Козловой кран грузоподъемностью 50/10 тонн





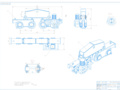
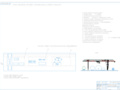

- Добавлен: 25.10.2022
- Размер: 12 MB
- Закачек: 1
Описание
Состав проекта
![]() |
![]() ![]() |
![]() ![]() ![]() ![]() |
![]() ![]() ![]() |
![]() |
![]() ![]() |
![]() ![]() ![]() ![]() |
![]() ![]() |
![]() ![]() ![]() |
![]() ![]() ![]() |
![]() ![]() |
![]() ![]() |
![]() |
![]() ![]() |
![]() ![]() ![]() ![]() |
![]() ![]() |
![]() ![]() ![]() ![]() |
![]() ![]() |
![]() ![]() |
![]() |
![]() ![]() |
![]() ![]() |
![]() |
![]() ![]() |
![]() ![]() ![]() ![]() |
Дополнительная информация
Электросхема тележки.dwg

Напряжение втягивания
Схема электрическая принципиальная
Контакт реле размыкается при токе равном 48А
Регулировочные параметры реле (при холодных катушках)
Раздел 3.doc
ПРИВОДА МЕХАНИЗМА ПЕРЕДВИЖЕНИЯ ТЕЛЕЖКИ
Наибольшее распространение на кранах получил привод с асинхронными двигателями с фазным ротором и ступенчатым регулированием угловой скорости путем изменения сопротивления в цепи ротора. Такой привод достаточно прост надежен допускает большое число включений в час и применяется при средних и больших мощностях. С помощью резисторов в цепи ротора можно в широких пределах изменять момент при пуске получать желаемые ускорения и плавность пуска уменьшать токи и потери энергии в двигателе при переходных процессах а также получать пониженные угловые скорости.
Комплектные электроприводы охватывают все крановые асинхронные двигатели с фазным ротором при управлении от магнитных контроллеров типа ТСД. Эти электроприводы выпускают только для механизмов общепромышленного исполнения.
Электроприводы с магнитными контроллерами имеют индивидуальную защиту. Контроллеры выпускаются двух типов соответственно для возбуждаемых и невозбуждаемых электродвигателей. Первые из этих контроллеров применяют для двигателей напряжение на кольцах ротора которых не превосходит 300 В при напряжении сети 380 В; вторые – при напряжении ротора более 300 В. Применение режима динамического торможения самовозбуждением позволяет получить устойчивые посадочные скорости при диапазоне регулирования 1 : 8; благодаря импульсно-ключевому включению на первом положении подъема обеспечивается регулирование диапазона скорости до 1 : 7.
Обладая повышенными регулировочными и энергетическими свойствами рассматриваемые электроприводы позволяют значительно улучшить использование двигателей и повысить надежность работы контакторной аппаратуры благодаря снижению числа включений приводов при осуществлении доводочных операций а также снизить нагрузки на механические передачи при натягивании грузовых канатов.
Силовая часть схемы управления двигателем механизма передвижения тележки изображена на рис. 4.1.
Цепь управления отображена на рис. 4.2. Реверсирование осуществляется контакторами КMl и КМ2. Включение тормозного электромагнита осуществляет КМ3. Контактор КМ4 осуществляет двойной разрыв силовой цепи.
Скорость регулируется контакторами КМ7 КМ10. Механические характеристики его приведены на рис.4.3.
Рис.4.1. Механические характеристики электропривода системы
управления с магнитным контроллером типа ТСД
Контактор КМ7 обеспечивает характеристику 2 КМ8 характеристику 3 КМ9 характеристику 4а КМ10 характеристику 4. Реле времени КТ1 обеспечивает переход с характеристики 3 на характеристику 4а КТ2 переход с характеристики 4а на характеристику 4 обеспечивая автоматический разгон на дух последних ступенях переключения.
Диодно-резисторный коммутатор работает в импульсно-ключевом режиме. Узел обратной связи по ЭДС ротора получает питание от зажимов обмотки ротора. В цепи выпрямителя включены стабилитрон VD17 и управляющая часть оптрона VS8. Выходная часть оптрона включена в управляющие цепи тиристоров блока VS. По уставке стабилитрона осуществляется автоматическое поддержание роторного напряжения независимо от нагрузки.
Максимальная защита двигателя осуществляется с помощью реле тока КА1 нулевая защита реле KV1. Реле KV2 осуществляет включение блоков бездуговой коммутации.
Грузовая тележка.dwg

Высота подъема груза главного подъема
Высота вспомогательного подъема
Скорость передвижения тележки
Скорость подъема груза
Группа режима работы М4
Электродвигатель механизма:
ВКР 1806.02.00.000 СБ
грузоподъемность 5010тонн
Текстовая часть работы.docx
Федеральное государственное бюджетное
образовательное учреждение высшего образования
«Тульский государственный университет»
Кафедра «Подъемно-транспортные машины и оборудование»
Направление 23.03.02
Наземные транспортно-технологические комплексы
Механизация участка сборки тепломеханического оборудования с разработкой механизмов козлового крана грузоподъемностью 5010 тонн.
