Коробка скоростей консольно-фрезерного станка 6Р82Ш




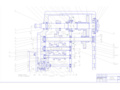
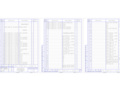
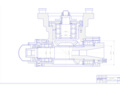
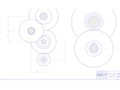
- Добавлен: 25.10.2022
- Размер: 917 KB
- Закачек: 4
Описание
Состав проекта
![]() |
![]() |
![]() ![]() ![]() ![]() |
![]() ![]() ![]() ![]() |
![]() ![]() ![]() ![]() |
![]() ![]() ![]() ![]() |
![]() ![]() ![]() ![]() |
![]() ![]() |
![]() ![]() |
![]() ![]() |
![]() ![]() |
![]() ![]() |
![]() ![]() ![]() |
Дополнительная информация
Коробка скоростей.dwg

Свертка.dwg

Спец. узел.dwg

Спецификация.dwg

широкоуниверсального
консольно-фрезерного
ВлГУ. 151001. 81. 03. 002.СБ
ВлГУ. 151001. 81. 4 .03. 001
ВлГУ. 151001. 81. 4. 03. 002
ВлГУ. 151001. 81. 4. 03. 003
ВлГУ. 151001. 81. 4. 03. 004
ВлГУ. 151001. 81. 4. 03. 005
ВлГУ. 151001. 81. 4. 03. 006
ВлГУ. 151001. 81. 4. 03. 007
ВлГУ. 151001. 81. 4. 03. 008
ВлГУ. 151001. 81. 4. 03. 009
ВлГУ. 151001. 81. 4. 03. 010
ВлГУ. 151001. 81. 4. 03. 011
ВлГУ. 151001. 81. 4. 03. 012
ВлГУ. 151001. 81. 4. 03. 013
ВлГУ. 151001. 81. 4. 03. 014
ВлГУ. 151001. 81. 4. 03. 015
ВлГУ. 151001. 81. 4. 03. 016
ВлГУ. 151001. 81. 4. 03. 017
ВлГУ. 151001. 81. 4. 03. 018
ВлГУ. 151001. 81. 4. 03. 019
ВлГУ. 151001. 81. 4. 03. 020
ВлГУ. 151001. 81. 4. 03. 021
ВлГУ. 151001. 81. 4. 03. 022
ВлГУ. 151001. 81. 4. 03. 023
ВлГУ. 151001. 81. 4. 03. 024
ВлГУ. 151001. 81. 4. 03. 025
ВлГУ. 151001. 81. 4. 03. 026
ВлГУ. 151001. 81. 4. 03. 027
Кольцо 65-76-11.6-2-4
Кольцо 127.5-141.5-14.6-2-4
Подшипник ГОСТ 8338-75
Подшипник 7215 ГОСТ 27365-87
Подшипник 67515 ГОСТ 27365-87
Кольцо ГОСТ 13943-80
Гайка М20-6H.5 ГОСТ 5915-70
Муфта упругая втулочнр-
польцевая 45-40-I.45-II.2-У3
Кинематика.dwg

Курсовой.docx
На станках можно изготавливать металлические модели штампы прессформы шаблоны кулачки и т.п.
Для обработки различного вида поверхностей а также крупногабаритных деталей превышающих по своим размерам габариты стола шпиндельная головка смонтирована на выдвижном хоботе и может поворачиваться под любым углом в двух взаимно перпендикулярных плоскостях.
Горизонтальный шпиндель станка может быть использован при обработке плоскостей торцевыми и цилиндрическими фрезами. Возможно как раздельная так и одновременная работа обоими шпинделями. При установке серег станки могут быть использованы как обычные горизонтально-фрезерные
Технологические возможности станков могут быть расширены с применением делительной головки поворотного круглого стола и других приспособлений.
Техническая характеристика и жесткость станков позволяют полностью использовать возможности быстрорежущего твердосплавного инструмента.
I. Обоснование технических характеристик.
Определение предельных габаритных размеров.
Размер Dб и Dм - наибольший и наименьший диаметры фрезы; b – ширина рабочего стола.
