Мостовой кран г/п 20 т. V подъема 10 м/мин




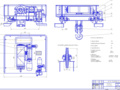
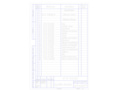
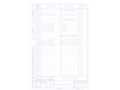
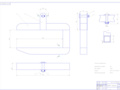
- Добавлен: 25.10.2022
- Размер: 1 MB
- Закачек: 0
Описание
Состав проекта
![]() |
![]() ![]() |
![]() ![]() |
![]() ![]() ![]() ![]() |
![]() ![]() ![]() |
![]() ![]() |
![]() ![]() |
![]() ![]() ![]() ![]() |
![]() ![]() ![]() ![]() |
![]() ![]() ![]() ![]() |
Дополнительная информация
ВО.dwg

) Высота подъема 10 м.
) Продолжительность включения 25%
) Грузоподъемность 20т.
) Скорость механизма:
-механизма подъема 4А250М4У3 - 90 кВт
-механизм передвижения MTF 311-6 - 17
-механизма подъема Ц2-500
-механизм передвижения ВКН-420
Установка уравнительного блока
Записка краны.docx
Федеральное государственное бюджетное образовательное
Учреждение высшего образования
«Тульский государственный университет»
Кафедра Подъемно-транспортные машины и оборудование
ВЫБОР И РАСЧЕТ ЗАХВАТНОГО ОРГАНА3
РАСЧЕТ МЕХАНИЗМА ПОДЪЕМА12
1 Определение кратности полиспаста13
2 Определение усилия в канате набегающем на барабан13
4 Определение требуемого диаметра блоков и барабана14
5 Выбор крюковой подвески15
6 Определение размеров барабана15
8 Определение передаточного числа привода17
10 Выбор муфты быстроходного вала18
11 Выбор муфты тихоходного вала19
12 Определение пусковых характеристик механизма19
13 Расчет электромагнитного колодочного тормоза21
14 Определение тормозных характеристик механизма21
15 Проверка двигателя на нагрев22
РАСЧЕТ МЕХАНИЗМА ПЕРЕДВИЖЕНИЯ24
1 Выбор типа привода24
2 Определение числа ходовых колес24
3 Кинематическая схема механизма24
4 Определение массы крана25
5 Выбор ходовых колес25
6 Определение сопротивления передвижению крана26
8 Определение передаточного числа привода27
10 Выбор муфты быстроходного вала28
11 Определение пусковых характеристик механизма29
12 Выбор тормоза и определение тормозных моментов31
13 Проверка пути торможения32
14 Проверка двигателя на нагрев32
ВЫБОР И РАСЧЕТ ЗАХВАТНОГО ОРГАНА
На производстве будем использовать промышленный кантователь для поворота
рулона в удобное положение для захвата.
Поворот рулона во время перемещения будем совершать с помощью крюковой подвески (крюк поворачивается относительно своей оси).
Определение расчетных нагрузок
Номинальная масса груза = 786 ·(154-007)·15=1733 т где γ - плотность стали; V – объем рулона стали.
С учетом коэффициента перегрузки собственного веса kг = 105 сила тяжести груза будет составлять = 105·981·1733 = 17851 кН.
По рассчитанным нагрузкам принимаем(табл.1) с-образный захват 4МВ4-1801500 с грузоподъемностью 18т массой 1486 кг. и максимальной шириной рулона 1500мм.
Представим эту нагрузку в виде равномерно распределенной сил тяжести рулона на основную часть захвата = 17851 1500 = 012 кНмм.
Построение расчетных схем
По варианту захвата груза С-образным захватом рассмотренному выше расчетная схема представляется в виде рамы с опорной точкой в узле подвеса захвата к крюковой подвеске.
Рис.2.4. Расчетная схема захвата на действие нагрузок при штатном подъеме рулона
Расчетные нагрузки при штатном случае нагружения:
-Продольная сила – N:
-Поперечная сила – Q:
Q – сумма проекций всех сил на ось перпендикулярную к оси участка.