Обзор конструкций козловых кранов5
Механизация укрупнительно- сборочного участка тепломеханического оборудования.8
РАСЧЕТ МЕХАНИЗМА ПЕРЕДВИЖЕНИЯ КРАНА12
1 Выбор типа привода12
2 Определение числа ходовых колес12
3 Кинематическая схема механизма12
4 Определение массы крана13
5 Выбор ходовых колес13
6 Определение сопротивления передвижению крана14
7 Определение мощности двигателя15
8 Определение передаточного числа привода16
9 Выбор мотор-редуктора17
10 Выбор муфты тихоходного вала17
11 Определение пусковых характеристик механизма18
12 определение тормозных характеристик привода23
13 Проверка пути торможения25
РАСЧЕТ МЕХАНИЗМА ПЕРЕДВИЖЕНИЯ ТЕЛЕЖКИ27
1 Выбор типа привода27
2 Определение числа ходовых колес27
3 Кинематическая схема механизма27
4 Определение массы крана27
5 Выбор ходовых колес28
6 Определение сопротивления передвижению крана29
7 Определение мощности двигателя30
8 Определение передаточного числа привода31
9 Выбор мотор-редуктора32
10 Выбор муфты тихоходного вала32
11 Определение пусковых характеристик механизма33
12 Определение тормозных характеристик привода38
13 Проверка пути торможения40
РАСЧЕТ МЕХАНИЗМА ПОДЪЕМА42
1 Определение кратности полиспаста42
2 Определение усилия в канате набегающем на барабан43
4 Определение требуемого диаметра блоков и барабана45
5 Выбор крюковой подвески45
6 Определение размеров барабана45
8 Определение передаточного числа привода50
10 Выбор муфты быстроходного вала51
11 Выбор муфты тихоходного вала53
12 Определение пусковых характеристик механизма54
14 Определение тормозных характеристик механизма59
15 Проверка двигателя на нагрев61
РАЗРАБОТКА ЭЛЕКТРИЧЕСКОЙ СХЕМЫ ПРИВОДА МЕХАНИЗМА ПЕРЕДВИЖЕНИЯ ТЕЛЕЖКИ66
Расчет САПР APM Winmachine.70
Подъемно-транспортные машины (ПТМ) -механизмы являющиеся основными средствами механизации и автоматизации погрузочно-разгрузочных и складских работ.
Целью данной работы является механизации участка сборки тепломеханического оборудования с разработкой механизмов козлового крана грузоподъемностью 5010 тонн.
Задачи которые необходимо выполнить для достижения поставленной цели :
-обоснование выбора козлового крана
-произвести расчет механизма передвижения крана
- произвести расчет передвижения грузовой тележки
- произвести расчет механизма подъема грузовой тележки
-разработать электрическую схему принципиальную
-произвести расчет элемента крана в САПР APM Win Machine
Проведенные расчеты помогут избежать выхода оборудования из строя.
Обзор конструкций козловых кранов
Назначение козловых кранов
Козловые краны — это грузоподъёмные механизмы получившие широкое применение в различных сферах в том числе при обслуживании складов контейнерных площадок промышленных предприятий монтаже сборных зданий и т. д. Основной характерной чертой козлового крана является наличие четырёх опорных точек опирающихся на крановые пути. Технические параметры: грузоподъемность – от 5 до 1600 т высота подъёма груза – от 3 до 100 м пролётов – от 20 до 130 м.
Виды козловых кранов
Краны козловые общего назначения (крюковые) предназначены как для проведения монтажных операций так и для работы на различных складских площадках.
Краны козловые монтажные используются на судостроительных верфях и судоремонтных предприятиях при секционном монтаже сборочных работах а также для монтажа оборудования и перемещения штучных грузов.
Пролетное строение козлового крана может быть выполнено как в виде коробчатой так и в виде ферменной металлоконструкции.
Рис.1.1. Козловой кран общего назначения
Краны козловые грейферные предназначены для перегрузки сыпучих и навалочных грузов при помощи специального грейферного захватного устройства. В зависимости от специфики грузоподъёмных операций козловой грейферный кран может оснащаться канатным ковшовым грейфером съёмным электромеханическим или электрогидравлическим грейфером.
Козловые грейферные краны широко применяются в угольной и металлургической промышленности в частности в шихтовых отделениях и на шлаковых дворах мартеновских цехов а также на предприятиях по переработке лома чёрных и цветных металлов.
При необходимости увеличения площади разгрузочной площадки например при разгрузке судов или автотранспорта пролётное строение козлового крана дополняется одной или двумя консолями.
Козловые грейферные краны оснащаются специальной грейферной лебёдкой которая наряду с механизмом подъёма имеет механизм замыкания грейфера. При этом возможна запасовка грейфера с раскрытием вдоль или поперёк пролёта моста.
Рис.1.2. Козловой грейферный кран
Козловые магнитные краны предназначены для выполнения основных операций при погрузо-разгрузочных и складских работах на открытых площадках предприятий металлургической промышленности крупных базах металла а также на заводах по переработки лома. С помощью перманентного или электрического магнита который навешивается на крюк или на траверсу козловой кран позволяет захватывать и перемещать листовой и профильный прокат заготовки слитки металлолом стружку скрап и другие ферромагнитные материалы. При этом при снятом электромагните магнитные краны могут работать со штучными грузами в крюковом режиме.
Рис.1.3. Магнитный козловой кран
Полукозловые краны — грузоподъемники несущая конструкция которых одной стороной опирается на две опоры перемещающихся по рельсовому пути а другая сторона двигается по путям закрепленных на консолях зданий или на специальных опорах. Кран полукозловой в зависимости от специфики выполняемой работы отличается своими техническими характеристиками — грузоподъемностью (т: 32; 5; 8; 10) рабочей зоной пролета несущего элемента конструкции (м: 125 - 320) высотой подъема грузозахватывающих устройств (крюк грейфер магнит)
Рис.1.4.Кран полукозловой
Механизация укрупнительно- сборочного участка тепломеханического оборудования.
