Подвесной грузонесущий конвейер


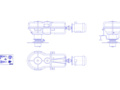
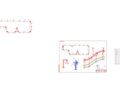
- Добавлен: 25.10.2022
- Размер: 2 MB
- Закачек: 0
Узнать, как скачать этот материал
Подписаться на ежедневные обновления каталога:
Описание
Подвесной грузонесущий конвейер
Состав проекта
![]() |
![]() ![]() |
![]() ![]() |
![]() ![]() ![]() |
![]() |
![]() ![]() ![]() ![]() |
![]() ![]() ![]() ![]() |
Дополнительная информация
Контент чертежей
Записка.docx
Министерство образования и науки Российской Федерации
Государственное учреждение высшего
профессионального образования
Белорусско-Российский университет
Кафедра “Строительные дорожные подъёмно-транспортные
машины и оборудование”
по дисциплине: МАШИНЫ НЕПРЕРЫВНОГО ТРАНСПОРТА
«Расчет и проектирование подвесного конвейера»
студент гр. ПДМР-031
Пояснительная записка
студент гр. ПДМР-061
Назначение область применения составные части и элементы
транспортирующей машины
Патентно – технический анализ
Выбор и расчет параметров конвейера ..
Тяговый расчет конвейера ..
Устройства безопасности ..
Техника безопасности при работе на конвейере
Смазка механизмов ..
Список использованных источников .
В решении задач по механизации и автоматизации подъемно-транспортных погрузочно-разгрузочных и складских работ многих технологических операций значимая роль отводится машинам непрерывного транспорта. В отличие от подъемно-транспортных машин периодического действия они перемещают груз непрерывным потоком без остановки для загрузки и разгрузки с совмещением времени рабочего и холостого (обратного) движений грузонесущего элемента. Благодаря этому производительность машин непрерывного транспорта выше производительности не только подъемно-транспортных машин периодического действия но и современных транспортных средств других видов - железнодорожного автомобильного.
Применение машин непрерывного транспорта обуславливает широкие возможности автоматизации следующих процессов: дистанционного управления работой одной машины или системой машин; сортировки транспортируемых грузов; взвешиванием и дозировкой; заполнением и опорожнением бункеров; загрузки разгрузки и распределения грузов; контроль состояния тягового и других основных элементов.
Машины непрерывного транспорта широкого применения во всех отраслях промышленности на транспорте и в сельском хозяйстве. Их основные элементы - тяговые и грузонесущие - используют в качестве подающих и транспортирующих частей в роторных экскаваторах перегрузочных и отвальных мостах в погрузочно-разгрузочных дорожно-строительных и сельскохозяйственных машинах. Конструктивные особенности некоторых видов машин непрерывного транспорта позволяют рационально совмещать процесс транспортирования с рядом технологических операций - мойкой очисткой покраской сушкой термообработкой сортировкой взвешиванием контролем сборкой и др. Такие конвейеры являются составной и неотъемлемой частью современного поточного производства с использованием автоматических линий. Транспортирующие машины применяют преимущественно в карьерах и на производственных предприятиях для перемещения сыпучих и однородных штучных грузов непрерывным потоком на небольшие расстояния в пределах одной или нескольких связанных между собой производственных площадок.
По принципу действия транспортирующие машины применяемые в строительстве классифицируют на конвейеры (ленточные пластинчатые ковшовые скребковые и др.) в которых перемещаемому материалу движение сообщается механическим путем и пневмотранспортные установки в которых перемещение материала осуществляется в потоке движущего воздуха или с аэрацией материала воздухом.
Пластинчатые конвейеры рассмотренный в данном курсовом проекте применяют для транспортирования крупнокусковых абразивных и нагретых материалов а также крупных штучных грузов в горизонтальном и слабо наклонном направлениях. Рабочим органом является тяговая цепь с плоскими или фасонными пластинами на которых размещается материал или отдельные штучные грузы.
Ленточные конвейеры предназначены для транспортирования сыпучих порошкообразных мелко- и среднекусковых материалов а также однотипных штучных грузов в горизонтальном и слабо наклонном направлении. Рабочим органом на котором размещается транспортируемый материал является резинотканевая лента состоящая из тканевых прокладок со связывающими их резиновыми прокладками и обкладками.
Для транспортирования материалов в вертикальном и сильно наклонном направлении применяют ковшовые конвейеры — элеваторы. Скребковые конвейеры перемещают малоабразивный материал волоком по желобу. Рабочим органом их является пластинчатая тяговая цепь; к ее звеньям прикрепляются скребки между которыми и размещается материал.
Винтовые конвейеры транспортируют сыпучие и вязкие материалы в горизонтальном и слабо наклонном направлениях а иногда и в вертикальном направлении. Рабочим органом является винт вращающийся в желобе с полукруглым днищем.
Роликовые конвейеры используют для перемещения однородных с развитой поверхностью штучных грузов Рабочим органом их являются неприводные или приводные вращающиеся ролики на которых размещается транспортируемый груз.
Тяговым элементом ленточных пластинчатых и ковшовых конвейеров служит лента или цепь замкнутая в бесконечный контур. На концах конвейера они огибают приводные и натяжные барабаны (при лентах) или звездочки (при цепях) а на трассе опираются на ролики (при лентах) или колесами на направляющие (при цепях). Опорой является несущая рама конвейера.
В пневмотранспортных установках материал преимущественно порошкообразный и пылевидный перемещается по трубопроводу под действием воздушного потока. В месте загрузки материал смешивается с воздухом в определенной концентрации а в месте выгрузки отделяется от воздуха.
При выполнении данного курсового проекта приводится расчет подвесного грузонесущего конвейера анализ результатов патентно-информационных исследований а также проектирование общего вида конвейера что является основной задачей курсовой работы.
НАЗНАЧЕНИЕ ОБЛАСТЬ ПРИМЕНЕНИЯ СОСТАВНЫЕЧАСТИ И ЭЛЕМЕНТЫ ТРАНСПОРТИРУЮЩЕЙ МАШИНЫ.
Подвесной конвейер служит для непрерывного транспортирования штучных грузов по замкнутому контуру сложной в большинстве случаев пространственной трассы. Подвесным он называется потому что грузы размещаются на подвесках или в коробах подвешенных к кареткам или тележкам движущимся по подвесному пути.
По основному признаку – способу соединения тяговой цепи с подвеской на которой находится транспортируемый груз и по характеру перемещения грузов подвесные конвейеры разделяют на следующие типы.
