Проектирование механизма подъема главной тележки литейного крана г/п 100 т




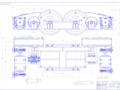
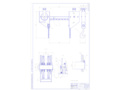
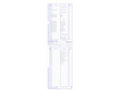
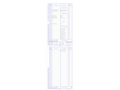
- Добавлен: 25.10.2022
- Размер: 2 MB
- Закачек: 0
Описание
Состав проекта
![]() |
![]() |
![]() ![]() ![]() ![]() |
![]() ![]() |
![]() ![]() ![]() ![]() |
![]() ![]() |
![]() ![]() ![]() ![]() |
![]() ![]() |
![]() ![]() ![]() ![]() |
![]() ![]() |
![]() ![]() |
![]() ![]() |
![]() ![]() |
![]() |
![]() ![]() ![]() |
Дополнительная информация
Траверса.dwg

Механизм подъема 100%.dwg

скорость подъема груза
Технические требования
Траверса _ CК.09405.01.000.dwg

Манжета 1.1-140х125-1
Пресс-масленка 1.2Ц6
Мехпнизм подъема главной тележки литейного крана _ СК.09405.00.000.dwg

Мой 100%.docx
«Ивановский государственный политехнический университет»
Автомобильно-дорожный факультет
Кафедра «Подъемно-транспортные строительные дорожные машины и системы гидроприводов»
По дисциплине «Специальные краны»
на тему: «Проектирование механизма подъема главной тележки литейного крана»
Каждыйлитейный кран имеет главный и вспомогательный подъемный механизм передвижной и приводной механизм отвечающий за перемещение крана. Грузозахватное приспособление главного подъемного механизма состоит из подъемной траверсы и двух крюков состоящих из набора листовых пластин т.е. подъемного стропа портального типа который используется для транспортировки разливочного ковша или сосуда с горячим металлом чей центр зафиксирован между подвесками кронштейна. Грузозахватное приспособление вспомогательного подъемного механизма состоит из кованого крюка или крюка состоящего из набора листовых пластин которые используются для опрокидывания разливочного ковша или сосуда с горячим металлом или при выполнении другого вспомогательного действия. Металлургические краны работая в тяжелых производственных условиях испытывают четыре основных вида нагрузок: статические динамические ударные и технологические. Поскольку они обычно работают в закрытых помещениях ветровые нагрузки на них не передаются. Статические нагрузки воздействуют от собственного веса и веса поднимаемых грузов. Динамические нагрузки возникают при разгоне и торможении механизмов и частей кранов.
Ударные нагрузки имеют разные причины возникновения. Достаточно часто возникают соударения кранов работающих в одном пролете. Имеются случаи ударов хоботов завалочных кранов о колонны или печи при повороте их кабин вокруг вертикальной оси. Возникают удары колонн колодцевых кранов о стенки вертикальных нагревательных колодцев нередки удары клещей кранов для раздевания мартеновских слитков об изложницы.
Технологические нагрузки как указывалось выше возникают во время «планирования» шихты завалочными машинами и кранами в мартеновских печах. Кроме того они возникают в ковочных кранах и кузнечных манипуляторах при ковке изделий прессами и молотами а также колодцевых кранов при чистке подин колодцев от шлака. Эти нагрузки будут описаны при рассмотрении конструкций металлургических кранов.
Разработка схемы полиспаста .
Выбор каната по стандарту и проверка его на прочность .
Определение размеров блоков и выбор для них подшипников .
Компоновка траверсы и расчет ее балки
1 Расчет оси блоков
Проверка пригодности заданного диаметра барабана и расчет элементов балки
Расчет храпового механизма .
РАЗРАБОТКА СХЕМЫ ПОЛИСПАСТА
Согласно заданному числу канатов Z на которых висит груз разрабатывается схема двух сдвоенных полиспастов при этом для каждого сдвоенного полиспаста принимается число канатов . Устанавливается кратность полиспастов in и место установки уравнительных блоков или уравнительных коромысел компенсирующих неравномерную вытяжку канатов. Для данного случая выбираем схему изображённую на рисунке 1[1].
