Курсовой проект по ТМС




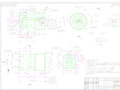
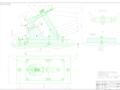
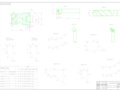

- Добавлен: 25.10.2022
- Размер: 2 MB
- Закачек: 0
Описание
Состав проекта
![]() |
![]() |
![]() ![]() |
![]() ![]() |
![]() ![]() |
![]() ![]() |
![]() ![]() |
![]() ![]() |
![]() |
![]() |
![]() ![]() ![]() ![]() |
![]() ![]() ![]() ![]() |
![]() ![]() ![]() ![]() |
![]() ![]() ![]() ![]() |
![]() ![]() ![]() ![]() |
![]() ![]() ![]() |
Дополнительная информация
резец_подрезной.dwg

Деталь.dwg

Карта наладок.dwg

Приспособление.dwg

Маршрут обработки.dwg

ТКП.09.42.02.00.00.100МК
Номер и содержание операции
Отрезать заготовки выдерживая размер l =125мм
выдерживая размер 123мм
Расточить сырые кулачки по Ш81
Б. Переустановить заготовку на правый шпиндель
выдерживая размер 122(-0
) выдерживая размер 47
Расточить торцевую канавку
выдерживая R1 и глубину 35(±0
выдерживая глубину 35(±0
Точить фаску 2х45&B на
Фрезеровать две лыски
выдерживая размеры b=55
выдерживая размеры 30(±0
выдерживая размеры 35(±0
l =54(±7) на глубину 28 (для захода фрезы)
выдерживая размеры R5
выдерживая размеры R5 и 2(+0
Зенкеровать отверстие
Развернуть отверстие
Нарезать резьбу Tr55х3-7Н
выдерживая размер 2х30&B
выдерживая размер 52(±0
выдерживая размер 1х45&B
Нарезать резьбу M16х1
выдерживая размер l =12
Многоцелевой двухшпиндельный
Nakamura-Tome Super NTJX
Полировать поверхности с обработкой
А. Расточить сырые кулачки
&C75f9 на левом шпинделе
Б. Переустановить заготовку на левый шпиндель
выдерживая размеры l =47(-0
выдерживая размеры &C39
Расточить коническое отверстие
; расточить коническое отверстие
Зенкеровать конические отверстия
выдерживая размеры &C52
выдерживая размер &C80h9
0. Сверлильная с ЧПУ
выдерживая размеры &C3
выдерживая размер &C
Сверлильно-фрезерный станок
Сверлить 4 отверстия
Зенкеровать 4 отверстия
Развернуть 4 отверстия
Полировать отверстие &C5Н11 и 4 отверстия &C7Н11
Нанести на заготовку олово методом окунания
Моечная и сушыльные машины
Расточить сырые кулачки
выдерживая размер &C75f9 на левом шпинделе
выдерживая размер &C80(-0
выдерживая размеры 47 и
Нарезать резьбу Tr80х4-8g
Курсак собранный.docx
Эффективность производства его технический прогресс качество выпускаемой продукции во многом зависят от опережающего развития нового оборудования машин станков от внедрения методов технико-экономического анализа обеспечивающего решение технических вопросов и экономическую эффективность технологических и конструкторских разработок.
Интенсификация технологических процессов на основе применения режущих инструментов из новых инструментальных материалов расширение области применения оборудования с ЧПУ повышение размерной и геометрической точности достигаемой при обработке – важнейшие направления развития технологии механической обработки в машиностроении.
Поэтому актуально создание технологических процессов созданных с учетом развития данных направлений и удовлетворяющих требованиям предъявляемым к современным технологиям обработки металлов резанием.
Целью данного курсового проекта является проектирование технологии изготовления сопла с применением станков с ЧПУ. В технологической части выполнены: анализ технологичности детали выбран наиболее экономически выгодный способ получения заготовки разработан технологический маршрут механической обработки корпуса переходника произведен расчёт припусков и оптимальных режимов резания; в конструкторской части спроектирован специальный режущий инструмент а также рассчитано и сконструировано специальное станочное приспособление; в экономической части проекта рассчитана себестоимость технологической операции.
ТЕХНОЛОГИЧЕСКАЯ ЧАСТЬ
Исходными данными для проектирования ТП изготовления сопла являются: рабочий чертёж детали с техническими требованиями; годовая программа выпуска продукции – 1500 шт.; режим работы – две смены; применяемое оборудование – станки с ЧПУ.
2.Назначение и конструкция детали
Конструкция сопла представляет собой круглую деталь в плане имеющую центральное не сквозное отверстие длинной 72мм для размещения в нём клапана а так же трапецеидальные резьбы наружная и внутренняя (для совмещения с мундштуком и фланцем) с шагом соответственно 4мм и 3мм. Сопло так же имеет 4 не центральных сквозных отверстия d=7мм которые предназначены для прохождения в них пластицированного материала поэтому для них необходимо произвести азотирование для увеличения износостойкости легированной стали 38Х2МЮА из которой изготовлено сопло. Так же азотированию подвергается входная часть сопла (поверхность И) и отверстие под углом 30 градусов относительно оси сопла предназначенное для отвода излишек материала.
Азотирование - это технологический процесс химикотермической обработки при которой поверхность различных металлов или сплавов насыщают азотом в специальной азотирующей среде. Азотированный слой не склонен к хрупкому разрушению. Твердость азотированного слоя легированных сталей — до 1100 HV. Защита участков поверхности от насыщения азотом производится нанесением олова (гальваническим методом или методом окунания; толщина слоя 10 мкм) обмазкой жидким стеклом с наполнителем (мел тальк асбест окись хрома и др.) химическим никелированием и заделкой отверстий металлическими пробками.
Наибольшие требования предъявляются к наружному диаметру D=75мм выполняемый по IT9 Ra=32 мкм который предназначен для дальнейшего базирования по нему и обеспечения радиального биения не более 003мм противоположно лежащего торца сопла. Так же к торцу предъявляются требования неплоскостности 002мм и шероховатости Ra=02мм. По IT7 выполняются два отверстия d=8мм и d=10мм.
В данной детали по внутренним частям протекает жидкость поэтому к этим поверхностям предъявляются жесткие требования по шероховатости Ra=08 и Ra=02; а так же для плотного соприкосновения плоскостей к торцу выполненному на глубине 35мм предъявляется требование по радиальному биению 003мм относительно поверхности Е и требование неплоскостности 002мм.
Сопло изготавливается из стали 38Х2МЮА – это сталь жаропрочная релаксационностойкая применяется в азотируемых деталях таких как шестерни валики пальцы втулки и т.д. работающие при температурах до 450 град. Химический состав приведён в таблице 1.1 механические свойства в таблице 1.2.
