Мобильная дробильная установка




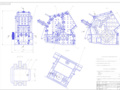
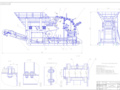
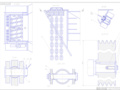
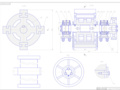
- Добавлен: 25.10.2022
- Размер: 7 MB
- Закачек: 1
Описание
Состав проекта
![]() |
![]() |
![]() ![]() |
![]() ![]() ![]() ![]() |
![]() ![]() ![]() |
![]() |
![]() |
![]() ![]() ![]() ![]() |
![]() ![]() ![]() ![]() |
![]() |
![]() ![]() |
![]() |
![]() ![]() |
![]() ![]() ![]() |
![]() |
![]() |
![]() ![]() ![]() ![]() |
![]() ![]() ![]() ![]() |
![]() ![]() ![]() ![]() |
![]() ![]() |
![]() |
![]() ![]() |
![]() ![]() ![]() ![]() |
![]() |
![]() ![]() |
![]() ![]() ![]() ![]() |
![]() ![]() ![]() ![]() |
![]() ![]() |
![]() |
![]() ![]() |
![]() ![]() |
![]() |
![]() ![]() ![]() ![]() |
![]() ![]() |
![]() |
![]() |
![]() |
![]() |
![]() |
![]() ![]() ![]() |
![]() ![]() |
![]() ![]() |
![]() |
![]() ![]() ![]() |
![]() ![]() |
![]() ![]() ![]() ![]() |
![]() ![]() |
![]() ![]() ![]() |
![]() ![]() ![]() ![]() |
![]() ![]() ![]() ![]() |
![]() ![]() |
![]() |
![]() |
![]() ![]() ![]() ![]() |
![]() ![]() ![]() |
![]() ![]() ![]() ![]() |
![]() ![]() ![]() ![]() |
![]() ![]() ![]() ![]() |
![]() ![]() |
![]() |
![]() ![]() |
![]() |
![]() |
![]() ![]() |
![]() ![]() |
![]() ![]() |
![]() |
![]() |
![]() |
![]() |
![]() ![]() ![]() ![]() |
![]() ![]() ![]() |
![]() ![]() |
![]() |
![]() ![]() |
![]() ![]() ![]() ![]() |
![]() ![]() ![]() ![]() |
![]() ![]() |
![]() |
![]() ![]() ![]() |
![]() ![]() ![]() |
![]() ![]() ![]() |
![]() ![]() ![]() |
![]() ![]() ![]() |
Дополнительная информация
Пресс пневматический.dwg

Проверить на герметичность
Перед применением провести испытание
0713 ДП 00.00.100 СБ
Пресс пневматический
Техническая характеристика:
Давление воздуха - 4МПа
развиваемое штоком - 82592н
Ход штока пресса - 35мм
Спецификация Пресс.doc
Пресс пневматический
Винт М8х30 ГОСТ 17475-80
Винт 7000-0232 ГОСТ 17773-72
Винт М10х20 ГОСТ 50383-92
Гайка М20-6Н ГОСТ 5915-70
Гайка М30-6Н ГОСТ 5915-70
Шайба 20 65Г ГОСТ 6402-70
Шайба 30 65Г ГОСТ 6402-70
ОБЩИЙ ВИД.dwg

Максимальный размер исходного материала
Мощность двигателя привода дробилки
Мощность двигателя привода конвейера
Мощность двигателя привода вибратора
Гидравлическое масло в гидравлической установаке
0713 ДП 00.00.000 СБ
Мобильная дробильная
2-й лист.dwg

Спецификация Общая часть.doc
Мобильная дробильная установка
Болт М8х30 ГОСТ7798-70
Болт М24х56 ГОСТ7798-70
Болт М24х90 ГОСТ7798-70
Болт М27х170 ГОСТ7798-70
Болт М32х110 ГОСТ7798-70
Гайка М22х15ГОСТ11871-88
Гайка М24 ГОСТ5915-70
Гайка М27 ГОСТ5915-70
Гайка М32 ГОСТ5915-70
Шайба 222 ГОСТ11872-89
Шайба 24Г ГОСТ11371-78
Шайба 24 ГОСТ11872-89
Шайба 32Г ГОСТ11371-78
Шпонка 8х7х22ГОСТ23360-78
Шплинт 63х45 ГОСТ397-79
Шплинт 8х56 ГОСТ397-79
Зажим.dwg

Сталь 15Л ГОСТ 977-88
Вал.dwg

Неуказанные предельные отклонения размеров:
Сталь 40Х ГОСТ 4543-85
Втулка.dwg

Палец 1.dwg

Палец.dwg

Верхняя тарелка.dwg

Сталь 45 ГОСТ 1050-88
Нижняя тарелка.dwg

Карты.doc
Колич. одн. обраб. детали
Оборудование (наименование модель)
Станок отрезной 8Г642
Приспособ-ление (код и наименование)
Зажимы клиновые ГОСТ 24351 - 80
Инструмент (код и наименование)
ОПЕРАЦИОННАЯ КАРТА МЕХАНИЧЕСКОЙ ОБРАБОТКИ
Станок токарный 16К20
Патрон трехкулачковый ГОСТ2675-80
Точить поверхность до
диаметра 80мм на длину
Тиски станочные ГОСТ 16518 - 96
диаметра 50мм на длину
Станок вертикально-сверлильный 2Н125
Тиски станочные ГОСТ16518 - 96
Установить закрепить и
Станок шлифовальный 3А11В
Патрон поводковый ГОСТ 2571 - 71
Шлифовать поверхность
Патрон трехкулачковый по ГОСТ 2675-71
Переустановить заготовку
1.doc
Изготовление детали состоит из следующих операций: отрезание точение сверление шлифование.
1 Операция 1 – отрезание
Отрезаем от круглого профиля диаметром 85 мм заготовку длиной 180 мм с помощью дисковой сегментной пилы ГОСТ 4047-82. Разрезание производим на отрезном станке 8Г642.
Для дисковой сегментной пилы принимаем подачу Sz по таблице 43 7
Скорость резания принимаем по таблице 44 7
Подача Sм определяется по формуле 7
где Z – число зубьев пилы
n – частота вращения пилы обс
где - окружная скорость пилы радс;
где Vр – скорость резания мс;
Продолжительность операции Топ:
где То – основное время операции с;
где Дз – диаметр заготовки мм;
Тв – вспомогательное время с;
Дополнительное время Тдоп определяется
Полное штучное время выполнения операции Тшт:
2 Операция 2 – точение
Заготовку устанавливаем в центра токарного станка.
Для обработки подведем резец проходной 1-го исполнения ГОСТ 18869-73.
Глубину резания t принимаем по 7:
для чернового точения: t = 16мм;
для чистового точения: t = 01мм;
Подачу S подбираем по 7 табл. 11:
для чернового точения: S = 09ммоб;
для чистового точения: S = 02ммоб.
Скорость резания при наружном продольном и поперечном точении и растачивании рассчитывают по эмпирической формуле 7
где Т – стойкость резца мин;
при одноинструментной обработке Т = 30-60 мин. Значения коэффициента Cv показателей степеней x y и m подбираем по 7 табл. 17
x = 015для чернового x = 015 для чистового
y = 045 точения y = 020 точения
Кv – поправочный коэффициент
Кv = Кmv ·Кnv ·К (6.10)
где Кmv –коэффициент учитывающий влияние материала заготовки;
Кmv находим по формуле 7 табл. 1;
где Кr – коэффициент характеризующий группу стали по обрабатываемости
- предел прочности при растяжении МПа;
nv – показатель степени
Кr и nv находим по таблице 7 табл. 2;
Кпv –коэффициент отражающий состояние поверхности заготовки 7 табл. 5;
Киv – коэффициент учитывающий качество материала инструмента 7 табл. 6;
Для чернового точения:
Для чистового точения:
Силу резания Н принято раскладывать на составляющие силы направленные по осям координат станка (тангенциальную Pz радиальную Py и осевую Px). При наружном продольном и поперечном точении эти составляющие рассчитывают по формуле 7.
Постоянная Ср и показатели степени x y и n находим по 7 табл. 22
Кр – поправочный коэффициент
где Кmp – коэффициент учитывающий влияние качества обрабатываемого материала на силовые зависимости;
где - предел прочности стали при растяжении МПа;
- поправочные коэффициенты учитывающие влияние
геометрических параметров режущей части инструмента 7 табл. 23;
Kpz=09·108·115·10=112;
Kpy=09·044·16·10=063;
Мощность резания N кВт рассчитывают по формуле 7:
где V – скорость ммин;
Pz– тангенциальная сила резания Н;
Частота вращения заготовки:
где V – скорость резания ммин;
D – диаметр обрабатываемой заготовки мм;
Основное операционное время:
где L – длина обработки мм;
Вспомогательное время:
Дополнительное время:
2 Операция 3 – точение
2 Операция 4 – точение
Операция 5– сверление
Глубина резания при сверлении принимается равной t=05D
Подачу подбираем S=03ммоб
Скорость резания рассчитываем по формуле 7:
где Т – период стойкости сверла мин;
D – диаметр отверстия мм;
Значения Cv и показателей степеней приведены 7 табл. 28
Кv – общий поправочный коэффициент учитывающий фактические условия резания;
Кv = Кmv ·Кuv·К (6.34)
где Кuv- коэффициент на инструментальный материал;
Кmv – коэффициент на обрабатываемый материал;
Кv = 128 ·10·10=128;
Крутящийся момент и осевую силу рассчитываем по формулам 7:
где D – диаметр отверстия мм;
Кp – коэффициент учитывающий фактические условия обработки:
где Кmp – коэффициент зависящий от материала обрабатываемой заготовки 7 табл. 9;
Мощность резания определяем по формуле 7:
где n – частота вращения инструмента обс;
где D – диаметр инструмента мм;
V – скорость резания ммин;
где nсв– частота вращения сверла обмин;
L – глубина отверстия мм;
7 Операция 6 – шлифование
Шлифование производим на круглошлифовальном станке 3М151 шлифовальным кругом прямого профиля на керамической связке ПП 300×100×50 ГОСТ 1375 – 71.
Основные параметры резания при шлифовании выбираем по 7 табл.55
При предварительном шлифовании:
скорость круга: Vк=35мс;
скорость заготовки Vз =20ммин;
глубина шлифования t=002мм;
продольная подача S=(03÷07)В;
При окончательном шлифовании:
скорость круга: Vк=35мс;
скорость заготовки Vз =40ммин;
глубина шлифования t=001мм;
продольная подача S=30ммоб;
Эффективную мощность при шлифовании определяем по формуле7:
где d – диаметр шлифования мм;
Значения коэффициента CN и показателей степени находим по
Частота вращения детали:
где D – диаметр заготовки мм;
Определяем основное операционное время:
где К – коэффициент зачистных проходов К = 15;
В – ширина круга мм;
Полное время операции:
К данному разделу прилагаются: маршрутно-операционные карты и спецификация нормального инструмента (приложение В).
Операция №5.dwg

Приспособление: Тиски станочные ГОСТ 16518-96
Инструмент: Сверло спиральное ГОСТ 4010-77
маршрутная карта Б.З..doc
Оборудование (код наименование инвентарный номер)
Приспособление и инструмент (код наименование)
Кол. одн. обраб. дет.
производственной партии
Отрезать заготовку на длину 170 мм и диаметром 85мм
Точить поверхность до диаметра 80мм на длину 170мм
Точить поверхность до диаметра 50мм на длину 150мм
Сверлить отверстие диаметром 10мм на глубину 50 мм
Шлифовать поверхность пальца на длину 150мм
Операция №4.dwg

Приспособление: Патрон трехкулачковый
Инструмент: Резец токарный фасонный
(Исполнение 1) ГОСТ 18869-73
Инструмент измерительный: ШЦ1-250 ГОСТ166-80
4_1.dwg

Операция №6.dwg

Приспособление: Патрон поводковый ГОСТ 2571-71
Инструмент: Круг шлифовальный ПП 250 -20 -50 ГОСТ 1375-71
Спецификация нормального инструмента.doc
Наименование инструмента
операция №1.dwg

Инструмент: Дисковая сегментная пила ГОСТ 4047-82
Приспособление: Зажимы клиновые ГОСТ 24351-80
Операция №2.dwg

Станок токарно-винторезный 16К20
Приспособление: 3-х кулачковый патрон
отогнутый левый ГОСТ18863-73
Измерительный инструмент:
Линейка измерительная ГОСТ166-78
Операция №3.dwg

Приспособление: Патрон трехкулачковый
Инструмент: Резец токарный проходной
(Исполнение 1) ГОСТ 18869-73
Инструмент измерительный: ШЦ1-250 ГОСТ166-80
Лист1.dwg

Наибольший размер куска исходного материала
Частота вращения ротора
Мощность электродвигателя
Технические требования:
Смещения валов электродвигателя не более:
Осевой зазор подшипников на валу 0
Запрещается разбивать негабаритный материал в горловине
0713 ДП 03.00.000 СБ
Дробилка ударного действия
Спецификация Дробилка.doc
Смотровое – откидное окно
Ударно-отражательный элемент
Дробилка ударного действия
Винт М12х40 ГОСТ50384-92
Болт М20х90 ГОСТ7798-70
Болт М27х100 ГОСТ7798-70
Гайка М27 ГОСТ5915-70
Гайка М30 ГОСТ5915-70
Гайка М45 ГОСТ5915-70
Маслёнка 6 ГОСТ20905-75
Подшипник1224ГОСТ28428-90
Шайба 27 ГОСТ11371-78
Шайба 27Г ГОСТ11371-78
Шайба 30 ГОСТ11371-78
Шайба 45 ГОСТ11371-78
Шпонка32х18х90ГОСТ23360-78
Шпонка56х32х140ГОСТ23360-78
Шплинт 63х60 ГОСТ397-79
Шплинт 8х90 ГОСТ397-79
3-й лист.dwg