Рисунок 1 - Схема полиспаста
ВЫБОР КАНАТА ПО СТАНДАРТУ И ПРОВЕРКА ЕГО НА ПРОЧНОСТЬ
Определяем максимальное натяжение ветви каната Н набегающий на барабан при подъеме груза [1]
где G – вес груза кН;
Gтр – вес траверсы кН;
Необходимое разрывное усилие каната вычисляется из условия [1]
(2) где [n]=6 – коэффициент запаса прочности при ГРР 5М
Условие выполняется.
По ГОСТ 7667-80 с учетом заданного диаметра каната выбирается канат с разрывным усилием Sк>Sр и устанавливается его маркировочная группа. Выбираем канат закрытый с одним слоем зетобразной проволоки с сердечником типа ТК ГОСТ 3090-73 по [3].
Gк – вес 1метра каната равен 057кг.
Проверяем фактический коэффициент запаса прочности каната
ОПРЕДЕЛЕНИЕ РАЗМЕРОВ БЛОКОВ И ВЫБОР ДЛЯ НИХ ПОДШИПНИКОВ
Диаметр блока по дну желоба мм.
где dк – диаметр каната мм;
Принимаем диаметр блока по [3] Dбл=900мм показанный на рисунке 2.
Рисунок 2 – блок канатный
Характеристики канатного блока: dк=32мм D1=810мм D2=550мм d=260мм d1=275мм d2=360мм d3=150мм H=95мм H1=31мм h=25мм h2=45мм B=55мм b1=80мм n=10мм R=155 r=40 r1=32 r2=6 r3=16 c=2
Диаметр блока мм по оси центра каната вычисляем по формуле
Нагрузка на один подшипник блока кН
где Zn=2 – число подшипников блока.
Статическая нагрузка кН на подшипник с учетом перегрузки
По стандарту выбирается подшипник так чтобы соблюдалась условие
где Со – статическая грузоподъемность подшипника по стандарту кН.
Частота вращения блока с-1
где – скорость подъема мс;
Do – диаметр блока по оси центра каната м;
in – кратность полиспаста.
Эквивалентная нагрузка на подшипник
где - коэффициент переменности нагрузки при коэффициенте нагрузки К=05 принятого класса нагружения В3.
Приведенная нагрузка Fпр кН
где Fэкв – эквивалентная нагрузка на подшипник кН;
Кк=12 – кинематический коэффициент учитывающий вращение наружного кольца подшипника;
Кб=12 – динамическая коэффициент учитывающий условия работы механизма;
Кт=14 – температурный коэффициент учитывающий рабочую температуру 250С.
Необходимая динамическая грузоподъемность подшипника С кН
где Fпр – приведенная нагрузка кН;
nбл – частота вращения блока с-1;
Lh=Tмаш=12500часа – долговечность работы подшипника соответствующая классу использования А4;
α=03 – для роликовых подшипников
По стандарту выбирается подшипник так чтобы соблюдалась условие C ≤ [C]
где С – расчетная динамическая грузоподъемность подшипника кН.
Выбираем по [2] подшипник 2134 ГОСТ 8328-75 который имеет следующие характеристики:dп=170мм Dп=260мм Hп=42мм С=275кН[C]=280кН.
Выбираем крюк пластинчатый для литейного крана по грузоподъёмности Q=100000кг Gкр=50000кг.
рисунок 3: Заготовка крюка 5 – II ГОСТ 6619-75 [4]
Рисунок 3 - Заготовка крюка
D = 280 мм; H = 2710 мм; B = 1070 мм; B1= 160мм; d = 140 мм; d1 = 170 мм;
b = 220 мм; b1 = 430 мм; b2 = 105 мм.