Рис.2.1. Схема стройбазы
На данном рисунке изображена схема стройбазы тепловой электростанции средней мощности . Стройбаза включает в себя участки : 1-контора управления строительством;2- бытовой корпус;3- столовая; 4- объединенное здание механической и арматурной мастерских и материального склада; 5- открытая площадка центрального материального склада;6- объединенное здание тепломонтажной и электромонтажной мастерских и склада оборудования; 7- бетонорастворное хозяйство;8-временная котельная;9-объединенное здание мастерских и складов обмуровки и теплоизоляции; 10- тепляк для производства сварочных работ; 11-участок управления гидротехническим строительством;; 12- участок управления строительной механизации;; 13- автохозяйство; 14- склад горючесмазочных материалов; 15- плотнично-опалубочная мастерская; 16- кислородный завод;17- площадка строительных конструкций; 18-укрупнительно-сборочная площадка тепломеханического оборудования.
Пунктирными линиями на рисунке обозначено движение заготовок по участкам базы а сплошной линией движение вне производственных и других участков. Сборочные единицы приходят на базу по железным путям или автотранспортом.
Укрупнительно-сборочная площадка представляет собой участок занимающий около 50% всей площади стройбазы так как на ней осуществляется хранение укрупнение тепломеханического оборудования и отправление его в зону окончательного монтажа.
Рис.2.2. Участок сборки
-место отведенное специально для хранения укрупнения и отправки к месту монтажа водогрейных котлов.
Рис.2.3. Водогрейный котел
Водогрейные котлы предназначаются для подогрева воды поступающей на отопление вентиляцию и горячее водоснабжение.
-место сборки паровых турбин.
Рис.2.4 Паровая турбина
Паровая турбина – двигатель в котором энергия пара преобразуется в механическую работу.
-место сборки регенеративных подогревателей.
Рис.2.5.Регенеративный подогреватель
Применение регенеративного подогревателя воды на ТЭЦ способствует экономии тепла повышая выработку электроэнергии на тепловом потреблении и уменьшая потери тепла в конденсаторе турбин.
Козловой кран на участке укрупнения и сборки обеспечивает приемку всех строительных конструкций сортировку погрузку их для подачи к месту сборки или на объект; сборку в монтажные блоки и погрузку блоков для подачи в монтажную зону. Выбор козлового крана грузоподъемностью 50 тонн обуславливается необходимостью перемещения укрупненных частей теплоэлектростанции а пролет 42м и ход тележки 62 м позволяет расширить площадку уменьшить ее длину и увеличить коэффициент использования занятой площади (уменьшается влияние железнодорожного проезда).
Паровая турбина доставляется на базу в полусобранном состоянии так как сборка ротора невозможна без специальных стендов для проведения испытаний . Козловой кран перемещает сборочные единицы турбины :верхнюю часть ротор и нижнюю часть из зоны прибытия в зону укрупнения .Укрупнение заключается в присоединении ротора к нижней и верхней частям турбины. Если время монтажа еще не подошло то турбина может находиться на участке сборки и укрупнения .Нет необходимости перегружать металлоконструкцию в складское помещение так как участком временного хранения может быть зона укрупнения и сборки.
РАСЧЕТ МЕХАНИЗМА ПЕРЕДВИЖЕНИЯ КРАНА
В качестве исходных данных для расчета механизма передвижения используем следующие данные:
- тип крана – козловой;
- грузоподъемность Q = 50 т;
- скорость передвижения крана Vпер. = 062 мс;
- пролет крана L = 42 м;
- режим работы крана М4 (средний);
- режим работы механизма М4 (средний);
- продолжительность включения механизма передвижения ПВ = 25%.
1 Выбор типа привода
В соответствии с невозможностью установить совмещенный привод принимаем для козлового крана – раздельный привод.
2 Определение числа ходовых колес
Для данного козлового крана грузоподъемностью 50 тонн – принимаем 16 ходовых колес.
3 Кинематическая схема механизма
Рис. 3.1 Схема механизма передвижения крана
4 Определение массы крана
Масса козлового крана 138127 т.
5 Выбор ходовых колес
Выбираем в зависимости от грузоподъемности крана его скорости передвижения и нагрузке на одно ходовое колесо согласно [1 с. 296 табл. III.2.3].
Наибольшая допускаемая нагрузка на колесо определяется по формуле:
где nк – количество принятых ходовых колес шт;
– коэффициент неравномерности нагрузки.
Принимаем для среднего режима работы двухребордное ходовое колесо диаметром Dк = 500 мм = 05 м.
Принимаем коэффициент трения качения ходового колеса по рельсам () и коэффициент трения в подшипниках качения колеса (f) в соответствии с рекомендациями [1 с. 33]:
- f = 0015 – (для шариковых и роликовых подшипников).
Диаметр цапфы вала ходового колеса определяется по формуле:
Принимаем коэффициент учитывающий дополнительные сопротивления от трения реборд ходовых колес о рельс согласно [1 с. 33]:
- kр =20 .25 – для подшипников качения.
- kр =12 .18 – для подшипников скольжения.