Лист 2.dwg

семи-мобильный дробильный ударный комплекс.doc
Общее описание ударного дробильного комплекса KKL 50 GE
На рисунке представлен ударный дробильный комплекс KKL 50 GE со смонтированными на раме рабочими узлами. Загрузка материала в засыпное отверстие осуществляется при помощи погрузчика. Загрузочное отверстие поз 2 смонтировано над вибробункером поз 4. Вибробункер подает материал – садиво из загрузки в ударную дробилку поз 09. Подаватель поз 5 с шириной ленты 650 мм принимает продукт дробления из-под дробилки и транспортирует наружу машины.
Техническое описание ударного дробильного комплекса KKL 50 GE
Ударный дробильный комплекс представленный на рисунке 516-00.000.00 состоит из следующих основных подузлов:
Гидравлическая установка
Ударная дробилка KU50
Оросительная установка
Электрическая установка
Рама рисунок 516-01.000.00
Рама является сварной конструкцией в которой четыре двутавровые продольные балки соединенные соответствующими поперечными элементами представляют собой основание служащее для монтажа рабочих узлов дробилки.
На передней части рамы смонтирован загрузочный вход и вибробункер. В центральной части расположен электрический двигатель служащий для приведения в действие самой дробилки. Собственно дробилка расположена в задней части рамы. Вдоль всей рамы проходит трасса подавателя принимающего дробления.
Загрузочный вход рис 516-02.000.00
В передней части загрузочного входа смонтированного к ударной дробилке имеется крышка с тремя рядами цепей защищающих от брызг образующихся в процессе работы. Крышка поднимается гидравлическим цилиндром для упрощения замены изношенных цепей.
Привод рис 516-03.000.00
Привод дробилки представлен электрическим двигателем передающим оборотный момент на дробилку посредством ременной передачи. Раздвижная рама двигателя дает возможность регулировать натяжение клиновых ремней.
Вибробункер рис 516-04.000.00
Вибробункер приводится в движение инертным электровибратором с возможностью шагового изменения возмущающей силы. Регулировка возмущающей силы осуществляется при выключенном оборудовании посредством изменения взаиморасположения неуравновешенных масс. Транспортировочная поверхность выложена облицовкой из устойчивых к истиранию металлических листов. Подаватель осажден на восьми цилиндрических пружинах. Для гашения вибрации во время запуска и остановки использованы резиновые амортизационные элементы.
Подаватель рис 516-05.000.00
Подаватель с шириной ленты 650 мм принимает продукт дробления транспортируя его наружу машины. Лента приводится в движение электробарабаном.
Подаватель состоит из следующих основных узлов:
- Узел обратного барабана поз 01;
- Узел приводного барабана поз 04;
Лента подавателя перемещается на верхних роликах поз 108 и поз 109 и на нижних роликах поз 115. Боковое смещение ленты ограничено двумя направленными роликами смонтированными в узле приводного барабана.
Для очищения ленты предусмотрены два скрепера:
- Скрепер поз 05 (для очищения внутренней поверхности);
- Крестовой скрепер смонтированный в узле приводного барабана.
На подавателе кроме того смонтирована боковая защита ленты и защита нижних роликов поз 115.
Гидравлическая система 516-07.000.00
Гидравлическая система служит для упрощения обслуживания машины:
- Замены цепного занавеса;
- Замены отбойных плит облицовки стен и ударных планок ротора.
Ударная дробилка KU50 рис 516-08.000.00
Ударная дробилка KU50 обеспечивает производительность на уровне 20-50 Мтчас одновременно позволяя перерабатывать широкую гамму материалов.
Основными элементами дробилки являются:
- Стены с отбойными плитами поз 4.
В корпусе дробилки на системе подшипников расположен ротор. В роторе имеются ударные планки задачей которых является дробление материала. Стены с отбойными плитами также предназначены для разбивания материала предназначенного для дробления. Изменяя положение стен с отбойными плитами по отношению к ротору дробилки мы получаем различный размер зазора благодаря чему получаем материал с различной степенью дробления.
Ротор рис 516-08.100.00
На валу ротора поз 2 смонтирован корпус ротора поз 1 при помощи блокирующих колец поз 8. Вал ротора поз 2 осажденный в корпусе подшипников поз 3 с бочкообразными роликоподшипниками прикреплен к нижним и боковым стенкам корпуса дробилки. Упомянутые подшипники оснащены внутренними крышками поз 4 и поз 5 а также наружными крышками поз 6 и поз 7.
Смазывание подшипников и лабиринтов крышек происходит периодически посредством программируемой установки централизованной смазки.
Корпус ротора поз 1 имеет четыре плеча – диски с соответствующими фигурными вырезами защищающими ударные плиты поз 14 от центробежных сил. Кроме того ударные плиты защищены от смещения вдоль оси ротора закладками поз 9.
Кожухи защищают блокирующие кольца от попадания в них мелких фракций материала.
Планки поз 13 и 15 защищают корпус ротора от быстрого износа.
Корпус ударной дробилки
Корпус дробилки является конструкцией изготовленной из отдельных элементов а именно:
- Нижних боковых стенок;
- Стенки с отбойными плитами;
Нижние боковые стенки и боковые стенки I оснащены ревизионными экранами соответственно закрываемыми дверями – для контролирования состояния ротора и отбойных стенок.
Стена с отбойными плитами 505-08.400.00
Эти стены являются наклонными плитами и смонтированы на петлях крепящих их к нижней задней стенке дробилки. С двух сторон стен с отбойными плитами смонтированы гидравлические цилиндры. Эти цилиндры после предварительного освобождения резьбовых соединений стен позволяют открыть дробилку давая возможность ремонтным службам заменить отбойные плиты и облицовку стен дробилки а также заменить ударные планки ротора. Верхняя и нижняя отбойные стенки прикреплены к задней стенке при помощи болтов с пружинами.
Верхняя отбойная стенка закреплена при помощи одного болта с дисковой пружиной а отбойная стенка нижняя – при помощи двух болтов со спиральными пружинами. Верхняя и нижняя отбойные стенки подвешены над ротором в качестве элементов взаимодействия с ротором обеспечивающих многократное возвращение материала в зону работы ротора а кроме того обеспечивают более эффективное раздробление материала и отбивание зерен от стен. Отбойные стены принимают своей инертностью энергию дробления и могут «натягиваться» пружинами увеличивающими силу «отбивания» .Кроме того они обеспечивают наклон отбойных стен в случае попадания в дробилку материала не подлежащего дроблению (стального лома).
Угол наклона отбойных стен может регулироваться при помощи натяжных болтов. Стены дробилки выложены облицовкой из стали устойчивой к истиранию защищающей стены от быстрого износа.
Целью оросительной установки является максимально ограничить запыление в зоне работы машины. Для этого установлены два комплекта оросительных форсунок – на входе в дробилку и на ленточном конвейере. Форсунки запитываются из трубопровода шахтной технологической воды с рекомендуемым давлением 5-10 bar.
Установка централизованной смазки
Задачей установки централизованной смазки является обеспечить периодическое независимое от оператора смазывание подшипников и их лабиринтных крышек.
Работу смазочного насоса контролирует программируемый командоконтролер дающий возможность установить время работы а также перерывов в работе. Объем смазочной порции поставляемой в конкретную точку регулируется при помощи прогрессивного распре.
Обслуживание дробильного комплекса
Дробилка по своей конструкции приспособлена для дробления материала содержащего стальные элементы но учитывая возможность повреждения ленты торчащими прутьями фасонными профилями и другими металлическими элементами раздробляемый материал необходимо предварительно подготовить. Подготовка заключается в разбивании материала с чрезмерными габаритами отделении стали от крошки контролировании ситуации когда металлические элементы не приведут к обездвиживанию дробилки или повреждению ленты основного транспортера.
Стальные элементы небольшого диаметра 3-5 мм в процессе дробления выгибаются сами по себе и укладываются вдоль ленты хотя в случае неблагоприятного уложения могут привести к небольшой перфорации конвейерной ленты что в свою очередь после дальнейшей эксплуатации может вызвать локальное расслоение резины со стороны внутренней оплетки и как следствие – ускоряет износ ленты.
Стальные элементы толщиной 5-12 мм приводят к локальному повреждению ленты если в процессе дробления будут в нее «вбиваться». Поэтому процесс необходимо вести таким образом чтобы прутья укладывались параллельно направлению движения ленты а не перпендикулярно.
Стальные элементы диаметром более 12 мм и другие металлические элементы наличие которых в садиве сложно исключить должны иметь такую форму и габариты чтобы обеспечить их свободное падение на ленту. В особенности это касается длины которая в любом случае должна быть меньше просвета между дробилкой и лентой транспортера. Максимальная длина свободного металлического элемента не может превышать 200 мм при толщине зависящей от величины зазора на I и II ступени дробления.
Регулировка зазоров между отбойными плитами и ротором ударной дробилки
Ударная дробилка KU50 производимая DFM “ZANAM-LEGMET” дает возможность получать крошку различной грануляции (зернистости). Для получения материала нужной зернистости необходимо отрегулировать зазоры между отбойными плитами и ротором дробилки. Регулировка осуществляется по такому принципу что чем меньше зазор между отбойными плитами и планками ротора тем больше будет раздроблен выходной материал и соответственно чем больше зазор тем более крупный получается материал.
Дробилка KU50 дает возможность получить материал со степенью раздробления от 1-10 до 1-50.
Регулировка осуществляется в соответствии со следующими правилами (см.рисунок 3 Инспекционные дверцы в ударной дробилке KU50):
- выключить двигатель и выждать до момента остановки ротора дробилки;
- демонтировать блокировки поз. 23 и 6 открыть боковые инспекционные дверцы поз. 1 и 5;
Регулировка зазора на I этапе дробления (рисунок 4 Отбойные плиты):
- провернуть ротор вручную до момента пока верхушка ударной планки не остановится напротив самой нижней точки и верхней отбойной плите поз.2;
- ослабить защиту болта поз 15 а затем проворачивать гайки поз 107 поднимая или опуская весь комплекс верхней отбойной плиты поз 2.
Поворот гайки поз 107 по ходу часовой стрелки приведет к увеличению зазора то есть получению материала с меньшей степенью раздробления. Поворот гайки поз 107 против хода часовой стрелки приведет к уменьшению зазора то есть получению материала с большей степенью раздробления;
- докрутить защиту болта поз 15 к гайке поз 107.
Регулировка зазора на II этапе дробления (рисунок 4 Отбойные плиты):
- провернуть ротор вручную пока верхушка ударной планки не остановится напротив самой нижней точки в нижней отбойной плите поз.3. Затем следует ослабить гайки поз 12 чтобы уменьшить напряжение на пружинах поз 7;
- регулировка положения нижней отбойной плиты осуществляется гайкой поз 9. Поворот гайки поз 9 по ходу часовой стрелки приведет к увеличению зазора то есть получению материала с меньшей степенью раздробления. Поворот гайки поз 9 против хода часовой стрелки приведет к уменьшению зазора то есть получению материала с большей степенью раздробления. По завершении регулировки заблокировать положение отбойных плит поворачивая гайку поз 11;
- докрутить гайки поз 12 таким образом чтобы получить соответствующее натяжение пружин (ощутимый упор при докручивании) так чтобы расстояние между обмоткой пружин составляло 25-30 мм;
Регулировка натяжения пружин должна осуществляться парами (поворачивая регулировочные болты на правом и левом болте).
Закрыть боковые инспекционные дверцы и предохранить их блокировками.
Проверить состояние натяжения пружин поз 7
Замена планок в роторе ударной дробилки
При необходимости замены изношенных планок следует:
- выключить электрический двигатель выждать до момента полной остановки дробилки;
- ослабить соответствующие рым-болты поз 105 и 106 (рисунок 3 Инспекционные дверцы в ударной дробилке KU50);
- включить гидравлический агрегат а затем переключить соответствующую секцию распределителя запустить гидравлические цилиндры поз 101. После отклонения в крайнее положение стены с отбойными плитами поз 4 вместе со связанными с ней боковыми стенками поз 7 предохранить их шкворнем поз 20;
- приступить к демонтажу ударных планок поз 14 выталкивая их из ротора (рисунок 5 Поперечный разрез ротора);
- после очищения гнезд смонтировать новые планки.
ОТ.doc
В соответствии с требованиями ГОСТ 12.0002 – 74 под охраной труда принято понимать систему законодательных социально-экономических технических санитарно-гигиенических и организационных мероприятий обеспечивающих безопасность сохранение здоровья и работоспособности человека в процессе труда.
В охране труда различают две системы мероприятий и средств: технику безопасности и производственную санитарию. Цель техники безопасности – предотвратить воздействие на работающих опасных производственных факторов. Производственная санитария решает задачу предотвращения воздействия на работающих вредных производственных факторов.
Требование безопасности на производственное оборудование в соответствии с ГОСТ 12.2.003 – 74 предусматривают общие положения сущность которых состоит в следующем:
Безопасность производственного оборудования обеспечивается в течение всего срока службы. Для этого при разработке выбираются безопасные конструктивные схемы и конструктивные элементы с учетом механизации автоматизации дистанционного управления и эргономических требований (удобств при запусках и управлении).
Вновь разрабатываемое и эксплуатируемое оборудование должно быть герметичным удобным для контроля и обслуживания малошумным не выделять в рабочую зону вредных веществ влаги тепла различных видов излучений в количествах превышающих установленные нормами пределы. Важным условием является наличие защиты от поражения электрическим током и исключение накопления зарядов статического электричества в опасных количествах.
Конструкция производственного оборудования машин и механизмов должна включать средства защиты к которым предъявляются требования постоянной готовности и исправности обеспечения прекращения функционирования оборудования и машин при неисправностях (в том числе и самих средств защиты) звуковой световой и цветовой сигнализации в зонах видимости и слышимости обслуживающего персонала. В качестве средств защиты оборудование следует окрашивать в сигнальные цвета и снабжать знаками безопасности установленными ГОСТ 12.4.026 – 76.
Оборудование используемое на мобильной дробильной установке должно быть не только высокопроизводительным но и безопасным. Безопасность производственного оборудования – это свойство производственного оборудования сохранять соответствие требованиям безопасности труда при выполнении заданных функций в условиях установленных нормативно-технической документацией.
Производственное оборудование должно отвечать требованиям безопасности в течение всего срока службы. Оно должно быть пожаро- и взрывобезопасным.
Пусковые устройства основных машин механизмов и аппаратов блокируются с предохранительными и ограждающими устройствами для исключения пуска их в работу при снятых защитных средствах.
Работать на неисправном оборудовании и пускать в эксплуатацию производственное оборудование без защитных средств сигнализации блокировок обеспечивающих безопасность его обслуживания запрещается.
Общая компоновка и расположение оборудования должны обеспечивать удобства обслуживания и проведения ремонтных работ а также удовлетворять санитарно-гигиеническим требованиям.
Оборудование находящееся в эксплуатации постоянно должно подвергаться осмотру контролю чистке и периодически планово-профилактическому ремонту. Перед осмотром оборудования должна быть прекращена подача электроэнергии.
Перед работой необходимо удостовериться в безопасном состоянии рабочего места и проверить наличие и исправность предохранительных устройств инструмента механизмов и приспособлений требующихся для работы наличие и исправность заземления электроустановок освещенность рабочего места. Если рабочий сам не может устранить выявленные нарушения он обязан сообщить о них мастеру и не приступать к работе до их устранения.
При эксплуатации оборудования необходимо руководствоваться следующими основными правилами:
- перед пуском машины убедиться в отсутствии на ней постоянных предметов;
- после пуска проверить оборудование в рабочем состоянии;
- немедленно остановить машину при появлении дыма или огня сильной вибрации поломке агрегата.
Для транспортировки материала используется ленточный конвейер. На ленточных конвейерах должны быть предусмотрены: устройства выключающие привод при обрыве и пробуксовке ленты обрыве канатов натяжных устройств и забивке разгрузочных воронок и желобов а также снижение скорости ленты до 75% номинальной; устройства для механической очистки ленты и барабанов от налипшего материала; устройство исключающее самопроизвольное движение разгрузочной тележки; приспособление исключающее боковое смещение ленты и т.д.
Конвейер отличаясь от другого оборудования простой конструкцией тем не менее является наиболее опасным механизмом.
При транспортировании ленточными конвейерами сухих и пылящих материалов герметически закрывают места загрузки и выгрузки материала а также предусматривают другие мероприятия по борьбе с пылевыделением (аспирация орошение и др.) для обеспечения предельно допустимых норм вредных примесей в воздухе.
Дробление. Загружаемый исходный материал попадая в дробильную камеру ограниченную лобовой и боковыми стенками станины отражательными плитами и ротором разрушается ударом по нему ножами ротора и ударами об отражательные плиты. Для избежания вылета загружаемого материала вокруг загрузочного отверстия роторной дробилки навешиваются цепи.
Если при дроблении руды образуется взрывоопасная пыль необходимо выполнять мероприятия исключающие взрыв пыли.
Защита от шума и вибрации
Шум и вибрация являются вредными производственными факторами воздействие которых на работающих в определенных условиях приводит к снижению работоспособности а при длительном воздействии к заболеванию.
Длительное воздействие шума на организм человека приводит к частичной а иногда и полной потере слуха воздействие на центральную нервную систему к шумовой болезни.
Источником шума на мобильной установке являются работа дробилки и вибробункера.
Уменьшить воздействие шума на организм человека можно снижением уровня шума в источнике его образования звукоизоляцией звукопоглощением установкой глушителей и применением комплекса этих мер. Снижение уровня шума в источнике образования т.е. непосредственно в машинах и механизмах является наиболее эффективным методом защиты человека от шума. Для этого необходимо совершенствовать конструкции машин и аппаратов регулировать их работу в процессе эксплуатации обеспечивать надежное и жесткое крепление ограждения или кожуха.
Звукоизоляция осуществляется устройством на пути распространения шума звукоизолирующих преград в виде стен перегородок перекрытий обшивок и т.д.
Простейшим средством защиты органов слуха от шума является вата или марля вставленные в слуховой канал; при этом снижается шум на 3-14 дБ в полосе частот 100-6000 Гц при применении марли смоченной жиром- до 18 дБ а шерстяной ваты с воском - до 30 дБ. Полупластичные предохранительные втулки плотно закрывающие слуховой канал обеспечивают снижение шума до 20 дБ. Применяемые в настоящее время некоторые конструкции антифонов (противошумов) закрывающих ушную раковину снижают шум до 30 дБ.
Для снижения воздействия вибрации на человека используют средства автоматизации применяют прогрессивную технологию исключающую контакт работающих с вибрацией используют виброзащитные приспособления конструкции и устройства. Важную роль по предупреждению вибрационной болезни имеет правильная организация труда при работе с ручными вибрирующими машинами. Через каждые 50-60 минут необходимо прекращать работу для отдыха на 7-10 минут. Кроме этого назначают дополнительные перерывы: первый – 20 минут через 15-2 часа после начала работы второй – 30 минут через 2 часа после обеденного перерыва. Первый перерыв рекомендуется использовать для производственной гимнастики легкого завтрака второй – для проведения физиотерапевтических процедур.
Суммарное время контакта с вибрирующими поверхностями не должно превышать 83 длительности рабочего дня. Сверхурочные работы на вибрирующем оборудовании не допускаются. Работы связанные с вибрацией выполняют как правило в отапливаемых помещениях при температуре воздуха не ниже 16°С влажности 40-60% и скорости движения не более 03 мсек. Работающему через каждый час работы должны предоставляться 10-15 минутные перерывы или поручаться работы не связанные с вибрацией При работе виброинструментом важно не допускать переохлаждения рук для чего надо выдавать рабочим рукавицы с прокладками из пенопласта пористой резины или фетра. Предельно допустимые величины общей вибрации рабочих мест (пол сиденье ограждение и т. д.) санитарными нормами устанавливаются по уровню виброскорости в диапазоне частот от 11 до 355 Гц который включает пять октавных частотных полос со среднегеометрическими значениями частот 16 32 63 125 и 250 Гц. Вибрации с частотой ниже 11 Гц нормируются по основной частоте колебаний
Суммарная масса вибрационного конвейера с находящимися в его рабочем органе порциями огарка m кг определяется по формуле 3.22 14:
m = mр.о. + mм + m2 ()
где mр.о. – масса рабочего органа кг (mр.о. = 4840 кг);
mм – масса материала в рабочем органе кг (mм = 2392 кг);
m2 – масса тяжелой уравновешивающей рамы кг (m2 = 22400 кг).
m = 4840 + 2392 + 22400 = 26632 кг
В качестве пружин – амортизаторов (шумовиброизоляторов) принимаем винтовые пружины жесткостью Св.и.=130000 Нм размером dDL=002001300354 м в количестве 58 штук (по 8 изоляторов на секцию и 2 дополнительных изолятора на приводной секции под рамой электродвигателя).
Нагрузка приходящаяся на один виброизолятор Ри Н определяется по формуле:
где: g – ускорение свободного падения мс2;
Рама тяжелая уравновешивающая
Пружины-амортизаторы;
Рисунок – Схема установки тяжелой уравновешивающей рамы на опорную раму
Статическая деформация каждой пружины-амортизатора Хстат м определяется по формуле:
где Св.и. – жесткость пружины-амортизатора Нм.
Суммарная жесткость всех пружин-амортизаторов Нм определяется по формуле:
Собственную частоту колебания виброустройства на шумовиброизоляторах wрез с-1 определяем по формуле:
Отношение g рабочей вынужденной частоты колебаний w с-1 к резонансной частоте системы wрез с-1 определяем по формуле:
Коэффициент передачи при отсутствии демпфирования h определяем по формуле:
Чем меньше коэффициент передачи вибрационной силы h тем лучше шумовиброизоляция системы.
Периодически действующая нагрузка кроме статической от силы тяжести конструкции виброконвейера передаваемой на опорную площадку Рдин.max Н определяется по формуле:
где: А2 – амплитуда колебаний тяжелой уравновешивающей рамы м (А2=20×10-3 м);
b - угол вибрации град (b=30°);
Рдин.max=20×10-3×sin 30°×7540000=7540 Н
На каждую опору под шумовиброизолятором передается нагрузка Риз Н определяется по формуле:
Динамическая нагрузка на опорную площадку незначительна что подтверждает хорошую вибрационную и шумовую изоляцию вибрационного конвейера.
Гигиеническими характеристиками вибрации согласно ГОСТ 12.1.012-90 являются среднеквадратичные значения виброскорости мс виброускорения мс2 или логарифмические уровни виброскорости и виброускорения дБ в октавных полосах частот. В нашем случае вибрационный конвейер относится к категории 3а вибрации по санитарным нормам и критериям оценки – технологическая вибрация воздействующая на операторов стационарных машин и оборудования или передающаяся на рабочие места не имеющие источников вибрации.
Место установки виброконвейера не является местом постоянного нахождения рабочих тем не менее производим расчеты логарифмических уравнений виброскорости и виброускорения и сравниваем их с нормативными.
Амплитуда колебаний опорной рамым определяем по формуле:
Скорость вибрации мс определяем по формуле:
где: f – частота колебаний с-1
Частота колебаний определяется по формуле:
где: n – частота колебаний мин-1
= 2×314×95×003×10-3=00018 мс
Сравниваем полученное значение с нормативным корректируем по частоте и эквивалентным корректированным значениям по таблице 7 ГОСТ 12.1.012-90 и получаем
Ускорение вибрации а мс2 определяем по формуле:
а=003×10-3×(2×314×95)2=01 мс2
Сравнивая полученные значения получаем:
Логарифмический уровень скорости L дБ определяется по формуле:
L=20×lg×( 5×10-8) ()
L=20×lg×(00018 5×10-8)=911 дБ
Сравнивая полученные значения с нормативным получаем
Логарифмический уровень виброускорения La дБ определяем по формуле:
Lа=20×lg×(а 10-6) ()
Lа=20×lg×(01 10-6)=100 дБ
Сравнивая полученные значения с нормативными получаем
По проведенному расчету можно сделать вывод о вибрационной безопасности виброконвейера.
Предусмотрены меры позволяющие снизить уровень вибрации отдельных частей виброконвейера например в подшипниках качения хотя они выбраны роликовыми двухрядными с большим уровнем вибрации чем у шариковых однорядных однако организована непрерывная смазка в виде смазочной ванны когда через масленку непрерывно поступает (по мере надобности) смазка – Литол-24 и периодически пополняется во время ТО и ремонтов. Передача крутящего момента от двигателя на вал вибратора осуществляется с помощью клиноременной передачи исключающей удары.
Величину максимальных касательных напряжений действующих в материале витков пружин-амортизаторов МПа определяем по формуле:
где: Ри – нагрузка на виброизолятор Н;
D – средний диаметр пружины м (D=011 м);
d – диаметр прутка пружины м (d=002 м);
К – поправочный коэффициент определяемый по формуле:
Это напряжение меньше допустимого принимаемого для пружин из стали 60С2 и 65Г =500 МПа следовательно запас прочности у пружин достаточен.
Все эти меры и настройка работы виброустройства после монтажа при его наладке на плавный околорезонансный режим приводят к тому что виброконвейер работает плавно и бесшумно что подтверждается опытом эксплуатации таких вибрационных конвейеров.
Установление опасных зон и расчет на прочность ограждения
Опасной зоной проектируемой машины которая может вызвать возможность механического захвата одежды обслуживающего персонала является клиноременная передача то есть расстояние между ремнем и шкивом. Для исключения захвата устанавливаем ограждение передачи листовым металлом. Для расчёта составляем расчётную схему представленную на рисунке.
Рисунок – Схема к расчёту ограждения.
Расчёт производим со следующими допущениями: от одного из шкивов вращающихся с большой частотой отламывается часть массой m = 4 кг и ударяется в боковую стенку ограждения по центру. На основании вышеперечисленного производим расчёт.
Центробежную силу Fц Н определяем по формуле:
где m – масса отломившейся части кг;
w - частота вращения шкива с-1 (w = 7693 с-1);
Fц = 4×76932×03 = 71 кН
Строим расчётную схему боковой стенки ограждения она представлена на рисунке.
Так как центробежная сила приложена по центру стенки изгибающий момент определяем по формуле:
Рисунок - Расчётная схема боковой стенки ограждения
Напряжения возникающие при столкновении определяем по формуле:
Момент сопротивления сечения W м3 определяется по формуле :
где а – толщина пластины м;
b – ширина пластины м.
Сравниваем полученное значение с пределом текучести sт МПа и получаем выполнение условия:
Ограждение пригодно к использованию.
Организация рационального освещения является одним из основных факторов создания высокопроизводительной и безопасной работы трудящихся. Недостаточное освещение само по себе не вызывает несчастных случаев но может обусловить их возникновение так как оно притупляет внимание и вызывает преждевременное утомление работающих. Кроме того источники света могут быть причиной возникновения пожара и взрыва.
В зависимости от источника света различают естественное и искусственное освещение.
Так как установка работает не в помещении рассчитаем прожекторное освещение. Для площадки необходимо предусматривать общее равномерное освещение. При этом освещенность должна быть не менее 2 лк независимо от применяемых источников света.
При проектировании установок в расчет следует вводить коэффициент запаса.
Вводим коэффициент запаса на запыленность светильников и старение источников света который определяем по таблице Кз = 15.
Затем в соответствии со СН – 80 – 81 «Инструкция по проектированию электрического тока освещения строительных площадок» из рекомендуемых схем расположения осветительных приборов по таблице выбираем основные параметры прожекторной установки.
Ширина освещаемой площади а = 100 м;
Высота прожекторных штанг Н = 15 м;
Расстояние между мачтами 70 м;
Тип лампы ПЗС – 35 или ПСМ– 40;
Мощность N = 500 кВт;
Прожекторы с лампами накаливания
Требуемая освещенность площади Ер лк определяется по формуле :
где Ео – наименьшая освещенность площади лк (Ео = 5 лк);
К – коэффициент запаса.
Количество прожекторов для освещения площади завода nопределяется по формуле :
где m – коэффициент использования светового потока (m = 05);
S – площадь освещаемой поверхности м2;
Рп – мощность лампы Вт.
В одной мачте устанавливаем по n = 4 прожектора тогда количество мачт будет равным
При нечетном количестве мачт принимаем шахматную систему и приводим схему на рисунке.
Далее по таблице в соответствии с типом прожектора и типам лампы определяем минимально допустимую высоту установки прожекторов для освещения площадки. Выбираем высоту установки прожекторов Н = 10 м.
Рисунок – Схема расположения мачт
Система организационных и технических мероприятий и средств обеспечивающих защиту людей от вредного и опасного воздействия электрического тока называется электробезопасностью.
Для защиты от поражения электрическим током применяются отдельно или в сочетании друг с другом защитное заземление зануление малое напряжение защитное отключение и т.д.
Общие требования безопасности при обслуживании электроустановок.
Оперативное обслуживание электроустановок может осуществляться как местным оперативным или оперативно-ремонтным персоналом за которым закреплена данная электроустановка так и выездным за которым закреплена группа установок. Лицам из оперативно-ремонтного персонала обслуживающим электроустановки эксплуатируемые без местного оперативного персонала при осмотре установок оперативных переключениях подготовке рабочих мест и допуски бригад к работе и т.п. В соответствие с настоящими правилами и "ПТЭ электроустановок потребителей" представляются все права и обязанности оперативного персонала. Вид оперативного обслуживания число лиц из оперативного персонала в смену или на электроустановки определяются лицом ответственным за электрохозяйство по согласованию с администрацией предприятия (организации) и указываются в местных инструкциях.