-Изгибающий момент – М:
Рис.2.4. Расчетная схема захвата на действие нагрузок при подъеме и зацепе рулона за захват на расстоянии от края (критическое положение)
Расчетные нагрузки при критическом случае нагружения:
Подбор сечений захвата
Металлоконструкцию захвата выполняем из стали марки 09Г2С–12 ГОСТ 19282-73 с характеристиками механических свойств: 330 МПа; 480 МПа;21 % [1 стр. 16 17]. Расчетное сопротивление листового проката толщиной от 10 до 20 мм по пределу текучести = 310 МПа по пределу прочности = 410 МПа [2 стр. 3–14].
Из условия прочности по нормальным напряжениям определяем требуемый момент сопротивления сечения по максимальному изгибающему моменту (пусть эта величина составляет = 186 кН·м).
Проектируем сечение захвата в виде сварного коробчатого сечения. Выполним приближенный подбор сечения задаваясь предварительно п = с = (рис. 2.6).
Рис.2.6. Схема поперечного сечения
Момент инерции сечения
Для обеспечения общей устойчивости захвата принимаем отношение высоты сечения к ширине .
тогда момент сопротивления сечения
Требуемая высота в опасном сечении:
увеличиваем размеры сечения до значений h = 220 мм; В = 220 мм = 20 мм
Уточненный момент инерции сечения
=14197 см4= 14197·10 – 5 м 4.
Проверяем условие прочности траверсы по нормальным напряжениям
коэффициент запаса прочности по пределу текучести составляет
что удовлетворяет условию прочности.
Распределение напряжений в сечении:
Проверка захвата на жесткость от действия статических нагрузок:
Прогиб считаем для штатного случая нагружения чтобы исключить соскальзывание рулона:
Отгиб консоли захвата определим с помощью интеграла Мора и его вычислением способом Верещагина (см. курс Сопротивления материалов)
Для этого сформируем единичное загружение в точках перемещения которых определяются и построим эпюру изгибающих моментов
Рис.2.9. Схема загружения балки единичными силами и эпюра
= 25 10 – 3 м = 25 мм
Относительный прогиб консоли
РАСЧЕТ МЕХАНИЗМА ПОДЪЕМА
В качестве исходных данных для расчета механизма подъема используем следующие данные:
- тип крана – мостовой двухбалочный;
- грузоподъемность Q =20 т;
- скорость подъема груза Vпод = 10 ммин = 017 мс;
- высота подъема Н = 16 м;
- режим работы крана 4А (Средний);
- продолжительность включения механизма подъема ПВ = 25%.
1 Определение кратности полиспаста
Кратность полиспаста механизма подъема груза выбираем в зависимости от грузоподъемности механизма. Принимаем Uп = 3 для сдвоенного полиспаста в соответствии с рекомендациями [1 c. 55 табл. 2.2].
Рис. 1 Схема полиспаста
2 Определение усилия в канате набегающем на барабан
где Q – номинальная грузоподъемность крана кг;
z – число простых полиспастов в системе;
Un – кратность полиспаста;
– общий КПД полиспаста и обводных блоков ().
где бл – КПД одного блока принимаем бл = 098 для подшипников качения.
где – количество обводных блоков (см. рис. 1).
Выбираем канат по расчетному разрывному усилию в канате:
где k – коэффициент запаса прочности принимаемый в зависимости от назначения
и режима работы крана принимаем k = 55 согласно [1 c. 55 табл. 2.3].
В соответствии с рекомендациями [1 c. 277 табл. III.1.1] принимаем канат двойной свивки типа ЛК-Р 6×19 (1 + 6 + 66) + 1о.с. диаметром d = 150 мм имеющий при маркировочной группе проволок 1950 МПа с разрывным усилием F =137000 H.
Обозначение каната: Канат 15 – Г – I – Н – 1950 ГОСТ 2688 – 80
– название изделия: ”канат”;
– диаметр наружного каната: d = 11 мм;
– назначение каната: Г – грузовой;
– марка проволок материала: I – первая;
– способ свивки: Н – нераскручивающийся;
– маркировочная группа прочности проволок: 1368 МПа;
Проверка фактического коэффициента запаса прочности каната:
4 Определение требуемого диаметра блоков и барабана
Допускаемый диаметр блока и барабана по средней линии навитого стального каната определяется по формуле:
где d – диаметр стального каната мм;
e – коэффициент зависящий от типа крана типа привода и режима работы
механизма принимаем e = 25 согласно [1 c. 59 табл. 2.7].