Таблица 1.1Химический состав легированной стали 38Х2МЮА (ГОСТ 4543-71) %
Содержание элементов %
Таблица 1.2 Механические свойства стали 38Х2МЮА
3.Анализ технологичности конструкции детали
В соответствии с ГОСТ 14.205 – 83 технологичность – это совокупность свойств конструкции изделия определяющих ее приспособленность к достижению оптимальных затрат при производстве эксплуатации и ремонте при заданных показателях качества объема выпуска и условиях выполнения работ.
Производственная технологичность конструкции детали – это степень ее соответствия требованиям наиболее производительного и экономичного изготовления. Чем меньше трудоемкость и себестоимость изготовления тем более технологичной является конструкция детали.
Оценка технологичности конструкции бывает двух видов: качественная и количественная. Качественная оценка предшествует количественной и сводится к определению соответствия конструкции детали определенным требованиям.
Качественная оценка технологичности является предварительной обобщенной и характеризуется показателями: «лучше - хуже» «рекомендуется - не рекомендуется» «технологично - нетехнологично». Технологичной при качественной оценке считают такую геометрическую конфигурацию детали и отдельных ее элементов при которой учтены возможности минимального расхода материала и использования наиболее производительных и экономичных для определенного типа производства методов изготовления.
Конструкция данной детали – сопло состоит из унифицированных элементов (трапецеидальная резьба метрическая резьба диаметры лыски); обеспечивает нормальный подвод и вывод режущего инструмента при обработке также она симметрична что упрощает составление программ обработки ее на станках с ЧПУ; содержит поверхности для надежных баз. Форма отверстий позволяет растачивать их напроход с одной стороны.
Но существуют также нетехнологичные элементы конструкции сопла а именно: есть глухое резьбовое отверстие М16х15-7H третьего класса точности что усложняет изготовление резьбы метчиком и увеличивает возможность его поломки а возможности заменить его сквозным нет; отверстие d=7мм сквозное но при выходе неизбежно возникновение одностороннего усилия что может привести к поломке сверла и увеличению расхода режущего инструмента (при сверлении с левой стороны конус предварительно проточен) либо инструмент изготовляющий конус будет работать на удар (при предварительном рассверливании отверстия d=7мм); угловое отверстие d=5мм необходимо сверлить непосредственно перед обработкой отверстия d=7мм для предотвращения увода инструмента так же при обработке отверстия d=5мм нет возможности использовать кондукторную втулку поэтому перед переходом сверление необходимо выполнить зацентровку и необходимо ужесточить допуск на размер для внутренней трапецеидальной резьбы необходим специальный режущий инструмент так как место для проточки резьбы ограничено.
Количественная оценка технологичности выражается показателем численное значение которого характеризует степень удовлетворения требований к технологичности. Рассчитаем три основных показателя:
Коэффициент точности рассчитывается по формуле:
Тср – средний квалитет точности обрабатываемых поверхностей;
ni - число размеров для каждого квалитета точности.
Коэффициент шероховатости рассчитывается по формуле:
где Raср – среднее значение параметра шероховатости обрабатываемых поверхностей;
ni – число поверхностей для каждого значения параметра шероховатости.
Коэффициент использования материала:
где Gд – масса детали кг;
Gзаг – масса заготовки кг.
В целом деталь считаю не технологичной хотя она и допускает применение высокопроизводительных режимов обработки имеет хорошие базовые поверхности но коэффициент использования материала мал и большое количество материала будет уходить в отход так же деталь довольно сложна по конструкции.
4.Определение типа производства
Согласно ГОСТ 3.1108 – 74 ЕСТД и ГОСТ 14.004 – 74 ЕСТПП одной из основных характеристик типа производства является коэффициент закрепления операций КЗ.О . Коэффициент КЗ.О показывает отношение числа всех операций выполняемых или подлежащих выполнению в цехе (на участке) в течении месяца к числу рабочих мест т.е. характеризует число операций приходящихся в среднем на одно рабочее место в месяц или степень специализации рабочих мест. При КЗ.О ≤ 1 производство массовое; если 1 КЗ.О ≤ 10 – крупносерийное; если 10 КЗ.О ≤ 20 – среднесерийное; если 20 КЗ.О ≤ 40 – мелкосерийное. В единичном производстве КЗ.О не регламентируется.
Для определения фонда времени работы оборудования и рабочих принимаем следующие исходные данные:
Полное (календарное) число дней в году – 365.
Количество выходных дней – 104.
Количество праздничных дней – 8.
Количество дней сокращаемых на один час в предпраздничные дни – 6.
Количество рабочих дней в году: Fо=365 – (104 + 8) = 253 дня.
Продолжительность рабочей недели – 41 час.
Продолжительность полной рабочей смены – 82 часа.
Количество рабочих дней с полной продолжительностью рабочей смены:
F = 253 – 6 = 247 дней.
Номинальный годовой фонд времени:
Действительный годовой фонд времени:
где П - Потери от номинального фонда – 13%;
Для расчета коэффициента закрепления операций составляется таблица (табл. 1.3)
Таблица 1.3. Расчет коэффициента закрепления операций.
5. Координатно-раст.
Определяется и записывается в третью графу таблицы расчетное количество станков mp для каждой операции:
где N – годовой объем выпуска деталей шт.; tшт (tшт-к)- штучное или штучно-калькуляционное время мин.; Fд- действительный годовой фонд времени ч.; з.н. - нормативный коэффициент загрузки оборудования (для расчетов в курсовом проекте принимается з.н = 075 085).
Принятое число рабочих мест Р устанавливают округлением значений тр (третья графа) до ближайшего большего целого числа.
Далее для каждой операции вычисляют значение фактического коэффициента загрузки:
Количество операций (последняя графа) выполняемых на рабочем месте определяется по формуле:
Коэффициент закрепления операций рассчитывается по формуле:
Производство среднесерийное.
Количество деталей в партии для одновременного запуска в производство согласно рекомендациям допускается определять следующим образом:
где N – годовая программа выпуска деталей;
а – число дней на которое необходимо иметь запас деталей (периодичность запуска-выпуска соответствующая потребности сборки);
F – число рабочих дней в году.
N = 1500 шт; F = 253 дня; а = 5 дней.
5.Выбор метода получения заготовки
Метод выполнения заготовок для деталей машин определяется назначением и конструкцией детали материалом техническими требованиями масштабом и серийностью выпуска а также экономичностью изготовления.
Выбор заготовки ведем по [1].
Определяем четыре основных показателя детали:
Материал детали – Сталь38Х2МЮА; по табл. 3.1 для данной марки стали определяем код – 6.