Подвесной грузонесущий конвейер (рис. 1 а) имеющий каретки с подвесками для грузов прикрепленные к цепи и перемещающиеся по постоянной трассе подвесных путей вдоль которых движется тяговая цепь.
Подвесной толкающий конвейер (рис. 1 б) у которого тележки с подвесками для грузов не прикреплены к тяговой цепи и движутся по отдельному подвесному пути при помощи толкателей. Последние закреплены на тяговой цепи и толкают находящиеся перед ними тележки с грузами. Цепь с каретками и толкателями движется по тяговому подвесному пути а тележки с грузами – по самостоятельному грузовому пути который может иметь различные ответвления.
Подвесной несуще – толкающий конвейер который представляет собой комбинированное сочетание грузонесущего и толкающего конвейеров. У конвейера такого типа к тяговой цепи прикреплены каретки с крюками - толкателями имеющими предохранительные запоры. Подвеска с грузом прикреплена к грузовой тележке и перемещается на одних участках трассы проталкиванием а на других – в подвешенном состоянии па крюке каретки.
Подвесной грузоведущий (грузотянущий) конвейер (рис. 1 в) у которого транспортируемый груз размещается на напольной тележке передвигаемой по полу цеха или склада. Тележка имеет вертикальную ведущую штангу; со штангой сцепляется захват или толкатель укрепленный на каретке которая присоединена к тяговой цепи и перемещается по подвесному пути.
Подвесной несуще – грузоведущий конвейер у которого напольная тележка шарнирно прикреплена к каретке движущейся вместе по подвесному пути. На одних участках трассы тележка с грузом перемещается по полу помещения как у грузоведущего конвейера а на других - например при переходе на другой этаж или через проезд поднимается и транспортируется в подвешенном состоянии.
По характеру привода различают одноприводные и многоприводные подвесные конвейеры а по типу тягового элемента – цепные и канатные. На подвесных конвейерах можно транспортировать штучные грузы разнообразные по форме и т.п.
Подвески загружаются и разгружаются на ходу конвейера автоматически или вручную – непосредственно или при помощи подъемных устройств.
Рис. 1. Схемы конвейеров: а - грушнесущий; б - толкающий; в - груюнедущий; 1 - каретка; 2 - подвеска; 3 - цепь; 4 - тележка; 5 - грузовой путь; 6 - тяговый путь; 7 - толкатель
Замкнутый контур подвесного пути конвейера позволяет транспортировать грузы почти на всем его протяжении сводя до минимума незагруженные участки .
По сравнению с другими транспортирующими машинами непрерывного действия подвесные конвейеры имеют следующие характерные особенности и преимущества: а) пространственная трасса; б) легкая приспосабливаемость трассы конвейера к возможным изменениям технологического процесса производства; в) возможность создания на конвейере подвижного запаса изделий для ликвидации промежуточных складов в цехе занимающих производственную площадь и требующих применения дополнительной рабочей силы; г) малый расход энергии на транспортирование; д) возможность широкого применения автоматизации управления конвейером автоматизации распределения грузов и погрузочно – разгрузочных работ.
Таблица 1 – техническая характеристика отечественных подвесных грузонесущих конвейеров
нагрузка на каретку кН
Диаметр катка каретки мм
Разгружающая нагрузка кН не менее
Разборная (ГОСТ – 589 – 74)
Двутавровая балка №10
Подвесной грузонесущий конвейер (рис. 2) имеет тяговую цепь замкнутую по контуру трассы с прикрепленными к ней каретками к которым шарнирно присоединены подвески. На подвески укладывают или подвешивают транспортируемые грузы. Каретки при помощи цепи движутся по замкнутому подвесному пути прикрепленному к частям здания или конструкциям конвейера. Тяговая цепь приводится в движение электродвигателем привода. Гибкость цепи в горизонтальной и вертикальной плоскостях позволяет подвесному конвейеру иметь пространственную трассу т. е. его подвесной путь может быть с поворотами как в горизонтальной так и в вертикальных плоскостях в любом направлении. В горизонтальной плоскости цепь поворачивается на поворотных устройствах а в вертикальной – при помощи вертикальных перегибов ходового пути выполняемых по соответственно выбранным радиусам. Первоначальное натяжение цепи создается при помощи натяжного устройства.
Рис. 2. Подвесной грузонесущий конвейер
2 Элементы конвейера.
Тяговый элемент. В качестве тягового элемента подвесного конвейера применяют чаще всего цепь различных типов или значительно реже стальной канат. Для конвейеров расположенных в горизонтальной плоскости можно применять цепи любого типа: тяговые пластинчатые роликовые с шагом 65 – 200 мм и пластинчатые приводные с шагом 25 – 38 мм. Для пространственных конвейеров используются цепи обладающие двухсторонней гибкостью. Наибольшее распространение получили на конвейерах легкого типа двухшарнирные цепи с сомкнутыми и разомкнутыми осями шарниров с шагом 160 и 200 мм на конвейерах тяжелого и среднего типов - горячештампованные разборные цепи (ГОСТ 588 – 81) с шагом 80 100 и 160 мм. Круглозвенные (сварные) термически обработанные цепи (ГОСТ 2319 – 74) диаметром 9 11 13 14 16 мм иногда применяют на конвейерах легкого типа. Сравнительно ограниченное применение имеют также и секционные цепи.
Применение двухшарнирной или секционной цепи с шарнирной подвеской в виде жесткого треугольника (или консольного стержня) позволяет иметь на конвейере вертикальные подъемы и спуски (рис. 3).
В конвейерах легкого типа зарубежных конструкций известно использование цепей из стекловолокна с шаровыми шарнирами.
Каретки. Каретка состоит из двух катков с консольными осями и подшипниками кронштейнов и прокладки. Кронштейны соединяются друг с другом болтами после установки во внутреннее звено разборной цепи.
Рис. 3.Участки трассы подвесного грузонесущего конвейера с вертикальным
Выступы кронштейнов жестко фиксируют положение звена цепи; болт с распорной трубкой служит для шарнирного крепления грузовой подвески.
Каретки. Каретка (рис.4) состоит из двух катков 2 с консольными осями и подшипниками кронштейнов 3 (к которым крепятся оси) и прокладки 4. Кронштейны соединяются друг с другом болтами 1 после установки во внутреннее звено 5 разборной цепи. Выступы 8 кронштейнов жестко фиксируют положение звена цепи; болт 6 с распорной трубкой 7 служит для шарнирного крепления грузовой подвески.