К оперативному обслуживанию электроустановок допускаются лица знающие оперативные схемы должностные и эксплутационные инструкции. Ценности оборудования и прошедшие обучение и проверку знаний в соответствий с указаниями настоящих правил.
Лица из оперативного персонала обслуживающие электроустановки единолично и старшие в смене или бригаде за которыми закреплена данная электроустановка должны иметь группу по электробезопасности не ниже 15 в установках напряжением выше 1000В и 111 в установках напряжением до 1000 В.
Оперативный персонал должен работать по графику утверждённому лицом ответственный за электрохозяйство предприятия или структурного подразделения.
В случае необходимости с разрешения лица утверждавшего график допускается замена одного дежурного другим.
Лицо из оперативного персонала придя на дежурство должно принять замену от предыдущего дежурного а после окончания работы сдать смену следующему дежурному в соответствии с графиком. Уход с дежурства без сдачи смены запрещается. В исключительных случаях оставление рабочего места допускается с разрешения вышестоящего лица из оперативного персонала.
При приемке смены оперативный персонал обязан: ознакомиться по схеме с состоянием и режимом работы оборудования на своем участке путем досрочного осмотра в объеме установленном инструкцией;
- получить сведения от дежурного сдающего смену об оборудовании за которым необходимо вести тщательное наблюдение для предупреждения аварии или неполадок и оборудовании находящимся в ремонте или резерве
- проверить и принять инструмент материалы ключи от помещений средства защиты оперативную документацию и инструкции;
- приемка и сдача смены при загрязненном оборудовании неубранном рабочем месте и обслуживаемом участке запрещается.
Приемка смены при неисправленном оборудовании или ненормальном режиме его работы допускается только с разрешения лица ответственного за данную установку или вышестоящего лица о чем делается отметка в оперативном журнале.
Лицо из оперативного персонала во время своего дежурства является ответственным за правильное обслуживание и безаварийную работу всего оборудования на порученном ему участке.
Старший по смене из оперативного персонала единолично или совместно с администрацией предприятия обязан выполнять требования диспетчера энергосистемы. Инспектора и дежурного предприятия "Энергонадзор" по снижению электрической нагрузки и сокращению расхода электропотребления требования диспетчера энергосистемы о включении питающих и транзитных линий электропередачи а также об отключении отдельных линий при аварийном положении в энергоснабжающей организаций.
Старший по смене из оперативного персонала обязан немедленно поставить в известность диспетчера энергоснабжающей организации об авариях вызвавших отключение.Одной или нескольких линий электропередачи питающих предприятие. Список лиц имеющих право проведения оперативных переговоров с энергосистемой определяет лицо ответственного за электрохозяйство и передаёт в соответствующую оперативную службу предприятия электрических сетей.
При нарушении режима работы повреждении или аварий с электрооборудованием оперативный персонал обязан самостоятельно и немедленно с помощью подчиненного персонала принять меры к восстановлению нормального режима работы и сообщить о происшедшем непосредственно старшему по смене или лицу ответственному за энергохозяйство.
В случае неправильных действий оперативного персонала при ликвидации аварии вышестоящее лицо обязано вмешаться вплоть до отстранения дежурного и принять на себя руководство и ответственность за дальнейший ход ликвидации аварии.
Оперативный персонал обязан проводить обходы и осмотры оборудования и производственных помещений на закрепленном за ним участке. Осмотр электроустановок могут выполнять единолично: лицо из административно-технического персонала с группой по электробезопастности V в установках напряжением выше 1000 Вис группой IV в установках напряжением до 114000В;-лицо из оперативного персонала обслуживающего данную электроустановку.
Список лиц из административно-технического персонала которым разрешается единоличный осмотр устанавливается распоряжением лица ответственного за электрохозяйство.
При осмотре распределительных устройств (РУ) щитов шинопроводов сборок напряжением до 1000В запрещается снимать предупреждающие плакаты и ограждения проникать за них касаться токоведущих частей и обтирать или чистить . их устранять обнаруженные неисправности.
Лицам из оперативного персонала обслуживающего производственное оборудование (электродвигатели генераторы электропечи) и электрическую часть различного технологического оборудования напряжением до 1000В разрешается единолично открывать для осмотра дверцы щитов пусковых устройств пультов управления и др.
При осмотре электроустановок напряжением выше 1000В единолично запрещается: проникать за ограждения входить в камеры РУ выполнять какие-либо работы. Камеры следует осматривать с порога или стоя перед барьером.
Осмотр камер закрытых распределительных устройств (ЗРУ) с входом за ограждение при необходимости разрешается выполнять только лицу с группой по электробезопастности не ниже IV при условии что в проходах расстояние от пола составляет : до нижних фланцев изоляторов - не менее 2м при напряжении до 10 кВ не менее 275 м при напряжении до 35 кВ не менее 35 м при напряжении 110 кВ
-ознакомится со всеми записями распоряжениями за время с его последнего дежурства
-оформить приёмку смены записью в журнале ведомости а также на
оперативной схеме подписями лица принимающего смену и лица сдающего её;
-доложить старшему по смене о вступлении на дежурство и о неполадках замеченные при приемке смены.
Приемка и сдача смены во время ликвидации аварии производства переключении или операции по включению и отключению оборудования запрещения администрации.
Перечень таких ячеек и камер определяется распоряжением лица ответственного за электрохозяйство. При расстояниях меньше указанных вход за ограждения разрешается только в присутствии второго лица с группой не ниже III.
Осмотры выявления и ликвидация нарушений на электроустановках без постоянного наружного персонала производится централизованно выездным персоналом осуществляющим надзор и работы по объекту (или группе объектов) периодичность которых устанавливается ответственным за электрохозяйство в зависимости от местных условий. Результаты осмотров фиксируются в оперативном журнале.
Лица не обслуживающие данную электроустановку допускаются к осмотру с разрешения лица за электрохозяйство цеха.
Двери помещений электроустановок (щитов сборок и т.п.) должны быть постоянно заперты. Для каждого помещения электроустановки должно быть не менее двух Комплектов ключей один из которых является запасным. Ключи от помещения РУ не должны подходить к дверям ячеек и камер.
Ключи должны находиться на учете у оперативного персонала. В электроустановках без постоянного оперативного персонала ключи должны находиться на пульте управления у старшего по смене лица из оперативного персонала. Ключи должны выдаваться под расписку:
-на время осмотра лицам которым разрешен единоличный осмотр и лицам из оперативно-ремонтного персонала в том числе и не находящимся в смене при выполнении ими работ в электропомещениях;
-на время производства работ понаряду или по распоряжению ответственному руководителю работпроизводителю работ или наблюдающему.
Персональные ключи для входа в электропомещение разрешается иметь только лицам из оперативного персонала принимающим и сдающим смену по телефону.
Расчет заземляющего контура.
Определяется сопротивлением растеканию тока одиночного вертикального заземлителя по следующей зависимости:
где р- расчетное удельное сопротивление (р=р0 х Кn);
р0- удельное сопротивление (по даблице 5.2. р0 = 1 х 102 Ом х см3);
Кn- повышающий коэффициент (по таблице 5.3. для IV климатической зоны принемаем Кn = 12);
- длина вертикального заземлителя (принемаем
d - диаметр вертикального заземлителя (принимаем d = 60мм);
h - заглубление полосы связи (принемаем h = 1м).
Выше указанная зависимость справедлива при следующих условиях:
Определяем сопротивление очага заземлителей:
где К0-коэффициент повышения сопротивления очага заземлителей (принимаем К0=25)
R0-допустимое значение сопротивления (по ГОСТ 12.1.030-81 R0=10 Ом)
Определяем ориентировочное количество вертикальных заземлителей:
По вычисленному результату принимаем целое число вертикальных заземлителей n=3.
Принимаем расстояние между вертикальными заземлителями а=2м.
Определяем коэффициент экранирования между вертикальными заземлителями i=086 (по таблице 5.4.).
В соответствии с выбранным значением i определяем истинное значение сопротивления очага заместителей R0:
Длина связи определяется по следующей зависимости:
Сопротивление полосы связи определяется по следующей зависимости:
где b - ширина полосы (принимаем b=60мм);
Сопротивление комбинированного заземлителя определяется по следующей
где 2 – коэффициент экранирования полосы связи с вертикальными заземлителями по табл. 5.5 для отношения расстояния между трубами по их длине al=2 2=089).
Так как расчитанное сопротивление оказалось не соответствующим норме
(Ry = 1639 > 10 Ом ) то необходимо увеличить число вертикальных заземлителей.
Принимаем п = 10 и производим пересчёт:
коэффициент экранирования между вертикальными заземлителями 1 =072
(по таблице 5.4.) истиное значение сопротивления очага заземлителей
Сопротивление полосы:
коэффициент экранирования полосы связи с вертикальными заземлителями 2=089 (по таблице 5.5);
R =––––––––––––––=566Ом
Электрическая система управления агрегатом должна быть подведена таким образом чтобы электрический кабель не терся о стационарные или подвижные элементы следует также исключать возможность намокания кабеля в масле. Рекомендуется подвести электрическую систему в термоустойчивых и маслоотталкивающих кожухах чтобы маршрут их прокладки не пересекался с зонами обслуживания агрегата.
Правила поведения в аварийных ситуациях
Чрезвычайные ситуации техногенного и природного характера продолжают приносить множество бед уносят человеческие жизни. Обстановка заставляет быть в напряжении и постоянной готовности без промедления активно реагировать на события. Неотложные работы при ликвидации ЧС — это деятельность но всестороннему обеспечению аварийно-спасательных работ оказанию населению пострадавшему в ЧС медицинской и других видов помощи созданию условий минимально необходимых для сохранения жизни и здоровья людей поддержания их работоспособности.
К аварийно-спасательным работам относятся поисково-спасательные горноспасательные газоспасательные противофонтанные а также аварийно-спасательные связанные с тушением пожаров работы по ликвидации медико-санитарных последствий ЧС и ряд других подобных работ. При возникновении производственной аварии немедленно проводится оповещение рабочих и служащих предприятия об опасности. Аварийно-спасательные работы приходится проводить при взрывах пожарах обрушениях обвалах наводнениях и других бедствиях. Экстренная медицинская (доврачебная) помощь должна быть оказана непосредственно на месте работ затем — первая врачебная и эвакуация в лечебные учреждения для специализированного лечения. Оказание помощи пострадавшим людям в большинстве случаев не терпит промедления так как по истечении даже незначительного времени все усилия могут оказаться бесполезными.
Специфика спасательных работ состоит в том что они должны выполняться в сжатые сроки. Для конкретных условий они определяются различными обстоятельствами. В одном случае — это спасение людей оказавшихся под обломками конструкций зданий среди поврежденного технологического оборудования в заваленных подвалах. В другом — это необходимость ограничить развитие аварии чтобы предупредить возможное наступление катастрофических последствий возникновение новых очагов пожаров взрывов разрушений. В третьем — быстрейшее восстановление нарушенных коммунально-энергетических сетей (электричество газ тепло канализация водопровод).
От качества проведения аварийно-спасательных и других видов работ в зоне ЧС зависит жизнь и здоровье людей тем или иным образом вовлеченных в условия чрезвычайных обстоятельств. Для достижения наибольшей эффективности работ на месте ЧС требуется комплекс мер включающий законодательную базу фонды экономической поддержки специальное техническое обеспечение обеспечение средствами связи. Не мене важен и организационный аспект позволяющий координировать действия специальных спасательных служб разных уровней в чрезвычайных условиях.
Противопожарные мероприятия
Пожарная безопасность объекта обеспечивает как в рабочем его состоянии так и в случае возникновения аварийной обстановки. Безопасность людей обеспечивается при возникновении пожара в любом месте объекта.
Опасными факторами пожара воздействующими на людей являются открытый огонь искры и дым; повышенная температура воздуха и предметов; пониженная концентрация кислорода и токсичные продукты горения; обрушение и повреждение зданий сооружений установок а также взрыв.
Предотвращение пожара достигают предупреждением образования горючей среды и источников зажигания в ней; поддержанием температуры горячей среды а также давления в горючей смеси ниже максимально допустимого по горючести.
Пожарную защиту обеспечивают максимально возможным использованием негорючих и трудногорючих веществ и материалов вместо пожароопасных т.е. веществ обладающих повышенной пожаровластностью; ограничением количества горючих веществ и изоляции горючем среды; предотвращением распространения пожара за пределы очага загорания; приминанием конструкции объектов с установленными пределами огнестойкости и горючести; эвакуацией людей ; применением средств пожаро тушения пожарной сигнализации и извещений о пожаре средств коллективной и индивидуальной защиты людей организацией пожарной охраны объекта и системой противодымной защиты.
Коллективную и индивидуальную защиту людей при пожаре осуществляют в тех случаях когда их эвакуация затруднена или нецелесообразна. Она должна обеспечивать безопасность людей в течение всего времени действия опасных факторов пожара. Для коллективной защиты используют убежища или защищенные помещения.
Территория предприятий должна постоянно содержаться в чистоте и порядке. Весь мусор производственные отходы и т.п. необходимо систематически удалять на специально отведенные участки. Ко всем зданиям и сооружениям должен быть обеспечен свободный доступ.
Противопожарные разрывы между зданиями и сооружениями не должны использоваться под складирования материалов оборудование и т.д.
Готовая продукция полуфабрикаты тара оборудование и т.п. должны складироваться на определённых участках расположение которых должно быть согласовано с пожарной охраной.
На пожаро- и взрывоопасных участках территории предприятия курение запрещается.
На этих участках устанавливается предупреждающие надписи: "Курить запрещается".
Курение разрешается только в специально отведенных местах где должны иметься урны или бочки с водой для окурков. Места отведенные для курения должны иметь надписи: "Место для курения".
Отогревание замерших водопроводных и канализационных труб открытым огнём запрещается. Трубопроводы следует отогревать паром горячей водой или горячем песком.
Въезд на территорию пожаро- и взрывоопасных предприятий и цехов а также предприятий и цехов со сгораемой кровлей здании не оборудованных искроуловительными приспособлениями с открытыми поддувалами и действующими менее 42 м при напряжении 130-220 кВ.
При въезде на такую территорию должны быть установлены предупреждающие знаки.
Все производственные помещения необходимо постоянно содержать в чистоте и порядке: мусор и отходы производства должны своевременно удаляться.
Проходы выходы коридоры тамбуры лестницы чердачные помещения должны постоянно содержаться в исправном состоянии и ничем не загромождаться.
Спецодежда должна храниться в специально предназначенных для этой цели помещениях. Промасленная спецодежда должна храниться только в развешенном виде в карманах спецодежды запрещается оставлять промасленные тряпки. Оставление после работы одежды на верстаках ящиках у рабочих мест не допускается.
Для цеховых кладовых специально предназначенных для хранения горючих и легковоспламеняющихся жидкостей должны быть установлены нормы хранения этих жидкостей.
Все цеха мастерские склады должны быть обеспечены первичными средствами пожаротушения в соответствии с нормами.
Стационарные пожарные лестницы и несгораемые ограждения на крышах зданий необходимо содержать в постоянной исправности.
В целях создания условий для быстрого использования пожарного инвентаря и облегчения наблюдения за ним рекомендуется устраивать специальные щиты пожарного инвентаря. В цехах мастерских и складах с большой площадью целесообразно устраивать несколько таких щитов. Дороги проезды и подъезды не должны использоваться под складирование различных материалов оборудования сырья готовой продукции и т.п. Все дороги проезды и подъезды должны содержаться в исправности а в ночное время освещаться для обеспечения безопасности проезда. Рельсовые пути и временные канавы не должны затруднять свободного и быстрого проезда пожарного транспорта. Для этого в необходимых местах по согласованию с пожарной охраной должны быть устроены удобные переезды через пути и канавы.
ОХРАНА ОКРУЖАЮЩЕЙ СРЕДЫ
Проблема охраны окружающей среды и рационального использования природных ресурсов является одной из наиболее актуальных тем среди глобальных общечеловеческих проблем так как от ее решения зависит жизнь на земле здоровье и благосостояние человечества.
В нашей Республике вопросам охраны природы и рационального использования ее ресурсов уделяется постоянное внимание. Необходимость охраны природы закреплена в Конституции Республике Казахстан. Для предупреждения правонарушений в области охраны окружающей среды законодательством Республике Казахстан предусмотрено привлечение виновных к ответственности: дисциплинарной административной материальной и уголовной. Для снижения вредного воздействия данной установки на окружающую среду при его эксплуатации предусматриваем мероприятия по борьбе с пылевыделением - орошение для обеспечения предельно допустимых норм вредных примесей в воздухе.
Установка орошения представлена следующими элементами:
- питающий коллектор смонтированный на раме дробилки;
- два комплекта форсунок установленных на входе в дробилку и на ленточном транспортере.
Вода в питающий коллектор подводится пользователем из внешней системы. Для орошения следует использовать только чистую воду так как разнообразные осаждающиеся загрязнения снижают эффективность орошения оказывают также значительное влияние на долговременность работы форсунок.
Дипломный проект Ноль.doc
ВОСТОЧНО-КАЗАХСТАНСКИЙ ГОСУДАРСТВЕННЫЙ ТЕХНИЧЕСКИЙ УНИВЕРСИТЕТ им. Д. Серикбаева
зав. кафедрой «ТМ и О»
РАЗРАБОТКА МОБИЛЬНОЙ ДРОБИЛЬНОЙ УСТАНОВКИ
Специальность 050713 – Транспорт транспортная техника и технологии
Пояснительная записка
0713 ДП 00. 00. 000 ПЗ
Научный руководитель
Усть-Каменогорск 2010
Технологическая часть
Безопасность и экологичность проекта
В данном дипломном проекте предлагается разработка мобильной дробильной установки а в частности упрощение и сокращение сроков по обслуживанию и ремонту одной из сборочных единиц – дробилки ударного действия.
На основании литературной и патентной проработки предлагается замена старых ударных и отражательных элементов на элементы с новой ситемой крепления. Также подобрано приспособление используемое в процессе изготовления детали представлена технология изготовления детали раздел с расчётами по технике безопасности и экологичности проекта. Произведён расчёт технико - экономических показателей внедрения.
Дипломный проект состоит из пояснительной записки и графической части:
Пояснительная записка содержит:
Графическая часть содержит 7 листов формата А1
Мобильная дробильная установка
1 Область применения дробильно-сортировочного оборудования
2 Основные преимущества мобильной дробильной установки
Модернизация мобильной дробильной установки
1 Общее описание мобильной дробильной установки
2 Литературно-патентный поиск и предложения по модернизации
3 Описание конструкции о принцип работы дробилки ударного действия
4 Определение работоспособности и расчет основных параметров мобильной дробильной установки
Технология изготовления детали
1 Спроектированное приспособление
2 Описание конструкции приспособления и принцип работы
3 Расчёт приспособления
4 Выбор материала и обоснование метода получения заготовки
5 Маршрут обработки детали
1 Общие правила безопасности проведения работ на установке
2 Защита от шума и вибрации
3 Установление опасных зон и расчет на прочность ограждения
5 Электробезопасность
6 Правила поведения в аварийных ситуациях
7 Противопожарные мероприятия
8Аварийные и чрезвычайные ситуации
9 Охрана окружающей среды
1Расчет единовременных затрат производства дробилки подрядным способом
2 Расчет единовременных затрат при хозяйственном способе производства дробилки
3 Расчет текущих затрат
4 Расчет экономической эффективности и срока окупаемости от внедрения в ОТМ
5 Расчет точки безубыточности для ББ и НО
Приложение А – Справка о патентно-информационном поиске при исследовании
Приложение Б – Маршрутная и операционная карты спецификация нормального инструмента
Минерально-сырьевая база является фундаментом строительной отрасли - одной из основных отраслей экономики. Постоянно растущие в последние годы темпы жилищного и промышленно-гражданского строительства а также рост государственных инвестиций в дорожное строительство вызвали необходимость увеличения добычи и переработки основных нерудных материалов: щебня гравия и песка. Производственные мощности существующих с советских времен стационарных щебеночных комбинатов уже не справляются с запросами рынка а поэтому для увеличения объема производства большинство комбинатов пошли на техническое переоснащение морально устаревшего дробильного оборудования.
Наряду с поставками стационарных дробильно-сортировочных комплексов стал развиваться и рынок мобильного дробильного оборудования. Это обстоятельство позволило включать в процесс разработки небольшие карьеры отвалы вскрышных пород и месторождения песчано-гравийных смесей на которых строительство стационарных дробильных заводов ранее было нерентабельно. Широкий модельный ряд дробилок – щековые конусные роторные и грохотов позволяет получать конечный продукт – щебень любого заданного в соответствии с ГОСТами и СНИПами качества. Мобильность таких дробильно-сортировочных комплексов позволяет быстро менять технологическую схему переработки первичного материала и получать конечные фракции щебня по количеству качеству и размеру соответствующие запросом заказчика что делает его актуальным.
Также в больших городах начинает остро вставать проблема по утилизации строительного мусора. Данную проблему позволило решить появление мобильного дробильного оборудования.
МОБИЛЬНАЯ ДРОБИЛЬНАЯ УСТАНОВКА
1 Область применения дробильно – сортировочного оборудования
Производство нерудных строительных материалов:
Дробление и сортировка (грохочение) горных пород для получения щебня и искусственного песка.
Дробление и сортировка песчано-гравийных смесей дробление сортировка валунов и галечника для получения щебня.
Сортировка отсевов дробления для получения щебня мелких фракций и искусственного песка.
Ремонт и строительство автомобильных и железных дорог:
Дробление и сортировка асфальта при технологиях рецикла дорожных покрытий.
Получение качественного щебня узких фракций для мобильных асфальтовых заводов в непосредственной близости проведения дорожно-строительных работ.
Ремонт и строительство железнодорожных путей:
Получение качественного щебня для устройства балластного слоя железнодорожного пути.
Переработка строительного мусора и железо-бетонных конструкций:
Дробление и сортировка железобетонных конструкций кирпичного лома и прочих отходов для получения вторичных нерудных строительных материалов и железного лома непосредственно на строительных площадках при сносе зданий и сооружений в качестве альтернативы вывозу строительного мусора
Горнорудная промышленность:
Рудоподготовка непосредственно в карьере для дальнейших технологических процессов.
Угольная промышленность:
Дробление измельчение и сортировка угля.
Дробление и сортировка шлаков регенерация литейных песков.
Эффективность и многофункциональность – мобильной дробильной-установки имеет большую удельную производительность и высокие технические характеристики благодаря чему достигаются кратчайшие сроки амортизации низкие затраты на обслуживание. Данные установки могут применяться для переработки (дробления и грохочения) самых разных материалов (нерудные материалы руда уголь строительный мусор и т.д.) и производства различного щебня;
Мобильность дробильной утсановки:
Автономность – каждая дробильная установка оснащена двигателем нет необходимости в отдельном источнике питания;
Экономия – низкие транспортные расходы т.к. дробильная установка не требует спецтранспорта для локальных перемещений и исключает необходимость применения самосвалов и конвейеров для транспортировки рудных и нерудных материалов к самой установке;
Универсальность – появляется возможность гибкого в построения различных дробильно-сортировочных комплексов на одном и том же комплекте дробильного оборудования;
Простота эксплуатации – не требуется комплекс мер для подготовки и ввода в эксплуатацию.
Практичность – для начала разработки любого месторождения (малого или большого) требуется только доставить дробильное оборудование на место и начать работать.
МОДЕРНИЗАЦИЯ МОБИЛЬНОЙ ДРОБИЛЬНОЙ УСТАНОВКИ
1 Общее описание мобильной дробильной установки
Мобильная дробильная установка представлена на листе графической части 050713 ДП 00.00.000 СБ со смонтированными на раме рабочими узлами. Загрузка материала в засыпное отверстие осуществляется при помощи погрузчика. Загрузочное отверстие смонтировано над вибробункером. Вибробункер подает материал из загрузки в ударную дробилку. Ленточный конвейер с шириной ленты 650 мм принимает продукт дробления из-под дробилки и транспортирует наружу машины.
Мобильная дробильная установка предназначен для раздробления материалов большой и средней жесткости с размером садива макс. 500 мм.
Состоит из следующих основных подузлов:
Гидравлическая установка
Оросительная установка
Электрическая установка
Рама является сварной конструкцией в которой четыре двутавровые продольные балки соединенные соответствующими поперечными элементами представляют собой основание служащее для монтажа рабочих узлов.
На передней части рамы смонтирован загрузочный бункер и вибробункер. В центральной части расположен электрический двигатель служащий для приведения в действие самой дробилки. Собственно дробилка расположена в задней части рамы. Вдоль всей рамы проходит трасса ленточного конвейера принимающего продукт дробления
Привод дробилки представлен электрическим двигателем передающим оборотный момент на дробилку посредством ременной передачи. Раздвижная рама двигателя дает возможность регулировать натяжение клиновых ремней
Вибробункер приводится в движение инертным электровибратором с возможностью шагового изменения возмущающей силы. Регулировка возмущающей силы осуществляется при выключенном оборудовании посредством изменения взаиморасположения неуравновешенных масс. Транспортировочная поверхность выложена облицовкой из устойчивых к истиранию металлических листов. Подаватель осажден на восьми цилиндрических пружинах. Для гашения вибрации во время запуска и остановки использованы резиновые амортизационные элементы.
Ленточный конвейер шириной ленты 650 мм принимает продукт дробления транспортируя его наружу машины. Лента приводится в движение электробарабаном.
Лента перемещается на верхних и на нижних роликах. Боковое смещение ленты ограничено двумя направленными роликами смонтированными в узле приводного барабана.
Для очищения ленты предусмотрены два скрепера:
- Скрепер (для очищения внутренней поверхности);
- Крестовой скрепер смонтированный в узле приводного барабана.
Гидравлическая система служит для упрощения обслуживания машины:
- Замены цепного занавеса;
- Замены отбойных плит облицовки стен и ударных планок ротора.
Целью оросительной установки является максимально ограничить запыление в зоне работы машины. Для этого установлены два комплекта оросительных форсунок – на входе в дробилку и на ленточном конвейере. Форсунки запитываются из трубопровода шахтной технологической воды с рекомендуемым давлением 5-10 bar.
Задачей установки централизованной смазки является обеспечить периодическое независимое от оператора смазывание подшипников и их лабиринтных крышек.
Работу смазочного насоса контролирует программируемый командоконтролер дающий возможность установить время работы а также перерывов в работе. Объем смазочной порции поставляемой в конкретную точку регулируется при помощи прогрессивного распре.
2 Литературно-патентный поиск и предложение по модернизации
Для анализа существующих разработок в области дробления материалов был произведен литературно-патентный поиск. Был рассмотрен ряд литературы просмотрены информационные Интернет-сайты наименования которых указаны в библиографии. Из указанных выше источников определились критерии выбора для модернизации оборудования мобиьной дробильной установки.
Авторское свидетельство RU B02C1306 – РОТОРНАЯ ДРОБИЛКА.
Роторная дробилка (рисунок 1) содержит корпус камеру дробления ротор с билами колосниковую решетку установленную на корпусе посредством горизонтального шарнирного узла и подпружиненную к корпусу колосники решетки выполнены в виде двуплечих рычагов и установлены независимо друг от друга а каждый из них подпружинен рессорами S-образного профиля при этом один конец рессоры закреплен на свободном конце колосника а второй свободный конец размещен с возможностью взаимодействия при повороте колосника с горизонтальной полкой съемного кронштейна шарнирный узел выполнен в виде неподвижной оси а колосники снабжены вырезами с возможностью их взаимодействия с осью и опирания на нее сверху плечо рычага со стороны рессоры выполнено прямоугольного поперечного сечения и установлено с возможностью взаимодействия с нижней кромкой колосника в его рабочем положении с упором полки а на остальном участке - трапецеидального между колосниками и с возможностью взаимодействия с ними на оси размещены сменные фиксаторы ширина которых принята равной заданной величине щелевого зазора между колосниками. Изобретение позволяет повысить надежность работы дробилки за счет исключения забивания колосников.
Рисунок 1 – Роторная дробилка
Авторское свидетельство RU B02C1318- РОТОРНАЯ ДРОБИЛКА