6 Определение сопротивления передвижению крана
где Fтр. – сопротивление трения:
Fукл. – сопротивление от уклона:
sin α – уклон пути принимаем для козлового крана: sin α = 0003
в соответствии с рекомендациями [1 c. 68 табл. 2.10];
Fв – сопротивление от ветровой нагрузки.
Ak Aг– площади поверхностей крана и груза (рассчитанные значения площади крана – 504 м2 груза выбираем по таблице гп -25 м2)
с - коэф. аэродинамической силы – (для крана -19 для груза – 12);
k – коэф. учитывающий высоту конструкции -13;
n – коэф. перегрузки 1;
7 Определение мощности двигателя
Статическая мощность двигателя механизма передвижения определяется по формуле:
где Fпер. – сопротивление передвижению крана Н;
Vпер. – скорость передвижения крана мс;
– КПД механизма передвижения крана принимаем согласно
[1 c. 23 табл. 1.18] для подшипников качения = 085.
Так как у нас используется в конструкции 6 двигателей тогда найденная необходимая мощность делится поровну на каждый из них.
Номинальную мощность одного двигателя механизма передвижения необходимо принимать равной или несколько большей статической мощности.
8 Определение передаточного числа привода
Частота вращения ходового колеса определяется по формуле:
где Vпер. – скорость передвижения крана мс;
Dк – диаметр ходового колеса м.
Требуемое передаточное число привода определяем по формуле:
9 Выбор мотор-редуктора
Выбираем мотор-редуктор МЧ-160.
-частота вращения 970
10 Выбор муфты тихоходного вала
Момент статических сопротивлений на колесе согласно [1 c. 23]:
Принимаем зубчатую муфту:
– крутящий момент Tмуф. =11800 Н·м;
– допускаемая частота вращения муфты nmax = 2500 мин-1.
11 Определение пусковых характеристик механизма
Фактическая скорость передвижения крана определяется по формуле:
где U и Uр – требуемое и фактическое передаточные числа привода.
Время пуска механизма передвижения без груза определяется по формуле:
где – коэффициент учитывающий влияние вращающихся масс привода
механизма за исключением ротора двигателя и муфты быстроходного вала
установленного на быстроходном валу принимаем = 125;
I – момент инерции ротора двигателя и муфты
Ip – момент инерции ротора двигателя кг · м2;
Iм1 – момент инерции муфты быстроходного вала 1 Iм1 = 01
Tср.п. – средний пусковой момент двигателя определяем по формуле:
Tном. – номинальный момент двигателя Н · м;
Tс – момент статического сопротивления на валу двигателя:
F'пер – сопротивления передвижению крана без груза (см. п. 2.6);
V фпер. – фактическая скорость передвижения крана мс;
– КПД механизма передвижения крана = 085.
Ускорение при пуске определяется по формуле:
Таблица 1 – Проверка полученных значений пусковых характеристик на соответствие рекомендуемым значениям для механизма передвижения
Допускаемое значение
Проверка фактического запаса сцепления колес с рельсами:
где Fпр – суммарная нагрузка на приводные колеса без груза:
zпр – количество приводных колес шт;
z – общее количество принятых ходовых колес шт.
φ – коэффициент сцепления ходовых колес с рельсами принимаем
φ = 015 согласно [1 с. 33];
F'пер – сопротивления передвижению крана без груза:
f – коэффициент трения в подшипниках качения колеса (см. п. 2.5);
– коэффициент трения качения ходового колеса по рельсам (см. п. 2.5).
Следовательно условие выполняется.
12 определение тормозных характеристик привода
Рекомендуемое замедление механизма передвижения в соответствии с рекомендациями [1 с. 32] равно: [a] = 01 02 мс2 принимаем среднее значение [a] = 015 мс2.
Тогда время торможения крана без груза определим по формуле:
Сопротивление при торможении крана без груза определяется по формуле аналогично п. 2.12:
Момент статических сопротивлений на тормозном валу при торможении крана определяется по формуле:
где – cопротивление при торможении крана без груза Н·м;
Uр – фактическое передаточное число привода.
Момент сил инерции при торможении крана без груза определяется по формуле:
где tТ – время торможения крана без груза c;
Расчетный тормозной момент на валу тормоза определяется по формуле:
Тормозной момент тормоза встроенного в выбранный мотор-редуктор составляет что соответствует расчетному значению.
13 Проверка пути торможения
Фактическая длина пути торможения и минимальная длина пути торможения согласно [1 с. 31] определяются из условия:
V фпер. – фактическая скорость передвижения крана мс.
Условие соответствует рекомендациям .
РАСЧЕТ МЕХАНИЗМА ПЕРЕДВИЖЕНИЯ ТЕЛЕЖКИ
- скорость передвижения крана Vпер. = 041 мс;
Для данной тележки грузоподъемностью 50 тонн принимаем 8 ходовых колес
Рис.4. 1 Схема механизма передвижения грузовой тележки.
Mг.т=04*Q=04*50=20 т.
Принимаем для среднего режима работы двухребордное ходовое колесо диаметром Dк = 400 мм = 04 м.
Ak Aг– площади поверхностей крана и груза (рассчитанные значения площади крана – 1174 м2 груза выбираем по таблице гп -25 м2)
k – коэф. учитывающий высоту конструкции -11;
Так как у нас используется в конструкции 4 двигателя тогда найденная необходимая мощность делится поровну на каждый из них.