Каретки бывают рабочие - грузовые (одинарные и траверсные) и вспомогательные — опорные (поддерживающие). Рабочие одинарные каретки предназначаются для непосредственного крепления подвески с грузом; к рабочим траверсным кареткам (обычно двум или четырем) крепят траверсу к которой подвешивают тяжелый или громоздкий длинномерный груз. Вспомогательные каретки устанавливают между рабочими каретками для предупреждения провисания тяговой цепи. Цепь может иметь жесткое (рис. 4) или шарнирное крепление к каретке. Последнее необходимо для обеспечения проходимости ходовой части по вертикальным перегибам путей с малым радиусом.
Катки кареток — безребордные. Профиль обода катка зависит от профиля пути до которому каток передвигается. Для ходового пути из двутавровой балки ободы катков) выполняют коническими цилиндроконическими сферическими и сфероконическими при горизонтальном расположении оси катка и цилиндрическими и двухконусными при наклонном расположении оси катка. Катки с коническим ободом обеспечивают устойчивое центрированное движение каретки по двутавровой балке но вызывают дополнительные потери от трения скольжения из-за разницы скоростей точек внутренней и наружной окружностей конуса в зоне контакта с полкой балки поэтому в современных конструкциях не применяются. Сферический обод с центром сферы на оси симметрии катка не обеспечивает устойчивого центрированного движения кареток создает возмож-
Рис. 4. Каретки подвесного грузонесущего конвейера конструкции Союзпроммеханизации
ность для ее бокового раскачивания и изнашивания пути в зоне контакта.
В современных каретках применяют катки-подшипники со сфероконическим ободом изготовляемые на заводах шарикоподшипниковой промышленности как единый комплект катка и подшипника. Каток-подшипник (рис. 5 а) состоит из наружного кольца - обода катка 3 внутреннего кольца 1 шариков 4 увеличенного диаметра сепаратора 5 крышки 6 и лабиринтного уплотнения 2 из штампованных деталей. Большой диаметр шариков (10—16 мм) обеспечивает высокие допускаемые нагрузки на каток; благодаря увеличенным зазорам между шариками и беговыми дорожками подшипник надежно работает даже при загрязнении смазочного материала и при температуре окружающей среды да 200°С.
Рис. 5. Катки каретки и тележки конвейера:
а – типовой каток-шарикоподшипник; б и в – специальные с игольчатыми и коническими (для работы и среде с высокой температурой) подшипниками соответственно
Поворотные устройства. Повороты конвейера в горизонтальной плоскости осуществляются при помощи поворотных устройств в качестве которых используют звездочки блоки роликовые батареи и направляющие шины.
Выбор того или (иного поворотного устройства зависит от типа тягового элемента eгo натяжения и радиуса поворота. Поворотное устройство со звездочкой (рис. 7а) применяет для разборной пластинчатой двухшарнирной и других цепей; причем в первом случае — главным образом на участках конвейера с большим натяжением (более 50% от допускаемого). Профиль зуба звездочек для разборной цепи выполняют по ГОСТ 593 — 75 для пластинчатой и двухшарнирной цепи — по ГОСТ 592 — 75 или специальному очертанию. Поворотные звездочки имеют обычно 6-13 зубьев и диаметр начальной окружности 300—1300 мм; изготовляют их литыми из стали 35Л с нормализацией из серого чугуна иди сварными из листовой стали Ст3.
Поворотные блоки (рис 7 б) разделяют по профилю обода (рис. 6). Блоки с гладким ободом (рис. 6 а) используют для разборных и пластинчатых (роликовых и безроликовых) цепей с канавкой для разгрузки внутренне* го звена разборной цепи (рис 6б) или сварной круглозвенной цепи (рис. 6 в). Блоки с гладким ободом для разборной цепи применяют только на участках с малым натяжением (до 50% от допускаемого) потому что внутреннее звено разборной цепи опираясь на обод блока в поперечном направлении обладает незначительной жесткостью и при большом натяжении в нем могут появиться остаточные деформации. _
Поворотные блоки имеют диаметр 300—1200 мм; отливают их как и звездочки; из серого чугуна или сваривают из стали. Сварные блоки выполняют диаметрам до 16—2 м.
Если в гладком ободе блока (или ролика батарей) выполнить концентрич- ную выемку (рис 6 б) глубиной 2-Змм и шириной на 3-4 мм больше ширины внутреннего звена разборной пени чтобы исключить его изгиб и опорными сделать наружные звенья цепи то такие блоки (и роликовые батареи) можно применять при полном допускаемом натяжении цепи.
Звездочку или блок устанавливают обычно на двух подшипниках качения (шариковых или роликовых конических радиально-упорных) монтируемых на неподвижной оси; закрепленной в опоре (см. рис. 7). Опору крепят болтами к поддерживающей металлоконструкции. Для правильного центрирования и надежного закрепление опору устанавливают на плиту с центрирующей расточкой в которую входит специальный выступ опоры. В современных конструкциях поворотное устройство изготовляют и монтируют в виде единого узла с поворотным участком ходового пути. Это обеспечивает более высокое качество монтажа поворотного участка (главным образом по соосности и взаимному расположению цепи и пути по высоте) и удобство замены его при ремонте.
Роликовая батарея представляет собой ряд стационарных расположенных по дуге вертикальных роликов по которым перекатываются звенья цепи (см рис 7 в) Оси роликов закрепляют на неподвижном каркасе прикрепляемом к поддерживающей металлоконструкции или непосредственно к ходовому пути конвейера при помощи кронштейнов.
Каждый ролик батареи монтируется на двух щарико- или роликоподшипниках и имеет диаметр 70 мм шаг роликов 90—170 мм. Ролики изготовляют из серого чугуна с отливкой в металлическую форму (чтобы получить обод повышенной твердости для предохранений от быстрого изнашивания) или из стали 40 с поверхностной закалкой до НС 42-50.
Рис. 6 Профили обода поворотных блоков.
В современных конструкциях применяют ролики с двумя встроенными шарикоподшипниками при этом обод и ступица ролика являются кольцами подшипников. Роликовые батареи обычно изготовляют по секциям с углом поворота на 15 30 45° и собирают из этих секций для получения требуемого полного угла поворота (до 180°). Радиусы роликовых батарей измеряемые по оси огибаемой цепи выбирают равными 10; 125; 16; 20; 25 м.