Изобретение относится к устройствам для дробления материалов. Сущность изобретения заключается в формировании направленного потока легкой фракции на отражающую решетку конструктивное выполнение которой препятствует выносу из дробилки вместе с волокном породных частиц крупностью более 1 мм. Роторная дробилка (Рисунок 2) содержит корпус 1 горизонтальный ротор 2 с билами 3 установленные одна за другой с зазором отбойные плиты 4 и 5 диффузор 6 для вывода из дробилки с помощью воздуха легкой фракции. В зазоре между отбойными плитами 4 и 5 размещены закрепленные к ним направляющие пластины 7 и 8 образующие канал 9 над которым под углом 20-30° к его оси установлена отражающая решетка 10. Отражающая решетка 10 состоит из двух ярусов продольных элементов.
Рисунок 2 – Роторная дробилка
Роторная дробилка модели «СМД-5 ВЕЙДЕР»
типоразмера «ДР 1500 4х2»
Роторная дробилка модели «СМД-5 ВЕЙДЕР» (Рисунок 3) предназначена для среднего и мелкого дробления шлака металлургического известняка доломита мергеля мрамора гипса руд малой абразивности и других подобных материалов предел прочности которых не превышает 600 кгссм2 а размер кусков 180 мм.
Помимо непосредственного дробления роторная дробилка данной модели также может использоваться в качестве динамического гранулятора что позволяет проводить обогащение каменных пород по форме и прочности за счет разрушения слабых включений без ослабления структурной прочности целевого продукта.
Роторная дробилка модели «СМД-5 ВЕЙДЕР» имеет простую но вместе с тем очень рациональную конструкцию каждый элемент которой продуман до мелочей и работает на повышение эффективности дробления упрощение технического обслуживания снижение стоимости эксплуатации оборудования.
Для достижения этих целей МП«ТЕХПРИБОР» был использован целый ряд оригинальных технических решений.
Краткий перечень основных преимуществ новых роторных дробилок позволяет убедиться в этом:
Оригинальные билы роторной дробилки «СМД-5 ВЕЙДЕР» имеют не одну а целых две рабочих грани что позволяет восстановить выбранные параметры дробления просто развернув ударные элементы. Такое техническое решение сделало возможным существенное увеличение сроков службы инструментов дробления за счет более полного использования металла бил. Теперь их замена может проводиться в два раза реже нежели в других моделях оборудования аналогичного назначения.
Рисунок 3 – Роторная дробилка
3 Описание конструкции и принцип работы дробилки ударного действия
Дробилка изображена на листе графической части 050713 ДП 03.00.000 СБ
Ударная дробилка обеспечивает производительность на уровне 20-50 тчас одновременно позволяя перерабатывать широкую гамму материалов.
Основными элементами дробилки являются:
- Стены с отбойными плитами.
На валу ротора смонтирован бандаж при помощи блокирующих колец. Вал ротора осажденный в корпусе подшипников с бочкообразными роликоподшипниками прикреплен к нижним и боковым стенкам корпуса дробилки. Упомянутые подшипники оснащены внутренними крышками а также наружными крышками.
Смазывание подшипников и лабиринтов крышек происходит периодически посредством программируемой установки централизованной смазки.
Корпус дробилки является конструкцией изготовленной из отдельных элементов а именно:
- Нижних боковых стенок;
- Стенки с отбойными плитами;
Нижние боковые стенки и боковые стенки оснащены ревизионными экранами соответственно закрываемыми дверями – для контролирования состояния ротора и отбойных стенок.
Стены с отбойными плитами являются наклонными плитами и смонтированы на петлях крепящих их к нижней задней стенке дробилки. С двух сторон стен с отбойными плитами смонтированы гидравлические цилиндры. Эти цилиндры после предварительного освобождения резьбовых соединений стен позволяют открыть дробилку давая возможность ремонтным службам заменить отбойные плиты и облицовку стен дробилки а также заменить ударные планки ротора. Верхняя и нижняя отбойные стенки прикреплены к задней стенке при помощи болтов с пружинами.
Верхняя отбойная стенка закреплена при помощи одного болта с дисковой пружиной а отбойная стенка нижняя – при помощи двух болтов со спиральными пружинами. Верхняя и нижняя отбойные стенки подвешены над ротором в качестве элементов взаимодействия с ротором обеспечивающих многократное возвращение материала в зону работы ротора а кроме того обеспечивают более эффективное раздробление материала и отбивание зерен от стен. Отбойные стены принимают своей инертностью энергию дробления и могут «натягиваться» пружинами увеличивающими силу «отбивания» .Кроме того они обеспечивают наклон отбойных стен в случае попадания в дробилку материала не подлежащего дроблению (стального лома).
Угол наклона отбойных стен может регулироваться при помощи натяжных болтов. Стены дробилки выложены облицовкой из стали устойчивой к истиранию защищающей стены от быстрого износа.
Внедрив билы новой конфигурации имеем: не одну а целых две рабочих грани что позволяет восстановить выбранные параметры дробления просто развернув ударные элементы. Такое техническое решение сделало возможным существенное увеличение сроков службы инструментов дробления за счет более полного использования металла бил. Теперь их замена может проводиться в два раза реже нежели в других моделях оборудования аналогичного назначения.
Практическая производительность дробильного оборудования серьезно страдает из-за сложности и высокой трудоемкости технического обслуживания необходимости держать на складе разнообразную номенклатуру инструментов дробления защитной брони и т.д.
Так же крепления элементов дробления требуют очень внимательного к себе отношения. Зачастую резьбовые соединения превращаются в трудно разъемные уже после переработки нескольких тонн каменных материалов. Вот почему для установки ударных элементов роторной дробилки не используются гайки. Билы просто вставляются в направляющие и удерживаются от осевого смещения специальными фиксаторами. Благодаря чему разворот или полная замена инструментов дробления выполняется в течение 15-20 минут силами одного человека без использования грузоподъемных механизмов.
Для сокращения времени технического обслуживания или сроков ожидания поставки сменных деталей билы ротора и билы отбойных плит имеют одинаковые размеры а 90% элементов брони корпуса полностью взаимозаменяемы.
4 Определение работоспособности и расчет основных параметров
мобильной дробильной установки
4.1 Выбор режима работы виброконвейера и определение основных параметров
Исходные данные для расчета:
Производительность тч 40
Длина одного виброконвейера м 28
Насыпная масса кгм3 1600
Максимальная температура огарка°С 300
Крупность частиц мм 500
Угол наклона виброконвейера к горизонту град 3
На рисунке 4 представлена схема сил действующих на частицу груза находящуюся на грузонесущей поверхности рабочего органа при вибротранспортировании. На частицу груза массой m при вибрации грузонесущей поверхности под углом b к горизонту с амплитудой А1 и частотой w действуют следующие силы: сила тяжести (mg); сила инерции (m×A1×w2) которая раскладывается на две составляющие – горизонтальную (m×A1×w2×cosb) стремящуюся сдвинуть частицу в сторону транспортирования и вертикальную (m×A1×w2×sinb) стремящуюся оторвать частицу груза от грузонесущей поверхности
и уменьшающую ее давление на эту поверхность и сила трения Fтр = (m×g – m×A1×w2×sinb)×f которая препятствует скольжению частицы груза вперед в сторону транспортирования.
Рисунок 4 – Схема сил действующих на частицу
Частица будет скользить вперед при выполнении условия:
m×A1×w2×cosb ³ (m×g – m×A1×w2×sinb)×f (1)
При оптимальном значении угла вибрации b = 30 ° при коэффициенте трения породы о сталь f = 07 условие движения частицы груза вперед выразится неравенством:
А1×w2 ³ 565 м×с-2 (2)
Условие скольжения частицы в сторону противоположную транспортированию будет выражаться следующим неравенством:
m×A1×w2×cosb ³ (m×g + m×A1×w2×sinb)×f (3)
При тех же значениях b и f это условие выразится неравенством:
Анализ показывает что частица груза значительно большую часть периода колебаний скользит вперед при этом сила трения из-за действия вертикальной составляющей ускорения (m×A1×w2×sinb) значительно уменьшается что способствует снижению изнашивающего эффекта и повышению долговечности грузонесущей поверхности рабочего органа виброконвейера при транспортировании даже высокоабразивных материалов. При значении вертикальной составляющей ускорения рабочего органа (А1×w2×sinb = g) равном ускорению силы тяжести сила трения частицы о грузонесущую поверхность становиться равной нулю частица отрывается от поверхности и совершает микрополет способствуя эффективности вибротранспортирования без изнашивающего воздействия на грузонесущую поверхность. При этом условие отрыва частицы от грузонесущей поверхности выразится следующим соотношением:
К основным параметрам вибрационного конвейера могут быть отнесены: поперечные размеры грузонесущего органа (диаметр труб или ширина и высота желоба) в м высота слоя материала в транспортирующем органе hс в м скорость вибротранспортирования V в мс амплитуда колебаний рабочего органа А1 и тяжелой уравновешивающей рамы А2 в м круговая частота колебаний w в радс угол вибрации b - острый угол между направлением колебаний и направлением транспортирования в град жесткость упругой системы С в Нм количество упругих элементов z.
Наименьший поперечный размер желоба Н м выбирается при соблюдении условия:
где d – наибольший диаметр транспортируемого материала м
Н ³ (3 5) × 05= 15 м
По конструктивным соображениям и с учетом того что в виброконвейера могут попадать крупные куски принимаем поперечное сечение шириной В = 06 м высотой Н = 03 м.
Высота слоя материала желобе hc м не должна превышать значения определяемого по формуле:
hc (04 05) × 15 = 06 075 м
Принимаем hc = 06 м. Необходимая скорость вибротранспортирования V мс в зависимости от заданной производительности и принятых значений В и Н определится по формуле:
где Fп – площадь поперечного сечения потока транспортируемого материала в желобе (определяется по выбранным размерам грузонесущего органа и высоте слоя транспортируемого материала) м2;
Q – производительность виброконвейера м3ч.
Площадь поперечного сечения потока транспортируемого материала Fп м2 определяем по формуле:
Fп = 06 × 06 = 036 м2
Скорость вибротранспортирования определяется параметрами вибраций и свойствами материала и может быть вычислена для грузов по формуле:
где А1 – амплитуда колебаний рабочего органа м;
w - круговая частота колебаний радс;
b - угол вибрации град;
е – основание натурального логарифма;
d - угол полета частиц груза рад;
j0 – угол отрыва частиц груза от грузонесущей поверхности град;
cх – коэффициент определяемый по формуле:
где nх – коэффициент характеризующий вязкостные сопротивления среды при перемещении груза в направлении транспортирования на участке полета.
Для мелкодисперсных грузов nх = 4 10 с-1 d = 2 3 рад j0 = 40 100. Для кусковых nх = 6 с-1 d = 3 рад j0 = 42 °.
Выбор параметров сводится к определению таких их значений при которых обеспечивалась бы высокая скорость вибротранспортирования надежная и долговечная работа всех элементов конструкции при наименьшем истирающем воздействии транспортируемого материала на грузонесущую поверхность рабочего органа и незначительный уровень динамических нагрузок. Обычно рекомендуется выбирать большую амплитуду колебаний и меньшую частоту. Приняв предварительно амплитуду колебаний А1 = 0008 м и частоту n = 570 колмин определим значение скорости вибротранспортирования.
Круговая частота колебаний w с-1 определяется по формуле:
По экспериментальным данным скорость вибротранспортирования при амплитуде колебаний 0008 м и частоте 570 колмин составляет 013 мс то есть совпадает с расчетной.
При скорости вибротранспортирования V=003 мс фактическое сечение потока транспортируемого материала Fф м составит
Высота слоя транспортируемого груза при этом составит hсл = 009 м а коэффициент заполнения сечения рабочего органа yф = 03.
Таким образом окончательно выбираем следующие основные параметры вибрационного конвейера: амплитуда колебаний рабочего органа А1 = 0008 м; частота колебаний n = 570 колмин; круговая частота колебаний w = 60 с-1; угол вибрации - b = 30 °.
Коэффициент режима работы вибротранспортирующей установки Кр представляющий собой отношение вертикальной составляющей ускорения рабочего органа к ускорению силы тяжести характеризующий режим работы установки и уровень вертикальных динамических нагрузок на узлы и детали конструкции определяется по выражению:
Это значит что режим движения груза реализуется с подбрасыванием обеспечивающим надежную и долговечную работу виброконвейера.
4.2 Определение основных параметров ленточного конвейера
Определение ширины ленты конвейера
Ширину ленты конвейера определяем по производительности конвейера и крупности перемещаемого материала.
Площадь поперечного сечения материала при желобчатой ленте F м2 определяется по формуле:
где В – ширина ленты м.
Производительность конвейера Q тч определяется по формуле:
Q = 3600 × F × V × g (14)
Q = 3600 × 011 × В × V × g (15)
где V – скорость движения ленты мс;
g - плотность транспортируемого материала тм3.
Ширина ленты В м определяется по формуле:
Из стандартного ряда по ГОСТ 20 – 76 принимаем ширину ленты В = 650 мм.
Определяем ширину ленты из условия крупности перемещаемого материала по формулам:
для отсортированного материала по формуле:
В ³ 33 × аmax + 02 (17)
где аmax – максимальная крупность перемещаемого материала м.
В ³ 33 × 044 + 02 = 0552 м
для рядового материала по формуле:
В ³ 2 × аmax + 02 (18)
В ³ 2 × 004 + 02 = 028 м
Определение необходимой мощности двигателя
Определение необходимой мощности двигателя начинаем с приведения кинематической схемы ленточного конвейера изображенной на рисунке 5.
Рисунок 5 – Схема ленточного конвейера
Мощность на валу приводного барабана Nб кВт определяется по формуле:
Nб = (000015 × Q × L + 0003 × Q × H + 003 × L × В × V) × К1 × К2 +К3 × Q (19)
где Q – производительность конвейера тч;
Н – высота подъема материала м;
V – скорость движения ленты мс;
К1 – коэффициент учитывающий влияние относительной длины конвейера (1; 005; 115; 125 для всей длины конвейера соответственно 50 30 – 50 15 – 30 более 15 м);
К2 – коэффициент равный 1 если разгрузочная тележка отсутствует;
К3 – коэффициент учитывающий расход энергии на разгрузку конвейера (0; 00008; 0005 при разгрузке через концевой барабан).
Nб = (000015 × 80 × 99 + 0003 × 80 × 05 + 003 × 99 × 065 × 228)
× 1 + 0005 × 80 = 6 кВт
Подбираем двигатель МТКF 112 – 6 с мощностью на валу N = 65 кВт и с числом оборотов n = 865 обмин.
Для последующего расчета необходимы следующие поточные нагрузки:
От транспортируемого груза q кгм определяем по формуле:
П – производительность ленточного конвейера м3ч.
От веса вращающихся частей роликов рабочей ветви qр кгм определяем по формуле:
От веса вращающихся частей роликов холостой ветви qх кгм определяем по формуле:
Gp – масса вращающихся частей роликов кг (Gр = 10 кг).
Геометрические размеры роликоопор для рабочей ветви выбираем следующие:
а = 006 × 650 = 39 мм
Принимаем а = 40 мм.
Геометрические размеры роликоопор для холостой ветви выбираем следующие:
d - толщина прокладки мм (d = 12 мм);
n1 – толщина верхней прокладки мм (n1 = 4 мм);
n2 – толщина нижней прокладки мм (n2 = 4 мм);
Натяжение в характерных точках тягового контура S определяем по формуле:
S = К × S = 103 × S1 (24)
- S = S × lw×d2 = 1035 × 2 × Н0035×0314 = 104 × S1
где w - коэффициент сопротивления движению ленты от типа подшипника смазки уплотнения запыленности атмосферы.
По рекомендациям w= 0065
- S5 = S4 + w4-5 = S4 + (q0 +qр) × L4-5 × w = 104 × S1 – 135 + (118 +73)
73 × 0035 = 104 × S1 – 93 (26)
- S6 = n × S5 = 105 (27)
- S7 = S6 + w6-7 = 102 (28)
Сопротивление движению ленты на загрузочном участке W кг определяется по формуле:
где g – ускорение свободного падения мc2 (g = 98 мс2);
h – высота падения груза на ленту м (h = 05 м).
По каталогу выбираем двигатель АОП – 41 – 4 по ГОСТ 19523 – 81 со следующей технической характеристикой:
Поскольку угол наклона боковых роликов желобчатых роликоопор составляет 20° то принимаем ленту с прокладками из синтетической резины с пределом прочности прокладки Gр = 50 кгмм.
Лента воспринимает максимальное натяжение Smax = S = 600 запас прочности n = 10.
Определяем число прокладок (основных) ленты iпо формуле:
где В – ширина ленты м;
n – запас прочности;
Gp – масса вращающихся частей роликов кг.
Принимаем ленту имеющую три основные прокладки.
Поскольку первоначально было принята для расчета лента с шестью прокладками то перерасчета не требуется.
Необходимая глубина проникновения дробимого материала в зону вращающегося ротора обеспечивается скоростью падения материала при загрузке его в дробилку.
Скорость падения куска Vк определяется по формуле:
где С – глубина падения
t – время приближения к куску.
где Dм – наибольший размер куска мм
где n – частота вращения ротора обмин;
z – число рядов бил на роторе
Высота падения куска Н определяется по формуле:
где g – ускорение свободного падения
Мощность электродвигателя:
где Dр – диаметр ротора
Определение реакций в опорах построения эпюр изгибающих моментов (рисунок 6).
Вертикальная плоскость
Горизонтальная плоскость
Суммарные реакции опор:
Величина расчетного момента:
где [] – допускаемое напряжение изгиба для материала вала Нм2.
Для Стали 45 В = 750 МПа т = 450 МПа []=08 · т=08·450=360МПа
Рисунок 6 Эпюра изгибающих моментов
Вал по прочности работоспособен.
ТЕХНОЛОГИЯ ИЗГОТОВЛЕНИЯ ДЕТАЛИ
1 Спроектированное приспособление
Для сокращения сроков по выполнению разборочных работ и уменьшения трудоемкости этих работ в качестве приспособления выбран пневматический пресс для распрессовки и запрессовки (смотреть лист графической части 050713 ДП .00.00.100 СБ).
Конструкция пневматического пресса состоит из корпуса который скреплен с матрицей при помощи колонок 18. На корпусе 23 с помощью шпилек 17 крепится крышка 16 в отверстие которой ввернут штуцер для подвода сжатого воздуха. Между корпусом и крышкой установлена резиновая диафрагма 13 к которой крепится шток 27 последний перемещается вдоль своей оси на шпонке в направляющих втулках. На конце штоке 27 при помощи насадки 24 крепится пуансон 22. Для управления пневматическим прессом служит кран. Он состоит из корпуса в котором находятся клапана 5 и 7. Управление краном осуществляется педалью 11 через толкатели 10 и 6.
Пневматический пресс работает следующим образом.
На матрицу 19 кладут заготовку. При нажатии на педаль 11 сжатый воздух из сети по открывающимся отверстиям направляется по шлангу в полость над диафрагмой пресса. Под действием давления диафрагма прогибается и действует на шток 27 который перемещается вниз.
Отпуская педаль клапана под действием пружин будут подниматься. При этом закроется впускное отверстие а выпускное откроется. Шток также под действием пружины 29 пойдет вверх и воздух из полости над диафрагмой уйдет в атмосферу.
Рассчитываем шпильки соединяющие крышку с цилиндрическим сосудом для сжатого воздуха. Давление сжатого воздуха в цилиндре равняется Р = 5 кгсм2 причём болты нормальной точности изготовленные из стали Ст3. Шпильки соединения нагружены одинаково.
Внешнюю силу Q действующую на болтовое соединение представляющую собой силу внутреннего давления сжатого воздуха на крышку цилиндра определяем по формуле:
Определяем внешнюю силу Р Н приходящуюся на один болт:
Определяем осевую растягивающуюся силу Ро Н действующую на болт после предварительной затяжки приложения к нему внешней силы Р:
где - коэффициент внешней нагрузки = 05
R - коэффициент затяжки болта R =3.
Примем по ГОСТ 380-94 для стали Ст3 предел текучести т = 22 кгмм2 для болтов допускаемый коэффициент запаса прочности (n) = 3 по формуле
определим для них допускаемое напряжение на растяжение (р) кг см2:
Вычислим требуемый внутренний диаметр резьбы болта D1 мм по формуле:
По СТСЭВ 180 – 75 для болтов принимаем резьбу М12 внутренний диаметр которой d1 = 101 мм.
Принятым размером резьбы болтов и толщины скрепленных деталей соответствуют: Болт М12 ГОСТ7798–70 и гайка М12 ГОСТ 591 –70.
Коэффициент запаса (n) = 3 был выбран правильно т.к. такой коэффициент запаса рекомендован для болтов М6 – М16.
По ГОСТ 5915 – 70 наружный диаметр опорной поверхности гайки а=20 мм. причём модуль упругости материала болта Ст3 Е1 = 21 х 10 6 кгсм2 и материал прокладки картон Е2 = 21 х 10 4 кгсм2.
По формуле определяем коэффициент податливости болта б см кг:
F=1131 см2 - площадь поперечного сечения стержня болта;
Е = 2 · 106 – модуль упругости материала болта.
Диаметр отверстия для болта примем dо = 13 мм по формуле вычислим коэффициент податливости скрепляемых болтом деталей б см кг:
где h1 =2 см h2 = 2 см – толщина сжимаемых болтом соединяемых деталей;
F1 = 57.4 см2 F2 = 1124см2 – площади поперечных сечений конусов давления соответствующих деталей.
Е12 = 21 · 106 кг см2 – модули упругости материалов этих деталей.
Затем по формуле определяем коэффициент внешней нагрузки :
Таким образом никакого перерасчёта не требуется.
4 Выбор материала и обоснование метода получения заготовки
При выборе заготовки для данной детали необходимо назначить метод ее получения определить размеры конфигурацию допуски и припуски на
обработку. Деталь – палец изображена на рисунке 7.
При выборе заготовки необходимо обеспечить заданное качество готовой детали при ее минимальной себестоимости.
Заготовкой в нашем случае является пруток прокатной стали.
Это объясняется тем что производство единичное и получить заготовку другими способами невыгодно.
В качестве материала заготовки назначена Сталь45 ГОСТ 1050 – 88. Тогда заготовка будет иметь вид и форму прутка диаметром 85мм и длиной не менее 170мм.
Изготовление детали состоит из следующих операций: отрезание точение сверление шлифование.
Операция 1 – отрезание
Отрезаем от круглого профиля диаметром 85 мм заготовку длиной 180 мм с помощью дисковой сегментной пилы ГОСТ 4047-82. Разрезание производим на отрезном станке 8Г642.
Для дисковой сегментной пилы принимаем подачу Sz = 005мм.
Скорость резания принимаем Vрез = 20ммин
Подача Sм определяется по формуле
где Z – число зубьев пилы
n – частота вращения пилы обс
где - окружная скорость пилы радс;
где Vр – скорость резания мс;
Продолжительность операции Топ:
где То – основное время операции с;
где Дз – диаметр заготовки мм;
Тв – вспомогательное время с;
Дополнительное время Тдоп определяется по формуле:
Полное штучное время выполнения операции Тшт:
Операция 2 – точение
Заготовку устанавливаем в центра токарного станка.
Для обработки подведем резец проходной 1-го исполнения ГОСТ 18869-73.
Глубину резания t принимаем:
для чернового точения: t = 16мм;
для чистового точения: t = 01мм;
Подача S для чернового точения: S = 09ммоб;
для чистового точения: S = 02ммоб.
Скорость резания при наружном продольном и поперечном точении и растачивании рассчитывают по эмпирической формуле:
где Т – стойкость резца мин;
при одноинструментной обработке Т = 30-60 мин. Значения коэффициента Cv показателей степеней x y и m подбираем
x = 015для чернового x = 015 для чистового
y = 045 точения y = 020 точения
Кv – поправочный коэффициент
Кv = Кmv ·Кnv ·К (54)
где Кmv –коэффициент учитывающий влияние материала заготовки;
Кmv находим по формуле:
где Кr – коэффициент характеризующий группу стали по обрабатываемости
- предел прочности при растяжении МПа;
nv – показатель степени
Кпv –коэффициент отражающий состояние поверхности заготовки
Киv – коэффициент учитывающий качество материала инструмента
Для чернового точения:
Для чистового точения:
Силу резания Н принято раскладывать на составляющие силы направленные по осям координат станка (тангенциальную Pz радиальную Py и осевую Px). При наружном продольном и поперечном точении эти составляющие рассчитывают по формуле:
Постоянная Ср и показатели степени x y и n
Кр – поправочный коэффициент
где Кmp – коэффициент учитывающий влияние качества обрабатываемого материала на силовые зависимости;
где - предел прочности стали при растяжении МПа;
- поправочные коэффициенты учитывающие влияние
геометрических параметров режущей части инструмента;
Kpz=09·108·115·10=112;
Kpy=09·044·16·10=063;
Мощность резания N кВт рассчитывают по формуле:
где V – скорость ммин;
Pz– тангенциальная сила резания Н;
Частота вращения заготовки:
где V – скорость резания ммин;
D – диаметр обрабатываемой заготовки мм;
Основное операционное время:
где L – длина обработки мм;
Вспомогательное время:
Дополнительное время:
Операция 3 – точение
Подбираем подачу S:
для чернового точения: S = 09ммоб;
при одноинструментной обработке Т = 30-60 мин. Значения коэффициента Cv показателей степеней x y и m подбираем по 7 табл. 17
Кv = Кmv ·Кnv ·К (67)
Киv – коэффициент учитывающий качество материала инструмента
где Кр – поправочный коэффициент
геометрических параметров режущей части инструмента
Для чернового точения:
Операция 4 – точение
Скорость резания при наружном продольном и поперечном точении и растачивании рассчитывают по эмпирической формуле
Кv = Кmv ·Кnv ·К (80)
Кmv находим по формуле ;
Силу резания Н принято раскладывать на составляющие силы направленные по осям координат станка (тангенциальную Pz радиальную Py и осевую Px). При наружном продольном и поперечном точении эти составляющие рассчитывают по формуле .
Операция 5– сверление
Глубина резания при сверлении принимается равной t=05D
Подачу подбираем S=03ммоб
Скорость резания рассчитываем по формуле:
где Т – период стойкости сверла мин;
D – диаметр отверстия мм;
Кv – общий поправочный коэффициент учитывающий фактические условия резания;
Кv = Кmv ·Кuv·К (93)
где Кuv- коэффициент на инструментальный материал;
Кmv – коэффициент на обрабатываемый материал;
Кv = 128 ·10·10=128;
Крутящийся момент и осевую силу рассчитываем по формулам:
где D – диаметр отверстия мм;
Кp – коэффициент учитывающий фактические условия обработки:
где Кmp – коэффициент зависящий от материала обрабатываемой заготовки;
Мощность резания определяем по формуле:
где n – частота вращения инструмента обс;
где D – диаметр инструмента мм;
V – скорость резания ммин;
где nсв– частота вращения сверла обмин;
L – глубина отверстия мм;
Операция 6 – шлифование
Шлифование производим на круглошлифовальном станке 3М151 шлифовальным кругом прямого профиля на керамической связке ПП 300×100×50 ГОСТ 1375 – 71.
Основные параметры резания при шлифовании
При предварительном шлифовании:
скорость круга: Vк=35мс;
скорость заготовки Vз =20ммин;
глубина шлифования t=002мм;
продольная подача S=(03÷07)В;
При окончательном шлифовании:
скорость круга: Vк=35мс;
скорость заготовки Vз =40ммин;
глубина шлифования t=001мм;
продольная подача S=30ммоб;
Эффективную мощность при шлифовании определяем по формуле:
где d – диаметр шлифования мм;
Частота вращения детали:
где D – диаметр заготовки мм;
Определяем основное операционное время:
где К – коэффициент зачистных проходов К = 15;
В – ширина круга мм;
Полное время операции:
К данному разделу прилагаются: маршрутно-операционные карты и спецификация нормального инструмента (приложение Б).
БЕЗОПАСНОСТЬ И ЭКОЛОГИЧНОСТЬ ПРОЕКТА
1 Общие правила безопасности проведения работ на установке
В соответствии с требованиями ГОСТ 12.0002 – 74 под охраной труда принято понимать систему законодательных социально-экономических технических санитарно-гигиенических и организационных мероприятий обеспечивающих безопасность сохранение здоровья и работоспособности человека в процессе труда.
В охране труда различают две системы мероприятий и средств: технику безопасности и производственную санитарию. Цель техники безопасности – предотвратить воздействие на работающих опасных производственных факторов. Производственная санитария решает задачу предотвращения воздействия на работающих вредных производственных факторов.
Требование безопасности на производственное оборудование в соответствии с ГОСТ 12.2.003 – 74 предусматривают общие положения сущность которых состоит в следующем:
Безопасность производственного оборудования обеспечивается в течение всего срока службы. Для этого при разработке выбираются безопасные конструктивные схемы и конструктивные элементы с учетом механизации автоматизации дистанционного управления и эргономических требований (удобств при запусках и управлении).
Вновь разрабатываемое и эксплуатируемое оборудование должно быть герметичным удобным для контроля и обслуживания малошумным не выделять в рабочую зону вредных веществ влаги тепла различных видов излучений в количествах превышающих установленные нормами пределы. Важным условием является наличие защиты от поражения электрическим током и исключение накопления зарядов статического электричества в опасных количествах.
Конструкция производственного оборудования машин и механизмов должна включать средства защиты к которым предъявляются требования постоянной готовности и исправности обеспечения прекращения функционирования оборудования и машин при неисправностях (в том числе и самих средств защиты) звуковой световой и цветовой сигнализации в зонах видимости и слышимости обслуживающего персонала. В качестве средств защиты оборудование следует окрашивать в сигнальные цвета и снабжать знаками безопасности установленными ГОСТ 12.4.026 – 76.
Оборудование используемое на мобильной дробильной установке должно быть не только высокопроизводительным но и безопасным. Безопасность производственного оборудования – это свойство производственного оборудования сохранять соответствие требованиям безопасности труда при выполнении заданных функций в условиях установленных нормативно-технической документацией.
Производственное оборудование должно отвечать требованиям безопасности в течение всего срока службы. Оно должно быть пожаро- и взрывобезопасным.
Пусковые устройства основных машин механизмов и аппаратов блокируются с предохранительными и ограждающими устройствами для исключения пуска их в работу при снятых защитных средствах.
Работать на неисправном оборудовании и пускать в эксплуатацию производственное оборудование без защитных средств сигнализации блокировок обеспечивающих безопасность его обслуживания запрещается.
Общая компоновка и расположение оборудования должны обеспечивать удобства обслуживания и проведения ремонтных работ а также удовлетворять санитарно-гигиеническим требованиям.
Оборудование находящееся в эксплуатации постоянно должно подвергаться осмотру контролю чистке и периодически планово-профилактическому ремонту. Перед осмотром оборудования должна быть прекращена подача электроэнергии.
Перед работой необходимо удостовериться в безопасном состоянии рабочего места и проверить наличие и исправность предохранительных устройств инструмента механизмов и приспособлений требующихся для работы наличие и исправность заземления электроустановок освещенность рабочего места. Если рабочий сам не может устранить выявленные нарушения он обязан сообщить о них мастеру и не приступать к работе до их устранения.
