цилиндров и позволяет несколько увеличивать степень сжатия бензиновых двигателей при работе на данном сорте топлива. Поэтому мощностные и экономические показатели двигателей при переходе на алюминиевые поршни улучшаются.
Недостатками алюминиевых поршневых сплавов являются: большой коэффициент линейного расширения (в 16 – 2 раза больший чем у чугуна) значительное уменьшение механической прочности при нагреве (нагрев до температуры 300 снижает их прочность на 50 – 55 % против 10 % у чугунных) и сравнительно малая износостойкость. Однако современные методы производства и конструирования алюминиевых поршней позволяют широко использовать алюминиевые сплавы для поршней автомобильных и тракторных двигателей. Опыт показывает что правильно сконструированные алюминиевые поршни могут работать с очень малыми зазорами не вызывая стука даже в холодном состоянии. В практике двигателестроения достигают этого несколькими дополняющими друг друга методами.
Использование цилиндрической юбки и косого разреза ее по всей длине (Рис. 3 а) не оставляет следа на стенках цилиндра и позволяет сближаться стенкам юбки при нагреве. (Этот способ широко применяли прежде.)
Разрез юбки в виде Т- или П-образных прорезей (Рис. 3 б) в сочетании с овальной формой юбки. Разность осей овала составляет 03 – 05 мм причем большую ось его располагают перпендикулярно оси поршневого пальца как показано на Рис. 3 поэтому юбка соприкасается со стенками цилиндра только в плоскости качания шатуна узкими полосками и при нагреве может свободно расширяться в обе стороны по оси поршневого пальца увеличивая зону своего контакта с цилиндром.
Юбке таких поршней придают не только овальную но и конусную форму располагая большой диаметр усеченного конуса по нижней кромке юбки с разницей в диаметрах равной 005 мм. Они удовлетворительно работают с очень малыми тепловыми зазорами составляющими в среднем 002 – 003 мм. Однако для дизелей и вообще форсированных двигателей такие поршни не применяют.
Компенсационные вставки ограничивающие тепловое расширение юбки в плоскости качания шатуна (Рис. 3 г д) представляют собой инварные (2) или стальные (1) пластины залитые основным металлом и связывающие стенки юбки с бобышками поршня. Чтобы уменьшить при этом нагрев юбки последнюю в двух сторон бобышек отделяют от головки поперечными изолирующими прорезями.
Инварные вставки (сталь содержащая около 35 % никеля) имеют весьма низкий коэффициент линейного расширения. С их помощью между юбкой поршня и стенками цилиндра практически удается сохранять неизменным как в холодном так и прогретом состоянии двигателя. Поршни с инварными вставками обычно имеют развитые холодильники и свободно расширяются только в направлениях оси порш. пальца (Рис. 3 д) сохраняя практически величину исходного зазора. Широко применяют и более дешевые вставки из нелегированной стали кот. заливают в бобышки так что вместе с тонким слоем основного алюминиевого сплава поршня они образуют биметаллические пары (Рис. 3 г). Вследствие разности коэффициентов линейного расширения стали и алюминиевого сплава при нагреве таких стенок они деформируются и придают юбке овальную форму изгибаясь наружу в разные стороны по оси порш. пальца. Такие поршни имеют повышенную прочность и жесткость поэтому их можно использовать в дизелях.
Иногда компенсационные вставки выполняют в виде различных стальных колец кот. заливают в верхнюю часть юбки как показано на Рис. 3 в.
Конусные и овально-конусные неразрезные юбки обладают повышенной прочностью и жесткостью поэтому их применяют для поршней тракторных и автомобильных дизелей. Однако тепловые зазоры при этом в сравнении например с разрезными конструкциями юбок приходится увеличивать в 5 – 10 раз. А это порождает шум и неприемлемо для двигателей легковых автомобилей.
Овально-бочкообразные профили юбок строят с учетом температурного состояния и нагруженности элементов поршня. На Рис. 3 е дан пример рассматриваемого профиля для двух взаимно перпендикулярных плоскостей тракторного поршня (в плоскостях качания шатуна и оси поршневого пальца).
Овально-бочкообразные профили позволяют работать с малыми тепловыми зазорами способствуют более правильному распределению масла в зонах соприкосновения поршня со стенками цилиндра а также исключают контакт с ними верхней и нижней кромок поршня в момент его перекладок от одной стенки к др. при изменении им направления движения. В современных двигателях внутреннего сгорания такие поршни находят исключительно широкое применение.
Рис. 4. Поршни автомобильных и тракторных двигателей:
а – ЗИЛ-130; б – КамАЗ; в – тракторного форсированного дизеля с масляным охлаждением
Охлаждение поршней в двигателях автомобилей и тракторов осуществляют маслом из системы смазки. При струйном охлаждении маслом омывают внутреннюю поверхность днища поршня с помощью форсунок. Последние размещают или на верхней головке шатуна а масло подводят по сверлению в стержне шатуна или через неподвижные форсунки расположенные в зоне НМТ поршня.
В настоящее время широко применяют более эффективный способ охлаждения поршня путем подачи масла в специальную кольцевую полость в его головке. Масло в нее вводят по вертикальному каналу конусной формы (Рис. 4 б в) в кот. входит сопло неподвижной форсунки при нахождении поршня в НМТ а удаляют через аналогичный канал на противоположной стороне юбки (Рис. 4 б). Применение полостного охлаждения головки поршня позволяет на 60 и более понижать температуру горячих ее точек и соответственно уменьшать тепловой поток в сторону юбки. Но отливка поршня осложняется необходимостью применения специального солевого стержня и последующего его вымывания.
Поршни современных автомобильных и тракторных двигателей как правило покрывают (электролитическим способом) тонким слоем олова (около 0005 мм). Это во всех случаях улучшает приработку их к стенкам цилиндров и предохраняет от возможных задиров в начальной стадии работы т. к. в случае местного перегрева олово плавится и выступает как смазка.
Поршни дизелей работают с большей чем в бензиновых двигателях механической и тепловой напряженностью поэтому отливают их сравнительно толстостенными из высококремнистых алюминиевых сплавов или штампуют причем с юбкой не имеющей разрезов прерывающих тепловые потоки и облегчающих деформацию ее стенок. Вследствие этого юбка всегда имеет повышенную температуру нагрева что вынуждает монтировать поршни с зазорами около 02 мм и применять масляное охлаждение.
Цилиндры относятся к главным элементам поршневых двигателей. Стенки их внутренней полости служат направляющими для поршня при его перемещениях между крайними положениями поэтому длина образующих цилиндра предопределяется величиной хода поршня и размерами последнего. Цилиндр работает в условиях резко переменных давлений в надпоршневой полости. Стенки ее соприкасаются с пламенем и горячими газами раскаленными до температуры 1500 – 2500 а средняя скорость скольжения поршня по стенкам достигает 11 – 17 мс поэтому цилиндры должны обладать большой механической прочностью повышенной жесткостью и хорошо противостоять различным видам износа при ограниченной смазке. Металл цилиндров должен обладать хорошими литейными свойствами и легко обрабатываться на станках.
В соответствии с этими требованиями основным материалом для цилиндров служит перлитный серый чугун с небольшими добавками легирующих элементов (никель хром и др.) а также высоколегированный чугун сталь и алюминиевые сплавы с хромовыми и др. покрытиями внутренних стенок. Поверхности последних тщательно обрабатывают и наз-ют зеркалом цилиндра.
Высокая температура газов в надпоршневой полости и большое количество теплоты выделяющейся при трении поршня и поршневых колец о зеркало цилиндра вызывают интенсивный нагрев стенок вследствие чего возникает необходимость в постоянном отводе от них теплоты. Достигают это непрерывным охлаждением стенок цилиндров жидкостью или воздухом. Даже кратковременное прекращение такого охлаждения приводит к аварии цилиндра и выходу из строя двигателя. На прогретом двигателе температуру стенок поддерживают в пределах 100 – 150 . Более высокую температуру имеют при этом стенки верхней зоны цилиндров омываемые наиболее горячими газами. В двигателях с воздушным охлаждением отдельные участки верхней зоны цилиндров нагреваются до 170 – 180 а средняя температура их стенок всегда бывает выше чем при жидкостном охлаждении. В зависимости от способа охлаждения конструкция цилиндров и всего двигателя приобретает свои характерные особенности.
Рис. 5. Цилиндры двигателей с воздушным охлаждением
Цилиндры двигателей воздушного охлаждения отливают индивидуально а для увеличения теплоотвода наружную поверхность их снабжают ребрами треугольного и реже прямоугольного сечения как показано на Рис. 5. Следовательно при воздушном охлаждении цилиндр строго говоря состоит из двух конструктивных элементов: гильзы или как ее наз-ют иногда втулки и оребрения. Размер ребер и межреберных промежутков выбирают из условий чтобы оребрение оказывало возможно меньшее сопротивление потоку охлаждающего воздуха и в то же время было достаточно развитым и обеспечивало нужную интенсивность теплоотвода. В существующих конструкциях площадь поверхности оребрения цилиндра примерно в 10 раз превышает площадь его зеркала в зоне оребрения.
Рис. 6. Остов двухрядного двигателя V-4 МеМЗ:
– поддон; 2 – картер туннельного типа; 3 – цилиндр; 4 – головка цилиндра; 5 – переходная втулка под свечу зажигания; 6 – направляющая втулка клапана; 7 – седло клапана; 8 – анкерная шпилька; 9 – ось отверстий под коренные опоры коленчатого вала
Оребряемой поверхности гильзы как показано на Рис. 5 а б придают цилиндрическую или коническо-цилиндрическую (корсетную) форму. Чаще применяют гильзы с цилиндрической средней частью и с конической формой ее периферийных зон. Это способствует выравниванию температуры как по окружности так и по высоте цилиндра в частности уменьшает перепад температур в зоне перехода от оребренной части цилиндра к неоребренной. Утолщение стенок гильзы в верхней и нижней ее зонах повышает также общую жесткость цилиндра а уменьшение толщины стенок гильзы в средней части увеличивает сечение воздушных каналов что способствует лучшему теплоотводу.
В двигателях с воздушным охлаждением применяют как монолитные так и комбинированные цилиндры. Первые из них отливают из чугуна реже делают стальными а в малых двигателях применяют также алюминиевые сплавы с хромированной поверхностью зеркала. Ребра отливают вместе с гильзой и механически не обрабатывают или нарезают на станках. Известен также способ навивки ребер из тонкой ленты (с развальцовыванием ее у основания). Чаще используют первый наиболее простой и экономически выгодный метод. Комбинированные цилиндры представляют собой алюминиевую оребренную основу с запрессованной в нее например чугунной гильзой (Рис. 5 в). В таких цилиндрах высокая износостойкость сочетается с хорошим теплоотводом т. к. теплопроводность алюминиевых сплавов в три-четыре раза выше теплопроводности чугуна. Более высокими качествами обладают биметаллические цилиндры получаемые методом заливки ребер обеспечивающим монолитность их соединения с основой цилиндра (Рис. 5 г).
В большинстве автомобильных и тракторных двигателей с воздушным охлаждением цилиндры вместе с их головками крепят общими болтами или шпильками к верхней части картера т. е. несквозными анкерными связами как показано например на Рис. 6. Способ крепления цилиндров с помощью сквозных несущих или анкерных шпилек и особенно болтов облегчает сборку и разборку двигателя не мешает необходимому сближению смежных цилиндров (компактен) и разгружает стенки цилиндров от растягивающих усилий возникающих в результате давления газов в надпоршневой полости. Все это благоприятно сказывается на общей компоновке двигателя и позволяет несколько улучшить толщину стенок цилиндра но в известной мере увеличивает негативное влияние тепловых деформаций.
В случае крепления цилиндров к картеру с помощью присоединительного фланца отливаемому совместно с гильзой (Рис. 5 д) стенки ее подвержены растягивающим усилиям и должны следовательно быть толще. Фланцевое крепление менее надежно наличие его затрудняет монтажно-демонтажные работы и увеличивает массу цилиндра. Поэтому в современных многоцилиндровых двигателях такой способ применяют редко хотя использование его уменьшает деформацию гильзы от затяжки и нагрева.
Многоцилиндровые тракторные и автомобильные двигатели с воздушным охлаждением снабжают общим для всех цилиндров картером а стык его с нижним торцом гильзы уплотняют металлическими прокладками используемыми также для выравнивания надпоршневого зазора до заданной величины.
Цилиндры двигателей с жидкостным охлаждением в отличие от рассмотренных оребренных изготовляют с полостью под охлаждающую жидкость что значительно усложняет их конструкцию (Рис. 7а). Внутренние стенки 1 образуют гильзу цилиндра а внешние 2 более тонкие – его рубашку. Стенки рубашки охватывают гильзовую часть цилиндра так что между ними образуется полость 3 для циркуляции охлаждающей жидкости.
Из соображений облегчения ремонта и увеличения срока службы цилиндров с жидкостным охлаждением их часто изготовляют комбинированными со вставками на всю длину зеркала цилиндра и с легкосъемными гильзами. В 50 – 60-х годах широко применяли также короткие вставки (около 50 мм длины) изготовлявшиеся из аустенитного износостойкого чугуна нирезист. Их запрессовывали в верхнюю наиболее изнашиваемую зону цилиндра как показано на Рис. 7 ж и обрабатывали совместно с зеркалом цилиндра (гильзы). Срок службы цилиндров с такими вставками увеличивался в 25 – 3 раза. В настоящее время в связи с резким улучшением качества горюче-смазочных материалов и совершенствованием фильтров для воздуха и масла дорогостоящие нирезистовые вставки утратили свое значение.
Рис. 7. Цилиндры двигателей жидкостного охлаждения:
– стенки цилиндра; 2 – стенки рубашки охлаждения; 3 – полость рубашки охлаждения; 4 – короткая противоизносная вставка; 5 – сухая гильза; 6 – сухая легкосъемная гильза; 7 - легкосъемная гильза; 8 – резиновое уплотняющее кольцо; 9 – медное уплотнительное кольцо
Вставки запрессовываемые на всю длину цилиндра как показано например на Рис. 7 б в не соприкасаются с охлаждающей жидкостью вследствие чего их наз-ют сухими гильзами. Сухие гильзы не ослабляют общую жесткость цилиндра но несколько усложняют его конструкцию и удорожают производство поэтому в двигателях автомобилей и тракторов с жидкостным охлаждением их используют сравнительно редко. При ремонтах двигателя связанных с расточкой цилиндров сухие гильзы сохраняют до тех пор пока их ремонтный размер находится в допускаемых пределах.
Легкосъемные гильзы устанавливают в цилиндры свободно с гарантированным зазором (примерно 08 мм). Это большое их достоинство. В случае износа их легко заменяют новыми или другими заранее отремонтированными. Легкосъемные гильзы (Рис. 7 г - з) непосредственно омываются охлаждающей жидкостью циркулирующей в рубашке охлаждения в связи с чем их наз-ют мокрыми гильзами. Они имеют как правило опорный пояс или фланец и один или два установочных пояса с наружной стороны гильзы. С помощью установочных хорошо обрабатываемых поясов гильзу центрируют в соответствующих гнездах цилиндра а опорный фланец фиксирует их положение по высоте цилиндра.
Нижний установочный пояс гильз уплотняют с помощью резиновых или медных колец. Резиновые кольца чаще всего круглые примерно 4-миллиметровые в количестве 2 – 3ставят с натягом обычно на нижнем утолщенном установочном поясе гильзы в специально сделанные для этой цели проточки (Рис. 7 г). Если резиновые кольца не ставят на гильзу то нижний установочный пояс ее изготовляют без утолщения (Рис. 7 д). Глубину проточек делают меньше сечения резинового кольца поэтому последние несколько выступают из канавок а при установке гильзы в гнездо деформируются и надежно уплотняют стык.
При использовании резиновых колец прямоугольного сечения нижний установочный пояс снабжают буртиком. Уплотнительное кольцо надевают с натягом непосредственно на нижний установочный пояс гильзы а в центрирующем гнезде цилиндра делают соответствующий уступ к кот. резиновое кольцо плотно прижимается буртиком гильзы (Рис. 7 е). Прямоугольные кольца применяют также для верхней канавки нижнего установочного пояса гильз. Канавку под такое кольцо делают шире других и ориентируют ее напротив заходной фаски гильзового отверстия цилиндра (Рис. 7 з). Резиновое кольцо плотно прижимается к этой фаске и полностью перекрывает зазор на стыке исключая этим разрушительную кавитацию в щели стыка.
Применение медного уплотнительного кольца показано на Рис. 7 ж. Легкосъемные гильзы при этом имеют только один удлиненный нижний установочный пояс к кот. вплотную примыкает опорный фланец гильзы. Между этим опорным фланцем и уступом в центрирующем гнезде цилиндра и зажимают уплотнительное кольцо. В верхней зоне цилиндра такая гильза совсем не соприкасается со стенками рубашки охлаждения а имеет только небольшое утолщение кот. улучшает уплотнение ее газового стыка достигаемого с помощью прокладки кот. устанавливают между цилиндром и его головкой. Однако данная конструкция гильзы приводит к некоторому короблению ее при затяжке головки цилиндров.
Легкосъемные мокрые гильзы в большинстве случаев отливают из серого перлитного чугуна СЧ 21-40 и подвергают закалке токами высокой частоты. Гильзы из легированного чугуна применяют незакаленными (двигатели ММЗ СМД).
Поршни моноклинного исполнения
Поршни этого типа выполняются с использованием моноклинной оснастки т.е. стержень формирующий внутреннюю поверхность поршня состоит из одной детали.