Роликовые батареи применяют для разборных и пластинчатых цепей при углах поворота до 45° или при больших (до 180°) когда надо иметь большой радиус поворота (более 650 мм) в горизонтальной плоскости так как в этом случае звездочки и блоки получаются слишком тяжелыми. На конвейере с разборными цепями роликовые батареи как и блоки с гладкими ободами устанавливают только на участках трассы с небольшим натяжением (примерно до 50% от допускаемого) из-за малой сопротивляемости внутренних звеньев цепи поперечному изгибу.
Направляющие шины представляют собой изогнутый по радиусу участок ходового пути по которому двухшарнирная цепь (или секционная) обкатывается своими катками. Поворотное устройство с направляющими шинами имеет простую конструкцию однако его можно применять только для тягового элемента имеющего собственные .катки (см. Ш 2). Направляющие шины применяют для углов поворота до 180° по радиусам (по оси цепи) 063; 08; 10; 125; 16; 20; 25 м.
Рис. 7 Поворотные устройства: а – со звездочкой; б – с блоком; в – на роликовой батарее
Радиус поворотного устройства выбирается из условия свободной проходимости подвесок с грузами на повороте и зависит от их габаритных размеров и расстояния между ними. Проходимость наибольших грузов на повороте проверяется графически. Минимальный зазор между выступающими частями грузов или подвесок должен быть не менее 100—150 мм. Чем выше скорость конвейера и высота подвески тем больше должен быть этот зазор чтобы подвески >не сталкивались друг с другом при пуске конвейера при случайном их раскачивании и от воздействия центробежной силы на повороте. Зазор зависит также от характера груза: для хрупких грузов принимают повышенные зазоры. Для длинномерных грузов длиной 3 — 12 м (например бревен пиломатериалов автомобильных рам железобетонных плит и т. п.) даже при их небольшой ширине радиус поворота и расстояние между параллельными ветвями конвейера получаются очень большими. Поэтому в таких случаях применяют специальные устройства обеспечивающие плоскопараллельное движение длинномерных грузов на повороте без их вращения.
Поворотные устройства крепят на металлических стойках с консолями на кронштейнах и специальных конструкциях или же подвешивают на тягах или жестких каркасах к перекрытию здания.
Подвесной путь. Подвесной путь по которому движутся каретки поддерживающие цепь и подвески с грузами называют направляющим или ходовым. Направляющий путь подвесного конвейера выполняют из одного или двух прокатных или гнутых профилей из сталей СтЗ Ст5 или 45 09Г2 и 14Г2; профили из стали 14Г2 обеспечивают длительный срок службы путей при больших нагрузках. Однобалочные пути (рис. 8а – в ) делают из двутавровых балок № 10 12 14 и 16 (ГОСТ 8239—72) из труб диаметром 60 100 и 150 мм с продольной прорезью и из специальных коробчатых профилей. Двухбалочные пути (рис. 8 г и д) выполняют из двух прокатных или гнутых уголков или двух специальных гнутых профилей.
Рис. 8 Профили пути подвесного грузонесущего конвейера
Путь из двутавровых балок имеет наибольшое распространение для конвейеров среднего и тяжелого типов К его преимуществам относятся простота изготовления монтажа и крепления значительная жесткость пути и возможность использования верхних полок в качестве контршин.
Пути из уголков и фасонных гнутых профилей применяют главным образом для конвейеров среднего легкого и весьма легкого типов с двухшарнирными и круглозвенными цепями. Их преимуществами являются возможность использования кареток с цилиндрическими катками наличие свободного промежутки между путями обеспечивающего возможность выполнения вертикальных перегибов с малым радиусом малая масса. К недостаткам относятся малая жесткость повышенная трудоемкость монтажа креплений и установки контршин. Сравнивая одно* профильные и двухпрофильные пути следует отдать предпочтение первым.
Пути изготовляют отдельными секциями в виде самостоятельных монтажных узлов. Секции соединяют друг с другом неподвижными (жесткими) и раздвижными стыками. Стыки делают сварными и болтовыми с центрирующей накладкой и располагают их не далее чем на 1 — 15м от опоры поскольку прочность стыкового соединения как правило меньше прочности целого сечения. Раздвижные стыки используют только на секциях примыкающих к натяжному устройству (ход раздвижки 100—400 мм) а также в качестве температурных компенсаторов изменения длины пути конвейеров проходящих через сушильные печи или холодильные камеры (ход раздвижки 15—20 мм)
Рис 9 Металлические конструкции для крепления подвесного пути конвейера: а – на тягах; б – на кронштейне; в – на отдельных стойках
При конструировании креплений пути конвейера необходимо максимально использовать конструкции здания в котором проходит конвейер и по возможности избегать специальных стоек чтобы не загромождать производственную площадь помещения. Поэтому путь крепят на круглых тягах (рис. 9 а) диаметром 16—20 мм или жестких подвесках к фермам перекрытия здания на кронштейнах — к стенам или колоннам (рис. 9 б ) и на специальных стойлах (рис. 9 в) когда нет возможности использовать элементы здания или когда . путь проходит близко (2 – 25 м) от уровня пола здания.
Радиус поворота подвесного пути в горизонтальной плоскости зависит от типа и размеров поворотного устройства и тягового элемента. Радиус поворота пути на звездочке должен быть меньше радиуса ее начальной окружной так как звено цепи с прикрепленной к нему кареткой устанавливается по хорде начальной окружности звездочки. Поэтому радиус поворота пути определяется по центрам расположения креплений кареток к цепи.
Привод. В подвесных конвейерах применяют угловые и прямолинейные гусеничные приводы с постоянной и переменной скоростью. Угловой привод может передавать тяговое усилие зацеплением при помощи звездочки (для разборных двухшарнирных и т. п. цепей) или кулачкового блока (для секционного тягового элемента) или же при помощи трения (фрикционный привод для каната и круглозвенной цепи). Угловой привод со звездочкой устанавливают обычно на повороте трассы конвейера на 90 или 180° хотя принципиально возможен и меньший угол обхвата звездочки цепью.
Угловой привод с передачей тягового усилия зацеплением (рис. 10) состоит из приводной звездочки 1 укрепленной на вертикальном валу редуктора 3 электродвигателя 5 соединенного с входным валом редуктора упругой муфтой 4 и предохранительного устройства 2.
Рис 10. Редукторный угловой привод подвесного конвейера
Существуют три основные схемы редукторов для привода подвесных конвейеров: 1) с червячной и цилиндрическими зубчатыми передачами (рис. 10 а); 2) с конической и цилиндрическими зубчатыми передачами (рис. 10 б); 3) с цилиндрическими зубчатыми передачами и фланцевым двигателем расположенным вертикально (рис. 10 в).
