Отделение конвертирования медных штейнов с разработкой мероприятий по увеличению стойкости футеровки в зоне фурменного пояса




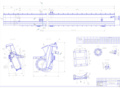
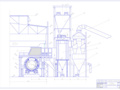
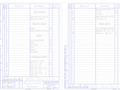
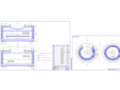
- Добавлен: 25.10.2022
- Размер: 1 MB
- Закачек: 0
Описание
Состав проекта
![]() |
![]() |
![]() ![]() ![]() ![]() |
![]() ![]() ![]() ![]() |
![]() ![]() ![]() ![]() |
![]() ![]() |
![]() ![]() |
![]() ![]() ![]() ![]() |
![]() ![]() |
![]() ![]() ![]() ![]() |
![]() ![]() |
![]() ![]() |
![]() |
![]() ![]() ![]() |
Дополнительная информация
фурмаколлектор.dwg

Спецификация Стройка 2.dwg

Стройка 2.dwg

Спецификация Фурмокол.dwg

Корпус фурмоколлектора
Гайка ГОСТ 5915 - 70
Шайба пружинная ГОСТ 6402 - 70
Штифт цилиндоический ГОСТ 3128 - 60
Кран пробковый проходной
муфтовый ГОСТ 2422 - 55
Футеровка.dwg

Кирпич прямой ПХСУ № 5
Кирпич прямой ПХСС №7
УСЛОВНЫЕ ОБОЗНАЧЕНИЯ:
- Клин торцевой двухсторонний.
- Клин переходный двухсторонний.
Проект отделения конвертирования медных штейнов с разработкой мероприятий по увеличению стойкости футеровки в зоне фурменного пояса.doc
Федеральное государственного автономное образовательное учреждение высшего профессионального образования
«Уральский федеральный университет имени первого Президента России Б.Н.Ельцина»
Кафедра металлургии тяжелых цветных металлов
ПОЯСНИТЕЛЬНАЯ ЗАПИСКА
Тема: «Проект отделения конвертирования медных штейнов с разработкой мероприятий по увеличению стойкости футеровки в зоне фурменного пояса»
(должность уч. ст. звание) (подпись) (расшифровка подписи)
(группа) (подпись) (расшифровка подписи)
ЗАДАНИЕ НА ПРОЕКТИРОВАНИЕ3
ОСОБЕННОСТИ ТЕХНОЛОГИЧЕСКОГО ПРОЦЕССА5
2 Конструкция конвертера6
3 Особенности тепловой работы конвертера8
Конвертирование - окислительный процесс заключающийся в обработке сульфидных расплавов кислородсодержащими газами (воздух кислородно-воздушная смесь) с целью количественного удаления железа а также частично или полностью серы. Технологические особенности конвертирования штейнов определяются их составом и схемой дальнейшей переработки. На конвертирование поступают штейны в расплавленном и частично твердом виде обороты богатые медью кварцит золотосодержащий подсушенный и окатанный медный концентрат иногда богатая медная руда. Основная задача процесса конвертирования - получение черновой меди; попутные - получение газа пригодного для производства серной кислоты а также извлечение золота из кварцита и возгонов некоторых редких металлов. Так при конвертировании медных штейнов удаляют примеси серы получают черновую медь (99 %). Процесс конвертирования по организации работы делится на периоды набора белого матта и варки черновой меди а по химическим процессам - на первый и второй периоды.
Газы полученные при конвертировании содержат до 7% SO2. Такие газы направляются на очистку и утилизацию с получением серной кислоты контактным способом.
ОСОБЕННОСТИ ТЕХНОЛОГИЧЕСКОГО ПРОЦЕССА
Конвертирование – окислительный процесс заключающийся в обработке сульфидных расплавов кислородсодержащими газами (воздух кислородо-воздушная смесь) с целью количественного удаления железа а также частично или полностью и серы.
Основные химические взаимодействия в процессе конвертирования медного штейна: в первом периоде окисляется главным образом сульфид железа в присутствии кремнезема подаваемого с кварцевым флюсом по реакции:
FeS + ЗО2 + SiO2 = Fe2SiO4 + 2SO2. (1.1)
При дефиците низком качестве флюса создаются предпосылки для переокисления железа до магнетита:
FeO + О2 = 2Fe3О4 (1.2)
который при повышении температуры взаимодействует с сульфидом железа:
Fe3O4 + FeS + 5SiO2 = 5(Fe2SiO4) + SO2. (1.3)
Эти реакции экзотермичны и не только обеспечивают поддержание температуры процесса но и формируют избыток тепла что приводит к повышению температуры расплава в конвертере. Поэтому в конвертер загружают холодные добавки: вторичное металлосодержащее сырье корки штейна из ковшей выломки и т. п.
Возможно окисление сульфида меди только после количественного окисления сульфида железа иначе происходит обратное сульфидирование:
Cu2S + 15O2 = Cu2О + Cu2O + FeS = Cu2S + FeO. (1.4)
Жидкими продуктами первого периода конвертирования являются шлак и белый матт. В шлак переходят фаялит и большая часть магнетита часть свободного кремнезема из флюса оксиды металлов-примесей. Медь в шлаке представлена в виде механических потерь в форме ее содержание в шлаке составляет 15-25 %. Этот шлак является оборотным и направляется в печь для плавки на штейн или на отдельную переработку флотационным или электротермическим обеднением.
Белый матт представляет собой Cu2S содержащий некоторое количество FeS и примесей.
Второй период конвертирования предлагает получение черновой меди. При продувке расплава происходит окисление Cu2S:
Cu2S + 2Ог = 2Cu2O + 2SO2 (1.5)
и взаимодействие оксида меди (1) с ее сульфидом:
Cu2О + Cu2S = 6Cu + SO2. (1.6)
Образующаяся металлическая медь растворяется и накапливается в сульфидном расплаве достигая предела растворимости при данной температуре. Происходит расслаивание расплава с образованием двух жидких продуктов: нижнего слоя металлической меди и верхнего слоя жидкого белого матта.
Второй период конвертирования завершается полным удалением серы и получением черновой меди качество которой регламентируется техническими условиями. Полученная медь содержит 975-995 % меди и примеси никеля цинка свинца сурьмы висмута селена теллура мышьяка и благородных металлов. Она направляется на рафинирование для получения товарной меди и извлечения примесей. Конвертерные газы охлаждают очищают от пыли и направляют на производство серной кислоты.
2Конструкция конвертера
Рабочее пространство конвертера конструкция которого показана на рисунке 1.1 ограничено стенками реакционной камеры имеющей форму цилиндра с отверстием в верхней части (горловиной) предназначенным для загрузки перерабатываемых материалов выгрузки продуктов конвертирования и удаления технологических газов в период продувки. Дутье в конвертер подают через стальные патрубки (фурмы) число которых достигает 41-52Их устанавливают в ряд с одной из сторон реакционной камеры параллельно ее оси.