При ширине стола b = 320 мм получим:
Dб = (64 96); Dб = 80 мм
Dм = (32 64); Dм = 40 мм
Вб и Вм - наибольшая и наименьшая ширина фрезерования.
Вб = (60 80); Вб = 80 мм
Вм = (30 40); Вм = 30 мм
Определение рациональных режимов обработки:
Наибольшая глубина резанья для сталей при максимальной ширине фрезерования tб = 12 мм при минимальной - tб = 6 мм. Наименьшая глубина резанья для сталей tм = 0.5 мм. Наибольшая глубина резанья для чугунов при максимальной ширине фрезерования tб = 4 мм при минимальной - tб = 2 мм. Наименьшая глубина резанья для чугунов tм = 0.5 мм.
Наибольшая подача при обработке самой мягкой стали:
- фрезы торцевые из Т5К10 Szб = 0.25 ммзуб.
Наименьшая подача при обработке самой мягкой стали:
- фрезы торцевые из Т5К10 Szм = 0.08 ммзуб.
Наибольшая подача при обработке самой твердой стали:
- фрезы торцевые из Т5К10 Szб = 0.18 ммзуб.
Наименьшая подача при обработке самой твердой стали:
- фрезы торцевые из Т5К10 Szм = 0.07 ммзуб.
Наибольшая подача при обработке чугуна:
- фрезы торцевые из ВК8 Szб = 0.35 ммзуб.
Наименьшая подача при обработке чугуна:
- фрезы торцевые из ВК8 Szм = 0.17 ммзуб.
При чистовом фрезеровании:
- Sz = Cs Rx Dz ty где Cs = 0.022 x = 1.25 y = 1 z = 1 Dб = 80 мм Dм = 40 мм tб = 12 мм tм = 0.5 мм R = 20 мкм = 0.2 мм.
Szб = 0.022 0.21.25 8010.51 ; Szб = 0.47 ммзуб;
Szм = 0.022 0.21.25 401121; Szм = 0.009 ммзуб.
Находим наибольшую и наименьшую скорости резанья:
Cv = 332; y = 0.4; z = 0.2; m = 0.2; n = 1; q = 0.2; Dм = 40 мм; Tм = 70 мин; tм = 0.5 мм; Sм = 0.009 ммзуб; Bм = 30 мм.
Vб = 332 400.2 1800.2 0.50.1 0.0090.4 51 300.2
Cv = 64.7; y = 0.4; z = 0.15; m = 0.25; n = 0.1; q = 0.25; Dб = 80 мм; Tб = 300 мин; tб = 12 мм; Sб = 0.35 ммзуб; Bб = 80 мм.
Vм = 64.7 800.25 3000.25 120.1 9 0.350.4 300.1 800.15
Найдём предельные значения частот вращения шпинделя:
nб = 1000 Vб Dм = 1000 204.998 40 = 1631 обмин;
nм = 1000 Vм Dб = 1000 8.435 80 = 33.56 обмин.
Найдём предельные значения подач:
Sб = Szб zб nм = 0.35 30 109.9 = 352.38 мммин;
Sм = Szм zм nб = 0.009 5 337.6 = 73.39 мммин.
Определим диапазон регулирования:
RV = nб nм = 1631 33.56 = 48.59;
RS = Sб Sм = 352.38 73.39 = 4.801.
Определение силовых параметров процесса резанья.
Определим главную составляющую силы резанья при фрезеровки:
Pz = C tx Syz Bz z Dn nw
C = 8.2 10-1; y = 0.8; z = 0.95; n =1.1; w = 0.2; t = 12 мм; S = 0.35 ммзуб; B = 80 мм; z = 30; D = 80 мм; n = 33.56 обмин.
Pz = 8.2 10-1 121.1 0.350.8 800.95 30 801.1 33.560.2
Крутящий момент на шпинделе:
Mкр = 41.943 80 1000 2 = 1.677 кН м
Расчет эффективной мощности привода и мощности электродвигателя.
Эффективная мощность:
Nэ = 41.943 8.435 61.2 = 5.781 кВт
Мощность электродвигателя:
Nдв = Nэ k где k = 1.2; = 0.8
Nдв = 5.781 1.2 0.8 = 6.02 кВт
Выбираем двигатель типа – 4A132S4Y3 у которого N = 7.5 кВт число оборотов U = 1460 мин-1.