Рис 11. Кинематические схемы редукторных приводов
Редукторы с червячной передачей очень компактны и имеют сравнительно небольшую массу даже при больших передаточных числах. К недостаткам таких редукторов относится пониженный КПД (до 044) что ограничивает их распространение. Типовые и наиболее распространенные редукторы конструкции Союзпроммеханизации выполнены по второй схеме (рис. 10 б); их параметры приведены в табл. 2.
Таблица 2 – основные параметры редукторных приводов конструкции Союзпроммеханизации
Максимальный крутящий момент на валу приводной звездочки Нм
Диапазон передаточных чисел редуктора при при 17 исполнениях
Диапазон скоростей движения цепи (ммин) при частоте вращения приводного электродвигателя обмин:
Максимальная консольная нагрузка на тихоходном валу редуктора кН
Общая масса редуктора кг
Общий расчетный КПД редуктора
Тип грузонесущего конвейера
Натяжные устройства. На подвесных конвейерах применяют грузовые пневматические гидравлические пружинно-винтовые и винтовые натяжные устройства. Грузовое натяжное устройство (рис. 11 ) состоит из подвижной тележки 9 к которой прикреплены поворотное устройство 1 (оборотная звездочка блок или роликовая батарея) и подвижной поворотный участок 3 пути конвейера натяжного груза б с тросами и направляющими блоками 5. Под действием силы тяжести натяжного груза тележка отходит назад и натягивает цепь огибающую поворотное устройство создавая тем самым необходимое первоначальное натяжение. Полный ход передвижения натяжной тележки (ход натяжного устройства) обычно равен 250 400 и 600 мм.
Натяжную тележку устанавливают на четырех вертикальных опорных 7 и горизонтальных направляющих 8 катках. Подвижной участок 3 пути конвейера размещенный на тележке соединяют с неподвижными концами путей при помощи специальных раздвижных стыков 2. Раздвижной стык состоит из верхней и нижней направляющих которые обеспечивают непрерывность путей на соединении подвижного и неподвижного участков пути несмотря на передвижение тележки на весь ее ход. В предельных положениях тележки установлены путевые выключатели 4.
Рис 12. Грузовое натяжное устройство: а – без полиспаста; б – с полиспастом
Грузовые натяжные устройства выполняют без полиспаста (рис. 11 а) при натяжении до 4 кН и с полиспастом (рис. 11 б) при натяжения до 16 кН.
Наибольшее распространение в подвесных конвейерах получили грузовые натяжные устройства вследствие автоматичности их действия и большой надежности; Применение грузовых натяжных устройств обязательно на конвейерах проходящих через сушильные нагревательные или охладительные камеры на конвейерах с фрикционным и объединенным приводами на многоприводных конвейерах. Число натяжных устройств на конвейерах с объединенными приводами должно быть равно числу приводных звездочек иначе возможно значительное перенапряжение цепи при неравномерном ее изнашивании. В многоприводном конвейере число натяжных устройств равно числу приводных механизмов. по формулам У конвейеров легкого типа (с натяжением цепи до 4 кН) натяжное устройство иногда объединяют с приводом устанавливая приводной механизм на натяжной тележке. Это упрощает проектирование трассы конвейера и позволяет исключить одно-два поворотных устройства но увеличивает величину натяжного усилия. При больших натяжениях цепи (например более 4 кН) объединение привода с натяжным устройством нецелесообразно из-за. неизбежного перекоса натяжной тележки (вследствие разницы натяжений набегающей и сбегающей ветвей тягового элемента) и возрастания натяжного усилия.
Подвески. В подвесном конвейере несущими элементами служат подвески разнообразной конструкции на которые укладывают или подвешивают транспортируемые грузы. Конструкция подвески зависит от характера груза его габаритных размеров и массы назначения конвейера и способа его загрузки и разгрузки. Подвески выполняют в виде этажерок лотков крюков рычажных захватов коробов цепных тяг стропов и т. л. (рис. 12 а — г). Параметры подвесок для транспортирования грузов в производственной таре нормализованы. Подвеска должна быть прочной легкой простой и экономичной по конструкции удобной для загрузки и разгрузки и надежной для безопасного транспортирования грузов как на горизонтальных так и на наклонных и поворотных участках конвейера она должна иметь шарнирное крепление к каретке или к траверсе чтобы находиться в вертикальном положении на наклонных участках конвейера и тем самым обеспечивать надежное положение транспортируемых грузов.
Конвейеры с двухшарнирными цепными а также с шарнирным креплением тягового элемента к кареткам могут иметь вертикальные участки подъемов и спусков. На таких конвейерах подвеску крепят к каретке при помощи консольного стержня или двух замкнутых стержней образующих треугольник. Вылет консоли должен быть больше половины наибольшего габаритного размера груза с подвеской чтобы груз не задевал за цепь на вертикальных участках трассы конвейера.
Загрузка и разгрузка подвесок конвейера могут производиться вручную при помощи грузоподъемных устройств полуавтоматически и автоматически.
Полуавтоматические загрузка и разгрузка конвейера предусматривают выполнение основных трудоемких операций самим конвейером. Наиболее часто для них используют участки вертикальных подъемов и спусков конвейера на которых можно легко подхватить (подцепить) груз на конвейер или же снять (отцепить) его с конвейера. Например на участке загрузки конвейер имеет вертикальный перегиб с крутым спуском и подъемом загружаемые грузы (короба ящики массивные отливки) подаются на стол расположенный под конвейером. Крюк стропы рычажный захват или обойму подвески конвейера рабочий вручную зацепляет за груз лежащий на столе. Непосредственный захват груза (отрыв от опоры) производится самим конвейером на участке подъема.
Разгрузка конвейера производится подобным образом но в обратном порядке: конвейер на участке спуска устанавливает груз на стол; отцепка крюка или захвата подвески от груза производится вручную. Разгрузка может выполняться также на прямом горизонтальном участке конвейера на подъемный стол управляемый рабочим. Подъем стола может быть ручным или ножным через систему рычагов пневматическим или электрическим с ручным или автоматическим управлением. Наибольшее распространение получают автоматическая загрузка и разгрузка подвесок с автоматическим адресованием грузов. Наиболее перспективными следует считать загрузку и разгрузку на горизонтальных участках пути.