Моноклинные поршни по сравнению с поршнями произведенными на многоклинных оснастках имеют простую но выполненную с более высокой точностью внутреннюю поверхность лучшую структуру и прочность материала. Моноклинные поршни применяются в основном в бензиновых двигателях и дизелях с частотой вращения не более 2500 обмин в тех случаях когда требования к качеству материала поршня предпочтительнее требований к его массе.
Поршни трехклинного исполнения
Поршни этого типа выполняются с использованием трехклинной оснастки т.е. стержень формирующий внутреннюю поверхность поршня состоит из трех деталей. Такая конструкция стержня позволяет получить сложную внутреннюю поверхность поршня с выборками и ребрами над бобышками. Трехклинные поршни представляют собой промежуточный вариант между моноклинными и пятиклинными поршнями и являются компромиссом при соблюдении требований по массе и прочности. Применяются как в бензиновых двигателях так и в дизелях.
Поршни пятиклинного исполнения
Поршни с термовставкой
Поршни этого типа выполняются со стальной кольцевидной термовставкой залитой ниже головки поршня или с двумя вставками прямоугольной формы заливаемыми в бобышки. Термовставки предназначены для уменьшения теплового расширения поршня. При наличии современных материалов и технологий изготовления поршней данная конструкция является устаревшей.
Поршни с нирезистовой вставкой
Поршни этого типа выполняются с нирезистовой вставкой которая повышает износостойкость канавки под первое компрессионное кольцо испытывающей наибольшие нагрузки. Вставка сделана из специального легированного чугуна (нирезиста). Поршни с нирезистовой вставкой применяются в высокофорсированных дизелях.
Поршни с маслоохлаждаемой полостью
Поршни этого типа выполняются с маслоохлаждаемой полостью служащей для снижения температуры головки поршня в зоне поршневых колец. Полость в отливке поршня формируется при литье солевым стержнем который затем вымывается. Масло в полость попадает через специальные отверстия находящиеся рядом с бобышками. Поршни с маслоохлаждаемой полостью применяются в высокофорсированных дизелях.
Поршни с маслоохлаждаемой трубкой
Поршни этого типа выполняются с залитой маслоохлаждаемой трубкой которая позволяет снизить температуру головки поршня в зоне поршневых колец.
Масло в трубку попадает через отверстия находящиеся в бобышках. Поршни с маслоохлаждаемой трубкой применяются в дизелях высокой мощности например тепловозных.
Патентное исследование
Составной поршень (варианты)
Изобретение относится к машиностроению в частности касается конструкции поршней двигателей внутреннего сгорания (ДВС) иили компрессоров. Составной поршень включает корпус с бобышками под поршневой палец головку с днищем и по меньшей мере одно поршневое кольцо. Головка посредством осевого пальца с окружной канавкой вокруг него подвижно с возможностью вращения и продольного перемещения сочленена с корпусом поршня. В окружной канавке головки установлена цилиндрическая пружина а в зазоре между посадочными плоскостями головки и корпуса - поршневое кольцо выполненное в виде плоской спирали. Приведен другой вариант выполнения поршня. Поршень обеспечивает повышение надежности и долговечности поршневой группы ДВС.
Описание изобретения.
Изобретение относится к машиностроению в частности касается конструкции поршней двигателей внутреннего сгорания (ДВС) иили компрессоров.
В зависимости от назначения типа и мощности двигателя поршни ДВС различаются по конструкции однако в общих чертах поршень обычно представляет собой деталь цилиндрической формы условно разделяемую на головку с днищем и среднюю часть - юбку с бобышками отверстия в которых предназначены для установки поршневого пальца. На боковой поверхности поршня в зоне головки выполнены окружные канавки для установки поршневых колец (см. например «ДВС. Устройство и работа поршневых и комбинированных двигателей». Под ред. А.С.Сорина и М.Г.Круглова. М. 1990 г. стр.68-70).
Надежность поршня как важнейшей детали двигателя в значительной степени определяет надежность ДВС в целом а так как помимо этого поршень в процессе работы подвергается воздействию значительных по величине знакопеременных тепловых и механических нагрузок то повышение надежности поршней является важнейшей задачей двигателестроения.
Известен например поршень по авт.свидетельству SU №1255730 МПК F02F 300 1986 г. в котором повышение надежности достигнуто за счет интенсификации его охлаждения для чего в корпусе между днищем и поршневым пальцем выполнена полость сообщающаяся с дренажными окнами в поршневой канавке и снабженная центральным отверстием с клапаном связывающим полость с подпоршневым пространством.
При работе машины масло снимаемое со стенок цилиндра и через дренажные окна поступающее в полость и далее через клапан - в подпоршневое пространство дополнительно охлаждает поршень облегчая условия его работы.
Недостатком известного технического решения обусловленным низкой эффективностью предложенной системы охлаждения является то что величина полученного положительного эффекта невелика и достигнута за счет значительного усложнения конструкции и снижения технологичности изделия.
Известен составной поршень (авт.свидетельство SU №1698469 МПК F02F 300 1989 г.) включающий головку с поршневыми кольцами и жестко связанный с головкой тонкостенный корпус причем головка и корпус изготовлены из материалов с различными физико-механическими свойствами.
В известном поршне головка изготовленная из термостойкого высокопрочного материала обладает достаточно высокой надежностью однако корпус жестко связанный с головкой и практически без ослабления воспринимающий действующие на нее силы и моменты остается слабым и ненадежным звеном поршня снижающим надежность поршневой группы в целом.
Задачей настоящего изобретения является разработка поршня повышенной надежности.
По первому варианту задача изобретения достигается за счет того что в составном поршне включающем корпус головку и по меньшей мере одно поршневое кольцо головка посредством осевого пальца с окружной канавкой снабженного средствами его крепления в корпусе подвижно с возможностью вращения и продольного перемещения сочленена с корпусом поршня при этом в окружной канавке головки установлена цилиндрическая пружина а в зазоре между посадочными плоскостями головки и корпуса - поршневое кольцо выполненное в виде плоской спирали.
По второму варианту задача изобретения достигается за счет того что в составном поршне включающем корпус головку и по меньшей мере одно поршневое кольцо головка посредством осевого пальца с окружной канавкой снабженного средствами его закрепления в корпусе подвижно с возможностью вращения и продольного перемещения сочленена с корпусом поршня при этом в окружной канавке головки установлена цилиндрическая пружина в зазоре между посадочными плоскостями головки и корпуса - поршневое кольцо выполненное в виде плоской спирали а боковая поверхность корпуса облицована рубашкой.
Кроме того по первому и второму вариантам изобретения в корпусе поршня напротив окружной канавки головки равномерно по окружности выполнены продольные дренажные каналы связывающие зазор между посадочными плоскостями головки и корпуса с подпоршневым пространством а на обращенной к шатуну поверхности поршневого кольца - радиальные канавки.
На фиг.1 и 2 приведены продольный разрез поршня соответственно по первому и второму варианту изобретения.
Поршень содержит головку 1 с пальцем 2 канавкой 3 и посадочной плоскостью 4 корпус 5 с дренажными каналами 6 отверстием 7 и посадочной плоскостью 8 пружину 9 поршневое кольцо 10 средство крепления головки в корпусе 11 рубашку 12.
При сборке поршня головка 1 с установленными в канавке 3 пружиной 9 а на плоскости 4 - поршневым кольцом 10 вставляется в отверстие 7 корпуса 4 после чего фиксируется одним из известных средств например штифтом 11 с гарантированными усилием прижатия и остаточным продольным зазором. Величины усилия прижатия и продольного зазора зависят от типа и мощности двигателя и определяются экспериментально в ходе доводки и испытаний двигателя.
Второй вариант изобретения предназначен для использования в мощных преимущественно дизельных двигателях в которых силы трения и кручения между стенками цилиндра и поршня значительно больше чем в бензиновых двигателях малой и средней мощности. Применение дополнительной защитной рубашки обеспечивает увеличение долговечности дорогостоящего поршня так как в первую очередь подвергается износу простая по конструкции дешевая рубашка которая путем замены в случае необходимости просто заменяется.
Формула изобретения.
Составной поршень включающий корпус головку и по меньшей мере одно поршневое кольцо отличающийся тем что головка посредством осевого пальца с окружной канавкой снабженного средствами его крепления в корпусе подвижно с возможностью вращения и продольного перемещения сочленена с корпусом поршня при этом в окружной канавке головки установлена цилиндрическая пружина а в зазоре между посадочными плоскостями головки и корпуса - поршневое кольцо выполненное в виде плоской спирали.
Составной поршень включающий корпус головку и по меньшей мере одно поршневое кольцо отличающийся тем что головка посредством осевого пальца с окружной канавкой снабженного средствами его крепления в корпусе подвижно с возможностью вращения и продольного перемещения сочленения с корпусом поршня при этом в окружной канавке головки установлена цилиндрическая пружина а в зазоре между посадочными плоскостями головки и корпуса - поршневое кольцо выполненное в виде плоской спирали а боковая поверхность корпуса облицована рубашкой.
Гильза цилиндра для двигателя внутреннего сгорания дизельного типа (варианты)
Гильза цилиндра для ДВС дизельного типа имеет по меньшей мере первую и вторую группы открытых внутрь выемок которые выполнены в форме удлиненных канавок последние расположены прерывистым образом в направлении по окружности гильзы. Выемки в группах расположены в верхних 15% длины ходовой поверхности при этом выемки в различных группах взаимно разделены в продольном направлении гильзы и размещены на постоянном уровне в направлении по окружности гильзы. Согласно другому варианту выполнения по меньшей мере одна канавка проходит по всей внутренней поверхности гильзы и имеет высоту менее 30% от минимальной высоты поршневых колец. Канавки имеют глубину в радиальном направлении гильзы больше половины их высоты в продольном направлении гильзы и расположены в верхних 15% длины ходовой поверхности. Гильза цилиндра позволяет во время работы предотвращать возникновение схватываний между поршневыми кольцами и той областью ходовой поверхности где контактное давление между кольцами и этой поверхностью особенно высоко.
Изобретение относится к гильзе цилиндра для двигателя внутреннего сгорания дизельного типа.
Для гильз цилиндров известной проблемой является то что иногда в неблагоприятных ситуациях между поршневыми кольцами и ходовой поверхностью гильзы могут возникать схватывания. Оказалось что такие схватывания носят случайный характер то есть они могут возникать как во время обкатки новой гильзы так и во время обычной работы. Предполагается что схватывания этого типа возникают в верхней части гильзы цилиндра где поршневые кольца и ходовая поверхность подвергаются наиболее сильной нагрузке.
Во время такта сжатия при работе поршня выше него происходит нарастание давления причем продувочный воздух поданный из турбокомпрессора сжимается от первоначального давления например между 03 и 04 МПа (4 бар) до значительно более высокого давления при верхнем положении поршня например 10-15 МПа (100-150 бар). Во время первой части такта сжатия давление нарастает медленно и наиболее сильного повышения давления не происходит до тех пор пока поршень не достигнет своего верхнего положения. Вблизи верхнего положения поршня открываются топливные клапана топливо впрыскивается в цилиндр и зажигается вследствие чего давление в цилиндре во время сгорания повышается до максимального характеризующего сгорание уровня который может составлять например от 16 до 20 МПа (160-200 бар) и в то же время температура в верхней части цилиндра повышается до более 500oС. Во время сгорания сильное повышение давления в камере сгорания выше головки поршня приводит к тому что газ сгорания проникает в кольцевые пространства между канавками поршневых колец и поршневыми кольцами где давление воздействует на обратную сторону колец и выдавливает их по направлению к ходовой поверхности гильзы. Высокая температура во время сгорания также приводит к понижению вязкости пленки смазывающего масла на ходовой поверхности в результате чего масляная пленка легче разрывается. Риск разрыва масляной пленки далее увеличивается из-за относительно медленного движения поршня вблизи его верхнего положения. При этом скорость скольжения поршневых колец относительно ходовой поверхности которая необходима для сохранения масляной пленки на ходовой поверхности является очень низкой. Во время такта расширения поршень проталкивается вниз и наиболее сильное понижение давления происходит в первой половине такта расширения после чего давление понижается относительно медленно и лишь перед тем как поршень проходит каналы для подачи продувочного воздуха давление может в типичном случае понизиться приблизительно до давления продувочного воздуха. Воздействие давления в верхней области цилиндра таким образом является очень сильным по сравнению с его воздействием в остальной части цилиндра. Верхняя область гильзы следовательно во всех отношениях представляет собой часть ходовой поверхности которая подвержена наиболее сильным нагрузкам.
Для предотвращения распространения схватываний которые происходят в нижней части гильзы в другие и более обширные области ранее предпринимались различные действия. Например DK 170430 описывает гильзу цилиндра с двумя кольцевыми выемками в форме канавок которые открыты только по направлению внутрь цилиндра и расположены соответственно непосредственно выше и непосредственно ниже каналов продувочного воздуха. Выемки собирают часть смазывающего масла которое во время такта расширения поршневыми кольцами выталкивается вниз и предотвращают распространение схватываний которые порождаются и распространяются в области ниже каналов продувочного воздуха касающейся гильзы цилиндра юбкой поршня в область выше канавок.
В JP-A 62-32207 описана гильза цилиндра с впускными отверстиями для подачи смазывающего масла в верхней части гильзы и с расположенным по окружности зигзагообразным масляным резервуаром в форме выемки организованным в нижней трети гильзы чуть выше каналов продувочного воздуха. Выемка открыта только в направлении внутрь гильзы и служит для улучшения распределения смазывающего масла причем масло собирается и сохраняется в выемке при проходе поршня мимо выемки во время его движения вниз и впоследствии высвобождается снова для поршневых колец. Благодаря зигзагообразной форме выемки масло распределяется по кольцам когда поршень движется вверх мимо масляного резервуара после того как он миновал свое нижнее положение ниже каналов продувочного воздуха. Выемка таким образом сохраняет смазывающее масло которое в ином случае потерялось бы в этих каналах.
В JP-A 60-259750 описана гильза цилиндра снабженная масляными резервуарами в форме круглых отверстий в ходовой поверхности. Во время работы масляные резервуары собирают смазывающее масло которое выносится вверх поршневыми кольцами от отверстий впрыска масла в нижней части гильзы. Масло сохраненное в резервуарах впоследствии подается к ходовой поверхности для улучшения смазки контактной зоны между поршневыми кольцами и ходовой поверхностью.
В FR-A 1133041 описана гильза цилиндра снабженная множеством маленьких маслозадерживающих полостей или пустот в ходовой поверхности расположенных предпочтительно по всей ее высоте с целью снижения до минимума области контакта и следовательно трения между поршневыми кольцами и ходовой поверхностью.
Известно что схватывания могут происходить из-за локального разрыва масляной пленки в результате чего поршневые кольца могут вступить в прямой контакт с ходовой поверхностью и таким образом инициировать схватывание. Также известно что схватывания вызывают локальный перегрев который при последующей проверке можно заменить как повреждение материалов гильзы и поршневых колец из-за нагрева. До сих пор предполагалось что образование схватываний обусловлено истиранием поверхностей из-за недостатка смазки которое при продолжении работы приводит к вредному выделению тепла вызывая образование на материалах цветов побежалости что является характеристикой схватывания.
Известна гильза цилиндра для ДВС дизельного типа имеющая ходовую поверхность в форме цилиндрической внутренней поверхности по меньшей мере один открытый внутрь масляный тракт с внешней подачей смазывающего масла по меньшей мере первую и вторую группу выемок которые открыты только по направлению внутрь цилиндра выполнены в форме удлиненных канавок и расположены прерывистым образом в направлении по окружности гильзы при этом выемки относящиеся к разным группам взаимно разделены друг относительно друга в продольном направлении гильзы (ЕР 0299174 кл. F 01 М 108 опубл. 1989).
Однако в известной конструкции возможны схватывания между поршневыми кольцами и областью ходовой поверхности где контактное давление между кольцами и этой поверхностью высоко.
Задачей настоящего изобретения является создание такой гильзы цилиндра для которой во время работы предотвращалось бы возникновение схватываний между поршневыми кольцами и той областью ходовой поверхности где контактное давление между кольцами и этой поверхностью особенно высоко.
Поставленная задача решается тем что в гильзе цилиндра для ДВС дизельного типа имеющей ходовую поверхность в форме внутренней поверхности по меньшей мере один открытый внутрь масляный тракт с внешней подачей смазывающего масла по меньшей мере первую и вторую группу выемок которые открыты только по направлению внутрь цилиндра выполнены в форме удлиненных канавок и расположены прерывистым образом в направлении по окружности гильзы при этом выемки относящиеся к разным группам взаимно разделены друг относительно друга в продольном направлении гильзы выемки в группах размещены в верхних 15% длины ходовой поверхности а канавки расположены друг относительно друга в направлении по окружности таким образом что любая линия на ходовой поверхности параллельная оси гильзы пересекается по меньшей мере одной из канавок.
Верх ходовой поверхности находится в продольном направлении гильзы там где расположена верхняя мертвая точка верхнего поршневого кольца и ходовая поверхность простирается вниз до нижней мертвой точки самого нижнего поршневого кольца. Длина ходовой поверхности таким образом больше хода поршня приблизительно на высоту блока колец.
Расположение канавок близко к верху ходовой поверхности в области с наиболее сильной нагрузкой фактически ликвидирует поддерживающую область и создает прерывистую поддержку колец которая должна была бы привести к усилению воздействия на кольца и увеличенному риску схватывания но вопреки этому износ колец и гильзы снижается так как канавки влияют на процесс первоначального образования схватываний.