II. Кинематический расчет.
Определение числа ступеней привода.
Зададимся знаменателем геометрической прогрессии привода равным φ = 1.26 тогда
Зная Zn пишем структурную формулу привода в общем виде:
Zn = P1 · P2 · P3 · · Pm
В частом виде Zn = 18 = 3 · 3 · 2; с учетом кинематического расположения основных и переборных групп и их характеристик
Zn = 18 = 3(1) · 3(3) · 2(9).
Из структурной сетки видно:
Пусть i7 = φ3.5 = 2.245 тогда φ3.5 : i8 = φ9 т.е. i8 = 1φ5.5 = 13.565
Пусть тогда i3 = = 1φ3 = 12.
Строим лучи графика соответствующие минимальны передаточным отношениям imin
Частота вращения вала IV будет:
Частота вращения вала III будет:
Частота вращения вала II будет:
Теперь строим лучи соответствующие максимальным передаточным отношениям imax
Частота вращения IV вала:
Частота вращения III вала:
Частота вращения II вала:
Построим лучи соответствующие средним передаточным отношениям i
Частота вращения III вала:
Для завершения построения графика частоты вращения проводим лучи параллельные построенным лучам i8 аналогично лучам структурной сетки.
Определим реальное передаточное отношение через числа зубьев колес с использованием нормали станкостроения Н21-5.
Определение частот вращения валов
Расчетное значение частоты;
Стандартное значение частоты; обмин.
n2 = n1 · φ = 31.5 · 1.26 = 42.28
n3 = n1 · φ2 = 31.5 · 1.58 = 50.0
n4 = n1 · φ3 = 31.5 · 2 = 63.01
n5 = n1 · φ4 = 31.5 · 2.52 = 79.39
n6 = n1 · φ5 = 31.5 · 3.18 = 100.04
n7 = n1 · φ6 = 31.5 · 4 = 126.05
n8 = n1 · φ7 = 31.5 · 5.04 = 158.82
n9 = n1 · φ8 = 31.5 · 6.35 = 200.11
n10 = n1 · φ9 = 31.5 · 8 = 252.12
n11 = n1 · φ10 = 31.5 · 10.09 = 317.69
n12 = n1 · φ11 = 31.5 · 12.71 = 400.3
n13 = n1 · φ12 = 31.5 · 16.01 = 504.38
n14 = n1 · φ13 = 31.5 · 10.18 = 635.52
n15 = n1 · φ14 = 31.5 · 25.42 = 800.75
n16 = n1 · φ15 = 31.5 · 32.03 = 1008.95
n17 = n1 · φ16 = 31.5 · 40.36 = 1271.27
n18 = n1 · φ17 = 31.5 · 50.85 = 1601.81
III. Определение силовых и кинематических параметров привода.
Так как для расчетов нас интересуют наиболее нагруженный режим то рассчитываем силовые и кинематические параметры для наименьших угловых скоростей валов.
Расчеты приведены в таблице
Минимальная частота вращения n обмин
Минимальная угловая скорость 1с
Максимальный вращающий момент Т Н · м
P1 = Pдв · м · пк = 6.63
P2 = P1 · зп · пк = 6.36
P3 = P2 · зп · пк = 5.99
P4 = P3 · зп · пк = 5.58
P5 = P4 · зп · пк = 5.41
IV. Геометрический расчет привода.
Расчет геометрических параметров зубчатых колес.
– Для первой ступени выбираем модуль m = 3.
Диаметр делительной окружности d = m · z = 3 · 27 = 81 мм.
Диаметр вершин зубьев da = d + 2 · m = 81 + 2 · 3 = 87 мм.
Диаметр впадин зубьев df = d – 2.4 · m = 81 – 2.4 · 3 = 73.7 мм.
Диаметр делительной окружности d = m · z = 3 · 53 = 159 мм.
Диаметр вершин зубьев da = d + 2 · m = 159 + 2 · 3 = 165 мм.