Рис 13. Характерные конструкции подвесок для грузов
Процесс автоматической загрузки подвесок состоит из следующих операций: грузы предназначенные для погрузки в заданном порядке подаются к месту загрузки конвейера; проходящие подвески автоматически подхватывают или подцепляют грузы на ходу конвейера или специальным устройством автоматического адресования включают погрузочное приспособление которое автоматически подготовляет груз к погрузке или непосредственно навешивает его на проходящую подвеску конвейера (рис 13 а). В процесс автоматической разгрузки подвесок входят следующие операции: при загрузке груза cпоcoбoм автоматического адресования назначается пункт его разгрузки; перед прибытием к месту разгрузки подвеска автоматически включает приспособление для разгрузки (или непосредственно встречается с ним) при помощи которого подвеска или ее опорная часть наклоняется поворачивается опрокидывается расцепляется и т п. и освобождается от груза или же груз на ходу конвейера передается (или сталкивается) на какое-либо другое стационарное или подвижное устройство (рис. 13 б в и г).
Предохранительные устройства. Для предохранения механизмов привода и ходовой части конвейера от поломок из-за случайных перегрузок или задевания подвесок за неподвижные конструкции на приводной звездочке устанавливают предохранительный штифт который срезается при превышении расчетного тягового усилия на 25%; специальное устройство выключает подачу тока к двигателю привода и конвейер останавливается.
Для исключения возможности падения транспортируемых грузов на пол на всех подъемах и спусках конвейера а также на горизонтальных участках расположенных над проходами и проездами ставят ограждения в виде лотка. Обычно ограждения делают из стальной сетки или листовой стали и укрепляют на рамке подвешенной к ходовому пути конвейера (рис. 14).
Рис 14. Схемы автоматических операций: а – загрузки; б в г - разгрузки; 1 – подвеска; 2 – загрузочный конвейер; 3 – упор; 4 – направляющие; 5 – подъемный стол; 6 – ролик на подвеске; 7 – направляющая шина; 8 – склиз
При обрыве или случайном разъединении тяговой цепи находящиеся на подъемах и спусках каретки и подвески с грузами под действием силы тяжести будут стремиться скатиться вниз что может вызвать повреждения грузов и конвейера. Для предупреждения этого на подъемах и спусках высотой более 1 м устанавливают ловители которые при обрыве цепи захватывают и останавливают ее. Конструкции ловителей разнообразны в зависимости от принципа действия (храповые рычажные электромеханические и т п.) местоположения на трассе конвейера (спуск ели подъем) типа -тягового элемента и профиля ходового пути. Ловитель простейшего типа устанавливаемый на участках подъема (рис. 15); имеет стальную скобу 1 подвешенную шарнирно на ось 3. Ось закреплена в стойке 4 приваренной к верхней полке путевого двутавра конвейера. При нормальном движении цепи конвейера (вверх) скоба свободно отклоняется корпусом кронштейна каретки 2 в возвращается в исходное положение пружиной 6. При аварийном движении скоба отклоняется назад и упираясь своей перемычкой в полку двутавровой балки останавливает каретку одновременно нажимая рычаг путевого выключателя 5 (или экранирует глазок бесконтактного переключателя) для выключения подачи напряжения к электродвигателю привода.
Рис 15. Типовая конструкция ограждения конвейера
При прохождении конвейера через покрасочные и пескоструйные камеры сушильные моечные и травильные (бондаризйционные) устройства рекомендуется закрывать ходовую часть конвейера специальным кожухом с резиновым асбестовым лабиринтным уплотнением. Такой кожух обычно соединяется с вентиляционной системой и надежно предохраняет цепь каретки и путь от загрязнения перегрева и вредного химического воздействия испарений. Поскольку такие укрытия не всегда бывают возможны и эффективны то целесообразно располагать ходовую часть и путь конвейера вне этих камер и устройств (над ними) перемещая через них только подвески с грузами.
Рис 16. Ловитель устанавливаемый на участках подъема конвейера
ПАТЕНТНО – ТЕХНИЧЕСКИЙ АНАЛИЗ
1 ПЕРЕГРУЗОЧНОЕ УСТРОЙСТВО ПОДВЕСНОГО КОНВЕЙЕРА
Изобретение относится к области промышленного транспорта и касается устройства для перегрузки грузов с подвесного конвейера на гравитационную дисковую дорожку для дальнейшего транспортирования. В районе разгрузки каждая из подвесок с грузом вначале передвигается по наклонному участку монорельса вниз. При этом контргруз подвески не задевает за монорельс поскольку монорельс оказывается в стволе вильчатой штанги. Подвеска со столом поворачивается на угол и занимает положение параллельное дисковой дорожке. При дальнейшем снижении подвески опорная плоскость груза входит в направляющие и ложится на диски. При опускании стола ниже дисков груз освобождается от подвески и свободно по наклонной дисковой дорожке скатывается вправо.
2 НАТЯЖНОЕ УСТРОЙСТВО ТЯГОВОЙ ЦЕПИ ПОДВЕСНОГО КОНВЕЙЕРА
Использование: натяжные устройства конвейеров преимущественно подвесного конвейера. Сущность изобретения: натяжное устройство содержит тележку с поворотным устройством для цепи. Тележка установлена на стационарной раме и связана через канат с грузом. Натяжное устройство имеет распорный механизм расположенный между тележкой и стационарной рамой. Распорный механизм может иметь различное конструктивное исполнение: в виде клина связанного с приводным механизмом и обкладок закрепленных на тележке и стационарной раме; в виде диска с криволинейной боковой поверхностью описанной по спиральному контуру и обкладки закрепленной на тележке; в виде приводного винта с гайкой и упорным подшипником. Натяжное устройство имеет также индикаторно-предохранительный механизм который может быть выполнен в виде размещенного в корпусе подпружиненного стакана с индикаторной стрелкой. Корпус имеет регулировочный винт шкалу и конечный выключатель.
3 ПОДВЕСНОЙ КОНВЕЙЕР
Подвесной конвейер содержащий тяговый элемент с приводом каретку подвесной путь в виде секций из фасонных гнутых профилей и силовую балку с элементами жесткого крепления к ней подвесного пути отличающийся тем что каждая секция подвесного пути выполнена в виде сварной конструкции включающей тонкостенный гнутый Г-образный профиль на вертикальной стенке которого сделаны выступы и основание в виде полосы со сквозными пазами соответствующими по размерам выступам при этом на концах основания с одной стороны сделаны вырезы а с другой - соответствующие им по размерам шипы причем длина основания секции превышает длину ее профиля на величину глубины выреза а сам профиль смещен в сторону выреза перекрывает его и закреплен на основании сваркой выполненной со стороны его подошвы в зоне сквозных пазов при этом шипы основания одной секции входят в вырезы основания другой секции образуя совместно с элементами крепления подвесного пути замок жесткой стыковки секций.