- корпус конвертера; 2 - бандаж; 3 - коллектор; 4 - фурменный пояс (фурмы); 5 - защитный кожух (фартук); 6 - футеровка; 7 - венцовая шестерня; 8 - горелка; 9 - горловина; 10 - фурменная трубка; 11 - опорный ролик
Рисунок 1.1 – Горизонтальный конвертер
Плавильная камера (корпус) конвертера имеет форму цилиндра. Изнутри ее выкладывают огнеупорным кирпичом снаружи заключают в металлический кожух из листовой стали толщиной 20-25 мм. Для футеровки применяют хромомагнезитовые магнезитохромитовые и периклазошпинелидные огнеупоры. Толщина кладки колеблется в пределах 230-380 мм. В области фурменного пояса где футеровка подвергается наиболее интенсивному агрессивному воздействию перегретого расплава ее толщину увеличивают до 540-800 мм. Между кладкой и кожухом расположена засыпка из магнезитового порошка толщиной около 100 мм для того чтобы футеровка имела возможность свободно расширяться при нагревании. Срок службы огнеупорной футеровки конвертера составляет 3-6 мес.
Ёмкость конвертера оценивают по количеству находящегося в ней металла. Обычно она колеблется от 20 до 100 т. В зависимости от емкости его длина и диаметр изменяются соответственно от 23 до 43 и от 45 до 100 м.
Горловина конвертера расположена под углом 13-30 град к вертикальной плоскости. Она имеет круглую прямоугольную или овальную форму. По ее периметру к кожуху крепят футерованную огнеупорным кирпичом литую стальную раму (воротник) высокой 550-900 мм.
Фурмы для подачи дутья в расплавленный штейн устанавливают на корпусе конвертера наклонно под углом 3-11 град к горизонтальной плоскости. Основной конструктивный элемент фурмы – литой корпус имеющий три патрубка: верхний служит для подключения к воздушному коллектору торцевой – для монтажа фурмы на кожухе конвертера и сочленения ее с фурменной трубкой внутренний диаметр которой варьируется в пределах 36-51 мм а наружный оборудованный шариковым клапаном – для ввода фурмовки представляющей собой стальной ломик с утолщенным концом для прочистки фурм.
Над горловиной конвертера устанавливают напыльник для сбора и удаления технологических газов. Как правило он представляет собой кессонированную камеру с подвижной передней стенкой что дает возможность производить очистку горловины и задней стенки напыльника от настылей. Его форму подбирают таким образом чтобы он полностью накрывал горловину. Для плотного прилегания напыльника к корпусу конвертера и защиты системы подвода дутья от брызг расплавленного материала в области горловины устанавливают вспомогательный защитный кожух (фартук).
На массивном бетонном фундаменте конвертера смонтированы специальные опорные устройства с несущими роликами из литой стали и привод механизма поворота. Установку корпуса конвертера на опорные ролики осуществляют с помощью двух стальных бандажей жестко скрепленных с кожухом. Около одного из бандажей на корпусе конвертера размещают большую кольцевую шестерню которая является последним звеном приводного механизма.
Загрузка флюсов и холодных присадок в горловину конвертера производится из сборного бункера с помощью ленточного или пневматического питателя. Таким же способом на ряде заводов в конвертер работающий на дутье обогащенном кислородом подают гранулированные концентраты.
Конструкция конвертеров применяемых для переработки медных полиметаллических медно-никелевых и никелевых штейнов практически одинакова. Они отличаются друг от друга только емкостью реакционной камеры.
3 Особенности тепловой работы конвертера
Конвертеры являются агрегатами периодического действия с изменяющимся во времени тепловым и температурным режимами. Сначала через горловину наполненного конвертера заливают расплавленный штейн с температурой от 1050оС до 1100 оС в количестве 1- 2 ковшей. Затем конвертер устанавливают в рабочее положение и продувают воздухом в присутствии кварцевого флюса в течение 35-50 мин.
Струя воздуха имеющая начальную скорость до 250 мс проникает в расплав примерно на одну треть ширины ванны. На этом участке развивается высокая температура существенно превышающая среднюю температуру ванны. При конвертировании медных штейнов она достигает 1400 - 1500 оС. За счет высокой скорости воздушная струя разбивает прилегающие к ней жидкости и образует в глубине ванны активный окислительный факел насыщенный мелкими брызгами сульфидов что обусловливает бурное протекание реакций окисления сульфидов:
FeS + 5О2 = Fe3O4 + 3SO2 (1.7)
FeS + 15О2 = FeO + SO2 (1.8)
Сульфид меди не подвергается окислению практически до полного окисления FeS. Образование магнетита существенно снижает производительность конвертера поскольку на окисление 1 кг железа до Fe3O4 необходимо в 13 раза больше кислорода чем на его окисление до FeO. Повышенное содержание магнетита в шлаке увеличивает его вязкость плотность и температуру плавления что заметно ухудшает свойства шлаков и приводит к увеличению содержания в них меди и никеля. Реальные возможности восстановления магнетита сульфидом железа возникают при наличии кремнезема:
Fe3О 4 + FeS + 5SiО2 = 5(2FeO SiО2) + SО2. (1.9)
Однако малая плотность кварцита по сравнению с плотностью шлака и тем более штейна не позволяет кускам кварцита проникать в глубь ванны даже при ее бурном перемешивании. В результате конвертере возникает пространственная разобщенность реакций окисления и шлакообразования так как между дутьевым факелом поверхностью ванны на которой плавает кварцевый флюс находится слой расплава толщиной 06 - 10 м. Чтобы иметь минимальную толщину слоя шлака который как бы изолирует ванну от флюсов по мере его накопления процесс продувки прекращают образовавшийся шлак сливают. После этого в конвертер заливают новую порцию штейна загружают флюсы и цикл повторяют.
В период окисления сульфидов железа который называют периодом накопления теплоты температура расплава непрерывно повышается достигая заданного значения (1250 - 1320 °С). Постепенно в конвертере накапливается обогащенная масса состоящая из Cu2S или NiS2.
После того как при переработке медных штейнов в конвертере будет накоплена полная ванна глубиной до 15 м практически чистой полусернистой меди начинается второй период процесса который осуществляют без остановок дутья и без загрузки флюсов и холодных материалов. Во втором периоде происходит окисление сульфида меди и по обменной реакции выделяется медь:
Cu2S + 15Cu2О = Cu2O + SО2. (1.10)
Cu2S + 2Cu2О = 6Cu + SО2. (1.11)
В результате реакции окисления сульфидов меди в расчете на 1 кг перерабатываемого штейна выделяется лишь 20 % того количества теплоты которое поступило в конвертер в первом периоде причем большую ее часть уносят технологические газы. Поэтому второй период протекает в условиях дефицита теплоты и носит название периода потребления теплоты.