КАМПАНОВКА ТРАВЕРСЫ И РАСЧЕТ ЕЕ БАЛКИ
Рассчитаем усилия действующие на траверсу рисунок 4:
Рисунок – 4 Траверса с крюками
Траверса состоит из балки к которой на осях подвешены пластинчатые крюки и нижние обоймы блоков полиспаста. Оси крюков расположены параллельно оси балки а оси блоков перпендикулярно. К балке снизу подвешен стальной экранирующий лист для защиты ее от действия высоких температур расплавленного металла в ковше. Блоки обойм снизу защищены кожухами.
Расстояние между осью крюка и осью блоков z0 м определяется по формуле [2]
где Dбл – диаметр блоков м.
Балка траверсы представляет собой сварную коробчатую конструкцию из листового проката с внутренними ребрами жесткости. Ширина траверсы обусловлена шириной обоймы с блоками. На траверсе также закреплены кронштейны коромысел полиспаста. Необходимая высота траверсы определяется расчетом траверсы на изгиб.
При расчете стальная конструкция балки представляется как балка на двух опорах. Балка работает на изгиб под действием нагрузок приложенных по осям крюков.
Рисунок 5 – Схема расчета балки
Определяем вес крюка Gкр Н по формуле
где ткр – масса крюка кг;
g – ускорение свободного падения мс2.
Определяем нагрузку приложенную по осям крюков P кН по формуле
где G - вес груза кН.
Расчетным является сечение по середине балки. Материал листового проката сталь ВМСт3пс толщина листа s=0010÷0025м. Допускаемое напряжение изгиба [изг]=
Принимаем толщину стального листа s=002м.
Определяем максимальный изгибающий момент балки Mmax кН·м по формуле
Определяем момент сопротивления Wx м3 по формуле
Рисунок 6-сечение балки траверсы
Определяем напряжение изгиба балки по формуле
Определяем расчетный момент сопротивления по формуле [4]
где H-высота траверсы м;
В- ширина траверсы м;
Размеры принимаем конструктивно:
Получившееся напряжение не превышает допускаемого значения.
Места прохождения осей через стенки балки усиливаются приваркой пластин и проверяются на смятие.
Определяем напряжение смятия см по формуле
где d – диаметр оси блоков м;
[см] - допускаемое напряжение смятия для сталь ВМСт3псравное .
Полученное напряжение смятия меньше допускаемого значения – условие (21) выполняется.
При расчете ось блоков представляется как ось на двух опорах. Ось работает на изгиб под действием нагрузок приложенных по осям блоков.
Рисунок 7 – Схема расчета оси
Определим нагрузку на блок P2 кН по формуле
Определи изгибающий момент Tизг кН определяем по формуле
а=02м расстояние от конца оси до центра приложения силы
Определяем напряжение изгиба оси оси по формуле
где dоси – диаметр оси блоков м
[] – допускаемое напряжение изгиба оси []=140103
ПРОВЕРКА ПРИГОДНОСТИ ЗАДАННОГО ДИАМЕТРА БАРАБАНА И РАСЧЕТ ЭЛЕМЕНТОВ БАЛКИ
Проверка диаметра барабана при известных диаметрах барабана Dб и каната dк должно выполнятся условие
где e=30 – коэффициент при ГРР 5М.
Определим размеры барабана м
где Н – высота подъема м;
t=0038м – шаг нарезки;
dк=32 – диаметр каната;
zн ≥15 – число неприкасаемых витков;
Dо – диаметр барабана по оси центра каната.
Длина на закрепление каната м
Расстояние между нарезанными участками барабана м L2=L3
Минимальная длина барабана м
Необходимая толщина стенки барабана м
[Gсж]=Gт2 – допустимое напряжение на сжатие Нм2.
Необходимое число втулок по условию среза
где Fвт=2SмахDoDвт – окружное усилие передаваемое втулками Н;
dн=006м – наружный диаметр втулки м;
dвн=004м – внутренний диаметр втулки м;
=85МПа - допускаемое напряжение среза втулки сталь 45.
Необходимая длина половины втулки м по условию смятия
Применяют двигатели переменного тока или постоянного тока.