принимаем Dб = 410 мм.
5 Выбор крюковой подвески
В соответствии с рекомендациям [1 c. 298]. и принятой схемой (см. рис. 1) принимаем подвеску крановую с двумя блоками конструкции ВНИИПТМАШ.
D = 320 мм; dк = 11 мм; режим работы легкий; грузоподъемность 5 т;
6 Определение размеров барабана
Длина каната навиваемого на барабан с одного полиспаста определяется по формуле:
где H – высота подъёма груза м;
Dб – диаметр барабана м;
z1 – число запасных (неиспользуемых) витков на барабане до места крепления:
z1 = 15 2 согласно [1 c. 60];
z 2 – число витков каната находящихся под зажимным устройством на барабане
z2 = 3 4 согласно [1 c. 60].
Так как полиспаст в системе сдвоенный и z = 2 то общая длина всего каната будет вдвое больше.
Рабочая длина барабана для навивки каната с одного полиспаста определяется по формуле:
где Lк – длина каната навиваемого на барабан м;
t – шаг витка (см. рис. 2) принимается в зависимости от диаметра каната: при
d = 150 мм тогда t = 17 мм = 0017 м в соответствии с рекомендациями
[1 c. 60 табл. 2.8];
Рис. 2 Профиль канавок на барабане
m – число слоев навивки (для нарезного барабана m = 1);
d – диаметр каната м;
Dб – диаметр барабана по средней линии навитого каната м;
φ – коэффициент неплотности навивки: φ = 1 для нарезных барабанов
Полная длина барабана для сдвоенного полиспаста определяется по формуле:
где l – длина не нарезанной части барабана (определяется из данных крюковой подвески).
Определяем минимальную толщину стенок литого чугунного барабана по формуле:
где Dдна – диаметр дна барабана м.
Произведем проверку прочности стенки барабана т.е. определим напряжения сжатия стенки барабана по формуле:
где Fб – усилие в канате H;
Принимаем для среднего режима работы механизма материал для барабана чугун марки СЧ 15 с допускаемым напряжением [сж ] = 130 МПа.
Статическая мощность двигателя механизма подъёма определяется по формуле:
где Q – номинальная грузоподъемность крана т;
g = 981 мс2 – ускорение свободного падения;
Vпод – скорость подъема груза мс;
– КПД механизма в целом (от крюка до двигателя) принимаем согласно [1 c. 23 табл. 1.18] для подшипников качения = 085.
Номинальную мощность двигателя необходимо принимать равной или несколько меньшей статической мощности на 30 35%.
Двигатель выбираем с учетом ПВ в % и мощности.
Принимаем электродвигатель 4А250М4У3-90 кВт согласно [6 с. 35 табл. 2]:
– мощность Pэл = 90 кВт;
– частота вращения nэл = 1480 мин-1;
– момент инерции ротора Ip = 116 кг · м2;
8 Определение передаточного числа привода
Частота вращения барабана определяется по формуле:
где Vпод – скорость подъема груза мс;
Dб – диаметр барабана м.
Требуемое передаточное число привода определяем по формуле:
Расчетную мощность редуктора находим по формуле:
Где Pc – статическая мощность двигателя
- коэффициент зависящий от типа механизма – для механизма подъема – 1.
Выбираем из каталога редуктор Ц2-500 с передаточным числом – 25
10 Выбор муфты быстроходного вала
Момент статических сопротивлений на валу двигателя с общим КПД всего механизма согласно [1 c. 23]:
где z – число простых полиспастов в системе;
Uр – фактическое передаточное число привода;
– КПД механизма в целом = 085.
Расчетный момент для выбора соединительной муфты с учетом ответственности и режима работы механизма определяется по формуле:
где k1 – коэффициент учитывающий степень ответственности механизма;
k2 – коэффициент учитывающий режим работы механизма.
Тогда согласно [1 c. 42 табл. 1.35] для механизмов подъёма: k1 = 13; k2 = 11 средний режим.
Принимаем втулочно-пальцевую муфту МУВП-Т1000 по ГОСТ 24246 – 80 согласно [3 с. 142 табл. 6.1]:
– номинальный крутящий момент Tном. =1000 Н·м;
– диаметр шкива Dшкива=300 мм;
– момент инерции Jм= 08 кгм2.