Рассмотрим тепловой баланс процесса конвертирования медного штейна по периодам:
Приход теплоты % Расход теплоты %
Физическая теплота штейна 238 Физическая теплота шлака 397
Теплота окисления . 736 Потери с отходящими газами 342
Теплота шлакообразования 26 Затраты на разложение сульфидов 164
Тепловые потери в окружающую среду 97
Физическая теплота штейна .480 Физическая теплота черновой меди .155
Теплота окисления Cu2S 519 Потери с отходящими газами 467
Теплота шлакообразования 01 Затраты на разложение Cu2S .151
Тепловые потери в окружающую среду..227
Из этих данных видно что если в первом периоде большую часть теплоты уносили шлаки то во втором периоде возросли потери с отходящими газами. Увеличение тепловых потерь в окружающую среду во втором периоде можно по-видимому объяснить тем что их абсолютная величина возросла незначительно (в результате прогрева огнеупорной кладки к концу первого периода) но в связи с резким сокращением поступления теплоты в конвертер во втором периоде относительная масса потерь заметно увеличилась.
Наиболее важная характеристика работы конвертеров — количество дутья подаваемого через фурмы. Производительность конвертеров как уже отмечалось выше определяется интенсивностью продувки т.е. расходом воздуха отнесенным к единице массы перерабатываемого штейна. При увеличении подачи дутья усиливается разбрызгивание расплава и при достижении какого-то определенного расхода воздуха вынос брызг из горловины возрастает настолько что работа персонала становится опасной а потери штейна недопустимо высокими. Этот расход воздуха считается предельным для данного конвертера. Уменьшения выбросов расплава из конвертера можно достичь снижением подачи дутья через средние фурмы расположенные под горловиной при одновременном увеличении дутья через крайние фурмы.
В процессе эксплуатации конвертеров может происходить резкое уменьшение пропускной способности фурм вследствие их зарастания которое объясняется застыванием штейновой массы в месте ее соприкосновения со струей холодного воздуха поступающего через фурму. Для удаления настылей необходима периодическая чистка фурм. Уменьшить зарастания дутьевых фурм можно за счет повышения температуры процесса и увеличения давления дутья.
Вместимость конвертеров оценивают массой штейна перерабатываемого в рабочем пространстве агрегата. В цветной металлургии используют конвертеры вместимостью от 20 до 100 т. Степень использования кислорода дутья в конвертере довольно высока: 90 95 %.
Достоинствами конвертеров являются: 1) отсутствие необходимости подачи топлива; 2) высокая степень удаления примесей; 3) возможность переработки цветного лома; 4) высокая интенсивность протекания физико-химических процессов в ванне; 5) высокое содержание в отходящих газах сернистого ангидрида позволяющее использовать их для производства серной кислоты.
Недостатки конвертеров: 1) невысокое прямое извлечение металлов из штейна; 2) невозможность получения отвальных шлаков; 3) необходимость постоянной чистки фурм; 4) необходимость очень частых остановок конвертера что резко увеличивает суммарную продолжительность процесса конвертирования штейнов; 5) значительное загрязнение окружающей атмосферы за счет выбивания технологических газов.
ТЕХНИКО – ЭКОНОМИЧЕСКОЕ ОБОСНОВАНИЕ
Конвертирование – один из основных переделов как в черной так и в цветной металлургии что обусловлено рядом преимуществ его перед другими методами переработки медных штейнов. Даже в настоящее время процесс конвертирования является основной операцией в производстве черновой меди.
Процесс конвертирования ведут либо на воздушном дутье либо на дутье обогащенном кислородом.
Применение дутья обогащенного кислородом приводит к снижению количества подаваемого воздуха увеличению теплового КПД конвертера. При этом в конвертере формируется избыток тепла что приводит к увеличению температуры расплава. Для снижения температуры в конвертер загружают дополнительные холодные присадки. В результате производительность конвертера возрастает.
В свою очередь с повышением температуры в конвертере происходит разрушение магнетитового гарниссажа и следовательно ускоренный износ футеровки. Однако по данным Л.М. Шалыгина температура дутьевого факела как основной показатель термической нагрузки фурменного пояса заметно снижается с повышением содержания меди в штейне. Так при продувке штейна с содержанием 50 % меди при 25 % кислорода в дутье температура дутьевого факела оказывается такой же как при продувке штейна с 30 % меди воздушным дутьем и даже ниже чем для 10 % штейна.
Отсюда следует что более или менее удовлетворительных температурных условий и приемлемых показателей стойкости футеровки при работе конвертера на дутье обогащенном кислородом можно добиться лишь при переработке богатых штейнов с содержанием меди не менее 40 – 50 %.
Преимущества обогащенного дутья перед воздушным следующие:
- производительность конвертера выше;
- процесс протекает быстрее;
- потери тепла с отходящими газами меньше;
- концентрация SO2 в газах выше.
Избежать быстрого износа футеровки и как следствие продлить межремонтную кампанию конвертера возможно за счет использования более стойких и плотных огнеупоров. В качестве таких огнеупоров можно использовать периклазовые огнеупоры.
Периклазовые огнеупоры (per для безобжиговыех периклазовых огнеупоров используют связки из лигносульфонатового сульфата магния и др. Периклазовые огнеупоры применяют для футеровки стенок мартеновских печей миксеров печей для плавки меди и никеля высокотемпературных нагревательных печей леток кислородных конвертеров и др. а также в виде плит шиберных затворов сталеразливочных ковшей стаканов для разливки сталей пористых фурм для продувки стали газами и т.п.
Наименование показателей
Кажущаяся плотность гсм3
Открытая пористость %
Предел прочности при сжатии Нмм2не менее
Температура начала деформации под нагрузкой 02 МПа °C не менее
Термостойкость теплосмены (1300°C- вода)
Теплопроводность Вт(мК) не болеепри температуре1000°C
Дополнительная линейная усадка при температуре 1650°C %не более
Изделия марки ПШАМ-1 используются для футеровки рабочего слоя дуговых печей сталеразливочных ковшей печей-ковшей внепечной обработки стали других тепловых агрегатов черной и цветной металлургии.
Изделия марки ПШАМ-2 изготовлены на основе плавленого периклаза и предназначены для использования в футеровке сталеразливочных ковшей и других тепловых агрегатов.
Изделия марки ПШАС предназначены для футеровки агрегатов внепечной обработки стали.
Изделия марки ПШАЦ используются для футеровки вращающихся печей цементной промышленности.
Одним из перспективных направлений применения периклазошпинельных огнеупоров является стекольная промышленность.
Цена на переклазошпинельные огнеупоры выше чем на традиционно используемые для футеровки конвертеров магнезитовые огнеупоры примерно на 30%. Однако за счет их большей стойкости межремонтная кампания конвертеров согласно данных практики увеличится на 15%. В свою очередь сокращение времени простоев оборудования в планово – предупредительных ремонтах в течении года позволит увеличить и общий годовой объем производства.