При эксплуатации оборудования необходимо руководствоваться следующими основными правилами:
- перед пуском машины убедиться в отсутствии на ней постоянных предметов;
- после пуска проверить оборудование в рабочем состоянии;
- немедленно остановить машину при появлении дыма или огня сильной вибрации поломке агрегата.
Для транспортировки материала используется ленточный конвейер. На ленточных конвейерах должны быть предусмотрены: устройства выключающие привод при обрыве и пробуксовке ленты обрыве канатов натяжных устройств и забивке разгрузочных воронок и желобов а также снижение скорости ленты до 75% номинальной; устройства для механической очистки ленты и барабанов от налипшего материала; устройство исключающее самопроизвольное движение разгрузочной тележки; приспособление исключающее боковое смещение ленты и т.д.
Конвейер отличаясь от другого оборудования простой конструкцией тем не менее является наиболее опасным механизмом.
При транспортировании ленточными конвейерами сухих и пылящих материалов герметически закрывают места загрузки и выгрузки материала а также предусматривают другие мероприятия по борьбе с пылевыделением (аспирация орошение и др.) для обеспечения предельно допустимых норм вредных примесей в воздухе.
Дробление. Загружаемый исходный материал попадая в дробильную камеру ограниченную лобовой и боковыми стенками станины отражательными плитами и ротором разрушается ударом по нему ножами ротора и ударами об отражательные плиты. Для избежания вылета загружаемого материала вокруг загрузочного отверстия роторной дробилки навешиваются цепи.
Если при дроблении руды образуется взрывоопасная пыль необходимо выполнять мероприятия исключающие взрыв пыли.
Шум и вибрация являются вредными производственными факторами воздействие которых на работающих в определенных условиях приводит к снижению работоспособности а при длительном воздействии к заболеванию.
Длительное воздействие шума на организм человека приводит к частичной а иногда и полной потере слуха воздействие на центральную нервную систему к шумовой болезни.
Источником шума на мобильной установке являются работа дробилки и вибробункера.
Уменьшить воздействие шума на организм человека можно снижением уровня шума в источнике его образования звукоизоляцией звукопоглощением установкой глушителей и применением комплекса этих мер. Снижение уровня шума в источнике образования т.е. непосредственно в машинах и механизмах является наиболее эффективным методом защиты человека от шума. Для этого необходимо совершенствовать конструкции машин и аппаратов регулировать их работу в процессе эксплуатации обеспечивать надежное и жесткое крепление ограждения или кожуха.
Звукоизоляция осуществляется устройством на пути распространения шума звукоизолирующих преград в виде стен перегородок перекрытий обшивок и т.д.
Простейшим средством защиты органов слуха от шума является вата или марля вставленные в слуховой канал; при этом снижается шум на 3-14 дБ в полосе частот 100-6000 Гц при применении марли смоченной жиром- до 18 дБ а шерстяной ваты с воском - до 30 дБ. Полупластичные предохранительные втулки плотно закрывающие слуховой канал обеспечивают снижение шума до 20 дБ. Применяемые в настоящее время некоторые конструкции антифонов (противошумов) закрывающих ушную раковину снижают шум до 30 дБ.
Для снижения воздействия вибрации на человека используют средства автоматизации применяют прогрессивную технологию исключающую контакт работающих с вибрацией используют виброзащитные приспособления конструкции и устройства. Важную роль по предупреждению вибрационной болезни имеет правильная организация труда при работе с ручными вибрирующими машинами. Через каждые 50-60 минут необходимо прекращать работу для отдыха на 7-10 минут. Кроме этого назначают дополнительные перерывы: первый – 20 минут через 15-2 часа после начала работы второй – 30 минут через 2 часа после обеденного перерыва. Первый перерыв рекомендуется использовать для производственной гимнастики легкого завтрака второй – для проведения физиотерапевтических процедур.
Суммарное время контакта с вибрирующими поверхностями не должно превышать 83 длительности рабочего дня. Сверхурочные работы на вибрирующем оборудовании не допускаются. Работы связанные с вибрацией выполняют как правило в отапливаемых помещениях при температуре воздуха не ниже 16°С влажности 40-60% и скорости движения не более 03 мсек. Работающему через каждый час работы должны предоставляться 10-15 минутные перерывы или поручаться работы не связанные с вибрацией При работе виброинструментом важно не допускать переохлаждения рук для чего надо выдавать рабочим рукавицы с прокладками из пенопласта пористой резины или фетра. Предельно допустимые величины общей вибрации рабочих мест (пол сиденье ограждение и т. д.) санитарными нормами устанавливаются по уровню виброскорости в диапазоне частот от 11 до 355 Гц который включает пять октавных частотных полос со среднегеометрическими значениями частот 16 32 63 125 и 250 Гц. Вибрации с частотой ниже 11 Гц нормируются по основной частоте колебаний
Суммарная масса вибрационного конвейера с находящимися в его рабочем органе порциями огарка m кг определяется по формуле:
m = mр.о. + mм + m2 (114)
где mр.о. – масса рабочего органа кг (mр.о. = 4840 кг);
mм – масса материала в рабочем органе кг (mм = 2392 кг);
m2 – масса тяжелой уравновешивающей рамы кг (m2 = 22400 кг).
m = 4840 + 2392 + 22400 = 26632 кг
В качестве пружин – амортизаторов (шумовиброизоляторов) принимаем винтовые пружины жесткостью Св.и.=130000 Нм размером dDL=002001300354 м в количестве 58 штук (по 8 изоляторов на секцию и 2 дополнительных изолятора на приводной секции под рамой электродвигателя).
Нагрузка приходящаяся на один виброизолятор Ри Н определяется по формуле:
где: g – ускорение свободного падения мс2;
Статическая деформация каждой пружины-амортизатора Хстат м определяется по формуле:
где Св.и. – жесткость пружины-амортизатора Нм.
Суммарная жесткость всех пружин-амортизаторов Нм определяется по формуле:
Собственную частоту колебания виброустройства на шумовиброизоляторах wрез с-1 определяем по формуле:
Отношение g рабочей вынужденной частоты колебаний w с-1 к резонансной частоте системы wрез с-1 определяем по формуле:
Коэффициент передачи при отсутствии демпфирования h определяем по формуле:
Чем меньше коэффициент передачи вибрационной силы h тем лучше шумовиброизоляция системы.
Периодически действующая нагрузка кроме статической от силы тяжести конструкции виброконвейера передаваемой на опорную площадку Рдин.max Н определяется по формуле:
где: А2 – амплитуда колебаний тяжелой уравновешивающей рамы м (А2=20×10-3 м);
b - угол вибрации град (b=30°);
Рдин.max=20×10-3×sin 30°×7540000=7540 Н
На каждую опору под шумовиброизолятором передается нагрузка Риз Н определяется по формуле:
Динамическая нагрузка на опорную площадку незначительна что подтверждает хорошую вибрационную и шумовую изоляцию вибрационного конвейера.
Гигиеническими характеристиками вибрации согласно ГОСТ 12.1.012-90 являются среднеквадратичные значения виброскорости мс виброускорения мс2 или логарифмические уровни виброскорости и виброускорения дБ в октавных полосах частот. В нашем случае вибрационный конвейер относится к категории 3а вибрации по санитарным нормам и критериям оценки – технологическая вибрация воздействующая на операторов стационарных машин и оборудования или передающаяся на рабочие места не имеющие источников вибрации.
Место установки виброконвейера не является местом постоянного нахождения рабочих тем не менее производим расчеты логарифмических уравнений виброскорости и виброускорения и сравниваем их с нормативными.
Амплитуда колебаний опорной рамым определяем по формуле:
Скорость вибрации мс определяем по формуле:
где: f – частота колебаний с-1
Частота колебаний определяется по формуле:
где: n – частота колебаний мин-1
= 2×314×95×003×10-3=00018 мс
Сравниваем полученное значение с нормативным корректируем по частоте и эквивалентным корректированным значениям по таблице 7 ГОСТ 12.1.012-90 и получаем:
Ускорение вибрации а мс2 определяем по формуле:
а=003×10-3×(2×314×95)2=01 мс2
Сравнивая полученные значения получаем:
Логарифмический уровень скорости L дБ определяется по формуле:
L=20×lg×( 5×10-8) (129)
L=20×lg×(00018 5×10-8)=911 дБ
Сравнивая полученные значения с нормативным получаем
Логарифмический уровень виброускорения La дБ определяем по формуле:
Lа=20×lg×(а 10-6) (131)
Lа=20×lg×(01 10-6)=100 дБ
Сравнивая полученные значения с нормативными получаем
По проведенному расчету можно сделать вывод о вибрационной безопасности виброконвейера.
Предусмотрены меры позволяющие снизить уровень вибрации отдельных частей виброконвейера например в подшипниках качения хотя они выбраны роликовыми двухрядными с большим уровнем вибрации чем у шариковых однорядных однако организована непрерывная смазка в виде смазочной ванны когда через масленку непрерывно поступает (по мере надобности) смазка – Литол-24 и периодически пополняется во время ТО и ремонтов. Передача крутящего момента от двигателя на вал вибратора осуществляется с помощью клиноременной передачи исключающей удары.
Величину максимальных касательных напряжений действующих в материале витков пружин-амортизаторов МПа определяем по формуле:
где: Ри – нагрузка на виброизолятор Н;
D – средний диаметр пружины м (D=011 м);
d – диаметр прутка пружины м (d=002 м);
К – поправочный коэффициент определяемый по формуле:
Это напряжение меньше допустимого принимаемого для пружин из стали 60С2 и 65Г =500 МПа следовательно запас прочности у пружин достаточен.
Все эти меры и настройка работы виброустройства после монтажа при его наладке на плавный околорезонансный режим приводят к тому что виброконвейер работает плавно и бесшумно что подтверждается опытом эксплуатации таких вибрационных конвейеров.
Опасной зоной проектируемой машины которая может вызвать возможность механического захвата одежды обслуживающего персонала является клиноременная передача то есть расстояние между ремнем и шкивом. Для исключения захвата устанавливаем ограждение передачи листовым металлом. Для расчёта составляем расчётную схему представленную на рисунке 8.
Рисунок 8 – Схема к расчёту ограждения.
Расчёт производим со следующими допущениями: от одного из шкивов вращающихся с большой частотой отламывается часть массой m = 4 кг и ударяется в боковую стенку ограждения по центру. На основании вышеперечисленного производим расчёт.
Центробежную силу Fц Н определяем по формуле:
где m – масса отломившейся части кг;
w - частота вращения шкива с-1 (w = 7693 с-1);
Fц = 4×76932×03 = 71 кН
Строим расчётную схему боковой стенки ограждения она представлена на рисунке 9.
Так как центробежная сила приложена по центру стенки изгибающий момент определяем по формуле:
Рисунок 9 - Расчётная схема боковой стенки ограждения
Напряжения возникающие при столкновении определяем по формуле:
Момент сопротивления сечения W м3 определяется по формуле :
где а – толщина пластины м;
b – ширина пластины м.
Сравниваем полученное значение с пределом текучести sт МПа и получаем выполнение условия:
Ограждение пригодно к использованию.
Организация рационального освещения является одним из основных факторов создания высокопроизводительной и безопасной работы трудящихся. Недостаточное освещение само по себе не вызывает несчастных случаев но может обусловить их возникновение так как оно притупляет внимание и вызывает преждевременное утомление работающих. Кроме того источники света могут быть причиной возникновения пожара и взрыва.
В зависимости от источника света различают естественное и искусственное освещение.
Так как установка работает не в помещении рассчитаем прожекторное освещение. Для площадки необходимо предусматривать общее равномерное освещение. При этом освещенность должна быть не менее 2 лк независимо от применяемых источников света.
При проектировании установок в расчет следует вводить коэффициент запаса.
Вводим коэффициент запаса на запыленность светильников и старение источников света который Кз = 15.
Затем в соответствии со СН – 80 – 81 «Инструкция по проектированию электрического тока освещения строительных площадок» из рекомендуемых схем расположения осветительных приборов по таблице выбираем основные параметры прожекторной установки.
Ширина освещаемой площади а = 100 м;
Высота прожекторных штанг Н = 15 м;
Расстояние между мачтами 70 м;
Тип лампы ПЗС – 35 или ПСМ– 40;
Мощность N = 500 кВт;
Прожекторы с лампами накаливания
Требуемая освещенность площади Ер лк определяется по формуле:
где Ео – наименьшая освещенность площади лк (Ео = 5 лк);
К – коэффициент запаса.
Количество прожекторов для освещения площади завода nопределяется по формуле:
где m – коэффициент использования светового потока (m = 05);
S – площадь освещаемой поверхности м2;
Рп – мощность лампы Вт.
В одной мачте устанавливаем по n = 4 прожектора тогда количество мачт будет равным
При нечетном количестве мачт принимаем шахматную систему и приводим схему на рисунке 10.
Далее по таблице в соответствии с типом прожектора и типам лампы определяем минимально допустимую высоту установки прожекторов для освещения площадки. Выбираем высоту установки прожекторов Н = 10 м.
Рисунок 10 – Схема расположения мачт
Система организационных и технических мероприятий и средств обеспечивающих защиту людей от вредного и опасного воздействия электрического тока называется электробезопасностью.
Для защиты от поражения электрическим током применяются отдельно или в сочетании друг с другом защитное заземление зануление малое напряжение защитное отключение и т.д.
Общие требования безопасности при обслуживании электроустановок.
Оперативное обслуживание электроустановок может осуществляться как местным оперативным или оперативно-ремонтным персоналом за которым закреплена данная электроустановка так и выездным за которым закреплена группа установок. Лицам из оперативно-ремонтного персонала обслуживающим электроустановки эксплуатируемые без местного оперативного персонала при осмотре установок оперативных переключениях подготовке рабочих мест и допуски бригад к работе и т.п. В соответствие с настоящими правилами и "ПТЭ электроустановок потребителей" представляются все права и обязанности оперативного персонала. Вид оперативного обслуживания число лиц из оперативного персонала в смену или на электроустановки определяются лицом ответственным за электрохозяйство по согласованию с администрацией предприятия (организации) и указываются в местных инструкциях.
К оперативному обслуживанию электроустановок допускаются лица знающие оперативные схемы должностные и эксплутационные инструкции. Ценности оборудования и прошедшие обучение и проверку знаний в соответствий с указаниями настоящих правил.
Лица из оперативного персонала обслуживающие электроустановки единолично и старшие в смене или бригаде за которыми закреплена данная электроустановка должны иметь группу по электробезопасности не ниже 15 в установках напряжением выше 1000В и 111 в установках напряжением до 1000 В.
Оперативный персонал должен работать по графику утверждённому лицом ответственный за электрохозяйство предприятия или структурного подразделения.
В случае необходимости с разрешения лица утверждавшего график допускается замена одного дежурного другим.
Лицо из оперативного персонала придя на дежурство должно принять замену от предыдущего дежурного а после окончания работы сдать смену следующему дежурному в соответствии с графиком. Уход с дежурства без сдачи смены запрещается. В исключительных случаях оставление рабочего места допускается с разрешения вышестоящего лица из оперативного персонала.
При приемке смены оперативный персонал обязан: ознакомиться по схеме с состоянием и режимом работы оборудования на своем участке путем досрочного осмотра в объеме установленном инструкцией;
- получить сведения от дежурного сдающего смену об оборудовании за которым необходимо вести тщательное наблюдение для предупреждения аварии или неполадок и оборудовании находящимся в ремонте или резерве
- проверить и принять инструмент материалы ключи от помещений средства защиты оперативную документацию и инструкции;
- приемка и сдача смены при загрязненном оборудовании неубранном рабочем месте и обслуживаемом участке запрещается.
Приемка смены при неисправленном оборудовании или ненормальном режиме его работы допускается только с разрешения лица ответственного за данную установку или вышестоящего лица о чем делается отметка в оперативном журнале.
Лицо из оперативного персонала во время своего дежурства является ответственным за правильное обслуживание и безаварийную работу всего оборудования на порученном ему участке.
Старший по смене из оперативного персонала единолично или совместно с администрацией предприятия обязан выполнять требования диспетчера энергосистемы. Инспектора и дежурного предприятия "Энергонадзор" по снижению электрической нагрузки и сокращению расхода электропотребления требования диспетчера энергосистемы о включении питающих и транзитных линий электропередачи а также об отключении отдельных линий при аварийном положении в энергоснабжающей организаций.
Старший по смене из оперативного персонала обязан немедленно поставить в известность диспетчера энергоснабжающей организации об авариях вызвавших отключение. Одной или нескольких линий электропередачи питающих предприятие. Список лиц имеющих право проведения оперативных переговоров с энергосистемой определяет лицо ответственного за электрохозяйство и передаёт в соответствующую оперативную службу предприятия электрических сетей.
При нарушении режима работы повреждении или аварий с электрооборудованием оперативный персонал обязан самостоятельно и немедленно с помощью подчиненного персонала принять меры к восстановлению нормального режима работы и сообщить о происшедшем непосредственно старшему по смене или лицу ответственному за энергохозяйство.
В случае неправильных действий оперативного персонала при ликвидации аварии вышестоящее лицо обязано вмешаться вплоть до отстранения дежурного и принять на себя руководство и ответственность за дальнейший ход ликвидации аварии.
Оперативный персонал обязан проводить обходы и осмотры оборудования и производственных помещений на закрепленном за ним участке. Осмотр электроустановок могут выполнять единолично: лицо из административно-технического персонала с группой по электробезопастности V в установках напряжением выше 1000 Вис группой IV в установках напряжением до 114000В;-лицо из оперативного персонала обслуживающего данную электроустановку.
Список лиц из административно-технического персонала которым разрешается единоличный осмотр устанавливается распоряжением лица ответственного за электрохозяйство.
При осмотре распределительных устройств (РУ) щитов шинопроводов сборок напряжением до 1000В запрещается снимать предупреждающие плакаты и ограждения проникать за них касаться токоведущих частей и обтирать или чистить . их устранять обнаруженные неисправности.
Лицам из оперативного персонала обслуживающего производственное оборудование (электродвигатели генераторы электропечи) и электрическую часть различного технологического оборудования напряжением до 1000В разрешается единолично открывать для осмотра дверцы щитов пусковых устройств пультов управления и др.
При осмотре электроустановок напряжением выше 1000В единолично запрещается: проникать за ограждения входить в камеры РУ выполнять какие-либо работы. Камеры следует осматривать с порога или стоя перед барьером.
Осмотр камер закрытых распределительных устройств (ЗРУ) с входом за ограждение при необходимости разрешается выполнять только лицу с группой по электробезопастности не ниже IV при условии что в проходах расстояние от пола составляет : до нижних фланцев изоляторов - не менее 2м при напряжении до 10 кВ не менее 275 м при напряжении до 35 кВ не менее 35 м при напряжении 110 кВ
-ознакомится со всеми записями распоряжениями за время с его последнего дежурства
-оформить приёмку смены записью в журнале ведомости а также на
оперативной схеме подписями лица принимающего смену и лица сдающего её;
-доложить старшему по смене о вступлении на дежурство и о неполадках замеченные при приемке смены.
Приемка и сдача смены во время ликвидации аварии производства переключении или операции по включению и отключению оборудования запрещения администрации.
Перечень таких ячеек и камер определяется распоряжением лица ответственного за электрохозяйство. При расстояниях меньше указанных вход за ограждения разрешается только в присутствии второго лица с группой не ниже III.
Осмотры выявления и ликвидация нарушений на электроустановках без постоянного наружного персонала производится централизованно выездным персоналом осуществляющим надзор и работы по объекту (или группе объектов) периодичность которых устанавливается ответственным за электрохозяйство в зависимости от местных условий. Результаты осмотров фиксируются в оперативном журнале.
Лица не обслуживающие данную электроустановку допускаются к осмотру с разрешения лица за электрохозяйство цеха.
Двери помещений электроустановок (щитов сборок и т.п.) должны быть постоянно заперты. Для каждого помещения электроустановки должно быть не менее двух Комплектов ключей один из которых является запасным. Ключи от помещения РУ не должны подходить к дверям ячеек и камер.
Ключи должны находиться на учете у оперативного персонала. В электроустановках без постоянного оперативного персонала ключи должны находиться на пульте управления у старшего по смене лица из оперативного персонала. Ключи должны выдаваться под расписку:
-на время осмотра лицам которым разрешен единоличный осмотр и лицам из оперативно-ремонтного персонала в том числе и не находящимся в смене при выполнении ими работ в электропомещениях;
-на время производства работ по наряду или по распоряжению ответственному руководителю работ производителю работ или наблюдающему.
Персональные ключи для входа в электропомещение разрешается иметь только лицам из оперативного персонала принимающим и сдающим смену по телефону.
Расчет заземляющего контура.
Определяется сопротивлением растеканию тока одиночного вертикального заземлителя по следующей зависимости:
где р- расчетное удельное сопротивление (р=р0 х Кn);
р0- удельное сопротивление ( р0 = 1 х 102 Ом х см3);
Кn- повышающий коэффициент (для IV климатической зоны принимаем Кn = 12);
- длина вертикального заземлителя (принимаем
d - диаметр вертикального заземлителя (принимаем d = 60мм);
h - заглубление полосы связи (принимаем h = 1м).
Выше указанная зависимость справедлива при следующих условиях:
Определяем сопротивление очага заземлителей:
где К0-коэффициент повышения сопротивления очага заземлителей (принимаем К0=25)
R0-допустимое значение сопротивления (по ГОСТ 12.1.030-81 R0=10 Ом)
Определяем ориентировочное количество вертикальных заземлителей:
По вычисленному результату принимаем целое число вертикальных заземлителей n=3.
Принимаем расстояние между вертикальными заземлителями а=2м.
Определяем коэффициент экранирования между вертикальными заземлителями i=086.
В соответствии с выбранным значением i определяем истинное значение сопротивления очага заместителей R0:
Длина связи определяется по следующей зависимости:
Сопротивление полосы связи определяется по следующей зависимости:
где b - ширина полосы (принимаем b=60мм);
Сопротивление комбинированного заземлителя определяется по следующей
где 2 – коэффициент экранирования полосы связи с вертикальными заземлителями по табл. 5.5 для отношения расстояния между трубами по их длине al=2 2=089).
Так как рассчитанное сопротивление оказалось не соответствующим норме
(Ry = 1639 > 10 Ом ) то необходимо увеличить число вертикальных заземлителей.
Принимаем п = 10 и производим пересчёт:
коэффициент экранирования между вертикальными заземлителями 1 =072 истинное значение сопротивления очага заземлителей
Сопротивление полосы:
коэффициент экранирования полосы связи с вертикальными заземлителями 2=089
Электрическая система управления агрегатом должна быть подведена таким образом чтобы электрический кабель не терся о стационарные или подвижные элементы следует также исключать возможность намокания кабеля в масле. Рекомендуется подвести электрическую систему в термоустойчивых и маслоотталкивающих кожухах чтобы маршрут их прокладки не пересекался с зонами обслуживания агрегата.
Чрезвычайные ситуации техногенного и природного характера продолжают приносить множество бед уносят человеческие жизни. Обстановка заставляет быть в напряжении и постоянной готовности без промедления активно реагировать на события. Неотложные работы при ликвидации ЧС — это деятельность но всестороннему обеспечению аварийно-спасательных работ оказанию населению пострадавшему в ЧС медицинской и других видов помощи созданию условий минимально необходимых для сохранения жизни и здоровья людей поддержания их работоспособности.
К аварийно-спасательным работам относятся поисково-спасательные горноспасательные газоспасательные противофонтанные а также аварийно-спасательные связанные с тушением пожаров работы по ликвидации медико-санитарных последствий ЧС и ряд других подобных работ. При возникновении производственной аварии немедленно проводится оповещение рабочих и служащих предприятия об опасности. Аварийно-спасательные работы приходится проводить при взрывах пожарах обрушениях обвалах наводнениях и других бедствиях. Экстренная медицинская (доврачебная) помощь должна быть оказана непосредственно на месте работ затем — первая врачебная и эвакуация в лечебные учреждения для специализированного лечения. Оказание помощи пострадавшим людям в большинстве случаев не терпит промедления так как по истечении даже незначительного времени все усилия могут оказаться бесполезными.
Специфика спасательных работ состоит в том что они должны выполняться в сжатые сроки. Для конкретных условий они определяются различными обстоятельствами. В одном случае — это спасение людей оказавшихся под обломками конструкций зданий среди поврежденного технологического оборудования в заваленных подвалах. В другом — это необходимость ограничить развитие аварии чтобы предупредить возможное наступление катастрофических последствий возникновение новых очагов пожаров взрывов разрушений. В третьем — быстрейшее восстановление нарушенных коммунально-энергетических сетей (электричество газ тепло канализация водопровод).
От качества проведения аварийно-спасательных и других видов работ в зоне ЧС зависит жизнь и здоровье людей тем или иным образом вовлеченных в условия чрезвычайных обстоятельств. Для достижения наибольшей эффективности работ на месте ЧС требуется комплекс мер включающий законодательную базу фонды экономической поддержки специальное техническое обеспечение обеспечение средствами связи. Не мене важен и организационный аспект позволяющий координировать действия специальных спасательных служб разных уровней в чрезвычайных условиях.
Пожарная безопасность объекта обеспечивает как в рабочем его состоянии так и в случае возникновения аварийной обстановки. Безопасность людей обеспечивается при возникновении пожара в любом месте объекта.
Опасными факторами пожара воздействующими на людей являются открытый огонь искры и дым; повышенная температура воздуха и предметов; пониженная концентрация кислорода и токсичные продукты горения; обрушение и повреждение зданий сооружений установок а также взрыв.
Предотвращение пожара достигают предупреждением образования горючей среды и источников зажигания в ней; поддержанием температуры горячей среды а также давления в горючей смеси ниже максимально допустимого по горючести.
Пожарную защиту обеспечивают максимально возможным использованием негорючих и трудногорючих веществ и материалов вместо пожароопасных т.е. веществ обладающих повышенной пожаровластностью; ограничением количества горючих веществ и изоляции горючем среды; предотвращением распространения пожара за пределы очага загорания; приминанием конструкции объектов с установленными пределами огнестойкости и горючести; эвакуацией людей ; применением средств пожаро тушения пожарной сигнализации и извещений о пожаре средств коллективной и индивидуальной защиты людей организацией пожарной охраны объекта и системой противодымной защиты.
Коллективную и индивидуальную защиту людей при пожаре осуществляют в тех случаях когда их эвакуация затруднена или нецелесообразна. Она должна обеспечивать безопасность людей в течение всего времени действия опасных факторов пожара. Для коллективной защиты используют убежища или защищенные помещения.
Территория предприятий должна постоянно содержаться в чистоте и порядке. Весь мусор производственные отходы и т.п. необходимо систематически удалять на специально отведенные участки. Ко всем зданиям и сооружениям должен быть обеспечен свободный доступ.
Противопожарные разрывы между зданиями и сооружениями не должны использоваться под складирования материалов оборудование и т.д.
Готовая продукция полуфабрикаты тара оборудование и т.п. должны складироваться на определённых участках расположение которых должно быть согласовано с пожарной охраной.
На пожаро- и взрывоопасных участках территории предприятия курение запрещается.
На этих участках устанавливается предупреждающие надписи: "Курить запрещается".
Курение разрешается только в специально отведенных местах где должны иметься урны или бочки с водой для окурков. Места отведенные для курения должны иметь надписи: "Место для курения".
Отогревание замерших водопроводных и канализационных труб открытым огнём запрещается. Трубопроводы следует отогревать паром горячей водой или горячем песком.
Въезд на территорию пожаро- и взрывоопасных предприятий и цехов а также предприятий и цехов со сгораемой кровлей здании не оборудованных искроуловительными приспособлениями с открытыми поддувалами и действующими менее 42 м при напряжении 130-220 кВ.
При въезде на такую территорию должны быть установлены предупреждающие знаки.
Все производственные помещения необходимо постоянно содержать в чистоте и порядке: мусор и отходы производства должны своевременно удаляться.
Проходы выходы коридоры тамбуры лестницы чердачные помещения должны постоянно содержаться в исправном состоянии и ничем не загромождаться.
Спецодежда должна храниться в специально предназначенных для этой цели помещениях. Промасленная спецодежда должна храниться только в развешенном виде в карманах спецодежды запрещается оставлять промасленные тряпки. Оставление после работы одежды на верстаках ящиках у рабочих мест не допускается.
Для цеховых кладовых специально предназначенных для хранения горючих и легковоспламеняющихся жидкостей должны быть установлены нормы хранения этих жидкостей.
Все цеха мастерские склады должны быть обеспечены первичными средствами пожаротушения в соответствии с нормами.
Стационарные пожарные лестницы и несгораемые ограждения на крышах зданий необходимо содержать в постоянной исправности.