Серийность производства – по табл. 3.3; вид заготовок – поковка масса – 3 кг программа выпуска – 500; определяем код – 1;
Конструктивная форма – по табл. 3.2; основные признаки детали – в соответствии с чертежом; определяем код – 7;
Масса заготовки – по табл. 3.4 определяем для 3 кг соответствующий код – 3.
Выбираем возможные виды и способы получения заготовок для данной детали учитывая определенные выше коды четырех основных показателей детали:
Код конструктивной формы – 7;
Из табл. 3.7 по определенным ранее кодам 6 – 1 – 7 – 3 из графы таблицы «Вид заготовки» выписываем рекомендуемые коды видов: 910.
Используя табл. 3.6 расшифровываем вычисляемые коды видов заготовок:
Технико-экономическое обоснование выбора заготовки
Себестоимость производства заготовки – свободная ковка определяем по зависимости:
где С – базовая стоимость 1 т заготовок руб.т; - коэффициенты зависящие от класса точности группы сложности массы марки материала и объёма производства заготовок kт=1; kс=077; kв=1; kм=113; kп=1; Sотх – стоимость 1т отходов (стружки) руб.;
где Gзаг - масса заготовки; Gд. – масса детали; Кр - расчётный коэффициент для определения ориентировочной расчётной массы поковки;
Так как Кр = 2 Gд = 3 кг то
Себестоимость производства заготовки – прокат определяем по зависимости:
где Сп. з – приведённые затраты на рабочем месте коп.ч; Тшт – штучное или штучно-калькуляционное время выполнения заготовительной операции.
где Lрез - длина резания при разрезании проката на штучные заготовки (может быть принята равной диаметру заготовки Lрез =82)мм; y-величина врезания и перебега (при разрезании дисковой пилой y=68мм); Sм –минутная подача при разрезании (Sм =50-80 мммин); φ- коэффициент показывающий долю вспомогательного времени в штучном (φ=15 для крупносерийного производства);
Экономический эффект вычислим по формуле:
где S1 и S2 – стоимость заготовки по первому и второму варианту руб.; N – годовой объём выпуска деталей;
Коэффициент использования материала определяем по зависимости:
где Gд – масса детали кг. Gд = 3 кг; Gзаг – масса заготовки кг;
Снижение материалоемкости определяется по формуле кг
где Nг – годовой объем выпуска деталей шт.; G1G2-массы заготовок при первом и втором варианте.
Выбираем способ получения заготовки – прокат так как стоимость заготовки ниже и за год будет экономия в 5100руб и как показывают расчёты уменьшение материалоёмкости составит 645кг.
Проанализируем выбор баз для сопла. Данная деталь преимущественно является телом вращения и на первых операциях обрабатывается на токарном оборудовании. Для того что бы обработать поверхность 1 наружный диаметр которой а так же торец в дальнейшем будут базами необходимо предварительно обработать поверхности 3 и 2 по которым заготовка будет базироваться на первой операции. Причём поверхность 2 является установочной базой и несёт три опорные точки поверхность 3 является двойной опорной базой (рис. 1.1).
Рис. 1.1 Эскиз детали. Операция 010.
На второй операции необходимо обработать поверхности 3. Деталь будет базироваться по поверхности 2-установочная база и по поверхности 1-двойная опорная. (рис 1.2)
Рис 1.2 Эскиз детали. Операция 015.
При сверлении сквозных отверстий поверхность 3 будет являться двойной опорной а поверхность 2 оустановочной.(рис 1.1)
При сверлении отверстия под углом 300 поверхность поверхность 2 установочная резьбовая поверхность двойная опорная(рис 1.2)
Для данной детали при принятой программе выпуска 1500 штук в год можно принять маршрут обработки поверхностей в соответствии с таблицей 1.4.
7.Выбор оборудования. Проектирование маршрутного технологического процесса.
)Многоцелевой двухшпиндельный токарный станок Nakamura-Tome Super NTJX
Функциональные возможности
Макс. диаметр точения
Расстояние между шпинделями
Наибольший диаметр прутка
Левый правый шпиндель
Скорости шпинделя (макс.)
Основной шпиндельный мотор
Правый шпиндель 11 7.5kw
Шпиндельный мотор вращающегося инструмента (инструментальный шпиндель)
5 3.7KW (Bult-in type)
Инструментальный шпиндель
00min-1 12000min-1 (op.)
Кол-во резервных инструментов
инструментов (опция 80120 инструментов)
Тип хвостовика инструмента
Диаметр инструмента (макс.) без смежного инструмента
Длина инструмента (макс.) Вес инструмента (макс. момент)
Вращающийся инструмент револьверная головка
Скорости вращающегося инструмента
№ инструментальных станций (вращающийся инструмент)
Шпиндельный мотор вращающегося инструмента
Индивидуальное вращение
Перемещение суппорта
Инструментальный шпиндель X1-ось
Инструментальный шпиндель Z1-ось
Инструментальный шпиндель Y-ось (инструментальный шпиндельнижняя револьверная головка)
Инструментальный шпиндель B1-градус индексирования оси
Револьверная головка X2-ось
Револьверная головка Z2-ось
Размеры (Шир. x Дл.x Выс.)