ТЕХНОЛОГИЧЕСКИЕ РАСЧЕТЫ
1 Материальный баланс
1.1 Исходные данные для расчёта
Таблица 3.1 – Средневзвешенный состав исходных материалов %
1.2 Рациональный состав штейна
Как следует из известных данных для заводских медных штейнов можно принять сумму Cu2S + FeS + Fe3O4 ~ 97%. Для штейна содержащего 30% Cu интерполяцией данных той же таблицы находим содержание серы 248%. Всю медь принимаем связанной в Cu2S и подсчитываем количество Cu2S в 100 кг штейна:
(159127) * 30 = 3756 кг.
остается серы на FeS
С ней связано железа
(559321) * 1724 = 3002 кг.
02 + 1724 = 4726 кг.
- 3756 – 4726 = 1218 кг
(1677232) * 1218 = 88 кг
Связано в магнетит кислорода
Полученный в результате расчетов рациональный состав штейна приведен в таблице 3.2
Таблица 3.2 - Рациональный состав медного штейна кг
1.3 Расчет состава кварцевого флюса
Примем что вся сера содержащаяся в кремнистой руде связана с медью и железом в халькопирит CuFeS2. Подсчитываем количество меди связанной в халькопирит:
(635642) * 07 = 07 кг.
Железа в халькопирите
(559642) * 07 = 061 кг.
Количество халькопирита
+ 07 + 061 = 201 кг.
Оставшаяся от халькопирита медь в количестве
4 - 07 = 024 кг связана в куприт Cu2О.
Кислорода в куприте
(16127) * 024 = 003 кг.
Оставшееся от халькопирита железо в количестве
- 061 = 065 кг связано в лимонит.
Количество кислорода связанного с железом в лимонит:
(481118) * 069 = 029 кг.
Кристаллической влаги в лимоните
(541118) * 069 = 033
Глинозем примем связанным в каолинит тогда кремнезема в каолините будет:
(1201022) * 25 = 293 кг.
Кристаллической влаги в каолините
(36102) * 25 = 088 кг.
Количество каолинита
+ 293 + 088 = 631 кг.
Оставшийся от каолинита кремнезем находится в форме кварца в количестве
СаО примем связанной в известняк СаСОз тогда углекислоты связанной с СаО будет
(44561) * 01 = 008 кг.
Количество известняка
Полученный в результате расчетов рациональный состав окисленной кремнистой руды приведен в таблице 3.3
Таблица 3.3 - Рациональный состав кварцевого флюса кг
1.4 Определение состава конвертерного шлака
В основу определения состава конвертерного шлака может быть положен ряд закономерностей выявленных заводской практикой и исследованиями процесса конвертирования:
а) Содержание меди в конвертерных шлаках колеблется обычно от 1 до 3% а кремнезема от 20 до 30%.
Данные заводской практики показывают что при бедных штейнах обычно работают на шлаках с умеренным содержанием кремнекислоты.
б) Содержание магнетита в конвертерных шлаках зависит от содержания кремнезема и может приниматься в соответствии с выявленными закономерностями. При этом должно быть предусмотрено такое содержание магнетита в шлаках которое обусловливало бы положительный баланс магнетита в процессе конвертирования т. е. чтобы количество магнетита в шлаках было несколько выше количества магнетита поступающего в конвертер со штейном и холодными материалами. Целью такого режима ведения процесса является стремление предохранить от разрушения магнетитовый гарниссаж в конвертере и тем увеличить стойкость футеровки.
в) Суммарное содержание кремнезема магнетита и закиси железа в конвертерных шлаках зависит главным образом от состава кварцевого флюса и состава холодных оборотов. При использовании чистых кварцитов содержащих выше 90% SiO2 и обычных цеховых оборотных холодных материалов сумма SiO2 + Fe3O4 + FeO в шлаке составляет 90 - 95%. При использовании малокремнистых флюсов (60 - 70% Si02) загрязненных глиной известняком и другими компонентами а также при загрузке в конвертер каких-либо загрязненных оборотов сумма этих компонентов в шлаке снижается до 80 - 85%.
Для упрощения расчетов допускаем что вся медь в конвертерном шлаке находится в форме Cu2S. Сульфид железа FeS в шлаке содержится в количестве пропорциональном содержанию FeS в штейне.
На основании изложенного принимаем содержание меди в конвертерном шлаке 25% сумма SiO2 + Fe3O4 + FeO = 85%:
%FeO = 85 - %Si02 - %Fe3O4.
По известному графику находим что балансовое содержание магнетита в конвертерном шлаке для 30% - ного штейна составляет 14% а содержание SiO2 равно 27%.
Содержание магнетита в шлаке нужно выбрать несколько выше балансового соответственно снизив содержание SiO2.
Примем содержание SiO2 в шлаке 25%. По экспериментальному графику находим что при такой кислотности шлака среднее содержание магнетита 16%.
Содержание FeO в шлаке
Примем что вся закись железа связана с кремнеземом в файялит 2FeO SiO2 тогда количество кремнезема в файялите на 100 кг шлака
(60143) * 44 = 183 кг.
Количество файялита:
Остается свободного кварца
Количество Cu2S по меди
(1591127) * 25 = 313 кг.
Серы на образование Cu2S идет
Поскольку при продувке штейна в конвертере он постепенно обогащается а содержание FeS в штейне снижается от начального практически до 0 (в белом матте) расчетное содержание FeS в конвертерном шлаке примем как среднее этих пределов т.е. 2363%.
По известному графику находим что такому содержанию FeS в штейне соответствует 41% FeS в конвертерном шлаке.
Полученный в результате расчетов рациональный состав конвертерного шлака приведен в таблице 3.4
Таблица 3.4 - Рациональный состав конвертерного шлака кг.
1.5 Состав и количество холодных материалов
Холодные материалы загружаемые в конвертер для регулирования температуры процесса имеют весьма разнообразный состав. Обычно в качестве холодных оборотов при конвертировании 'медных штейнов служат: холодный штейн того же состава что и горячий (корки от чистки штейновых желобов корки из штейновых ковшей случайно разлитый из штейновых ковшей в цехе или специально заготовленный холодный штейн) богатые шлаки из печей огневого рафинирования меди оборотные материалы самого процесса конвертирования - выплески массы и шлака настыли снятые с горловины и напильника пыль уловленная в газоходе и т. п.
В том случае когда технологическая схема завода не предусматривает огневого рафинирования черновой меди а конвертер также загружают выплески черновой меди и другой медный скрап получаемый при отливке штыков и их обработке.
Таким образом в холодных материалах может содержаться металлическая медь сульфиды и разнообразные окислы из конвертерного шлака и флюсов.
Примем что 50% меди содержащейся в холодных материалах находится в металлическом виде а остальные 50% в форме Cu2S.
При расчете на 100 кг холодных получим что в них металлической меди содержится 6 кг и меди в виде Cu2S - 6 кг.
(1591127) * 6 = 75 кг.
Приняв что оставшаяся сера связана с железом в FeS находим количество FeS:
(88321) * 6 = 165 кг
Остальное железо должно находиться в окисленной форме в виде FeO и Fe3O4. Примем что вся закись железа связана с кремнеземом в файялит 2FeO SiO2.