Выбираем мотор-редуктор F-67.
Передаточное число U=5094
Принимаем зубчатую муфту :
– крутящий момент Tмуф. =700 Н·м;
I – момент инерции ротора двигателя и муфты:
Iм1– момент инерции муфты быстроходного вала 1 Iм1 = 01
Таблица 1 – Проверка полученных значений пусковых характеристик на
соответствие рекомендуемым значениям для механизма передвижения
12 Определение тормозных характеристик привода
Условие соответствует рекомендациям [1 с.32 табл. 1.26].
РАСЧЕТ МЕХАНИЗМА ПОДЪЕМА
В качестве исходных данных для расчета механизма подъема используем следующие данные:
- скорость подъема груза Vпод = 013 мс;
- высота подъема Н = 145 м;
- продолжительность включения механизма подъема ПВ = 25%.
1 Определение кратности полиспаста
Кратность полиспаста механизма подъема груза Uп = 4 для сдвоенного полиспаста.
Рис. 5.1 Схема сдвоенного полиспаста
2 Определение усилия в канате набегающем на барабан
где Q – номинальная грузоподъемность крана кг;
z – число простых полиспастов в системе;
Un – кратность полиспаста;
– общий КПД полиспаста и обводных блоков ().
где бл – КПД одного блока принимаем бл = 098 для подшипников качения.
где – количество обводных блоков (см. рис. 1).
Выбираем канат по расчетному разрывному усилию в канате:
где k – коэффициент запаса прочности принимаемый в зависимости от назначения
и режима работы крана принимаем k = 55 согласно [1 c. 55 табл. 2.3].
В соответствии с рекомендациями [1 c. 277 табл. III.1.1] принимаем канат двойной свивки типа ЛК-Р 6×19 (1 + 6 + 66) + 1о.с. диаметром d = 280 мм имеющий при маркировочной группе проволок 1568 МПа с разрывным усилием F = 39600 H.
Проверка фактического коэффициента запаса прочности каната:
4 Определение требуемого диаметра блоков и барабана
Допускаемый диаметр блока и барабана по средней линии навитого стального каната определяется по формуле:
где d – диаметр стального каната мм;
e – коэффициент зависящий от типа крана типа привода и режима работы
механизма принимаем e = 25 согласно [1 c. 59 табл. 2.7].
принимаем Dб = 810мм.
5 Выбор крюковой подвески
Принимаем крюковую подвеску ООО”Завод Промышленного Краностроения”
D = 810 мм; dк = 28 мм; режим работы средний; грузоподъемность 50 т;
6 Определение размеров барабана
Длина каната навиваемого на барабан с одного полиспаста определяется по формуле:
где H – высота подъёма груза м;
Dб – диаметр барабана м;
z1 – число запасных (неиспользуемых) витков на барабане до места крепления:
z1 = 15 2 согласно [1 c. 60];
z 2 – число витков каната находящихся под зажимным устройством на барабане
z2 = 3 4 согласно [1 c. 60].
Так как полиспаст в системе сдвоенный и z = 2 то общая длина всего каната будет вдвое больше.
Рабочая длина барабана для навивки каната с одного полиспаста определяется по формуле:
где Lк – длина каната навиваемого на барабан м;
t – шаг витка (см. рис. 2) принимается в зависимости от диаметра каната: при
d = 280 мм тогда t = 34 мм = 0034 м в соответствии с рекомендациями
[1 c. 60 табл. 2.8];
Рис. 2 Профиль канавок на барабане
m – число слоев навивки (для нарезного барабана m = 1);
d – диаметр каната м;
Dб – диаметр барабана по средней линии навитого каната м;
φ – коэффициент неплотности навивки: φ = 1 для нарезных барабанов
Полная длина барабана для сдвоенного полиспаста определяется по формуле:
где l – длина не нарезанной части барабана (определяется из данных крюковой подвески).
Определяем минимальную толщину стенок литого чугунного барабана по формуле:
где Dдна – диаметр дна барабана м.
Произведем проверку прочности стенки барабана т.е. определим напряжения сжатия стенки барабана по формуле:
где Fб – усилие в канате H;
Принимаем для среднего режима работы механизма материал для барабана чугун марки СЧ 15 с допускаемым напряжением [сж ] = 130 МПа.
Статическая мощность двигателя механизма подъёма определяется по формуле:
где Q – номинальная грузоподъемность крана т;
g = 981 мс2 – ускорение свободного падения;
Vпод – скорость подъема груза мс;
– КПД механизма в целом (от крюка до двигателя) принимаем согласно [1 c. 23 табл. 1.18] для подшипников качения = 085.
Номинальную мощность двигателя необходимо принимать равной или несколько меньшей статической мощности на 30 35%.
Двигатель выбираем с учетом ПВ в % и мощности.
Принимаем электродвигатель 4А280S6У3
– мощность Pэл = 75 кВт;
– частота вращения nэл = 985 мин-1;
– момент инерции ротора Ip = 292 кг · м2;
Частота вращения барабана определяется по формуле:
где Vпод – скорость подъема груза мс;
Dб – диаметр барабана м.
Расчетную мощность редуктора находим по формуле:
Где Pc – статическая мощность двигателя
- коэффициент зависящий от типа механизма – для механизма подъема – 1.