11 Выбор муфты тихоходного вала
Момент статических сопротивлений на валу барабана с КПД барабана согласно [1 c. 23]:
где б – КПД барабана (б = 095 096).
Расчетный момент для выбора соединительной муфты с учетом ответственности и режима работы механизма определяется по формуле аналогично (п. 1.10):
Принимаем зубчатую муфту с разъемной обоймой:
– крутящий момент Tмуф. =23600 Н·м;
– момент инерции Jм= 225 кгм2.
12 Определение пусковых характеристик механизма
Фактическая частота вращения барабана определяется по формуле:
где nэл. – частота вращения электродвигателя мин-1;
Uр – фактическое передаточное число привода.
Фактическая скорость подъёма груза определяется по формуле:
где Dб – диаметр барабана м;
Un – кратность полиспаста.
Время пуска при подъёме груза определяется по формуле:
где – коэффициент учитывающий влияние вращающихся масс привода
механизма за исключением ротора двигателя и тормозного шкива
установленного на быстроходном валу: = 11 125;
I – момент инерции ротора двигателя и тормозного шкива установленного
на быстроходном валу:
Ip – момент инерции ротора двигателя кг · м2;
Iм – момент инерции муфты кг · м2;
Tср.п. – средний пусковой момент двигателя определяем по формуле:
Tном. – номинальный момент двигателя определяем по формуле:
Tс – момент статических сопротивлений на валу двигателя (см. п. 1.10) Н·м;
Q – номинальная грузоподъемность крана кг;
V – фактическая скорость подъёма груза мс;
Ускорение при пуске определяется по формуле:
Таблица 1 – Проверка полученных значений пусковых характеристик на
соответствие рекомендуемым значениям для механизма подъёма
Допускаемое значение
для массовых грузов
13 Расчет электромагнитного колодочного тормоза
Момент статического сопротивления на валу двигателя при торможении механизма определяется по формуле:
– КПД механизма в целом = 085;
Необходимый по нормам Ростехнадзора момент развиваемый тормозом определяется по формуле:
где KТ – коэффициент запаса торможения принимаем KТ = 15 – для среднего
режима работы механизма.
Выбираем тормоз ТКГ-300 с L=772 мм H=526 мм Тт=800 Н*м
14 Определение тормозных характеристик механизма
Время торможения при опускании груза определяется по формуле:
где TТ – необходимый момент развиваемый тормозом (см. п. 1.13) Н·м;
TсТ – момент статического сопротивления на валу двигателя при торможении
механизма (см. п. 1.13) Н·м.
Наибольшее допускаемое время торможения в соответствии с рекомендациями [4 с. 397]: tTmax = 1 2 с.
Замедление при торможении определяется по формуле:
Таблица 2 – Проверка полученных значений тормозных характеристик на
Замедление при торможении
15 Проверка двигателя на нагрев
Во избежание перегрева двигателя необходимо чтобы развиваемая им среднеквадратическая мощность удовлетворяла условию:
Средняя квадратичная мощность электродвигателя определяется по формуле:
где Tср – средний квадратичный момент преодолеваемый электродвигателем Н·м;
nэл. – частота вращения электродвигателя мин-1.
где tп – общее время пуска при подъёме и опускании груза с;
tу – время установившегося движения с;
t – общее время работы электродвигателя с;
Tср.п. – средний пусковой момент двигателя (см. п. 1.12) Н·м;
Tс – момент статических сопротивлений на валу двигателя при подъёме Н·м;
TсТ – момент статических сопротивлений на валу двигателя при торможении механизма т.е. при опускании груза (см. п. 1.13) Н·м.
За время цикла (подъём и опускание груза) механизм будет работать с номинальным грузом Q = 19000 кг – 10 раз
Таблица 3 – Результаты расчетов26
Результаты расчета при Q кг
(см. [1 с.24 рис.1.2])
Время пуска при подъёме
Момент при опускании груза
Время пуска при опускании (по формуле из п.1.12
Общее время пуска при подъёме и опускании груза определяется по формуле:
где ni – число подъёмов i-го груза.
Время установившегося движения определяется по формуле:
где Hср – средняя высота подъёма груза: Hср = 08·H м;
V – фактическая скорость подъёма груза мс.