По-видимому до сих пор общее понимание основного механизма образования схватываний было неправильным так как оно предполагало равномерный постепенный процесс который в течение некоторого периода времени приводил к схватываниям. Схватывание вызывается внезапным очень локальным перегревом обусловленным сильным трением между поршневым кольцом и ходовой поверхностью приводящим к краткому систематическому свариванию поршневого кольца и ходовой поверхности. Сваривание происходит во время такта расширения под действием высокого давления сгорания выталкивающего поршневое кольцо наружу через масляную пленку на ходовой поверхности. Так как давление сгорания также вызывает чрезвычайно сильный толчок вниз воздействующий и на поршень и на поршневое кольцо поршневое кольцо снова подвергается воздействию непосредственно срезаясь с одновременным срезанием материала ходовой поверхности которая становится шероховатой. Срезание вызывает дальнейшее выделение тепла таким образом вызывая следующее сваривание. При последующем прохождении поршневых колец локальное схватывание может быть либо сглажено либо может распространиться на большей области ходовой поверхности.
Размещение на ходовой поверхности даже очень узкой канавки поперек направления движения поршневых колец влияет на фактическое первоначальное образование схватываний в области вокруг канавки. Необходимой предпосылкой для возникновения сваривания является повышенный уровень температуры. Если поршневое кольцо разрывает масляную пленку из-за увеличенного трения между кольцом и ходовой поверхностью будет вырабатываться тепло. В момент когда кольцо проходит канавку в ходовой поверхности нагрев на короткое время заменяется охлаждением и так как материалы как поршневого кольца так и гильзы имеют относительно низкие средние температуры тепло непрерывно отводится от нагретой точки на поршневом кольце.
Кроме противодействия возникновению схватываний канавки предлагаемые настоящим изобретением имеют следующее по существу известное преимущество которое состоит в том что они служат пассивными масляными резервуарами и предотвращают распространение возникших схватываний.
Не обязательно располагать канавки на ходовой поверхности в том месте где поршневые кольца выталкиваются сильнее всего по направлению к этой поверхности и где также характеристики температуры и смазывающего масла как описано выше являются критическими. Так как канавки удаляют некоторую часть поддерживающей области существует риск что кольцо может деформироваться в своей канавке в поршне при прохождении канавки так как оно будучи относительно тонким и упругим подвергается сильной нагрузке. Если кольцо деформируется оно может повредиться от удара о кромку канавки.
Такая деформация поршневых колец и их результирующий износ могут быть предотвращены согласно настоящему изобретению образованием канавок расположенных прерывистым образом в направлении по окружности гильзы и размещением их с взаимным разделением в продольном направлении гильзы. Когда поршневое кольцо проходит некоторые из этих канавок оно поддерживается оставшейся ходовой поверхностью между канавками.
Подобная организация прерывистых канавок когда любая линия на ходовой поверхности параллельная оси гильзы цилиндра пересекается по меньшей мере одной из канавок гарантирует что любая точка на периферии поршневых колец будет проходить одну или несколько охлаждающих канавок в каждом тракте поршня.
Канавки в группах могут быть ориентированы в направлении по окружности гильзы что делает возможным преимущественно простое изготовление гильзы. Канавки на ходовой поверхности могут например быть изготовлены при помощи процессов резания или шлифования.
Канавки в группе предпочтительно размещены на одном уровне в продольном направлении гильзы что еще более упрощает изготовление так как требуется меньшее количество позиционирований при механической обработке.
Далее предпочтительно канавки в каждой группе имеют суммарную протяженность в направлении по окружности гильзы максимум 80% и предпочтительно максимум 60% от окружности ходовой поверхности. Если канавки в группе имеют суммарную протяженность в направлении по окружности гильзы более чем 80% от окружности ходовой поверхности необходимо чтобы поршневые кольца имели нецелесообразно высокую жесткость для предотвращения излишней деформации их в своих канавках. Если канавки в группе имеют суммарную протяженность в направлении по окружности гильзы максимум 60% от окружности ходовой поверхности это обеспечит удовлетворительную поддержку поршневых колец и в то же время всего лишь две группы канавок будут способны покрыть всю окружность ходовой поверхности.
Особенно благоприятный баланс между необходимостью предотвратить схватывания и необходимостью минимизировать деформацию поршневых колец при проходе канавок может быть получен если каждая группа включает по меньшей мере пять и предпочтительно восемь канавок. При пяти и предпочтительно восьми канавках в каждой группе расстояние между областями поддержки поршневых колец в направлении по окружности является небольшим.
Далее канавки в каждой группе могут быть равномерно распределены вдоль окружности ходовой поверхности упрощая таким образом изготовление гильзы и сводя до минимума длину проходящих через канавки частей поршневых колец.
Ходовая поверхность предназначена для использования ее поршневыми кольцами поршня при этом кольца имеют заранее определенную минимальную высоту а канавки в группах имеют высоту которая меньше упомянутой минимальной высоты поршневых колец и предпочтительно составляет максимум 75% от этой минимальной высоты то есть канавки имеют соответственно высоту в интервале от 1 до 3 мм. Если высота канавок больше минимальной высоты поршневых колец они будут прерывать плотное прилегание к ходовой поверхности по меньшей мере одного из колец при его проходе через канавки. Так как канавки расположены в области с максимальным давлением во время как сжатия так и расширения прерывание будет оказывать негативное влияние на эффективность двигателя. Если высота канавок составляет максимум 75% от минимальной высоты поршневых колец это будет эффективной гарантией от нарушения герметичности и улучшит поддержку поршневых колец. Высота канавки от 1 до 3 мм будет эффективно препятствовать образованию схватываний и в то же время сохранять хорошую поддержку поршневых колец в типичном случае при высоте колец более 10 мм.
Канавки принадлежащие к разным группам могут располагаться в продольном направлении гильзы на расстоянии по меньшей мере 35 мм друг от друга. В этом случае предотвращается взаимное влияние концентраций напряжений в областях вокруг кромок канавок относящихся к различным группам.
Канавки имеют глубину по меньшей мере 2 мм в только что изготовленной гильзе.
Масляный тракт расположен ниже канавок.
Из указанного выше источника известна гильза цилиндра для ДВС дизельного типа где гильза имеет внутреннюю цилиндрическую поверхность которая может образовывать ходовую поверхность для поршневых колец поршня имеющих заранее определенную минимальную высоту и где гильза имеет по меньшей мере один открытый внутрь масляный тракт с внешней подачей смазывающего масла и по меньшей мере одну канавку которая открыта только по направлению внутрь цилиндра.
Согласно второму варианту выполнения задача достигается тем что в гильзе цилиндра для ДВС дизельного типа причем гильза имеет цилиндрическую внутреннюю поверхность которая может образовывать ходовую поверхность для поршневых колец поршня имеющих заранее определенную минимальную высоту а также гильза имеет по меньшей мере один открытый внутрь масляный тракт с внешней подачей смазывающего масла и по меньшей мере одну канавку которая открыта только по направлению внутрь цилиндра по меньшей мере одна канавка проходит вокруг всей внутренней поверхности гильзы и имеет высоту менее 30% от минимальной высоты поршневых колец а канавки имеют глубину в радиальном направлении гильзы больше половины их высоты в продольном направлении гильзы и расположены в верхних 15% длины ходовой поверхности.
Деформация поршневых колец в своих канавках с результирующим износом колец предотвращается в данном варианте тем что по меньшей мере одна канавка имеет высоту менее 30% от минимальной высоты поршневых колец. Поршневое кольцо таким образом всегда поддерживается ходовой поверхностью на площади соответствующей по меньшей мере 70% высоты поршневого кольца и может соответственно проходить канавку без нецелесообразной деформации его в своей канавке. Как упомянуто выше канавки противодействуют возникновению схватываний.
Приемлемый срок службы гильзы может быть достигнут при использовании канавок имеющих глубину в радиальном направлении гильзы больше половины их высоты в продольном направлении гильзы. Если например минимальная высота поршневых колец составляет 6 мм а ходовая поверхность во время нормальной плавной работы изнашивается на приблизительно 002 мм за 1000 часов работы то в этом случае канавки будут иметь глубину 06 мм и не будут полностью изнашиваться в течение приблизительно 3 4 лет непрерывной работы. Обычно морские двигатели разрабатываются на приблизительно два года непрерывной работы между проверками их работоспособности в данной перспективе указанная глубина канавок рассматривается как подходящий нижний предел.
Каждая канавка может проходить по всей окружности ходовой поверхности на постоянном уровне в продольном направлении гильзы. Таким образом как описано выше предотвращается прерывание канавками плотного прилегания поршневых колец.
Далее могут быть изготовлены по меньшей мере три канавки. Так как канавки согласно данному варианту настоящего изобретения являются относительно узкими может быть выгодным расположение трех или более канавок близко друг к другу для улучшения предотвращения схватываний.
В верхних 10% длины ходовой поверхности расстояние между канавками может быть меньше восьмикратной высоты канавок. При таком относительно близком расположении в верхней части ходовой поверхности можно в значительной степени предотвратить образование схватываний в области ходовой поверхности с наибольшей нагрузкой.
Каждая канавка может простираться вверх и вниз между границами цилиндрической секции ходовой поверхности при этом высота этой секции меньше чем минимальная высота поршневых колец. В этом случае предотвращается прерывание канавками плотного прилегания поршневых колец и в то же время при той же площади канавок область поддержки поршневых колец увеличивается.
В обоих описанных выше вариантах настоящего изобретения канавки могут соответственно иметь глубину по меньшей мере 2 мм в только что изготовленной гильзе чтобы гарантировать долгий срок службы гильзы без необходимости повторного изготовления канавок на ходовой поверхности путем механической обработки.
Масляный тракт может быть расположен ниже канавок для предотвращения воздействия на подачу масла высоких давлений возникающих в верхней части гильзы.
Изобретение поясняется чертежами.
Фиг. 1 представляет собой вид сбоку гильзы цилиндра с частичным продольным разрезом на котором поршень показан без разреза в его верхней мертвой точке.
Фиг.2 представляет собой развертку верхней части гильзы цилиндра с канавками на внутренней поверхности.
Фиг. 3 представляет собой развертку аналогичную развертке на фиг.2 верхней части гильзы цилиндра с канавками на внутренней поверхности согласно второму варианту изобретения.
Фиг.4 представляет собой развертку верхней части гильзы цилиндра с канавками на внутренней поверхности в форме отверстий.
Фиг. 5 представляет собой развертку аналогичную развертке на фиг.2 верхней части гильзы цилиндра с канавками на внутренней поверхности согласно третьему варианту изобретения.
Фиг.6 представляет собой увеличенное поперечное сечение канавки на ходовой поверхности гильзы цилиндра с показанными одновременно поршневым кольцом и поршнем.
Гильза цилиндра для большого двухтактного двигателя показана на фиг.1. В зависимости от размера двигателя гильза цилиндра может быть изготовлена различных размеров с диаметром расточки в типичном случае в интервале от 250 до 1000 мм и соответствующими длинами в типичном случае в интервале от 100 до 420 см. Гильза 1 обычно изготавливается из литого чугуна и может быть цельной или составной из нескольких секций которые собираются одна на другую. В случае составной гильзы также возможно изготовить верхнюю секцию из стали покрытой подходящим рабочим слоем. Двигатели с шатуном вышеупомянутого типа могут иметь высокоэффективные степени сжатия например 1:16-1:20 которые обуславливают высокие нагрузки на поршневые кольца.
Гильза 1 может быть смонтирована в двигателе (не показан) известным способом путем установки кольцевой нижней поверхности 2 на верхнюю плоскость коробчатой рамы или блока цилиндров двигателя после чего поршень 3 устанавливается в гильзу цилиндра а крышка цилиндра 4 размещается сверху гильзы по ее кольцевой верхней поверхности 5 и прикрепляется к верхней плоскости посредством болтов крышки (не показаны).
Гильза 1 имеет цилиндрическую внутреннюю поверхность которая образует ходовую поверхность 6 для поршневых колец 7 на поршне 3. В нижней части гильзы цилиндра расположен кольцевой ряд каналов 8 продувочного воздуха. Поршень 3 может двигаться в продольном направлении гильзы между верхней мертвой точкой (ВМТ) в которой верхняя поверхность 9 поршня размещается в отверстии в крышке цилиндра 4 и нижней мертвой точкой (НМТ) в которой верхняя поверхность поршня находится чуть ниже нижней границы каналов 8 продувочного воздуха. Ходовая поверхность 6 простирается от верхней границы 10 расположенной чуть выше ВМТ верхнего поршневого кольца до нижней границы 11 расположенной чуть ниже НМТ нижнего поршневого кольца. Волнообразный тракт 12 смазывающего масла может быть расположен на внутренней поверхности гильзы ниже верхней трети ходовой поверхности смазывающее масло на этот тракт подается через впускные отверстия 13 для смазки ходовой поверхности 6 на внутренней поверхности гильзы.
В области помеченной буквой "а" которая составляет верхние 15% длины ходовой поверхности на ходовой поверхности 6 расположено некоторое количество канавок которые открыты только по направлению внутрь гильзы цилиндра.
На фиг. 6 показана часть ходовой поверхности 6 и поршня 3 (увеличено). Поршень 3 имеет канавку 16 в которой известным способом расположено поршневое кольцо 7. Канавка 16 по высоте больше поршневого кольца 7 и во время сгорания газы распространяются сверху через зазор 17 в кольцевое пространство 18 имеющееся между дном канавки 16 и цилиндрической внутренней поверхностью поршневого кольца. Из-за высокого давления газа сгорания упругое поршневое кольцо 7 выталкивается в направлении показанном стрелкой к ходовой поверхности 6 которая покрыта пленкой 19 смазывающего масла в результате чего поршневое кольцо 7 создает уплотнение между поршнем 3 и ходовой поверхностью 6. Ходовая поверхность 6 снабжена канавкой 14 которая в данном примере представляет собой канавку с острыми кромками но может также иметь скругленные кромки 20 в месте ее сопряжения с ходовой поверхностью 6. Когда поршень перемещается вверх и вниз смазывающее масло соскабливается в канавку 14.
Высота канавки 14 значительно меньше высоты поршневого кольца 7 и соответственно при проходе канавки 14 поршневое кольцо хорошо поддерживается ходовой поверхностью 6. По второму варианту изобретения (не показан) высота канавки 14 меньше высоты поршневого кольца 7 чтобы сделать возможной некоторую утечку газа через одно или несколько поршневых колец 7.
Если точка 22 на внешней поверхности поршневого кольца 7 перегревается она охлаждается при прохождении канавок 14. Если вопреки ожиданиям между точкой 22 на поршневом кольце 7 и ходовой поверхностью 6 происходит сваривание его распространение можно предотвратить при прохождении этой точкой канавки 14 и любая более серьезная шероховатость может быть сглажена посредством одной из кромок 20 канавки.
На фиг. 2 изображена развертка верхней части гильзы цилиндра на которой для показанного варианта изобретения область "а" (см. фиг.1) имеет две группы канавок 14 на ходовой поверхности 6. Каждая группа образует ряд канавок 14 расположенных вдоль линии перпендикулярной продольной оси гильзы и размещенных с интервалами 21. Интервалы 21 образуют поддерживающую поверхность на которую опираются поршневые кольца 7 когда они перемещаются вверх или вниз через данный ряд канавок таким образом что кольца 7 не деформируются в канавках колец. Ряды канавок 14 расположены на разных уровнях друг относительно друга в продольном направлении гильзы и канавки в верхнем ряду слегка перекрывают канавки в нижнем ряду в направлении по окружности гильзы таким образом что любая линия на ходовой поверхности параллельная продольной оси гильзы пересекает одну или несколько канавок 14. Канавки равномерно распределены по окружности и имеют одинаковую длину. Для гильзы цилиндра 1 с диаметром например 700 см каждая группа может соответственно включать 11 канавок каждая длиной 125 мм высотой 2-3 мм и глубиной 2-3 мм. Если используются только две группы верхний ряд канавок может быть расположен на расстоянии приблизительно от 100 до 200 мм от верхней границы 10 ходовой поверхности а нижний ряд канавок может быть расположен на приблизительно 50 мм ниже верхнего ряда. Большее количество групп улучшает эффект предотвращения схватываний но при этом соответственно увеличивается стоимость изготовления гильзы.
На фиг. 3 показан другой вариант гильзы цилиндра согласно которому на ходовой поверхности 6 на разных уровнях друг относительно друга в продольном направлении гильзы расположены три группы канавок 14 и 15. Верхняя и нижняя группы состоят из ряда отдельных канавок 14 расположенных вдоль линии перпендикулярной продольной оси гильзы. Группа в середине состоит из ряда канавок наклоненных поочередно вверх и вниз. Канавки слегка перекрываются в направлении по окружности таким образом что любая линия на ходовой поверхности параллельная продольному направлению гильзы пересекает одну или несколько канавок 14 15.
На фиг. 4 изображена гильза цилиндра 1 с круглыми выемками в форме равномерно распределенных отверстий 23.
Согласно настоящему изобретению выражение "группа канавок" должно пониматься в широком смысле. Группа канавок может включать выемки расположенные на различных позициях в продольном направлении гильзы.
На фиг.5 изображен другой вариант настоящего изобретения в котором пять узких кольцевых канавок 24 проходят непрерывно по всей окружности ходовой поверхности и расположены в непосредственной близости одна от другой. Высота канавок составляет максимум 30% от минимальной высоты поршневых колец в значительной степени соответствуя фиг.6. Эти узкие канавки позволяют поршневому кольцу проходить канавку без такой деформации которая привела бы к удару кромки кольца о кромку канавки.
Не выходя за пределы области изобретения можно организовать канавки с различной конфигурацией например расположенные волнообразно под прямым или иным углом также возможно объединить различные варианты. Например прерывистые канавки могут быть расположены ближе друг к другу в направлении окружности гильзы если они имеют малую высоту.