Выбираем из каталога редуктор ЦЗУ-200 с передаточным числом – 80 крутящий момент на тихоходном валу – 2000 Н*м КПД – 096
10 Выбор муфты быстроходного вала
Момент статических сопротивлений на валу двигателя с общим КПД всего механизма согласно [1 c. 23]:
где z – число простых полиспастов в системе;
Uр – фактическое передаточное число привода;
– КПД механизма в целом = 085.
Расчетный момент для выбора соединительной муфты с учетом ответственности и режима работы механизма определяется по формуле:
где k1 – коэффициент учитывающий степень ответственности механизма;
k2 – коэффициент учитывающий режим работы механизма.
Тогда согласно [1 c. 42 табл. 1.35] для механизмов подъёма: k1 = 13; k2 = 12 средний режим.
Принимаем втулочно-пальцевую муфту с тормозным шкивом
– номинальный крутящий момент Tном. =5500 Н·м;
– диаметр шкива Dшкива=400 мм;
– момент инерции Jм= 225 кгм2.
11 Выбор муфты тихоходного вала
Момент статических сопротивлений на валу барабана с КПД барабана согласно [1 c. 23]:
где б – КПД барабана (б = 095 096).
Расчетный момент для выбора соединительной муфты с учетом ответственности и режима работы механизма определяется по формуле аналогично (п. 1.10):
Принимаем зубчатую муфту встроенную в грузовой барабан:
– крутящий момент Tмуф. =98070 Н·м;
12 Определение пусковых характеристик механизма
Фактическая частота вращения барабана определяется по формуле:
где nэл. – частота вращения электродвигателя мин-1;
Фактическая скорость подъёма груза определяется по формуле:
где Dб – диаметр барабана м;
Un – кратность полиспаста.
Время пуска при подъёме груза определяется по формуле:
механизма за исключением ротора двигателя и тормозного шкива
установленного на быстроходном валу: = 11 125;
I – момент инерции ротора двигателя и тормозного шкива установленного
на быстроходном валу:
Iм – момент инерции муфты кг · м2;
Tном. – номинальный момент двигателя определяем по формуле:
Tс – момент статических сопротивлений на валу двигателя (см. п. 1.10) Н·м;
Q – номинальная грузоподъемность крана кг;
V – фактическая скорость подъёма груза мс;
соответствие рекомендуемым значениям для механизма подъёма
для массовых грузов
Момент статического сопротивления на валу двигателя при торможении механизма определяется по формуле:
– КПД механизма в целом = 085;
Необходимый по нормам Ростехнадзора момент развиваемый тормозом определяется по формуле:
где KТ – коэффициент запаса торможения принимаем KТ = 15 – для среднего
режима работы механизма.
Выбираем тормоз ТКГ-400 с L=940 мм H=620 мм Тт=1500 Н*м
14 Определение тормозных характеристик механизма
Время торможения при опускании груза определяется по формуле:
где TТ – необходимый момент развиваемый тормозом (см. п. 1.13) Н·м;
TсТ – момент статического сопротивления на валу двигателя при торможении
механизма (см. п. 1.13) Н·м.
Наибольшее допускаемое время торможения в соответствии с рекомендациями [4 с. 397]: tTmax = 1 2 с.
Замедление при торможении определяется по формуле:
Таблица 2 – Проверка полученных значений тормозных характеристик на
Замедление при торможении
Соответствует с небольшими допущениями
15 Проверка двигателя на нагрев
Во избежание перегрева двигателя необходимо чтобы развиваемая им среднеквадратическая мощность удовлетворяла условию:
Средняя квадратичная мощность электродвигателя определяется по формуле:
где Tср – средний квадратичный момент преодолеваемый электродвигателем Н·м;
nэл. – частота вращения электродвигателя мин-1.
где tп – общее время пуска при подъёме и опускании груза с;
tу – время установившегося движения с;
t – общее время работы электродвигателя с;
Tср.п. – средний пусковой момент двигателя (см. п. 1.12) Н·м;
Tс – момент статических сопротивлений на валу двигателя при подъёме Н·м;
TсТ – момент статических сопротивлений на валу двигателя при торможении механизма т.е. при опускании груза (см. п. 1.13) Н·м.
В качестве исходных данных для расчета используем график загрузки механизма в соответствии с рекомендациями [1 с. 16 рис. 1.1]. Соответственно для легкого режима работы механизма подъёма график будет иметь следующий вид (см. рис. 3):
Рис. 3 Усредненный график загрузки механизма подъёма козлового крана (для среднего режима работы)
Согласно графику за время цикла (подъём и опускание груза) механизм будет работать с номинальным грузом Q = 50000 кг – 1 раза с грузом 05·50000 кг – 5 раз с грузом 02·50000 кг – 1 раз с грузом 005·50000 кг – 3 раз
Сведем результаты расчетов с различными грузами в таблицу 3.
Таблица 3 – Результаты расчетов
Результаты расчета при Q кг
(см. [1 с.24 рис.1.2])
Время пуска при подъёме
Момент при опускании груза
Время пуска при опускании (по формуле из п.1.12
Общее время пуска при подъёме и опускании груза определяется по формуле:
где ni – число подъёмов i-го груза.
Время установившегося движения определяется по формуле:
где Hср – средняя высота подъёма груза: Hср = 08·H м;
V – фактическая скорость подъёма груза мс.
Определим общее время работы средний квадратичный момент и среднюю квадратичную мощность электродвигателя:
Pср = 266 кВт Pном = 75 кВт – следовательно условие выполняется.