В целях создания условий для быстрого использования пожарного инвентаря и облегчения наблюдения за ним рекомендуется устраивать специальные щиты пожарного инвентаря. В цехах мастерских и складах с большой площадью целесообразно устраивать несколько таких щитов. Дороги проезды и подъезды не должны использоваться под складирование различных материалов оборудования сырья готовой продукции и т.п. Все дороги проезды и подъезды должны содержаться в исправности а в ночное время освещаться для обеспечения безопасности проезда. Рельсовые пути и временные канавы не должны затруднять свободного и быстрого проезда пожарного транспорта. Для этого в необходимых местах по согласованию с пожарной охраной должны быть устроены удобные переезды через пути и канавы.
8 Аварийные и чрезвычайные ситуации
Проблема охраны окружающей среды и рационального использования природных ресурсов является одной из наиболее актуальных тем среди глобальных общечеловеческих проблем так как от ее решения зависит жизнь на земле здоровье и благосостояние человечества.
В нашей Республике вопросам охраны природы и рационального использования ее ресурсов уделяется постоянное внимание. Необходимость охраны природы закреплена в Конституции Республике Казахстан. Для предупреждения правонарушений в области охраны окружающей среды законодательством Республике Казахстан предусмотрено привлечение виновных к ответственности: дисциплинарной административной материальной и уголовной. Для снижения вредного воздействия данной установки на окружающую среду при его эксплуатации предусматриваем мероприятия по борьбе с пылевыделением - орошение для обеспечения предельно допустимых норм вредных примесей в воздухе.
Установка орошения представлена следующими элементами:
- питающий коллектор смонтированный на раме дробилки;
- два комплекта форсунок установленных на входе в дробилку и на ленточном транспортере.
Вода в питающий коллектор подводится пользователем из внешней системы. Для орошения следует использовать только чистую воду так как разнообразные осаждающиеся загрязнения снижают эффективность орошения оказывают также значительное влияние на долговременность работы форсунок.
Темой дипломного проекта является разработка мобильной дробильной установки а в частности одной из её сборочных единиц – дробилки ударного действия.
При работе дробилки её рабочие элементы изнашиваются. Соответственно необходимо проводить обслуживание и ремонт что занимает немало времени. Для сокращения продолжительности ремонта предлагается модернизировать рабочие элементы дробилки.
Замена элементов старой конфигурации на элементы новой позволит повысить надежность работы и сократить сроки выполнения обслуживания и ремонта.
За базовый вариант принимаем расчет затрат на производство и эксплуатацию исходной дробилки в качестве нового оборудования рассчитываем затраты на производство и эксплуатацию новой дробилки. Расчет затрат будем производить в два этапа: на производство изделия и его эксплуатацию.
1 Расчет единовременных затрат производства дробилки подрядным способом
Определяется по формуле:
Кпд = Соб + Смон + Стр(149)
где Кпд – капитальные вложения которые необходимы будут при подрядном способе реализации данного проекта (тыс.тенге);
Соб – стоимость оборудования (тыс. тенге);
Смон – стоимость монтажа (тыс. тенге);
Стр – транспортные расходы (тыс. тенге).
Так как затраты на монтаж и транспортировку неизвестны то принимаем их в следующем соотношении: Соб = 100%; Смон = 40 – 50%; Стр = 20–25%.
Капитальные вложения для производства разрабатываемой дробилки:
Кпд1 = 2380 (1+ 05 + 025) = 4165тыс. тенге
Капитальные вложения для производства базовой модели дробилок:
Кпд2 = (1700 + 1780)·(1+ 05 + 025) = 6090тыс. тенге
2 Расчет единовременных затрат при хозяйственном способе производства дробилки
Если отдельные установки приспособления и оборудование изготовлять и монтировать на самом предприятии тогда капитальные затраты рассчитываются следующим образом:
Кхс = Смз + Сэл + Стоп + Сзп + Спр(150)
где Смз – материальные затраты (тыс. тенге);
Сэл – затраты на электроэнергию (тыс. тенге);
Стоп – затраты на топливо (тыс. тенге);
Сзп – затраты на заработную плату (тыс. тенге);
Спр – прочие затраты (35% от суммы предыдущих затрат).
а) Расчет материальных затрат. Так как присутствуют материалы которые существенно различаются между собой по весу цене качеству и другим показателям составляется смета затрат и сводится в таблицы 1 2.
Таблица 1 – Смета материальных затрат на производство нового оборудования
Цена за единицу измерения (тыс. тенге)
Штампованные изделия
Таблица 2 – Смета материальных затрат на производство базового оборудования
б) Расчет затрат на электроэнергию:
где N – средняя мощность оборудования при проведении строительно-монтажных работ (кВт);
T – время работы оборудования (час);
Цэ – стоимость электроэнергии (тенгекВт·ч).
Сэл1 = 80·168·5 = 672 тыс. тенге
Сэл2 = 80·256·5 = 1024 тыс. тенге
в) Расчет затрат на топливо
Так как при монтаже топливо не требуется а затраты на доставку материалов включены в их стоимость то расчет затрат на топливо не производится.
г) Расчет заработной платы на проведение строительно-монтажных работ.
Расчет производим через минимальную заработную плату (МЗП) установленную на предприятии (28000 тенге).
Количество отработанных часов при СМР на одного рабочего:
Тотр = Nр·Tсм·k(152)
где Nр – количество рабочих дней необходимых для выполнения СМР;
Tсм – продолжительность смены ч;
k – количество смен.
Принимаем что бригада состоит из 8 человек и работает в одну смену. Продолжительность смены 8 часов. Предполагаем что СМР для разрабатываемой дробилки займут один календарный месяц или 21 рабочий день а для базового варианта примерно 32 рабочих дня.
Тотр1 = 21·8·1 = 168 ч
Тотр1 = 32·8·1 = 256 ч
Расчет часовой тарифной ставки производится по формуле:
Фтар = МЗП·Ктар n0 (153)
где n0 – количество рабочих часов в месяц по плану (среднемесячный баланс составляет 16667 ч)
Ктар – тарифный коэффициент.
Расчет часовой тарифной ставки сведен в таблицы 3 4
Расчет заработной платы к начислению:
Фзп = Фтар·Тотр· Кдол (154)
где Кдол – должностной коэффициент - доплата по индивидуальному контракту (1 Кдол 4). Принимаем равным 1.
Расчет отчислений на социальный налог:
Фсс1 = 011·311316 = 4044768 тенге
Фсс2 = 011·474112= 6163456 тенге
Расчет фонда заработной платы на СМР в целом:
Сзп = Фзл + Фсс(156)
Сзп1 = 311 316 + 4044768 = 35158368 тенге
Сзп2 = 474112 + 6163456 = 53574656 тенге
Расчет заработной платы на проведение СМР сведен в таблицы 3 и 4.
Таблица 3 – Расчет заработной платы на СМР нового оборудования
Тарифный коэффициент (Ктар)
МЗП на предприятии тенге
Часовая тарифная ставка (Фтар) тенгечас
Должностной коэффициент
Количество отработанных часов (Тотр)
Заработная плата к начислению (Фзр)
Таблица 4 – Расчет заработной платы на СМР базового оборудования
Из таблиц 3 4 видно что затраты на заработную плату рабочих строительно-монтажной бригады выполняющей монтаж нового оборудования ниже так как продолжительность монтажа меньше ввиду простоты конструкции.
Составляется смета капитальных затрат в которую входят затраты на изготовление и монтаж нового оборудования осуществляемые хозяйственным способом (таблица 5 6).
Таблица 5 – Капитальные затраты на изготовление и монтаж нового оборудования осуществляемые хозяйственным способом
Таблица 6 – Капитальные затраты на изготовление и монтаж базового оборудования осуществляемые хозяйственным способом
Из таблиц 5 и 6 видно что единовременные затраты при хозяйственном способе изготовления ниже для обоих рассматриваемых вариантов поэтому выбираем именно этот способ.
Текущие затраты это затраты на эксплуатацию оборудования или приспособления их еще называют производственной себестоимостью.
Сначала определяется на сколько повысилась производительность (П) оборудования в связи с внедрением мероприятий затем определяется снижение (повышение) материалоемкости энергоемкости трудоемкости и т. д. На основе изменения трудоемкости можно будет рассчитать количество условно высвободившихся рабочих или созданых новых рабочих мест.
Полные текущие затраты определяются по формуле:
С = Смз + Сзп + Сэл + Стоп + Сам + Собс + Спр(157)
где Смз Сзп Сэл Стоп – это затраты соответственно на материалы заработную плату электроэнергию и топливо.
Смета материальных затрат Смз на обслуживание нового и базового вариантов представлена в таблице 7 .
Таблица 7 – Смета материальных затрат при обслуживании
Цена за единицу измерения (тенге)
Разрабатываемая дробилка
Сам – затраты на амортизацию определяются 1012% от величины единовременных затрат;
Собс – затраты на ТО (23%) от стоимости оборудования;
Спр – прочие затраты (35%) от суммы выше указанных затрат.
Результаты расчета текущих затрат сводим в таблицу 8.
Для обслуживания дробилок в обоих рассматриваемых вариантах достаточно 1 человека в смену. Завод работает в 2 смены. Следовательно для обслуживания дробилок в течение года необходимо 2 рабочих третьего разряда. Для рабочих обслуживающих дробилки базового варианта вводим должностной коэффициент 15. Тогда расходы на заработную плату составят:
Фзп1 = 202·8·2·1·128 = 413696тенге
Фзп2 = 202·8·2·15·128 = 620544тенге
Фсс1 = 011·413696 = 5378048 тенге
Фсс2 = 011·620544 = 8067072 тенге
Сзп1 =413696 + 5378048 = 46747648 тенге
Сзп2 = 620544 + 8067072 = 70121472тенге
Ежегодные затраты на электроэнергию рассчитываются исходя из продолжительности работы дробильных агрегатов и их установленной мощности.
Таблица 8 – Текущие затраты на эксплуатацию оборудования
После вне-дрения ОТМ
Материальные затраты
продолжение таблицы 8
Обслуживание оборудования
4 Расчет экономической эффективности и срока окупаемости
Производительность оборудования изменяется (повышается) экономическую эффективность рассчитываем через удельные приведенные затраты:
DЭ = (Z2 – Z1)·П1(158)
где П2 – производительность оборудования после ОТМ;
Z1 и Z2 – соответственно удельные приведенные затраты для НО и БВ:
Zi = (Сi + Ен·КХПi) Пi(159)
Ен – нормативный коэффициент экономической эффективности его можно принять в пределах 01015 если нет никакой информации о нем. Принимаем равным 0125 и нормативный срок службы Тн = 8 лет.
Z1 = (11683 + 0125·12549) 319488 = 0004 тыс. тенге
Z2 = (177367 + 0125·2038) 114688 = 0018 тыс. тенге
DЭБВ = (0018 – 0004)·114688 =16056 тыс. тенгесезон
DЭНВ = (0018 – 0004)·319488 =44728 тыс. тенгесезон
Эффект от внедрения мероприятий определяется как экономия полученная за счет снижения издержек или дополнительная прибыль.
Далее делается расчет срока окупаемости НО:
То = 2038 16056 = 325 дней = 09 года
То = 12549 44728 = 72 дня = 020 года
Так как Т0Тн то это свидетельствует об экономической целесообразности внедрения НО.
Результаты расчета сводим в таблицу 9 и выносим на лист 050713 ДП 00.00.000 ТЭО графической части.
5 Расчет точки безубыточности для БВ и НО
Аналитически точка безубыточности определяется по формуле:
П0 = Спос (Ц – Sпер) (161)
где П0 – «критическая» производительность (т);
Спос – постоянные затраты (тыс. тенге);
Ц – цена за единицу выпускаемой продукции (тыс. тенгет);
Sпер – удельные переменные затраты на единицу продукции (тыс. тенгет).
Точка безубыточности показывает при какой минимальной производительности предприятие может покрывать текущие затраты.
Стоимость постоянных затрат определяется по формуле:
Спос = Сам + Снр (162)
где Снр – стоимость накладных расходов тыс. тенге составляют 30% от стоимости переменных затрат Спер:
Снр = Спер · 03 (163)
Спер = Сзп + Собс + Сэл + Смз + Спр (164)
Спер НО = 4675 + 5195 + 36714+ 4188 + 5162 = 9801 тыс. тенге
Спер БВ = 70121 + 869 + 50236 + 9932 + 7818 = 146797 тыс. тенге
Снр НО = 9801 · 03 = 29403 тыс. тенге
Снр БВ = 146897 · 03 = 44039 тыс. тенге
Спос НО = 188235 + 29403 = 482265 тыс. тенге
Спос БВ = 3057 + 44039 = 746091 тыс. тенге
Также определяются удельные полные затраты на выпуск продукции Sпол по формуле:
Стоимость полных затрат Спол определяется по формуле:
Спол = Спос + Спер(167)
Спол НО = 9801 + 482265 = 1228356 тыс. тенге
Спол БВ = 146797 + 746091 = 2214061 тыс. тенге
Sпер НО = 9801 319488 = 307 тенгет
Sпер БВ = 146797 114688 = 128 тенгет
Sпол НО = 1228356 319488 = 385 тенгет
Sпол НО = 2214061 114688 = 193 тенгет
П0 НО = 482265 (1700 – 3067) = 2842 т
П0 БВ = 746091 (1700 – 128) = 44221 т
Результаты произведенных расчетов выносятся на график точки безубыточности на лист графической части 050713 ДП 00.00.000 ТЭО.
Рисунок 11 – Расчет точки безубыточности
Таблица 9 – Расчет экономической эффективности от внедрения нового объекта
Условн. обозна-чения
Капитальные вложения
Годовые эксплуатационные затраты
Затраты на амортизацию
Затраты на заработную плату
Затраты на обслуживание оборудования
Продолжение таблицы 9
Затраты на электроэнергию
Затраты на материалы
Удельные приведенные затраты
Экономическая эффективность
Коэффициент экономической эффективности
Срок окупаемости капитальных вложений
Удельные переменные затраты
По данным расчета видно что внедрение является экономически целесообразным.
В данном дипломном проекте были решены вопросы связанные с облегчением труда рабочих и сокращением продолжительности технического обслуживания и ремонта тем самым повышение экономичности и увеличением производительности на мобильной дробильной установки.
Модернизированная дробилка ударного действия отвечает всем требованиям по экономичности и безопасности а так же данная модернизация является экономически выгодной и целесообразной что и было доказано в разделе - экономическая часть.
Экономический эффект который составил 27525 тыс. тенге определяется как снижение издержек за счет выбора предпочтительного варианта на основе приведенных затрат и представлен в виде коэффициента экономической эффективности который составил 1245.
Гузенков П. Г. [Текст] «Детали машин» М: Высшая школа 1982
Иванов М.Н. [Текст] «Детали машин» М: Высшая школа 1991
Лахтин Ю. М. [Текст] «Материаловедение» М: Машиностроение 1990
Шестопалов К. К. [Текст] «Подъемно-транспортные строительные и дорожные машины и оборудование» М: Мастерство 2002
Н.Я. Хархута и др. [Текст] Дорожные машины. Теория конструкция и расчет. Учебник для вузов Изд. 2-е доп. и перераб. Л. «Машиностроение» 1976
Адрышев А.К. [Текст] Проектирование вентиляционных и сапирационных систем: Учебное пособие для студентов ВУзов - Усть-Каменогосрк. ВКГТУ 1998
Касилова А. Г. [Текст] «Справочник конструктора машиностроителя» В 2 т. М: Машиностроение 1986
Анурьев В. И. [Текст] «Справочник конструктора машиностроителя»: В 3 т. 8-е изд. перераб. и доп. М: Машиностроение 2001
Закон Республики Казахстан «О промышленной безопасности на опасных производственных объектах» от 13.07.1999
Закон Республики Казахстан «О санитарно- эпидемиологическом благополучии населения» № 110- ХIII от 8 июля 1994 г.
Закон Республики Казахстан «О пожарной безопасности» № 48-I- ЗРК от 22 ноября 2006 г
ППБ РК- 2006 Правила пожарной безопасности в Республике Казахстан
ПУЭ. Правила устройства электроустановок. М. 1990
СНиП РК 2.02-05-2002 Пожарная безопасность зданий и сооружений
СНиП РК 2.04-05-2002* Естественное и искусственное освещение
СН – 80 – 81 «Инструкция по проектированию электрического тока освещения строительных площадок»
СН-245-71. Санитарные нормы проектирования промышленных предприятий
СНиП РК 4.02-05-2001* Отопление вентиляция и кондиционирование
ГОСТ 12.1.009 – 76 «Электробезопасность»
ГОСТ 12.0.004-90 «Организация обучения безопасности труда»
Система стандартов безопасности труда: [сборник]. – М. : Изд-во стандартов 2002. – 102 [1] с.: ил.; 29 см. – (Межгосударственные стандарты). – Содерж.: 16 док. – 1231 экз.
Справка о патентно-информационном поиске
Маршрутная и операционные карты
спецификация нормального инструмента
патенты.doc
ПО ИНТЕЛЛЕКТУАЛЬНОЙ СОБСТВЕННОСТИ
ПАТЕНТАМ И ТОВАРНЫМ ЗНАКАМ
(12) ОПИСАНИЕ ИЗОБРЕТЕНИЯ К ПАТЕНТУ
Статус: по данным на 16.04.2010 - может прекратить свое действие
(21) (22) Заявка: 200412064003 06.07.2004
(24)начала отсчета срока действия патента:
(43)публикации заявки: 10.01.2006
(46) Опубликовано: 20.07.2006
(56) Список документов цитированных в отчете о
поиске: SU 1396335 A1 15.11.1994. RU 2111056 С1 20.05.1998. DE 19781515 A 09.01.2003. US 3589627 A 29.06.1971. ЕР 0583515 А 23.02.1994.
Адрес для переписки:
7018 г.Якутск пр. Ленина 43 ИГДС им. Н.В. Черского СО РАН
Матвеев Андрей Иннокентьевич (RU)
Львов Евгений Степанович (RU)
(73) Патентообладатель(и):
(54) ВЕРТИКАЛЬНАЯ РОТОРНАЯ ДРОБИЛКА
Изобретение относится к области дезинтеграции и переработки горных пород и руд и предназначено для использования в горнодобывающей химической промышленностях для переработки твердых полезных ископаемых. Вертикальная роторная дробилка для среднего и мелкого дробления состоит из цилиндрического корпуса с верхним загрузочным патрубком отбойными кольцами на внутренней стенке корпуса вертикально установленными роторами и нижним разгрузочным отверстием при этом роторы размещены на одном уровне центры вращения роторов симметрично расположены вокруг центрального ротора имеющего распределитель материала над которым соосно установлен загрузочный патрубок. Изобретение позволяет повысить эффективность работы дробилки. 2 ил.
Статус: по данным на 16.04.2010 - прекратил действие
(21) (22) Заявка: 200313819903 31.12.2003
(46) Опубликовано: 20.05.2005
поиске: ВОЛКОВ В.Т. и др. Механизация и автоматизация в промышленности строительных материалов. Государственное издательство литературы по строительным материалам. - М. 1963 с.130-132 рис.25. SU 583814 А 15.12.1977. SU 1123721 А 15.11.1982. RU 2205694 С1 10.06.2003. US 3659794 A 02.05.1972. FR 2713107 A1 09.06.1995. WO 92111942 A 23.07.1992.
9106 Санкт-Петербург В.О. 21 линия 2 СПГГИ (ТУ) патентный отдел
(54) РОТОРНАЯ ДРОБИЛКА
Изобретение предназначено для дробильных машин. Роторная дробилка содержит корпус камеру дробления ротор с билами колосниковую решетку установленную на корпусе посредством горизонтального шарнирного узла и подпружиненную к корпусу колосники решетки выполнены в виде двуплечих рычагов и установлены независимо друг от друга а каждый из них подпружинен рессорами S-образного профиля при этом один конец рессоры закреплен на свободном конце колосника а второй свободный конец размещен с возможностью взаимодействия при повороте колосника с горизонтальной полкой съемного кронштейна шарнирный узел выполнен в виде неподвижной оси а колосники снабжены вырезами с возможностью их взаимодействия с осью и опирания на нее сверху плечо рычага со стороны рессоры выполнено прямоугольного поперечного сечения и установлено с возможностью взаимодействия с нижней кромкой колосника в его рабочем положении с упором полки а на остальном участке - трапецеидального между колосниками и с возможностью взаимодействия с ними на оси размещены сменные фиксаторы ширина которых принята равной заданной величине щелевого зазора между колосниками. Изобретение позволяет повысить надежность работы дробилки за счет исключения забивания колосников. 3 з.п.ф-лы3 ил.
(21) (22) Заявка: 200213384403 15.12.2002
(46) Опубликовано: 27.05.2004
поиске: ВОЛКОВ В.Т. и др. Механизация и автоматизация в промышленности нерудных строительных материалов. - М.: Государственное издательство литературы по строительным материалам 1963 с.130-132.
SU 583814 А 15.12.1977.
SU 1123721 А 15.11.1982.
RU 2205694 С1 10.06.2003.
US 3659794 A 02.05.1972.
FR 2713107 A1 09.06.1995.
WO 9211942 A1 23.07.1992.
Изобретение предназначено для дробления материала. Роторная дробилка содержит корпус камеру дробления ротор с билами колосниковую решетку установленную на корпусе посредством горизонтального подпружиненного к корпусу шарнирного узла в виде закрепленной на корпусе дробилки неподвижной оси колосники решётки выполнены в виде двуплечих рычагов и установлены независимо друг от друга а каждый из них подпружинен самостоятельными плоскими рессорами S-образного профиля при этом один конец рессоры закреплен на свободном конце колосника а второй свободный конец размещен с возможностью взаимодействия при повороте колосника с горизонтальной полкой и корпусом дробилки а колосники снабжены спрофилированными по дуге окружности вырезами с возможностью их взаимодействия с осью и опирания на неё сверху плечо рычага со стороны рессоры выполнено прямоугольного поперечного сечения а на остальном участке -трапецеидального между колосниками и с возможностью взаимодействия с ними на оси размещены сменные фиксаторы ширина которых принята равной заданной величине щелевого зазора между колосниками при этом параметры колосниковой решетки выбираются из приведенного соотношения. Изобретение позволяет повысить надежность работы дробилки за счет исключения забивания колосников. 3 з.п. ф-лы 4 ил.
(21) (22) Заявка: 200212560503 25.09.2002
(46) Опубликовано: 10.02.2004
поиске: ВОЛКОВ В.Т. и др. Механизация и автоматизация в промышленности нерудных строительных материалов. - М. 1963 с.130-132 рис. 25.
SU 315330 A 06.12.1971.
SU 1071307 A 07.02.1984.
SU 641991 A 19.01.1979.
SU 149669 A 23.07.1962.
RU 1794480 A1 15.02.1993.
GB 992785 A 20.01.1964.
GB 2012188 A 25.07.1979.
DE 2034074 A 23.12.1971.
CH 636279 A5 31.05.1983.
WO 0149417 A1 12.07.2001.
9026 Санкт-Петербург В.О. 21 линия 2 СПГГИ (ТУ) патентный отдел
(54) Роторная дробилка
Роторная дробилка включает корпус камеру дробления ротор с билами съемную футеровку корпуса которая выполнена в виде размещенных в шахматном порядке конусов обращенных вершинами внутрь камеры дробления при этом угол при вершинах конусов принят меньше двойного угла трения в паре футеровка - дробимая порода. Каждый конус в своем основании может быть снабжен хвостовиком цилиндрической формы с винтовой нарезкой на конце ориентированным по оси конуса и с возможностью размещения хвостовика в отверстии корпуса дробилки и фиксации на нем с помощью гайки. Изобретение позволяет уменьшить износ футеровочного материала снизить его стоимость и уменьшить трудоемкость работ при замене футеровки. 1 з.п. ф-лы 2 ил.
Статус: по данным на 16.04.2010 - действует
(21) (22) Заявка: 99105024039910502403 10.03.1999
(46) Опубликовано: 20.12.2000
поиске: SU 1507449 A 15.09.1989. SU 606621 A 18.04.1978. FR 2456557 A1 12.12.1980. DE 1285278 A 12.12.1068. DE 3936390 C1 06.12.1990. US 5248100 A 28.09.1993.
7376 Санкт-Петербург ул. Проф.Попова д.5 СПГЭТУ патентный отдел
Санкт-Петербургский государственный электротехнический университет
(54) СПОСОБ АВТОМАТИЧЕСКОГО РЕГУЛИРОВАНИЯ ПРОЦЕССА ИЗМЕЛЬЧЕНИЯ В РОТОРНОЙ ДРОБИЛКЕ И УСТРОЙСТВО ДЛЯ ЕГО ОСУЩЕСТВЛЕНИЯ
Изобретение предназначено для автоматического регулирования процесса измельчения в роторной дробилке. Способ автоматического регулирования включает измерение и изменение скорости вращения ротора задание угла установки лимитирующей отражательной плиты измерение крупности исходного материала и изменение углов установки управляющих отражательных плит при этом осуществляется регулирование сжатия пружин отражательных плит в зависимости от частоты упругих колебаний отражательных плит и частоты вращения ротора с билами. Устройство для осуществления способа включает датчик крупности исходного материала исполнительный электродвигатель и систему регулирования установки углов отражательных плит включающую последовательно соединенные управляемые источники питания электродвигатели элемент сравнения задатчик включающий последовательно соединенные индикаторную шкалу датчик регулируемый источник питания при этом введена система автоматического сжатия пружин отражательных плит содержащая последовательно соединенные датчик упругих колебаний блок подстройки частоты регулируемый источник питания электродвигатель регулирующий сжатие пружины. Изобретение расширяет функциональные возможности автоматического регулирования процесса измельчения. 2 с.п. ф-лы 4 ил.
(21) (22) Заявка: 94003499039400349903 31.01.1994
(46) Опубликовано: 27.09.1997
поиске: 1. Касаткин А.Г. Основные процессы и аппараты химической технологии. Издание восьмое переработанное. - М.: Химия 1971. 2. Авторское свидетельство СССР N 1400660 кл. B 02 C 1306 198. 3. Авторское свидетельство СССР N 157049 кл. B 02 C 1306 1991. 4. Авторское свидетельство СССР N 1704820 кл. B 02 C 1306 1992.
Мостепаненко Виктор Кузьмич
Изобретение может быть применено в химической сельскохозяйственной и других отраслях промышленности. Камера дробления роторной дробилки имеет по четыре ротора и по паре загрузочных и выгрузочных патрубков причем роторы установлены с возможностью вращения со скоростью не более 40 мс. Рабочие элементы ротора могут быть выполнены в виде зубьев расположенных по винтовой линии под углом 30-90o к плоскости торцового сечения ротора. Дробилка может быть снабжена еще тремя камерами дробления. 2 з. п. ф-лы 2 ил.
(21) (22) Заявка: 95111517039511151703 04.07.1995
(46) Опубликовано: 20.08.1997
поиске: 1. Авторское свидетельство СССР N 1757738 кл. B 02 C 1302 1992. 2. Авторское свидетельство СССР N 1727889 кл. B 02 C 1302 1992.
Товарищество с ограниченной ответственностью - Научно-производственное предприятие "Ермак М Лтд.
Акционерное общество закрытого типа "Золотой дождь
Изобретение может быть применено в комбикормовой промышленности для измельчения зерен сельскохозяйственных культур на корм животных. Роторная дробилка состоит из кожуха 1 выполненного в виде диффузора внутри которого закреплен корпус 2 с измельчающими выступами 3 на внутренней 4 цилиндрической поверхности. На валу 5 смонтирован ротор 6 с билами 7. На наружной 11 цилиндрической поверхности корпуса 2 выполнены кольцевые щелевые канала 12 вскрывающие внутреннюю цилиндрическую поверхность 4 корпуса между смежными измельчающими выступами. Щелевые каналы могут быть выполнены по винтовой линии трапециевидной формы с расширением в сторону разгрузки. Просеивающая поверхность может быть образована навитой на измельчающие выступы со стороны кожуха стальной износостойкой проволокой с фиксированным зазором между витками. Просеивающая поверхность может быть изготовлена из перфорированной стальной ленты закрепленной на измельчающих выступах со стороны кожуха. 3 з.п. ф-лы 7 ил.
(12) ПАТЕНТ НА ПОЛЕЗНУЮ МОДЕЛЬ
(21) (22) Заявка: 200913238222 27.08.2009
(46) Опубликовано: 10.01.2010
3096 Самарская обл. г.Самара ул. Осипенко 11 оф.410-412
Бурыгин Руслан Викторович (RU)
Бурыгин Виктор Сергеевич (RU)
Формула полезной модели
Роторная дробилка включающая вертикальную круглую в поперечном сечении измельчительную камеру в которой на коаксиальном ей валу установлен роторный нож-измельчитель а также привод вала роторного ножа загрузочное устройство классификатор и разгрузочную полость отличающаяся тем что на валу дополнительно установлены два роторных ножа в измельчительной камере размещена регулировочная мембрана а на боковой поверхности камеры радиально выполнены щелевые отверстия классификатор выполнен в виде перегородки которая установлена снизу первого дополнительного роторного ножа и внешней кромкой плотно соединена с боковой стенкой измельчительной камеры при этом в перегородке выполнено калибровочное отверстие соединяющее измельчительную камеру с разгрузочной полостью а под перегородкой установлен второй дополнительный роторный нож.
Дробилка по п.1 отличающаяся тем что роторные ножи установлены коаксиально и имеют ромбовидную форму при этом кромки лезвия ножей заточены с двух сторон с углом атаки 45°.
Дробилка по п.1 отличающаяся тем что регулировочная мембрана выполнена в виде съемного кольца и установлена между ножом-измельчителем и первым дополнительным роторным ножом.
Дробилка по п.1 отличающаяся тем что калибровочное отверстие перегородки имеет овальную форму и расположено эксцентрично оси вала.
Дробилка по п.1 отличающаяся тем что в нижней части разгрузочной полости установлены лопасти вытяжного вентилятора.
(21) (22) Заявка: 200913075522 11.08.2009
Закрытое акционерное общество "Машиностроительная компания "Технэкс" (RU)
(54) ДРОБИЛКА МОЛОТКОВАЯ
Дробилка молотковая содержащая основание выполненное из двух частей установленный на основании корпус с загрузочным и разгрузочным патрубками сервисными окнами и опорными площадками с размещенной в нем горизонтально ориентированной цилиндрической дробильной камерой образованной ситами установленными на выдвижных рамах зафиксированных снаружи на лицевой торцевой стенке корпуса в которой размещены ротор включающий горизонтально расположенный вал с насаженными на него роторными дисками установленный в подшипниковых опорах смонтированных на опорных площадках и кассеты с молотками закрепленные между роторными дисками с возможностью вращения на осях проходящих через диски на определенном радиальном расстоянии от вала и параллельно ему и двигатель установленный на плите размещенной на основании и соединенный через муфту с ротором отличающаяся тем что основание выполнено как единое целое и установлено на виброизолирующих опорах корпус жестко связан с основанием и выполнен как единое целое с ним выдвижные рамы с ситами дополнительно закреплены внутри корпуса при помощи подпружиненных кулачков установленных на задней стенке корпуса опорные площадки размещены под сервисными окнами и жесткосвязаны с торцевыми стенками корпуса и основанием сервисные окна выполнены размером и формой обеспечивающей монтаж и демонтаж ротора из корпуса без разборки ротора а двигатель установлен на регулируемой по высоте плите.
(21) (22) Заявка: 94034359039403435903 08.09.1994
(46) Опубликовано: 20.06.1997
поиске: 1. Порошин В.В. и др. Двобильно-размольное оборудование. - Алма-Ата: Мектоп 1984 с.188. 2. Косарев А.И. и др. Современное дробильное оборудование.- Машмир 1991 с.49 (Обзорная информация: Строительное дорожное и коммунальное машиностроение. Серия 4. Машины и оборудование для промышленности строительных материалов.). 3. Авторское свидетельство СССР N 856546 кл. B 02 C 1314 1981. 4. Авторское свидетельство СССР N 1031504 кл. B 02 C 1316 1983. 5. Авторское свидетельство СССР N 1576198 кл. B 02 C 1316 1990.
Свинарев Борис Михайлович
Москвичев Александр Федорович
Целью изобретения является повышение эффективности процесса дробления материала. В предлагаемой дробилке диски основного и дополнительного роторов попарно связаны между собой дифференциалами позволяющими обеспечить встречное вращение соседних дисков с удвоением относительных скоростей вращения при использовании только одного общего привода. Предложена компактная система обеспыливания потока с использованием только одного общего привода. Предложена компактная система обеспыливания потока с использованием естественной вибрации корпуса дробилки (без индивидуального привода для встряхивания фильтрующей ткани). Для подмола крупных кусков использована накладка с ударными штырями на лопастях верхнего диска. Для обеспечения требуемой тонины помола корпус в нижней части снабжен перфорацией а ротор - набором отбойников и радиальных лопаток на вращающемся поддоне. 2 ил. 1 табл.
(21) (22) Заявка: 200613080922 25.08.2006