Размещение канавок в верхней области ходовой поверхности подвергающейся наиболее сильному воздействию оказывает разрушительное влияние на механизм возникновения схватываний. Если в верхней области схватываний не возникает поршневые кольца практически не способны вызывать схватывания так как воздействие на кольцо уменьшается в направлении вниз по ходовой поверхности.
Гильза цилиндра (1) для двигателя внутреннего сгорания дизельного типа имеющая ходовую поверхность в форме внутренней поверхности (6) по меньшей мере один открытый внутрь масляный тракт (12) с внешней подачей (13) смазывающего масла по меньшей мере первую и вторую группы выемок которые открыты только по направлению внутрь цилиндра выполнены в форме удлиненных канавок (14 15) и расположены прерывистым образом в направлении по окружности гильзы при этом выемки относящиеся к разным группам взаимно разделены относительно друг друга в продольном направлении гильзы (1) отличающаяся тем что выемки в группах размещены в верхних 15% длины ходовой поверхности (6) а канавки расположены относительно друг друга в направлении по окружности таким образом что любая линия на ходовой поверхности (6) параллельная оси гильзы цилиндра пересекается по меньшей мере одной из канавок (14 15).
Гильза цилиндра по п. 1 отличающаяся тем что канавки (14) в группах ориентированы в направлении по окружности гильзы.
Гильза цилиндра по п. 1 или 2 отличающаяся тем что канавки (14 15) в группе расположены на одном уровне в продольном направлении гильзы (1).
Гильза цилиндра по любому одному из пп. 1-3 отличающаяся тем что канавки (14 15) в каждой группе имеют суммарную протяженность в направлении по окружности гильзы (1) максимум 80% и предпочтительно максимум 60% от окружности ходовой поверхности (6).
Гильза цилиндра по любому одному из пп. 1-4 отличающаяся тем что каждая группа включает по меньшей мере пять и предпочтительно по меньшей мере восемь канавок (14 15).
Гильза цилиндра по любому одному из пп. 1-5 отличающаяся тем что канавки (14 15) в каждой группе равномерно распределены по окружности ходовой поверхности (6).
Гильза цилиндра по любому одному из пп. 1-6 отличающаяся тем что ходовая поверхность (6) предназначена для использования ее поршневыми кольцами (7) поршня (3) причем поршневые кольца (7) имеют заранее определенную минимальную высоту а канавки (14 15) в группах имеют высоту которая меньше упомянутой минимальной высоты поршневых колец (7) и предпочтительно составляет максимум 75% от этой минимальной высоты то есть канавки имеют соответственно высоту в интервале от 1 до 3 мм.
Гильза цилиндра по любому одному из пп. 1-7 отличающаяся тем что канавки (14 15) принадлежащие к различным группам расположены друг от друга на расстоянии по меньшей мере 35 мм в продольном направлении гильзы (1).
Гильза цилиндра по любому одному из пп. 1-8 отличающаяся тем что канавки (14 15 24) имеют глубину по меньшей мере 2 мм в только что изготовленной гильзе (1).
Гильза цилиндра по любому одному из пп. 1-8 отличающаяся тем что масляный тракт (12) расположен ниже канавок (14 15 24).
Гильза цилиндра (1) для двигателя внутреннего сгорания дизельного типа где гильза (1) имеет внутреннюю поверхность которая может образовывать ходовую поверхность (6) для поршневых колец (7) поршня (3) имеющих заранее определенную минимальную высоту и где гильза также имеет по меньшей мере один открытый внутрь масляный тракт (12) с внешней подачей (13) смазывающего масла и по меньшей мере одну канавку (24) которая открыта только по направлению внутрь цилиндра отличающаяся тем что по меньшей мере одна канавка (24) проходит во всей внутренней поверхности (6) гильзы (1) и имеет высоту менее 30% от минимальной высоты поршневых колец (7) а канавки (24) имеют глубину в радиальном направлении гильзы (1) больше половины их высоты в продольном направлении гильзы (1) и расположены в верхних 15% длины ходовой поверхности (6).
Гильза цилиндра по п. 11 отличающаяся тем что каждая канавка (24) проходит по окружности ходовой поверхности (6) на постоянном уровне в продольном направлении гильзы (1).
Гильза цилиндра по п. 11 или 12 отличающаяся тем что она включает по меньшей мере три канавки (24).
Гильза цилиндра по любому одному из пп. 11-13 отличающаяся тем что в верхних 10% длины ходовой поверхности (6) расстояние между канавками (24) меньше восьмикратной высоты канавки.
Гильза цилиндра по любому одному из пп. 11 13 и 14 отличающаяся тем что каждая канавка (24) простирается вверх и вниз между границами цилиндрической секции ходовой поверхности (6) при этом высота этой секции меньше минимальной высоты поршневых колец (7).
Гильза цилиндра по любому одному из пп. 11-15 отличающаяся тем что канавки (14 15 24) имеют глубину по меньшей мере 2 мм в только что изготовленной гильзе (1).
Гильза цилиндра по любому одному из пп. 11-15 отличающаяся тем что масляный тракт (12) расположен ниже канавок (14 15 24.
Обоснование темы и описание разрабатываемой конструкции
Значительный рост всех отраслей народного хозяйства требует перемещения большого количества грузов и пассажиров. Высокая маневренность проходимость и приспособленность для работы в различных условиях делает автомобили и тракторы одними из основных средств перевозки грузов и пассажиров выполнения различных работ в промышленности и сельском хозяйстве.
Сердцем любого автомобиля или трактора является двигатель внутреннего сгорания. Именно благодаря этому агрегату автомобили и трактора выполняют свои функции. Поэтому к двигателям предъявляются жесткие требования в отношении надежности работы и долговечности а если точнее – к деталям двигателя его механизмам.
Без преувеличения поршень — главная деталь автомобильного двигателя во многом определяющая его облик. Поршень эволюционировал вместе с развитием двигателей и достиг высокой степени совершенства. Конструктивные особенности поршня должны строго соответствовать характеристикам мотора. В противном случае возможны неоправданные материальные затраты при производстве и эксплуатации двигателя и даже его преждевременная кончина.
Высказанный тезис о ключевой роли поршня в конструкции автомобильного двигателя может показаться излишне категоричным. Поэтому приведем несколько аргументов в его подтверждение. Требования к конструкции поршня определяются его функциональным назначением той ролью которую он играет в слаженно функционирующем техногенном организме называемом поршневым ДВС. Поршень — это элемент который воспринимает энергию выделяющуюся при сгорании заряда топливо-воздушной смеси. Она воздействует на поршень в виде тепла и давления газообразных продуктов. Поэтому первое что должно отличать поршень — способность продолжительно работать в условиях высоких циклически меняющихся механических нагрузок и тепловых потоков. Помимо этого поршень должен вносить свой вклад в обеспечение герметичности надпоршневого пространства препятствуя прорыву газов в картер и встречному поступлению масла из картера в камеру сгорания. Поршень должен обладать высокой износостойкостью рабочих поверхностей и низким трением при минимально возможном зазоре в цилиндре. Поршень должен должен должен Перечень того что поршень должен можно продолжить но и упомянутых требований достаточно чтобы понять насколько непросто им удовлетворить. Тем более что при этом нужно сделать главную деталь двигателя еще и максимально легкой. В противном случае Действительно представим что будет в противном случае.поршня — параметр который опосредованно отражает степень совершенства его конструкции. Для среднестатистического двигателя современного легкового автомобиля он составляет 300—350 г. Допустим что массу поршня пришлось увеличить граммов эдак на 50. Казалось бы пустяк. Теперь умножим «привес» на годовую программу производства поршней (обычно это несколько миллионов изделий) и получим несколько «лишних» вагонов стратегического металла. Кстати металла недешевого. Ведь это только у нас некоторые производители изготавливают поршни из вторсырья. На Западе для этой цели используют только первичные алюминиевые сплавы иначе невозможно гарантировать качество продукции. К сожалению это наименьшее из последствий просчетов конструкторов и технологов. Припомним что поршень совершает колебательные движения в цилиндре с частотой до 100 раз в секунду. При этом максимальная скорость его перемещения на отрезке пути длиной 70—80 мм достигает 25 мс а возникающие тысячекратные перегрузки превращают каждый лишний грамм в несколько килограммов избыточной нагрузки. Нагрузка передается на поршневой палец шатун коленчатый вал и наконец воспринимается блоком двигателя. Увеличение массы поршня однозначно отражается на массе каждой из этих деталей тем более что они работают в циклическом режиме провоцирующем усталостные явления. В результате исходные граммы «на выходе» превращаются в десятки килограммов качественного металла. Еще раз множим на объем производства двигателей приплюсуем сюда повышение расхода топлива за счет больших потерь на трение и массы мотора увеличение вредных выбросов в атмосферу прочие неучтенные последствия.
Особое место также занимает гильза. Контактируя с поршнем и газами она воспринимает тепловые нагрузки большой величины. В связи с этим к ней предъявляются серьезные требования в отношении теплопроводности термостойкости и износостойкости. Важное значение имеет масса цилиндра так как не учет этого параметра колоссально влияет на вес двигателя а значит и на себестоимость его производства.
Из всего вышеперечисленного следует что гильза и в особенности поршень – важные детали двигателя во многом определяющие его конструкцию производственные затраты экономичность и экологичность. И поэтому разработка их в данной Выпускной квалификационной работе обосновывается их важностью в общей структуре двигателя является решением требований предъявляемых к поршню и гильзе блока цилиндров.
Тепловой и динамический расчет двигателя
В соответствии с ГОСТ 305-73 для рассчитываемого двигателя принимаем дизельное топливо (для работы в летних условиях – марки Л и для работы в зимних условиях – марки З). Цетановое число топлива – не менее 45.
Средний элементарный состав дизельного топлива
Низшая теплота сгорания топлива
Параметры рабочего тела.
Теоретически необходимое количество воздуха для сгорания 1 кг топлива
Количество свежего заряда:
Количество отдельных компонентов продуктов сгорания при полном сгорании топлива:
Общее количество продуктов сгорания:
Коэффициент молекулярного изменения свежей смеси:
Параметры окружающей среды и остаточные газы:
Атмосферные условия:
Температуру остаточных газов примем .
Давление остаточных газов примем .
Температура подогрева свежего заряда:
Рассчитываемый двигатель не имеет специального устройства для подогрева свежего заряда. Однако естественный подогрев заряда в дизеле без наддува может достигать а при наддуве за счет уменьшения температурного перепада между деталями двигателя и температурой наддувочного воздуха величина подогрева сокращается. Поэтому примем для дизеля без наддува .
Плотность газов на впуске:
Потери давления на впуске в двигателе:
где приняты в соответствии со скоростным режимом двигателя и с учетом небольших гидравлических сопротивлений во впускной системе дизеля.
Давление в конце впуска:
Коэффициент остаточных газов:
Температура в конце впуска:
Коэффициент наполнения:
Средние показатели адиабаты и политропы сжатия:
При работе дизеля на номинальном режиме можно с достаточной степенью точности принять показатель политропы сжатия приблизительно равным показателю адиабаты который определяется по номограмме: для данного дизеля при и .
Давление в конце сжатия:
Температура в конце сжатия:
Средняя мольная теплоемкость в конце сжатия:
б) остаточных газов (определяем по таблице методом интерполяции)
Коэффициент молекулярного изменения рабочей смеси:
Теплота сгорания рабочей смеси:
Средняя мольная теплоемкость продуктов сгорания:
Коэффициент использования теплоты для современных дизелей с неразделенными камерами сгорания и хорошо организованным струйным смесеобразованием можно принять для двигателя без наддува .
Степень повышения давления примем .
Температуру в конце видимого процесса сгорания определим по уравнению сгорания:
Максимальное давление сгорания:
Степень предварительного расширения:
Степень последующего расширения:
Принимаем показатель политропы расширения .
Давление в конце расширения:
Температура в конце расширения:
Проверка ранее принятой температуры остаточных газов:
Индикаторные параметры рабочего цикла.
Теоретическое среднее индикаторное давление:
Среднее индикаторное давление действительного цикла:
где коэффициент полноты диаграммы принят .
Индикаторный удельный расход топлива:
Эффективные показатели двигателя.
Среднее давление механических потерь:
где средняя скорость поршня предварительно принята =102 мс .
Среднее эффективное давление:
Механический КПД двигателя:
Эффективный удельный расход топлива:
Основные размеры цилиндра и показатели двигателя.
Рабочий объем одного цилиндра:
где - число цилиндров.
Диаметр и ход поршня дизеля как правило выполняются с отношением хода поршня к диаметру цилиндра . Однако с уменьшением для дизеля так же как и для карбюраторного двигателя снижает скорость поршня и повышает .
По окончательно принятым значениям D и S определяем основные параметры и показатели двигателя:
эффективная мощность
эффективный крутящий момент
часовой расход топлива
среднюю скорость поршня
что достаточно близко к ранее принятому значению:
Построение индикаторной диаграммы дизеля.
Приведенные величины:
рабочего объема цилиндра
объема камеры сгорания
Максимальная высота диаграммы (ордината точек и ):
Положение по оси абсцисс:
Ординаты характерных точек:
Построение политроп сжатия и расширения проводим графическим способом Бауэра:
а) для луча ОС принимаем угол ;
в) используя лучи ОD и ОС строим политропу сжатия начиная с точки С;
д) используя лучи ОЕ и ОС строим политропу расширения начиная с точки Z.
Выбираем величину безразмерного геометрического параметра КШМ .
Силу давления газов на поршень подсчитываем по формуле
Результаты расчета силы сведены в табл. 1.
Определение масс деталей поршневой и шатунной групп.
Двигатель дизельный . В качестве материала выбираем алюминиевый сплав. Из соответствующей таблицы выбираем .Тогда масса поршня
где - площадь поршня.
Из соответствующей таблицы выбираем . Тогда масса шатуна
Часть массы шатуна приведенная к оси поршневого пальца
Часть массы шатуна приведенная к кривошипу
Сила инерции возвратно-поступательно движущихся масс КШМ
где - масса части шатуна и поршневого комплекта совершающая возвратно-поступательное движение; - радиус кривошипа; .
Суммарная сила действующая на поршень вдоль оси цилиндра вычисляется алгебраическим сложением газовой силы и инерции возвратно-поступательно движущихся масс :
Результаты вычислений силы сведены в табл. 1.
Вычисление нормальной силы действующей перпендикулярно оси цилиндра и воспринимаемой стенками цилиндра производится по формуле
где значение силы берется из табл. 1 а тригонометрической функции из соответствующей таблицы.
Результаты вычислений силы сведены в табл. 2.
Сила действующая вдоль шатуна определяется по формуле
где значение выражения при берется из соответствующей таблицы.
Тангенциальная сила направленная к окружности радиуса кривошипа вычисляется по формуле
где значение тригонометрического многочлена при берется из соответствующей таблицы.
Масштабные коэффициенты:
Расчет разрабатываемых узлов
Расчет поршня дизеля
Рис. 8. Основные конструктивные размеры поршня
На основании данных расчетов (теплового и динамического) диаметр цилиндра ход поршня максимальное давление сгорания при площадь поршня наибольшая нормальная сила при масса поршневой группы частота вращения .
В соответствии с существующими аналогичными двигателями и с учетом соотношений параметров поршня от диаметра принимаем: высоту поршня высоту юбки поршня радиальную толщину кольца радиальный зазор кольца в канавке поршня толщину стенки головки поршня толщину верхней кольцевой перемычки число и диаметр масляных каналов в поршне и . Материал поршня – алюминиевый сплав ; материал гильзы цилиндра – чугун .
Напряжение сжатия в сечении х-х:
максимальная сжимающая сила
Напряжение разрыва в сечении х-х:
максимальная угловая скорость холостого хода
масса головки поршня с кольцами расположенными выше сечения х-х
максимальная разрывающая сила
Напряжения в верхней кольцевой перемычке:
Удельные давления поршня на стенку цилиндра:
Диаметры головки и юбки поршня:
Диаметральные зазоры в горячем состоянии:
где и приняты с учетом водяного охлаждения двигателя.
Расчет гильзы цилиндра дизеля
На основании проведенного теплового расчета имеем: диаметр цилиндра ; максимальное давление в конце сгорания при ; материал гильзы цилиндра – чугун; ; и .
Толщину стенки гильзы цилиндра выбирают конструктивно: .
Расчетная толщина стенки гильзы
где - допустимое напряжение на растяжение для чугуна.
Толщину стенки гильзы выбирают с некоторым запасом прочности так как .
Напряжение растяжения в гильзе от действия максимального давления газов
Температурные напряжения в гильзе
где - температурный перепад между внутренней и наружной поверхностью гильзы.
Суммарные напряжения в гильзе от давления газов и перепада температур:
на наружной поверхности
на внутренней поверхности
Расчет поршневого пальца дизеля
Основные данные для расчета приведены в тепловом и динамическом расчетах. Кроме того принимаем: наружный диаметр пальца внутренний диаметр пальца длину пальца длину втулки шатуна расстояние между торцами бобышек . Материал поршневого пальца – сталь 12ХН3А . Палец плавающего типа.
Расчетная сила действующая на поршневой палец:
Удельное давление пальца на втулку поршневой головки шатуна
Удельное давление пальца на бобышки
Напряжение изгиба в среднем сечении пальца
Касательные напряжения среза в сечениях между бобышками и головкой шатуна
Наибольшее увеличение горизонтального диаметра пальца при овализации
Напряжения овализации на внешней поверхности пальца:
в горизонтальной плоскости ()
в вертикальной плоскости ()
Напряжения овализации на внутренней поверхности пальца:
Определить (расчет стоимости поршня):
Стоимость основных фондов и величину амортизации.