18mm x 2922mm x 2445mm
)Сверлильно-фрезерный станок с ЧПУ Rapimill 700 700 HS
Расстояние от торца шпинделя до пов-сти стола
Расстояние от центра шпинделя до станины
Быстрый ход x у z-оси
Рабочая подача x у z-оси
Число оборотов шпинделя
Инструментальный магазин
Конус зажима инструмента
макс.диаметр инструмента
макс.длина инструмента
макс. вес инструмента
Время смены инструмента
Необходимое рабочее давление воздуха
Габариты: длина x ширина x высота
Мотор-шпиндель с ЧПУ фирмы
ЧПУ Фирмы “Сименс” 802 D
Таблица 1.4 Маршрут обработки поверхностей
Содержание и наименование операции
Отрезать заготовки выдерживая размер l =125мм
Подрезать торец выдерживая размер 123мм
Точить фаску 06х45º на 806
A.Расточить сырые кулачки по 813 на правом шпинделе
Б. Переустановить заготовку на правый шпиндель
Подрезать торец выдерживая размер 122(-03)
Точить 76(-05) выдерживая размер 475
Сверлить отверстие выдерживая размеры 95 и l= 715(+03)
Расточить отверстие выдерживая 515(+03) и l= 8(+036)
Расточить отверстие выдерживая 15 515(+03) и l= 15
Расточить торцевую канавку выдерживая 355 R1 515 и глубину 345(+03)
Точить 35 выдерживая R1 и глубину 35(±03)
Точить 52(+03) выдерживая глубину 35(±03)
Точить канавку выдерживая R16 R05 b=5 45º
Точить фаску 2х45º на 52
Фрезеровать две лыски выдерживая размеры b=55 l =40 и l =28
Фрезеровать лыску выдерживая размеры 30(±026) l =40 и l =30
Фрезеровать лыску выдерживая размеры 35(±03) l =40 и l =30
Сверлить отверстие выдерживая 10 l =54(±7) на глубину 28 (для захода фрезы)
Фрезеровать паз выдерживая размеры R5 l =40 и l =30
Фрезеровать скос выдерживая размеры R5 и 2(+05)
Сверлить отверстие выдерживая размеры 77 54(±01) и 20(±01)
Зенкеровать отверстие выдерживая 792
Развернуть отверстие выдерживая 8H7
Нарезать резьбу Tr55х3-7Н
Зенкеровать отверстие выдерживая размер 995 и l =72(+074)
Развернуть отверстие выдерживая размер 10Н7 и l =72(+1)
Точить фаску выдерживая размер 2х30º
Точить поверхность выдерживая размеры 75f9 и 47(-04)
Центровать торец выдерживая размер 52(±03)
Сверлить отверстие выдерживая размеры 8 14 и 195max 16max
Зенкеровать отверстие выдерживая размеры 8 145H11 и точить фаску выдерживая размер 1х45º
Нарезать резьбу M16х15-7H выдерживая размер l =12
Точить фаску выдерживая размер 16х45º на 75
Многоцелевой двухшпиндельный токарный станок Nakamura-Tome Super NTJX
)Полировать поверхности с обработкой
А. Расточить сырые кулачки выдерживая размер
f9 на левом шпинделе
Б. Переустановить заготовку на левый шпиндель
Подрезать торец выдерживая размеры l =47(-062) l =120(-0087)
Сверлить отверстие выдерживая размеры 395 l =29
Расточить коническое отверстие выдерживая размеры 15º 418; расточить коническое отверстие выдерживая 120º
Зенкеровать конические отверстия выдерживая размеры 42(±0089) и l =30(-052)
Точить поверхность выдерживая размеры 52 1х45º
Точить поверхность выдерживая размер 80h9
Точить фаску выдерживая размер 05х45º на 80h9
Полировать поверхности с обработкой
Сверлить отверстие выдерживая размеры 34 и l =18
Зенкеровать отверстие выдерживая размер 44
Развернуть отверстие выдерживая размер 5Н11
Сверлильно-фрезерный станок с ЧПУ Rapimill 700
Сверлить 4 отверстия выдерживая размеры 67. 25 15(±20) 35(±20)
Зенкеровать 4 отверстия выдерживая размер 695
Развернуть 4 отверстия выдерживая размер 7Н11
Полировать отверстие 5Н11 и 4 отверстия 7Н11
Нанести на заготовку олово методом окунания
Расточить сырые кулачки выдерживая размер 75f9 на левом шпинделе
Точить поверхность выдерживая размер 80(-03)
Точить фаску выдерживая размер 25х45º на 80
Точить поверхность выдерживая размеры 47 и 45º
Нарезать резьбу Tr80х4-8g
8 Расчёт припусков на механическую обработку
Рассчитать припуск на обработку поверхности 75f9.
Заготовка - горячекатаный прокат обычной точности.
Материал-сталь 38Х2МЮА.
Требуемые технологические переходы определяют путем расчёта коэффициентов уточнения. Обработку выполняют на многоцелевом станке за одну установку. В результате обработки необходимо обеспечить точность и шероховатость поверхности 32 мкм. Размер заготовки Таким образом в результате обработки необходимо обеспечить требуемое уточнение по диаметру отверстия:
Для обработки поверхности принимаем следующий маршрут: точение черновое точение чистовое точение тонкое.
Назначаем допуски на межоперационные размеры: Т1=03 (квалитет точности IT12) T2=012 (квалитет точности IT10) T3=0074 (квалитет точности IT9).
При данном сочетании технологических переходов:
Определяем общее уточнение для принятого маршрута обработки:
Полученное значение пр. показывает что при принятом маршруте точность обработки поверхности ) обеспечивается так как о пр. (18911893)
Технологический маршрут обработки поверхности 75f9 состоит из трех операций: чернового чистового и тонкого точения выполняемых при одном переходе обрабатываемой детали.
Заготовка базируется на данной операции по отверстию 80 в трёх кулачковом патроне. Величину отклонений для заготовки из проката определяют по формуле:
где - общее отклонение оси от прямолинейности; - смещение оси заготовки в результате погрешности центрирования.
где - отклонение оси детали от прямолинейности мкммм; - длина детали.
где ITD – допуск на диаметральный размер базы заготовки использованной при центрировании мм.
Определяют величину остаточной пространственной погрешности
где Ку – коэффициент уточнения.
После точения чернового:
После точения чистового:
При черновом точении деталь закрепляется в трёхкулачковом патроне погрешность базирования равна нулю. Погрешность установки определяется по формуле:
где - погрешность закрепления.
Погрешность закрепления складывается из двух составляющих: радиальной и осевой. Её значение можно определить по формуле
Для чистового точения:
Выбираем формулу для расчета припусков
где Rz и Т характеризуют качество поверхности на i-ом переходе.
Для проката Rz = 200 мкм Т = 300 мкм. Для чернового чистового и тонкого растачивания Rz и Т принимают следующие значения:
черновое - Rz = 125 мкм Т = 120 мкм;
чистовое - Rz = 63 мкм Т = 120 мкм;
Минимальный припуск:
Под черновое точение:
Под чистовое точение:
Максимальный припуск определим по формуле:
где ITD ITDi - поле допуска на размер обрабатываемой поверхности обеспечиваемый на выполняемом переходе.
Вычисляем предельные размеры:
Для тонкого точения:
Наибольший:Наименьший:
dmax = 74896+0074=7497 мм. dmin = 75- 0104=74896мм.
Для чистового точения:
dmax = 7505 + 012 = 7517 мм dmin = 74896 + 0156 = 7505 мм.
Для чернового точения:
dmax = 755 + 03 = 758 мм dmin = 7505 + 044 = 755 мм.
dmax = 773 +11 = 784 мм dmin = 755 + 1778 = 773 мм.
Расчетные данные сводим в табл.1.5
Маршрут обработки поверхности 75f9
Элементы припуска мкм
Расчетный припуск 2zmin мкм
Допуск на выполняемые размеры мкм
Принятые (округлённые) размеры заготовки по переходам мм
Предельный припуск мкм
Таблица 1.5 Результаты расчётов припусков на обработку поверхности 75f9.
Рассчитать припуск на обработку отверстия 10Н7
Технологический маршрут обработки поверхности 10Н7 состоит из четырёх операций: сверление зенкерование черновое развёртывание точное развёртывание тонкое выполняемых при одном переходе обрабатываемой детали.
Заготовка базируется на данной операции по отверстию 80 в трёх кулачковом патроне.