Диаметр впадин зубьев df = d – 2.4 · m = 159 – 2.4 · 3 = 151.8 мм.
Межосевое расстояние a = m · (z1 + z2)2 = 3 · (27 + 53)2 = 120 мм.
Ширина венца колес b = 0.2 · a = 0.2 · 120 = 24 мм.
– Для второй ступени выбираем модуль m = 4.
Диаметр делительной окружности d = m · z =4 · 19 = 76 мм.
Диаметр вершин зубьев da = d + 2 · m = 76 + 2 · 4 = 84 мм.
Диаметр впадин зубьев df = d – 2.4 · m = 76 – 2.4 · 4 = 66.4 мм.
Диаметр делительной окружности d = m · z = 4 · 22 = 88 мм.
Диаметр вершин зубьев da = d + 2 · m = 88 + 2 · 4 = 96 мм.
Диаметр впадин зубьев df = d – 2.4 · m = 88 – 2.4 · 4 = 78.4 мм.
Диаметр делительной окружности d = m · z = 4 · 16 = 64 мм.
Диаметр вершин зубьев da = d + 2 · m = 64 + 2 · 4 = 72 мм.
Диаметр впадин зубьев df = d – 2.4 · m = 64 – 2.4 · 4 = 54.4 мм.
Диаметр делительной окружности d = m · z = 4 · 35 = 140 мм.
Диаметр вершин зубьев da = d + 2 · m = 140 + 2 · 4 = 148 мм.
Диаметр впадин зубьев df = d – 2.4 · m = 140 – 2.4 · 4 = 130.4 мм.
Диаметр делительной окружности d = m · z = 4 · 32 = 128 мм.
Диаметр вершин зубьев da = d + 2 · m = 128 + 2 · 4 = 136 мм.
Диаметр впадин зубьев df = d – 2.4 · m = 128 – 2.4 · 4 = 118.4 мм.
Диаметр делительной окружности d = m · z = 4 · 38 = 152 мм.
Диаметр вершин зубьев da = d + 2 · m = 152 + 2 · 4 = 160 мм.
Диаметр впадин зубьев df = d – 2.4 · m = 152 – 2.4 · 4 = 142.4 мм.
Межосевое расстояние a = m · (z1 + z2)2 = 4 · (16 + 38)2 = 108 мм.
Ширина венца колес b = 0.2 · a = 0.2 · 108 = 21.6 мм.
– Для третьей ступени выбираем модуль m = 4.
Диаметр делительной окружности d = m · z = 4 · 27 = 108 мм.
Диаметр вершин зубьев da = d + 2 · m = 108 + 2 · 4 = 116 мм.
Диаметр впадин зубьев df = d – 2.4 · m = 108 – 2.4 · 4 = 98.4 мм.
Диаметр делительной окружности d = m · z = 4 · 17 = 68 мм.
Диаметр вершин зубьев da = d + 2 · m = 68 + 2 · 4 = 76 мм.
Диаметр впадин зубьев df = d – 2.4 · m = 68 – 2.4 · 4 = 58.4 мм.
Диаметр делительной окружности d = m · z = 4 · 37 = 148 мм.
Диаметр вершин зубьев da = d + 2 · m = 148 + 2 · 4 = 156 мм.
Диаметр впадин зубьев df = d – 2.4 · m = 148 – 2.4 · 4 = 138.4 мм.
Диаметр делительной окружности d = m · z = 4 · 46 = 184 мм.
Диаметр вершин зубьев da = d + 2 · m = 184 + 2 · 4 = 192 мм.
Диаметр впадин зубьев df = d – 2.4 · m = 184 – 2.4 · 4 = 174.4 мм.
Диаметр делительной окружности d = m · z = 4 · 26 = 104 мм.
Диаметр вершин зубьев da = d + 2 · m = 104 + 2 · 4 = 112 мм.
Диаметр впадин зубьев df = d – 2.4 · m = 104 – 2.4 · 4 = 94.4 мм.
Межосевое расстояние a = m · (z1 + z2)2 = 4 · (17 + 46)2 = 126 мм.
Ширина венца колес b = 0.2 · a = 0.2 · 126 = 25.2 мм.