Расход материалов топлива энергии инструментов.
Фонды заработной платы.
Комплексные и прочие денежные расходы.
Себестоимость единицы продукции.
Исходные данные: тип производства – серийный.
План годового выпуска продукции: 400000(алюминий).
Трудоемкость по отдельным видам работы: 1600 нчас (норма час).
Ожидаемое выполнение норм (коэффициент выполнения норм): 105 – 13 (принимаем 12).
Годовой действительный (эффективный) фонд времени работы оборудования в плановом периоде: металлорежущие при двусменной работе – 4020 час.
Расчет стоимости основных фондов и величины амортизации.
Расчет потребного количества оборудования
- количество технологического оборудования;
- трудоемкость изделий (с учетом обслуживания машин);
- годовой объем выпуска изделий;
- годовой действительный фонд времени работы оборудования;
- коэффициент выполнения норм;
Мощность электродвига-
Рассчитать количество:
и средний коэффициент загрузки оборудования
- расчетное количество оборудования;
- принятое количество оборудования.
Ведомость потребного количества основного оборудования для механического цеха
Ст-сть монтажа (10%)
Стоимость ценного и долгослужащего инструмента – до 10 % от стоимости оборудования.
Стоимость производственного и хозяйственного инвентаря принимается в размере 1-5 % первоначальной стоимости оборудования и здания.
Стоимость контрольно-измерительных приборов (КИП) можно принять 7000 сум на один станок.
Определяем стоимость зданий и сооружений.
Стоимость зданий производственного и вспомогательного назначения рассчитывается исходя из стоимости 1 . 1 производственного здания обходится в 125000 сум вспомогательная площадь составляет 20 % от основной площади. Удельная площадь на 1 станок (принимаем) 12 .
Основные фонды и их амортизация
-хозяйственный инвентарь
Расчет стоимости материалов и энергоносителей.
Затраты по основным материалам на программу
сум где - норма расхода материала кг;
- цена материала за 1 кг сум;
- масса возвратных отходов (20 %) кг;
- цена возвратных отходов (40 – 50 % от цены материала)сум.
Потребность во вспомогательных материалах определяется исходя из установленных норм. Примерные затраты на один станок – 50 тыс. сум в год.
Годовой расход электроэнергии определяется по формуле
- действительный годовой фонд времени работы оборудования;
- коэффициент загрузки оборудования по времени (расчетный по проекту);
- коэффициент спроса учитывающий недогрузку по мощности как за основное технологическое время (025);
- установленная мощность оборудования.
Расход электроэнергии для освещения определяется по формуле
- средний расход в 15 Втчас на ;
- площадь производственных и бытовых помещений;
- время горения электросветильников в год (2300 часов).
Стоимость электроэнергии за 1 604 сума.
Расчет количества сжатого воздуха:
Примерный расход воздуха 012 на 1 деталь.
Средняя стоимость 1 воздуха 1500 сум.
Средний расход воды на 1 металлорежущий станок – 06 л в час.
Стоимость 1 воды 600 сум.
Расчет расхода воды на бытовые нужды ведется на основе следующих данных:
А) для хозяйственно-санитарных нужд – 25 л на каждого работающего в смену (основные и вспомогательные рабочие).
Б) для душевых – 40 л на каждого работающего.
Число рабочих дней в году – 230.
На отопление примерно 047 т 1 .
Расход пара для подогрева в душевых от 07 до 1 т в год на работающего.
Стоимость 1 т пара – 644 сума.
Расчет численности персонала и фондов зплаты.
Количество основных рабочих
- число производственных (основных) рабочих;
- годовой действительный фонд времени работы в часах – 3680 ч.;
- трудоемкость одного изделия;
- коэффициент выполнения норм.
Количество вспомогательных рабочих – 40 % от числа производственных рабочих.
Годовой фонд заработной платы производственных рабочих по сдельным расценкам определяется:
- часовая тарифная ставка среднего разряда работы 850 сум. Доплаты и премии составляют 25 % от тарифного фонда заработной платы основных рабочих.
Фонд заработной платы вспомогательных рабочих определяется по формуле:
- часовая тарифная ставка среднего разряда работы 770 сум;
- количество вспомогательных рабочих;
- коэффициент приработка 20 % (12).
Расчет численности ИТР СКП МОП.
% от числа осн. и вспомогат. рабочих
Ведомость фондов зпл ИТР СКП МОП
Среднемесячная зпл персонала цеха
Категория работников
Производственные рабочие
Вспомогательные рабочие
Смета цеховых расходов
Расчет по разделу пособия
Амортизация оборудования
ценного и долгослужащего
Эксплуатация оборудования.
Затраты на вспомогательные материалы
ээнергию сжатый воздух воду.
Текущий ремонт оборудования
ценного и долгослужащего
На ед. шлифовального токарного станков
000 сум в год фрез. и протяж. 24500 сум
в год и др. – 18500 сум в год. Ремонт цен-
ного инструмента принимается 10-20 % его
первоначальной стоимости.
Износ малоценных и быстроиз-
нашивающихся инструментов и
Составляет 2040 тыс. сум на одного рабо-
Зарплаты осн. и доп.:
Отчисления на соц. страхов-е.
% от основной и дополнительной зпл.
Амортизация зданий сооруже-
Содержание зданий сооруже-
Затраты ээнергии на освещение затраты
на воду для бытовых нужд пар для отоп-
ления. С-ть вспомогательных материалов
% от стоимости зданий. Расходы на содержание инвентаря – 1 % от первона-
чальной стоимости оборудования и зданий.
Текущий ремонт зданий сору-
% от превоначальной их стоимости.
Затраты на инновационную де-
0-400 тыс. сум на олного работающего
-80 тыс. сум на одного рабочего.
Итого цеховых расходов
Калькуляция себестоимости (наименование выпускаемого изделия детали)
Основная и дополнительная зпл
производственных и вспомогат. рабочих
Затраты на соц. страхование
% от осн. и доп. зпл
производственных рабочих
Производств. сстоимость
Внепроизводственные расходы
% от производственной
Итого полная сстоимость
Плановые накопления (прибыль)
НДС (налог на добавленную стоимость 20 %)
Цена одного поршня : 5143639936400000 = 1286 тыс. сум.
Безопасность жизнедеятельности
Размещение санитарно-бытовых помещений согласно нормативным требованиям
К вспомогательным зданиям и помещениям промышленных предприятий относятся помещения: санитарно-бытовые общественного питания здравоохранения культурного обслуживания конструкторских бюро учебных занятий общественных организаций и т. п. Размещать их рекомендуется в пристройках к производственным зданиям.
Вспомогательные помещения различного назначения следует размещать в одном здании при условии что это не противоречит санитарным нормам и эстетическим требованиям. Эти помещения должны иметь улучшенную отделку и содержаться в хорошем состоянии.
В группу санитарно-бытовых помещений входят: гардеробные; душевые; уборные; умывальные; курительные комнаты; помещения для обезвреживания сушки и обеспыливания рабочей одежды; помещения для личной гигиены женщин; помещения для кормления грудных детей и помещения для обогревания рабочих. При размещении бытовых помещений предназначенных для обслуживания работающих в отапливаемых производственных зданиях в отдельно стоящих зданиях необходимо устройство теплых переходов между этими зданиями.
Состав и устройство санитарно-бытовых помещений зависят от группы производственного процесса. Группы производственного процесса установлены СНиП II-92-76 в зависимости от санитарной характеристики производственных процессов.
Гардеробные для хранения домашней и рабочей одежды уборные умывальные и душевые выполняются отдельными для мужчин и женщин. Гардеробные уличной одежды предусматриваются общими.
Душевые размещают в помещениях смежных с гардеробными. Расположение душевых кабин у наружных стен здания не допускается.
Уборные размещают так чтобы расстояние до них от рабочих мест находящихся в зданиях было не более 75 м а от рабочих мест на территории предприятия – не более 150 м. Уборные в многоэтажных производственных зданиях должны быть на каждом этаже.
Умывальные размещают в помещениях смежных с гардеробными специальной одежды или в помещениях общих гардеробных.
Курительные предусматриваются когда курение в производственных помещениях по условиям производства не допускается а также при объеме производственного помещения на одного работающего менее .
Помещения для стирки химической очистки сушки обезвреживания и обеспыливания рабочей одежды предусматриваются в зависимости от вида производства. Они должны быть обособленными и при самообслуживании располагаться смежно с гардеробными для хранения рабочей одежды.
Меры по предупреждению вредных выделений паров газов и пыли в проектируемом цехе
Важнейшее значение для нормальной жизнедеятельности человека имеет наличие чистого воздуха необходимого химического состава и имеющего оптимальные температуру влажность и скорость движения.
В производственных помещениях при работе станков машин оборудования от технологического процесса и нахождения работающих людей могут выделяться избыточные количества тепла и влаги а также загрязняющих воздух газов паров пыли.
В механических цехах процессы обточки шлифовки полировки сопровождаются пылевыделением интенсивность которого зависит от вида обрабатываемого металла используемого абразивного или другого инструмента сухого или влажного метода обработки наличия и конструкции пылеотсасывающих устройств. При обработке металлов используются токарные фрезерные сверлильные точильные шлифовальные полировальные и другие станки при работе которых применяются смазочно0охлаждающие жидкости (СОЖ). В результате механического разбрызгивания и испарения СОЖ так как температура режущего инструмента орошаемого СОЖ может достигать нескольких сот градусов ее компоненты поступают в воздух в виде масляных и иных аэрозолей а также сложных парогазовых смесей. Вдыхание их может быть причиной раздражающего влияния на органы дыхания легочную ткань а также неблагоприятного воздействия на др. системы организма.
Санитарными нормами предусмотрено технологические процессы и производственное оборудование принимать такими чтобы отсутствовали или были минимальными выделения в воздух помещений в атмосферу и в сточные воды вредных или неприятно пахнущих веществ тепла и влаги а также пыли.
Осуществление необходимых мероприятий надлежит проводить заменяя вредные вещества в производстве безвредными или менее вредными; сухие способы переработки пылящих материалов – мокрыми; пламенный нагрев – электрическим; твердое и жидкое топливо – газообразным а также используя герметизацию и максимальное уплотнение стыков и соединений в технологическом оборудовании и трубопроводах – для предотвращения выделения вредностей в процессе производства; тепловую изоляцию нагретых поверхностей оборудования воздухопроводов и трубопроводов; укрытие погрузочных емкостей механического транспорта; применяя гидропневмотранспорт при транспортировке пылящих материалов.
Снижение концентрации пыли до допустимых величин можно производить различными способами. Борьбе с пылью следует уделять внимание уже на стадии проектирования производственных помещений конструирования технологического оборудования станков и инструмента с тем чтобы они обеспечивали беспыльность технологических процессов.
При проектировании и размещении особо пыльных цехов следует предусматривать их изоляцию от непыльных цехов. В пыльных цехах стены рекомендуется окрашивать масляной краской а полы делать гладкими не впитывающими пыль. Уменьшению пылеобразования может способствовать увлажнение воздуха.
Автоматизация технологических процессов связанных с пылевыделением позволит рабочему управлять процессом с пульта расположенного вне зоны пылеобразования.
Одним из основных мероприятий по оптимизации параметров микроклимата и состава воздуха в производственных помещениях является обеспечение надлежащего воздухообмена.
Общеобменная вентиляция должна устраиваться таким образом чтобы исключалась возможность поступления воздуха из помещений с большим пылеобразованием в помещения с меньшим выделением пыли.
Создание в рабочей зоне надлежащих метеорологических условий благоприятно воздействует на организм способствует хорошему самочувствию повышает безопасность работы обеспечивает высокую работоспособность.
Промышленная вентиляция
Вентиляция – это организованный воздухообмен в помещениях.
Вентиляция должна обеспечивать условия отвечающие требованиям технологического процесса сохранения оборудования и строительных конструкций здания. Устройство вентиляции в производственных и вспомогательных помещениях промышленных предприятий является обязательным.
Вентиляция по способу перемещения воздуха подразделяется на естественную и механическую. Возможно их сочетание – смешанная вентиляция.
Естественная вентиляция подразделяется на аэрацию и проветривание.
Механическая вентиляция в зависимости от направления воздушных потоков бывает вытяжной (отсасывающей) приточной (нагнетательной) приточно-вытяжной.
По характеру охвата помещения различают общеобменную и местную (локализующую) вентиляцию; возможно также сочетание этих двух видов вентиляции.
По времени действия – постоянно действующую и аварийную.
Естественная вентиляция осуществляется под влиянием разности температур и весов воздуха производственных помещений а также ветрового побуждения.
Проветривание помещений проводят открывая форточки и фрамуги в окнах и световых фонарях; это периодически дейчтвующая естественная вентиляция.
Аэрация – это организованная естественная вентиляция выполняющая роль общеобменной вентиляции производственных помещений в заданных параметрах.
Нормального и эффективного действия аэрации можно достигнуть лишь при соответствующем расположении здания. Здание необходимо располагать перпендикулярно направлению господствующих ветров или под углом к ним.
В производственных помещениях где допустима небольшая кратность воздухообмена устанавливают вытяжные трубы или шахты наружная часть которых располагается над крышей. В целях повышения эффективности воздухообмена через вытяжные трубы или шахты на них устанавливают дефлекторы.
Дефлекторы обеспечивая удаление воздуха из помещения за счет теплового напора дополнительно увеличивают эффект вытяжки воздуха из помещения за счет действия силы ветра.
Инфильтрация относится к неорганизованному воздухообмену происходящему через неплотности в притворах окон дверей и через поры материалов конструктивных элементов зданий.
Механическая вентиляция более совершенна по сравнению с естественной вентиляцией но требует значительных капитальных и эксплуатационных затрат.
Механическая вентиляция обеспечивает забор поступающего воздуха из мест где он наиболее чист; допускает обработку воздуха – его подогрев увлажнение или подсушку; позволяет подводить воздух к любому рабочему месту или оборудованию а также и удалять его из любых мест с очисткой.
Приточная вентиляция обеспечивает подачу в производственные помещения чистого воздуха. При этом загрязненный воздух удаляется через фрамуги дефлекторы или вентиляционные воздуховоды не только вследствие теплового напора ветрового побуждения но и благодаря подпору создаваемому приточной вентиляцией.
Свежий приточный воздух по воздухопроводам направляют в различные зоны производственного помещения и через распределительные насадки подают в рабочую зону.
Вытяжная вентиляция может применяться в производственных помещениях в которых отсутствуют вредные выделения и необходима малая кратность воздухообмена во вспомогательных и бытовых помещениях на складах. В этом случае свежий воздух поступает через форточки путем инфильтрации через стены потолок неплотности в дверях и окнах а также из смежных помещений. Последнее возможно когда в смежных помещениях отсутствуют вредные выделения.
Приточно-вытяжная вентиляция применяется во всех производственных помещениях когда требуется повышенный и особо надежный обмен воздуха.
При этом виде вентиляции целесообразно в производственных помещениях с малыми выделениями вредностей создавать небольшой подпор воздуха а в смежных с ними помещениях со значительными выделениями вредностей такого подпора (избыточного давления) воздуха не создавать. Этим будет обеспечена своеобразная изоляция производственных помещений с малыми выделениями вредностей от проникновения в них загрязненного воздуха из смежных помещений.
Смешанную вентиляцию применяют когда в дополнение к механической допустимо частичное использование естественной вентиляции для притока или удаления воздуха.
Местная вентиляция предназначена для удаления выделяемых вредностей непосредственно в месте их образования для предотвращения распространения их в воздухе всего производственного помещения а также для уменьшения вредных выделений в воздушную среду на отдельных участках производственных помещений. Преимуществом местной вытяжной вентиляции является то что отсос минимальных объемов воздуха с большим содержанием вредных примесей в нем предупреждает загрязнение воздуха всего помещения.
Аварийная вентиляция устраивается в производственных помещениях в воздух которых возможно внезапное поступление больших количеств вредных или взрывоопасных газов. Такие поступления возможны в газогенераторных и компрессорных помещениях при выполнении некоторых производственных процессов.
Кондиционирование воздуха создает и автоматически поддерживает внутри производственных помещений независимо от наружных метеорологических условий заданную температуру относительную влажность чистоту и скорость движения воздуха.
Правильно выбранная система вентиляции должна очищать помещение от пыли газов и паров выделяющихся при производственных процессах.
Цех для механической обработки поршней размещается в одноэтажном корпусе высотой 5м.
Общая установленная мощность станков .
Обработка ведется с эмульсионным охлаждением.
Максимальное количество рабочих чел.
Требуется рассчитать приточную общеобменную механическую вентиляцию. Вредными выделениями считаются тепло и влаговыделения от работающих станков и людей. Количество влаги выделяющееся от работающих станков при охлаждении определяется из расчета 150 гр на 1 кВт установленной мощности. Количество влаги выделенной людьми обычно принимается 160 грч на 1 человека.
Общее количество влаги выделяющейся за час станками и рабочими:
Определим количество тепловыделений станков:
Определим количество тепла выделенного рабочими:
Общее количество тепла выделенного станками и рабочими:
Определим требуемый воздухообмен:
где m – высотный коэффициент помещения (до 5 м m = 06 08) - абсолютная влажность воздуха (=7 8 гркг) =1 гркг.
Вывод: выделяющаяся влага компенсируется теплопотерями и поэтому проведение дальнейшего расчета не требуется.
Расчет по теплообмену ведем по тепловыделениям .
При температуре воздуха снаружи происходит превышение на .