Из рационального состава конвертерного шлака (таблица 3.3) находим что отношение свободного кремнезема к общему содержанию кремнезема составляет около 1 : 4.
Поскольку кремнезем в холодных материалах в основном присутствует за счет конвертерного шлака можно считать что это отношение сохранится и для холодных материалов. Тогда в холодных материалах свободного кремнезема будет
Связано кремнезема в 2FeO SiO2
Количество FeO связанное в файялит:
(143860) * 128 = 309 кг.
(559719) * 309 = 24 кг.
Остается железа на магнетит
Количество магнетита
(23171677) * 95 = 131 кг
Рациональный состав холодных материалов приведен в таблице 3.5.
Таблица 3.5 - Рациональный состав холодных материалов (обороты медеплавильного завода) кг
Количество холодных материалов необходимое для поглощения избытка тепла возникающего в первом периоде процесса конвертирования штейнов содержащих до 45 - 50% Cu ориентировочно можно определять по графику составленному на основании тепловых расчетов.
По графику находим что при переработке штейна содержащего 30% Cu необходимо загрузить в конвертер около 28% холодных материалов.
В последующем эта величина проверяется по тепловому балансу конвертера.
1.6 Расчеты технологического процесса первого периода
) Количество конвертерного шлака и кремнистой руды
Все расчеты ведутся на 100 кг горячего штейна.
х кг — количество конвертерного шлака образующегося на 100 кг горячего штейна;
у кг — потребное количество кремнистой руды.
Железа в конвертер поступает кг:
Из 100 кг горячего штейна
Из 28 кг холодных материалов
Из у кг кремнистой руды
Всего поступает железа
Количество железа в х кг шлака
При полном извлечении железа в шлак должно быть справедливо уравнение
14 + 0013 * у = 04838 * х (а)
Кремнекислоты в конвертер поступает кг:
Количество SiO2 в х кг конвертерного шлака 025 * х кг. При полном переходе всей кремнекислоты в конвертерный шлак должно быть справедливо уравнение
6 + 09235 * у = 025 * х (б)
Решая уравнения (а) и (б) находим
х = 10633 кг; у = 2327 кг.
) Количество FeS участвующее в процессе
Со штейном и холодными материалами в конвертер поступает
26 + 28 * 0165 = 5188 кг FeS.
С кремнистой рудой поступает халькопирита
27 * 00201 = 046 кг.
Халькопирит в конвертере диссоциирует по реакции
CuFeS2 = Cu2S + 2FeS + S.
В результате реакции образуется:
(046367) * 1591 = 02 кг Cu2S
(046367) * 1758 = 022 кг FeS
(046367) * 32 = 004 кг S
С учетом диссоциации халькопирита в процесс вводится
88 + 022 = 521 кг FeS.
Часть FeS увлекается в шлак в виде корольков штейна в количестве
633 * 0041 = 436 кг.
Необходимо также учесть количество FeS взаимодействующее с Fe2Оз и Cu2О поступающими в ванну конвертера с кремнистой рудой.
В 2327 кг кварцевого флюса поступает:
27 * 00027 = 006 кг Cu2О;
27 * 00098 = 023 кг Fe2O3.
Примем что эти окислы взаимодействуют с FeS по реакциям:
FeS + Cu2O = FeO + (1)
FeS + 3Fe2O3 = 7FeO + S02. (2)
В реакции (1) участвует FeS в количестве
(0061432) * 8791 = 003 кг.
В результате реакции (1) образуется:
(0061432) * 719 = 003 кг FeO (в нем 0022 кг Fe);
(0061432) * 15911 = 0066 кг Cu2S.
В реакции (2) участвует FeS в количестве
(0234791) * 8791 = 0042 кг.
В результате реакции образуется
(0234791) * 5033 = 024 кг FeO (в нем 018 кг Fe)
(0234791) * 64 = 003 кг SО2.
В результате потерь со шлаками и реакций окисления за счет кислорода высших окислов из штейна выводится FeS в количестве
6 + 003 + 0042 = 443 кг.
Необходимо подвергнуть окислению кислородом дутья остальное сернистое железо в количестве
1 – 443 = 4767 кг (3032 кг Fe и 1735 кг S).
) Окисление железа и серы
В конвертерном шлаке содержится железа в форме магнетита:
633 * 01157 = 123 кг.
С горячим штейном железа в форме магнетита вводится 88 кг. С холодными материалами железа в форме магнетита поступает
Всего в процесс поступает железа в форме магнетита
Окисляется железа кислородом дутья до магнетита
В конвертерном шлаке содержится железа в форме FeO
633 * 0342 = 3636 кг.
С холодными материалами поступает железа в виде FeO
Кроме того окисляется железа до FeO по реакциям (1) и (2)
Окисляется железа кислородом дутья до FeO
36 – 672 – 02 = 2944 кг.
Количество кислорода для окисления железа по реакции 3Fe + 2O2 = Fe304 (3) составит
(641677) * 084 = 032 кг.
Количество кислорода для окисления железа по реакции 2Fe + О2 = 2FeO (4) составит
(321118) * 2944 = 842 кг.
Всего на окисление железа теоретически требуется кислорода
В первый период конвертирования окисляется 1735 кг серы сернистого железа. Кроме того имеется 004 кг элементарной серы образовавшейся в результате диссоциации халькопирита. Следовательно окисляется всего 1739 кг серы.
На основании экспериментальных данных примем что отношение количества серы окисляющейся до SO2 к количеству серы окисляющейся до SO3 составляет 6:1.
Окисляется серы до SO2
(17397) * 6 = 149 кг (образуется 298 кг SО2 требуется кислорода 149 кг).
Окисляется серы до SО3
(17397) * 1 = 248 кг (образуется 621 кг SO3 требуется 373 кг кислорода)
Всего на окисление серы теоретический расход кислорода составит 149 + 373 = 1863 кг.
Всего на окисление железа и серы теоретически необходимо кислорода 874 + 1863 = 2737 кг.
Приняв на основании данных практики использование кислорода ванной конвертера 95% находим практически необходимое количество кислорода:
(2737095) = 2881 кг.
При 23% содержания кислорода в воздухе необходимо в I периоде подать воздуха
(2881023) = 12526 кг или (12526129) = 971 м3.
С воздухом подается азота
226 - 2881 = 9645 кг.
В первом периоде в конвертер загружается 2327 кг кварцевого флюса из которого в газы выделится влага в количестве
27 * 00121 = 028 кг.
Выделяющейся в газы из руды углекислотой пренебрегаем ввиду ее малого количества.
На основании выполненных расчетов находим количество и состав конвертерных газов I периода (таблица 3.6).
Таблица 3.6 - Количество и состав газов 1 периода
1.7 Количество белого матта
Белый матт содержит Cu2S металлическую медь и примеси. В конвертер поступает Cu2S кг:
Из 100 кг горячего штейна
Из 30 кг холодных материалов
В результате диссоциации CuFeS2 в конвертере образуется 02 кг Cu2S.