Величину отклонений для заготовки из проката определяют по формуле:
где - общее отклонение оси от прямолинейности; - смещение оси заготовки в результате погрешности центрирования - отклонение связанное с уводом сверла.
где - значение увода оси сверла; - смещение оси отверстия; -длина просверливаемого отверстия мм.
Определяем величину остаточной пространственной погрешности
После зенкерования чернового:
При точении деталь закрепляется в трёхкулачковом патроне погрешность базирования равна нулю. Погрешность установки определяется по формуле:
Для проката - Rz = 200 мкм Т = 300 мкм.
Сверление - Rz = 40 мкм Т = 60 мкм;
Зенкерование черновое - Rz = 30 мкм Т = 40 мкм;
Развёртывание точное -Rz = 5мкм Т =10мкм;
Развёртывание тонкое- Rz = 4мкм
Под зенкерование черновое:
Под развёртывание точное:
Под развёртывание тонкое:
Максимальный припуск:
Для тонкого развёртывания:
dmax = 10015 мм. dmin = 10015 – 0015 = 110 мм.
Для точного развёртывания:
dmax = 10015 – 0008 = 10007 мм dmin = 1001 – 0036 = 997 мм.
Для чернового зенкерования:
dmax = 10007 – 003 = 9977 мм dmin = 998 – 0058 = 992 мм.
dmax = 9977 – 0392 = 9585 мм dmin = 959 – 0090 = 95 мм.
dmax = 9585 – 18 = 7785 мм dmin = 779 – 11 = 669 мм.
Расчетные данные сводим в табл.1.6
Маршрут обработки поверхности 8H7
зенкерование черновое H10
развёртывание точное H8
развёртывание тонкое H7
Таблица 1.6 Результаты расчётов припусков на обработку поверхности 10H7
9. Расчёт режимов резания
Подрезать торец выдерживая размеры l =47(-062) l =120(-0087) .
Исходные данные для расчета: Материал 38Х2МЮА (229-269НВ) точность обработки поверхности IT9 параметр шероховатости Ra 16 мкм.
Станок: Многоцелевой двухшпиндельный токарный станок Nakamura-Tome Super NTJX. Частота вращения шпинделя n мин-1: до 6000.
Мощность привода главного движения кВт: 11.
Для получения размера детали l =120(-0087) Ra 16 необходимо вести обработку в две стадии: получистовое точение чистовое точение.
Резцы следует применять наименьшей технологически возможной длины и наибольшего технологически допустимого сечения. Принимаем резец с сечением 25х25 мм и вылетом l=150 мм.
Обработку проводим пластиной из твердого сплава СР200. Угол в плане составит φ=90.
Геометрические параметры режущей части инструмента выбирают из приложения 8[4]:
γ=5° - передний угол;
r=003 мм – радиус скругления режущей кромки;
rв= 08 мм – радиус вершины резца.
Принимаем нормативный период стойкости Т=30 мин как для пластин с механическим креплением винтом с конической головкой .
)Выбор глубины резания:
Выбор минимально необходимой глубины резания для получистового точения осуществляется по карте 2 [4].Глубина резания для получения 9го квалитета составляет t=15мм.
Для получистовой стадии обработки подачу выбирают по карте 4[4]: SoT=016 ммоб. Выбранное значение подач корректируют с учетом поправочных коэффициентов которые выбирают по карте 5[4].
Окончательно значение подачи для получистовой стадии обработки определяют по формуле:
)Выбор скорости резания:
Скорость резания для получистового точения выбирают по карте 21[4]. Получистовой стадии обработки соответствует скорость резания vт=174 ммин. По этой же карте скорости резания корректируют с учетом инструментального материала Кvи=1.
Коэффициенты на скорость резания для получистовой стадии обработки для измененных условий выбирают также по карте 23 [4].
Скорректированная скорость резания:
Для чистовой стадии обработки:
)Частоту вращения шпинделя определяют по формуле:
Выбор минимально необходимой глубины резания для чистового точения осуществляется по карте 2 [4].Глубина резания для получения 9го квалитета составляет t=08мм.
Для чистовой стадии обработки подачу выбирают по карте 6[4]: SoT=009 ммоб. Выбранное значение подач корректируют с учетом поправочных коэффициентов которые выбирают по карте 8[4] для измененных условий в зависимости от:
механических свойств обрабатываемого материала KSм=09;
схемы установки заготовки KSу=08;
радиуса вершины KSr=10;
квалитета обрабатываемой детали KSк=08;
кинематического угла в плане Kφк=10;
Окончательно значение подачи для черновой стадии обработки определяют по формуле:
Скорость резания для чистового точения выбирают по карте 22[4]. Чистовой стадии обработки соответствует скорость резания vт=370 ммин. По этой же карте скорости резания корректируют с учетом инструментального материала Кvи=1.
Коэффициенты на скорость резания для чистовой стадии обработки для измененных условий выбирают также по карте 23 [4].
Сверлить отверстие выдерживая размеры 395 Расточить коническое отверстие выдерживая размеры 15º 418; расточить коническое отверстие выдерживая 120º; Зенкеровать конические отверстия выдерживая размеры 42(±0089) и l =30(-052)
Глубину резания на переходе зенкерование определяют по карте 45 [4] и корректируют с учётом последовательности переходов маршрута. Для данного случая глубина резания при чистовом зенкеровании t=048мм
Предшествующим переходом перед чистовым зенкерованием был переход растачивание. Для этого случая поправочный коэффициент Кti=10. Окончательно глубина резания для перехода зенкерование t=048·10=048мм. Аналогично определяют глубину резания для перехода растачивание черновое t=07.
Глубина резания для перехода сверление принимается равной половине диаметра сверла.
)Расчет диаметров обрабатываемого отверстия по переходам маршрута и выбор инструмента:
Диаметры обрабатываемого отверстия по переходам находят по формуле:
С учётом раннее определённых глубин резания диаметры отверстия находят для:
Зенкерования чистового D=42мм;
Растачивания чернового D=42-2×048=41мм
Сверления D=41-2×07=396
Сверло выбирают по ГОСТ 10903-77: d=395мм
)Выбор подачи скорости мощности и осевой силы резания осуществляют по картам 46 51[4] для ближайшего большего табличного значения диаметра инструмента.
В данном случае значения этих величин выбирают для переходов:
1) Сверление при диаметре 395мм ближайшее большее табличное значение Vт=160ммин; Nт=28кВт; Pт=15298Н.
Подачу корректируют по формуле:
Коэффициент КSм выбирают по карте 53[4].
Скорость корректируют по формуле:
v=vт·Кvм·Кvз·Кvж·Кvт·Кvw·Кvи·Кv
v=16·074·1·1·27·1·1·11·1=35 ммин.