(46) Опубликовано: 10.09.2008
Лихтенвальд Сергей Валерьевич (RU)
ОБЩЕСТВО С ОГРАНИЧЕННОЙ ОТВЕТСТВЕННОСТЬЮ "ЦЕНТР СОПРОВОЖДЕНИЯ БИЗНЕСА" (RU)
(54) МОДУЛЬНАЯ ЛИНИЯ ГРАНУЛИРОВАНИЯ
Модульная линия гранулирования включающая гранулопроизводящий блок оборудования и блок аспирации отличающаяся тем что оба блока установлены в стандартных транспортных контейнерах с взаимосвязью оборудования в технологической последовательности и возможностью раздельной поблочной транспортировки контейнеров при этом контейнер с гранулопроизводящим блоком оборудования в рабочем положении является нижним и одновременно основанием для установки на нем контейнера блока аспирации а стенки обоих контейнеров снабжены сквозными люками для технологических потоков отверстиями для ввода энергоносителей и проемами для обслуживания.
Линия по п.1 отличающаяся тем что гранулопроизводящий блок оборудования включает молотковую дробилку приемный бункер-смеситель сырья пресс-гранулятор транспортер гранул элеваторы противоточный охладитель роторный сепаратор гранул бункер-циклон для гранул упаковщик транспортер пульт управления.
Линия по п.1 отличающаяся тем что блок аспирации включает циклоны вентиляторы воздуховоды системы кабелей и датчиков.
Линия по п.1 отличающаяся тем что оборудование обоих блоков жестко закреплено за стенки иили жесткий каркас контейнеров.
(21) (22) Заявка: 500667033 28.08.1991
(46) Опубликовано: 27.09.1995
поиске: 1. Авторское свидетельство СССР N 1329819 кл. B 02C 13 09 1986.
поиске: 2. Патент США N 2957633 кл. 241 -57 1960.
Уральский асбестовый горно-обогатительный комбинат им.50-летия СССР
Изобретение относится к устройствам для дробления материалов. Сущность изобретения заключается в формировании направленного потока легкой фракции на отражающую решетку конструктивное выполнение которой препятствует выносу из дробилки вместе с волокном породных частиц крупностью более 1 мм. Роторная дробилка содержит корпус 1 горизонтальный ротор 2 с билами 3 установленные одна за другой с зазором отбойные плиты 4 и 5 диффузор 6 для вывода из дробилки с помощью воздуха легкой фракции. В зазоре между отбойными плитами 4 и 5 размещены закрепленные к ним направляющие пластины 7 и 8 образующие канал 9 над которым под углом 20-30° к его оси установлена отражающая решетка 10. Отражающая решетка 10 состоит из двух ярусов продольных элементов. 2 з. п. ф-лы 3 ил.
(21) (22) Заявка: 200613940122 25.10.2006
(46) Опубликовано: 10.04.2007
Шеремет Игорь Михайлович (RU)
Темников Александр Владимирович (RU)
Ледовских Александр Вячеславович (RU)
Курушов Владимир Анатольевич (RU)
Борисов Геннадий Александрович (RU)
Общество с ограниченной ответственностью "Инжиниринговая компания "ТЭСИ" (RU)
(54) КОМПЛЕКСНАЯ ТЕХНОЛОГИЧЕСКАЯ ЛИНИЯ ПРОИЗВОДСТВА ГРАНУЛИРОВАННОГО ПОРИСТОГО МАТЕРИАЛА
Комплексная технологическая линия производства гранулированного пористого материала содержащая приемные бункеры сырья оборудование для измельчения сырья дозаторы добавок бункеры запаса дробленого сырья и полуфабрикатов оборудование для помола и механоактивации дробленого сырья с водой смесители гранулятор оборудование для сушки вспенивания и отжига классификатор транспортеры для подачи сырья полуфабрикатов готовой продукции склад готовой продукции отличающаяся тем что состоит из двух параллельно действующих участка обработки сырьевых компонентов соединенных с участком смешения формования и получения гранул причем первый участок обработки сырьевых компонентов включает последовательно установленные приемный бункер кремнеземистого материала роторный измельчитель вальцы грубого помола дробилку валковую смеситель двухвальный с подведенной к нему системой подачи и дозирования воды смесители планетарно-шнековые насос суспензии аттриторы в качестве оборудования для помола и механоактивации дробленого сырья с водой насос суспензии второй участок обработки сырьевых компонентов включает последовательно установленные приемный бункер стеклообразного материала роторный измельчитель дробилку щековую дробилку валковую вибросито бункер накопительный аттриторы в качестве оборудования для помола и механоактивации дробленого сырья с водой с подсоединенной к ним системой подачи и дозирования воды и технологических добавок насос суспензии участок смешения формования и получения гранул включает последовательно установленные смеситель-диспергатор насос суспензии накопительную емкость распылительную сушилку бункер пресс-порошка гранулятор тарельчатый сушилку гранул печь вспенивания охладитель гранул классификатор склад готовой продукции.
Комплексная технологическая линия по п.1 отличающаяся тем что подача измельченного стеклообразного сырья в аттриторы осуществляется через распределительное устройство с весовым дозатором.
Комплексная технологическая линия по п.1 отличающаяся тем что измельченное кремнеземистое сырье в виде водной суспензии подается в аттриторы насосом через планетарно-шнековые смесители с весовыми дозаторами.
Комплексная технологическая линия по п.1 отличающаяся тем что перемешивание компонентов в виде водных суспензий осуществляется в смесителе-диспергаторе.
Комплексная технологическая линия по п.1 отличающаяся тем что сушилка гранул отапливается отходящими газами от печи вспенивания.
(12) СВИДЕТЕЛЬСТВО НА ПОЛЕЗНУЮ МОДЕЛЬ
(21) (22) Заявка: 200211714620 02.07.2002
(46) Опубликовано: 10.01.2003
Закрытое акционерное общество "Союзмашэкспорт
Роторная дробилка содержащая корпус ротор с билами колосниковую решетку установленную на корпусе посредством горизонтального шарнира и подпружиненную к корпусу спиральными пружинами отличающаяся тем что колосники решетки выполнены в виде двухплечих рычагов и установлены независимо друг от друга а каждый из них подпружинен самостоятельными пружинами кинематически связывающими колосник с горизонтальным кронштейном закрепленным на корпусе при этом плечо рычага от шарнира до пружин выполнено прямоугольного поперечного сечения а на остальном участке - трапецеидального.
Дробилка по п.1 отличающаяся тем что колосники снабжены отверстиями со свободно размещенной в них осью с возможностью независимого поворота колосника относительно этой оси.
Дробилка по п.1 отличающаяся тем что каждый колосник снабжен двумя полуосями с возможностью их размещения в прорезях проушин кронштейна причем прорези ориентированы наклонно с подъемом и расширением в сторону кронштейна.
Дробилка по п.1 отличающаяся тем что жесткость пружин принята чередующейся по величине при переходе от одного колосника к другому.
Дробилка по п.1 отличающаяся тем что каждый колосник с нерабочей стороны снабжен петлей с возможностью захвата за нее грузозахватным приспособлением.
Добываемые нерудные каменные материалы используемые в строительстве в качестве заполнителей для изготовления бетонных и железобетонных изделий и конструкций; подстилающего слоя в дорожном строительстве и др. — требуют переработки (дробления измельчения).
Особого внимания заслуживает проблема переработки отходов промышленности бетонного и кирпичного лома образованного при разборке ветхих и безликих зданий отслуживших свой срок.
Остро встает вопрос о переработке техногенных отходов запасы которых огромны.
Техногенные отходы могут служить ценнейшим сырьем для производства строительных материалов. Комплексное использование отходов производства с дополнительным их обогащением позволяет сократить расход некоторых основополагающих сырьевых компонентов бетонной смеси. Так например переработкой отвальных шлаков доменной металлургии получают шлаковые песок и щебень вполне пригодные для замещения природных заполнителей в технологии бетонов; использование зол ТЭС — улучшает формовочные свойства бетонных и растворных смесей позволяет получить улучшенное качество поверхности готовых изделий снизить плотность а следовательно и теплопроводность бетона что особенно важно в технологии легких и ячеистых бетонов. Однако основной целью утилизации техногенных отходов является решение вопросов по экономии традиционного минерального сырья и оздоровления общей экологической обстановки районов используемых в настоящее время как полигоны хранения а попросту свалки отходов различных производств.
Получение готового продукта стандартного качества осуществляется с использованием дробильно-измельчительной техники.
Для дробления исходных малоабразивных горных пород средней прочности (известняков доломитов мергелей и др.) с размером кусков 100-1100 мм успешно применяют роторные дробилки. Универсальность роторных дробилок состоит в том что их можно использовать как для крупного так и для среднего и мелкого дробления.
Рабочим органом дробилки является ротор с жестко закрепленными на нем в несколько рядов (от 2 до 6) ножами. Загружаемый исходный материал попадая в дробильную камеру ограниченную лобовой и боковыми стенками станины отражательными плитами и ротором разрушается ударом по нему ножами ротора и ударами об отражательные плиты.
Получение необходимой конечной крупности зерен дробимого материала осуществляется регулировкой положения отражательных плит посредством регулировочных устройств различной конструкции.
Производительность роторных дробилок П (м3ч) рассчитывается по формуле:
Lp и Dp — длина и диаметр ротора м
k — коэффициент учитывающий положение отражательных плит
vp — окружная скорость ножей мс
z — число рядов ножей на роторе
Благодаря малым габаритным размерам и массе по сравнению со щековыми и конусными дробилками простоте устройства обеспечению выхода щебня преимущественно кубообразной формы — роторные дробилки нашли широкое применение в промышленности строительных материалов.
Инженер—технолог МП «ТЕХПРИБОР»
Удачное сочетание прогрессивных технических решений характерных как для вихревых мельниц так и многорядных стержневых дезинтеграторов обеспечивает неизменно превосходный результат сверхмелкого дробления и тонкого помола самых различных материалов уже в первую стадию измельчения.
Принцип действия и технические особенности
Простая но вместе с тем очень эффективная конструкция роторов с консольным расположением ударных элементов позволяет использовать общую массу подвижных частей при измельчении самых разных материалов. Измельчение сырья происходит в результате контакта отдельных частиц с быстродвижущимися в противоположных направлениях ударными стержнями (пальцами-билами) и последующих ударах вторичных осколков частиц о неподвижную массивную преграду — стенок помольной камеры.
Материал подлежащий измельчению через загрузочный патрубок поступает в центральную часть одного из роторов (закрытую корзину) в зону действия первого круга ударных стержней (пальцев-бил). Уже при первом контакте материала с ударными элементами дезинтегратора происходит мгновенное разрушение многочисленных агломератов комков и сростков образование которых так характерно для порошковообразных веществ. Последующее движение частиц материала от центра ротора к его периферии происходит в распыленном состоянии так называемого «дисперсного занавеса». В зависимости от частоты вращения роторов и свойств обрабатываемого материала конфигурация а также расположение ударных элементов дезинтегратора назначается таким образом чтобы каждая частица при прохождении вращающихся роторов получила определенное число ударов пальцев-бил. Продвигаясь от первого ряда ударных элементов к последующим каждая отдельная частица разрушается в результате многократных ударов о пальцы-билы при этом интенсивность разрушения постоянно возрастает поскольку с увеличением диаметра ряда возрастает линейная скорость ударных элементов. Покидая последний ряд пальцев-бил частицы обрабатываемого материала получив максимальное ускорение отбрасываются по касательной к окружности вращения этого ряда ударяются о стенки помольной камеры и выводятся из корпуса агрегата через широкое разгрузочное окно.
Технические характеристики и основные преимущества
Наименование параметров
Вариант расположение роторов
горизонтально-соосное
Номинальная частота вращения роторов обмин
Направление вращения роторов
Количество ударных элементов (пальцев-бил) шт.
Линейная скорость пальцев-бил мс
Номинальная мощность кВт
Количество электродвигателей шт.
Производительность тч
Допустимый максимальный размер измельчаемого или смешиваемого материала мм не более
Твердость обрабатываемого материала по шкале Мооса не более
Номинальные габаритные размеры (L×B×H) мм
Широкие возможности для комплексных решений
Компоновка технологического оборудования в составе модульного комплекса «МОЛОТ А - 300» обеспечивает легкий доступ к отдельным узлам и агрегатам для их ревизии и технического обслуживания. При эксплуатации комплекса обеспечивается соблюдение действующих норм и правил по технике безопасности и производственной санитарии.
Комплект поставки и технические характеристики модульного помольного комплекса «МОЛОТ А - 300»
Наименование параметров
Циклон — разгрузитель ЦРК- 600
Двухступенчатый пылеулавливающий агрегат ФРЦ — 5000
Дисковый затвор ДЗ-260
Шкаф управления серии ШУ
Номинальные габаритные размеры комплекса (L×B×H) мм
Приемный бункер материала;
Циклон- разгрузитель;
Патрубок вывода материаловоздушной смеси;
Двухступенчатый пылеулавливающий агрегат;
Патрубок ввода материаловоздушной смеси;
Дисковые затворы разгрузки материала.
ВЫСОКАЯ ЭФФЕКТИВНОСТЬ - БЛАГОПРИЯТНАЯ ЦЕНА
Оборудование сертифицировано в системе ГОСТ Р Госстандарта России.
Роторная дробилка модели «СМД-5 ВЕЙДЕР»
типоразмера «ДР 1500 4х2»
Представленное оборудование относится к дробилкам ударного действия разрушение кусков дробимого материала происходит в результате ударов бил жестко закрепленных на роторе.
Дробилки данного типа отличают высокая степень дробления большая производительность малый расход энергии простота конструкции и надежность.
Роторная дробилка модели «СМД-5 ВЕЙДЕР» предназначена для среднего и мелкого дробления шлака металлургического известняка доломита мергеля мрамора гипса руд малой абразивности и других подобных материалов предел прочности которых не превышает 600 кгссм2 а размер кусков 180 мм.
Помимо непосредственного дробления роторная дробилка данной модели также может использоваться в качестве динамического гранулятора что позволяет проводить обогащение каменных пород по форме и прочности за счет разрушения слабых включений без ослабления структурной прочности целевого продукта.
Большая производительность возможность производства фракционированных материалов кубовидной формы малая энергонагруженность и отсутствие необходимости в устройстве массивного фундамента позволяют использовать роторную дробилку «СМД-5 ВЕЙДЕР» в качестве высокоэффективного агрегата первичного или вторичного дробления твердых материалов самого разного происхождения.
Область применения дробилок различных типов
Технические особенности и конкурентные преимущества
Роторная дробилка модели «СМД-5 ВЕЙДЕР» имеет простую но вместе с тем очень рациональную конструкцию каждый элемент которой продуман до мелочей и работает на повышение эффективности дробления упрощение технического обслуживания снижение стоимости эксплуатации оборудования.
Для достижения этих целей МП«ТЕХПРИБОР» был использован целый ряд оригинальных технических решений.
Краткий перечень основных преимуществ новых роторных дробилок позволяет убедиться в этом:
Ударные элементы двухстороннего действия - для уменьшения себестоимости дробления
Оригинальные билы роторной дробилки «СМД-5 ВЕЙДЕР» имеют не одну а целых две рабочих грани что позволяет восстановить выбранные параметры дробления просто развернув ударные элементы. Такое техническое решение сделало возможным существенное увеличение сроков службы инструментов дробления за счет более полного использования металла бил. Теперь их замена может проводиться в два раза реже нежели в других моделях оборудования аналогичного назначения.
Установка ударных элементов ротора и отбойных плит - максимально быстро - без болтов и гаек
Не секрет что практическая производительность дробильного оборудования серьезно страдает из-за сложности и высокой трудоемкости технического обслуживания необходимости держать на складе разнообразную номенклатуру инструментов дробления защитной брони и т.д.
Так же не является секретом что крепления элементов дробления требуют очень внимательного к себе отношения. Зачастую резьбовые соединения превращаются в трудно разъемные уже после переработки нескольких тонн каменных материалов. Вот почему для установки ударных элементов роторной дробилки «СМД-5 ВЕЙДЕР» не используются гайки. Билы просто вставляются в направляющие и удерживаются от осевого смещения специальными фиксаторами. Благодаря чему разворот или полная замена инструментов дробления выполняется в течение 15-20 минут силами одного человека без использования грузоподъемных механизмов.
Для сокращения времени технического обслуживания или сроков ожидания поставки сменных деталей билы ротора и билы отбойных плит имеют одинаковые размеры а 90% элементов брони корпуса полностью взаимозаменяемы.
Широкая распашная дверь - для того чтобы осмотр и обслуживание выполнялись в самые короткие сроки
В целях сокращения времени простоев узлы технического обслуживания роторной дробилки «СМД-5 ВЕЙДЕР» организованы таким образом чтобы сделать ремонтные и профилактические работы максимально простыми удобными и быстро выполнимыми.
На боковой плите корпуса дробилки выполнена широкая распашная дверца открыв которую можно получить доступ абсолютно ко всем узлам и деталям камеры дробления для их осмотра ревизии или замены.
Устройства поддержания заданного усилия дробления объединенные с пружинными блоками безопасности
Во время работы дробильного агрегата в карьере существует вероятность попадания в камеру дробления посторонних включений (например зубьев экскаватора) которые ни при каких условиях не могут быть измельчены. Защиту от поломок роторной дробилки обеспечивает система выгрузки недробимых включений которая автоматически удаляет из камеры дробления посторонние предметы.
В роторной дробилке «СМД-5 ВЕЙДЕР» система выгрузки объединена с устройством поддержания заданного усилия дробления что позволяет сразу после удаления препятствия немедленно возвратиться к выбранным настройкам параметров дробления.
Устройство технические характеристики принцип действия
Ударное дробление является динамическим процессом. В дробилке «СМД-5 ВЕЙДЕР» осуществляется сразу три стадии кинетического дробления. Первая стадия начинается в тот момент когда билы ротора ударяют по дробимому материалу. Вторая стадия дробления осуществляется при столкновении кусков с отражательными плитами. Третья стадия обеспечивается за счет соударений частиц дробимого материала.
Рабочими органами дробилки «СМД-5 ВЕЙДЕР» являются: массивный ротор (1) с жестко закрепленными на нем билами (2) и отражательные плиты (3).
Фракционный состав продукта дробления зависящий от величины зазора между окружностью вращения бил ротора и отражательными плитами регулируется посредством многофункционального устройства поддержания заданного усилия дробления объединенного в пружинных блоках (4). Продукт дробления выводится из корпуса дробилки по наклонной пластине (5).
Технические характеристики роторной дробилки «СМД-5 ВЕЙДЕР» типоразмера «ДР 1500 4х2»
Габаритные размеры (L×B×H)
Установленная мощность
Линейная скорость бил ротора
Длина и диаметр ротора с установленными билами
Размеры загрузочного окна
Размеры загружаемого материала не более
* Производительность дробилки при обработке конкретного вида материала может изменяться в зависимости от физико-механических свойств данного материала
Комплексная поддержка до и после продажи
Являясь разработчиком и производителем оборудования для переработки каменных материалов МП«ТЕХПРИБОР» способно не только предложить заказчику стандартные решения но также разработать и изготовить оригинальное оборудование полностью соответствующее производственно-технологическим требованиям конкретного предприятия.
Независимо от того используется ли роторная дробилка «СМД-5 ВЕЙДЕР» как отдельная единица или же она интегрирована в состав дробильно-сортировочного комплекса каждая модель обеспечивается комплексным обслуживанием и технической поддержкой которые начинаются уже с момента анализа потребностей заказчика и разработки наиболее рациональных схем дробления и сортировки.
Принципы сотрудничества с заказчиками основанные на индивидуальном подходе в решении самых сложных производственных задач неизменно дают свои положительные результаты укрепляя репутацию МП«ТЕХПРИБОР» как надежного делового партнера способного не только предложить но и воплотить в жизнь самые смелые проекты.
Роторная дробилка модели «СМД-10 ВЕЙДЕР»
типоразмера «ДР 1500 4х4»
Роторная дробилка модели «СМД-10 ВЕЙДЕР» предназначена для среднего и мелкого дробления шлака металлургического известняка доломита мергеля мрамора гипса руд малой абразивности и других подобных материалов предел прочности которых не превышает 600 кгссм2 а размер кусков 350 мм.
Большая производительность возможность производства фракционированных материалов кубовидной формы малая энергонагруженность и отсутствие необходимости в устройстве массивного фундамента позволяют использовать роторную дробилку «СМД-10 ВЕЙДЕР» в качестве высокоэффективного агрегата первичного или вторичного дробления твердых материалов самого разного происхождения.
Роторная дробилка модели «СМД-10 ВЕЙДЕР» имеет простую но вместе с тем очень рациональную конструкцию каждый элемент которой продуман до мелочей и работает на повышение эффективности дробления упрощение технического обслуживания снижение стоимости эксплуатации оборудования.
Оригинальные билы роторной дробилки «СМД-10 ВЕЙДЕР» имеют не одну а целых две рабочих грани что позволяет восстановить выбранные параметры дробления просто развернув ударные элементы. Такое техническое решение сделало возможным существенное увеличение сроков службы инструментов дробления за счет более полного использования металла бил. Теперь их замена может проводиться в два раза реже нежели в других моделях оборудования аналогичного назначения.
Так же не является секретом что крепления элементов дробления требуют очень внимательного к себе отношения. Зачастую резьбовые соединения превращаются в трудно разъемные уже после переработки нескольких тонн каменных материалов. Вот почему для установки ударных элементов роторной дробилки «СМД-10 ВЕЙДЕР» не используются гайки. Билы просто вставляются в направляющие и удерживаются от осевого смещения специальными фиксаторами. Благодаря чему разворот или полная замена инструментов дробления выполняется в течение 15-20 минут силами одного человека без использования грузоподъемных механизмов.
В целях сокращения времени простоев узлы технического обслуживания роторной дробилки «СМД-10 ВЕЙДЕР» организованы таким образом чтобы сделать ремонтные и профилактические работы максимально простыми удобными и быстро выполнимыми.
В роторной дробилке «СМД-10 ВЕЙДЕР» система выгрузки объединена с устройством поддержания заданного усилия дробления что позволяет сразу после удаления препятствия немедленно возвратиться к выбранным настройкам параметров дробления.
Ударное дробление является динамическим процессом. В дробилке «СМД-10 ВЕЙДЕР» осуществляется сразу три стадии кинетического дробления. Первая стадия начинается в тот момент когда билы ротора ударяют по дробимому материалу. Вторая стадия дробления осуществляется при столкновении кусков с отражательными плитами. Третья стадия обеспечивается за счет соударений частиц дробимого материала.
Рабочими органами дробилки «СМД-10 ВЕЙДЕР» являются: массивный ротор (1) с жестко закрепленными на нем билами (2) и отражательные плиты (3).
Технические характеристики роторной дробилки «СМД-10 ВЕЙДЕР» типоразмера «ДР 1500 4х4»
Независимо от того используется ли роторная дробилка «СМД-10 ВЕЙДЕР» как отдельная единица или же она интегрирована в состав дробильно-сортировочного комплекса каждая модель обеспечивается комплексным обслуживанием и технической поддержкой которые начинаются уже с момента анализа потребностей заказчика и разработки наиболее рациональных схем дробления и сортировки.
Ударно-отражательные дробилки моделей «ДУО-ВЕЙДЕР-4x2Реверс»
Дробилки «ДУО-ВЕЙДЕР» - являются представителями нового поколения высокоэффективных ударно-отражательных измельчительных агрегатов преимущества которых обеспечены применением самой совершенной технологии ударного дробления твердых материалов.
Предлагаемое оборудование относится к типу быстроходных ударно-отражательных дробилок реализующих оригинальный способ разрушения твердых материалов методом «свободного удара» или «кинетического дробления».
Ударно-отражательные дробилки «ДУО - ВЕЙДЕР» имеют простую но вместе с тем очень эффективную конструкцию массивного ротора с жестко закрепленными ударными элементами что позволяет использовать общую массу подвижных частей при измельчении особо прочных материалов. Интенсивное дробление материала происходит в результате контакта с быстродвижущимися ударниками ротора и ударов о неподвижную преграду — отражательные элементы отбойных плит. Основной особенностью новых дробилок является уникальная комбинация высокой скорости движения ударных элементов ротора рациональной конструкции камеры дробления и функциональной простоты основных операций по техническому обслуживанию и регулировке.
Идеи заложенные в конструкцию дробилок «ДУО - ВЕЙДЕР» позволяют одинаково эффективно решать задачи дробления - ресайклинга как нерудных материалов в частности взорванных горных пород прочностью до 1500 кгссм2 так и отходов дорожного полотна бетонного производства строительного лома от сноса ветхих зданий и сооружений. К несомненным достоинствам дробильного оборудования данного типа следует отнести большую производительность высокую степень измельчения низкий расход энергии минимальные требования по качеству и периодичности технического обслуживания.
ПРУЖИННЫЕ АМОРТИЗАТОРЫ - НАДЕЖНОСТЬ И БЕЗОПАСНОCТЬ
УДАРНЫЕ ЭЛЕМЕНТЫ РОТОРА -
ПРОСТОТА МОНТАЖА И НАДЕЖНОСТЬ
Высокая надежность - Низкие производственные затраты
Надежная и безопасная работа дробилок «ДУО - ВЕЙДЕР» обеспечивается благодаря применению высококачественных износостойких сталей пружинных амортизаторов отбойных плит и прекрасно сбалансированной конструкции подвижных частей.
Конструкторским бюро МП«ТЕХПРИБОР» был использован свой многолетний опыт в создании оптимального профиля ударных элементов и самые новейшие разработки в области металлургии чтобы свести к минимуму расход стали на тонну произведенного продукта даже при дроблении материалов высокой прочности и абразивности.
Оригинальная конструкция ударно - отражательных элементов позволяет при сохранении стабильных показателей дробления найти желаемый компромисс между высокой производительностью оборудования и низкими эксплуатационными расходами.
Защита от поломок дробильного агрегата обеспечивается системой выгрузки недробимых включений которая автоматически удаляет из камеры дробления материалы которые не могут быть измельчены. Пружинные амортизаторы и устройство поддержания заданного усилия дробления после удаления препятствия немедленно возвращают отбойные плиты дробилки в исходное положение. Таким образом при попадании в камеру дробления неизмельчаемых включений отбойные плиты с отражательными элементами автоматически возвращаются к выбранным настройкам режимов дробления.
Низкая себестоимость дробления при использовании дробилок «ДУО - ВЕЙДЕР» обеспечивается благодаря целому ряду оригинальных технических решений направленных на более полное использование сменных ударно-отражательных элементов на фоне снижения расхода стали на тонну продукции. В частности отражательные элементы двухроторной ударно-отражательной дробилки «ДУО-ВЕЙДЕР-4x4 Дубль Ротор» полностью взаимозаменяемы что позволяет переустанавливать их с менее нагруженных участков отбойных плит в места наиболее интенсивного контакта с обрабатываемым материалом. Благодаря возможности «циркуляции» отражательных элементов достигается их высокая степень использования.
Реверсивная ударно-отражательная дробилка модели «ДУО-ВЕЙДЕР-4x2 Реверс» имеет симметричные отбойные пластины и ударные элементы особой формы что существенно увеличивает срок службы инструментов дробления. Каждый ударник имеет не одну рабочую поверхность а две! Подобное техническое решение позволяет существенно сократить простои оборудования связанные с заменой ударных элементов. При износе одной стороны ударных элементов для поддержания высокой плотности наполнения камеры дробления и восстановления прежней эффективности измельчения достаточно изменить направление вращения ротора при этом дополнительных регулировок положения отбойных плит и перенастройки режимов дробления не требуется. В результате замена ударных элементов дробилки «ДУО - ВЕЙДЕР - 4х2 Реверс» производится в два раза реже нежели в другом оборудовании аналогичного назначения.
Широкие возможности использования - Легкая адаптация
Дробилки «ДУО - ВЕЙДЕР» обеспечивают получение больших объемов высококачественного продукта кубовидной формы на вторых и третьих стадиях измельчения при среднем мелком и сверхмелком дроблении.
Сегодня дробление твердых материалов является широко распространенным технологическим переделом в различных отраслях промышленности. Строительная дорожно-строительная горнодобывающая металлургическая промышленности - все это далеко неполный перечень областей применения ударно-отражательных дробилок «ДУО - ВЕЙДЕР». Независимо от того используется ли данная дробилка как самостоятельный агрегат или в составе дробильно-сортировочного комплекса высокая универсальность возможность альтернативного выбора производительности мощности привода количества и конфигурации элементов дробления делает возможным использование данного оборудования для решения широчайшего круга задач переработки твердых материалов.
Новые ударно-отражательные дробилки «ДУО-ВЕЙДЕР» - это не только уникальное сочетание надежности и производительности но и совершенно новые возможности:
получения высококачественного щебня для отсыпки дорог;
производства кубовидного щебня как наполнителя бетонов;
эффективной переработки отходов бетонного производства и строительного лома;
дробления сырьевых компонентов в цементном производстве;
измельчения каменного угля в целях его обогащения и факельного сжигания;
дробления и измельчения руд металлических и неметаллических полезных ископаемых для их обогащения;
измельчения известняка доломита и металлургических шлаков;
производства материалов для раскисления почв;
измельчения самых разнообразных материалов для нужд химической промышленности.
Отличный баланс подвижных частей дробилок «ДУО-ВЕЙДЕР» виброизолированные опоры корпуса автоматическая система вывода недробимых включений возможность регулирования усилия дробления позволяют снизить нагрузку на силовую часть агрегата и делают возможным отказ от устройства массивного фундамента. Наиболее высокие в классе показатели использования подведенной энергии на единицу диаметра ротора возможность получения продукта преимущественно кубовидной формы за меньшее количество стадий дробления позволяют существенно уменьшить капитальные вложения при организации на производстве участка дробления - ресайклинга.