По реакции Cu2O + FeS = Cu2S + FeO образуется еще 0066 кг Cu2S.
Общее количество Cu2S поступившее и образовавшееся в конвертере:
66 + 02 + 0066 = 39926 кг.
С конвертерным шлаком увлекается
633 * 00313 = 333 кг Cu2S.
Остается в белом матте
926 - 333 = 36596 кг Cu2S (2922 кг Cu и 7376 кг S).
Примем что металлическая медь поступающая в конвертер с холодными материалами полностью переходит в белый матт в количестве 28 * 006= 168 кг.
Общее количество Cu2S и металлической меди образующих белый матт:
596 + 168 = 38276 кг.
Примем что сумма меди и серы в белом матте составляет 955% и 45% приходится на прочие. Находим количество белого матта:
(382760955) = 4008 кг.
1.8 Материальный баланс первого периода
Результатом расчетов технологического процесса первого периода является развернутый материальный баланс (таблица 3.7). При условии правильного выполнения всех приведенных выше расчетов составление баланса не вызывает затруднений. Невязка баланса может обнаружиться лишь в графе «прочие» поскольку количество прочих в статьях прихода и расхода принимается произвольно без достаточной предварительной увязки. В случае обнаружения такой неувязки она обычно уничтожается соответствующей корректировкой количества и процентного состава шлаков.
Таблица 3.7 – Материальный баланс первого периода
1.9 Расчет технологического процесса второго периода
При продувке белого матта полусернистая медь окисляется с образованием металлической меди SO2 и SO3.
Как правило второй период процесса ведется без остановок дутья и без добавления холодных материалов.
Продуктами процесса являются черновая медь газы и небольшое количество так называемой изгари образующейся из примесей содержащихся в белом матте остатков шлака от первого периода и окислившейся меди.
Примем по практическим данным извлечение меди из белого матта в черновой металл (без пылеуноса) 988 %. Количество меди извлекаемой в черновой металл:
При содержании в черновой меди 988% Cu количество меди
(30740988) = 3111 кг.
Серы в черновой меди 020% что составляет
(3111 * 00020) = 006 кг.
Всего серы в белом матте 738 кг следовательно необходимо окислить серы
Примем что во втором периоде сера окисляется до SO2 и SO3 в соотношении 5:1.
До SO2 окисляется серы
(7326) * 5 = 61 кг (образуется 122 кг SO2 и 61 кг O2).
До SO3 окисляется серы
(7326) *1=122 кг (образуется 303 кг SO3 и 181 кг O2)
Общий теоретический расход кислорода на окисление серы
При 95% использования кислорода ванной конвертера практически необходимое количество кислорода составляет
Воздуха потребуется
(832023) = 3617 кг или (3617129) = 2804 м 3 .
С воздухом поступает азота
Количество и состав газов второго периода приведены в таблице 3.8 а материальный баланс второго периода в таблице 3.9.
Таблица 3.8 - Количество и состав газов второго периода
Таблица 3.9 - Материальный баланс второго периода
1.10 Сводный материальный баланс конвертирования
При составлении сводного материального баланса (таблица 3.10) учитывается пылеунос в размере 1 % от всех жидких и твердых материалов загружаемых в конвертер. От суммарного прихода каждого из элементов шихты в пыль снимается 1%. В результате соответственно уменьшается количество данного элемента в жидких продуктах процесса - черновом металле и шлаке пропорционально его содержанию в этих продуктах.
Распределение меди между черновым металлом и шлаком:
В черновом металле меди
Соответственно этому распределению за счет чернового металла снимается в пыль
Получаем в черновом металле
74 - 03 = 3044 кг Cu.
Аналогично рассчитывается унос в пыль всех других элементов.
Таблица 3.10 – Сводный материальный баланс процесса конвертирования медного штейна
2.1 Пропускная способность конвертера по воздуху
На основании сводного материального баланса находим практический удельный расход воздуха на 1 т штейна:
Vуд = (1614301 * 129) = 1250 м3т
Приняв по данным практики коэффициент использования конвертера под дутьем К = 075 найдем необходимую пропускную способность конвертера из формулы:
Vконв = (250 * 12501440 * 075) = 289 м3мин
2.2 Удельная нагрузка фурм конвертера
Находится по формуле:
g = 174√ ((p1-Hгидр)С).
Примем на основании данных практики давление на коллекторе p1 = 12 кгсм2 противодавление ванны Hгидр = 03 кгсм2 значение показателя гидравлического сопротивления воздухораспределительной системы применяемой в настоящее время конструкции С = 60:
2.3 Площадь сечения работающих фурм
Fф = (Vконв g) = 289067 = 431 см2
2.4 Число работающих фурм
Приняв на основании практических данных диаметр фурменных трубок d = 46 мм получим по формуле необходимое число одновременно работающих фурм:
nр = 1272 * ( Fфd2) = 1272 * (4312116) = 26
2.5 Число установленных фурм
С учетом резерва 20% число установленных фурм:
2.6 Тип и размеры конвертера
Исходя из найденных значений площади сечения фурм Fф = 431 см2 диаметра фурм d = 46 мм и числа фурм пуст = 31 выбираем стандартный горизонтальный конвертер с размерами по кожуху 366 X 61 м и емкостью по черновой меди 40 т.
2.7 Проверка размеров горловины
Проверяем сечение горловины выбранного конвертера по скорости газов.
В соответствии с технологическим расчетом общее количество газов за оба периода на 1 т штейна
Vгазуд = (9066 + 2766)01 = 1183 нм3т.
По формуле для производительности А = 250 тсутки находим секундное количество конвертерных газов при t = 1000°:
Vt = A * Vгазуд * (273 + t)(86400 * K * 273) = 228 м3сек.
Скорость газов в сечении горловины составит
wt = VtFгорл = 706 мсек.
Поскольку полученное значение скорости газов не превышает пределов установленных практикой (8 - 12 мсек) стандартные размеры горловины не нуждаются в изменениях.
2.8 Параметры воздуходувной машины и расчет воздухопроводов
По формуле производительность воздуходувной машины с учетом 10% резерва на восполнение потерь
Vвозд = 11 * vконв = 11 * 289 = 320 м3мин.
Давление дутья на воздуходувке с учетом 20% резерва по формуле
pвозд = 12 * p1 = 144 aти
Секундное количество воздуха проходящего по воздухопроводу на 1 конвертер при давлении 144 ати и t = 60°:
Vt p = (28960 * 244) * (273+60)273 = 24
При скорости воздуха wt р = 20 мсек диаметр воздухопровода
d = 113 * √( Vt p wt р) = 04 м.
2.9 Определение числа операций
При заданной производительности конвертера по горячему штейну А = 250 тсутки черновой меди будет получено
0 * 0308 = 77 тсутки.