Скорректированную частоту вращения шпинделя рассчитывают по формуле:
Скорость резания определяют по формуле:
Формулы для корректировки мощности резания и осевой силы:
2) Зенкерования чистового по карте 51[4]: Sот=024ммоб; Vт=150ммин; Nт=052кВт; Pт=117Н.
S0=024·074=018 ммоб.
v=15·074·1·1·27·1·1·11·1=33ммин
3) Растачивания чернового по карте 9[4]: Sот=036 ммоб. Выбранное значение подачи корректируют с учётом поправочных коэффициентов которые выбирают по карте 11[4]:
КSм=08; КSп=10; КS КSφ=10; КSD=062; КSи=10
Окончательно значение подачи определяют по формуле:
Скорость резания определяют по карте 21[4]:
vт=187ммин. По карте 21[4] выбирают поправочные коэффициенты в зависимости от инструментального материала Кvи=10. По карте 23 [4] выбирают поправочные коэффициенты.
vS=016·1000=160 мммин.
Для получения размера детали по 12 квалитету точности и шероховатости Ra=32 необходимо выполнить получистовое точение.
Выбор минимально необходимой глубины резания для получистового точения осуществляется по карте 2 [4].Глубина резания для получения 12 квалитета составляет t=15мм назначаем глубину резания t=1мм.
Обработку проводим пластиной из твердого сплава СР200. Угол в плане составит φ=45.
rв= 10 мм – радиус вершины резца.
Выбор скорости резания:
Частоту вращения шпинделя определяют по формуле:
Для получистового точения:
Для получения размера детали 80h9 Ra 32 необходимо вести обработку в одну стадию: чистовое точение.
Для чистовой стадии обработки подачу выбирают по карте 6[4]: SoT=008 ммоб. Выбранное значение подач корректируют с учетом поправочных коэффициентов которые выбирают по карте 8[4] для измененных условий в зависимости от:
Сверлить отверстие выдерживая размеры 34 и Зенкеровать отверстие выдерживая размер 44; Развернуть отверстие выдерживая размер 5Н11.
Глубину резания на переходе развёртывания определяют по карте 45 [4] и корректируют с учётом последовательности переходов маршрута. Для данного случая глубина резания при черновом развёртывании t=018мм
Предшествующим переходом перед черновым развёртыванием был переход зенкерование. Для этого случая поправочный коэффициент Кti=16. Окончательно глубина резания для перехода развёртывания t=018·16=03мм. Аналогично определяют глубину резания для перехода зенкерование t=05.
С учётом раннее определённых глубин резания диаметры отверстия находят для: Развёртывания чернового D=5мм;
Зенкерование получистовое D=5-2×029=44мм
Сверления D=44-2×05=34
Сверло выбирают: d=34мм
1) Сверление при диаметре 34мм ближайшее большее табличное значение Vт=290ммин; Nт=013 кВт; Pт=460Н.
v=16·074·1·1·27·1·1·11·1=64 ммин.
vS=005·6000=300мммин.
2) Зенкерования по карте 51[4]: Sот=019ммоб; Vт=410ммин; Nт=11кВт; Pт=955Н.
S0=019·074=014 ммоб.
v=15·074·1·1·27·1·1·11·1=90ммин
vS=014·6500=910мммин.
3) Развёртывания по карте 48[4]: Sот=071ммоб; Vт=110ммин; Nт=085кВт; Pт=828Н.
S0=071·074=053 ммоб.
v=11·074·1·1·27·1·1·11·1=24ммин
vS=071·1500=1065мммин.
10. Расчет норм времени
Техническая норма времени на обработку заготовки является одной из основных параметров для расчёта стоимости изготовляемой детали числа производственного оборудования заработной платы рабочих и планирования производства.
Техническую норму времени определяют на основе технических возможностей технологической оснастки режущего инструмента станочного оборудования и правильной организации рабочего места.
Норма времени является одним из основных факторов для оценки совершенства технологического процесса и выбора наиболее прогрессивного варианта обработки заготовки.
В условиях среднесерийного производства штучное время затрачиваемое на операцию механической обработки определяется расчетно-аналитическим методом:
где - основное технологическое (машинное) время на операцию мин;
- вспомогательное время (время затраченное: на поворот стола на перемещение шпинделя и т.д.) на операцию мин;
- время организационного и технического обслуживания рабочего места в течение смены мин;
- время перерывов на личные потребности мин;
- оперативное время мин;
Тобс и Тотд устанавливают по нормативам и в сумме составляют 16% от оперативного времени.
Основное время затраченное на операцию складывается из основного времени каждого перехода этой операции:
- время выполнения одной операции мин
где - расчетная длина рабочего хода;
у – величина врезания и перебега мм;
n – частота вращения шпинделя.
Вспомогательное время определяется по формуле (2) [7 с.4]:
где ty – вспомогательное время на установку крепление и открепление детали мин
tвсп - вспомогательное время связанное с выполнением операции мин
tи - вспомогательное неперекрываемое время на измерение мин (3% от ).
Штучно-калькуляционное время рассчитывается по формуле (4) [7 с.4]:
где - подготовительно заключительное время мин;
- число деталей в партии шт.
Подготовительно заключительное время определяется (5) [7 с.4]:
где tорг – время организационной подготовки мин
tнал – время наладки станка инструмента и приспособлений мин
tпр – время на пробный проход по программе мин (20 % от ).
Рассчитаем нормы времени токарной операции.
Операция 015. Токарная с ЧПУ.
Переход 1: Подрезать торец выдерживая размеры l =47(-062) l =120(-087) .
Основное время подрезания чистового мин определяем по формуле:
Основное время подрезания получистового мин:
Переход 2: Центрование отверстия ( на глубину 5 мм у = 3 мм.)
Основное время сверления мин:
Переход 3: Сверлить отверстие выдерживая размеры 32
Переход 4: Расточить коническое отверстие выдерживая размеры 15º 418; расточить коническое отверстие выдерживая 120º;
Основное время растачивания мин:
Переход 5: Зенкеровать конические отверстия выдерживая размеры 42(±0089) и l =30(-052)
Основное время зенкерования мин:
Переход 6: Точить поверхность выдерживая размеры 52 1х45º
Основное время точения мин:
Переход 7: Точить поверхность выдерживая размер 80h9
Основное время на операцию мин:
То =083+054+01+054+029+078+024+107=404.
Вспомогательное время на операцию мин табл. 235 [7 с.9]:
Оперативное время мин:
Подготовительно-заключительное время мин табл. 6 [7 с.13]:
Штучно-калькуляционное время мин:
Операция 030. Сверлильная с ЧПУ.
Переход 1: Сверлить отверстие выдерживая размеры 34 и l =18.
Переход 2: Зенкеровать отверстие выдерживая размер 44.
Переход 3: Развернуть отверстие выдерживая размер 5Н11.
То =019+006+007=032.