Радиационное тепло определяется по таблице: .
Для таких цехов допускается в летний период повышение температуры рабочей зоны не более относительно наружной температуры:
В верхних слоях помещения происходит повышение температуры:
Определим количество приточного воздуха:
Кратность обмена воздуха: .
Вывод: за 1 ч надо обновлять воздух 881 раза.
Метеорологические условия
Микроклимат (метеорологические условия) на рабочем месте в производственных помещениях определяется температурой воздуха относительной влажностью скоростью движения воздуха барометрическим давлением и интенсивностью теплового излучения от нагретых поверхностей.
Рабочей зоной считается пространство высотой до 2 м над уровнем пола или площадки на котором находятся места постоянного или временного пребывания работающих. Постоянным рабочим местом считается место на котором работающий находится более 50 % своего рабочего времени или более 2 ч непрерывно.
В нормативах при определении метеорологических условий введено понятие микроклимат производственных помещений – это климат внутренней среды этих помещений который определяется действующими на организм человека сочетаниями температуры влажности и скорости движения воздуха а также температуры окружающих поверхностей.
Нормативы определены раздельно для оптимальных и допустимых микроклиматических условий. Оптимальные микроклиматические условия – это сочетания параметров микроклимата которые при длительном и систематическом воздействии на человека обеспечивают сохранение нормального функционального и теплового состояния организма без напряжения реакций терморегуляции. Они обеспечивают ощущение теплового комфорта и создают предпосылки для высокого уровня работоспособности.
Допустимые микроклиматические условия – это сочетание параметров микроклимата которые при длительном и систематическом воздействии на человека могут вызвать преходящие и быстро нормализирующиеся изменения функционального и теплового состояния организма и напряжение реакций терморегуляции не выходящие за пределы физиологических приспособительных возможностей. При этом не возникают изменения состояния здоровья но могут наблюдаться дискомфортные теплоощущения ухудшение самочувствия и понижение работоспособности.
Благоприятные (комфортные) метеорологические условия на производстве являются важным фактором в обеспечении высокой производительности труда и в профилактике заболеваний. При несоблюдении гигиенических норм микроклимата снижается работоспособность человека возрастает опасность возникновения травм и ряда заболеваний в том числе профессиональных.
Мероприятия по борьбе с производственным шумом и вибрацией
Мероприятия по борьбе с шумом
Шумом принято называть любой нежелательный звук воспринимаемый органом слуха человека. Шум представляет собой беспорядочное сочетание звуков различной интенсивности и частоты.
Борьбу с шумом следует начинать на этапе проектирования предприятий или при его реконструкции.
Планируя территорию предприятия следует предусматривать рациональное размещение отдельных зданий и цехов внутри зданий. Производства создающие уровень звукового давления более 90 дБ должны размещаться в изолированных зданиях или помещениях. Для изоляции фундаментов таких зданий устраивают так наз. акустические разрывы – идущие по всему периметру щели заполненные изолирующим материалом; между “шумными цехами” устраивают свободные зоны которые для большей эффективности озеленяют так как листва хорошо поглощает шум. Озелененная зона шириной в 50 м может значительно снизить уровень шума.
При планировке цехов и участков внутри здания необходимо объединять станки и оборудование по степени их шумности. При этом размещать их желательно в отдельных помещениях или устраивать вокруг таких зон специальные ограждения. Располагать помещения с большим шумообразованием надо с подветренной стороны.
Наиболее эффективным мероприятием по борьбе с шумом надо считать снижение его в источниках образования т. е. непосредственно в агрегатах машинах механизмах и т. п.
Для этого могут быть использованы след. мероприятия:
Замена ударных процессов и механизмов безударными. Например вместо оборудования с кривошипным или эксцентриковым приводом применение гидропривода замена ударной клепки сваркой рихтовки – вальцовкой и т. п.
Замена возвратно-поступательного движения вращательным желательнее равномерным.
Замена зубчатых и цепных передач на клино- и зубчатоременные.
Замена прямозубых шестерен косозубыми и шевронными.
Замена металлических деталей пластмассовыми или изготовление их из других “не звучащих” материалов. Соединение соударяемых и трущихся металлических деталей с пластмассовыми например стальных шестерен в паре с текстолитовыми или капроновыми.
Размещение зубчатых зацеплений в масляных ваннах. Применение принудительной смазки в сочленениях для предотвращения их износа и возникновения шума от трения.
Применение прокладочных материалов и упругих вставок в соединениях для уменьшения или исключения передачи колебаний от одной части агрегата к другой.
Уменьшение интенсивности вибраций поверхностей создающих шум (корпусов кожухов крышек и т. п.) путем обеспечения их жесткости и надежности крепления. Возможно также их покрытие звукопоглощающими материалами.
Применение в бункерах и др. таре выполненной из металла и предназначенной для приема от станков и оборудования заготовок и деталей резиновых прокладок на днище.
Большое значение имеет своевременное профилактическое обслуживание станков и оборудования при котором обеспечивается надежность креплений и правильная регулировка сочленений.
Для борьбы с шумом на пути его распространения устанавливают звукоизолирующие и звукопоглощающие конструкции а также глушители аэродинамических шумов.
Звукоизоляцию осуществляют устраивая ограждающие конструкции для снижения уровня шума в смежных помещениях.
В основу звукоизоляции положен принцип отражения – большая часть падающей на ограждение звуковой энергии отражается и лишь ее небольшая доля (около 11000 и менее) проникает через ограждение. Звукоизолирующая конструкция должна не пропускать звук из шумного помещения.
Звукопоглощение основано на том что звуковые волны падающие на преграды поглощаются в большей или меньшей степени. Чем больше звуковых волн будет поглощаться тем меньше их отразится и это приведет к снижению общего шума в помещении.
Большинство материалов применяемых в строительстве (бетон кирпич стеклоблоки и т. п.) поглощает меньше 2 % падающей на их поверхность звуковой энергии отражая остальные 98 % обратно в помещение. Уровень шума от источника расположенного в помещении на 5-15 дБ больше шума создаваемого этим же источником на открытом воздухе.
Применение звукопоглощающих материалов и конструкций с высокими коэффициентами звукопоглощения для стен и потолка позволяет уменьшить долю шума создаваемого за счет отражения и тем самым уменьшить общий шум в помещении.
Рис. 9. Акустическая обработка помещений:
а – звукопоглощающие облицовки; б – штучные звукопоглотители; 1 – защитный перфорированный слой; 2 – защитная стеклоткань; 3 – звукопоглощающий материал; 4 – стена или потолок; 5 – воздушный промежуток; 6 – плита из звукопоглощающего материала.
Мероприятия по устранению вибраций
Мероприятия по борьбе с производственными вибрациями должны намечаться при проектировании зданий конструировании машин и агрегатов при строительстве промышленных зданий изготовлении станков и оборудования а также при их эксплуатации.
Общие мероприятия по борьбе с вредным воздействием вибрации могут производиться по трем направлениям: инженерно-техническому организационному и лечебно-профилактическому.
Инженерно-технические мероприятия включают: внедрение средств автоматизации и прогрессивной технологии исключающих контакт работающих с вибрацией; изменение конструктивных параметров машин технологического оборудования и механизированного инструмента.
Организационные мероприятия включают контроль за монтажом оборудования на производственных площадках; своевременным и качественным проведением планово-принудительного обслуживания и ремонта; выполнением правил технической эксплуатации машин и агрегатов.
К средствам защиты отнесены след. устройства: оградительные виброизолирующие виброгасящие и вибропоглощающие а также средства автоматического контроля сигнализации дистанционного управления.
Лечебно-профилактические мероприятия обеспечивают необходимый микроклиматический режим и комплекс физиотерапевтических процедур (водные ванны массаж гимнастика и ультрафиолетовое облучение).
Виброизолирующие устройства предназначены для уменьшения уровня вибраций передаваемых от их источника на тело работающего. Выполняется это путем введения в колебательную систему промежуточной упругой связи. При стационарной установке оборудования это можно выполнить соответствующим устройством фундаментов или использованием виброизолирующих опор.
Вибропоглощение. В технологическом оборудовании существенное значение имеет устранение резонансных режимов и вибродемпфирование способствующее уменьшению уровня вибраций посредством превращения энергии механических колебаний возникающих в оборудовании в другие виды энергии.
Такое превращение может быть выполнено путем: а) использования конструктивных материалов с большим внутренним трением; б) нанесения на поверхность изделия слоя упруговязких материалов обладающих большим внутренним трением; в) использования поверхностного трения при введении в конструкцию дополнительного поглощающего элемента или покрытия увеличивающего активные потери в системе; г) перевода механической колебательной энергии в энергию токов Фуко или электромагнитного поля.
Автоматический контроль и сигнализация. Параметры вибрации не постоянны они могут значительно меняться в процессе работы на одном и том же оборудовании. Определить эти изменения путем ощущений весьма затруднительно вследствие чего возникает необходимость автоматического контроля и сигнализации.
Дистанционное управление является перспективным и должно получить большое применение. Оно исключает необходимость постоянного нахождения работающего в зоне вибрирующих машин и оборудования а периодическое нахождение в этой зоне менее опасно для обслуживающего персонала.
Для защиты рабочего от воздействия общей вибрации применяют обувь с амортизирующими подошвами.
Значительное внимание уделено защите рук от вибраций. Для этого могут применяться рукавицы с упругодемпфирующими вкладышами; рукавицы и перчатки с мягкими наладонниками; упругодемпфирующие прокладки и пластины для обхвата вибрирующих рукояток и деталей и т. п.
Освещение обеспечивающее нормальные зрительные условия работы является важным фактором в организации производства. В процессе работы человеку приходится различать всевозможные предметы материалы детали в машиностроении — структуру материала чистоту обработки поверхности детали деление шкалы измерительного инструмента при замере точности обработки и т. п.
При недостаточной или значительно изменяющейся освещенности или условий видимости органам зрения приходится приспосабливаться; это возможно благодаря свойствам глаз — аккомодации и адаптации.
Аккомодация — это способность глаза приспосабливаться к ясному видению предметов находящихся от него на различных расстояниях.
Адаптация — это способность глаза изменять чувствительность при изменении условий освещения.
Естественное освещение используется в дневное время суток. Оно обеспечивает хорошую освещенность равномерность; вследствие высокой диффузности (рассеивания) благоприятно действует на зрение и экономично. Помимо этого солнечный свет оказывает биологически оздоровляющее и тонизирующее воздействие на человека.
Первичным источником естественного (дневного) света является Солнце излучающее в мировое пространство мощный поток световой энергии. Эта энергия достигает поверхности Земли в виде прямого или рассеянного (диффузного) света. В светотехнических расчетах естественного освещения помещений учитывается только диффузный свет.
Величина естественной наружной освещенности имеет большие колебания как по временам года так и по часам суток. Значительные колебания величин естественной освещенности в течение дня зависят не только от времени суток но и от перемены облачности.
Таким образом источники естественного света обладают особенностями которые создают резко изменяющиеся условия освещения. Задача проектирования естественного освещения помещений сводится к рациональному использованию имеющихся в данном районе природных световых ресурсов.
Естественное освещение помещений осуществляется через световые проемы и может быть выполнено в виде бокового верхнего или комбинированного.
Боковое — осуществляется через окна в наружных стенах здания; верхнее — через световые фонари располагаемые в перекрытиях и имеющие различные формы и размеры; комбинированное — через окна и световые фонари.
В темное время суток а также при недостаточном естественном освещении необходимо применять искусственное освещение как в помещениях так и на открытых площадках проездах и т. п. В связи с этим качеству искусственного освещения придают серьезное значение. Электрический свет не только заменяет естественное освещение но и облегчает труд снижает усталость. На качество освещения помещения оказывает влияние световой поток лампы а также тип и цвет светильника цвет окраски помещения и оборудования их состояние (свежесть окраски и запыленность).
Искусственное освещение по способу расположения источников света подразделяется на общее местное и комбинированное (общее + местное). В производственных помещениях одно местное освещение использовать не разрешается.
В осветительных установках промышленных предприятий применяют лампы накаливания и газоразрядные источники света. Основные характеристики ламп: номинальное напряжение электрическая мощность световой поток световая отдача и срок службы.
Лампы накаливания основаны на способности нагретого до высокой температуры тела (нити из тугоплавкого металла) излучать видимый свет а газоразрядные — на принципе люминесценции.
В лампе накаливания световой поток зависит от потребляемой электрической мощности и температуры вольфрамовой нити помещенной в стеклянную колбу наполняемую при изготовлении инертным газом: аргоном ксеноном криптоном и их смесями. Это обеспечивает повышение температуры вольфрамовой нити и уменьшает ее распыление.
Рис. 10. Основные типы осветительных приборов:
а – рассеянного света; б – прямого света “Универсал”; в – прямого света “Глубокоизлучатель”; г – рассеянного света “Школьный”; д – пыле- и влагонепроницаемый; е – повышенной надежности против взрыва.
Лампы накаливания несложны в изготовлении просты и надежны в эксплуатации. К их недостаткам следует отнести: низкую световую отдачу (в три—шесть раз меньшую по сравнению с газоразрядными лампами) небольшой срок службы (около 1000 ч) неблагоприятный спектральный состав искажающий светопередачу. В них видимое излучение преобладает в желтой и красной частях спектра при недостатке в синей и фиолетовой его частях по сравнению с дневным естественным светом. Лампы накаливания обладают большой яркостью но не дают равномерного распределения светового потока. Чтобы исключить прямое попадание света в глаза и вредное воздействие большой яркости на зрение нить накаливания лампы необходимо закрывать. Помимо этого при применении открытых ламп почти половина светового потока не используется для освещения рабочих поверхностей поэтому лампы накаливания устанавливают в осветительной арматуре.
Газоразрядные источники света включают люминесцентные ртутные и ксеноновые лампы. Последние в осветительных установках промышленных предприятий не применяются.
Газоразрядные лампы дают свет в результате электрического разряда в атмосфере инертных газов паров металла и их смесей. Они имеют следующие преимущества по сравнению с лампами накаливания: высокую светоотдачу в несколько раз большую чем у ламп накаливания весьма продолжительный срок службы (8—14 тыс. ч); спектр излучения люминесцентных ламп близок к спектру естественного света.
К недостаткам газоразрядных ламп надо отнести относительно сложную схему включения и необходимость специальных пусковых приспособлений поскольку напряжение зажигания у этих ламп значительно выше напряжения сети а период разгорания довольно продолжителен. Эти лампы могут дать стробоскопический эффект выражающийся в искажении зрительного восприятия (быстродвижущиеся или вращающиеся детали могут казаться неподвижными). Это явление возникает в результате пульсации светового потока которая к тому же может вызывать помехи радиопередач.
Наличие стробоскопического эффекта в большинстве производственных помещений недопустимо. Устранить его можно пользуясь специально разработанными схемами включения люминесцентных ламп. Эти схемы требуют установки соответствующей пускорегулировочной аппаратуры в которой предусмотрены также конденсаторы для повышения коэффициента мощности установки и устранения радиопомех.
Люминесцентные лампы представляют собой стеклянную прозрачную трубку наполненную дозированным количеством ртути и инертного газа а по концам впаяны электроды. Внутренняя поверхность трубки покрыта тонким слоем люминофора в зависимости от вида которого создается та или иная цветность излучения. Промышленность выпускает люминесцентные лампы: белого света (ЛБ) теплого белого света (ЛТБ) холодного белого света(ЛХБ) дневного света (ЛД) с исправленной цветопередачей (ЛДЦ). Помимо основных типов выпускаются также лампы для целей местного освещения.
Освещение люминесцентными лампами следует применять в помещениях в которых необходимо создать особо благоприятные условия для зрения. Например при выполнении точных работ требующих значительного зрительного напряжения или при выполнении работы связанной с различением цветовых оттенков а также в помещениях с постоянным пребыванием людей при недостаточном или вообще отсутствующем естественном освещении.
Если по условиям работы необходимо правильное различение цветов и их оттенков надлежит применять лампы ЛДЦ. При работе с блестящими поверхностями в установках общего освещения следует применять люминесцентные лампы ЛД поскольку их световая отдача выше а глубина колебаний светового потока меньше. При этом в светильниках местного освещения целесообразно использовать люминесцентные лампы ЛХБ или ЛД.
Люминесцентные лампы чувствительны к температуре окружающего воздуха оптимальной величиной которой является 20—25 °С. Отклонение температуры от оптимального предела вызывает уменьшение светового потока лампы. При температурах близких к 0 ' С зажигание ламп затруднено.
Ртутные лампы высокого давления ДРЛ имеют следующее устройство. В кварцевой трубке содержащей дозированную долю ртути и инертного газа происходит электрический разряд. Трубка помещена в колбу из жароустойчивого стекла внутренние стенки которого покрыты слоем люминофора. Ультрафиолетовое излучение в кварцевой трубке воздействует на люминофор и вызывает его свечение. Световая отдача ртутных и люминесцентных ламп примерно одинакова. Срок их службы около 5000 ч. Режим работы ртутных ламп высокого давления в отличие от люминесцентных ламп низкого давления не зависит от температуры окружающего воздуха. Включение их в сеть производится посредством специального прибора включения (ПРА).
Под светильником понимается комплект лампы (источника света) и осветительной арматуры. Светильник обеспечивает крепление лампы подсоединение к ней электрического питания предохранение ее от загрязнения и механического повреждения.
Светильники предназначены для размещения в них ламп в целях повышения санитарно-гигиенических качеств освещения и снижения расхода электроэнергии. Они устраняют слепящее действие источника света предохраняя глаза работающих от чрезмерной яркости. Это обеспечивается защитным углом светильника.