4 ТЕЛЕЖКА ПОДВЕСНОГО КОНВЕЙЕРА
Формула полезной модели
Тележка подвесного конвейера содержащая корпус ролики горизонтального перемещения отличающаяся тем что корпус тележки выполнен в виде пластины при этом тележка оснащена роликами установленными на пластине с возможностью обеспечения перемещения тележки в вертикальном направлении при этом тележка прикреплена к тяговому элементу конвейера обеспечивающему ее прижатие к подвесному пути конвейера.
Тележка по п.1 отличающаяся тем что пластина выполнена из металла полимерных материалов.
Тележка по любому из пп.1 и 2 отличающаяся тем что в ее нижней части выполнено отверстие играющее роль подвески для удерживания грузов.
Тележка по п.3 отличающаяся тем что в отверстии размещается один из концов крюка осуществляющего удерживание груза.
Тележка по п.1 отличающаяся тем что тяговый элемент конвейера представляет собой цепь канат трос.
Тележка по п.1 отличающаяся тем что подвесной путь конвейера имеет «Т» (тавровый) «Г» (угловой) «П» (швеллерный) «О»-образный профиль.
Рис 17. Схема подвесного конвейера 3. ВЫБОР И РАСЧЕТ ПАРАМЕТРОВ КОНВЕЙЕРА
В качестве ходовой части конвейера предварительно принимаем тяговую разборную цепь типа Р2 – 100 – 220 ГОСТ 589 – 74 с шагом 100 мм. Исходя из габаритов груза принимаем шаг подвесок ап=5м. Наибольший угол наклона пути конвейера на вертикальном перегибе max=45º.
- минимальный гарантийный зазор между подвесками или грузами
Для обеспечения заданной производительности на каждую подвеску подвешиваем один каркас т. е. i = 1. Тогда скорость конвейера
где Z – производительность конвейера
Принимаем скорость цепи = 025 мс.
Определяем линейные нагрузки:
на незагруженном участке
где mП – масса подвески;
mЦ – линейная масса цепи;
на загруженном участке
где mГ – масса полезного груза на подвеске
ТЯГОВЫЙ РАСЧЕТ КОНВЕЙЕРА
Приближенно определяем наибольшее натяжение цепи
где Км - суммарный коэффициент местных сопротивлений движению кареток [здесь φ λ — коэффициенты сопротивлений соответственно на вертикальном перегибе горизонтальном повороте на звездочке или блоке () и на роликовой батарее (λ); х у z — число вертикальных перегибов (х) горизонтальных: поворотов на звездочках или блоках (у) и на роликовых батареях (z) на трассе конвейера]; w — коэффициент сопротивления на прямолинейном участке; Н – наибольшая высота подъема груза на трассе конвейера м; Б – коэф. зависящий от числа поворотов и перегибов и их расположения на трассе (Б=03 05); S0 =(500 1000 Н) – первоначальное натяжение цепи
где согласно схеме трассы конвейера
где Lг и Lx – горизонтальные проекции соответсвенно загруженной и холостой ветви конвейера
Коэффициенты сопротивления по табл. 8.5 [1] и 8.6 [1] для средних условий работы при массе груза 200 кг w = 0025; φ = 1025; 1 = 1020; 1 = 1025.
где k3 – коэффициент запаса (8 10);
Sразр – максимальное разрывное усилие
Полученное наибольшее натяжение Smax = 9070 Н показывает что цепь выбрана правильно так как для принятой цепи допускаемая нагрузка равна 13000 Н (см. табл. 8.7 [1]).
Минимальное натяжение цепи следует ожидать после спуска в точке 9; с нее и начнем тяговый расчет по движению цепи конвейера. Принимаем S0 = 500 H. Тогда
Для горизонтального прямолинейного участка:
Для поворотной звездочки (блока):
Для вертикального перегиба:
Наибольшее натяжение получилось в точке 12: S3=6221 Н; оно на 23% отличается от приближенно подсчитанного Smax=9070 Н.
Для определения натяжений в точках 11 10 необходимо вести
расчет против хода конвейера в обратном порядке начиная с точки 9:
Тяговое усилие на приводной звездочке
где Sнб Sсб – натяжение цепи в точке набегания и сбегания с натяжного блока или звездочки
Потребную мощность электродвигателя находим по формуле
Принимаем электродвигатель MTF-012-6 мощностью N = 17 кВт и частотой вращения .
Масса натяжного груза
- усилие передвижению натяжной тележки.
Для привода цепи принимаем звездочку с диаметром делительной окружности D0=10215 мм числом зубьев z=16 шагом t=100.
Частота вращения приводной звездочки
где - диаметр делительной окружности звездочки
Передаточное число редуктора
По таблице XCIV выбираем редуктор КДВ – 250M1 исполнение передаточное число .
Действительная скорость цепи
Поскольку действительная скорость цепи незначительно отличается от первоначально принятой перерасчет параметров конвейера не производим.
Динамическое усилие в цепи при пуске
где м – КПД механизма
движущихся частей конвейера и груза на нем равна:
где - коэф. учитывающий упругое удлинение цепи
Угловое ускорение вала двигателя
Средний пусковой момент
Статический момент при пуске
где W0 – тяговое усилие на приводном валу
Момент инерции всех движущихся масс приведенных к валу двигателя
- радиус делительной окружности звездочки;
- момент инерции ротора;
- момент инерции муфты;
- коэф. учитывающий момент инерции деталей привода вращающихся медленнее чем вал двигателя
Параметры срезного штифта
Находим окружную силу:
где к – коэф. учитывающий предельное значение превышения нагрузки (т.е. 25% от расчетной).
Средний диаметр штифта по плоскости среза:
УСТРОЙСТВА БЕЗОПАСНОСТИ.
Вопросам техники безопасности при проектировании и эксплуатации транспортирующих машин уделяется большое внимание. На всех стадиях создания машины – от проектирования монтажа и до постоянной эксплуатации – закладываются условия её безопасной работы и обслуживания.
Общие требования безопасности при проектировании конвейеров регламентированы ГОСТ 12.2.022 -80. Они включают требования к конструкции (по назначению конвейера особенностям транспортируемых грузов и безопасности эксплуатации) устройствам средств защиты (защитным ограждениям блокировкам сигнализации) и размещению конвейеров в производственном помещении (устройству проходов переходов для обслуживания и т.п.). Требования к электрооборудованию регламентированы «Правилами устройства электроустановок».