Простое и быстрое техническое обслуживание - Легкость доступа
При создании дробилок «ДУО-ВЕЙДЕР» вопросам упрощения операций по техническому обслуживанию оборудования в ограниченном рабочем пространстве уделялось особое внимание.
Не секрет что зачастую практическая производительность дробильного оборудования серьезно страдает из-за сложности и высокой трудоемкости технического обслуживания необходимости держать на складе разнообразную номенклатуру инструментов дробления защитной брони и т.д. Так же не является секретом что болтовые крепления элементов дробления требуют очень внимательного к себе отношения. Зачастую резьбовые соединения крепящие инструменты дробления превращаются в трудно разъемные уже после переработки нескольких тонн материала. Болты и гайки крепления ударных элементов оказываются настолько плотно забиты каменной мелочью что отвернуть их становится очень непросто.
Специалисты МП «ТЕХПРИБОР» понимая что время потерянное при замене инструментов дробления регламентном обслуживании и ожидании поставки сменных деталей - это время потерянное в производстве использовали целый ряд технических решений направленных на снижение времени вынужденного простоя оборудования. Именно поэтому ударные и отражательные элементы дробилок «ДУО-ВЕЙДЕР» совершенно идентичны а 90 % элементов защитной брони имеют одинаковые размеры и полностью взаимозаменяемы.
В целях сокращения времени простоев дробилки узлы технического обслуживания организованны таким образом чтобы все регламентные операции были максимально простыми и легко выполнимыми.
ОТРАЖАТЕЛЬНЫЕ ЭЛЕМЕНТЫ ОТБОЙНОЙ ПЛАСТИНЫ - БЫСТРО И ДОСТУПНО БЕЗ БОЛТОВ И ГАЕК
Наглядным примером такого подхода является оригинальная схема установки инструментов дробления. Правильное положение отражательных элементов достигается благодаря тщательно проработанной конструкции направляющих отбойных плит. Крепление выполняется без использования болтов и гаек при этом фиксация положения обеспечивается элементами самого корпуса дробилки. Для замены отражательных элементов достаточно открыть распашные створки корпуса и извлечь изношенную деталь из камеры дробления. Широкие распашные створки позволяют получить доступ абсолютно ко всем узлам и деталям камеры дробления для их осмотра ревизии или замены.
Благодаря продуманной конструкции сопрягаемых деталей замена ударных элементов ротора также не представляет каких-либо затруднений и может выполняться силами одного человека без использования грузоподъемных механизмов. Ударные элементы устанавливаются в специальные пазы и удерживаются от смещения сегментами ротора. Такая система фиксации позволяет точно установить инструменты дробления надежно их закрепить сохранить балансировку ротора сэкономив при этом время и силы.
Каждая дробилка «ДУО-ВЕЙДЕР» обеспечивается комплексным обслуживанием и технической поддержкой. Обслуживание начинается уже с момента анализа потребностей заказчика и разработки наиболее рациональной схемы дробления учитывающей конкретные условия производства.
Основные технические характеристики реверсивной ударно-отражательной дробилки «ДУО-ВЕЙДЕР - 4х2 Реверс»
Масса без ударно-отражательных элементов
Номинальная мощность
Линейная скорость ударных элементов ротора
Длина и диаметр ротора с установленными ударными элементами
Количество ударно-отражательных элементов
Макс. размеры загружаемого материала
Основные технические характеристики двухроторной ударно-отражательной дробилки «ДУО-ВЕЙДЕР - 4х4 Дубль Ротор»
Количество ударно- отражательных элементов
ДА ПРИБУДЕТ С ВАМИ СИЛА!
Роторная дробилка «ВЕЙДЕР-3000»
Роторная дробилка модели «ВЕЙДЕР-3000» относится к измельчительным агрегатам ударного действия и предназначена для среднего и мелкого дробления каменных материалов с пределом прочности до 600 кгссм2.
К несомненным достоинствам дробилок данного типа следует отнести большую производительность и высокую степень измельчения что позволяет одновременно выполнять дробление первой и второй ступени.
Использование роторной дробилки «ВЕЙДЕР-3000» делает возможным упрощение технологической схемы получения фракционированных материалов самого различного происхождения позволяет сократить капитальные затраты связанные с ее установкой уменьшить количество обслуживающего персонала.
Помимо непосредственного измельчения роторная дробилка «ВЕЙДЕР-3000» также может использоваться в качестве динамического гранулятора. При этом обогащение каменных пород по форме и прочности происходит за счет разрушения слабых включений и повышения структурной прочности целевого продукта.
По мнению специалистов именно агрегаты динамического дробления к которым относятся роторные и молотковые дробилки наиболее эффективны в работах по улучшению формы отдельных зерен фракционированных материалов. В этом случае высокая технологическая ценность продукта дробления достигается при меньших удельных затратах. В частности хорошо известно что повышенное содержание зерен лещадной формы снижает плотность и ухудшает удобноукладываемость асфальтобетонной смеси. Механическая прочность лещадных зерен значительно меньше чем у кубовидного щебня. Использование роторной дробилки «ВЕЙДЕР-3000» позволяет выпускать большие объемы материалов наивысшего качества уже в первую стадию дробления.
Роторная дробилка «ВЕЙДЕР-3000» имеет простую но вместе с тем очень рациональную конструкцию (Рис. 1). Рабочими органами дробилки является массивный ротор (1) с жестко закрепленными на нем дробящими ножами (2). Разрушение материала происходит в результате его контакта с быстродвижущимися ножами ротора и ударов о неподвижную преграду — отражательную пластину (3). Особенностью дробилки данной модели является уникальная комбинация высокой скорости движения ударных элементов ротора оригинальной формы камеры дробления и функциональной простоты основных операций по техническому обслуживанию и регулировке.
Материал подлежащий измельчению поступает в камеру дробления (Рис. 2) образованную лобовой броней (4) и отражательными пластинами с установленными на них дробящими ножами. Фракционный состав продукта дробления регулируется за счет изменения зазора между отражательными пластинами и дробящими ножами ротора. Регулировка зазоров производится эксцентриковым валом (5).
Защита от поломок элементов дробления обеспечивается системой выгрузки недробимых включений которая автоматически выводит предметы которые не могут быть измельчены. Отражательные пластины под действием пружин после удаления препятствия немедленно возвращаются в исходное положение. Таким образом в случае попадания в камеру дробления посторонних включений отбойные пластины с отражательными элементами автоматически возвращаются к выбранным настройкам режимов дробления.
Для упрощения процедуры проведения регламентных работ корпус дробилки выполнен разборным а органы регулировки расположены в легко доступных местах что облегчает обслуживание агрегата замену бронефутеровки дробящих ножей и т.д.
Технические характеристики роторной дробилки «ВЕЙДЕР - 3000»
Наименование показателей
Значения показателей
Габаритные размеры (LxBxH)
Масса без электродвигателя
Установленная мощность
Кол-во оборотов ротора
Зазор между ротором и отбойными пластинами
Максимальный размер кусков загружаемого материала
* возможна поставка в трехтонном контейнере
Высокая производительность возможность получения фракционированных материалов кубовидной формы малая энергонагруженность и отсутствие необходимости в устройстве массивного фундамента позволяет использовать роторную дробилку «ВЕЙДЕР-3000» как высокоэффективный агрегат первичного или вторичного дробления твердых материалов самого разного происхождения.
Дробление осадочных и метаморфических горных пород строительного мусора и отходов производства грануляция и обогащение подготовка питания мельниц и дезинтеграторов все это далеко не полный перечень вариантов использования роторной дробилки «ВЕЙДЕР-3000».
Вибрация или сотрясения - одна из разновидностей механических колебаний и в отличие от воздушного звукового шума представляет собой материальный шум передающийся на человека непосредственно от источника вибрации или по элементам конструкций производственных зданий. Четкого определения выделяющего вибрацию из многообразия механических колебаний нет. Условно считают что вибрация - это колебания с малой амплитудой и большой частотой.
Однако инфразвуковые колебания с частотой до 16 Гц и часть диапазона звуковых колебаний (с частотой 16-20 000 Гц) различных тел и поверхностей воспринимаются организмом как вибрация и сотрясения. По воздействию на организм человека вибрацию делят на общую и местную. Общая вибрация вызывает колебания всего организма местная действует на руки или другие части тела.
На многих заводах по производству железобетонных изделий основания вибрационных машин и механизмов жестко связаны с фундаментом здания что приводит к распространению вибрации на перекрытие и пол. На таких участках работающий подвергается вибрации в течение всего рабочего дня. Лица подвергающиеся систематическому воздействию общей вибрации превышающей санитарные нормы заболевают вибрационной болезнью характеризующейся приступами головокружений непереносимостью вибраций головными болями.
Местная вибрация действует на работающих с ручным виброинструментом в результате чего появляются повышенная утомляемость в области кистей и пальцев рук сильные боли наблюдаются онемения. Иногда бывают судороги пальцев повышается чувствительность рук к охлаждению. Оценку физиологического действия вибрации нельзя давать без учета амплитуды частоты скорости и ускорения колебательного процесса которые являются основными величинами характеризующими колебательные движения.
Амплитуда и частота колебания в производственных условиях могут быть определены при помощи вибрографов. Для точного измерения параметров вибрации применяют электрические измерительные приборы которые в отличие от механических требующих непосредственного контакта с вибрирующей поверхностью можно улавливать на значительном расстоянии он места измерения получая информацию от датчиков смонтированных на измеряемом объекте.
Оценку степени вредности вибрации инструментов и производственного оборудования осуществляют по уровню виброскорости в диапазоне частот 11-2800 Гц который включает в себя 8 октавных частотных полос со среднегеометрическими значениями частот (16 32 63 125 250 500. 10002000 Гц). Для предупреждения вибрационной болезни необходимо чтобы вес инструмента или другого виброоборудования удерживаемого в руках не превышал 10 кг а сила нажима работающих на вибрирующем оборудовании не превышала 20 кгс.
Суммарное время контакта с вибрирующими поверхностями не должно превышать 8з длительности рабочего дня. Сверхурочные работы на вибрирующем оборудовании не допускаются. Работы связанные с вибрацией выполняют как правило в отапливаемых помещениях при температуре воздуха не ниже 16°С влажности 40-60% и скорости движения не более 03 мсек. Работающему через каждый час работы должны предоставляться 10-15 минутные перерывы или поручаться работы не связанные с вибрацией.
При работе виброинструментом важно не допускать переохлаждения рук для чего надо выдавать рабочим рукавицы с прокладками из пенопласта пористой резины или фетра. Предельно допустимые величины общей вибрации рабочих мест (пол сиденье ограждение и т. д.) санитарными нормами устанавливаются по уровню виброскорости в диапазоне частот от 11 до 355 Гц который включает пять октавных частотных полос со среднегеометрическими значениями частот 16 32 63 125 и 250 Гц. Вибрации с частотой ниже 11 Гц нормируются по основной частоте колебаний.
Приведенные нормы применяют при непрерывном воздействии вибраций в течение рабочего дня. Если продолжительность воздействия вибраций не более 20% рабочего времени величину смещения и скорости можно увеличить но не более чем в 15 раза. Уменьшение передачи вибраций через грунт достигается применением при устройстве фундаментов под вибромашины акустических швов с засыпкой их асбестовой крошкой препятствующей распространению колебаний за пределы засыпки.
С этой же целью применяют акустические зазоры шириной около 10 см в которых изолирующей прослойкой является воздух. Для уменьшения вибраций при работе вибрирующего оборудования на пол настилают виброизоляционные асбестоцементные или древесноволокнистые плиты или коврики из губчатой резины войлока пробки. Применяют специальную обувь на толстой губчатой резиновой подошве.
Ширина лестничных маршей
Ширина лестничных маршей дверей и проходов должна обеспечивать возможно более быструю эвакуацию людей в случае пожара и составлять не менее 1 м на каждые 100 эвакуирующихся. Для успешной эвакуации людей большое значение имеет удаленность рабочих мест от эвакуационного выхода в лестничную клетку или непосредственно из помещений первого этажа наружу.
В зависимости от категории пожароопасности данного производства степени огнестойкости здания и его этажности эти расстояния должны быть в одноэтажных зданиях не более 30- 100 м а в многоэтажных - не более 25-75 м.
Эвакуационные выходы
Число эвакуационных выходов из производственных и вспомогательных зданий или помещений должно быть как правило не менее двух при площади помещения более 300 ж2. Иногда допускается в качестве второго выхода использовать наружные пожарные лестницы но в таком случае пожарные лестницы должны иметь на уровне эвакуационных проемов площадки с перилами высотой не менее 08 м уклон таких лестниц должен быть не более 60° а ширина - не менее 07 м.
Лестничные клетки должны быть закрытыми чтобы предотвратить проникание в них огня и дыма должны иметь естественное и электрическое освещение. Чтобы выход был свободным запрещается устанавливать в лестничных клетках выступающие из стен отопительные приборы прокладывать огнеопасные трубопроводы устраивать выход из шахты лифта.
Нормы по хранению материалов
Количество хранимых материалов устанавливают в зависимости от их пожарной опасности и способа хранения а также необходимости бесперебойного протекания технологического процесса. Легковоспламеняющиеся и горючие жидкости допускается хранить лишь в производственных зданиях I или II степени огнестойкости.
При строительстве промышленных зданий расположении в них цехов планировке оборудования должны быть учтены безопасность и быстрота эвакуации людей из здания в случае пожара или аварии. В первую очередь должно быть предусмотрено наличие достаточного количества эвакуационных выходов (проходы двери ворота) с необходимой пропускной способностью.
В отдельную группу промышленных зданий следует выделить склады. Пожарная опасность складов заключается в том что на сравнительно небольших площадях сконцентрированы значительные количества сгораемых материалов. Общезаводские и цеховые склады сгораемых материалов допускается размещать в производственных или вспомогательных зданиях только при условии выделения этих складов противопожарными стенами.
Значительную пожарную опасность с точки зрения возникновения и распространения пожара представляют расположенные внутри производственных зданий разнообразные складские помещения. Как правило все промежуточные склады выделяют от основных производственных помещений несгораемыми стенами и перекрытиями.
Шум действует не только на слуховой аппарат человека но и на нервную систему а через нее на другие Жизненно важные системы и органы прежде всего на сердечнососудистую систему. Степень нарушения деятельности нервной системы и других органов вызванного воздействием шума зависит от его уровня распределения по частотам длительности действия и от индивидуальных особенностей человека.
Установлено что производственный шум превышающий санитарные нормы рассеивает и притупляет внимание работника снижает производительность труда. Механические колебания материальных частиц в зависимости от частоты подразделяют на инфразвуковые шумовые и ультразвуковые с частотами соответственно до 16 (не воспринимаемые слухом) с 16 до 20 000 (воспринимаемые слухом) и выше 20 000 (невоспринимаемые слухом).
Для измерения силы звука или его уровня интенсивности применяется логарифмическая шкала. Каждая ступень такой шкалы носит название бел который указывает во сколько раз данная сила звука превышает исходную величину. Для измерения силы звука принята единица - дб (децибел) равная 01 бела. Уровень шума измеряют шумомерами действие которых основано на преобразовании микрофоном акустических сигналов в электрические.
Состав частоты производственного шума определяют анализатором спектра шума в комплекте с шумомером. Во избежание вредного действия шума на организм применяют следующие основные методы: уменьшение шума в источнике звукоизоляцию виброизоляцию звукопоглощение; архитектурно-планировочные мероприятия средства индивидуальной защиты.
Предотвращение распространения шума от его источника осуществляют путем замены механизмов ударного действия механизмами безударного действия металлических деталей пластмассовыми подшипников качения подшипниками скольжения путем ограничения скорости газовых потоков ослабления вибрации деталей при помощи вибропоглощающих прокладок и фундаментов облицовок из резины войлока пробки асбеста и т. п. смазывания соударяющихся деталей устройства глушителей на выходе выхлопных газов и др.
Если снизить уровень шума в самом источнике невозможно механизмы и агрегаты генерирующие шум помещают в изолирующие кожухи или кабины обеспечив дистанционное управление и наблюдение за шумными агрегатами. Для улучшения звукоизолирующих свойств металлического кожуха внутреннюю поверхность его облицовывают техническим войлоком стекловатой паклен асбестом.
Для предотвращения шума возникающего от колебаний конструкций (корпусной шум) применяют виброизоляцию при помощи резиновых амортизаторов. Производственные здания на территории предприятия должны быть размещены так чтобы шум проникающий из шумных помещений не увеличивал уровень шума помещений других зданий более чем на 3 дБ.
Простейшим средством защиты органов слуха от шума является вата или марля вставленные в слуховой канал; при этом снижается шум на 3-14 дБ в полосе частот 100-6000 Гц при применении марли смоченной жиром- до 18 дБ а шерстяной ваты с воском - до 30 дБ. Полупластичные предохранительные втулки плотно закрывающие слуховой канал обеспечивают снижение шума до 20 дБ. Применяемые в настоящее время некоторые конструкции антифонов (противошумов) закрывающих ушную раковину снижают шум до 30 дБ.
Многие технологические процессы и операции на предприятиях промышленности строительных материалов (дробление помол просеивание транспортирование твердых материалов) сопровождаются большим выделением пыли. Тепловые процессы на многих заводах - сушка в сушильных барабанах и обжиг во вращающихся печах также сопровождаются интенсивным запылением и загазованностью производственных помещений.
Пыль представляет собой мельчайшие твердые частицы органического или неорганического происхождения способные находиться в течение некоторого времени в воздухе или промышленных газах во взвешенном состоянии. Органическая пыль (угольная древесная хлопчатобумажная и др.) является неагрессивной пылью.
Неорганическая пыль - минеральная (кварцевая керамическая цементная асбестовая карборундовая металлическая) является агрессивной (токсичной) пылью присутствие которой в воздухе производственных помещений в количествах превышающих санитарные нормы представляет опасность. Степень измельчения (дисперсность) пыли находится в широких пределах.
Пыль разделяется на три группы: видимая с размерами частиц более 10 мк микроскопическая - 10-025 мк и ультрамикроскопическая - меньше" 025 мк видимая только через электронный микроскоп (системы содержащие более мелкие частицы принято считать дымами).
Мероприятия по снижению запылённости
Для уменьшения образования и выделения пыли осуществляют мероприятия: технологического характера изменяющие производственные процессы и полностью исключающие или сокращающие выделение пыли (например влажный способ дробления помола и смешивания пылящих материалов и др.); санитарно-технического характера направленные на герметизацию оборудования улавливание и удаление пыли в источнике ее образования (местная вытяжная механическая вентиляция и т. п.).
Для уменьшения пылеобразования конвейерные ленты необходимо оборудовать устройствами исключающими возможность падения с них материалов и перекос лент. При транспортировании сухих кусковых материалов (глина известняк мергель и т. п.) скорость лент не должна превышать 16 мсек при перемещении зернистых материалов с размером кусков 3-4 мм (угольная крошка) и молотых материалов с размером частиц менее 05 мм (опока трепел известняк) - соответственно 05-1 и 02-06 мсек.
Кроме того высота свободного падения сыпучих материалов должна быть не более 05 g а места падения материалов должны быть надежно укрыты. На холостой ветви конвейерной ленты следует устраивать механические гидравлические или пневматические приспособления для снятия налипающего на нее материала. Открытые ленточные конвейеры необходимо заменять герметичными транспортными устройствами (пневмотранспорт аэрожелоб).
Для устранения выделения пыли из шнеков места сопряжений крышки с корытом изготовляют в виде песочного затвора а при жестком соединении фланцы снабжают войлочными прокладками. Низы бункеров и силосов для хранения порошковых или иных сыпучих материалов выкладывают пористыми плитками для подачи под них сжатого воздуха. Для разгрузки емкостей (бункеров и др.) содёржащих сыпучие материалы выделяющие пыль применяют дозирующие устройства (объемные или весовые) исключающие неравномерное поступление материала его обрушение или свободное падение связанное с большим пылевыделением.
В целях предупреждения полного опорожнения бункер снабжают автоматическим приспособление или сигнальным устройством указывающим допустимый предел опорожнения. Одна герметизация не всегда даёт положительный эффект. Поэтому герметизацию необходимо сочетать с аспирацией. Аспирация обеспечивается устройством местных отсосов пыли с места их образования для чего под укрытием пылящего оборудования создается разрежение препятствующее выделению пыли через неплотности.
Для очистки воздуха рабочих помещений от пыли применяют механические и электрофизические способы улавливания и осаждения пыли в специальных устройствах пылеосадительных камерах и "шахтах" центробежных осадителях (циклонах) рукавных фильтрах и электрофильтрах ультразвуковых аппаратах комплексных иных пылеосадителях и др. В пылеосадительных камерах пыль осаждается под воздействием силы тяжести за счет изменения скорости движения запыленного воздуха.
Для уменьшения скорости движения воздуха с 10 до 002-001 мсек сооружают камеры ("шахты") с относительно большими сечениями. Центробежные пылеосадители – циклоны при значительно меньших объемах более эффективны чем пылеосадительные камеры Циклоны устанавливают на всасывающий или нагнетающий трубопровод.
Поток запыленного воздуха поступает из трубопровода в циклон по касательной к его сечению и движется вниз по спирали между наружным кожухом и внутренней выходной трубой при этом на частицы пыли действуют центробежные силы отбрасывая их на внутреннюю поверхность кожуха. Здесь пылинки агрегируются и следуя за движением воздуха опускаются в нижний кожух циклона а затем направляются в приемный бункер Циклоны обладают высокой эффективностью осаждения ныли размером 10 мк и выше.
При размере пылинок 5 мк коэффициент очистки запыленного воздуха не превышает 50%. Поэтому для улавливания высокодисперсной пыли после грубой очистки запыленного воздуха в циклонах устанавливают различные фильтры (матерчатые бумажные масляные водяные и др.). В цементной промышленности широкое применение по улавливанию и осаждению пыли после цементнообжиговых печей сушильных барабанов мельниц сухого помола сырья и клинкера получила электрическая очистка отходящих газов и аспирационного воздуха при помощи электрофильтров. Электрофильтры являются наиболее эффективными пылеуловителями и при определенных условиях обеспечивают высокую степень очистки газов.
Требования к воздушному режиму и устройство вентиляции
Для проветривания все производственные помещения кроме помещений с кондиционированием воздуха должны иметь независимо от наличия вентиляционных устройств окна с открывающимися створками. Стены одноэтажных зданий у которых верхняя часть остекленных поверхностей находится на высоте более 10 м от уровня пола а также фонари с тремя и более ярусами переплетов оборудуют устройствами позволяющими легко их очищать.
Двери производственных помещений опасных в пожарном отношении должны открываться наружу а двери ведущие из комнат в коридоры - внутрь. Ширина наружных дверей принимается 14-15 м а для пропуска людских потоков - до 2 м Чтобы на рабочих местах поддерживать необходимый состав воздуха удовлетворяющий гигиеническим требованиям осуществляют вентиляцию производственных помещений.
Вентиляция может быть естественной или механической. естественная вентиляция осуществляется за счет разности удельных весов наружного воздуха и воздуха помещений или действия ветра. естественная вентиляция при которой поступление (приток без подогрева и очистки) и удаление (вытяжка) шелуха происходят через отверстия в окнах и фонарях называется аэрацией. Механическая вентиляция осуществляется при помощи вентиляционной установки состоящей из вентилятора с электродвигателем калорифера для подогрева приемного воздуха и фильтров для очистки воздуха от загрязнений. Приточная вентиляционная установка дополненная специальной камерой для увлажнения и охлаждения воздуха называется кондиционером.
Вентиляция не может быть только вытяжной или приточной так как количество удаляемого воздуха должно быть равно количеству поступающего приточного воздуха. В практических условиях часто имеются только вытяжные вентиляционные установки в помещениях куда неизбежно поступает воздух вследствие действия вытяжной вентиляции и некоторого снижения давления воздуха.
В этих случаях (когда приточная вентиляция не предусмотрена) наружный воздух притекает неорганизованным путем через открытые двери окна щели и т. п. В теплое время года неорганизованное поступление притока воздуха в большинстве случаев может быть оправданным. В холодное время года такое поступление воздуха может привести к значительному понижению температуры в производственном помещении а во влажных цехах к ухудшению действия вентиляции.
Из-за отсутствия организованного притока воздуха (при наличии только вытяжной вентиляции) условия труда на рабочих местах настолько ухудшаются что нередко пользоваться такой вентиляцией в холодное время года невозможно. Вентиляцию при которой приток и вытяжка организованы называют приточно-вытяжной. Камеры приточного воздуха и особенно места его забора должны быть гарантированы от загрязнения выбросами производства и как правило не располагаться на крышах горячих цехов.
В производствах с выделением пыли приточный воздух должен подаваться с небольшой скоростью чтобы не поднимать осевшей пыли. В связи с этим приточный воздух подают в верхнюю зону помещения. При тепло- газо- и влаговыделенпях приточный воздух подают в рабочую зону. В зависимости от способа организации воздухообмена вентиляция может быть местной и общей (общеобменной). Удаление газов паров пыли теплоты наиболее эффективно у мест их возникновения.
Для этой цели применяют местную вытяжную вентиляцию. При устройстве местной вытяжной вентиляции (местных отсосов) стремятся удалить из помещения большую часть вредностей чтобы меньшее их количество оставалось на разбавление с приточным воздухом. В качестве местных отсосов применяют вытяжные шкафы вытяжные зонты бортовые отсосы и другие специальные устройства.
Кроме местной вытяжной вентиляции иногда предусматривают местную приточную вентиляцию в виде воздушных завес воздушных душей и воздушных оазисов. Воздушные завесы создают своеобразную воздушную преграду или изменяют движение загрязненных потоков воздуха направляя их например к вытяжным отверстиям. Воздушный душ представляет собой сосредоточенный поток воздуха определенных параметров направленный непосредственно на человека.
Воздушные души устраивают на местах работы или длительного пребывания рабочих (если рабочее место непостоянно) и кратковременных перерывов для отдыха. Воздушный оазис - один из видов местной приточной вентиляции в горячем цехе представляющий собой выделенную перегородками вентилируемую часть помещения в которую подается воздух более чистый и с более низкой температурой чем воздух всего помещения.
Перегородки высотой около 2 м остекленные в верхней части снабжают решетками или другими воздухораспределительными устройствами через которые в огражденное (сверху открытое) пространство поступает воздух подаваемый по каналам вентилятором. Поступающий воздух будучи более тяжелым чем окружающий как бы затопляет рабочую площадь обеспечивая в воздушном оазисе более благоприятные температурные условия чем во всем помещении.
Когда технологический процесс затрудняет или делает невозможным применение местных отсосов устраивают общую (общеобменную) вентиляцию в цехах где вредные пары или газы выделяются во многих местах. Эффект действия общеобменной вентиляции основан главным образом на разбавлении подаваемым свежим воздухом уже поступивших в помещение вредных паров и газов до предельно допустимых концентраций.
Приложение А.doc
о патентно-информационном поиске при исследовании
(наименование объектов разработки)
(наименование вида исследования)
Страна период за который
проведено исследование
Индексы МКИ и национал.
Наименование источника информации
№№ автор: свидет. краткая аннотация техническая характеристика формула изобретения основные данные технического решения эскиз
Сведения о возможности использован. изобрет. в проекте
Описание изобретения
Роторная дробилка содержит корпус
В проекте не используется
камеру дробления ротор с билами
колосниковую решетку установленную на
корпусе посредством горизонтального
шарнирного узла и подпружиненную к
корпусу колосники решетки выполнены
в виде двуплечих рычагов и установлены
независимо друг от друга а каждый из них
подпружинен рессорами S-образного
Изобретение позволяет повысить
надежность работы дробилки за счет
исключения забивания колосников.
Сущность изобретения заключается в
формировании направленного потока
легкой фракции на отражающую решетку
конструктивное выполнение которой т
препятствует выносу из дробилки вместе с
волокном породных частиц крупностью
Рекомендуемые чертежи
- 23.08.2014
Свободное скачивание на сегодня
Другие проекты
- 17.04.2020