Аварийное освещение устраивается когда оно необходимо для продолжения работы или для эвакуации людей из помещения при аварийном отключении рабочего освещения. Аварийное освещение должно иметь постоянно действующий источник питания и автоматически включаться при аварии рабочего освещения.
На машиностроительных предприятиях аварийное освещение предусматривается в следующих случаях:
Для продолжения работы в помещениях прекращение рабочего освещения в которых может привести к взрыву пожару или отравлению вследствие нарушения нормального обслуживания механизмов или в случае когда отсутствие освещения может вызвать длительное нарушение технологического процесса. При этом аварийное освещение должно обеспечивать на рабочих поверхностях не менее 5% освещенности от норм одного общего освещения но не менее 2 лк внутри зданий и 1 лк на открытых площадка х.
Для эвакуации людей из помещений с числом работающих более 50 человек если при прекращении рабочего освещения может возникнуть опасность травматизма вследствие продолжения работы производственного оборудования или наличия в помещении мест опасных для прохода людей.
В проходных помещениях пожарных проездах коридорах и на лестницах служащих для эвакуации людей из производственных зданий с числом работающих более 50 человек.
В отдельных помещениях где одновременно могут находиться более 100 человек (красные уголки аудитории и т. п.).
Овещенность создаваемая аварийным освещением необходимым для эвакуации принимается не менее 05 лк на полу помещения и 02 лк на открытых площадках.
Ограждающие и блокирующие устройства
Движущиеся части производственного оборудования если они являются источниками опасности должны быть ограждены.
В таких случаях под опасной зоной машин и оборудования понимается пространство (на производственном оборудовании механизмах машинах или вблизи них) проникновение в которое человека может быть опасным для его здоровья и жизни. Опасную зону могут создать открытые вращающиеся или перемещающиеся детали машин или обрабатываемые изделия она может быть даже на расстоянии от источника опасности – от отлетающей стружки частиц абразива и т. п. Положение опасной зоны в пространстве может быть постоянным или непрерывно меняющимся. В первом случ. – это пространство между нижней и верхней частями штампа молота или пресса вращающимися зубьями шестерен шкивами ременной передачи и т. п. а во втором – отлетающая стружка пространство перед перемещаемым грузом и др.
При проектировании машин и механизмов надлежит предусмотреть устройства исключающие возможность случайного проникновения человека в опасную зону. Оградительные (защитные) устройства и выполняют эту функцию.
Их конструкции весьма разнообразны. Все открытые вращающиеся части станков и механизмов закрываются глухими кожухами плотно прикрепленными к станине или неподвижной части станка. Кожухи на сменных зубчатых и ременных передачах делают откидными с принудительным закрыванием. Передачи (ременные цепные зубчатые и др.) расположенные вне корпуса станков если они представляют опасность травмирования оборудуются ограждениями. Ограждения должны иметь устройства обеспечивающие их безопасное открывание снятие установку и перемещение.
Защитные устройства (экраны) изолирующие зону обработки должны также защищать рабочего от отлетающей стружки и смазочно-охлаждающей жидкости (СОЖ).
Защитные устройства удаляемые при смене детали инструмента измерении детали подналадке станка и в др. случаях должны иметь массу не более 6 кг а их крепление не требовать применения ключей и отверток. Перемещаться они должны после трогания с места при установившемся движении с усилием не более 40 Н. Выполняют их жесткими при толщине материла не менее: для листовой стали – 08 мм для листового алюминия – 2 мм и прочной пластмассы – 4 мм.
Применение съемных защитных ограждений оборудования допускается в случае когда по конструктивным причинам не представляется возможным установить их постоянно.
Ко всем защитным ограждениям независимо от вида станка и оборудования на котором они установлены предъявляются требования надежности безопасности и удобства в эксплуатации.
Если по условиям работы необходимо наблюдать за процессом: обработки ограждения снабжают смотровыми окнами. Материал смотрового окна выбирают с учетом действия на него высоких температур металлической стружки частиц абразивного инструмента и т. п.
При работе на станках которые конструктивно могут быть обеспечены ограждениями рабочих снабжают средствами индивидуальной защиты.
Станки на которых обрабатываются чугун бронза и другие пыле-образующие материалы оборудуются не только ограждениями но и устройствами для удаления этой пыли в процессе работы.
Предохранительные устройства предназначены для автоматического отключения агрегатов и машин при появлении в их работе отклонений от заданных параметров или в целях предупреждения опасности для работающего. Они рассматриваются по отдельным видам производственного оборудования.
Блокировка является одним из широко распространенных методов борьбы с травматизмом и применяется на различном оборудовании.
В целях безопасности используют автоматические предохранительные блокировочные устройства.
Такие устройства осуществляющие фиксацию рабочих частей элемента аппарата или схемы в определенном (рабочем или нерабочем) положении служат для:
-предотвращения неправильного управления агрегатом или сочетания движений механизмов опасных для персонала;
-немедленной остановки агрегата при возникновении опасности или нарушении нормальных условий работы;
-недопущения работы агрегата без предохранительных приспособлений;
-ограничения движения механизмов за заданные пределы и др.
Для блокировки используют электрическую механическую оптическую и магнитную связи.
Применяется блокировка ограждений фрезы ремней шкивов шестерен станков и оборудования при которой последние не могут быть приведены в действие пока их ограждения отведены в сторону и не установлены на месте.
По принципу блокировки производится защита следующих устройств: защитного щитка на абразивном станке предохраняющего рабочего от травмирования отлетающими частицами при заточке инструмента и обработке изделий—при откинутом щитке двигатель блокируется и включить его невозможно; люка кабины крановщика открываемого для выхода на верх мостовых кранов — при открывании люка подача тока ко всем механизмам и приводам крана прекращается; дверей помещения в котором имеется оборудование находящееся под высоким напряжением—при открывании дверей оборудование обесточивается.
Сигнализацию используют для информирования о наступлении тех или иных событий. По назначению сигнализация бывает оперативной предупредительной и опознавательной; по способу информации — визуальной и звуковой.
Для визуальной сигнализации используются: загорающаяся лампа; мигающий свет; подсветка табло е надписью указывающей характер события; освещение изображения на мнемонической схеме того или иного участка. Для звуковой сигнализации — сирена гудок или звонок.
Звуковая сигнализация должна давать ясно различимый в окружающих условиях звук по возможности низкой частоты (до 2000 Гц). Звуковой сигнал должен восприниматься независимо от ориентирования головы оператора.
Световой сигнал воспринимается лишь в том случае если взгляд оператора направлен в его сторону иначе он не будет замечен. Световую сигнализацию устраивают двухцветной (чтобы исключить последствия повреждений устройства) а именно: в зависимости от условий горит одна из ламп (зеленая или красная); потухание обеих ламп свидетельствует о неисправности сигнального устройства. Для надежности световые сигналы включают параллельно так что при выходе из строя лампы одного из сигналов другая будет работать.
Оперативная сигнализация необходима для фиксации выполнения отдельных этапов технологических процессов. Ее используют также для согласования действий работающих.
Предупредительная сигнализация оповещает о наличии опасности или ее возникновении. Средствами такой сигнализации являются: плакаты предупредительные надписи световые и звуковые сигналы работающие от датчиков регистрирующих отклонение технологического процесса или работы оборудования от заданного параметра.
Опознавательная сигнализация предназначена для выделения того или иного оборудования его частей или рабочих зон представляющих опасность или требующих особого внимания. Для этого применяют окраску их в различные цвета peгламентируемые ГОСТ 15548—70.
Установлены следующие сигнальные цвета: красный —явная опасность желтый — предупреждение о возможной опасности зеленый — безопасность. Для пояснительных надписей используются ахроматические цвета: белый — на красном и зеленом фоне черный — на белом и желтом фоне.
Красный цвет — запрещающий — сигнализирует о необходимости немедленного вмешательства указывает устройство которое прервало процесс или движение. Красный цвет применяют для обозначения органов управления запрещающих знаков окраски емкостей с огнеопасным содержимым внутренних поверхностей ограждений опасных частей оборудования средств пожаротушения ламп сигнализирующих об опасности.
Желтый цвет — предупреждающий — указывает предстоящий переход на автоматический цикл работы на приближение одного из параметров (тока температуры и т. п.) к предельным значениям. Желтый цвет используют для предупреждающих знаков окраски элементов строительных конструкций представляющих опасность аварий и несчастных случаев элементов производственного оборудования требующих осторожного обращения перил площадок элементов транспорта ламп сигнализирующих об изменении режима работы оборудования емкостей с вредным содержимым.
Зеленый цвет — извещающий — свидетельствует о нахождении механизмов в подготовленном к работе состоянии о нормальном давлении воздуха воды и т. п. о нормальном режиме работы и получении доброкачественной продукции. Зеленый цвет применяют для предписывающих знаков окраски средств обеспечения безопасности ламп сигнализирующих о нормальном режиме работы оборудования.
Синий цвет — сигнализирующий — используется для указательных знаков и элементов производственной технической информации в специальных случаях когда не могут быть применены упомянутые ранее три цвета.
Белый (молочный) или бесцветный прозрачный светофильтр подтверждает наличие напряжения (включен вводный выключатель) сигнализирует о выбранной скорости и направлении движения о вспомогательных действиях которые не могут осуществляться в автоматическом цикле. Белым цветом обозначают линии движения места сбора отходов.
В целях обеспечения безопасности движения транспортных средств на территории предприятия и в цехах и для информации водителей о принятой системе организации движения применяют дорожные знаки (ГОСТ 1080—71). Установлено четыре группы дорожных знаков: предупреждающие имеющие форму равностороннего треугольника; запрещающие имеющие форму круга с красной окаймляющей полосой за исключением знака «Стоп» имеющего форму восьмигранника; предписывающие имеющие форму круга но без окаймляющей полосы; указательные имеющие форму квадрата или прямоугольника.
Электробезопасность конструкций
Все металлические части производственного оборудования (станины корпусы электродвигатели каркасы шкафов пультов управления и др.) если они могут оказаться под напряжением выше 42 В должны быть заземлены. Для этого их оснащают легкообозримыми устройствами заземления или соединяют с нулевым проводом. Указанные устройства должны иметь заземляющие винты или присоединяемые зажимы. На их поверхность наносится антикоррозийное токопроводящее покрытие для соединения с заземляющими шинами или зануляющими проводами. Между головками винтов используемых для заземления и заземляемыми частями не допускается электроизолирующий слой краски эмали. Если такой слой был нанесен ранее его необходимо удалить.
Гайки крепежных деталей заземляющих устройств оснащают пружинными шайбами или другими элементами предотвращающими ослабление соединения. Использовать для заземления винты шпильки гайки выполняющие роль крепежных деталей не разрешается.
Электрооборудование станков независимо от величины напряжения выполняется проводами имеющими изоляцию следующих цветов:
-силовые цепи постоянного и переменного тока — черный (темно-коричневый);
-цепи управления сигнализации измерения и местного освещения переменного тока — красный (оранжевый розовый);
-цепи управления сигнализации измерения и местного освещения постоянного тока — синий (фиолетовый);
-цепи заземления — двухцветный зелено-желтый (зеленый);
-цепи соединенные с нулевым проводом и не предназначенные для заземления — голубой (серый белый).
Допускается производить монтаж электропроводки одноцветными проводами с обязательной установкой на их концах трубок из поливинилхлорида указанных цветов.
Пожарная безопасность
Пожарная безопасность предусматривает такое состояние объекта при котором исключалось бы возникновение пожара а в случае его возникновения предотвращалось бы воздействие на людей опасных факторов пожара и обеспечивалась защита материальных ценностей.
Пожарная безопасность обеспечивается системами предотвращения пожара и пожарной защиты включающими комплекс организационных мероприятий и технических средств. На машиностроительных предприятиях имеются вновь разрабатываются и внедряются различные виды производственного оборудования новые технологические процессы. При недостаточном внимании к их особенностям они могут стать источником пожара или взрыва. Предотвратить это можно зная пожаро- и взрывоопасные особенности оборудования свойства материалов и их изменение в технологическом процессе.
Современная пожарная защита имеет на вооружении системы быстрого обнаружения пожара совершенную технику и эффективные средства тушения своевременное и квалифицированное использование которых дает возможность ликвидировать пожар в самом начале его возникновения.
Пути эвакуации. Для обеспечения при пожаре безопасной эвакуации людей находящихся в зданиях производственного вспомогательного и другого назначения предусматриваются эвакуационные выходы. Они должны обеспечивать безопасный выход людей наружу кратчайшим путем в минимальное время. Эвакуационными считаются выходы если они ведут из помещения первого этажа наружу непосредственно или через коридор вестибюль лестничную клетку; из помещений любого этажа кроме первого в коридор или проход ведущий к лестничной клетке или в лестничную клетку имеющую самостоятельный выход наружу или через вестибюль; из помещения в соседние помещения в том же этаже обеспеченные выходами наружу и не содержащие производств категории А Б и Е.
Эвакуационных выходов должно быть как правило не менее двух.
В производственных зданиях расстояние от наиболее удаленного рабочего места до выхода наружу или на лестничную клетку принимается в зависимости от категории производства по степени пожарной опасности степени огнестойкости и этажности здания.
В многоэтажных зданиях для помещений имеющих выход в тупиковый коридор расстояние от дверей производственного помещения до ближайшего выхода наружу или на лестничную клетку не должно превышать 20 м.
Двери предназначенные для эвакуации должны открываться в сторону выхода из здания. Устройство раздвижных и подъемных дверей на путях эвакуации запрещается. Минимальная ширина эвакуационных дверей – 08 м высота – 2 м.
Автоматические огнегасительные устройства.
Для автоматического тушения пожара водой в самом начале его возникновения с одновременной подачей сигнала пожарной тревоги используют спринклерные установки.
Основные цехи машиностроительных предприятий этими установками обычно не оборудуются поскольку они не представляют повышенной пожарной опасности.
Спринклер — это прибор автоматически открывающий выход воды при повышении температуры в помещении вызванной возникновением пожара. Вода вытекающая от открывшегося отверстия спринклера ударяется в специальную розетку и разбрызгивается в виде мелких капель (душа).
Спринклерная установка состоит из сети водопроводных труб установленных под перекрытиями в которые на определенном расстоянии ввернуты спринклеры. Один спринклер устанавливают на площади 6—9 помещения в зависимости от пожарной опасности производства.
Вода поступающая в спринклерную сеть предварительно проходит через контрольный сигнальный клапан который обеспечивает подачу сигнала пожарной тревоги одновременно с началом расхода воды через спринклеры. Разность между температурой помещения и температурой вскрытия спринклерной головки составляет 30—40 °С.
Для определения потребности в пожарном облрудовании и первичных средствах пожаротушения вводятся специальные нормы приведенные в табл. 11.
Спринклерные сети должны всегда находиться под давлением воды создаваемым водопроводом водонапорным или пневматическим баком способным подать 10 лс в течение 10 мин. Если этого для тушения-пожара окажется недостаточно включается основной водопитатель — обычно насос который должен подать не менее 30 лс в течение 1 ч (соответствует вскрытию 25—27 спринклеров). Приближенно можно считать что для автоматического водопитателя напор должен составлять 015—018 а для основного водопитателя —05—06 МПа по отношению к уровню на котором расположен наиболее возвышенный спринклер.
Спринклерные установки могут быть трех систем: водяной сухо-трубной и смешанной. При водяной системе все трубопроводы постоянно наполнены водой. Эта система применяется для отапливаемых помещений. При сухотрубной системе трубы наполнены сжатым воздухом выходящим при пожаре и открывающим доступ воде. Эта система применяется в не отапливаемых холодных помещениях. При смешанной системе трубы в теплое время заполнены водой а в холодное время — сжатым воздухом.
Наименование помещений
сооружений и установок
Наименование пожарного оборудования и первичных средств огнетушения на единицу измерения
Механические цехи по обработке металлов механосборочные
Кузнечные и прессовые цехи работающие на твердом топливе и газе
То же работающие на жидком топливе
Газосварочные и электросварочные цехи жестяницкие и медницкие мастерские
Термические цехи с печами:
Малярные лакировочные и т п. цехи
Деревообделочные модельные столярные цехи
Сборочные и переборочные цехи моторных заводов
Ацетиленовые подстанции
Трансформаторные подстанции
На каждую установку
Долголетняя практика применения спринклерных установок показывает что они обеспечивают тушение свыше 90% пожаров возникающих в зданиях оборудованных этими установками до прибытия пожарных команд.
Дренчерная система предназначена для образования водяных завес для защиты здания от возгорания при пожаре в соседнем сооружении для образования водяных завес в помещении с целью предупреждения распространения огня и для противопожарной защиты в условиях повышенной пожарной опасности.
Дренчер внешне похож на спринклер но его отверстие замка не имеет и всегда открыто. Устройство дренчеров системы трубопроводов для воды и их присоединение к водопитающим установкам и сетям мало отличается от спринклерных установок. Пуск воды в дренчерную сеть осуществляется открытием кранов водопроводной сети вручную или автоматически при этом вода начинает поступать в помещение сразу из всех дренчеров.
Рис. 11. Спринклер и дренчер:
а – спринклер; б – дренчер; 1 – шайба поддерживающая клапан; 2 – штуцер; 3 – диафрагма; 4 – рамка для крепления замка и розетки; 5 – клапан; 6 – замок клапана; 7 – разбрызгиватель; 8 – боковая направляющая; 9 – кольцевая направляющая.
Основные положения экологии экологической безопасности автомобильного транспорта
Экология и автомобильный транспорт
Экология (от греч. оicos – дом logos - наука) – наука изучающая условия существования живых организмов и взаимосвязи между ними и средой. В условиях нарастающей автомобилизации современного общества приобретает особый социальный характер.