РАЗРАБОТКА ЭЛЕКТРИЧЕСКОЙ СХЕМЫ ПРИВОДА МЕХАНИЗМА ПЕРЕДВИЖЕНИЯ ТЕЛЕЖКИ
Наибольшее распространение на кранах получил привод с асинхронными двигателями с фазным ротором и ступенчатым регулированием угловой скорости путем изменения сопротивления в цепи ротора. Такой привод достаточно прост надежен допускает большое число включений в час и применяется при средних и больших мощностях. С помощью резисторов в цепи ротора можно в широких пределах изменять момент при пуске получать желаемые ускорения и плавность пуска уменьшать токи и потери энергии в двигателе при переходных процессах а также получать пониженные угловые скорости.
Комплектные электроприводы охватывают все крановые асинхронные двигатели с фазным ротором при управлении от магнитных контроллеров типа ТСД. Эти электроприводы выпускают только для механизмов общепромышленного исполнения.
Электроприводы с магнитными контроллерами имеют индивидуальную защиту. Контроллеры выпускаются двух типов соответственно для возбуждаемых и невозбуждаемых электродвигателей. Первые из этих контроллеров применяют для двигателей напряжение на кольцах ротора которых не превосходит 300 В при напряжении сети 380 В; вторые – при напряжении ротора более 300 В. Применение режима динамического торможения самовозбуждением позволяет получить устойчивые посадочные скорости при диапазоне регулирования 1 : 8; благодаря импульсно-ключевому включению на первом положении подъема обеспечивается регулирование диапазона скорости до 1 : 7.
Обладая повышенными регулировочными и энергетическими свойствами рассматриваемые электроприводы позволяют значительно улучшить использование двигателей и повысить надежность работы контакторной аппаратуры благодаря снижению числа включений приводов при осуществлении доводочных операций а также снизить нагрузки на механические передачи при натягивании грузовых канатов.
Силовая часть схемы управления двигателем механизма передвижения тележки изображена на рис. 6.1.
Рис. 6.1. Силовая часть схемы управления двигателем.
Цепь управления отображена на рис. 7.2. Реверсирование осуществляется контакторами КMl и КМ2. Включение тормозного электромагнита осуществляет КМ3. Контактор КМ4 осуществляет двойной разрыв силовой цепи.
Рис. 6.2. Цепь управления
Скорость регулируется контакторами КМ7 КМ10. Механические характеристики его приведены на рис.6.3.
Рис.6.3. Механические характеристики электропривода системы
управления с магнитным контроллером типа ТСД
Контактор КМ7 обеспечивает характеристику 2 КМ8 характеристику 3 КМ9 характеристику 4а КМ10 характеристику 4. Реле времени КТ1 обеспечивает переход с характеристики 3 на характеристику 4а КТ2 переход с характеристики 4а на характеристику 4 обеспечивая автоматический разгон на дух последних ступенях переключения.
Диодно-резисторный коммутатор работает в импульсно-ключевом режиме. Узел обратной связи по ЭДС ротора получает питание от зажимов обмотки ротора. В цепи выпрямителя включены стабилитрон VD17 и управляющая часть оптрона VS8. Выходная часть оптрона включена в управляющие цепи тиристоров блока VS. По уставке стабилитрона осуществляется автоматическое поддержание роторного напряжения независимо от нагрузки.
Максимальная защита двигателя осуществляется с помощью реле тока КА1 нулевая защита реле KV1. Реле KV2 осуществляет включение блоков бездуговой коммутации.
Расчет САПР APM Winmachine.
В качестве расчета в САПР APMWinmachine было выбрано ходовое колесо козлового крана.
Так как конструкция ходового колеса козлового крана симметрична относительно главных осей то для удобства строим одну четвертую детали а также горизонтальную ось симметрии. В результате чего получается стержневая конструкция. Пользуясь командами вкладки «Инструменты» достраиваем верхнюю часть детали (Рис.8.1).
Рис.7.1.Колесо в стержневой конструкции
Командой «Рисование-Пластина-Произвольная с разбивкой» разбиваем получившуюся конструкцию на конечные элементы с максимальной длиной стороны 20 мм. Удаляем все вспомогательные стержни при этом оставляем узлы и пластины а также горизонтальную ось симметрии (Рис.7.2.).
Рис.7.2. Колесо разбитое на пластины
Следующим шагом при помощи команды «Полярный массив» достраиваем конструкцию ходового колеса путем вращения верхней половины сечения относительно горизонтальной оси симметрии. В появившемся диалоговом окне указываем количество секций 36 угол 3600 и ставим галочку в пункте «Создавать объемные элементы». Пользуюсь фильтрами вида необходимо удалить все вспомогательные стержни пластины оставляя только узлы и объемные элементы (Рис.7.3.)
Рис.7.3.Геометрическая модель колеса
Проставляем опоры (жесткая заделка) по внутреннему диаметру кранового колеса и задаем материал нашей конструкции. Прикладываем нагрузку на место пятна кантакта колеса с рельсом. Производим статистический расчет и выводим результаты(Рис.7.4 Рис 7.5. табл.7.1).
Рис.7.4. Карта напряжений.
Рис.7.5. Карта перемещений.
Результаты статистического расчета ходового колеса козлового крана.