При емкости конвертера по черновой меди до 40 т операций в сутки
2.10 Выход черновой меди
Выход черновой меди от веса горячего штейна тт:
143(129*01) = 125139
2.13 Расход кварцевого флюса
Расход кварцевого флюса тт:
Тепловой баланс процесса рассчитывается на основании данных материальных балансов по периодам при значениях температур и теплоемкостей материалов и продуктов процесса принимаемых по данным практики и исследований (таблица 4.1).
Таблица 4.1 - Температуры и теплоемкости материалов и продуктов
процесса конвертирования медного штейна
Теплоемкость МДжкг* 0С
Поверхность кожуха конвертера
Внутренняя полость конвертера
1 - Тепловой баланс первого периода
Тепло горячего штейна
Qшт = Gштсштtшт = 100 * 084 * 1100 = 924 МДж.
Qв = Vвсвtв = 971 * 13 * 60 = 0007 МДж.
Тепло реакций окисления железа (расчет по железу):
а) 3Fe + 2О2 = Fe3O4 + 111713 МДж;
g1 = (11171301677) * 084 = 56 МДж
б) Fe + 12О2 = FeO + 26652;
g2 = (266520559) * 2944 = 14036 МДж
Всего от окисления железа до магнетита и закиси
QFe = g1 + g2 = 56+ 14036 = 14596 МДж
Тепло реакций окисления серы (расчет по сере):
a) S + О2 = SO2 + 2969 МДж;
g1 = (2969321) * 149 = 13781 МДж
б) S + 12О2 = SO3 + 39518;
g2 = (39518321) * 248 = 3053 МДж
Всего от окисления серы
Qs = g1 + g2 = 13781 + 3053 = 16834 МДж
Тепло реакций шлакообразования (расчет по количеству железа окисляющегося до FeO которого имеем 2944 + 0022 + 018 = 2964 кг):
Qошл = (497901118) * 2964 = 132 МДж.
Тепло прочих экзотермических реакций:
FeS + Cu2O = FeO + Cu2S + 8426 МДж (расчет по количеству Cu2O которой имеем 006 кг);
Qпроч = (84261432) * 006 = 0035 МДж.
Всего приход тепла составит
Qприх = Qшт + Qв + QFe + Qs + Qошл + Qпроч =
= 924 + 00075 + 14596 + 16834 + 132 + 0035 = 41994 МДж
Q6.м = Gб.мcб.мtб.м = 4008 * 075 * 1250 = 3757 МДж.
Qшл = Gшлcшлtшл = 10633 * 123 * 1200 = 15604 МДж.
Qг = (VSO2 * cSO2 + VSO3 * cSO3+VN2cN2+VH2OcH2O) * tг = (104 * 224 + 174 * 389 + 100 * 147 + 7718 * 14 + 034 * 171) * 1000 = 14017 МДж
Тепло эндотермических процессов:
a) FeS = Fe + S – 9506 МДж (расчет по количеству сульфидного железа которого имеем 3032 кг);
Qдис = (9506559) * 3032 = 5156 МДж.
б) FeS + 3Fe 2O3 = 7FeO + SO2 - 39899 МДж (расчет по количеству Fe2O3 которого имеем 023 кг);
Q = (39899 4791) * 023 = 019 МДж
в) Тепло на испарение 028 кг влаги кремнистой руды
Всего на эндотермические процессы затрачивается тепла
56 + 019 + 07 = 5245 МДж.
Потери тепла во внешнюю среду.
Рассчитываем балансовое время переработки 100 кг штейна при суточной производительности 250 тсутки:бал = (24250) * 01 = 00096 часа.
Балансовое время I и II периодов определяется из отношения количества воздуха поданного в I и II периодах:
= (0009616143) * 12526 = 00074 часа
= (0009616143) * 3617 = 00022 часа
а) Потеря тепла ребристостью кожуха конвертера.
Поверхность кожуха конвертера вычисляется как поверхность цилиндра диаметром 366 и длиной 61 м за вычетом площади горловины (17 * 19) с учетом ребристости кожуха.
Коэффициент ребристости по практическим данным можно принимать реб = 13 - 15. Приняв реб = 14 получим Fст = 12306 м2
Удельную потерю тепла стенками (конвекцией и излучением) определяем по экспериментальному графику.
При температуре наружной поверхности кожуха 200° qуд = 1464 МДжм2 * час:
Qст = qуд * Fст * t1
Qст = 1464 * 12306 * 00074 = 1333 МДж
б) Потеря тепла излучением через открытую горловину.
Приняв коэффициент диафрагмирования Ф = 07 при температуре внутренней полости конвертера 1300° находим
qуд = 8368 МДжм2*час
Qизл = qуд * Fст * 1
Qизл = 8368 * 323 * 00074 = 20 МДж
Всего потери тепла во внешнюю среду
Qвн = Qст + Qизл = 1333 + 20 = 3333 МДж
Всего расход тепла составит:
Qрасх = Qб.м + Qшл + Qгаз + Qэнд + Qвн =
= 3757+ 15604 + 14017 + 5245 + 3333 = 41956 МДж
На основании проделанных расчетов составляем тепловой баланс первого периода (таблица 4.2).
Таблица 4.2 - Тепловой баланс первого периода (на 100 кг горячего штейна)
Тепло реакции окисления железа
Тепло реакции окисления серы
Тепло эндотермических реакций
Тепло шлакообразования
Потери тепла во внешнюю среду
Тепло прочих экзотермических реакций
Неучтенные потери и
Хорошая сходимость баланса (невязка менее 1%) показывает что количество холодных было принято верно. В том случае когда обнаруживается значительная невязка баланса необходимо изменить количество холодных.
2 – Тепловой баланс второго периода
Тепло белого матта (рассчитано в первом периоде):
Qв = Vвсвtв = 2804 * 13 * 60 = 219 МДж.
Тепло реакций окисления серы:
а) Реакция S + О2 = S02 +2969 МДж;
q1 = (2969 321) * 61 = 5642 МДж.
б) Реакция S + 12O2 = SO3 + 39518 МДж;
q2 = (39518321) * 122 = 1502 МДж.
Всего от окисления серы:
Qs= 5642 + 1502 = 7144 МДж.
Qприх = Q6 м + QB + Qs = 3757 +219 + 7144 = 1112 МДж.
Тепло черновой меди при t = 1200°
Qм = 3111 * 045 * 1200 = 168 МДж.
Тепло газов при t = 1200°
Qг = tг * (VSO2 * cSO2 + VSO3 * cSO3+Vо2 * cO2 +VN2*c N2) = 1200(428 * 228 + 085 * 391 + 029 * 15 + 2224 * 142) = 541 МДж.
Тепло эндотермических реакций Cu2Sж = 2 Cuж + S – 9635 МДж
Qэнд = (9635321) * 732 = 2200 МДж.
а) Потеря тепла стенками: для t кож = 300° qуд = 2928 МДжм2 * час;
Qст = 2928*12306*00022 = 792 МДж.
б) Излучение горловиной: для tвнут = 1350 оС и Ф = 07 qуд = 100416 МДжм2 * час.
Qизл = 100416 * 323 * 00022 = 713 МДж.