Безопасность при эксплуатации машин определяется соответствующими правилами эксплуатации и подробным инструктажем рабочих и обслуживающегося персонала.
ТЕХНИКА БЕЗОПАСТНОСТИ ПРИ РАБОТЕ НА КОНВЕЙЕРЕ
К эксплуатации конвейера допускаются лица не моложе 18 лет.
Перед началом работы необходимо проверить техническое состояние основных механизмов и узлов.
Также необходимо проверить техническое состояние и исправность устройств безопасности рассмотренных ранее.
Все машины непрерывного транспорта сменные элементы и сменные приспособления должны быть изготовлены в полном соответствии с настоящими правилами и стандартами.
Электрическое оборудование машин его монтаж и демонтаж токопровод и заземление должны отвечать правилам устройства электроустановок.
Металлоконструкции и металлические детали конвейеров должны быть предохранены от коррозии.
К механизмам предохранительным устройствам электрооборудованию требующим постоянного технического обслуживания а также для осмотра металлоконструкции конвейера должен быть обеспечен безопасный доступ. Машины непрерывного транспорта с электрическим приводом должны быть оборудованы устройствами для автоматической остановки.
Легкодоступные находящиеся в движении части конвейера которые могут быть причиной несчастного случая должны быть закрыты прочно укрепленными металлическими заграждениями допускающими удобный осмотр и смазку.
Одним из условии бесперебойной работы конвейеров является правильная организация их работы. В целях предотвращения неожиданного и преждевременного выхода конвейеров из строя эти мероприятия проводятся по плану. Системой предусматривается межремонтное обслуживание и ремонт конвейеров: малый средний капитальный. Межремонтное обслуживание – наблюдение регулировочные работы и устранение мелких неисправностей. Нормальное в том числе и безопасная эксплуатация конвейеров обеспечивается при условии что износ деталей не превышает некоторых предельных величин.
На работоспособность и надежность деталей КПД конвейерных механизмов и соответственно на расход электроэнергии при эксплуатации конвейеров большое влияние оказывает выбор и режим смазки которое кроме уменьшения трения предохраняет также от коррозии попадания во взаимодействующие поверхности абразивных пылевидных частиц уплотняет зазоры отводит тепло от трущихся поверхностей.
Смазка конвейера осуществляется согласно технологической карты.
В конвейерах смазываются зубчатые передачи и зацепления подшипники качения шарниры (тормозов и систем управления).
При унификации режимов смазки и материалов должен обеспечиваться минимальный ассортимент применяемых марок а также возможность большей длительности периодов между смазочными операциями и очистки смазочных систем.
Из систем смазки наиболее прогрессивной является централизованная однако для некоторых элементов целесообразно применение индивидуальной ручной смазки.
Смазка редукторов производится автотракторным маслом АКЗп-6 или другими близкими по свойствам по ГОСТ 1862-63.
Зубчатые муфты по рекомендации ГОСТ 50006-83 заполняют следующими смазочными материалами в зависимости от окружающей температуры: ТСп-10 МТ-8п ИПП-200.
При систематическом обслуживании осуществляется доливка масла в редуктора до требуемого уровня. Подшипники качения смазываются через масленки.
Стандартизация – это деятельность заключающееся в нахождении решений для повторяющихся задач в сфере науки техники и экономики направленная на достижение оптимальной степени упорядочения в определенной области.
В зависимости от сферы действия Государственный комитет по стандартизации предусматривает следующие категории стандартов: государственные отраслевые стандарты предприятия.
При выполнении графической части использовались ГОСТы ЕСКД.
При выполнении курсового проекта использовались следующие стандарты и ГОСТы:
ГОСТ 588-81 – Цепи тяговые пластинчатые.
ГОСТ 22281-76 – Настил пластинчатых конвейеров.
ГОСТ 4366-76 - Смазка для подшипников.
СТ СЭВ 189-75 – Размеры сечений шпонок и пазов.
ГОСТ 20720-75 – Муфты зубчатые МЗ.
ГОСТ 21424-75 – Муфты втулочно-пальцевые типа МУВП.
ГОСТ 19523-81 – Электродвигатели асинхронные типа 4А.
ГОСТ 5720-75 – Подшипники роликовые радиальные сферические двухрядные.
ГОСТ 5721-75 – Подшипники шариковые радиальные сферические двухрядные.
СПИСОК ИСПОЛЬЗОВАННЫХ ИСТОЧНИКОВ
Спиваковский А.О. Транспортирующие машины: Учеб. пособие для
машиностроительных вузов А.О. Спиваковский В.К. Дьячков. - 3-е изд. перераб. - М.: Машиностроение 1983. - 487 с.
Вайнсон А.А. Подъемно-транспортные машины: Учеб. для вузов. -
-е изд. перераб. и доп. - М.: Машиностроение 1989. - 536 с.
Зенков Р.Л. Машины непрерывного транспорта: Учеб. Р.Л. Зенков
Й.И. Ивашков Л.Н. Колобов. - 2-е изд. перераб. и доп. - М.: Машинострое
Иванченко Ф.К. Конструкция и расчет подъемно-транспортных ма
шин.-Киев: Вищашк. 1983. - 351 с.
Иванченко Ф.К. Расчеты грузоподъемных и транспортирующих ма
шин. - Киев: Вища шк. 1978. - 576 с.
Кузьмин А.В. Справочник по расчетам механизмов подъемно-
транспортных машин А.В. Кузьмин Ф.Л. Марон. - 2-е изд. перераб. и доп. -
Мн: Выш. щк. 1983. - 350 с.
Транспортирующие машины: Атлас конструкций А.О. Спиваков
ский СМ. Бжезовский В.К. Дъячков и др. - 2-е изд. перераб. и доп. - М.:
Машиностроение 1971. - 116 с.
Антипенко Г.Л. Курсовые и дипломные проекты. Общие правила
оформления конструкторской документации Г.Л. Антипенко A.M. Щеме-
лев. - Могилев: ММИ 1995. - 105 с.
Конвейер подвесной (привод).dwg

Остальные технические требования по СТБ 1014-95
Конвейер подвесной ОВ.dwg

*Размеры для справок
Остальные технические требования по СТБ 1014-95
Заимствованные изделия
Вновь разрабатываемые
Технологические камеры покраски и сушки
Рекомендуемые чертежи
- 23.08.2014
- 23.08.2014
Свободное скачивание на сегодня
Обновление через: 11 часов 4 минуты