Определим общее время работы средний квадратичный момент и среднюю квадратичную мощность электродвигателя:
Pср = 40 кВт Pном = 90 кВт – следовательно условие выполняется.
РАСЧЕТ МЕХАНИЗМА ПЕРЕДВИЖЕНИЯ
В качестве исходных данных для расчета механизма передвижения используем следующие данные:
- тип крана – грузовая тележка мостового крана;
- грузоподъемность Q = 20 т;
- скорость передвижения крана Vпер. = 08 мс;
- режим работы механизма А4 (средний);
- продолжительность включения механизма передвижения ПВ = 25%.
1 Выбор типа привода
Принимаем тип привода - совмещенный.
2 Определение числа ходовых колес
Принимаем количество колес равное 4 (2 приводных 2 холостых).
3 Кинематическая схема механизма
Рис. 1 Схема механизма передвижения крана.
4 Определение массы крана
Масса грузовой тележки в соответствии с краном аналогом: 63 т.
5 Выбор ходовых колес
Выбираем в зависимости от грузоподъемности крана его скорости передвижения и нагрузке на одно ходовое колесо согласно [1 с. 296 табл. III.2.3].
Наибольшая допускаемая нагрузка на колесо определяется по формуле:
где nк – количество принятых ходовых колес шт;
– коэффициент неравномерности нагрузки.
В соответствии с рекомендациями [1 с. 33] принимаем одноребордное ходовое колесо тележки диаметром Dк = 250 мм = 025 м.
Принимаем коэффициент трения качения ходового колеса по рельсам () и коэффициент трения в подшипниках качения колеса (f) в соответствии с рекомендациями [1 с. 33]:
- f = 0015 – (для шариковых и роликовых подшипников).
Диаметр цапфы вала ходового колеса определяется по формуле:
Принимаем коэффициент учитывающий дополнительные сопротивления от трения реборд ходовых колес о рельс согласно [1 с. 33]:
- kр =20 .25 – для подшипников качения.
- kр =12 .18 – для подшипников скольжения.
6 Определение сопротивления передвижению крана
где Fтр. – сопротивление трения:
Fукл. – сопротивление от уклона:
sin α – уклон пути принимаем для тележек мостовых кранов: sin α = 0002
в соответствии с рекомендациями [1 c. 68 табл. 2.10];
Fв – сопротивление от ветровой нагрузки отсутстувет т.к. кран работает в цеху.
Статическая мощность двигателя механизма передвижения определяется по формуле:
где Fпер. – сопротивление передвижению крана Н;
Vпер. – скорость передвижения крана мс;
– КПД механизма передвижения крана принимаем согласно
[1 c. 23 табл. 1.18] для подшипников качения = 085.
Номинальную мощность одного двигателя механизма передвижения необходимо принимать равной или несколько большей статической мощности.
Принимаем крановый электродвигатель:
– мощность Pэл = 175 кВт;
– частота вращения nэл = 950 мин-1;
– момент инерции ротора Ip = 0312 кг · м2;
– максимальный крутящий момент Tмах = 480 Н·м;
Частота вращения ходового колеса определяется по формуле:
где Vпер. – скорость передвижения крана мс;
Dк – диаметр ходового колеса м.
Расчетная мощность редуктора определяется по формуле:
где kр – коэффициент учитывающий условие работы редуктора принимаем
kр = 225 – для среднего режима работы [1 с. 40 табл. 1.34].
Выбираем редуктор ВКН-420:
– передаточное число Uрред.= 16;
Определение фактической частоты вращения ходового колеса
Тогда согласно [1 c. 42 табл. 1.35] для механизмов передвижения: k1 = 12; k2 = 12 средний режим.
Выбираем втулочно-пальцевую №1 с тормозным шкивом у которой:
Так же для дополнительного разнесения двигателя от редуктора применим втулочно-пальцевую муфту №2 у которой:
11 Определение пусковых характеристик механизма
Фактическая скорость передвижения крана определяется по формуле:
где U и Uр – требуемое и фактическое передаточные числа привода.