Определим мощность двигателя кВт
Принимаем двигатель постоянного тока серии Д814 по [1] со следующими характеристиками:
-мощность двигателя кВт 96;
- частота вращения nдв с-1 78;
- маховой момент J кгм2 41;
Определим необходимое передаточное число Uред. по формуле [5]
где nдв.- частота вращения двигателя с-1
nбар - частота вращения барабана с-1
где - скорость подъема груза мс
nбар=0125 3(3140932)= 012с-1
Передаточное число открытой передачи u0=5 необходимое передаточное число рассчитывается по формуле
Расчетный крутящий момент Мр Нм на тихоходном валу определяем по формуле [3]
Коэффициент долговечности Кq определяем по формуле [4]
где U2ст. – передаточное число тихоходной ступени
Траб - общее время работы механизма часы
NT - Частота вращения тихоходного вала с-1
КQ - коэффициент неравномерности нагрузок
NHO - базовое число циклов контактных напряжений
Общее время работы механизма принимаем Траб = 6300 ч.
Частоту вращения тихоходного вала NТ с-1 определим по формуле [4]
Базовое число циклов контактных напряжений примем NHO=125106
Эквивалентный момент Мэ определим по формуле [4]
Выбираем редуктор цилиндрический горизонтальный крановый марки ГК-1300 со следующими характеристиками:
- крутящий момент на выходном валу Т Нм 87000;
-передаточное число u 179;
-мощность подводимая к редуктору кВт 96;
РАСЧЕТ ХРАПОВОГО МЕХАНИЗМА
Храповый механизм выполнен с внутренним зацеплением собачки с зубом и совмещен с зубчатым колесом тихоходной передачи редуктора. Размеры зубьев храповых колес конструктивно увязаны с размерами зубчатых колес редуктора ГК-1300. Число зубьев храповых колес Z=25 и модуль m=45мм рисунок 8.
Рисунок 8 – Схема зубчатое колесо с храповым механизмом
Шаг зубьев храповых колес мм находим по формуле
Размеры храповых колес мм находим по формуле
радиус храпового колеса .
Ширину храпового колеса мм находим по формуле
где В – ширина зубчатого колеса мм
Размеры рабочей части собачки мм находим по формуле
Ширину собачки мм находим по формуле
Диаметр по вершине зубьев колеса мм рассчитывается по формуле
Диаметр по основанию зубьев колеса мм рассчитывается по формуле
Статический момент Нм от массы груза приведенный к валу редуктора на котором закреплена обойма с собачками определяется по формуле
Окружное усилие на зубе храповика Н определяется по формуле
Сила действующая в плоскости контакта собачки с зубом храповика Н определяется по формуле
где α=30 градусов угол наклона плоскости каната относительно осевой линии
Напряжения смятия Па определяется по формуле
где А – площадь каната м2;
h1 – высота собачки м;
=60103Нм – напряжение смятия зуба из стали 35ХМ.
Условие G[Gсм] выполняется.
Расчетный тормозной момент одного тормоза Нм [1] определяется по формуле
где Кт=11 – коэффициент запаса торможения
Выбираем тормоз марки ТКТ – 100 [4] со следующими характеристиками:
- тормозной момент Мт Нм 20;
-Момент якоря тормоза Мя Нм 55;
-масса тормрза m кг 12;
Балашов В.П. Методические указания по курсовому проекту
«специальные краны» - М.: Высшая школа 1989-101c.
Шейнтблинт А.Е. Курсовое проектирование деталей машин: Учеб. пособие.
Изд-е 2-е перераб. и дополн. — Калининград: Янтар. сказ. 2002. — 454 с: ил. черт. — Б. ц
Казак С.А. Курсовое проектирование грузоподъемных машин - М.: Высшая школа 1989-319c.
Атлас конструкций. Учебное пособие для технических вузов. – М.: Машиностроение 1976 – 151с
Гохберг М.М. Справочник по кранам: В 2 т. Том 2. – М.: Машиностроение 1988–559 с.