– Для четвертой ступени колес с числом зубьев z1 = 82 и z2 = 38 выбираем модуль m = 3; а для колес с числом зубьев z1 = 19 и z2 = 69 выбираем модуль m = 4.
Диаметр делительной окружности d = m · z = 3 · 82 = 246 мм.
Диаметр вершин зубьев da = d + 2 · m = 246 + 2 · 3 = 252 мм.
Диаметр впадин зубьев df = d – 2.4 · m = 246 – 2.4 · 3 = 238.8 мм.
Диаметр делительной окружности d = m · z = 3 · 38 = 114 мм.
Диаметр вершин зубьев da = d + 2 · m = 114 + 2 · 3 = 120 мм.
Диаметр впадин зубьев df = d – 2.4 · m = 114 – 2.4 · 3 = 106.8 мм.
Межосевое расстояние a = m · (z1 + z2)2 = 3 · (82 + 38)2 = 180 мм.
Ширина венца колес b = 0.2 · a = 0.2 · 180 = 36 мм.
Диаметр делительной окружности d = m · z = 4 · 19 = 76 мм.
Диаметр делительной окружности d = m · z = 4 · 71 = 284 мм.
Диаметр вершин зубьев da = d + 2 · m = 284 + 2 · 4 = 292 мм.
Диаметр впадин зубьев df = d – 2.4 · m = 284 – 2.4 · 4 = 274.4 мм.
Межосевое расстояние a = m · (z1 + z2)2 = 4 · (19 + 71)2 = 180 мм.
Расчет диаметров валов
Диаметры валов рассчитываются приближенно по формуле
где M = T – крутящий момент равный вращающему моменту на валу;
[]k – допускаемое напряжение на кручение.
V. Определение контактных напряжений и напряжений изгиба зубьев зубчатых колес привода.
Выбор материала и термообработки
Определим контактные напряжения в зацеплении H Нм по формуле:
где K – вспомогательный коэффициент (для прямозубых колес K = 436);
Ft = 2T · 103 d2 – окружная сила в зацеплении;
KHα – коэффициент учитывающий распределение нагрузки между зубьями (для прямозубых колес KHα = 1);
KH – коэффициент неравномерности нагрузки по длине зуба
KH – коэффициент динамической нагрузки зависящий от окружной скорости колес и степени точности передачи.
Определим напряжения изгиба зубьев шестерни и колеса:
для цилиндрических колес
где: KFα – аналогичен KHα (для прямозубых колес KFα = 1);
KF – аналогичен KH (для прирабатывающих колес KF = 1);
YF1 и YF2 – коэффициент формы зуба шестерни и колеса;
Определение контактных напряжений для III вала.
Материал для всех колес – Сталь 40Х.
Термообработка: закалка ТВЧ HRC 45 ÷ 50.
v = 29 · 140 = 4.09 (мс) KH = 1.14;
Ft = 2 · 206 · 103 140; Ft = 2942.86 (Н);
d2 = 140 мм; b2 = 21.6 мм;
v = 29 · 128 = 3.7 (мс); KH = 1.10;
Ft = 2 · 206 · 103 128; Ft = 3218.75 (Н);
d2 = 128 мм; b2 = 21.6 мм;
v = 29 · 158 = 4.5 (мс); KH = 1.17;
Ft = 2 · 206 · 103 158; Ft = 2607.59 (Н);
d2 = 158 мм; b2 = 21.6 мм;
v = 11 · 184 = 4.5 (мс); KH = 1.17;
Ft = 2 · 507 · 103 184; Ft = 5510.86 (Н);
d2 = 184 мм; b2 = 25.2 мм;
Допустимое значение []H;
[]H = 14 · 50 + 170 = 870 (Нмм2);
Условие прочности по контактным напряжениям H []H выполняется для всех колес III вала.
Определение напряжений изгиба для III вала.