Экологические показатели – это показатели качества характеризующие уровень вредных воздействий на окружающую среду возникающие при эксплуатации и потреблении продукции.
В настоящее время автотранспорт является одним из наиболее энергоемких отраслей народного хозяйства. В зависимости от уровня развития на его долю приходится 20 60 % всего потребления жидких топлив нефтяного происхождения а его удельный вес в загрязнении окружающей среды составляет до 60 80 %.
Поршневые двигатели внутреннего сгорания (ДВС) являясь основным энергоисточником современных автомобилей одновременно способствуют загрязнению атмосферы. Они являются источником различных вредных веществ (ВВ) пыли продуктов износа шума вибрации и излучений.
Загрязнение окружающей среды автотранспортом является ингредиентным и параметрическим имеющим минеральную и органическую основу.
Причем механизм воздействия автотранспорта на окружающую среду имеет ряд особенностей которые следует учесть при изучении данной проблемы. К ним относятся:
динамический рост процесса автомобилизации;
широкий диапазон отрицательных воздействий автотранспорта на окружающую среду;
довольно низкие показатели экологической безопасности автотранспорта;
ограниченность технических возможностей и сложность улучшения показателей экологической безопасности автотранспорта;
отставание подготовленности общественного сознания в оценке экологической безопасности автотранспорта;
отсутствие действенных механизмов (моделей) управления для улучшения экологической безопасности автотранспорта.
В среднем автомобили в масштабе земного шара ежегодно потребляют 2.1 млрд. т топлива выбрасывая при этом около 700 млн. т вредных веществ (СО – 420 млн. т СН – 170 млн. т NOх – 60 млн. т сажи – 17 млн. т свинца – 0.6 млн. т).
Состав и токсичность газов автомобильных двигателей
Отработавшие газы (ОГ) двигателей представляют собой весьма многокомпонентную смесь в состав которых входит около 200 составляющих. Однако для классификации и анализа состава все компоненты сводятся к нескольким группам которые сходны по химической структуре свойствам а также по характеру воздействия на живой организм.
Первую группу составляют нетоксичные вещества: азот кислород водяной пар а также углекислый газ содержание которого не достигает уровня вредного для человека. Однако по мнению ученых чрезмерное его содержание в составе атмосферного воздуха может привести к глобальным природным изменениям.
Во вторую группу входит окись углерода (СО) присутствие которого в больших количествах характерно для ОГ бензиновых двигателей. Согласно теории цепного окисления углеводородов окись углерода образуется в цилиндре двигателя в качестве стадии холодно-пламенного процесса предшествующего процессу основного горения.
Механизм токсичного действия окиси углерода определяется его способностью соединяясь с гемоглобином крови образовывать карбоксигемоглобин СОНв (соединение же кислорода с гемоглобином дает окисгемоглобин О2Нв) и тем самым лишает ткани тела кислорода.
В третью группу входят окислы азота состоящие из окиси (NO) и двуокиси (NO2) азота. Механизм и кинетика образования окислов азота объясняются результатами термической обратимой реакции азота воздуха под действием высокой температуры и давления в цилиндре двигателя. Причем по мере охлаждения ОГ и разбавления их воздухом окись азота окисляется дальше превращаясь в двуокись трехокись и четырехокись. На организм человека NO2 действует как острый раздражитель а 200-300
опасно при кратковременном вдыхании попадая в легкие и соединяясь с гемоглобином крови вызывает отек легких.
Под действием солнечной радиации окислы азота в присутствии углеводородов образуют фотохимические оксиданты или фотохимический смог.
Четвертую группу токсичных веществ составляет самая многочисленная группа углеводородов состоящая из представителей всех гомологических рядов: алканы алкены алкадиены цикланы. Из общего количества органических компонентов ОГ на долю предельных углеводородов приходится 32 % непредельных – 27.2 % ароматических – 4 % альдегидов и кетонов – 2.2 %.
Кроме этого также в составе ОГ обнаружены полициклические ароматические углеводороды (ПАУ) представителем которых является бензапирен. Механизм образования этих веществ заключается в том что они под действием термических процессов разлагаются на ряд простых углеводородов и свободных радикалов а затем в условиях недостатка кислорода атомы водорода отщепляются от образовавшихся продуктов. Полученные соединения объединяются между собой во все более сложные циклические а затем и полициклические структуры т. е. при температурах от 400 до 800 происходит пиролиз углеводородных топлив образуя при этом ПАУ. ПАУ могут вызывать некоторые формы раковых заболеваний легких.
Пятая группа токсичных веществ состоит из альдегидов (формальдегид 60 % алифатические альдегиды 32 % ароматические альдегиды 3 % и др.).
Формальдегиды обладают высокой токсичностью и резким неприятным запахом. Из алифатических альдегидов в ОГ автомобилей в основном содержится акролейн представляющий собой прозрачную с желтоватым оттенком жидкость обладающую неприятным резким запахом.
Шестую группу вредных компонентов составляет сажа которая характерна для дизелей. Она способна адсорбировать концерогены содержащиеся в ОГ.
В таблице 12 приведен ориентировочный состав ОГ бензиновых двигателей и дизелей.
Анализ приведенных данных в таблице показывает что разница составляющих компонентов ОГ объясняется особенностями работы двигателей (топлива состав горючей смеси организация рабочего процесса и др.).
В таблице 13 приведены вторичные загрязнители атмосферы – фотооксиданты (продукты фотохимических реакций) и их воздействие на окружающую среду.
В таблице 14 приведены предельно допустимые концентрации (ПДК) некоторых веществ в воздухе рабочей зоны.
Особенно следует подчеркнуть вредное воздействие свинца и его органических соединений. В наибольших количествах свинец накапливается в печени почках поджелудочной железе и костях поражает их.
Результаты множества исследований связанных с изучением влияния организации движения (режимов работы автомобиля или двигателя) на расход топлива автомобилем показали что уровень расхода топлива может быть использован в качестве косвенного критерия отражающего выброс вредных веществ ОГ автомобилем в зависимости от технического состояния узлов агрегатов и неисправностей.
бензиновый двигатель
Углеводороды неканцерогенные
В соответствии с существующими государственными стандартами ГОСТ 27435 и ГОСТ 27436 регламентируется внешний и внутренний шум автомобилей.
Важную роль в снижении расхода топлива и следовательно токсичности ОГ автомобилей играет выбор соответствующих режимов движения. На Рис. 12 и Рис. 13 приводятся закономерности изменения компонентов ОГ грузового автомобиля (двигателя) в зависимости от различных факторов объясняющие физический смысл возможности достижения снижения расхода топлива и токсичности ОГ в условиях эксплуатации.
Непрерывная в рабочее время
Натяжение и растрескивание резины
Повреждение растительности
Спазмы дыхательных путей
Раздражение носоглотки спазмы
Обострение респираторных заболеваний
Ухудшение спортивных показателей
Наименования веществ
Агрегатное состояние
Окиси азота (в пересчете на )
Свинец и его неорганические соединения
Бензин (углеводороды)
Рис. 12. Скоростная характеристика грузового автомобиля с полезной нагрузкой 6 т.
Автомобилизация и окружающая среда
Известно что автомобили являются системой со сложным уровнем оказывающей мгогоплановое воздействие на окружающую среду. Для автомобильной промышленности характерно интенсивное потребление природных ресурсов. Установлено что на производство 10 млн. автомобилей (преимущественно легковых) затрачивается 10 млн. т стали 500 тыс. т стекла 2.5 млн. чугуна 230 тыс. т алюминия более 1 млн. т резины и др.
Однако данное воздействие не ограничивается только воздействием на ОС т. е. вводится понятие автомобилизация в которое следует вкладывать все то что связано с научным обоснованием необходимости автомобиля и его естественного окружения – дорог кадров системы управления с проектированием эксплуатационных свойств этих составляющих с их изготовлением эксплуатацией ремонтом и реконструкцией.
Таким образом автомобилизация рассматривается как:
- явление в природе и обществе;
- элемент системы коммуникаций общества;
- одно из ярких и необходимых проявлений научно-технического прогресса;
- система (социальная экономическая и техническая) которой надо управлять т. е. объект управления;
- отрасль производящая и эксплуатирующая различные автомобили;
- процесс насыщения автомобилями;
- наивысшее достижение в области потребительской техники;
- наибольший потребитель природных материальных ресурсов оказывающий значительное воздействие на ОС.
При этом автомобилизация должна развиваться исходя из следующего:
Технический прогресс автомобилизации должен соответствовать людским и природным ресурсам.
Темп роста автомобилизации среди других видов транспорта определяется ее относительной экономической эффективностью.
Социальные взаимоотношения между людьми должны быть основным критерием для установления уровня автомобилизации.
Автомобилизация не должна нарушать экологического равновесия.
Все года развития независимого Узбекистана особо подчеркивается актуальность сложность и многогранность проблем ООС. Решения этих задач вытекают из учета и анализа следующих положений:
- в процессе поступательного развития транспорта объективно возрастает потенциальная возможность усиления неблагоприятного воздействия его на природу;
- многие из ныне известных природоохранных мер по экономическим причинам не могут быть реализованы немедленно а лишь в будущем. Наряду с этим даже реализуемые мероприятия в срок не выполняются;
- некоторые технические средства и процессы на которые возлагались надежды в деле защиты среды обитания оказались не эффективными или неработоспособными в эксплуатационных условиях. Для ряда негативных воздействий на природу пока вообще не найдено методов защиты;
- окружающая среда практически едина и имеет глобальные масштабы. Вредные вещества сброшенные в почву реки море или воздух соответственно поверхностными и грунтовыми водами речными и морскими течениями и атмосферными потоками могут переноситься на сотни и тысячи километров от источника загрязнения.
Все это приводит к необходимости:
Во-первых развивать и ускорять природоохранные работы непосредственно в сфере транспортного хоз-ва обеспечивающих своевременный ввод в эксплуатацию более экологически чистых транспортных средств и технологических процессов более совершенных в названном смысле конструкций постоянных транспортных сооружений.
Пример: электрификация тяги железнодорожного транспорта.
Во-вторых развертывать и углублять НИИОКР в целях изыскания новых экономически и экологически эффективных образцов транспортной техники и технологий существенно снижающих и исключающих загрязнение среды обитания.
В-третьих всемерно развивать пропаганду экологических знаний раскрывать сущность и знание проблемы охраны природы для общества в целом.
“Экологическая безопасность” – положение при котором отсутствует угроза нанесения ущерба природной среде и здоровью населения и достигается совокупностью мероприятий направленных на снижение отрицательного антропогенного воздействия на окружающую среду.
Понятие экологической безопасности взаимосвязано также с понятиями энергетической производственной и технической безопасности.
На экологическую безопасность автотранспортных средств (АТС) влияют различные факторы:
- удельный вес автотранспорта общего пользования;
- степень развития производственно-технической базы предприятий;
- организация технического обслуживания и ремонта;
- конструкция техническое состояние условия и режимы работы ДВС АТС;
- система утилизации производственных отходов и чистки сточных вод;
- градостроительные решения;
- совершенствование рабочих процессов ДВС;
- применение нейтрализаторов и сажеуловителей ОГ;
- дизелизация автотранспорта;
- антитоксичные топливные добавки;
- применение экологически чистых альтернативных топлив;
- применение встроенных эколого-диагностических систем;
- оснащенность предприятий газоанализаторами дымомерами;
- сбор переработка и утилизация производственных отходов;
- правовые и нормативные стороны качества используемых моторных топлив;
- наличие бестранспортных зон в крупных городах;
- состояние и системы управления движением автомобильных дорог улиц;
- оснащенность автодорог экологическими сооружениями;
- систематическое инвентаризация вредных выбросов и постоянное обновление экологического паспорта предприятий;
- применение этилированных бензинов;
- эколого-правовая подготовленность юридических и физических лиц автотранспорта;
- введение экологической и энергетической экспертизы различных проектов;
- социально-экономические вопросы и ряд других.
В результате выполнения Выпускной квалификационной работы мной был проведен комплексный анализ выбранной темы исходя из которого было сформулировано назначение двигателя внутреннего сгорания марки СМД 31-А определены технические экономические и экологические требования предъявляемые к двигателям вообще проведен тепловой и динамический расчет двигателя расчет разрабатываемых узлов (поршня гильзы цилиндра). В экономической БЖД и экологической частях проведены расчеты по этой теме характеризующие себестоимость безопасность и экологичность конструкции.
Проведя патентные изыскания в качестве инновационной разработки была выбрана конструкция составного поршня который обладает рядом преимуществ по сравнению с общепринятыми конструкциями:
– энергосбережением (при предлагаемой конструкции поршня теплопередача от днища поршня к его направляющей части затруднена);
– меньшей тепломеханической напряженностью корпуса поршня;
– оригинальной конструкцией боковой части поршня;
– экологичностью (минимальный тепловой зазор между поршнем и гильзой при различных температурных режимах работы двигателя – уменьшаются прорыв газов в полость масляного картера а также расход масла на угар).
Основная сущность изобретения заключается в том что предлагаемая конструкция обеспечивает возможность свободного вращения и малых продольных перемещений головки относительно корпуса. Как следствие последний оказывается в значительной степени разгружен от действующих на него со стороны головки тангенциальных сил и крутящих моментов работает в облегченных условиях что обусловливает повышение надежности и долговечности поршня.
Кроме того за счет насосного эффекта обусловленного малыми продольными колебаниями головки во время работы поршня через зазоры между смежными поверхностями поршневого кольца головки и корпуса в дренажные отверстия прокачивается масло снимаемое со стенок цилиндра что интенсифицирует охлаждение поршня.
Кроме того выполнение головки и корпуса разъемными и подвижными друг относительно друга позволило использовать поршневое кольцо в виде плоской спирали содержащей по меньшей мере три витка. Кольцо предлагаемой конструкции имеет большую площадь уплотняющей поверхности и не имеет сквозных радиальных стыков. Более того это же кольцо одновременно служит и маслосъемным кольцом.
Другим преимуществом кольца предлагаемой конструкции является то что оно независимо от степени износа трущихся поверхностей обеспечивает постоянство усилия его прижатия к стенкам цилиндра и стабильность зазора между стенками цилиндра и поршня.
Технический результат - повышенные надежность и долговечность работы поршневой группы ДВС.
В качестве примера также предложен вариант конструкции гильзы цилиндра (для двухтактного двигателя).
Все чертежи выполнены в проектно-конструкторской программе «КОМПАС» а расчеты – на компьютере.
Колчин А. И. Демидов В. П. – Расчет автомобильных и тракторных двигателей: Учеб. пособие для вузов. – 2-е изд. перераб. и доп. – М.: Высш. школа 1980.
Двигатели внутреннего сгорания: Конструирование и расчет на прочность поршневых и комбинированных двигателей. Учебник для студентов втузов обучающихся по специальности “Двигатели внутреннего сгорания” Вырубов Д. Н. Ефимов С. И. Иващенко Н. А. и др.; Под ред. Орлина А. С. Круглова М. Г. – 4-е изд. перераб. и доп. – М.: Машиностроение 1984.
Двигатели внутреннего сгорания: Системы поршневых и комбинированных двигателей. Учебник для студентов втузов обучающихся по специальности “Двигатели внутреннего сгорания” Ефимов С. И. Иващенко Н. А. Ивин В. И. и др.; Под общ. ред. Орлина А. С. Круглова М. Г. – 3-е изд. перераб. и доп. – М.: Машиностроение 1985.
Ягудин М. Л. – Технология производства двигателей внутреннего сгорания: Учебник для машиностроительных специальностей средних специальных учебных заведений – 2-е изд. перераб. и доп. – М.: Машиностроение 1981.
Двигатели внутреннего сгорания: Учеб. для вузов по спец. “Строительные и дорожные машины и оборудование” Хачиян А. С. Морозов К. А. Луканин В. Н. и др.; Под. ред. Луканина В. Н. – 2-е изд. перераб. и доп. – М.: Высш. школа. 1985.
Райков И. Я. Рытвинский Г. Н. – Конструкция автомобильных и тракторных двигателей: Учебник для вузов по спец. “Двигатели внутреннего сгорания”. – М.: Высш. шк. 1986.
Базаров Б. И. – Экологическая безопасность автотранспортных средств – Ташкент: ТАДИ 2005.
Полтев М. К. – Охрана труда в машиностроении: Учебник. – М.: Высш. школа 1980.
Глушаков С.В. Лобяк А.В. AutoCAD 2008. Самоучитель изд. 2-е доп. и перераб. – М.: АСТ: АСТ МОСКВА: Хранитель 2008. – 448 с.
Двигатели внутреннего сгорания. В 3 кн. Кн. 3. Компьютерный практикум: Учеб. В. Н. Луканин М.Г. Шатров А. Ю. Труш и др.; Под ред. В.Н. Луканина. – М.: Высшая школа. 1995.
Корячко В.П. Курейчик В.М. Норенков И.П. Теоретические основы САПР. – Минск.: Вышэйшая школа. 1987.
Красильникова Г. Самсонов В. Тарелкин С. Автоматизация инженерно-графических работ. – СПб.: Изд-во «Питер» 2000. – 256 с.
Ткачев Д.А. AutoCAD 2007. – СПб.: Питер Киев BHV 2007. – 464 с.
Филькенштейн Э. AutoCAD 2000. Библия пользователя. – М.: Издательский дом «Вильяме» 2001. – 1040 с.
Хрящев В. Шипова Г. Моделирование и создание чертежей в системе AutoCAD. – СПб.: BHV 2006. – 224 с.
Рекомендуемые чертежи
- 24.04.2014