Qвн = Qcг + Qизл = 792 + 713 = 1510 МДж.
Qрасх = Qм + Qг + Qэнд + Qвн = 1680 + 5410 + 2200 + 1510 = 1080 МДж.
На основании проделанных расчетов составляем тепловой баланс второго первого периода и сводный тепловой баланс (таблицы 4.3 4.4).
Таблица 4.3 – Тепловой баланс второго периода
Тепло теряемое во внешнюю среду
Неучтенные потери и невязка баланса
Таблица 4.4 – Сводный тепловой баланс конвертера перерабатывающего медный штейн
Тепло эндотермических
ХАРАКТЕРИСТИКА ОТХОДЯЩИХ ГАЗОВ И СХЕМЫ ПЫЛЕУЛАВЛИВАНИЯ
Значительная запыленность газов конвертеров применяемых в производстве меди имеет среднее значение концентрации пыли 10 - 15 гм3 и высокую дисперсность. Температура технологических газов на выходе из конвертеров может достигать 1000-1200 °С. Содержание SO2 в газах непостоянно и колеблется в зависимости от величины подсосов на напыльнике и по газовому тракту от 4 до 6 %. Совокупность этих характеристик диктует необходимость предварительной подготовки газов перед их тонкой очисткой: снижение температуры и уменьшение начальной запыленности. Поэтому требуется применение ступенчатой очистки. Исходя из этого выбираем схему очистки газов от пыли представленную на рисунке 5.1.
1 Описание выбранной схемы
Повышенное содержание в газах сернистого ангидрида допускает применение только сухих пылеуловителей. Очищать газы от крупных частиц пыли целесообразно в циклонах устанавливаемых непосредственно у печей.
Циклоны - одни из наиболее распространенных пылеулавливающих аппаратов. Работа циклона основана на использовании центробежных сил возникающих при вращении газового потока внутри корпуса циклона. Это вращение достигается путем тангенциального ввода газа в циклон. В результате действия центробежных сил частицы пыли взвешенные в потоке газа отбрасываются на стенки корпуса и выпадают из потока. Запыленный газ обычно вводят через входной патрубок в верхнюю часть корпуса циклона представляющего собой цилиндр заканчивающийся в нижней части конусом (рисунок 2). Как правило циклоны выполняют из листовой стали толщиной 4-8 мм. При улавливании высокообразивной пыли стенки циклонов защищают от истирания покрывая их базальтовыми плитками или другими материалами. При очистке газов с высокой температурой (свыше 400 °С) внутреннюю поверхность корпуса необходимо футеровать огнеупорным кирпичом. После входа в циклон со скоростью 20-25 мс газовый поток образует внешний вращающийся вихрь постепенно опускающийся вниз. Частицы пыли выброшенные из потока центробежной силой тоже двигаются вниз по стенкам корпуса накапливаясь в нижней части циклона. Газ освобожденный от пыли продолжая вращаться переходит во внутренний вихрь и уходит из циклона вверх через выхлопную трубу. Циклон необходимо периодически освобождать от уловленной пыли выгружая ее через специальные герметические устройства в пылесборные бункеры установленные внизу под циклоном. В циклонах степень улавливания пыли составляет от 70% .до 85 %.
Использование циклонов позволяет предотвратить засорение пылью длинных газоходов снижает запыленность газов перед аппаратами тонкой очистки и повышает содержание высокодисперсных фракций металлов в пыли. Предварительная очистка газов снижает концентрацию пыли до 10-
гм3 температуру до 380-390 °С.
Из циклона посредством вентилятора газы соответствующие требованиям необходимым для дальнейшей тонкой очистки направляются в сухой электрофильтр.
Электрофильтры достаточно широко используют в цветной металлургии. Корпус фильтра выполняют из листовой стали бетона кирпича листового свинца и других материалов в зависимости от температуры и агрессивности газов. В корпусе электрофильтра размещают осадительные и коронирующие электроды обеспечивающие ионизацию запыленного газа за счет коронного разряда устройство для удаления осажденной пыли решетки для равномерного распределения газа по сечению и др. Принципиальная схема электрофильтра состоит из ряда параллельных пластин или труб играющих роль осадительных поверхностей (рисунок 5.3).
Между этими пластинами соединенными с заземлением располагают коронирующие электроды в виде провода круглого или квадратного сечения либо в виде колючей проволоки. На коронирующие электроды подают отрицательное напряжение величина которого ограничена (25-100 кВ) так как проводимость ионизированного газа настолько увеличивается что между электродами происходит замыкание. Запыленный газ подают в нижнюю часть электрофильтра. Затем газовый поток направляют вертикально вверх. Получившие заряд частицы пыли оседают на осадительных поверхностях после чего ее удаляют встряхиванием электродов. Степень улавливания пыли в электрофильтрах достигает 980 - 995 %.
- источник постоянного тока высокого напряжения; 2 - коронирующий электрод игольчатого типа; 3 - пластинчатые осадительные электроды; 4 - заземление;5 - пылесборный бункер; 6 - газораспределительное устройство
Рисунок 5.3 - Принципиальная схема электрофильтра
Надежная и устойчивая работа электрофильтров достигается при скорости газов 07-08 мс. После тонкой очистки содержание пыли в газе не превышает 01.-015 гм3 и поэтому далее газы могут быть использованы для получения серной кислоты.
В данном курсовом проекте приведен расчет отделения конвертирования медных штейнов производительностью 70 тыс.т черновой меди в год.
Рассчитаны материальный тепловой балансы представлено описание расчет и выбор оборудования для конвертерного отделения пылегазоочистки. Предложены мероприятия по увеличению стойкости футеровки в зоне фурменного пояса за счет применения более стойких и плотных периклазошпинельных огнеупоров.
СПИСОК ИСПОЛЬЗОВАННОЙ ЛИТЕРАТУРЫ
Диомидовский Д.А. Расчеты пиропрцессов и печей цветной металлургии.Д.А. Диомидовский Л.М. Шалыгин. - М: Металлургия1963. 460 с.
Гущин С.Н. Теплотехника и теплоэнергетика металлургического производства С.Н. Гущин [и др.]– М.: Металлургия 1993. 368с.
Кабахидзе В.В. Тепловая работа и конструкции печей цветной металлургии. В.В. Кабахидзе – М.: МИСиС 1994. 356с.
Набойченко С.С. Процессы и аппараты цветной металлургии С.С. Набойченко [и др.]. Екатеринбург: УГТУ-УПИ 1997. 648с.
Васильев Б.Т. Технология серной кислоты. Б.Т. Васильев М.И. Отвагина. – М.: Химия 1985 384 с..
Логинова И.В. Оформление дипломных и курсовых проектовсост. И.В. Логинова Н.П. Пенюгалова. Екатеринбург: ГОУ ВПО УГТУ–УПИ 2004. 45 с.
Рекомендуемые чертежи
- 25.01.2023
- 29.07.2014
Свободное скачивание на сегодня
Другие проекты
- 20.08.2014