11. Расчет точности операции
Расчет точности выполняем на переход одной из операций разработанного технологического процесса на котором обеспечивается 9 квалитет точности.
Величина суммарной погрешности обработки не должна превышать величины допуска на получаемый размер Тдет:
Получаемый размер 80Н9 Тдет = 74 мкм.
Величина суммарной погрешности обработки для цилиндрической поверхности рассчитывается по формуле (2.36) [6 с.34]:
где Δу – погрешность от изменения величины упругих деформаций технологической системы под влиянием нестабильности нагрузок (сил резания сил инерции и т.п.) действующих в системе переменной жесткости;
Δн – погрешность наладки технологической системы на выдерживаемый размер с учетом точностной характеристики применяемого метода наладки;
ΔИ – погрешность в результате размерного износа режущего инструмента;
ΔСТ – суммарные погрешности станка влияющие на выдерживаемый параметр с учетом износа станка за период эксплуатации;
ΔТ – суммарные погрешности упругих объемных и контактных деформаций элементов технологической системы вследствие их нагрева при резании трения подвижных элементов системы изменения температуры в цехе;
K – коэффициент относительного рассеяния характеризующий суммарную погрешность для заданной гарантированной надежности;
i – индекс элементарной погрешности.
Погрешность обработки возникающая в результате колебаний упругих деформаций технологической системы под влиянием нестабильности сил резания действующих в системе переменной жесткости определяется по формуле (2.38) [6 с.36]:
Pymax и Pymin – максимальное и минимальное значение составляющей силы резания.
Wma Wm Pyma Pymin = 11 кН табл.
Суммарные погрешности станка влияющие на выдерживаемый параметр с учетом износа станка за период эксплуатации принимаем мкм:
Погрешность в результате влияния температурных деформаций принимаем по табл. 30 [8 с.118] ºС:
Суммарная погрешность обработки мкм:
Суммарная погрешность обработки не превышает величины допуска на получаемый размер следовательно требуемая точность параметра достигается.
КОНСТРУКТОРСКАЯ ЧАСТЬ
1. Расчет и проектирование специального приспособления
1.1. Техническое задание
Необходимо спроектировать приспособление к Сверлильно-фрезерный станок с ЧПУ Rapimill 700 для механической обработки сопла.
Исходные данные: годовой объем выпуска деталей –1500 шт.; материал – сталь 38Х2МЮА.
В данном приспособлении производится сверление отверстия d=34мм
Принятый режим для сверления: S=005 ммоб; V=64 ммин.
Приспособление должно обеспечивать необходимую точность обработки детали.
1.2. Выбор и обоснование схемы приспособления
Для установки заготовки в приспособление за базы следует принять поверхность 1 и внутреннюю резьбу 2(рис. 2.1). Базирование производится плоскостью (установочная база; опорные точки 1 2 3) внутренней поверхностью (двойная опорная база; опорные точки 4 5).
Рис.2.1. Эскиз. Операция 030
1.3. Расчет приспособления на точность
Расчет заключается в определении точности изготовления приспособления по принятым параметрам.
На точность обработки влияет ряд технологических факторов вызывающих общую погрешность обработки 0 которая не должна превышать допуск выполняемого размера при обработки заготовки:
Допустимая погрешность изготовления приспособления рассчитывается по формуле (2.47) [6 с.39]:
где - допуск выполняемого размера заготовки Т = 018 мм;
- коэффициент учитывающий отклонение рассеяния значений составляющих величин от закона нормального распределения ;
- коэффициент учитывающий уменьшение предельного значения б ;
- коэффициент учитывающий долю погрешности обработки в суммарной погрешности ;
- погрешность базирования заготовки в приспособлении;
з - погрешность закрепления заготовки в приспособлении;
- погрешность установки приспособления на станке;
- погрешность износа установочных элементов приспособления;
- погрешность от перекоса инструмента;
- экономическая точность обработки.
Расчетный параметр – размер 34 IT13
Погрешность базирования = 002 мм.
Погрешность установки приспособления на станке рассчитываем по формуле:
где - длина обрабатываемой детали = 18 мм;
- максимальный зазор между шпонками приспособления и пазом стола станка S = 0017 мм;
- расстояние между шпонками l = 157мм.
Определим погрешность установки мм:
мм - для закрепления в приспособлении с винтовыми зажимами;
- для сверления по 13 квалитету табл. П6 [11 с.211];
- т.к. отсутствуют направляющие элементы для инструмента.
Определим допустимую погрешность изготовления приспособления мм:
Сравним рассчитанную допустимую погрешность приспособления с допуском на выполняемый размер: - следовательно точность изготовления приспособления позволяет обработать деталь с заданной точностью.
2. Проектирование специального режущего инструмента
Проектируемый резец со сменными пластинами предназначен для подрезания торца 80.
Задача проектирования подрезных резцов сводится к выбору следующих конструктивных элементов:
главного угла в плане ;
вспомогательного угла в плане 1;
радиуса закругления режущей кромки .
Для более долгого использования резца режущая пластина выполнена из сплава SP200 толщина которой 476 мм. Материал опорной пластины – ВК15 по ГОСТ 3882-74 с толщиной 318 мм. Крепежная часть резца изготовлена из стали 45Х ГОСТ 4543-71. Пластинки крепятся к корпусу резца с помощью зажимного механизма.
Для твердосплавного резца важно знать правильное значение заднего угла . Он влияет на интенсивность износа резца на прочность режущего клина и на условия отвода тепла из зоны резания. По сравнению с резцами из быстрорежущей стали угол примерно в 2 раза меньше: =6 8º принимаем = 6.
Передний угол зависит от механических свойств материала инструмента и влияет на износостойкость чем больше тем больше износостойкость. С другой стороны угол влияет на силу резания чем больше угол тем меньше сила резания. Принимаем = 5º.
В условиях малой жесткости СПИД главный угол в плане выбирается не менее 60º. В данном случае = 90º.
Вспомогательный угол 1 определяет шероховатость обработанной поверхности поэтому 1 берут в пределах 0º 10º принимаем 1 = 5º.
С целью повышения прочности режущей части резца предусматривается также радиус скругления его вершины в плане: r = 08 мм.
При подаче 016ммоб и глубине резания 15мм
Изгибающий момент равен: Py
Расчет производится с использованием значения допускаемого напряжения изгиба для стали 45Х с термообработкой нормализацией [И]=240 МПа. Необходимый минимальный диаметр будет равен:
Расчет на прочность выдержан.
Расчет технологической себестоимости
Технологической себестоимостью детали называется та часть ее полной себестоимости элементы которой существенно изменяются для различных вариантов технологического процесса.
Расчёт технологической себестоимости выполнения операции механической обработки выполняется по формуле (6.21)[5 с.168]:
Элементы входящие в структуру определяем методом прямого калькулирования.