YF1 = 4.10; YF2 = 3.75; Y = 1; KFα = 1; KF = 1; KH = 1.11; Ft = 2942.86 (Н); b2 = 21.6 мм; m = 4;
YF1 = 3.98; YF2 = 3.78; Y = 1; KFα = 1; KF = 1; KH = 1.10; Ft = 3218.75 (Н); b2 = 21.6 мм; m = 4;
YF1 = 4.28; YF2 = 3.73; Y = 1; KFα = 1; KF = 1; KH = 1.40; Ft = 3218.75 (Н); b2 = 21.6 мм; m = 4;
YF1 = 4.27; YF2 = 3.66; Y = 1; KFα = 1; KF = 1; KH = 1.40; Ft = 5510.86 (Н); b2 = 25.2 мм; m = 4;
Допустимое значение []F;
Для колес из стали твердостью HRC 45 ÷ 50 и модулем m = 4 принимаем []F = 370 (Нмм2).
Условие прочности по напряжениям изгиба F []F выполняется для всех колес на III вала.
VI. Расчетные схемы валов коробки скоростей.
Горизонтальная плоскость:
а) Определение реакции в опорах:
10.86 · 0.171 + 2607.59 · 0.266 – RBx · 0.334 = 0
– 5510.86 · 0.162 – 2607.59 · 0.067 + RAx · 0.334 =0
б) Строим эпюру изгибающих моментов относительно оси X:
MY2 = 3196.01 · 0.171 = 546.52 Н · м;
MY3 = 546.41 · 0.067 = 36.58 Н · м;
Вертикальная плоскость:
– 2005.59 · 0.171 + 949.09 · 0.266 + RBY · 0.334 = 0
– 949.09 · 0.067 + 2005.59 · 0.162 – RAY · 0.334 = 0
б) Строим эпюру изгибающих моментов относительно оси Y:
MX2 = 270.95 · 0.171 = 46.33 Н · м;
MX3 = 782.38 · 0.067 = 52.42 Н · м;
Строим эпюру крутящих моментов:
Mкр = Mz = 206 Н · м
Определение суммарной радиальной реакции:
Определение суммарного изгибающего момента в опасном сечении:
VII. Уточненный расчет валов.
Определяем предел выносливости стали 40Х
Осевой момент сопротивления вала:
Полярный момент инерции сопротивления вала
Нормальное напряжение
Касательные напряжения от нулевого цикла
Определение коэффициента концентрации нормальных и касательных напряжений
Определение предел выносливости
Определение коэффициента запаса прочности по нормальным и касательным напряжениям
Определяем общий коэффициент запаса прочности
Сравниваем общий коэффициент запаса прочности с допускаемым:
Т.е. условие прочности выполняется.
VIII. Проверочный расчет подшипников.
Пригодность подшипников определяется сопоставлением расчетной динамической грузоподъемности Cгр = базовой Cг.
Расчетная грузоподъемность Cгр определяется по формуле:
где m = 3 для шариковых подшипников;
Lh = 10000 ч для зубчатых передач;
RE – эквивалентная динамическая нагрузка:
где Ra – осевая нагрузка подшипника;
Rr = R – суммарная реакция подшипника;
V – коэффициент вращения (V = 1);
X – коэффициент радиальной нагрузки;
K – коэффициент безопасности;
KT – температурный коэффициент (KT = 1).
Cгр Cг подшипник годен.
Проверяем на смятие:
z – число шлицев z = 6;
Расчетная поверхность смятия
Условие прочности на смятие шлицев выполняется.
Список использованной литературы.
“Металлорежущие станки” методические указания и контрольные задания для выполнения курсового проекта студентами заочного отделения специальности 120100 Р.А. Тихомиров В.Н. Жарков. Владимир 2003 г.
“Металлорежущие станки. Кинематический расчет коробок скоростей и подач” методические указания к выполнению курсового проекта для студентов заочного отделения специальности 120100 В.Г. Гусев В.Н. Жарков. Владимир 2004 г.
“Обоснование технических характеристик приводов металлорежущих станков” учебное пособие к курсовому проектированию для студентов заочников Р.А. Тихомиров В.Н. Жарков. Владимир 2003 г.
А.Е. Шейнблит “Курсовое проектирование деталей машин” издание второе Янтарный сказ 2002 г.
“Металлорежущие станки” Под ред. В.К. Тепинкевича «Машиностроение» М. 1973 г.
Рекомендуемые чертежи
- 15.09.2024