Время пуска механизма передвижения без груза определяется по формуле:
механизма за исключением ротора двигателя и муфты быстроходного вала
установленного на быстроходном валу принимаем = 125;
I – момент инерции ротора двигателя и муфты быстроходного вала:
Iм1 Iм2 – момент инерции муфт быстроходного вала 1 и 2 соответственно Iм1 = 024 Iм2 =032;
Tном. – номинальный момент двигателя Н · м;
Tс – момент статического сопротивления на валу двигателя:
F'пер – сопротивления передвижению крана без груза (см. п. 2.6);
V фпер. – фактическая скорость передвижения крана мс;
– КПД механизма передвижения крана = 085.
Проверка фактического запаса сцепления колес с рельсами:
где Fпр – суммарная нагрузка на приводные колеса без груза:
zпр – количество приводных колес шт;
z – общее количество принятых ходовых колес шт.
φ – коэффициент сцепления ходовых колес с рельсами принимаем
φ = 015 согласно [1 с. 33];
F'пер – сопротивления передвижению крана без груза:
f – коэффициент трения в подшипниках качения колеса (см. п. 2.5);
– коэффициент трения качения ходового колеса по рельсам (см. п. 2.5).
Следовательно условие выполняется.
12 Выбор тормоза и определение тормозных моментов
Рекомендуемое замедление механизма передвижения в соответствии с рекомендациями [1 с. 32] равно: [a] = 01 02 мс2 принимаем среднее значение [a] = 015 мс2.
Тогда время торможения крана без груза определим по формуле:
Сопротивление при торможении крана без груза определяется по формуле аналогично п. 2.12:
Момент статических сопротивлений на тормозном валу при торможении крана определяется по формуле:
где – cопротивление при торможении крана без груза Н·м;
Момент сил инерции при торможении крана без груза определяется по формуле:
где tТ – время торможения крана без груза c;
Расчетный тормозной момент на валу тормоза определяется по формуле:
Выбираем тормоз ТКТ-200 с тормозным моментом 160 Нм. Следовательно данный тормоз необходимо отрегулировать до
13 Проверка пути торможения
Фактическая длина пути торможения и минимальная длина пути торможения согласно [1 с. 31] определяются из условия:
V фпер. – фактическая скорость передвижения крана мс.
Условие соответствует рекомендациям [1 с.32 табл. 1.26].
14 Проверка двигателя на нагрев
Т.к. в расчете двигателя был принят двигатель MTF 311-6 с мощностью больше расчетной 175кВт > 16 то проверка на нагрев не требуется.
СПИСОК ИСПОЛЬЗОВАННЫХ ИСТОЧНИКОВ
А.В. Кузьмин Ф.Л. Марон Справочник по расчетам механизмов подъёмно-транспортных машин. Изд. 2-е. перераб. – Минск: Высш. шк.1983.
Курсовое проектирование грузоподъёмных машин: Учеб. Пособие для вузов под ред. С.А. Казака. – М.: Высш. шк.1989. – 319 с.: ил.
Курсовое проектирование деталей машин: учеб. пособие В.Д. Соловьёв В.И. Фатеев. – Тула: Изд-во ТулГУ 2007.- 324 с.
Справочник по кранам Т2 Под ред. М.М.Гохберга. Л.: Машиностроение 1988. 559 с.
Вайснон А.А. Атлас конструкций. Подъёмно-транспортные машины строительной промышленности. - 2-е изд. перераб. – М.: Машиностроение 1976.
Подъёмно-транспортные машины. Атлас конструкций. Под. ред. М.П. Александрова Д.Н. Решетова. - 2-е изд. перераб. и доп. – М.: Машиностроение 1987. – 122 с.: ил.
Иванов М.Н. Детали машин.- 5-е изд. перераб. – М.: Высш. шк.1991.- 383 с.
Захват.dwg

Грузоподъемность захвата 18т.
Масса захвата 1496кг.
Материал 09Г2С-12 ГОСТ 19282-73
Максимальная длина рулона 1500 мм.
общий вид.dwg

Редуктор мех.передвижения
Редуктор мех.подъема
Вал(двиг-ред.)(передв)
Тормоз мех.перевижения
Верхняя обойма блоков
спец захват.dwg

Гайка М16 ГОСТ 5915-70
Стандартаные изделия
Шайба 16 ГОСТ 11371-78
Рекомендуемые чертежи
- 29.07.2014
- 04.11.2022