Заработная плата станочника с учётом всех видов доплат и начислений руб (6.23) [5 с.169]:
где - норматив часовой заработной платы станочника соответствующего разряда рубч. =40 рубч [5];
- масштабно-ценовой коэффициент =8 [5];
- коэффициент учитывающий оплату основного рабочего при многостаночном обслуживании =1 [5];
- штучно-калькуляционное время на операцию =113 мин.
Заработная плата наладчика учётом всех видов доплат и начислений руб (6.24) [5 с.170]:
где - норматив часовой заработной платы станочника соответствующего разряда рубч.
m – число смен работы станка;
- число станков обслуживаемых наладчиком в смену;
- действительный годовой фонд времени работы оборудования =3600 ч.
Амортизационные отчисления от стоимости оборудования руб (6.25) [5 с.170]:
где - общая норма амортизационных отчислений %. =75%[5];
Ф – стоимость оборудования руб.
С учётом затрат на трансформирование и монтаж станка стоимость оборудования:
где Ц – оптовая цена на оборудование Ц=1777500 руб.;
Ф=11223000000=3366000 руб.
Амортизационные отчисления от стоимости технологического оснащения приходящиеся на одну деталь при расчётном сроке службы оснастки 2 года руб. (6.26) [5 с.171]:
где - стоимость технологического оснащения руб. =2000 руб. [5].
- годовая программа выпуска деталей.
Затраты на ремонт и обслуживание оборудования руб. (6.27) [5 с.171]:
где - нормативы годовых затрат на ремонт соответственно механической и электрической частей оборудования руб.год
=371 руб.год =79 руб.год [5];
- категория сложности ремонта соответственно механической и электрической частей оборудования =14 =26 [5];
- коэффициент зависящий от класса точности оборудования (для оборудования нормальной точности =1).
Затраты на инструмент отнесённые к одной детали руб. (6.28) [5 с.171]:
где 14 – коэффициент учитывающий затраты на переточку инструмента;
- цена единицы инструмента руб.;
- коэффициент машинного времени;
- срок службы инструмента до полного износа мин. = 60 мин.
Затраты на силовую электроэнергию руб. (6.29) [5 с.171]:
где - цена электроэнергии (принимаем равной 084 руб. за 1кВтч);
- установленная мощность электродвигателя станка =15 кВт;
- общий коэффициент загрузки электродвигателей
Затраты на содержание и амортизацию производственных площадей руб. (6.30) [5 с.172]:
где - норматив издержек приходящихся на 1 производственной площади руб (10 руб. );
- удельная площадь приходящаяся на станок и равная габаритной площади станка умноженной на коэффициент учитывающий добавочную площадь =137920=276 .
- коэффициент учитывающий площадь для систем управления станков с ЧПУ (принимаем 20).
Затраты на подготовку и эксплуатацию управляющих программ руб. (6.31) [5 с.172]:
где - стоимость программы руб. =1050 руб.;
- коэффициент учитывающий потребность в восстановлении программоносителя =11;
- срок выпуска данной детали год.
Определим технологическую себестоимость руб.:
Вычислим минимум приведенных затрат по формуле:
Где С - технологическая себестоимость изготовления детали руб.;
ЕН – нормативный коэффициент эффективности капитальных вложений (ЕН = 012);
Ко – удельные капитальные вложения отнесенные к единице продукции руб. (6.34) [5 с.173]:
Минимум приведенных затрат руб.:
В ходе выполнения курсового проекта была изучена конструкция и служебное назначение кронштейна проведён анализ технологичности детали качественной и количественной. Выбран способ получения заготовки - прокат проведен расчет себестоимости заготовки и выбран наиболее экономичный разработан технологический маршрут механической обработки сопла. Был произведен расчет припусков на самые точные по требованиям поверхности а также режимов резания норм времени и ожидаемая погрешность обработки.
Спроектирован специальный режущий инструмент а также была выбрана и рассчитана конструкция специального станочного приспособления произведен расчет на точность обработки детали.
В экономической части проекта рассчитывается себестоимость технологической операции.
БИБЛИОГРАФИЧЕСКИЙ СПИСОК
Горбацевич А.Ф. Курсовое проектирование по технологии машиностроения.- Минск 1975 г. 288с
Гузеев В.И. Батуев В.А Сурков И.В. Режимы резания для токарных и сверлильно-фрезерно-расточных станков с числовым программным управлением: Справочник Под ред. В.И. Гузеева. М.: Машиностроение 2005. 368с.
Расчет припусков и межпереходных размеров в машиностроении: Учеб. пособ. для машиностроит. спец. вузов Я.М. Радкевич В.А. Тимирязев А.Г. Схиртладзе М.С. Островский; под ред. В.А. Тимирязева. – М.: Высш. шк. 2004. – 272 с.
Сборник задач и примеров по резанию металлов и режущему инструменту. Нефедов Н.А. и Осипов К.А. М. «Машиностроение» 1969 336 с.
Технология машиностроения: Сборник задач и упражнений: Учеб. пособие В.И. Аверченков и др. Под общ. ред. В.И. Аверченкова – М.: ИНФРА-М 2005. – 288с.
Технология машиностроения: методические указания к выполнению курсового проекта для студентов специальности 151001 «Технология машиностроения» всех форм обучения Н.А. Амельченко В.Д. Утенков Л.С. Добрынина; СибГАУ. – Красноярск 2007. – 92 с.
Сборник нормативов времени на работы выполняемые на станках «Обрабатывающий центр».
Справочник технолога-машиностроителя. В 2-х т. Т. 1 Под ред. А.М. Дальского А.Г. Косиловой Р.К. Мещерякова А.Г. Суслова. – 5-е изд. исправл. – М.: Машиностроение – 1 2003 г. 912 с. ил.
Справочник технолога-машиностроителя. В 2-х т. Т. 2 Под ред. А.М. Дальского А.Г. Косиловой Р.К. Мещерякова А.Г. Суслова. – 5-е изд. исправл. – М.: Машиностроение – 1 2003 г. 944 с. ил.
Станочные приспособения: Справочник. В 2-х т. Ред. совет: Б.Н. Вардашкин (пред) и др. – М.: Машиностроение 1984. – Т1Поо ред. Б.Н. Вардашкина А.А. Шатилова 1984. 592 с. ил.
Проектирование и расчет приспособлений: Учеб. пособие для студентов вузов машиностроительных спец. – Мн.: Выш. шк. 1986. – 238 с.: ил.
Обработка металлов резанием: Справочник технолога [Текст] А.А. Панов В.В. Аникин Н.Г. Бойм и др.; Под общ. ред. А.А. Панова. 2-е изд. перераб. и доп. - М.: Машиностроение 2004. – 784 с.: ил.