Л - Изотропный материал
Модуль Юнга : 210000 [Нмм^2]
Коэф. Пуассона : 0.30
Плотность : 7.8e-06 [кгмм^3]
Коэф. температурного расширения : 1.2e-05 [°C]
модели 133.633730 [кг]
Центр тяжести модели ( 0.000000 359.002672 -47.500000 ) [мм]
Моменты инерции модели ( 2976359.302448 5517888.431047 2976359.302448 ) [кг·мм·мм]
Общая масса конструкции 133.63 кг
Суммарные реакции (Загружение 0)
Суммарная реакция опор
( -0.000000 -0.000000 1037000.000000 ) [Н]
Момент относительно центра масс
( -2770.608092 -0.000000 0.000001 ) [Н*мм]
Абсолютные значения:
Реакции 1037000.000000 [Н];
Момента 2770.608092 [Н*мм]
В работе приведены основные типы козловых кранов и их конструктивные особенности .Описано назначение каждого из представленных кранов .Представлена механизация участка укрупнения и сборки тепломеханического оборудования с разработкой механизмов подъема и передвижения козлового крана грузоподъемностью главного подъема 50 тонн и вспомогательного 10 тонн пролетом 42 метра и вылетом тележки 62 метра.
В представленных расчетах механизмов передвижения и подъема крана были рассчитаны такие элементы как :полиспаст крюковая подвеска двигатель редуктор барабанмуфты и тормоз. Была проведена проверка двигателя на нагрев рассчитано время пуска и торможения.
Произвели расчет ходового колеса крана в APM Win Machine на нагрузку напряжение и перемещение и получив результаты убедились что выбранное колесо имеет достаточную степень прочности и жесткости.
Кузьмин А.В. Марон Ф.А. Справочник по расчетам механизмов подъемно-транспортных машин. Справочник 2-е издание. Высшая школа 1983.
Маликов О.Б. Малкович А.Р. Склады промышленных предприятий.
Справочник. Под общей редакцией О.Б. Маликова. Машиностроение 1989ГОСТ 1050-2013 Металлопродукция из нелегированных конструкционных качественных и специальных сталей. Общие технические условия. Межгосударственный стандарт 2014
Барышев А.И. Стеблянко В.Г. ХомичукВ.А. Механизация ПРТС работ. Курсовое и дипломное проектирование транспортирующих машин: Учебное пособие Под общей редакцией А.И. Барышева - Донецк: ДонГУЭТ 2003 - 471 с. ил.
Александров М.П. Подъемно-транспортные машины. Изд. 4-е. Учебник для вузов. М.: Высшая школа 1972 г.
Курсовое проектирование грузоподъемных машин под ред. С.А. Казака. Учебное пособие М.: Высшая школа 1989.
Павлов Н.Г. Примеры расчетов кранов. Изд. 3-е. Л.: Машиностроение. 1967.
Справочник по кранам. Т.1. Под ред. М.М. Гохберга. - Л. : Машиностроение 1988. – 536 с.
СоколовС.А. Металлические конструкции подъемно-транспортных машин: учебное пособие для вузов С.А.Соколов .- СПб. : Политехника 2005. - 423с.
Справочник по Электрические машинам Под Ред. И.П. Копылова Б. К. Клокова М.: Энергоатомиздат 1998.
КасаткинА.С. Электротехника А.С. Касаткин М. В. Немцов М.: Высшая школа 2000.
Чиликин М.Г. Общий курс электропривода М.Г. Чиликин А. С. Сандлер М.: Энергоатомиздат 1984.
Системы автоматизированного проектирования: Учеб. пособие для втузов: В 9 кн. Под ред. И.П. Норенкова. – М.: Высш. шк.; 1986.
Кудрявцев Е.М. Основы автоматизации проектирования машин: Учебник для студентов вузов по спец. "Подъемно-транспортные строительные дорожные машины и оборудование". - М.: Машиностроение 1993. - 336с.
Норенков И.П. Основы автоматизированного проектирования : учебник для вузов И.П. Норенков. – 3-е изд. перераб. и доп. – М.: Изд-во МГТУ им. Н.Э.Баумана 2006 . – 448 с.
Кран козловой.dwg
Грузоподъемность 5010 тонн
Высота главного подъема 14
Высота вспомогательного подъема 16
Скорость движения крана 0
Скорость передвижения тележки 0
Ходовая тележка.dwg

Скорость передвижения
Мотор-редуктор: МЧ-160
ВКР 1806.10.00.000 СБ
Расчет APM.dwg

Расчет ходового колеса козлового крана грузоподъемностью 50 тонн в APM Win Machine
Геометрическая модель колеса
Механизация.dwg

бъединенное здание механической
астерских и материального склада;
открытая площадка центрального материального склада;
объединенное здание тепломонтажной
и электромонтажной мастерских и склада оборудования;
- бетонорастворное хозяйство;
временная котельная;
объединенное здание мастерских
и складов обмуровки и теплоизоляции;
тепляк для производства сварочных работ;
-участок управления гидротехническим строительством;
участок управления строительной механизации;
склад горючесмазочных материалов;
плотнично-опалубочная мастерская;
- площадка строительных конструкций;
-укрупнительно-сборочная площадка
тепломеханического оборудования
-участок сборки водогрейных котлов
-участок сборки паровых турбин
-участок сборки регенариваных подогревателей
Механизация участка сборки
ВКР 1806.00.00.000 И1
Схема стройбазы тепловой электростанции средней мощности
Участок сборки тепломеханического оборудования
Рекомендуемые чертежи
- 03.03.2014
Свободное скачивание на сегодня
Другие проекты
- 23.08.2014